Nove applicazioni della produzione additiva nel settore aerospaziale
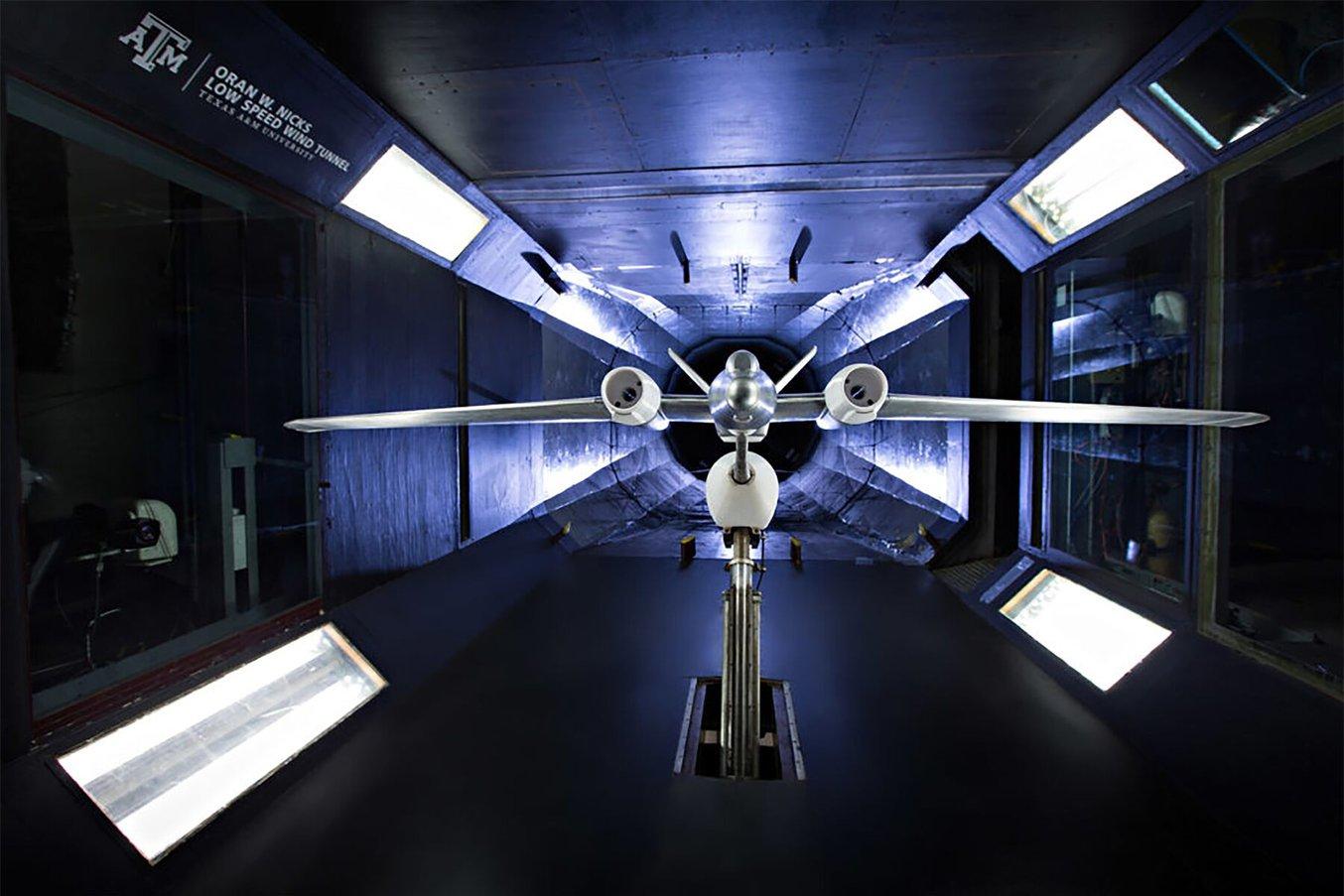
La produzione additiva, chiamata anche stampa 3D, ha molte applicazioni nel settore aerospaziale, dalla progettazione alla produzione e oltre.
Il settore aerospaziale è stato uno dei primi ad adottare la stampa 3D, o produzione additiva, quando è stata inventata. Molte aziende produttrici di parti originali, fornitori e agenzie governative la usano già da decenni e le ultime generazioni di aeromobili commerciali includono migliaia di parti stampate in 3D.
Tuttavia, tranne che per le organizzazioni più grandi e finanziariamente forti, le stampanti 3D industriali tradizionali hanno un costo generalmente proibitivo. Negli ultimi 10 anni abbiamo assistito a un forte calo dei prezzi delle stampanti 3D, anche quelle più avanzate, che combinato ai progressi nel campo della scienza dei materiali ha aperto la strada a numerose applicazioni ad alte prestazioni. Quando hanno un prezzo accessibile, le stampanti 3D possono essere usate anche nelle piccole organizzazioni o nei nuovi dipartimenti di grandi organizzazioni, dove in passato sarebbero state relegate a officine di prototipazione centralizzate. Estendendo l'accesso alla tecnologia additiva a un maggior numero di utenti finali, le stampanti 3D Formlabs possono essere usate dai team di ingegneria e ricerca aerospaziale per ampliare sempre di più i confini del settore.
Scopri i nove modi in cui la stampa 3D sta promuovendo l'innovazione nel settore aerospaziale, dal design alla produzione e oltre.
Stampa 3D per lo sviluppo di prodotti aerospaziali
1. Prototipi rapidi stampati in 3D per test funzionali su motori a razzo
Gravity Industries sta sviluppando una speciale tuta a propulsione che sembra uscita direttamente da un film di fantascienza. La Jet Suit è progettata per le operazioni di ricerca e salvataggio in aree in cui un elicottero non può arrivare o atterrare in sicurezza. Utilizzando diverse tecnologie di stampa 3D, l'azienda ha accelerato il processo di prototipazione ed eseguito numerosi test, identificando la resina fotopolimerica termoindurente come il migliore materiale a disposizione.
Sam Rogers, pilota collaudatore e capo designer, ha usato parti stampate in Clear Resin sulla Form 3 per sviluppare il sistema di accensione di un motore a razzo con raffreddamento a vortice. Grazie alla sua trasparenza, il materiale si è rivelato perfetto per le condizioni di prova e ha permesso di osservare gli schemi di combustione all'interno del componente.
Per testare il design, Rogers ha progettato una camera modulare che consentisse di combinare versioni diverse di camera e ugello. Attraverso la generazione di uno "scudo a vortice di ossigeno", che serviva a mantenere il calore lontano dalle pareti della camera, le parti in resina arrivavano a resistere diversi secondi. Questa durata era sufficiente per riuscire a osservare lo schema di accensione durante ogni test.
Se Rogers avesse realizzato ognuno delle decine di design di prova in metallo, la spesa sarebbe stata esorbitante. Invece, trattandosi di test brevi con costi dei materiali molto bassi, ha ottenuto parti ad alte prestazioni con spese e tempi di realizzazione minimi.
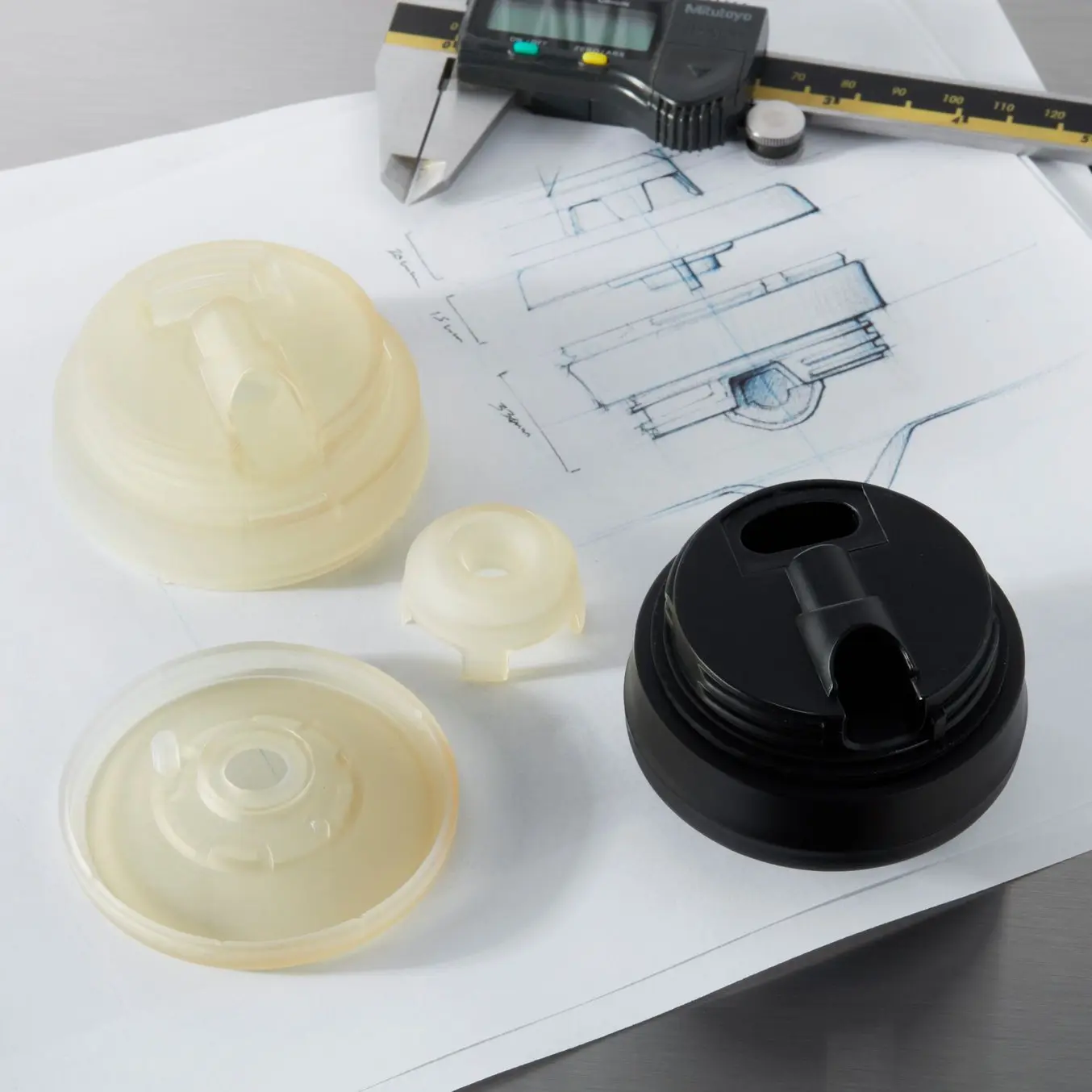
La guida definitiva alla prototipazione rapida per lo sviluppo di nuovi prodotti
In questa guida scoprirai come la prototipazione rapida si inserisce all'interno del processo di sviluppo dei prodotti, quali sono le sue applicazioni e quali strumenti per la prototipazione rapida hanno a disposizione oggigiorno i team di sviluppo.
2. Creazione di parti complesse per razzi con la stampa 3D
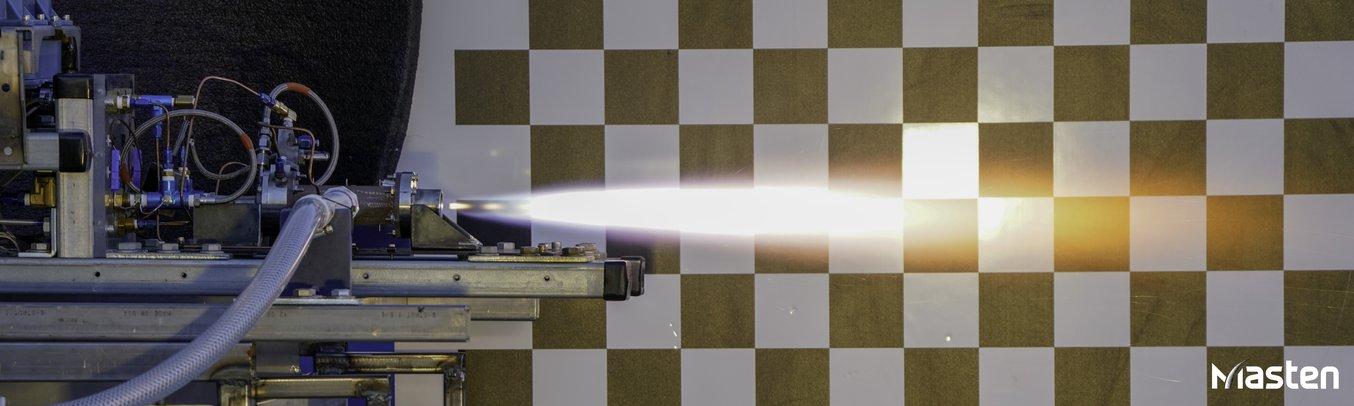
Masten Space Systems produce parti complesse per razzi con la stampa 3D.
Masten Space Systems è un'azienda specializzata in missilistica a decollo e atterraggio verticale. Ha iniziato a stampare in 3D motori a razzo nel 2014, partendo da piccoli propulsori di prova, e nel 2016 è arrivata a realizzare un motore a propulsione Broadsword da oltre 11 tonnellate. I materiali scelti per la produzione additiva includevano sia plastiche che metalli. Come spiega Kimberly Devore, ingegnera di ricerca e sperimentazione presso Masten, i motori a razzo sono stati prodotti usando sia la lavorazione meccanica tradizionale che la stampa 3D. Pur continuando a usare metodi di produzione tradizionale per i motori meno recenti, l'azienda ha implementato la stampa 3D per aumentare flessibilità di progettazione e velocità di produzione.
"Il grande vantaggio [della stampa 3D] è la possibilità di creare modelli con esattamente le caratteristiche che vuoi. E rispetto alla lavorazione meccanica tradizionale, non richiede lo stesso livello di iterazioni. La libertà di progettazione che offre è davvero impareggiabile", commenta Devore. "Molte volte, la lavorazione meccanica tradizionale ci obbligava a giocare al ribasso. Ogni dettaglio extra significava costi aggiuntivi".
Con la stampa 3D, invece, è possibile aumentare la complessità per migliorare le prestazioni, il tutto senza rischi o costi aggiuntivi, permettendo di sperimentare e produrre più parti in modo rapido ed economico. "Poter eseguire iterazioni rapide di questi oggetti è fantastico".
3. Prototipazione di attrezzature per il settore aerospaziale con la stampa 3D
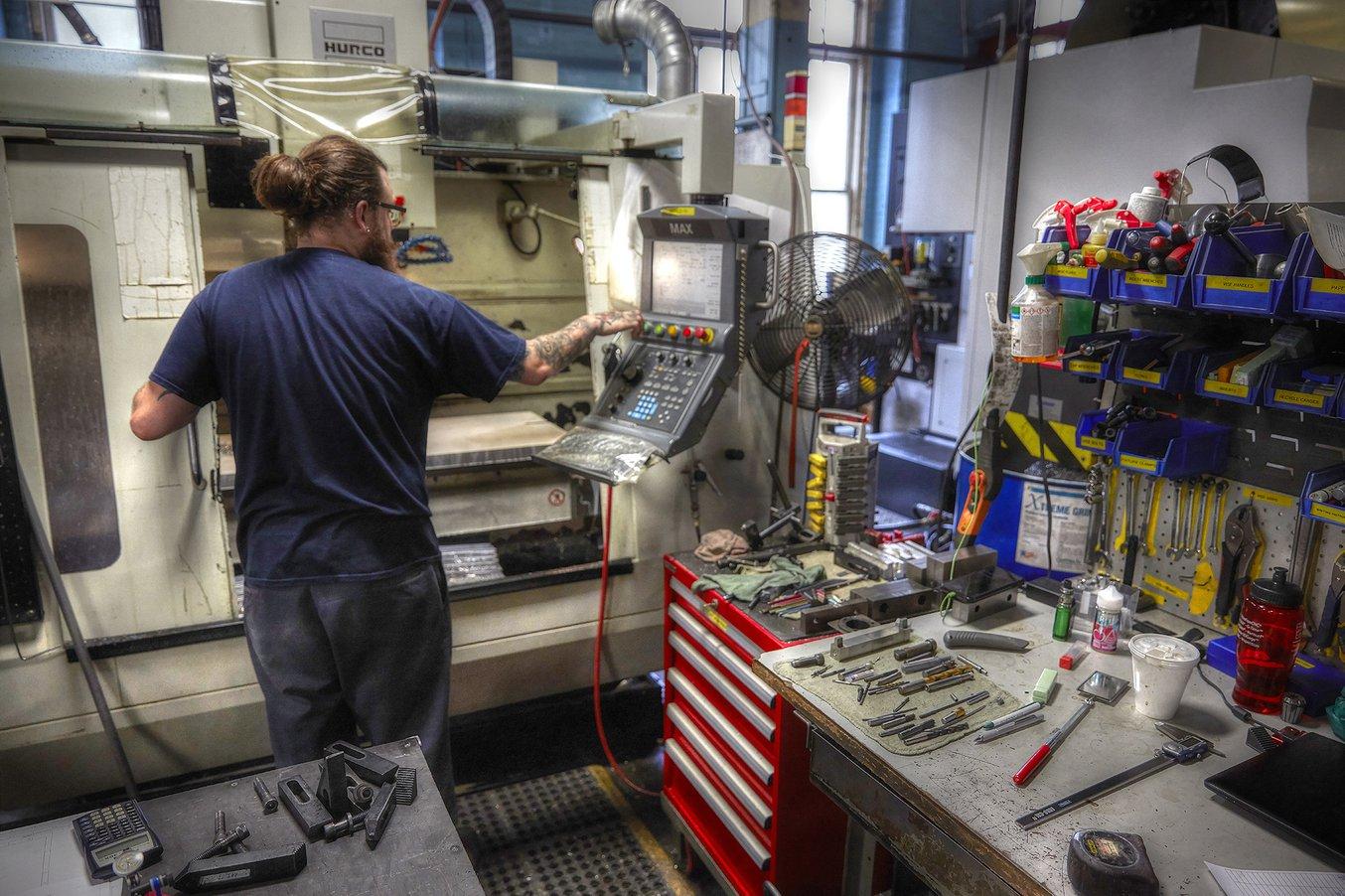
Le macchine a controllo numerico richiedono tempo ed esperienza per essere programmate. Se una parte non deve essere realizzata in metallo, la stampa 3D può essere uno strumento pratico per creare prototipi o strumenti di produzione in modo più veloce e a un costo ridotto.
A&M Tool and Design produce parti e apparecchi personalizzati per il settore aerospaziale, ottico e della robotica. Negli anni l'attività si è modernizzata introducendo un'ampia gamma di nuove attrezzature, incluse stampanti 3D, da affiancare all'affidabile tecnologia tradizionale e alle soluzioni aggiornate. Ryan Little, ingegnere meccanico di A&M Tool, ha condotto una ricerca su quali stampanti 3D rispondessero meglio alle necessità dell'azienda, scegliendo infine quelle di Formlabs.
Per la prototipazione, l'azienda ha cominciato a usare stampe 3D per testare l'aderenza e la funzionalità. In questo modo, Little e il suo team possono realizzare parti molto più velocemente e usare tutte le ore della giornata, programmando le stampe in modo che vengano eseguite durante la notte, così da poter usare le parti il giorno seguente. La stampa 3D è particolarmente utile per realizzare forme geometriche che risulterebbero costose e richiederebbero molto tempo per essere prodotte da una macchina a controllo numerico.
"La stampante è quasi uno strumento di ausilio al CAD", spiega Little. "Facciamo molta prototipazione per diversi tipi di attrezzature. Se non avessimo la Form 2, molti prototipi rimarrebbero nel software CAD in attesa di procedere con la lavorazione meccanica, inoltre alcune parti non potrebbero mai essere realizzate o progettate per problemi di praticità."
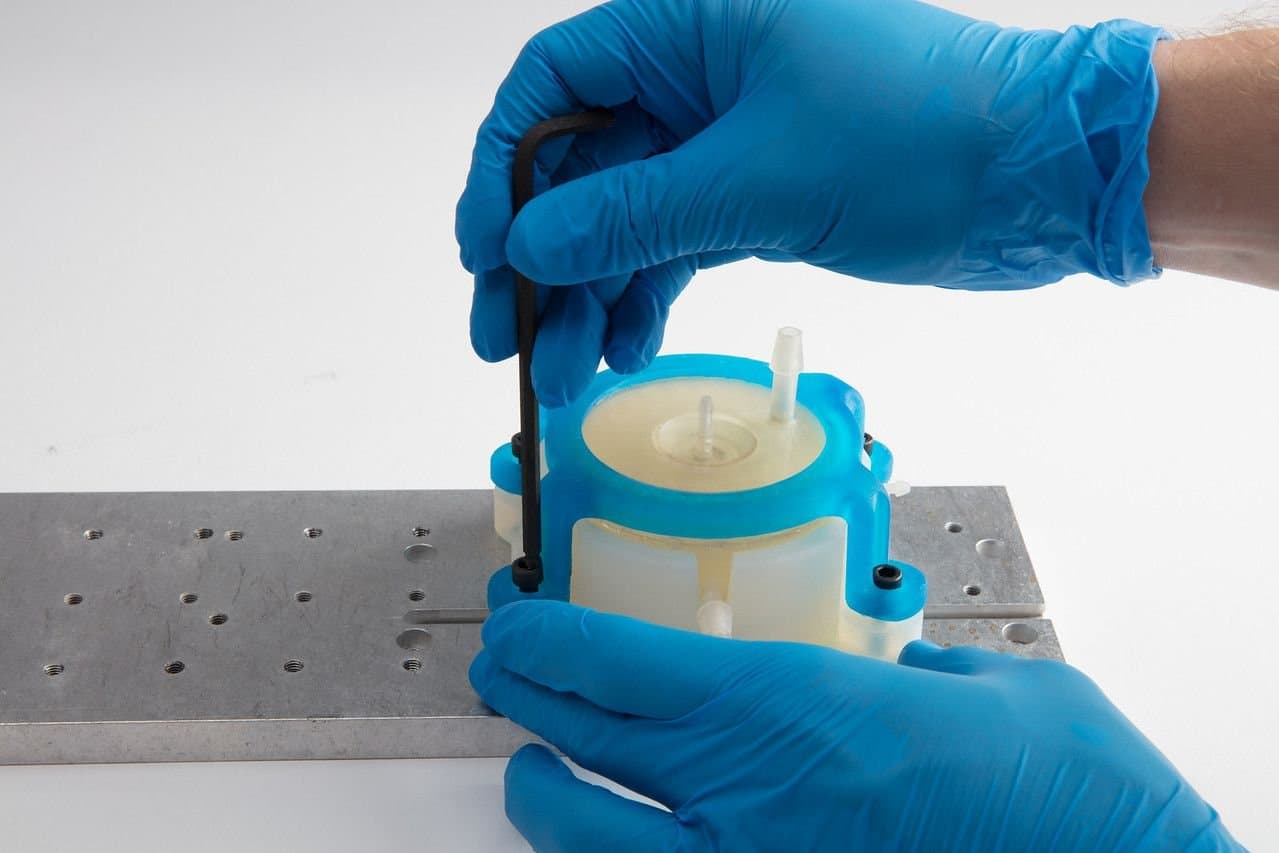
Progettazione di dime e attrezzi destinati alla stampa 3D
Per chi fabbrica parti, massimizzare la velocità di produzione conservando un’elevata qualità delle parti è di importanza cruciale. Le dime e i fissaggi vengono utilizzati per semplificare i processi di fabbricazione e assemblaggio, rendendoli al contempo più affidabili ed efficienti, per ridurre i tempi di ciclo e migliorare la sicurezza del personale.
Stampa 3D per la produzione aerospaziale
4. Risparmio di denaro con attrezzature personalizzate stampate in 3D per parti di aeromobili
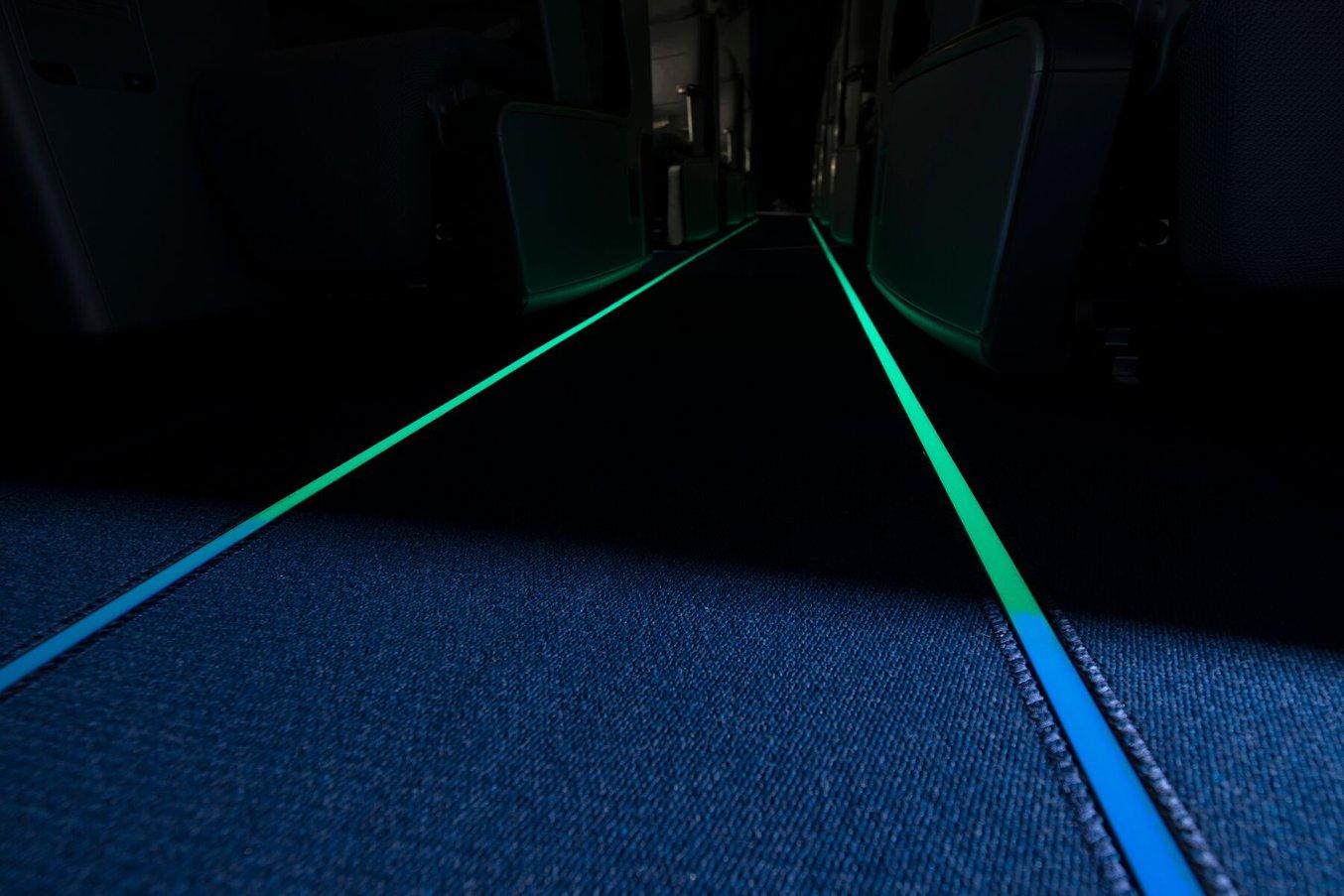
Lufthansa Technik ha stampato in 3D l'ugello di estrusione per produrre indicazioni delle vie di fuga che si illuminano da sole con la luce di bordo.
Lufthansa Technik è uno dei più grandi fornitori di servizi di manutenzione, riparazione e revisione nel settore dell'aviazione. Le esclusive indicazioni delle vie di fuga GuideU sono progettate per l'installazione post-vendita nelle cabine degli aeromobili. Queste innovative guide da pavimento sono dotate di pigmenti di natura fotoluminescente, in grado di caricarsi con la normale luce di bordo e continuare a funzionare anche in caso di blackout.
Prima della produzione sono stati testati diversi materiali e processi di fabbricazione. La stampa 3D di ugelli di estrusione personalizzati è risultata essere il metodo di produzione più economico e flessibile. "In teoria avremmo potuto realizzare gli ugelli tramite stampaggio a iniezione, ma non avremmo avuto la stessa flessibilità in termini di forma e messa a punto. Questo è il grande vantaggio della stampa 3D", spiega Ulrich Zarth, ingegnere di progettazione per GuideU.
Questo strumento di produzione è stato realizzato sulla Form 3L, in collaborazione con il partner Formlabs myprintoo. La piattaforma di stampa di grandi dimensioni della Form 3L ha permesso di realizzare 72 parti in un singolo ciclo di stampa. Sono stati testati diversi materiali Formlabs, ma alla fine la scelta è ricaduta sulla Clear Resin: oltre a offrire la stabilità e la finitura superficiale necessarie, permette a Lufthansa Technik di ottimizzare continuamente il proprio processo di produzione.
"Se vuoi ottenere forme precise in poco tempo, specie con le materie plastiche, la stampa 3D è sempre la scelta migliore."
Ulrich Zarth, ingegnere di progettazione presso Lufthansa Technik AG
Realizzare in-house questo piccolo componente con una stampante 3D ha permesso a Zarth e al suo team di ottenere un notevole risparmio in termini di tempo e denaro. Inoltre, rispetto ai metodi convenzionali per la creazione di attrezzature di questo tipo, hanno potuto evitare ordini minimi elevati e mantenere un'eccezionale flessibilità in termini di ottimizzazione del processo.
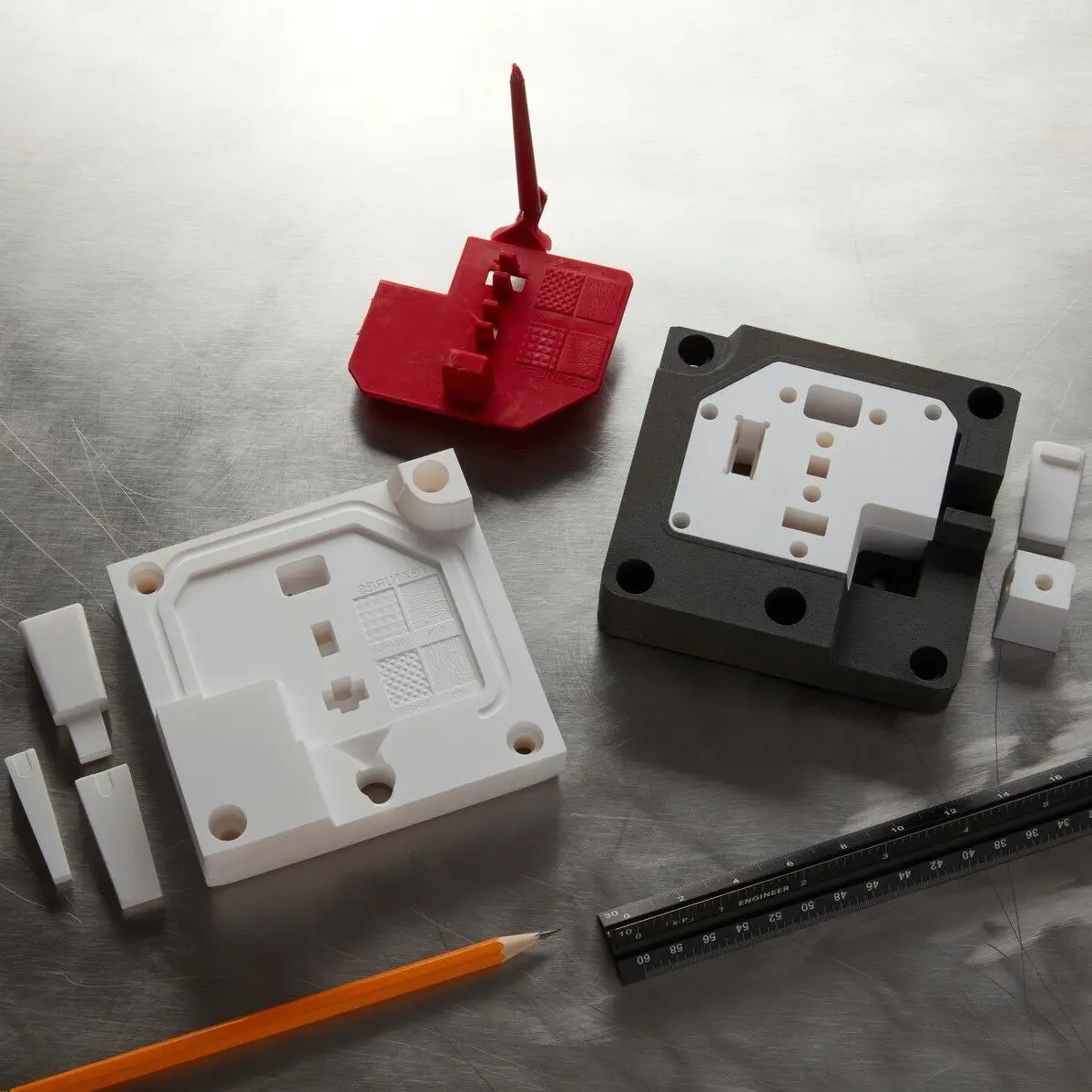
Guida alla creazione rapida di attrezzature
In questo whitepaper scoprirai di più su come combinare la creazione rapida di attrezzature con processi di fabbricazione tradizionali come lo stampaggio a iniezione, la termoformatura o la fusione.
5. Risparmio di tempo nella produzione aerospaziale con dime di mascheratura stampate in 3D
L'Integrated Manufacturing Group dell'AMRC lavora con partner industriali per combinare tecnologie all'avanguardia e sviluppare sistemi integrati. Questo gruppo di ricerca si è occupato di un progetto per Airbus, la più grande azienda produttrice nel settore aerospaziale in Europa, che prevedeva la foratura ad alta tolleranza e la lavorazione meccanica di componenti in fibra di carbonio, alluminio e titanio. "Dopo aver eseguito un foro e prima di passare a quello successivo, dovevamo coprire il primo, in modo che gli scarti generati dall'operazione di foratura non contaminassero il secondo", afferma George Sleath, un ingegnere di progettazione di AMRC.
Il team ha prima provato a usare un pezzo di alluminio con un piccolo O-ring in gomma, ma questa soluzione non era sufficiente a risolvere il problema. Inoltre, si aggiungevano due problemi: occorrevano coperchi di diverse dimensioni e, per rispettare la scadenza, avevano solo dieci giorni per procurarsene 500.
Avendo a disposizione così poco tempo per realizzare prodotti personalizzati, l'unica opzione di produzione praticabile era la stampa 3D. Non sapendo bene quali fossero le capacità interne dell'AMRC, Sleath ha chiesto un preventivo a tre laboratori di stampa esterni, ma i costi erano elevati.
"Ne parlai con Mark Cocking del nostro gruppo di progettazione e prototipazione e gli chiesi se fosse possibile produrre i coperchi internamente. Non si fece sentire per 24 ore, ma quando lo ricontattai mi disse che ne avevano già stampati la metà. Duecentocinquanta coperchi protettivi stampati in 24 ore: era straordinario", dice Sleath.
Alla fine, Cocking è riuscito a far produrre tutti i componenti in due giorni. Inoltre, i coperchi funzionavano esattamente come previsto. "Il riscontro degli operatori che li hanno installati è stato fantastico. La maggioranza dei coperchi ha funzionato come doveva e nessuno si è rotto durante il progetto", racconta Sleath.
6. Parti aerospaziali per utilizzo finale stampate in 3D e galvanizzate
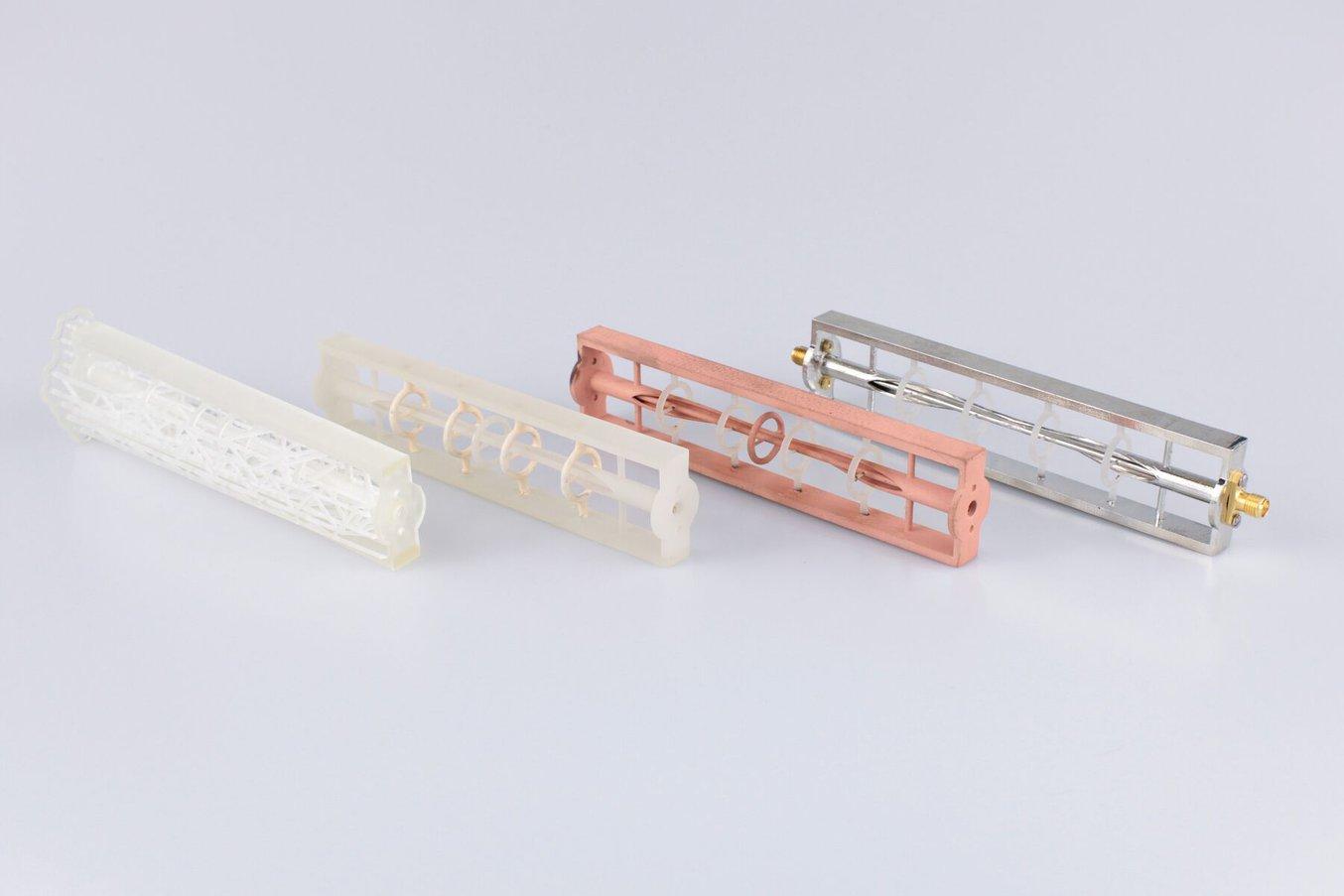
La stampa 3D di parti per utilizzo finale consente a Elliptika di creare nuovi design di antenne in modo più rapido ed economico.
Elliptika è un'azienda specializzata nella progettazione e nello sviluppo di prodotti e soluzioni a radiofrequenze (RF) e microonde. Realizza filtri e antenne personalizzati, che vengono usati in ambito di ricerca e sviluppo nei settori automobilistico, della difesa, medico e dell'istruzione. I designer di articoli a radiofrequenze Gwendal Cochet e Alexandre Manchec hanno l'esigenza di ottenere geometrie complesse a basso costo e con tempi di realizzazione rapidi. Per farlo, hanno dovuto spingersi oltre i limiti delle tecniche di produzione tradizionali.
Dopo aver lavorato con diversi processi di produzione additiva, il team di Elliptika ha individuato nella stampa 3D stereolitografica (SLA) il metodo che meglio si adatta alla galvanizzazione, vista la superficie liscia delle parti stampate. "Al termine della stampa 3D, è necessario rimuovere il supporto, pulire la superficie della parte e polimerizzarla. Quindi la parte viene sottoposta a un processo chimico di galvanizzazione per applicare uno strato di rame di circa 3 µm. Infine, si può passare alla finitura superficiale della parte, applicando ad esempio uno strato di stagno più spesso".
Con soli due progetti, Elliptika è riuscita a recuperare l'investimento per l'acquisto della stampante 3D Formlabs. La realizzazione di una parte a opera di un fornitore esterno costa circa 3000 €, mentre il costo dei materiali e della manodopera per la stampa 3D e la galvanizzazione di un'antenna in-house è di soli 20 €.
Anche il ritmo di lavoro è molto più veloce. Con le tecniche di produzione tradizionali, fabbricare un'antenna poteva richiedere fino a tre mesi. "Con la stampa 3D in-house, otteniamo parti funzionanti in due giorni: uno per la stampa e uno per la galvanizzazione. Così è tutto molto più veloce", spiega Cochet.
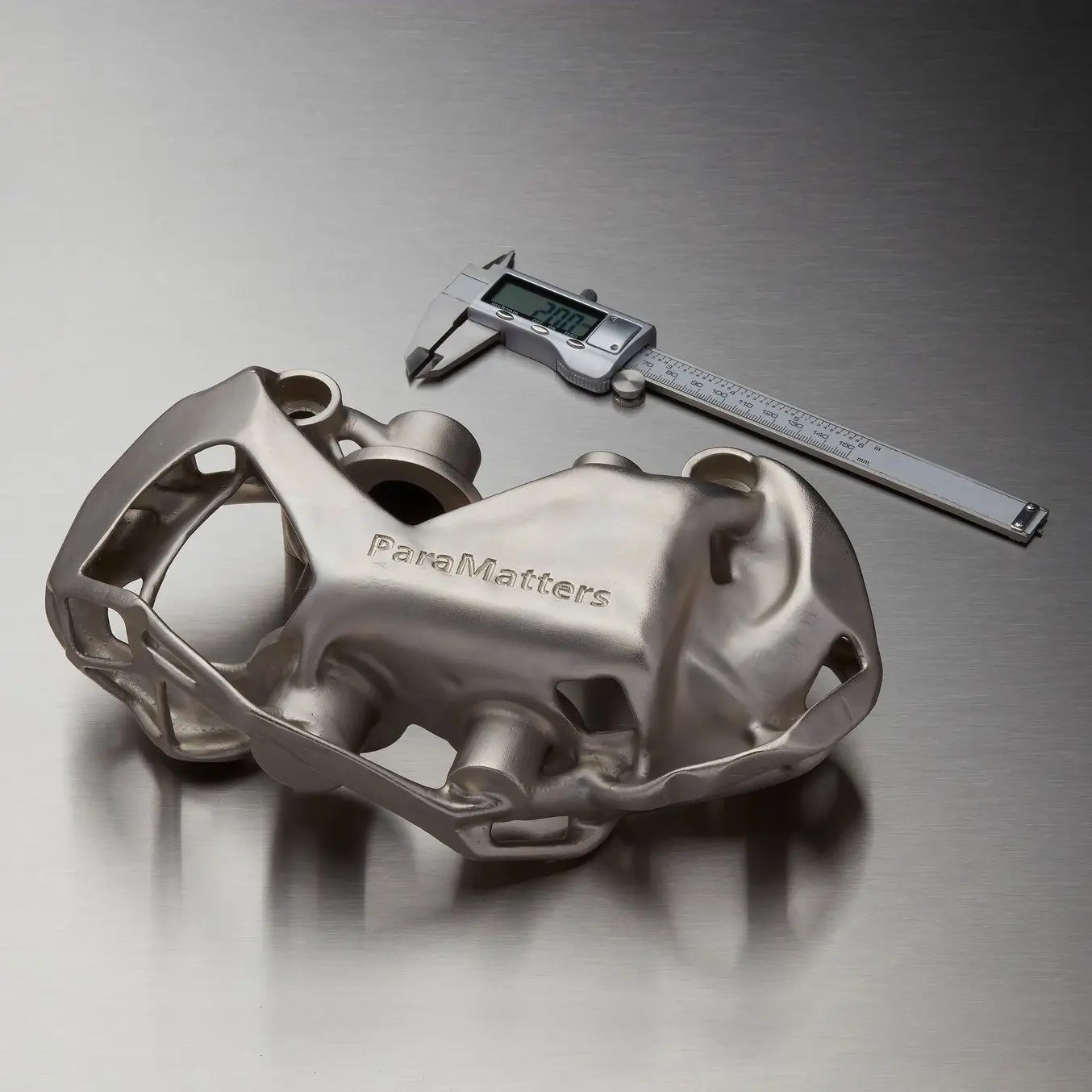
La resistenza del metallo: strategie e casi d'uso per la galvanizzazione di parti SLA
Scopri come i team ingegneristici aggiungono il metallo alle stampe 3D in resina e perché le parti ibride possono aprire la strada a un'ampia gamma di applicazioni, incluse resistenza e robustezza delle parti per utilizzo finale e molto altro ancora.
Stampa 3D per la ricerca e l'istruzione nel settore aerospaziale
7. Test nello spazio di parti stampate in 3D
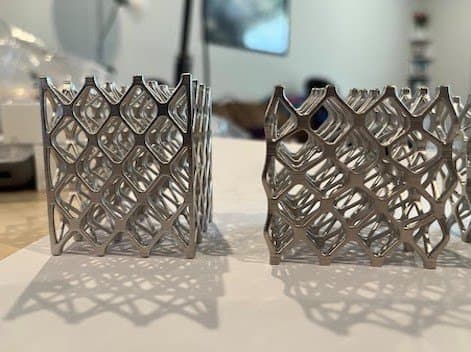
Campione realizzato con la Rigid 10K Resin e galvanizzato prima del test di compressione dall'alto (a sinistra) e dopo il test (a destra).
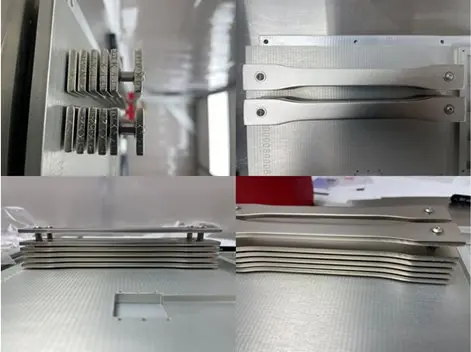
Parti stampate in 3D con la Rigid 10K Resin e galvanizzate inviate sulla ISS.
I team di ricerca della NASA stanno studiando le prestazioni nello spazio di parti stampate tramite SLA e galvanizzate. Gli ingegneri NASA del Goddard Space Flight Center hanno progettato delle staffe che sono state stampate in 3D su stampanti Formlabs, galvanizzate e poi inviate nello spazio nell'estate del 2022, nell'ambito della missione Commercial Resupply Services (CRS-25) di SpaceX per rifornire la Stazione Spaziale Internazionale (ISS).
Utilizzando la piattaforma di analisi Materials International Space Station Experiment (MISSE-16) di Alpha Space, posta all'esterno della ISS, i campioni verranno esposti all'ambiente esterno alla stazione spaziale, prima di essere riportati sulla Terra per ulteriori test. I risultati ottenuti potrebbero fornire informazioni utili alla NASA, ed eventualmente ad altre aziende del settore aerospaziale, su come includere la galvanizzazione e la produzione additiva in eventuali progetti futuri di produzione.
8. Parti stampate in 3D per test nella galleria del vento
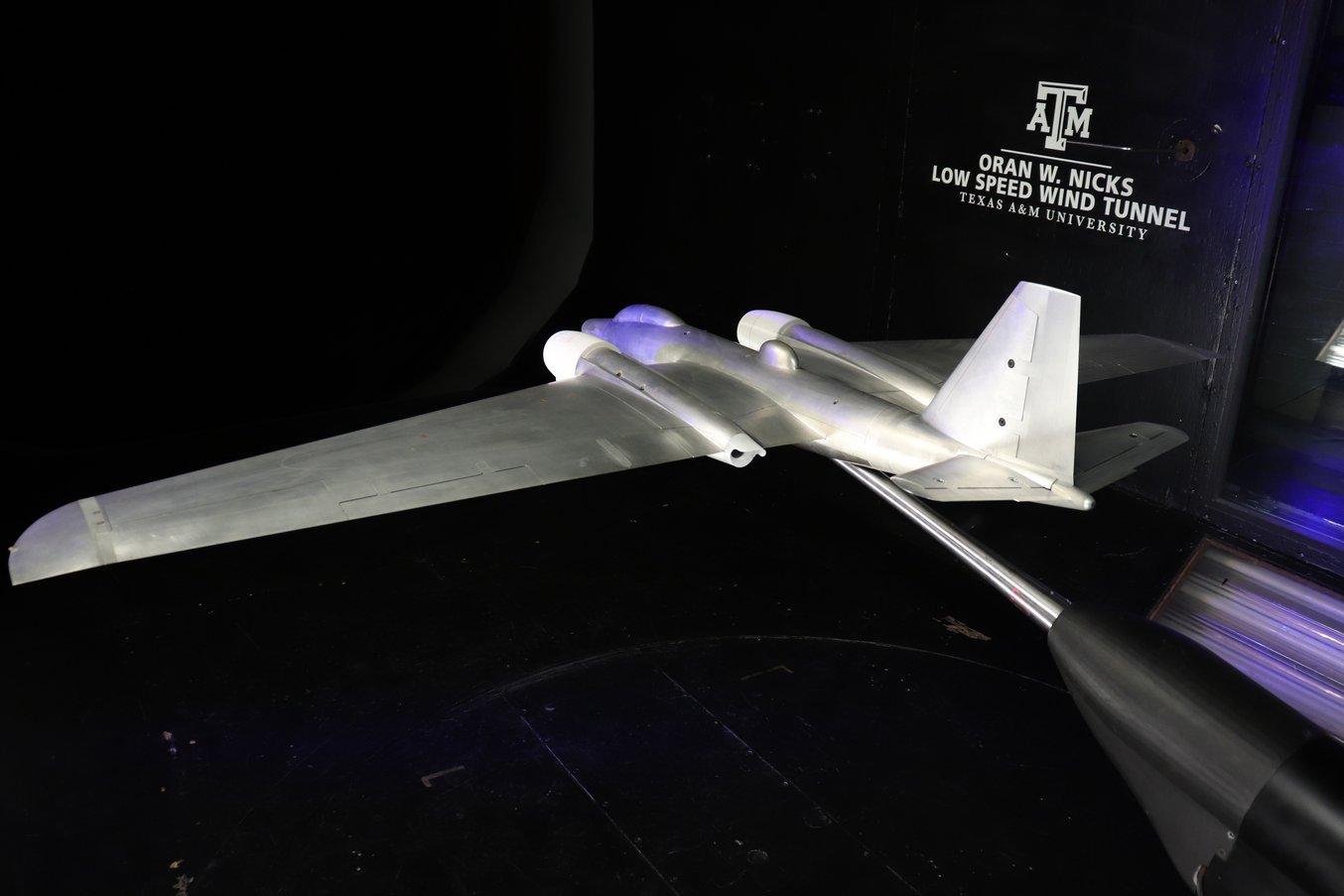
È possibile montare componenti stampati in 3D ad alte prestazioni sui modelli di aereo in scala installati in una galleria del vento.
Le stampanti 3D di Formlabs sono utilizzate da docenti e studenti di tutto il mondo per eseguire test nella galleria del vento e ottenere dati per le loro ricerche.
La galleria del vento a bassa velocità Oran W. Nicks della Texas A&M University viene usata per condurre test in molti progetti. Lisa Brown, responsabile e ingegnera presso questa galleria del vento, aiuta i team di ricerca a pianificare i test, progettare i modelli e creare il codice informatico per la raccolta dei dati. Il suo team sfrutta la stampa 3D per creare modelli in scala per testare un'ampia gamma di componenti.
Brown racconta di un progetto di ricerca in cui la stampa 3D è stata usata per testare una pala flessibile per elicotteri. "Quando si raggiunge una certa velocità di flappeggio, si formano onde d'urto sul bordo di attacco delle pale. Quando sei a bordo di un elicottero, non è una situazione auspicabile. È stato emozionante vedere dal vivo la formazione di queste onde d'urto nella nostra galleria del vento a bassa velocità", spiega Brown. "Abbiamo stampato un piccolo inserto contenente sensori da montare sul bordo di attacco. Il modello era quindi formato da una pala in alluminio con questo piccolo inserto sostituibile."
Quale materiale ha scelto Lisa Brown? Leggi il caso di studio per scoprirlo.
Sull'altra sponda dell'Oceano Atlantico, anche l'Istituto di Tecnologia di Karlsruhe (KIT) usa una galleria del vento per testare parti stampate in 3D. Il dottorando Lars von Deyn studia metodi per prevedere i flussi turbolenti. Il suo lavoro ha l'obiettivo di ridurre la frizione nella mobilità e mira a fornire informazioni utili in termini di materiali e progettazione.
Von Deyn ha scelto la stampa 3D per creare le parti per i suoi test. "Voglio analizzare le strutture difficili da produrre tramite processi di lavorazione meccanica", afferma. Ha quindi scelto la Form 3L per via dell'ampia area di stampa, che gli avrebbe permesso di posizionare nella galleria del vento un minor numero di parti singole e ottenere una maggiore continuità nel modello.
Leggi il caso di studio per scoprire i risultati dei suoi esperimenti.
9. Formazione della nuova generazione di ingegneri con la stampa 3D
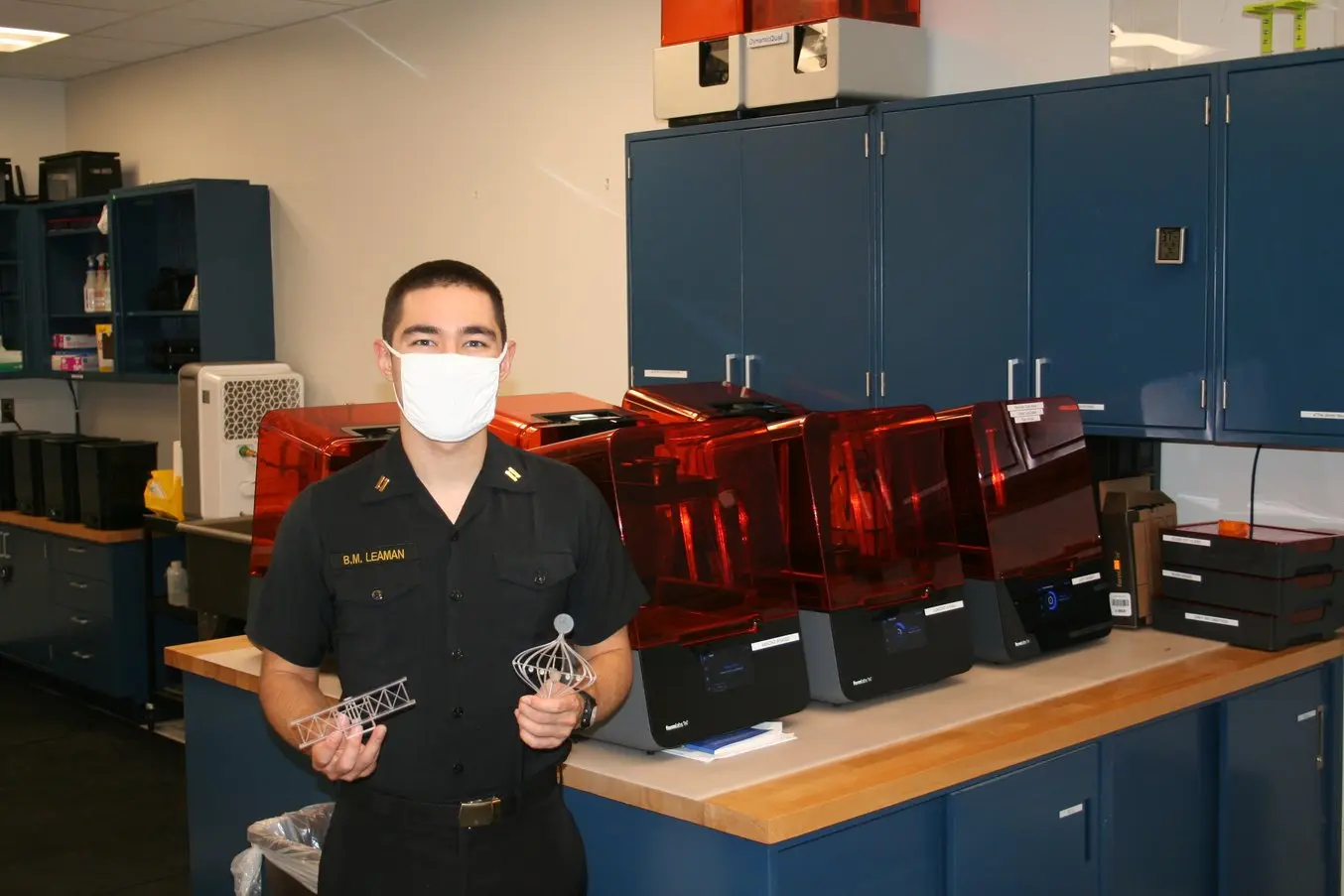
Ben Leaman, guardiamarina di prima classe e studente presso la facoltà di architettura navale della USNA, mostra le parti stampate sulla Form 3 di Formlabs vincitrici della gara di produzione additiva AM Olympics nel 2021.
La United States Naval Academy (USNA) prepara giovani uomini e donne a diventare ufficiali di professione nella marina statunitense e nel corpo dei Marines. Il capitano Brad Baker, professore associato della USNA, si è reso conto che il mancato accesso a capacità di produzione costituiva un ostacolo nel processo iterativo dei suoi studenti di ingegneria e di conseguenza al loro ritmo di apprendimento. Nonostante la presenza di un laboratorio per la lavorazione meccanica con apparecchiature per i progetti di base, gli studenti, lavorando individualmente o in gruppo, non riuscivano a completare più di tre o quattro iterazioni in un anno.
Il capitano Baker non è stato il primo professore del campus a mettere a disposizione degli studenti del suo corso delle stampanti 3D, ma è stato l'unico ad aver portato i processi di progettazione e produzione in un unico luogo: il MakerSpaceUSNA. Partendo da un paio di stampanti a modellazione a deposizione fusa (FDM), ha iniziato a integrare gli apparecchi nel curriculum di ingegneria meccanica e li ha messi a disposizione degli studenti per completare i loro progetti.
Quando gli studenti intraprendono un corso di studi in ingegneria, la prima cosa che imparano a usare è un software CAD, poi si passa alle stampanti FDM, alla stereolitografia (SLA), infine alle stampanti 3D a sinterizzazione laser selettiva (SLS). Ora si possono cimentare anche nella scansione 3D e sono in grado di portare a termine interi progetti di ingegneria inversa utilizzando tutti gli strumenti che hanno imparato a usare.
Le stampanti FDM, SLA e SLS affidabili e di alta qualità di MakerSpaceUSNA permettono a ogni studente di fare esperienza con un'ampia gamma di tecnologie di produzione additiva. La filosofia del capitano Baker, secondo cui la formazione deve essere pratica e passa anche dal commettere e analizzare i propri errori, permette agli studenti di ingegneria di avere una preparazione più completa e li prepara per una carriera sia all'interno della marina americana che in altri campi.
Come evolverà la produzione additiva nel settore aerospaziale?
Grazie a tecnologie additive ogni giorno più potenti e accessibili, i contributi al settore saranno sempre più numerosi e diversificati. Non possiamo prevedere se le innovazioni più rivoluzionarie dei prossimi 5-10 anni verranno da aziende produttrici di parti originali, fornitori, agenzie pubbliche, start-up o università, ma vista la rapida e progressiva diffusione della stampa 3D, siamo sicuri che lo scopriremo presto.
Mentre la conoscenza dalla stampa 3D continua a diffondersi nel settore aerospaziale, con tecnologie e materiali sempre più versatili, la produzione additiva continua a rivoluzionare le modalità di costruzione e manutenzione di aeromobili e veicoli spaziali.