Guida alla stampa 3D di dispositivi medici: dalla prototipazione alla commercializzazione
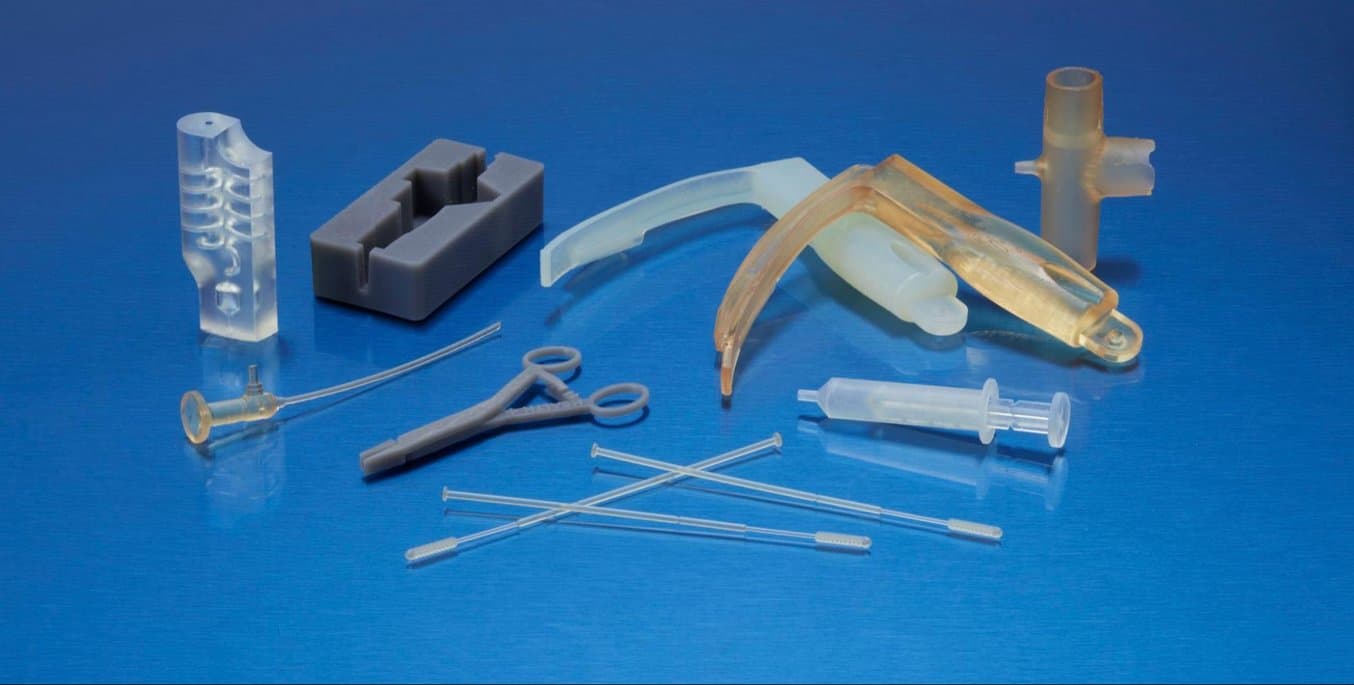
Da decenni la stampa 3D stimola soluzioni innovative e influenza lo sviluppo di dispositivi medici dalla fase di ricerca e sviluppo alla produzione. Man mano che le stampanti 3D diventano sempre più convenienti e aumentano gli investimenti negli apparecchi e nei materiali, un numero sempre maggiore di aziende inizia a utilizzare la stampa 3D, rivoluzionando il settore sanitario.
Portando la stampa 3D in-house, gli sviluppatori e i produttori di dispositivi medici possono ridurre i costi e il tempo per immettere sul mercato i loro articoli. La tecnologia consente uno sviluppo di prodotto più rapido, parti per uso finale innovative e la creazione di dispositivi medici personalizzati che sarebbero impossibili da realizzare con gli strumenti tradizionali. Come dimostrato dall'inizio del 2020, la produzione additiva consente inoltre una velocità senza precedenti dall'ideazione alla produzione su larga scala di forniture mediche di emergenza.
In questa guida completa esamineremo diverse applicazioni della stampa 3D per la produzione di dispositivi medici, confronteremo i più comuni processi di stampa 3D per il settore medico e forniremo una breve panoramica (con link ad altre risorse) sul processo normativo dei dispositivi medici stampati in 3D.
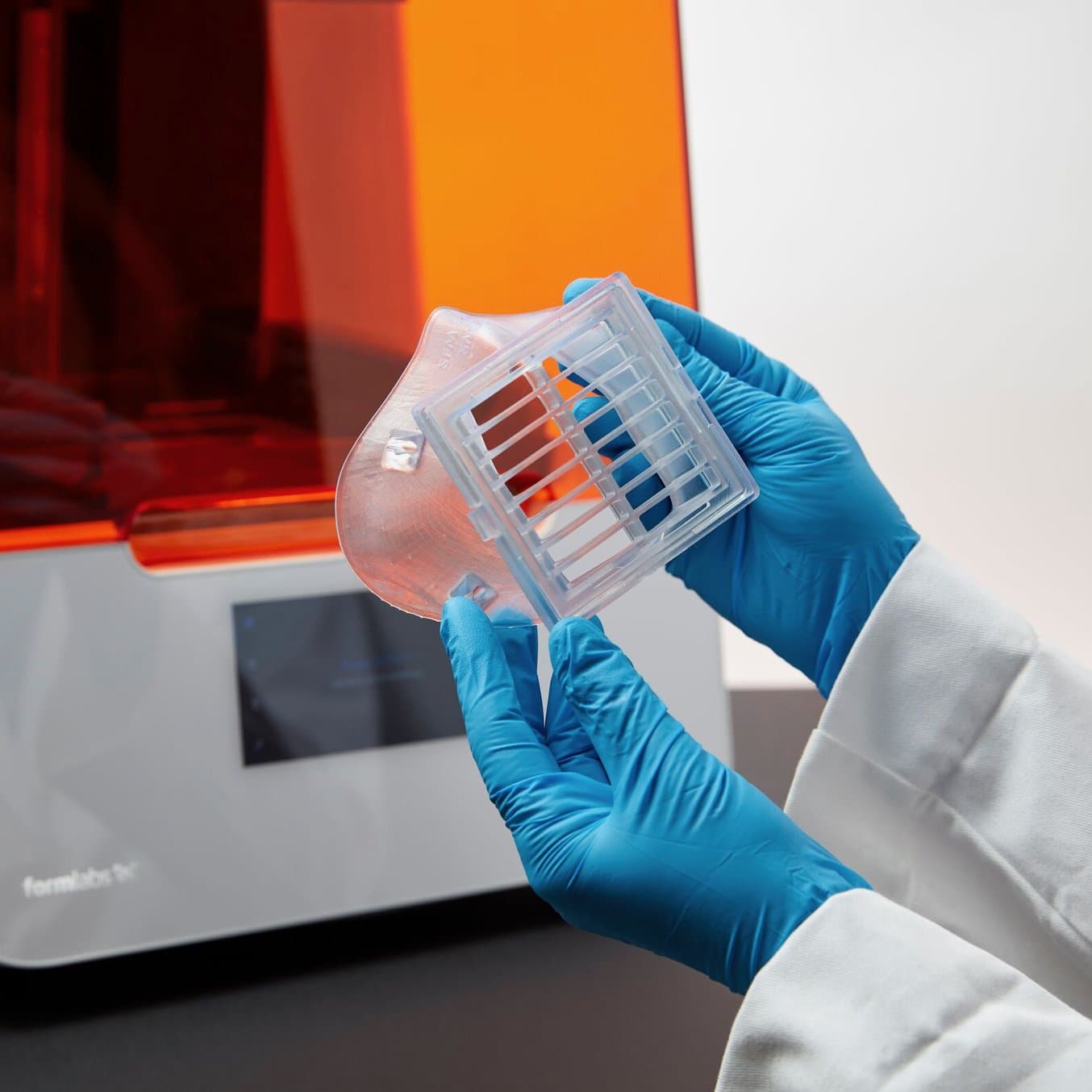
Come produrre con successo dispositivi medici con la stampa 3D
Scopri in questo articolo come Formlabs Medical aiuta i produttori di dispositivi medici a portare la produzione digitale in-house e lasciati ispirare dall'esempio di quattro aziende che creano dispositivi rivoluzionari con la stampa 3D.
Applicazioni della stampa 3D per i dispositivi medici
La stampa 3D, con la sua velocità, i prezzi accessibili, la possibilità di personalizzare i dispositivi e la libertà di design che è in grado di offrire, si è prestata a un'ampia varietà di casi d'uso nel settore dei dispositivi medici. Prendiamo in considerazione le applicazioni più comuni ed esempi reali che mettono in luce la versatilità della stampa 3D.
Prototipazione rapida di dispositivi medici
Lo sviluppo di prodotti innovativi procede di pari passo con gli avanzamenti nella cura dei pazienti e con i progressi del settore sanitario. La prototipazione è un elemento cruciale in questo processo iterativo in cui i dispositivi vengono creati, implementati e testati in un ambiente controllato.
Con prototipazione rapida si intende l'insieme di tecniche impiegate per fabbricare velocemente un modello in scala reale di una parte fisica o di un assemblaggio usando dati CAD tridimensionali. La stampa 3D va a braccetto con la prototipazione: infatti consente una libertà di forme pressoché illimitata, non richiede attrezzature specifiche e dà la possibilità di produrre parti con proprietà meccaniche molto simili a quelle ottenute con i metodi di produzione tradizionali.
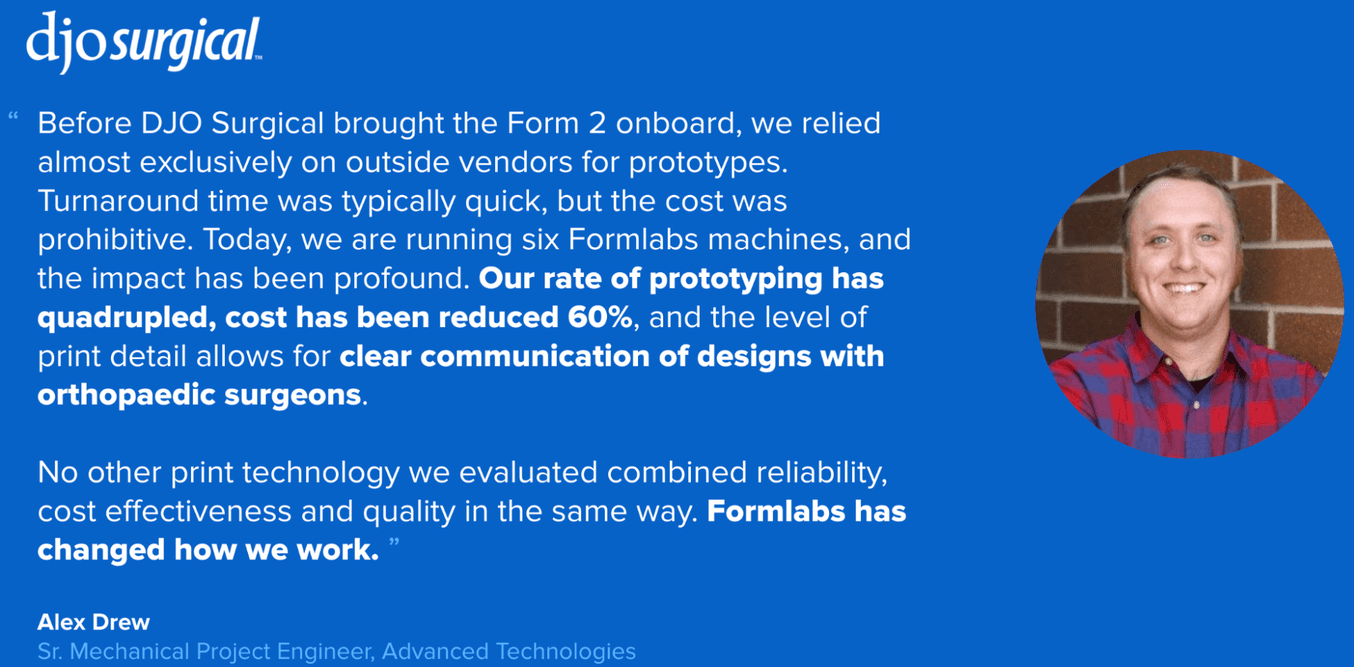
La stampa 3D offre ai produttori la flessibilità di realizzare prototipi funzionali in grado di riprodurre l'aspetto e il funzionamento dei dispositivi medici più complessi. In poche ore è possibile completare nuove iterazioni e convalidarle per determinare se siano necessarie ulteriori modifiche. Utilizzare la stampa 3D consente inoltre lo sviluppo di prototipi di dispositivi medici impiegando vari materiali in contesti in cui proprietà come la forza, la flessibilità o la resistenza al calore sono criteri importanti per il funzionamento del dispositivo.
Testare un prototipo funzionale utilizzando processi di validazione reali fornisce al produttore risultati su cui basare le successive iterazioni. I prototipi stampati in 3D possono anche servire come parti di esempio quando si presentano i prodotti agli investitori o ai futuri clienti.
La facilità di utilizzo e il basso costo della stampa 3D in-house hanno inoltre rivoluzionato lo sviluppo di prodotto. Più dell'85% dei 50 maggiori produttori di dispositivi medici hanno adottato la tecnologia Formlabs per fabbricare prototipi, attrezzature di produzione o dispositivi per utilizzo finale. Con spese in conto capitale che partono da meno di 5000 $, anche molte startup e piccole attività hanno potuto usufruire di questa tecnologia.
Coalesce Product Development, un’azienda britannica che progetta dispositivi medici, sviluppa dispositivi per la somministrazione dei farmaci come inalatori e iniettori. Date le alte spese di avviamento e le lunghe operazioni associate agli strumenti di produzione tradizionali, l'azienda ha riscontrato difficoltà nello sviluppo di prototipi di dispositivi medici complessi con i processi di fabbricazione tradizionali.
Così è passata alle stampanti 3D stereolitografiche desktop in-house per prototipare, testare e creare diversi dispositivi in un'ampia varietà di forme e dimensioni. Grazie alla stampa 3D Coalesce Product Development ha creato nuovi prototipi in meno di 24 ore, a un costo tra 10 e 20 volte inferiore rispetto a quello dell'esternalizzazione. Oltre alla stampa 3D dei prototipi, l'azienda stampa in 3D anche dime e fissaggi di prova per accelerare i test degli inalatori.
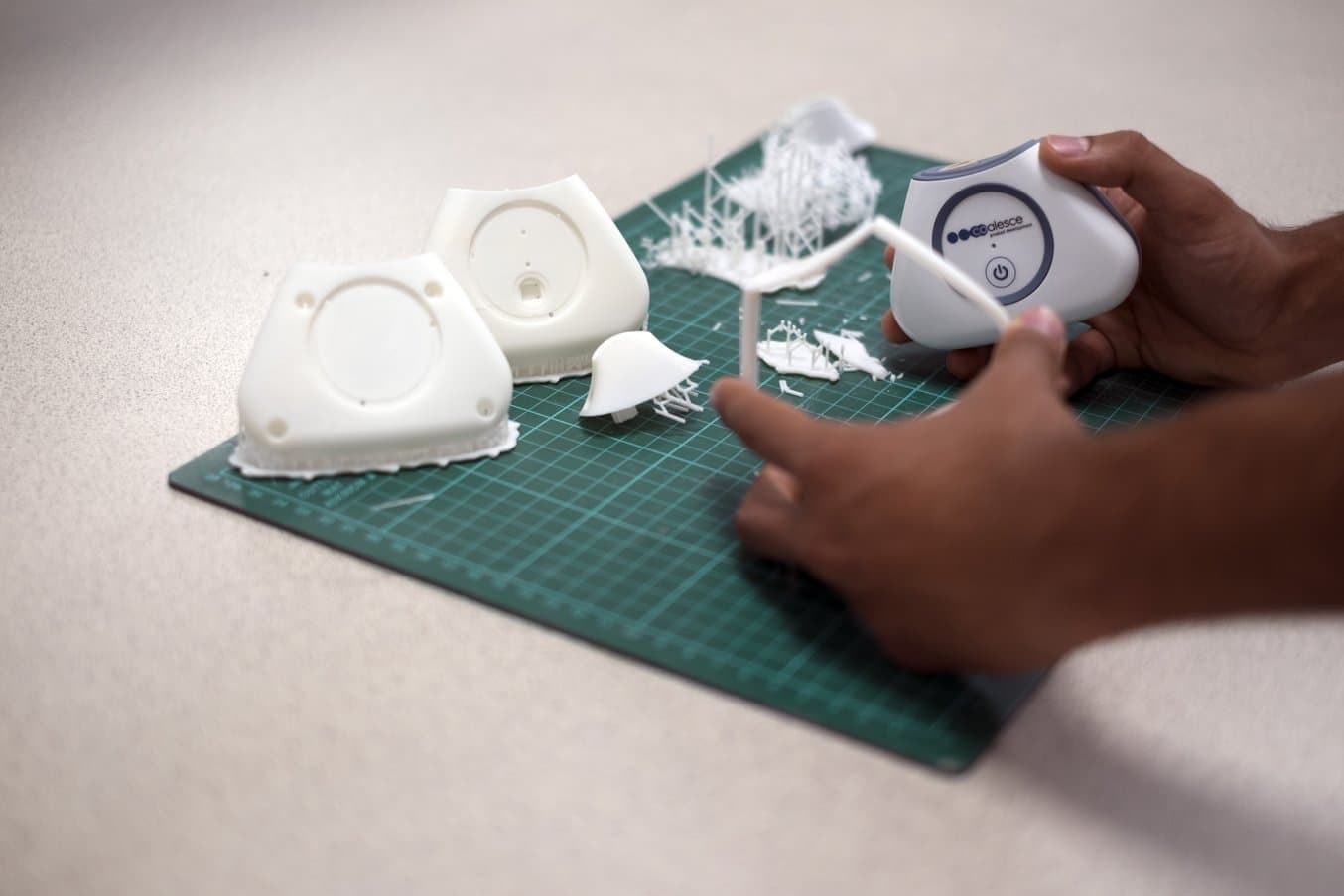
Coalesce, azienda che progetta dispositivi medici, utilizza la stampa 3D per la prototipazione di dispositivi per la somministrazione di farmaci, come gli inalatori.
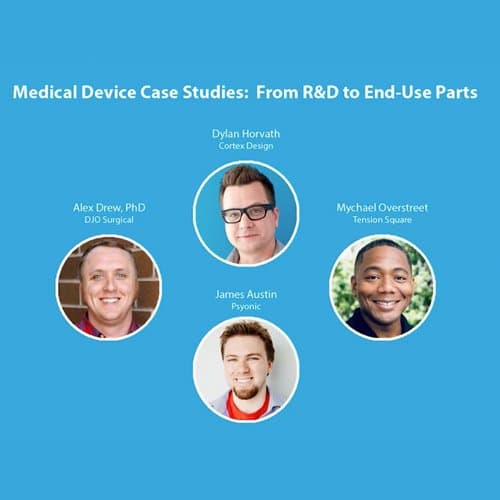
Casi di studio nell'ambito dei dispositivi medici: dalla fase di ricerca e sviluppo alle parti per uso finale
In questo webinar Gaurav Manchanda, direttore dello sviluppo del mercato medico di Formlabs, ospita alcuni clienti di Formlabs che operano nel settore medico. Si va dalle startup ad aziende più consolidate con vendite superiori a un miliardo di dollari, tra cui Cortex Design, DJO Surgical, Psyonic e TensionSquare.
Produzione di dispositivi medici su misura per i pazienti
La maggior parte dei processi di fabbricazione tradizionali, come lo stampaggio a iniezione e la termoformatura, richiedono attrezzature costose, e la spesa non viene ottimizzata se si producono parti personalizzate o su misura. La stampa 3D risponde a questa sfida in due modi.
Creazione rapida di attrezzature per i processi di fabbricazione tradizionali
Innanzitutto, la stampa 3D può essere utilizzata per la produzione rapida di attrezzature personalizzate come stampi, modelli, calchi e impronte per un'ampia varietà di processi di fabbricazione tradizionali, tra cui lo stampaggio a iniezione, la termoformatura, il sovrastampaggio, lo stampaggio con inserti, in silicone, a compressione, la fusione e molto altro.
Un esempio di formatura sottovuoto sono gli allineatori dentali e i retainer progettati e creati in base alla specifica anatomia di un paziente, riprodotta con dispositivi di scansione intraorali o desktop. Per produrre questi dispositivi è necessaria la formatura sottovuoto di un foglio di plastica su un modello personalizzato per ciascun passaggio del trattamento. Poiché sono in grado di realizzare questi modelli direttamente da file digitali nel giro di poche ore, le stampanti 3D sono diventate il metodo di riferimento per la produzione di questi dispositivi sempre più usati nell'ortodonzia.
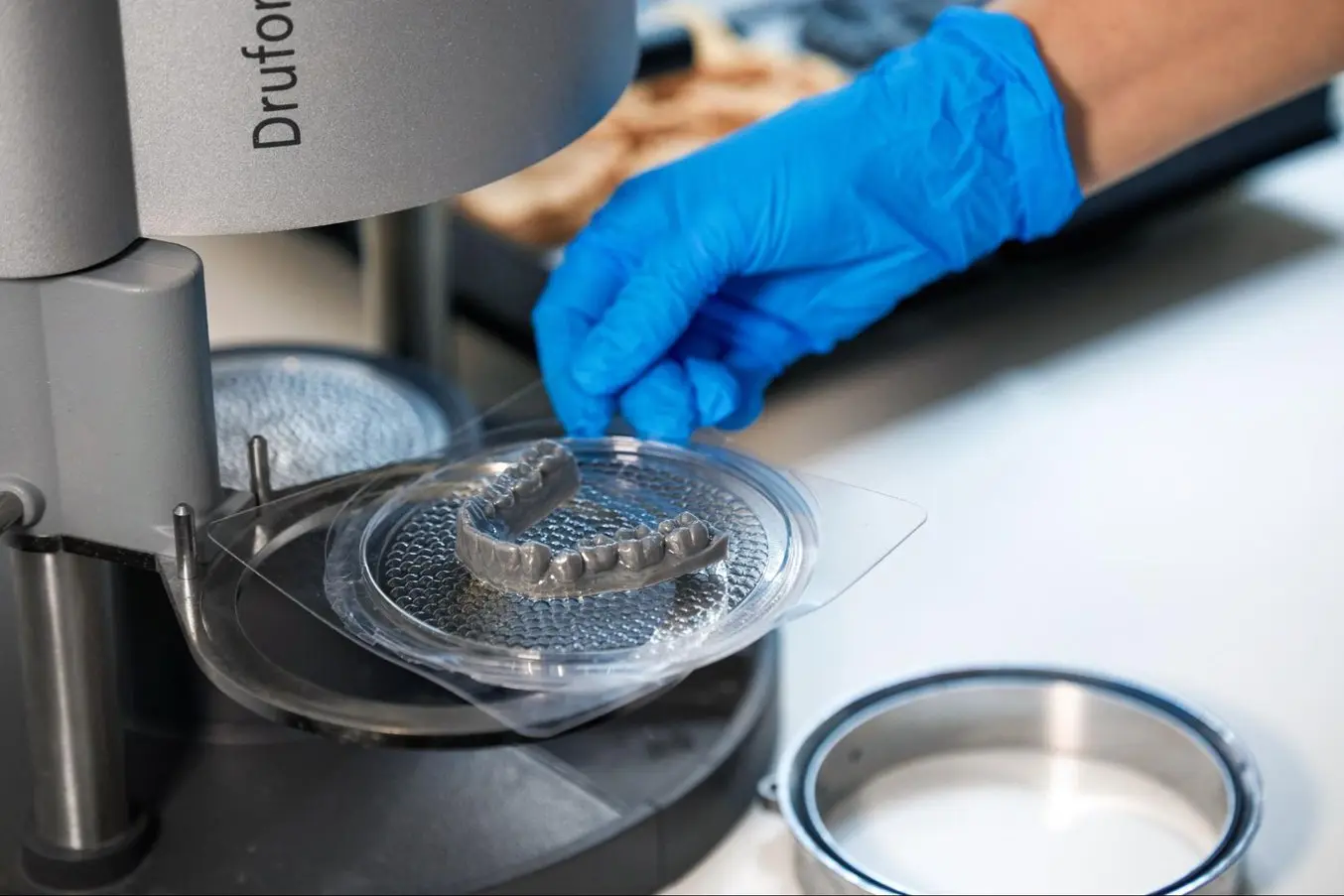
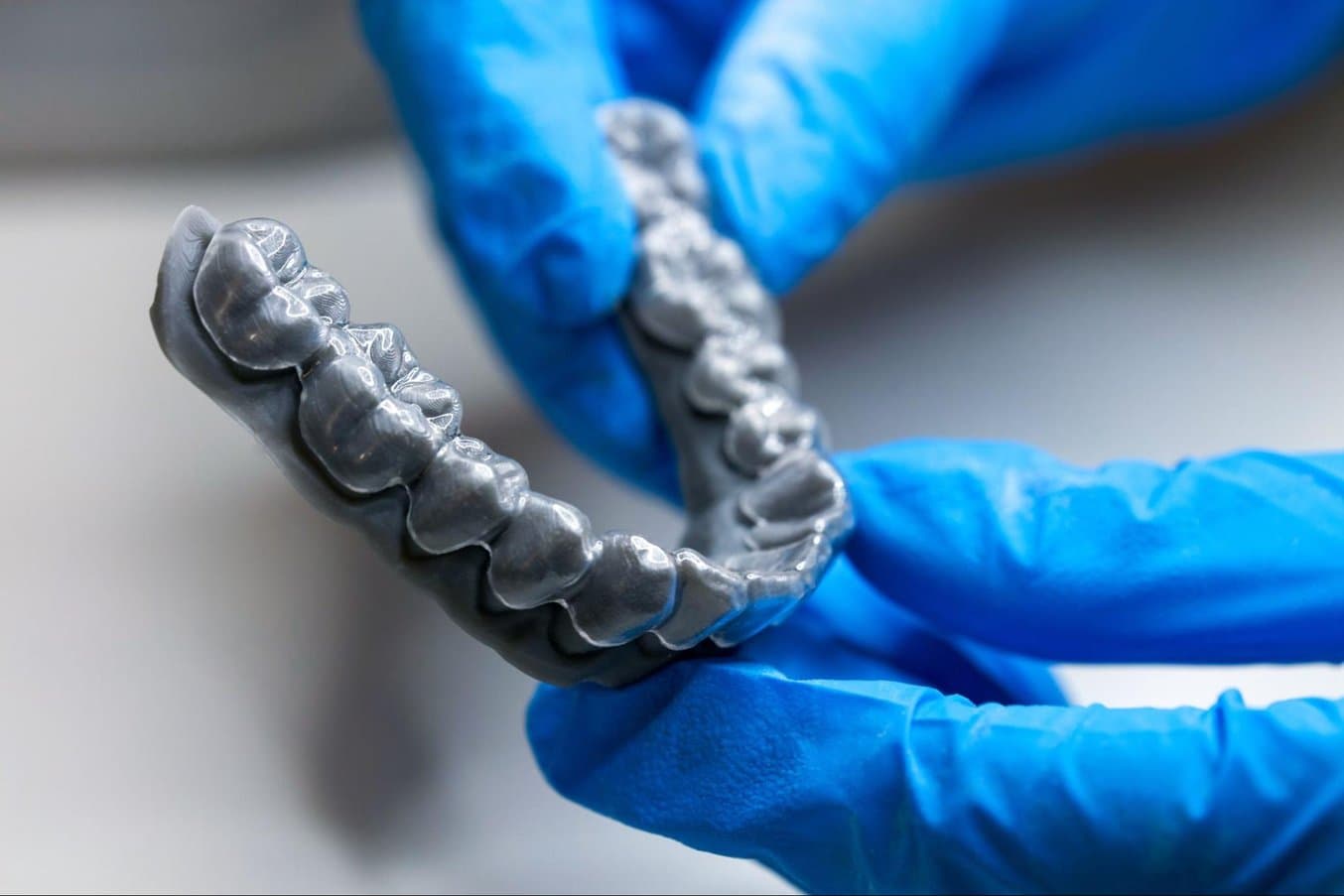
La stampa 3D è il metodo di riferimento per la produzione di modelli per la formatura sottovuoto di allineatori trasparenti e retainer.
Un altro esempio arriva da Cosm, un'azienda di dispositivi medici che ha sviluppato un trattamento di supporto per pazienti che soffrono di disturbi del pavimento pelvico. L'azienda utilizza stampi realizzati in 3D per lo stampaggio in silicone, così da creare un trattamento su misura per ciascun caso specifico.
L'utilizzo della stampa 3D offre a Cosm la flessibilità e la convenienza necessarie a produrre stampi di pessari su misura in 24 ore.
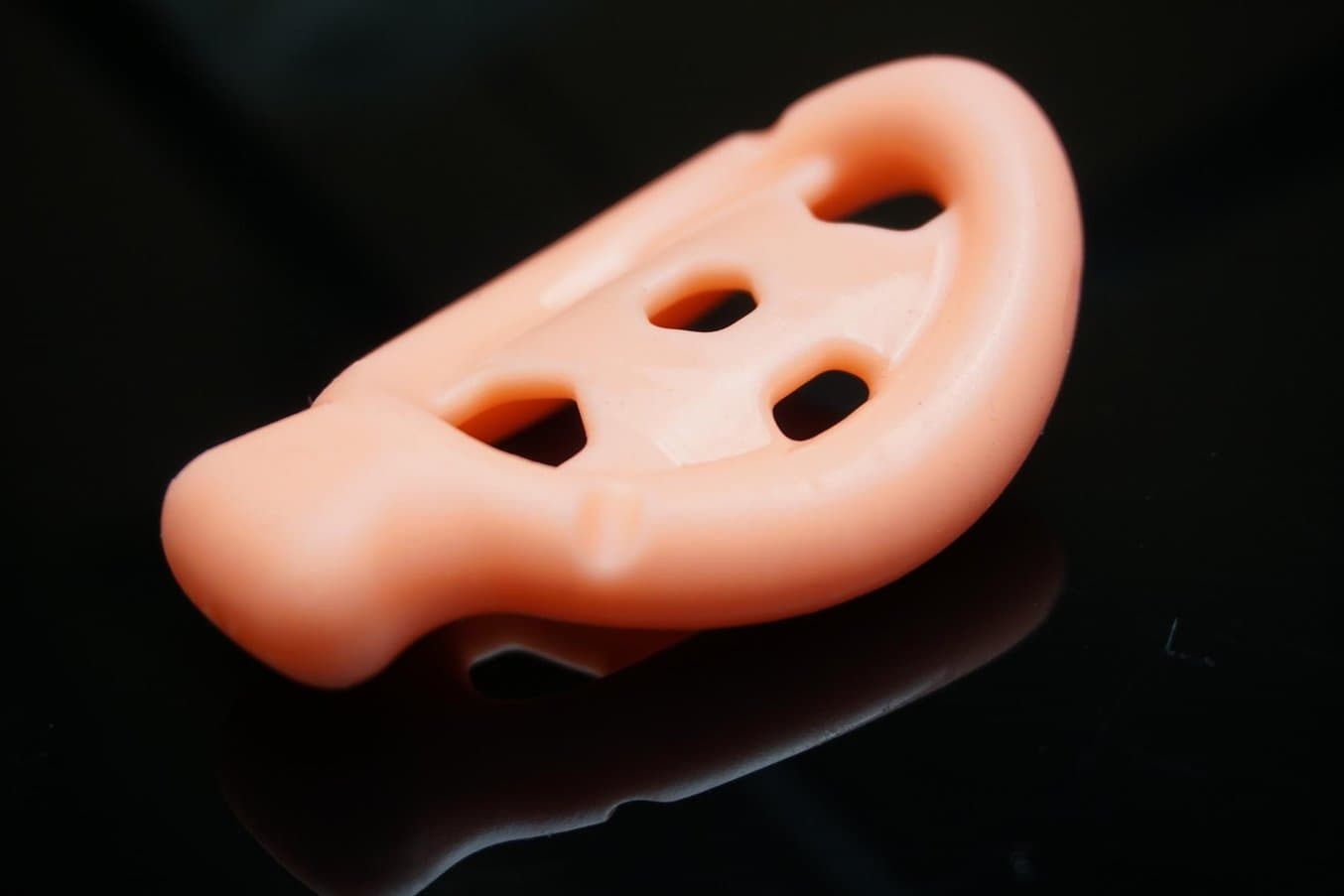
Cosm produce pessari personalizzati tramite lo stampaggio in silicone.
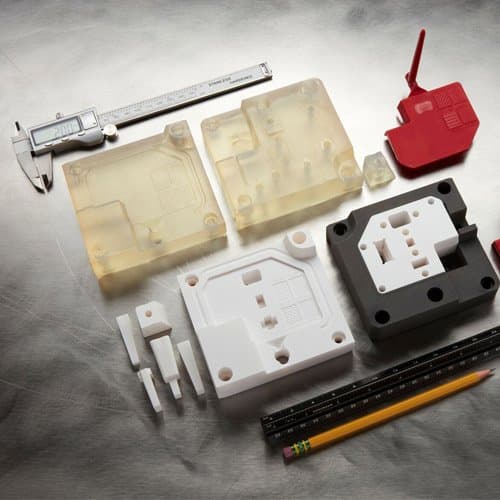
Realizzazione di stampi con la stampa 3D: tecniche di prototipazione e produzione
Scarica il nostro whitepaper per scoprire sei processi di stampaggio che si possono eseguire con una stampante 3D SLA in-house, tra cui lo stampaggio a iniezione, la formatura sottovuoto, lo stampaggio in silicone e tanti altri.
Stampa 3D diretta di dispositivi medici su misura per i pazienti
La stampa 3D è inoltre sempre più utilizzata per la produzione di dispositivi medici per utilizzo finale su misura per i pazienti. Poiché i processi di stampa 3D non richiedono attrezzature, è possibile creare parti su misura e design complessi in modo agile, conveniente ed efficiente.
Ancora una volta l'odontoiatria è uno dei campi della medicina che più si serve della stampa 3D. Dime chirurgiche, bite dentali, restauri temporanei e permanenti e protesi dentali possono essere stampati direttamente in 3D.
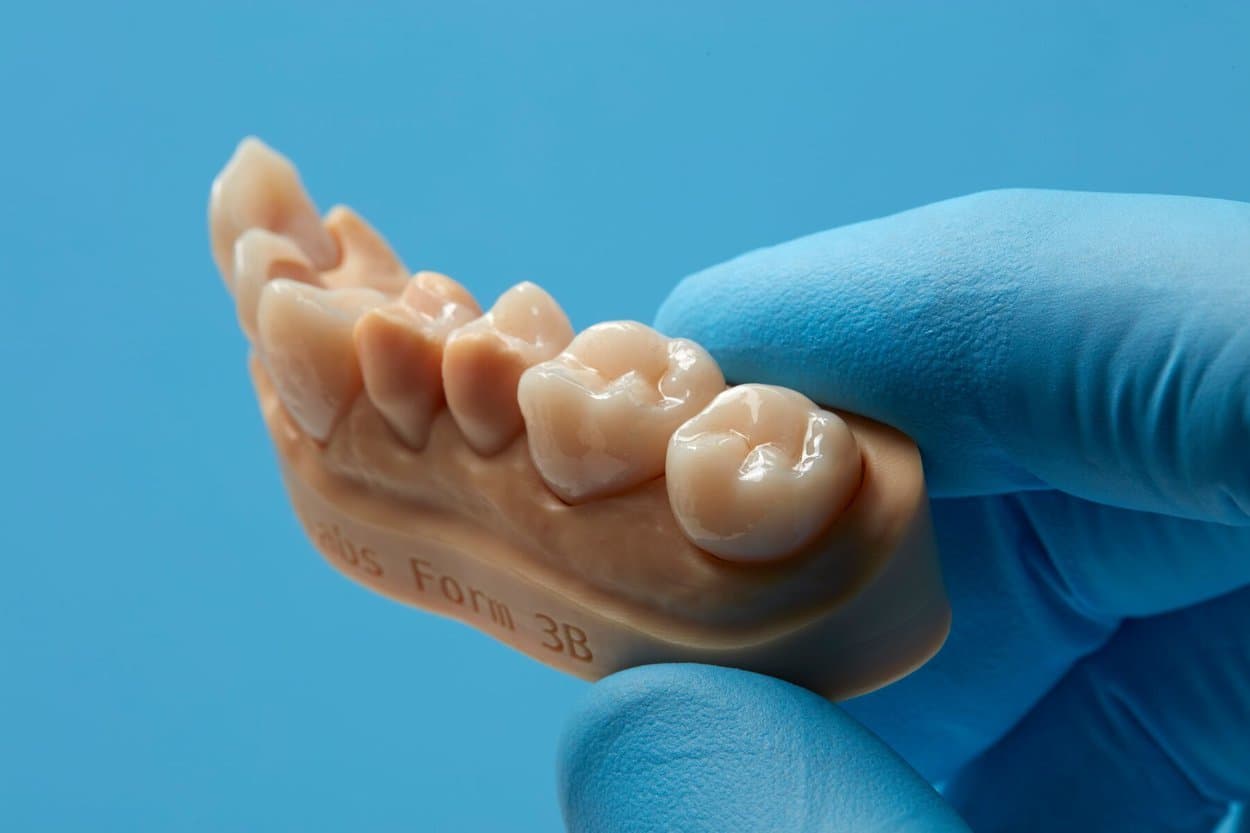
Le corone permanenti sono prodotte utilizzando una resina rafforzata con ceramica.
Altre applicazioni mediche della stampa 3D per utilizzo finale includono dispositivi auricolari su misura, come apparecchi acustici e attrezzature per la protezione dal rumore, nonché protesi su misura robuste e resistenti, plantari e molto altro.
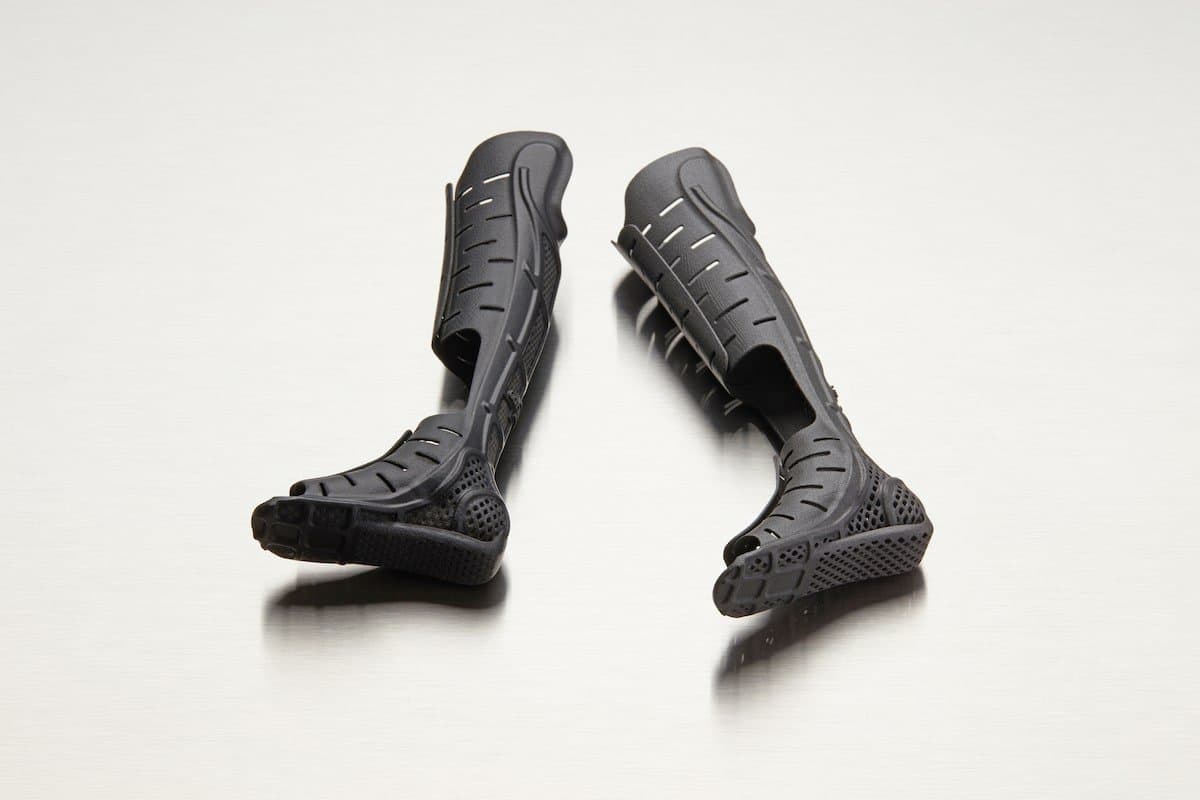
Con la stampa 3D è possibile creare protesi e plantari biocompatibili, resistenti e su misura per i pazienti a un prezzo accessibile e in tempi estremamente rapidi.
Il produttore di strumenti chirurgici restor3D sfrutta le possibilità le offerte dalla stampa 3D per migliorare notevolmente la fornitura di trattamenti chirurgici stampando in 3D strumenti specifici per impianti della spina cervicale. L'uso della stampa 3D consente all'azienda di creare strumenti sterili progettati apposta per la chirurgia, con un processo di sviluppo davvero agile. L'approccio di restor3D riduce le spese di sterilizzazione, stoccaggio e sala operatoria per ospedali e centri di chirurgia. C'è stata infatti un'alta richiesta: oltre 25 apparecchi Formlabs sono attivi giorno e notte per la produzione dei dispositivi.
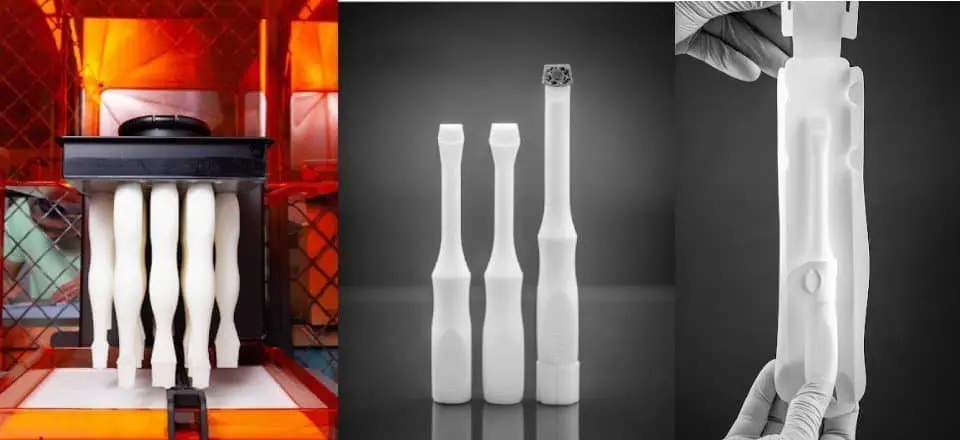
restor3d utilizza la stampa 3D per produrre strumenti chirurgici specifici per ciascun intervento.
Produzione di dispositivi medici per utilizzo finale
La stampa 3D è sempre più diffusa, oltre che nell'ambito degli strumenti chirurgici, in quello dei dispositivi medici o dei loro componenti, soprattutto nel caso di design complessi che sarebbero inefficienti o impossibili da realizzare con i processi tradizionali.
TensionSquare ha commercializzato un dispositivo con un sistema di decompressione mediante ago fissato in posizione per impedire pieghe, attorcigliamenti o spostamenti che spesso causano incidenti evitabili. Dopo anni di ricerca e sviluppo, oggi l'azienda stampa in 3D il dispositivo per utilizzo finale sulla stampante a sinterizzazione laser selettiva (SLS) Fuse 1, che consente di dipendere meno da fornitori esterni e produrre oltre 100 dispositivi a stampante nel giro di 24 ore. L'azienda, fondata da un paramedico e da un veterano, ha l'obiettivo di produrre milioni di parti l'anno con la stampa 3D nei suoi impianti di produzione negli Stati Uniti.
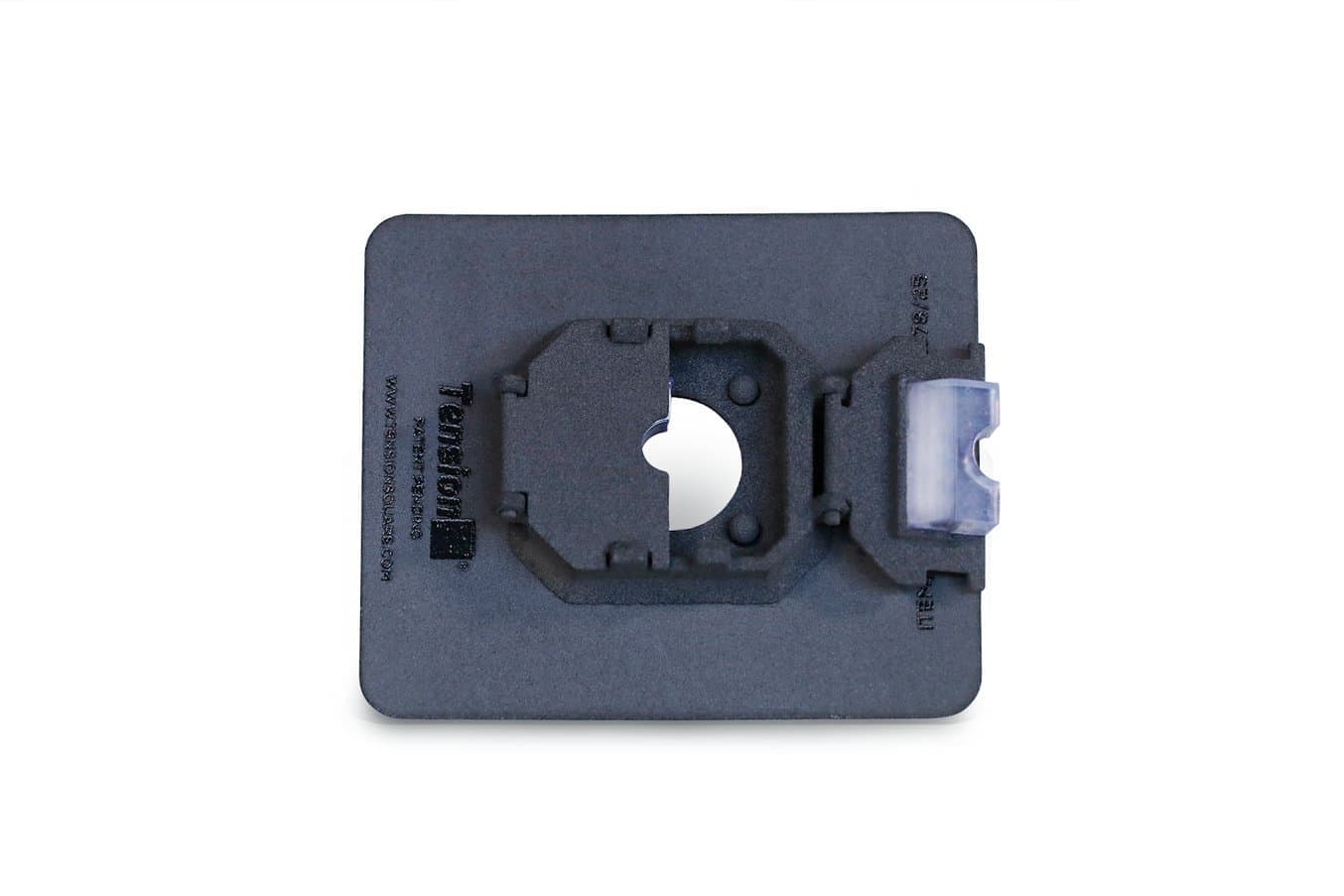
TensionSquare realizza un dispositivo di stabilizzazione del catetere a decompressione PTX utilizzando direttamente la stampa 3D SLS.
VO2 Master ha sviluppato un analizzatore metabolico più facile da utilizzare e meno costoso degli apparecchi già in commercio. Dopo essersi servita ampiamente della stampa 3D nel processo di prototipazione, l'azienda ha deciso di stampare in 3D anche le scocche esteriori per utilizzo finale del dispositivo, così da lanciarlo più velocemente sul mercato. Le scocche vengono realizzate con stampanti 3D SLA in Tough 1500 Resin, un materiale resiliente che simula la resistenza e la rigidità del polipropilene. Le parti stampate sono verniciate di bianco prima di essere fissate alla mascherina, in questo modo si migliora la finitura superficiale, la colorazione goffrata e la resistenza.
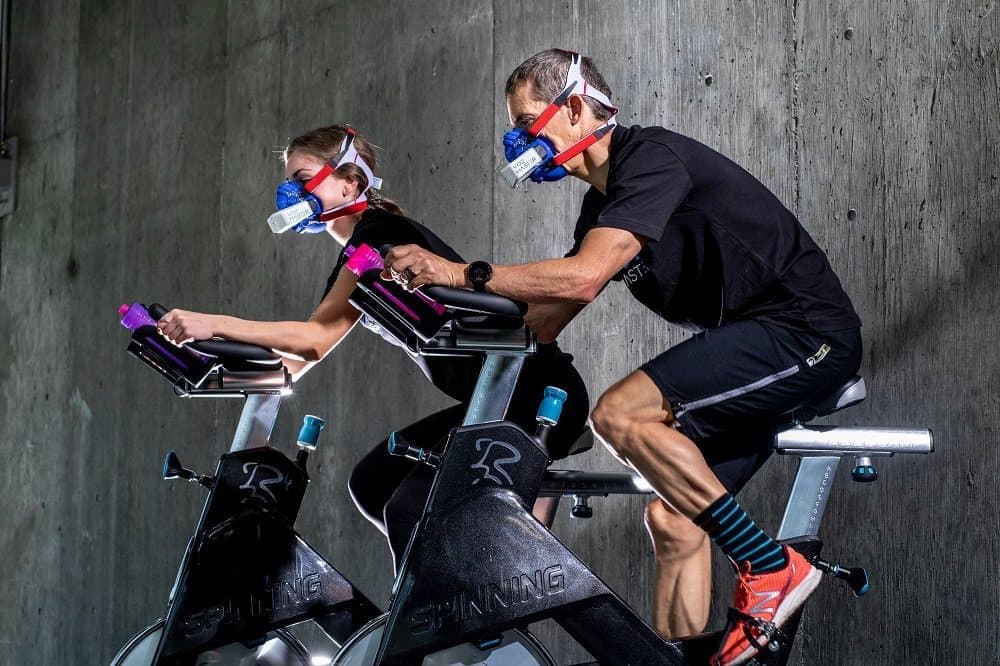
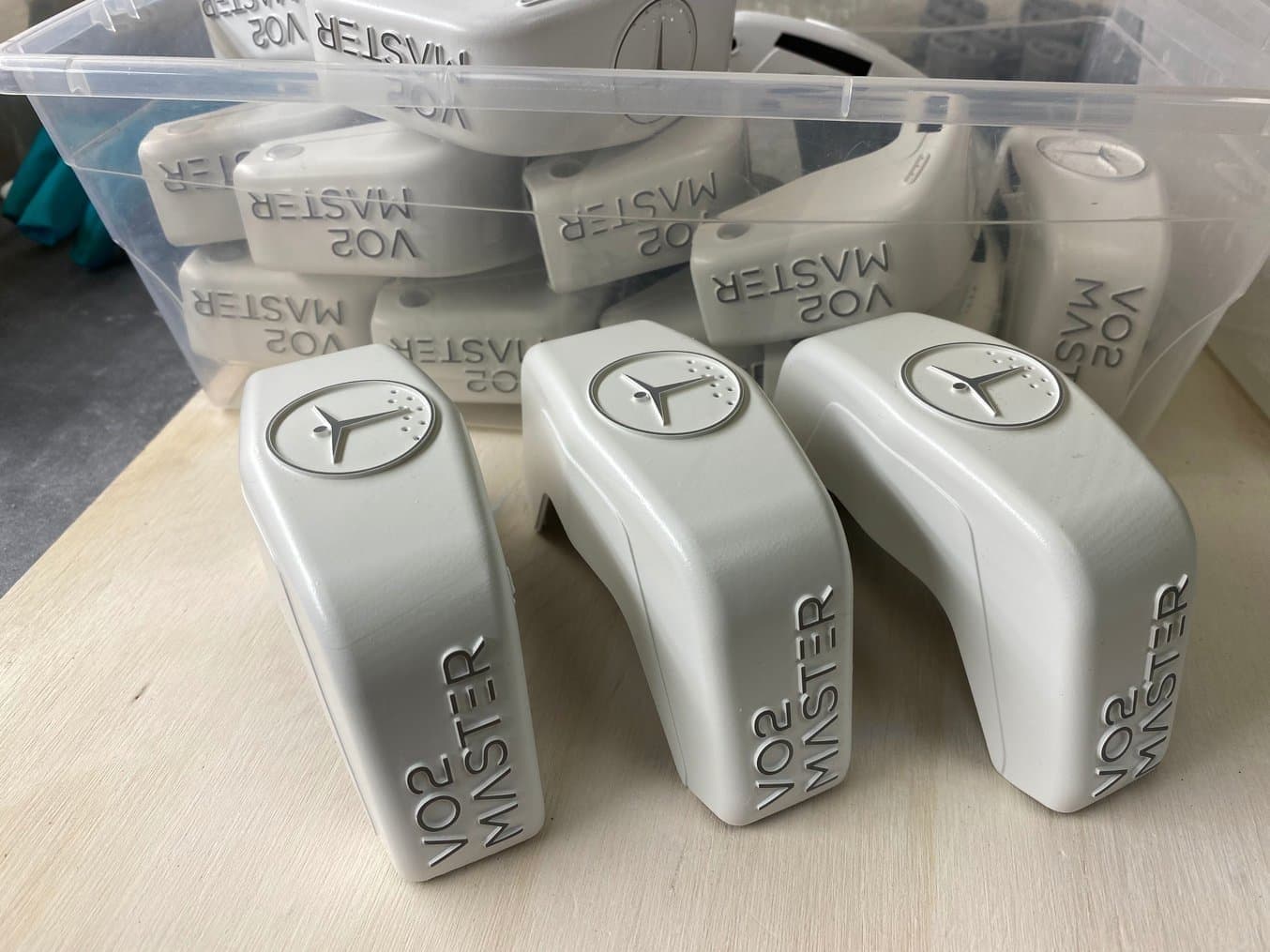
VO2 Master stampa la scocca esterna per l'analizzatore metabolico portatile, così da farlo arrivare prima sul mercato.
Produzione di forniture mediche d’emergenza
A causa della pandemia di COVID-19 si è verificata una situazione senza precedenti, con strutture sanitarie congestionate e scarsità di forniture mediche, così i governi hanno cercato risorse in luoghi inesplorati. Per affrontare la crescente necessità di forniture, i produttori di automobili si sono dedicati alla fabbricazione di respiratori, mentre le case di moda hanno prodotto attrezzature protettive per contribuire ad affrontare le nuove sfide associate alla pandemia.
Con l'aumento di casi di COVID-19, è cresciuta l'esigenza di test su larga scala, e questo ha portato a una carenza a livello globale di tamponi nasofaringei, necessari a raccogliere i campioni per i test. Una volta appurato che i tamponi nasali per i test COVID-19 erano molto richiesti e le forniture erano estremamente limitate, un gruppo di esperti di USF Health, Northwell Health e Formlabs ha collaborato alla creazione di un'alternativa realizzata tramite stampa 3D. Il team ha lavorato per una settimana alla sviluppo di un prototipo di tampone nasale e l'ha testato nei laboratori di USF Health e Northwell Health. In due giorni USF Health e Northwell Health hanno sviluppato prototipi con le stampanti 3D Formlabs e resine biocompatibili e autoclavabili. A soli dodici giorni dall'idea iniziale il design finale è stato approntato per l'uso clinico e il file 3D è stato messo a disposizione di altri sistemi sanitari in tutto il mondo. Oltre al file gli esperti hanno sviluppato un flusso di lavoro dettagliato con linee guida, in modo che utenti qualificati del settore sanitario potessero stampare i tamponi e garantire la salute e la sicurezza dei pazienti.
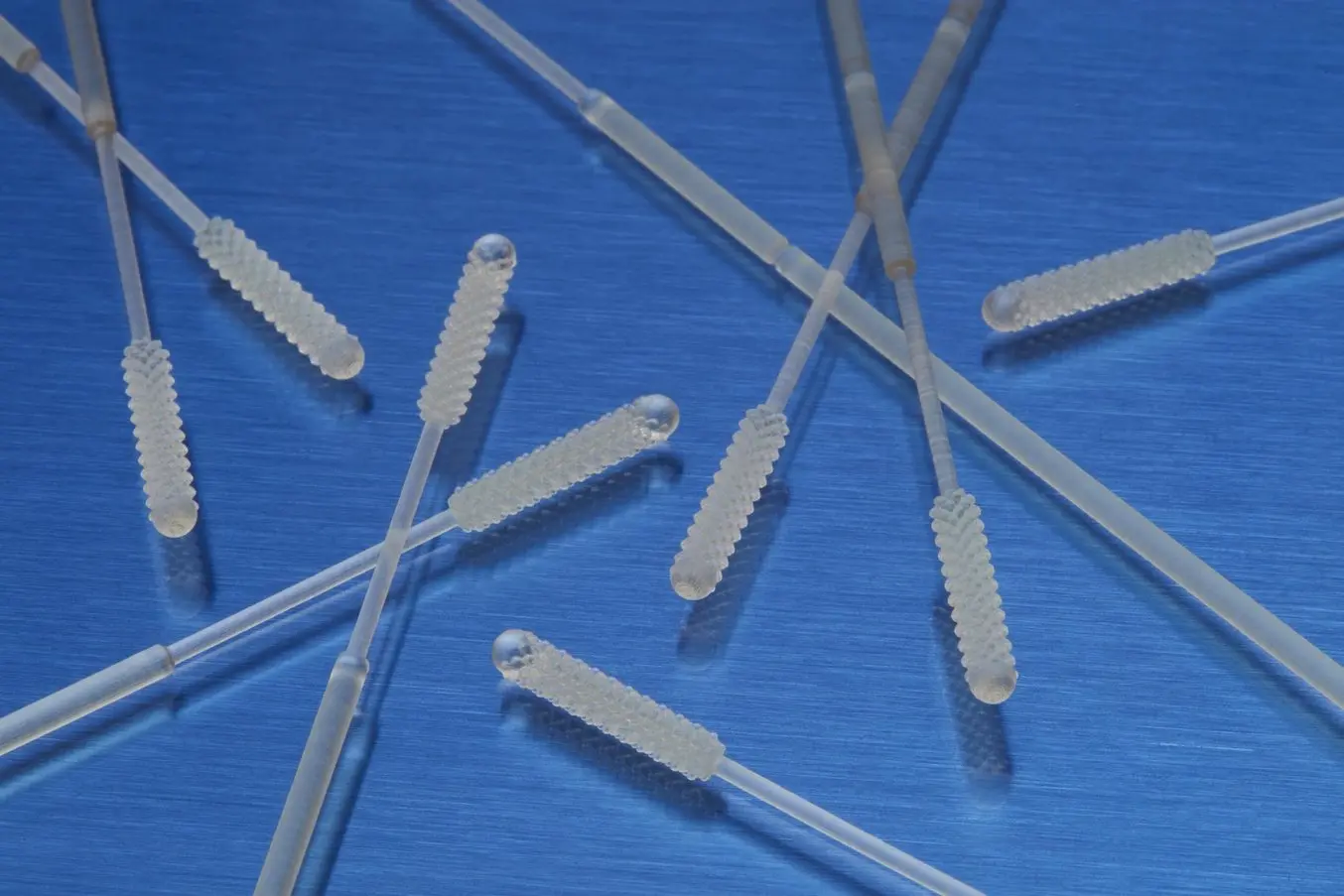
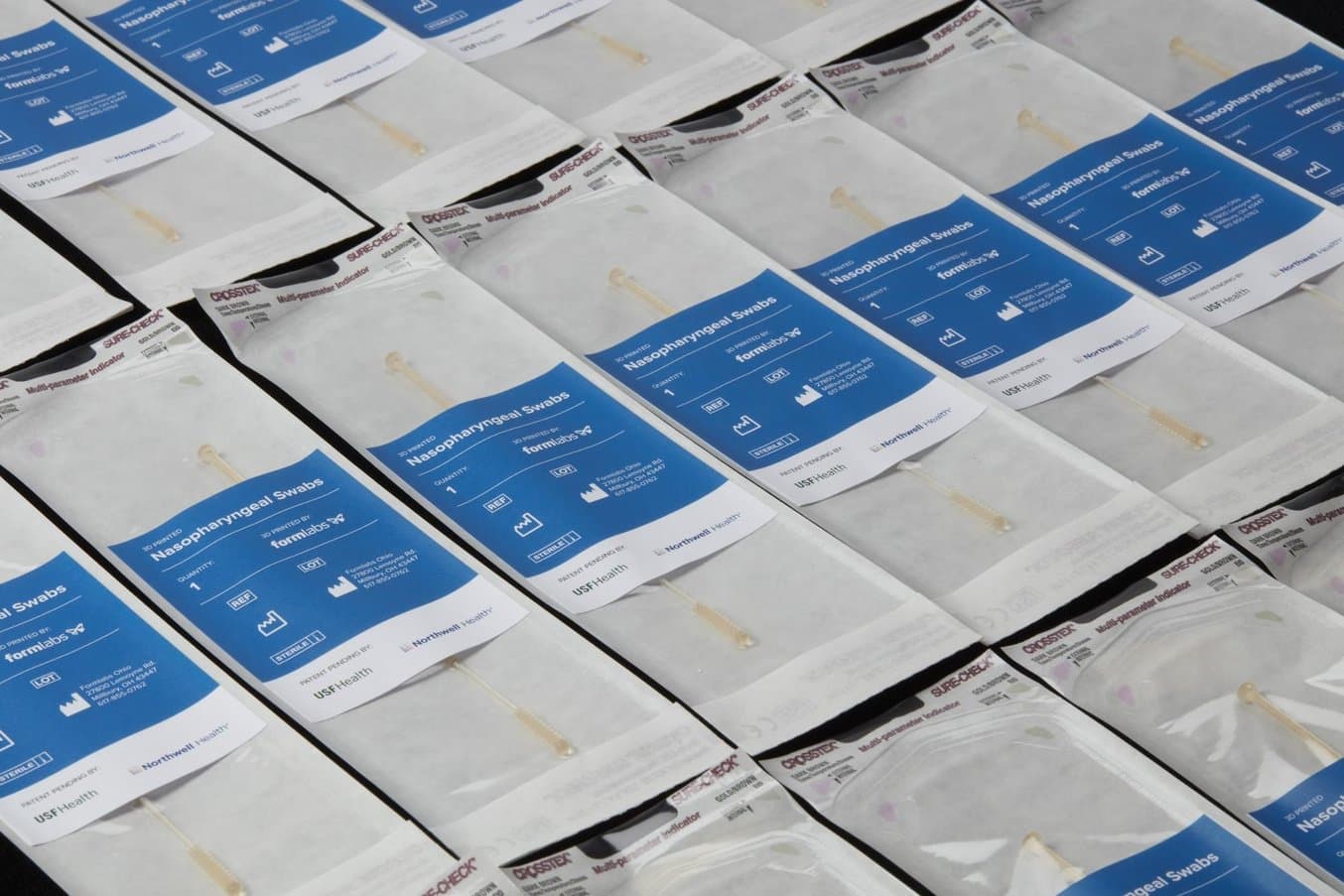
Nella fase iniziale della pandemia di COVID-19 i tamponi stampati in 3D hanno consentito oltre 70 milioni di test in 25 Paesi.
Ospedali, laboratori odontotecnici e centri medici accademici che usavano le stampanti 3D per realizzare dispositivi chirurgici su misura per i pazienti sono stati in grado di utilizzare l'attrezzatura per un nuovo scopo e hanno supplito alle mancanze della catena di fornitura producendo tamponi stampati in 3D in-house. Con un design accessibile, un'attrezzatura poco costosa e processi collaudati, la progettazione del tampone ha consentito la realizzazione di oltre 70 milioni di test COVID in 25 Paesi.
Tra le altre soluzioni per soddisfare la richiesta di nuovi respiratori c'è stata la conversione di macchinari BiPAP normalmente impiegati per le apnee notturne. Affinché la conversione vada a buon fine, è necessario l'uso di un adattatore che trasforma le macchine in respiratori meccanici invasivi funzionali.
Per garantire la creazione rapida di un numero sufficiente di adattatori BiPAP che supportassero la respirazione artificiale, Northwell Health, il più grande fornitore medico di New York, ha progettato degli adattatori BiPAP stampabili in 3D. L'Agenzia per gli alimenti e i medicinali degli Stati Uniti (FDA) ha fornito a Formlabs un'autorizzazione d'emergenza per stampare in 3D gli adattatori, così da assistere le strutture sanitarie quando i respiratori tradizionali non erano disponibili.
Processi di stampa 3D per dispositivi medici
Quando si tratta di stampare in 3D dispositivi medici, non tutti i metodi sono uguali. È importante scegliere la tecnologia di stampa più adatta a ogni specifico caso d'uso.
Tra le tecnologie di stampa 3D per dispositivi medici più note ci sono la stereolitografia (SLA), la sinterizzazione laser selettiva (SLS), la modellazione a deposizione fusa (FDM), la sinterizzazione laser diretta dei metalli (DMLS), che si usa per le parti in plastica e in metallo, e la fusione laser selettiva (SLM) per i metalli.
Stereolitografia (SLA)
Le stampanti SLA utilizzano un laser per polimerizzare la resina liquida, trasformandola in plastica indurita: questo processo viene chiamato fotopolimerizzazione. La stereolitografia è uno dei processi più apprezzati dai professionisti del settore medico grazie all'alta risoluzione, alla precisione e alla versatilità dei materiali.
-
Vantaggi della stereolitografia
Le parti stampate in stereolitografia presentano una migliore risoluzione e precisione, dettagli più precisi e finiture superficiali più lisce rispetto a tutte le altre tecnologie di stampa 3D. Il vantaggio principale della SLA rimane comunque la sua versatilità. La formulazione delle resine per stereolitografia offre una vasta gamma di proprietà ottiche, meccaniche e termiche in grado di imitare quelle delle termoplastiche industriali, standard e ingegneristiche.
La stereolitografia è un'ottima scelta per prototipi di dispositivi medici estremamente dettagliati che richiedono tolleranze strette e superfici lisce, nonché per stampi, attrezzature, modelli per uso medico e parti per uso finale funzionali. La stereolitografia offre la più ampia gamma di materiali biocompatibili per applicazioni odontoiatriche e mediche. Con la Draft Resin le stampanti SLA di Formlabs sono anche l'opzione più rapida per la stampa 3D di prototipi di grandi dimensioni, fino a dieci volte più velocemente rispetto alla modellazione a deposizione fusa.
-
Svantaggi della stereolitografia
L'ampia versatilità della stereolitografia si accompagna a una fascia di prezzo leggermente più alta rispetto alla modellazione a deposizione fusa, ma rimane comunque più economica di tutti gli altri processi di stampa 3D. Dopo la stampa, le parti in resina ottenute tramite stereolitografia richiedono inoltre una post-elaborazione, cioè il lavaggio e la polimerizzazione post-stampa delle parti.
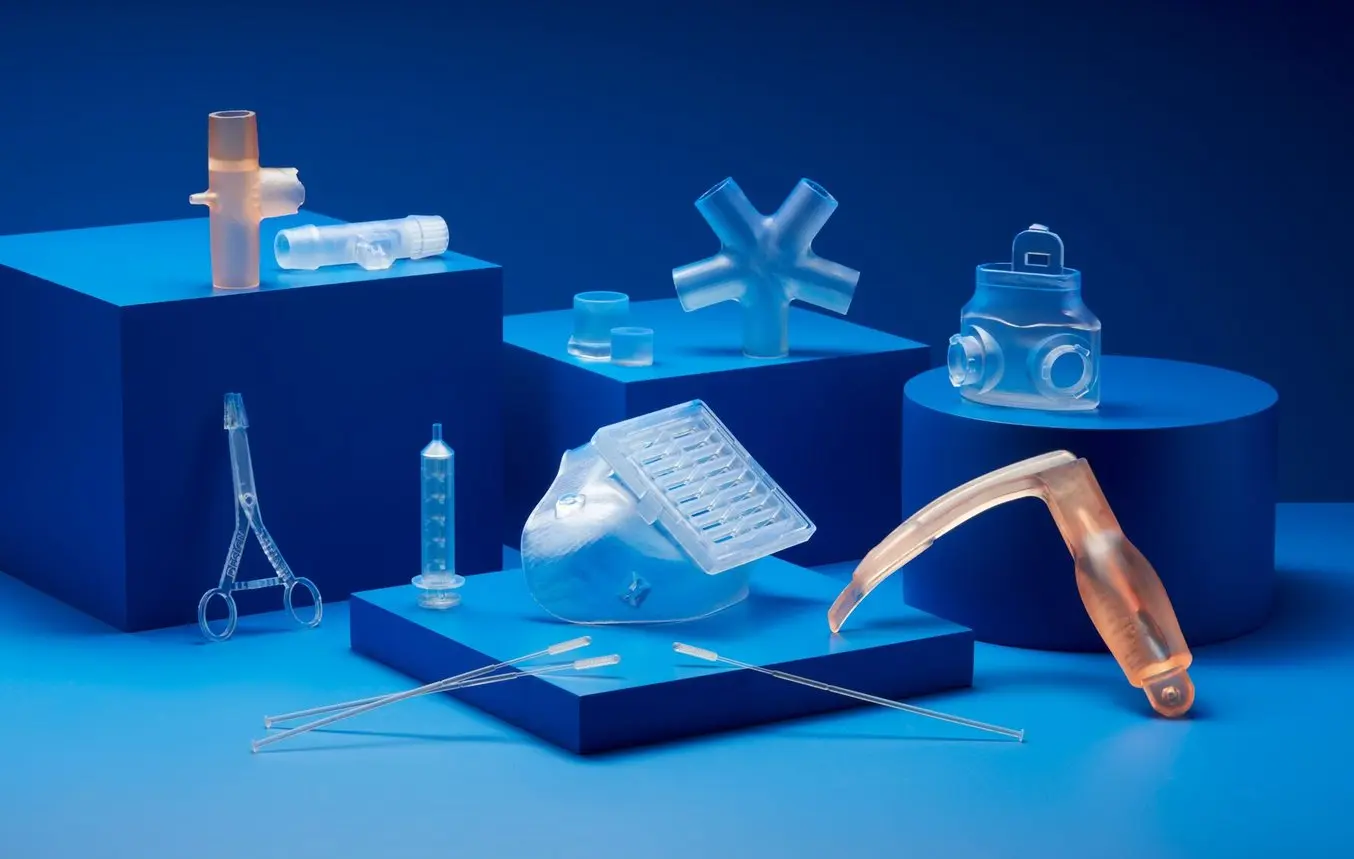
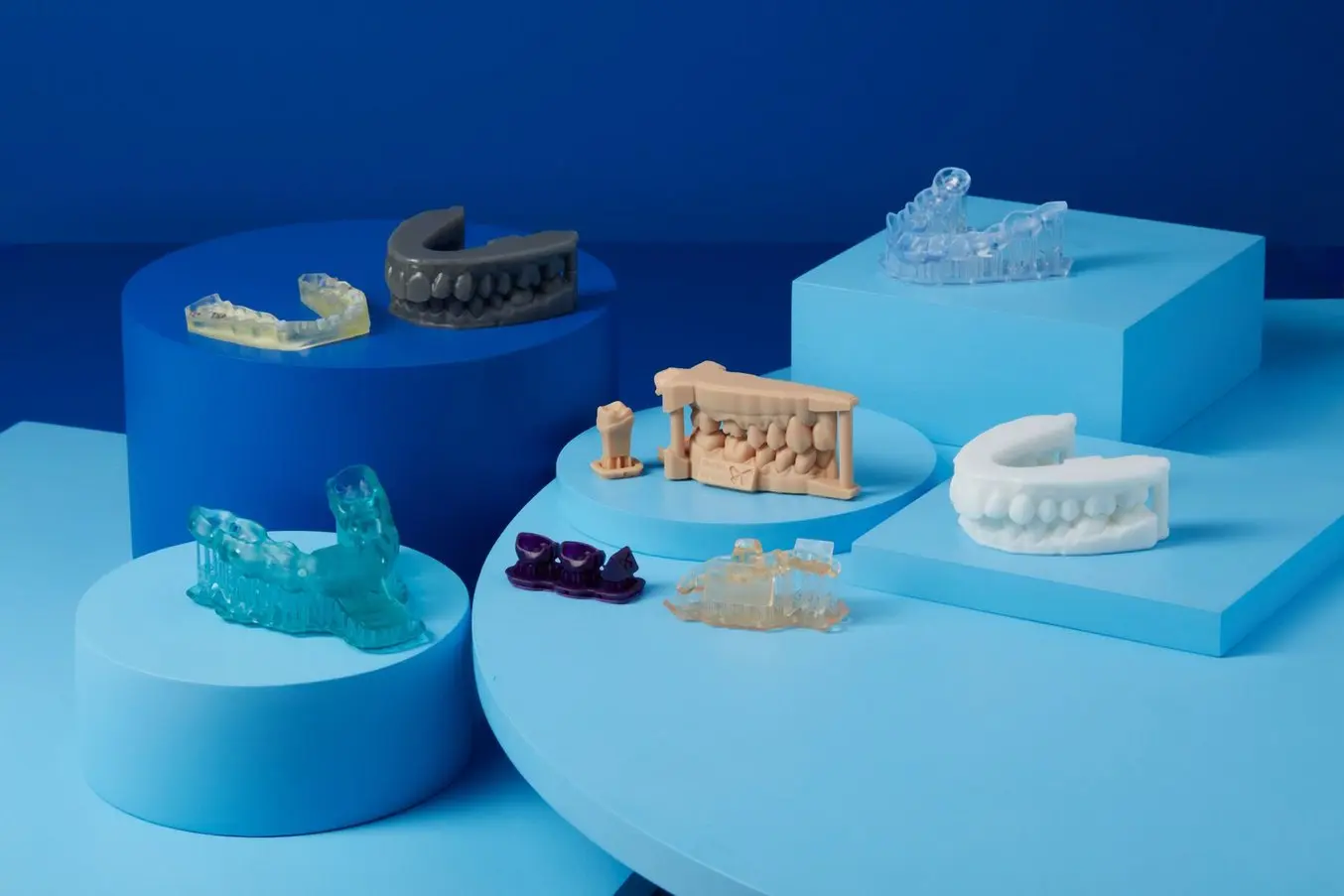
La stampa 3D SLA offre un'ampia gamma di materiali per la stampa 3D, tra cui materiali biocompatibili per una grande varietà di applicazioni mediche e odontoiatriche.
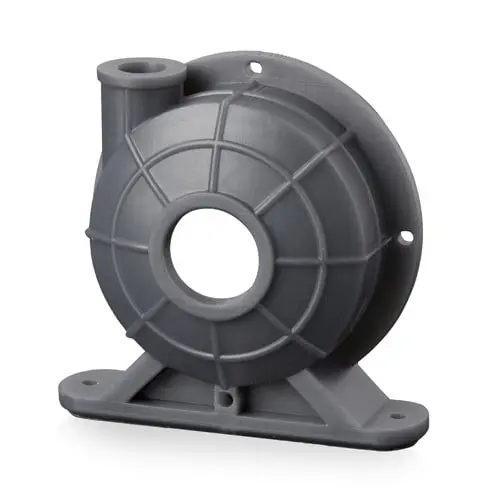
Richiedi un campione gratuito
Guarda e tocca con mano la precisione di Formlabs. Saremo lieti di inviare presso la tua azienda un campione gratuito.
Sinterizzazione laser selettiva (SLS)
Le stampanti 3D SLS utilizzano un laser ad alta potenza per fondere piccole particelle di polvere di polimeri. La polvere non fusa sostiene la parte durante il processo di stampa ed elimina la necessità di strutture di supporto dedicate, una caratteristica che rende la sinterizzazione laser selettiva particolarmente efficace per la realizzazione di parti meccaniche complesse.
Grazie alla sua capacità di produrre parti con ottime proprietà meccaniche, la sinterizzazione laser selettiva è la tecnica di produzione additiva polimerica più comune per le applicazioni industriali. A seconda del materiale, le parti SLS in nylon possono essere anche biocompatibili e sterilizzabili.
-
Vantaggi della sinterizzazione laser selettiva
La sinterizzazione laser selettiva (SLS) non richiede strutture di supporto specifiche ed è ideale per figure geometriche complesse, inclusi dettagli interni, sottosquadri, pareti sottili e dettagli in negativo. Le parti stampate con la sinterizzazione laser selettiva hanno caratteristiche meccaniche eccellenti, con una resistenza simile a quella delle parti create a iniezione.
Il materiale più utilizzato per la sinterizzazione laser selettiva è il nylon, una termoplastica ingegneristica molto diffusa, con proprietà meccaniche eccellenti. Il nylon è leggero, robusto, flessibile e resistente agli impatti, alle sostanze chimiche, al calore, ai raggi UV, all'acqua e allo sporco. Le parti in nylon stampate in 3D possono anche essere biocompatibili e non sensibilizzanti, quindi sono pronte da indossare e garantiscono un uso sicuro in molti contesti.
La combinazione di costo ridotto per parte, alta produttività, materiali diffusi e biocompatibilità rende la sinterizzazione laser selettiva una scelta molto diffusa tra i creatori di dispositivi medici per la prototipazione funzionale, nonché un'alternativa economica allo stampaggio a iniezione per la produzione ponte o di un numero limitato di parti.
-
Svantaggi della sinterizzazione laser selettiva
Le stampanti SLS, rispetto a quelle FDM ed SLA, richiedono un investimento iniziale più alto. Nonostante il nylon sia un materiale estremamente versatile, la gamma di materiali adatti alla sinterizzazione laser selettiva è più limitata rispetto alla modellazione a deposizione fusa o alla stereolitografia. Le parti escono dalla stampante con una finitura superficiale leggermente ruvida e per renderle lisce è necessario un processo di sabbiatura.

La stampa 3D SLS è l'ideale per ottenere prototipi funzionali robusti, nonché parti per uso finale come protesi e plantari.
Modellazione a deposizione fusa (FDM)
La modellazione a deposizione fusa (FDM), nota anche come fabbricazione a fusione di filamento (FFF), è un metodo di stampa che crea parti fondendo ed estrudendo un filamento termoplastico, che viene poi depositato sull’area di stampa dall’ugello della stampante, strato per strato.
La modellazione a deposizione fusa è la forma di stampa 3D più diffusa tra i consumatori, soprattutto grazie a un numero crescente di hobbisti. Ma le stampanti FDM industriali sono diffuse anche tra i professionisti.
-
Vantaggi della modellazione a deposizione fusa
La modellazione a deposizione fusa può essere utilizzata con un’ampia gamma di termoplastiche standard, come ad esempio l’acrilonitrile-butadiene-stirene (ABS), l’acido polilattico (PLA) e le loro varie miscele. Questo comporta un costo contenuto per l’investimento iniziale e i materiali. La modellazione a deposizione fusa è più adatta ai modelli Proof-of-Concept semplici e alla prototipazione a basso costo di parti semplici. Alcuni materiali FDM sono anche biocompatibili.
-
Svantaggi della modellazione a deposizione fusa
La modellazione a deposizione fusa offre una risoluzione e una precisione inferiori rispetto ad altre tecniche di stampa 3D per le plastiche come la stereolitografia o la sinterizzazione laser selettiva. Questo vuol dire che non è l'opzione più adatta per la stampa di design complessi o parti con dettagli elaborati. Per ottenere una finitura di alta qualità sono necessari lenti processi di lucidatura meccanica e chimica, che richiedono molta manodopera. Alcune stampanti 3D FDM industriali utilizzano supporti solubili per ridurre al minimo queste problematiche e offrire una vasta gamma di termoplastiche ingegneristiche, ma hanno un costo decisamente elevato. Inoltre, quando si realizzano parti di grandi dimensioni, la stampa FDM tende a essere più lenta della stereolitografia o della sinterizzazione laser selettiva.
Sinterizzazione laser diretta dei metalli (DMLS) e fusione laser selettiva (SLM)
Le stampanti 3D a sinterizzazione laser diretta dei metalli (DMLS) e a fusione laser selettiva (SLM) hanno un funzionamento simile alle stampanti SLS, ma anziché servirsi dei polimeri, usano un laser per fondere insieme particelle di polvere di metallo strato dopo strato.
Le stampanti 3D SLM e DMLS sono in grado di creare prodotti in metallo robusti, precisi e complessi, il che rende questo processo ideale per applicazioni aerospaziali, automobilistiche e mediche.
-
Vantaggi della sinterizzazione laser diretta dei metalli e della fusione laser selettiva
Il più grande vantaggio di questi processi è costituito naturalmente dai materiali, perché le stampanti 3D DMLS ed SLM sono in grado di produrre dispositivi medici per utilizzo finale ad alte prestazioni e componenti metallici. Questi processi possono riprodurre geometrie complesse e i prodotti finali sono robusti, resistenti e biocompatibili. Possono inoltre essere usati per produrre impianti generici (per ginocchia, anche, colonna vertebrale, ecc.) e impianti personalizzati per il trattamento di tumori o di traumi, nonché per protesi dentali e per prodotti tecnologici medici e ortopedici.
-
Svantaggi della sinterizzazione laser diretta dei metalli e della fusione laser selettiva
Anche se i prezzi delle stampanti 3D per il metallo hanno iniziato ad abbassarsi, con costi che vanno da 200 000 $ a oltre un milione di dollari, risultano ancora proibitivi per la maggior parte delle aziende. I processi di stampa 3D in metallo hanno inoltre un workflow complesso, che richiede un intervento consistente da parte dell'utente.
In alternativa, la stampa 3D SLA è adatta ai workflow di fusione di parti metalliche a costi ridotti, con una maggiore libertà di design e tempi di realizzazione inferiori rispetto ai metodi tradizionali.
Processi di stampa 3D per dispositivi medici
La tabella qui di seguito mostra le tecnologie di stampa più adatte a gestire le diverse applicazioni della stampa 3D di dispositivi medici.
Stereolitografia (SLA) | Sinterizzazione laser selettiva (SLS) | Modellazione a deposizione fusa (FDM) | Stampa 3D in metallo (DMLS, SLM) | |
---|---|---|---|---|
Volume di stampa | Fino a 300 x 335 x 200 mm (stampanti 3D desktop e da banco) | Fino a 165 x 165 x 300 mm (stampanti 3D da banco industriali) | Fino a 300 x 300 x 600 mm (stampanti 3D desktop e da banco) | Fino a 400 x 400 x 400 mm (DMLS/SLM industriali di grande formato) |
Fascia di prezzo | A partire da 3500 $ | A partire da 16 500 $ | A partire da 2500 $ | A partire da 200 000 $ |
Materiali | Varietà di resine (plastiche termoindurenti). Standard, ingegneristiche (simili ad ABS, simili a PP, simili al silicone, flessibili, resistenti al calore, rigide), colabili, dentali e mediche (biocompatibili). | Termoplastiche ingegneristiche, di solito il nylon e i suoi composti (il nylon è biocompatibile e compatibile con la sterilizzazione). | Termoplastiche standard, ad esempio ABS, PLA e loro miscele. | Acciaio inossidabile, acciaio per strumenti, titanio, cobalto cromato e alluminio. |
Applicazioni ideali | Prototipi molto dettagliati che richiedono tolleranze strette e superfici lisce, stampi, attrezzature, modelli per uso medico, parti funzionali, dispositivi medici e odontoiatrici per utilizzo finale. | Geometrie complesse, prototipi funzionali, produzione ponte o di piccoli lotti, plantari e protesi. | Modelli Proof-of-Concept semplici, prototipazione a basso costo di parti semplici. | Parti robuste e resistenti con geometrie complesse, impianti, protesi dentali, componenti medici e ortopedici in metallo. |
Biocompatibilità dei materiali di stampa 3D
A seconda dell'applicazione, i dispositivi medici potrebbero richiedere parti biocompatibili. Per candidarsi alla certificazione 510(k) e alla Premarket Approval (PMA) negli Stati Uniti e per altri regolamenti in tutto il mondo sono richieste informazioni sulla biocompatibilità. In questo modo è possibile verificare che il dispositivo sia compatibile con il sistema biologico per cui è stato realizzato. Informazioni mancanti o insufficienti possono comportare notevoli ritardi nell’immissione del dispositivo sul mercato.
I requisiti dei test di biocompatibilità vanno determinati sulla base dell’uso previsto per il dispositivo (tipologia, area e durata dell’esposizione). Determinare i requisiti per i test in anticipo rispetto al processo di sviluppo consentirà un ampio margine di tempo per completare i test prima di sottoporre i dispositivi agli enti regolatori. Questi parametri dovrebbero derivare dal contatto che ci si aspetta tra il dispositivo e il corpo umano.
Il contatto è solitamente definito da tre diverse categorie:
-
Contatto diretto: il dispositivo entra in contatto fisico con i pazienti.
-
Contatto indiretto: il dispositivo entra in contatto fisico con un fluido, un gas o altro materiale che poi ha un contatto diretto con i pazienti.
-
Nessun contatto: non si verifica nessun tipo di contatto, né diretto né indiretto, con i pazienti, quindi non è soggetto ai requisiti di biocompatibilità.
Alcuni produttori di stampanti 3D e materiali per la stampa 3D, come Formlabs, eseguono test di biocompatibilità basati sulle norme ISO 10993, ISO 18562 e ISO 7405 e pubblicano le informazioni riguardanti le resine in questione.
Poiché i test sono condotti su campioni stampati standardizzati, è responsabilità dei produttori rispettare le istruzioni di stampa e di post-elaborazione e validare in modo indipendente la biocompatibilità delle loro rispettive parti.
Approvazione regolamentare di dispositivi medici stampati in 3D
I dispositivi medici stampati in 3D devono soddisfare le linee guida regolamentari nei loro rispettivi Paesi.
Parte di questo processo consiste nello stabilire un sistema di gestione della qualità che comprenda le principali direttive, procedure, moduli e istruzioni di lavoro, così come la loro sequenza, le interazioni e le risorse richieste per portare avanti l'attività di produzione di dispositivi medici.
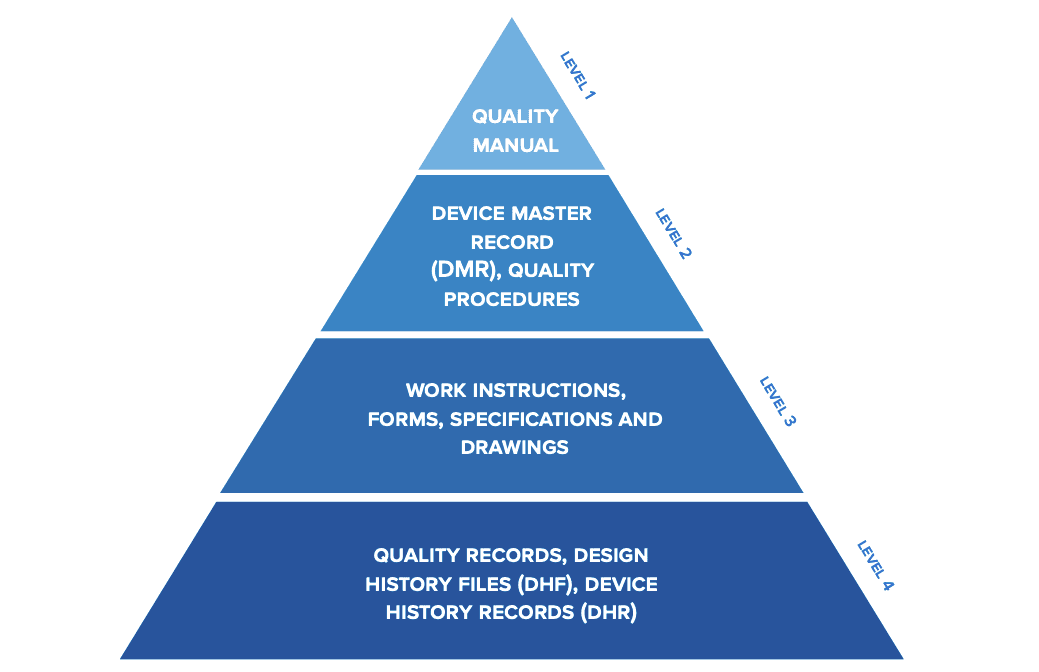
Esempio di gerarchia del sistema di gestione della qualità.
La documentazione della qualità dimostra che il sistema di gestione della qualità viene applicato e seguito, e descrive il modo in cui l'azienda rispetta le norme relative ai dispositivi medici. L'Agenzia per gli alimenti e i medicinali degli Stati Uniti (FDA) definisce le regole al punto 21 CFR Parte 820. Se si ha intenzione di rivolgersi al mercato statunitense, questi regolamenti devono essere rispettati.
In Europa è necessario stabilire un sistema di qualità per soddisfare le norme relative ai dispositivi medici (e/o le norme IVD). Molte aziende produttrici di dispositivi medici implementano un sistema di qualità certificato ISO 13485:2016 per soddisfare le esigenze dell'Unione Europea.
Per scoprire di più riguardo agli specifici requisiti regolamentari, scarica il nostro whitepaper completo, scritto in collaborazione con il partner di Formlabs Greenlight Guru, che mette a disposizione un'ampia varietà di risorse per assistere gli utenti in ogni passaggio del processo.
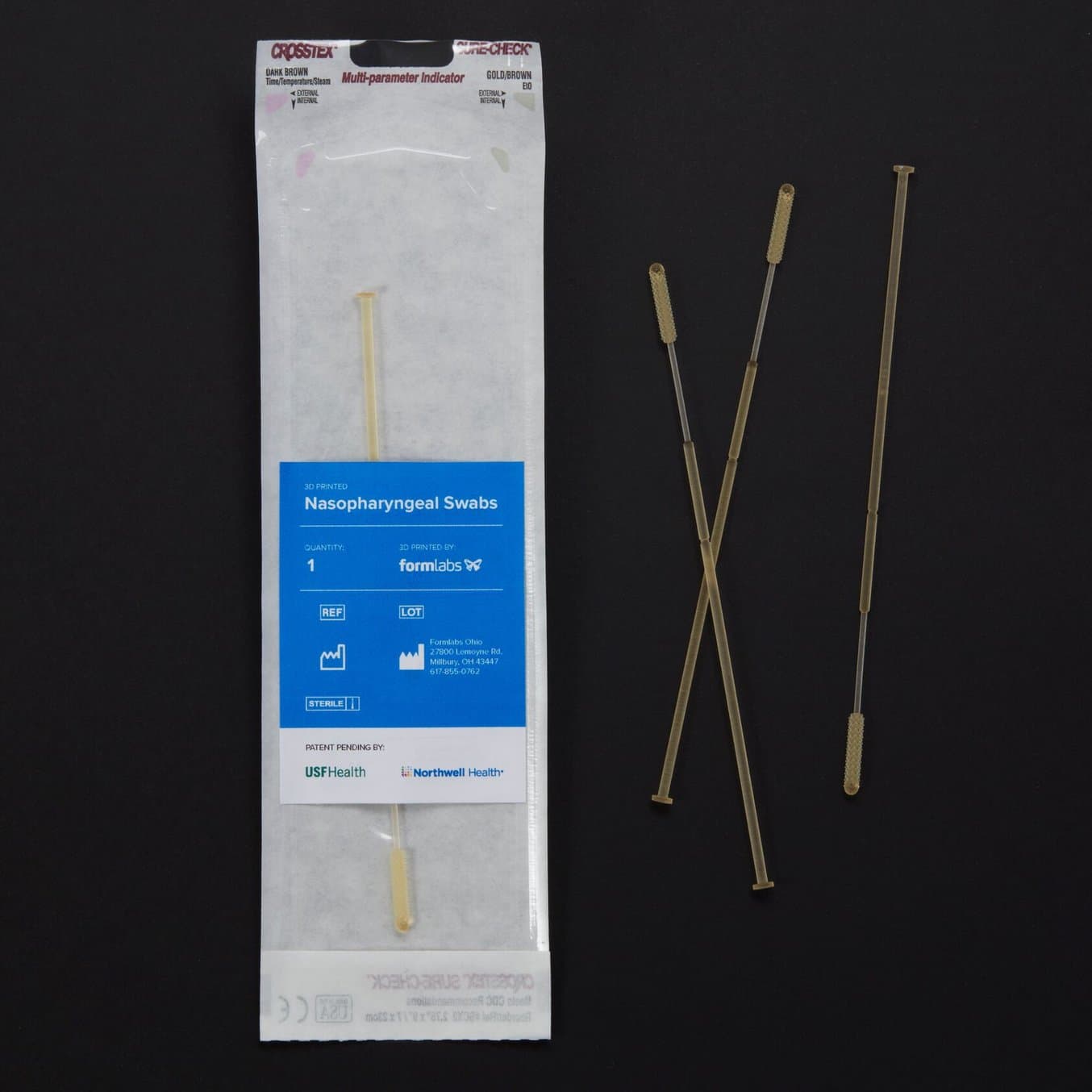
La guida definitiva alla garanzia di qualità e alle regolamentazioni nell'ambito della stampa 3D medica
Questo whitepaper ha lo scopo di guidare gli utenti del settore dei dispositivi medici in ogni passaggio del processo di sviluppo di prodotto, dalla valutazione dei metodi di produzione e delle tecnologie di stampa 3D fino agli specifici requisiti normativi per la commercializzazione e il marketing di dispositivi medici per utilizzo finale stampati in 3D.
Inizia a stampare in 3D i dispositivi medici
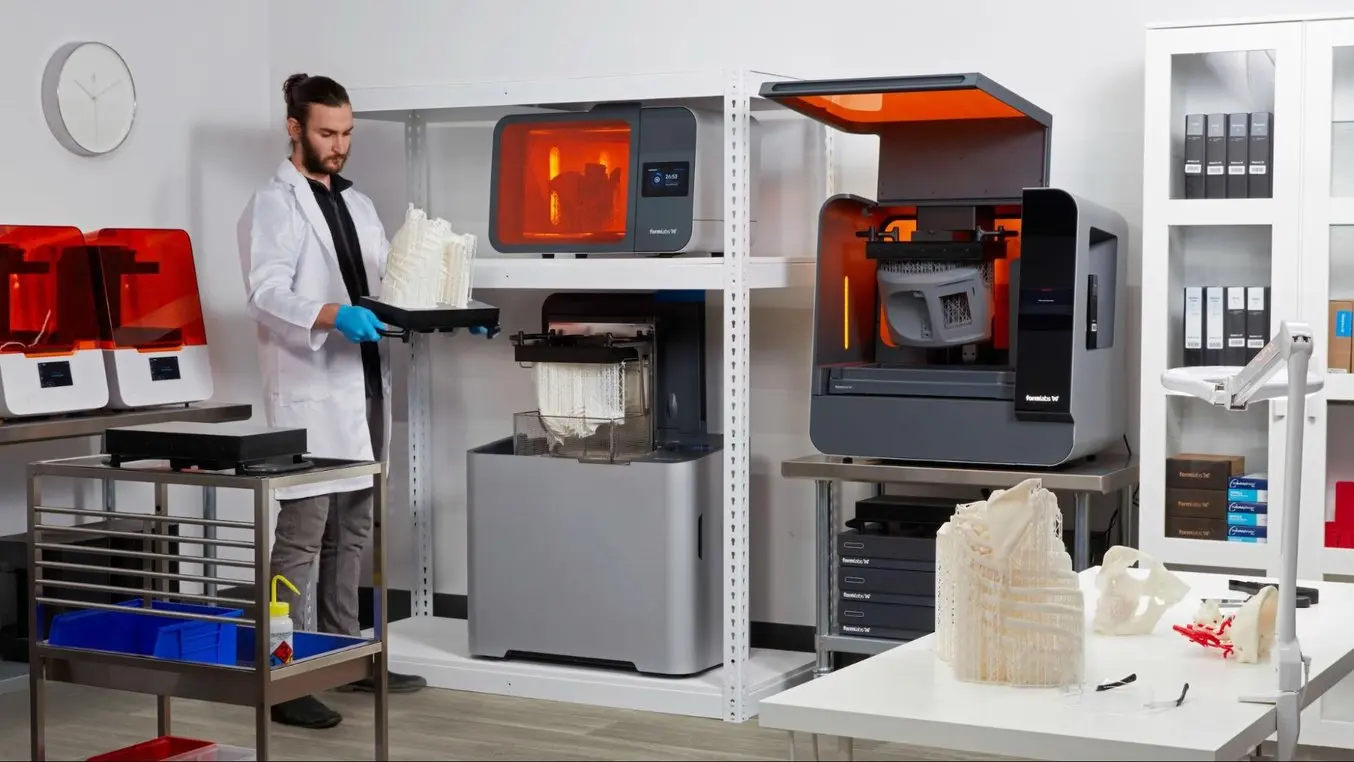
Per i produttori di dispositivi medici, la stampa 3D in-house consente di realizzare cicli di iterazione rapidi, accorciando il ciclo di sviluppo del prodotto e liberando tempo per dare spazio alle soluzioni creative.
Ogni struttura sanitaria dovrebbe avere accesso agli strumenti più recenti per migliorare le cure e fornire la migliore esperienza possibile ai pazienti. Inizia ora o amplia la tua produzione in-house con Formlabs, un partner affidabile e all'avanguardia nella stampa 3D per il settore medico.
Parla con i nostri esperti in ambito sanitario per saperne di più su come la stampa 3D in-house può integrarsi nel tuo attuale workflow di design e di produzione di dispositivi medici.