Which 3D Printing Technology Is the Right One for You?
Compare Formlabs SLA and SLS 3D Printers
SLA
SLA
Stereolithography (SLA)
SLA 3D printers use a light source to cure liquid resin into hardened plastic in a process called photopolymerization.
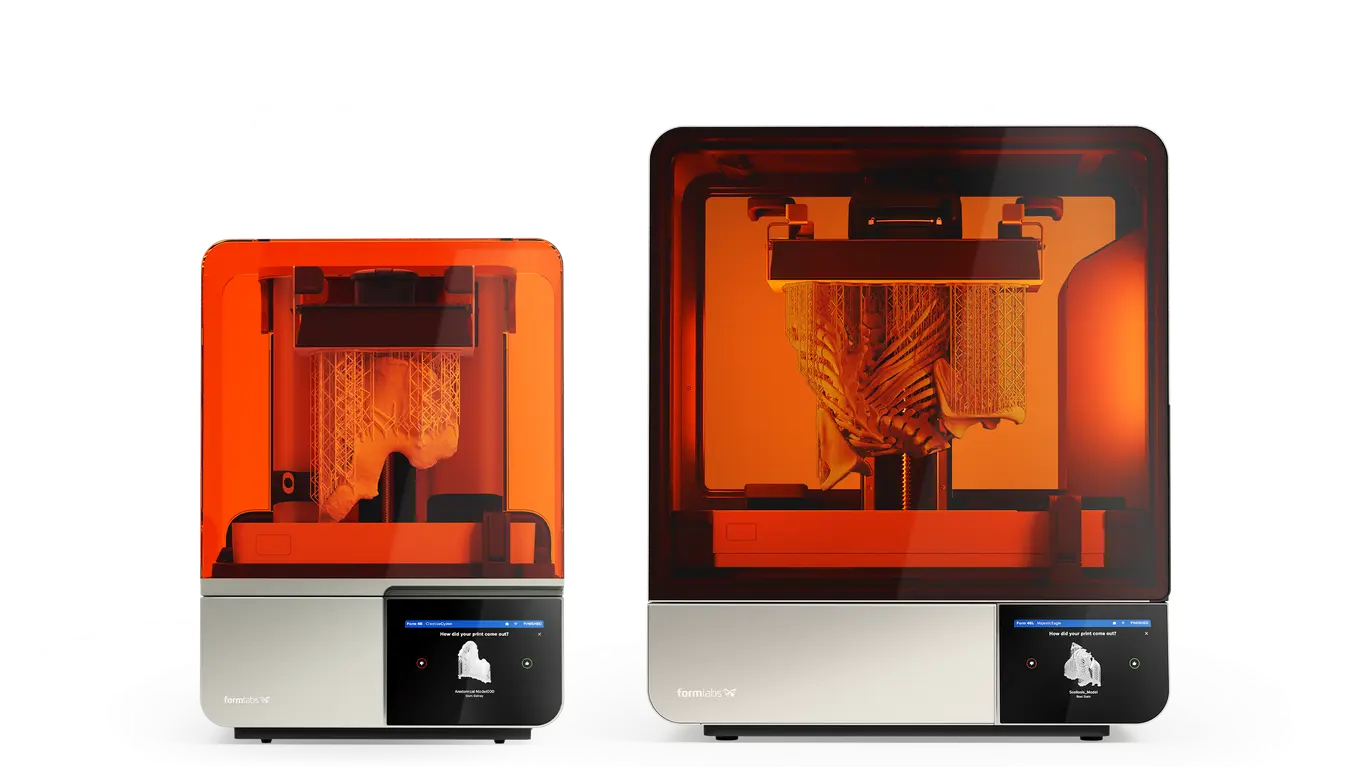
Overview
TECHNOLOGY
Stereolithography (SLA)
Formlabs SLA 3D printers use next-generation Low Force Display™ (LFD) technology to quickly deliver incredible surface quality and print accuracy, meeting the demands of today’s market for scalable, reliable, industrial-quality 3D printing.
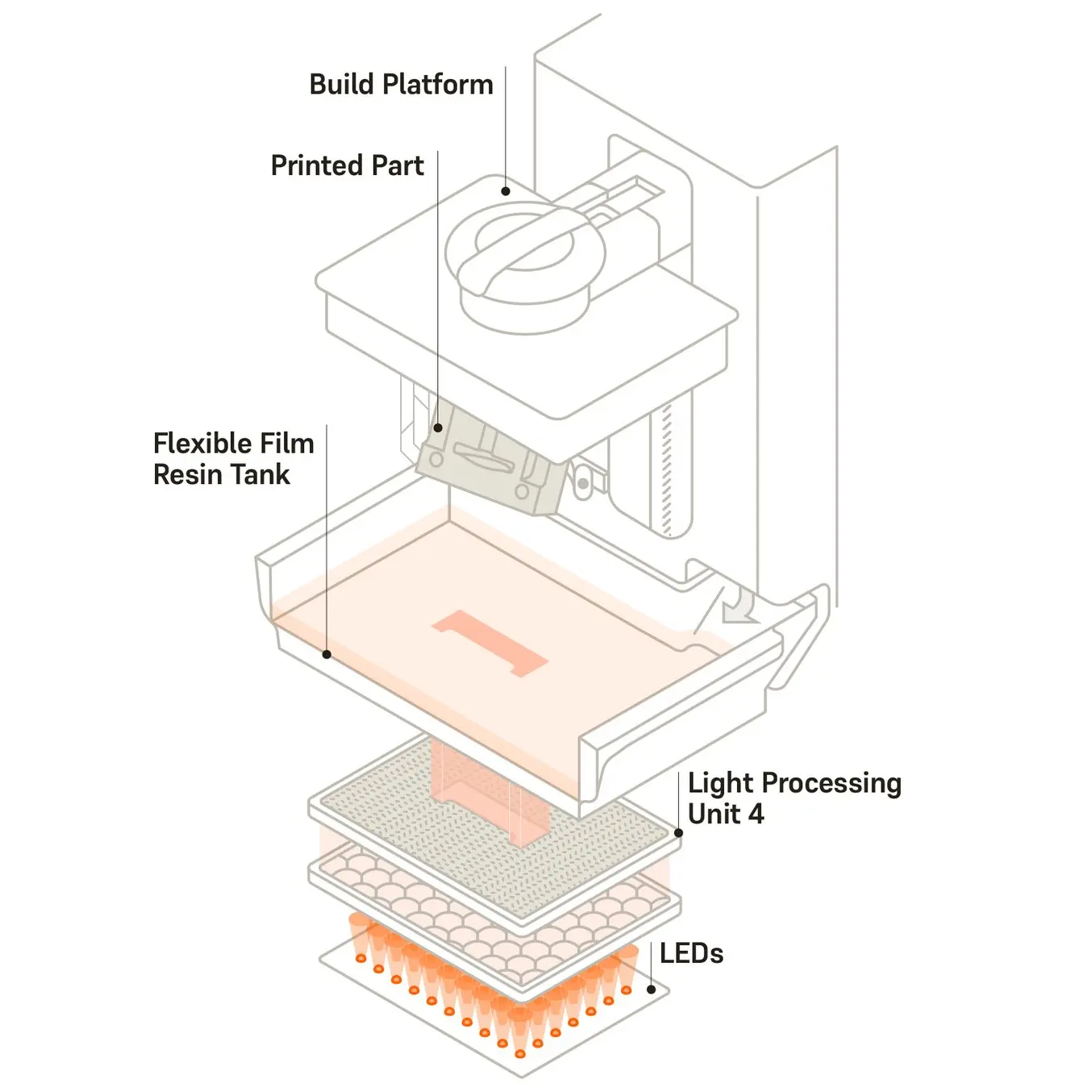
BENEFITS
- Blazing-fast print speed
- High resolution and fine details
- Great accuracy and print quality
- Wide range of materials
- Easy to use
APPLICATIONS
- Rapid prototyping
- Functional prototyping
- Concept modeling
- Rapid tooling
- Manufacturing aids
- Low volume manufacturing
- Dental models and appliances
- Medical models and medical devices
- Jewelry prototyping and casting
- Models and props
Material
SURFACE FINISH
Smooth, minimal layer lines
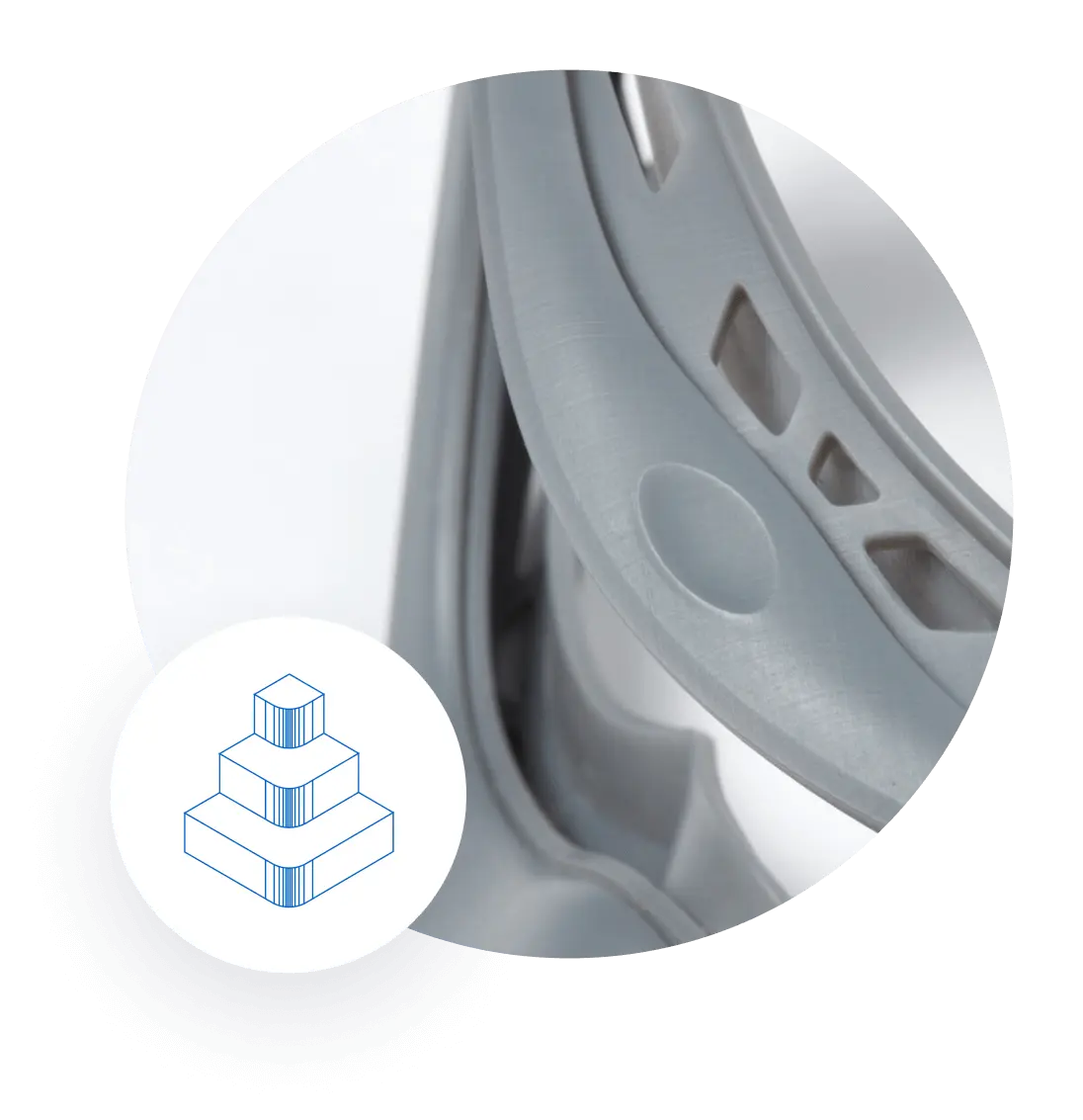
MATERIAL LIBRARY
40+ functional resins for a wide range of applications
A wide range of materials for prototyping and production from true silicone to flexible, tough, durable, and rigid varieties. Specialty materials for high-temperature applications, castable patterns, and ESD-safe, flame-retardant, or pure ceramic parts. A wide variety of resins for dental and medical applications, including materials for biocompatible parts.
CHANGING MATERIALS
Easy with a cartridge system
Switch between a wide range of functional materials in seconds with our swappable resin cartridge system.
Build Volume
FORM 4L AND FORM 4BL
35.3 x 19.6 x 35.0 cm
13.9 x 7.7 x 14.0 in
FORM 4 AND FORM 4B
20.0 × 12.5 × 21.0 cm
7.9 × 4.9 × 8.3 in
THROUGHPUT
High
Formlabs SLA 3D printers offer a streamlined and blazing-fast means of producing functional, high-quality prototypes and end-use parts. Choose the large-format Form 4L and Form 4BL for producing large-scale parts as well as batches of small parts with minimal printer interaction.
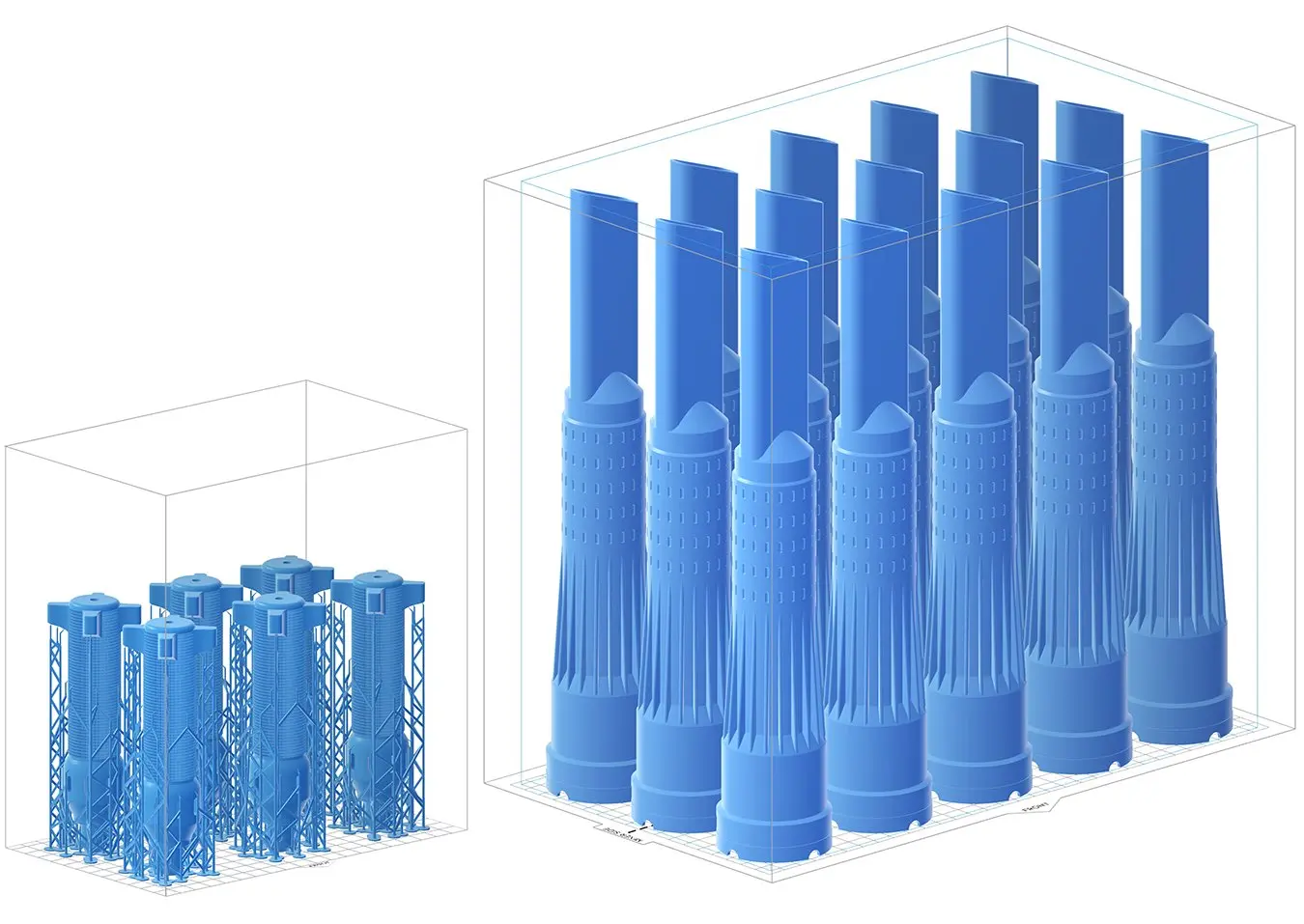
Form 4L and Form 4BL offer 4.6x larger build volumes than Form 4 and Form 4B.
Setup & Ease of Use
Plug and print
Easy workflow empowers anyone at your company to use the system independently after minimal training. Formlabs offers contact-free delivery and online or in-person advanced training for the entire team to make onboarding even easier.
Maintenance
Minimal
Formlabs SLA 3D printers require minimal maintenance. In the rare case when something does go wrong, the optical systems are replaceable in-house to prevent the need for replacement printer shipments and maximize your uptime. Improved failure detection and handling means you can experiment with confidence.
Post-Processing
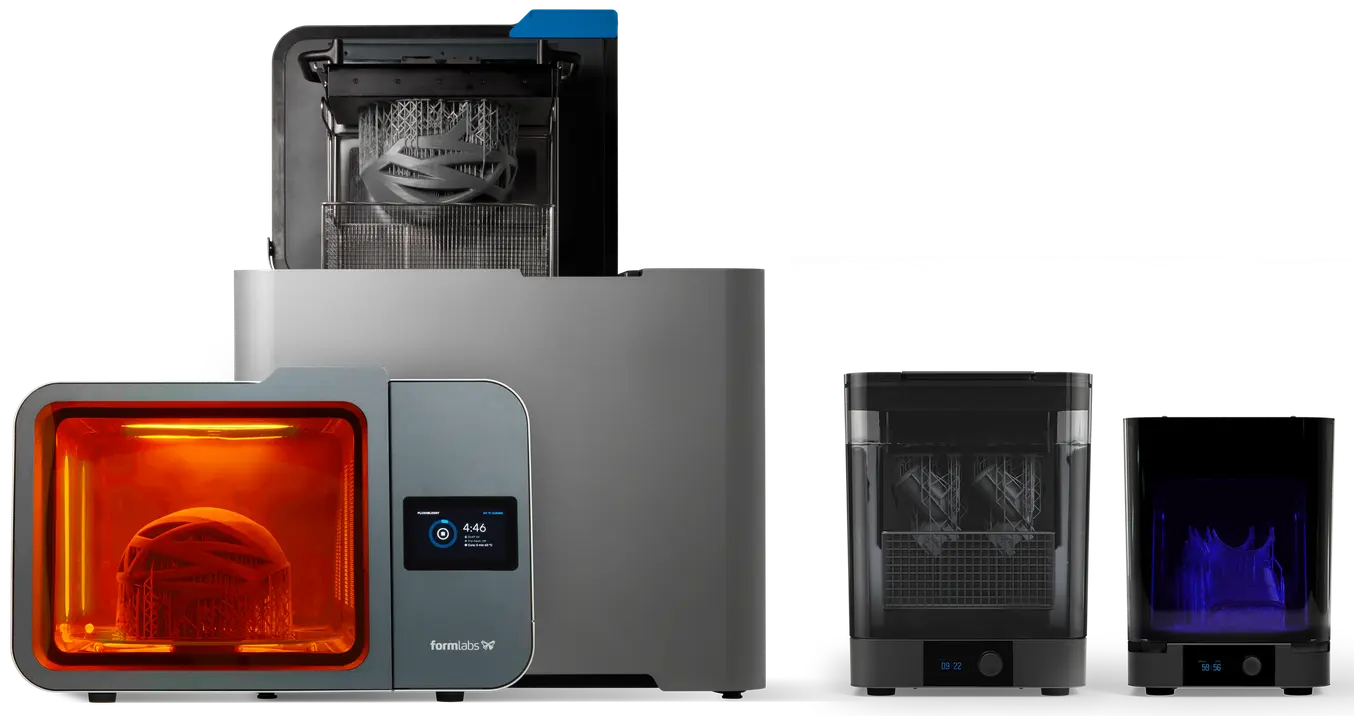
Form Wash and Form Cure, Form Wash L and Form Cure L
Our automated washing and curing solutions streamline the SLA post-processing workflow to consistently deliver high-quality results with less time and effort.
SUPPORTS
Light-touch supports
Our light-touch supports break off with ease, leaving behind minimal support marks that can be easily removed with light sanding.
CLEANING
Wash parts in a solvent
Cleaning printed parts in a wash solvent removes any uncured resin from the part, leaving you with a smooth surface finish. Automate washing with the Form Wash and Form Wash L.
FINISHING
Post-curing (optional)
When an SLA part finishes printing, it remains on the build platform in a “green state.” Through exposure to a combination of light and heat, post-curing unlocks this last mile of material properties. Post-curing is required for certain materials and for biocompatible parts. Automate curing with the Form Cure and Form Cure L.
Space
ENVIRONMENT
Office and workshop
Formlabs SLA 3D printers are suitable for various environments, including the office, lab, workshop and the manufacturing floor. Our most compact SLA printers, the Form 4 and Form 4B, can fit on a desktop.
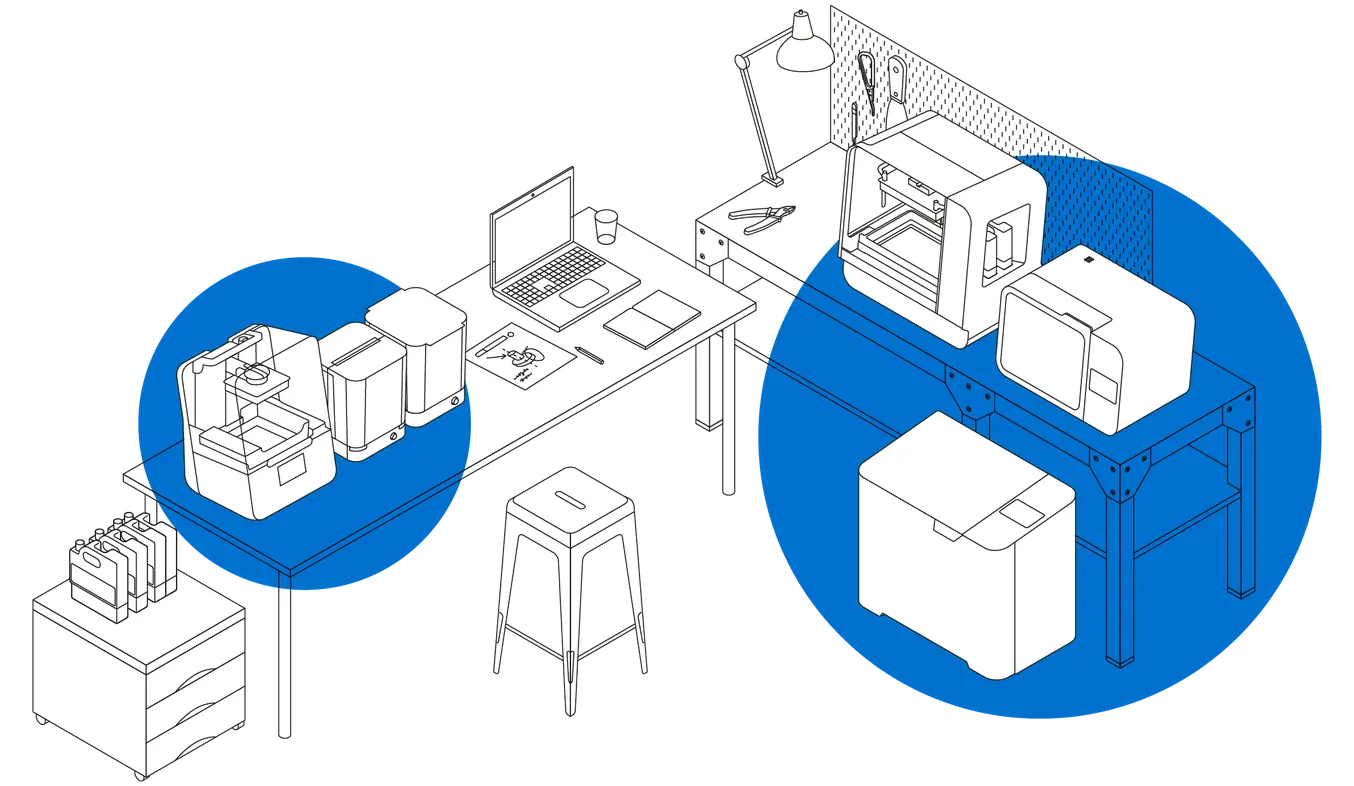
SLS
SLS
Selective Laser Sintering (SLS)
SLS 3D printers use a high-power laser to sinter small particles of polymer powder into a solid structure.
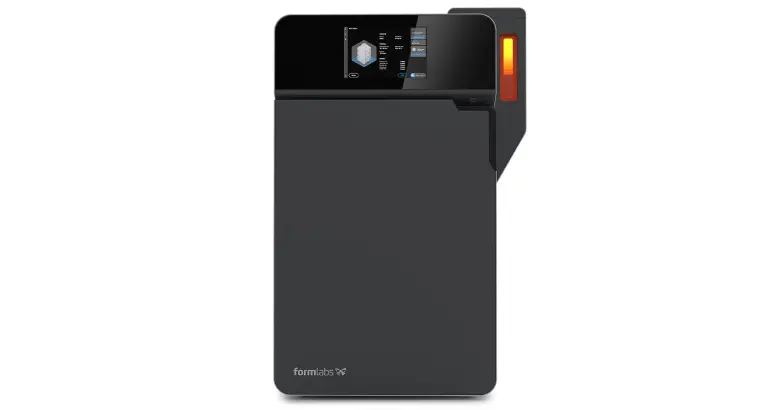
Learn More
Overview
TECHNOLOGY
Selective Laser Sintering (SLS)
Fuse Series is the first benchtop industrial SLS 3D printer ecosystem that offers high quality end-use parts in a compact footprint. The complete, simplified workflow delivers high throughput at a fraction of the cost of traditional industrial SLS systems.
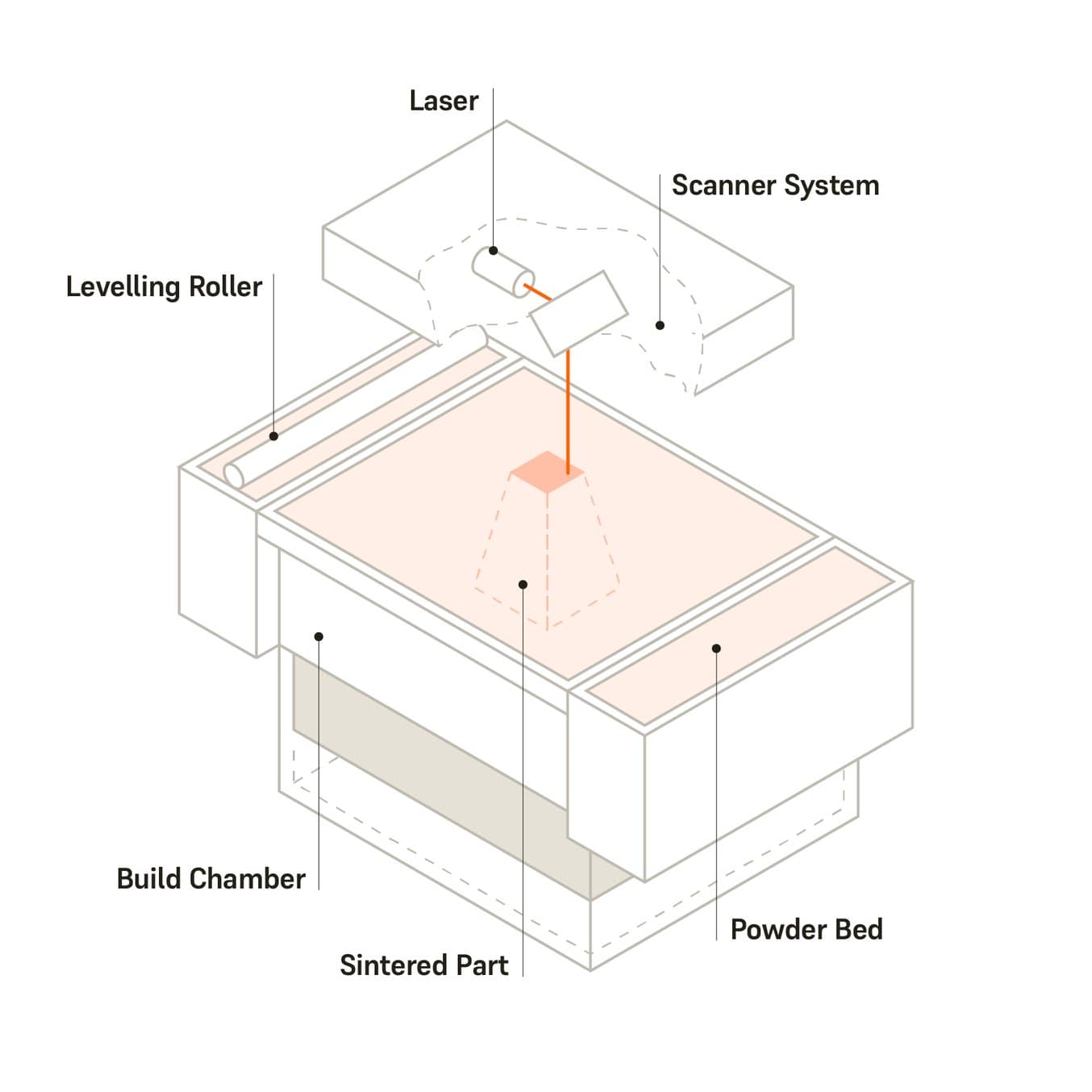
BENEFITS
- End-use parts in under 24 hours
- Excellent mechanical properties
- Great accuracy and print quality
- No need for support structures
- Cost-efficient for series production
APPLICATIONS
- End-use parts
- Low volume, bridge, or custom manufacturing
- Functional prototyping
- Long-lasting, durable manufacturing aids
- Medical devices, prosthetics, and orthotics
Material
SURFACE FINISH
Slightly grainy finish
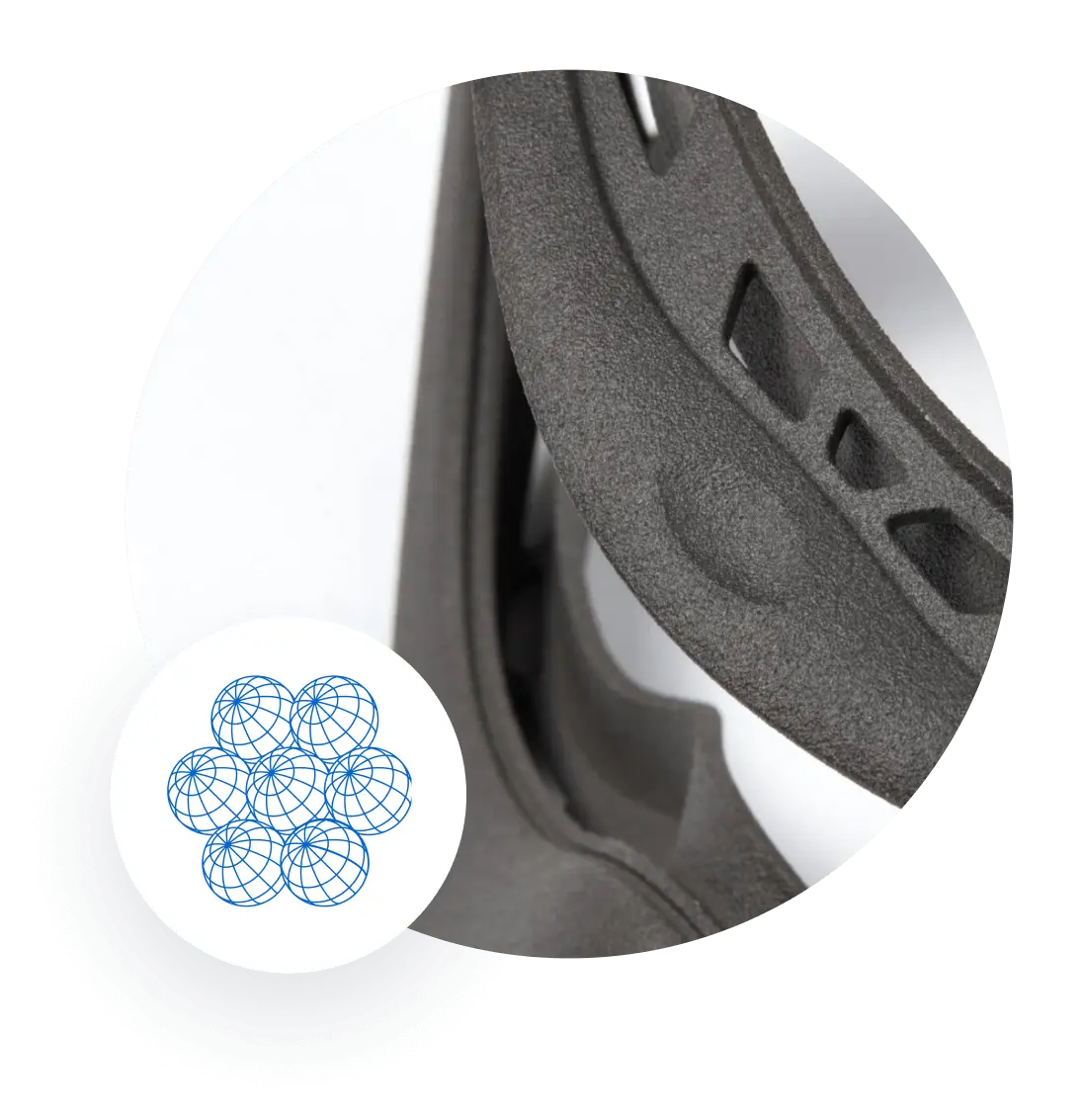
MATERIAL LIBRARY
8 high-performance industrial-grade materials
The Fuse 1+ 30W currently prints with nylon 12, nylon 11, TPU (elastomer), as well as glass and carbon-filled nylon composites. All SLS Powders are ideal for 3D printing long-lasting, durable, end-use parts and functional prototypes.
CHANGING MATERIALS
Manageable
Requires thorough cleaning of the 3D printer and related accessories, but it's possible, and substantially faster and less involved than with traditonal SLS systems.
Maximum Part Size
FUSE 1+ 30W and FUSE 1
16.5 x 16.5 x 30 cm
6.3 x 6.3 x 11.6 in
THROUGHPUT
High
Fuse Series SLS 3D printers are designed for nonstop throughput. They come with a removable build chamber, allowing you to start new prints right after the previous print has finished to minimize downtime. Cooldown time takes only about half the print time for large builds, an industry-leading value that allows you to get to finished parts quickly.
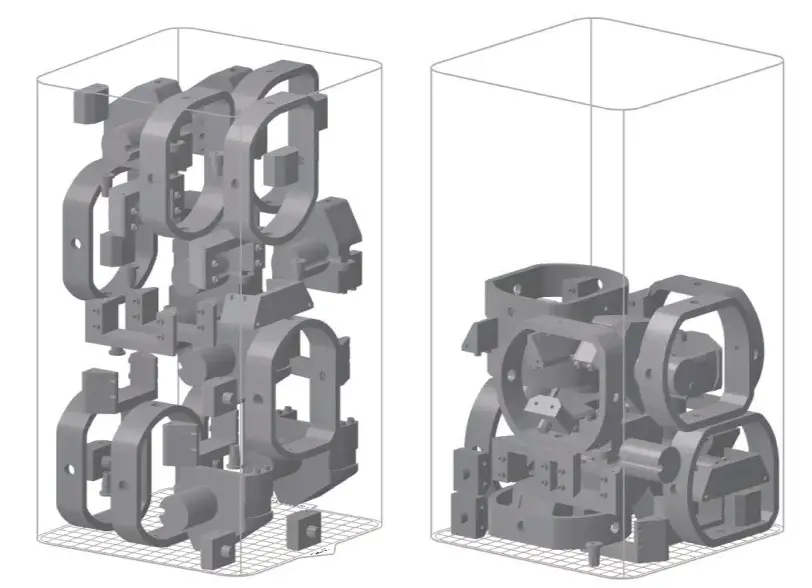
Fuse Series SLS 3D printers allow you to pack parts tightly to optimize each build for the highest productivity.
Setup & Ease of Use
SLS made manageable
From print setup to powder management to finishing, our hardware and software are designed to maximize your efficiency, with an intuitive interface to walk you through all steps of printing and maintenance. Anyone at your company can use the system independently after a quick online or in-person training.
Maintenance
Efficient
The Fuse Series ecosystem is designed for minimal upkeep, offering proactive maintenance alerts and a full-color touchscreen interface that guides you through every step of printing and maintenance.
Post-processing
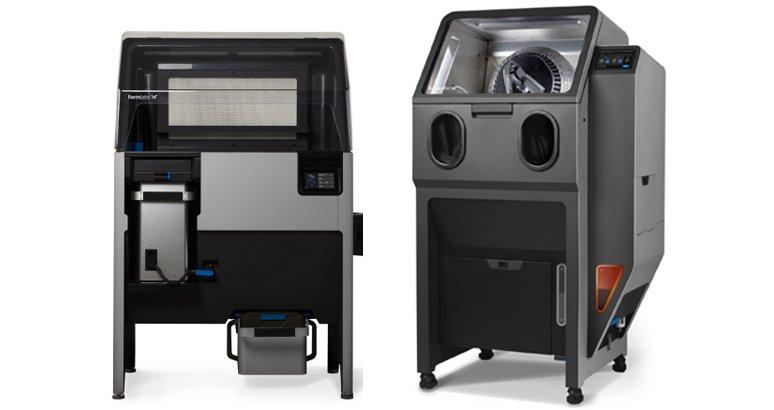
Fuse Sift and Fuse Blast
Our advanced SLS post-processing solutions enable you to go from printed to finished parts in as little as 15 minutes with an efficient, hands-off workflow.
SUPPORTS
No supports needed
SLS parts are supported by powder as they print, so no supports are needed, reducing post-processing labor.
CLEANING
Clean excess powder
Extract and clean your parts from the build chamber and recover unused powder to be recycled in future prints. Use Fuse Sift as an all-in-one station.
FINISHING
Media blasting
Formlabs recommends using media blasting to fully depowder and improve surface finish of SLS parts. Use Fuse Blast for an easy-to-use, fully automated cleaning and polishing solution that consistently delivers professional parts that are clean to the touch.
Space
ENVIRONMENT
Workshop
Fuse Series SLS 3D printers are best suited for a workshop or machine shop setting, though it can be used in an office environment if you have a large open space with consistent housekeeping practices.
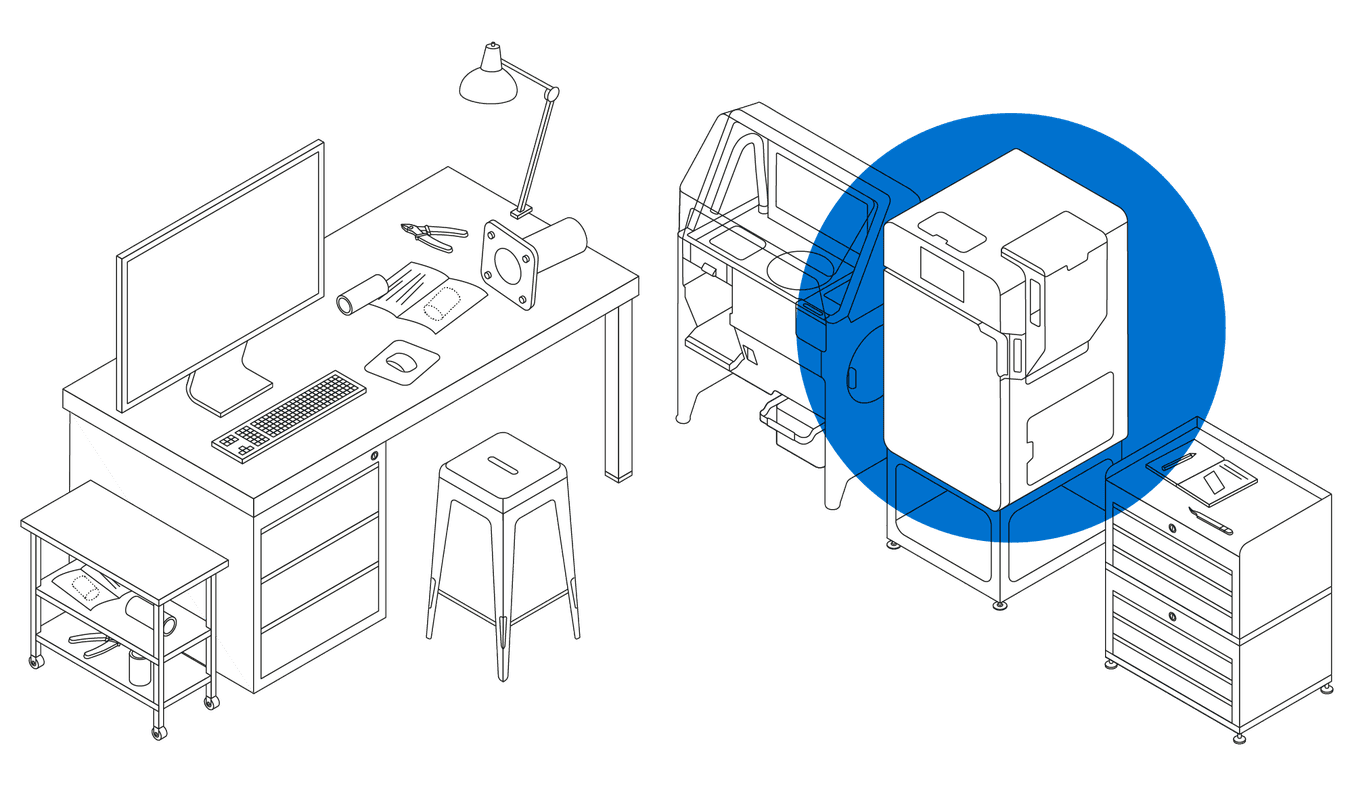
Compare Formlabs 3D Printer Tech Specs
Technology
Masked Stereolithography (MSLA)
Material Type
Resin
Biocompatible Materials
No (available on Form 4B)
Maximum Part Size
20.0 × 12.5 × 21.0 cm
7.9 × 4.9 × 8.3 in
Layer Thickness
25 – 200 microns
.001 – .008 in
Light Source
Backlight Unit (60 LEDs)
Supports
Auto-generated
Light-touch removal
Materials
23 industry-leading Formlabs materials or third-party materials using Open Material Mode. More exciting new materials are currently in development.
Printing Environment
Ambient conditions. Only PU Resins require a dry cabinet for humidity control.
Printer Dimensions (W × D × H)
39.8 × 36.7 × 55.4 cm
15.7 × 14.5 × 21.9 in
Technology
Masked Stereolithography (MSLA)
Material Type
Resin
Biocompatible Materials
No (available on Form 4BL)
Maximum Part Size
35.3 x 19.6 x 35.0 cm
13.9 x 7.7 x 14.0 in
Layer Thickness
25 – 200 microns
.001 – .008 in
Light Source
Backlight Unit (145 LEDs)
Supports
Auto-generated
Light-touch removal
Materials
19 industry-leading Formlabs materials or third-party materials using Open Material Mode. More exciting new materials are currently in development.
Printing Environment
Ambient conditions. Only PU Resins require a dry cabinet for humidity control.
Printer Dimensions (W × D × H)
66.4 x 52.8 x 79.4 cm
26.1 x 20.8 x 31.3 in
Technology
Selective Laser Sintering (SLS)
Material Type
Powder
Biocompatible Materials
Yes
Maximum Part Size
15.9 × 15.9 × 29.5 cm (Nylon 12 Powder)
6.3 × 6.3 × 11.6 in (Nylon 12 Powder)
Layer Thickness
110 microns
0.004 in
Laser Power
One 30W Ytterbium fiber laser
Supports
No supports required
Materials
8 high-performance industrial-grade materials, including nylon 11, nylon 12, TPU, and glass and carbon-filled nylon composites, or third-party materials using Open Material Mode. More exciting new materials are currently in development.
Printing Environment
Air environment, with the option to print in a nitrogen atmosphere for enhanced material properties and lower refresh rates.
Printer Dimensions (W × D × H)
64.5 × 68.5 × 107 cm (165.5 cm with stand)
25.4 × 27 × 42 in (65.0 in with stand)