Leitfaden zum 3D-Druck von Polypropylen: Vergleich von Prozessen, Materialien und Anwendungen
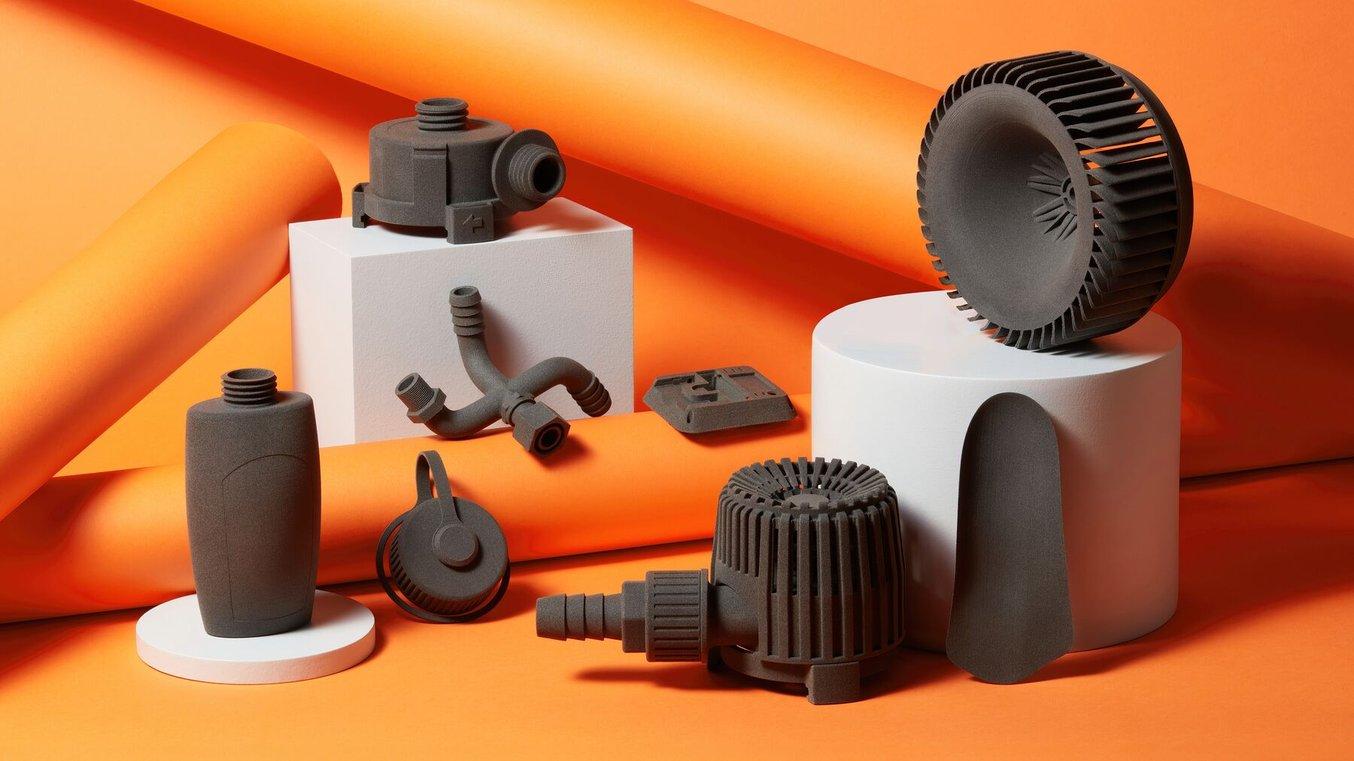
Angesichts stetiger Fortschritte in der 3D-Drucktechnologie stützen sich Designteams und Hersteller jeder Branche in allen Phasen des Design- und Fertigungsprozesses zunehmend auf 3D-gedruckte Teile. Die Möglichkeit, ein Material wie Polypropylen für den gesamten Fertigungsprozess zu verwenden, bringt enorme Vorteile mit sich: geringere Kosten und eine Verringerung des Risikos, dass Produktionswerkzeuge nachgearbeitet werden müssen, kontinuierliche Einhaltung der behördlichen Vorschriften und ein reibungslose Validierung des Arbeitsablaufs.
Materialien, die in der Branche weit verbreitet sind, aber dennoch die Vorteile des 3D-Drucks bieten, sind stark gefragt. Der Thermoplast Polypropylen ist der weltweit am zweithäufigsten hergestellte Standardkunststoff und wird im Ingenieurwesen und in der Fertigung nahezu universell und tagtäglich eingesetzt.
Polypropylen mittels 3D-Druck zu fertigen bietet Anwender*innen die Gestaltungsfreiheit, den schnellen Durchsatz und die Flexibilität der Lieferkette, die der 3D-Druck mit sich bringt, während sie sich gleichzeitig auf vertraute, standardisierte Materialeigenschaften verlassen können. In diesem Leitfaden werden gängige Anwendungen für Polypropylen sowie die Vor- und Nachteile des Erstellens von Teilen aus Polypropylen durch traditionelle Umformung sowie FDM-, SLS-, MJF- und SLA-3D-Druck behandelt.
Was ist Polypropylen?
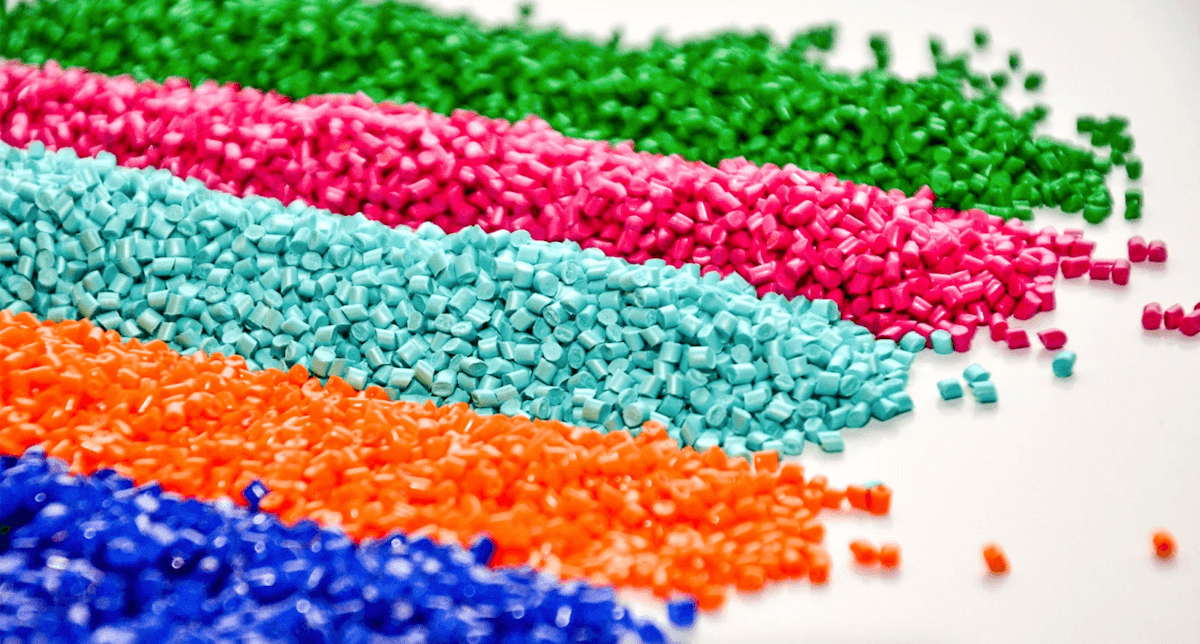
Polypropylen ist sehr farbecht, was bedeutet, dass das Färben einfach ist und das Granulat leicht mit Pigmenten gesättigt werden kann. Diese Eigenschaft macht es zu einem geeigneten Material für die Massenproduktion von Konsumgütern. (Bild: All3dp.com)
Polypropylen (PP) ist ein Polyolefin, das Polyethylen ähnlich ist. Es handelt sich um einen Thermoplast, der in der Fertigungs- und Konsumgüterbranche für die Massenproduktion gängiger Artikel wie Kunststoffflaschen verwendet wird. Polypropylen wird durch Polymerisierung eines einzelnen Propylenmonomers durch Kettenwachstum gebildet. Es ist einem anderen gängigen Kunststoff, nämlich Polyethylen, sehr ähnlich. Die beiden Materialien werden manchmal in Recyclingprozessen kombiniert, um recycelte Polyolefinfasern herzustellen. Polypropylen wurde erstmals 1951 von amerikanischen Mitarbeitern von Philips Petroleum entwickelt, doch Forschung und Entwicklung laufen bis heute weiter, und es gibt vielversprechende Forschungsarbeiten zu Materialien aus Polypropylen auf biologischer Basis sowie zu neuartigen Recyclingverfahren.
Anwendungsbereiche von Polypropylen
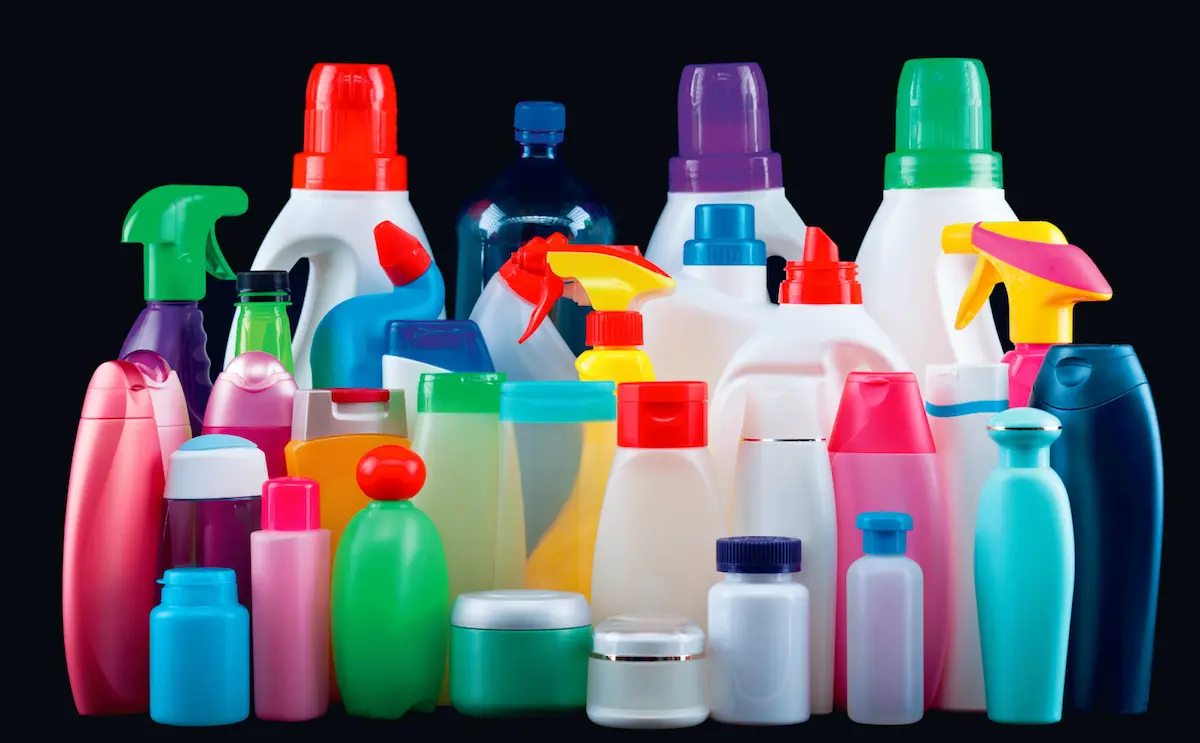
Polypropylen ist einer der am weitesten verbreiteten Massenkunststoffe der Welt. Aufgrund seiner Duktilität und seiner kostengünstigen Herstellung eignet es sich hervorragend für die Verpackung von Konsumgütern, wie z. B. Flaschen für Kosmetika, Reinigungsmittel und Arzneimittel. (Bild: Adreco Kunststoffe)
Aufgrund seiner Duktilität, seines geringen Gewichts und seiner Chemikalien- und Wasserbeständigkeit eignet sich Polypropylen ideal für Konsumgüter mit dünnen Wänden, die dennoch Festigkeit erfordern, wie z. B. Kunststoffbehälter für Lebensmittel. Am häufigsten werden aus Polypropylen Flaschen für Flüssigkeiten wie Shampoo, Motoröl, Reinigungslösungen etc. sowie Laborschläuche und -flaschen, Lebensmittel- und Arzneimittelbehälter und Medizinprodukte produziert. Eine weitere häufige Verwendung von Polypropylenmaterialien ist die Fertigung von Kunststoff-Jalousien.
Aufgrund seiner Duktilität eignet sich Polypropylen ideal für die Fertigung von Teilen mit Biegescharnieren, wie z. B. Deckel von Süßigkeitenverpackungen oder Shampooflaschen. PP ist ermüdungsbeständig und hält wiederholter Verwendung stand.
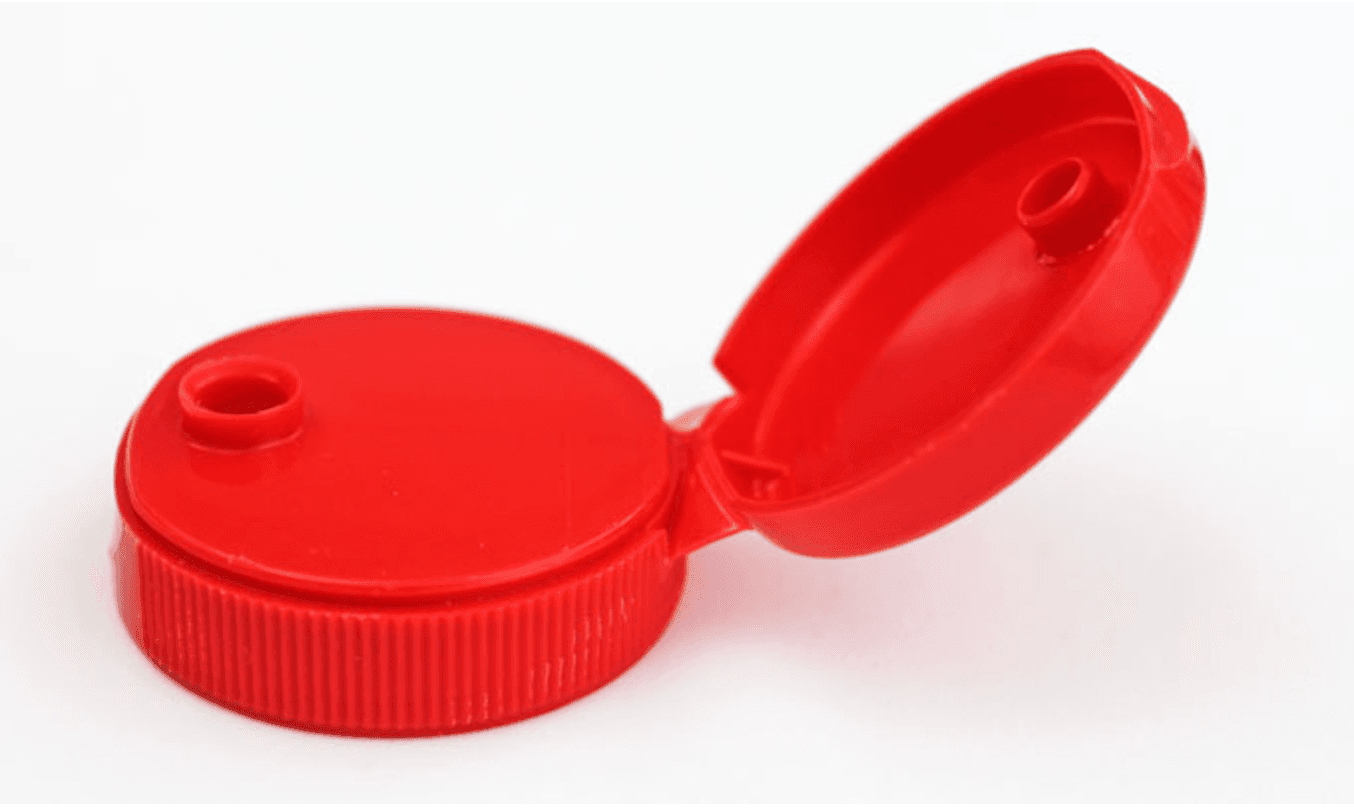
Die Duktilität von Polypropylen macht es zu einer guten Wahl für Designs wie Biegescharniere, bei denen Verbindungen wiederholt gebogen werden müssen, ohne zu reißen. (Bild: RevPart)
Materialeigenschaften von Polypropylen
Polypropylenmaterialien sind leicht, wasserdicht, chemikalienbeständig und duktil. Die Dichte von Polypropylen ist mit einer Spanne von etwa 0,895 bis 0,93 g/cm3 eine der niedrigsten unter den Kunststoffen, weshalb sich das Material gut für Anwendungen eignet, die Leichtigkeit erfordern.
Polypropylen weist eine gute Temperaturbeständigkeit sowie hydrophobe und oleophobe Eigenschaften auf, was ein Grund für seine häufige Verwendung für Lebensmittelverpackungen ist. In Kombination mit anderen Komponenten kann Polypropylen sehr belastbar sein und für technische Anwendungen verwendet werden, bei denen es zu wiederholter Druckeinwirkung oder Stößen kommt. Die Wärmeformbeständigkeitstemperatur (HDT) vieler Polypropylenmaterialien beträgt etwa 100 °C bei 0,45 MPa, was zwar nicht sehr hoch ist, aber eine große Bandbreite von Anwendungen ermöglicht.
Fertigungsmethoden für Polypropylen
Polypropylen wird am häufigsten in Gießverfahren eingesetzt, in der Regel durch Spritzgießen von geschmolzenem Polypropylen-Granulat. Platten aus Polypropylen können auch thermogeformt werden. Diese Fertigungsmethoden ergeben in der Massenproduktion extrem günstige Stückkosten und decken die überwiegende Mehrheit der aus Polypropylen produzierten Teile ab.
Herkömmliche Massenproduktionsverfahren haben jedoch einige schwerwiegende Nachteile, wie z. B. die hohen Vorlaufkosten für die Fertigung von Produktionswerkzeugen und das damit verbundene Risiko der Obsoleszenz, die Durchlaufzeiten, die Abhängigkeit von Outsourcing sowie die Einschränkungen des Produktdesigns und des Entwicklungsprozesses.
Der 3D-Druck von Polypropylen ist mit der fortgeschrittenen Entwicklung von Hardware, Software und Materialien in der 3D-Druck-Branche immer beliebter geworden. 3D-gedruckte Polypropylenteile können dieselben Materialeigenschaften aufweisen wie spritzgegossene Polypropylenteile und bieten dabei die Vorteile der additiven Fertigung: Designfreiheit, Individualisierung, Effizienz, weniger Abfall, Vermeidung von obsoletem Werkzeug und Flexibilität in der Lieferkette.
3D-Druck-Technologien für Polypropylen
Es gibt mehrere Möglichkeiten für den 3D-Druck von Polypropylenmaterialien, darunter selektives Lasersintern (SLS) oder Multi-Jet Fusion (MJF) mit Polypropylen-Pulver sowie Schmelzschichtung (Fused Deposition Modeling, FDM) mit Polypropylen-Filament. Auch für die Stereolithografie (SLA) sind Polypropylen-ähnliche Materialien verfügbar, die die Materialeigenschaften von Polypropylen genau simulieren können.
Selektives Lasersintern (SLS) | Multi-Jet Fusion (MJF) | Schmelzschichtung (FDM) | Stereolithografie (SLA) | |
---|---|---|---|---|
Auflösung | ★★★★☆ | ★★★★☆ | ★★★☆☆ | ★★★★★ |
Genauigkeit | ★★★★★ | ★★★★★ | ★★★★☆ | ★★★★★ |
Oberflächengüte | ★★★★☆ | ★★★★☆ | ★★☆☆☆ | ★★★★★ |
Durchsatz | ★★★★★ | ★★★★★ | ★★★☆☆ | ★★★★☆ |
Komplexe Designs | ★★★★★ | ★★★★★ | ★★★☆☆ | ★★★★★ |
Benutzerfreundlichkeit | ★★★★☆ | ★★★☆☆ | ★★★★★ | ★★★★★ |
Materialeigenschaften | ★★★★★ | ★★★★★ | ★★★☆☆ | ★★★☆☆ |
Verfügbare Materialien | Polypropylene, nylon | Polypropylene, nylon | Polypropylene, nylon | Polypropylen-ähnliche Materialien: Tough 1500 Resin, Durable Resin |
Kosten | Industrielle SLS-3D-Drucker im Benchtop-Format beginnen bei unter 30 000 € für den Drucker und 60 000 € für das komplette Ecosystem, einschließlich Pulververwaltungs- und Reinigungsstationen. Konventionelle industrielle SLS-Drucker beginnen bei etwa 200 000 €. | Ab 350 000 €. | Kostengünstige Drucker, die PP drucken können, beginnen bei 1000 €, Mittelklasse-Drucker bei 3500 € und industrielle Systeme ab 15 000 €. | Professionelle SLA-3D-Drucker kosten etwa 2500 € bis 10 000 € und großformatige Kunstharz-3D-Drucker etwa 5000 € bis 25 000 €. |
Vorteile | Hochwertige Teile Designfreiheit Keine Stützstrukturen erforderlich Hoher Durchsatz Vereinfachter Arbeitsablauf Geringer Platzbedarf Geringe Wartung | Großes Bauvolumen Hochwertige Teile Designfreiheit Keine Stützstrukturen erforderlich Hoher Durchsatz | Kostengünstige Geräte und Materialien für Verbraucher Schnelle Option für einfache, kleine Teile Große Auswahl an Farben | Erschwinglich Qualitativ hochwertige Teile Designfreiheit |
Nachteile | Mäßiges Bauvolumen | Teure Geräte Großer Platzbedarf Anforderungen an die Infrastruktur Personal zur Bedienung erforderlich | Geringe Genauigkeit Geringere Druckteilqualität Anisotrop Eingeschränkte Designfreiheit Stützstrukturen erforderlich | Kein echtes Polypropylen |
Anwendungen | Funktionsfähige Prototypen Kleinserienfertigung, Übergangsfertigung oder kundenindividuelle Fertigung | Funktionsfähige Prototypen Kleinserienfertigung, Übergangsfertigung oder kundenindividuelle Fertigung | Kostengünstige schnelle Prototypenfertigung Einfache Konzeptmodelle | Funktionsfähige Prototypen |

So wählen Sie die richtige 3D-Drucktechnologie
Brauchen Sie Hilfe bei der Wahl des richtigen Kunststoff-3D-Druckers für Ihre Bedürfnisse? In diesem Videoleitfaden vergleichen wir die FDM-, SLA- und SLS-Technologien in Bezug auf häufige Kaufkriterien.
SLS-3D-Druck (selektives Lasersintern) mit Polypropylen
Das selektives Lasersintern (SLS) ist auf dem besten Weg, eine der beliebtesten Methoden für den 3D-Druck von langlebigen, hochwertigen Teilen für die Endverwendung zu werden. SLS-3D-Drucker verwenden einen Hochleistungslaser, um kleine Partikel aus Polymerpulver zu sintern. Da das ungesinterte Pulver das Teil beim Drucken stützt, sind keine zusätzlichen Stützstrukturen erforderlich.
Polypropylen-Pulver für SLS-3D-Drucker sind nicht bei allen Herstellern erhältlich. Daher ist es wichtig, bei der Auswahl eines SLS-3D-Druckers zu überprüfen, ob PP-Pulver als Teil der Materialbibliothek angeboten wird.
Polypropylen-Pulver für den SLS-3D-Druck
Polypropylen-Pulver ist zwar nicht das gängigste Material für den SLS-3D-Druck (sondern Nylon), aber dennoch ein sehr beliebtes Material, das von Herstellern industrieller SLS-3D-Drucker angeboten wird. Angesichts der Allgegenwärtigkeit von Polypropylen auf dem Markt der Massenkunststoffe sollten Hersteller, die Lösungen für die Fertigung von Endprodukten anbieten, dieses Material in ihrem Portfolio führen. Einige SLS-Drucker der Einstiegsklasse im Desktop- oder Benchtop-Format bieten kein Polypropylen-Pulver an, die meisten größeren industriellen Lösungen hingegen schon.
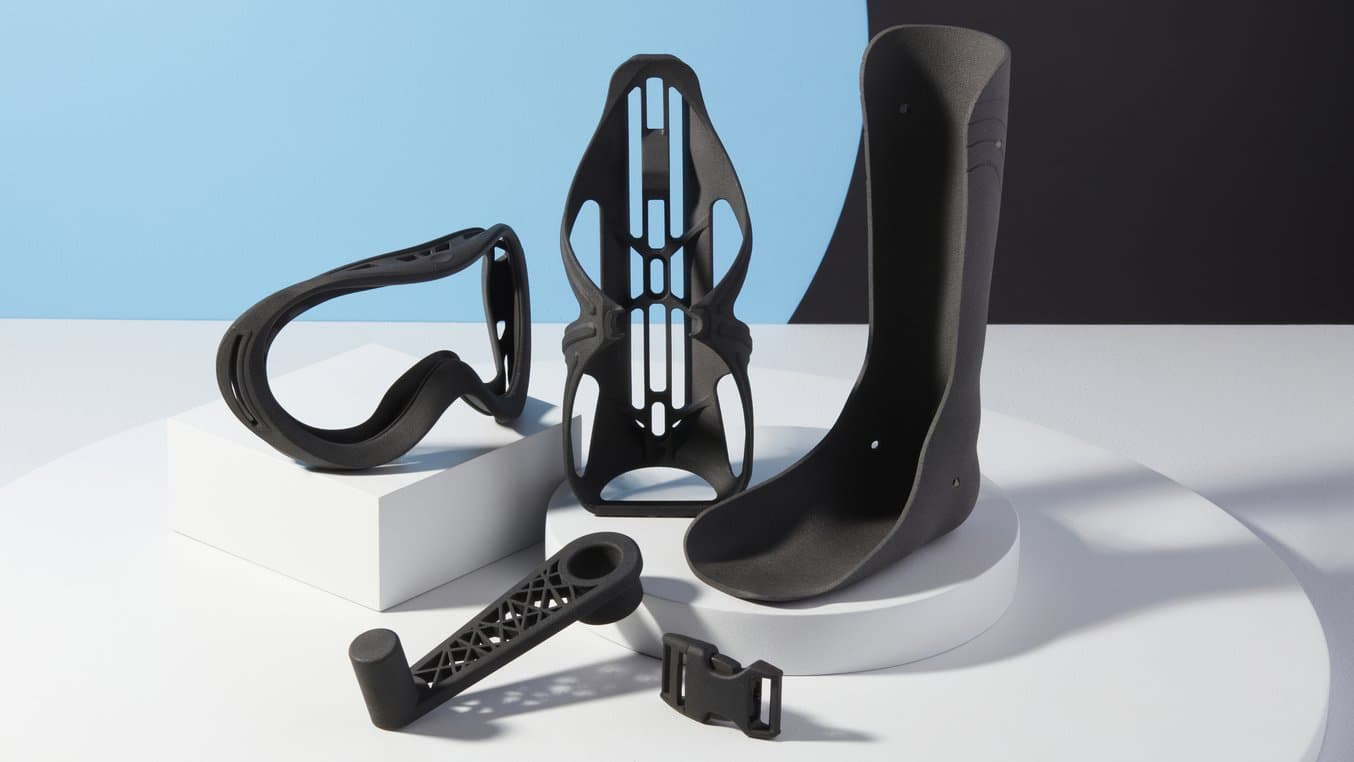
Nylon 11 Powder offers similar properties to polypropylene.
Formlabs bietet Polypropylene Powder für die SLS-3D-Drucker der Fuse-Serie und macht damit 3D-gedruckte Endverbrauchsteile aus Polypropylen mit hoher Qualität, Duktilität und Haltbarkeit zugänglich. Polypropylene Powder bietet eine Bruchdehnung von 34 % in der X/Y-Ebene und 16 % in der Z-Ebene sowie eine maximale Zugfestigkeit von 29 MPa und ist damit nahezu identisch mit spritzgegossenem Polypropylen. Von der Prototypenentwicklung bis zur Fertigung kleinerer Serien ermöglichen die Fuse-Serie und Polypropylene Powder neue Arbeitsabläufe, die kostspielige Produktionswerkzeuge überflüssig machen und die Designmöglichkeiten ausdehnen.
Dank ihrer moderaten Kosten macht die Fuse-Serie den SLS-3D-Druck von Polypropylen erschwinglich für Produktdesigner, Entwickler und Hersteller, die die Vorteile des Materials mit dem Potenzial des betriebsinternen 3D-Drucks kombinieren möchten.
Wie man Polypropylen-Teile mit SLS-Technologie druckt
Der 3D-Druck von Teilen aus Polypropylen mit der SLS-Technologie ermöglicht die Herstellung von einzelnen Prototypen oder kleinen bis mittleren Serien. Der SLS-Arbeitsablauf beinhaltet einen Arbeitsschritt vor dem Druck, um die Teile effizient im Pulverbett zu verpacken.
Packdichte und Neuzuführungsrate sind wichtige Faktoren zur Steigerung der Effizienz und zur Senkung der Kosten pro Teil. Dieser Schritt kann – insbesondere bei der Fertigung größerer Stückzahlen – durch den Einsatz eines Packalgorithmus wie dem von Formlabs' PreForm oder der NetFabb-Lösung von Autodesk vereinfacht werden. Formlabs' Polypropylene Powder hat eine Neuzuführungsrate von 50 %, was bedeutet, dass die Hälfte des Pulvers in der Konstruktionskammer recycelt sein kann. Obwohl diese Neuzuführungsrate höher ist als bei anderen SLS-Pulvern von Formlabs, wird aufgrund der geringeren Dichte von Polypropylene Powder insgesamt weniger Pulver verbraucht, was die Kosten pro Teil recht niedrig hält.
Nach Abschluss des Drucks erfolgen weitere Nachbearbeitungsschritte: das Entfernen des Pulvers und das Sandstrahlen. Einige Hersteller von SLS-Druckern bieten ein komplettes Ecosystem für diese Schritte an, andere jedoch nicht, sodass zusätzliche Geräte von Drittanbietern für den Entpulverungs- und Bestrahlungsprozess erforderlich sein können. Formlabs' Fuse Sift und Fuse Blast erleichtern die Nachbearbeitung von Polypropylen-SLS-Teilen und verbessern die Effizienz der Pulvernutzung und die Sauberkeit Ihres SLS-Druckbereichs.
Nachbearbeitungslösungen wie Vapor Smoothing, Vibrationsgleitschleifen, Keramikbeschichtung oder Färben können sowohl die Ästhetik als auch die mechanische Leistung von SLS-3D-gedruckten Teilen aus Polypropylen verbessern.
Vor- und Nachteile des SLS-3D-Drucks von Polypropylen
Mit SLS-3D-Druck produzierte Polypropylenteile sind nahezu isotrop, d. h. sie weisen unter Belastung in allen Achsen ähnliche Materialeigenschaften auf. Diese Isotropie macht es möglich, 3D-Druckteile aus Polypropylen in der Endanwendungen einzusetzen, in denen Krafteinwirkungen oder Stöße aus verschiedenen – oder unvorhergesehenen – Richtungen kommen können. FDM-3D-Drucker können keine isotropen Teile erstellen, sodass FDM-gedruckte Teile aus Polypropylen-Filament sich bei einem Aufprall entlang ihrer Schichtlinien spalten können.
Der SLS-3D-Druck von Polypropylen ist eine leistungsstarke Lösung für das Prototyping, und da Polypropylen so häufig für Konsumgüter verwendet wird, eröffnet der SLS-Druck von Polypropylen die Möglichkeit, Verbraucherprodukte neu zu konzipieren, die Iterationsschleifen zu beschleunigen und kleinen oder mittelständischen Unternehmen die Mittel an die Hand zu geben, Teile zu fertigen und auf den Markt zu bringen, ohne große Teile ihres Arbeitsablaufs auslagern zu müssen. Bei 3D-gedruckten Polypropylenteilen in Endproduktqualität ist der Design- und Fertigungsprozess straffer, effizienter und kostengünstiger.
MJF-3D-Druck mit Polypropylen
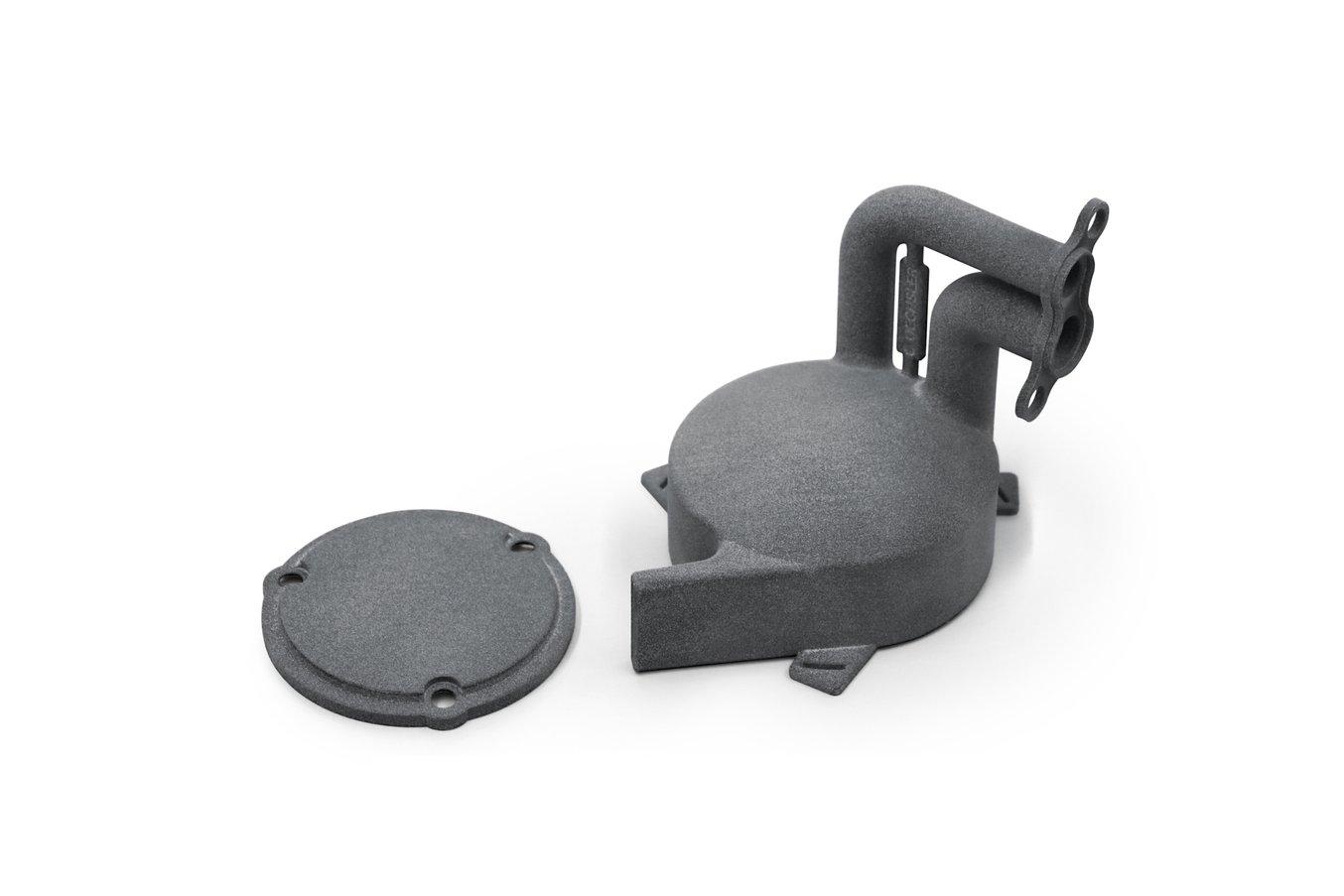
Die MJF-Drucker von HP eignen sich gut für die Fertigung von Polypropylenteilen in kleinen bis mittleren Stückzahlen. (Bild: Make Parts Fast)
Multi-Jet Fusion ist ein von Hewlett Packard (HP) patentierter und exklusiv angebotener additiver Fertigungsprozess auf Grundlage von Pulverbettfusion. MJF-3D-Drucker stellen Teile her, indem sie ein flüssiges Bindemittel auf ein Bett aus Polymerpulverpartikeln abgeben, um diese in einen halbfesten Zustand zu versetzen, bevor sie die Schicht mit einer Infrarot-Wärmequelle aushärten und die nächste Schicht beginnen.
Polypropylen-Pulver für den MJF-3D-Druck
HP bietet seit 2020 ein Polypropylen-Pulver für den MJF-3D-Druck an. MJF-Anwender profitieren von der Möglichkeit, echte Polypropylenteile zu erstellen, um eine Kontinuität in der Prototypenentwicklung und im Design zu schaffen, sodass die Materialeigenschaften von der Prototypenentwicklung bis hin zur Massenproduktion stets gleich bleiben. Das Polypropylen-Pulver von HP bietet eine Bruchdehnung von 20 % und eine maximale Zugfestigkeit von 30 MPa. Damit ähnelt es in seiner Leistung Formlabs' Polypropylene Powder für die Fuse-Serie, allerdings mit einer etwas ungünstigeren Bruchdehnung.
Wie man Polypropylen-Teile mit MJF-Technologie druckt
Nur eines der fünf MJF-Druckermodelle von HP ist mit dem PP-Pulver kompatibel, daher sollten Kunden vor dem Kauf bestätigen, dass sie das richtige Modell gewählt haben.
Das Drucken von Teilen aus Polypropylen-Pulver auf den HP-MJF-Druckern erfordert größtenteils dieselben Schritte wie der SLS-3D-Druck von Polypropylen. Da viele der MJF-Drucker größer sind als die Drucker der Fuse-Serie, sollte ein Packalgorithmus verwendet werden, um unnötige Pulververschwendung zu vermeiden. MJF-Drucker benötigen spezielle Stromkreise, große Stellflächen und häufig eigenes geschultes Personal für die Bedienung der Maschine.
Nach dem Druck werden die Teile entpulvert und sandgestrahlt und können anschließend mit einer Reihe von Optionen nachbearbeitet werden, um eine Oberflächenbeschaffenheit in Endproduktqualität zu erreichen. Mit diesen Nachbearbeitungsmethoden können Polypropylenteile von Prototypen in Endprodukten verwandelt werden.
Vor- und Nachteile des MJF-3D-Drucks von Polypropylen
MJF-3D-Druck von Polypropylen liefert Teile mit den Materialeigenschaften von spritzgegossenem Polypropylen, was entscheidend ist, um während der gesamten Design- und Produktionsphase dasselbe Material nutzen zu können. MJF-Drucker erstellen zuverlässig hochwertige Teile und können aufgrund ihrer größeren Baukammern auch für Serienproduktion eingesetzt werden.
Mit Preisen von häufig über 340 000 € sind MJF-Drucker jedoch kostspielig, wobei jährliche Serviceverträge, spezielle Infrastrukturanforderungen und hohe Materialpreise noch hinzukommen.
FDM-3D-Druck (Schmelzschichtung) mit Polypropylen
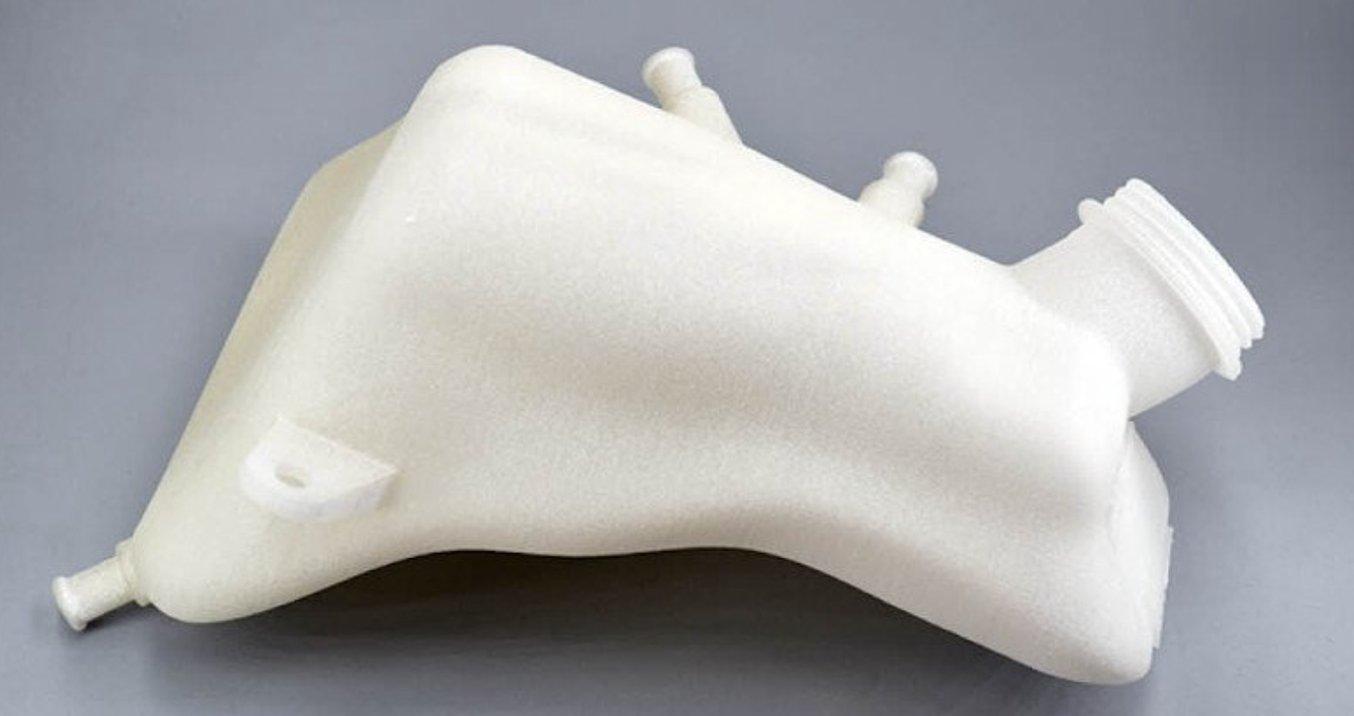
Polypropylen-Filament für den FDM-Druck eignet sich für schnelle Prototypen, wie dieses mit einem FDM-Drucker gedruckte Bauteil. (Bild: Sculpteo)
Der FDM-3D-Druck ist das bekannteste 3D-Druckverfahren, da es weit verbreitet ist und eine niedrige Einstiegshürde bietet. In diesem sogenannten „Klebepistolen-Verfahren“ schmilzt und extrudiert der FDM-Drucker Kunststoff-Filament in der Form des Teils und trägt das Material Schicht für Schicht auf. Polypropylen-Filament für den FDM-Druck wird von vielen Herstellern angeboten, aber FDM-3D-gedruckte Polypropylenteile erreichen selten die Materialeigenschaften von traditionell gefertigtem Polypropylen.
Polypropylen-Filament für den FDM-3D-Druck
Viele Hersteller bieten Polypropylen-Filamente an, die jedoch teurer sind als andere, gängigere Materialien für den FDM-3D-Druck wie ABS- oder PLA-Filamente. Aufgrund der höheren Wärmeformbeständigkeitstemperatur von Polypropylen müssen FDM-3D-Drucker im Extruder sowie in der Druckkammer eine hohe Temperatur aufrechterhalten. Daher ist es wichtig, vor der Entscheidung für einen FDM-Drucker und dem Kauf des Polypropylen-Filamentes die Kompatibilität zu prüfen.
FDM-3D-gedrucktes Polypropylen eignet sich nicht für fortgeschrittene Anwendungen wie Teile für die Endverwendung. Für solche Fälle bieten Polypropylen-Pulver für SLS- und MJF-3D-Druck erstklassige Leistungen. Kostengünstige Drucker für den Druck mit Polypropylen sind ab 1000 € erhältlich, Drucker der mittleren Preisklasse kosten etwa 3500 € und industrielle Systeme beginnen ab rund 15 000 €.
Wie man Polypropylen-Teile mit FDM-Technologie druckt
Polypropylen-Filament ist schwieriger zu drucken als standardmäßige FDM-Materialien. Es erfordert eine Extrudertemperatur von etwa 240 °C bei einer Betttemperatur von 85–120 °C. Zum Drucken von Polypropylen auf einem FDM-Drucker ist auch ein Kühlungslüfter erforderlich, da sich Polypropylen-Filament während der Kühl- oder Aushärtungsphase verziehen kann. Ein Lüfter kann helfen, dieses Risiko zu mindern, indem er die kühlere Luft gleichmäßig um das Teil herum verteilt.
Vor- und Nachteile des FDM-3D-Drucks von Polypropylen
Der FDM-3D-Druck von Polypropylen ist eine gute Methode, um in der Anfangsphase schnell und kostengünstig Prototypen oder Konzeptmodelle zu erstellen. Da viele FDM-3D-Drucker sowohl einen zugänglichen Arbeitsablauf als auch erschwingliche Preise bieten, eignet sich diese Technologie gut für Hobbyprojekte oder für erste physische Modelle im Produktdesign, vor dem Einstieg in intensivere Designphasen.
FDM-3D-gedruckte Teile sind weder isotrop nich wasserdicht. Daher können Polypropylenteile aus FDM-Druckern nicht als Flaschen, Gehäuse oder Schläuche verwendet werden – die üblichen Anwendungsfälle von Polypropylen.
SLA-3D-Druck (Stereolithografie) mit Polypropylen-ähnlichen Materialien
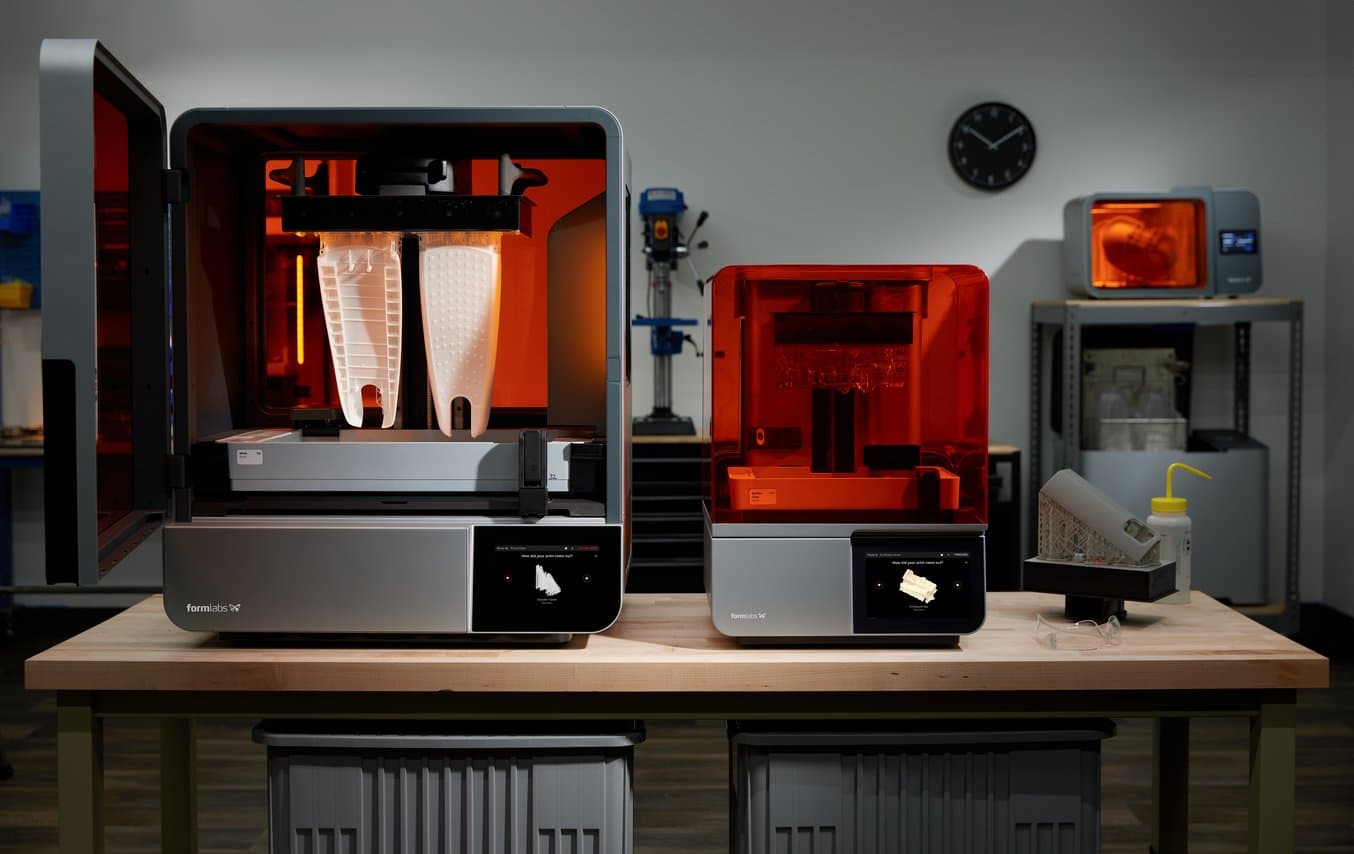
SLA-Drucker wie der Form 3+ (Mitte) und der Form 3L (rechts) sind eine hervorragende Ergänzung für SLS-Arbeitsabläufe. Der Druck mit einem Polypropylen-ähnlichen Harz wie Tough 1500 Resin ist eine schnelle Option, erste Prototypen zu fertigen, um anschließend mit dem SLS-Drucker Fuse 1+ 30W (links) und Polypropylene Powder zu Funktionstests oder größeren Chargen überzugehen.
Der Stereolithographie-3D-Druck (SLA) verwendet einen Laser oder eine andere Lichtquelle, um flüssige Kunstharze Schicht für Schicht auszuhärten, wodurch Teile entstehen, die sowohl zwischen den Schichten isotrop und chemisch sowie physisch gebunden ist. Die Hersteller von SLA-3D-Druckern produzieren ihre eigenen Materialien – für branchenübliche Materialien wie ABS, PLA oder Nylon gibt es in den SLA-Materialbibliotheken allerdings keine exakten Entsprechungen, sodass es kein „echtes“ Polypropylen-Kunstharz auf dem Markt gibt.
Viele Hersteller bieten jedoch Harze an, die fast dieselben Materialeigenschaften bieten wie Polypropylen und als adäquater Ersatz im Design und der Prototypenentwicklung dienen können, bevor die Massenfertigung von Polypropylenteilen mit traditionellen Verfahren beginnt.
Polypropylen-ähnliche Harze für den SLA-3D-Druck
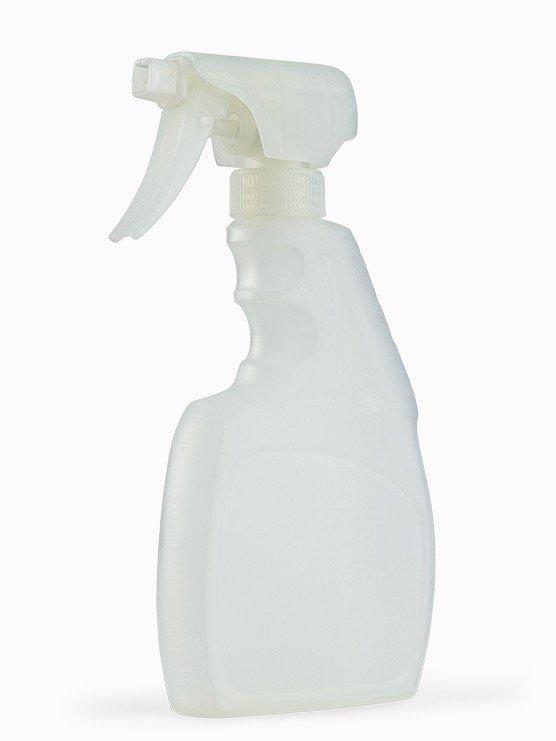
Durable Resin von Formlabs ist ein guter Ersatz für Polypropylen in der Prototypenentwicklung. Mit einer Bruchdehnung von 55 % ist Durable Resin eine gute Wahl für Verpackungen von Verbrauchsgütern, wie diese Flasche.
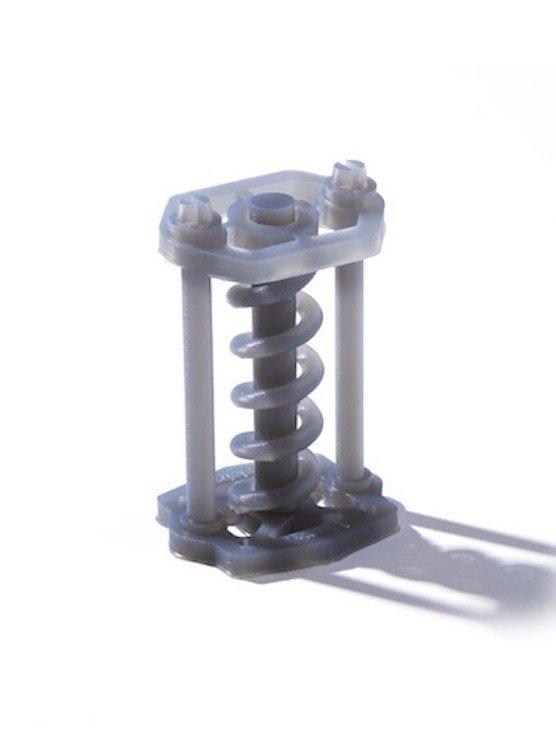
Tough 1500 Resin von Formlabs hat eine höhere Zugfestigkeit (33 MPa) als Durable Resin und ist etwas flexibler als spritzgegossenes Polypropylen.
Mehrere Kunstharze von Formlabs eignen sich ideal für die Prototypenentwicklung für Teile, die später aus Polypropylen gefertigt werden, z. B. Verpackungen für Konsumgüter. Da es viele verschiedene Arten von Polypropylen gibt, lässt es sich je nach Anwendung durch unterschiedliche Kunstharze ersetzen.
Tough 1500 Resin bietet sehr ähnliche Materialeigenschaften wie spritzgegossenes Polypropylen. Mit einer maximalen Zugfestigkeit von 33 MPa und einer Bruchdehnung von 51 % ist es etwas flexibler als spritzgegossenes Polypropylen.
Durable Resin bietet mit 55 % eine ähnliche Dehnbarkeit, aber eine geringere maximale Zugfestigkeit von 28 MPa. Es wird häufiger anstelle von Polyethylen eingesetzt.
SLA-3D-Druck von Polypropylen-ähnlichen Kunstharzen
Der Arbeitsablauf für das Drucken von Polypropylen-ähnlichen Materialien mit SLA-3D-Druck hängt vom Druckerhersteller ab. Die Arbeitsabläufe und Kosten der Drucker erstrecken sich von preiswert und unkompliziert bis hin zu komplexen und kostspielig. Formlabs' SLA-Drucker des Typs Form 3+ sind preiswert, mit Preisen ab rund 2500 €, und der Arbeitsablauf ist intuitiv und sauber.
Nachdem Sie sich für ein Kunstharz zur Simulation von Polypropylen entschieden haben, setzen Sie die Harzkartusche in den Drucker ein und starten Sie den Druck. Nach dem Druck müssen die Teile gewaschen und – bei Verwendung von Tough 1500 Resin oder Durable Resin – nachgehärtet werden. Diese beiden Schritte können mit den Nachbearbeitungslösungen von Formlabs – Form Wash oder Form Wash L und Form Cure oder Form Cure L – rationalisiert werden.
Vor- und Nachteile des SLA-3D-Drucks mit Polypropylen-ähnlichen Harzen
Der SLA-3D-Druck mit PP-ähnlichen Materialien ist ideal für hochwertige funktionsfähige Prototypen von Teilen, die in der Regel aus Polypropylen hergestellt werden. Für Kunden, die bereits SLA-Drucker nutzen, ist die Verwendung von Tough 1500 Resin oder Durable Resin eine einfache und kostengünstige Möglichkeit, vergleichbare mechanische Leistungen zu erzielen wie mit Polypropylen. Der Wechsel zwischen den Materialien ist einfach und erfordert keinen Reinigungsschritt.
Der größte Nachteil des Drucks mit diesen Kunstharzen besteht darin, dass es sich nicht um echte Polypropylen-Materialien handelt, sodass die Kontinuität zwischen Prototyping und Fertigung etwas eingeschränkt ist.
Erste Schritte für den 3D-Druck mit Polypropylen
Es stehen immer Lösungen für den 3D-Druck mit Polypropylen zur Verfügung, da die Hersteller von SLS-, MJF-, FDM- und SLA-Druckern eine wachsende Auswahl an Polypropylen-Filamenten und -Pulvern auf den Markt bringen, wie auch Harze, die den Eigenschaften von Polypropylen nahekommen.
Um mit dem 3D-Druck von Teilen aus Polypropylen zu beginnen, sollten Sie zunächst überlegen, welche Funktionen Sie für Ihren individuellen Arbeitsablauf benötigen und welche Ansprüche Sie an einen 3D-Drucker stellen. Für die schnelle und kostengünstige Prototypenentwicklung im Frühstadium ist Polypropylen-Filament für den FDM-3D-Druck möglicherweise die effizienteste Option. Für funktionsfähige Prototypen höherer Qualität ist der SLA-Druck mit einem Harz wie Tough 1500 Resin oder Durable Resin eine gute Möglichkeit, viele der Vorteile von Polypropylen zu nutzen. Für echte, wasserdichte Polypropylenteile, die Funktionstests und Endverwendung standhalten, sind SLS- und MJF-3D-Druck die beste Wahl.
Das SLS-Ecosystem der Fuse-Serie ermöglicht das Erstellen von Teilen aus Polypropylen in Industriequalität. Erfahren Sie mehr über Polypropylene Powder und das SLS-Ecosystem der Fuse-Serie. Haben Sie Fragen zur richtigen Lösung? Kontaktieren Sie gern unser Expertenteam.