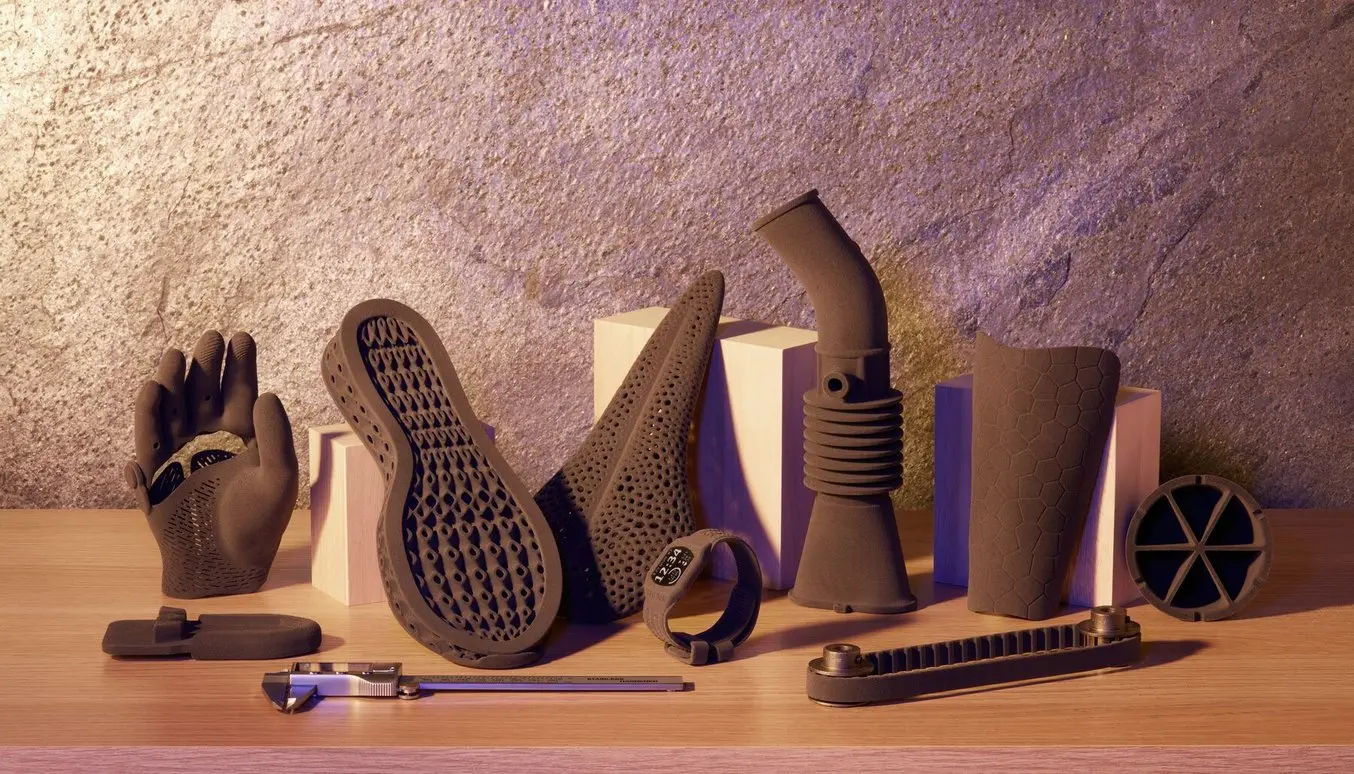
Formlabsは、FuseシリーズSLSプリンタ用に開発した、初の柔らかい感触の材料、TPU 90Aパウダーを発表しました。TPUは、高い引裂強さと破断伸びを兼ね備えたゴム製材料で、SLS方式3Dプリントによるデザインの自由度と耐久性と合わせることで、新しい用途の可能性を生み出します。
TPU 90Aパウダーは弾力性のあるエラストマーで、以下のようなパーツの3Dプリントに最適です:
- 皮膚に安全なウェアラブル
- ソール、スプリント、歯列矯正用装置、義肢装具
- 保護用スポーツ器具
- ガスケット、シール、マスク、ベルト、プラグ、チューブ
- パッド、ダンパー、クッション、グリッパー
TPU 90Aパウダーをお持ちのSLS 材料ライブラリに加えると、Fuseシリーズプリンタの効率性、リーズナブルな価格、使いやすさに、全くの新しい力がプラスされ、柔らかい感触のSLSパーツの内製での製造が可能になります。20%のリフレッシュ率は、現在までに販売されているFormlabsのパウダーの中で最も低く、パーツの単価が抑えられ、ゴム製の試作品や実製品の製作、生産補助ツールの製造が、高価な金型を使うことなく内製で行えます。
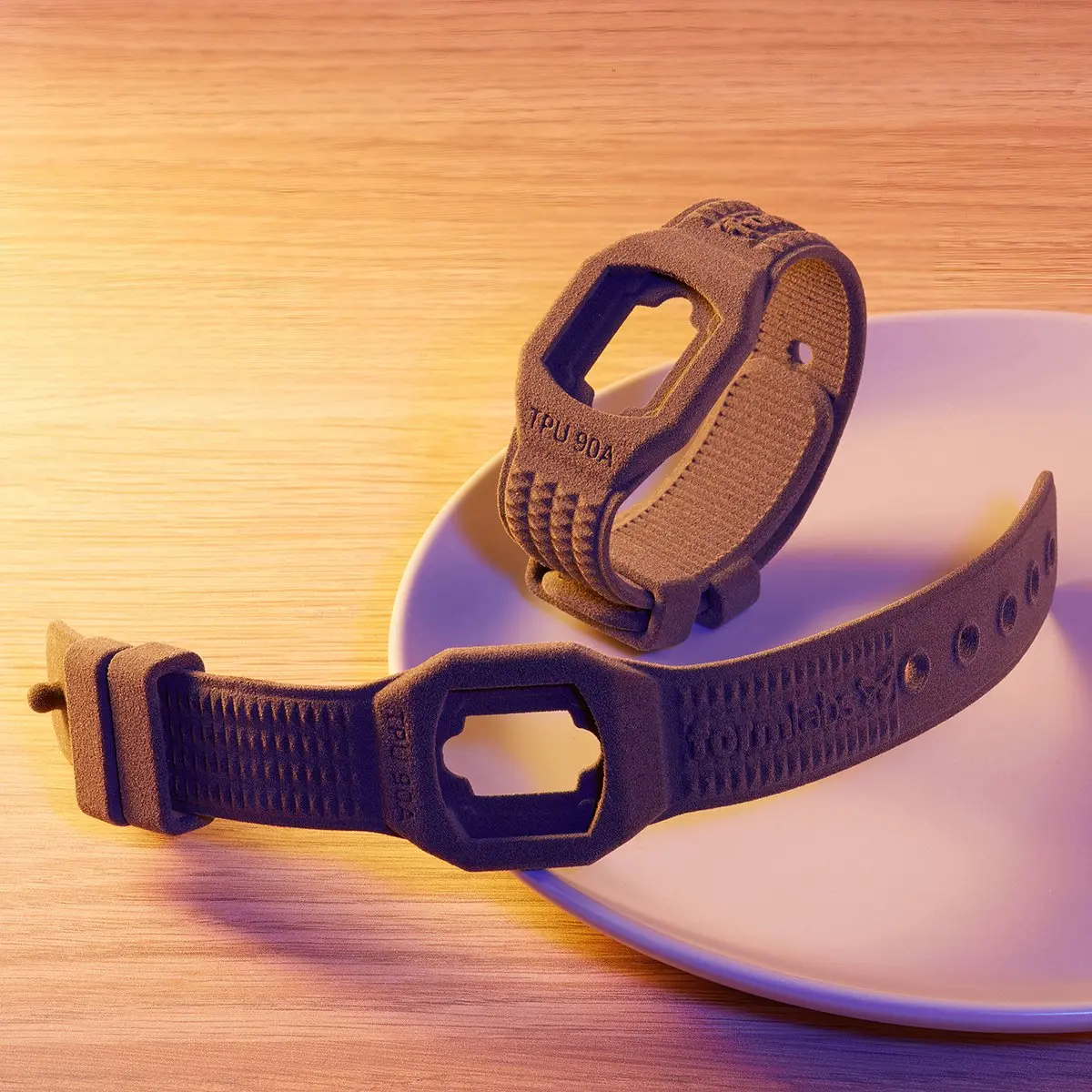
Formlabs SLSの軟質材:TPU 90Aパウダーの特徴と活用法とは?
TPU 90Aパウダーを使った柔らかい感触のゴム製パーツを、Fuseシリーズ3Dプリンタで内製する方法をウェビナーでご紹介します。
FuseシリーズでTPUを使う理由
現在、従来の鋳造ワークフローや従来のパウダーベッド方式3Dプリンタ等、エラストマーでパーツを製造する方法は数多くあります。これらのワークフローは、鋳造における形状制限や、大型の工業用3Dプリントの高価で複雑なプロセスがネックになっています。FormlabsのFuseシリーズ用のTPU 90Aパウダーは、複雑な形状の柔らかいパーツを、内製にてスピーディーに製造するのに最適な材料です。
FormlabsのFuseシリーズプリンタは、省スペースおよび低価格にて工業用レベルのSLSプリントが行える初のパウダーベッド方式3Dプリンタです。何千人に及ぶFuseカスタマーによってそのワークフローが実証された今、パウダーライブラリを拡大することがFormlabsの最優先事項です。入手しやすいSLSの登場で、小規模会社は生産方法の一貫性とその管理が可能になり、大規模会社は生産方法を多様化および分散化でき、サプライチェーンの安定化を図ることができます。Fuseシリーズにとって新しく、産業にとって馴染みのある材料の登場は、イノベーションを実現し、部門を超えて新しいワークフローを推し進める大きなきっかけとなります。
特性 | Nylon 11 CFパウダー | Nylon 12 GFパウダー | Nylon 12パウダー | Nylon 11パウダー | TPU 90Aパウダー |
---|---|---|---|---|---|
剛性 | ★★★★ | ★★★★ | ★★★ | ★★ | ★ |
延性 | ★★★ | ★ | ★★ | ★★★★ | ★★★★★ |
熱安定性 | ★★★★ | ★★★★ | ★★★ | ★ | ★ |
リフレッシュ率 (未使用パウダー比率) | 30% (不活性ガス) | 30~50% (空気) | 30% (空気) | 30% (不活性ガス) 50% (空気) | 20% (空気) |
TPU 90Aパウダーは、FormlabsのSLS用パウダーの中で最小の剛性と最大の延性を備えています。
TPU 90Aパウダーについて
熱可塑性ポリウレタン、略してTPUは、エンジニアリング、設計、製造分野で最も広く使われているエラストマーの熱可塑性樹脂です。この耐久性のあるゴム状材料は、スポーツ用品から医療機器、またシューズの靴底など、非常に幅広く使われています。
TPU製パーツの従来の製造には確立されたワークフローがあり、それらは依然として、ゴム製品の大量生産に適しています。FuseシリーズプリンタでTPU 90Aパウダーを使ってプリントすることのメリットは、ラピッドプロトタイピング、注文対応の生産用治具、およびカスタマイゼーションへの適用が簡単に行える点にあります。
ラピッドプロトタイピング
Fuseシリーズを使うことで、製造業者は内製によるプロトタイプが実現し、リードタイムを短縮し、今までサービスビュローや機械加工業者に費やしていたコストも削減できます。
例えばスポーツヘルメットのプロトタイピングには、硬い外郭と柔らかい内側クッションの両方の製造が必要となります。革新的な企業は、それらのクッションを作るために、新しいラティス構造と衝撃吸収テクノロジーの設計に取り組んでおり、その材料としてTPUは最適です。
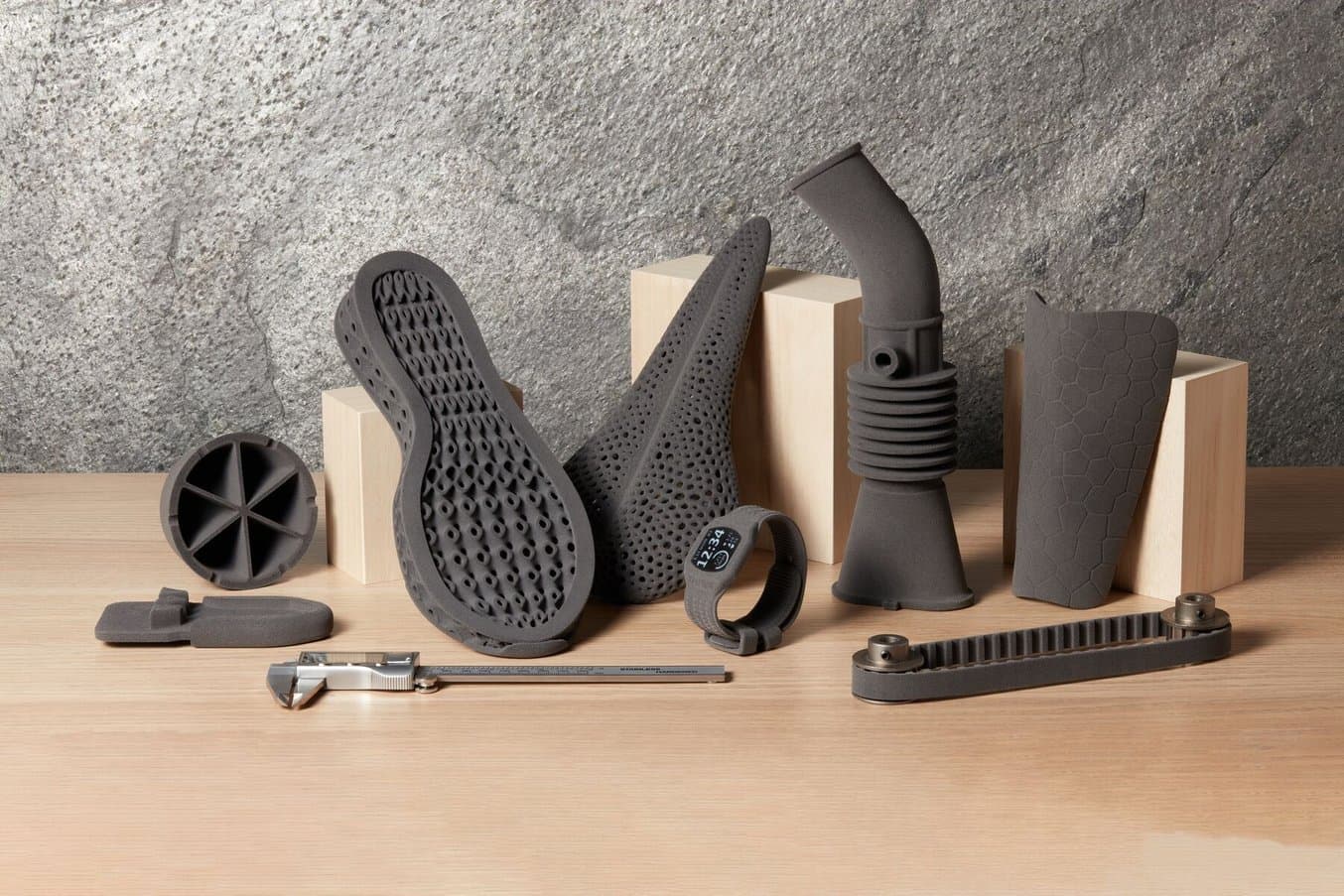
TPU 90Aパウダーは、皮膚に安全なウェアラブル製品、高性能スポーツ備品、靴底など、弾力性を必要とするパーツの機能確認用試作の製造に適しています。
しかし、新しいデザインや形状の検証を従来の金型方式で行うと極めて高コストとなり、デザインビュローに外注すると数週間かかってしまいます。硬い外郭と柔らかい内側クッションの両方を、1つのワークフローと1種類のテクノロジーのみで製造できるなら、イノベーターたちは反復検証を遥かに素早く行えます。これらのヘルメットには広範な物理的検証が不可欠で、1つのテスト段階にクッションパッドが10個必要です。この数は、クッション表面を丁寧に手作業するには多過ぎ、従来のTPUの鋳造を適用するには少な過ぎます。その解決策が内製による3Dプリントです。Fuseシリーズ 3Dプリンタがあれば、TPU 90Aパウダーを使って、ゴム製ラティス構造のわずかに異なる複数バージョンを簡単にプリントしデザイン検証を行えます。壁の厚み等、パーツそのもののデザインを変更することにより、それぞれのパーツの用途に合わせて硬度レベルを変えたり、テスト後に反復検証をしたりできます。
Fuseシリーズのワークフローで、多様な機械特性を備えた様々な材料を使うことができるため、すべて内製にて、1つの技術のみで多くの異なる部品の設計を行うことができます。TPU 90Aパウダーを使えば、信頼性のある1つのプラットフォームで、全く新しい種類の部品の3Dプリントが行えます
米国の玩具&電動自転車メーカーのプロトタイプ事例:Radio Flyer(ラジオフライヤー)とTPU材料
100年以上にわたり子供たちとその家族の信頼と人気を誇るRadio Flyerは、おもちゃの殿堂入りしたアイコニックなOriginal Little Red Wagon(オリジナルリトルレッドワゴン)®を製造しているメーカーです。同社は、子供たちのお出かけ先の想像が膨らむような、リトルワゴン、キックスケーター、三輪車、ゴーカート、電動自転車等の乗用玩具、その他多くの画期的な製品を手掛ける世界的トップメーカーとして、ポピュラーカルチャーの最前線に立ち続け、子供たちのクリスマスプレゼントに欲しいものの上位に登場しています。
Radio Flyerの開発において3Dプリントは非常に重要なプロセスであり、デザインエンジニアのAgostino Lobelloは、TPU 90Aパウダーが機能確認用試作に真に役立つと実感しています。「ハイグリップな表面仕上がりは、今までに使ったことのある他の3Dプリント製TPE/TPUとは異なっています。どちらかというと、当社が射出成形したTPE/TPUのような感じで、それが試作品用途で使えるのはありがたいことです。現在、このプロセスへ最良の策になり得るものとしては、プロトタイピングツールと実際のTPEまたはその他のウレタンの注入で、これによりさらにコストと時間が削減できます」とLobelloは言います。
Radio Flyerは、自社の製品がユーザーである子供たちにとって安全で使いやすく、楽しいものであるために、広範囲なテストを行っています。実際の使用環境での試作品テストが不可欠であり、それにはデザインチームが、頑丈で摩滅や消耗に耐えるパーツを素早く反復検証することが必要です。「パーツ自体非常に丈夫に作られています。それらのパーツを完成品に近い試作品に組み込み、家庭に送り人間工学およびユーザビリティに関するフィードバックを求めることができます。将来、タイヤの溝、ハンドグリップ、バンパー、シートクッションにこの材料を使うこと、また特定のばね定数でのTPE製ばねを試作する手段としても使えるようになることを楽しみにしています」とLobelloは述べています。
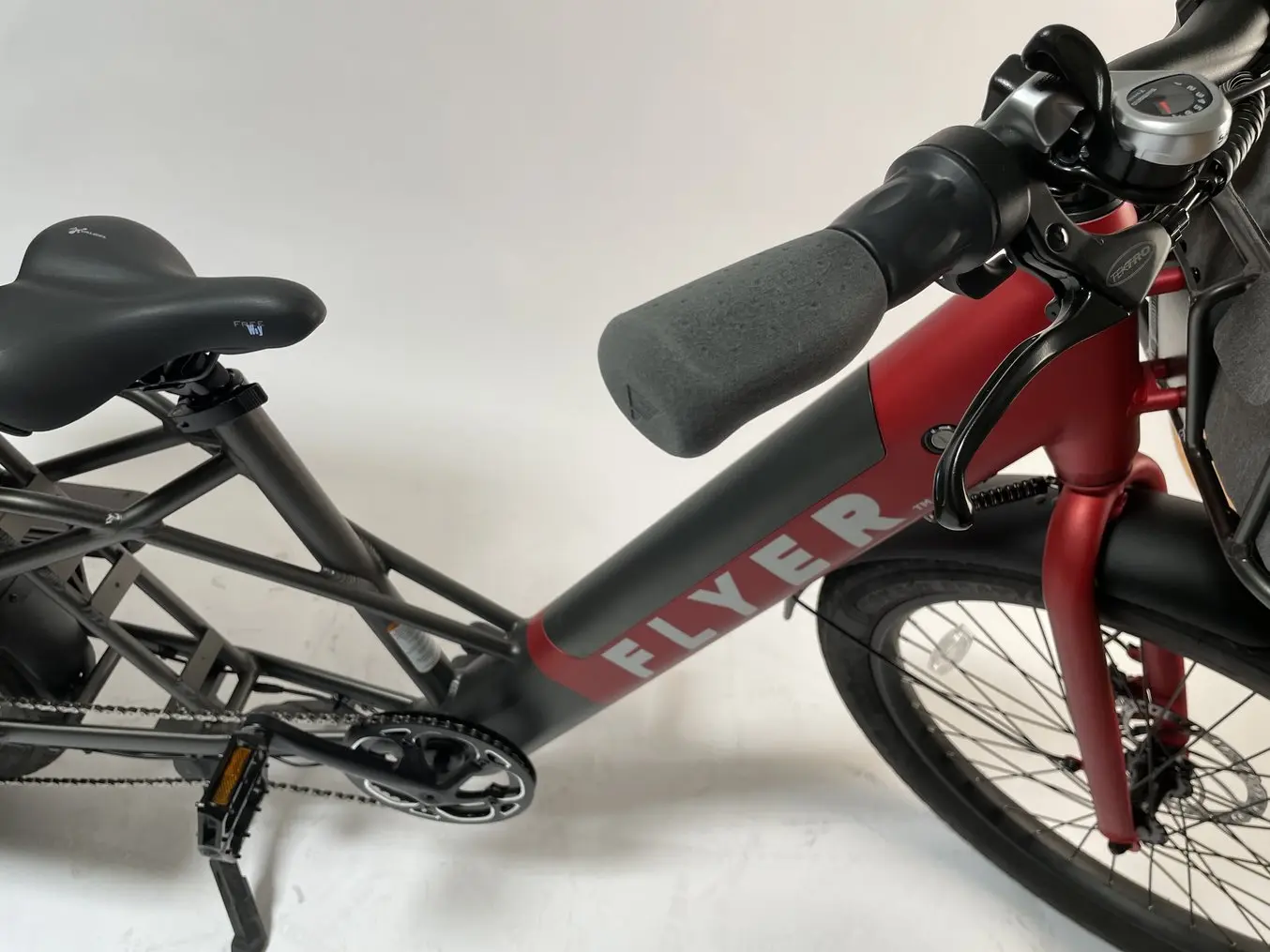
FuseシリーズプリンタでTPU 90Aパウダーを使うことは、Radio Flyer製品Flyer™ L885 Family Cargo eBikeのソフトグリップハンドルバーのようなパーツの機能確認用試作に役立ちます。
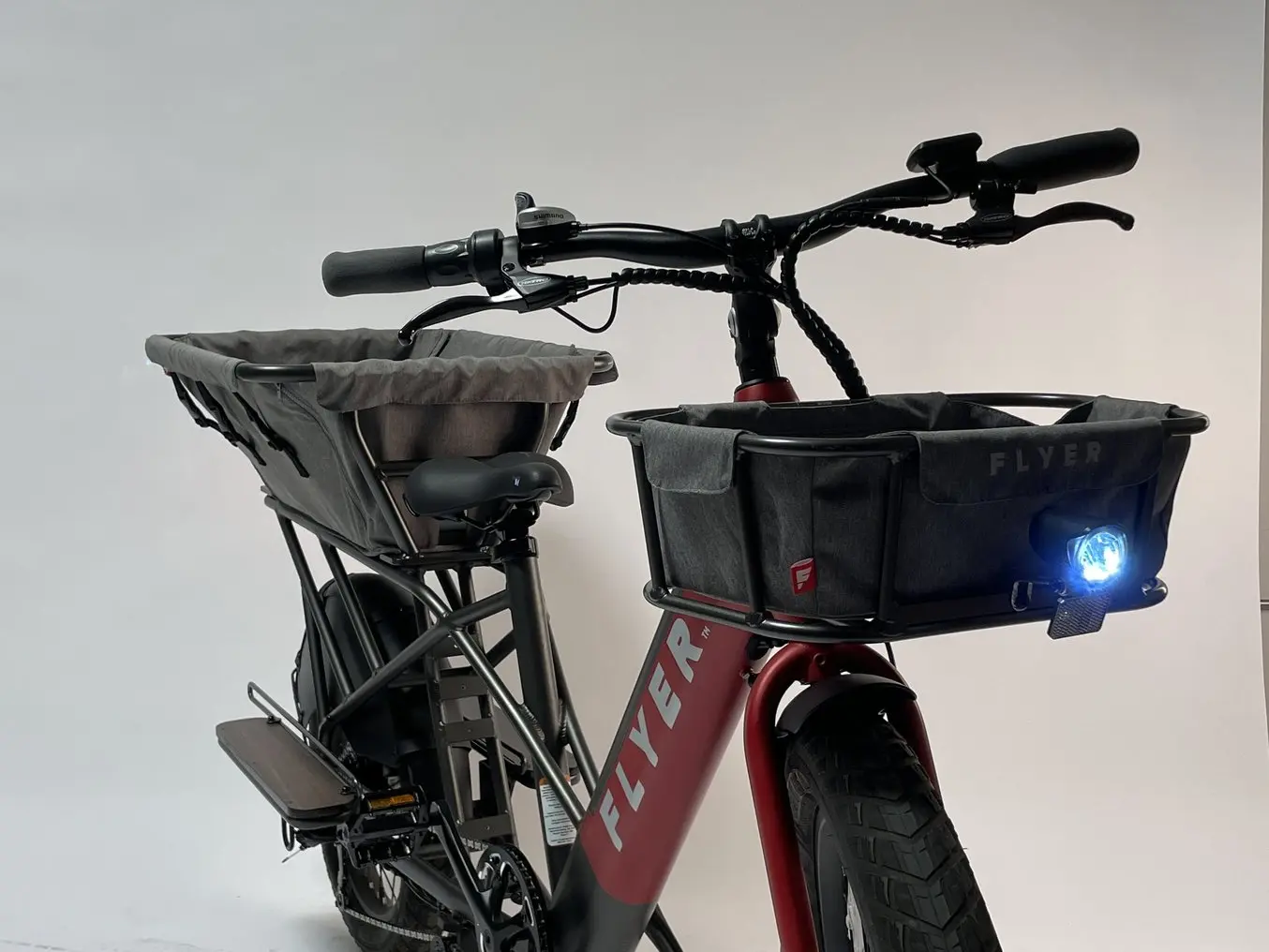
生産用治具
製造ビジネスに携わっていない限り、生産用治具の種類の違い等について説明することは容易ではないでしょう。肝心なことは、治具でも、ブラケットでも、筺体でも、その他の多くの方法の1つでも同じで、必要なときに、どうしても必要なときに、機械が連結して作動することです。TPU 90Aパウダーは多くの製造業者が直面する問題への解決策となります: 何百万ドルも費やした製造技術を数々の摩滅・消耗から守る方法。
柔らかな生産用治具を使うことで、一定の衝撃へのクッションや完璧な形状のグリッパが重機の寿命の延長をサポートします。長年に及ぶ反復利用により、密封部分やガスケットが破損した場合、作業者は即座に代わりの治具をプリントすれば、数時間以内に製造ラインに戻して作 動を開始できます。
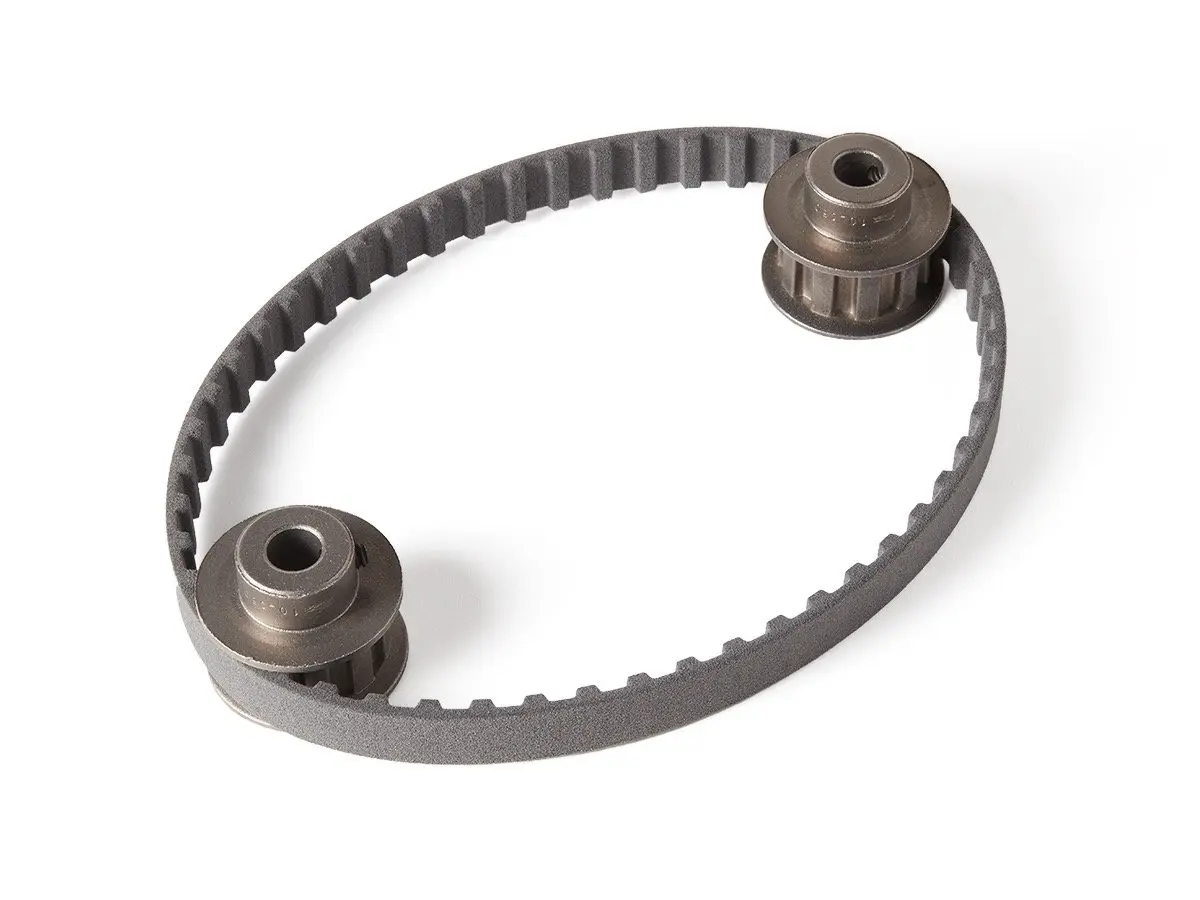
TPU材料があれば、柔らかい代替部品や生産用治具がその日のうちに設計・プリントできるため、継続的な製造が可能です。
新たな材料特性が加わることで、部品の破損や機械の不具合が避けられ、製造業者にとって生産の継続性がより確かなものとなります。内製にてより多くの機械的特性を使えるならば、サプライチェーンの遅延やOEMの高コストな修理代を避けることができます。3Dプリントしたゴム製パーツを使って、全く新しい設備部品の1部を、注文に応じて修理や交換することができるようになります。向上のラインや工程の停止を防ぐことで 何千ドルに及ぶ損失を免れることができます。
TPU 90Aは、自動車や航空宇宙産業のテストの振動ダンパー、また、独特な形状の部品の熱成形といった工業工程用治具にも用いられます。自動車工場では、大規模なロボットシステムが、曲げたり回したりできる構台の上で作動しています。カスタム化したクッションや柔らかい筐体によって、これらの機械の摩擦の軽減、寿命の延長につながります。
少量およびカスタム化した既製服
スポーツ、ファッション、ウェアラブルテクノロジー産業において、市場シェアを狙うブランドにとって、パーソナライズした製品の提供は不可欠です。金型を用いて少量または一点物の生産を行うことは、3Dプリントによる可能性が開けるまではコスト的にほぼ不可能でした。そして、ほとんどの3Dプリント材料はスポーツ用品やウェアラブル市場にとって、TPU 90Aパウダーが登場するまでは、柔らかさに欠けていました。個人の足形と重量分散に合わせてカスタマイズできる靴底から、衝撃吸収用に設計されたフットボールヘルメット、そしてそれぞれの手首に合わせて成形した腕時計バンドまで、可能性は無限に広がります。
皮膚に安全な品質のTPU 90AパウダーとFuseのワークフローを組み合わせることで、直接プリントしたウェアラブルのカスタマイゼーションがついに実現可能になります。腕時計、アクセサリー、シューズの高級ブランドの中には、モノグラムやグラフィックなどの細部のパーソナライズを必要とする場合があり、アイテムの実際の外形や形のカスタム化は極めて高額に及んでいました。Fuseシリーズのワークフローと皮膚に安全な品質のTPU 90Aパウダーが身近になることで、ウェアラブル産業のカスタマイゼーションが可能になります。
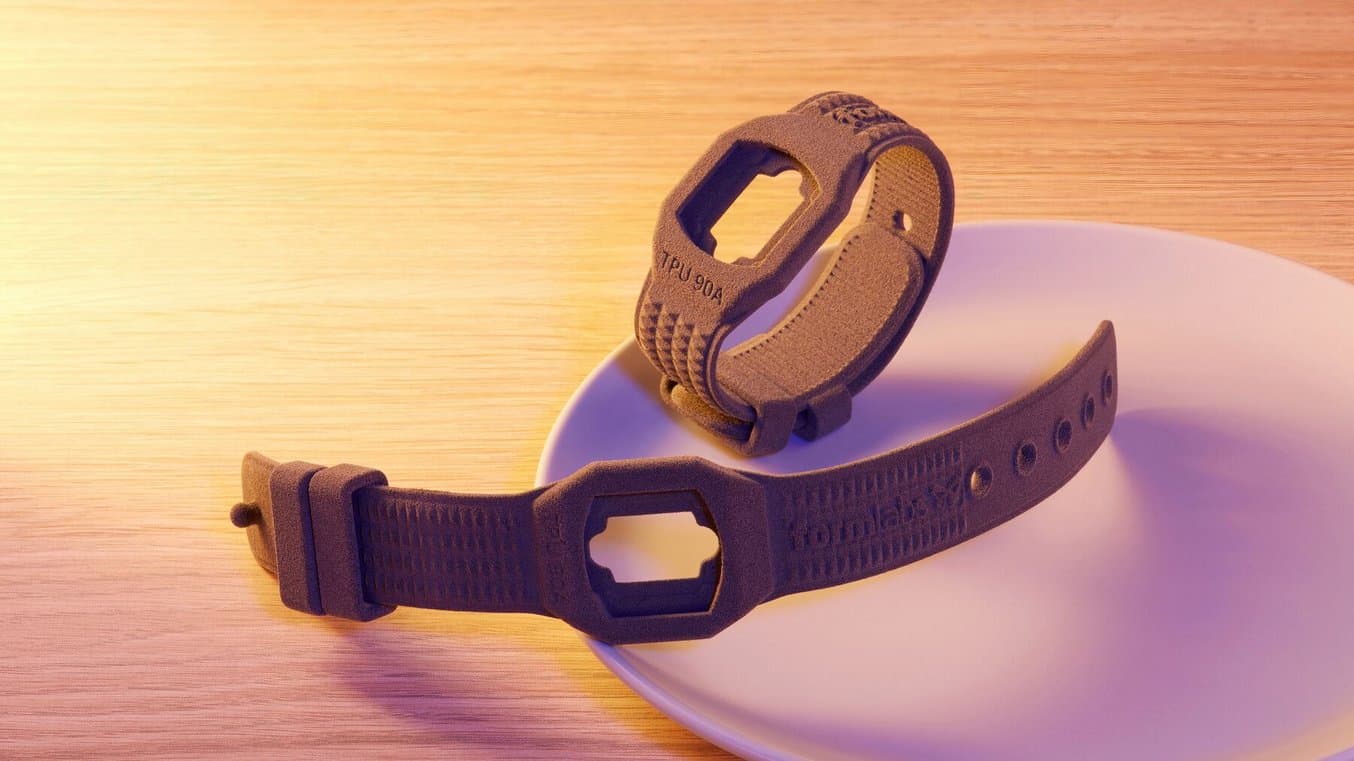
FuseシリーズのワークフローでTPU 90Aパウダーを使えば、現実的な価格と効率的な設定にて、カスタム生産が内製で行えます。
医療機器
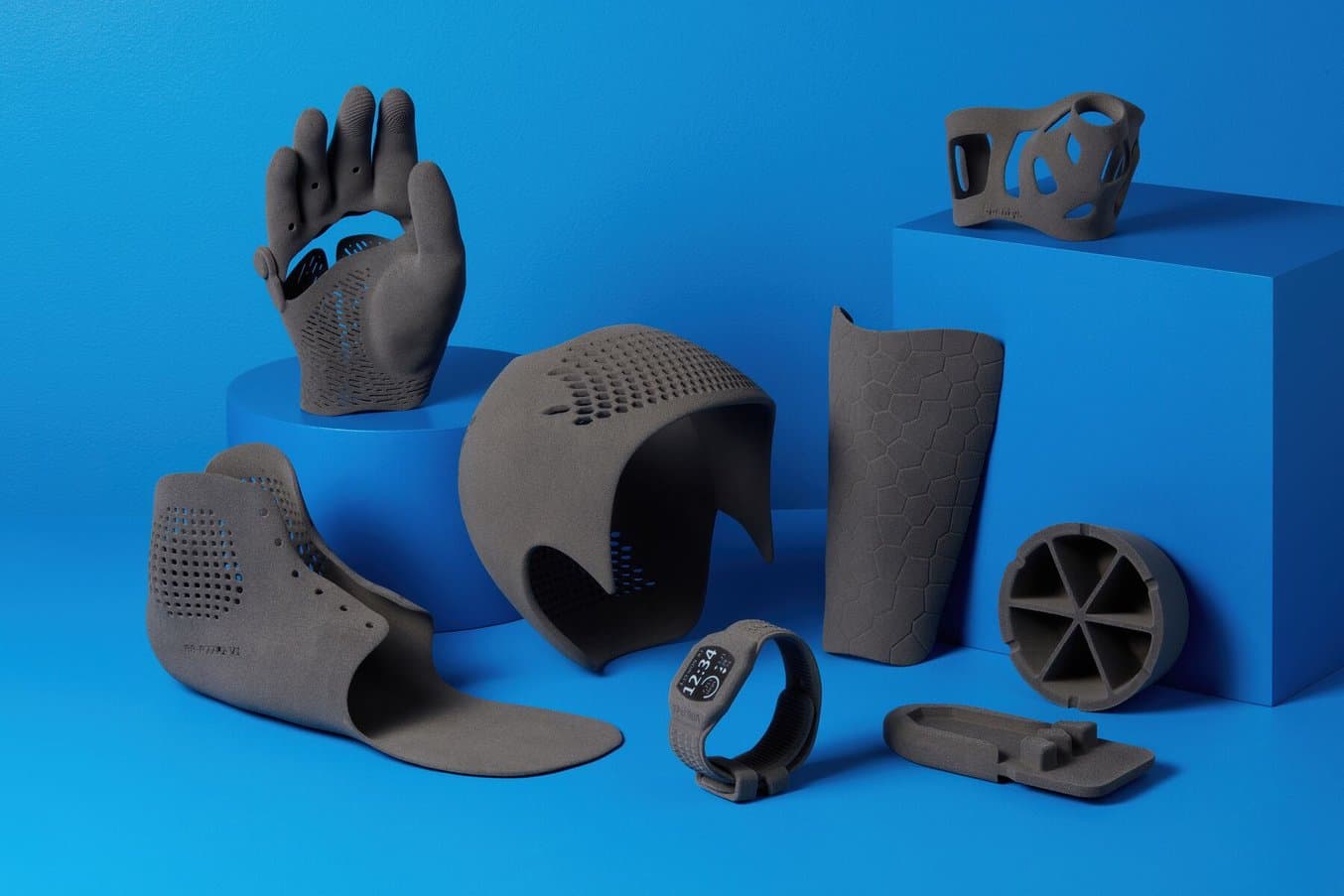
TPU 90Aパウダーによって様々な高性能医療用部品の製造が可能になります。例:義肢装具(OT Supply GmbH提供)、親指サポーター(Spentys提供)、足首サポーター(Spentys提供)、腕時計バンドその他。
Formlabs Medicalは、すべての医療機関がより良い治療を各患者様に提供するため、最新のツールを利用できるよう尽力しています。TPU 90Aパウダーは、Formlabsのビジョンの次のステップとして、業界をリードするSLS用パウダーシリーズに新しく加わり、Formlabs Fuseシリーズ3Dプリンタで使うことによってさらに価値を高めます。
優れた耐久性と堅牢性を備えたTPU 90Aパウダーは、義肢装具、歯列矯正装置、患者専用機器、医療機器への使用に最適です。この材料は、高い引裂強さと破断伸びを兼ね備えたゴム製材料で、SLS方式3Dプリントによるデザインの自由度と耐久性と合わせることで、医療従事者たちに新しい可能性を生み出します。
TPU 90Aパウダーは弾力性のあるエラストマーで、以下のような医療用パーツの3Dプリントに最適です:
-
医療機器プロトタイプおよび実製品用医療機器とその構成部品
-
矯正パッドや義肢ライナー
-
ウェアラブル、シール、バンパー、チューブ
-
スプリント、頭蓋形状矯正ヘルメット
-
運動選手用および矯正用インソール
他のSLS材料同様、TPU 90Aパウダーを使うことで医療従事者は、コスト効率の最も良い方法での生産が内製で行えます。個人の足形と重量分散に合わせてカスタマイズできる靴底から、衝撃吸収用に設計されたフットボールヘルメット、そしてそれぞれの手首に合わせた腕時計バンドまで、可能性は無限に広がります。
TPU 90Aパウダーは、短期の皮膚接触認定を受けており、皮膚に装着しても安全と見なすことができます。しかし、生体適合性用途への追加検証は行われておらず、プリントしたパーツが目的の用途に適しているかどうかの検証は、製造者の責任となります。
TPU 90Aパウダーを内製での生産に導入する方法
TPU 90AパウダーはFuseシリーズとFuse Sift のワークフローに簡単に統合できます。この材料は空気環境でプリントでき、不活性環境は不要です。さらに、TPU製パーツはSurface Armor(より硬いパウダーでのパーツ表面の半焼結シェル)を使わないため、脱パウダー処理がとても簡単です。TPU 90AはSurface Armorは使いませんが、滑らかで使いやすい材料にするためには、ブラスト処理によってパーツからすべての余分なパウダーを取り除くことが奨励されています。
現在お持ちのFuseプリンタをTPU 90A用プリンタにすることはもちろん可能ですが、専用のFuse、Sift、ビルドチャンバーのご使用をおすすめします。
TPU 90Aによる新しい可能性
初めて自社製品を市場に送り出そうとしている小規模会社でも、この数年間のサプライチェーンの混乱を避けようとしている大規模会社でも、高性能の3Dプリントを内製で行うことによりコストを削減し、安定性を向上させることができます。TPU 90Aパウダーのような材料は、新しい用途、さらには全く新しいビジネスモデルへの可能性を開くことで、これらのメリットを押し広めていきます。確実性を求めて大量生産せざるを得なかった柔らかいパーツは、今、入手しやすくなった3Dプリンタによって、一貫したプリントが行えるようになります。
デザインと製造の方法を新たに再構築するための鍵となるのは材料です。TPU製パーツは至る所で使われており、その定評ある性能とパワフルなFuseによるSLSワークフローを組み合わせることで、あらゆる産業にイノベーションをもたらすことでしょう。