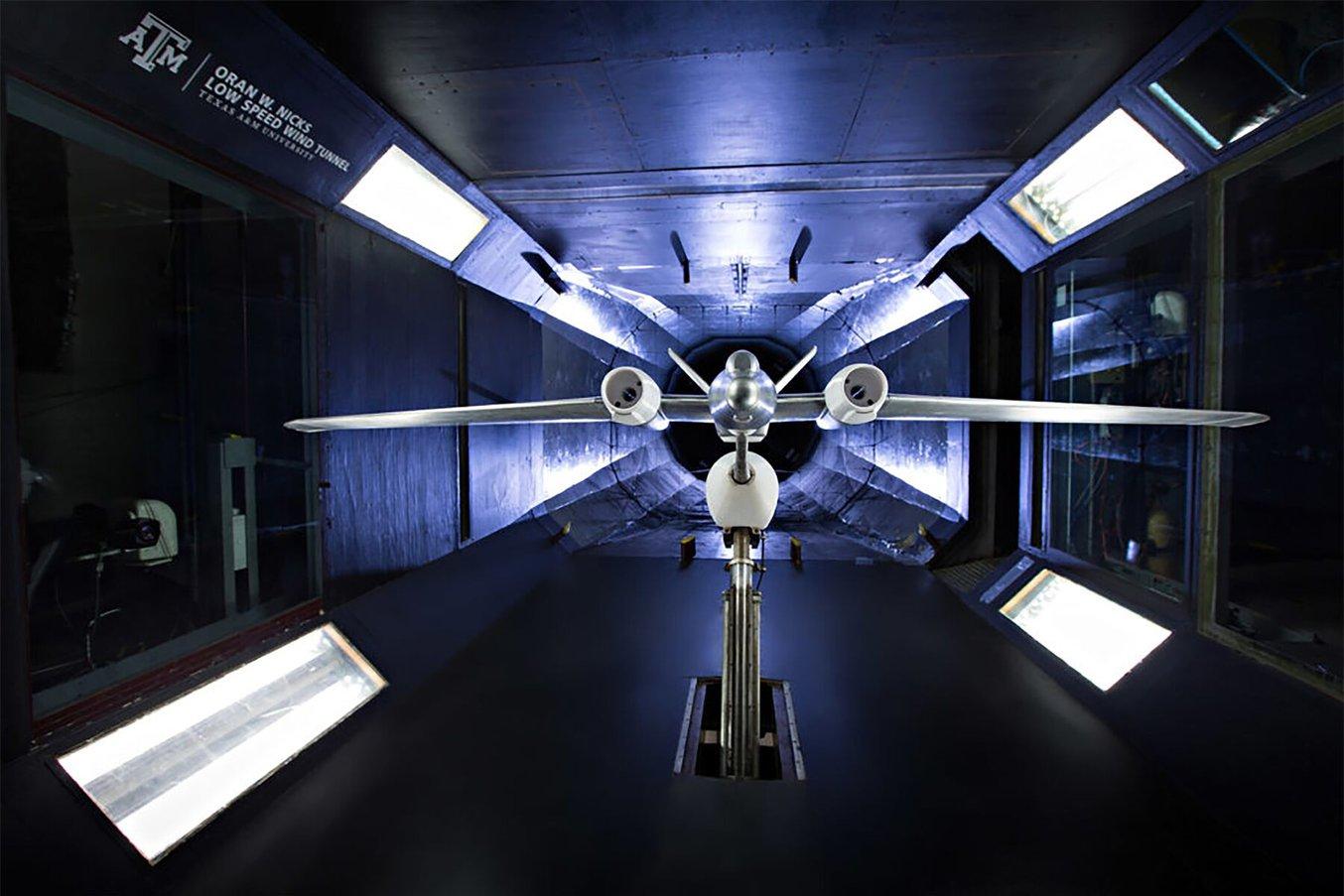
Vom Design bis zur Fertigung und darüber hinaus findet die additive Fertigung, oft kurz als 3D-Druck bezeichnet, viele Anwendungsbereiche in der Luft- und Raumfahrt.
Die Luft- und Raumfahrtbranche gehörte zu den ersten Wirtschaftsbereichen, die nach der Erfindung der Technologie den Wert des 3D-Drucks bzw. der additiven Fertigung für sich erkannten. Tatsächlich benutzen viele Erstausrüster, Zulieferer und Behörden den 3D-Druck schon seit Jahrzehnten. So kommt es, dass die jüngsten Generationen kommerzieller Airliner mehr als 1000 3D-gedruckte Teile beinhalten.
Und doch sind herkömmliche industrielle 3D-Drucker nur für die finanzstärksten Organisationen überhaupt eine Option. In den letzten 10 Jahren kam es zu einer drastischen Senkung der Preise leistungsstarker 3D-Drucker. Und Innovationen in Sachen Materialien ermöglichen ganz neue Hochleistungsanwendungen. Durch einen erschwinglichen Preis haben jetzt auch kleinere Organisation Zugang zu 3D-Druckern. Aber auch bei größeren Organisationen findet sich nun in neuen Abteilungen das, was früher in zentralisierten Prototypenwerkstätten abgeschottet war. Dank der 3D-Drucker von Formlabs erreicht die Technologie mehr Endnutzer*innen – und eben diese zahlreicheren Ingenieur*innen und Wissenschaftler*innen der Luft- und Raumfahrt durchbrechen so die alten Grenzen und Einschränkungen ihrer Branche.
Im Folgenden erfahren Sie, wie der 3D-Druck auf neun wesentliche Weisen Innovationen in der gesamten Luft- und Raumfahrtbranche vorantreibt – vom Design bis zur Fertigung und darüber hinaus.
3D-Druck in der Produktentwicklung der Luft- und Raumfahrt
1. 3D-Druck zwecks Rapid Prototyping beim Test funktionaler Raketen
Gravity Industries entwickelt Jetpack-Anzüge, die aus einem Science-Fiction-Film stammen könnten. Sinn und Zweck solcher Jetpack-Anzüge sind beispielsweise Rettungsmissionen in für Hubschrauber unzugänglichen Bereichen. Die Verwendung mehrerer 3D-Drucktechnologien beschleunigt dort die Prototypenfertigung und deren Tests. Darunter fallen auch Tests, bei denen Duroplast-Kunstharze die klar beste Option sind.
Der Testpilot und leitende Designer Sam Rogers verwendete Teile aus Clear Resin gedruckt mit dem Form 3 beim Entwurf eines Wirbelrohr-gekühlten Raketenzündsystems. Das transparente Material war ideal für das Testumfeld, da Rogers so die Verbrennungsmuster im Inneren des Versuchaufbaus beobachten konnte.
Für die Designtests setzte Rogers auf eine modulare Brennkammer, um verschiedene Versionen der Kammer und der Düse miteinander zu kombinieren. Ein „Hitzeschild aus wirbelndem Sauerstoff“ hält die größte Hitze von der Kammerwand fern. Dadurch halten die Kunstharzteile jeweils mehrere Sekunden. Diese kurze Zeit reichte aus, da die Testzündung nur lange genug laufen muss, um das Zündmuster zu beobachten.
Hätte Rogers diese verschiedenen Designs dutzendweise aus Metall anfertigen lassen, wäre dies unsagbar teuer geworden. Die Tests waren kurz und die Materialkosten gering, deshalb setzte er stattdessen auf ein Hochleistungsdesign bei minimalem Aufwand und kurzer Durchlaufzeit.
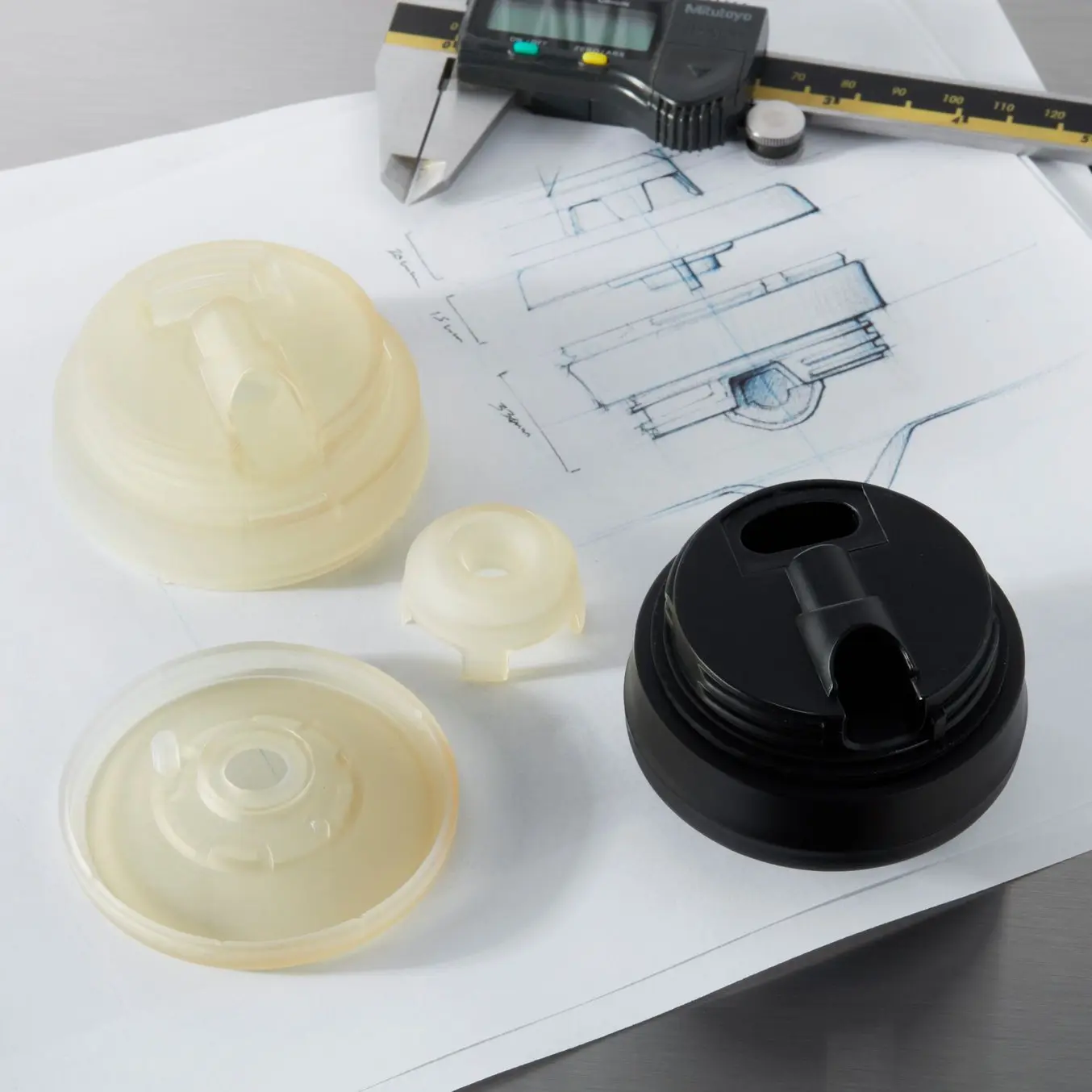
Leitfaden zum Rapid Prototyping für die Produktentwicklung
In diesem Leitfaden erfahren Sie, wie sich Rapid Prototyping in Produktentwicklungsprozesse einfügt, welche Anwendungsfälle dafür bestehen und welche Rapid-Prototyping-Werkzeuge den Produktentwicklungsteams von heute zur Verfügung stehen.
2. Erstellung komplexer Raketenteile mithilfe von 3D-Druck
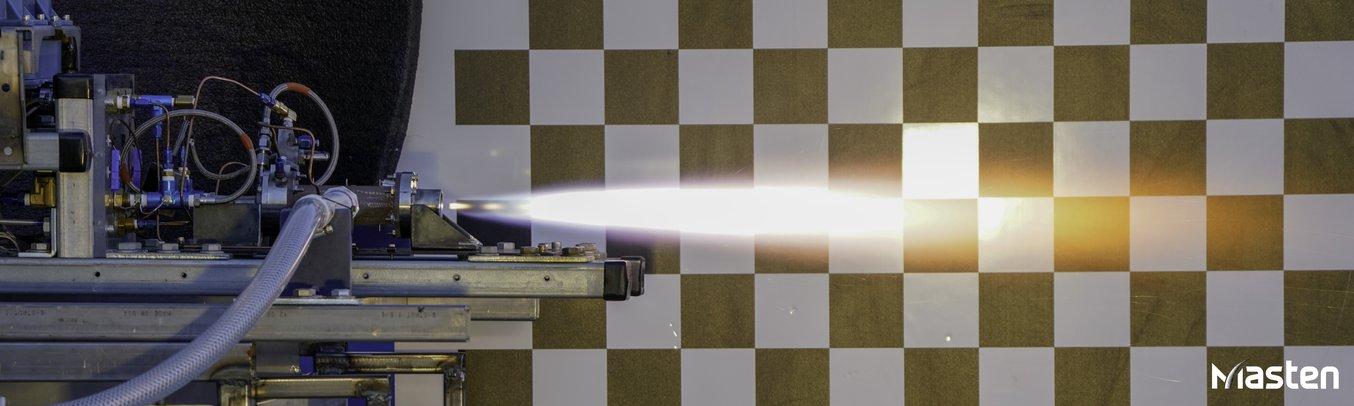
Masten Space Systems stellt mithilfe von 3D-Druck komplexe Raketenteile her.
Masten Space Systems ist spezialisiert auf Raketentechnik für vertikale Starts und Landungen. Dort begann man 2014 mit dem 3D-Druck der Raketenantriebe – zunächst mit kleinen Testdüsen bis man 2016 schließlich bis zum „Broadsword“-Antrieb mit 110 kN Schubkraft hochskalierte. Das Team arbeitet mit der additiven Fertigung sowohl von Kunststoffen als auch von Metallen. Laut Kimberly Devore, Forschungs- und Testingenieurin bei Masten, verwendete das Unternehmen sowohl herkömmliche Zerspanung als auch 3D-Druck zur Produktion der Raketenantriebe. Obgleich Masten noch immer traditionelle Fertigungsverfahren für die älteren Modelle einsetzt, konzentriert man sich dort auf 3D-Druck aus Gründen der Gestaltungsfreiheit und Produktionsgeschwindigkeit.
„Das Schöne [am 3D-Druck] ist, dass man alles genau so modellieren kann, wie man möchte. Und auch Iterationen gehen viel leichter von der Hand als bei der traditionellen Zerspanung. Man entwirft es einfach genau so, wie man es braucht“, berichtet Devore. „Bei der traditionellen CNC-Bearbeitung muss man die Dinge oft ziemlich einfach gestalten. Jedes Zusatzfeature, das man einarbeitet, spiegelt sich sofort in zusätzlichen Kosten wider.“
Beim 3D-Druck hingegen kostet Komplexität zur Leistungsverbesserung nicht extra – genauso wenig wie eingegangene Risiken. Da mehrere Ausführungen relativ schnell und billig vonstattengehen, kann man leicht neue Dinge ausprobieren. „Die Möglichkeit schneller Iterationen bei diesen Teilen macht einen himmelweiten Unterschied.“
3. Prototypenentwicklung von Luftfahrtwerkzeugen mithilfe von 3D-Druck
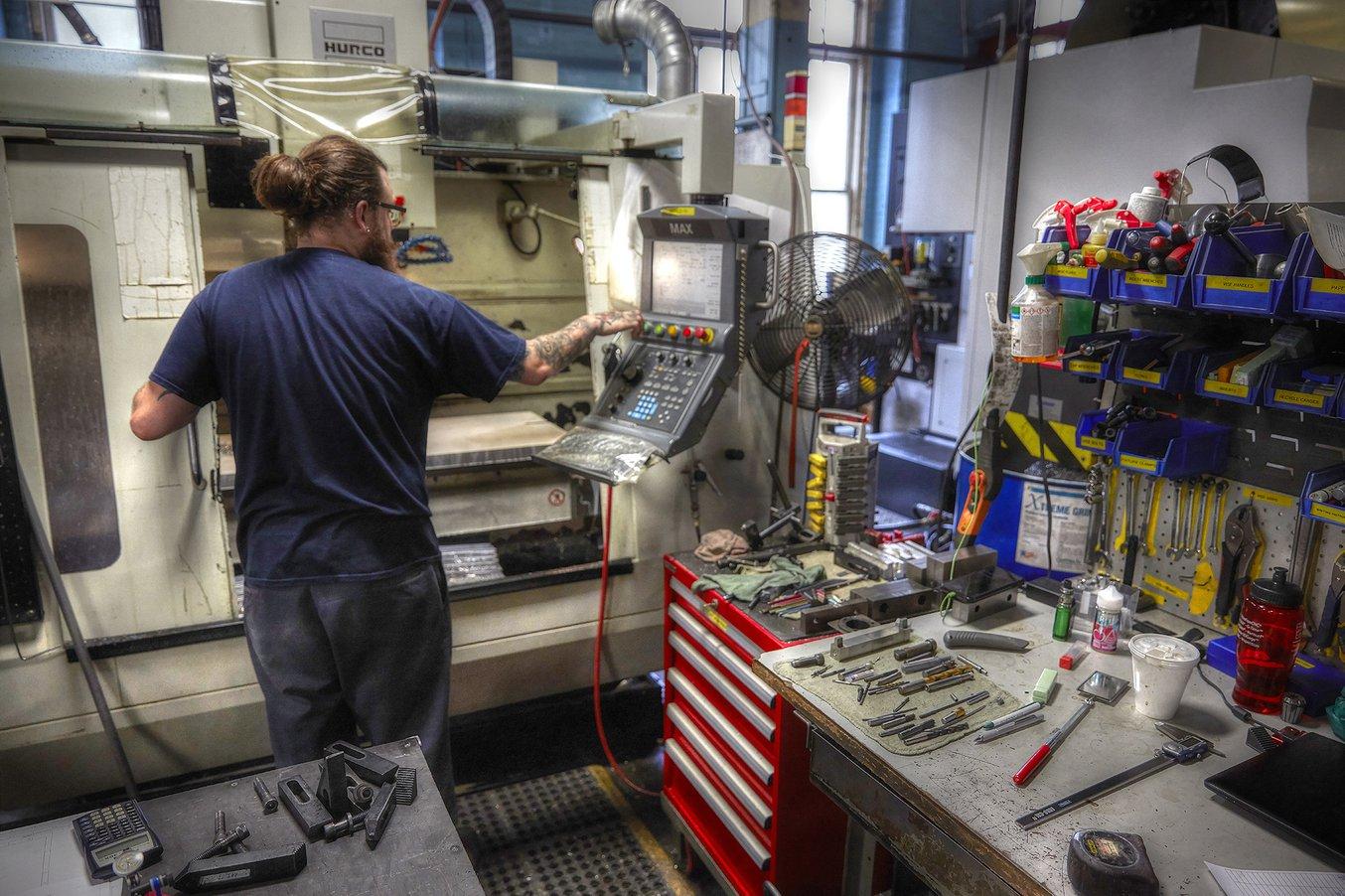
Die Programmierung von CNC-Fräsen erfordert Expertise und Zeit. Wenn ein Teil nicht aus Metall bestehen muss, ist 3D-Druck die erste Wahl, um Prototypen oder Fertigungswerkzeuge schneller und kostengünstiger herzustellen.
A&M Tool and Design fertigt Teile und maßgeschneiderte Maschinerie für die Raumfahrt, optische Anwendungen und die Robotik. Die Werkstatt wurde im Laufe der Jahre immer wieder mit verschiedenen neuen Anlagen modernisiert, darunter auch 3D-Druck – als Ergänzung traditioneller Technologien und nachgerüsteter Lösungen. Ryan Little ist ein Maschineningenieur bei A&M Tool. Er untersuchte, welcher 3D-Drucker den dortigen Anforderungen am besten gewachsen ist, und entschied sich dann für die Geräte von Formlabs.
Bei der Prototypenentwicklung helfen die 3D-Drucke bei der Prüfung der Passung und der Funktion. Mithilfe von 3D-Druck stellen Little und sein Team Teile viel schneller her und nutzen den Tag voll aus. Sie drucken Teile über Nacht und haben diese somit direkt am nächsten Morgen zur Verfügung. 3D-Druck ist besonders für geometrische Formen hilfreich, deren Fertigung mit einer CNC-Maschine kosten- oder zeitintensiv wäre.
„Der Drucker fühlt sich fast an wie ein Beiwerkzeug zur CAD-Software“, so Little. „Wir fertigen eine Menge von Prototypen für verschiedene Werkzeugarten. Ohne den Form 2 blieben viele Prototypen in der CAD-Software gefangen, bis wir zur Zerspanung übergehen. Und einige Ideen könnten wir nie umsetzen, weil sie nicht praktikabel wären.“
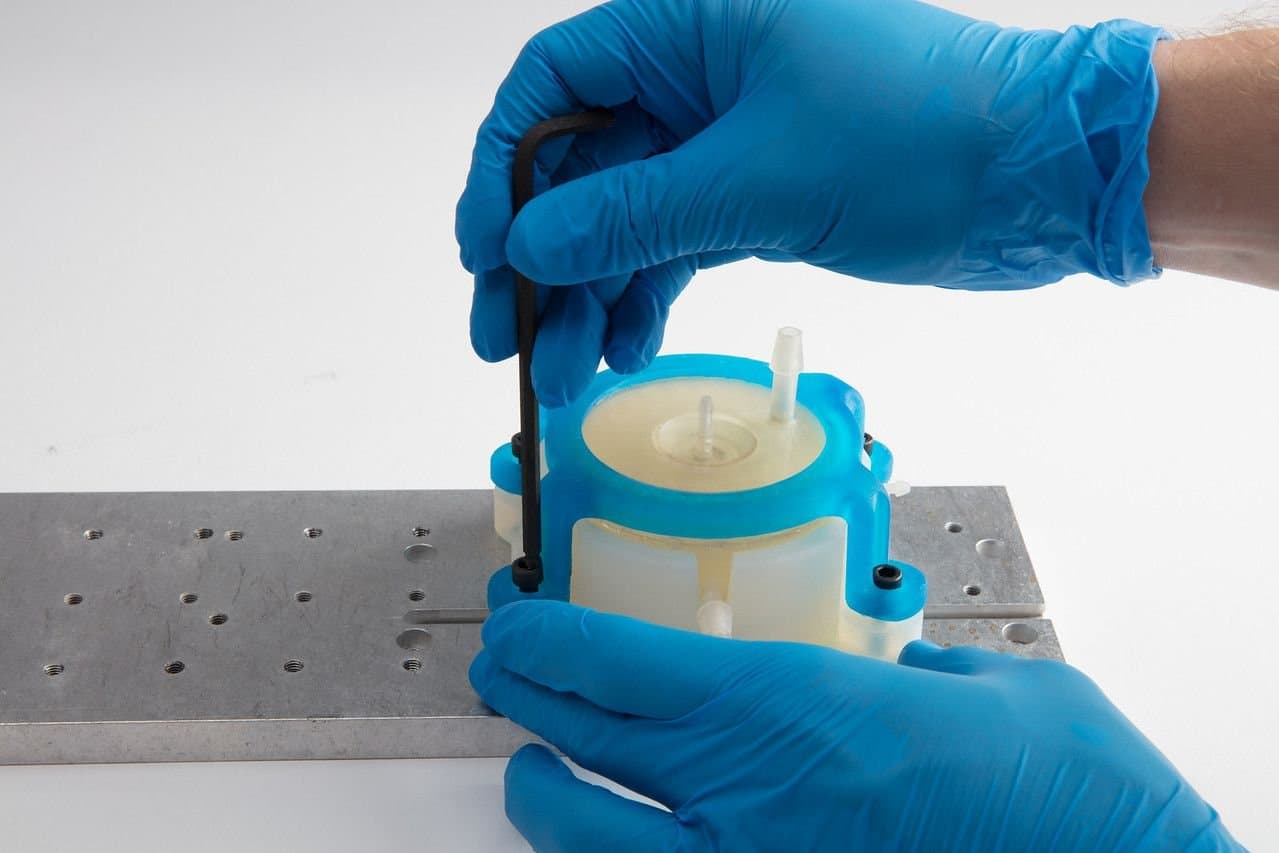
Konstruktion von Vorrichtungen mit 3D-Druck
Für den Unternehmenserfolg von Herstellern ist es ausschlaggebend, die Produktionsgeschwindigkeit zu maximieren und gleichzeitig hohe Teilequalität zu erzielen. Halterungen und Vorrichtungen kommen zur Anwendung, um Fertigungs- und Montageprozesse einfacher, zuverlässiger und effizienter zu gestalten, die Zyklen zu verkürzen und gleichzeitig die Sicherheit des Personals zu gewährleisten.
3D-Druck in der Fertigung für Luft- und Raumfahrt
4. Kostenersparnis durch 3D-gedruckte Werkzeugbestückung für Flugzeugteile
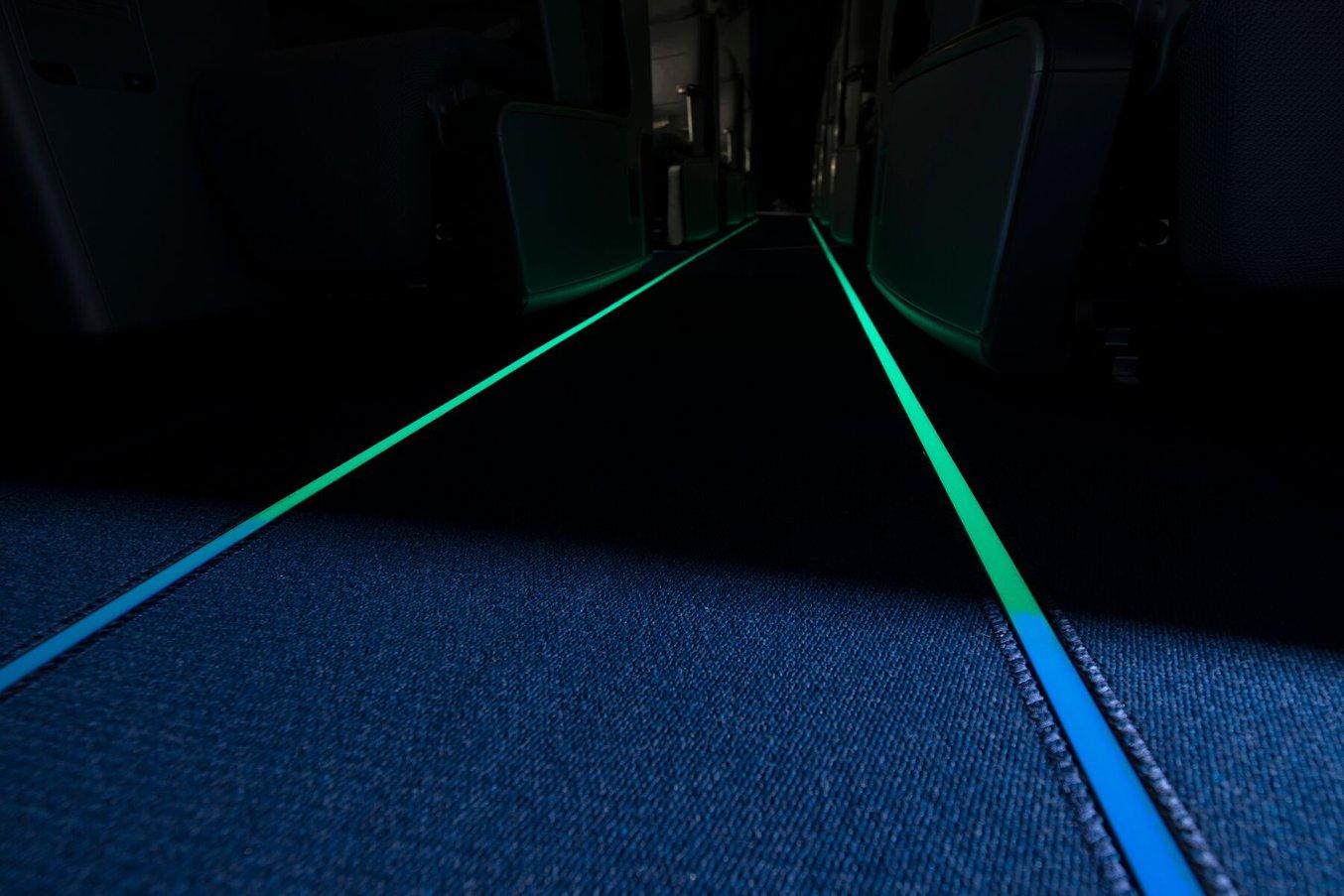
Lufthansa Technik druckte die Düse zur Produktion dieser selbstleuchtenden Fluchtwegmarkierungen in 3D.
Lufthansa Technik ist einer der weltweit größten Zulieferbetriebe und Dienstleister für Wartung, Reparatur und Überholung (MRO, von engl. Maintenance, Repair and Operations) in der Luftfahrt. Die patentierten Fluchtwegmarkierungen des Typs „Guide U“ für Flugzeugkabinen wurden vom Unternehmen für die Installation als Aftermarket-Produkt entwickelt. Die innovativen Leuchtstreifen sind photolumineszierend (nachleuchtend). Das bedeutet, sie sind mit selbstleuchtenden Farbpigmenten ausgestattet, die sich durch das normale Kabinenlicht aufladen und im Falle eines Notfalls ohne Strom im Dunkeln weiterleuchten.
Vor der Produktion wurden verschiedene Werkzeugmaterialien und Herstellungsverfahren unter die Lupe genommen. Die Herstellung spezieller Extrusionsdüsen mittels 3D-Druck erwies sich als die kosteneffizienteste und flexibelste Fertigungsmethode. „Theoretisch könnten wir unsere Teile auch im Spritzgussverfahren herstellen. Damit wären wir aber nie so flexibel bei der Form und den Anpassungen der Düse gewesen. Da sehe ich den großen Vorteil des 3D-Drucks,“ erklärt Ulrich Zarth, Projektingenieur für Guide U.
Das Produktionswerkzeug wurde in Kooperation mit Formlabs-Partner myprintoo auf dem Form 3L gedruckt. Die großflächige Konstruktionsplattform des Form 3L erlaubte es dem Team, 72 Düsen in einem einzigen Druckvorgang herzustellen. Verschiedene Formlabs-Materialien wurden getestet, und letztendlich fiel die Wahl auf Clear Resin, welches Lufthansa Technik neben der richtigen Stabilität und Oberflächengüte auch noch dabei hilft, seinen Produktionsprozess stets zu optimieren.
„Wenn präzise Geometrien insbesondere aus Kunststoff benötigt werden und das in kurzer Zeit, dann würde ich immer auf 3D-Druck zurückgreifen.“
Ulrich Zarth, Project Engineer bei der Lufthansa Technik AG
Zarth und sein Team sparten durch den betriebsinternen 3D-Druck dieser kleinen Komponente in ihrem Produktionsprozess enorm viel Zeit und Geld. Außerdem konnten sie im Vergleich zu herkömmlichen Methoden zur Herstellung von Betriebsmitteln dieser Art hohe Mindestbestellwerte umgehen und blieben in ihrer Prozessoptimierung deutlich flexibler.
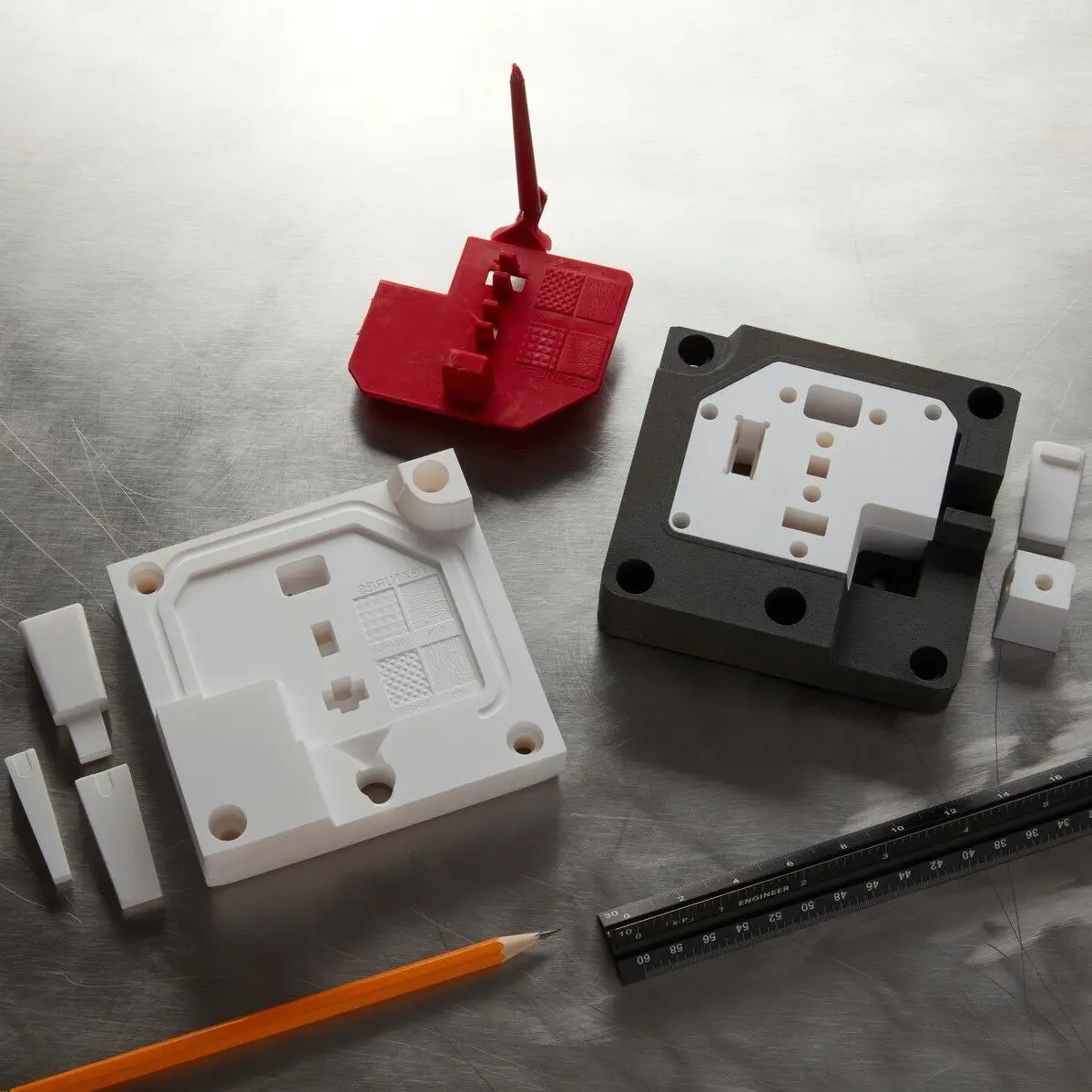
Leitfaden zum Rapid Tooling
In diesem Whitepaper sprechen wir über die Kombination von Rapid Tooling mit traditionellen Herstellungsverfahren wie Spritzguss, Thermoformen oder anderen Gießverfahren.
5. Zeiteinsparung in der Luftfahrtfertigung durch 3D-gedruckte Masken
Die Integrated Manufacturing Group des AMRC arbeitet mit Partnern aus der Industrie zusammen, um fortschrittliche Technologien zusammenzubringen und integrierte Systeme zu entwickeln. Die Forschungsgruppe arbeitete vor Kurzem an einem Projekt für Airbus, Europas größtes Luft- und Raumfahrtunternehmen, bei dem Bohr- und Zerspanungsarbeiten mit engen Toleranzen an Kohlenstofffaser-, Aluminium- und Titanbauteilen durchgeführt wurden. „Nach dem Bohren eines Lochs mussten wir das erste Loch abdecken, bevor wir zum nächsten übergingen, damit die entstandenen Späne die zweite Bohrung nicht verunreinigten“, berichtet George Sleath, Projektingenieur bei AMRC.
Das Team versuchte es zunächst mit einem Aluminiumteil mit einem kleinen O-Ring aus Gummi, doch das löste das Problem nicht befriedigend. Außerdem gab es zwei zusätzliche Hürden: Es wurden Kappen in mehreren Größen benötigt und es blieben nur zehn Tage Zeit, um insgesamt 500 Kappen fristgerecht fertigzustellen.
Bei einer so kurzen Durchlaufzeit für maßgefertigte Produkte wäre die Nutzung praktisch jeder anderen Fertigungsmethode außer 3D-Druck unmöglich. Da er die betriebsinternen Produktionsmöglichkeiten von AMRC zu der Zeit nicht genau kannte, forderte Sleath Angebote von drei externen Druckdienstleistern an, doch die Kostenvoranschläge waren sehr teuer.
„Ich sprach dann mit Mark Cocking in unserer Gruppe für Design und Prototyping und fragte nach, ob wir das nicht in unserem Betrieb herstellen könnten. Einen Tag lang hörte ich nichts von ihm, doch als er sich schließlich meldete, sagte er, ‚Klar, die Hälfte haben wir schon gedruckt.‘ 250 Bohrkappen in 24 Stunden zu fertigen, das war eine beeindruckende Durchlaufzeit“, so Sleath.
Schließlich schaffte es Cocking, alle Teile innerhalb von zwei Tagen herzustellen. „Das Feedback des einbauenden Personals war einfach fantastisch. Fast alle Teile funktionierten genauso wie vorgesehen und keines ging im Betrieb kaputt“, berichtet Sleath.
6. Galvanisierung 3D-gedruckter Endverwendungsteile für Flugzeuge
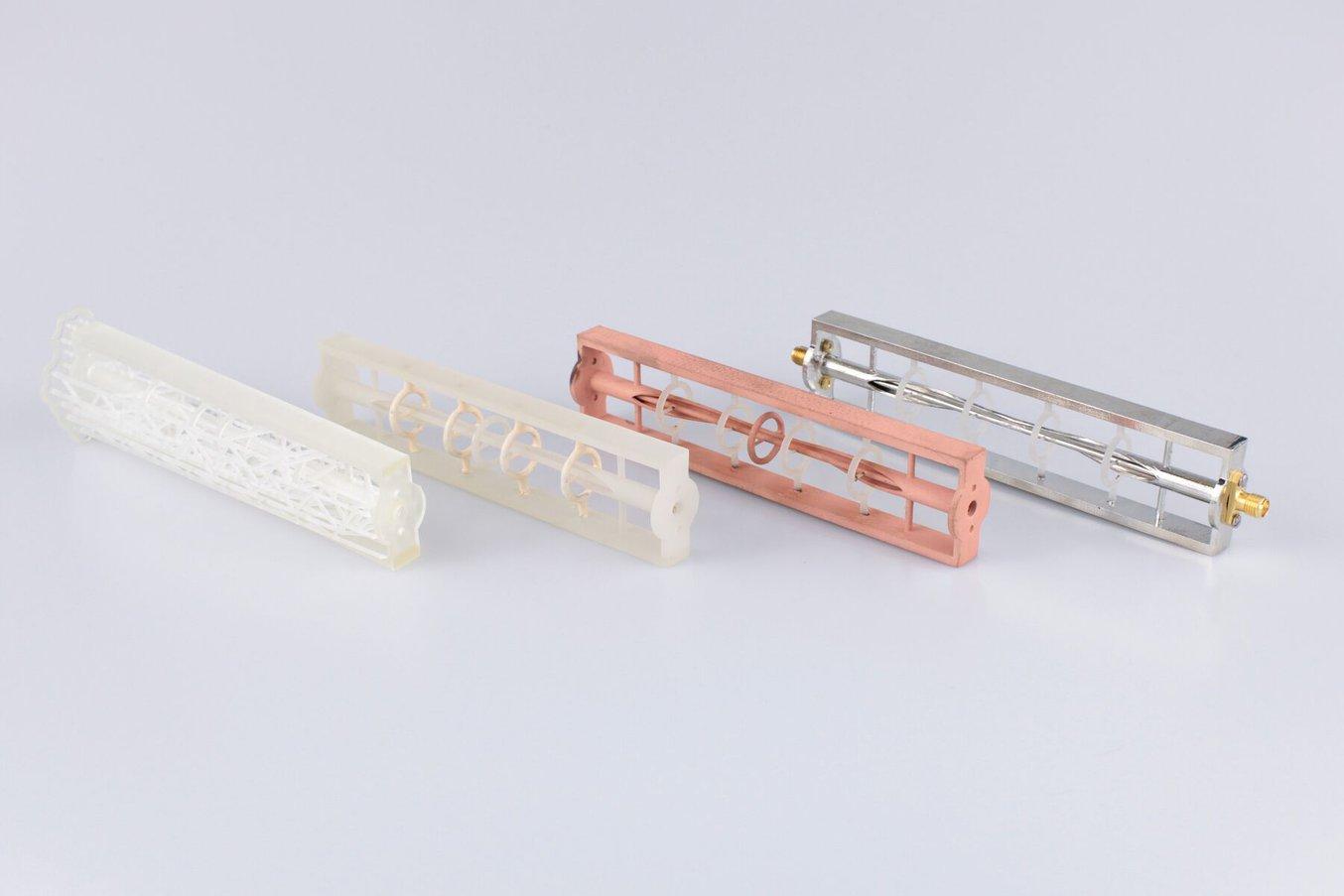
Mithilfe 3D-gedruckter Endverwendungsteile erstellt Elliptika neuartige Antennendesigns schneller und spart dabei noch Geld.
Elliptika ist spezialisiert auf das Design und die Entwicklung von Hochfrequenz- (HF) und Mikrowellenprodukten und -lösungen. Das Unternehmen entwirft maßgefertigte Filter und Antennen für die Forschung und Entwicklung in der Automobilindustrie, im Verteidigungswesen, der Medizin und der Bildung. Die Funkfrequenzdesigner Gwendal Cochet und Alexandre Manchec müssen komplexe Geometrien umsetzen, die Kosten gering halten und ihre Designs schnell abliefern. Um diese anspruchsvollen Bedingungen zu bewältigen, greift das Team auf Lösungen jenseits der Beschränkungen traditioneller Fertigungsverfahren zurück.
Das Team bei Elliptika hat verschiedene additive Fertigungsverfahren ausprobiert und entschied sich aufgrund der glatten Oberfläche der Druckteile für Stereolithografie-3D-Druck (SLA) als beste Grundlage für die Galvanisierung. „Nach dem Druck des Teils entfernen wir die Stützstrukturen, reinigen die Oberfläche und härten es nach. Dann wird das Druckteil in chemischen Prozessen mit einer dünnen Schicht Kupfer überzogen (ca. 3 µm). Zu guter Letzt wird die Oberfläche gegebenenfalls verfeinert, zum Beispiel durch eine dickere Zinnschicht.“
Elliptika erreichte mit dem 3D-Drucker von Formlabs schon nach zwei Druckaufträgen einen positiven ROI. Die Fertigung einer Antenne durch einen externen Dienstleister kostet ungefähr 3000 €; die Kosten für Material und Arbeitszeit bei betriebsinterner Herstellung mit 3D-Druck und Galvanisierung betragen nur 20 €.
Auch die Arbeitsgeschwindigkeit steigerte sich. Mit traditionellen Fertigungsverfahren kann die Herstellung einer Antenne bis zu drei Monate in Anspruch nehmen. „Mit betriebsinternem 3D-Druck haben wir in nur zwei Tagen funktionsbereite Teile. Ein Tag zum Drucken, ein Tag zum Galvanisieren und los. Es geht also viel, viel schneller“, berichtet Cochet.
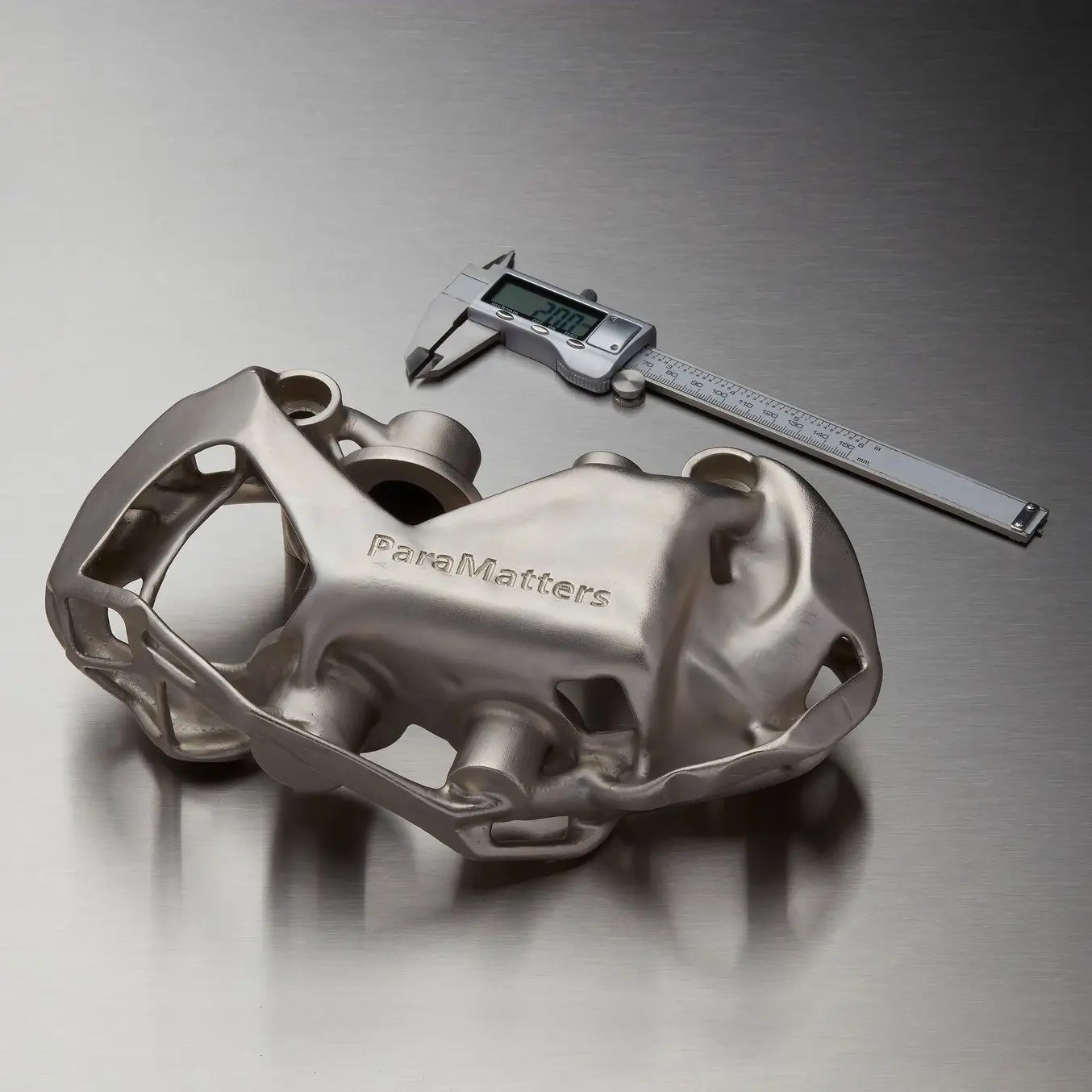
Metallische Festigkeit: Strategien und Anwendungsfälle zur Galvanisierung von SLA-Teilen
Im Folgenden erfahren Sie, wie Ingenieurteams 3D-Druckteile aus Kunstharz mit Metall überziehen und warum solche Hybridteile eine überraschend große Anzahl an Anwendungsbereichen eröffnen, z. B. durch mehr Festigkeit und Haltbarkeit in der Endverwendung.
3D-Druck in der Luft-&-Raumfahrtforschung und -bildung
7. Tests 3D-gedruckter Teile im Weltall
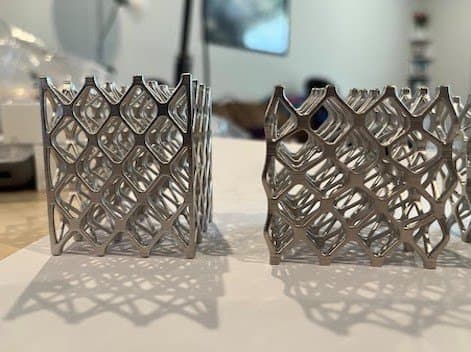
Gitterstruktur aus galvanisiertem Rigid 10k Resin vor einem Test (links) und nach einem Test mit Belastung von oben (rechts)
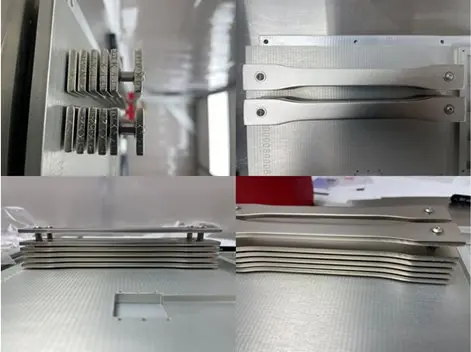
Galvanisierte 3D-Druckteile aus Rigid 10K Resin, die zur ISS gesandt wurden
Die Forschungsteams der NASA untersuchen, wie sich galvanisierte SLA-Teile im Weltraum bewähren. Die Ingenieur*innen im zur NASA gehörigen Goddard Space Flight Center haben Klemmen entworfen, die mit den 3D-Druckern von Formlabs gedruckt und anschließend galvanisiert wurden. Die Teile machten sich dann 2022 mit der SpaceX-Versorgungsmission CRS-25 auf zur Internationalen Raumstation ISS.
Mithilfe von Alpha Spaces ISS-Versuchsaufbau „Materials International Space Station Experiment“ (MISSE-16) werden die Musterdrucke der Außenumgebung der Raumstation ausgesetzt. Zu einem späteren Zeitpunkt werden sie dann für weiterführende Untersuchungen zur Erde zurückgebracht. Die Ergebnisse bieten der NASA und anderen Herstellern aus Luft- und Raumfahrt dann Aufschlüsse darüber, wie sich die additive Fertigung in zukünftige Produktpläne einfügt.
8. 3D-Drucke für Windkanaltests
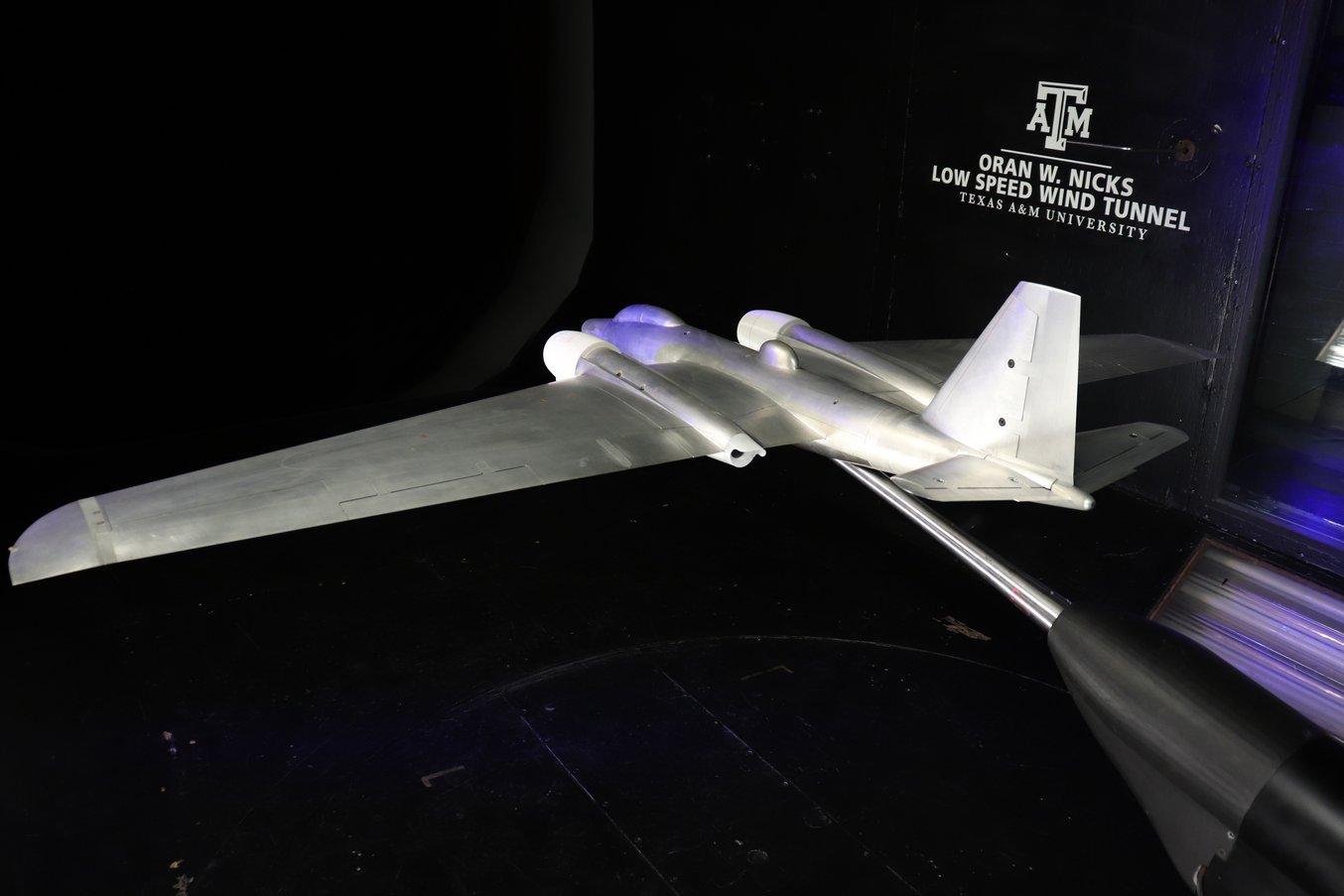
Hochleistungsfähige 3D-Druckkomponenten können für Windkanaltests an maßstabsgetreuen Flugzeugmodellen befestigt werden.
Lehrkörper und Studierende auf der ganzen Welt nutzen die 3D-Drucker von Formlabs für Windkanaltests zu Forschungszwecken.
Am Texas A&M University Oran W. Nicks Low-Speed Wind Tunnel (TAMU LSWT, Niedergeschwindigkeitskanal Oran W. Nicks an der Universität Texas A&M) werden Windkanaltests für Projekte aus vielen Bereichen durchgeführt. Lisa Brown, Managerin und Ingenieurin am Windkanal von Texas A&M, hilft Forscher*innen dabei, ihre Testpläne zu entwickeln, Modelle zu designen und den Code zu erstellen, mit dem relevante Daten gesammelt werden. Ihr Team fertigt mit 3D-Druck maßstabsgetreue Modelle für eine Reihe von Testobjekten.
Brown erinnert sich an ein Projekt, bei dem sich das Team mit einem klappernden Hubschrauber-Rotorblatt befasste und 3D-Druck in den Test integrierte. „Wenn wir schneller wurden und die Rotorblätter schnell genug schlugen, gingen Schockwellen von der Anströmkante der Rotorblätter aus. Das ist bei einem Hubschrauber eher weniger erwünscht. Wir konnten diese Schockwellen in unserem Niedergeschwindigkeitskanal beobachten, was schon spannend war“, erzählt Brown. „Wir hatten einen kleinen, gedruckten Einsatz mit Sensoren an dieser Anströmkante. Beim ganzen Modell handelte es sich also um ein Aluminiumrotorblatt mit diesem kleinen Einsatz, den wir austauschen konnten.“
Welches Material Brown dafür verwendete und aus welchem Grund, das erfahren Sie in unserer Fallstudie.
Auf der anderen Seite des Atlantiks führt auch das Karlsruher Institut für Technologie (KIT) Windkanaltests mit 3D-Druckteilen durch. Doktorand Lars von Deyn untersucht Möglichkeiten, turbulente Ströme vorherzusagen. Seine Arbeit birgt das Potenzial, Material- und Designentscheidungen zu beeinflussen, um Reibung und Luftwiderstand im Verkehrswesen zu verringern.
Für seine Testteile entschied sich von Deyn für den 3D-Druck. „Ich möchte Strukturen untersuchen, die mit CNC-Bearbeitung nur schwer herzustellen sind“, erklärt er. Er entschied sich für die Arbeit mit dem Form 3L aufgrund des großen Fertigungsvolumens, da er so große Teile des Windkanals mit weniger Einzelteilen abdecken konnte, also mit weniger Unterbrechungen im Strommuster.
Die Ergebnisse seiner Experimente können Sie in unserer Fallstudie nachlesen.
9. 3D-Druck als Teil der Ausbildung der nächsten Generation von Ingenieur*innen
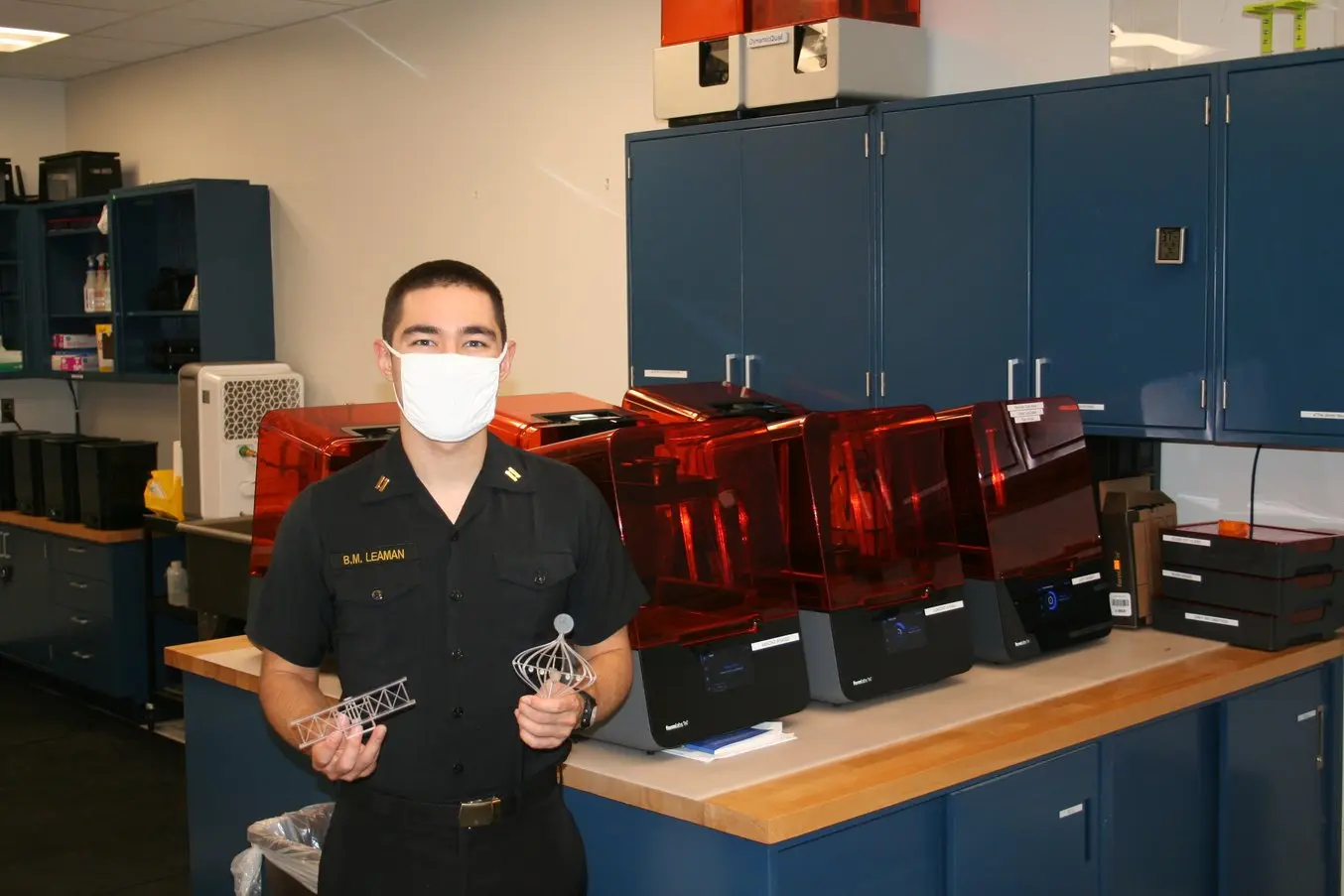
Midshipman First Class Ben Leaman, Student mit Hauptfach Schiffstechnik an der USNA, zeigt seine preisgekrönten Drucke aus dem Formlabs-Drucker Form 3 bei den AM Olympics 2021.
An der United States Naval Academy werden junge Männer und Frauen zu professionellen Offizieren der U.S. Navy und des Marine Corps ausgebildet. Captain Brad Baker, ein Dozent der USNA, erkannte, dass mangelnder Zugang zu Fertigungsmöglichkeiten seine Ingenieurstudent*innen in ihrem Iterationsprozess behinderte – und damit auch in ihrem Lernfortschritt. Obwohl eine Werkstatt einzig für die Abschlussprojekte der Studierenden zur Verfügung stand, war es individuellen Studenten oder Teams nicht möglich, mehr als drei oder vier Iterationen pro Jahr durchzuführen.
Captain Baker war zwar nicht der erste Dozent an der Hochschule, der Studierenden 3D-Drucker für ihre Projekte anbot, er brachte jedoch die Ressourcen für Design und Fertigung an einen zentralen Standort, indem er den MakerSpaceUSNA gründete. Als gerade einmal ein paar Schmelzschichtungsdrucker (FDM, Fused Deposition Modeling) vorhanden waren, begann er bereits, die Geräte in den Lehrplan des Maschinenbaustudiums zu integrieren und sie den Studierenden für ihre Abschlussprojekte bereitzustellen.
Zu Beginn ihres Ingenieurstudiums lernen die Studierenden zunächst, CAD-Software zu benutzen und FDM-Drucker zu bedienen, gehen dann zur Stereolithografie (SLA) über und gelangen schließlich zu SLS-3D-Druckern (selektiven Lasersintern). Mittlerweile lernen sie sogar 3D-Scanverfahren, sodass sie mithilfe aller erlernten Hilfsmittel komplette Projekte im Reverse Engineering durchführen.
Die zuverlässigen Qualitätsdrucker für FDM, SLA und SLS im MakerSpaceUSNA gewähren allen Studierenden dort großflächige Erfahrung mit einer ganzen Bandbreite an additiven Fertigungsverfahren. Captain Baker geht durch seinen Ansatz einer praxisnahen Ausbildung und durch seine Philosophie, aus Misserfolgen zu lernen, noch einen Schritt weiter und bereitet seine Studierenden so auf eine Karriere im Dienst der US Navy und darüber hinaus vor.
Was birgt die Zukunft für die additive Fertigung in der Luft- und Raumfahrt?
Leistungsfähigere und erschwinglichere additive Technologien geben der Branche Grund, sich auf noch mehr Innovationen denn jemals zuvor zu freuen, denn diese können heute noch von viel mehr Seiten kommen. Ob die größten Beiträge zur Innovation der nächsten 5 bis 10 Jahre nun von den Erstausrüstern stammen oder von Zulieferern, Behörden, Start-ups oder Bildungseinrichtungen, das ist schwer vorherzusagen. Mehr Köpfe als jemals zuvor haben heute Zugang zum 3D-Druck, also treffen die Innovationen auch schneller denn je ein.
Mit dem wachsenden Verständnis des 3D-Drucks in der Luft- und Raumfahrtbranche und der zunehmenden Vielseitigkeit in Technologie und Materialien wird die additive Fertigung weiter an Dynamik gewinnen und die Art und Weise verändern, wie wir Luft- und Raumfahrzeuge warten und konstruieren.