Formlabs' neuer Form 4: Beispiellose Schnelligkeit, Genauigkeit und Zuverlässigkeit definieren 3D-Druck neu
Formlabs präsentiert mit Stolz den neuen Form 4: unseren Kunstharz-3D-Drucker der nächsten Generation, der die Branchenstandards für Schnelligkeit, Genauigkeit, Zuverlässigkeit und Materialvielfalt neudefiniert.
Der Form 4 und seine biokompatible Version, der Form 4B, bilden die nächste Entwicklungsstufe im SLA-3D-Druck (Stereolithografie), basierend auf Jahren bahnbrechender Innovationen auf dem Gebiet Hardware, Software und Materialwissenschaft. Dank seiner unvergleichlichen Geschwindigkeit liefert der Form 4/B die Mehrheit der Teile in unter zwei Stunden, unabhängig vom Material und ohne jegliche Abstriche bei der Maßgenauigkeit und Oberflächenqualität.
Der Form 4 kombiniert ein neues Drucksystem mit einer erweiterten Formlabs-Materialbibliothek – ab Lieferstart stehen 23 Kunstharze für den Form 4 und 37 Kunstharze für den Form 4B zur Verfügung. Zusätzlich stellen wir neues Zubehör und Nachbearbeitungslösungen vor, die eine verbesserte Anwendererfahrung bieten. Mit diesen Neuerungen untermauert Formlabs die Position seines Ecosystems für den Kunstharz-3D-Druck als die leistungsstärkste verfügbare Lösung für professionelle Anwender*innen, um ihre Ideen Wirklichkeit werden zu lassen.
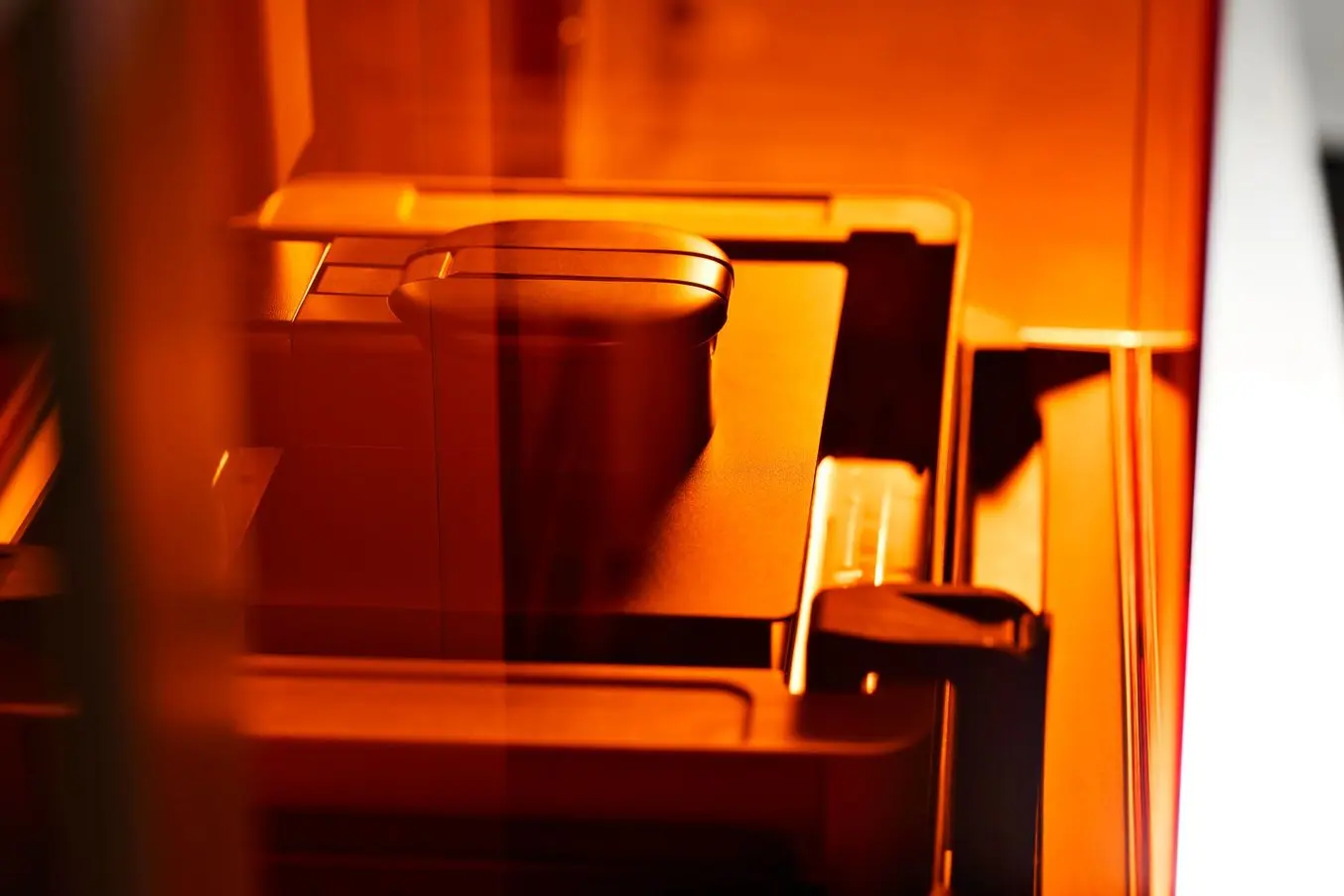
Produktdemo: Form 4
Entdecken Sie, wie der Form 4 neue Maßstäbe der Produktivität und Innovation setzt, dank beispielloser Schnelligkeit, Genauigkeit und Zuverlässigkeit.
Die nächste Stufe in der Evolution von SLA
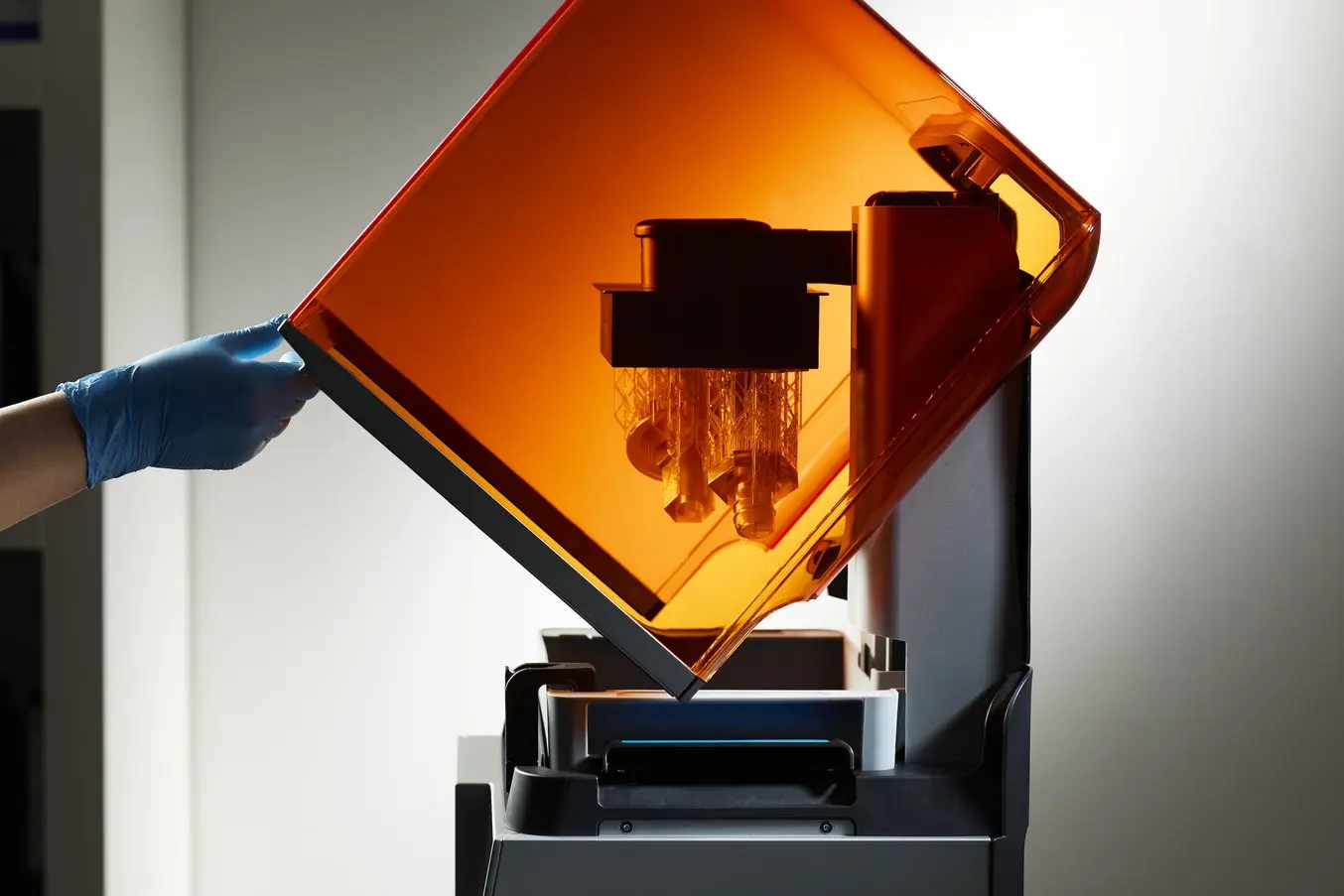
Der Form 4 nimmt die besten Eigenschaften der weltweit führenden Kunstharz-Drucker und entwickelt sie weiter. Damit erreicht er blitzschnelle Druckgeschwindigkeiten, ein 30 % größeres Fertigungsvolumen und eine höhere Maßgenauigkeit und Präzision als je zuvor.
Seit 2011 verfolgt Formlabs die Mission, leistungsstarke 3D-Druck-Ausrüstung für Maschinenbau, Produktdesign, Fertigung, Forschung, Gesundheitswesen und mehr bereitzustellen. Indem sie fortschrittliche 3D-Druck-Technologien zum ersten Mal erschwinglich machten, ebneten die frühen Versionen unserer Drucker den Weg für Innovationen in sämtlichen Branchen und bereiteten dem Kosten- und Zeitaufwand traditioneller Fertigung ein Ende.
Die Entwicklung von Produkten und die Arbeit mit physischen Teilen ist nach wie vor eine riesige Herausforderung – jede Idee muss unzählige Hürden nehmen, bevor das Produkt den Endkunden erreicht, und auch die Skalierung der Produktion hält Hindernisse bereit. Der 3D-Druck beseitigt zwar viele der grundlegenden Barrieren von Fertigungsprozessen, doch selbst die betriebsinterne Herstellung von Prototypen, Werkzeug und Kleinserien von Endverbrauchsteilen kann noch zu langsam oder zu kostspielig ausfallen.
Ein 3D-Drucker muss als Fertigungswerkzeug mit der Geschwindigkeit der Geistesblitze von Produktdesignern, dem täglichen Bedarf an Vorrichtungen für das Montageband oder auch mit der Produktion im großen Maßstab mithalten können. Durch die Zusammenarbeit mit über 50 000 Unternehmen, die schon seit Jahren auf Formlabs-Drucker vertrauen, haben wir die Problemstellen des 3D-Druckprozesses identifiziert und alles daran gesetzt, sie durch die kontinuierliche Verbesserung unserer Produkte zu beheben.
Der Form 4 schafft neue Möglichkeiten für jedweden Anwendungsfall, indem er die Iterationsschleifen von Designteams verkürzt, den Durchsatz von Herstellern erhöht und die Materialvielfalt von Fertigungsdienstleistern erweitert.
Seine Druckgeschwindigkeit von bis zu 100 mm pro Stunde1, sein um 30 % größeres Fertigungsvolumen, neue fortschrittliche Materialien und Neuerungen beim Arbeitsprozess machen den Form 4 zum leistungsstärksten professionellen Fertigungswerkzeug auf dem Markt.
1Bei Verwendung von Fast Model Resin V1 und 200 μm Schichthöhe. Basierend auf tatsächlicher Druckzeit einer Reihe von Testteilen, die gängige Anwendungen in Maschinenbau, Produktdesign, Fertigung und Zahnmedizin abdecken.
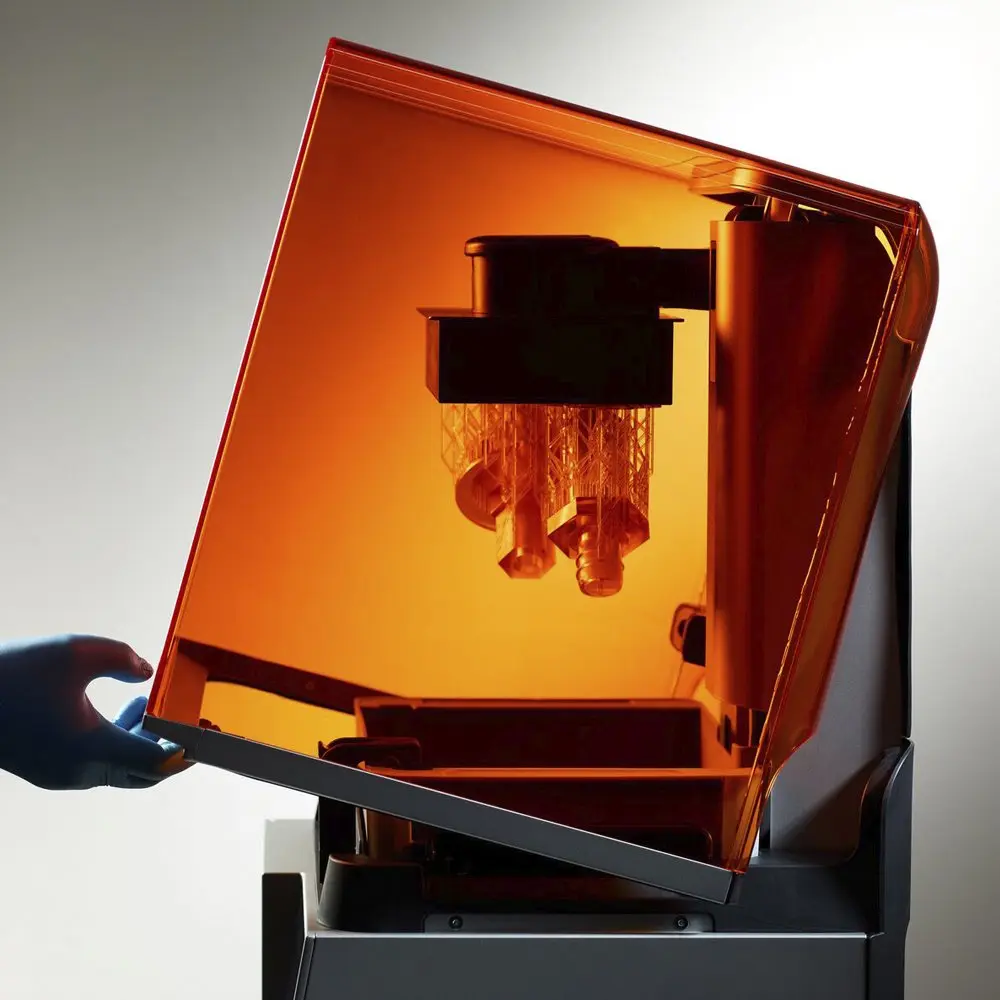
Leitfaden zum 3D-Druck mit Stereolithografie (SLA)
Sie suchen einen 3D-Drucker, der Ihre 3D-Modelle in hochauflösender Qualität Wirklichkeit werden lässt? Lernen Sie in diesem Whitepaper das Verfahren der Stereolithografie (SLA) näher kennen – von seiner Funktionsweise bis hin zu den Gründen für seinen Status als populärste 3D-Drucktechnologie bei der Umsetzung hochgradig detailtreuer Modelle.
Vom Konzept zur Realität – noch vor der Mittagspause
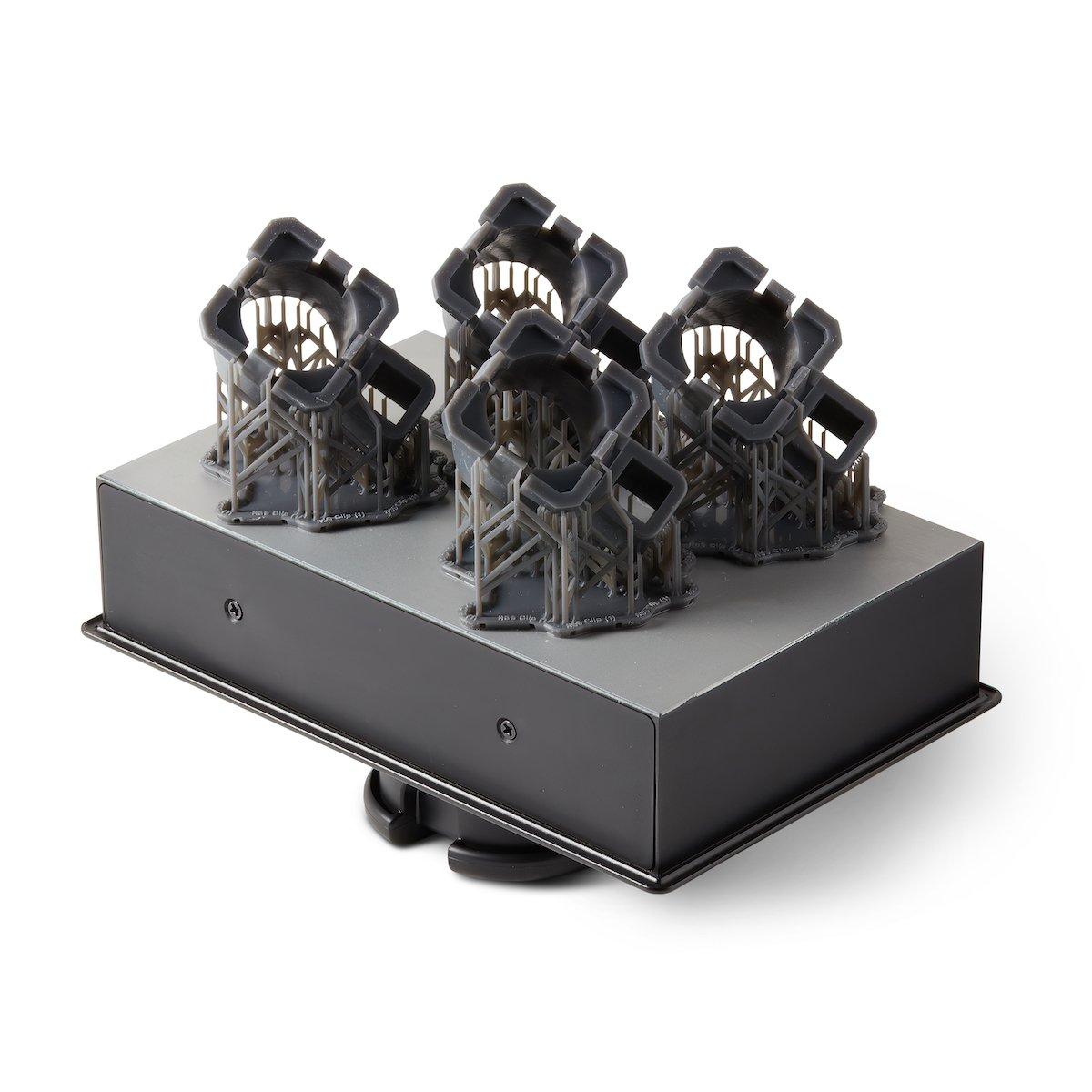
Diese Clips wurden innerhalb von einer Stunde und 53 Minuten auf dem Form 4 aus Tough 2000 Resin gedruckt. Auf dem Form 3+ dauert ihr Druck vier Stunden und 47 Minuten.
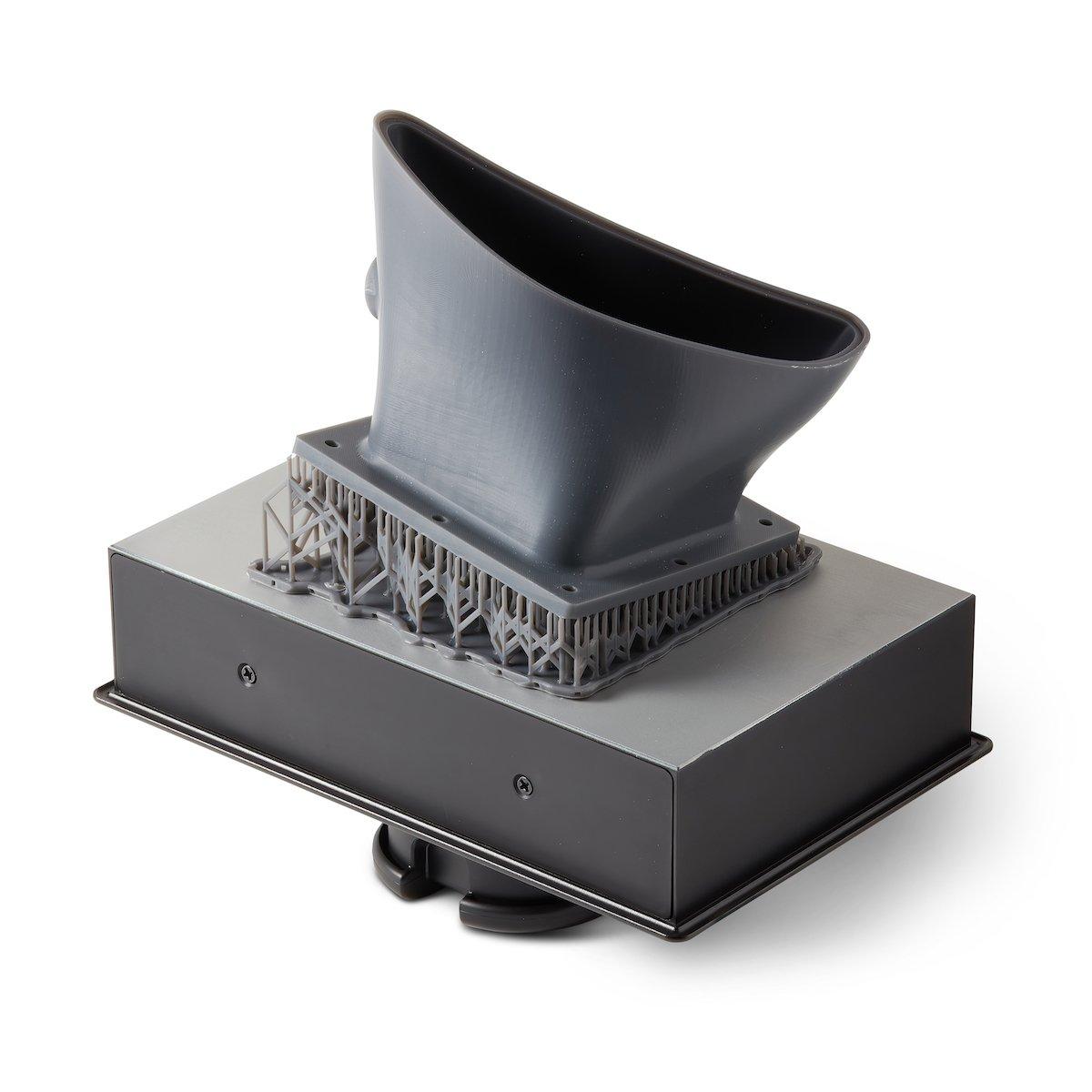
Diese große Luftstromdüse wurde innerhalb von zwei Stunden und 56 Minuten auf dem Form 4 aus Grey Resin V5 gedruckt. Auf dem Form 3+ dauert der Druck fast neun Stunden.
Der Form 4 verleiht jeder Person, jedem Team und jedem Unternehmen die Chance, mehr zu schaffen. Die Grenzen der Produktivität sind niemals durch einen Mangel an Ideen bestimmt – sondern durch die Kapazität, diese umzusetzen. Dank schnellerer Druckzeiten als jemals zuvor können Produkte jetzt mehrmals am Tag den Zyklus von Design, Druck und Test durchlaufen.
Auf dem Form 4 werden Drucke zwei- bis viermal schneller fertiggestellt als mit jedem anderen Kunstharz-3D-Drucker der Form-Serie, sogar hohe Teile und Seriendrucke. Damit ist das Gerät sonstigen professionellen 3D-Druckern jeder beliebigen Technologie und Kategorie weit voraus.
Die Schnelligkeit des Form 4 beruht auf dem neuen Drucksystem Low Force Display™ mit einer leistungsstarken Kombination aus Hochleistungs-LEDs und Maskierungsvorrichtungen, die ganze Schichten von Kunstharz auf einmal härten – unabhängig von der Größe und Anzahl der Teile. Die Druckzeit ist somit nicht länger davon abhängig, wie viel von der Konstruktionsplattform bedeckt ist. Dadurch können mehrere Teile zugleich gedruckt werden, ohne dass sich die Druckzeit verlängert.
Wie der Form 4 die Prozesse von OXO neugestaltet
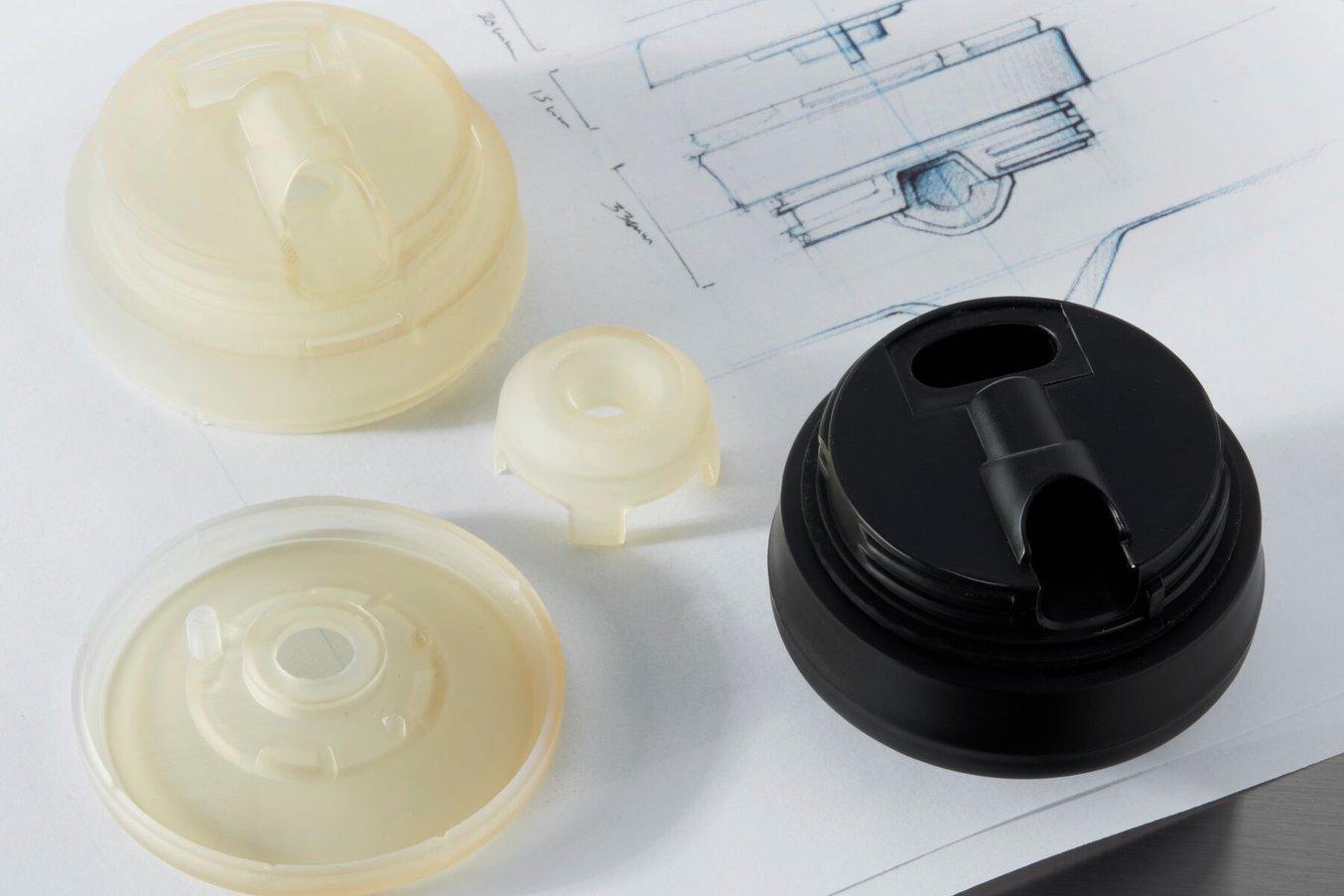
Das Produktentwicklungsteam von OXO muss mit dem schwindelerregenden Tempo des Konsumgütermarktes Schritt halten und dabei sicherstellen, dass seine Produkte noch vor den zahlreichen Mitstreitern auf den Markt für Küchenutensilien und -geräte kommen.
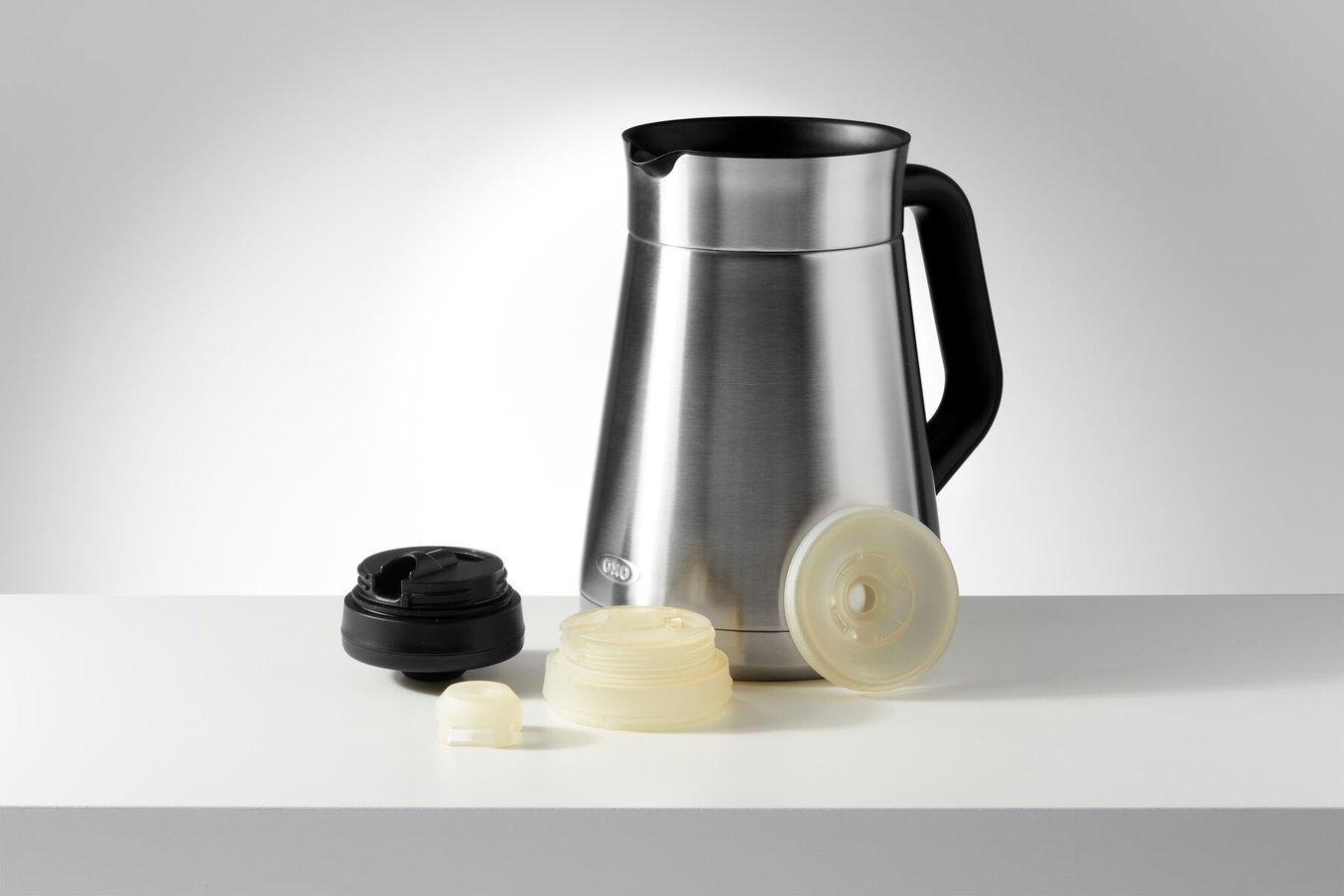
Deckel wie diese, von denen auf dem Form 4 mehrere Prototypen pro Tag erstellt wurden, spiegeln Monate der Arbeit von Ingenieur- und Designteams wider. Durch die Verdopplung der Anzahl der Designverbesserungen pro Tag unterstützt der Form 4 OXO dabei, ansprechende, funktionale und langlebige Produkte zu erschaffen.
Jesse Emanuel leitet bei OXO das Labor für Rapid Prototyping, das von Teams im Industriedesign, der Produktvalidierung und der globalen Fertigung genutzt wird. OXO verfügt über einen immensen Produktkatalog, der alles von Handutensilien wie Gemüseschälern bis hin zu komplexeren Küchengeräten wie Mixern und Kaffeemaschinen umfasst.
Um Hilfsmittel zu entwickeln, auf die sich die Kundschaft jahrelang verlassen kann, drucken Emanuel und seine Flotte von 3D-Druckern zwischen 100 und 200 Kunstharz-Druckteile pro Woche. Die Teile werden von sämtlichen Teams benötigt – mit einfachen Formmodellen werden beim Industriedesign Ideen validiert, Modelle für funktionale Praxistests helfen dem Produktteam, die Prozesse für die Massenproduktion abzustimmen, und präsentationsreife, ästhetische Teile werden vom Marketing und Vertrieb zur Vorführung vor OXO's zahllosen Händlern genutzt. Schnelligkeit, Qualität und Materialvielfalt sind bei einem 3D-Drucker unerlässlich, und der Form 4 kam genau zur richtigen Zeit.
„Der Form 4 hat unseren Arbeitsprozess revolutioniert. Früher hatten wir aus Zeitgründen oft Probleme mit unserer Warteschlange. Mit dem Form 4 ist das jetzt Geschichte – Zeit stellt für uns keine Einschränkung mehr dar.“
Jesse Emanuel, Prüfingenieur, OXO
Küchenprodukte müssen simpel, effizient und leicht zu verwenden sein – und einfach gut in der Hand liegen. Aufgrund dieser Anforderungen sind reine CAD-basierte Iterationen nahezu unmöglich, denn das Designteam von OXO muss Teile in die Hand nehmen können, um sie zu beurteilen. Mit dem Form 4 „kann das Team Iterationen spontan während eines Tages durchführen. Früher mussten wir meistens eine Nacht abwarten, um neue Produktiterationen in den Händen zu halten. Jetzt liefert uns der Form 4 drei oder vier Drucke an einem Tag“, so Emanuel.
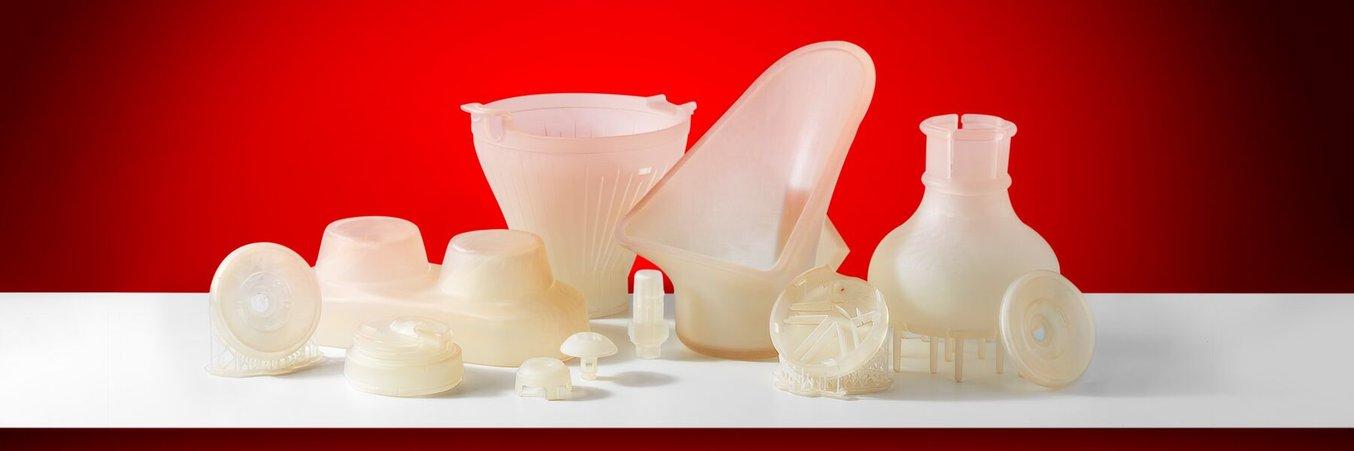
Viele der Produktlinien von OXO erfordern Prototypen wie diese Druckteile aus High Temp Resin, die ausgiebige Tests bei Hochtemperaturen durchlaufen.
Wegen seines umfangreichen Produktkatalogs benötigt OXO ein Werkzeug für die Produktentwicklung, das Schnelligkeit, Vielseitigkeit und eine hohe Fertigungskapazität bietet. Der Form 4 sorgt dafür, dass Emanuel und der Rest seines Teams ihre neuen Ideen (fast) genauso schnell testen können, wie sie ihnen einfallen.
Dass das Team die Formlabs-Kunstharze stellvertretend für gängige Industriekunststoffe verwenden kann, macht die Design- und Testphase für OXO einfacher. „Ein wichtiger Grund, weshalb wir SLA statt FDM nutzen, sind die Materialoptionen“, erklärt Emanuel. Das Team verwendet Tough 2000 Resin für ABS-ähnliche Teile, Tough 1500 Resin für Polypropylen, Silicone 40A Resin für Validierungsmodelle aus echtem Silikon, High Temp Resin für Prototypen, die in kochendem Wasser getestet werden, und Rigid 10K Resin für Spritzgussformen.
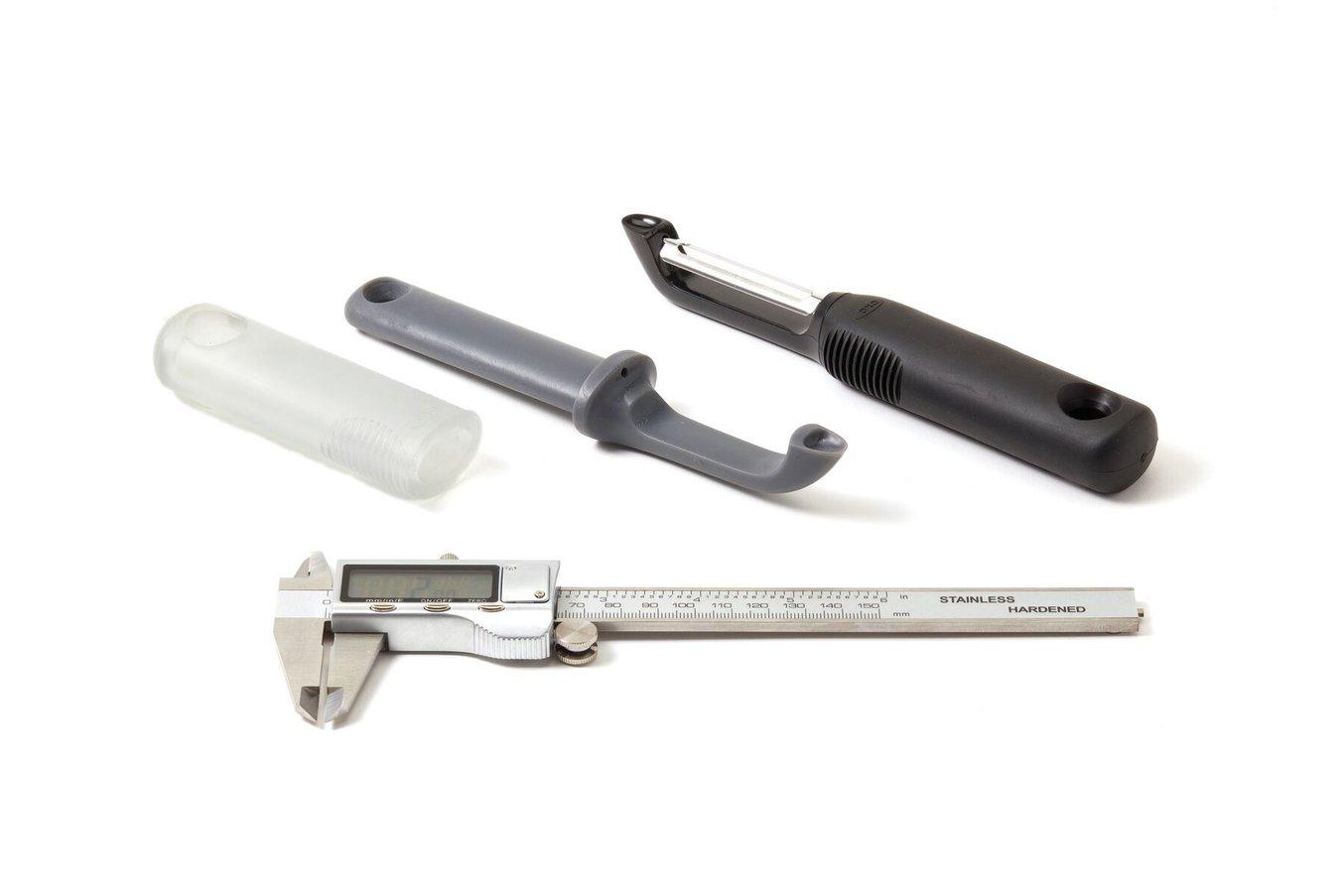
Für den OXO-Gemüseschäler, der in den Vereinigten Staaten in fast jeder Küche zu finden ist, wurden auf dem Form 4 Prototypen entwickelt. Ein vertikal gedruckter Schäler benötigt nur drei Stunden und zwanzig Minuten Druckzeit, und auf die Konstruktionsplattform passen mehr als acht verschiedene Iterationen auf einmal.
„Für alle unserer Produkte nutzen wir eine Unmenge an unterschiedlichen Komponenten und Produkten. Wir nutzen etwa 12–15 verschiedene Formlabs-Materialien, die wir aus den unterschiedlichsten Gründen einsetzen.“ Der Form 4 hat es einem schon vorher hochproduktiven Team möglich gemacht, seine Iterationsgeschwindigkeit noch zu erhöhen. Während sich der Produktentwicklungsprozess immer mehr beschleunigt, eröffnet der Form 4 ein neues Niveau der Produktivität und Effizienz. Um mehr über OXO zu erfahren, lesen Sie den vollständigen Anwenderbericht.
Branchenführende Maßgenauigkeit
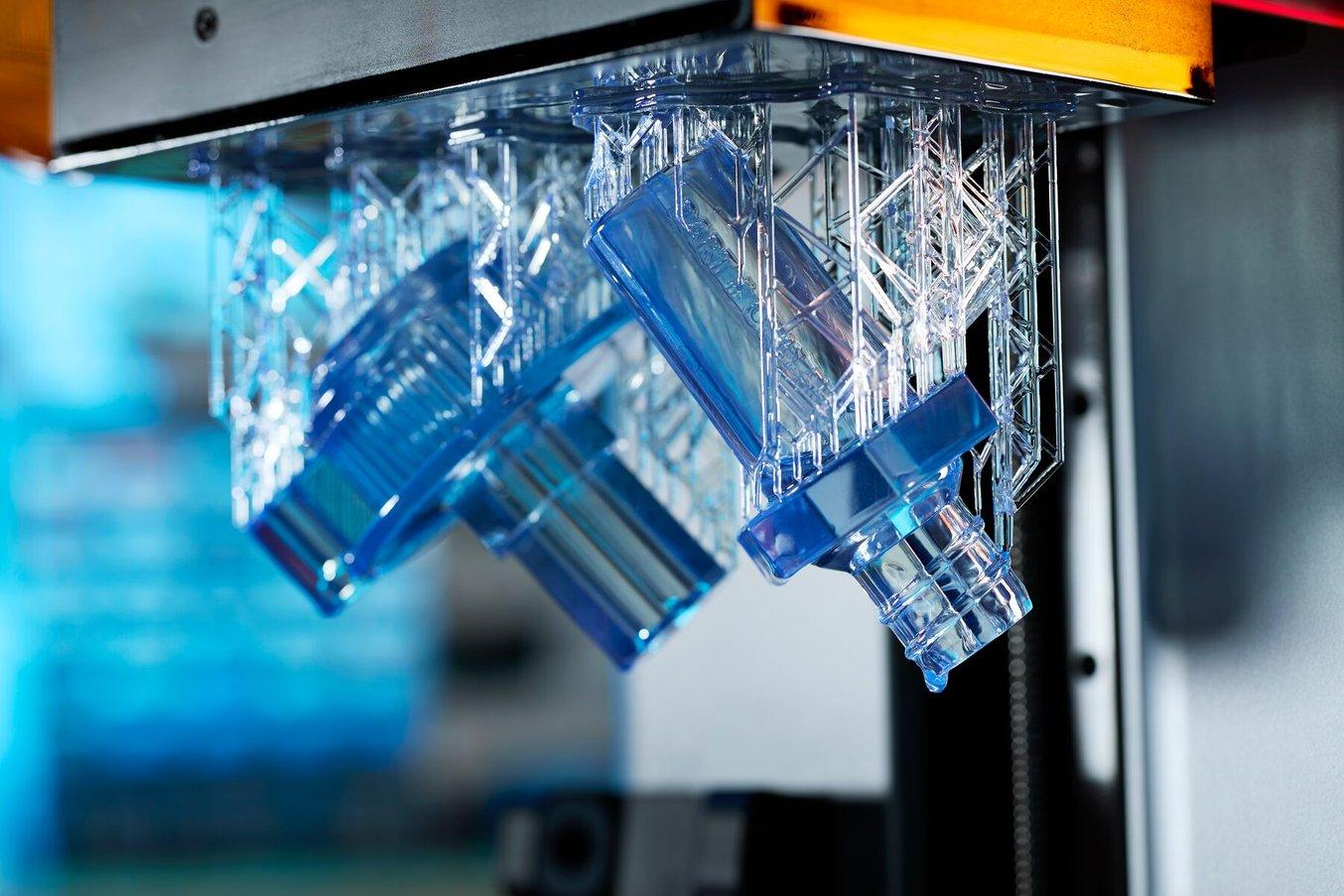
Dank der engen, einheitlichen Toleranzen, die der Form 4 erzielt, erhalten Sie Druckteile mit scharfen Kanten, klar definierten Ebenen und vollkommen glatten Oberflächen.
3D-gedruckte Teile müssen präzise sein, um von Nutzen zu sein. Egal, ob es um Prototypen geht, die Spritzgussteilen ähneln sollen, oder Vorrichtungen, die auf bestehende Komponenten einer Fertigungslinie passen müssen – Toleranzen zählen. Schnelligkeit sollte niemals auf Kosten von Genauigkeit und Präzision erreicht werden.
Der Form 4 hält den Branchenstandard in Sachen Toleranzen nicht nur ein, sondern übertrifft ihn sogar noch. Durch zuverlässige Einhaltung besonders enger Toleranzen liefert der Form 4 stets Teile, die Ihren Designparametern entsprechen, egal aus welchem Kunstharz und bei jedem Druck. Die Light Processing Unit (LPU) des Form 4 erzielt eine XY-Auflösung von 50 µm. Diese sorgt dafür, dass mehrteilige Baugruppen ohne Reibung ineinandergleiten, Fertigungshilfsmittel sich nahtlos in Prozesse integrieren lassen und Teile für die Endverwendung mit der einheitlichen Präzision von massenproduzierten Spritzgussteilen aus Kunststoff mithalten.
Durch die reproduzierbaren Toleranzen, die den ursprünglichen Designs entsprechen, arbeiten Sie über alle Phasen der Produktentwicklung hinweg mit einheitlichen Teilen. Ob Sie schnelle Konzeptmodelle drucken, fortgeschrittene Prototypen funktional testen oder sogar Funktionsteile als Übergangslösung produzieren – die Optik und Leistung aller Teile bleibt konstant. Mit einem Oberflächenfinish, das von spritzgegossenem Kunststoff nicht zu unterscheiden ist, wird der Übergang vom Design zur Massenproduktion einfacher. Die Genauigkeit des Form 4 erlaubt es Ihnen, sich auf Ihr Produkt zu fokussieren, statt für alle Eventualitäten von Maßabweichungen zu planen.
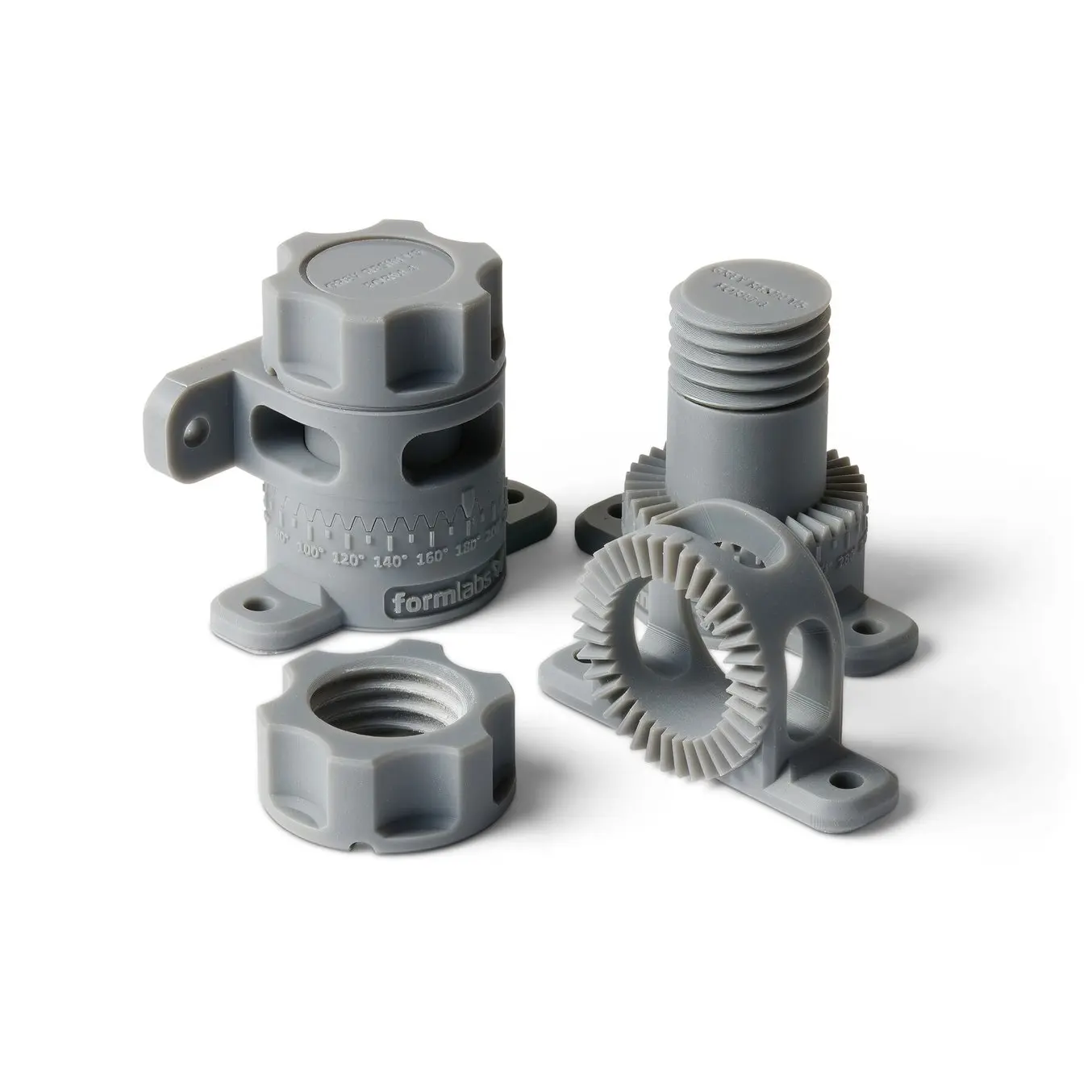
Kostenlosen Probedruck anfordern
Sehen und fühlen Sie die Qualität von Formlabs aus erster Hand. Wir senden Ihnen einen kostenlosen 3D-Probedruck an Ihren Arbeitsplatz.
In 15 Minuten zum ersten Druck – unabhängig von Erfahrungsgrad und Anwendung
Bevor hochwertiger, zugänglicher 3D-Druck dank der früheren Modelle der Form-Serie verfügbar wurde, waren SLA-Druckprozesse meist kompliziert. Einige erforderten eigenes Bedienpersonal, eine komplexe Infrastruktur und große Räumlichkeiten für den Kunstharz-Druck von oben nach unten.
Mit der Form-Serie bewies Formlabs, dass zugänglicher 3D-Druck mehr bedeutet als nur bezahlbare Preise – auch der Arbeitsprozess sollte leicht zu erlernen und der Drucker in bestehenden Räumlichkeiten unterzubringen sein, einschließlich Büros, Wohnungen, Klassenräumen und Werkstätten. Der Form 4 geht noch einen Schritt weiter: Er vereinfacht die Druckereinrichtung, die Drucküberwachung und das Wechseln von Materialien, sodass jeder in der Lage ist, innerhalb von 15 Minuten mit dem Drucken zu beginnen.
Zusätzlich zur Geschwindigkeitssteigerung, die durch das Drucksystem und die Materialeinstellungen ermöglicht wird, verringern auch neue Funktionen zur automatischen Harzhandhabung die Vorbereitungszeit bis zum Druckbeginn. Die automatische Harzabgabe nutzt eine Reihe intelligenter Sensoren, um die Betriebszeit zu maximieren. Dadurch wird die Arbeitszeit zwischen Drucken vernachlässigbar kurz und Sie können sich statt auf den Prozess ganz auf Ihre Teile konzentrieren.
Die Drucker der Form-Serie kommen in überaus komplexen Anwendungen zum Einsatz, wie etwa dem Zellaufbau durch Bioengineering, der Herstellung von Metallturbinen durch Feinguss oder der Fertigung chirurgischer Implantate. Wenn 3D-Drucker in derart komplexe Prozesse integriert werden, dann sollte der Druck selbst der einfachste Arbeitsschritt sein. Mit dem Form 4 ist das Realität. Von der Lieferung des Druckers bis zum Start des ersten Drucks benötigen Sie nur 15 Minuten für die Einrichtung und können minütlich beobachten, wie Ihre Ideen Gestalt annehmen.
Intuitive Bedienung Schritt für Schritt
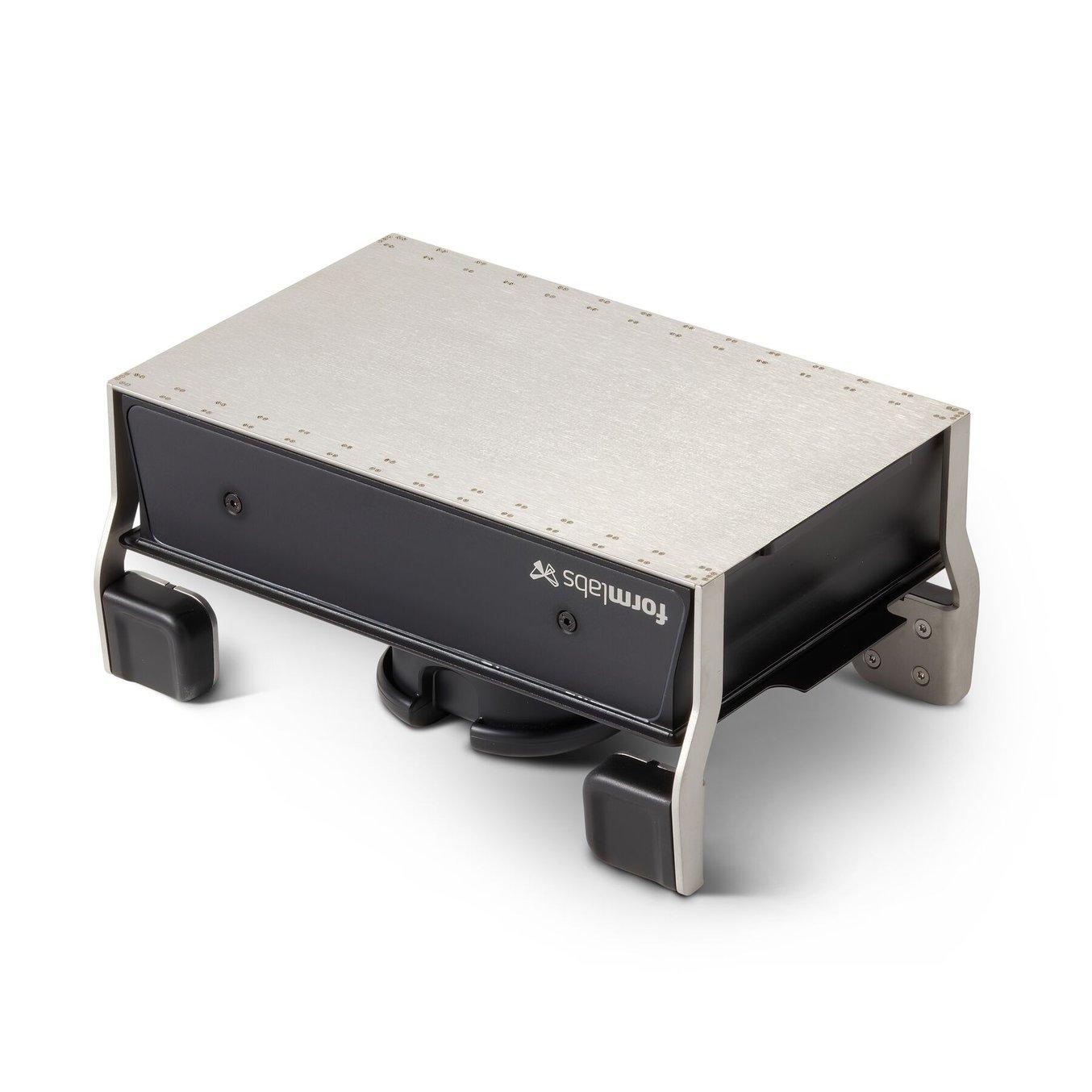
Das gesamte Formlabs-Ecosystem ist darauf ausgelegt, die Effizienz zu maximieren und das Risiko von Fehldrucken zu verringern. Formlabs' kostenlose Druckvorbereitungssoftware PreForm analysiert automatisch Ihr Modell und ermittelt die optimale Ausrichtung und Platzierung von Stützstrukturen. Formlabs' Softwareentwicklungsteam arbeitet kontinuierlich an der Verbesserung unserer Softwareeinstellungen, um die Druckgeschwindigkeit, die Materialeinstellungen sowie die automatische Ausrichtung und Stützstrukturgenerierung zu perfektionieren.
Auch der Ablauf nach Abschluss Ihres Druckes ist auf Einfachheit, Wiederholbarkeit und Effizienz ausgelegt. Die Schnellablösetechnologie (Quick Release Technology) der Build Platform Flex beschleunigt das Ablösen der Druckteile und vermindert Beschädigungen von Teilen. Die Druckteile werden anschließend im neuen Form Wash automatisch gewaschen, der dank verbesserter Umspülung mit Isopropylalkohol einen schnelleren, saubereren Prozess bietet. Der neue Form Wash ist so verstellbar, dass die Konstruktionsplattformen sämtlicher Desktop-Drucker von Formlabs darin eingesetzt werden können. Bei Teilen, die nach dem Waschen eine Nachhärtung erfordern, sorgen die präzisen Einstellungen des Form Cure dafür, dass die optimalen mechanischen Eigenschaften ausgebildet werden.
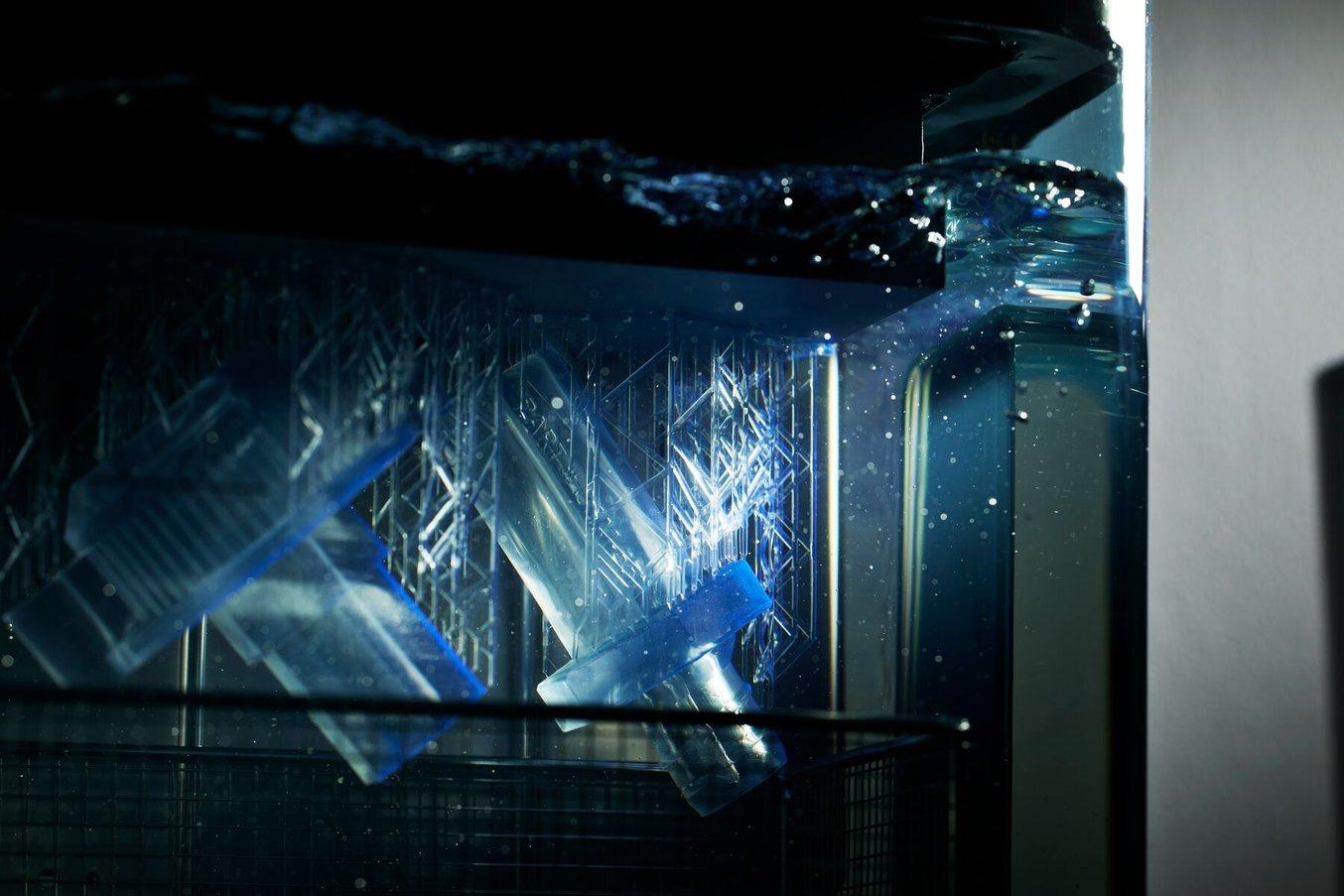
Die zweite Generation des Form Wash lässt sich an Konstruktionsplattformen unterschiedlicher Größen anpassen und bietet verbesserte Lösungsmittelbewegung, für sauberere Teile in kürzerer Zeit.
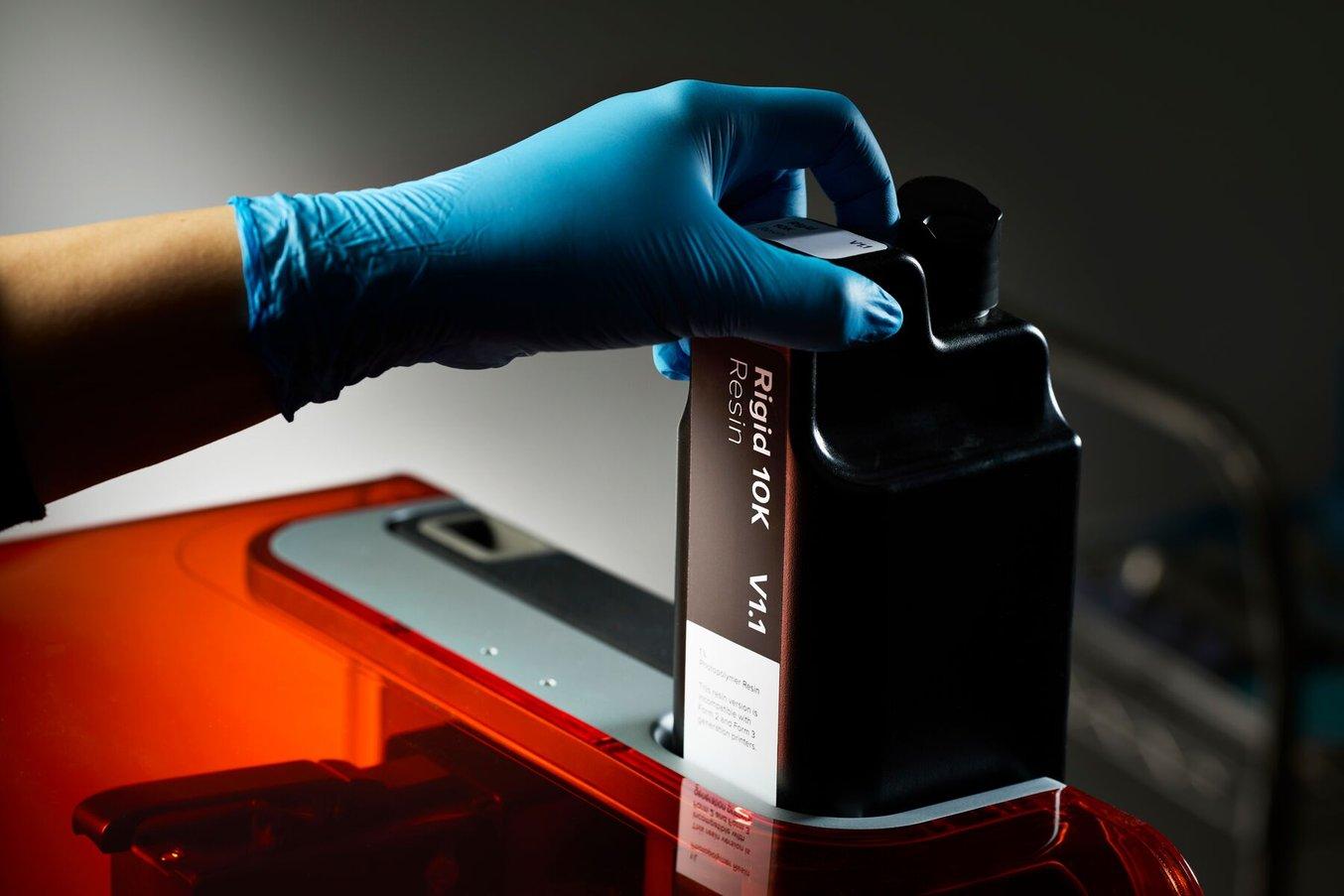
Das neue Design der Kunstharzkartusche verbraucht weniger Plastik, fasst aber dennoch einen vollen Liter Druckmaterial. Dadurch werden Lagerung und Wartung erheblich vereinfacht.
Zuverlässigkeit bei hohem Durchsatz und konsistente Erfolge
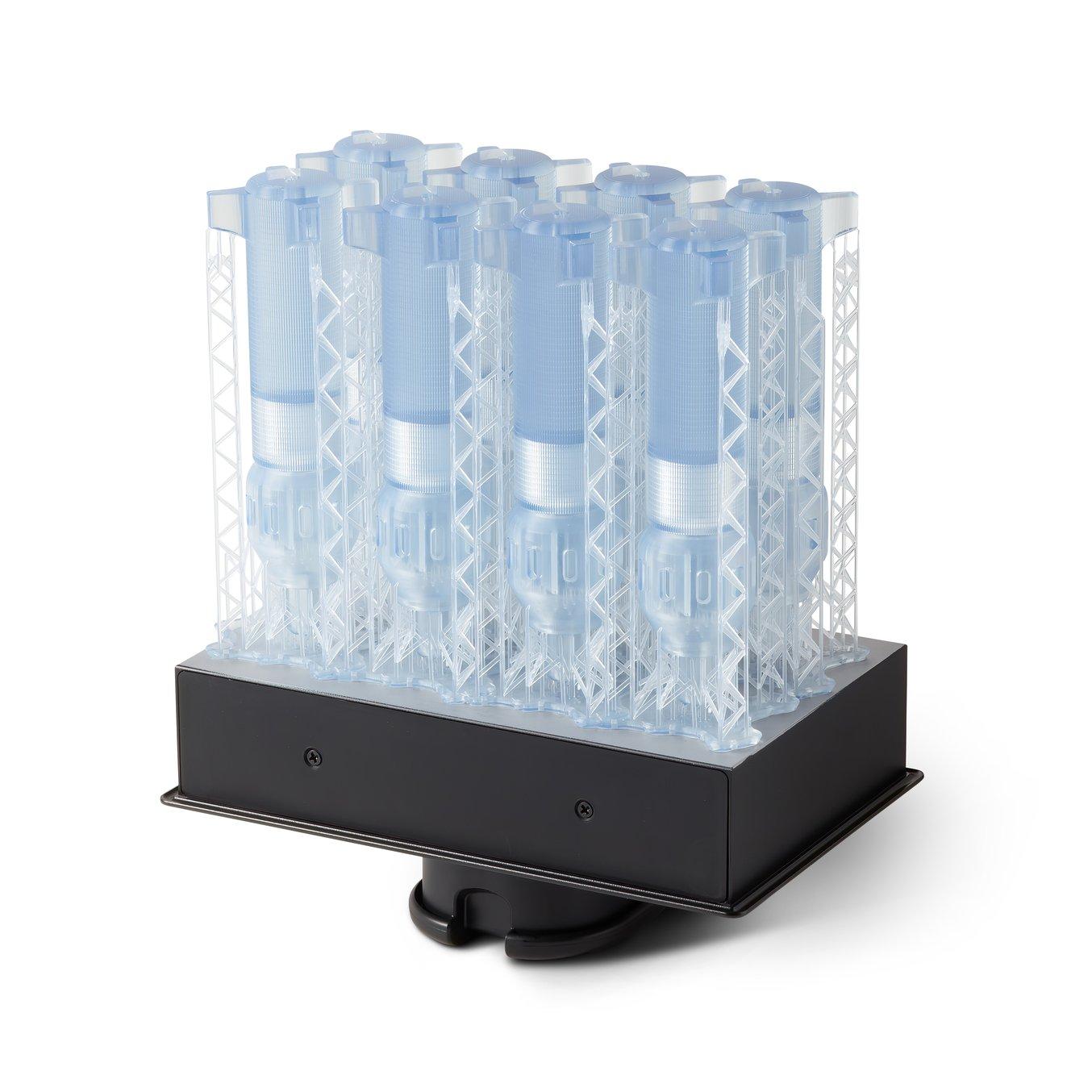
Der gesamte Druckauftrag – acht chirurgische Ratschen für die einmalige Verwendung – wird in nur fünf Stunden und 45 Minuten gedruckt, während er auf dem Form 3+ über 25 Stunden beansprucht. Nun können chirurgische Fachkräfte und medizinische Dienstleister dreimal täglich ein volles Fertigungsvolumen drucken, ohne ihre Arbeitszeit zu verlängern.
Bei der Form-Serie steht Zugänglichkeit auch für Zuverlässigkeit. Selbst wenn Kunden jeden Tag von früh bis spät drucken, lässt sie der Drucker nie im Stich. Die Form-Serie hat in Hinsicht auf Druckerfolg und wiederholbare, zuverlässige, durchsatzstarke Verwendung bereits zuvor hohe Maßstäbe gesetzt, doch der Form 4 übertrifft selbst diese.
Seine Zuverlässigkeit verdankt der Form 4 zum Teil der Sorgfalt der Qualitätskontrolle während des Fertigungsprozesses: Jeder Drucker durchläuft 60 Kontrollpunkte zur Prüfung der Funktionalität, bevor er das Werk verlässt. So wird sichergestellt, dass jede Einheit Ihre Prozesse als maximal zuverlässiges, hochleistungsfähiges Werkzeug unterstützt. Darüber hinaus hat Formlabs' für die Druckoptimierung zuständiges Team Jahre damit verbracht, Tausende von Teilen zu drucken, um die idealen Einstellungen für jedes Material zu bestimmen, damit auch komplexe Geometrien unabhängig vom Material mit branchenführender Zuverlässigkeit gedruckt werden.
Sowohl das zentrale Drucksystem und Komponenten wie der Harztank und die Konstruktionsplattform wurden überarbeitet, um noch reibungsloser zu funktionieren und gleichzeitig länger zu halten, selbst bei durchsatzstarken Anwendungen. Die Harztanks halten dem Druck von über 75 000 Schichten2 stand, was die Betriebszeit des Druckers verlängert und die Betriebskosten sowie die Anzahl manueller Eingriffe für den Druck hoher Stückzahlen verringert.
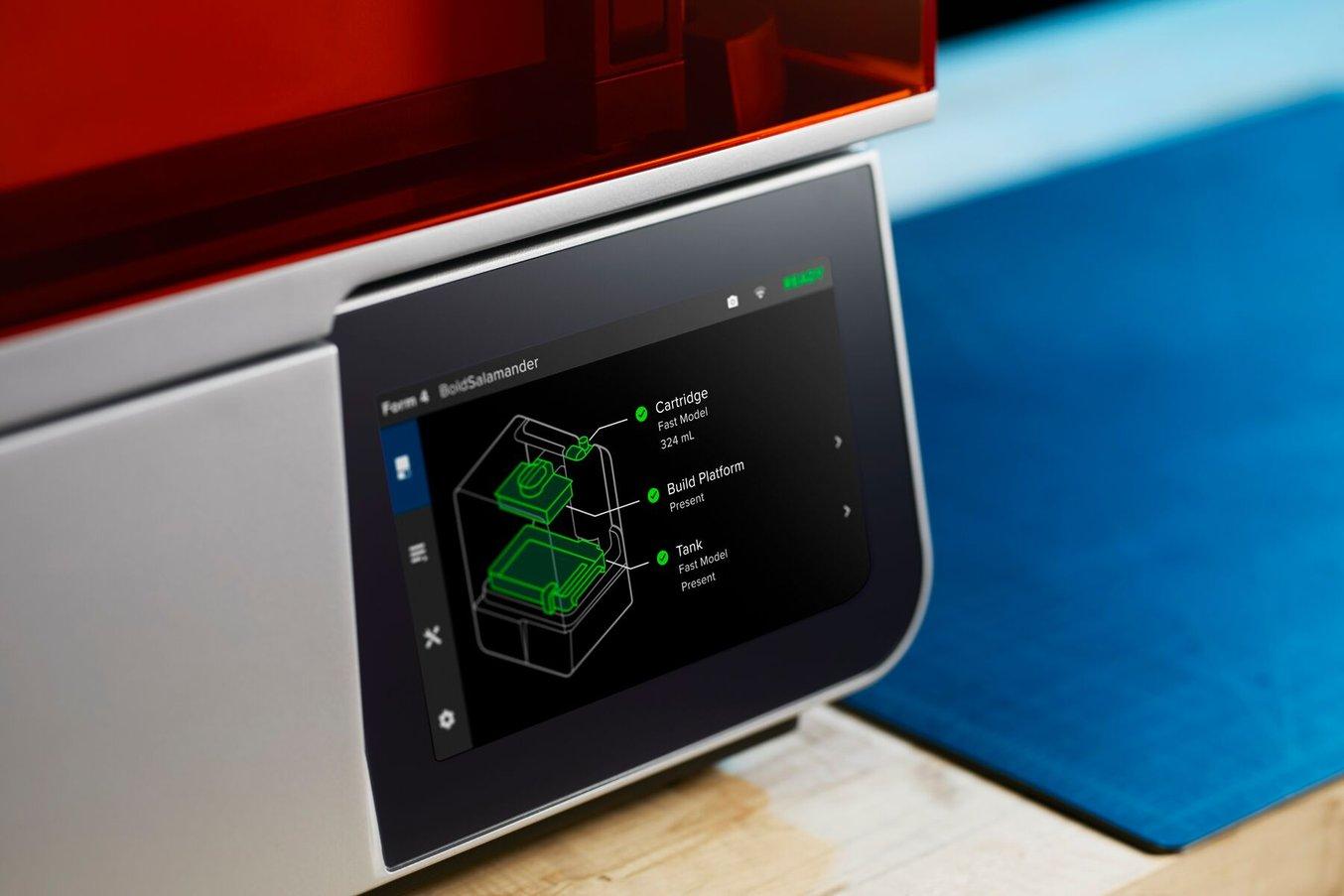
Das verbesserte Sensorensystem des Form 4 reagiert innerhalb kurzer Zeit auf potenzielle Probleme beim Druckprozess, was Anwender*innen reichlich Zeit gewährt, um ihren Arbeitsprozess anzupassen und so einen reibungslosen Druck zu garantieren.
Die automatische Fehlerdiagnose und integrierten Sensoren des Form 4 benachrichtigen Sie über potenzielle Probleme beim Druckvorgang, was Ihnen die Möglichkeit gibt, den Risiken eines unvorteilhaft eingerichteten Drucks vorzubeugen sowie ein Verständnis von der optimalen Druckernutzung zu erlangen. Das integrierte Sensorensystem sorgt dafür, dass der Form 4 stets einsatzbereit bleibt, selbst beim Druck hoher Stückzahlen – und das über Jahre hinweg. Bei erhöhter Nutzung sollte die Zuverlässigkeit niemals nachlassen. Der Form 4 ist ein Hilfsmittel, das sich gemeinsam mit Ihren Prozessen immer weiter steigert.
2 Mit jedwedem Formlabs-Material. Die genaue Lebensdauer eines Harztanks hängt von den gedruckten Schichten, dem physischen Verschleiß und versehentlichen Beschädigungen ab.
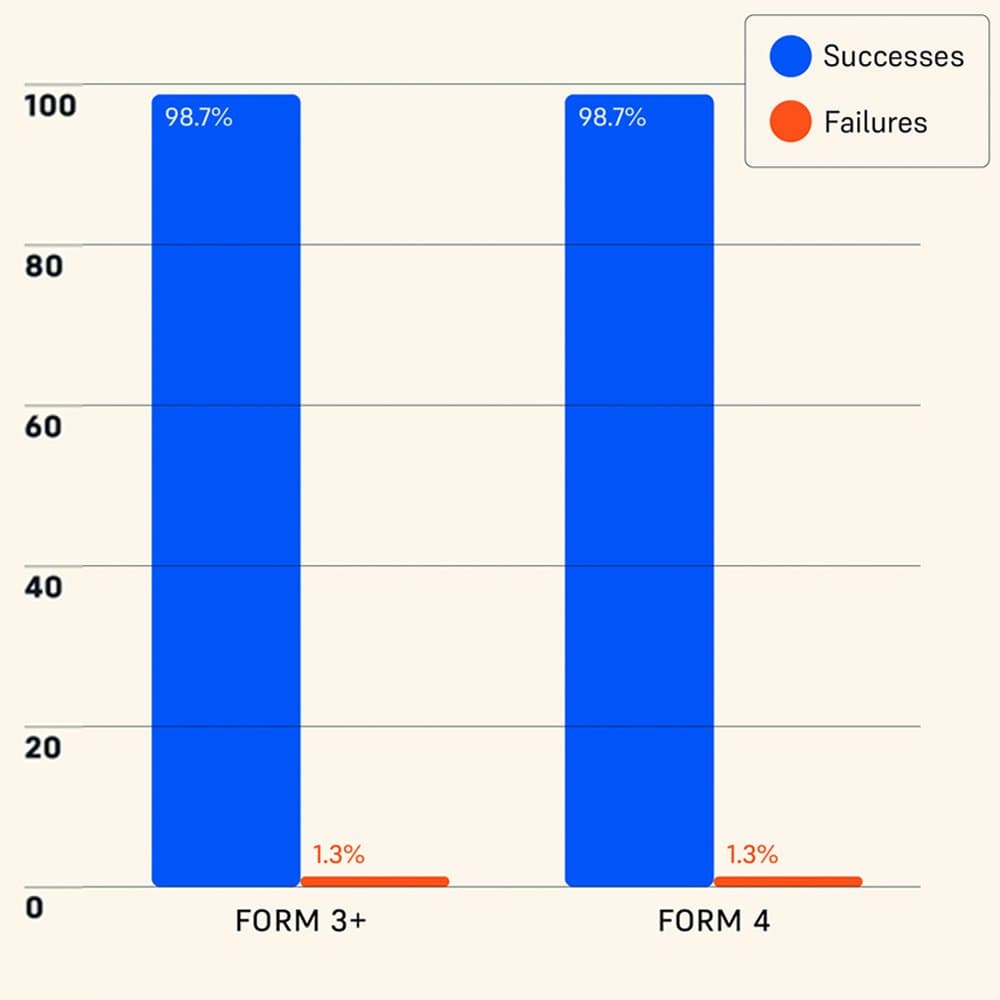
Zuverlässigkeit von Form 4 und anderen Kunstharz-3D-Druckern unabhängig getestet
Der Form 4 von Formlabs erreichte in einer Untersuchung eines unabhängigen, weltweit führenden Produkttesters eine Druckerfolgsrate von 98,7 %. Eine vollständige Beschreibung der Testmethode und die Ergebnisse finden Sie in unserem Whitepaper.
Erschließen Sie neue Anwendungen durch einen umfassenden Materialkatalog
Die Drucker von Formlabs vereinen hochpräzises Hardware-Design mit bahnbrechender Software, um einen Arbeitsprozess zu erschaffen, der bei jedem Druck komplexe Formen mit engen Toleranzen liefert. Das volle Potenzial zur Umsetzung neuer Anwendungen in immer mehr Industriezweigen wird jedoch durch Formlabs' Materialbibliothek von über 23 zweckorientierten Kunstharzen erschlossen – darunter reines Silikon, technische Keramik, Polyurethan und einzigartige Formulierungen wie Tough 1500 Resin, Rigid 10K Resin und Flame Retardant Resin.
Mit der Einführung des Form 4 werden sechs neue Materialien verfügbar, zu einem verringerten Preis:
Die optimierte automatische Harzabgabe und Harzerhitzung des Form 4 erlauben es Formlabs, Materialien zu entwickeln, die zuvor außer Reichweite waren, wie etwa Kunstharze mit sehr hoher Viskosität oder hoher Anreicherung mit anderen Stoffen. Bei den neuen Materialien handelt es sich um verbesserte Formulierungen von einigen der meistverwendeten Materialien der Welt im Kunstharz-3D-Druck. Die Eigenschaften, die Materialien wie Grey Resin und Clear Resin so beliebt gemacht haben, werden von den neuen Versionen noch gesteigert. So erhalten die Druckteile einen noch schärferen Detailgrad und überlegene ästhetische Eigenschaften. Clear Resin V5 ergibt nahezu gänzlich transparente Teile, während Black Resin V5 über eine glatte, vollkommen matte Oberfläche verfügt.
Als Formlabs im Jahr 2019 die Vorgängerversion des Form 4 ankündigte, den Form 3, standen 20 einzigartige Kunstharze zur Verfügung. Seitdem haben wir unseren Kunstharzkatalog so gut wie verdoppelt, mit insgesamt 37 verfügbaren Materialien für den Form 4B und weiteren in der Entwicklung. Die Integration des Form-4-Ecosystems in Ihre Abläufe ebnet Ihnen den Weg zur Nutzung zukünftiger innovativer Materialien, die neue Maßstäbe in puncto Zähigkeit, Haltbarkeit, Hitze- und Verschleißbeständigkeit setzen.
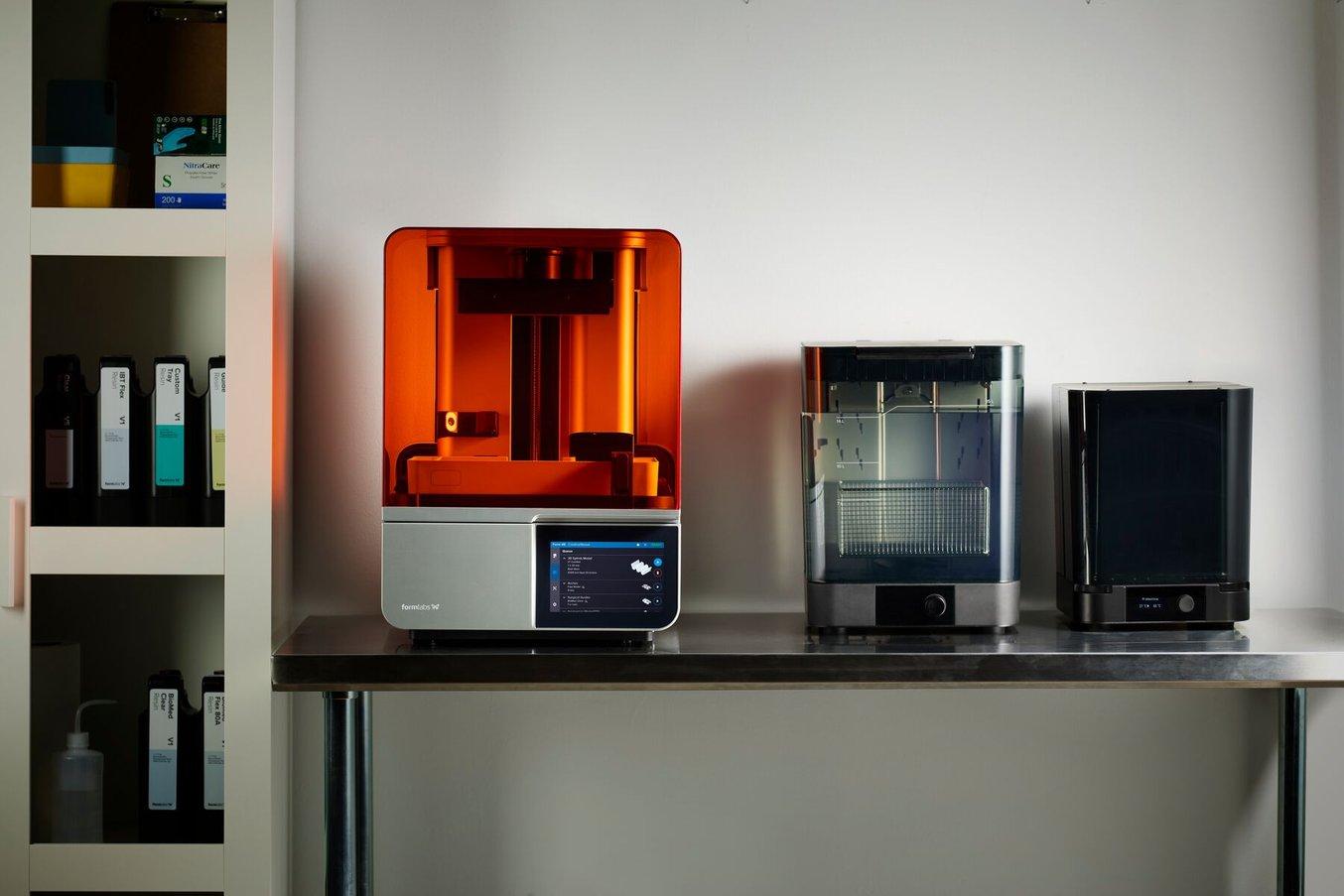
Zusammen bilden der Form 4, Form Wash und Form Cure das komplette Formlabs-Ecosystem für den Kunstharz-3D-Druck. Dieses System macht den Druck mit jedem Formlabs-Material zum Kinderspiel, da Sie sich auf vorprogrammierte Einstellungen stützen können, die stets für optimale Materialeigenschaften sorgen.
Für Kunden, die auch mit Kunstharzen experimentieren möchten, die derzeit noch nicht Teil der Formlabs-Materialbibliothek sind, steht Open Platform auch auf dem Form 4 zur Verfügung. Somit können Sie eine noch größere Materialauswahl ausschöpfen, indem Sie validierte Materialien von Drittanbietern und benutzerdefinierte Druckeinstellungen nutzen sowie von der Freiheit profitieren, mit jedem beliebigen bei 405 nm härtenden Photopolymer-Kunstharz zu drucken.
Die Kundschaft von Formlabs hat es mit Umgebungen zu tun, in denen die Wärmeformbeständigkeitstemperatur, Dehnung, Biegemodul und Zugfestigkeit ausschlaggebend dafür sind, ob 3D-gedruckte Teile eine Option sind oder konventionell gefertigte Teile benötigt werden. Jahrelang zwangen eingeschränkte Materialeigenschaften Kunden dazu, auf die sofortige Verfügbarkeit, die erschwinglichen Kosten und die Gestaltungsfreiheit des 3D-Drucks zu verzichten. Materialien machen den Unterschied. Der Form 4 wurde zusammen mit unserer Bibliothek zweckorientierter Kunstharze entwickelt, damit Sie dank vorprogrammierter Einstellungen mit jedem Druck leistungsstarke Teile erhalten.
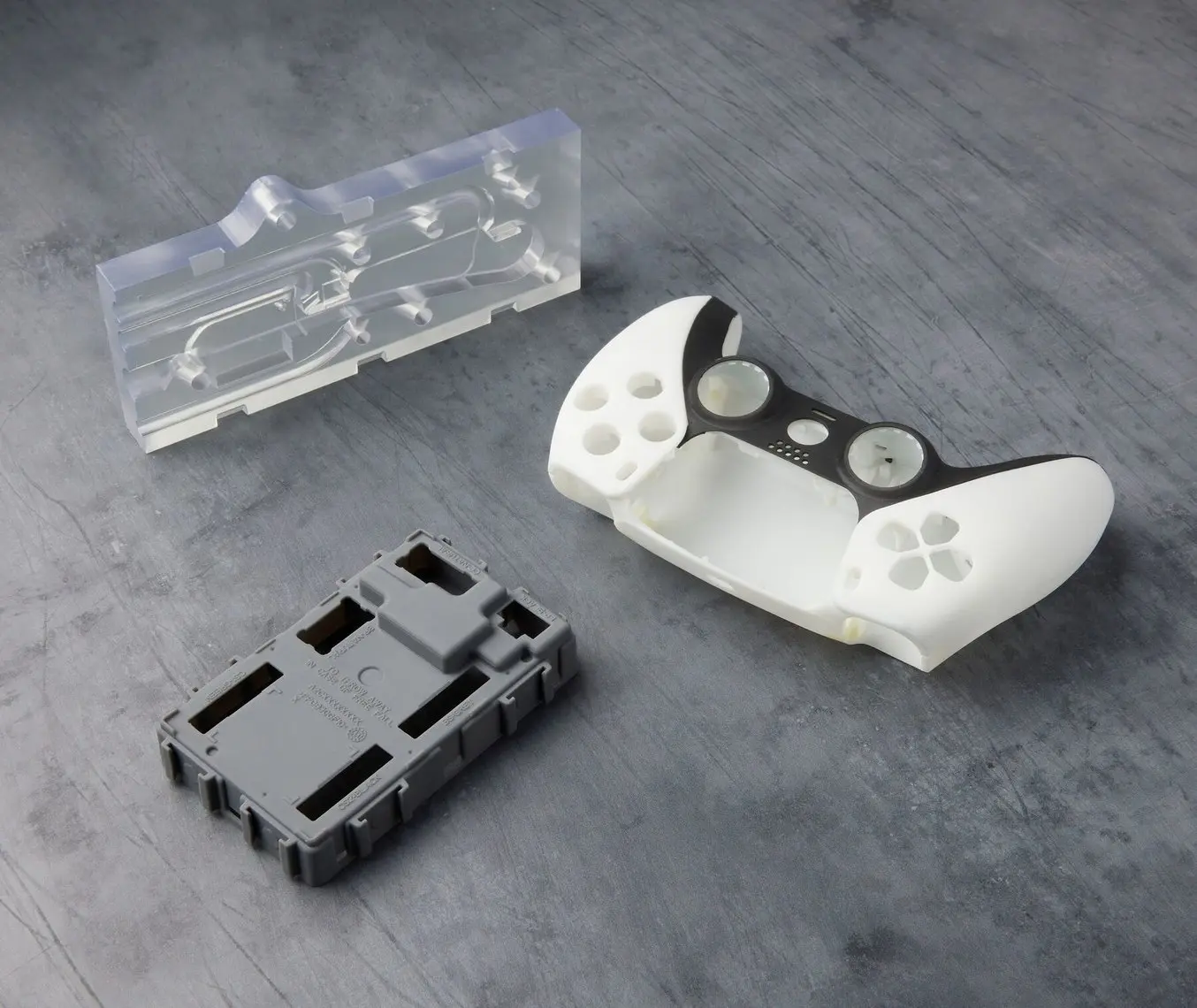
Materialleitfaden zum Form 4
Erfahren Sie mehr über alle Hochleistungsmaterialien, die auf dem Form 4 nutzbar sind, und lernen Sie, wie Sie das richtige Material für Ihre Anwendung auswählen.
So beflügelt der Form 4 die Prozesse jeglicher Branchen
Form 4 verhilft Black Diamond Equipment zu geschwindem Aufstieg
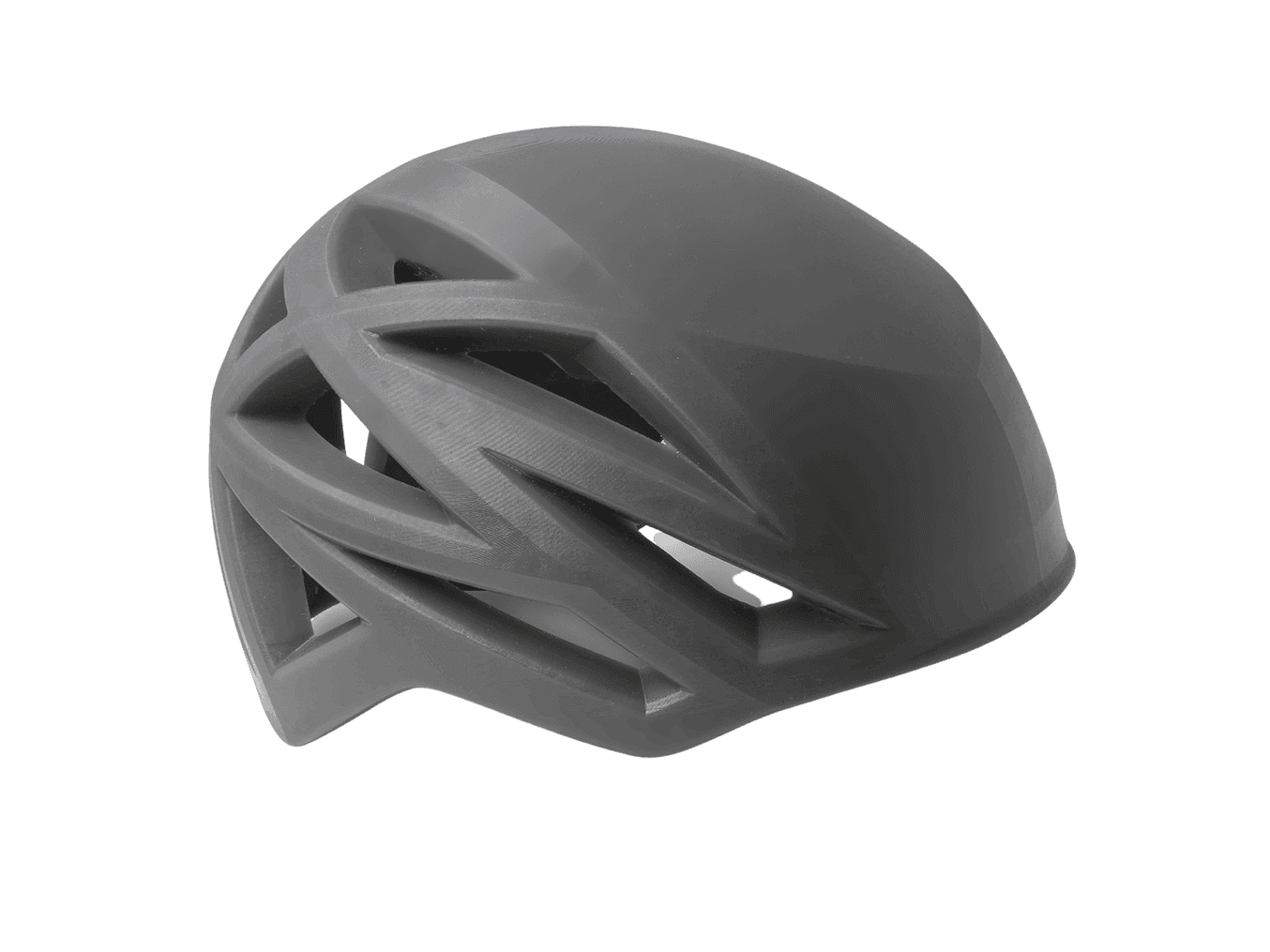
Black Diamond Equipment ist stolzer Produzent extrem hochwertiger Ausrüstung für Outdoor-Fans – und dank des Form 4 iteriert das Team heute noch gründlicher und erschafft Produkte, die ein sicheres Naturerlebnis und gesteigerte Leistung bieten.
Black Diamond Equipment stellt an sein Designteam eine einzige, unerlässliche Bedingung: uneingeschränkte, ansteckende Begeisterung für die Ausrüstung, die das Team kreiert. Matt Tetzl, Leiter des Product Design Labs, hat sich mit uns über den Designprozess des Unternehmens unterhalten und erklärt, wie der Form 4 dem Team dazu verholfen hat, mehr Zeit mit dem Testen der Produkte im Wasatch-Gebirge zu verbringen, anstatt im Labor auf die Fertigstellung von Drucken zu warten.
Effizienter Einstieg dank wohlbekanntem Formlabs-Ecosystem
Tetzl druckt schon seit Jahren täglich mit Formlabs-3D-Druckern. Dennoch kann die Integration eines neuen Druckers immer eine Herausforderung darstellen. Nicht aber beim Form 4 – schon innerhalb von 30 Minuten war das Gerät ausgepackt und der erste Druck im Gange.
„Es war größtenteils Plug-and-Play und sehr selbsterklärend. Der Drucker wirkt genauso unkompliziert wie alle anderen Formlabs-Systeme – in 99 % der Fälle kann ich mir sicher sein, einen erfolgreichen Druck zu erhalten. Und beim Rest weiß ich, dass ich das Problem selbst lösen kann und der Druck noch am selben Tag gelingen wird. Es ist toll, diese Gewissheit zu haben.“
Matt Tetzl, Prototyping Manager, Black Diamond
Während die Zuverlässigkeit die Integration des Druckers erleichtert, ist es die Geschwindigkeit, die die Ausnutzung des Kunstharz-Druckers für Black Diamond am meisten beeinflusst. Ein Projekt, nämlich ein Linsendesign für eine Kopflampe, schritt in halsbrecherischem Tempo voran – das Designteam forderte im Tagesrhythmus neue Iterationen an. Durch den Form 4 beschleunigte sich der Fortschritt noch mehr. „Wir stellten drei Iterationen an einem einzigen Tag fertig, um bis zu unserem Meeting am Nachmittag drei verschiedene Teile zu haben.“ In seiner Funktion als interner Fertigungsdienstleister für mehrere Designabteilungen gelang es Tetzl bisher, ein Lieferversprechen von 24 Stunden einzuhalten. Das konnte er jetzt sogar noch überbieten. „Der Form 4 überbrückt diese Lücke und macht die Lieferung am selben Tag zur Realität.“
Designteams sind daran gewöhnt, dass die Produktentwicklung Kompromisse erfordert: Größe gegen Packbarkeit, Leichtigkeit gegen Festigkeit. Doch der Form 4 hat den Entwicklungsprozess beschleunigt, ohne dabei die Maßgenauigkeit zu beeinträchtigen. „Wir brauchen Teile, die dem ursprünglichen CAD-Design entsprechen, sich nahtlos in Baugruppen einfügen und als mehrteilige Formen eng aufeinander passen. Die Formen aus Grey Resin V5 passen alle perfekt“, so Tetzl.
Ermüdungsprüfung und Oberflächenfinish von Grey Resin V5
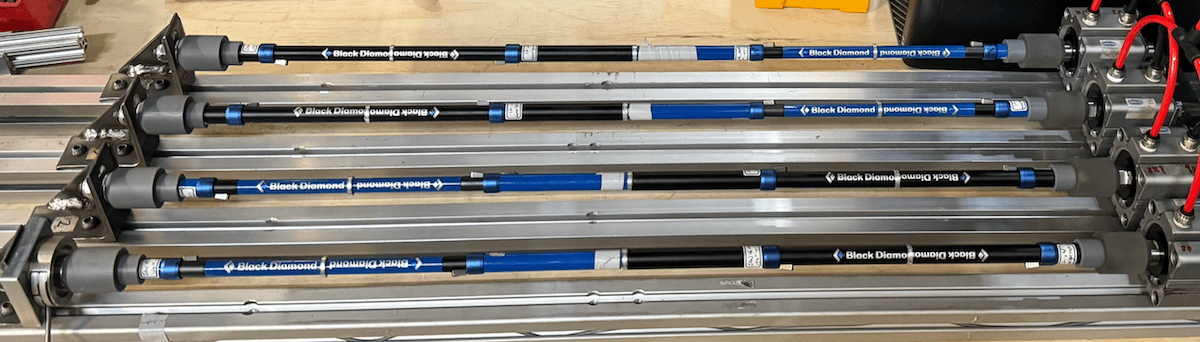
Grey Resin V5 hält erheblichen Kräften stand, selbst bei Testzyklen von 2,5 Millionen. Durch die kurzfristige Herstellung von Teilen für Validierungszyklen kann Black Diamond neue Ideen testen, ohne zu riskieren, dass Fristen überschritten werden.
Bei den Wanderstöcken von Black Diamond gehen die Ermüdungsprüfungen noch weit über das hinaus, was in anderen Unternehmen schon als grenzwertig gelten würde – doch Grey Resin V5 hielt der Herausforderung stand. Tetzl druckte aus Grey Resin V5 auf dem Form 4 eine Halterung für die Knopfbaugruppe, mit der die Teleskopfunktion des zusammenschiebbaren Wanderstocks gesteuert wird. Anschließend wurde der Stock einer simulierten Ermüdungsprüfung ausgesetzt, bei der eine spezielle Vorrichtung den Knopf mit erheblichem Kraftaufwand auf das Gehäuse wiederholte Male betätigte. Selbst nach ausgiebiger Prüfung mit beträchtlicher Belastung war Tetzl von der Robustheit der neuen Harzformulierung beeindruckt. Er berichtet: „Bei 55 Pfund pro Zyklus haben wir 2,5 Mio. Zyklen durchgeführt und keinerlei Verschleiß oder Verformung festgestellt.“
Durch die Schnelligkeit, Maßgenauigkeit und verbesserte Oberflächenqualität war Tetzl in der Lage, die wachsende Nachfrage nach SLA-Teilen seitens der Designteams von Black Diamond zu bedienen. Der Form 4 verhilft dem Team dazu, gründlicher zu iterieren, und lässt die frühere Wartezeit auf Druckteile praktisch Vergangenheit werden. Dadurch kann sich das Team schon früh auf in die Berge machen, um die Funktion der Teile zu testen – was für sie das optimale Ergebnis bedeutet.
Form 4B fördert die Medizinproduktentwicklung bei restor3d
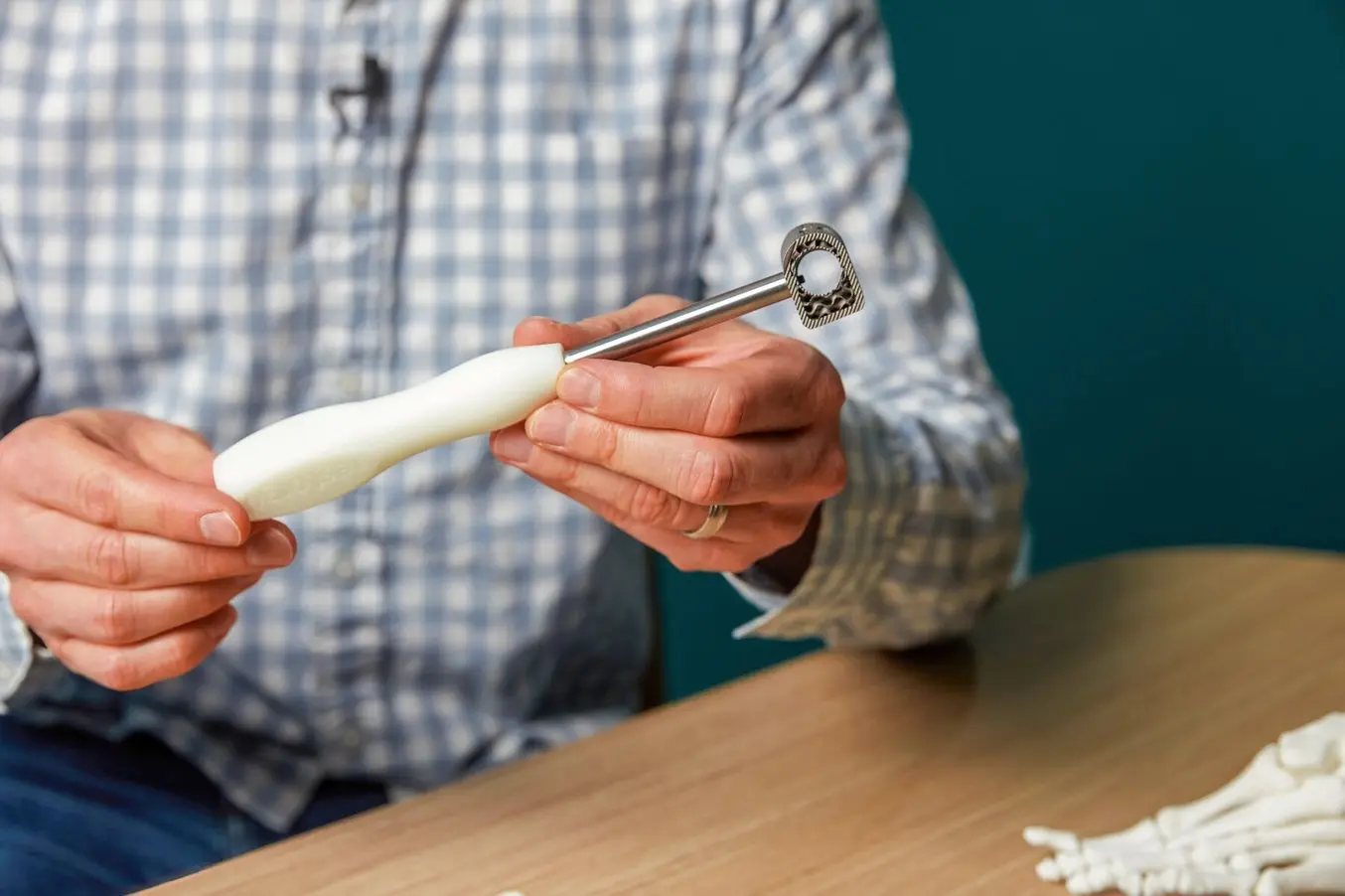
Von der Entwicklung von Medizinprodukten bis hin zu patientenspezifischen Bohrschablonen und dentalen Anwendungen unterstützt der Form 4B lebensverändernde Eingriffe durch seine Schnelligkeit und Genauigkeit.
Die Entwicklung und Herstellung von Medizinprodukten ist an strenge Qualitätskontrollen gebunden. Bei restor3d, einem führenden Unternehmen auf dem Gebiet der Medizinprodukte mit Fokus auf patientenspezifischen Lösungen unter Einsatz von additiver Fertigung, werden sowohl standardmäßige als auch patientenspezifische chirurgische Instrumente mithilfe von fortschrittlicher, polymerbasierter additiver Fertigung hergestellt. Elena Tercheria, Leiterin der additiven Fertigung, ist auf die Polymerproduktion spezialisiert, die von ihr und ihrem Team mittels 3D-Druck umgesetzt wird.
Tercherias primäre 3D-Druckerflotte besteht aus den Modellen Form 3, Form 3+ und Form 3B. Etwa 90 % der aus Polymeren gedruckten Produkte werden an diese Flotte gesendet und aus einem speziell formulierten Kunstharz gefertigt, das auch in Röntgenaufnahmen sichtbar ist. Nachdem Tercheria bereits jahrelang Erfahrungen mit dem Form 3/B/+ und Druckern anderer Hersteller gesammelt hatte, fiel ihr am Form 4B als Allererstes die Druckgeschwindigkeit auf.
„Die Steigerung der Druckgeschwindigkeit beeindruckte uns am meisten. In meinen acht Jahren Erfahrung mit additiver Fertigung habe ich noch kein SLA-Gerät so schnell drucken sehen. Bei fast jedem Druckauftrag war der Form 4B schneller.“
Elena Tercheria, Leiterin Additive Fertigung, restor3D
Bei der Zusammenarbeit mit chirurgischen Fachkräften, die sich auf eine OP vorbereiten, ist Agilität entscheidend. Im Falle eines unerwarteten Bedarfs an Ersatzteilen, zusätzlichen Exemplaren oder auch Überarbeitungen in letzter Minute „hilft uns die beschleunigte Druckzeit [des Form 4B], viel agiler auf solche Situationen zu reagieren.“ Tercheria fügt hinzu: „Wir lieben die erhöhte Genauigkeit der Zeitangabe. Zu sehen, wie der Drucker jede Schicht mischt und trotzdem eine drastische Verkürzung der Druckzeit erreicht, ist beeindruckend.“ Ursprünglich hatte das Team von restor3d nämlich erwartet, dass die häufige Harzmischung die Druckzeit negativ beeinflussen würde. Doch wie sie feststellten, wurden die Drucke „fast exakt zur angekündigten Zeit fertiggestellt. Das ist für uns eine große Sache, denn so können wir zuverlässig planen und die Verfügbarkeit der Geräte voraussehen.“
Im Hinblick auf Geschwindigkeit ist die Dauer der Nachbearbeitung einer der zentralen Faktoren, die in die Durchlaufzeit einfließen. Die Veröffentlichung des Form 4/B geht auch mit Verbesserungen des Form Wash und Form Cure einher. Tercheria meint: „Die Neuerungen am Form Wash sind toll: Das größere Laufrad bewegt das Lösungsmittel viel besser, um Reste ungehärteten Harzes von den Teilen zu entfernen. Für den neuen Form Wash gibt es von uns einen großen Daumen hoch.“
Dank der erstklassigen Oberflächenqualität ist nur minimale Nachbearbeitung erforderlich, was Zeit spart und die Produktionsgenauigkeit erhöht. Die Kunstharze für den Form 4/B wurden zur Verbesserung der Druckqualität neuformuliert. „Tatsächlich gibt es fast gar keine Schichtlinien“, so Tercheria. „Die Seitenwände sehen extrem glatt aus – fast als wären sie nicht 3D-gedruckt.“
Mit dem Form 4B ist auch der Druck von biokompatiblen Kunstharzen für die Gesundheitsbranche möglich. Angefangen von der Entwicklung von Medizinprodukten bis hin zu patientenspezifischen Bohrschablonen und dentalen Anwendungen unterstützt der Form 4B lebensverändernde Eingriffe durch seine Schnelligkeit und Genauigkeit.
Die nächste Stufe des industriellen 3D-Drucks
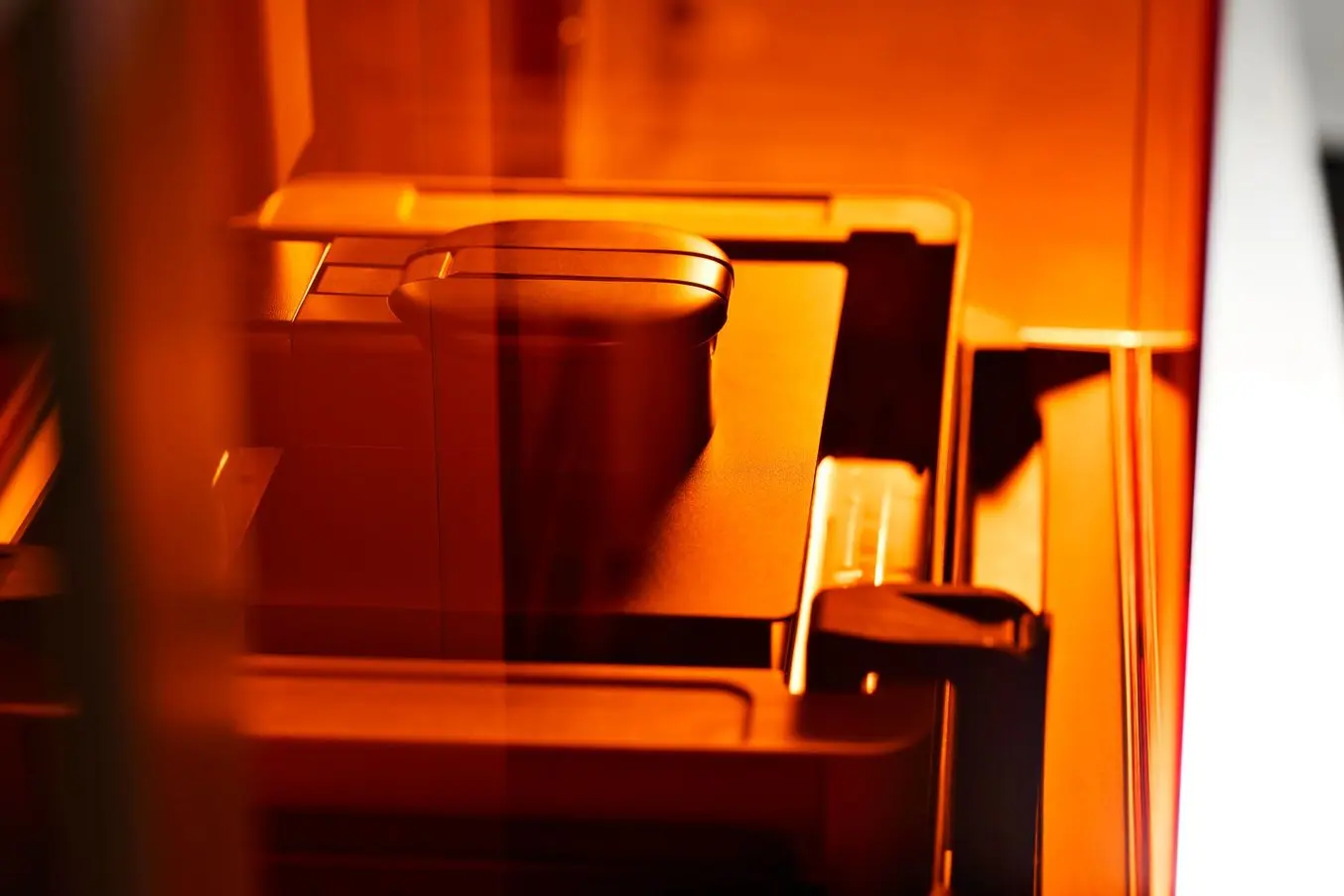
Der Form 4 und der Form 4B bilden die nächste Entwicklungsstufe im SLA-3D-Druck (Stereolithografie), basierend auf Jahren bahnbrechender Innovationen auf dem Gebiet Hardware, Software und Materialwissenschaft.
Der Form 4 setzt neue Maßstäbe für den professionellen 3D-Druck. Indem er die vielseitigste Materialbibliothek der Branche mit einem leistungsstarken neuen Drucksystem vereint, erschließt der Form 4 eine neue Stufe der Kreativität und Produktivität.
Iterieren Sie dreimal schneller, mehrmals am Tag, um jeden erdenklichen Ansatz zu erproben. Produzieren Sie einheitliche Teile in hohen Stückzahlen, ohne sich Gedanken um Ausfallzeiten oder mangelnde Zuverlässigkeit zu machen. Stemmen Sie größere Produktionsmengen und erfüllen Sie mehr Anfragen, um die Produktivität in Ihrem gesamten Unternehmen zu steigern.
Dank zwei- bis viermal schnellerer Druckgeschwindigkeiten, eines 30 % größeren Fertigungsvolumens, unvergleichlicher Zuverlässigkeit und Präzision sowie des strengsten Qualitätskontrollsystems der Branche sind Ihren Kreationen mit dem Form 4 keinerlei Grenzen gesetzt.