How the US Naval Academy Uses 3D Printing to Train the Next Generation of Naval Engineers
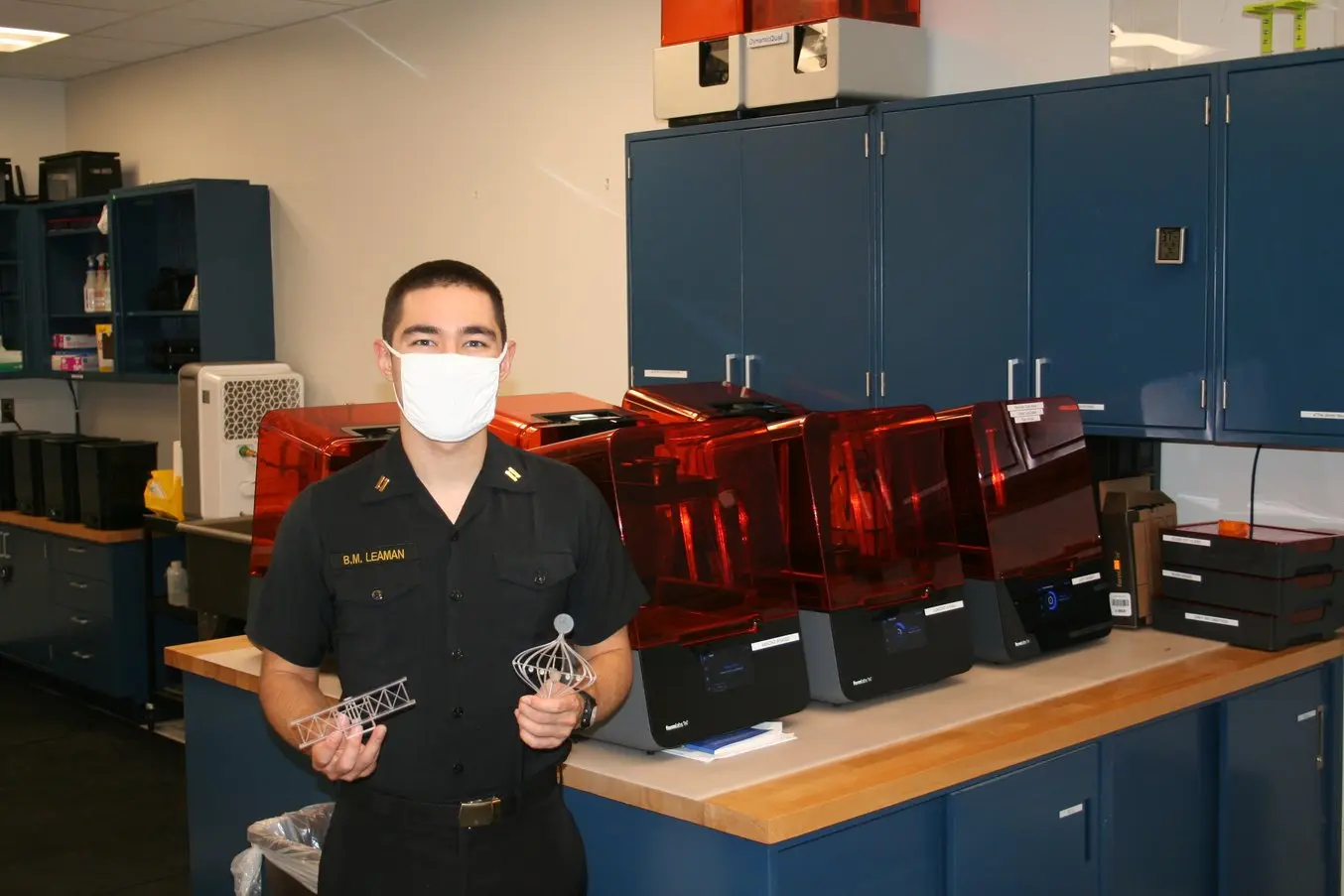
Midshipman 1/C Ben Leaman, a Naval Architecture major at USNA, showing his award winning prints using Formlabs Form 3 printers during an AM Olympics challenge in 2021.
Federal directives regarding the adoption of additive manufacturing in the armed forces are becoming clearer and more explicit as global crises push manufacturers to find alternative and more agile means of production. In order to help train the defense workforce in these technologies, educators in the undergraduate programs of the armed forces are increasing the focus on 3D printing. One educator, Captain Brad Baker, an Associate Professor at the United States Naval Academy (USNA), is already ahead of the curve, and has been focusing on different additive technologies for years.
Through MakerSpaceUSNA, every single student at the United States Naval Academy, regardless of major, is exposed to various additive manufacturing technologies. For the engineering students specifically, their exposure goes much further, preparing them for careers as Naval engineers and leaders in the advanced manufacturing and defense industries. This level of education is made possible by a fleet of 3D printers, including the Form 3, Form 3B, Form 3L, and Fuse 1 from Formlabs, as well as printers and equipment from other vendors.
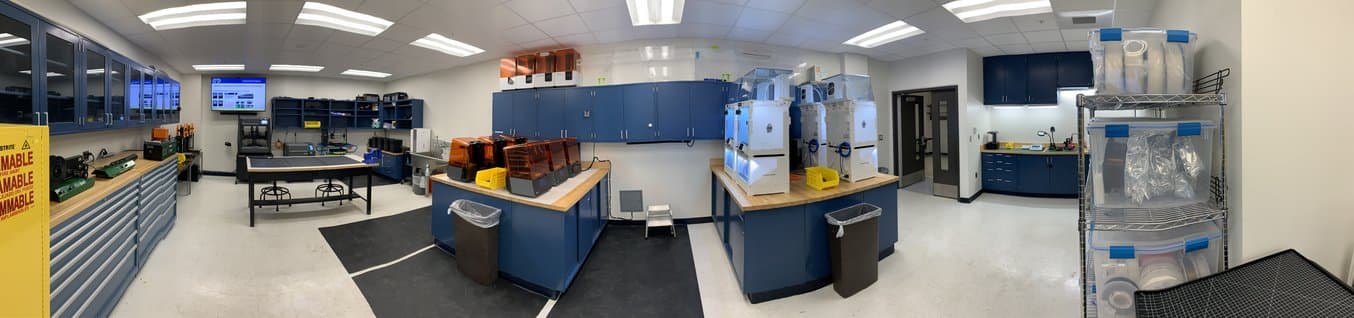
Captain Baker is the laboratory director for all material science equipment in the Mechanical Engineering Department and the School of Engineering and Weapons at the US Naval Academy (USNA)—managing everything from microscopy to materials development and now to additive manufacturing. We sat down with him to discuss his approach to teaching advanced manufacturing skills, the federal and departmental guidance for these technologies, and some of the projects students are working on in the makerspace.
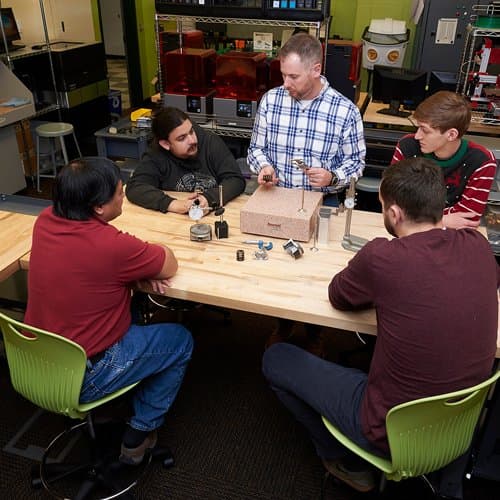
Guide to 3D Printing In Education
In this guide, we’ll discuss the benefits of 3D printing in education, from improved student collaboration to workforce development and empowered creativity.
Starting Slow
Captain Baker started MakerSpaceUSNA five years ago after serving as a technical advisor for a student engineering capstone project. During the process of advising students tasked with designing a submarine-launched unmanned air vehicle (UAV), Captain Baker realized that the students’ iterative process, and thus pace of learning, was impeded by lack of access to their own manufacturing capability. Even with a machine shop dedicated to the students’ capstone projects, each individual or team wasn’t able to do more than three or four iterations over the course of a year.
“They did a great job designing the parts and getting them to fit into a small design space, but there was an inherent really long delay time to get parts manufactured since that was outside of the student’s control. In an entire year, the students only went through three or four iterations; that’s slow prototyping. And the students are missing out on an opportunity—how to actually manufacture something. So I really wanted to fill that gap. Find a way to get something made faster and get the students involved in the actual manufacturing process.”
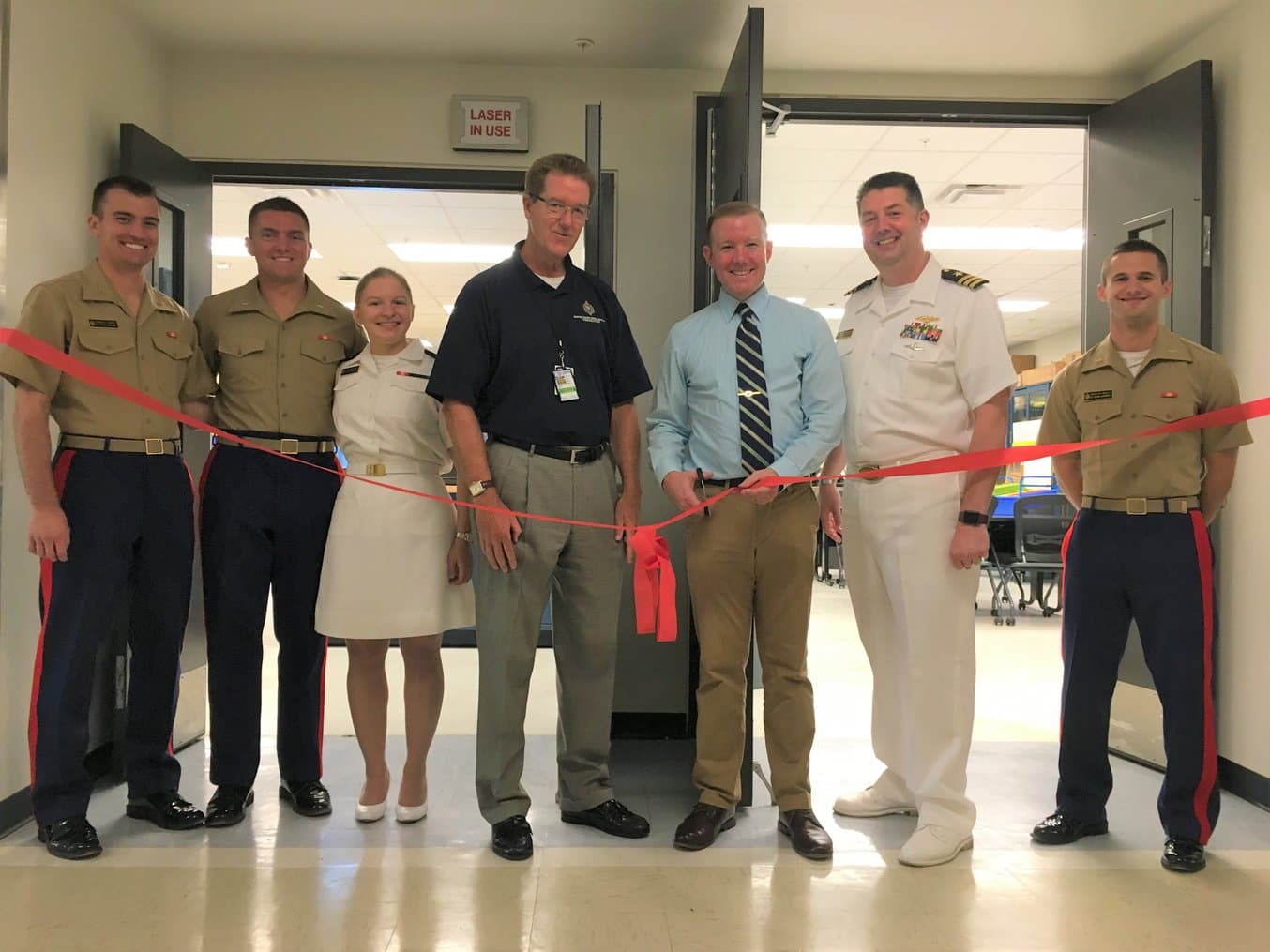
Captain Brad Baker and colleagues on the opening day of MakerSpaceUSNA.
Captain Baker wasn’t the first professor on campus to offer 3D printers to the students for their coursework, but he brought the entire design and manufacturing capability all under one centralized location when he started MakerSpaceUSNA. With just a couple fused deposition modeling (FDM) printers to start, he began integrating the machines into the mechanical engineering curriculum and making the machines available to students completing their capstone projects.
“It was successful right out of the gate—there was immediate student involvement, student interest and demand. We started with two printers, then quickly expanded CAD capabilities as well as 3D printing, and we were the first place on campus to centralize powerful computers, powerful CAD, and powerful 3D printers, all available directly to students.”
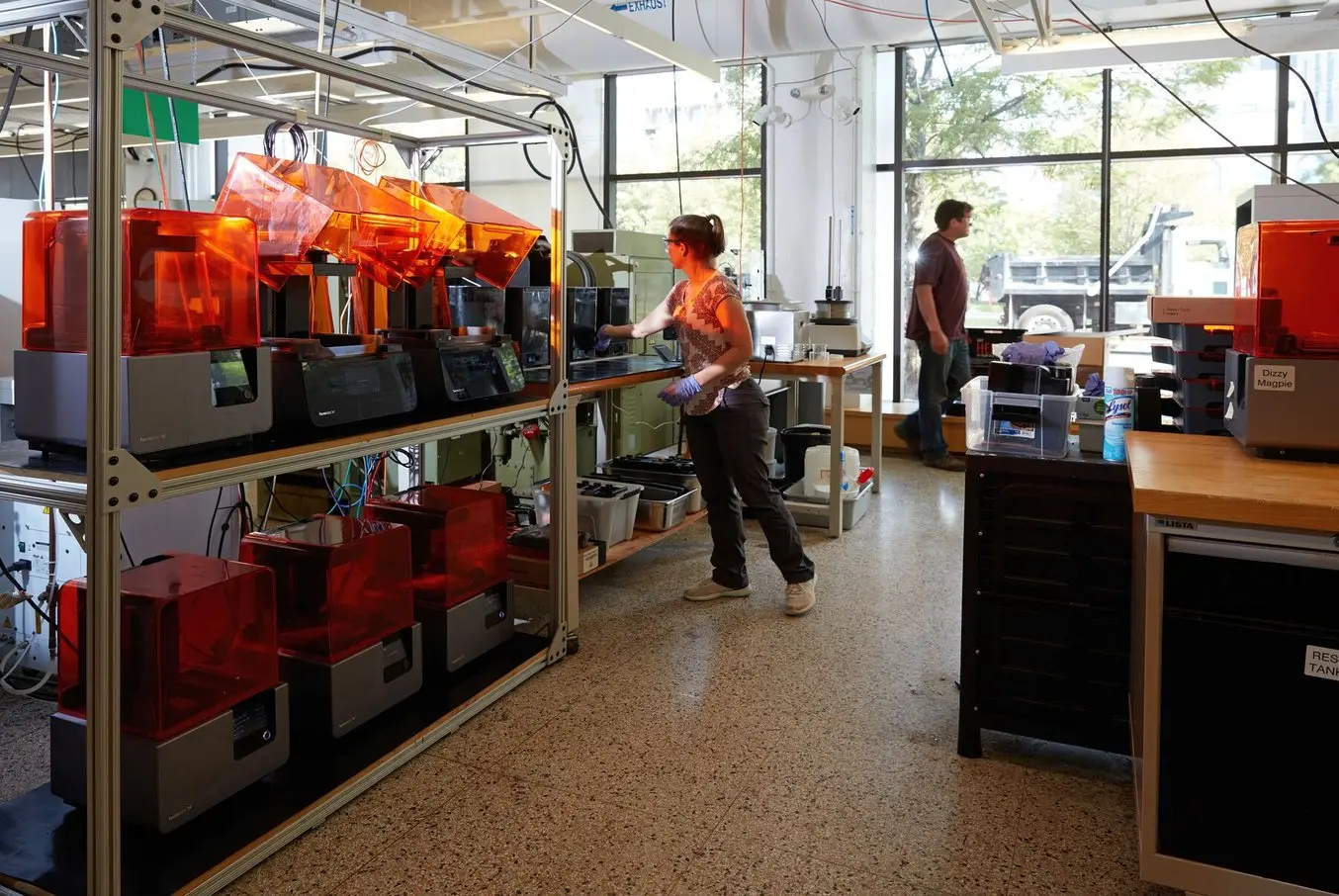
Special Pricing for Educational Institutions
Accredited educational institutions are eligible for special pricing, including a 10% discount on printers, hardware, and select accessories, and free Open Material Mode. Contact Formlabs or an Authorized Reseller to verify your eligibility.
Hands-On Learning
For many programs, the expense of outfitting a lab with these technologies makes the lab managers wary of letting undergraduate students have full access to the machines. For Captain Baker, there’s less of a concern with failures or mess, in fact, he encourages it.
“I want students to have failed prints. That’s where they’re going to learn the most. It may not be popular and certainly has a cost, but students really do learn that way. We have up to 100 users a semester. That’s a lot, so I rely on them to learn on their own—if they have adhesion or support problems, they then learn they need more supports or better adhesion, or need to resize or reorient the object. That’s the challenge, and it’s difficult to teach in words alone."
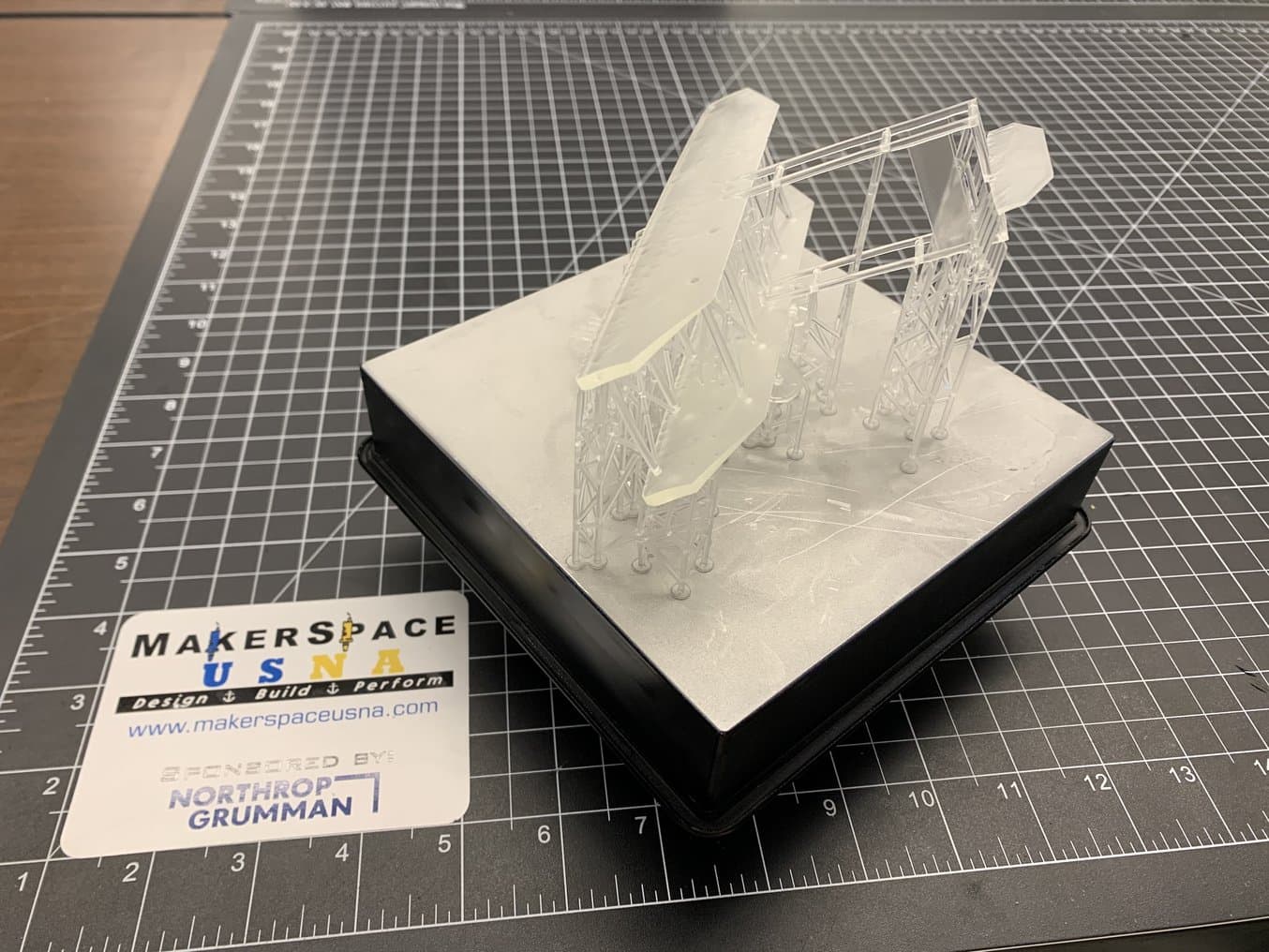
A model of the Wright brothers plane, printed in Clear Resin on the Form 3.
To mitigate the loss of time and material, Captain Baker recently implemented a tiered training program. When students start their engineering curriculum, they first learn how to use CAD software, then how to operate FDM printers, then move to stereolithography (SLA), and finally work their way up to selective laser sintering (SLS). Now they even learn 3D scanning and can complete full reverse engineering projects using all the tools they have learned.
"Building and running a MakerSpace with over 30 3D printers that supports over 100 users with only three people has been a challenging process, and just like my Navy training has taught me, the best way to do this is to train and then qualify users to use our facilities. There’s a hierarchy in how we do 3D printing, the students can get all the way to powder bed fusion on the Fuse 1 and our metal printers by learning how to fail first."
Captain Brad Baker
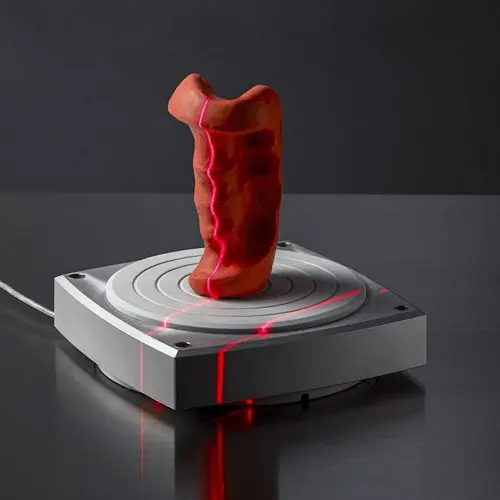
3D Scanning for Reverse Engineering, Restoration, and Metrology
3D scanning and 3D printing workflows can be applied to replication and restoration, reverse engineering, metrology, and more. Download our white paper to explore these applications and learn how to get started.
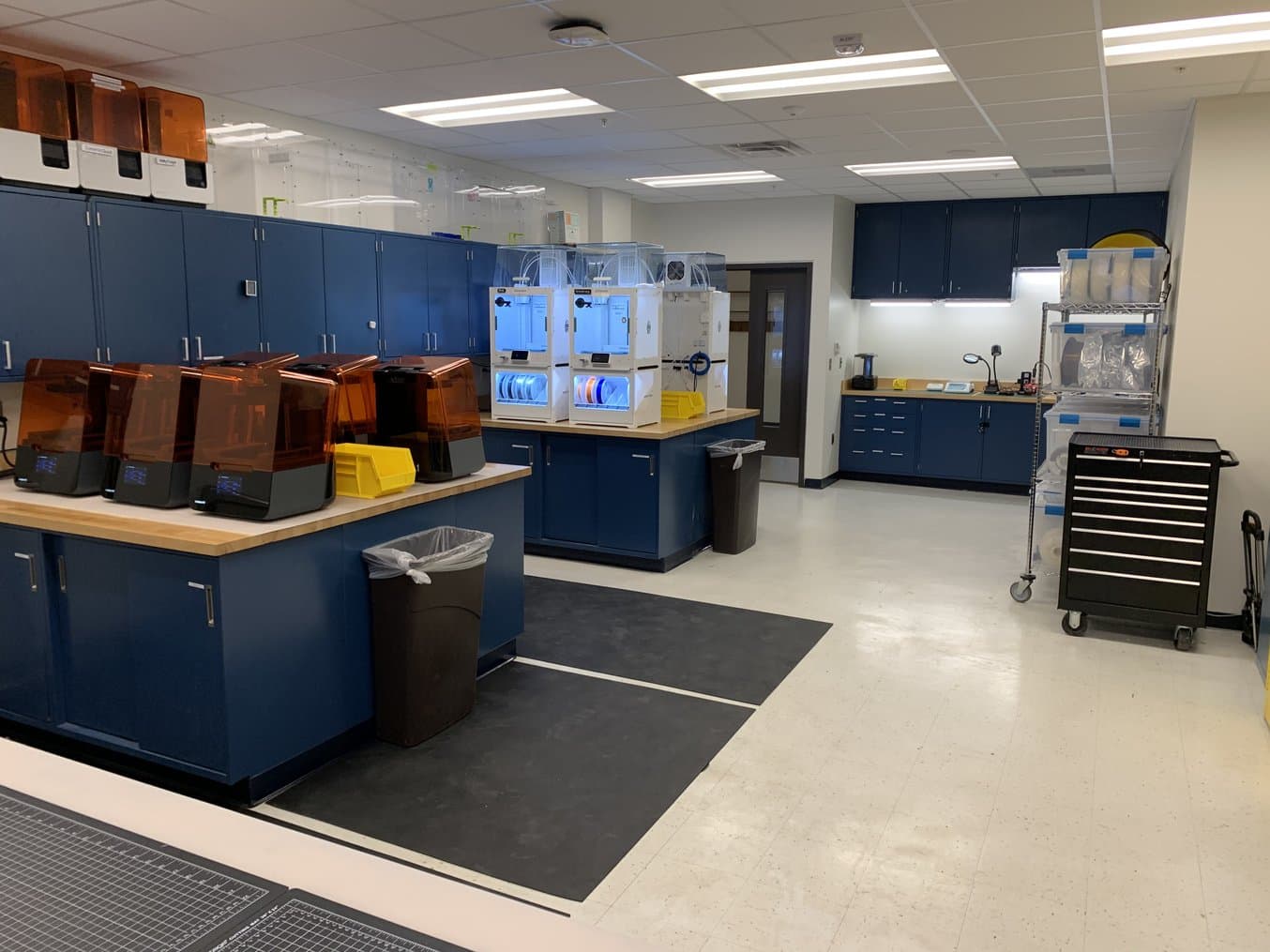
The MakerSpaceUSNA advanced section, housing Form 3 and Form 2 printers, as well as FDM printers.
Training and qualifying users puts a lot of pressure on the machines themselves to perform consistently. Captain Baker’s tailored teaching approach progresses students from more error-prone but simple FDM systems, to the progressively more robust low failure rate SLA printers, to finally the easiest to use yet most complex SLS systems.
“The failure rate on our SLA printers is extraordinarily low. I tell them, ‘wait until you get to SLS.’ On SLS [Fuse 1] it’s almost 0. Virtually no failures, material properties are good, and the accuracy is really good.”
Captain Brad Baker
New Applications With Materials Settings Editor
In addition to teaching mechanical engineering students how to choose the right 3D printing technology for their projects, the Form 3, Form 3L, and Fuse 1 printers all help with research.
A material scientist at heart, Captain Baker has been experimenting with ‘doping’ resins for years, creating new polymers with additives like ceramic particles. Using the Formlabs software program Materials Settings Editor, MakerspaceUSNA was able to take greater control over some of the Form 3’s settings to experiment with ceramicized resins as well as other proprietary blends.
“Materials Settings Editor helped us understand the printer better—how to adjust the different knobs and levers that operate the machine. Originally we got it for very specific applications because we wanted to use ceramics. We had a lofty ambition, to create a thermoelectric material, one that under heat flux will produce current. There were none that we could find that were additively manufactured, so we started working on different ways of manufacturing our own.”
Adding the Fuse 1
Research experiments like this are often part of engineering students’ capstone projects, which were the original impetus behind the centralization of MakerSpaceUSNA five years ago. But even when the original idea starts off in one direction, it can often get pulled in another. Such was the case with the initial idea of bringing a Fuse 1 into the fold. Captain Baker initially wanted to expand the material experimentation and development project into SLS and had to find a printer with an accessible price point and footprint that could still produce accurate parts consistently.
“We got the Fuse 1 for some unusual reasons, but it’s been an amazing success for so many additional reasons. The printer is amazingly fast, comparatively. It’s been a huge success. Resolution is good and dimensional accuracy is outstanding. Dimensional accuracy is the best out of all the printers we have. My students often wonder why we did not start with the Fuse 1 and I tell them simply, ‘you have to earn the privilege of getting to the Fuse 1.’”
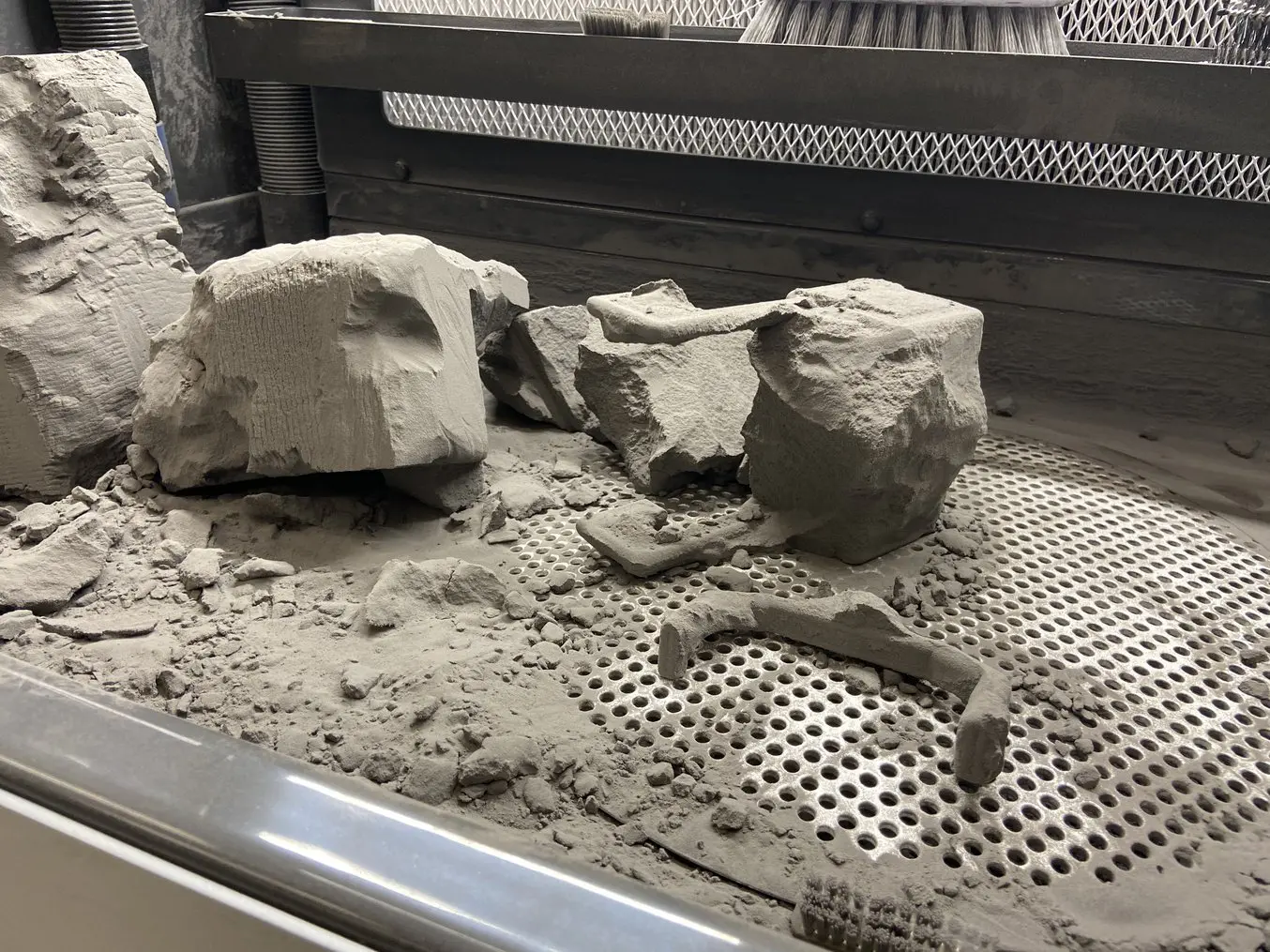
Nylon 12 Powder parts being post-processed in the Fuse Sift.
Though the initial push had been to create new materials, Captain Baker found that working with the Formlabs Nylon 12 Powder was a smooth and efficient process, saying, “the material properties of Nylon 12 are very appealing. It’s lightweight and strong. We made some UAV parts and some other end-use parts. It has good strength, good enough ductility, it’s solid, and perhaps best of all, it requires no supports so it can print challenging models very well.”
Variety in Technology, Materials, and Application
One application that Captain Baker hadn’t envisioned when he was initially building out his space was the use of his 3D printers for dentistry. Working closely with Navy Prosthodontist, Captain Peter Barndt, he developed a scanning, digital design, and 3D printing workflow for the dental needs of Naval Academy Midshipmen. Using his Form 3 and Form 3B printers with Grey Resin, Draft Resin, Surgical Guide Resin, and BioMed Clear Resin, Captain Baker and his colleague Captain Barndt are working on printing mouthguards, nightguards, and even surgical guides. Between typical student projects and side applications like dentistry, Captain Baker’s machines are running non-stop.
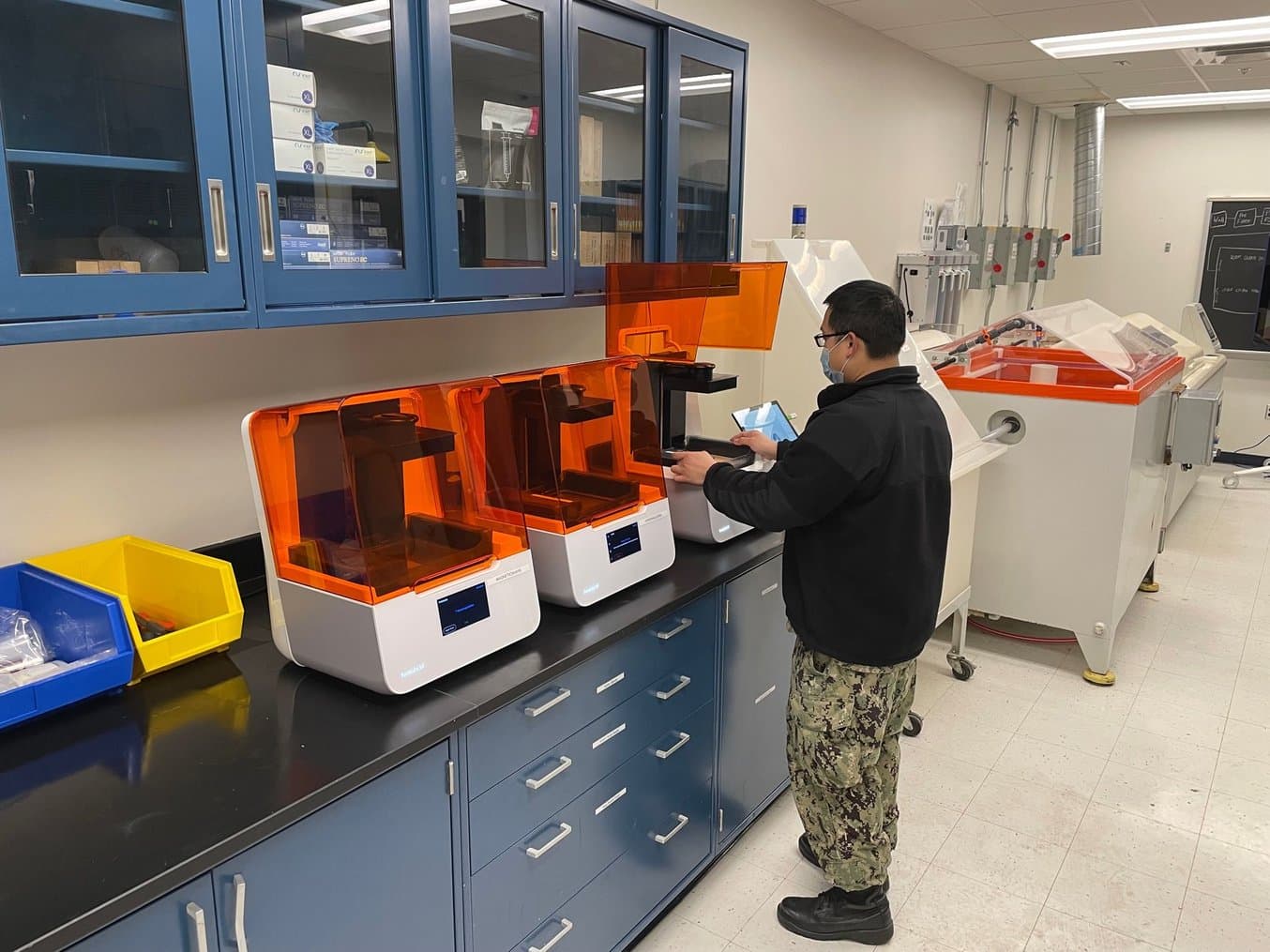
USNA Dental Technician inserting a Resin Tank into the Form 3B printer.
Having high quality, reliable printers that use FDM, SLA, and SLS technologies allows MakerSpaceUSNA to do something seemingly impossible—get every single USNA student in front of three different kinds of additive manufacturing. Captain Baker’s philosophy of hands-on education and a learning-through-failure approach takes that exposure a step further for the engineering students, and prepares them for careers serving in the United States Navy and beyond.
“It’s clear that the Navy has intentions to use additive manufacturing. There’s publicly available guidance, and it’s clear that the Marine Corps and the rest of the Department of Defense institutions are moving that way. The DoD has an interest in the technology, but you can’t just magically drop the machines into the field—you’ve got to build the personnel base to support that, which starts at MakerSpaceUSNA.”