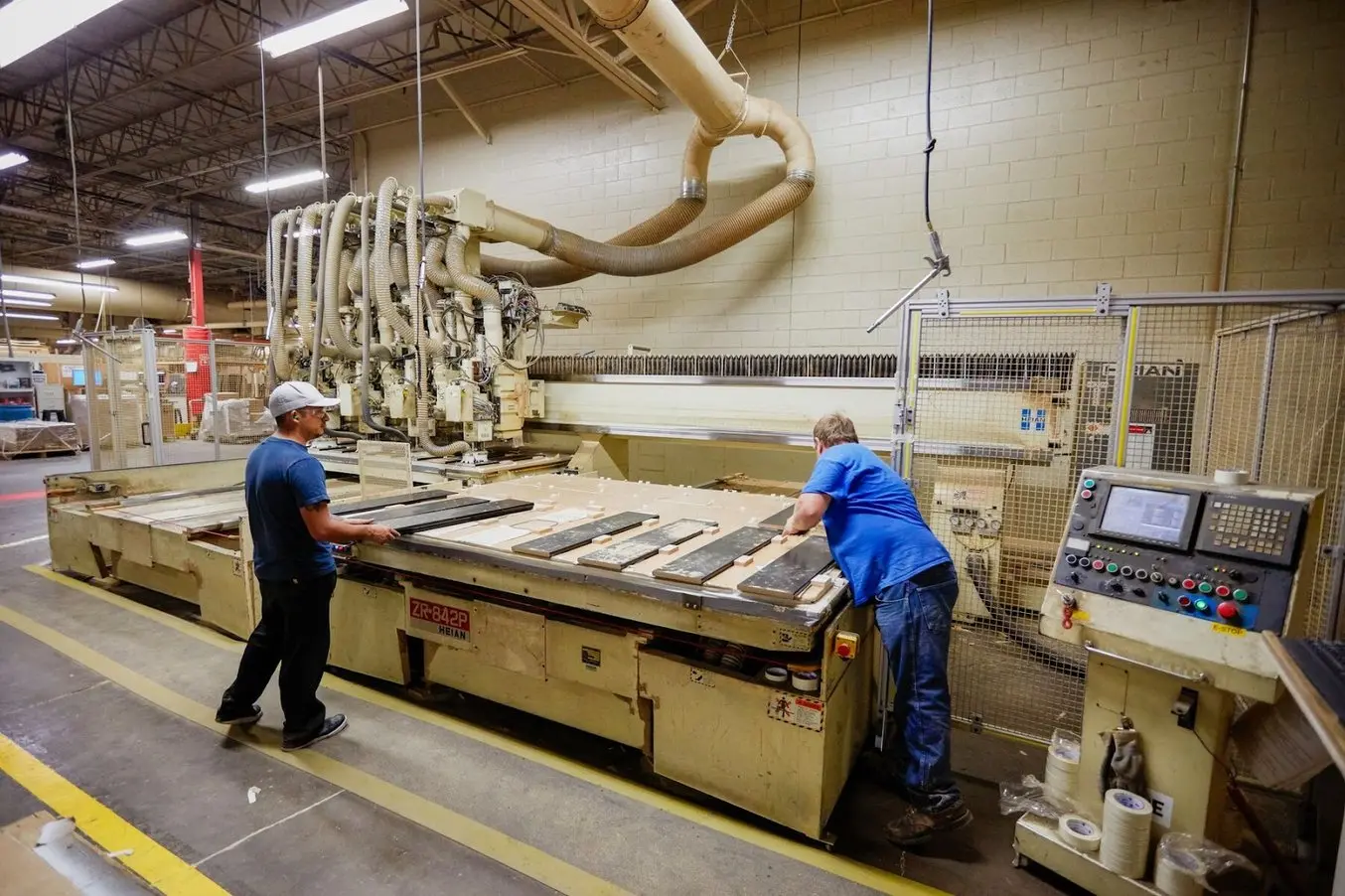
For manufacturers, maximizing production speed while maintaining high part quality is critical for success.
In this guide, we outline the principles behind creating effective jigs, fixtures, and other manufacturing aids in-house, with an emphasis on leveraging 3D printing to reduce costs, shorten development time, and create more efficient production workflows from design engineer to manufacturing floor technician.
What Are Jigs and Fixtures?
Jigs and fixtures are tools used in manufacturing and assembly processes to hold, support, fasten, or secure products and equipment.
In their most basic form, jigs and fixtures hold a part in a specific position while withstanding forces from a secondary operation — without the held part undergoing an unacceptable amount of deflection, movement, or rotation. As such, they’re part of a larger group of implements called manufacturing aids, because they facilitate, streamline, or improve the efficiency of various manufacturing and assembly processes.
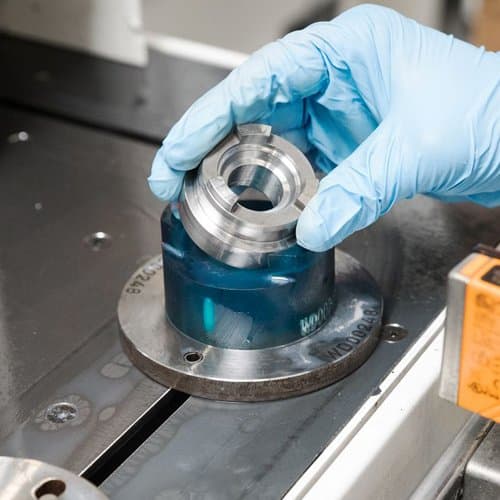
How to 3D Print In-House Jigs, Fixtures, and Other Manufacturing Aids
This white paper outlines the principles behind creating effective jigs, fixtures, and other manufacturing aids in-house.
The Difference Between Jigs and Fixtures
Though both jigs and fixtures are used in contact with products and are referred to as workholding devices, they do have slightly different uses:
-
Jigs: tools and devices designed to hold the workpiece, or product, while also guiding the equipment to ensure proper alignment and avoid misdirection or damages
-
Fixtures: clamps, jaws, vises, chucks, crankshafts, or other devices that hold the workpiece in place to secure it during secondary processes
Both jigs and fixtures are typically customized to closely match the unique geometry of a particular part, and in the case of jigs, may also be customized for the equipment. Jigs and fixtures are commonly used in processes like welding, drilling, molding, or assembly.
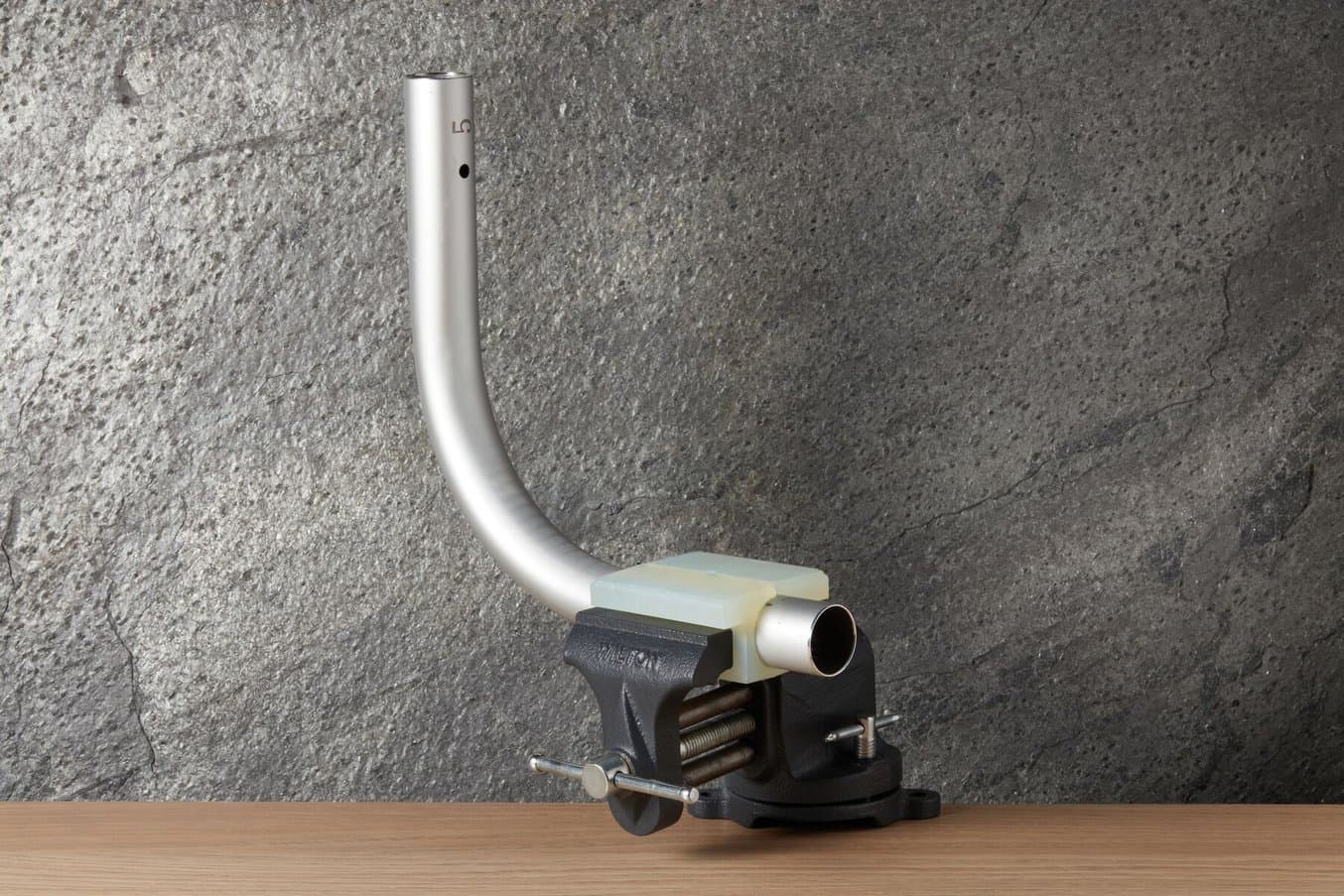
A jig or guide holds the workpiece and guides the tool printed in Durable Resin on a Formlabs SLA 3D printer.
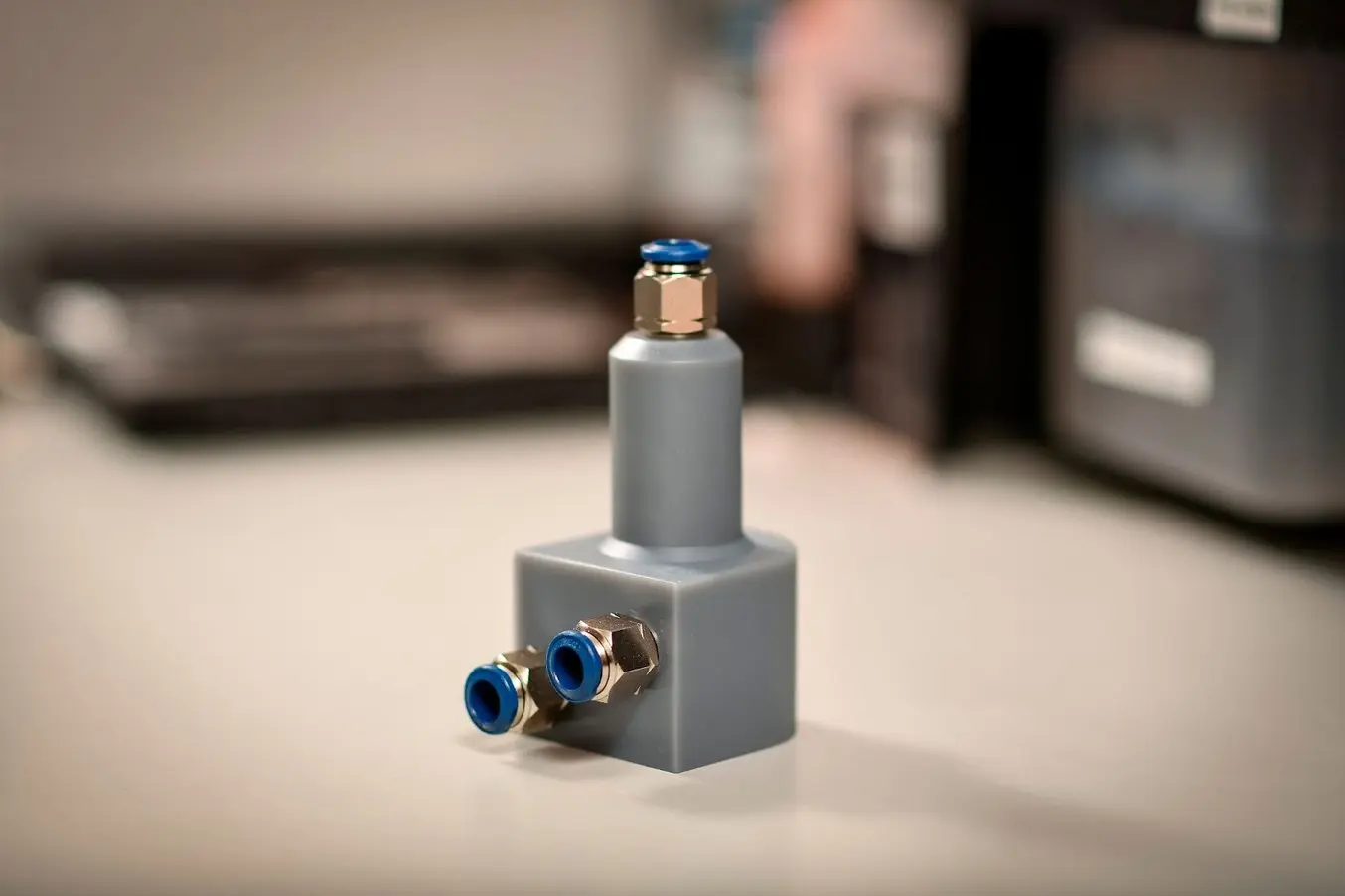
A test fixture by Dorman Products (right) for pressurized hose test and go/no-go gauges, 3D printed with the Form 3 in Grey Resin.
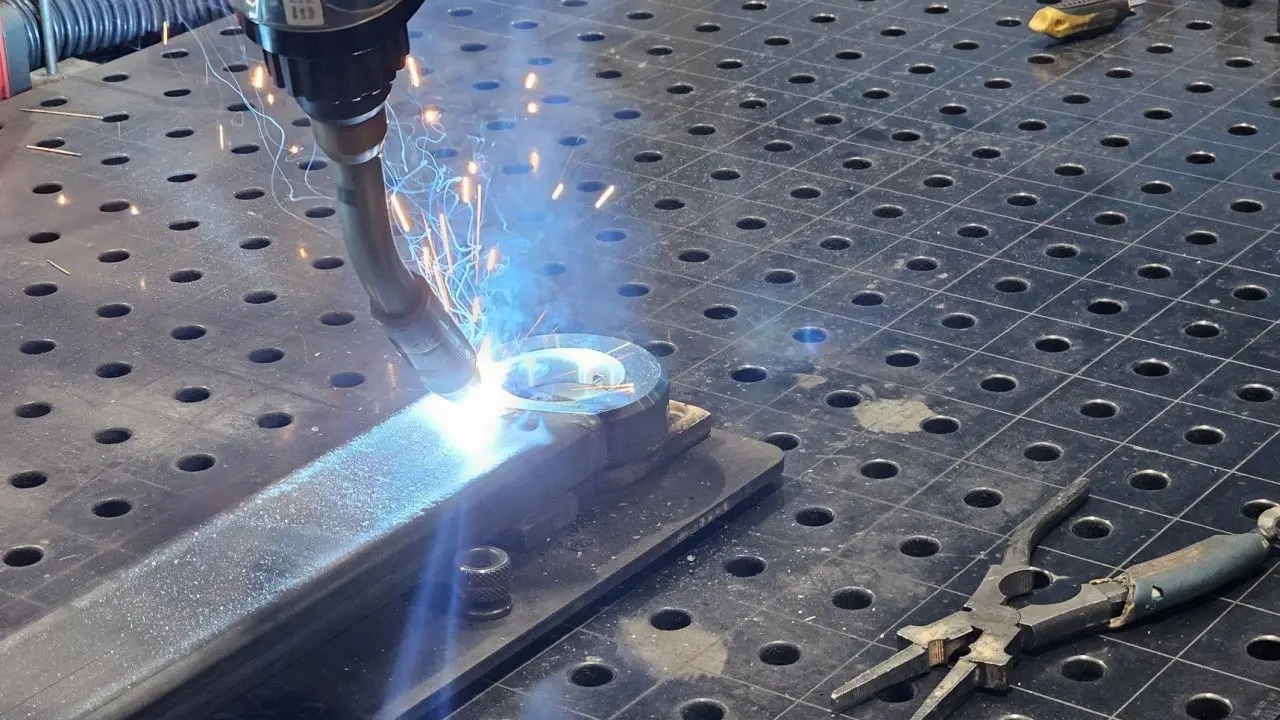
Quick Custom Welding Fixtures With 3D Printing
Discover how to streamline your tooling process to accelerate rapid prototyping and low-volume production of metal parts with quick and modulable welding fixtures. Our R&D machine shop coordinator shares methods and best practices for 3D printing welding fixtures, including design guidelines, tool temperature study, practical examples, and cost analysis.
What Are Jigs and Fixtures Used For
Jigs and fixtures are used in many different kinds of manufacturing processes, bolstering efficiency, solving problems, and reducing costs on the factory floor. Manufacturers use large standardized machines for repeated processes like milling, molding, or machining, but every product is different. Jigs and fixtures are the solutions that enable one machine to work for many different products.
Traditionally, many equipment manufacturers supply manufacturing aids along with their machines, but these aids are typically standardized to fit a certain assumed set of parts. Standardization also lends itself to heavier, bulky metal pieces that can be difficult to handle, and they may not fit the entire range of products that the machine purchaser will create. Customized jigs and fixtures are then needed to make the machines work even as new products and processes come through.
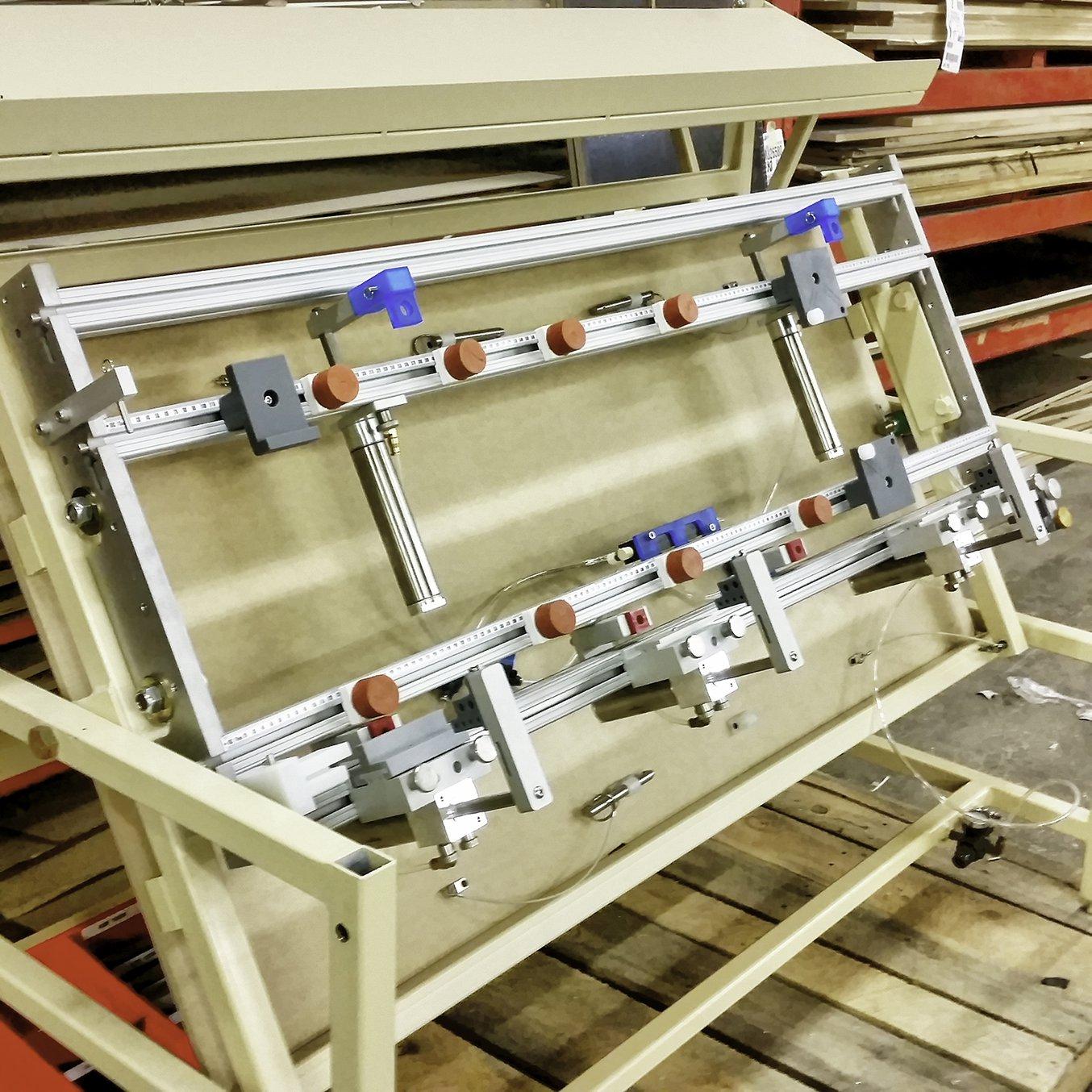
3D Print Jigs and Fixtures to Boost Manufacturing Efficiency
Watch this webinar to learn how to 3D print custom jigs, fixtures, and tools in-house to streamline manufacturing operations and reduce production costs.
Types of Jigs and Fixtures
There are as many types of jigs and fixtures as there are manufacturing processes and parts — each jig and fixture is designed to perform a specific function for a specific part. They may be as simple as blocks, or as complicated as multi-part crankshafts.
Here are several types of jigs and fixtures commonly used in manufacturing scenarios. Many of these jig types can also be used as fixtures — that is to say that a jig could guide a piece of equipment but may also just be holding the part in place.
Jigs | Fixtures | |||
---|---|---|---|---|
Molding jigs | Soft-jaw fixtures | |||
Machining jigs | Clamps | |||
Assembly jigs | Vises | |||
Painting/coating/post-processing jigs | Chucks | |||
Forming jigs | Crankshafts | |||
Inspection/checking fixtures |
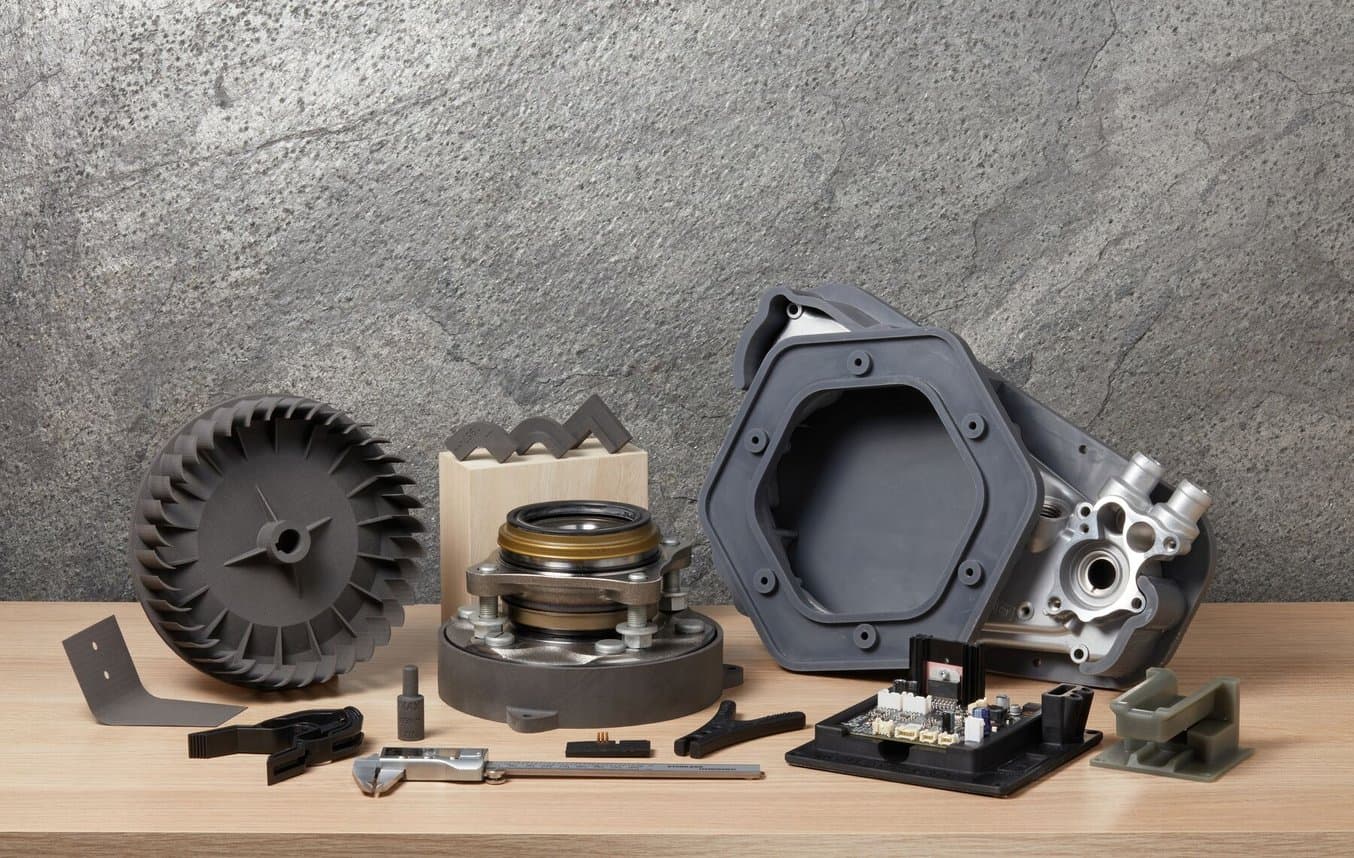
Jigs, fixtures, and replacement parts are all considered manufacturing aids, and can be efficiently and cost-effectively 3D printed in-house to reduce downtime and improve productivity.
How to Make Your Own Jigs and Fixtures
Traditionally, jigs and fixtures are molded, machined, or milled, and are often fabricated by the manufacturer of the machine on which they’ll eventually be used. For example, a drill manufacturer may make and provide a series of drill guide fixtures along with the drill. Though these jigs or fixtures may work for several parts, they’re designed for only a small subset of products, leaving manufacturers at a loss when they have a new or altered product.
Because of these limitations, 3D printing is becoming a more widely used method of fabricating manufacturing aids such as jigs and fixtures. 3D printed jigs and fixtures can be made on-demand and in-house, and are cost-efficient to produce in low quantities or for customized applications.
Designing Custom Jigs and Fixtures
Designing custom jigs and fixtures can be easily accomplished with appropriate measuring tools and a manufacturing method that enables complex geometries such as 3D printing. First, design the model in CAD based on CAD designs, caliper measurements, or 3D scans of the parts and equipment. Your resulting design can either be 3D printed, machined, or used as a master from which to create a mold.
Best Practices for Designing Customized Jigs and Fixtures
There are several ways to optimize your design process for customized jigs and fixtures, including:
-
Increasing geometric complexity: 3D printing enables complex features and the addition of numbers, names, dates, and other relevant information at no extra cost.
-
Reducing the number of parts: Multi-part jigs and fixtures have traditionally been molded with some degree of difficulty, but can often be 3D printed in one piece, simplifying the workflow.
-
Building datum features into the design: Jigs and fixtures that include an idealized feature, such as a perfect right angle, make the inspection of the finished part easier and more accurate.
-
Reinforcing to increase rigidity: Adding reinforcing ribs and fillets provides additional structure without dramatically increasing the cost or build time of the part.
-
Adding threaded inserts to improve durability: Add threaded inserts or pockets to 3D printed parts to restrain nuts while a bolt is tightened improves the durability of a 3D printed jig or fixture.
-
Making allowances to enable removal of machining debris: Adding grooves, channels, and rounded edges to jigs and fixtures facilitates easy removal of extra material while they’re being used to secure a part during subtractive processes that create debris.
-
Considering user experience: Design jigs or fixtures so they can be used with one hand, easily identify placement errors, and hold the part without human support or interaction.
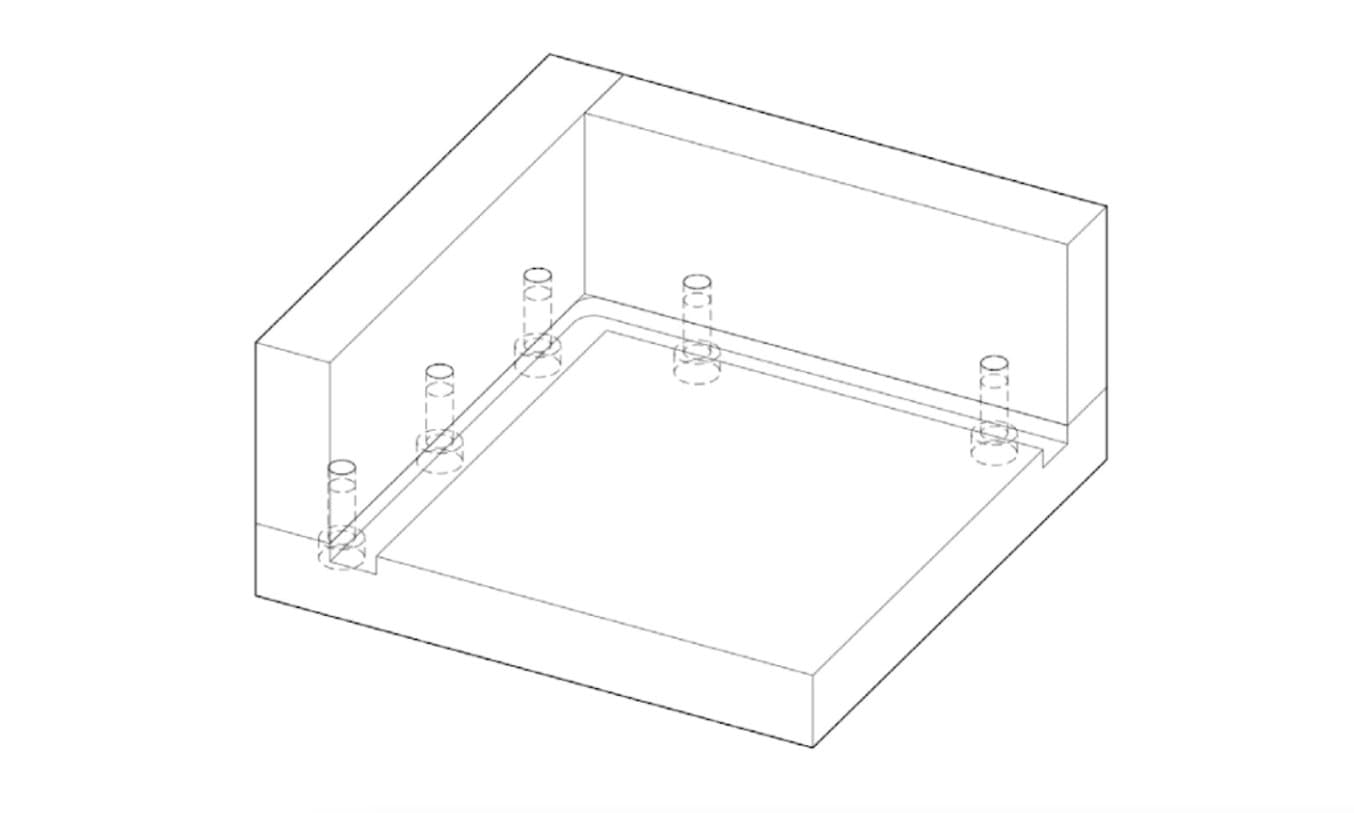
A typical milled and assembled corner locator, composed of three bolted plates creates more opportunities for chips to become wedged.
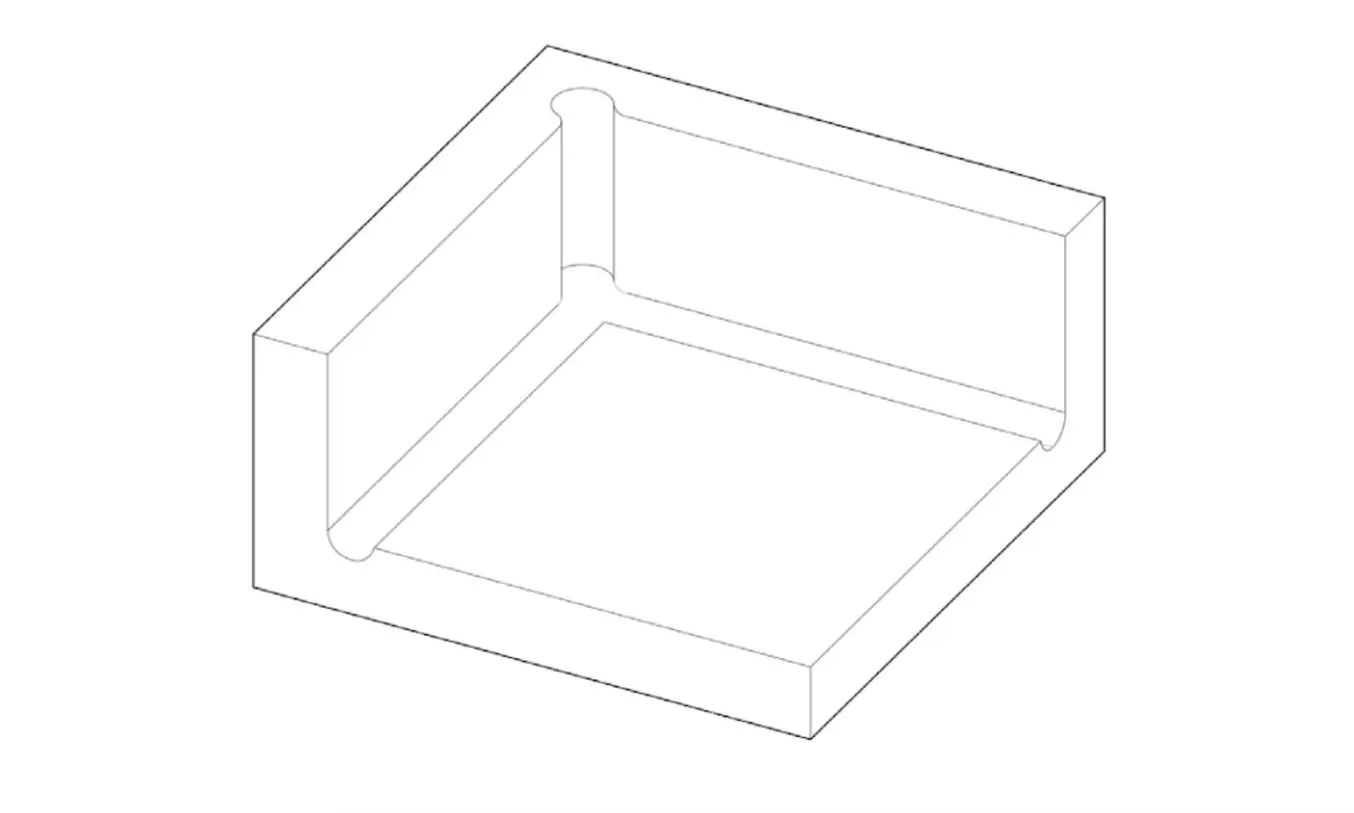
A typical geometry for a 3D printed corner locator with eased edges, smooth relief pockets, and no seams, all without increasing the cost of the part.
Materials for Custom Jigs and Fixtures
Jigs and fixtures can be made from a wide variety of materials, and are often made in the same materials (and through the same processes) as the workflow they support. Typically, manufacturers machine tooling in metal (though sometimes in POM (Delrin) or other plastics) either in-house or through outsourced vendors. Machining requires expensive equipment and skilled labor for CAM settings and machine operation. Besides, most tools are made of multiple-part assemblies, adding complexity. Outsourcing comes with weeks of lead time and high costs. As a result, producing such tools customized and just-in-time can be challenging. Depending on the forces experienced by the part, however, it is not always necessary to produce these tools in metal.
When choosing a material, consider cost, ease of manufacturing, lead time, and structural needs. Custom jigs and fixtures in a variety of plastic materials can be fabricated through additive manufacturing or through a more traditional process like milling.
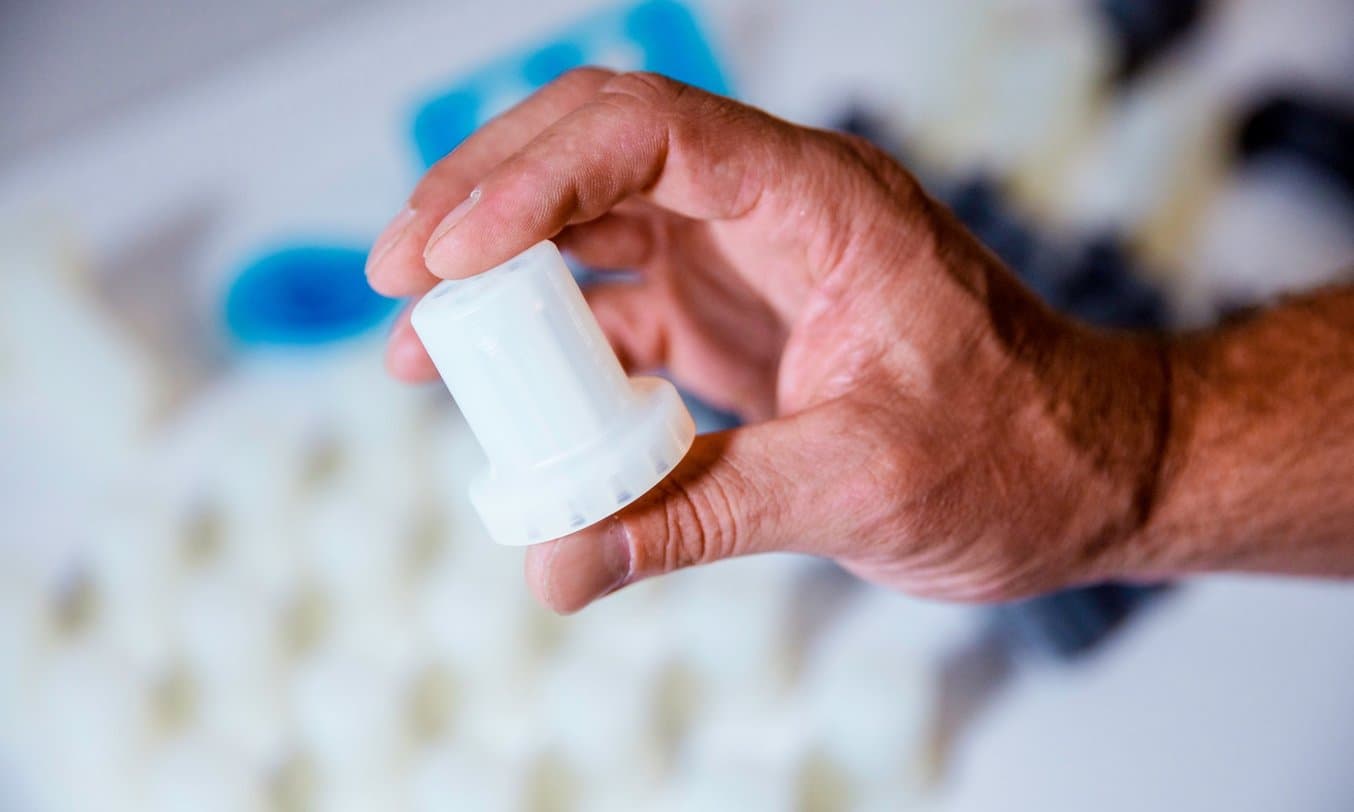
Ashley Furniture uses 3D printing to replace outsourced fixtures from a machine shop, cutting their cost in half.
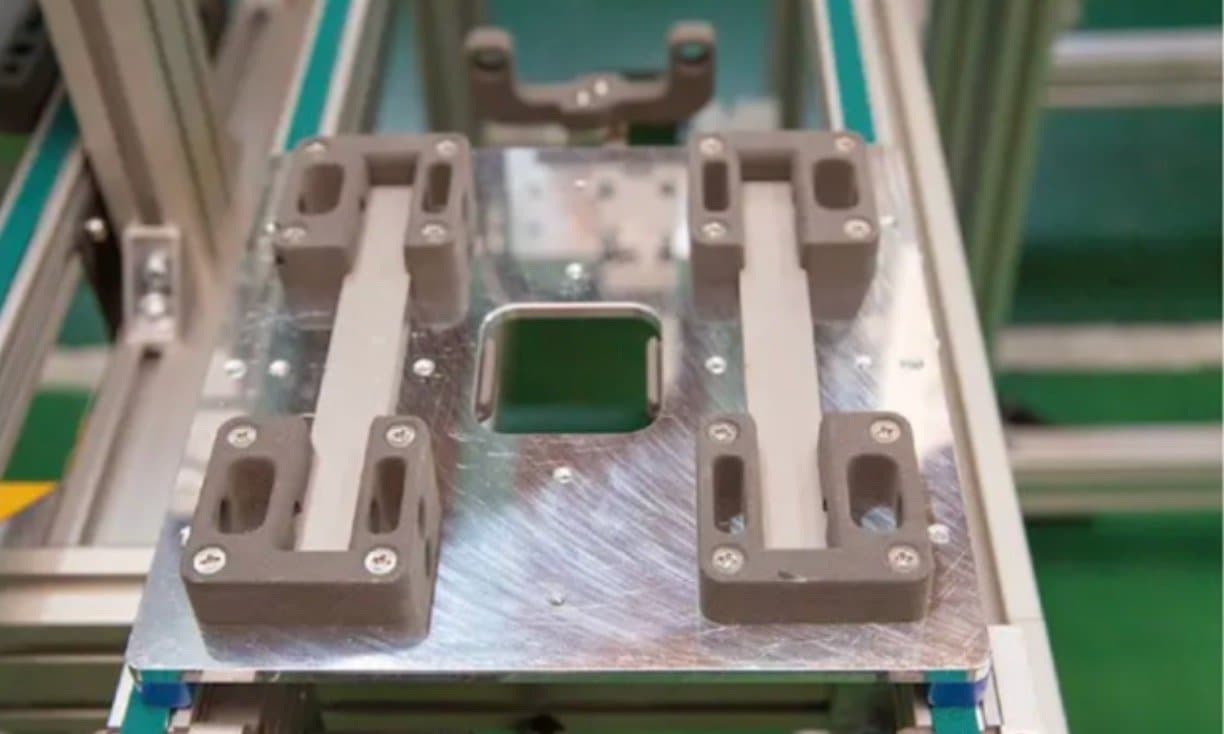
These alignment pins, printed on the Form 3 Series SLA printers in Durable Resin, quickly relocate pins on a simple grid work.
Koshi Kagaku Kogyo's automated assembly machines use many jigs and fixtures printed with Fuse 1 SLS 3D printer.
Additive manufactured plastics can have a range of materials properties, from softer durometer rubber-like materials such as Formlabs’ Elastic 50A Resin or Flexible 80A Resin, to stiff and strong materials such as PEEK, Formlabs Rigid 10K Resin or Formlabs SLS materials like Nylon 12 Powder. Specialty materials like ESD Resin offer unique advantages like safely dissipating electrostatic discharge, which is esssential for applications like electronics assembly.
This range of material options enables manufacturers to adjust their design or material choice based on performance, without rendering a machined or molded aid obsolete. Additively manufactured plastic jigs and fixtures often have much shorter lead times, and can be fabricated in-house in a matter of hours.
Metal jigs and fixtures should be still used for applications where there are intense high temperatures, very heavy loads, or where the process will remain the same through hundreds or thousands of repetitions — making wear and durability very important. Metal manufacturing aids are more expensive than plastic, often have a lead time of at least two weeks, and are heavier and less ergonomic.
Manufacturing Methods for Custom Jigs and Fixtures
Jigs and fixtures are typically required in low volumes or as single parts. One manufacturing aid can often be used for many repetitions of a process, or they are required for a customized process that won’t be repeated. Based on the required quantity, most are manufactured by either milling, a subtractive process that carves a part from a solid block of material, or through additive manufacturing, also known as 3D printing. These two processes lend themselves to highly accurate and customized parts, and often have shorter lead times than traditional multi-step processes like molding.
If the application requires a metal jig of fixture, for a high heat or high force application, machining is the appropriate fabrication method. However, as 3D printing technologies advance in terms of accuracy and material availability, they present an alternative that is often more affordable and faster. In many cases, manufacturers can rely on advanced polymers, like Rigid 10K Resin or Nylon Powders, for jigs and fixtures that were previously only done with metals.
3D Printing Custom Jigs and Fixtures
Over the last few years, high-resolution 3D printers have become more affordable, easier to use, and more reliable. As a result, 3D printing technology is now accessible to more businesses, but choosing between the various competing 3D printing solutions can be difficult. Read this technology guide to compare the three most established 3D printing technologies, fused deposition modeling (FDM), stereolithography (SLA), and selective laser sintering (SLS).
3D printed jigs and fixtures are often fabricated with FDM because it is fast, easy to use, and low cost. However, SLA and SLS are better suited for manufacturing aids that require:
-
Higher resolution, better accuracy, and a smoother surface finish
-
Superior mechanical characteristics, such as strength and durability
-
Complex designs
-
Higher throughput
The following table summarizes some key considerations to choose between SLA or SLS for 3D printing manufacturing aids. Check out Formlabs’ in-depth technology comparison for more details.
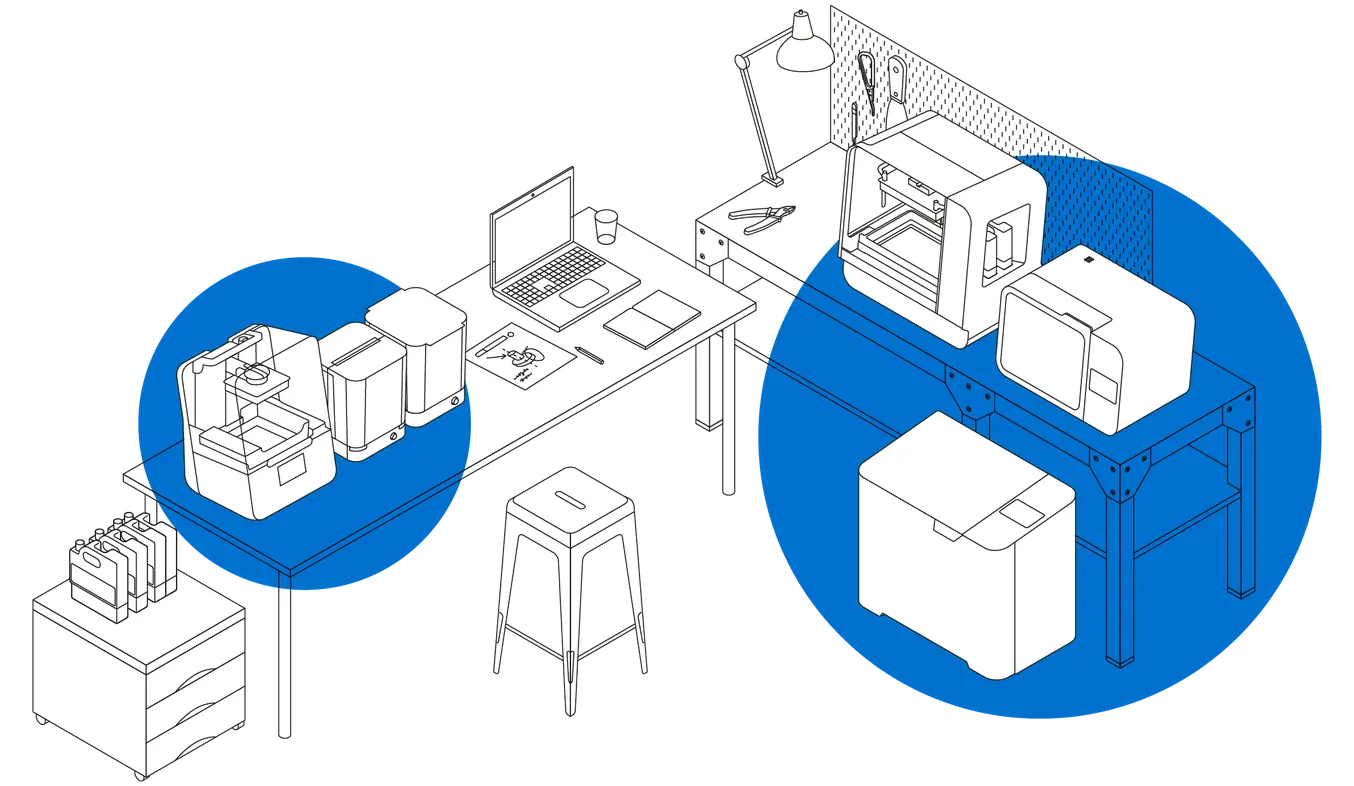
SLA 3D Printing - Form Series
- Fine details and smooth surface finish
- Wider range of materials
- Easier to use
- Lower hardware costs
SLA 3D Printing - Form Series |
---|
Fine details and smooth surface finish |
Wider range of materials |
Easier to use |
Lower hardware costs |
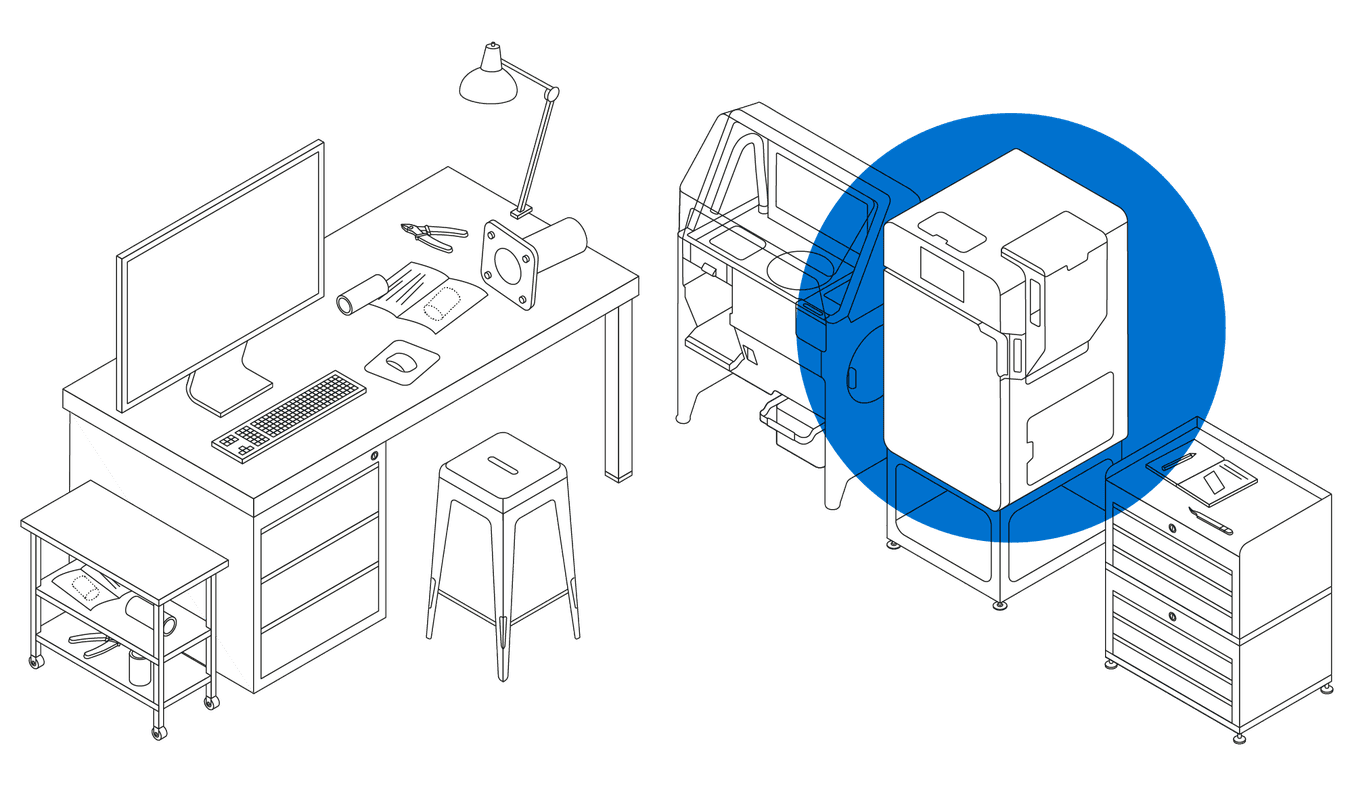
SLS 3D Printing - Fuse Series
- Sturdy, stable, and long-lasting tools
- No supports, better suited for complex designs
- Higher throughput
- More cost-efficient for large production
SLS 3D Printing - Fuse Series |
---|
Sturdy, stable, and long-lasting tools |
No supports, better suited for complex designs |
Higher throughput |
More cost-efficient for large production |
Benefits of 3D Printed Jigs and Fixtures
Additive manufacturing (AM), also known as 3D printing, is a powerful solution to fabricate manufacturing aids rapidly and at a low cost in-house. 3D printing jigs and fixtures is one way for manufacturers to gain greater control over their supply chain, increase operational efficiency, lower costs, and reduce instances of mistakes, damaged goods, or waste.
Accessibility of 3D Printed Jigs and Fixtures
3D printers can be purchased and brought in-house with relatively low overhead costs or footprint requirements. Desktop 3D printers like the Formlabs Form 3+ cost as low as $2500, and enable a wide range of material properties. Benchtop machines like the Formlabs Form 3L SLA 3D printer, or industrial power laser sintering technologies like the Fuse Series SLS 3D printer are also accessibly priced and don’t require the complex infrastructure systems of many traditional large 3D printers.
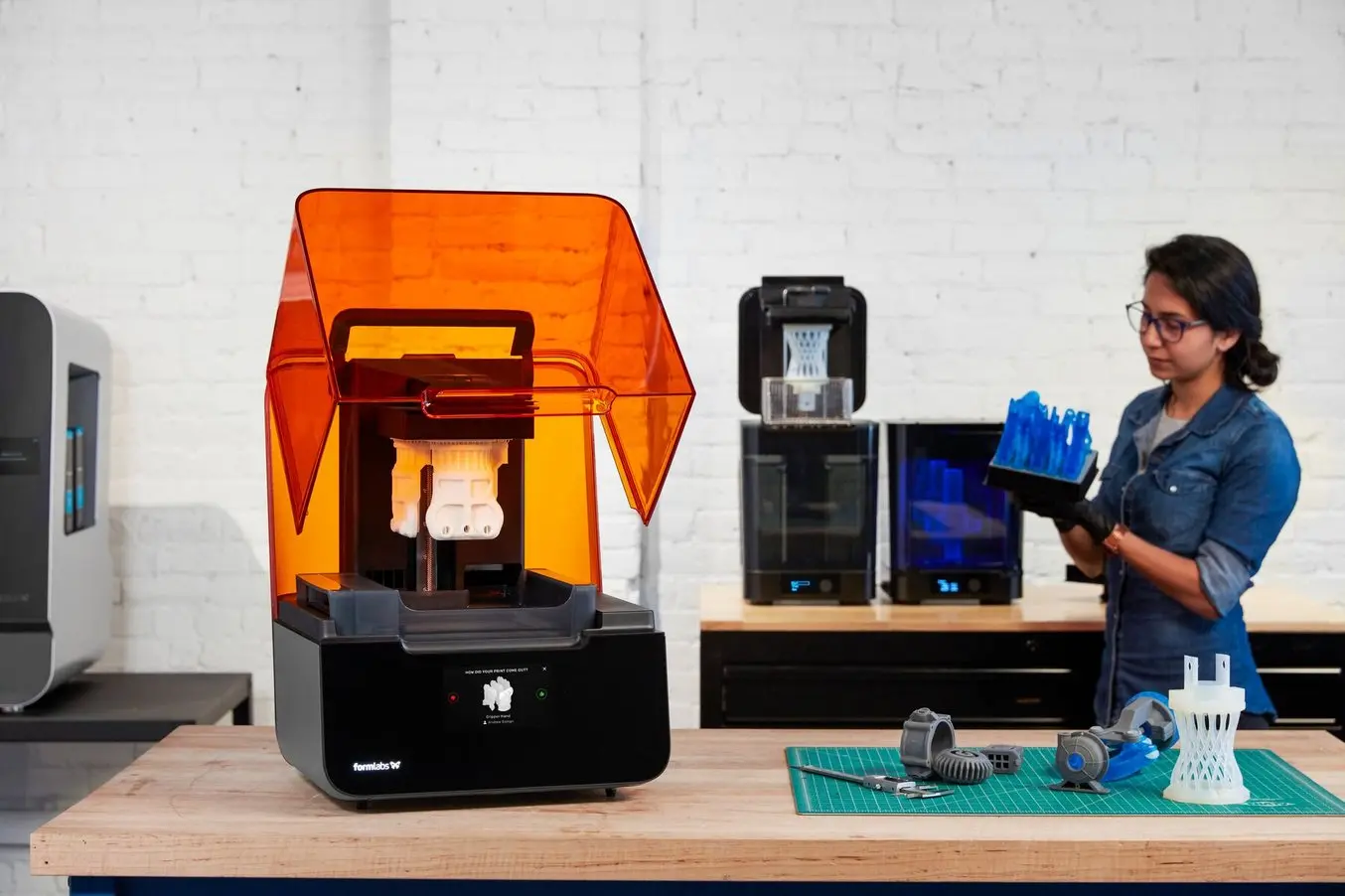
The Form 3+ is an affordable, industrial-quality desktop SLA 3D printer.

The Fuse Series SLS 3D printers have a convenient, intuitive workflow, small footprint, and affordable price.
Greater Control Over Supply Chain
Having these technologies in-house means that employees responsible for one process, such as thermoforming or painting, can easily access the 3D printing technology to produce a custom jig or fixture. The whole process can take less than a day, reducing downtime and making almost immediate improvements to workflow. The manufacturer controls more of the elements involved in production and can easily pinpoint any areas where a customized jig or fixture could immediately make a positive impact on the workflow.
Reducing Damaged Goods With 3D Printed Jigs and Fixtures
3D printing is a good solution for creating jigs and fixtures to reduce instances of damaged goods or equipment. Traditional workholding systems like vises and clamps can’t secure and support amorphous shapes or parts with very fine details. If they’re used, they can cause damage by virtue of a poor fit or forced attachment. For example, locating fixtures that are 3D printed in a softer durometer material might reduce jarring from the assembly process compared to rigid fixtures made from a milled plastic or metal block.
Case Studies
Machining Hardware: Custom Jigs for Automatic Lathes
Automotive supplier Pankl Racing Systems specializes in developing engine and drivetrain components for racing cars, high-performance vehicles, and aerospace applications. They introduced SLA 3D printing in-house to produce custom jigs and other tooling.
For one particular order, they had to manufacture motorcycle gearbox assemblies through multiple stages of steel machining using automatic lathes. Each stage of turning in the automatic lathes requires custom jigs for every individual gear type. They were looking at a six-week lead time to outsource the jigs. By 3D printing them in-house with the Formlabs SLA printers, they decreased lead time by 90 percent and costs by 80-90 percent, leading to €150,000 in savings.
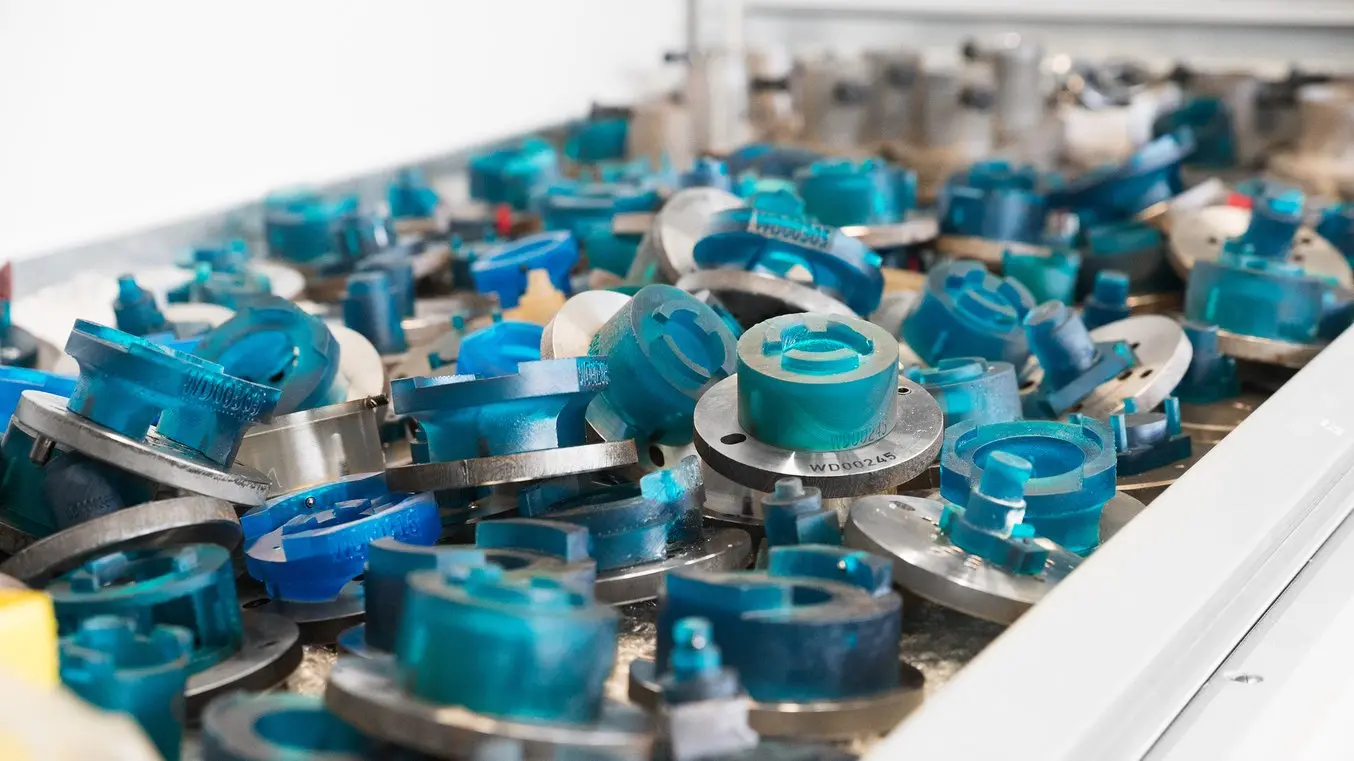
The jigs are 3D printed in Tough Resin and attached to the conveyor belt using standard shuttles. Each jig is printed with a unique identifier on its side.
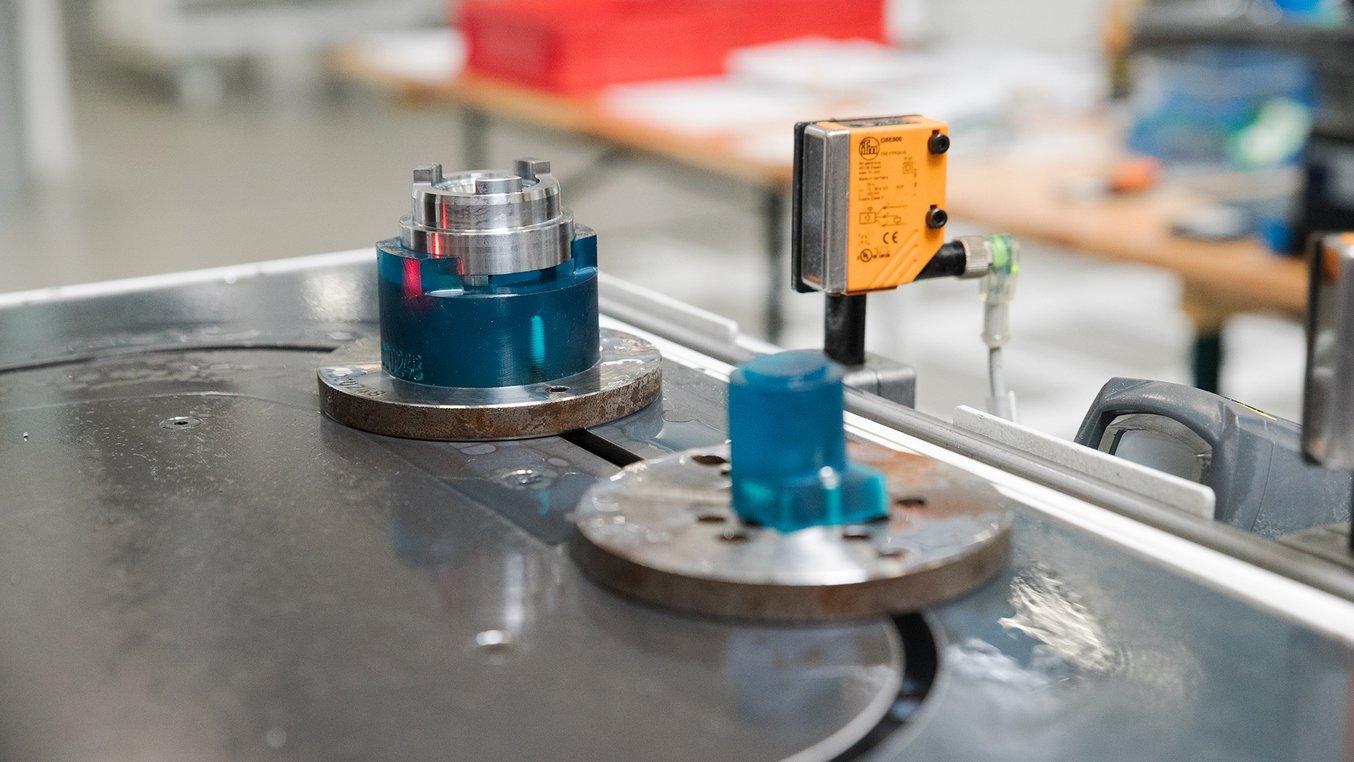
Pankl uses Formlabs printers and materials to streamline their operations and reduce costs during fabrication and assembly.
Thermoforming Different-Sized Sheets: Clamping Fixtures at Productive Plastics
Thermoforming is a manufacturing process that heats and molds sheets of plastic into a desired shape under vacuum, pressure, or mechanical forces. For one job at Productive Plastics, the machine clamp frame was bigger than the mold, meaning had to stop to wait for a customized spacing fixture, or an unnecessarily large plastic sheet would have to be used, adding to costs. Productive Plastics used in-house 3D printing to fabricate a customized fixture that corrected the spacing between the mold and the frame.
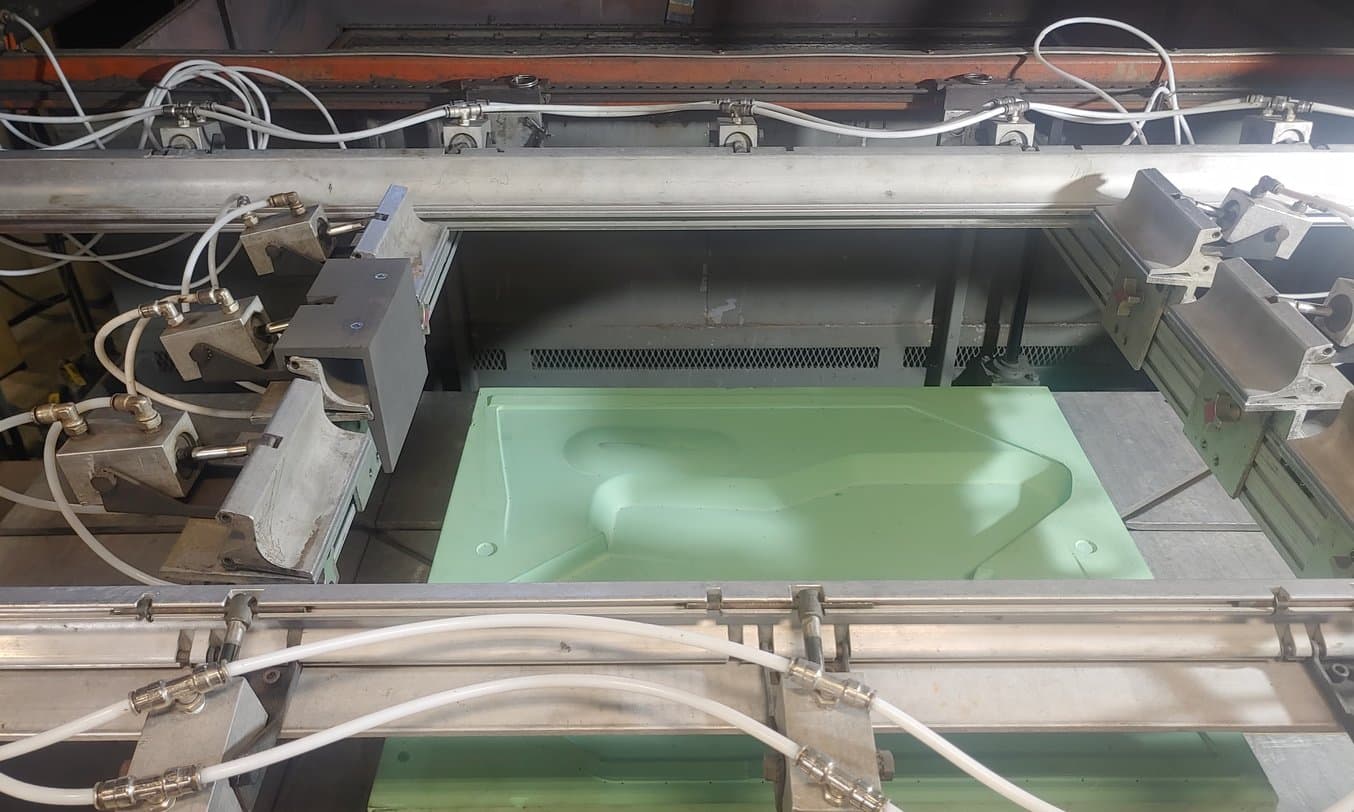
The clamping fixture is designed to secure 0.25 in (0.63 cm) spacing. It was 3D printed on the Fuse 1 in Nylon 12 Powder for strength and durability.
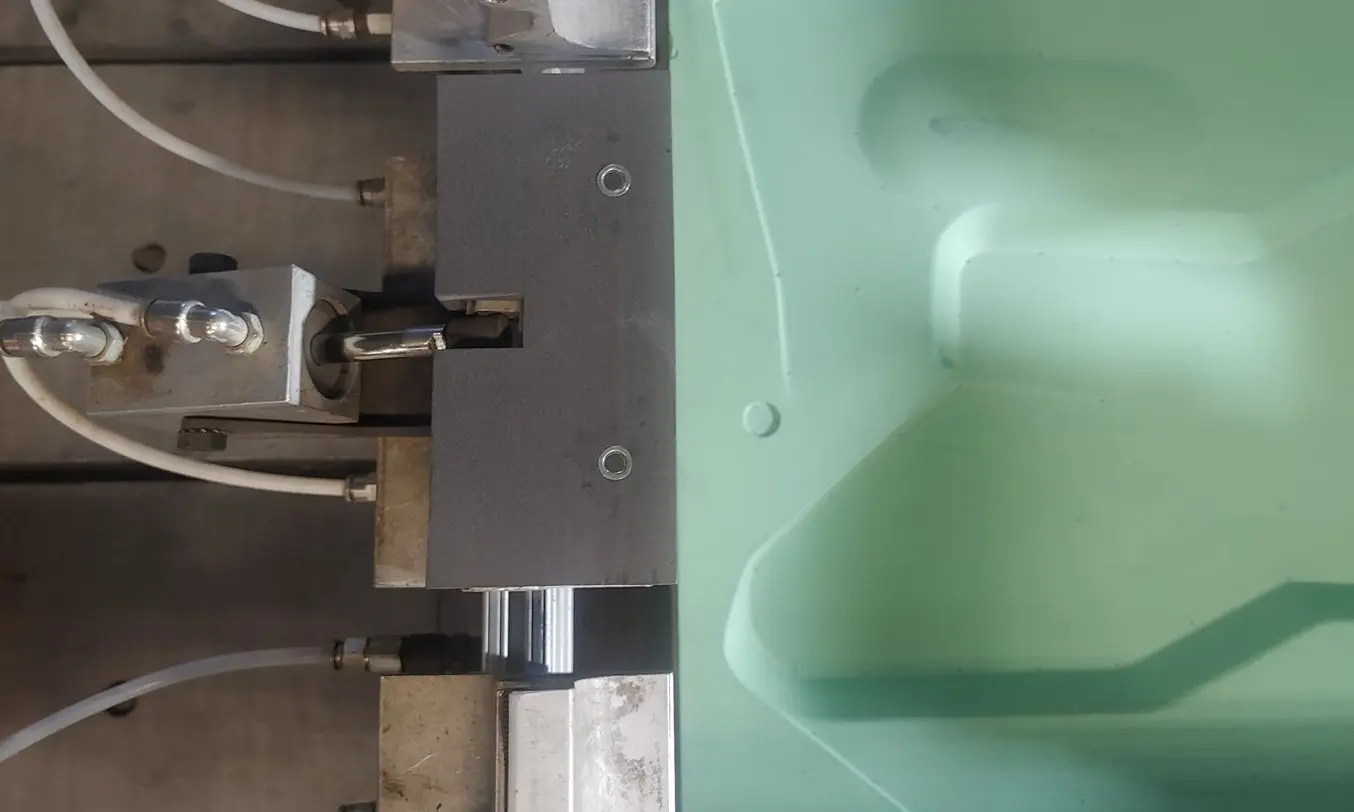
No further finishing methods were necessary; the fixture fit directly onto the equipment.
Jigs and Fixtures Costs
Producing customized parts has traditionally been an expensive process, but with the advance of additive manufacturing, customization is both affordable and accessible. For jigs and fixtures, that means a wider range of possible geometries and a better fit for specific processes that had previously been reliant on standardized parts. Customized, on-demand jigs and fixtures also make manual processes like many kinds of assembly or packaging much easier, and can reduce the workload for factory employees, freeing up their time for higher value tasks.
3D printed | CNC Machined | |||
---|---|---|---|---|
Lead time | 5-9 hours | 2-3 weeks | ||
Cost | $9-$28 | $45-$340 |
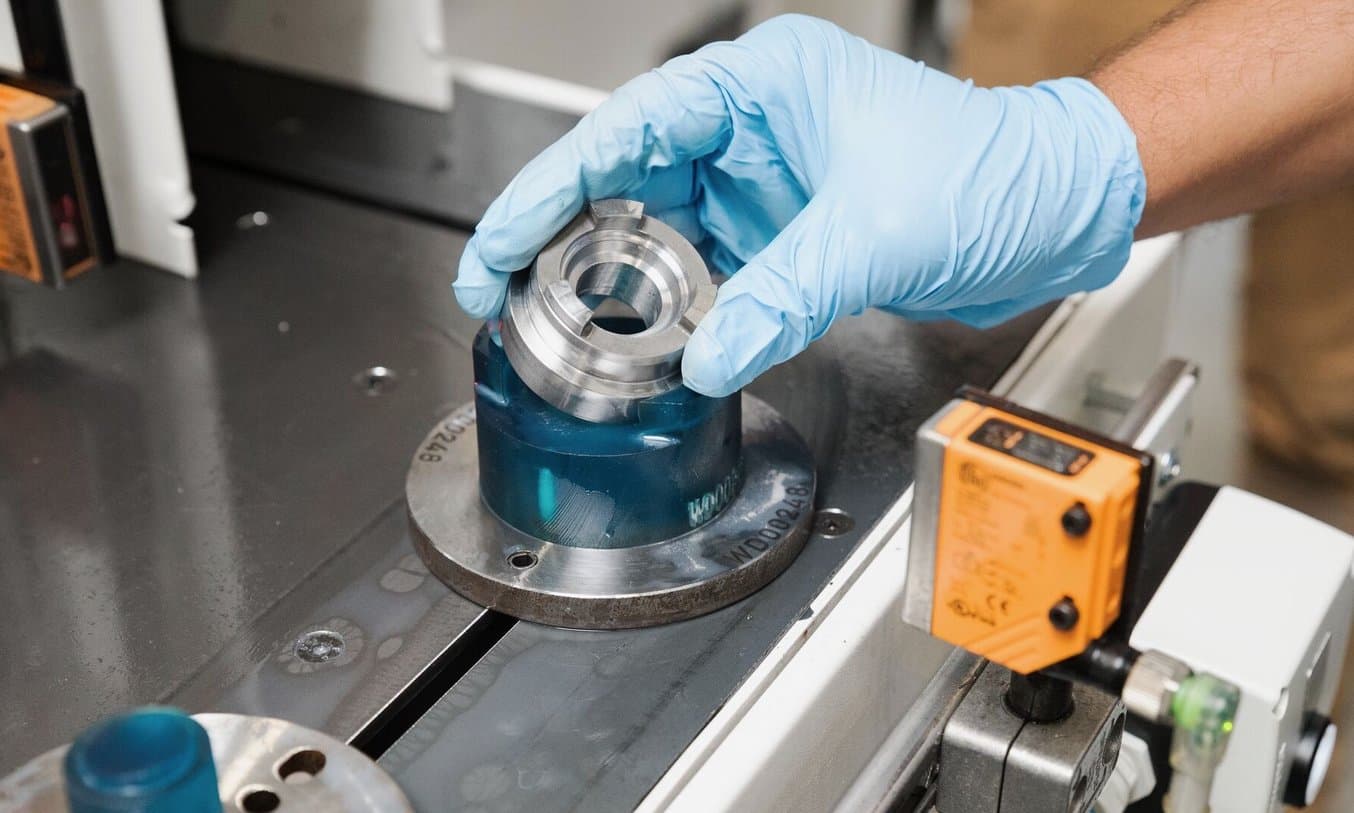
Looking at the cost comparison of Pankl Racing Systems jigs production: in-house 3D printing is 48x faster and 12x cheaper than outsourcing milling.
In-House Production vs. Outsourcing
In-house fabrication of 3D printed jigs and fixtures can reduce downtime by shortening the distance between the issue and the solution. Employees familiar with the manufacturing flow can identify issues before they arise, and design jigs and fixtures to streamline processes before problems come up. By easily communicating with their colleagues, they can identify pain points and design jigs and fixtures within 24 hours that make processes safer, more efficient, or more precise.
Comparatively, outsourcing jigs and fixtures is inherently reactive — and a customized manufacturing aid that solves a problem after it arises may cause days or weeks of downtime.
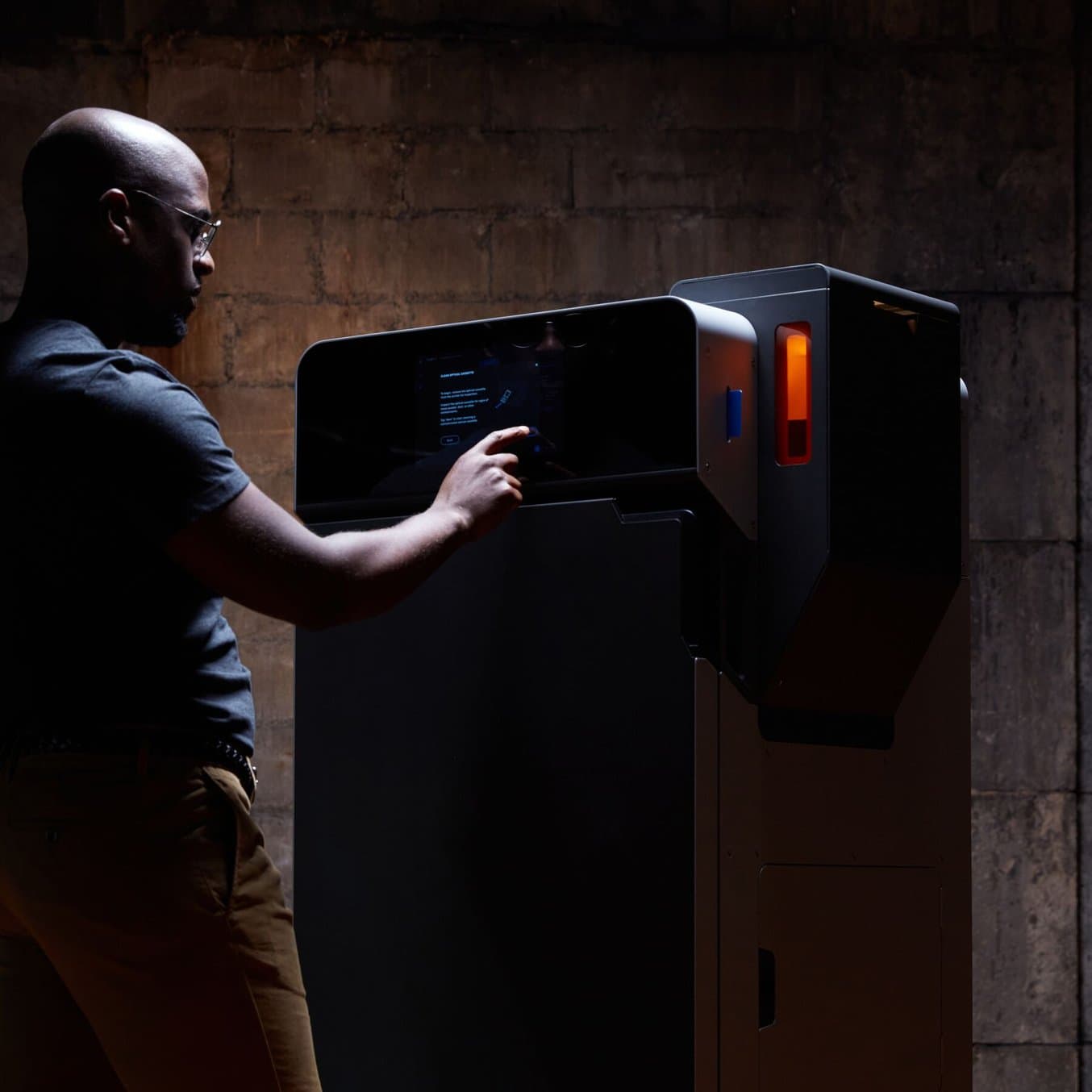
Outsourcing vs. In-House: When Does it Make Sense to Bring SLS 3D Printing In-House?
In this white paper, we evaluate the value proposition of bringing SLS 3D printers in-house, in comparison with outsourcing SLS parts from a service bureau.
Get Started With Custom Jigs and Fixtures
Modern factories must constantly adapt to changing customer requirements and look for new ways to stay efficient, nimble, and competitive. Companies are already leveraging the power of in-house 3D printing technology for other applications, such as rapid prototyping, rapid tooling fabrication, and end-use part production. Read Formlabs’ guides to learn how 3D printed parts can replace traditional methods in these applications.
Manufacturing aids, like custom jigs and fixtures, can improve all facets of production; they are enormously beneficial to manufacturing operations, reducing downtime, improving efficiency, avoiding loss of material or equipment damage, and boosting production. With in-house 3D printing technology, the same teams that are in charge of production can take ownership of their processes, and create customized parts for their unique workflows.
3D printing offers a range of material properties and an affordable way of producing strong, geometrically complex jigs or fixtures that can support any workflow. Both SLA and SLS systems are affordable and easy to integrate into an existing shop atmosphere, enabling manufacturers to get started with this workflow immediately.
Download our white paper for detailed guidelines on designing and manufacturing jigs and fixtures, and contact our 3D printing specialists to find the right solution for your application.