Wie Rosenberger mit 3D-gedruckten Hilfsmitteln und Endverbrauchsteilen die traditionelle Fertigung und Lieferzeiten optimiert
Die 1958 im bayerischen Fridolfing gegründete Rosenberger-Gruppe ist ein weltweit führender Hersteller von Hochfrequenz-, Faseroptik- und Hochvolt-Verbindungslösungen. Mehr als 14 200 Mitarbeiter sind bei Rosenberger weltweit für die Entwicklung, die Fertigung und den Verkauf des gesamten Produktportfolios im Einsatz. Namhafte Hightech-Unternehmen aus den Bereichen Mobil- und Telekommunikation, industrieller Messtechnik, Automobil-, Medizin- und Industrie-Elektronik, Datentechnik sowie Luft- und Raumfahrttechnik setzen auf die Präzision, Qualität und Zuverlässigkeit der Steckverbinder und Kabelassemblies von Rosenberger.
Schon immer war Rosenberger darauf bedacht, seine vielseitige Produktion zu optimieren, und installierte 2017 die ersten Formlabs-3D-Drucker im Werkzeugbau in der Firmenzentrale in Fridolfing. Seitdem wurde die Druckerflotte immer weiter skaliert und auf weitere Standorte übertragen, denn der 3D-Druck schrieb schnell Erfolgsgeschichten.
So werden Betriebsmittel und Halterungen kostengünstig 3D-gedruckt, die vorher aus Metall gefertigt wurden, der Bau von Prototypen für alle Unternehmensbereiche ermöglicht, Fertigungsanlagen optimiert und die Fertigung von Ersatzteilen beschleunigt. Heute stehen den Betriebsmittelkonstrukteur*innen neben traditionellen Produktionsanlagen wie CNC-Fräsen sieben SLA-Drucker (Stereolithographie) und drei SLS-Drucker (selektives Lasersintern) von Formlabs zur Verfügung, um die Arbeit des Teams zu unterstützen.
Wir haben mit Betriebsmittelkonstrukteur Manuel Kapsreiter darüber gesprochen, wie der 3D-Druck bei Rosenberger zur Erfolgsgeschichte wurde, Innovativität fördert, die Herstellung von Ersatzteilen beschleunigt und Fertigungsprozesse optimiert.
Innovation trifft Tradition – Bewusstsein schaffen für 3D-Druck
Während Kapsreiter 3D-Druck bei Rosenberger heute stolz als erfolgreiches Innovationsprojekt beschreiben kann, waren seine Kolleg*innen noch skeptisch, als der erste Formlabs-SLA-Drucker in die Fridolfinger Werkstatt einzog. Denn als renommiertes Industrieunternehmen legt Rosenberger Wert auf höchste Qualität seiner Produkte und setzt hierfür seit mehr als 60 Jahren auf den Einsatz traditioneller Fertigungsverfahren. 3D-Druck kannten die meisten Mitarbeitenden hingegen lediglich als FDM (Fused Deposition Modelling, auf Deutsch Schmelzschichtung) und verbanden damit (zurecht) geringe Druckgenauigkeit, raue Oberflächenbeschaffenheit und Anisotropie. Für Kapsreiters Team im Werkzeugbau bestand die Herausforderung darin, das erfahrene Kollegium von den Vorteilen, Einsatzgebieten und der Qualität der 3D-Drucktechnologien SLA und SLS zu überzeugen.
„Zunächst wurde 3D-Druck bei uns von vielen als Spielzeug belächelt, das gegen Maschinen wie Fräsen nicht mithalten könne. Viele haben bei 3D-Druck den FDM-Druck im Kopf, und das hat sie abgeschreckt. Da musste man dann auch Überzeugungsarbeit leisten, dass SLA oder SLS nicht mit FDM vergleichbar ist. [...] Wenn Teile eine gute Oberfläche haben sollen, dann ist SLA wirklich eine gute Option. Aus dem richtigen Material gedruckt und gut in PreForm ausgerichtet, können die SLA-gedruckten Teile auch mit einem Spritzgussteil mithalten. Dann braucht man sich wirklich nicht verstecken, wenn man die Teile auf einer Messe herzeigt”, sagt Manuel Kapsreiter
Überzeugt von Nutzen und Druckqualität des Form 3+ und Fuse 1+ 30W wird das Werkzeugbau-Team nicht müde, unternehmensintern für 3D-Druck zu werben. Hierfür haben die Kolleg*innen Videos erstellt, die die Prozesse rund um den SLA- und SLS-Druck darstellen (siehe Artikelbeginn und weiter unten). Damit möchte das Team bei den allein in Fridolfing mehr als 3100 Mitarbeitenden mehr Bewusstsein für 3D-Druck schaffen und sie motivieren, eigene innovative Ideen zu Produkten oder Betriebsmitteln kostengünstig und schnell mit 3D-Druck in die Tat umzusetzen.
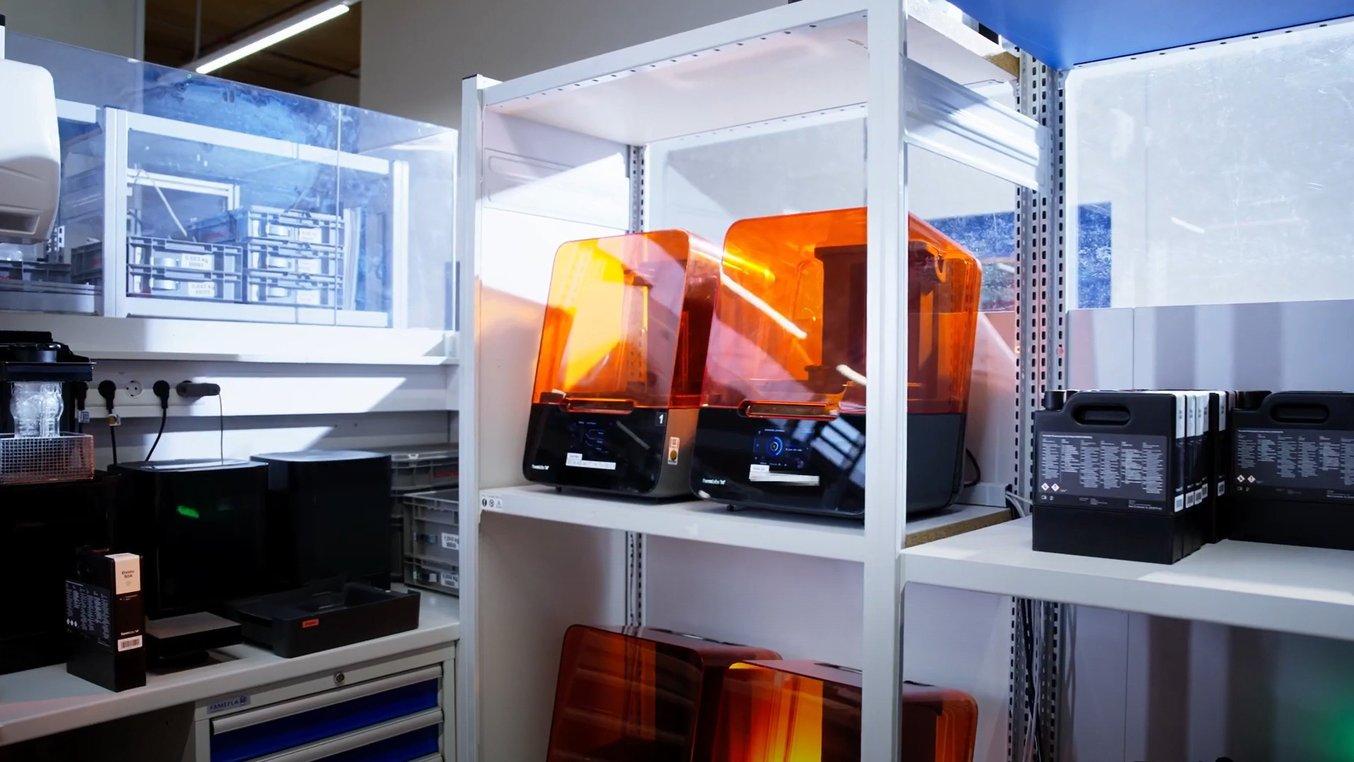
Die Drucker vom Typ Form 3+ sind beim Traditionsunternehmen Rosenberger nahezu ununterbrochen im Einsatz für die Fertigung von Werkzeugen, Prototypen, Ersatzteilen und Fertigungshilfsmitteln.
Wie erfolgreich die Aufklärungsarbeit war, zeigt sich heute an der stetig wachsenden Anzahl an Druckaufträgen aus sämtlichen Unternehmens- und Fertigungsbereichen. Heute laufen die 3D-Drucker bei Rosenberger im Dauerbetrieb zur Herstellung von Prototypen, Werkzeugen, Ersatzteilen und Fertigungs- oder Montagehilfsmitteln.
Bei Kollegen, aber auch allgemein in der Industrie, ist mittlerweile die Erkenntnis gewachsen, dass wir mit 3D-Druck schneller und agiler sein können als mit Zerspanung, um Lösungen für Probleme zu entwickeln.
Manuel Kapsreiter, Betriebsmittelkonstrukteur, Rosenberger
Wie Rosenbergers industrielle Fertigung von 3D-Druck profitiert
Verringerte Produktionsausfallkosten – mit 3D-gedruckten Ersatzteilen Stillstandszeiten verkürzen
Zur Produktion der vielfältigen Produkte Rosenbergers sind vielfältige Maschinen gefordert, deren Instandhaltung und Optimierung den Werkzeugbau vor ebenso vielfältige und spontane Herausforderungen stellt. Denn die hochgradig spezifischen Ersatzteile können nur auf Anfrage produziert werden. Das ständige Ziel für das Team ist daher, unterschiedlichste Ersatzteile schnellstmöglich bereitzustellen, um optimale und reibungslose Produktion zu garantieren.
Das Problem bestand darin, dass für die aufwendige Herstellung und Lieferung der meist metallenen Ersatzteile lange Wartezeiten notwendig waren. Mit der Flotte von Formlabs-3D-Druckern kann Rosenberger heute in kürzester Zeit provisorische Ersatzteile drucken, um diese Wartezeiten zu überbrücken.
Gegenüber dem Fräsen erhalten wir Teile durch 3D-Druck 80 % schneller und können über Nacht auf Anforderungen reagieren.
Manuel Kapsreiter, Betriebsmittelkonstrukteur, Rosenberger
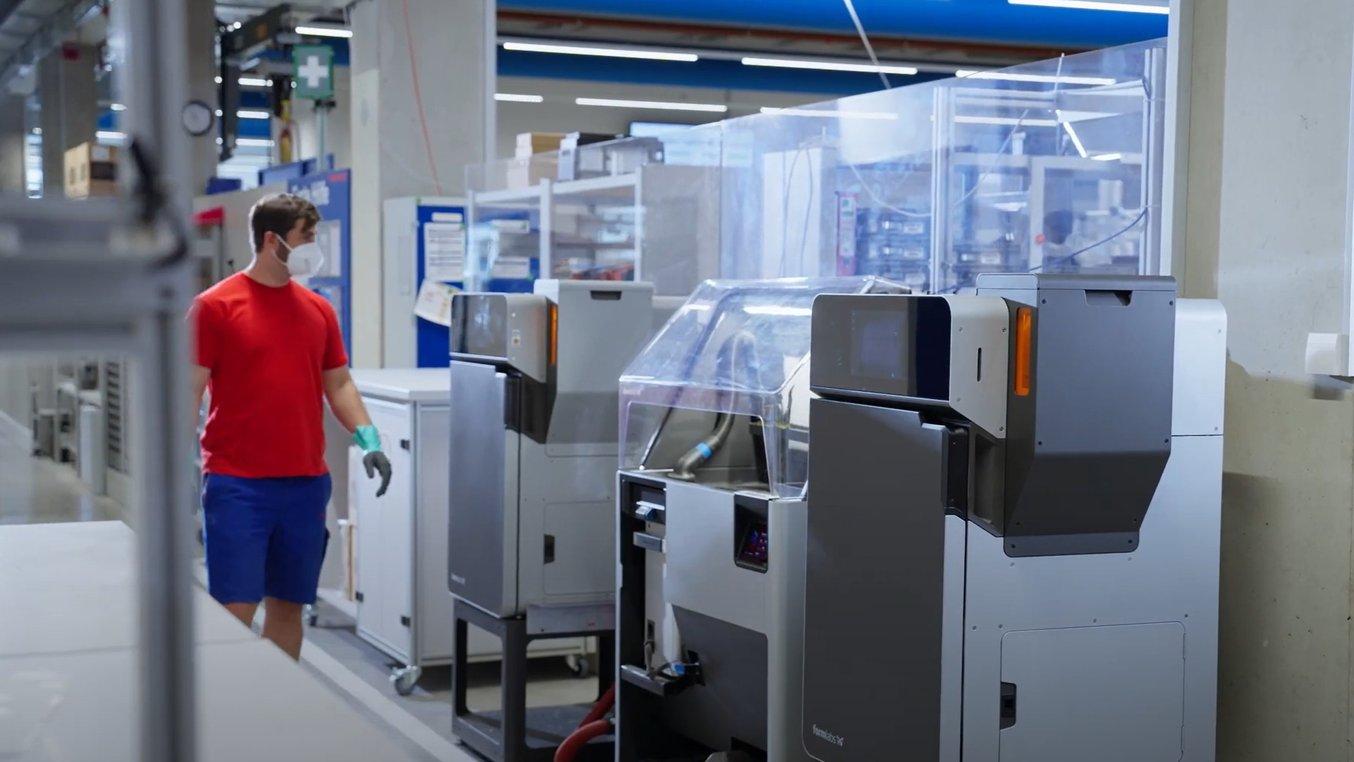
Mit professionellen SLS-Teilen in Industriequalität werden bei Rosenberger Ersatzteile gefertigt.
Reduzierte Kosten für Hilfsmittel – mit günstigem 3D-Druck Metallteile in der Fertigung ersetzen
Um Herstellungskosten von Teilen zu reduzieren, greift Rosenbergers Werkzeugbau zunehmend auf Formlabs-3D-Drucker zurück und ersetzt teure Betriebsmittel aus Metall – wie beispielsweise Alu-Winkel – durch günstige Kunststoffteile.
Kapsreiter freut sich, dass seine Kolleg*innen 3D-Druck zunehmend als kostengünstige Alternative ihrer Betriebsmittelkonstruktionen wahrnehmen, sodass immer „weniger Teile aus Stahl oder Ähnlichem hergestellt, sondern einfach kostengünstig gedruckt werden.”
Gesteigerte Fertigungseffizienz – mit komplexen 3D-gedruckten Einzelstücken Anlagen optimieren
Das zunehmende Umdenken auf 3D-Druck zeigt sich auch in der steigenden Zahl von Druckaufträgen, die der Werkzeugbau aus den verschiedenen Fertigungsbereichen erhält. Seit der Implementation von 3D-Druck konnte das Unternehmen nicht nur Metallteile ersetzen, sondern auch gänzlich neue Betriebsmittel konstruieren, mit denen Durchsatz und Effizienz der Anlagen gesteigert werden.
Additive Fertigung eröffnet gegenüber traditionellen Verfahren gänzlich neue Anwendungsfelder im Bereich der Betriebsmittel- und Prototypenerstellung. Dank der Designfreiheit des 3D-Drucks können bestehende Produktionsanlagen mit sonst unvorstellbaren Teilen optimiert werden, wie der Anwendungsfall aus dem Video zum SLA-Druck bei Rosenberger zeigt.
Angefangen hat alles mit der Erkenntnis eines Fertigungsmitarbeiters, dass die Optimierung der Reinigungsleistung einer automatischen Waschstraße die Effizienz der Produktion steigern würde. Er wandte sich daher an den Werkzeugbau, der eine Waschkugel konzipierte, um den Wasserfluss gezielter zu leiten. In mehreren Iterationen optimierte das Team seinen Prototyp durch Variation von Bohrdurchmesser und Anstellwinkel. „Heute ist die Kugel serienreif und wird, weil es eine relativ große Maschine ist, 40 Mal gedruckt und eingebaut, um die komplette Anlage zu verbessern”, berichtet Kapsreiter. Die Herstellung der Waschkugel wäre aufgrund der komplexen Geometrie mit traditionellen Verfahren kaum umsetzbar.
Die Kugel ist innen hohl, hat Bohrungen in sämtliche Richtungen und Winkel. Das ist eine Geometrie, die anders nicht herstellbar ist. Ohne 3D-Druck wäre es viel aufwendiger, viel komplizierter zu fertigen und nicht so gut im Ergebnis.
Manuel Kapsreiter, Betriebsmittelkonstrukteur, Rosenberger
Ohne additive Fertigung müssten die Konstrukteure auf komplexe Gussverfahren oder das Fräsen mehrerer Teile zurückgreifen, die in einem weiteren Schritt umständlich zusammengesetzt würden. Diese teuren Verfahren können sie sich heute sparen. Mit dem Form 3+ wird die Herstellung schneller, kostengünstiger und erfordert weniger manuelle Schritte, denn die transparente Kugel wird in einem Stück gedruckt. Nur für die abschließenden Bohrungen setzt das Team CNC-Fräsen ein, was dank der hohen Zähigkeit, Steifigkeit und Festigkeit von Clear Resin problemlos möglich ist.
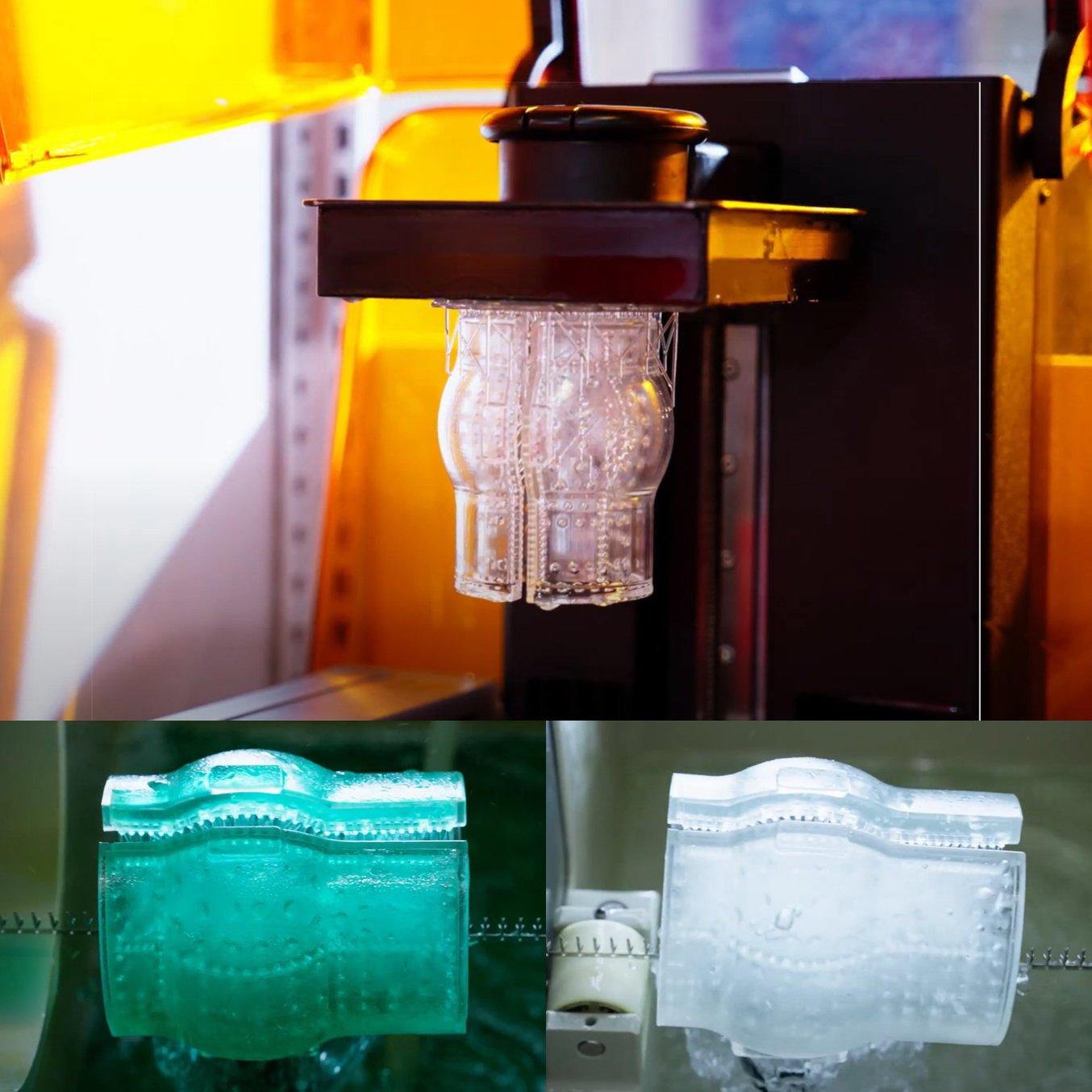
Mit dem Form 3+ druckt Rosenbergers Werkzeugbau Teile mit komplexen Geometrien wie diese Waschkugel aus Clear Resin, die mit traditionellen Verfahren nur aufwändig und teuer herstellbar wären.
Durch die Vermeidung von Fräs-, Guss- und Dreharbeiten reduziert Rosenberger nicht nur die Herstellungskosten und -dauer der gedruckten Teile, sondern optimiert dadurch auch den Betrieb der traditionellen Maschinen. Denn mit jedem Prozess, der auf 3D-Druck ausgelagert wird, werden „Kapazitäten teurerer Fertigungsmaschinen gespart, die man daher für spezialisierte Anwendungen, die durch 3D-Druck nicht herstellbar sind, einsetzen kann und eine optimalere Auslastung und Nutzung von dem vorhandenen Equipment erreicht”, erklärt Kapsreiter.
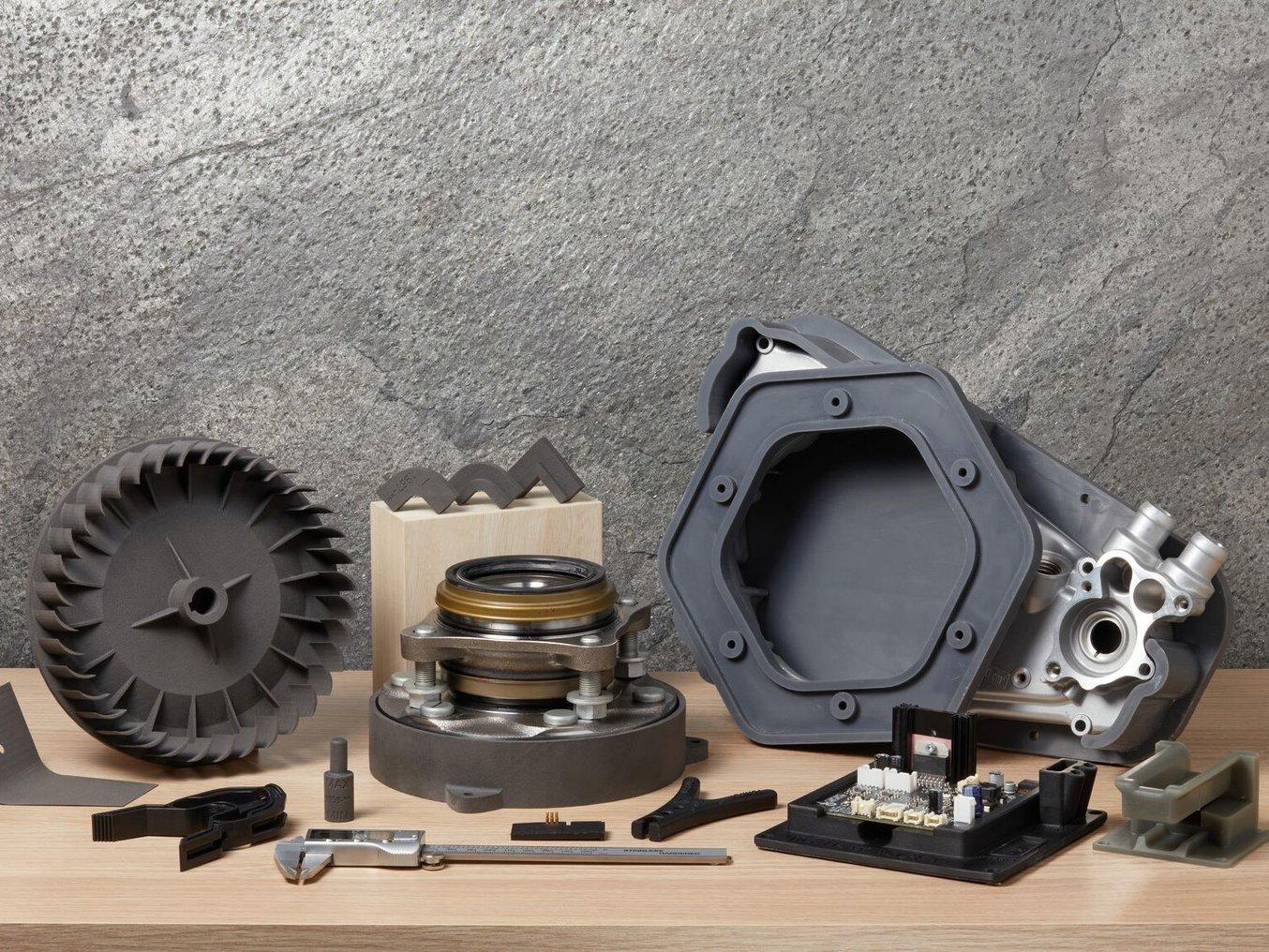
Wie Sie Halterungen, Vorrichtungen und sonstige Fertigungshilfen betriebsintern 3D-drucken
Dieses Whitepaper gibt einen Überblick über die Grundlagen der betriebsinternen Herstellung effektiver Halterungen, Vorrichtungen und sonstiger Fertigungshilfsmittel.
Die positiven Rückmeldungen aus den Fertigungsabteilungen bestärken das Team in der Entscheidung, die Druckerflotte im Werkzeugbau weiter auszubauen. Denn jedes abgeschlossene Projekt inspiriert weitere Ideen zu Prozessoptimierungen, die sie mit 3D-Druck umsetzen.
„Der Kollege, der die Waschkugel angefragt hat, ist absolut begeistert. Er hat jetzt auch schon mehrere andere Projekte angestoßen, wo er das Potenzial sieht, mit 3D-gedruckten Komponenten Aufgaben besser erledigen zu können", sagt Kapsreiter.
Erhöhter Durchsatz – kostengünstige 3D-Druck-Serienproduktion
Dank des hohen Durchsatzes, der niedrigen Arbeitskosten durch die geringe Zahl notwendiger manueller Arbeitsschritte und der abfallarmen Produktion mit kostengünstigen Materialien wie Nylon 12 Powder eignet sich der SLS-Druck mit dem Fuse 1+ 30W zur Produktion größerer Stückzahlen. So konnte Rosenberger Werkzeugbau einen weiteren Kollegen dabei unterstützen, eine automatische Waschstraße, die bislang nur kleine Stückzahlen gleichzeitig reinigte, zu optimieren und damit auch hier die Produktion effizienter zu gestalten. Als Lösung entwickelte der Kollege ein Trägersystem, mit dem größere Chargen, auf einer Edelstahlplatte platziert, in das Ultraschallbad getaucht werden können. Für die Befestigung der Platte konstruierte und druckte das Team 8500 Clips aus Nylon 12 Powder. „Da ist unser Fuse 1[+ 30W] fünf Wochen durchgelaufen”, erinnert sich Kapsreiter. Mithilfe des hohen Durchsatzes des SLS-Drucks konnte sie den Durchsatz der automatischen Waschstraße steigern.
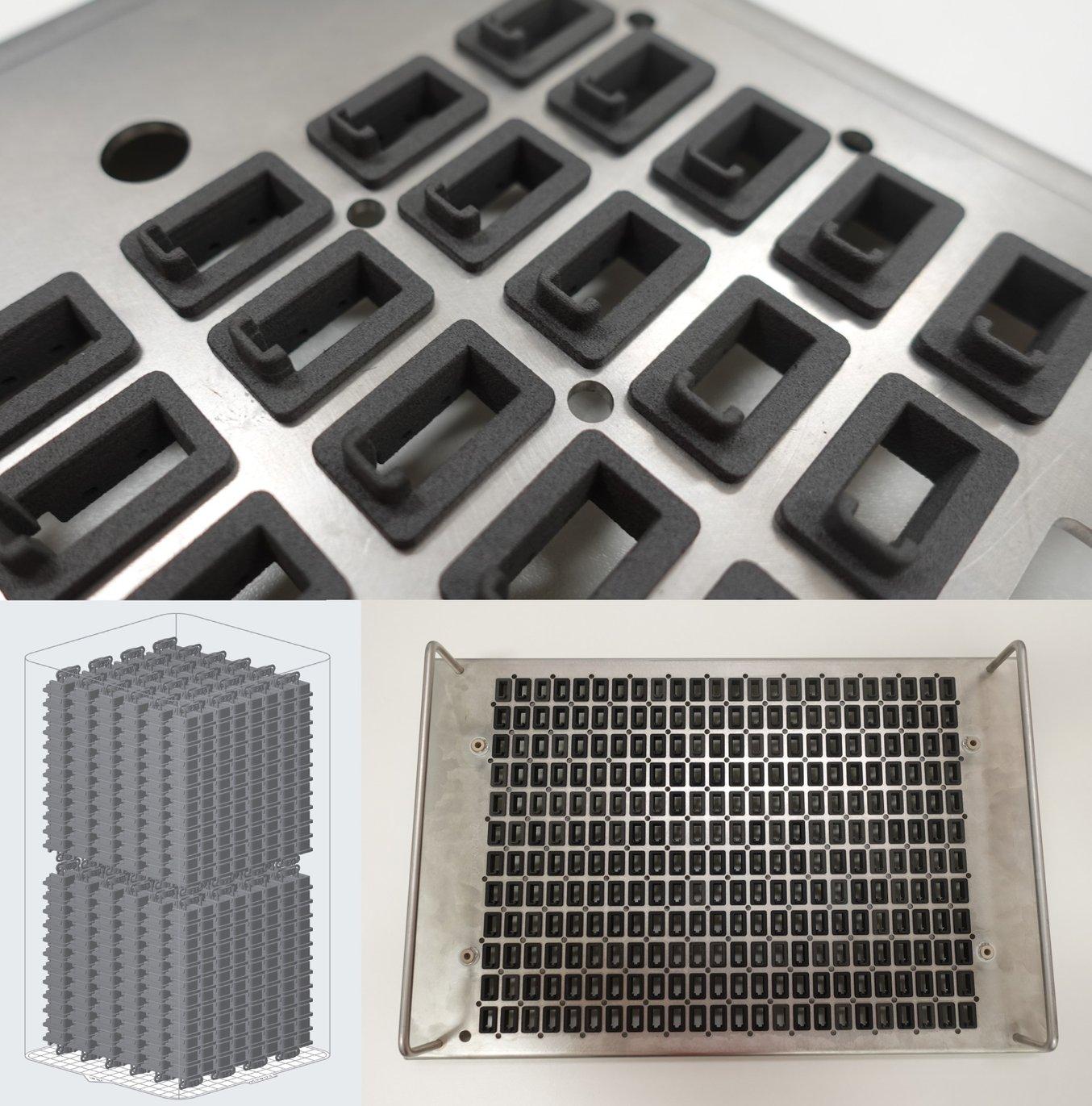
Der große Bauraum und der hohe Durchsatz des Fuse 1+ 30W ermöglicht Rosenberger die kostengünstige Produktion von SLS-Teilen in Großserie, wie beispielsweise diese Clips aus Nylon 12 Powder für den Einsatz in einer Waschstraße.
Insbesondere im Zusammenspiel mit dem Fuse Sift eignet sich der Fuse 1+ 30W für Produktionen großer Serien mit geringem Aufwand und niedrigem Stückpreis. Im 7,5 l fassenden Bauraum des Fuse 1+ 30W finden mehrere Teile gleichzeitig Platz, denn SLS-Druck erfordert keine Stützstrukturen, wodurch zusätzlich Material und manuelle Bearbeitung gespart werden kann. Mit dem Fuse Sift befreit Rosenbergers Werkzeugbau die Druckteile von ungesintertem Pulver, von dem 60 % wiederverwertet werden. Seit kurzem setzt das Team zusätzlich eine vollautomatische Sandstrahlanlage ein – ähnlich dem neu veröffentlichten, innovativen Fuse Blast von Formlabs –, mit der es Chargen gedruckter Teile geschlossen reinigt und so die Produktion großer Stückzahlen weiter beschleunigt.
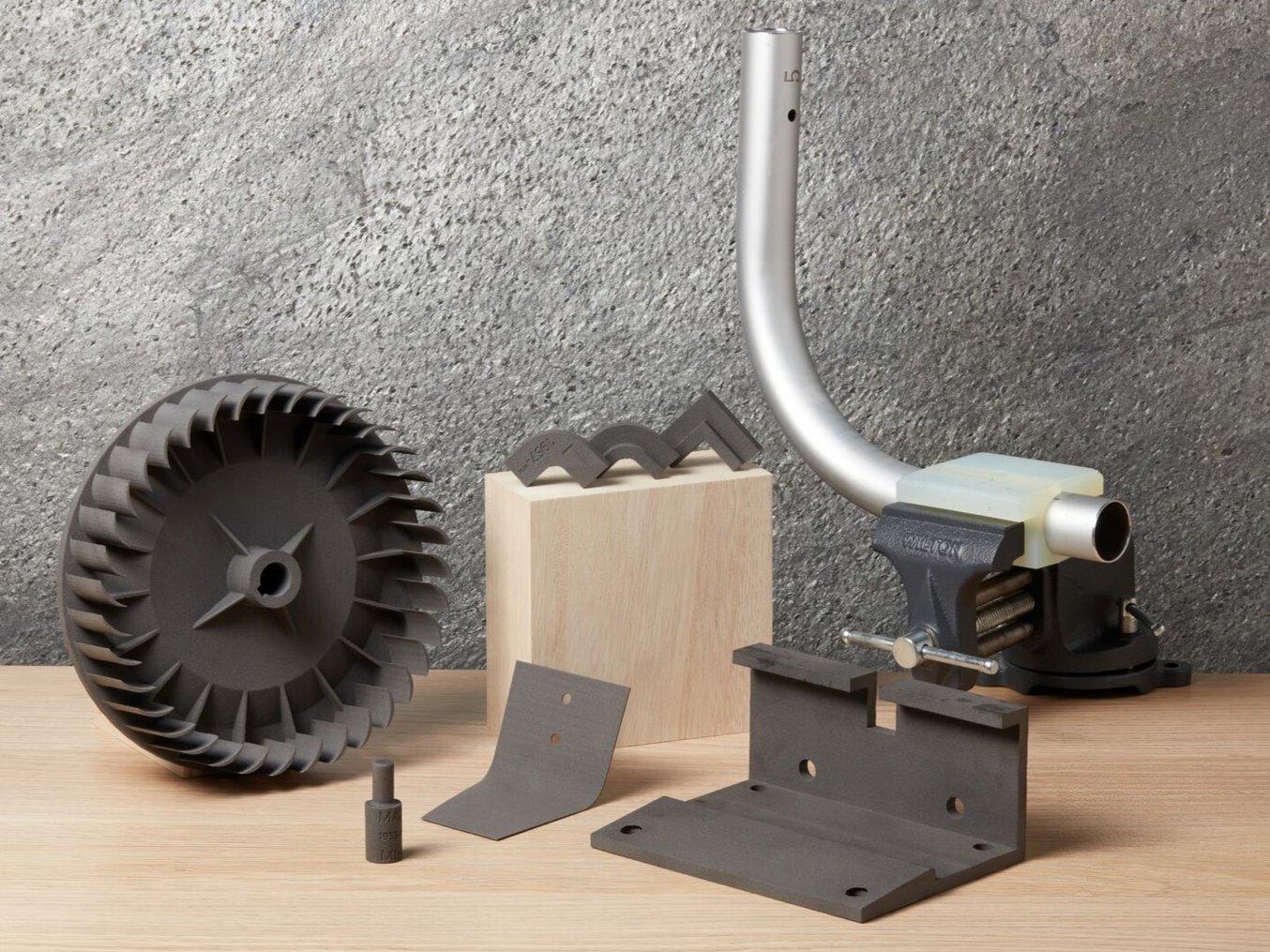
Steigern Sie Ihre Fertigungseffizienz mit 3D-gedruckten Vorrichtungen
Lernen Sie in diesem Webinar, wie Sie maßgeschneiderte Vorrichtungen und Werkzeuge mittels 3D-Druck herstellen können, um Ihre Fertigungsprozesse zu optimieren, Produktionskosten zu senken und Lieferengpässe zu vermeiden.
Gesteigerte Innovativität – Innovationsgeist zum Anfassen mit Rapid Prototyping
Früher konnte Rosenberger für die Herstellung von Prototypen lediglich auf das Spritzgussverfahren zurückgreifen. Doch hohe Fixkosten, die zur Vorbereitung neuer Spritzgusswerkzeuge notwendig sind, ließen Mitarbeitende zumeist von der Erstellung kleiner Stückzahlen von Sichtmustern absehen. Durch 3D-Druck konnte der Werkzeugbau die Kosten und Herstellungszeit für Prototypen drastisch reduzieren.
Wichtiger als die Kostenreduktion an sich ist für Kapsreiter jedoch, dass Kolleg*innen nun überhaupt auf Prototypen für ihre Entwicklungsprojekte zurückgreifen. Beispielsweise bei der Akquise und Bearbeitung von Kundenprojekten unterstützen 3D-gedruckte Prototypen Rosenbergers Mitarbeitende, um Vertrauen in deren Entwicklung zu erzeugen.
„Früher sind Musterwerkzeuge gemacht worden, um ganz kleine Stückzahlen per Spritzguss herzustellen. Mit 3D-Druck können wir auf teure Metallwerkzeuge verzichten, wodurch das Prototyping wesentlich günstiger wird. Das Tolle ist, dass man jetzt auch Musterteile herstellt über 3D-Druck, die vorher nicht gemacht worden wären. So können wir Kunden den Entwicklungsstand zeigen – nicht nur am Computer, sondern auch mal physisch was herzeigen. Man kann sich das im CAD schon anschauen und auch versuchen zu simulieren, aber wenn man das Teil physisch in der Hand hat und am Einsatzort hinhält, bekommt man ein ganz anderes Gefühl dafür”, erklärt Kapsreiter.
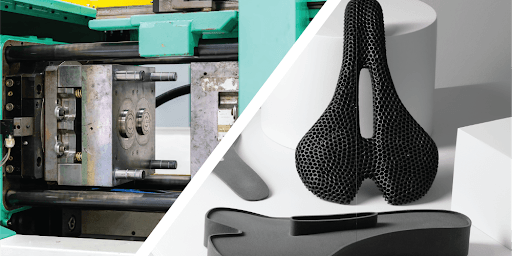
SLS-3D-Druck oder Spritzguss: Wann sollte man Spritzgussteile durch 3D-Druck ersetzen?
In diesem Whitepaper werden der Spritzguss und seine Vor- und Nachteile erörtert sowie der SLS-3D-Druck und die Anwendungen vorgestellt, bei denen er als ergänzende Technologie eingesetzt werden kann.
Neben der Arbeit mit Kund*innen sind Prototypen unternehmensintern für die Erforschung innovativer Ideen wertvoll. Seit seiner Gründung verfolgt Formlabs die Mission, 3D-Druck durch geringe Kosten und einfache Bedienung so zugänglich wie möglich zu machen. Auch für Rosenberger liegt gerade in dieser Zugänglichkeit die außerordentliche Stärke additiver Fertigung, die alle Kolleg*innen einlädt, ihre Idee zu verfolgen, und den internen Innovationsgeist fördert. Mit frühzeitigen Funktionstests und der Möglichkeit schneller Iterationen beschleunigen die gedruckten Prototypen Entwicklungsprojekte bei Rosenberger.
Der große Vorteil von 3D-Druck ist die Zugänglichkeit. Dass man schnell zu einem physischen Artikel kommt und das eben bei geringem Stückpreis, hat die Hemmschwelle, Neues auszuprobieren, stark gesenkt. Weil es so billig ist, kann man auch mal einen Fehler machen, daraus lernen und beim nächsten Versuch wieder etwas verbessern. Und das ist eine große Stärke von 3D-Druck.
Manuel Kapsreiter, Betriebsmittelkonstrukteur, Rosenberger
Die Implementation additiver Fertigung fördert so eine anhaltende Innovationsdynamik – auch in Traditionsunternehmen wie Rosenberger mit langer Erfahrung im Umgang mit konventionellen Verfahren.
Verlässliche Lösung für einzigartige Herausforderungen – der optimale 3D-Drucker für Rosenberger
Die besondere Herausforderung für das Team in Rosenbergers Werkzeugbau ist, dass es ständig einzigartige und dringend benötigte Teile produzieren muss, die wiederum die Vorbereitung individueller Druckaufträge erfordern. Unbedingt vermeiden wollte es, dass die Bearbeitung seiner Aufträge durch komplexe Abläufe oder mangelhafte Druckergebnisse verlangsamt wird. Durch die einfache Bedienung von PreForm und der Formlabs-Drucker können die Konstrukteure ihren zeitlichen Aufwand minimieren. Hinsichtlich der Prozesssicherheit sind sie vom Form 3+ vollkommen begeistert, der hinsichtlich seiner Verlässlichkeit konkurrenzlos ist. So werden Mehraufwände aufgrund gescheiterter Drucke verhindert.
Wichtig für uns war immer eine gewisse Maßhaltigkeit, dass die Materialien belastbar sind, gute mechanische Eigenschaften vorweisen können sowie Prozesssicherheit. [...] Der Form 3 ist sehr prozesssicher – das ist kein Vergleich zu anderen Systemen. Da wir eine sehr große Vielfalt an Teilen haben, die wir fast nie zweimal drucken, ist es für uns immer wichtig, dass der Aufwand pro Druck relativ gering ist. Und das waren genau die Argumente für das Formlabs-System.
Manuel Kapsreiter, Betriebsmittelkonstrukteur, Rosenberger
Als Querschnittsabteilung muss Rosenbergers Werkzeugbau Teile nicht nur schnell produzieren, sondern auch für eine Vielzahl verschiedener Bereiche mit verschiedenen Anforderungsprofilen. Die Anforderungen an Druckqualität, -präzision und Materialeigenschaften sind hoch, damit Drucke in der professionellen Produktion von Rosenberger eingesetzt werden können. Für die Arbeit des Teams ist es daher unbedingt notwendig, auf ein breites Portfolio an Materialien zurückgreifen zu können. Ein wesentliches Argument für 3D-Drucker von Formlabs war für Kapsreiter daher „auch die breite Masse an Materialien, die zur Verfügung stehen und mit denen wir viele verschiedene Anwendungsfälle abdecken können”.
Die Entscheidung zwischen SLA und SLS basieren die Konstrukteure auf dem notwendigen Fertigungsvolumen und den erforderlichen Materialeigenschaften der zu druckenden Teile. So nutzen sie den Form 3+ vor allem, wenn glatte Oberflächen und ein hoher Detailgrad erforderlich sind. Bei größeren Bauteilen, großen Chargen oder wenn spritzgussähnliche Teile hergestellt werden sollen, bevorzugt das Team den großen Bauraum und die kostengünstigen, thermoplastischen Druckmaterialien des Fuse 1+ 30W. Besonders häufig benutzt Rosenbergers Werkzeugbau folgende Materialien:
-
Tough 2000 Resin, aufgrund der hohen Ähnlichkeit zu ABS, Stabilität und Bruchfestigkeit beispielsweise für Gehäusemuster mit Rastnasen oder Montagehalter
-
Rigid 4000 Resin, aufgrund der hohen Stabilität und Steifigkeit beispielsweise für Stempel für Kniehebelpressen in der Montage
-
Rigid 10K Resin, aufgrund sehr hoher Stabilität, sehr hoher Steifigkeit und Hitzebeständigkeit beispielsweise für verschleißfeste Teile wie Gleitplatten
-
Grey Resin, aufgrund des geringen Preises für Prototypen
-
Flexible 80A Resin, aufgrund der Biegsamkeit beispielsweise für wasserdichte Dichtungen für Stecker, Gehäuse und Werkzeuge sowie Robotergreifeinheiten
-
ESD Resin, aufgrund des tiefen Schwarztons für Anschauungsmaterial
-
High Temp Resin, aufgrund der sehr hohen Hitzebeständigkeit beispielsweise für Lötvorrichtungen
-
Clear Resin, aufgrund der Transparenz beispielsweise für Waschkugeln und durchsichtige Abdeckungen
-
Nylon 12 Powder, aufgrund des niedrigen Preises und großen Bauraums des Fuse 1+ 30W beispielsweise für große Bauteile oder Kleinserien
Neben Materialvielfalt, Druckqualität, Verlässlichkeit und intuitiver Bedienung waren auch die geringen Anschaffungskosten bei Rosenbergers Entscheidung für das Formlabs-Ecosystem maßgeblich.
Die Drucker [von Formlabs] sind einfach sehr günstig. Das ist natürlich auch ein Argument, wo die Konkurrenz wirklich schlucken muss.
Manuel Kapsreiter, Betriebsmittelkonstrukteur, Rosenberger
Kontinuierliche Expansion des 3D-Druck bei Rosenberger – aus Fridolfing in die Welt
Für ein internationales und traditionell gewachsenes Unternehmen wie Rosenberger steht die perfekte Organisation von Arbeitsabläufen im Mittelpunkt, um die große Zahl an Mitarbeitenden und Prozessen zu koordinieren. Angesiedelt in der Abteilung Werkzeugbau, die als „interner Dienstleister für das Thema 3D-Druck” fungiert, wird das Potenzial von additiver Fertigung einem Großteil des Unternehmens zugänglich gemacht.
Mithilfe eines selbstentwickelten Ticketing-Systems erhält Rosenbergers Werkzeugbau 3D-Druckaufträge aus sämtlichen Unternehmensbereichen. Mit Abschluss von Druck und Nachbearbeitung gehen die Teile auf die Reise – und das aktuell mitunter noch bis zu entfernten Unternehmensstandorten in Asien. Doch seit dem großen Erfolg des 3D-Drucks am Standort Fridolfing möchten auch andere Produktionsstätten nicht länger auf die Vorteile additiver Fertigung verzichten und bauen hausinterne Druckerflotten auf.
Unser Standort in Augsburg hat jetzt innerhalb von einem Jahr einen Drucker gekauft und ein paar Monate darauf schon den zweiten. Ja, die Erfolgsgeschichte aus Fridolfing, wenn man es mal so nennen darf. Das zeigt natürlich auch in den anderen Standorten die Vorteile auf, und dann sind die natürlich auch nachgezogen.
Manuel Kapsreiter, Betriebsmittelkonstrukteur, Rosenberger
Nach mittlerweile sechs Jahren positiver Erfahrungen bei Rosenberger empfiehlt Kapsreiter allen Industrieunternehmen, eventuelle Vorurteile über additive Fertigung zu überdenken, die auch sein Kollegium zu Beginn skeptisch stimmten. Denn dank der vielseitigen Anwendungsmöglichkeiten, günstigen Herstellungskosten und schnellen Produktionszeiten ist 3D-Druck eine wertvolle Erweiterung industrieller Produktionsanlagen. Durch den gezielten Einsatz additiver Fertigung können Prozesse von traditionellen Anlagen substituiert und damit die Auslastung des gesamten Maschinenparks durch Spezialisierung optimiert werden.
3D-Druck ist schlichtweg ein zusätzliches Werkzeug, mit zusätzlichen Möglichkeiten und zusätzlichen Stärken und für die allermeisten Unternehmen eine richtige Entwicklung. Die sollte man nicht vernachlässigen, sondern das Bestmögliche für sich heraussuchen. Für die meisten wird es ein Wachrütteln sein, wenn sie feststellen, was sie alles drucken und wieviel Zeit sie sparen können.
Manuel Kapsreiter, Betriebsmittelkonstrukteur, Rosenberger
Heute erhält das Team aus Rosenbergers Werkzeugbau kontinuierlich Druckaufträge. Immer mehr Mitarbeitende aus Fertigung und Montage möchten ihre Ideen zur Prozessoptimierung mit 3D-Druck umsetzen. Für Manuel Kapsreiter ist daher klar, dass 3D-Druck bei Rosenberger eine Erfolgsgeschichte ist, die er unbedingt weiterschreiben möchte. Hierfür möchte er die internen additiven Fertigungskapazitäten aufstocken, “weil die Nachfrage einfach immer weiter steigt”.
Um diese wachsende Zahl an Anfragen umsetzen zu können, plant Rosenberger die 3D-Druckproduktion zukünftig mit Automatisierung beispielsweise durch Form Auto und Flottenmanagement zu optimieren.