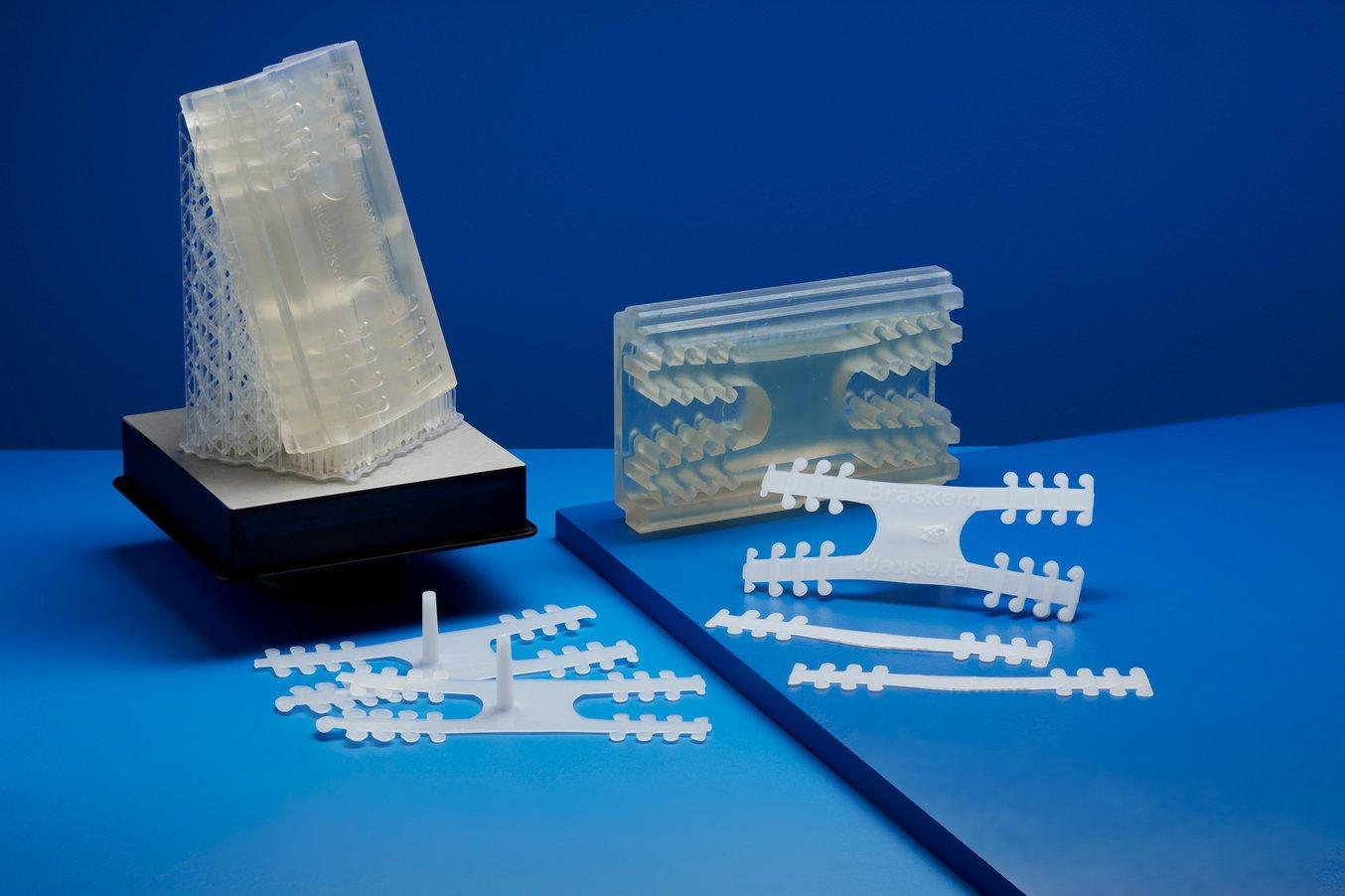
※本記事は現在翻訳中です。近日のアップデートをお待ちください。本記事の内容詳細をお求めの方は、[email protected]までお問合せください
Moldmaking is used across industries by product designers, entrepreneurs, and teachers to create identical parts. Injection molding specifically is a versatile molding process that is used to typically produce these parts in high-volume. Injection molding in large quantities is cost-effective, highly efficient, repeatable, and produces high-quality parts. For smaller quantities though, the cost and time required to fabricate the mold out of common tooling metals introduce barriers to the process, often making injection molding at this scale unobtainable for many companies.
So what do you do when you receive an urgent request to produce a few thousand identical parts with a one-week turnaround? Leveraging 3D printed injection molds for low-volume production significantly reduces cost and time compared to CNC milling metal molds, while still producing high-quality and repeatable parts.
Formlabs spoke with Technology Development Engineers Michelle Sing and Jake Fallon, Additive Manufacturing Process Engineer Collin Azinger, and Global Additive Manufacturing Technology Manager Fabio Lamon of Braskem, one of the world’s leading petrochemical companies, to talk about their first foray into injection molding with a 3D printed mold.
How to Quickly Fabricate Short Run Injection Molds: A Live Panel Discussion
Join us for a panel discussion in which experts from the injection molding industry will discuss how 3D printing enables in-demand mold fabrication to generate hundreds of parts, from idea to production, in a matter of days.
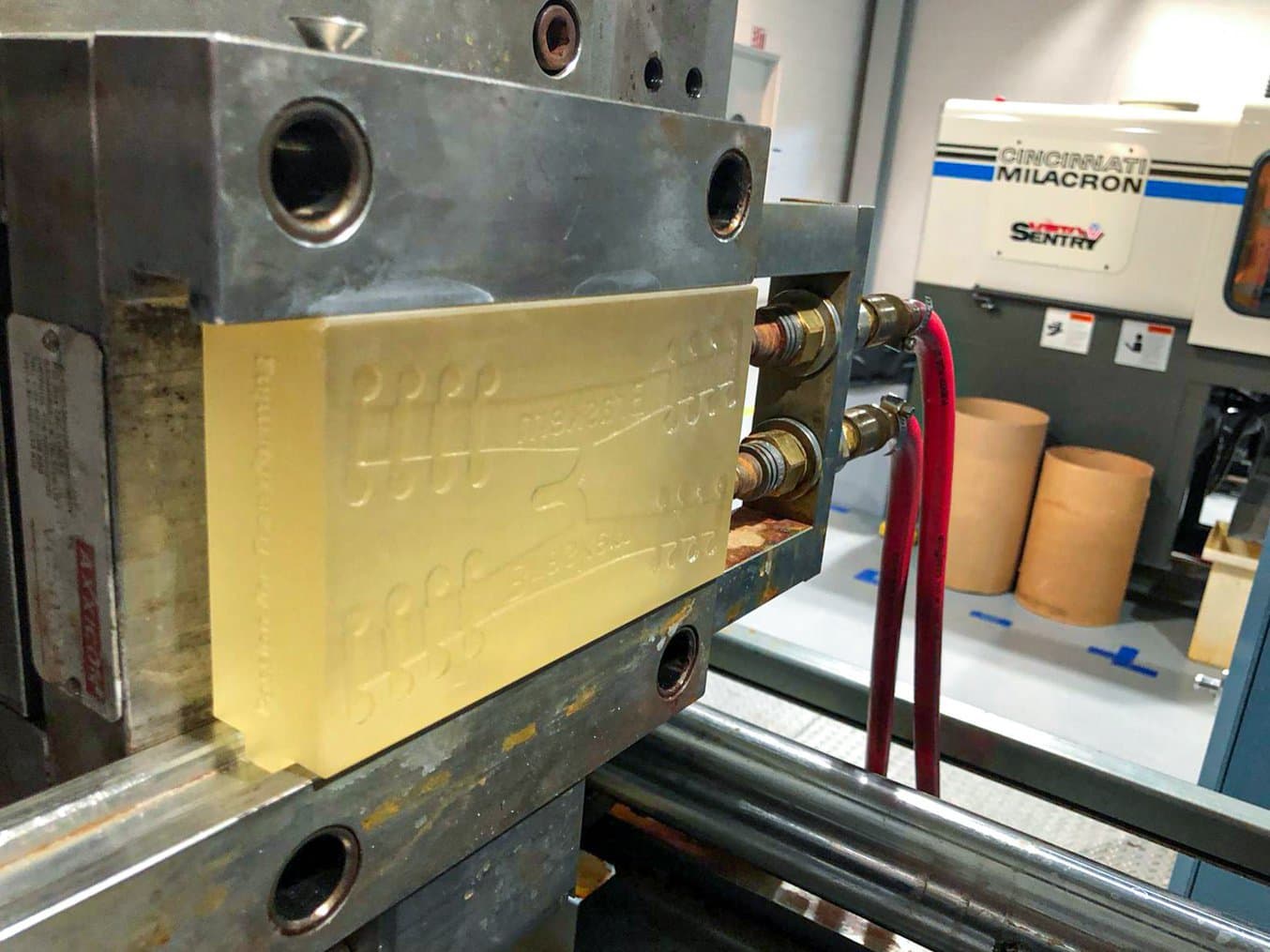
Direct Printing or Injection Molding?
Jake Fallon opened his inbox to see an urgent email from one of Braskem’s VPs—with COVID-19 spreading, the company needed to create thousands of straps for masks to protect their global workforce. What could Jake do in 48 hours with the equipment in Braskem’s tool chest?
When Jake met with his coworkers on the Braskem additive manufacturing team, their first thought was to 3D print the straps directly using a fused deposition modeling (FDM) printer. However, even with the speed of FDM, they estimated it would take 17 minutes per strap. Given the request called for creating thousands of straps, this would take far too much time. In addition to their benchtop FDM printers, Braskem’s Pittsburgh Tech Center also had a Formlabs Form 3 and industrial injection molding equipment. This seeded an idea, but also many questions.
What can injection molding offer? Injection molding is widely known to be an efficient and quick way to mass-produce parts, but there was early skepticism around creating a plastic 3D printed mold for their all-electric Cincinnati Milacron 110 Ton Roboshot machine. Could a plastic mold hold up to the pressure of the machine? Would it break after 50, 500, or even 1,000 shots?
Braskem turned to High Temp Resin, a Formlabs material capable of printing molds and inserts that can be used with demanding processes like injection molding to produce parts in end-use production materials. High Temp Resin has a heat deflection temperature of 238 °C @ 0.45 MPa. This was important because the team had to keep pressure as low as possible to reduce the risk of breakage on the mold gate. This required increasing temperature for lower viscosity; High Temp Resin was the ideal material to handle the higher temperatures and lower pressures required for this specific mold.
The team designed a mold that produces two straps per shot. They took their first 3D printed mold off the Form 3, removed supports and put it through a minimal sanding process. As the shots started firing, the straps began to pile up. A flexible low viscosity polypropylene was injected into the mold in order to reduce pressure in the cavity and extend the lifetime of the 3D printed part.
The very first iteration of the mold held up to 5-ton clamping pressure, 20-second cycle time, injection speed of 0.5in/s, and holding pressure of 5000 psi for approximately eight seconds. Average molding temperatures were about 230°C.
“We use High Temp Resin V2 at 50 microns. The quality was super nice, the resolution was fantastic. If you picked up the strap off a table, you would have a hard time differentiating it from a part made with a metal mold.”
Jake Fallon
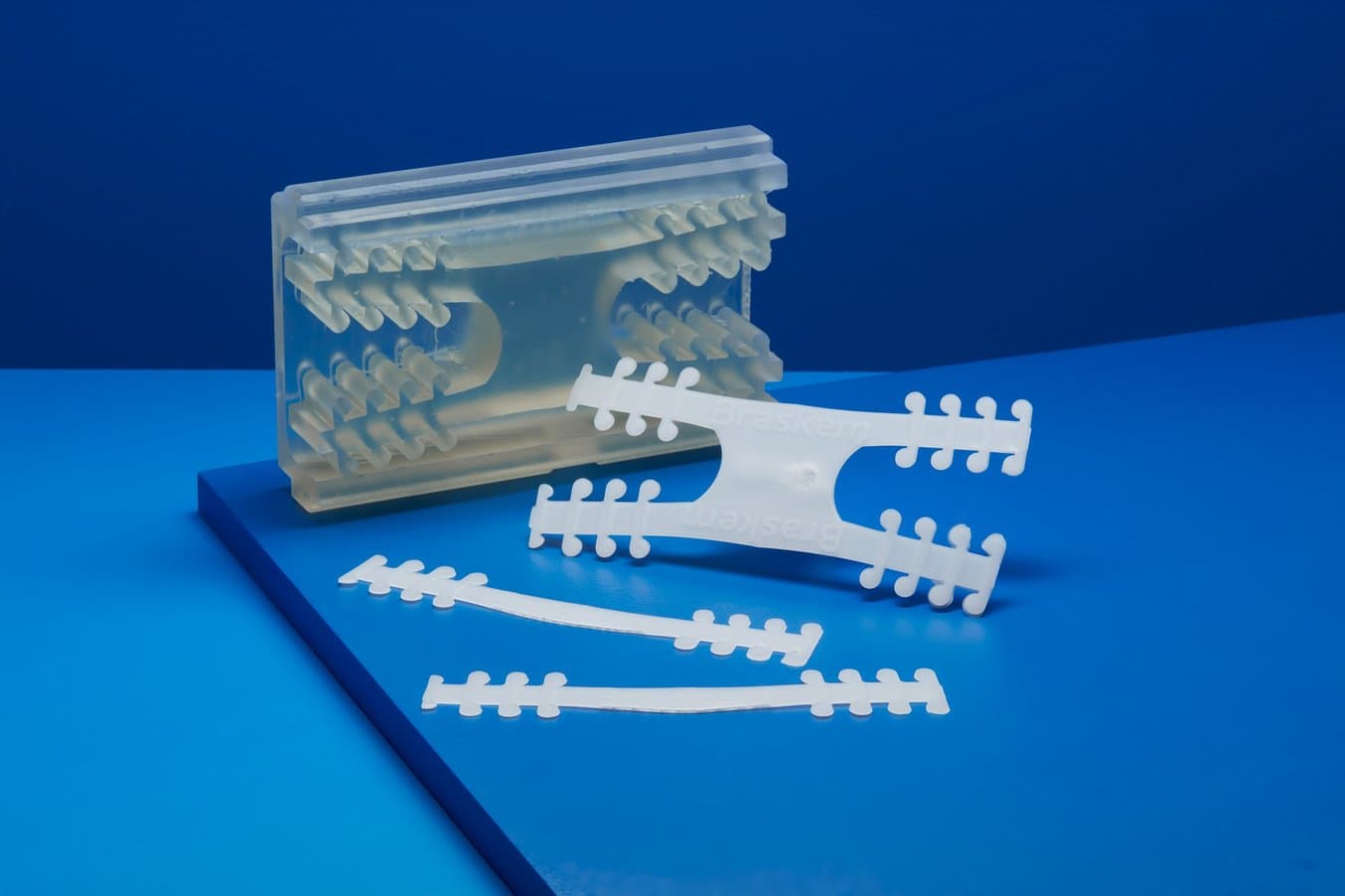
The team used a standard mold release spray, which gave them 40 to 50 shots per spray. The effectiveness of the spray was improved by printing at 50 micron layer height, creating a super smooth surface finish which allowed for the parts to be easily removed from the mold. There was no additional cooling needed for the 3D printed mold; there was no trace of reaction between the injected material and the printed resin.
Without access to 3D printing, Braskem would have had to outsource an expensive metal mold, costing the team money and valuable time. By leveraging 3D printing, the team was producing thousands of straps within a week of receiving the VP’s email and preparing them for shipping to offices around the world.
Design Iterations and Injections
“We reduced material use by 28% through design iterations”
Jake Fallon
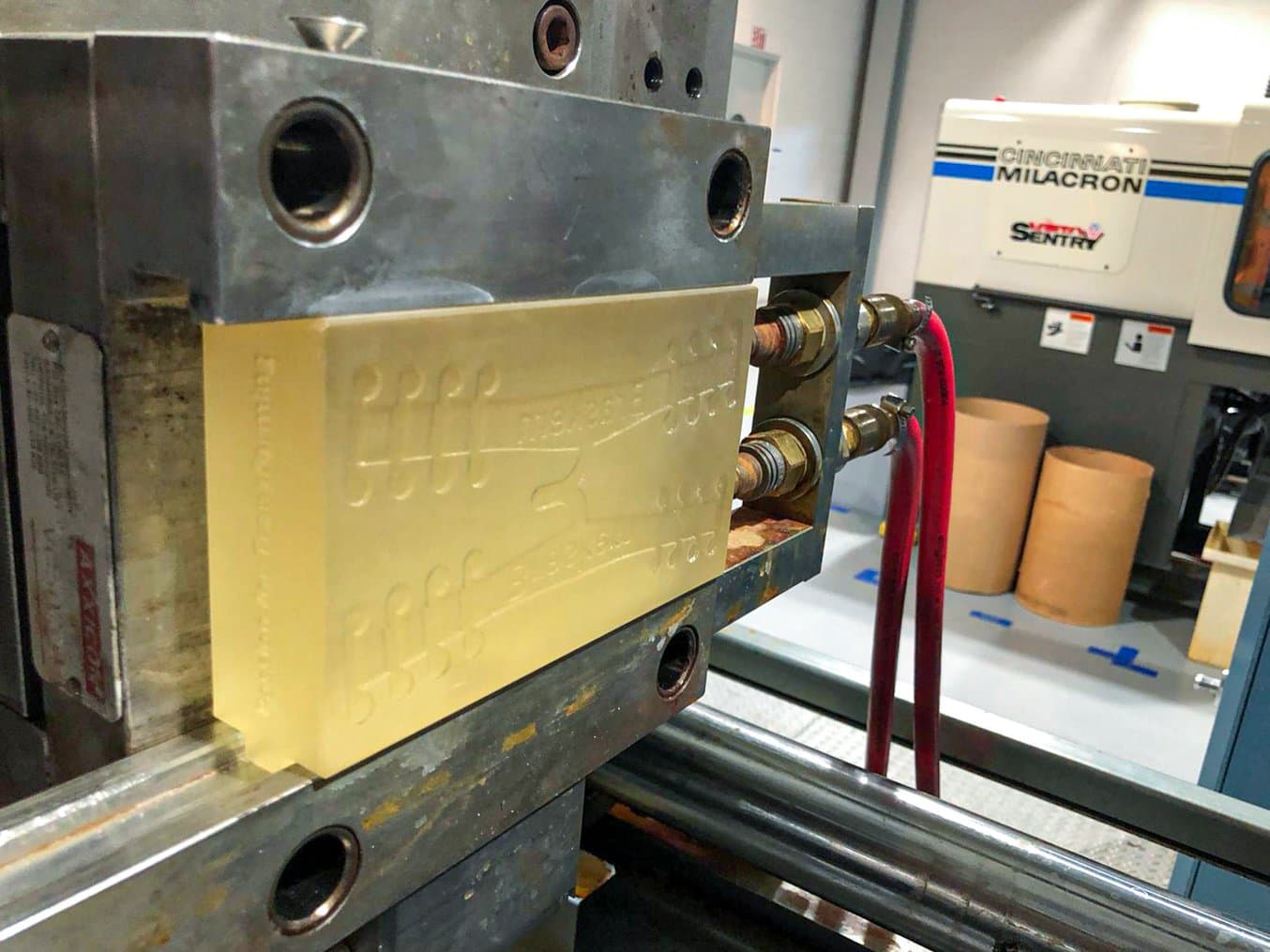
With the Roboshot machine creating straps, Jake went back to his CAD software to upgrade the mold’s design, with a focus on enlarging the gate. Jake wanted to reduce pressure and improve the flow inside the cavity in order to extend the lifetime of the mold, and to avoid flashing. In the process of improving the mold, he was able to reduce the amount of High Temp Resin used to print the mold by 28%, saving the company money and reducing print time.
Although mold V1 worked on the first attempt, mold V2, now with a larger gate, was designed to withstand thousands of shots. The new mold could withstand at least 1,500 shots before needing to be replaced, and enabled the team to fulfill the strap orders. Creating four straps per minute, the new and improved mold was exactly what the team needed to complete the task.
The Braskem team sees dozens of potential uses for 3D printed molds in the future. Affordable 3D printed molds, which cost less than $100 per unit to create, could help clients quickly produce small batch runs. An example would be seasonal packaging to make a product stand out on the shelf. Before, smaller firms would not be able to justify the cost of metal molds and tooling. But 3D printing molds that hold up to thousands of shots could open new marketing and branding opportunities.
Learn More
“Time was the number one benefit. We were testing the mold in one week, and then in one day created a second design which delivered significant improvements.”
Jake Fallon
The Braskem team was impressed with how injection molding expanded the capabilities of their 3D printer beyond rapid prototyping and into the realm of production. With hundreds of materials available for injection molding, Braskem has long been a reliable partner for firms using injection molding for mass production. They also sell over 300 materials for thermoforming, blow molding, and other manufacturing processes which could benefit from 3D printing molds.
In the future, the team is interested in injection molding possibilities with the Form 3L, given its ability to create large parts. According to Jake, “the 3D printed mold was near the limits of the build volume for the Form 3; we are really excited to explore the opportunities that the Form 3L enables”.
Download our free white paper or watch the webinar for a detailed process workflow, design guidelines, and other best practices for using 3D printed molds in the injection molding process and see additional real-life case studies with Novus Applications and Holimaker.