Draft Resin is fantastic. It will print large parts at the height of the platform in less than 3 hours. It is a game changer for prototyping, testing and reaching the final design.
Luiz Maracaja
Draft Resin is the latest addition to our resin library, with print times three to four times faster than other Standard Resins. Since we launched this new material in the spring of 2019, our users wasted little time incorporating it into their product design processes. Our goal with Draft Resin was to create a material accurate enough to meet prototyping needs while enabling faster design iterations, and that’s exactly how customers like Lance Winkel, Albatross Bikes, and TACK Architects incorporated the material into their workflows.
Read on to learn how these three users are creating with Draft Resin, plus how Formlabs has used the material internally.
Printing Same-Day Architectural Models at TACK Architects
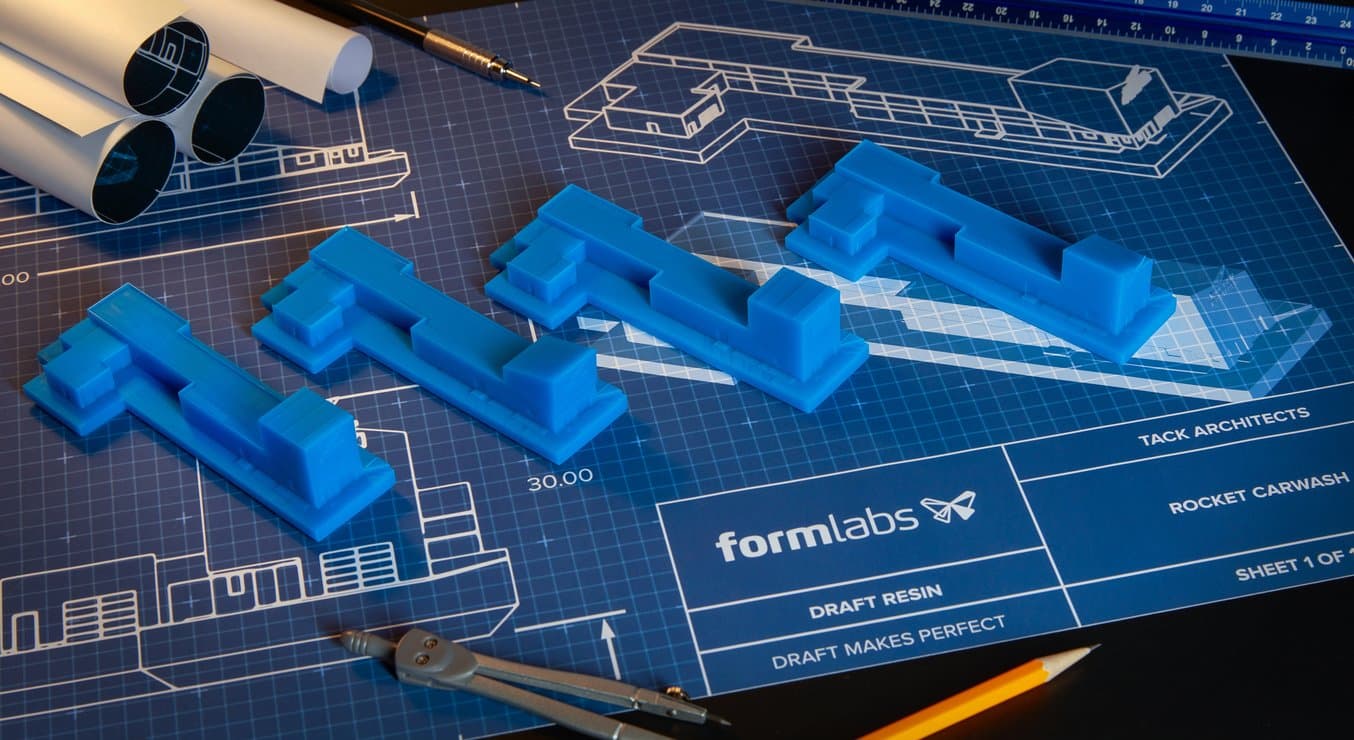
Ryan Hier and the TACK Architects team has been incorporating Formlabs printers into their workflow for a few years. The team has historically 3D printed their final models on a Formlabs printer, using materials such as Standard Resins to visualize their high-quality architectural models. These prints take approximately ten hours for most models, meaning they could be finished overnight. While overnight printing is significantly quicker than outsourcing 3D models, it still limited the team to around one print per day.
Draft Resin turns this process on its head. Those same ten-hour models now print in only two, meaning multiple variants of a project can be created in one work day. This allows the team to use additional physical models to explore a wider range of designs. Now, from the start of any project, Ryan Hier builds his architectural models knowing that he will be able to quickly print and hold them. This has changed how he creates in CAD, smoothing the transition into PreForm.
“Not only is the print time reduced, but we can print directly on the build plate without loss of quality, significantly reducing post-processing time. The printer has become a double-threat: we can print final quality models as well as quick-and-dirty study models.”
Now the team uses both Draft Resin and Standard Resins on the same machine, turning their desktop 3D printer into a dual purpose tool for both prototypes and final prints.
“There is no right or wrong way to integrate 3D printing into your design process. Find someone in your team who is passionate about 3D printing and can look for ways to test the limits of the printer, calibrating the machine to your workflow.”
Lance Winkel: Incorporating Draft Resin in and Outside the Classroom
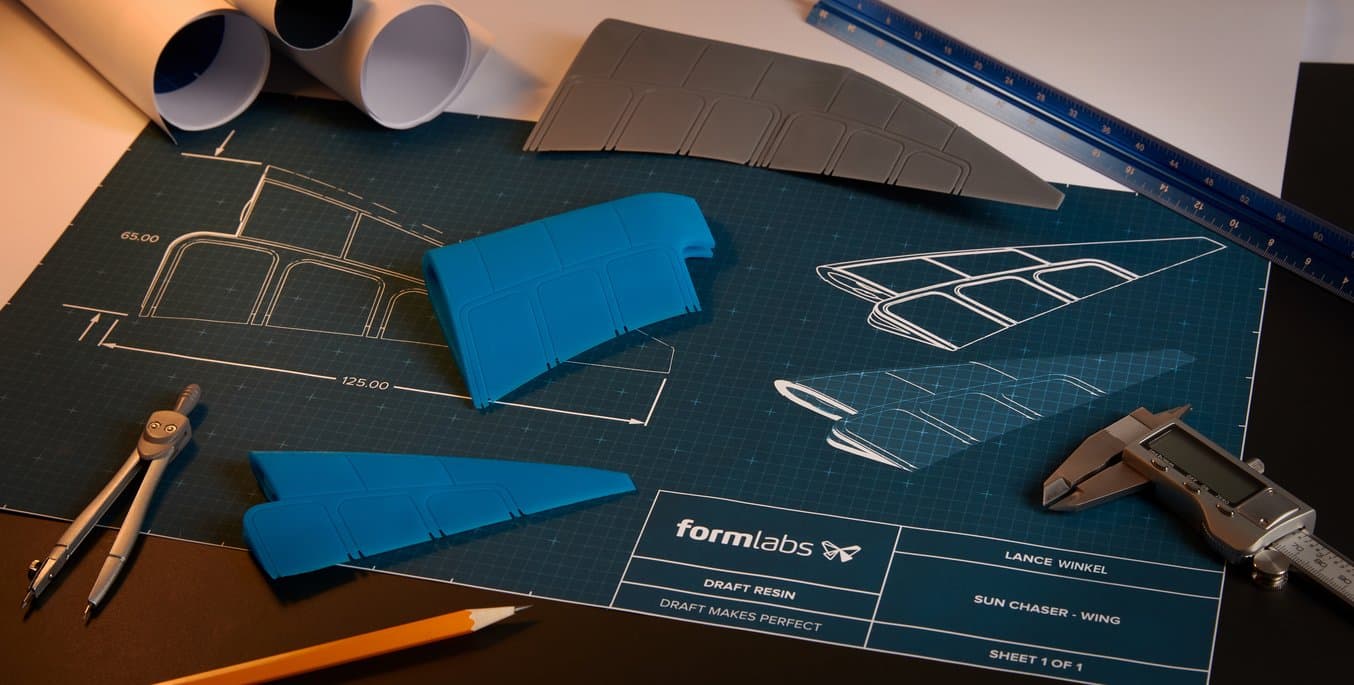
One thing users love about Draft Resin is how easily it integrates into PreForm. Lance Winkel, an award-winning animated filmmaker and senior lecturer at the USC Viterbi School of Engineering, was surprised when he realized that no additional setup was required in PreForm when switching between standard resins and Draft Resin. This means less hassle when going from final prototype to finished part; it’s as easy as swapping the resin cartridge and clicking print.
“Because of the unique Formlabs printer and PreForm ecosystem, there is no reprocessing necessary to up a model from Draft Resin to Grey Pro or other standard resins. Same exact layout, same exact orientation, and all one has to do is change resin types in PreForm, recalculate the supports optimized for the new resin, and resubmit the job.”
Using this new super-fast material has led Lance to intense ideation about future projects, including how to incorporate Draft Resin into projects from the get-go. One possible idea is printing the internal structures and supports of large projects in Draft Resin, cutting out approximately twelve hours of printing from the final development time.
“As an artist, I am also beginning to see a future where Draft Resin can replace my internal structural modeling on large scale projects, while still printing thin outside shells in high resolution resins for detail. The combination of this process is allowing me to substantially increase the size of my 3D printed sculptures and may allow me to potentially double the size of my finished pieces at roughly the same total print time.”
Lance does more than create and design in his spare time. He has taught 3D computer graphics animation for over a decade at many prominent universities across southern California, bringing 3D printing into the classroom. Time is of the essence when using traditional resins, because students are often unable to print projects during the school day and have to wait overnight for prints to finish instead. With Draft Resin, Lance has seen project print times reduced to three hours. This allows students to start a print in the morning and have it done by lunch.
“Draft Resin can often be as much as four times faster to complete a stage. The same Form 2 printer using Standard Grey Resin completed a recent print in 12 hours. The same exact stage layout, but with only some slight print support adjustments to accommodate Draft Resin, finished in just under 3 hours! It means that four times as many projects or iterations can be completed by the same printer in the same amount of time. That is transformational!”
The benefit for Lance and other users isn’t just the time saved on the prints, but the superior end-use parts that come from additional rounds of iteration.
Using Draft Resin Internally at Formlabs
Before attending the Additive Manufacturing Users Group (AMUG) conference, the Formlabs events marketing team wanted to create unique swag in the form of custom 3D printed pens. Time was short, so the team decided to see if Draft Resin was up to the task.
The goal of the project was to show the power of 3D printing for end-use parts; all the pens given away at AMUG would be produced on a Formlabs printer. The benefits of Draft Resin were clear: a single pen could be printed in 50 minutes, compared with six hours for the same STL file in Black Resin. This speed allowed the team to print multiple designs in a single day before selecting the best ones. Multiple iterations led to subtle changes in designs to improve comfort. Similar to what Lance Winkel observed in the classroom, the speed of Draft Resin actually expands what is possible in any given project, creating better final prints.
Once the designs were set, the team switched to Grey Pro and Color Kit. Each build platform could fit 81 pens, printing in 20-24 hours. The pens were ready for AMUG, and the team is now exploring other ways to print in-house swag with Draft Resin.
Albatross Bikes: Printing Bike Components in Hours
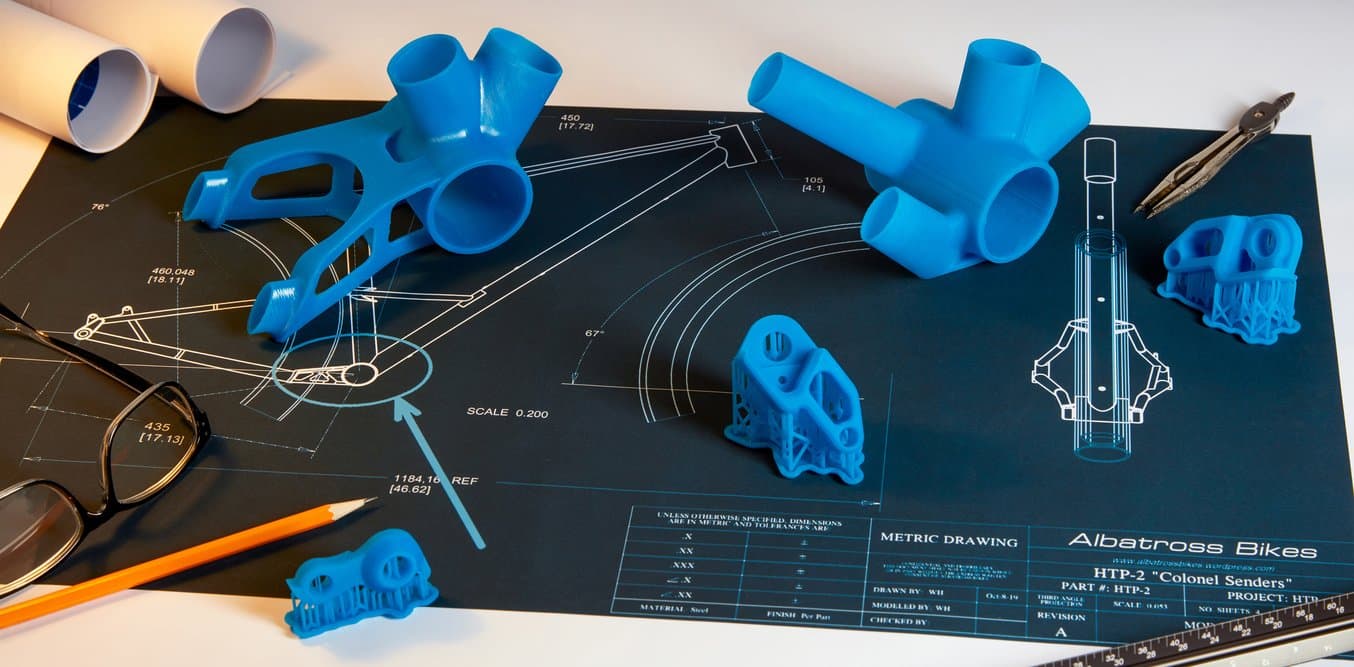
We recommend looking at 3D printing not as a substitute for traditional subtractive methods, but to rethink the entire design and production process to leverage quick part turnaround, ease of use, and flexibility of additive production methods.
Will Hilgenberg
Will has been using 3D printing to bring his CAD bike component to life, iterating on designs to get perfect fit and tolerances. Will started by using in-house 3D printing on Formlabs printers to quickly create engineering samples, with prints taking most of the day to finish. Draft Resin has pushed completion times down even further, with prints taking only a few hours. Now, Will can create and iterate on a design multiple times in a single day. This leads to more experimentation and better performing, unique bike components for his customers. Once the final design has been selected, Will simply switches out the resin cartridge and tray, and completes a final print in either Black Resin or Durable Resin depending on his needs. For some parts, he is able to incorporate the 3D print directly from the printer into the final bike.
Quickly and cheaply iterating on designs allows for ideas to be tested in the physical world before committing to expensive tooling and production samples. In fact, the ability to iterate with Draft Resin has reduced Will’s total tooling time.
We Want to Hear From You
This is a small sample of how Draft Resin is currently being used, and we look forward to sharing more in the coming months. If you have any exciting use cases of Draft Resin, let us know on social media by tagging @Formlabs in your posts!
Never Used Draft Resin?
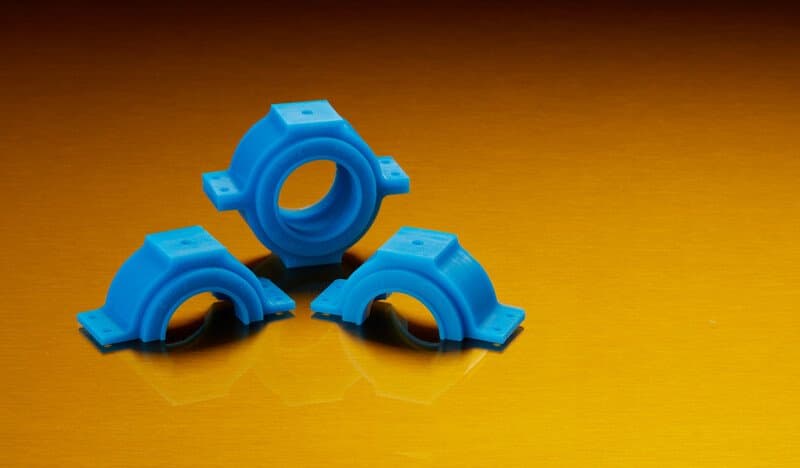
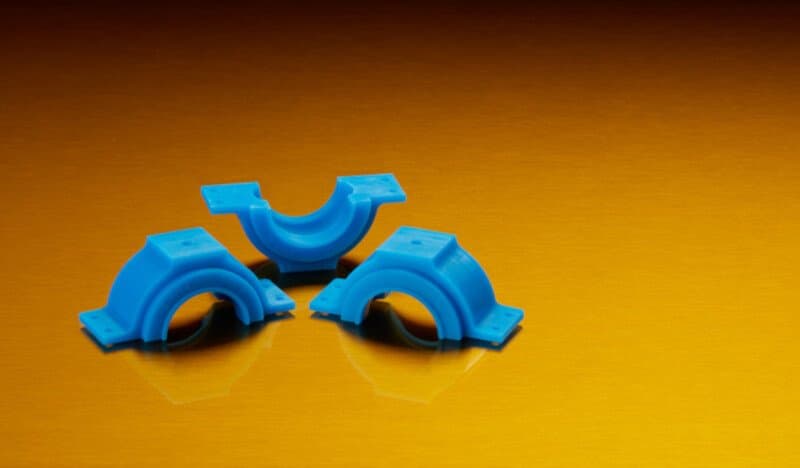