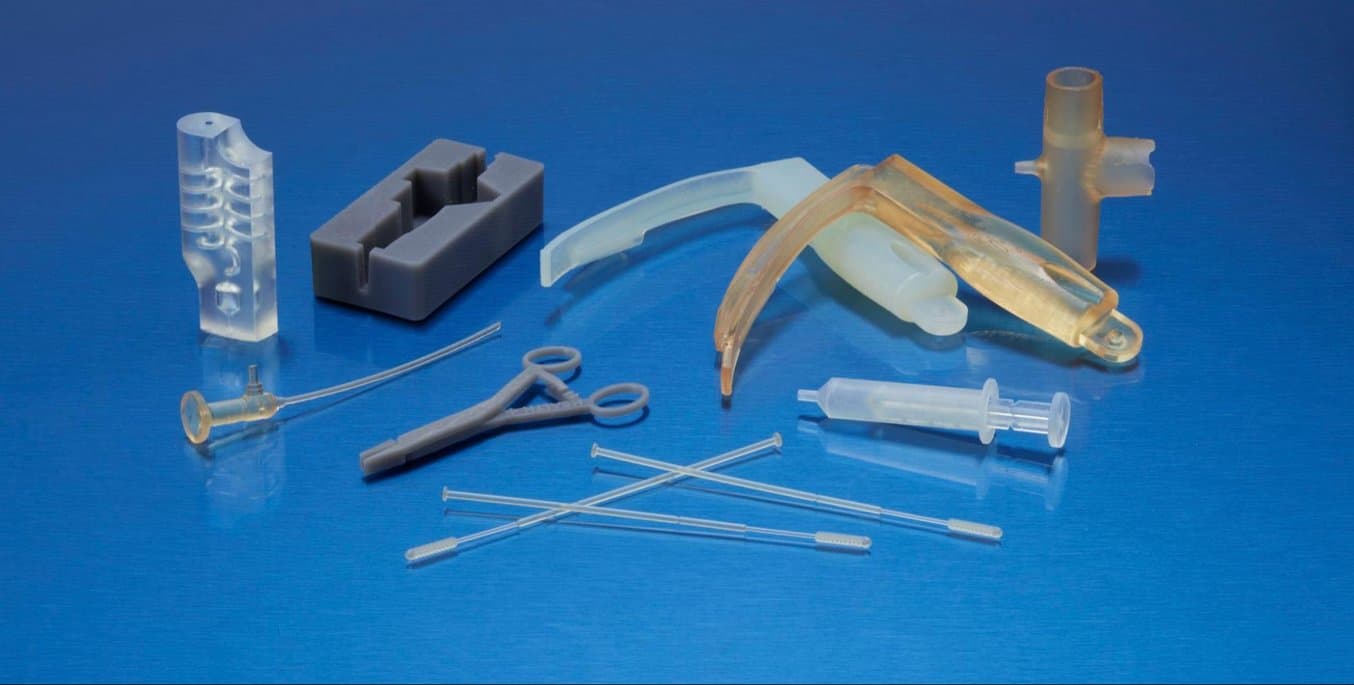
3D printing has been driving innovative solutions and impacting the development of medical devices for decades from R&D through to production. As 3D printers have become more affordable and investments in machines and materials accelerate, more companies are gaining access to 3D printing to disrupt the status quo of the healthcare industry.
By bringing 3D printing in-house, medical device developers and manufacturers can reduce both cost and time to market. The technology enables more nimble product development, novel final-use parts, and the creation of personalized medical devices that would be impossible to produce using traditional tools. As demonstrated since early 2020, additive manufacturing also enables unprecedented speed from concept to mass production of emergency medical supplies.
In this comprehensive guide, we look at the different applications of 3D printing for medical devices, compare the most common 3D printing processes for the medical industry, and provide a brief overview (and links to more resources) about the regulatory process for 3D printed medical devices.
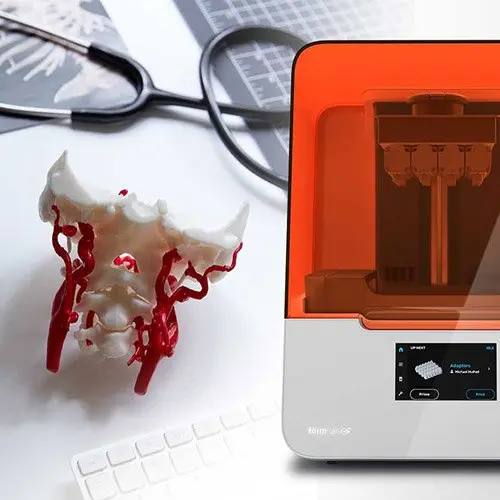
Intro to Medical 3D Printing
Join Formlabs for this introduction to learn best practices for medical 3D printing and see the latest Formlabs Medical ecosystem, including multiple new medical-grade products!
3D Printing Applications for Medical Devices
The combination of speed, affordability, customizability, and design freedom that 3D printing offers has led to a wide range of use cases in the medical device industry. Let’s look at the most common applications and real-world examples that highlight the versatility of 3D printing.
Rapid Prototyping Medical Devices
Developing innovative products goes hand in hand with advancing patient care and improving outcomes within the healthcare industry. Prototyping is a key element of this iterative process in which revisions are made, implemented, and tested in a controlled environment.
Rapid prototyping is the group of techniques used to quickly fabricate a full scale model of a physical part or assembly using three-dimensional computer-aided design (CAD) data. 3D printing is a natural match for prototyping: it provides almost unlimited form freedom, doesn’t require tooling, and can produce parts with mechanical properties that closely match those produced with traditional manufacturing methods.
“Previously, we relied almost exclusively on outside print vendors for prototypes. Today, we are running four Formlabs machines, and the impact has been profound. Our rate of 3D printing has doubled, cost has been reduced by 70 percent, and the level of print detail allows for clear communication of designs with orthopedic surgeons.”
Alex Drew, Mechanical Project Engineer, DJO Surgical
3D printing provides manufacturers with the flexibility to develop looks-like, feels-like, and works-like prototypes of even the most complex medical devices. New iterations can be completed within hours and validated to determine if further changes are required. Applying 3D printing also enables the development of medical device prototypes using diverse materials in scenarios in which properties like strength, flexibility, or heat resistance are important criteria for the functioning of the device.
Testing a functional prototype using real-world validation processes provides the manufacturer with results to base further iterations. 3D printed prototypes can also serve as presentation pieces when pitching investors or engaging with future customers.
The ease of use and low cost of in-house 3D printing has also revolutionized product development. Over 85 percent of the 50 largest medical device manufacturers have adopted Formlabs technology to produce prototypes, manufacturing aids, or end-use devices. Due to a CAPEX starting under $5,000, many startups and small businesses have also benefited from the technology.
For example, UK-based medical device design company Coalesce Product Development develops drug delivery devices, including inhalers and injectors. The manufacturer struggled with developing complex medical device prototypes using traditional manufacturing processes due to the high start-up costs and time-consuming operations associated with traditional production tools.
The company turned to in-house desktop stereolithography (SLA) 3D printers to prototype, test, and create various devices in a multitude of different shapes and sizes. With 3D printing, they created new prototypes in under 24 hours at 10-20x lower cost compared to outsourcing. Beyond 3D printing the prototypes, they also 3D print test fixtures and jigs to accelerate the testing of their inhalers.
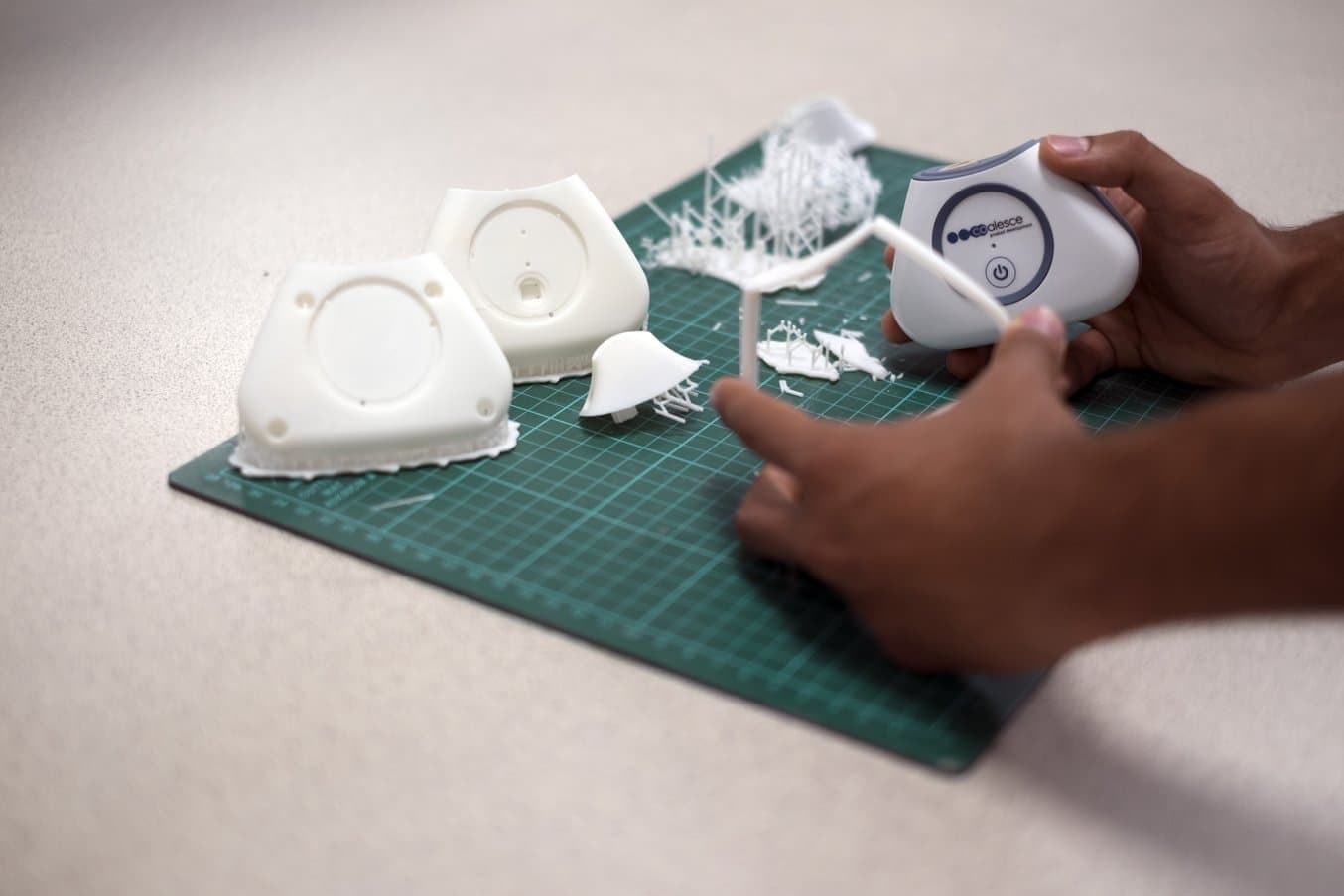
Medical device design company Coalesce uses 3D printing to prototype drug delivery devices, such as inhalers.
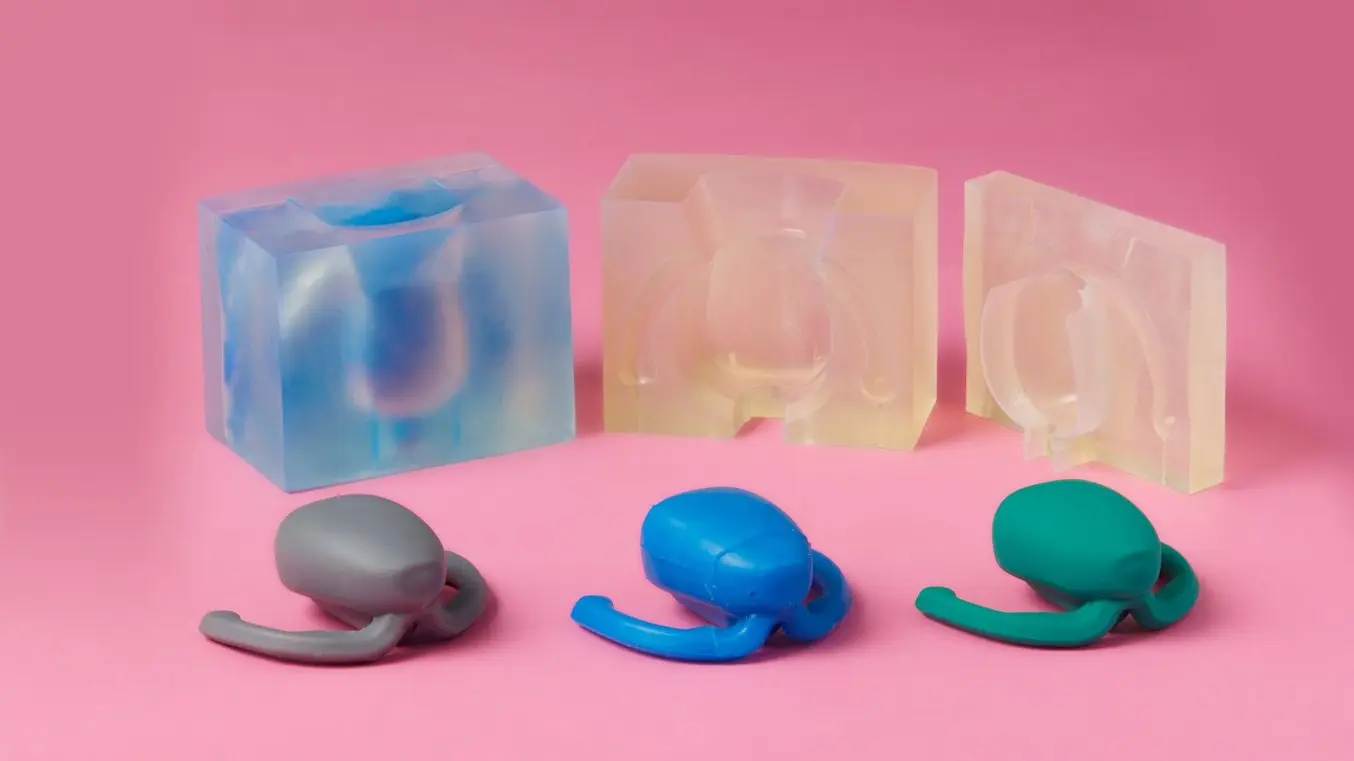
Creating Silicone Medical Devices
This guide aims to help the user decide on the best method of silicone part production for their intended use, and provides step-by-step instructions for both printing with Silicone 40A, and molding silicone using SLA 3D printed tooling (including two-part injection molds, overmolds, and compression molds).
Manufacturing Patient-Specific Medical Devices
Most traditional manufacturing processes such as injection molding or thermoforming require expensive tooling, which means they are not efficient for producing customized or personalized parts. 3D helps address this challenge in two ways.
Rapid Tooling for Traditional Manufacturing Processes
First, 3D printing can be used to manufacture custom rapid tooling such as 3D printed molds, patterns, casts, and dies for a range of traditional manufacturing processes, including injection molding, thermoforming, silicone molding, overmolding, insert molding, compression molding, metal casting, and more.
One vacuum forming example is dental aligners and retainers that are designed and created based on unique patient anatomy collected through intraoral or desktop scanning devices. Manufacturing these devices involves vacuum forming a plastic sheet over a custom model for each step of the treatment. As 3D printers can produce these models directly from the digital files within a few hours, they’ve become the go-to method for producing these increasingly popular devices in orthodontics.
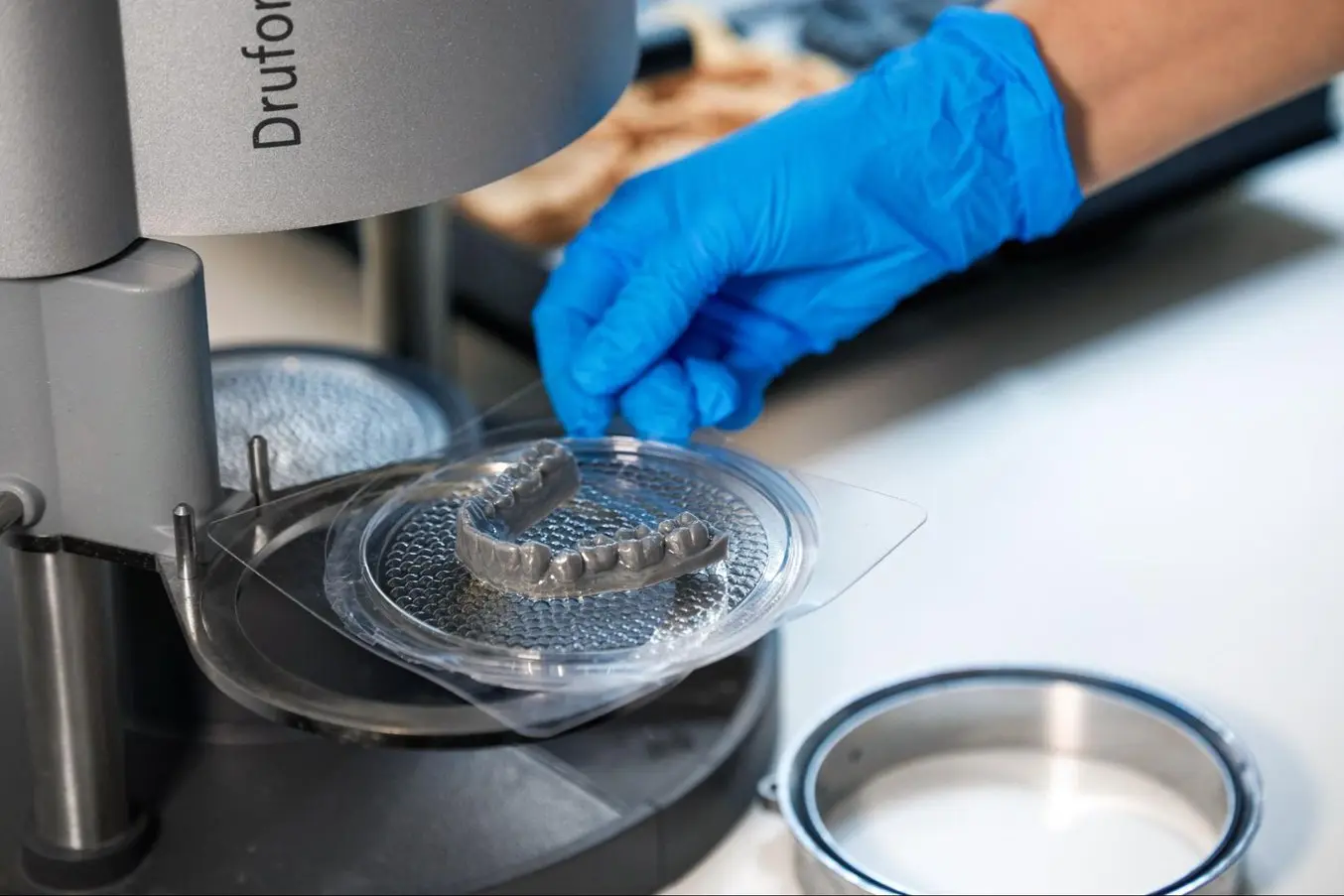
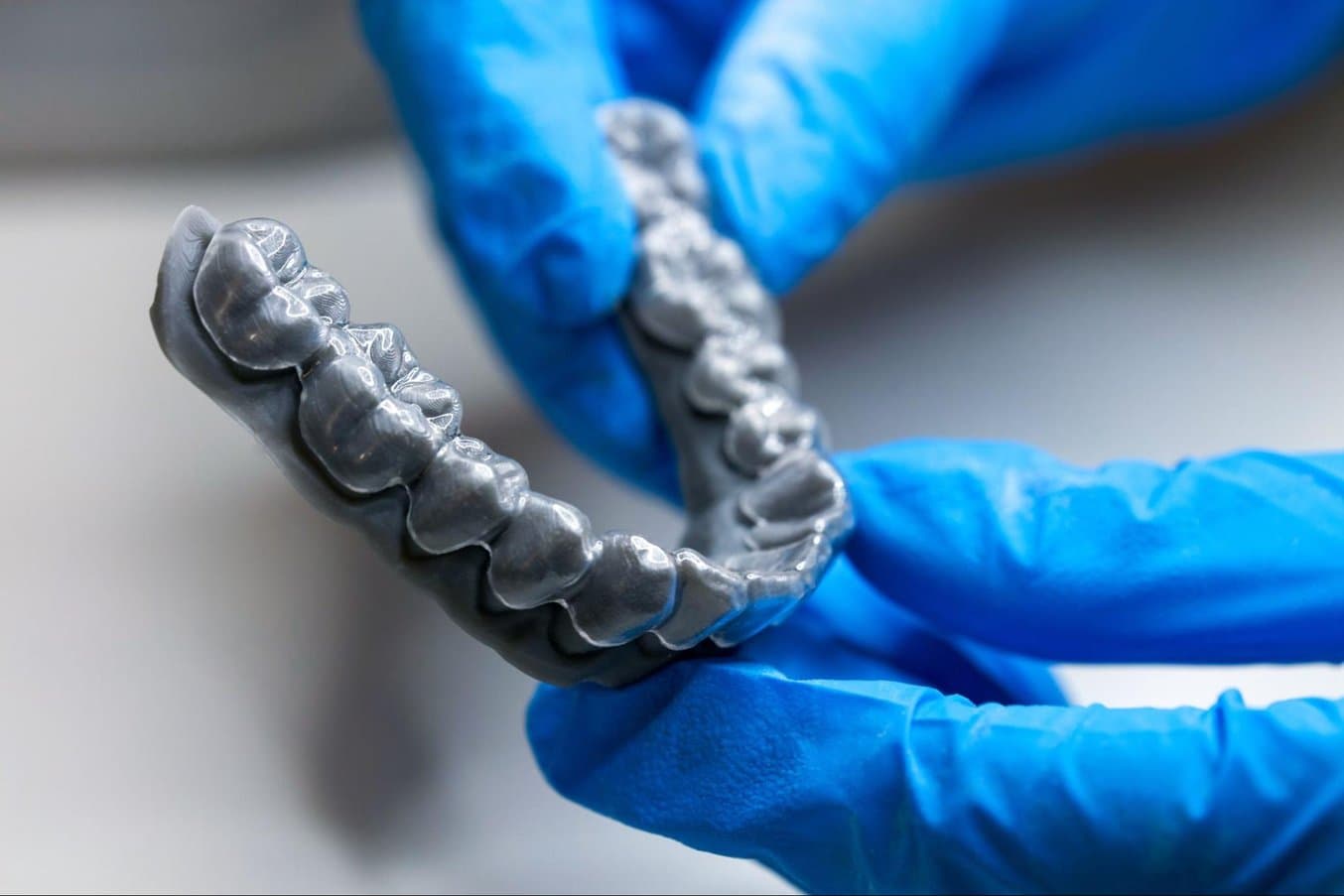
3D printing is the go-to method for manufacturing models for vacuum forming clear aligners and retainers.
Another example comes from Cosm, a medical device company developing a supportive treatment for patients suffering from pelvic floor disorders. The company uses 3D printed molds for silicone molding to create a tailored treatment for each patient’s specific case.
Utilizing 3D printing gives Cosm the flexibility and affordability it requires to manufacture custom pessary molds within 24 hours.
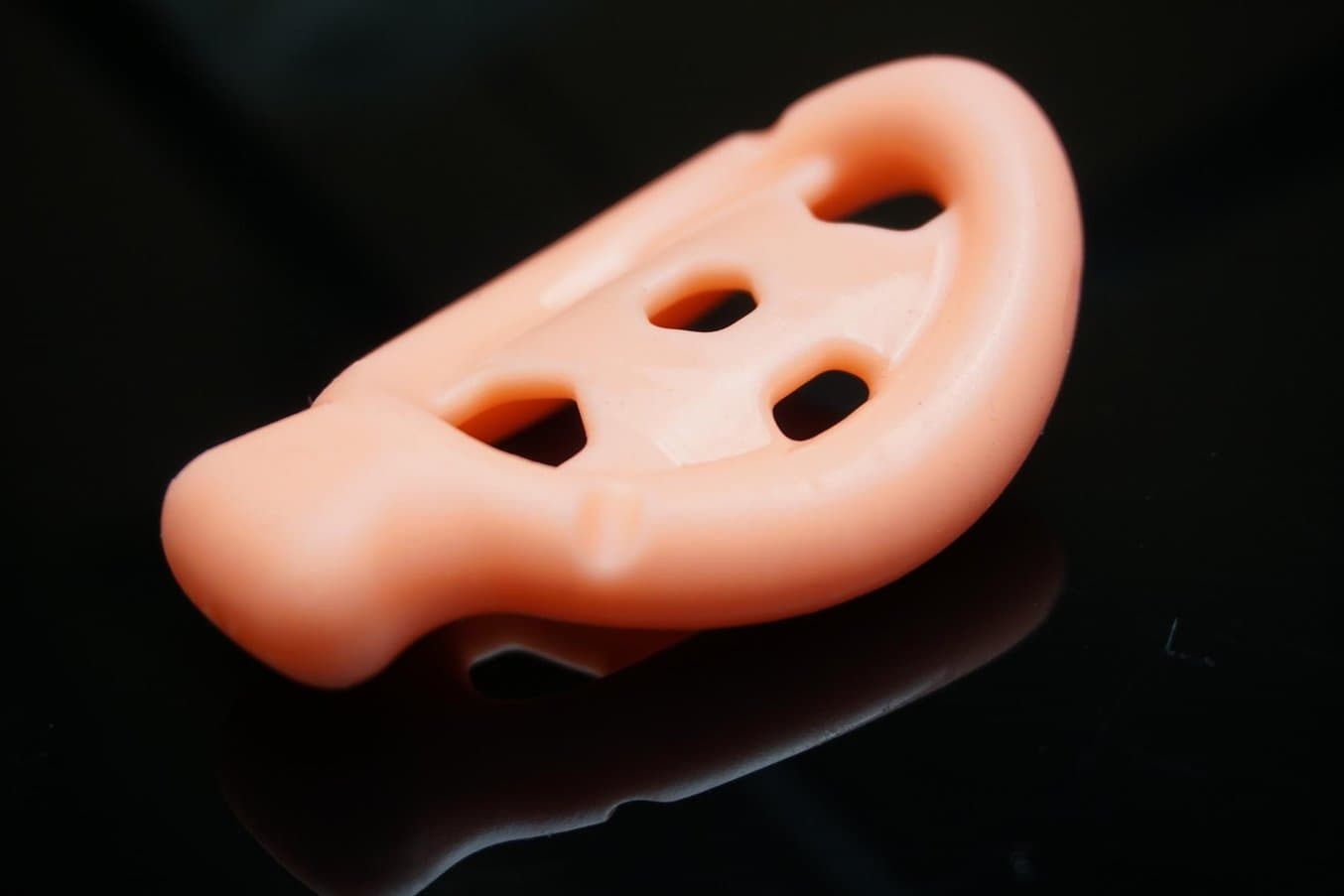
Cosm manufactures custom pessaries using silicone molding.
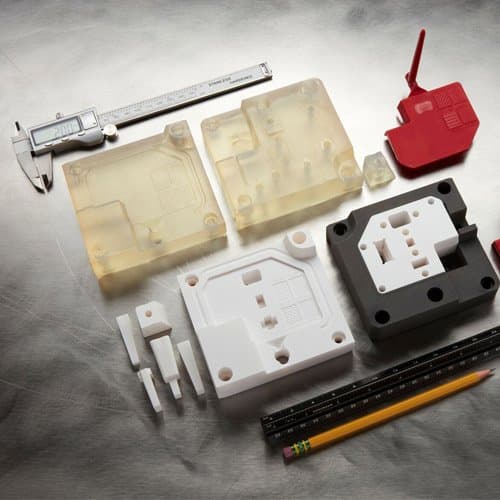
Moldmaking with 3D Prints: Techniques for Prototyping and Production
Download our white paper to learn about six moldmaking processes that are possible with an in-house SLA 3D printer, including injection molding, vacuum forming, silicone molding, and more.
Directly 3D Printing Patient-Specific Medical Devices
Second, 3D printing is also increasingly used to manufacture final-use, patient-specific medical devices. As 3D printing processes don’t require tooling, they make it possible to create custom parts and complex designs in a streamlined, cost-efficient manner.
Once again, dentistry is one of the fields leading the adoption of 3D printing in medicine. Surgical guides, splints, temporary and permanent restorations, and dentures can all be directly 3D printed.
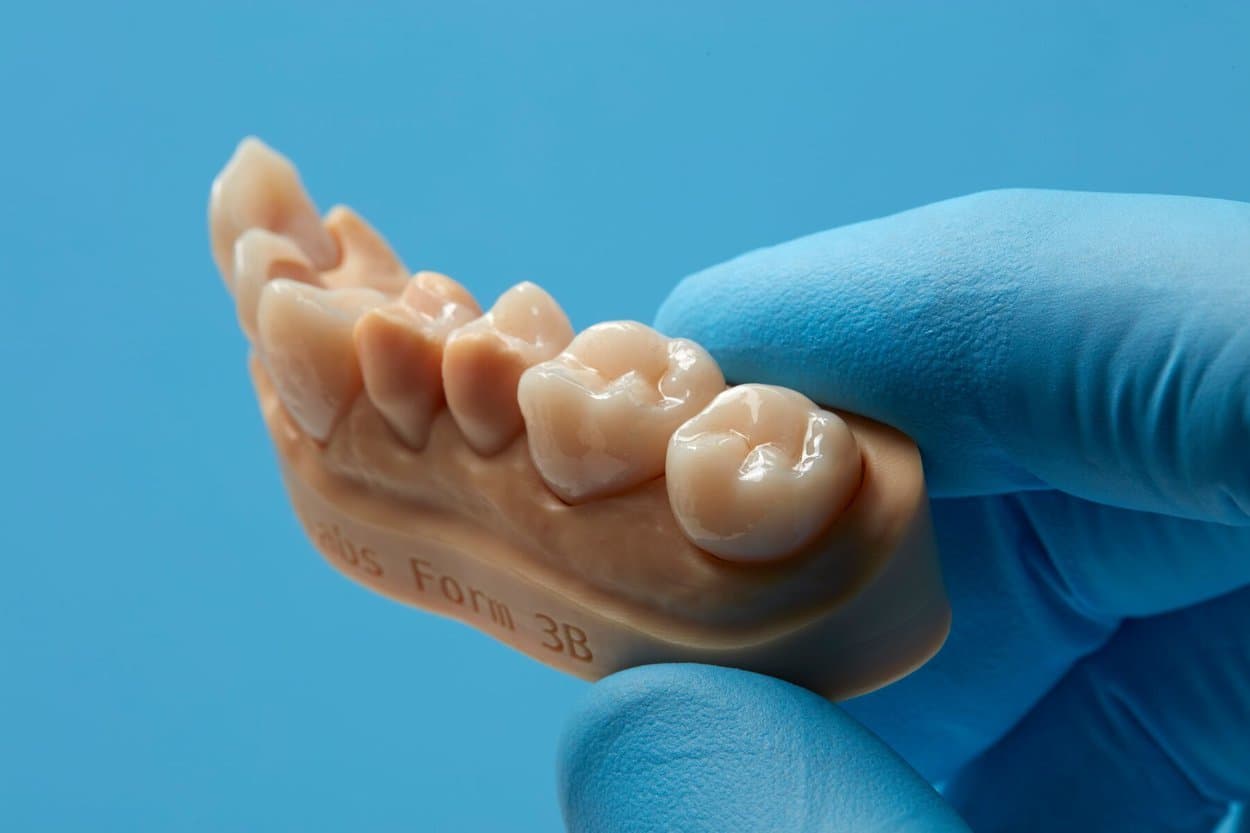
Permanent crowns manufactured using a ceramic-filled resin material.
Other end-use 3D printed medical device applications include custom-fit ear devices such as hearing aids and noise protection equipment as well as strong and durable custom prosthetics, orthotics, and more.
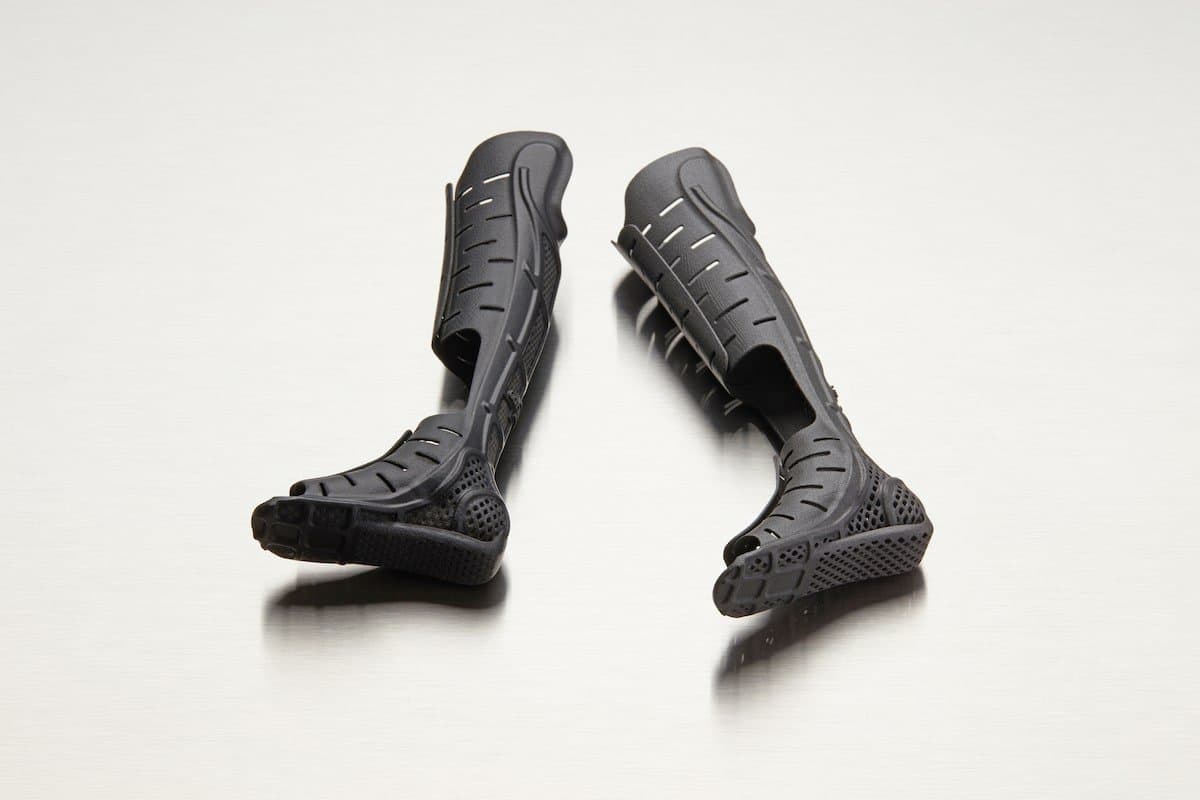
3D printing can be used to create durable and biocompatible patient-specific prosthetics and orthotics at an affordable price and faster than ever before.
Surgical instruments manufacturer restor3d leverages 3D printing capabilities to drastically improve surgical care delivery by 3D printing procedure-specific instruments for cervical spine implants. Using 3D printing empowers them to create sterile, surgeon-designed tools using a truly agile development process. The restor3d approach leads to reduced sterilization, warehousing, and OR costs for hospitals and surgical centers and demand has been strong: over 25 Formlabs machines are manufacturing devices around the clock.
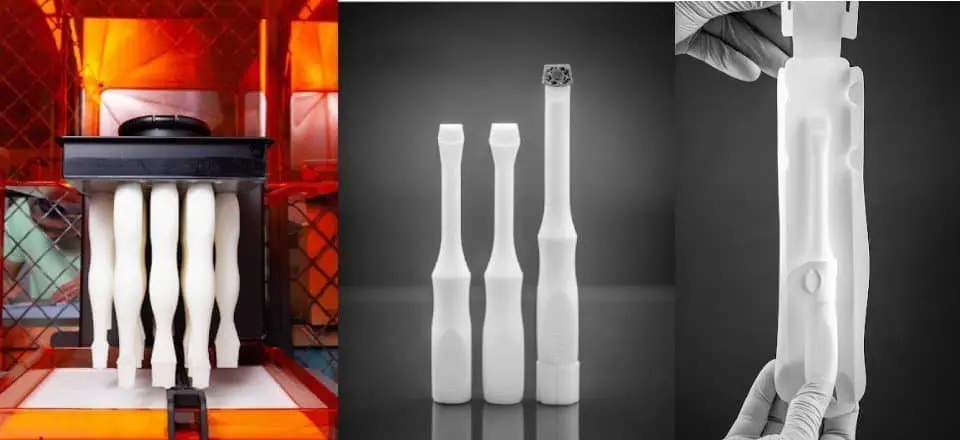
restor3d uses 3D printing to manufacture procedure-specific surgical instruments.
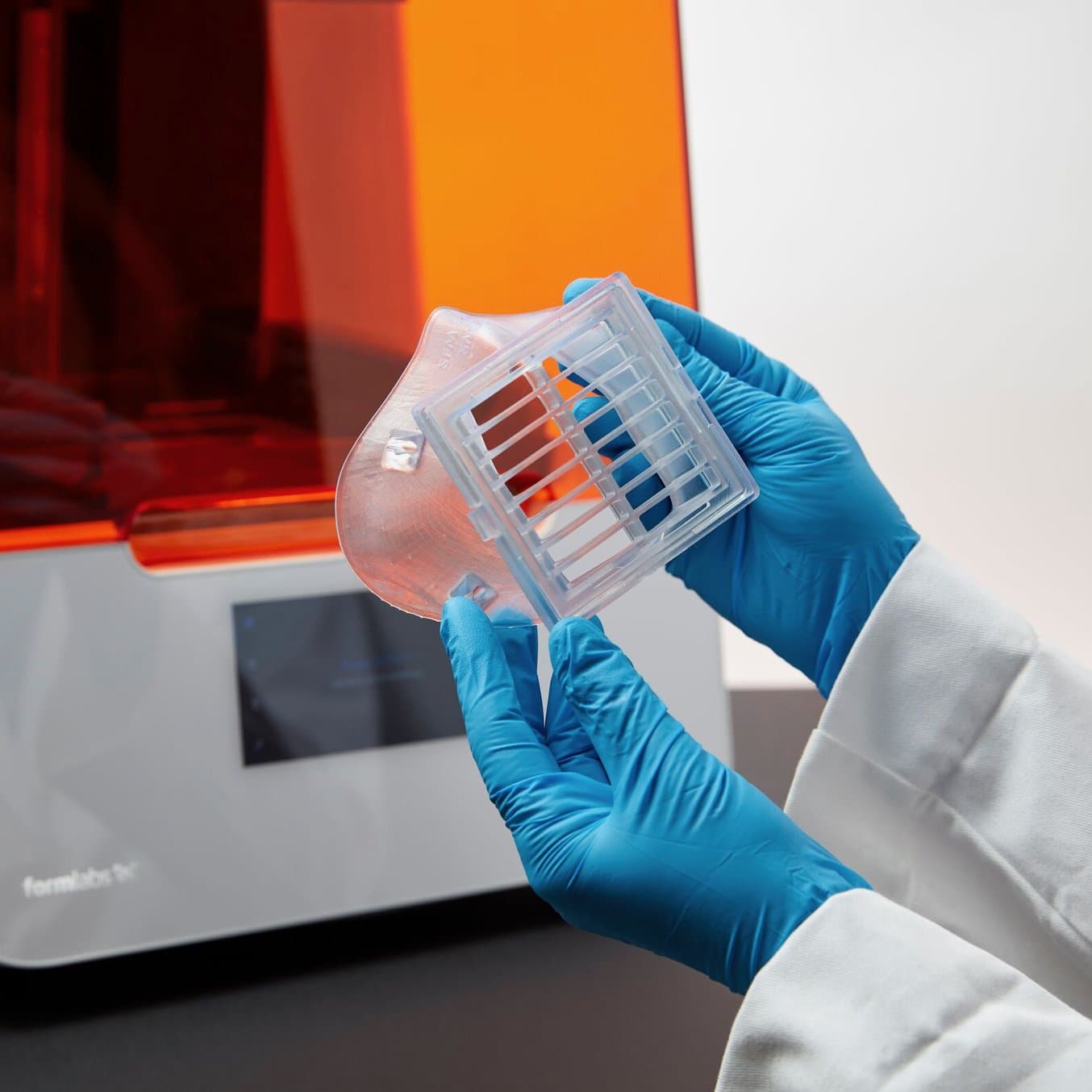
How to Find Success 3D Printing Medical Devices
In this report, learn how Formlabs Medical helps medical device firms bring digital fabrication in-house, and get inspired through the examples of four companies currently creating groundbreaking devices using 3D printing.
Producing End-Use Medical Devices
Beyond surgical tools, 3D printing is also increasingly popular for producing medical devices or components of medical devices, especially for complex designs that would be inefficient or impossible to manufacture with traditional processes.
Tension Square has commercialized a device that holds a needle decompression secure in place while preventing kinking, folding, or dislodgement that often lead to preventable fatalities in the field. After years of R&D, the company is now 3D printing the final end-use device on a Fuse 1 selective laser sintering (SLS) 3D printer, that allows them to reduce the reliance on outsourced providers and produce 100+ devices per printer within 24 hours. The company, founded by a veteran and paramedic, intends to produce millions of parts per year using 3D printing at its US-based manufacturing facilities.
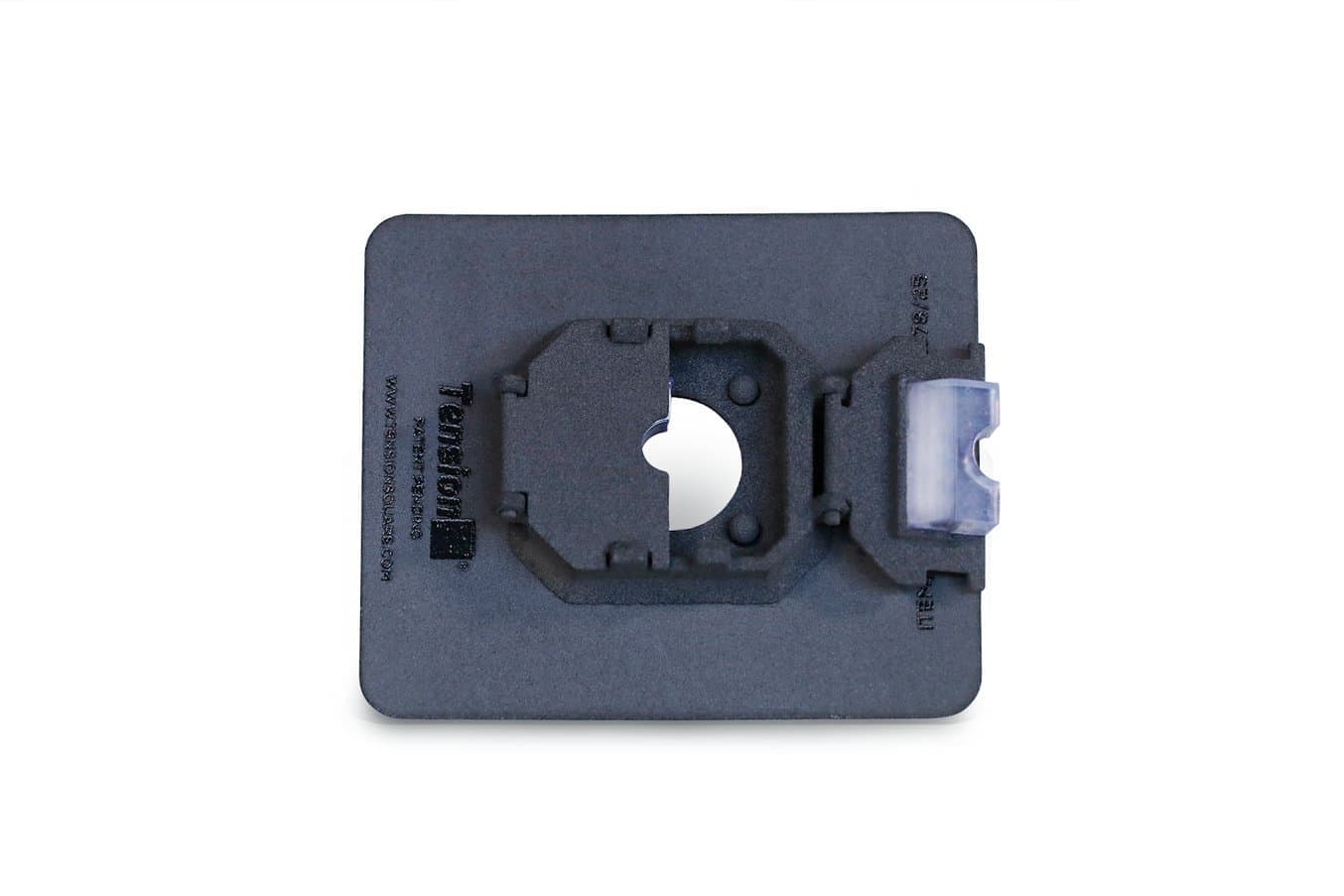
Tension Square 3D prints a PTX decompression catheter stabilization device directly using SLS 3D printing.
VO2 Master develops a portable metabolic analyzer that is easier to use and more affordable than established machines. After using 3D printing extensively in the prototyping process, the company also decided to 3D print the end-use outside shells of the device to be able to get to market faster. The shells are printed on SLA 3D printers in Tough 1500 Resin, a resilient material that simulates the strength and stiffness of polypropylene. The printed parts are painted white before being fastened to the mask, to improve surface finish, emboss coloration, and durability.
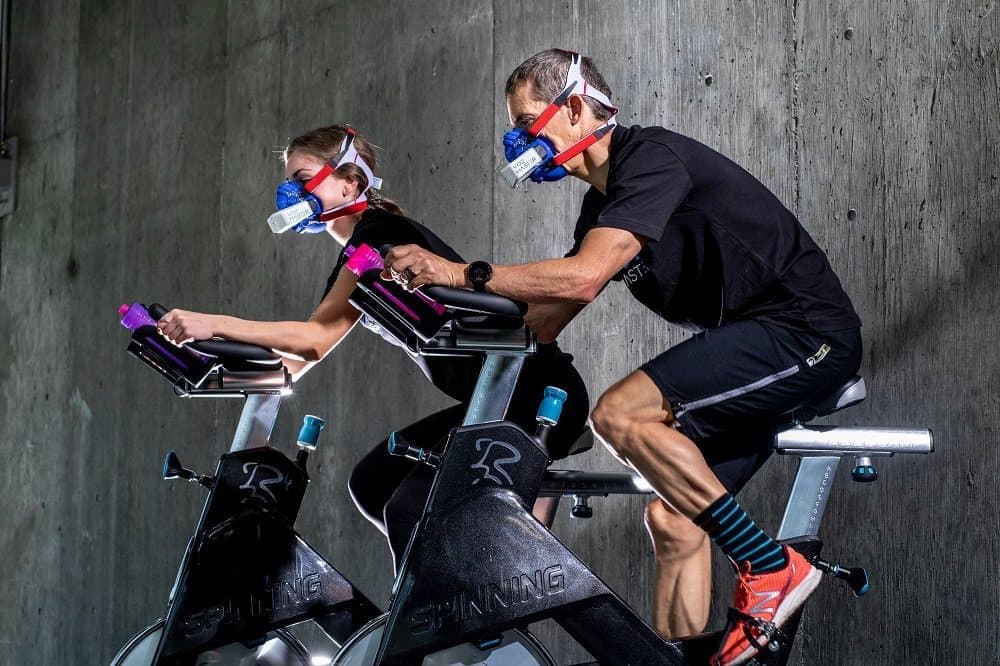
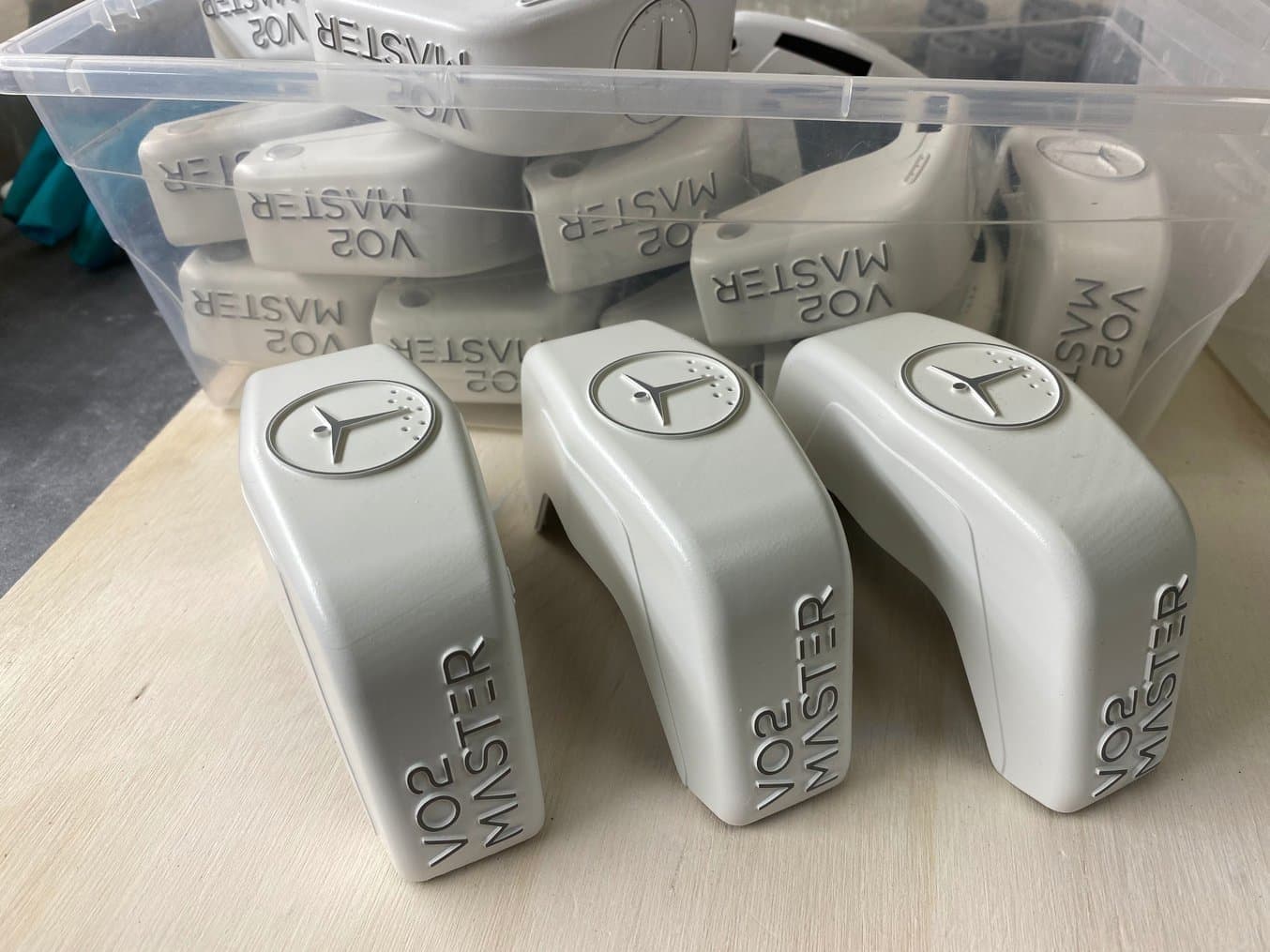
VO2 Master 3D prints the outer shell for their portable metabolic analyzer, allowing them to get to market faster.
Manufacturing Emergency Medical Supplies
The COVID-19 pandemic overwhelmed healthcare centers and medical supplies in unprecedented ways that left most governments scrambling for resources in unlikely places. To deal with the overwhelming need for supplies, automobile manufacturers pivoted to manufacturing respirators while fashion houses produced protective equipment to mitigate challenges associated with the pandemic.
As COVID-19 cases soared, the need for widespread testing increased, which led to a global shortage of the nasopharyngeal (NP) swabs needed to collect samples for COVID-19 testing. After identifying that nasal swabs for testing COVID-19 were in high demand and extremely limited supply, a team from USF Health, Northwell Health, and Formlabs collaborated to create a 3D printed alternative. Over the span of one week, the teams worked together to develop a nasal swab prototype and test it in the USF Health and Northwell Health labs. In two days, USF Health and Northwell Health developed prototypes using Formlabs’ 3D printers and biocompatible, autoclavable resins. Just 12 days after the initial idea, the final design was cleared for clinical use and the 3D file was made available for other health systems worldwide. Along with the file, the collaborators developed a detailed workflow with guidelines for qualified users in healthcare to print the swabs and ensure the health and safety of patients.
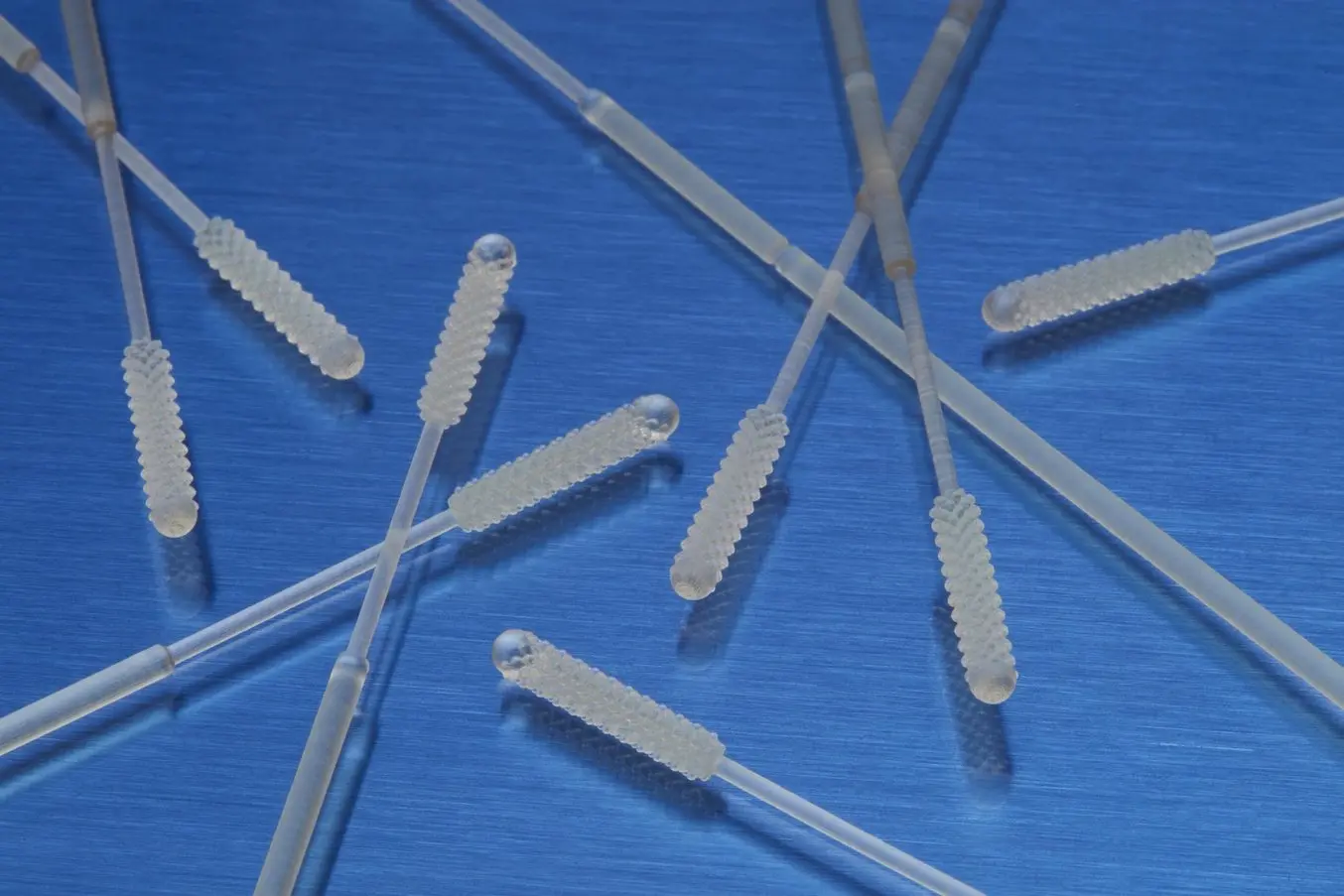
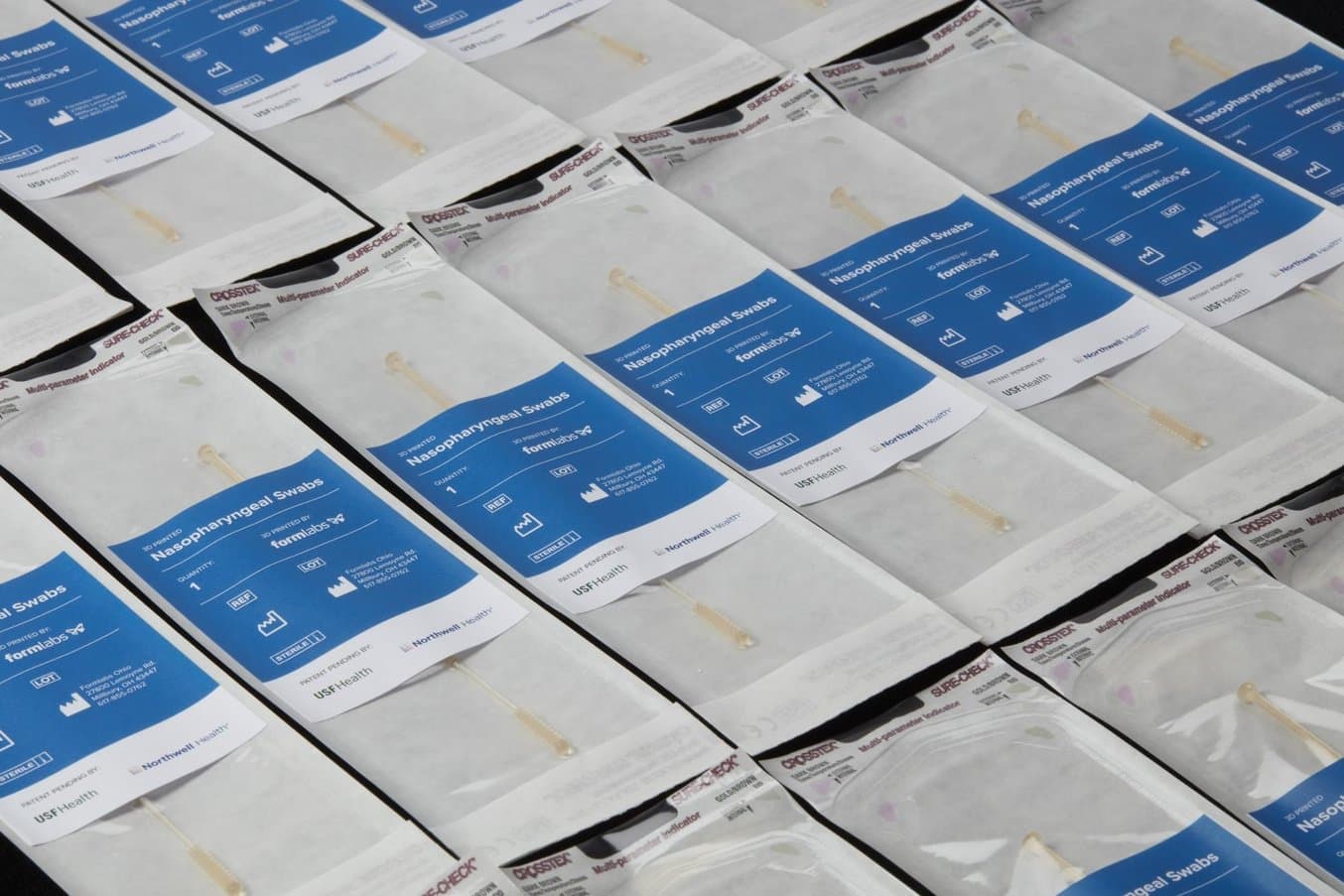
3D printed swabs enabled over 70 million COVID tests in 25 countries in the early stages of the COVID-19 pandemic.
Hospitals, dental labs, and academic medical centers that had been using their 3D printers for patient-specific surgical devices were able to repurpose their equipment and fill a gap in their own supply chains by producing 3D printed swabs in-house. With the accessible design, affordable equipment, and validated processes, the swab design enabled over 70 million COVID tests in 25 countries.
Other solutions to meet the need for more ventilators included the conversion of bi-level positive airway pressure (BiPAP) machines that are normally used to relieve sleep apnea. Successful conversion requires the use of a BiPAP adapter that turns these machines into functional invasive mechanical ventilators.
To ensure enough BiPAP adapters were quickly created to provide patients with breathing support, Northwell Health, New York’s largest healthcare provider, designed 3D printable BiPAP adapters. The FDA granted Formlabs an Emergency Use Authorization to 3D print these adaptors to assist healthcare centers while traditional ventilators were unavailable.
3D Printers for Medical Devices
When it comes to 3D printers for medical devices, not all methods are created equal. It is important to choose the right printing technology for specific use cases.
The most popular 3D printing technologies for medical devices include stereolithography (SLA), selective laser sintering (SLS), and fused deposition modeling (FDM) for plastic parts, and direct metal laser sintering (DMLS) and selective laser melting (SLM) for metals.
Stereolithography (SLA)
SLA 3D printers use a laser to cure liquid resin into hardened plastic in a process called photopolymerization. SLA is one of the most popular processes among medical professionals due to its high resolution, precision, and material versatility.
-
Advantages of SLA
SLA parts have the highest resolution and accuracy, the clearest details, and the smoothest surface finish of all plastic 3D printing technologies. The main benefit of SLA, however, lies in its versatility. SLA resin formulations offer a wide range of optical, mechanical, and thermal properties to match those of standard, engineering, and industrial thermoplastics.
SLA is a great option for highly detailed medical device prototypes requiring tight tolerances and smooth surfaces, as well as molds, tooling, patterns, medical models, and functional end-use parts. SLA also offers the widest selection of biocompatible materials for dental and medical applications. With Draft Resin, the Formlabs SLA printers are also the fastest options for 3D printing large prototypes, up to 10X faster than FDM.
-
Disadvantages of SLA
SLA’s wide versatility comes with a slightly higher price tag than FDM, but it is still more affordable than all other 3D printing processes. SLA resin parts also require post-processing after printing, which includes washing the parts and post-curing.
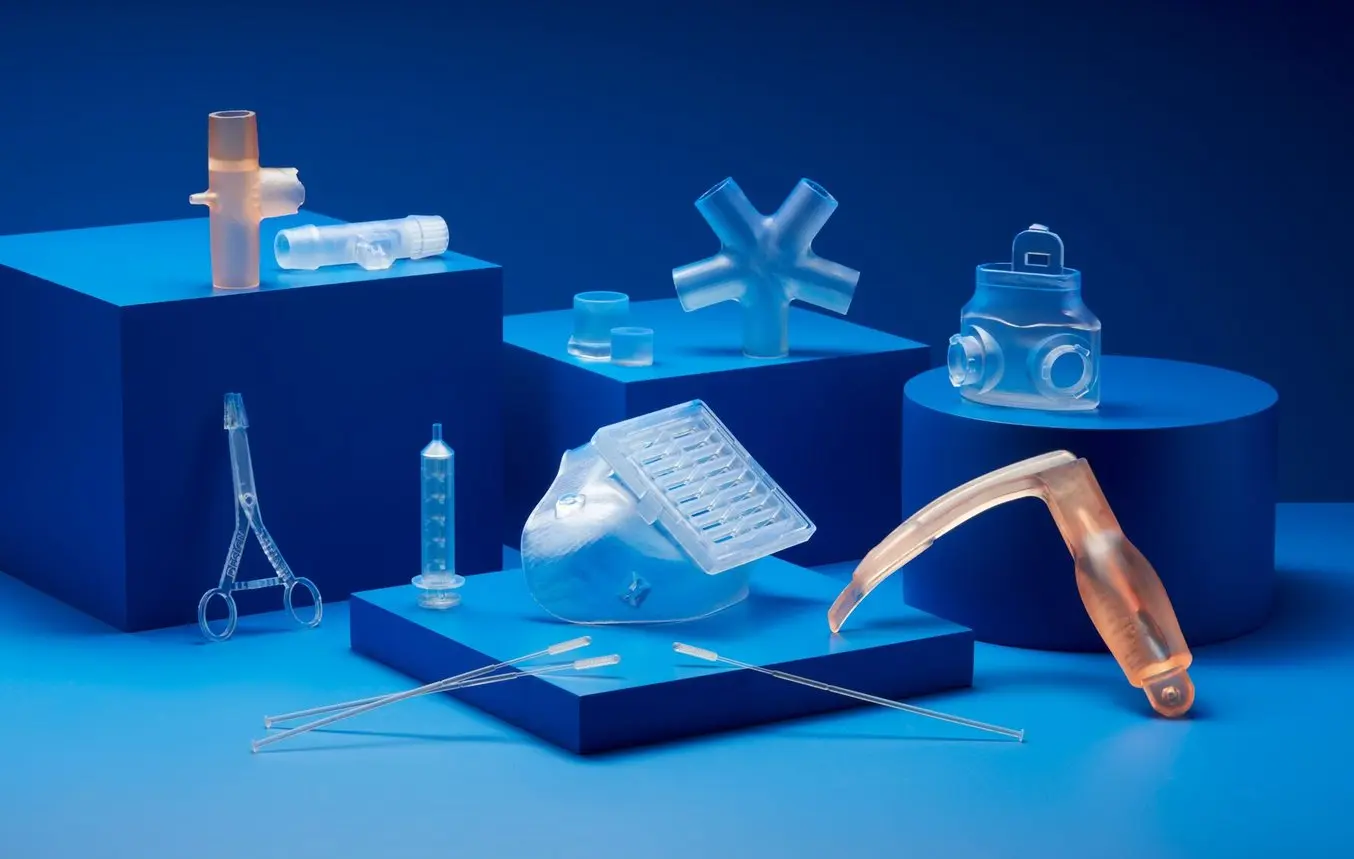
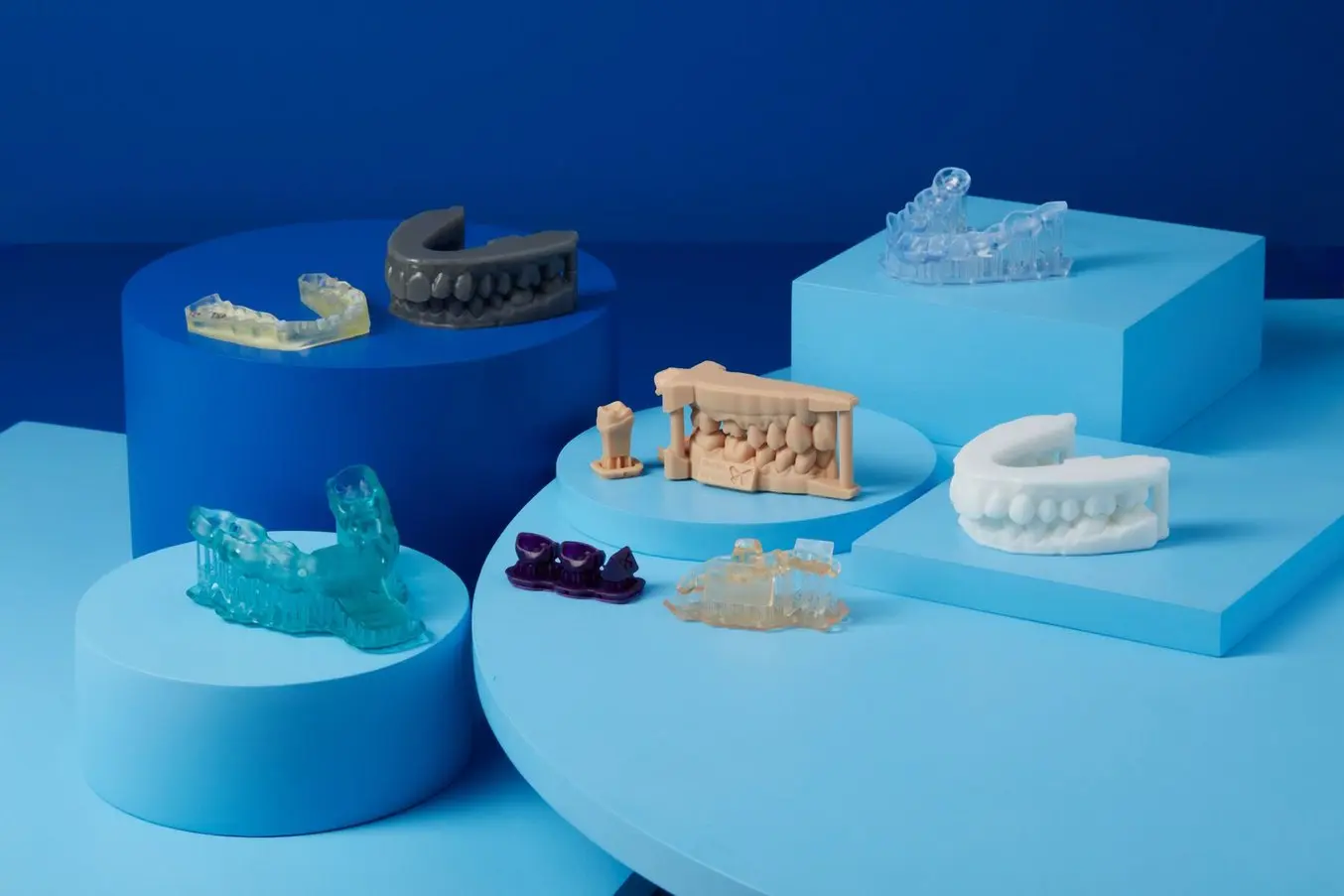
SLA 3D printing offers a wide selection of 3D printing materials, including biocompatible materials, for a variety of medical and dental applications.
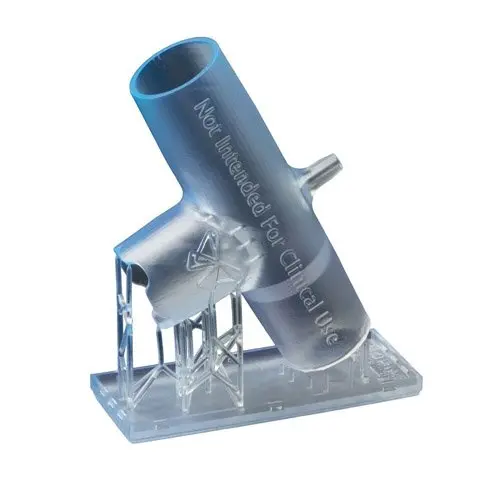
Request a Free Sample Part
See and feel Formlabs SLA quality firsthand. We’ll ship a free sample part to your office.
Selective Laser Sintering (SLS)
SLS 3D printers use a high-powered laser to fuse small particles of polymer powder. The unfused powder supports the part during printing and eliminates the need for dedicated support structures, making SLS a particularly effective choice for complex mechanical parts.
Its ability to produce parts with excellent mechanical capabilities makes SLS the most common polymer additive manufacturing technology for industrial applications. Depending on the material, SLS nylon parts may also be biocompatible and sterilizable.
-
Advantages of SLS
Since SLS printing doesn’t require dedicated support structures, it’s ideal for complex geometries, including interior features, undercuts, thin walls, and negative features. Parts produced with SLS printing have excellent mechanical characteristics, with strength resembling that of injection-molded parts.
The most common material for SLS is nylon, a popular engineering thermoplastic with excellent mechanical properties. Nylon is lightweight, strong, and flexible, as well as stable against impact, chemicals, heat, UV light, water, and dirt. 3D printed nylon parts can also be biocompatible and not sensitizing, which means that they are ready to wear and safe to use in many contexts.
The combination of low cost per part, high productivity, established materials, and biocompatibility makes SLS a popular choice among medical device developers for functional prototyping, and a cost-effective alternative to injection molding for limited-run or bridge manufacturing.
-
Disadvantages of SLS
SLS 3D printers have a higher entry price than FDM or SLA technologies. While nylon is a versatile material, material selection for SLS is also more limited than for FDM and SLA. Parts come out of the printer with a slightly rough surface finish and require media blasting for a smooth finish.

SLS 3D printing is ideal for strong, functional prototypes and end-use parts, such as prosthetics and orthotics.
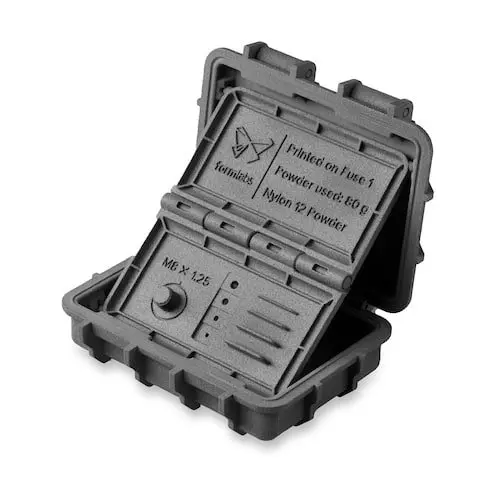
Request a Free Sample Part
See and feel Formlabs SLS quality firsthand. We’ll ship a free sample part to your office.
Fused Deposition Modeling (FDM)
FDM, also known as fused filament fabrication (FFF), is a printing method that builds parts by melting and extruding thermoplastic filament, which a printer nozzle deposits layer by layer in the build area.
FDM is the most widely used form of 3D printing at the consumer level, fueled by the emergence of hobbyist 3D printers. Industrial FDM printers are, however, also popular with professionals.
-
Advantages of FDM
FDM works with an array of standard thermoplastics, such as ABS, PLA, and their various blends. This results in a low price of entry and materials. FDM best suits basic proof-of-concept models and the low-cost prototyping of simpler parts. Some FDM materials are also biocompatible.
-
Disadvantages of FDM
FDM has the lowest resolution and accuracy when compared to other 3D printing technologies for plastics such as SLA or SLS, which means that it is not the best option for printing complex designs or parts with intricate features. Higher-quality finishes require labor-intensive and lengthy chemical and mechanical polishing processes. Some industrial FDM 3D printers use soluble supports to mitigate some of these issues and offer a wider range of engineering thermoplastics, but they also come at a steep price. When creating large parts, FDM printing also tends to be slower than SLA or SLS.
Direct Metal Laser Sintering (DMLS) and Selective Laser Melting (SLM)
Direct metal laser sintering (DMLS) and selective laser melting (SLM) 3D printers work similarly to SLS printers, but fuse metal powder particles together layer by layer using a laser instead of polymers.
DMLS and SLM 3D printers can create strong, accurate, and complex metal products, making this process ideal for a variety of medical applications.
-
Advantages of DMLS and SLM
The biggest advantage of these processes is obviously the materials, as DMLS and SLM 3D printers are capable of producing high-performing end-use medical devices and components from metal. These processes can reproduce complex geometries and the finished products are strong, durable, and biocompatible. They can be used to manufacture generic implants (hips, knees, spine implants, etc.), custom implants for cancer or trauma treatment, dentures, as well as medical and orthopedic technology products.
-
Disadvantages of DMLS and SLM
While the prices of metal 3D printers have also begun to decrease, with costs ranging from $200,000 to $1 million+, these systems are still not accessible to most businesses. Metal 3D printing processes also have an involved and complex workflow.
Alternatively, SLA 3D printing is well-suited for casting workflows that produce metal parts at a lower cost, with greater design freedom, and in less time than traditional methods.
Compare 3D Printers for Medical Devices
The table below highlights the 3D printing technologies that are best equipped to handle the different applications of 3D printing medical devices.
Stereolithography (SLA) | Selective Laser Sintering (SLS) | Fused Deposition Modeling (FDM) | Metal 3D Printing (DMLS, SLM) | |
---|---|---|---|---|
Build volume | Up to 300 x 335 x 200 mm (desktop and benchtop 3D printers) | Up to 165 x 165 x 300 mm (benchtop industrial 3D printers) | Up to 300 x 300 x 600 mm (desktop and benchtop 3D printers) | Up to 400 x 400 x 400 mm (large industrial DMLS/SLM) |
Price range | Starting from $3,750 | Starting from $18,500 | Starting from $2,500 | Starting from $200,000 |
Materials | Varieties of resin (thermosetting plastics). Standard, engineering (ABS-like, PP-like, silicone-like, flexible, heat-resistant, rigid), castable, dental, and medical (biocompatible). | Engineering thermoplastics, typically nylon and its composites (nylon is biocompatible + compatible with sterilization). | Standard thermoplastics, such as ABS, PLA, and their various blends. | Stainless steel, tool steel, titanium, cobalt chrome, and aluminum. |
Ideal applications | Highly detailed prototypes requiring tight tolerances and smooth surfaces; molds, tooling, patterns, medical models, functional parts, dental and medical end-use devices. | Complex geometries, functional prototypes, short-run or bridge manufacturing, orthotics, and prosthetics. | Basic proof-of-concept models, low-cost prototyping of simple parts. | Strong, durable parts with complex geometries, implants, dentures, medical and orthopedic components out of metal. |
Biocompatibility of 3D Printing Materials
Depending on the application, biocompatible parts may be required for medical devices. Biocompatibility information is required for 510(k) and premarket approval (PMA) submissions in the United States and other regulatory submissions worldwide. It proves whether the device will be compatible with the biological system in which it is intended. Missing or inadequate information can lead to significant delays in bringing the device to market.
Biocompatibility testing requirements should be determined based on the intended use of the device (type, area, and duration of exposure). Determining testing requirements early in the development process will allow ample time to complete testing before submission to regulatory bodies. It should stem from the expected contact between the device and the human body.
Three different categories typically define contact:
-
Direct Contact: Comes into physical contact with the patient.
-
Indirect Contact: Comes into physical contact with a fluid, gas, or other material that has direct contact with the patient.
-
No Contact: Does not have direct or indirect contact with the patient and is therefore exempt from biocompatibility requirements.
Some 3D printer and 3D printing material manufacturers, like Formlabs, conduct biocompatibility testing based on ISO 10993, ISO 18562, and ISO 7405 standards and publish the information on relevant materials.
As the testing is conducted on standardized printed samples, manufacturers are responsible for following printing and post-processing instructions and for independently validating the biocompatibility of their respective parts.
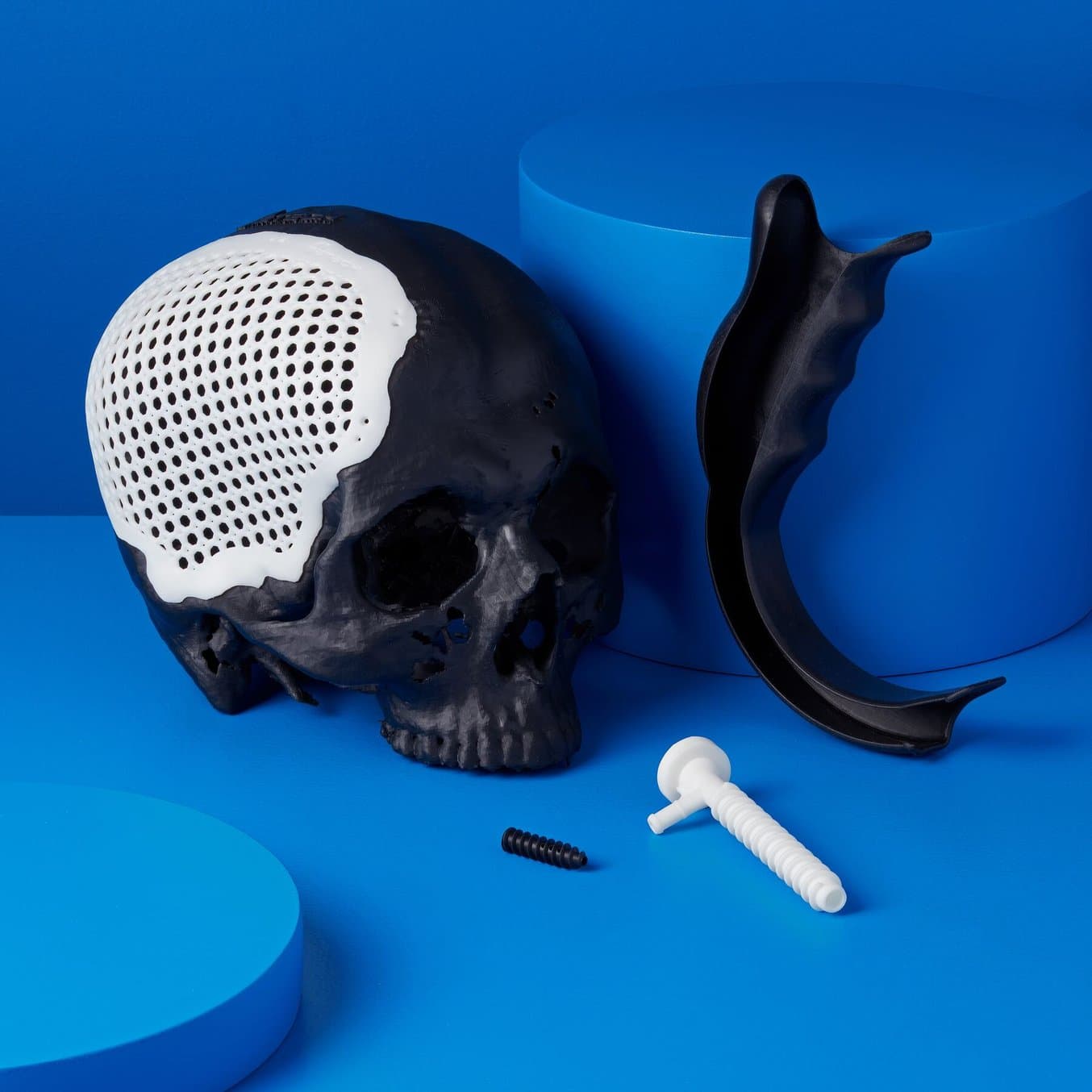
3D Printed Medical Devices for Precision Surgery: Clinical, Commercial, and Regulatory Perspectives
Join Formlabs and Nelson Labs for a deep dive into biocompatibility, including an introduction to our new materials and best practices for medical manufacturers from industry experts.
Regulatory Approval for 3D Printed Medical Devices
3D printed medical devices must meet the regulatory guidelines in their respective locations.
Part of this process is establishing a quality management system (QMS) which is comprised of the core set of policies, procedures, forms, and work instructions, along with their sequence, interactions, and resources required to conduct business as a medical device company.
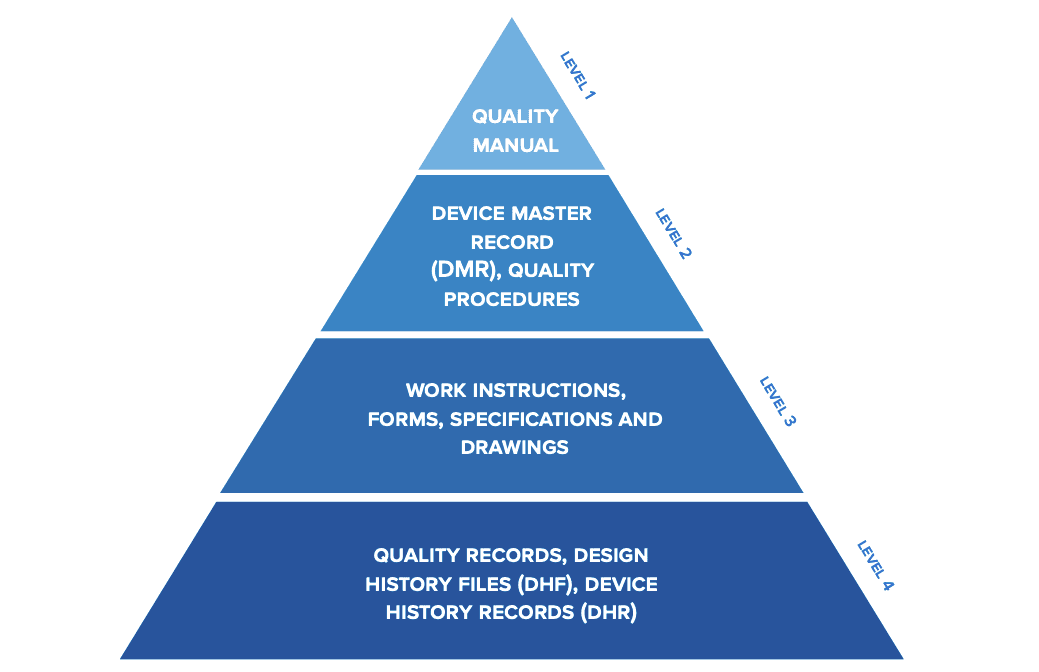
Example of QMS hierarchy.
Quality records are documentation that demonstrate the QMS is being executed and followed and describe how your company addresses medical device regulations. The FDA defines the rules in 21 CFR Part 820. And if you plan to go to market in the U.S., these regulations are required.
Outside the U.S., Europe requires a quality system to be established to meet the medical device regulations (and/or IVD regulations). Many medical device companies implement a quality system certified to ISO 13485:2016 to satisfy EU needs.
To learn more about the specific regulatory requirements, download our comprehensive white paper, co-authored by Formlabs partner Greenlight Guru, that includes a variety of resources to support users in each step of the process.
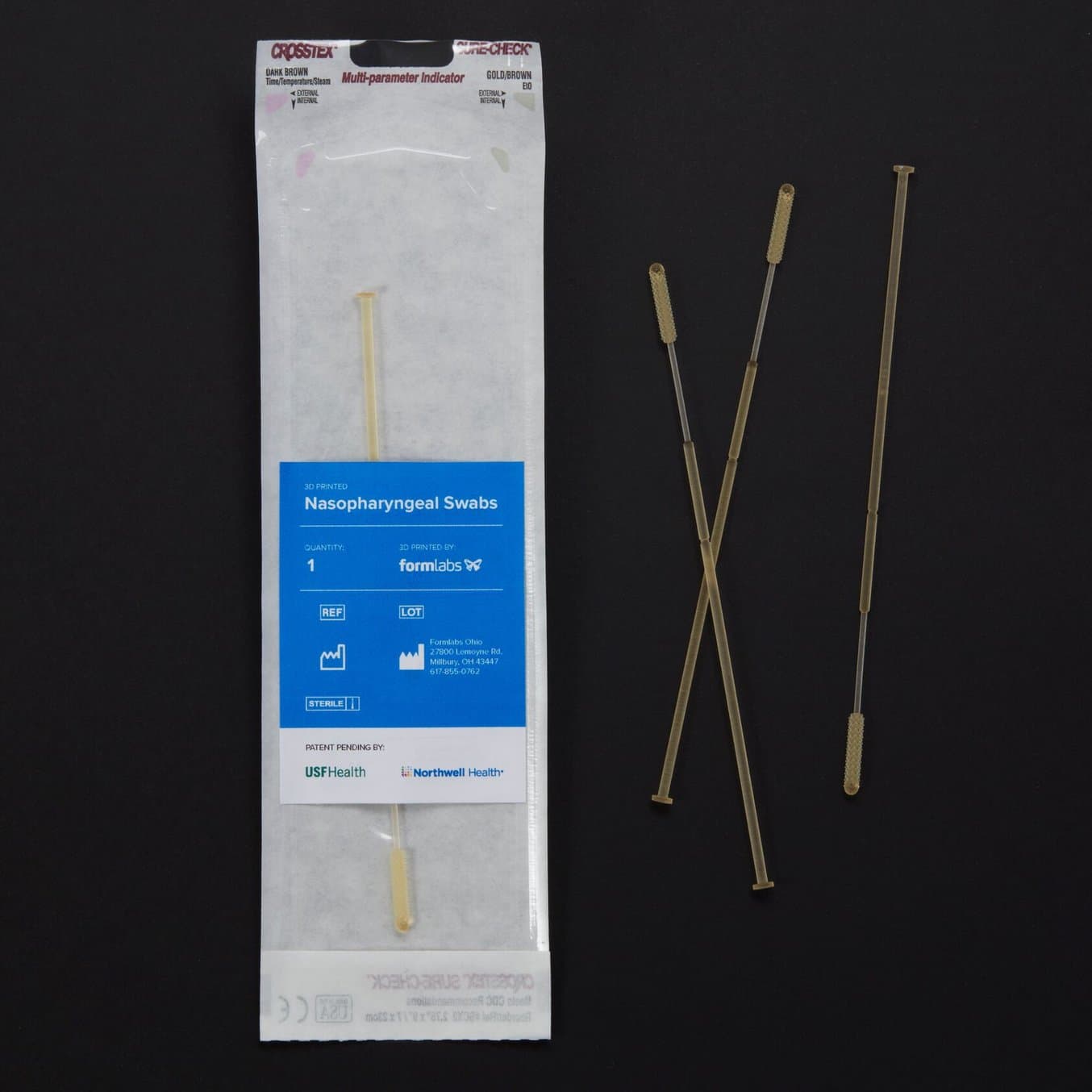
The Ultimate Guide to Quality Assurance and Regulatory Affairs in Medical 3D Printing
This white paper aims to guide users in the medical device industry through every stage of the product development process, from evaluating manufacturing methods and 3D printing technologies to specific regulatory requirements for commercializing and marketing end-use 3D printed medical devices.
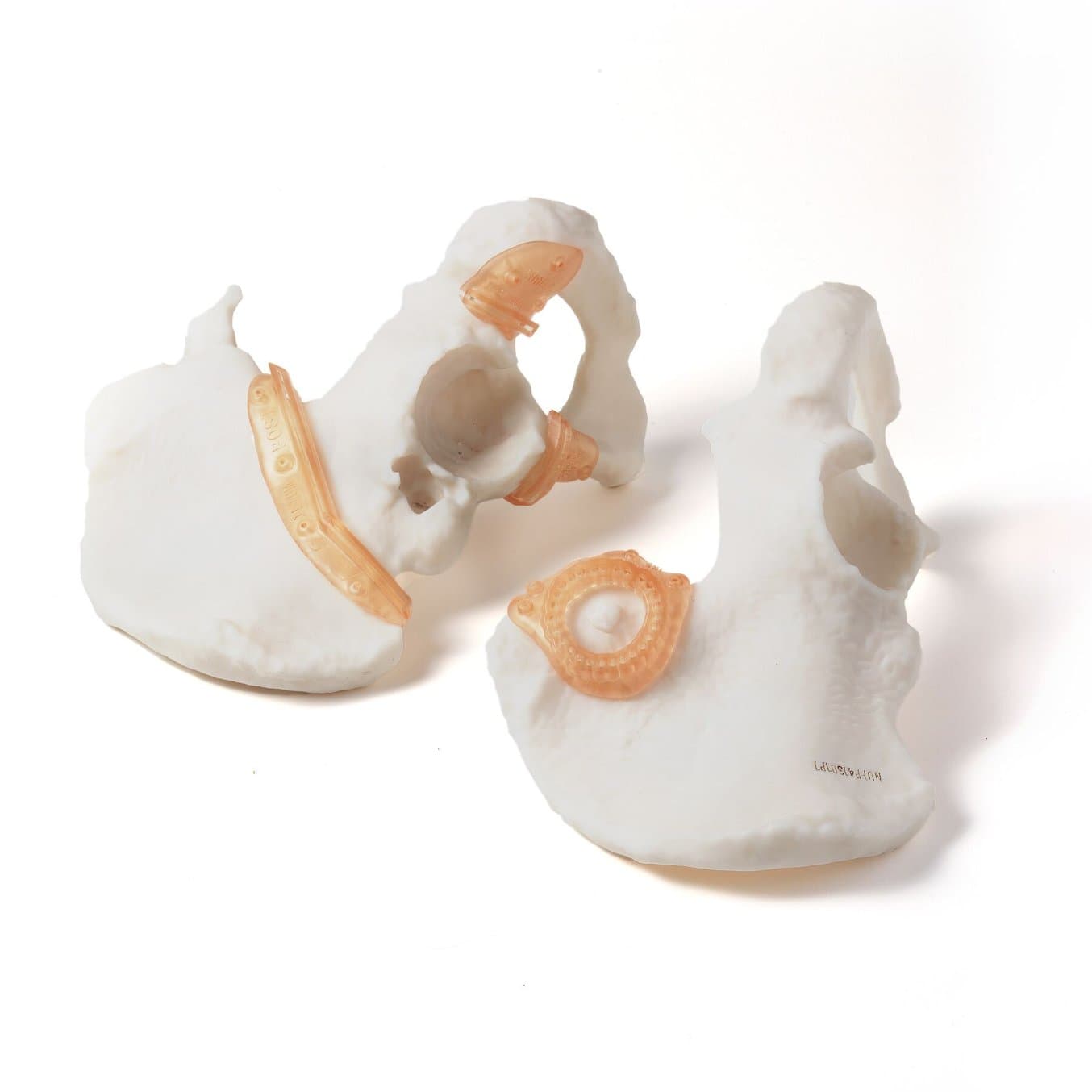
Biocompatibility, Materials & Strategies for Medical Additive Manufacturing
In this webinar, representatives from the FDA, industry, and healthcare discuss recent developments and address some intriguing questions:
Get Started With 3D Printing Medical Devices
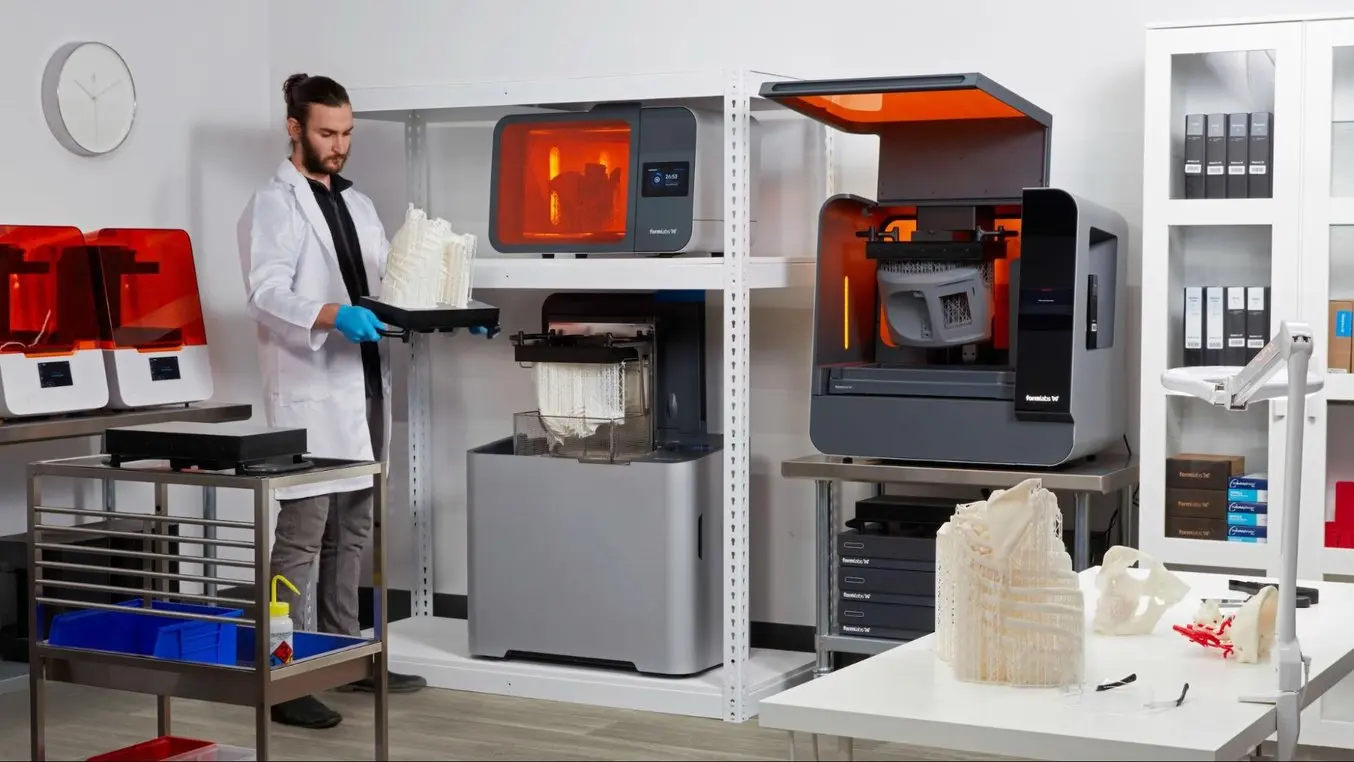
For medical device firms, in-house 3D printing allows quick iteration cycles, shortening the product development cycle and creating more time for creative solutions.
Every medical facility should have access to the latest tools to improve care and provide the best patient experience. Get started now or expand your in-house production with Formlabs, a proven, cutting-edge partner in medical 3D printing.
Reach out to our medical experts to learn more about how in-house 3D printing can supplement your current medical device design and manufacturing workflow.