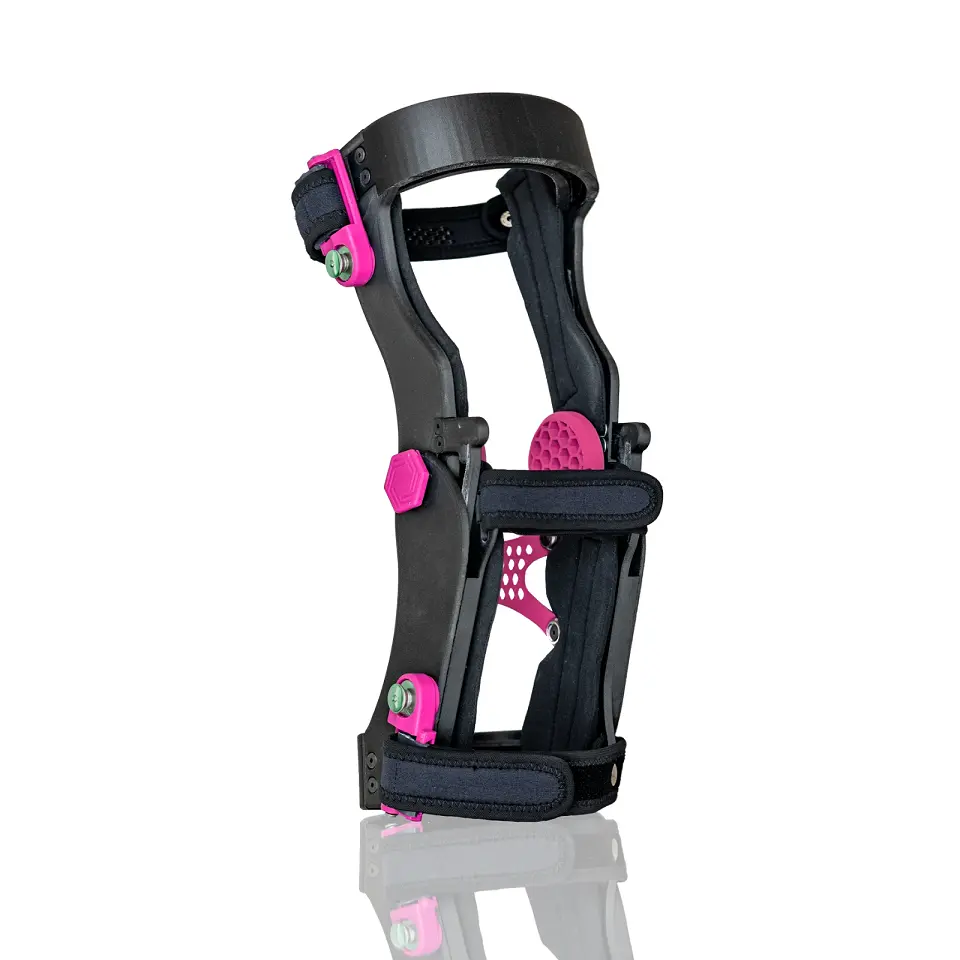
While studying engineering in college, Mike Geldart suffered a significant knee injury in a racing accident. After surgery, he was given a knee brace that was stiff, didn’t properly fit, and was inadequate for a fast recovery.
Now CEO of GRD Biomechanics, Geldart is turning his frustrating recovery experience into action by creating a truly innovative knee brace. Designed with 3D printing, the knee brace enables faster recovery times and reduces surgeries for early patients. In this post, Geldart explains why 3D printing is empowering the next generation of medical applications for lower-limb recovery.
Changing Lower Limb Recovery
Basic care for lower limb recovery has seen little change in 50 years, with current leg braces being made of simple metal frames, foam, and plastic parts. The goal of these devices is simple: to hold the patient's leg in place until it heals. According to Geldart, this view of bone and muscle healing isn’t based on solid evidence. “These devices offer long lead times, suboptimal experience, and they are not terribly effective at healing the patient,” he said.
In order to change how the market thinks about leg and knee recovery, the GRD team began prototyping dozens of new devices aimed at strengthening muscles instead of reducing patient movement. Over time the team settled on combining 3D printing molds alongside 3D printing end-use parts to help create a state of the knee exoskeleton, which they are calling the Ascend Knee Brace.
The main strap that holds the Ascend onto the leg is an end-use part printed directly with Tough 2000 Resin. This part is put under constant stress, adjusted by the patient everyday, and is exposed to daily wear and tear. Due to the shape of the strap, Geldart said “it would be difficult to machine or mold this part, so we print it directly on the Form 3.”
The ability to print functional end-use parts is a significant cost and time saver for a small business. According to Geldart, “this clip would be near impossible to injection mold, and even if we could do it, it would burn through our working capital. Using the Form 3, we are making more complex geometries that suit each application, and we are doing it for less money.”
Geldart’s team also prints molds for two interior hinges. This allows the team to access small-batch production with their 3D printer, guaranteeing affordability despite each patient requiring a custom brace. Using these two methods - end use production and 3D printed molds - show the versatility of in-house printing for start-ups such as GRD. For patients, this means that it is feasible, for the first time, to have access to truly customized medical solutions, accelerating recovery times.
When looking to invest in a new 3D printer, Geldart considers a couple of vital components, with material properties of the materials being most important. For Ascend, the design requirements come directly from each customer, and so there can be no compromise. The goal is for each Ascend to be a perfect fit. Parts must be durable, but not fragile, flexible, but strong. Each brace calls for parts of different material properties, meaning a 3D printer must be able to handle multiple requirements.
Small businesses are acutely aware of wasted time and resources, which for GRD can potentially dampen relationships with doctors and patients who are waiting for brace. That’s why the second most important trait Geldart looks for is reliability. He said, “we can’t use a printer that gets 18 or 20 hours into a print and fails. We are looking for a printer that will, in part, be used for production. So we want a reliable printer that can handle running 24 hours per day.”
Early Success: Avoiding Surgery
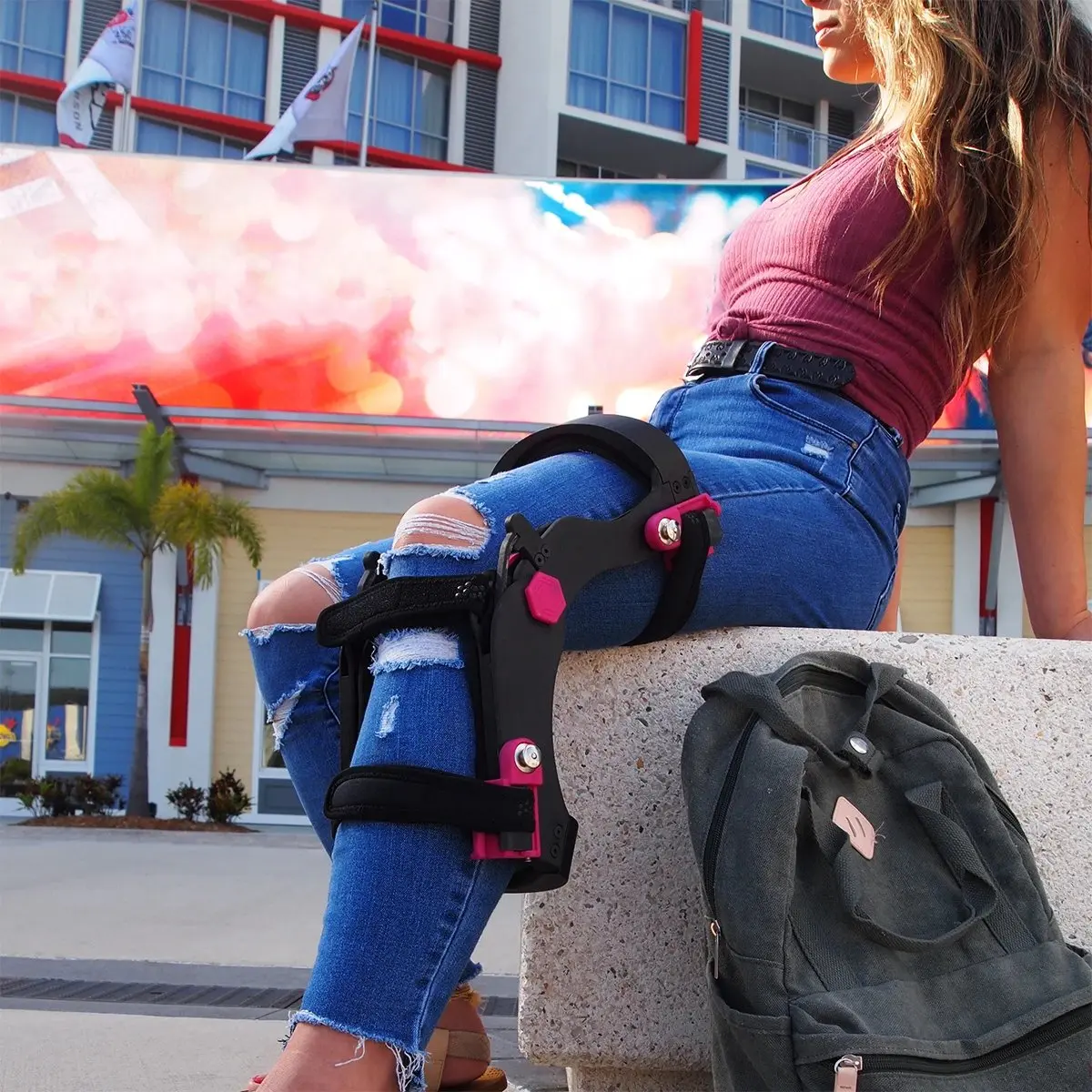
The company has seen early success with Ascend. In one case, a young woman was heading toward her fifth knee surgery before being put in touch with GRD. They created a patient-specific brace, and the surgery was cancelled. The patient quickly recovered, saving her time and money by skipping the fifth surgery. Quicker recovery times also free up healthcare professionals to focus on other patients, eliminating multiple unnecessary surgeries for the same patient.
Knee braces are especially important for runners. One patient GRD worked with had suffered from runners' knees for years. After using the Ascend, he was able to run five miles without serious pain. This type of patient outcome is only possible with cutting edge customer specific medical devices.
One day, Geldart expects to see these types of stories become commonplace. “I think the market is heading toward a blend of standardized production and customization. We envision a world where we can manufacture to design instead of design to manufacture. Right now we are making more complex geometries that suit the application requirements, and we are doing it for less money than traditional manufacturing.” Until then, he expects to continue to refine his design with relentless prototyping and R&D, saying “I’ve lost count of how many prototypes we have created. 3D printing allows use, effectively, to make endless prototypes until we get the part exactly right.”
Learn More About the Form 3
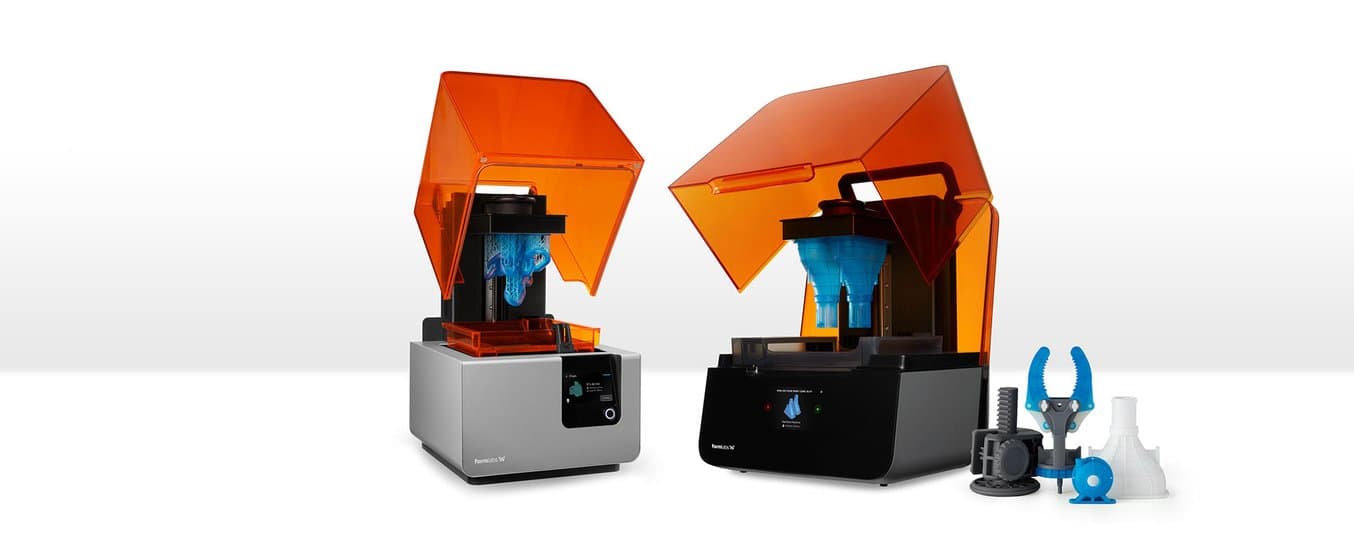
GRD used both the Form 2 and Form 3 for their parts.
Currently, the GRD team has four Form 3s and three Form 2s. This allows for flexibility, running all seven printers at once for maximum productivity when demand is high, or to reserve a few printers for R&D. Right now, the team is happy with their fleet of SLA printers, but are always eyeing future expansion. According to Geldart, “we are interested in Nylon printing and Fuse 1. Right now they are using Nylon parts on the base of the brace, and we see room to explore and expand in that area.”
Looking to learn more about the Form 3? Request a free sample part in Tough 2000, the same material used by GRD on the Ascend.