Jahrelang hat der 3D-Druck immer wieder Schlagzeilen in den Massenmedien gemacht und eine große Faszination ausgeübt. Man malte sich eine Zukunft aus, in der 3D-Drucker in jeden Haushalt gehören – kühne Prognosen, die nicht ins Detail gingen und sich größtenteils nicht bewahrheiteten. Dennoch ließen sich die Möglichkeiten des 3D-Drucks nicht leugnen, selbst wenn die Technologie noch in den Kinderschuhen steckte und zu diesem Zeitpunkt erst wenige Anwendungen erschlossen waren.
Hinter dem anfänglichen Hype steckten legitime, geschäftsrelevante Anwendungsmöglichkeiten für den 3D-Druck, die sich zudem stetig vermehrten. Dank der Markteinführung einer Reihe hochleistungsfähiger Geräte für Desktop und Benchtop steigen jetzt immer mehr Unternehmen in den 3D-Druck ein, um ihr Produktangebot auszudehnen und ihren Kunden bessere Ergebnisse zu liefern.
Was kann man mit einem 3D-Drucker machen? Entdecken Sie in diesem Beitrag 25 (eher unerwartete) Anwendungsbeispiele für 3D-Druck, die die Fülle an Möglichkeiten zur sinnvollen Nutzung dieser Technologie illustrieren.
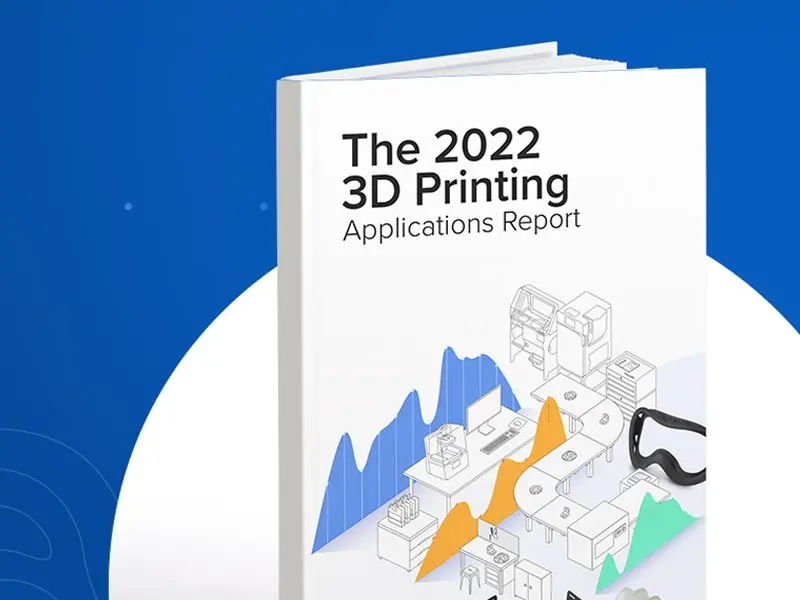
Der 3D-Druck-Anwendungsbericht 2022
Ein neuer Branchenbericht, in dem verglichen wird, wie Früh- und Neueinsteiger den 3D-Druck für ihre Geschäfte nutzen, und der zukunftsweisende Trends der Technologie erkundet.
Die Entwicklung der Autos von morgen
Der 3D-Druck bietet einen enormen Mehrwert für Lieferketten und stellt ein breites Spektrum von Produktionsanwendungen zur Verfügung. Die Technologie lässt sich immer leichter einsetzen und wird immer erschwinglicher, sodass Unternehmen additive Fertigungsverfahren betriebsintern zur Unterstützung von Fabrikabläufen anwenden können. Neue, widerstandsfähige 3D-Druckmaterialien ermöglichen die Produktion hochpräziser, funktionaler 3D-Druckteile, die als Ersatz für fertige Teile dienen können und leicht kundenspezifisch anzupassen sind. Dadurch dehnen Sie die Grenzen des Designs für Hochleistungsfahrzeuge radikal aus. Das industrielle Designstudio Vital Auto hat sich diese Technologie zunutze gemacht, um originalgetreue Prototypen und Konzeptfahrzeuge zu produzieren, und führte dank einer Vielzahl fortschrittlicher Werkzeuge – darunter eine große Flotte betriebsinterner 3D-Drucker – Iterationen im Rekordtempo durch.
„Wir nutzen 3D-Druck schon vom ersten Tag an. Wir wollten ihn in unseren Fertigungsprozess integrieren, nicht nur, um die Kosten zu senken, sondern auch damit wir den Kunden mehr Abwechslung und Vielseitigkeit bieten, was Designs und Ideen angeht“, so Design-Ingenieur Anthony Barnicott.
In der Automobilindustrie hat die additive Fertigung sich bereits in zahlreichen Phasen der Fahrzeugherstellung bewährt. Ihre Nutzung geht also weit über das Rapid Prototyping hinaus. Der 3D-Druck kommt auch für Folgendes zum Einsatz:
- Herstellung maßgefertigter, komplexer und hochleistungsfähiger Teile
- Herstellung von Werkzeugausstattung und Fertigungshilfen
- Fertigung von Ersatzteilen und Austauschteilen auf Abruf
- Senkung der Kosten und Durchlaufzeiten um bis zu 90 % verglichen mit Outsourcing
Der Kopfhörer mit dem perfekten Sitz
Durch neueste Fortschritte in der 3D-Drucktechnologie hat ein fundamentaler Wandel in der Audiobranche eingesetzt, denn noch nie war der digitale Druck individuell an die Ohren angepasster Geräte für die Audiologie, den Lärmschutz und die verbraucherorientierte Audiobranche so erschwinglich wie heute. In den vergangenen paar Jahren haben Hersteller der 3D-Druckbranche hautverträgliche, biokompatible Materialien auf den Markt gebracht, die die betriebsinterne Produktion von Ohrmodellen und Ohrstöpseln für Kopfhörer möglich machen.
Dank der individuellen Anpassung bieten diese ein einzigartiges Hörerlebnis, das ganz auf dem perfekten Sitz des In-Ear-Kopfhörers im Ohr aufbaut. Die Ohrstöpsel schmiegen sich so genau an, dass ein Herausrutschen aus dem Ohr praktisch ausgeschlossen ist, während der Tragekomfort und die Geräuschisolierung deutlich gesteigert werden.
„Wir sind begeistert von der Möglichkeit, Kopfhörer individuell anzupassen, um Kunden eine individuelle Erfahrung und damit ein noch eindringlicheres Hörerlebnis zu bieten. Das Streben nach Innovation haben Formlabs und Sennheiser gemeinsam – die Art, wie dieser Prototyp das Kundenerlebnis verbessert, ist der Beweis dafür.“
Veronique Larcher, Director AMBEO Immersive Audio bei Sennheiser
Die Herausforderungen, die mit der kundenindividuellen Fertigung einhergehen, lassen sich durch die Kombination von Formlabs' bahnbrechender Drucktechnologie mit mobilen Scanlösungen und maschinellem Lernen leicht überwinden. Von Kundenseite erleichtert das den Zugang zu maßgefertigten In-Ear-Kopfhörern enorm: Betrugen die Lieferzeiten früher vier Tage, kann man sein fertiges Produkt jetzt schon am nächsten oder sogar noch am selben Tag entgegennehmen.
Chirurgische Instrumente der nächsten Generation aus dem 3D-Drucker
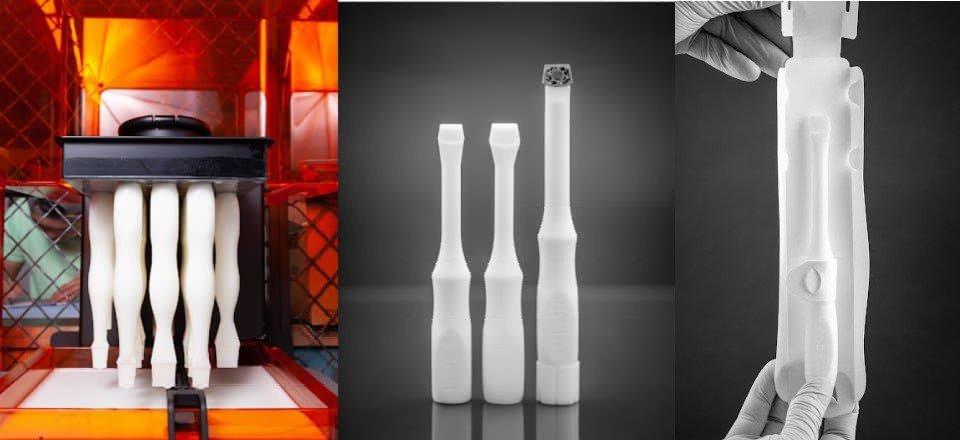
Instrumente von restor3D beim Druck, neben ihrer endgültigen Form.
Vor zehn Jahren war noch kaum davon die Rede, welchen riesigen Einfluss der 3D-Druck auf die Gesundheitsbranche haben würde, angefangen von seiner Rolle bei der Herstellung fortschrittlicher Medizinprodukte bis hin zur Erstellung patientenspezifischer Bohrschablonen für die Chirurgie. Ein Unternehmen, das wie aus dem Nichts auf diesem Markt einschlug, war restor3d. Das Unternehmen nutzt die Möglichkeiten des 3D-Drucks, um die chirurgische Versorgung erheblich zu verbessern, indem es verfahrensspezifische Polymerinstrumente druckt, die auf Implantate der Halswirbelsäule zugeschnitten sind.
Mit einer Flotte von über 25 3D-Druckern von Formlabs in seiner Produktionslinie druckt restor3d bereits die nächste Generation chirurgischer Werkzeuge. Chirurgischen Teams bieten diese verfahrensspezifischen, einzeln verpackten, sterilen Instrumente zahlreiche Vorteile:
- Ersatz von großen, teuren chirurgischen Wannen.
- Iterationsfähigkeit der Entwürfe und schnelle Einführung neuer Hilfsmittel oder Funktionen je nach den Wünschen der chirurgischen Fachleute.
- Drastische Senkung der Lieferketten- und Sterilisationskosten für Krankenhäuser.
Forschung zum Tissue Engineering wird beschleunigt
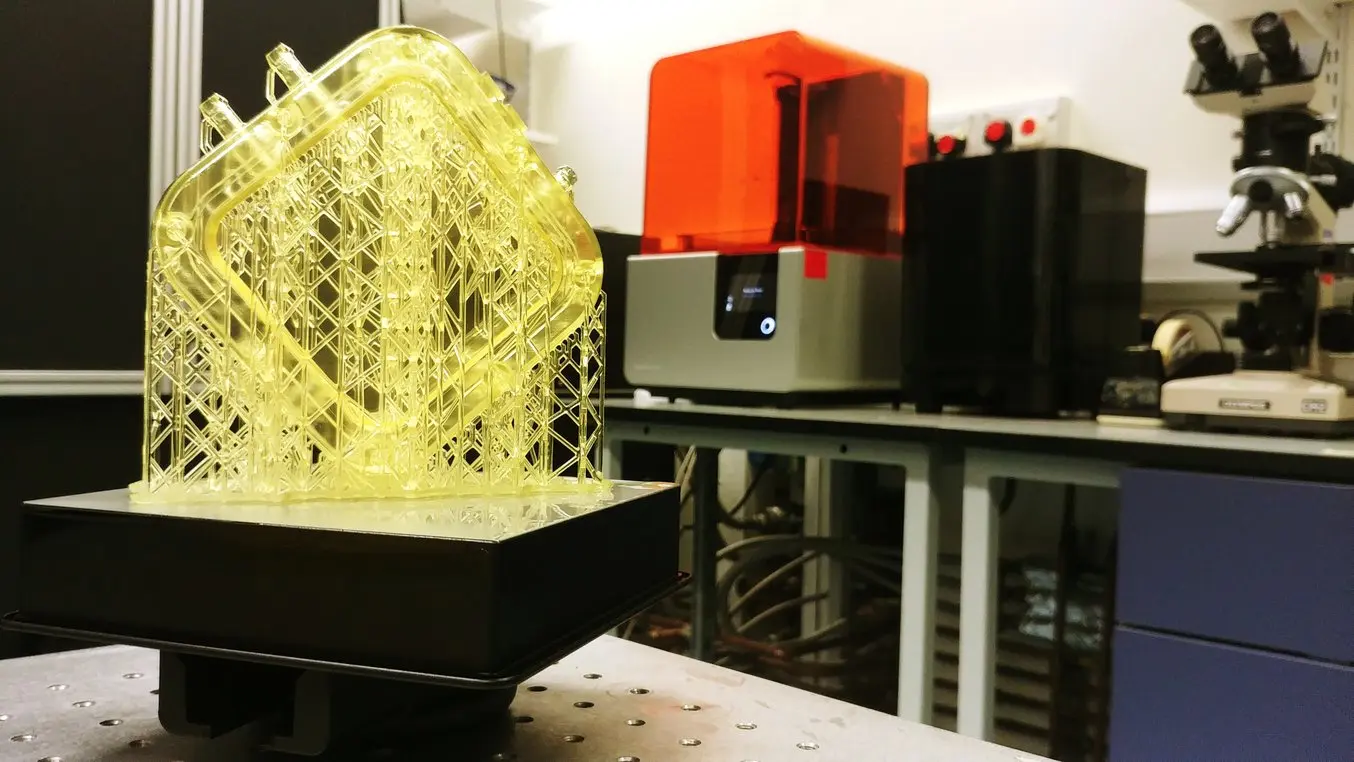
So sehr sich die 3D-Drucktechnologie in den letzten Jahren auch entwickelt hat – es gibt noch viel weitreichendere Anwendungsmöglichkeiten, die sich aktuell noch in der Entwicklung befinden. Der 3D-Druck von Organen ist eine davon.
Seit Jahrzehnten ist es der Traum von Forschenden in der regenerativen Medizin, problemlos neue Organe anfertigen zu können. Auch wenn sich dieser Anwendungsfall noch in den frühen Entwicklungsstadien befindet, trägt der Einsatz von 3D-Druckprozessen in der Produktion von organischem Transplantationsgewebe bereits die ersten Früchte.
Dr. Sam Pashneh-Tala von der University of Sheffield spielt dabei eine leitende Rolle. In seiner Forschung verwendet er hochpräzisen Desktop-Stereolithografie-3D-Druck (SLA), um die Herstellung von künstlich gezüchteten Blutgefäßen mit einer Vielzahl von geometrischen Formen zu ermöglichen. Dadurch lassen sich patientenspezifische Gefäßtransplantate entwerfen sowie chirurgische Möglichkeiten optimieren. Außerdem bietet diese Forschung eine einzigartige Testplattform für neue Medizinprodukte für Menschen mit Herz-Kreislauf-Erkrankungen – derzeit weltweit die häufigste Todesursache.
„Das Besondere an meinem Ansatz ist, dass ich in der Lage bin, Blutgefäße in Formen zu erzeugen, die enger mit denen im Körper übereinstimmen. Dies bietet bessere Möglichkeiten bei chirurgischen Eingriffen, und sogar auf den Patienten abgestimmtes Blutgefäßdesign. Ohne hochpräzisen, preiswerten 3D-Druck wäre die Erstellung dieser Strukturen nicht möglich“, so Dr. Pashneh-Tala.
Städte zum Leben erwecken
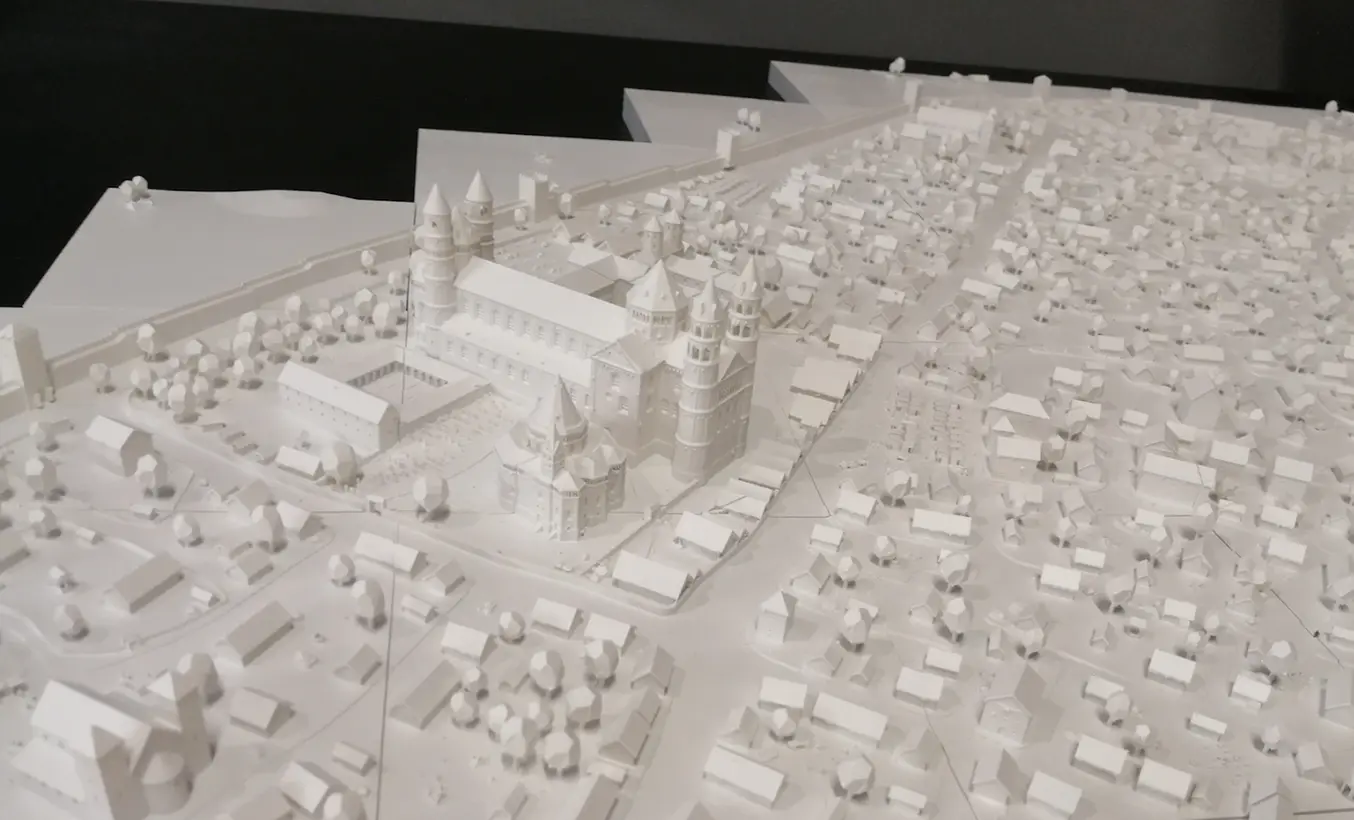
Für die Rekonstruktion dreier Städte in zwei verschiedenen Epochen wurden über 650 Einzelteile hergestellt, die aus Formlabs' White Resin gedruckt wurden und je 12 x 12 cm groß waren.
Für die Architektur, eine Branche, die bereits auf geometrischer Gestaltung, Prototypenfertigung und Modellierung basiert, sind durch 3D-Druckverfahren enorme Fortschritte zu erwarten.
Abgesehen von der Zeitersparnis bei der Modellherstellung bieten 3D-gedruckte Modelle für die Architektur auch den Vorteil, dass die Effekte bestimmter Designelemente mit größerer Wahrscheinlichkeit vorhergesehen werden können. So ist es zum Beispiel möglich, Aspekte wie den Lichteinfall innerhalb einer Struktur genauer zu bestimmen, indem man ein Modell vor sich hat, das aus einer größeren Bandbreite an Materialien gefertigt wurde.
Die Möglichkeiten des 3D-Drucks in der Architektur gehen allerdings weit über einzelne Modelle hinaus: Einige Unternehmen bilden sogar ganze Städte nach. Lehrstuhl für Architektur an der Hochschule Mainz – University of Applied Sciences. Das Ergebnis ist eine außergewöhnliche Ausstellung, die großformatige Modelle von sechs Städten in ihrem Zustand in den Jahren 800 bis 1250 n. Chr. umfasst. Die Modelle bestehen aus über 650 Teilen, die ausnahmslos mit SLA-3D-Druck erstellt wurden.
Endverbrauchsteile für hochleistungsfähige Schuhe
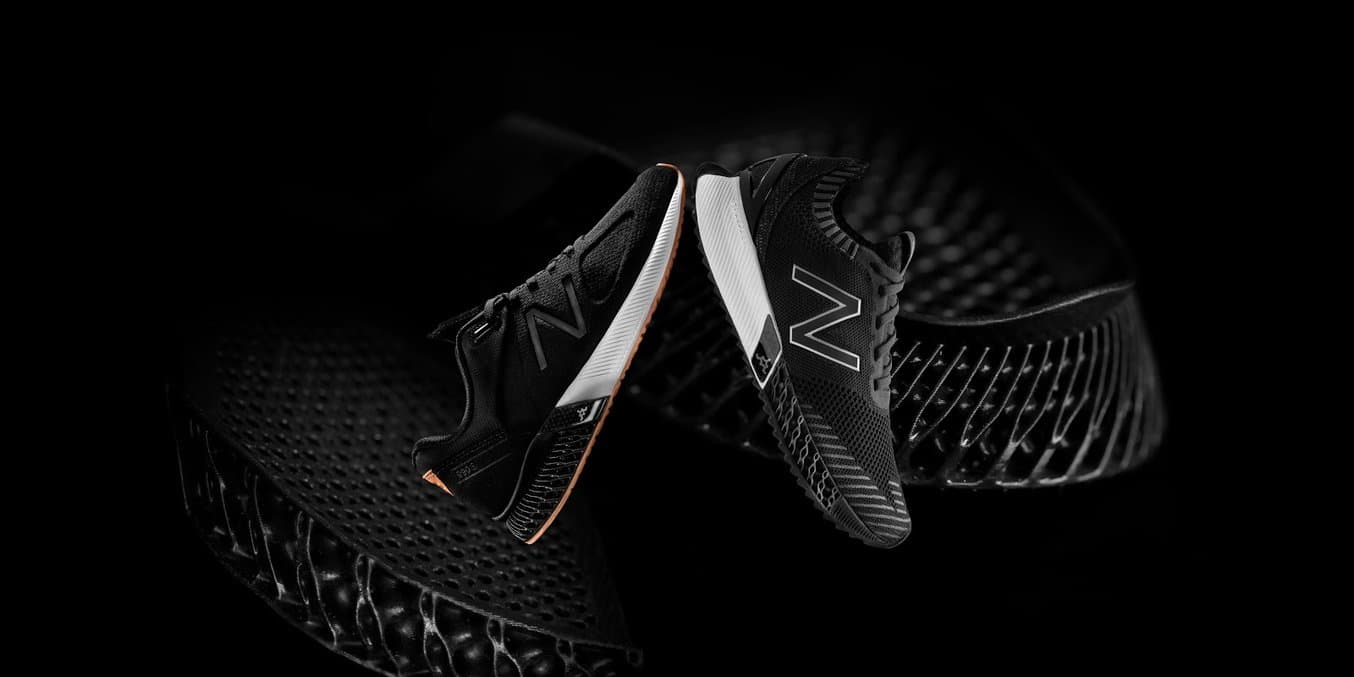
Der 990S TripleCell und der FuelCell Echo Triple.
Die Sportschuhbranche verlässt sich schon lange auf Technologie, um die Leistung ihrer Produkte zu verbessern. Dank des digitalen Arbeitsablaufs hat sie bei der Individualisierung mehr Möglichkeiten als je zuvor.
Große Marken wie New Balance, Adidas und Nike haben die Möglichkeiten der additiven Fertigung erkannt und setzen auf die Massenproduktion individueller Zwischensohlen aus 3D-Druckmaterialien. Wie auch in anderen Branchen wird der digitale Arbeitsablauf herkömmliche Fertigungsmethoden ergänzen – kritische, stark individualisierte Komponenten der einzelnen Produkte werden mit 3D-Druck gefertigt, während der Rest herkömmlich hergestellt wird.
Aufgrund der einzigartigen Materialeigenschaften, die in der Schuhbranche gefordert sind, arbeitete New Balance mit Formlabs zusammen an der Entwicklung eines individuellen Druckmaterials, das der täglichen Beanspruchung eines Sportschuhs standhält. Schuhmaterialien kommen in verschiedenen Umgebungen zum Einsatz und müssen zusätzlich jeden Tag tausenden unterschiedlichen Lastwechseln widerstehen. Rebound Resin wurde für federnde, widerstandsfähige Gitterstrukturen entwickelt und bietet eine deutlich höhere Energierückgabe, Reißfestigkeit und Dehnung als alle anderen Formlabs-Materialien. Rebound Resin ist fest genug, um in Dichtungen und Automobilinnenräumen eingesetzt zu werden. Gleichzeitig ist es leicht und flexibel genug für die Anwendung in Schuhsohlen.
„Was wir besonders aufregend finden, ist, dass das Erlebnis für Läufer ein ganz anderes ist.“
Katherine Petrecca, General Manager of Footwear beim Innovation Design Studio, New Balance
Neue Wege des modernen Storytelling
Der 3D-Druck hat bereits seinen Weg in die Produktion von Hollywood-Filmen gefunden und wird in großem Umfang für praktische visuelle Effekte und Kostüme eingesetzt.
Während das Erschaffen fantastischer Filmkreaturen bislang haargenaue Handarbeit erforderte, verlangt der Termindruck der modernen Filmbranche nach einer schnelleren Methode zur Erzeugung praktischer Effekte. Effektstudios wie Aaron Sims Creative nutzen nun eine gemischte Herangehensweise, bei der praktische Effekte durch den digitalen Arbeitsablauf unterstützt werden, um neue Chancen der Zusammenarbeit zu schaffen und die Durchlaufzeiten bei der Umsetzung von Ideen zu verkürzen.
„Der Demogorgon war einer unserer ersten Drucke mit dem 3D-Drucker von Formlabs und wir waren echt erstaunt. Bis dahin hatten wir das Drucken immer extern machen lassen. Das Ganze im eigenen Haus zu haben und mit eigenen Augen zu sehen, wie das von uns erstellte Design gedruckt wird, war ein tolles Gefühl. Es war fast wie früher, als wir noch mit Modelliermasse gearbeitet haben“, berichtet Aaron Sims.
Eine neue Art von Tanz und Musik
Das künstlerische Potenzial von 3D-Druck ist nicht bloß auf physische Kunstwerke beschränkt. 3D-Druck kann auch Kunstformen wie Tanz und Musik ganz neue Dimensionen verleihen. Dank der inhärenten Gestaltungsfreiheit der additiven Fertigung können selbst die komplexesten und einzigartigsten Instrumente aus dem Nichts erschaffen oder angepasst werden, und das zu einem Bruchteil des Preises traditionell hergestellter Instrumente.
Die Geige ist schon seit Jahrhunderten fast unverändert präsent und ihre Form ist daher jedem vertraut. Die Geigenmusik wurde bis zu einem so hohen Niveau entwickelt, dass das Instrument in unserer Kultur einen nahezu legendären Status innehat. Formlabs-Ingenieur Brian Chan stellte sich der Herausforderung, mithilfe eines 3D-Druckers und White Resin von Formlabs eine voll funktionsfähige akustische Geige zu drucken.
Kunstrestauration: Alte Kunst zu neuem Leben erwecken
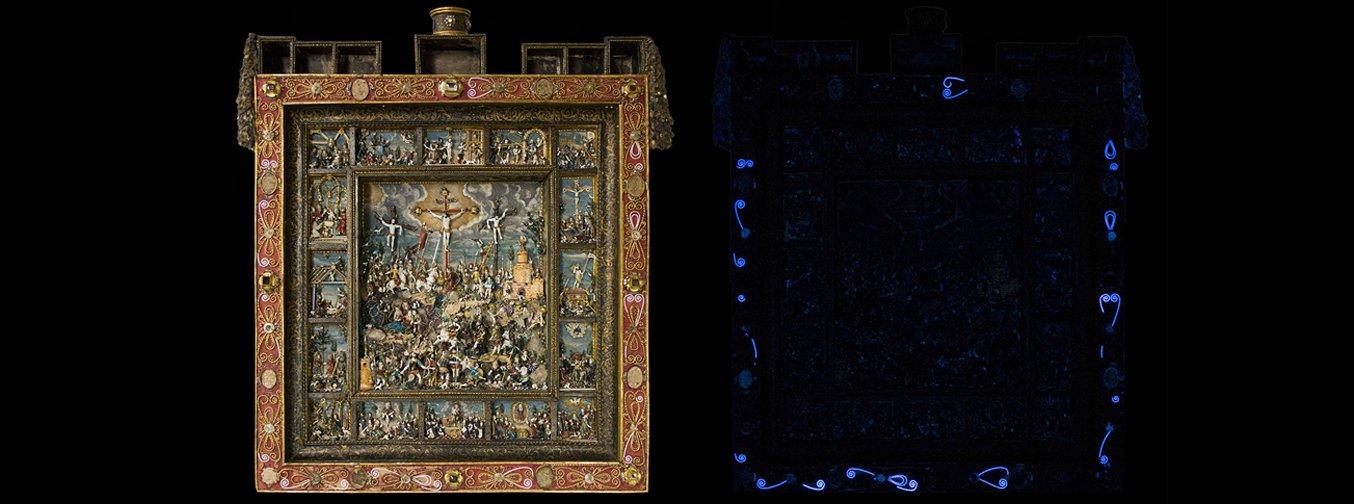
3D-Scans, CAD und 3D-Druck wurden eingesetzt, um die Arbeiten von einigen der berühmtesten Künstler aller Zeiten zu restaurieren. So konnte Werken von Meistern wie Michelangelo und da Vinci wieder zu ihrer einstigen Schönheit verholfen werden.
Solche Projekte zur Restauration von Kunstwerken könne durch die Kombination von 3D-Druck und 3D-Scan stark aufgewertet werden. Die beiden Technologien machen es möglich, physische Objekte in dreidimensionale digitale Modelle umzuwandeln, an denen Änderungen oder Nachbildungen durchgeführt werden und die schließlich neu 3D-gedruckt werden können.
Mattia Mercante nutzt 3D-Nachbildung, um verloren gegangene Teile von Skulpturen und Kunstwerken am weltberühmten Opificio-Institut in Florenz zu ersetzen. Dadurch können die Werke wieder in ihrer ursprünglichen Form erlebt werden.
Bei der unten abgebildeten Reliquie aus dem 17. Jahrhundert hat Mercante an einer anderen Stelle des Teils feine Details mit einem HP-3D-Streifenlichtscanner gescannt, um dann die fehlenden Teile mithilfe eines Formlabs-3D-Druckers nachzubilden. Die Drucke wurden lackiert, damit sie wie die originalen Ornamente aussehen. Das Beste daran: Es war nur wenig CAD-Modellierung für diese Restauration notwendig und sie war im Vergleich zur Handarbeit schnell und kostengünstig.
Flugzeuge, Schädel und Koffer: Die Aufklärung des perfekten Verbrechens
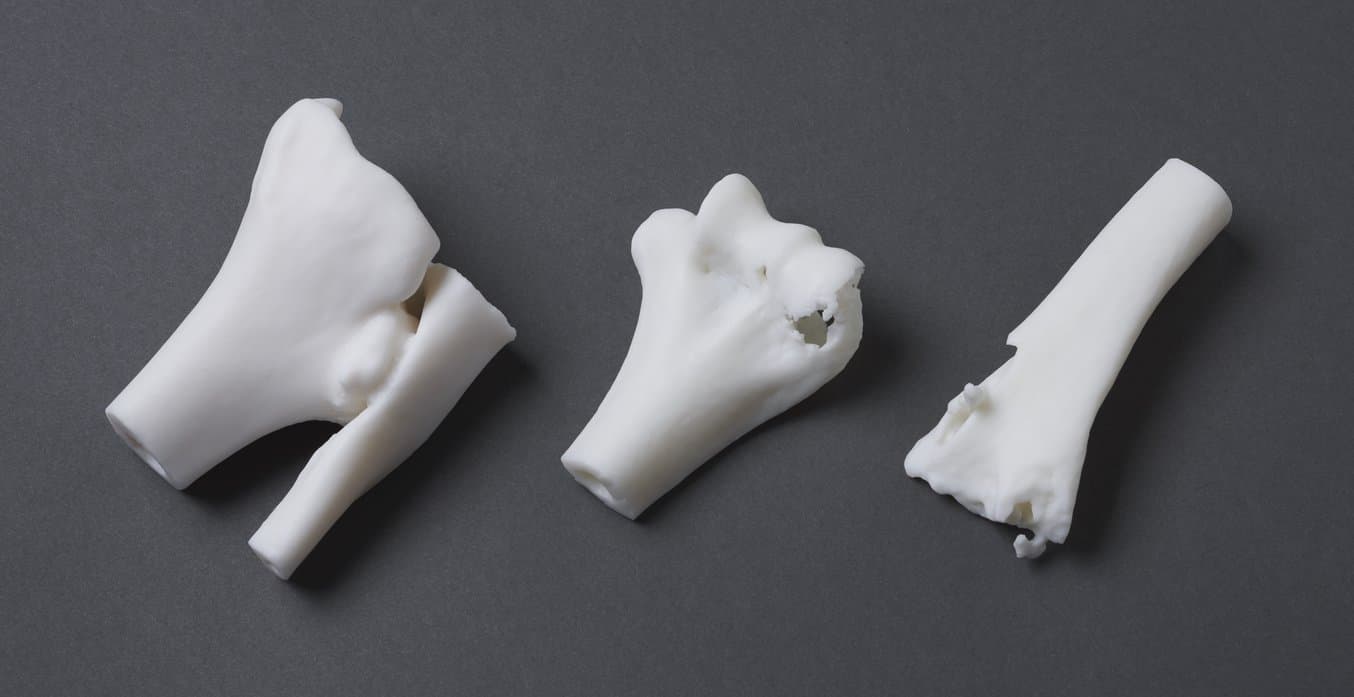
Der 3D-Druck hat bei der Rekonstruktion genauso viel potenziellen Nutzen wie bei der Produktion. In der Forensik wird die Arbeit häufig durch Beweismangel erschwert. Digitale Technologien können einen großen Nutzen für die Strafverfolgung mit sich bringen und Forensikteams dabei helfen, genaue Modelle von Verdächtigen oder Opfern zu rekonstruieren.
Beim digitalen Arbeitsablauf wird in diesem Fall aus CT-Scans ein 3D-Druck erstellt, um die Identifizierung zu unterstützen. Wenn Ermittler beispielsweise nur einen Teil eines Schädels als Beweisstück finden, lässt sich mit einem Drucker das gesamte Beweisstück modellieren und replizieren.
Rekonstruktionen des Aussehens von Verbrechensopfern haben bereits eine wichtige Rolle bei Prozessen gespielt, was wiederum unterstreicht, dass der Nutzen von 3D-Druck über Design und Produktionseffizienz hinausgeht.
Genau wie der 3D-Druck in der präoperativen Planung zum Einsatz kommen kann, liefern auch CT-Scans von Verbrechensopfern den nötigen Einblick in die Knochenstruktur. Aus Daten digitaler CT-Scans und Röntgenbildern der Überreste können mittels 3D-Druck Nachbildungen verschiedener Körperteile erstellt werden. Daraus ermitteln Fachleute der Pathologie die genauen Tatumstände, angefangen von der Zahl der Täter bis hin zur Art der verwendeten Waffe.
Leben verbessern durch bessere Prothesen
Der Einfluss von 3D-Druck ist nicht nur auf die Verbesserung von Arbeitsprozessen oder auf Rapid Prototyping beschränkt. Er kann auch Leben direkt verändern. Weltweit benötigen über 30 Millionen Menschen künstliche Gliedmaßen und Stützschienen. Es besteht die Hoffnung, dass der 3D-Druck neue Lösungen für Probleme bietet, bei denen Kosten und Spezifikationen in der Vergangenheit immer wieder Hürden darstellten.
Der 3D-Druck kann eine erschwingliche Alternative darstellen, die wie viele ähnliche Fortschritte bei der Medizin eine Therapie ermöglicht, die viel besser auf die individuellen Patientenbedürfnisse zugeschnitten ist. Die Erschwinglichkeit und Individualisierbarkeit des 3D-Drucks kann die Lebensqualität von Personen mit Verletzungen oder Behinderungen entscheidend verbessern, wie wir in dieser Geschichte über einen Vater und seinen Sohn erfahren haben.
Der Fall von Matejs und Matejas Sohn Nik, der an einer Zerebralparese litt, war der erste, in dem uns diese Art der Innovation begegnet ist. Matej hatte sich ein klares Ziel gesetzt: dafür zu sorgen, das Nik laufen konnte. Nach Monaten der Forschung und Entwicklung stellte er eine maßgefertigte 3D-gedruckte Orthese her, die Nik genau doch Halt und Korrektur bot, wo er dies brauchte. Mithilfe dieser Konstruktion machte er schließlich seine ersten eigenständigen Schritte. Sehen Sie sich oben das Video in voller Länge an und lesen Sie die ganze Geschichte.
Abgesehen von Prothesen, die verlorene Körperfunktionen wieder möglich machen, lassen sich mit 3D-Druck auch Geräte herstellen, die auf gewisse Weise sogar noch besser sind als die Gliedmaßen, als deren Ersatz sie dienen. Dank 3D-Drucktechnologien sind bionetische Körperteile nach dem Prinzip von RoboCop keine Zukunftsmusik mehr, sondern bereits ein Teil modernster, innovativer Prothesenproduktion. Einige Unternehmen wie z. B. Psyonic liefern solche Prothesen der neuen Art bereits heute.
Neue Konzepte in Wohnungsbau und Bauwesen
Viele stellen sich unter 3D-Druck vielleicht die Herstellung kleiner Objekte vor, die man in der Hand halten kann. In den letzten Jahren haben Unternehmen jedoch auch additive Verfahren auf Fertigungsniveau ausgetestet, mit denen sich weitaus größere, funktionsfähige Komponenten produzieren lassen. Es wurden in den vergangenen Jahren zahlreiche Initiativen auf den Weg gebracht, in deren Rahmen Häuser und größere Strukturen vollständig mit 3D-Druck gefertigt werden sollen, was neue Möglichkeiten für nachhaltige Wohnungen und Baustrukturen eröffnet.
Die 3D-Drucktechnologie bietet der Architektur Formenfreiheit, und das sogar bei ehemals weniger formbaren Baustoffen wie Beton. Vereinfacht gesagt ermöglicht sie vollständig nachhaltige und energieeffiziente Wohngebäude, die auch modernen Komfortansprüchen gerecht werden. Der Wohnungsbau könnte auf diese Weise vollkommen abfallfrei werden, sowie auch kostengünstiger als traditionelle Methoden und weniger schädlich für die Umwelt.
Selbst wenn ein Einzug in ein komplett 3D-gedrucktes Haus in naher Zukunft noch nicht realistisch ist, gibt es auf 3D-Druck gestützte Bauprojekte schon heute in der Praxis. Die Brücke von MX3D in Amsterdam ist bereits für den Fußgängerverkehr eröffnet worden. Laut Informationen von dezzen.com besteht die Konstruktion aus „4500 Kilogramm Edelstahl, den Roboter über einen Zeitraum von sechs Monaten in einer Fabrik 3D-druckten, bevor er dieses Jahr mithilfe von Kränen über dem Kanal in Position gebracht wurde.“
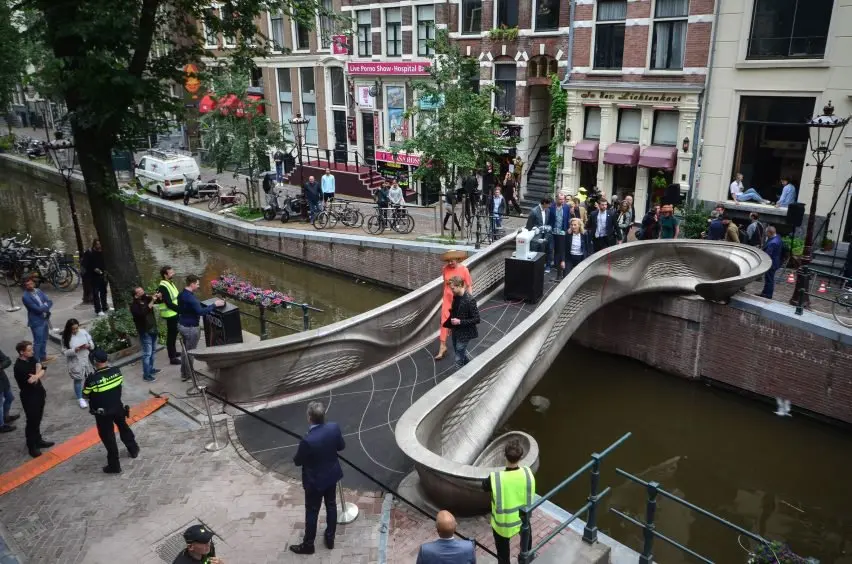
Quelle: www.dezeen.com
Neuer Ansporn für den Wettlauf ins All
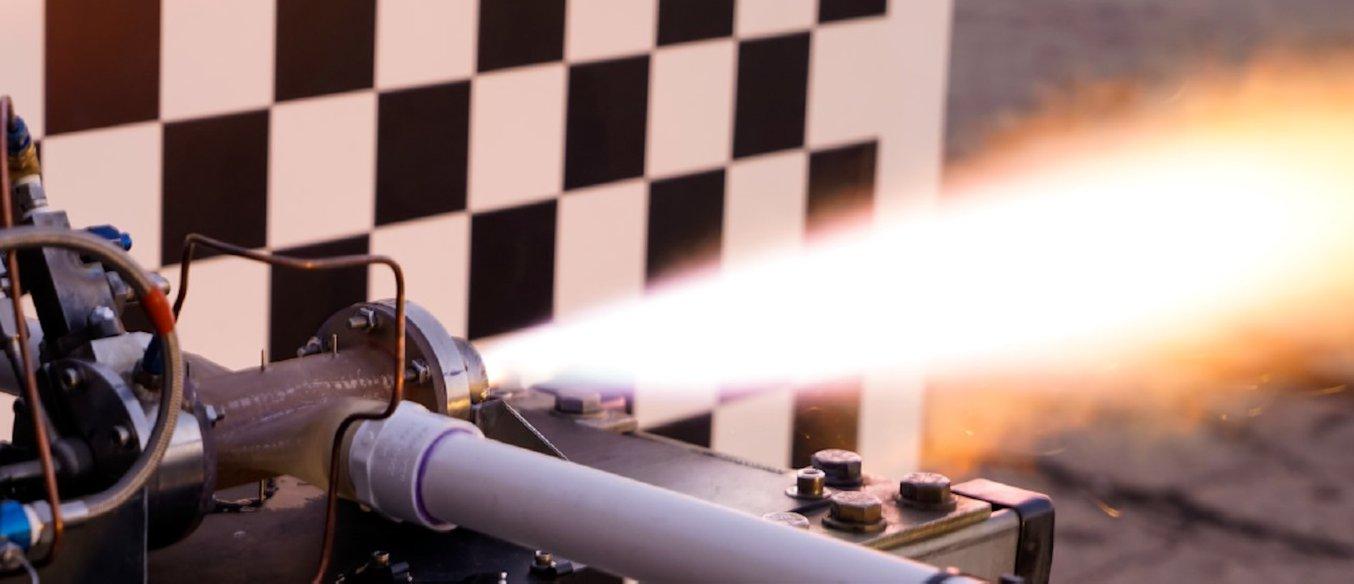
Mit einer der höchsten Einstiegshürden unter allen Branchen der Welt ist die Raumfahrt reif für Innovationen durch 3D-Druck. Indem sich Prototypen für teure, raumfahrtspezifische Werkzeuge und Geräte günstiger herstellen lassen, werden Kosten gesenkt, sodass auch kleinere Unternehmen an der Innovation der Raumfahrt teilnehmen können.
Das Raumfahrt-Startup Relativity hat die Herstellung von Raketentriebwerken aus Aluminium durch additive Fertigung erprobt. Im Erfolgsfall würde diese Anwendung die Kosten und praktischen Schwierigkeiten der Raumfahrt senken und die Branche für neue Geschäfte und ein großes Wachstumspotenzial öffnen.
Ein weiterer Innovator im Bereich 3D-Druck in der Raumfahrt ist Masten Space Systems, ein 2004 gegründetes Unternehmen, das sich auf Raketenbau für vertikale Starts und Landungen spezialisiert hat. Das Unternehmen startet 2022 eine Mondmission als Teil des NASA-Projekts Commercial Lunar Payload Services (CLPS). Mithilfe von 3D-Druckern von Formlabs hat Masten Raketentriebwerke aus Kunststoff für F&E-Tests hergestellt.
Das Unternehmen hat sowohl mit Kunststoff- als auch Metall-3D-Druck Erfahrung und hat für sein Projekt im Rahmen von NASA's Initiative Tipping Point sogar an der Entwicklung neuer, individualisierter Metalle teilgehabt. „Wir arbeiten wirklich gern mit 3D-gedruckten Raketentriebwerken, denn sie eröffnen eine Menge Möglichkeiten, die es mit traditionellen Fertigungsverfahren nicht gibt. In unserem Bestreben, Kosten zu senken und unsere Effizienz zu steigern, haben wir untersucht, wie uns Stereolithografie-Drucker dabei unterstützen können, vor allem nach der Einführung von Ceramic Resin und High Temp Resin. Diese haben ziemlich reizvolle technische Eigenschaften im Hinblick darauf, wie wir sie konkret in einer Rakete einsetzen können“, erklärt Matthew Kuhns, leitender Ingenieur bei Masten.
Formlabs' High Temp Resin und Rigid 10K Resin sind Beispiele für Materialien, deren technische Eigenschaften sich optimal für Anwendungen in der Luft- und Raumfahrt eignen. High Temp Resin wurde für funktionales Prototyping und Anwendungen unter Hitzeeinwirkung entwickeln, während Rigid 10K Resin das steifste Material unserer Materialfamilie der technischen Kunstharze ist und sich daher für Prototypen in Industriequalität eignet.
Generatives Design wird möglich gemacht
Generatives Design, oder generative Gestaltung, ist für praktisch alle Fertigungsbranchen der nächste große Schritt im CAD-Design. Dabei wird künstliche Intelligenz (KI) eingesetzt, um neue leistungsstarke Designiterationen zu entwickeln und so komplexe Anforderungen zu lösen, das Gewicht von Bauteilen sowie die Fertigungskosten zu senken, skalierbare Maßanfertigung zu liefern und die Leistung zu verbessern.
Der 3D-Druck zeichnet sich durch seine Fähigkeit aus, komplexe, organische Objekte zu fertigen. Dank der großen Bandbreite von Materialeigenschaften für verschiedenste Anwendungsbereiche können Sie die Entwicklung von noch nie dagewesenen Designstrukturen erwarten. Durch die Nutzung von KI, um neue und komplexe Designiterationen schnell, effizient und in großem Maßstab zu entdecken und zu testen, lässt sich die für Forschung und Entwicklung neuer Produkte benötigte Zeit drastisch verkürzen. Mit einem betriebsinternen 3D-Drucker werden aus komplexen Modelle dann handfeste, greifbare Objekten.
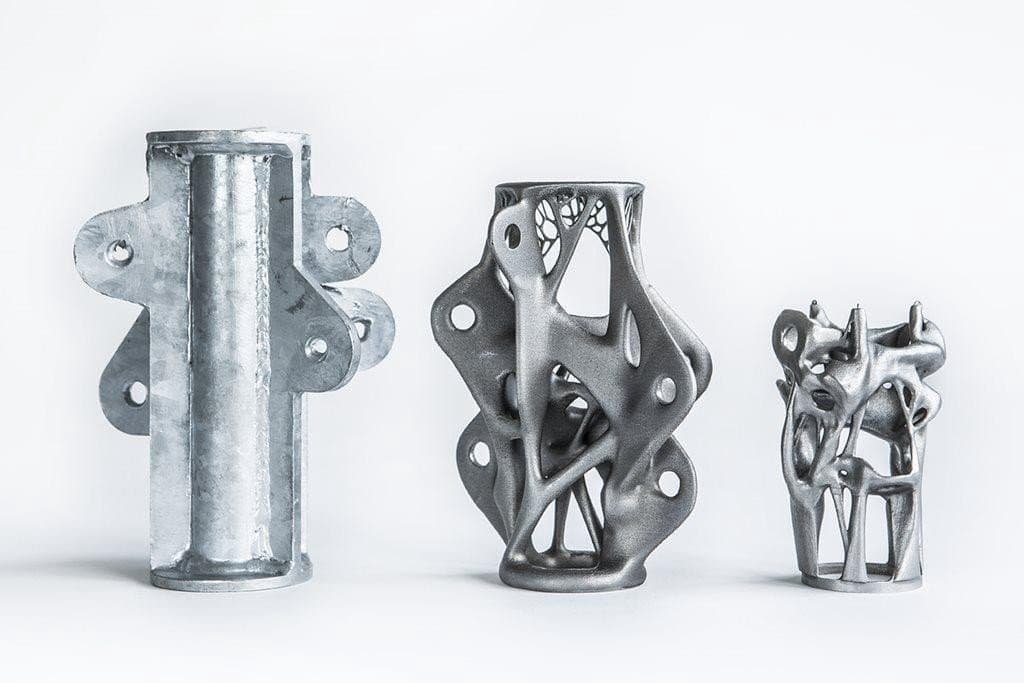
Halterungen und Streben, die genau definierten Kräften ausgesetzt sind, sind Teile, bei denen das generative Design häufig eingesetzt wird.
Möchten Sie mehr über generatives Design erfahren? Sehen Sie sich unser kostenloses Webinar an und erhalten Sie unter anderem Antworten auf folgende Fragen: Warum erhält man so viele Bilder von Halterungen, wenn man „generatives Design“ bei Google sucht? Wie richtet man ein Designproblem in Autodesk Fusion 360 ein? Wie konnte ein Unternehmen eine Rollstuhlklammer um 40 % leichter machen, indem es zum ersten Mal ein generatives Designverfahren nutzte?
Die Arbeitskräfte von morgen ausbilden
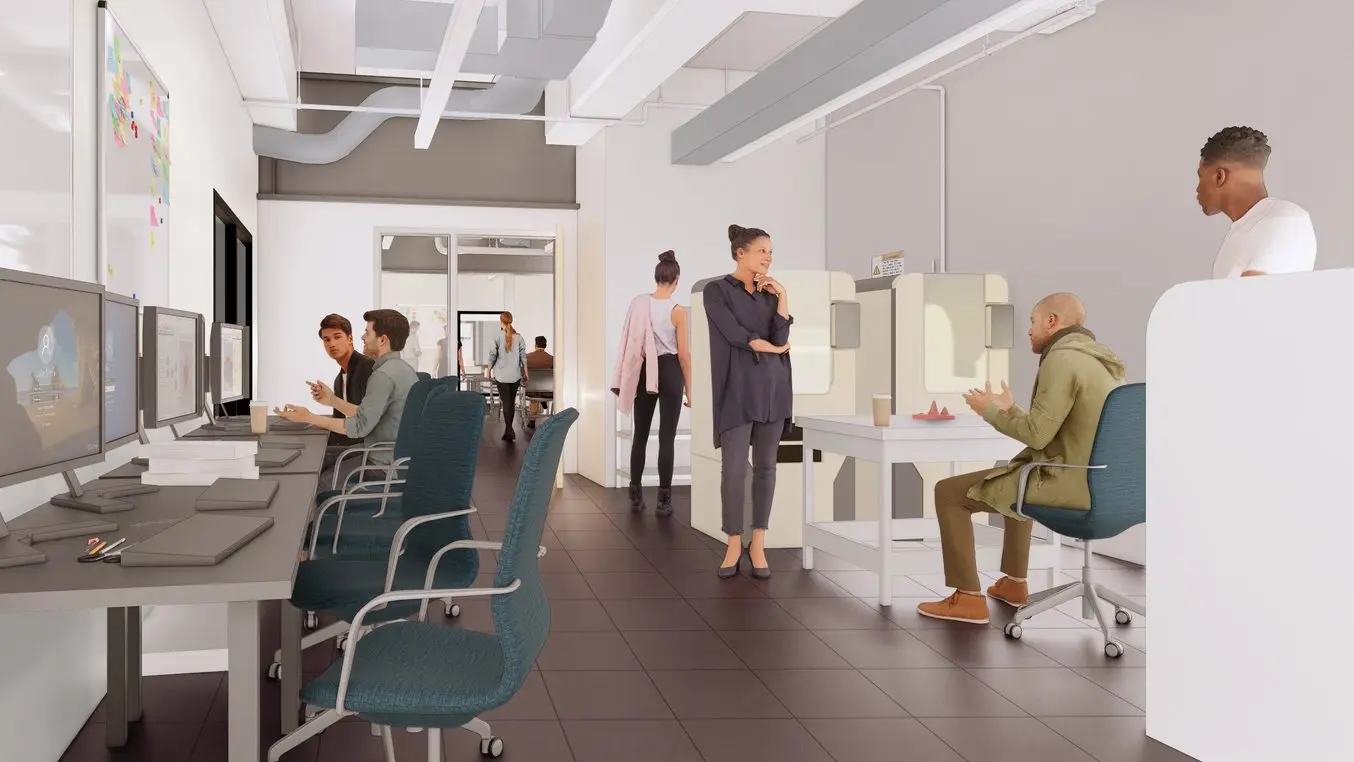
Mit seinem neuen Innovation Hub erhält Origin Labs einen Raum, der ganz für die Nutzung des 3D-Druck durch Studierende und die erweiterte Öffentlichkeit vorbehalten ist.
Die meisten höheren Bildungseinrichtungen sind darauf ausgerichtet, Studierende auf ihre Zukunft in der Arbeitswelt vorzubereiten. Die Pennsylvania State University legt den Fokus daneben auch auf jetzige Arbeitnehmer und investierte kürzlich Millionen von Dollars in den Bau des Eric J. Barron Innovation Hub, das sowohl der Öffentlichkeit als auch der Universitätsgemeinschaft zur Verfügung steht.
Historisch war der Gebirgszug der Appalachen im westlichen und zentralen Pennsylvania der Mittelpunkt der Kohleindustrie der Vereinigten Staaten. Dies verhalf der Region in der ersten Hälfte des zwanzigsten Jahrhunderts zu einer stabilen und blühenden Wirtschaft. Durch die Abwendung der Wirtschaft vom Kohlebergbau sowohl auf globaler als auch nationaler Ebene hatte die Appalachenregion mit steigender Arbeitslosigkeit und einem der niedrigsten Durchschnittseinkommen des Landes zu kämpfen, wie die Appalachian Regional Commission berichtet.
In den vergangenen zwei Jahrzehnten haben sowohl kommunale als auch staatliche Autoritäten versucht, diesen Trend durch Investitionen in die Fertigung, Bildung und Technologie umzukehren. Die Appalachian Regional Commission stellt Stipendien von 1 Mio. Dollar zur Verfügung, um „Bildungsmöglichkeiten und -einrichtungen zu unterstützen, vor allem bei der Verknüpfung von beruflichen und fertigkeitsorientierten Schulungen mit örtlichen und regionalen Wirtschaftsinteressen und Chancen.“
Da sich die additive Fertigung in einer großen Bandbreite von Branchen rasant ausbreitet (wie auch dieser Beitrag deutlich macht), sind Arbeitskräfte, die in digitalen Prozessen geschult und Profis im CAD sind, bei Personalleitern hoch begehrt. Deshalb bemühen sich Universitäten, diesem Marktanspruch gerecht zu werden, indem sie große, gut finanzierte Innovationszentren einrichten.
Ein Upgrade für traditionelle Unterrichtspläne
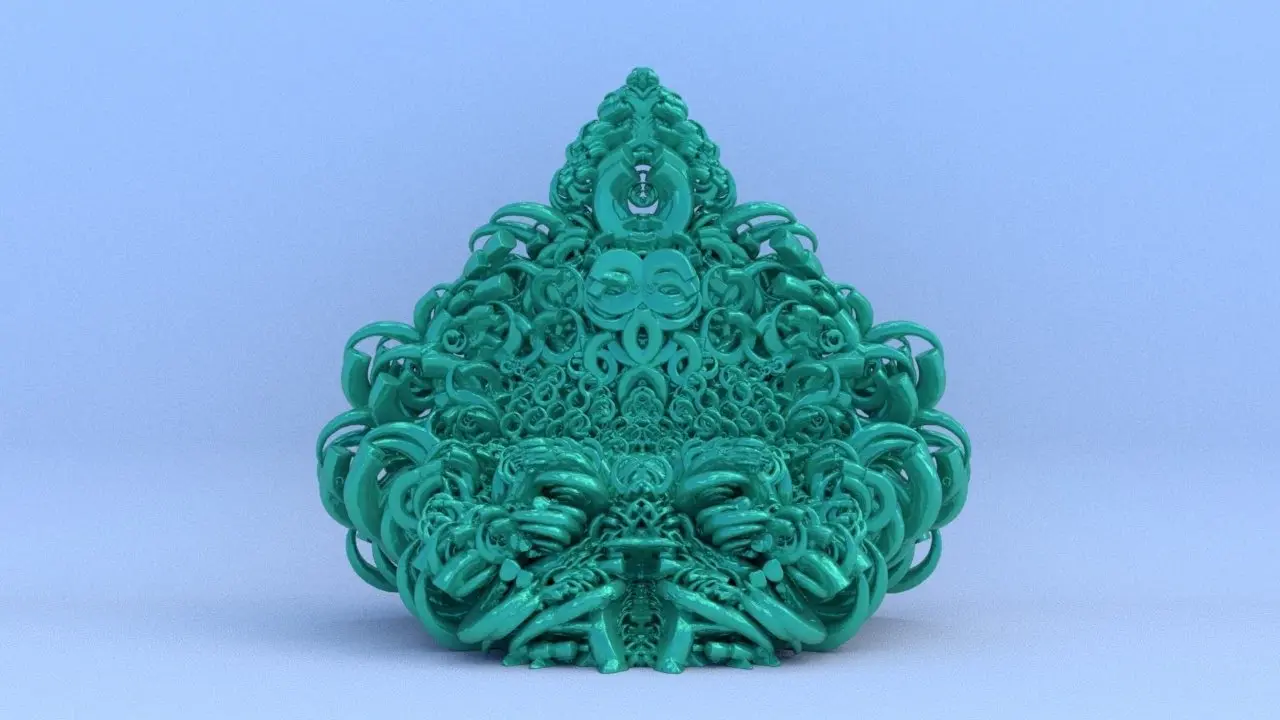
Abgesehen von der Lehre von CAD und 3D-Druck zeigen sich die Vorteile des Einsatzes von 3D-Druckern an Universitäten noch in einer ganzen Reihe von Bildungsbereichen.
An der UMass Lowell wurden die Bildhauerei- und 3D-Designkurse an das 21. Jahrhundert angepasst. Hier tritt Yuko Oda auf den Plan, die seit 2017 an der Universität arbeitet und damit angefangen hat, eine Reihe von 3D-Druckern zu bestellen, darunter ein SLA-Gerät von Formlabs.
Yuko kann ihre Leidenschaft für Kunst und Technologie im Unterrichtsraum ausleben, da sie aktuell Bildhauerei, 3D-Modellierung und Animation sowie interaktive Medien unterrichtet. Die meisten Studierenden wissen, dass ein Verständnis der 3D-Animation und 3D-Modellierung für ihre zukünftigen Karrieren in verschiedenen Bereichen essenziell ist, so auch in der Modellierung für den Film. Für Studiokünstler ist 3D-Modellierung zu einer grundlegenden Fähigkeit geworden.
„Studenten entwerfen ein 3D-Modell, importieren es in Zbrush und drucken es dann mit verschiedenen Kunstharzen, darunter auch mit Clear Resin. Die Fähigkeit der Formlabs-Geräte, Details darzustellen, die in Zbrush bearbeitet wurden, sind beim Vergleich mit anderen Druckern im Labor unerreicht.“
Yuko Oda
Eine der vielversprechendsten neuen Entwicklungen in der Bildhauerei ist die Integration von 3D-Druck und Virtual Reality (VR). Das ist besonders der Fall bei Studierende, die von 3D-Design eingeschüchtert sind. VR reduziert schnell die Einstiegshürden beim 3D-Design und ermöglicht es Künstler*innen und Studierenden, in Programmen wie Oculus Medium mit ihren Händen schöpferisch tätig zu werden. In der achten Klasse führte Yuko vor, wie man in 30 Minuten in VR ein 3D-Objekt erstellt und das Kunstwerk dann auf einem 3D-Drucker druckt. Selbst wenn man Erfahrung in der Bildhauerei hat, reduziert VR die Zeit von der Idee zum physischen Objekt, wodurch potenziell neue Bereiche für die experimentelle Kunst eröffnet werden können.
Die Rettung eines gefährdeten Vogels
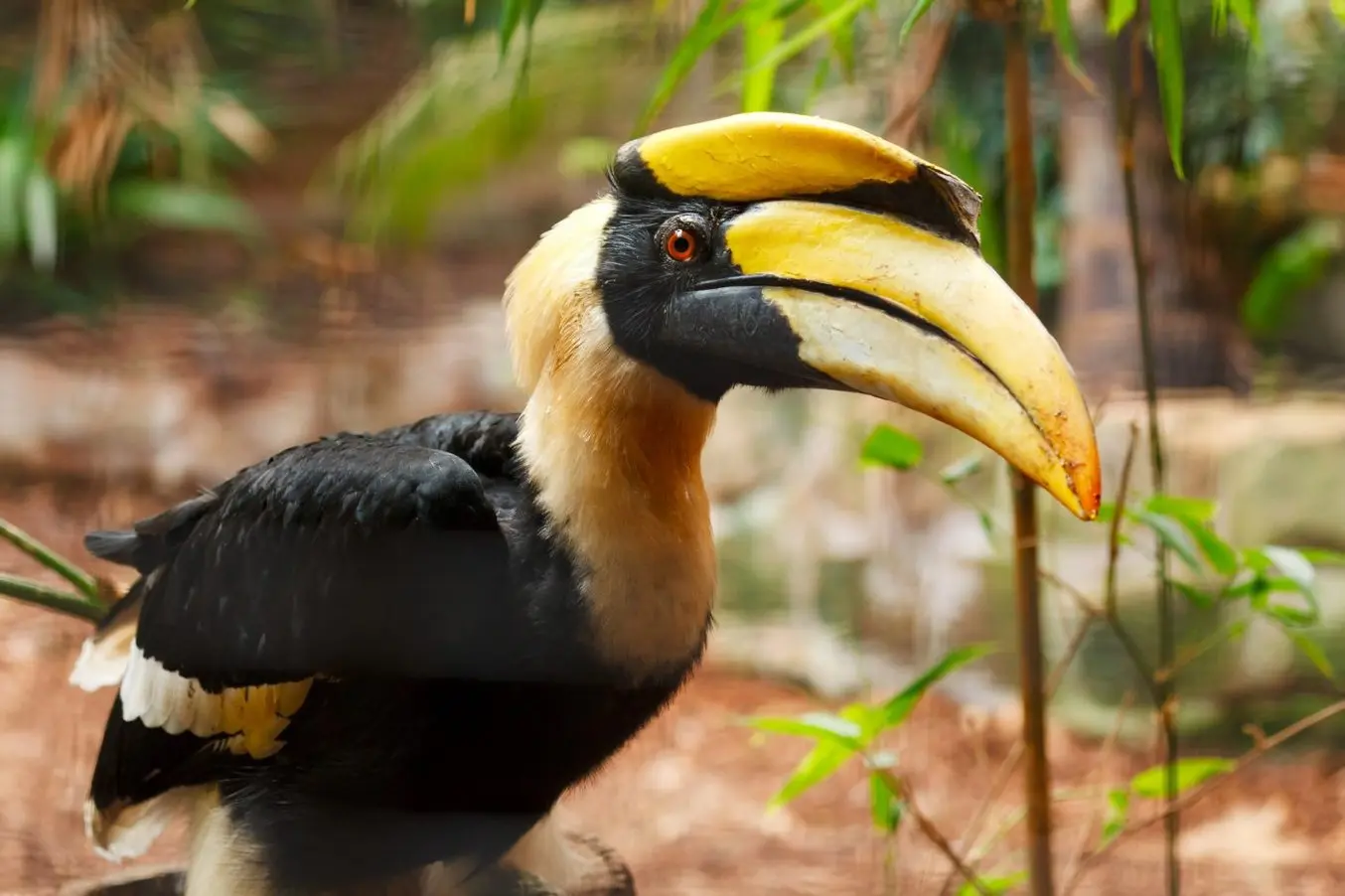
Während einer Routineuntersuchung eines 25 Jahre alten Doppelhornvogels im Tierpark ZooTampa entdeckten Pfleger eine Läsion am Hornaufsatz des Tieres - dem charakteristischen gelben, helmartigen Auswuchs auf seinem Kopf. Eine genauere Analyse ergab, dass der Vogel namens Crescent lebensbedrohlich an Krebs erkrankt war.
Der vom Krebs befallene Bereich des Hornaufsatzes nahe des Schädels umschloss zum Teil auch die Stirnhöhle des Vogels, sodass er nicht entfernt werden konnte. Das Team untersuchte, ob es möglich war, das Horn durch eine 3D-gedruckte Nachbildung zu ersetzen, die speziell für diesen Vogel entworfen wurde. Patientenspezifische Prothesen und Medizinprodukte wurden bei Menschen bereits vielfach eingesetzt, doch eine derartige Behandlung eines Doppelhornvogels war etwas noch nie Dagewesenes. War es überhaupt machbar, und wenn ja, welche Materialien konnten sicher an dem Vogel verwendet werden?
Wie der Tierpark ZooTampa berichtet, wurde aus BioMed White Resin erfolgreich ein 3D-gedruckter „Ersatzschnabel“ gefertigt. Dies ist ein lichtundurchlässiges, weißes Material für biokompatible Anwendungen, bei denen es über längere Zeit zum Kontakt mit Haut oder über kürzere Zeit mit Schleimhäuten kommt. Dieses Material in medizinischer Qualität ist auch für den kurzzeitigen Gewebe-, Knochen- oder Dentinkontakt validiert, was es zu einer Besonderheit unser den 3D-Druckmaterialien von Formlabs macht.
Störungen in der Lieferkette überwinden
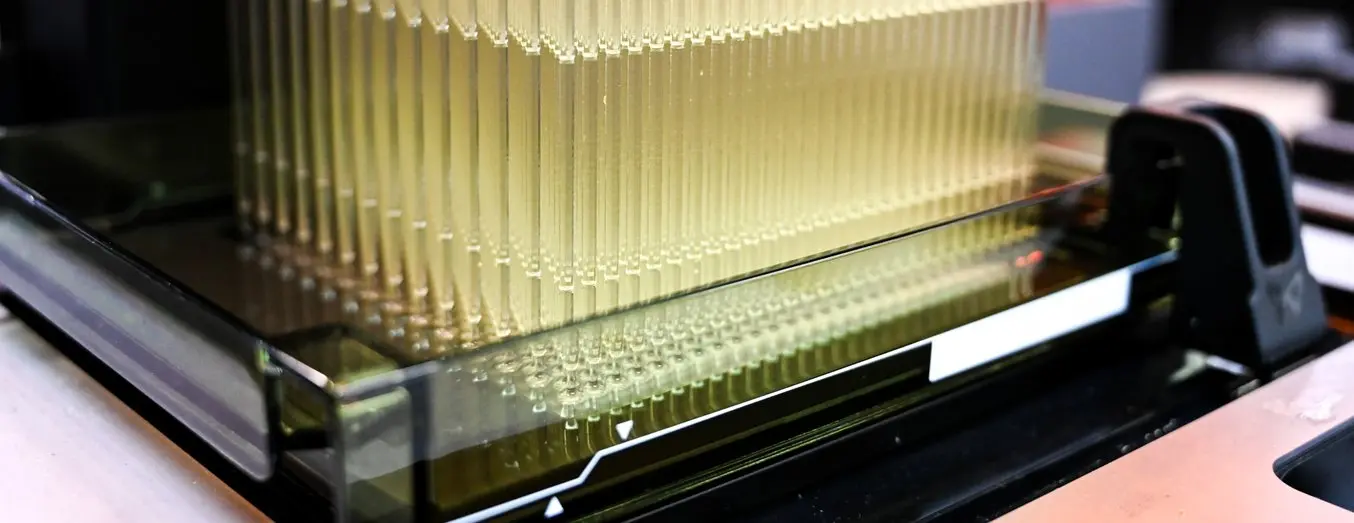
Während der COVID-19-Pandemie und der daraus resultierenden Lieferkettenkrisen im Jahr 2021/22 gingen viele Unternehmen zum 3D-Druck über, damit Ihre Maschinen am Laufen bleiben konnten und der Fertigungsstrom von Produkten nicht versiegen musste. Durch die Verbreitung der Nutzung betriebsinternen 3D-Drucks zur Herstellung von Endverbrauchsteilen, wie etwa Ersatzteilen für Maschinen, spielte die additive Fertigung eine Schlüsselrolle bei der Lösung von Lieferkettenproblemen.
Formlabs hat den 3D-Druck-Anwendungsbericht 2022 erstellt, um ein besseres Verständnis darüber zu erlangen, was sich in den letzten Jahren an der Einstellung zur Nutzung von 3D-Druck geändert haben kann. Der Bericht zeigt einen Wandel in der Auffassung des 3D-Drucks auf, von einem Hilfsmittel für F&E und Prototypenentwicklung hin zu einer unschätzbaren Fertigungsmethode, die unerlässlich ist, um wachsenden Verbraucheransprüchen gerecht zu werden und Lieferkettenengpässe zu überwinden. Sowohl hinsichtlich der Milderung von Lieferkettenproblemen als auch bei der Herstellung limitierter Auflagen oder personalisierter Produkte mussten Unternehmen ihre Produktionsmethoden überdenken, um die Kundennachfrage weiterhin zu befriedigen.
3D-gedruckte 3D-Drucker
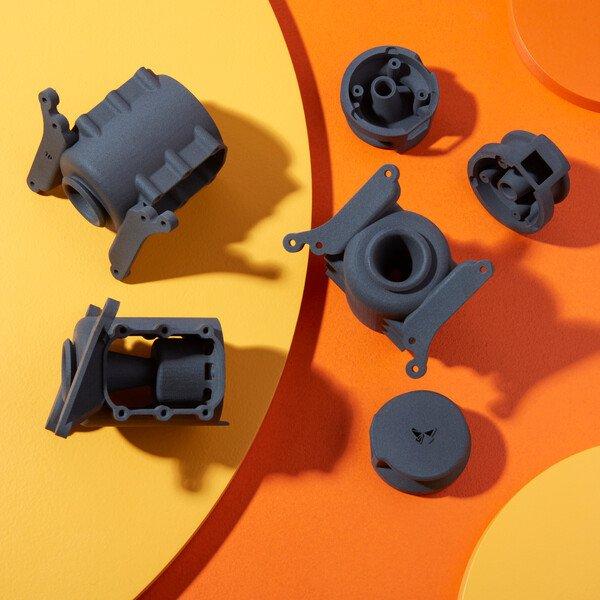
Endverbrauchsteile, gedruckt auf dem Fuse 1.
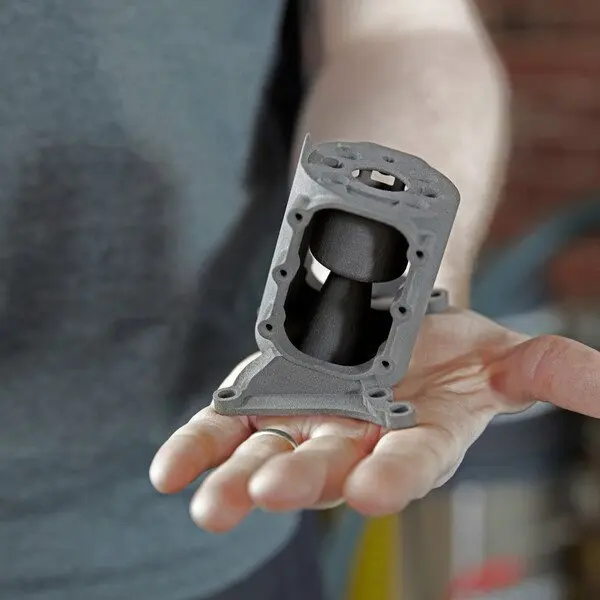
Eine IR-Sensorluftspülung, gedruckt auf dem Fuse 1 mit Nylon 12 Powder.
Die Konstruktion von 3D-Druckern stellt maschinenbautechnisch immer einer Herausforderung dar. Industrielles Leistungsvermögen in einen kostengünstigen und schnittigen 3D-Drucker für den Desktop zu packen, erfordert Jahre der Ingenieur- und Designarbeit. Dies war vor allem bei Formlabs' lang erwartetem 3D-Drucker für selektives Lasersintern (SLS) der Fall, dem Fuse 1.
Eines der Werkzeuge des Ingenieurteams von Formlabs zur Herstellung der entsprechenden Prototypen war der Fuse 1 selbst. Der Einsatz von 3D-Druck im Produktionsprozess ging jedoch weit über die Prototypenentwicklung hinaus. Jeder einzelne Fuse 1, der unsere Produktion verlässt, enthält eine Vielzahl an Teilen, die direkt mit Nylon 12 Powder auf einem Fuse 1 gedruckt werden.
Laut Seth Berg, dem technischen Programmleiter des Fuse 1, gewährte die Verwendung des SLS-Druckers Fuse 1 für Prototypen und Endverbrauchsteile drei wesentliche Vorteile:
- Genügend Gestaltungsfreiheit für komplexe Teile, ganz ohne interne Stützstrukturen.
- Weniger Abhängigkeit von Lieferketten dank betriebsinterner Prototypenentwicklung und Fertigung der Endverbrauchsteile.
- Kein Outsourcing und daher eine erschwingliche Lösung zur Kleinserienfertigung mit einem bewährten und vielseitigen Nylon-12-Material.
Um zu erfahren, wie das Team diese Lösung entwickelte und welche Teile des 3D-Druckers 3D-gedruckt wurden, sehen Sie sich das untenstehende Video an.
Abstrichtupfer zur Notfallversorgung in der COVID-19-Pandemie
Im Mai 2020 veröffentlichte Forbes einen Artikel zum Thema, wie 3D-gedruckte Abstrichtupfer das Knappheitsproblem in Amerika lösen würden. Darin wurde beschrieben, dass die 3D-Druckbranche sich zusammengeschlossen hatte, um sich des Mangels an COVID-19-Abstrichtupfern anzunehmen, indem Formlabs, HP, Origin, Carbon, Desktop Metal und weitere gemeinsam die Abstrichtupferproduktion ankurbelten.
Die Schwere der COVID-19-Pandemie machte eine globale und abgestimmte Reaktion notwendig. In Zusammenarbeit mit der University of South Florida und Northwell entwickelte Formlabs eine Lösung, die seitdem weltweit eingesetzt wurde. Dank der freien Verfügbarkeit, der erschwinglichen Geräte und validierten Prozesse ermöglichte das Abstrichtupferdesign die Produktion von über 40 Millionen COVID-Tests in 25 Ländern. Im vergangenen Jahr sind Formlabs-3D-Drucker weiterhin von Behörden und Gesundheitsversorgern genutzt worden, um die Test- und Behandlungsmöglichkeiten zu verbessern. Diese globale Lösung ist nur ein Beispiel dafür, wie die Agilität des 3D-Drucks zum Wohl der Gesellschaft eingesetzt werden kann.
Ähnliches war auch in Singapur zu beobachten, wo Eye-2-Eye Communications die Abstrichtupferproduktion auf über 30 000 Stück pro Tag steigerte, um zur Sicherheit der Stadt beizutragen.
„Es war nicht nur eine herausragende Möglichkeit, die Vorteile des 3D-Drucks zum schnellen Designen und Entwickeln zu demonstrieren, sondern auch die Effizienz von Formlabs zu zeigen, Produkte in einer sehr kurzen Zeit in Serie zu fertigen. Da wir steigende Fallzahlen auf der ganzen Welt verzeichnen, ist es beruhigend zu wissen, dass wir unsere Produktion bei Bedarf relativ einfach hochfahren können“, so Miles Podmore, Chief Executive Officer von Eye-2-Eye Communications.
Agile Fertigung: Aftermarket- und maßgefertigte Teile
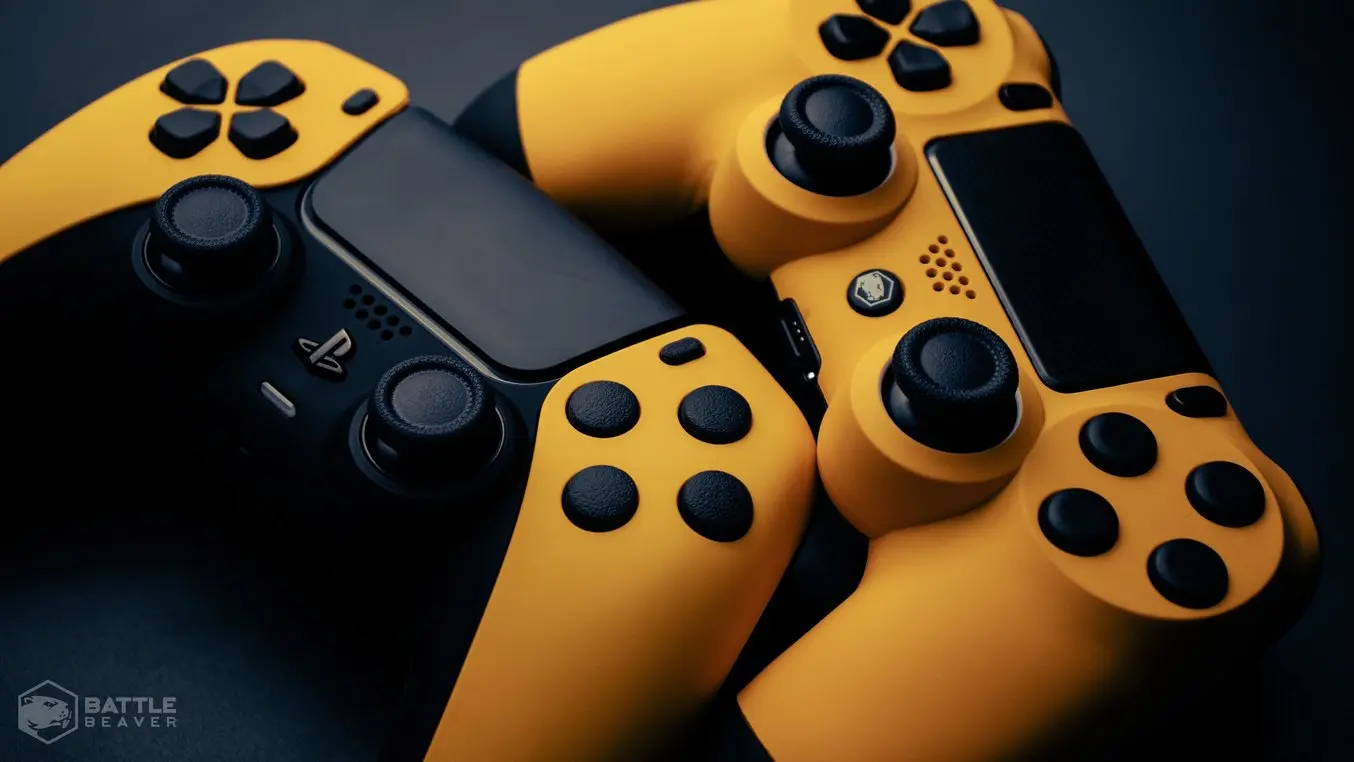
Ein Videospielcontroller inklusive Tasten gedruckt auf dem Fuse 1 (links) und ein anderer hergestellt im Spritzgussverfahren (rechts).
Die Produktion für den Aftermarket birgt das Problem, dass normalerweise geringe Stückzahlen hergestellt werden. Zudem müssen Unternehmen sicherstellen, dass ihre Teile immer den Neuerungen und Weiterentwicklungen der ursprünglichen Hersteller folgen. Mit der Verbreitung des betriebsinternen 3D-Drucks hat die Fertigung individualisierter oder maßgefertigter Teile jedoch in mehreren Branchen Fuß gefasst.
Die Firma Battle Beaver Customs spezialisiert sich auf erstklassige Spielerlebnisse durch maßgefertigte Videospielcontroller. Dank ihrer Modifikationen sind die Spielcontroller reaktionsschneller und wettbewerbsfähiger. Sie erlauben es, das Spielpotenzial beim Gaming zu steigern und bei einer Vielzahl von Spielen Spitzenleistungen zu erzielen. Dank Rapid Prototyping mit dem SLS-3D-Drucker Fuse 1 kann Battle Beaver Customs die Halterungen und Tastendesigns flexibel anpassen. Bei der Herstellung kundenspezifischer Konsumgüter zahlen sich kurze Durchlaufzeiten für Unternehmen aus, weil sie ihren Mitbewerbern immer einen Schritt voraus sein wollen. Michael Crunelle, Leiter von Forschung und Design bei Battle Beaver Customs, erklärt: „Der Fuse 1 ist großartig, wenn wir schnell Änderungen vornehmen müssen, sei es bei einem Konzept oder einem Endverbrauchsteil. Unsere Konkurrenz kann da nicht mithalten.“
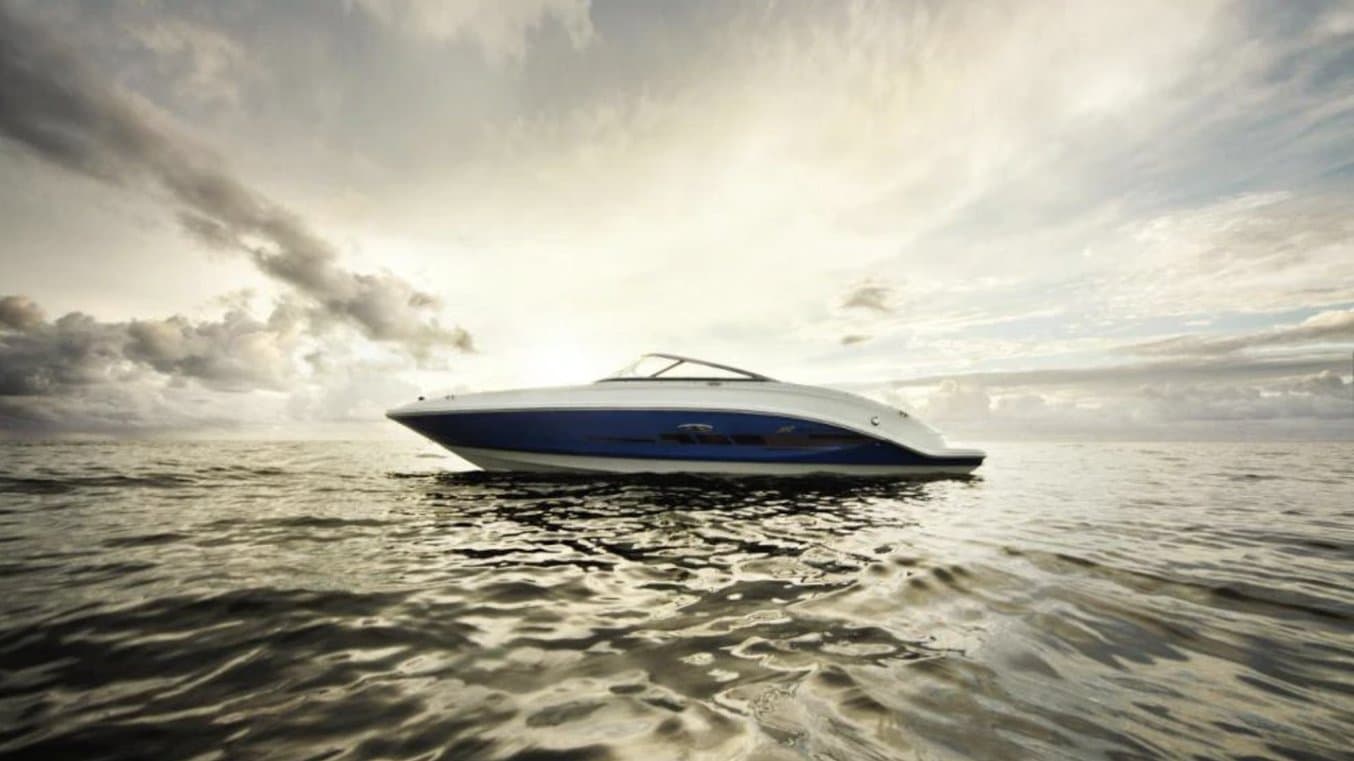
JetBoatPilot ist ein Hersteller von Zubehör- und Nachrüstteilen mit speziellem Fokus auf Wasserfahrzeugen. Einen Namen hat sich das Unternehmen mit seinen Produkten zur Nachrüstung von Jetbooten gemacht, die die Leistung und insbesondere die Manövrierbarkeit dieser Bootsklasse bei niedrigen Geschwindigkeiten verbessern.
JetBoatPilot nutzt dafür den SLA-3D-Drucker Form 3 und den SLS-Drucker Fuse 1 von Formlabs, um Prototypen zu entwickeln wie auch endgültige Aftermarket-Produkte zu fertigen. So auch für den Lateral Thruster 2.0: Design und Fertigung dieses neu konzipierten Produkts, das inzwischen zu den Verkaufsschlagern des Unternehmens gehört, erfolgten mit dem Fuse 1. Mit dem SLS-3D-Drucker und Nylon 12 Powder betrugen die Kosten gerade einmal ein Sechstel von dem, was JetBoatPilot mit seinen früheren Produktionsverfahren veranschlagen musste. „Ich hätte für die Version aus Aluminium wahrscheinlich einen Verkaufspreis um die 400 USD, vielleicht sogar 600 USD angesetzt. Für 600 USD hätte ich aber weitaus weniger verkaufen können. Jetzt biete ich es dagegen zu einem Preispunkt von gerade einmal 199 USD an und meine Kunden sind gänzlich zufrieden. Das ist wohlgemerkt das 20-fache von dem, was meine Fertigungskosten ausmachen“, betont JetBoatPilot-Gründer Will Owen.
Die besten Badebomben entwerfen
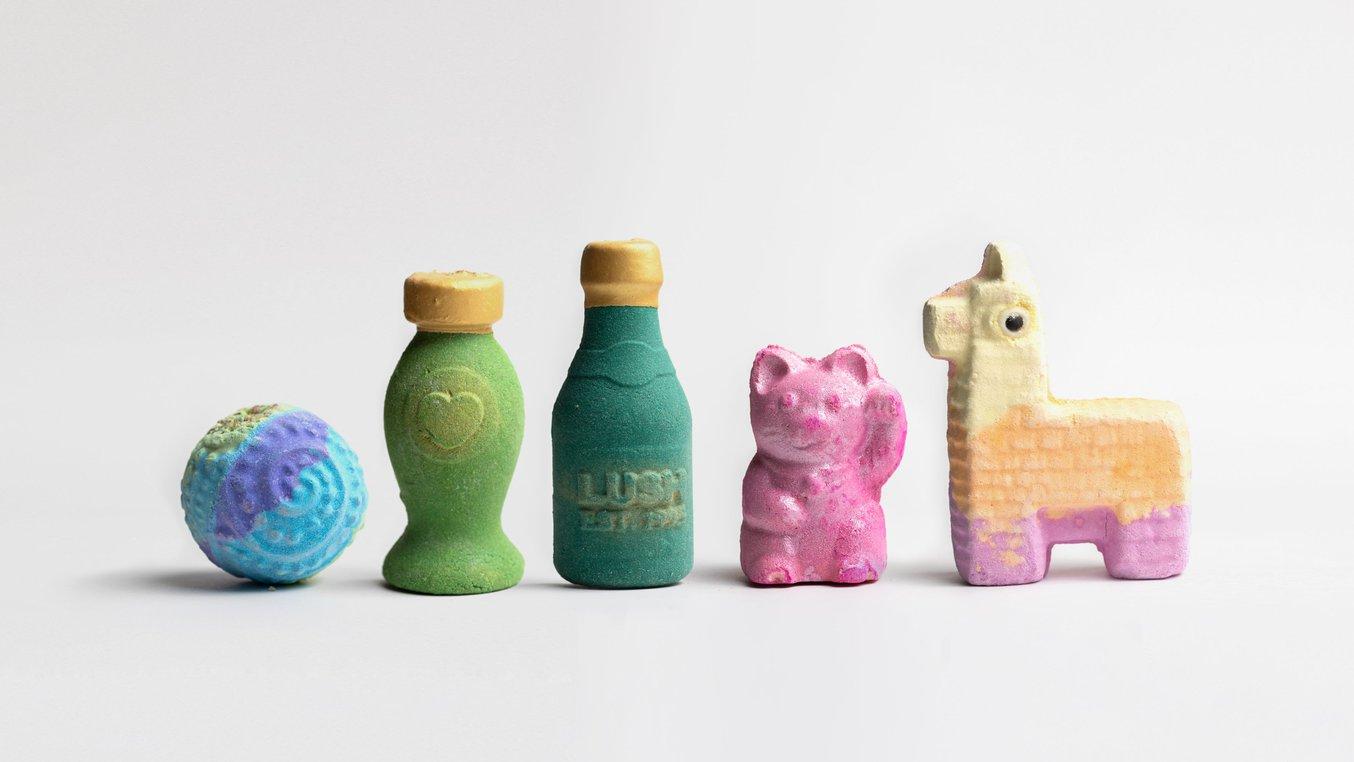
Lush Cosmetics ist mit 928 Niederlassungen in 48 Ländern auf der ganzen Welt für seine kreativen, ansprechenden Kosmetikprodukte wie Massagebars, Bodylotions, Badebomben und mehr bekannt. Ein Erfolgsrezept ist die Fähigkeit, schnell auf Trends und Kundenwünsche reagieren zu können.
Um neue, branchenprägende und hochdetaillierte Kosmetikprodukte Wirklichkeit werden zu lassen, stieg Lush in den 3D-Druck ein, den das Unternehmen für weitaus mehr als das Prototyping neuer Formen nutzt. Der Kosmetikhersteller investierte in ein neuartiges Fertigungszentrum für additive Verfahren, das zum Formenbau, zur Werkzeugausstattung und zur Herstellung von Endverbrauchsteilen dient.
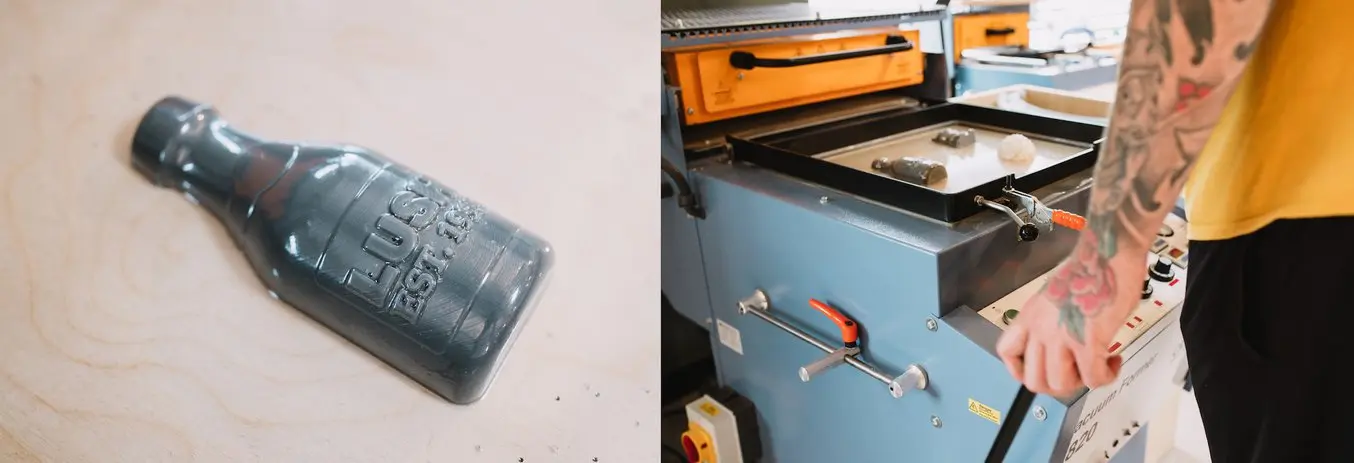
Mithilfe von 3D-gedruckten Formwerkzeugen wird bei Lush Cosmetics betriebsintern vakuumgeformt.
„Wir nutzen die 3D-Drucker von Formlabs für die Herstellung von Formen, maßgefertigter Werkzeugbestückung und von Endverbrauchsteilen. Wir sind ein innovationsfreudiges Unternehmen und die betriebsinterne Möglichkeit bedeutet für uns, dass wir unsere Entwürfe nicht extern teilen müssen, sondern den gesamten Produktentwicklungsprozess in der Hand haben“, erläutert Damien Carter, Innovation Lab Manager bei Lush Cosmetics
Erstmals echte Mass Customization
3D-Druck erschließt neues Potenzial und Geschäftsmöglichkeiten, wie etwa die kundenindividuelle Massenproduktion. Was früher für die Produktion mit herkömmlichen Methoden zu komplex, unerschwinglich oder unpraktisch war, ist heute mit digitalen Technologien ohne zusätzliche Kosten möglich. So haben Designer vollständige Kontrolle und umfassend individualisierbare Konsumgüter werden zur Wirklichkeit.
Ein ideales Beispiel hierfür ist der Razor Maker™ von Gillette, der Kunden die Möglichkeit gibt, den Griff des Rasierers mithilfe von verschiedenen Designs, Farben oder eigenem Text individuell zu gestalten.
„Für Gillette stellt das Pilotprojekt Razor Maker™ einen wichtigen Schritt hin zu einer stärkeren Personalisierung seiner Produkte dar. Hierzu müssen sich Technologie und neue Geschäftsmodelle verbünden und Produkte liefern, die genauso individuell sind wie unsere Kunden“, sagt Donato Diez, Global Brand Manager bei Gillette und für Razor Maker™ zuständig.
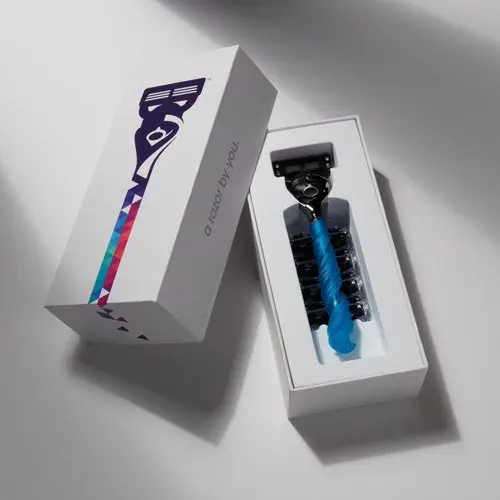
Leitfaden zu Mass Customization
In diesem Leitfaden erhalten Hersteller Einblick in die verschiedenen Ansätze zur Individualisierung von Produkten, die Auswahl der passenden Methode und mehr.
Ein neues Gebiss aus dem 3D-Drucker
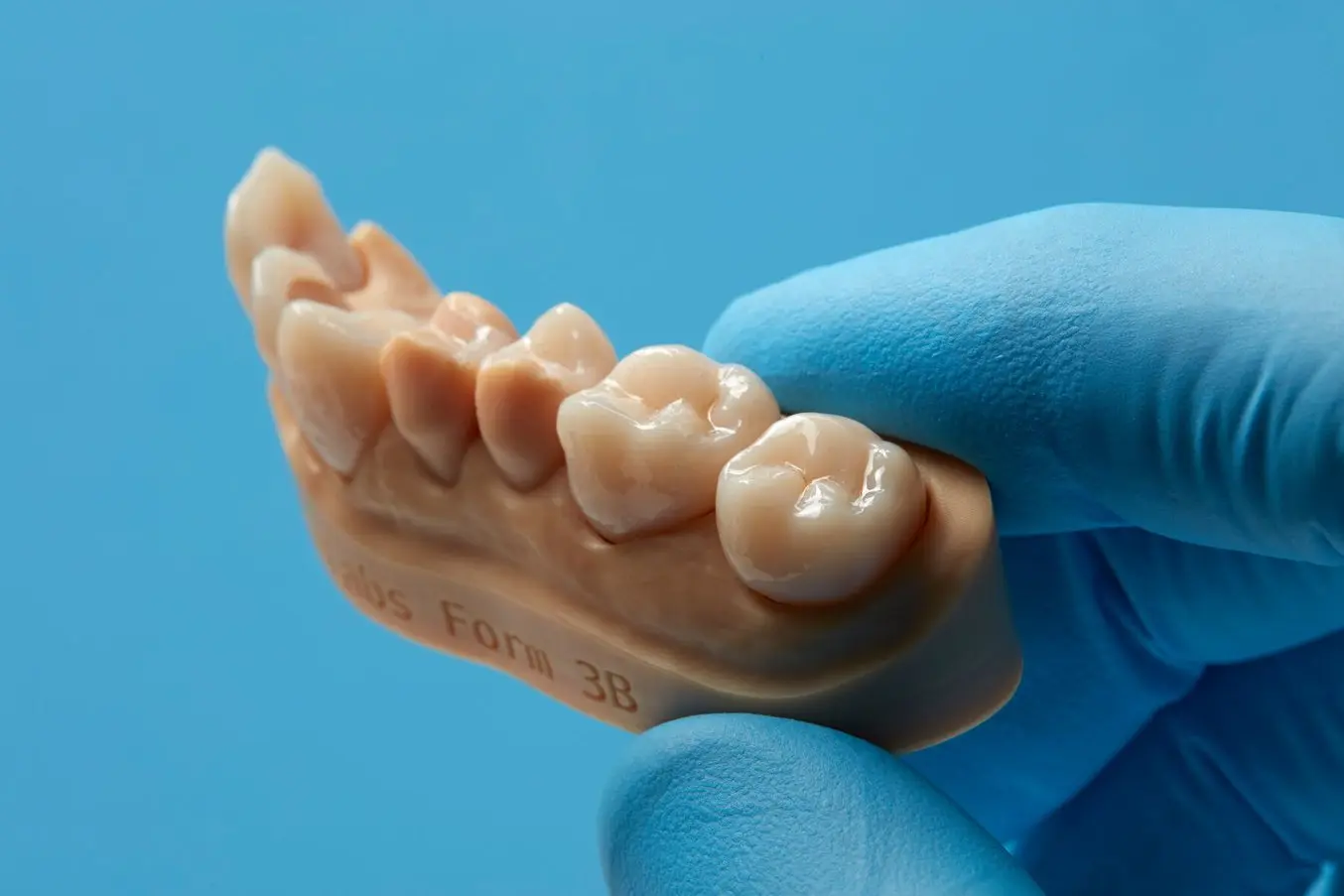
Einer der bedeutendsten Antreiber der Investition in den 3D-Druck ist die Zahnmedizin, denn in Dentallaboren und zahnmedizinischen Praxen werden Desktop-3D-Drucker immer mehr zum Standard. Wahrscheinlich sind transparente Aligner, die auf 3D-gedruckten Formen thermogeformt wurden, sogar der bislang erfolgreichste Einzelanwendungsfall von 3D-Druck.
Im letzten Jahrzehnt hat der zahnmedizinische 3D-Druck eine derartige Entwicklung zurückgelegt, dass heute keine neuen Dentallabore mehr eröffnet werden, die nicht irgendeine Form der digitalen Zahntechnik nutzen. Es sind heute Materialien in einer Qualität verfügbar, die sogar den 3D-Druck von permanenten Kronen, Vollprothesen und mehr zulässt.
3D-Drucktechnologien glänzen in Situationen, in denen aufgrund der Einzigartigkeit des menschlichen Körpers individuell angepasste Lösungen erforderlich sind. Deshalb durchläuft die Zahnmedizin einen schnellen digitalen Wandel. Digitale Arbeitsabläufe sorgen für gesteigerte Effizienz, gleichbleibend hohe Qualität und sinkende Kosten in Dentallaboren und Zahnarztpraxen.
3D-gedruckte Luxusbrillen
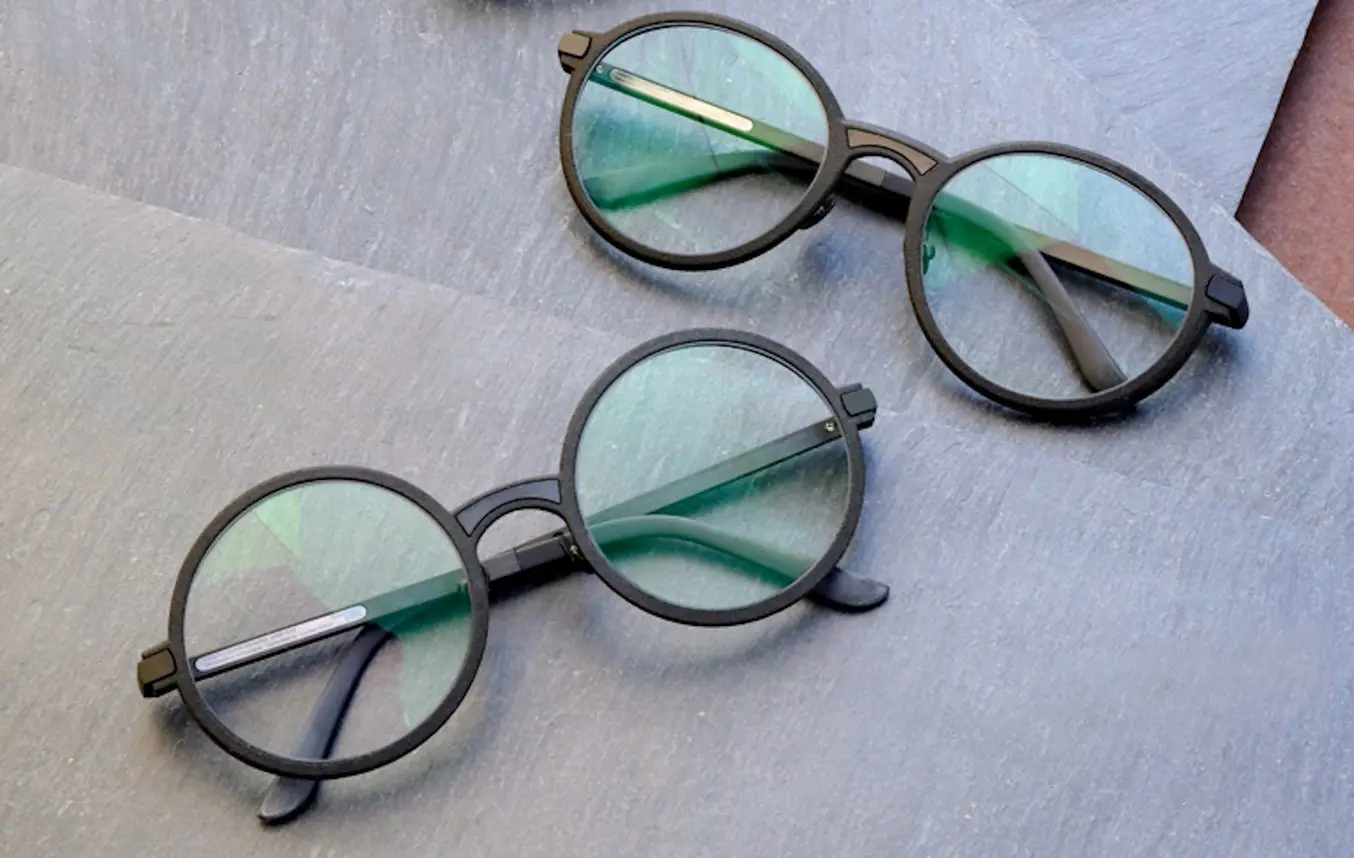
Wenn Sie das nächste Mal abends ausgehen, halten Sie Ausschau nach dem nächsten unerwarteten Anwendungsbeispiel für 3D-Druck: Jetzt ist der 3D-Druck nämlich auch in der Fertigung individualisierter Brillengestelle angelangt.
Die Marcus Marienfeld AG hebt sich von Feld der herkömmlichen Brillenrahmen ab, indem sie ihre Brillengestelle mit anderen, einzigartigen Produktionsverfahren herstellt. Vor Kurzem hat das Schweizer Unternehmen auch den 3D-Druck durch selektives Lasersintern (SLS) in seine Produktion von Brillenrahmen integriert, um damit Endverbrauchsteile und Rapid Tooling zur Umformung von Titan herzustellen.
„Wenn man über betriebsinterne 3D-Drucker verfügt, wird man sehr kreativ und erfinderisch. Ich kann jetzt mit wenig Aufwand Dinge vollbringen, die ich andernfalls gar nicht versucht hätte", erzählt Marcus Marienfeld.
Unbegrenzte Möglichkeiten
Sich die Veränderungen auszumalen, die durch den 3D-Druck vorangetrieben werden, erfordert nicht mehr dieselbe lebhafte Vorstellungskraft wie früher. Angesichts der Weiterentwicklung und Etablierung von Arbeitsprozessen in verschiedenen Branchen in den letzten Jahren werden wir Zeugen dieses revolutionären Potenzials.
Von der Zahntechnik über das Gesundheitswesen hin zu Konsumgütern, Architektur und Fertigung kommt die Öffentlichkeit immer mehr mit den vielen nützlichen Anwendungen des 3D-Drucks in Kontakt. Angesichts der kosteneffizienten Herstellung maßgefertigter Produkte, der Verkürzung von Durchlaufzeiten und der Minimierung von Mehraufwand sowie der Einbindung der Kundenwünsche in die Produktentwicklung, kann man nur davon ausgehen, das der 3D-Druck noch weiter wächst.