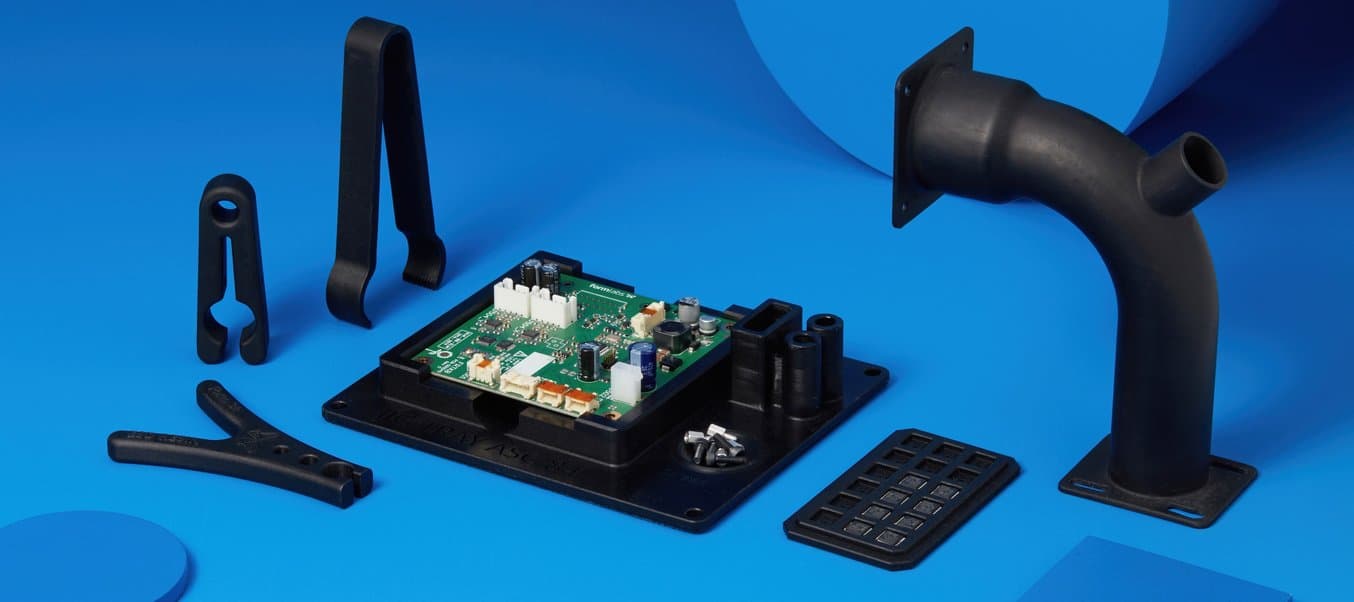
Formlabs is pleased to announce the release of ESD Resin, a material designed for manufacturers to reduce risk and increase yield on their electronics manufacturing lines. ESD Resin is a cost-effective solution for producing static-dissipative parts designed for use on the factory floor.
Read on to learn how ESD Resin works, and how the indoor air quality company HAVEN uses ESD Resin to scale manufacturing and prevent laser failures through the use of ESD safe jigs and fixtures.
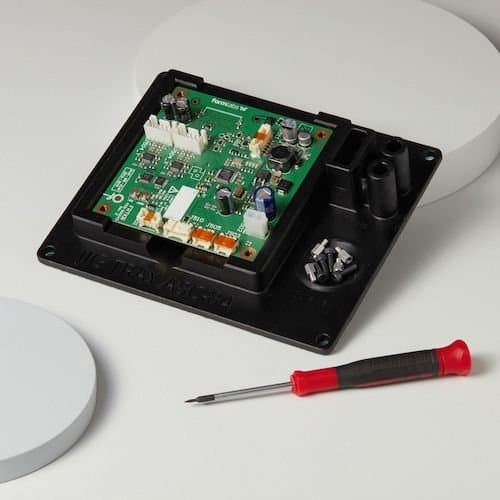
How 3D Printing with ESD Resin Streamlines Electronics Manufacturing
Hear from HAVEN Indoor Air Quality lead engineer Phil Tsao of how they used ESD Resin to reduce the cost and lead time of ESD-safe production fixtures by up to 90%.
What is Electrostatic Discharge?
Electrostatic discharge (ESD) occurs when there is a sudden flow of electricity between two charged objects. Static electricity accumulates when there is friction between multiple insulating components. When one of these components comes in contact with a conductor, the electricity discharges into the conductor. This is particularly dangerous in the electronics industry, where ESD-sensitive parts such as circuit boards can be damaged from unregulated static discharge. Something as small as the friction created by a jig touching an enclosure can cause a buildup of electrons and result in an electrostatic discharge, shorting out electrical components and leading to a nonfunctional product. Lack of control over processes involving ESD sensitive parts can decrease overall production yield.
What are ESD Materials?
ESD materials dissipate static electricity in order to protect components that may be sensitive to static shock, like electronics. ESD materials are not true “conductors”, but electrons are able to flow across their surfaces to dissipate static shocks if they occur.
When grounded, ESD materials give electric charge a place to go, allowing the electrons to flow harmlessly across their surface and into a grounded point. An added benefit is that ESD materials are anti-static when grounded, meaning that small particles like dust, powder, and styrofoam won’t stick to them. In many electronics manufacturing facilities, these particles cause buildup and eventual failure to delicate electrical and mechanical systems. ESD materials for tooling and assembly procedures minimize the risk of failures both in cases of electric charge overload and static buildup. Manufacturers have traditionally relied on machined metals for these materials, but there are now solutions in 3D printing.
ESD Resin for 3D Printing Parts in Electronics Manufacturing
3D printing is a less expensive and faster alternative to machining in many applications, but there have previously been few options to 3D print high-quality ESD materials. They are either part of a high-priced system out of the reach of many small- to medium-sized manufacturers, or they are printed on lower quality machines, and unreliable in industrial environments.
Formlabs professional printers with ESD Resin now offer a solution that is vital for specific applications and workflows across a broad range of industries. Many manufactured products have electronics components, and thus need ESD-safe materials for handling them.
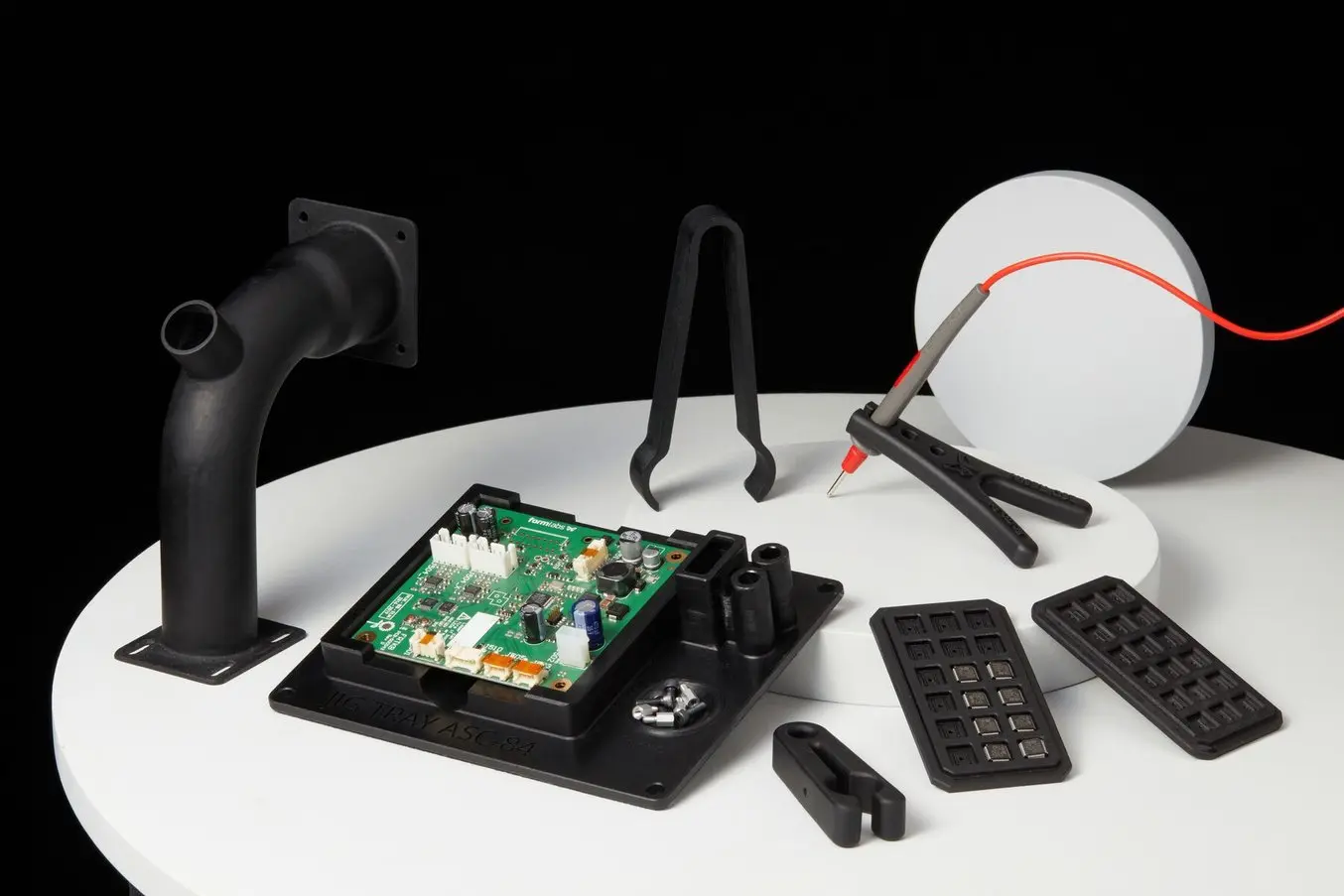
When prototyping manufacturing parts, testing and validation require all components to function together, and electronic components need to operate smoothly. Machining is expensive to outsource, coming with long lead times, which prohibits manufacturers from getting their products out of the prototyping stage. Because the toughness of ESD Resin is higher than that of many other 3D printed ESD-safe materials, engineers can prototype without risk of mechanical or electrical failure.
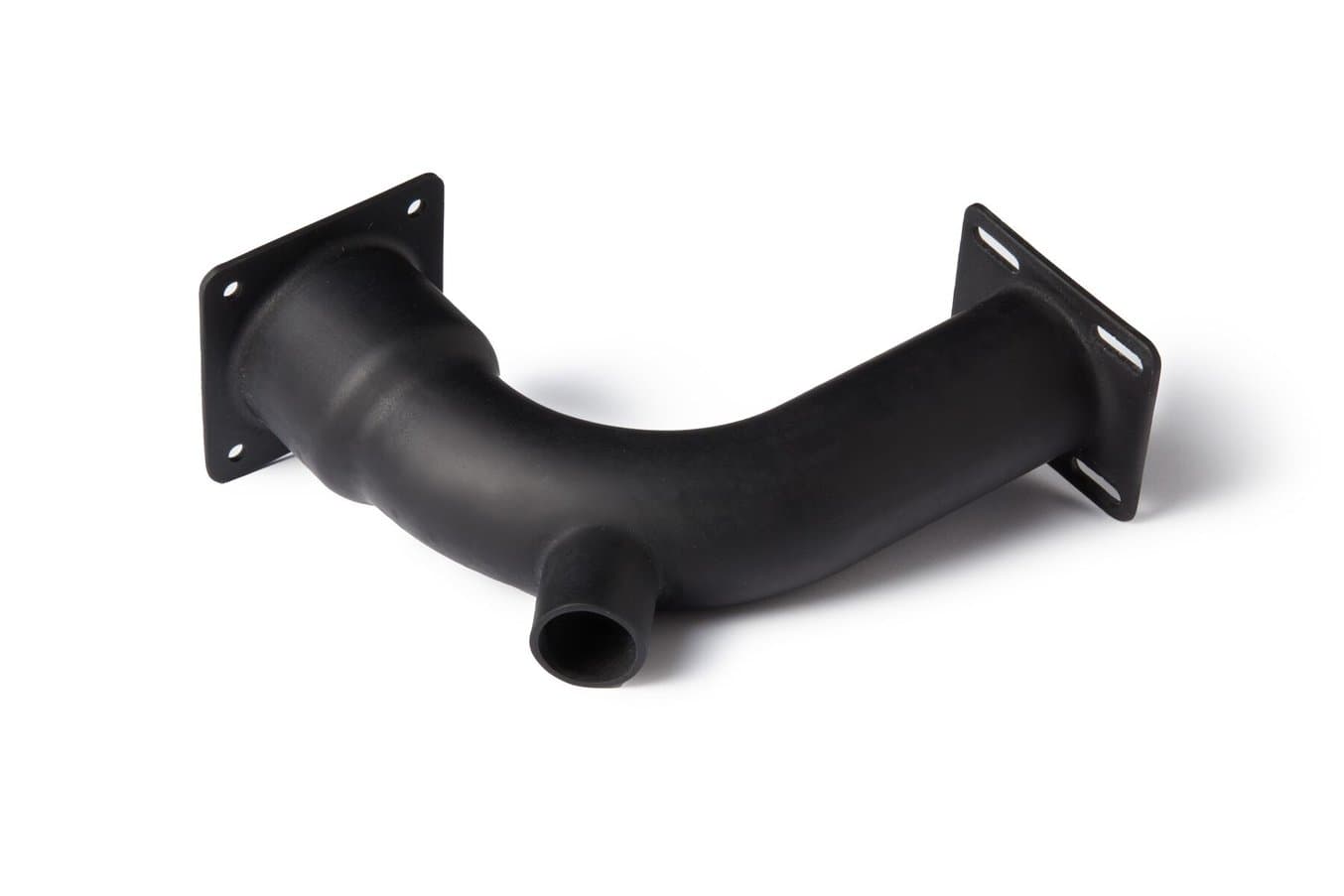
A prototype powder-handling tube within the Fuse Sift, printed in ESD Resin. Its anti-static nature allows powder to flow freely instead of clinging inside the tube.
On a production line involving electrical components, ESD-safe materials are necessary at all contact points, so jigs and fixtures have typically been machined out of metals, which are conductors by nature. Now, manufacturers can print jigs and fixtures in ESD Resin to safely divert static electricity away from sensitive electrical parts. The high modulus and toughness of ESD Resin make it ideal for production environments where strength and durability are critical.
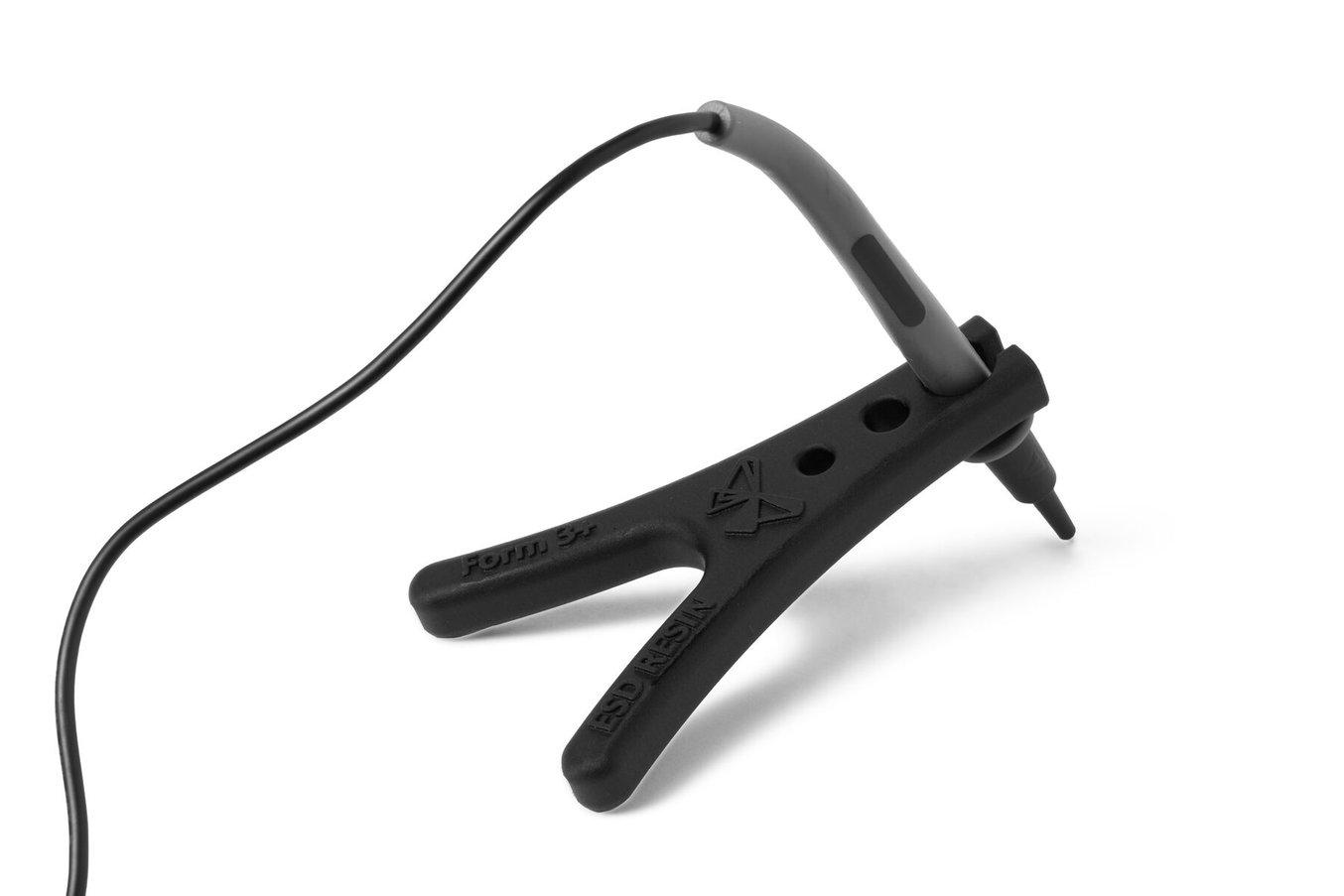
The ESD Resin sample part is a fixture to support a multimeter probe during use, reducing the likelihood of static charge buildup while allowing engineers to take readings hands-free.
After assembly, electrical components need to be safely enclosed and held during different stages of the process, or before leaving the factory floor. Holding trays are large and often have customized geometries, making them expensive to machine. With ESD Resin, holding trays and enclosures can be quickly manufactured to custom fit the product specifications and safely hold the products without static from the room or contact from handlers shorting out the part.

This component tray made from ESD Resin holds integrated circuit boards for safe storage and transportation in a manufacturing facility.
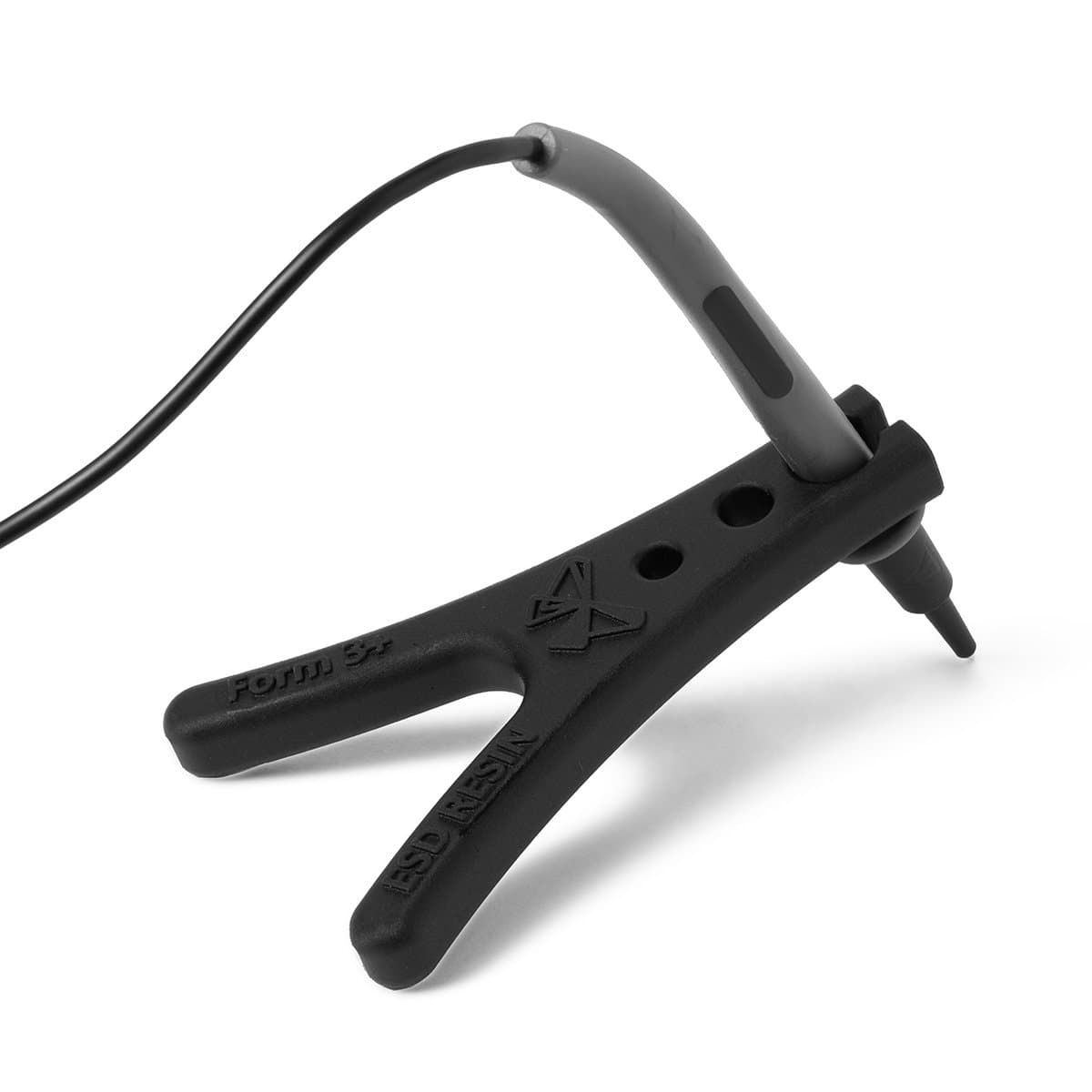
Request a Free Sample
Want to test ESD Resin for yourself? Request our free, ESD-safe, 3D printed multimeter probe holder for your electrical workbench. Test its surface resistivity to validate ESD-safety.
How Electronics Manufacturer HAVEN Reduced the Cost and Lead Time of ESD Safe Parts by up to 90%
With Formlabs’ new ESD Resin, manufacturers of all sizes can increase the operational efficiency of their electronics manufacturing lines with a cost-effective solution to create custom ESD-safe production tooling.
Vancouver based indoor air quality company HAVEN immediately recognized the benefits of having an ESD material available on the same high quality and affordable SLA printers they already relied on for prototyping and design.
“Everyone recognizes the utility of 3D printing in product design and rapid prototyping. We’re starting to see the value of it in manufacturing—building the line that builds the product.”
- Vlad Lavrovsky, HAVEN CTO
HAVEN creates a line of indoor air quality products. The HAVEN product line is composed of an air quality monitor and an air controller that provides a full, closed-loop solution for indoor air quality. Using Form 3 and Form 3L printers, HAVEN engineers have been prototyping HAVEN components for years, but had to outsource metal machining for ESD tooling components.
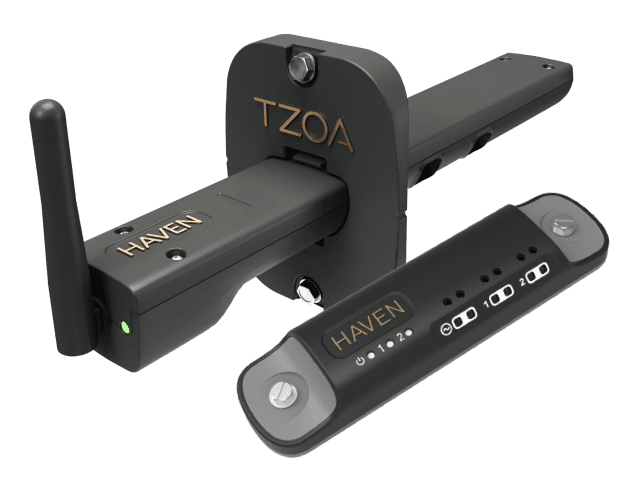
“Because of the ESD requirements, historically we used the printers to prototype first, then CNC machine. When we didn’t have ESD constraints we would print directly and get parts in two days instead of two weeks,” said HAVEN lead engineer Phil Tsao.
ESD hygiene is particularly important for HAVEN’s production line—even a small amount of electrostatic discharge could fry their integral laser component. HAVEN learned this the hard way several years ago when a significant amount of early devices had latent or premature failures.The team eventually traced the cause of the failure back to their soldering station, where a few volts of electrostatic discharge were damaging the laser. Since then, ESD protocol has been at the forefront of their operations.
“It was an all-hands, tools down, find the root-cause situation. It really forced us to have a higher standard of care forever. It forced eternal vigilance when it comes to anything ESD-related,” said Lavrovsky.
Using ESD Resin allows HAVEN to utilize the speed of in-house 3D printing without sacrificing ESD compliance. When given a chance to beta test ESD Resin, HAVEN saw the business case for switching their outsourced metal machining workflow to an in-house 3D-printable solution.
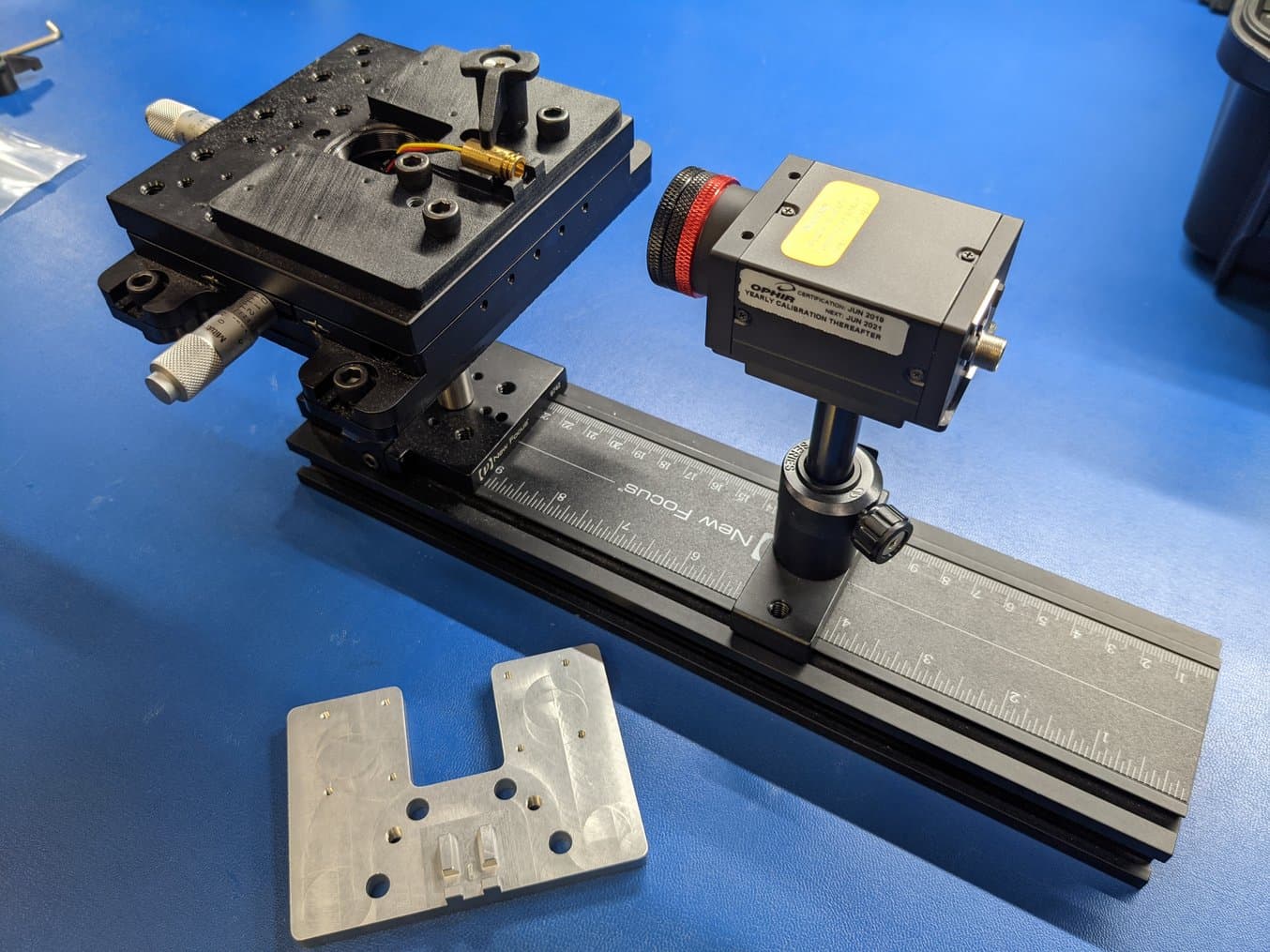
“There were definitely solutions to dealing with ESD in the past, but they were slow and expensive. One of our small aluminum parts is around $500. We printed it in ESD Resin and had it the next day for a 10th of the cost, or less,” said Tsao.
Process | Cost | Lead Time |
---|---|---|
Aluminum Machining | $500 | Two Weeks |
ESD Resin | $40-$50 | One Day |
Being able to prototype, test, and manufacture in one workflow using a single material allows HAVEN’s process to be more agile, which is important to them as a hardware startup. That agility also represents scaling opportunities. Lavrovsky plans to scale production now that he can use both the original production line with legacy aluminum fixturing, but also add a new line with 3D printed ESD Resin fixturing.
“Our objective is to make our manufacturing workflow perfect. We want there to be minimal uncertainty… You take all possible measures. ESD Resin gives us the chance to reduce risk further,” said Lavrovsky.
Get Started With ESD Resin Now
ESD Resin is available now in our store and from resellers, for use on the Form 3/3B, Form 3+/3B+, and Form 3L/3BL. Do you have questions about the new material? Contact our sales team to evaluate ESD Resin for your application.
Want to test ESD Resin for yourself? Request our free, ESD-safe, 3D printed multimeter probe holder for your electrical workbench. Test it's surface resistivity to validate its ESD-safety.