3D-Drucktechnologien haben sich in den letzten Jahren rasant weiterentwickelt – sowohl in Bezug auf Hardware, Software als auch Materialien. Dadurch haben sich 3D-Drucker von Neuheiten für Technikfans zu integralen Bestandteilen von Design-, Konstruktions- und Fertigungsabläufen in allen Branchen etabliert.
Schmelzschichtung (FDM), Stereolithografie (SLA) und selektives Lasersintern (SLS) sind die drei beliebtesten Arten von 3D-Druckern auf dem Markt. Dank des rasanten Innovationstempos im vergangenen Jahrzehnt haben heute mehr Unternehmen Zugang zu diesen drei 3D-Drucktechnologien. Die Wahl zwischen den verschiedenen konkurrierenden 3D-Drucklösungen kann jedoch schwierig sein.
In diesem umfassenden Einkaufsführer werfen wir einen genaueren Blick auf FDM-, SLA- und SLS-3D-Drucker (auch bekannt als Filament-, Resin- und Pulverdrucker) und vergleichen sie in Sachen Druckqualität, Materialien, Anwendungen, Arbeitsprozess, Geschwindigkeit, Kosten und mehr, damit Sie fundiert entscheiden können, welches Verfahren sich für Ihr Unternehmen am besten eignet.

So wählen Sie die richtige 3D-Drucktechnologie
Brauchen Sie Hilfe bei der Wahl der richtigen 3D-Drucktechnologie, zugeschnitten auf Ihre Bedürfnisse? In diesem Videoleitfaden vergleichen wir die FDM-, SLA- und SLS-Technologien in Bezug auf häufige Kaufkriterien.
Was ist FDM-3D-Druck?
Schmelzschichtung oder Fused Deposition Modeling (FDM), auch bekannt als Fused Filament Fabrication (FFF) oder Filament-3D-Druck, ist das am weitesten verbreitete Verfahren des 3D-Drucks auf Verbraucherebene und für den Durchschnittsverbraucher am vertrautesten, da das allgemeine Konzept des 3D-Drucks mit der „Klebepistolen“-Methode in Verbindung gebracht wird.
FDM-3D-Drucker stellen für viele Menschen den Einstieg in den 3D-Druck dar. Sie sind der häufigste Typ von 3D-Druckern an Grund- und weiterführenden Schulen und sogar in vielen Makerspaces an Universitäten. In Design-, Maschinenbau- und Fertigungsbetrieben werden FDM-Drucker vor allem für schnelle Konzeptnachweise zur Abstimmung im Designteam eingesetzt, bevor zum funktionalen Prototyping übergegangen wird.
FDM-3D-Drucker sind in einer Vielzahl von Größen und Preisen erhältlich. Die Einfachheit der Technologie und des Arbeitsablaufs machen den FDM-3D-Druck zu einer attraktiven, unkomplizierten Option für alle, die in den 3D-Druck einsteigen möchten. Allerdings geht die Einfachheit und Erschwinglichkeit dieser Drucker oft auf Kosten von Qualität und Leistung der Druckteile. Für alle, die funktionale Leistung, Wasserdichtigkeit, Isotropie oder glatte Oberflächen benötigen, sind SLA- und SLS-3D-Drucker weitaus bessere Alternativen.
Was ist SLA-3D-Druck?
Die Stereolithografie (SLA-3D-Druck) wurde in den 1980er Jahren erfunden und war damit die erste 3D-Drucktechnologie der Welt. Dennoch hat es länger gedauert, bis sich der SLA-Druck auf so breiter Basis durchsetzte wie der FDM-Druck und an Bekanntheit gewann, da er in der Regel teurer ist und ein etwas komplexeres Druckverfahren erfordert.
Stereolithografie oder Kunstharz-3D-Druck bezeichnet ein Verfahren, bei dem eine Lichtquelle flüssiges Kunstharz bzw. Resin Schicht für Schicht aushärtet. Als Lichtquelle diente ursprünglich ein Laser, der aber in jüngerer Zeit durch digitale Lichtprojektoren in DLP-3D-Druckern oder Leuchtdioden (LEDs) in MSLA- oder LCD-3D-Druckern ersetzt wurde. Im Grunde genommen handelt es sich bei allen heutigen Kunstharz-3D-Druckern um Stereolithografie-3D-Drucker, obwohl der Begriff am häufigsten mit 3D-Druckern in Verbindung gebracht wird, die das Harz mit einem Laser aushärten.
SLA-3D-Drucker produzieren Teile mit glatteren Oberflächen, engeren Toleranzen und höherer Maßgenauigkeit als andere 3D-Drucktechnologien. Diese Drucker eignen sich ideal für funktionales Prototyping, da sie die Optik und die Leistung spritzgegossener Teile genau nachbilden können, aber auch für die Herstellung von Endprodukten und Werkzeugen, aufgrund ihrer hervorragenden Oberflächengüte und extrem vielseitigen Materialeigenschaften.
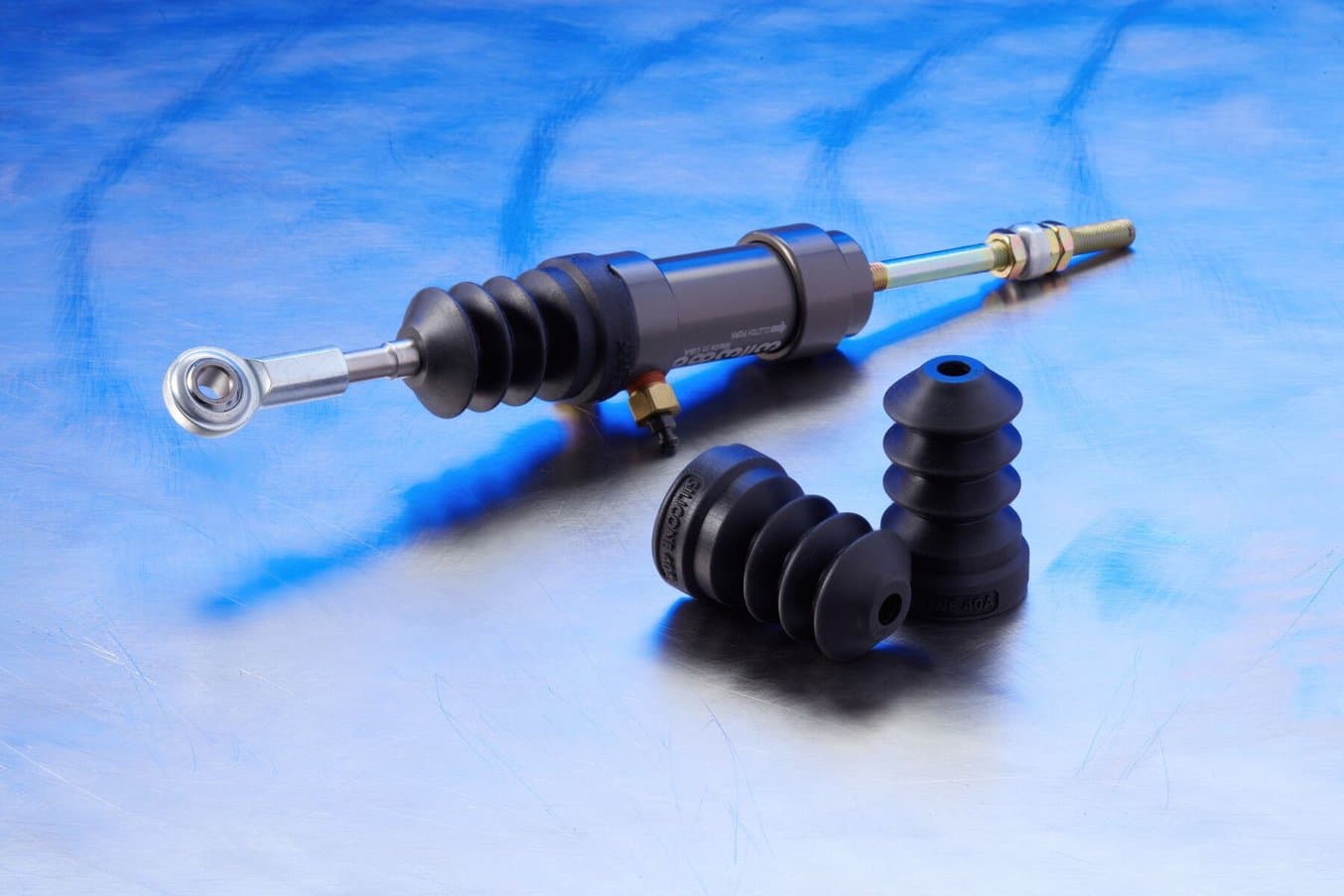
Einer der größten Vorteile der SLA-Technologie ist die Vielfalt der verfügbaren Materialien und der damit möglichen Anwendungen. Dieser Faltenbalg für einen Kupplungszylinder wurde auf Formlabs' MSLA-3D-Drucker Form 4 aus Silicone 40A Resin gedruckt.
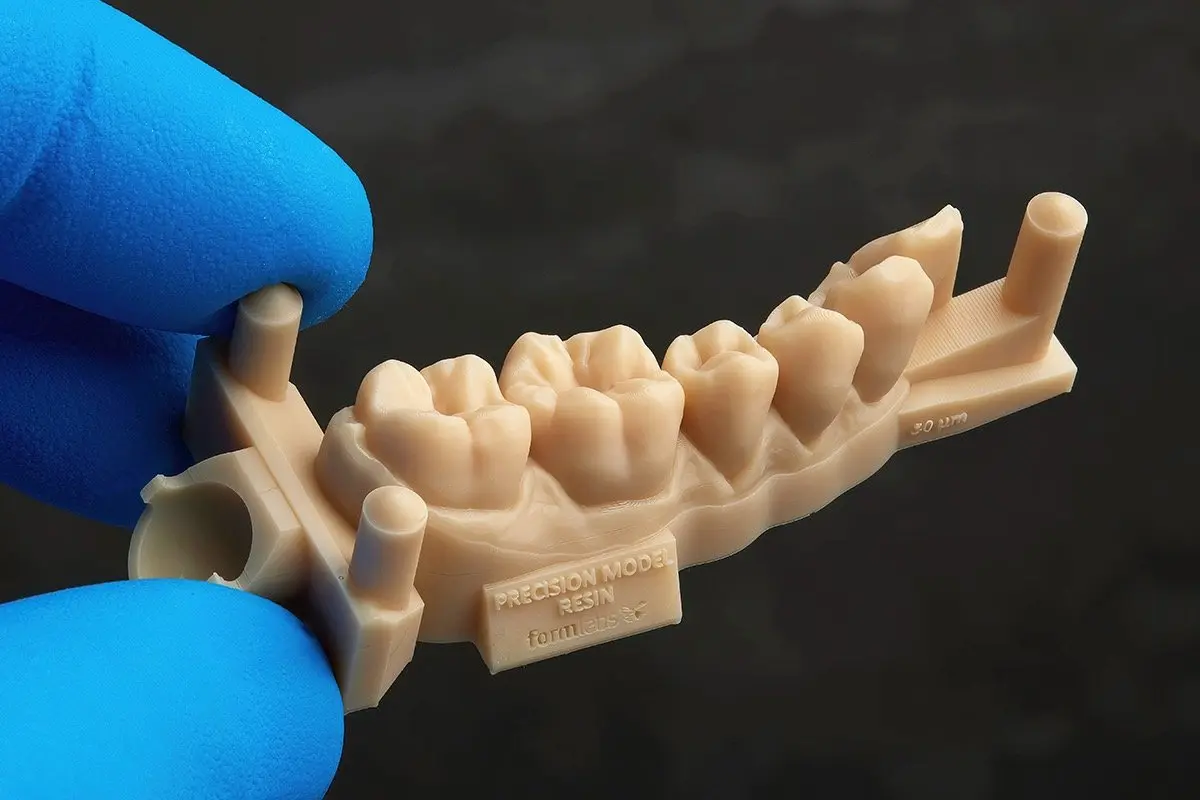
SLA-Teile haben glatte Oberflächen, extrem enge Toleranzen und eine überragende Maßgenauigkeit, was sie zur idealen Technologie für anspruchsvolle Anwendungen wie Zahnersatzmodelle macht.
Im Gegensatz zu den Standardthermoplasten, die im FDM- und SLS-3D-Druck verwendet werden, beruhen SLA-Materialien auf einzigartigen Formulierungen. Einer der Hauptvorteile von SLA liegt in der Materialvielfalt – es gibt innovative Formulierungen von SLA-Photopolymerharzen mit einem breiten Spektrum an optischen, mechanischen und thermischen Eigenschaften, die denen von Standard-, technischen und industriellen Thermoplasten gleichkommen, aber auch Spezialmaterialien, die besondere Eigenschaften wie Flammhemmung, elektrostatische Ableitung oder Biokompatibilität bieten. Diese breite Palette von Eigenschaften, gepaart mit der Genauigkeit und Oberflächenqualität von SLA-Teilen, ermöglicht Anwendungen in sämtlichen Branchen, einschließlich Luft- und Raumfahrt, Automobilbau, Konsumgüterherstellung, Gesundheitswesen, Zahnmedizin und mehr.
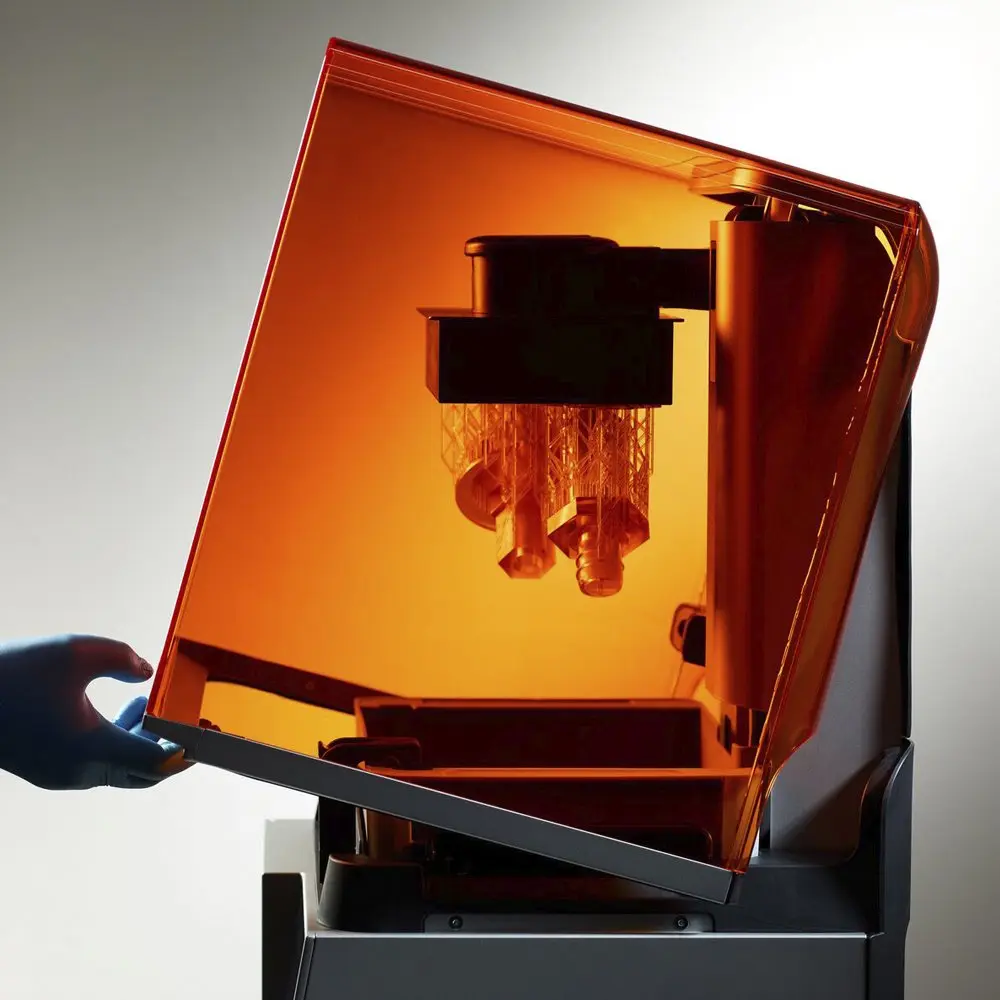
Einführung in den 3D-Druck mit Desktop-Stereolithografie (SLA)
Sie suchen einen 3D-Drucker, um in kurzer Zeit Modelle in hochauflösender Qualität zu erstellen? Lernen Sie in diesem Whitepaper das SLA-Druckverfahren näher kennen – von seiner Funktionsweise bis hin zu den Gründen für seinen Status als populärste 3D-Drucktechnologie bei der Umsetzung von Teilen mit unglaublichem Detailgrad, hoher Maßgenauigkeit und überragender Oberflächenqualität.
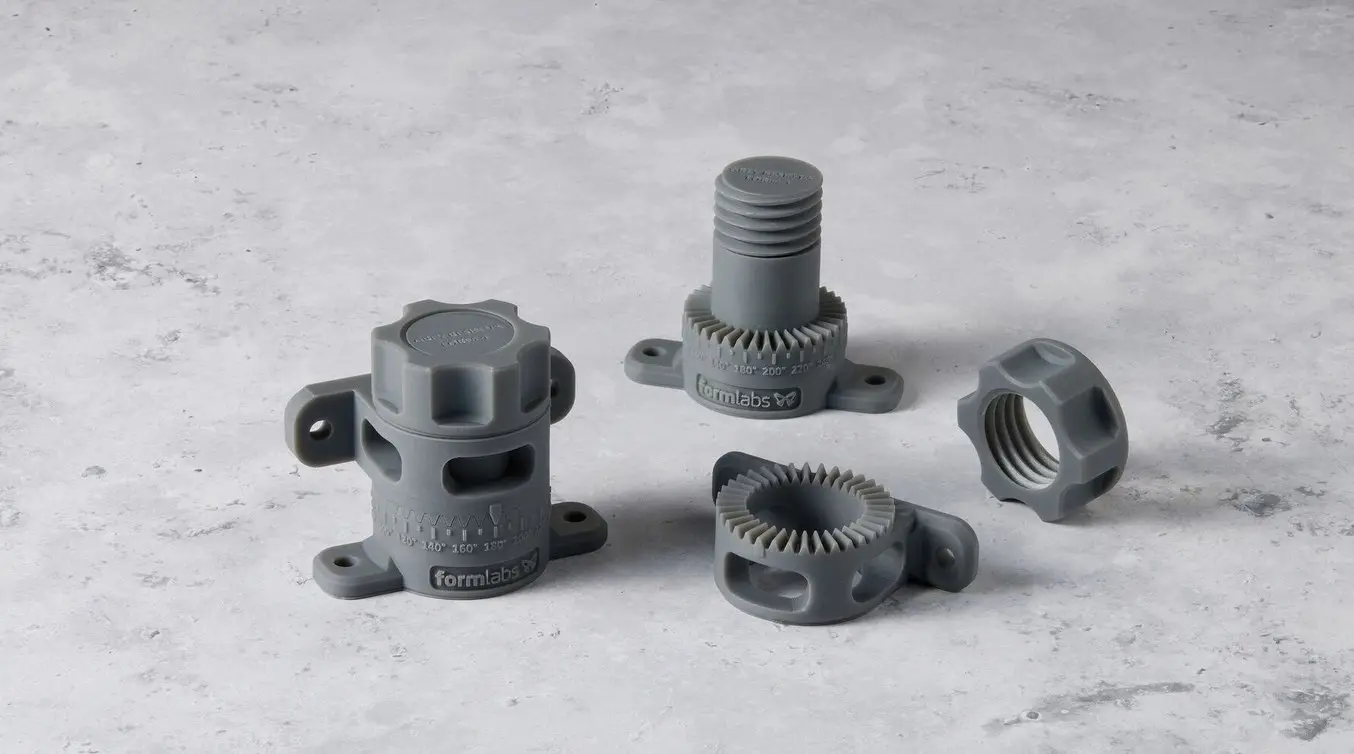
Kostenlosen Probedruck anfordern
Sehen und fühlen Sie die Qualität von Formlabs aus erster Hand. Wir senden Ihnen einen kostenlosen SLA-Probedruck an Ihren Arbeitsplatz.
Was ist SLS-3D-Druck?
Selektives Lasersintern (SLS) ist die am häufigsten genutzte Technologie der additiven Fertigung bei industriellen Anwendungen. Ingenieur*innen und Hersteller verschiedener Branchen vertrauen darauf, um starke und funktionsfähige Teile zu produzieren.
SLS-3D-Drucker verwenden einen Hochleistungslaser, um kleine Partikel aus Polymerpulver zu sintern. Da das ungesinterte Pulver das Teil beim Drucken stützt, sind keine zusätzlichen Stützstrukturen erforderlich. Deshalb eignet sich der SLS-3D-Druck ideal für komplexe Geometrien, einschließlich innerer Merkmale, Hinterschneidungen, dünner Wände und negativer Merkmale. Darüber hinaus ermöglicht er die Herstellung höherer Stückzahlen – im selbststützenden Druckbett können Teile ineinander „verschachtelt“ werden, um die Konstruktionskammer vollständig auszufüllen und auf Produktionsniveau zu fertigen, selbst mit nur einem Drucker.
SLS-Teile bieten herausragende mechanische Eigenschaften, unter anderem eine Festigkeit vergleichbar mit der von Spritzgussteilen. Das gängigste SLS-Material ist Nylon, ein beliebter technischer Thermoplast mit exzellenten mechanischen Eigenschaften. Nylon ist leicht, fest und flexibel und bietet Schlagfestigkeit, Chemikalienbeständigkeit, Hitzebeständigkeit sowie Beständigkeit gegenüber UV-Licht, Wasser und Schmutz. Weitere beliebte Materialien für den SLS-3D-Druck sind Nylon-Verbundstoffe, Polypropylen (PP) und das flexible TPU.
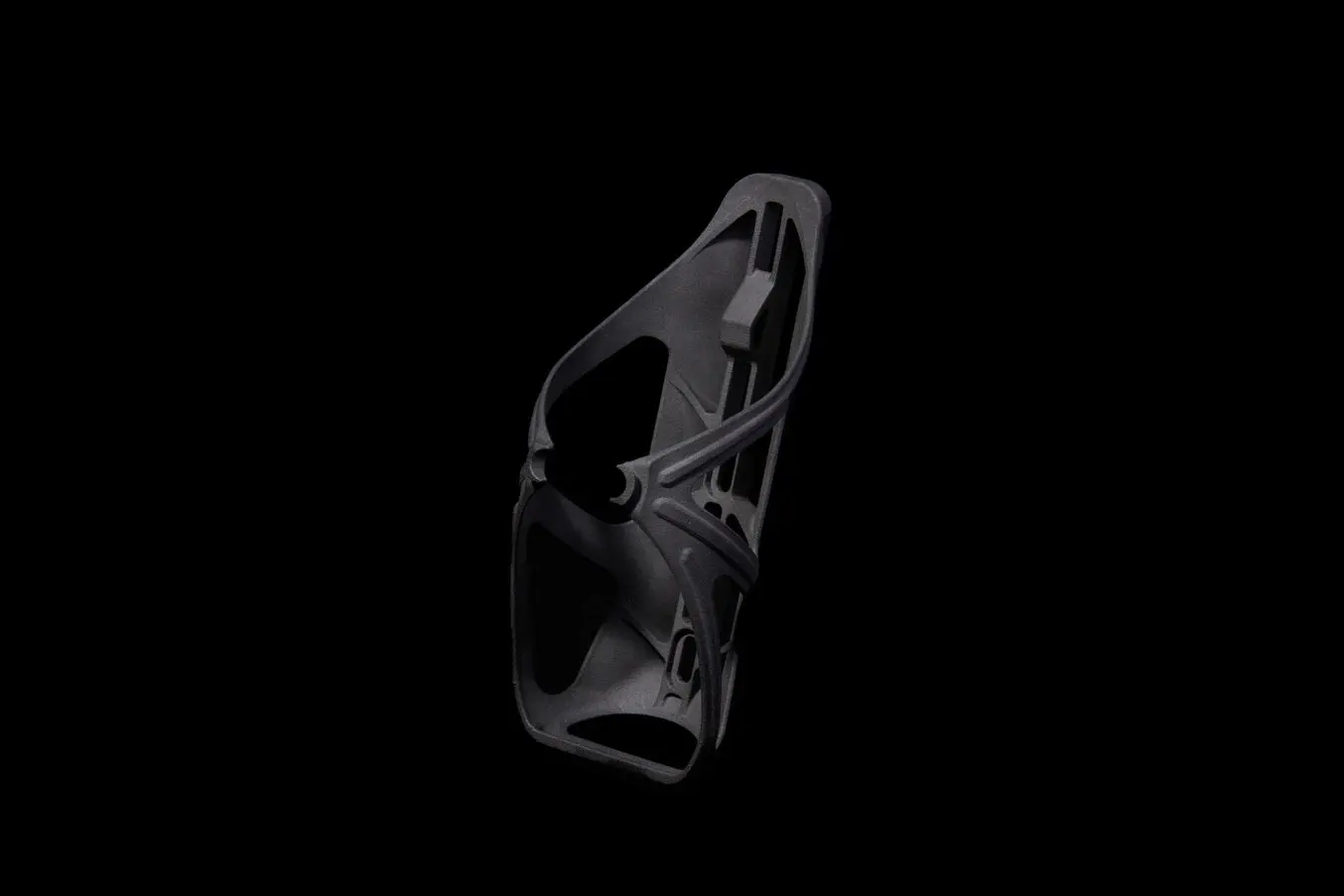
Der SLS-3D-Druck eignet sich ideal für funktionales Prototyping und ist eine kostengünstige Alternative zum Spritzguss für die Kleinserien- oder Übergangsfertigung.
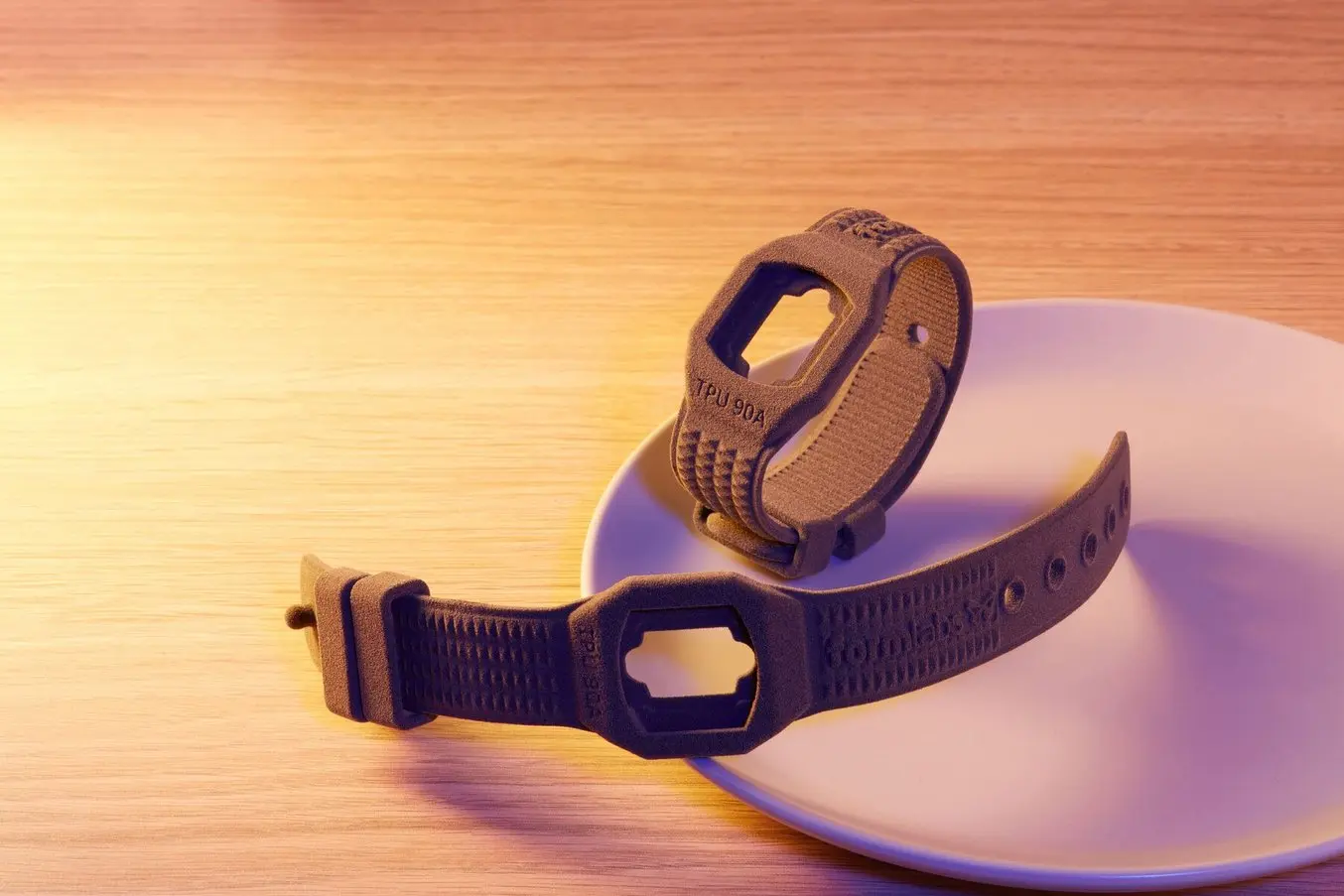
Mit SLS-3D-Druck lassen sich sogar Endprodukte herstellen, auch aus flexiblen Materialien wie dieses Uhrenarmband aus TPU 90A Powder, das auf dem SLS-3D-Drucker Fuse 1+ 30W gedruckt wurde.
Die Kombination aus geringen Kosten pro Teil, hoher Produktivität und bewährten Materialien macht SLS zu einer beliebten Wahl für die Herstellung funktionsfähiger Prototypen. Selektives Lasersintern stellt auch eine kosteneffiziente Alternative zum Spritzguss bei der Kleinserienfertigung und beim Bridge Manufacturing dar. Da der SLS-Arbeitsablauf unkomplizierter und der Einstiegspreis erschwinglicher geworden sind, holen immer mehr Unternehmen SLS-Kapazitäten ins eigene Haus, um ihre Lieferkette zu stärken und die Prozesse vom Prototyping bis zur Produktion zu beschleunigen.
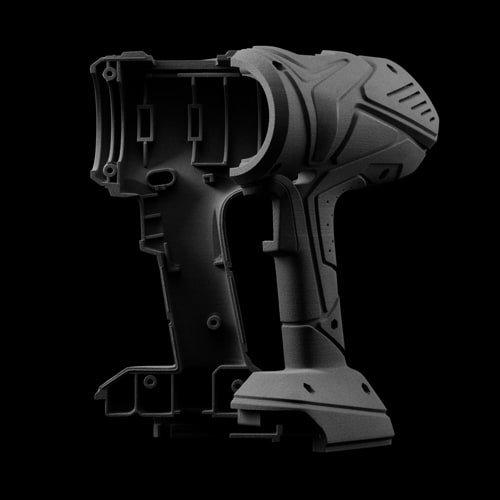
Einführung in den 3D-Druck mit selektivem Lasersintern (SLS)
Suchen Sie nach einem 3D-Drucker, mit dem Sie feste, funktionsfähige Teile herstellen können? Laden Sie unser Whitepaper herunter und erfahren Sie, wie der SLS-Druck funktioniert und wieso er ein beliebtes 3D-Druckverfahren für funktionales Prototyping und die Produktion von Teilen für die Endverwendung ist.
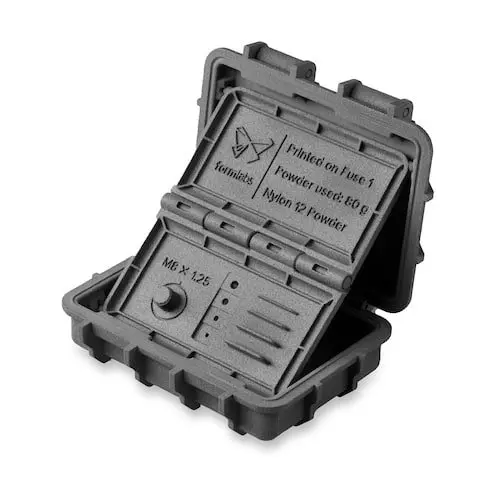
Kostenlosen Probedruck anfordern
Sehen und fühlen Sie selbst die SLS-Qualität von Formlabs. Wir senden Ihnen einen kostenlosen SLS-Probedruck an Ihren Arbeitsplatz.
FDM vs. SLA vs. SLS: Filament-, Kunstharz- und Pulver-3D-Drucker im Vergleich
Die meisten Unternehmen, die in 3D-Druck investiert haben, verwenden mehr als eine Art von 3D-Technologie. Jedes Verfahren hat seine eigenen Vor- und Nachteile. Deshalb erzielt man den optimalen Workflow in der Regel, indem man jede Technologie als ein Werkzeug für bestimmte Szenarien betrachtet.
Unternehmen, die eine Technologie für ihre spezifischen Anforderungen auswählen möchten, sollten dabei mehrere Faktoren berücksichtigen. Im Folgenden fassen wir die wichtigsten Faktoren zusammen, die bei der Wahl zwischen FDM-, SLA- und SLS-3D-Druckern zu beachten sind.
Schmelzschichtung (FDM) | Stereolithografie (SLA) | Selektives Lasersintern (SLS) | |
---|---|---|---|
Auflösung | ★★☆☆☆ | ★★★★★ | ★★★★☆ |
Genauigkeit | ★★★★☆ | ★★★★★ | ★★★★★ |
Oberflächengüte | ★★☆☆☆ | ★★★★★ | ★★★★☆ |
Durchsatz | ★★★☆☆ | ★★★★☆ | ★★★★★ |
Komplexe Designs | ★★★☆☆ | ★★★★☆ | ★★★★★ |
Benutzerfreundlichkeit | ★★★★★ | ★★★★★ | ★★★★☆ |
Vorteile | Kostengünstige Geräte und Materialien für Verbraucher Schnelle und einfache Option für einfache, kleine Teile | Großartiges Preis-Leistungs-Verhältnis Hohe Genauigkeit Hohe Oberflächengüte Schnelle Druckgeschwindigkeit Verschiedene funktionale Anwendungen | Starke funktionsfähige Teile Gestaltungsfreiheit Keine Stützstrukturen erforderlich |
Nachteile | Geringe Genauigkeit Grobe Details Eingeschränkte Gestaltungsfreiheit | Einige Materialien sind empfindlich gegenüber langer UV-Lichteinwirkung | Leicht raue Oberfläche Eingeschränkte Materialoptionen |
Anwendungen | Konzeptmodellierung Rapid Prototyping Funktionales Prototyping Fertigungshilfsmittel | Konzeptmodellierung Rapid Prototyping Funktionales Prototyping Rapid Tooling Fertigungshilfsmittel Kleinserien-, Übergangs- oder kundenspezifische Fertigung Dentalmodelle und -anwendungen Medizinische Modelle und Medizinprodukte Schmuckprototyping und -guss Modelle und Requisiten | Rapid Prototyping Funktionales Prototyping Kleinserien-, Übergangs- oder kundenspezifische Fertigung Langlebige, robuste Fertigungshilfsmittel Medizinprodukte, Prothetik und Orthetik |
Fertigungsvolumen | Bis zu 300 × 300 × 600 mm (Desktop- und Benchtop-3D-Drucker) | Bis zu 353 × 196 × 350 mm (Desktop- und Benchtop-3D-Drucker) | Bis zu 165 × 165 × 300 mm (industrielle Benchtop-3D-Drucker) |
Materialien | Standardthermoplaste wie ABS, PLA und deren Mischungen. | Verschiedene Kunstharze (Duroplaste). Allzweckkunstharze, technische Kunstharze (ABS-ähnlich, PP-ähnlich, flexibel, wärmebeständig, glasgefüllt und starr), Gusskunstharze, biokompatible Kunstharze (zahnmedizinische und medizinische Anwendungen). Pures Silikon und Keramik. | Technische Thermoplaste. Nylon 12, Nylon 11, glas- oder carbonfaserverstärkte Nylon-Verbundstoffe, Polypropylen, TPU (Elastomer). |
Schulung | Geringer Schulungsaufwand zur Einrichtung von Druckteilen, Bedienung und Fertigstellung, mittlerer Schulungsaufwand zur Wartung. | Plug-and-Play. Geringer Schulungsaufwand zur Einrichtung von Druckteilen, Wartung, Bedienung und Nachbearbeitung. | Mittlerer Schulungsaufwand zur Einrichtung von Druckteilen, Wartung, Bedienung und Nachbearbeitung. |
Anforderungen an die Räumlichkeiten | Klimatisierte Umgebung oder vorzugsweise individuelle Belüftung bei Desktop-Geräten. | Desktop- und Benchtop-Drucker eignen sich für den Einsatz in Büroräumen. | Werkstattumgebung mit mäßigen Platzanforderungen für Benchtop-Systeme. |
Zubehör | System zur Entfernung von Stützstrukturen bei Maschinen mit löslichen Stützstrukturen (optional automatisiert), Fertigstellungswerkzeuge. | Waschstation und Nachhärtestation (beide optional automatisiert), Fertigstellungswerkzeuge. | Nachbearbeitungsstationen für Pulvermanagement und Teilereinigung. |
Anschaffungskosten | Preiswerte FDM-Drucker und 3D-Drucker-Kits beginnen bei ca. 200 €. Professionelle Desktop-FDM-Drucker liegen zwischen 2000 € und 8000 € und industrielle Systeme sind ab 15 000 € erhältlich. | Kostengünstige Kunstharz-3D-Drucker sind für 200 € bis 1000 € erhältlich, professionelle SLA-3D-Drucker liegen im Bereich von 2500 € bis 10 000 € und großformatige Kunstharz-3D-Drucker im Bereich von 5000 € bis 25 000 €. | Industrielle SLS-3D-Drucker im Benchtop-Format beginnen bei unter 30 000 € für den Drucker und 60 000 € für das komplette Ecosystem, einschließlich Pulververwaltungs- und Reinigungsstationen. Konventionelle industrielle SLS-Drucker beginnen bei etwa 200 000 €. |
Materialkosten | 50–150 €/kg für die meisten Standard-Filamente und 100–200 €/kg für Stützmaterial oder technische Filamente. | 100–200 €/l für die meisten Standard- und technischen Kunstharze, 200–500 €/l für biokompatible Materialien. | 100 €/kg für Nylon. SLS erfordert keine Stützstrukturen. Ungesintertes Pulver kann wiederverwendet werden, wodurch die Materialkosten sinken. |
Arbeitsaufwand | Manuelles Entfernen der Stützstrukturen (für industrielle Systeme mit löslichen Stützstrukturen größtenteils automatisierbar). Für eine hochwertige Oberfläche ist umfangreiches Nachbearbeiten erforderlich. | Waschen und Nachhärten (beides größtenteils automatisierbar). Einfache Nachbearbeitung zum Entfernen von Stützspuren. | Einfacher, halbautomatischer Arbeitsablauf zur Reinigung von Teilen und Rückgewinnung von Pulver. |
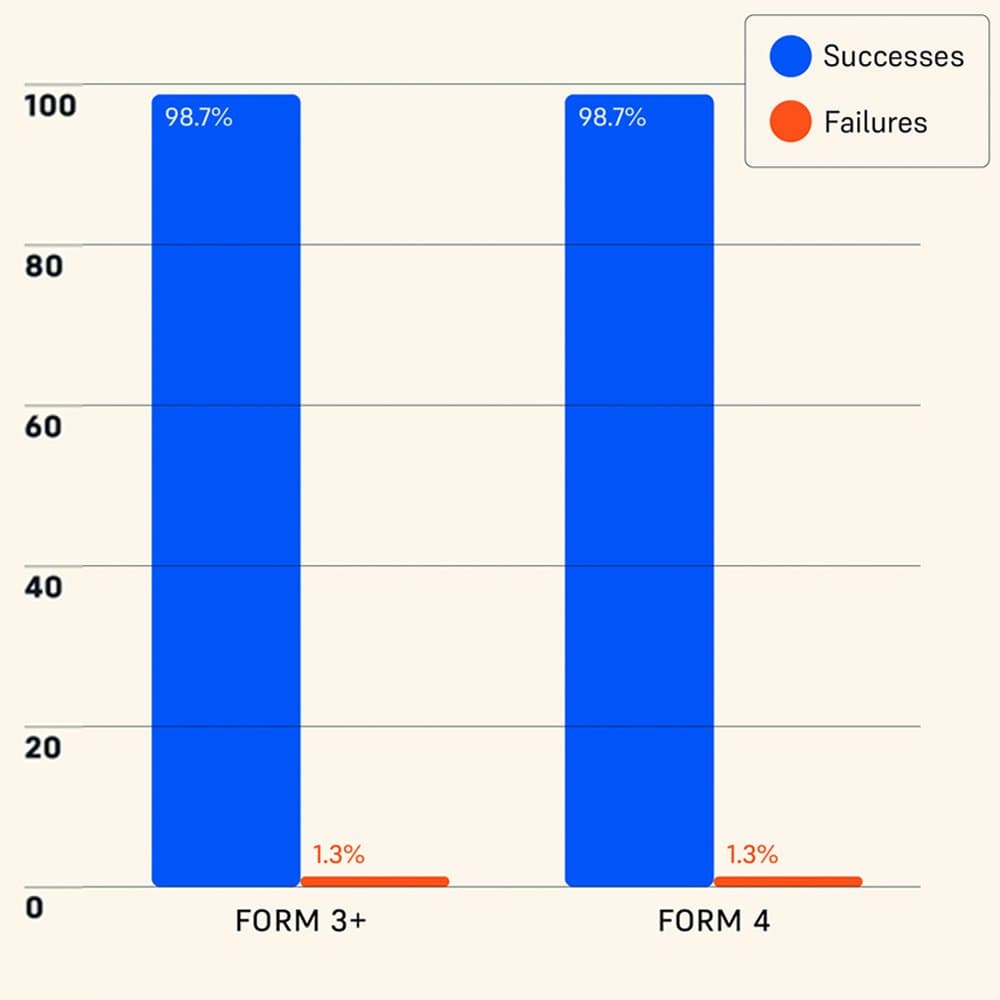
Zuverlässigkeit von Form 4 und anderen Kunstharz-3D-Druckern unabhängig getestet
Der Form 4 von Formlabs erreichte in einer Untersuchung eines unabhängigen, weltweit führenden Produkttesters eine Druckerfolgsrate von 98,7 %. Eine vollständige Beschreibung der Testmethode und die Ergebnisse finden Sie in unserem Whitepaper.
Auflösung
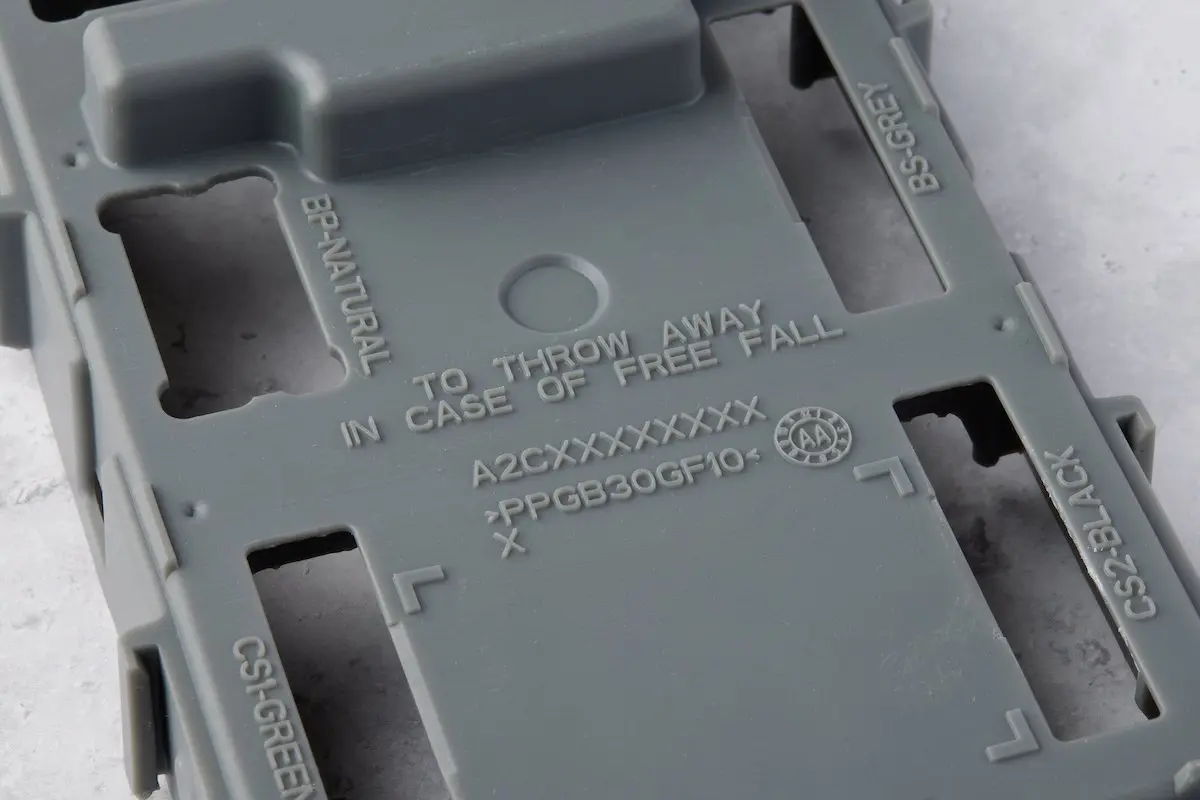
SLA-3D-gedruckte Teile, wie dieses auf Formlabs' Form 4 gedruckte Gehäuse, haben scharfe Kanten, glatte Oberflächen und nur minimal sichtbare Schichtlinien.
Die Auflösung ist eine Angabe, die häufig missverstanden wird, und der Ansatz zur Messung der Auflösung variiert oft zwischen den Herstellern und verschiedenen 3D-Druckverfahren. In der Regel bezieht sie sich auf die kleinstmöglichen Merkmale, den feinsten Detailgrad oder das Maß der Komplexität von Oberflächenstrukturen, die ein 3D-Drucker reproduzieren kann. Sie kann durch Kennzahlen wie die minimale Strukturgröße gemessen werden. Die Mechanik der drei verschiedenen 3D-Druckverfahren (Schmelzschichtung (FDM), Stereolithografie (SLA) oder selektives Lasersintern (SLS)) hat einen großen Einfluss auf die Auflösung der Teile.
FDM-3D-Drucker bilden Schichten, indem sie geschmolzenen Kunststoff in einer vorgegebenen Form durch eine Düse extrudieren, dann nach oben fahren und die nächste Schicht auftragen. Die Auflösung von FDM-3D-Druckteilen hängt daher von der Größe der Düse, den Materialeigenschaften des geschmolzenen Filaments und der Kontrolle ab, mit der der Motor die Düse auf der X- und Y-Achse bewegt, wie auch zwischen den Schichten auf der Z-Achse. FDM-3D-Drucker können in der Regel etwa 0,8 mm dicke Wände erstellen, und geprägte oder gravierte Details müssen etwa 0,6 mm breit und 2 mm hoch sein, um sichtbar zu sein.
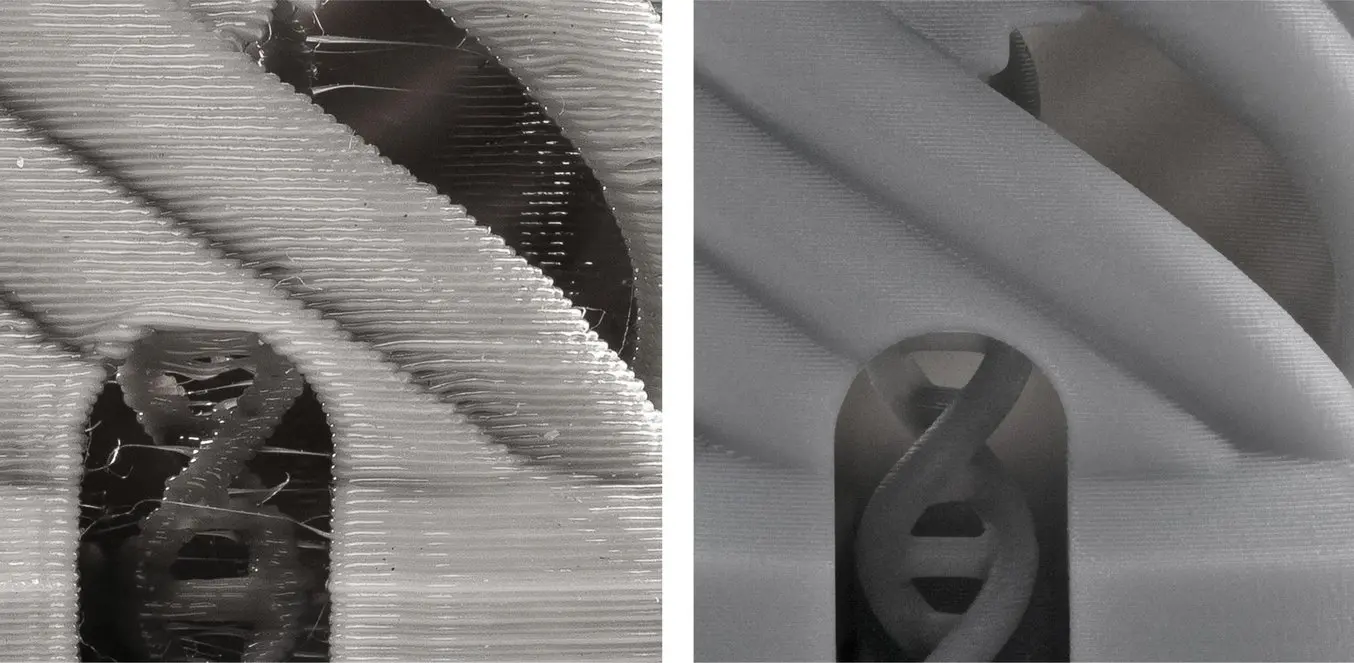
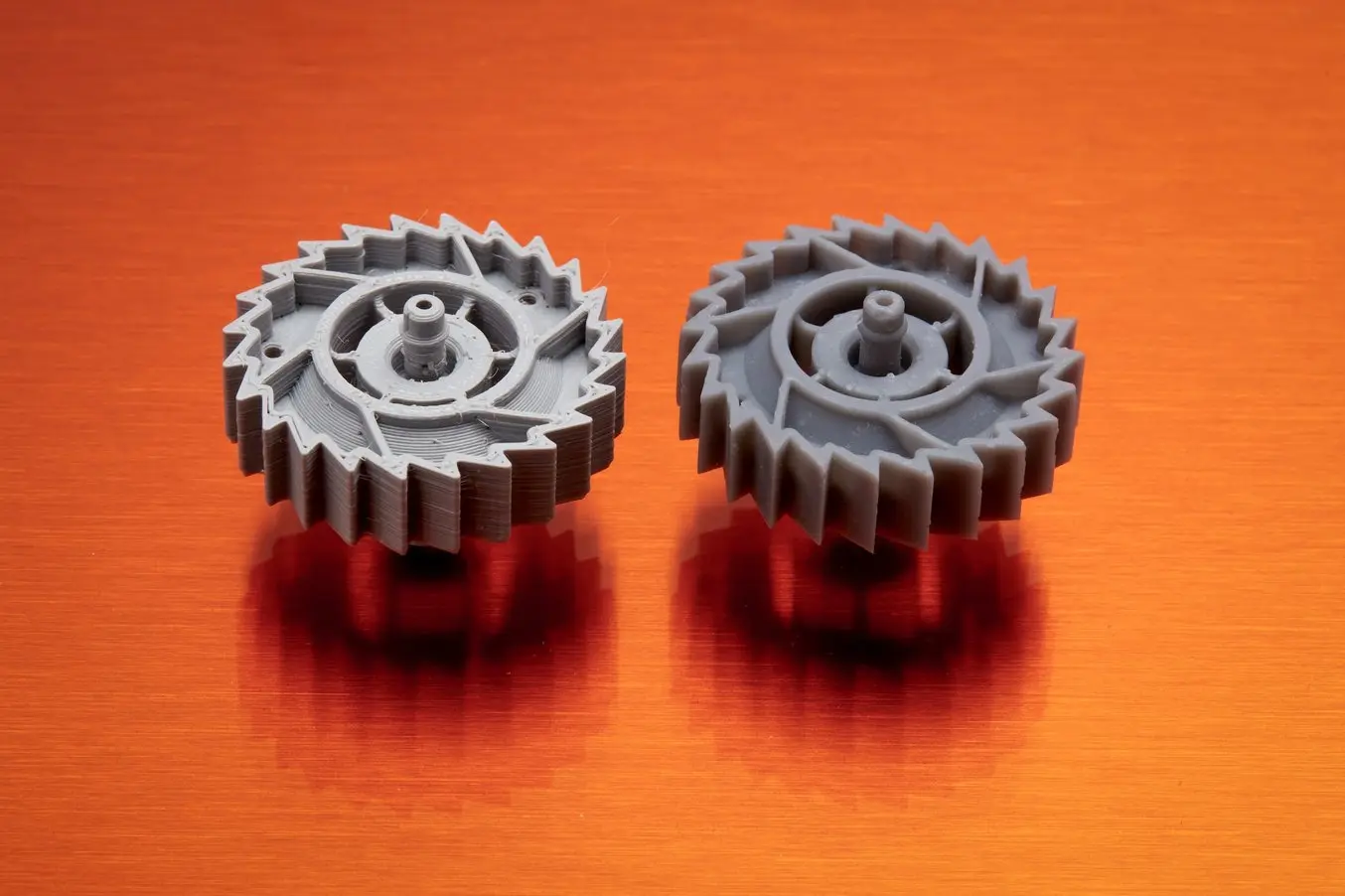
FDM-Drucker (links) haben mit komplexen Designs oder filigranen Details im Vergleich zu SLA-Druckern (rechts) Schwierigkeiten.
SLA-3D-Drucker formen Teile, indem sie flüssiges Kunstharz mithilfe einer Lichtquelle (einem Laser, einem digitalen Lichtprojektor oder LEDs) Schicht für Schicht aushärten. Die Auflösung von SLA-3D-Druckern hängt von vielen Faktoren ab, unter anderem von der Art der verwendeten Lichtquelle und dem Streuungs-, Ausblutungs- und Polymerisationsverhalten des Kunstharzes. Im Allgemeinen kann sie jedoch als die Fähigkeit betrachtet werden, Teile in der XY-Ebene genau nachzuzeichnen, kombiniert mit der minimalen Schichthöhe auf der Z-Achse.
Trotz der Unterschiede bei der Art der Lichtquelle, die in verschiedenen SLA-3D-Druckern verwendet wird, hat diese Technologie im Vergleich zum FDM- oder SLS-3D-Druck die höchste Auflösung. Unabhängig davon, ob es sich bei der Lichtquelle um einen Laser, einen digitalen Projektor oder um LEDs handelt, deren Licht von einem LCD-Bildschirm maskiert wird, kann das Licht sehr präzise auf das Flüssigharz gerichtet werden. Die überlegene Auflösung von SLA-3D-gedruckten Teilen aus Kunstharz spiegelt sich in ihren feinen Merkmalen, komplizierten Oberflächenstrukturen oder ihrer perfekten Glätte und hohen Maßgenauigkeit wider. Professionelle SLA-3D-Drucker wie der Form 4 von Formlabs können Wände ab einer Stärke von 0,2 mm sowie geprägte und gravierte Details mit einer Stärke von nur 0,1 mm bzw. 0,15 mm herstellen.
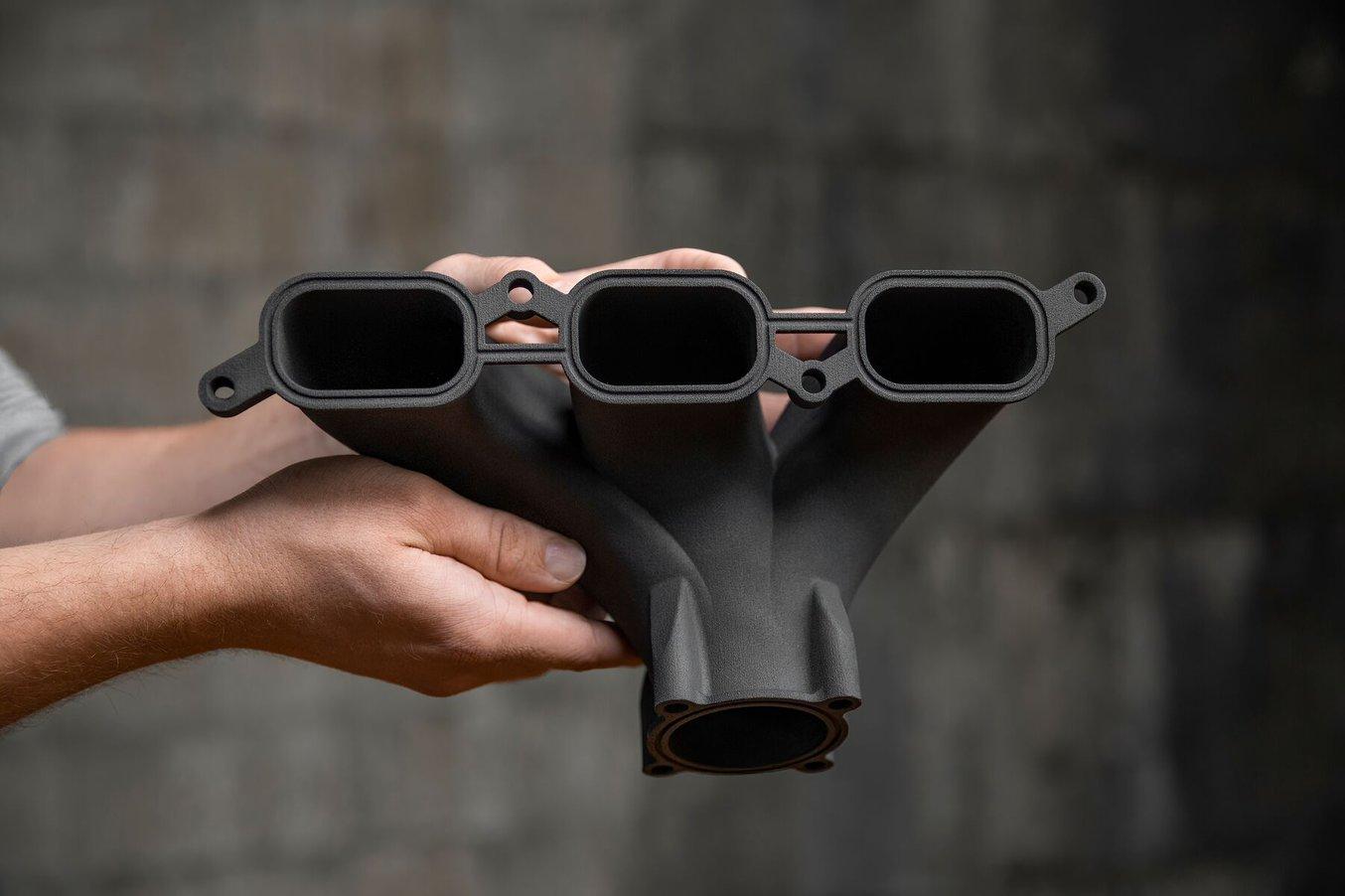
SLS-3D-Drucker in Industriequalität, wie der Fuse 1+ 30W, haben eine hervorragende Auflösung und können hochdetaillierte Teile herstellen, die Festigkeit mit organisch gekrümmten Oberflächen und präzisen negativen oder positiven Merkmalen kombinieren.
SLS-3D-Drucker formen Teile mithilfe eines Hochleistungslasers, der kleine Partikel aus Polymerpulver miteinander versintert. Die Auflösung von SLS-Teilen ist davon abhängig, wie präzise dieser Laser von den Galvanometern kontrolliert wird – was auf die Qualität des Lasers, die Programmierung der Software und Firmware und die Kalibrierung der gesamten Laser-Baugruppe zurückgeht. Dank des selbststützenden Verfahrens des SLS-Pulverbettdrucks lassen sich auch hochgradig filigrane Geometrien mit feinen Details umsetzen, ohne dass diese durch Stützstrukturen beeinträchtigt werden. Der Fuse 1+ 30W kann horizontale Wände von 0,3 mm Dicke und vertikale Wände von 0,6 mm Dicke erstellen. Geprägte und eingravierte Merkmale erfordern eine minimale Tiefe und Breite von 0,1 mm bis 0,4 mm, je nach Layout des Druckauftrags.
Vergleich der Designrichtlinien
Schmelzschichtung (FDM) | Stereolithografie (SLA) | Selektives Lasersintern (SLS) | |
---|---|---|---|
Mindestwandstärke gestützte Wand | 0,8 mm | 0,2 mm | 0,3 mm (horizontale Wände) 0,6 mm (vertikale Wände) |
Mindestwandstärke ungestützte Wand | 0,8 mm | 0,2 mm | 0,3 mm (horizontale Wände) 0,6 mm (vertikale Wände) |
Mindestdurchmesser vertikaler Draht | 3 mm | 0,3 mm (7 mm Höhe) 0,6 mm (30 mm Höhe) | 0,8 mm |
Mindestwert geprägter Details | 0,6 mm Breite 2 mm Höhe | 0,1 mm | 0,15 mm (Tiefe, horizontale Flächen) 0,35 mm (Breite, horizontale Flächen) 0,35 mm (Tiefe, vertikale Flächen) 0,4 mm (Breite, vertikale Flächen) |
Mindestwert eingravierter Details | 0,6 mm Breite 2 mm Höhe | 0,15 mm | 0,1 mm (Tiefe, horizontale Flächen) 0,3 mm (Breite, horizontale Flächen) 0,15 mm (Tiefe, vertikale Flächen) 0,35 mm (Breite, vertikale Flächen) |
Die Designrichtlinien können je nach Druckermodell variieren. Die aufgeführten Werte basieren auf Schätzungen von Protolabs / Hubs für FDM-3D-Drucker, den Designrichtlinien für den SLA-3D-Drucker Form 4 und den Designrichtlinien für SLS-3D-Drucker der Fuse-Serie.
Unter den drei 3D-Drucktechnologien bietet SLA die beste Auflösung, SLS liegt knapp dahinter. Beide Verfahren können die winzigen Details des ursprünglichen CAD-Entwurfs reproduzieren, während FDM-3D-Drucker im Allgemeinen Schwierigkeiten haben, Texturen von flachen Oberflächen präzise abzugrenzen oder kleine Merkmale klar zu definieren.
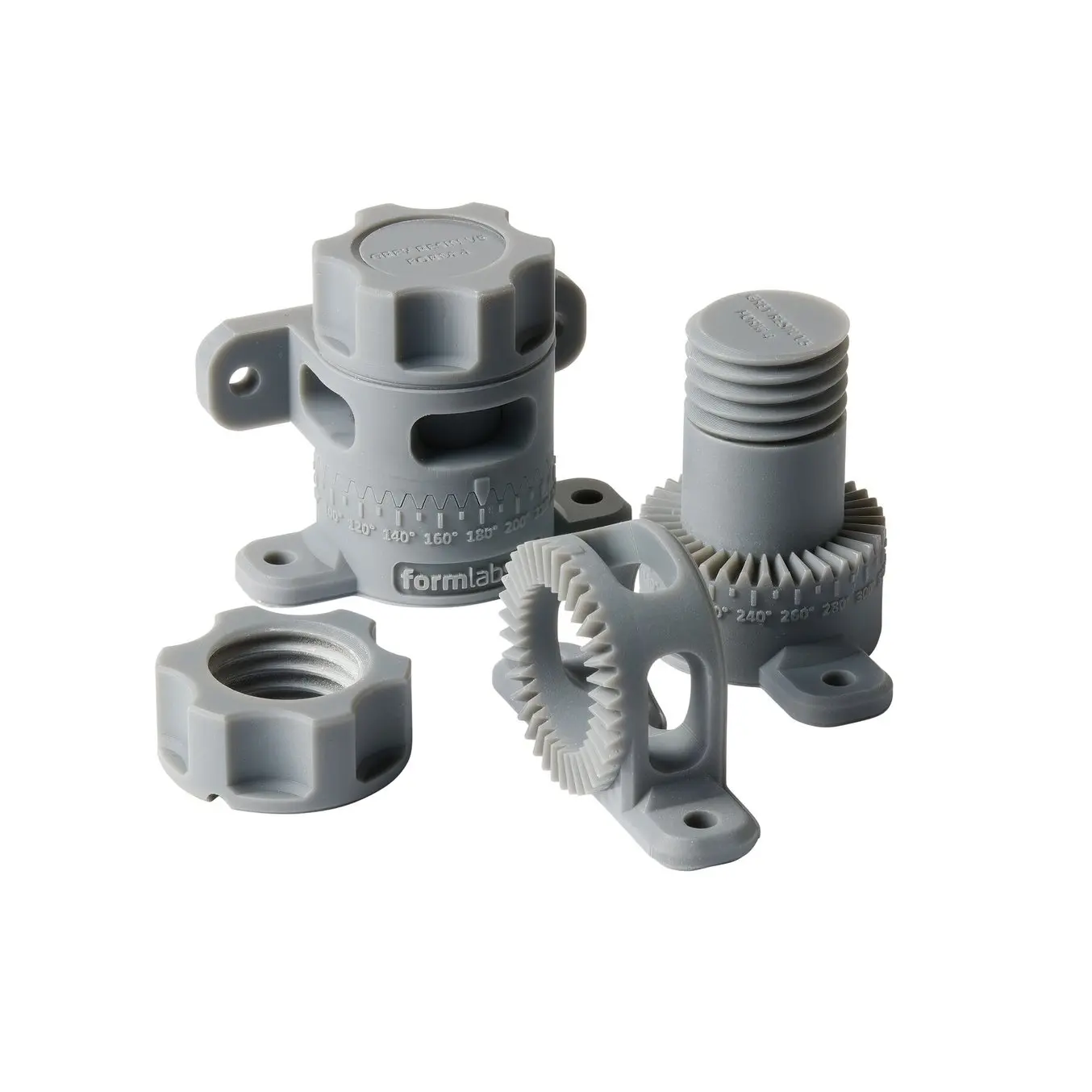
Design-Leitfaden für die Serie Form 4
Ein erfolgreicher 3D-Druck beginnt mit einem passenden Modelldesign. Befolgen Sie unsere bewährten Praktiken, um Designs zu optimieren und Fehler zu vermeiden.
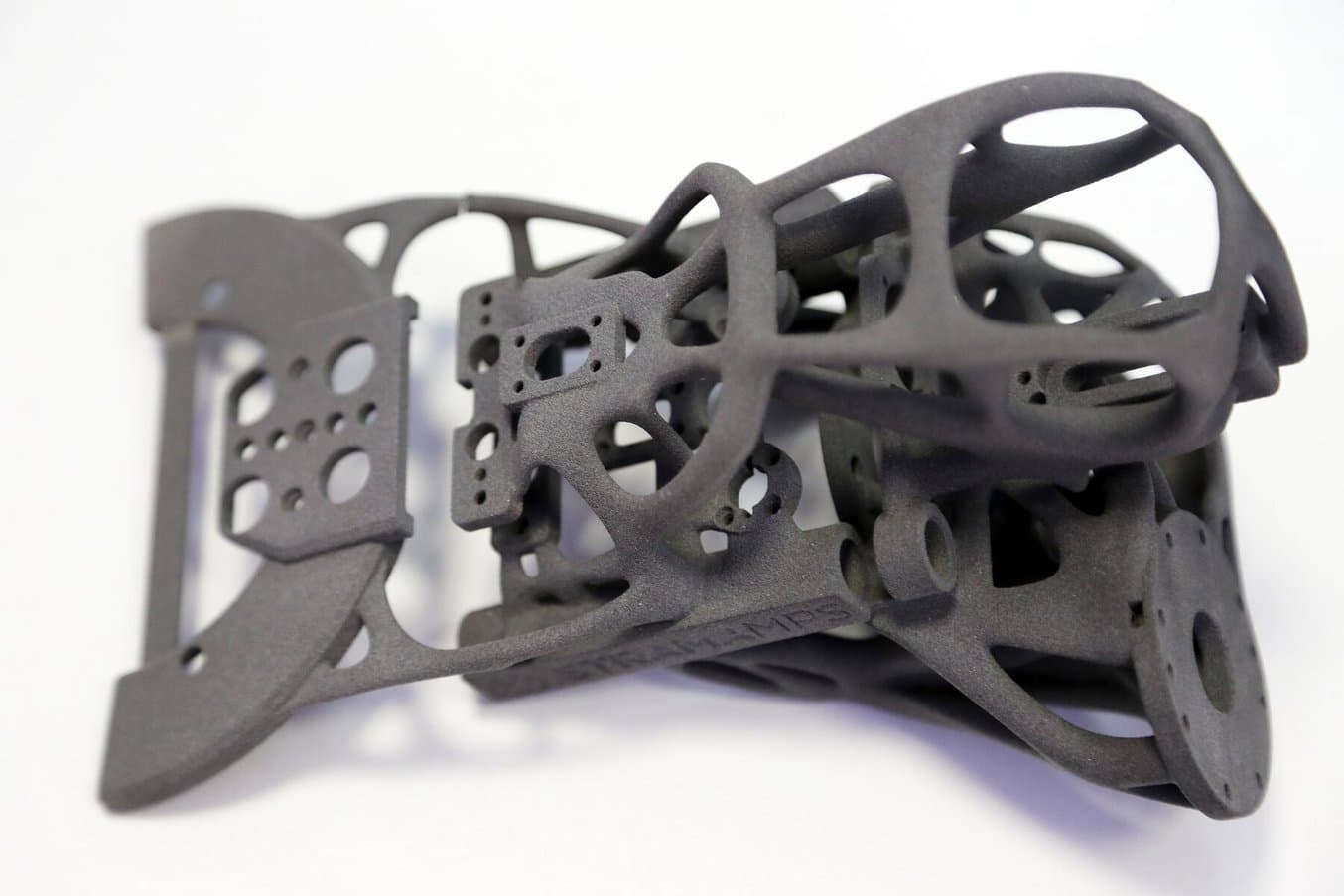
Design-Leitfaden für die Fuse-Serie
Dieser Leitfaden behandelt die wichtigen Abmessungen und Designüberlegungen, die bei der Konstruktion von Teilen für den SLS-3D-Druck auf der Fuse-Serie zu beachten sind. Sie lernen, wie Sie sich diese Praktiken zunutze machen, um leistungsstarke Teile zu produzieren.
Maßgenauigkeit und Präzision
Die Genauigkeit – wie genau also jeder Querschnitt des Teils die beabsichtigte Form der 3D-Datei reproduziert – und die Präzision – wie konsistent diese Genauigkeit im gesamten Teil wiederholt wird – variieren sowohl zwischen den verschiedenen 3D-Drucktechnologien als auch zwischen den einzelnen Herstellern.
Bei FDM-3D-Druckern hängt die Genauigkeit von der Gleichmäßigkeit und Wiederholbarkeit des Extrusionsprozesses und den Eigenschaften des Filaments beim Schmelzen und Extrudieren ab. Der Extrusionsprozess kann zu Unregelmäßigkeiten innerhalb und zwischen den Schichten führen, z. B. wenn die Bewegung nicht gleichmäßig ist, das Filament keinen einheitlichen Durchmesser hat, die Extrusionstemperatur schwankt oder das Material nicht überall mit der gleichen Geschwindigkeit und Menge aufgetragen wird.
Hinsichtlich der Gesamtpräzision kann der „Quetschungseffekt“ von halb gehärteten Schichten weitere Uneinheitlichkeit verursachen. Die beim Extrudieren angewandte Hitze kann zu Verformungen der Teile führen. Einige Hersteller verwenden jedoch beheizte Druckbetten und geschlossene Konstruktionskammern, um durch eine konstante Temperatur einen kontrollierteren Prozess zu gewährleisten.
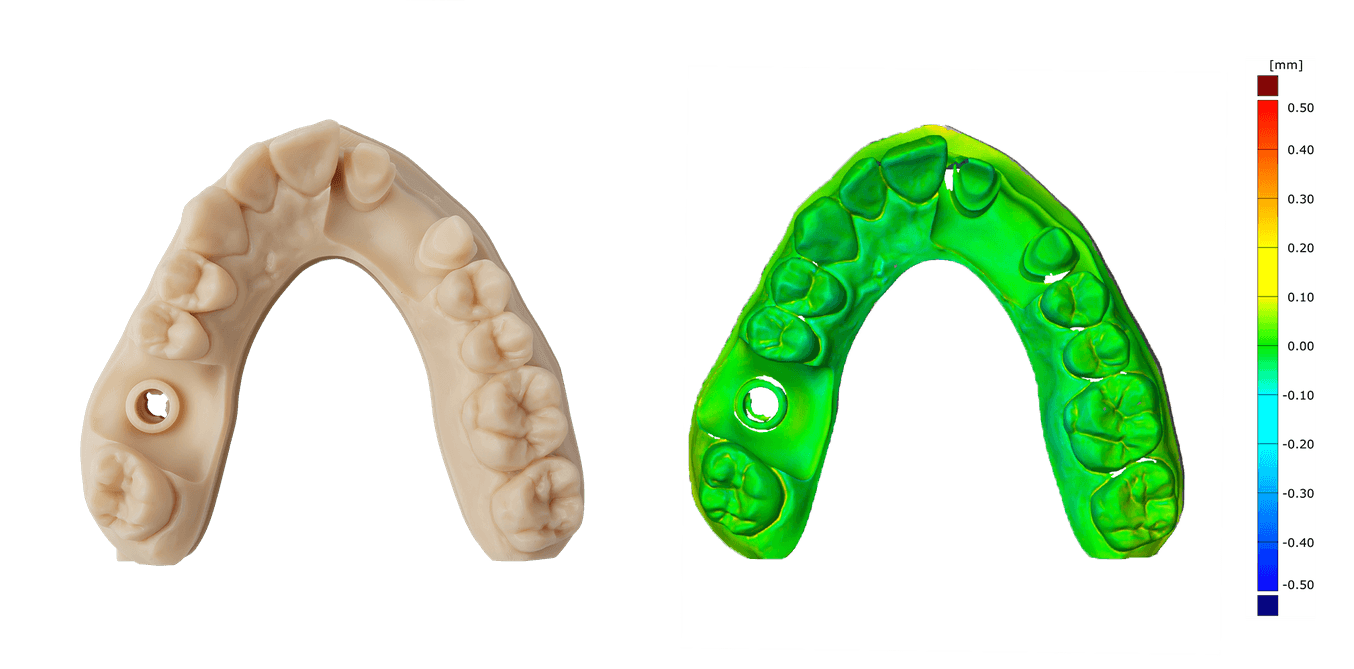
Die Genauigkeit lässt sich durch das 3D-Scannen der 3D-gedruckten Teile und das Vergleichen mit dem Originalmodell messen. Noch besser ist folgendes Vorgehen: Bitten Sie um einen kostenlosen Probedruck oder ein individuelles Muster Ihres eignen Designs, um die Passung zu untersuchen oder die Abmessungen mit dem ursprünglichen Design zu vergleichen. Dieses Dentalmodell wurde auf einem MSLA-Drucker vom Typ Form 4B hergestellt, und der Test zeigt, dass über 99 % seiner Oberfläche weniger als 100 μm von den Designparametern abweichen.
Die Genauigkeit von SLA-Druckern ist abhängig von der optischen Leistung des Druckers, den Kräften, denen Teile während des Drucks ausgesetzt sind, und den Eigenschaften des flüssigen Harzes im Drucker. Verschiedene Lichtquellen und Optik-Einheiten härten die einzelnen Schichten mit unterschiedlicher Genauigkeit aus, wobei die Gesamtleistung in der Regel dennoch die Genauigkeit von FDM-3D-Druckern übertrifft.
Zusätzlich übt die Ablösebewegung nach der Fertigstellung einer Schicht, wenn die Konstruktionsplattform sich von der Lichtquelle wegbewegt, eine starke Belastung auf die neu gehärtete Schicht aus, was zu leichten Verformungen führen kann. Professionelle Kunstharz-Drucker setzen verschiedene Lösungen ein, um diese Kräfte abzumildern. Der Form 4 von Formlabs verwendet beispielsweise einen Tank mit zweischichtigem, flexiblem Film, der die Abzugskräfte minimiert, sowie eine eigens entwickelte, mikrotexturierte optische Folie, die sogenannte Ablösetextur, die für einen Luftstrom zwischen dem Harztank und dem LCD-Bildschirm sorgt. Dadurch werden Saugkräfte verhindert und die Druckgenauigkeit gesteigert.
Der dritte Faktor, der die Genauigkeit von Resin-3D-Druckern beeinflusst, sind die Materialeigenschaften. Der Vorgang der Aushärtung flüssigen Kunstharzes ist von vielen Variablen abhängig, unter anderem der Harztemperatur, der Homogenität, der Streuung und der Viskosität. Bei jeder dieser Variablen können kleine Änderungen dazu führen, dass sich die Menge des gehärteten Harzes verändert, was Abweichungen von bis zu Hunderten Mikrometern in der Größe oder Form der ausgehärteten Schichten zur Folge haben kann. Die meisten 3D-Drucker kontrollieren diese Variablen nicht, sodass es zu häufigen, unvorhersehbaren Maßabweichungen kommt.
Formlabs' Form 4 löst dieses Problem, indem er die Temperatur und die Homogenität des flüssigen Kunstharzes mithilfe von Heizelementen, Infrarot-Temperatursensoren und einem extrem schnellen Harzmischer präzise steuert. Formlabs entwickelt und produziert seine Materialien zudem selbst, wobei die Reaktivität, Viskosität und die Streuungseigenschaften jedes Materials streng kontrolliert werden.
Um die erreichbare Maßgenauigkeit zu ermitteln, wurde ein Testmodell mit verschiedenen Merkmalsgrößen auf drei verschiedenen Druckern mit Grey Resin V5 und 100 µm Schichthöhe gedruckt und fünf Minuten lang bei Raumtemperatur nachgehärtet. Die gemessene Genauigkeit der Modelle fiel wie folgt aus:
- Strukturen von 1–30 mm: ±0,15 % (unterer Grenzwert: ±0,02 mm)
- Strukturen von 31–80 mm: ±0,2 % (unterer Grenzwert: ±0,06 mm)
- Strukturen von 81–150 mm: ±0,3 % (unterer Grenzwert: ±0,15 mm)
SLS-3D-Drucker sind in der Regel recht genau; der Laser und die Galvanometer erzielen eine exakte Steuerung. Die Genauigkeit von SLS-3D-Druckern ist abhängig von der optischen Leistung des Lasers, von der Abstimmung der Druckparameter auf die Pulvereinstellungen sowie von der Kontrolle der Druckumgebung. Für einen genauen Druck erfordert der SLS-3D-Druck äußerst konstante, präzise eingestellte Temperaturen. Offene Einstellungen für die Nutzung von Materialien von Drittanbietern erhöhen die Wahrscheinlichkeit einer schlechten Druckteilqualität und -leistung sowie von Druckfehlern wie Verzug.
Im Allgemeinen sind Kunstharz- und Pulver-3D-Drucker die genauesten und präzisesten Arten von 3D-Drucktechnologien. Im Vergleich zu den standardmäßigen Toleranzen der CNC-Bearbeitung von +/- 0,3 mm halten Formlabs' SLA-Drucker vom Typ Form 4 und die SLS-Drucker der Fuse-Serie vollkommen mit.
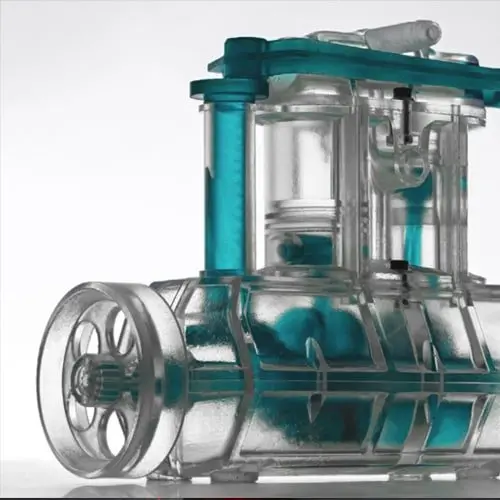
Designoptimierung für funktionale 3D-gedruckte Bauteile
Toleranz und Passung sind grundlegende Konzepte, mit denen Ingenieure die Funktionalität mechanischer Baugruppen und die Produktionskosten optimieren. Dieses Whitepaper dient als Ressource für das Design funktionsfähiger 3D-gedruckter Baugruppen und kann zudem als Ausgangspunkt für Entwürfe passgenauer Teile dienen.
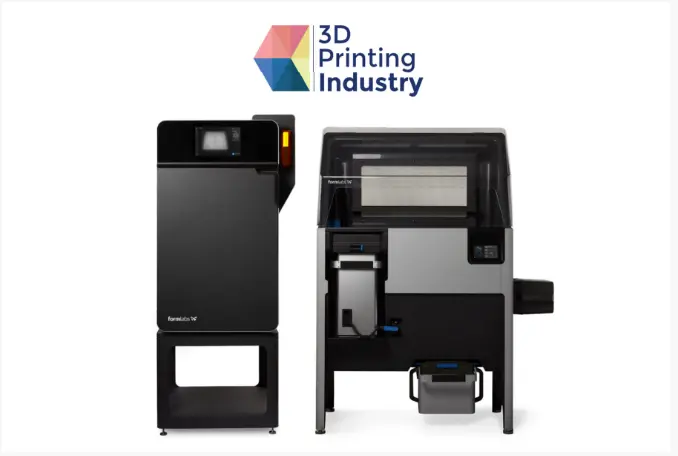
3D Printing Industry: Testbericht zu Fuse 1 & Fuse Sift von Formlabs
Lesen Sie diesen tiefgehenden Bericht des Ingenieurteams von 3D Printing Industry, in dem die SLS-3D-Drucker von Formlabs bewertet und detaillierte Ergebnisse von Präzisionstest dargestellt werden.
Isotropie und Wasserdichtigkeit
Isotropie und Anisotropie sind im 3D-Druck häufig Thema. Da die Teile beim 3D-Druck schichtweise gefertigt werden, gibt es bei den fertigen Druckteilen abhängig von der Ausrichtung des Teils möglicherweise Unterschiede in der Festigkeit. Dabei weisen die Teile in den X-, Y- und Z-Achsen unterschiedliche Eigenschaften auf.
FDM-3D-gedruckte Teile sind dafür bekannt, dass sie aufgrund der durch den Druckprozess entstehenden Unterschiede von Schicht zu Schicht anisotrop sind. Diese Anisotropie begrenzt die Tauglichkeit von FDM für bestimmte Anwendungen oder macht zusätzliche Anpassungen bei der Druckgeometrie erforderlich, um sie zu kompensieren.
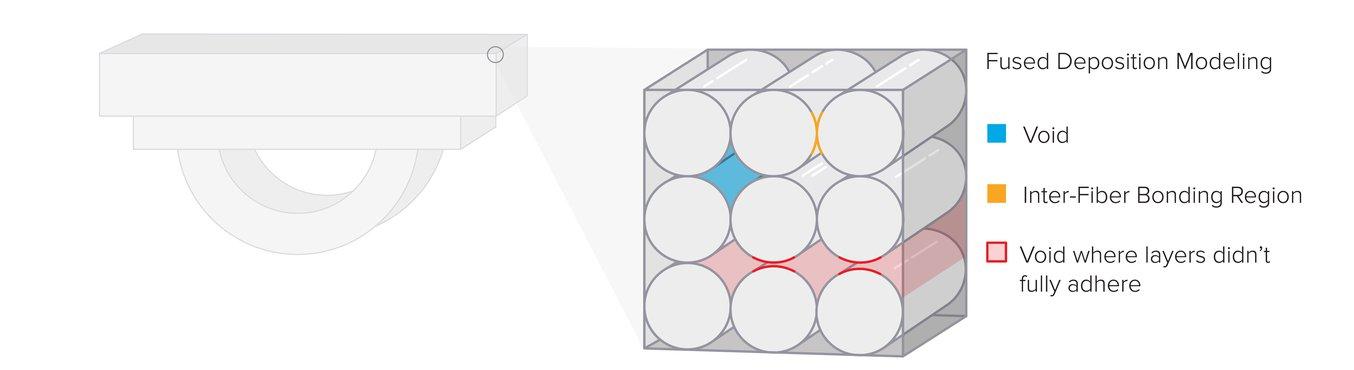
FDM-3D-Drucker bilden Schichten, indem sie Linien aus geschmolzenen Thermoplasten auftragen. Dieser Prozess führt dazu, dass die Schichten miteinander nicht so stark verbunden sind wie die einzelnen Linien (Filamentextrusion) in sich selbst. Es gibt Hohlräume zwischen den abgerundeten Linien und so ist es möglich, dass die Schichten nicht vollständig aneinander haften.
Im Gegensatz dazu sorgen Kunstharz-Drucker für hochgradig isotrope Teile. Die Isotropie hängt von verschiedenen Faktoren ab, die über die Integration der Materialchemie in den Druckprozess genau gesteuert werden können. Während des Druckvorgangs bilden die Harzbestandteile kovalente Bindungen, doch von Schicht zu Schicht bleibt das Teil ein halb reagiertes „Grünteil“.
In diesem Grünteilzustand bleiben im Kunstharz polymerisierbare Gruppen zurück, die Verbindungen über Schichten hinweg eingehen können. Bei der finalen Nachhärtung werden dem Teil Isotropie und Wasserdichtigkeit verliehen. Auf molekularer Ebene gibt es dadurch keine Unterschiede zwischen den X-, Y- oder Z-Schichten. Dies führt zu Teilen mit vorhersehbaren mechanischen Eigenschaften, wie sie für Anwendungen wie Halterungen und Vorrichtungen, Endverbrauchsteile und funktionsfähige Prototypen erforderlich sind.
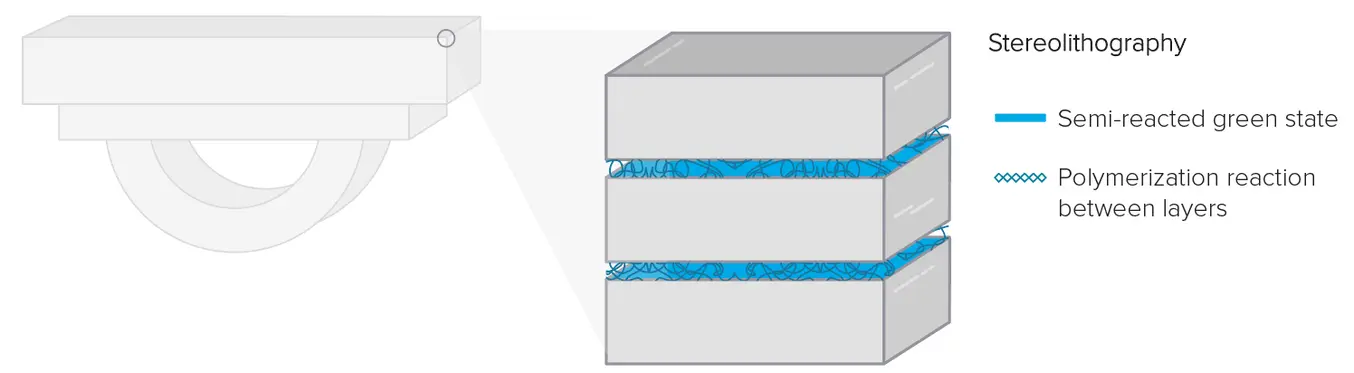
Bei SLA-Druckteilen gibt es durch chemische Bindungen keinen Unterschied zwischen der Z-Achse und der XY-Ebene. Jedes auf einem SLA-Gerät gedruckte Teil ist ein fortlaufendes Polymernetzwerk.
SLS-3D-Drucker erzeugen Teile, die größtenteils isotrop sind. Im Gegensatz zum FDM-3D-Druck, bei dem das Filament vor der Extrusion geschmolzen wird und so mit den vorhergehenden Schichten in Kontakt kommt, sintern SLS-3D-Drucker Partikel, die bereits mit dem umgebenden Material in Kontakt sind. Somit verschmelzen die Partikel in derselben Ebene oder Schicht miteinander, sowie teilweise auch mit der Ebene/Schicht darunter. Da es jedoch variiert, wie lange Materialien Wärme speichern und im halbgesinterten Zustand verbleiben, kann die Isotropie von SLS-Teilen je nach Pulvertyp unterschiedlich ausfallen. Verschiedene Pulver verschmelzen unterschiedlich schnell mit den darunter liegenden Schichten, manche vollständiger als andere.
Die Isotropie hängt auch mit der Oberflächenporosität und der Partikeldichte zusammen, und all diese Merkmale wirken sich auf die Wasserdichtigkeit und Wasserfestigkeit eines Teils aus. Wasserdichtigkeit bezieht sich auf die Fähigkeit eines Teils oder einer Baugruppe, das Eindringen oder Austreten von Flüssigkeit zu verhindern, und Wasserfestigkeit bezieht sich auf die Fähigkeit einer Außenfläche, Wasser abzuweisen. Bei 3D-gedruckten Teilen werden solche Eigenschaften durch die Wasserdichtigkeit besser abgebildet, denn 3D-gedruckte Teile und Baugruppen dienen häufig zum Schutz von Komponenten in ihrem Inneren, statt lediglich zur Wasserabweisung – so etwa Unterwasser-Elektronikgehäuse.
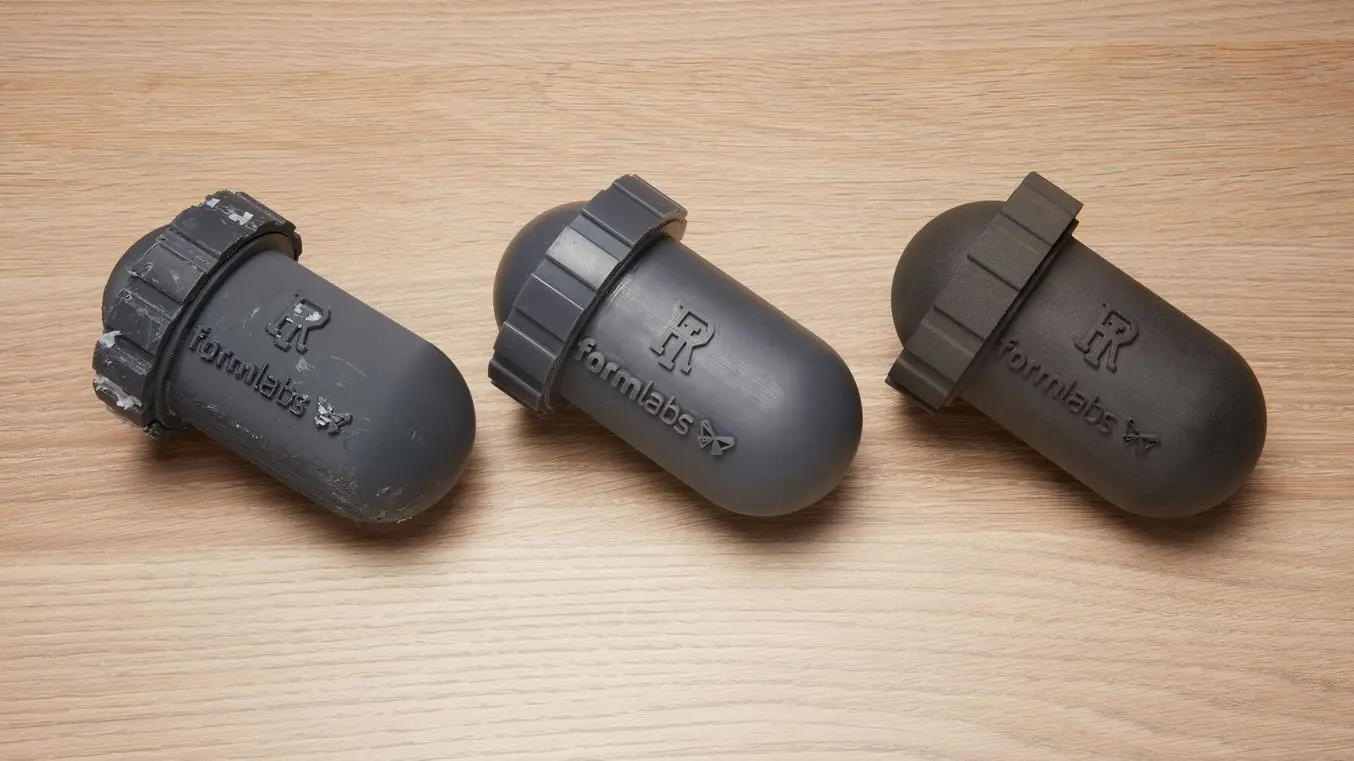
In umfangreichen Tests vom University of Rhode Island Underwater Robotics and Imaging Laboratory (URIL) wurden FDM- (links), SLA- (Mitte) und SLS-3D-gedruckte Gehäuse (rechts) in einer Druckkammer getestet.
In einer umfassenden Studie des University of Rhode Island Underwater Robotics and Imaging Laboratory wurde festgestellt, dass 3D-gedruckte FDM-Robotikgehäuse die interne Mechanik unter Wasser nicht einmal für ein paar Sekunden trocken halten können. SLA-3D-gedruckte Teile erwiesen sich bis zu einem sehr hohen Druck als wasserdicht, während SLS-3D-gedruckte Teile die innere Elektronik bei mäßigem Druck trocken hielten. SLS-Gehäuse, die dampfgeglättet wurden, blieben auch unter erhöhtem Druck wasserdicht.
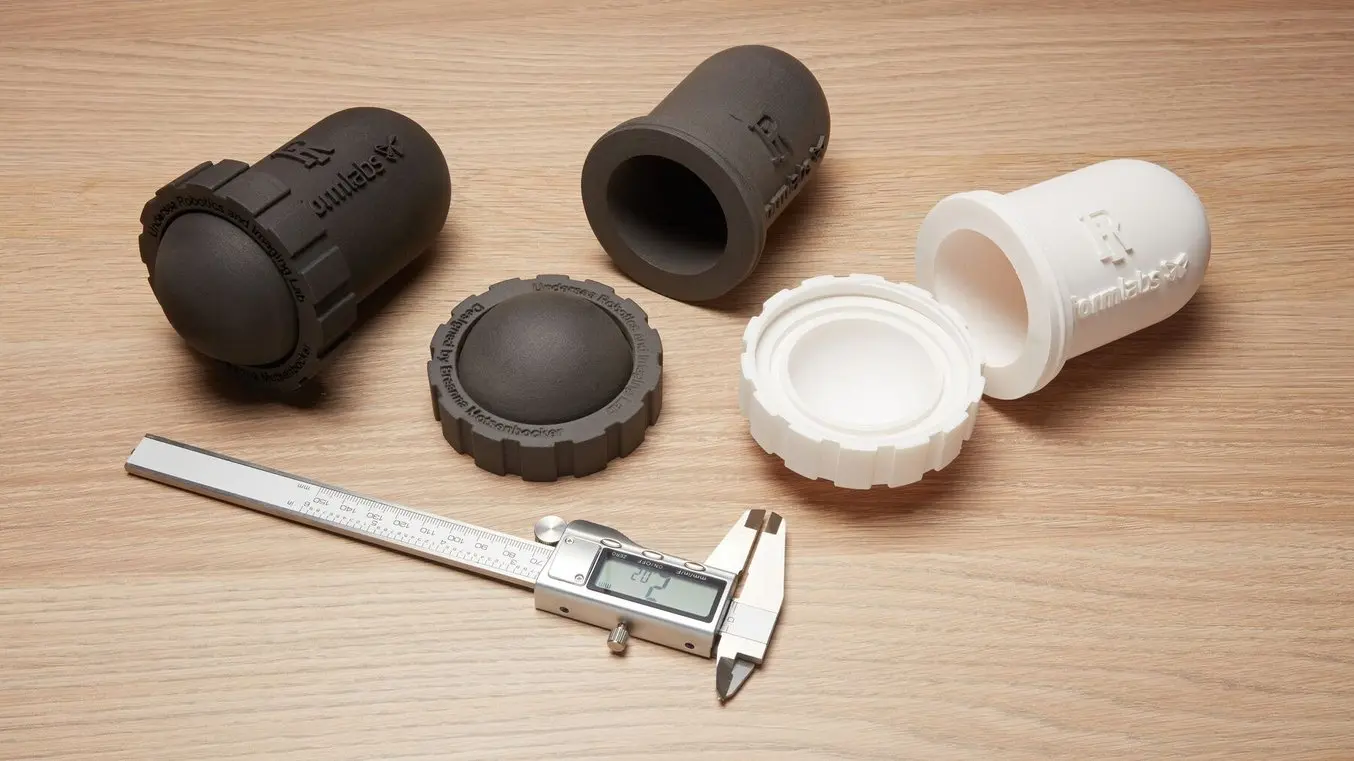
3D-Druck wasserdichter Behälter und Ergebnisse von Druckprüfungen
In diesem Whitepaper stellen wir die Testergebnisse vor und geben klare Richtlinien zum kostengünstigen 3D-Druck individueller wasserdichter Behälter.
Oberflächengüte
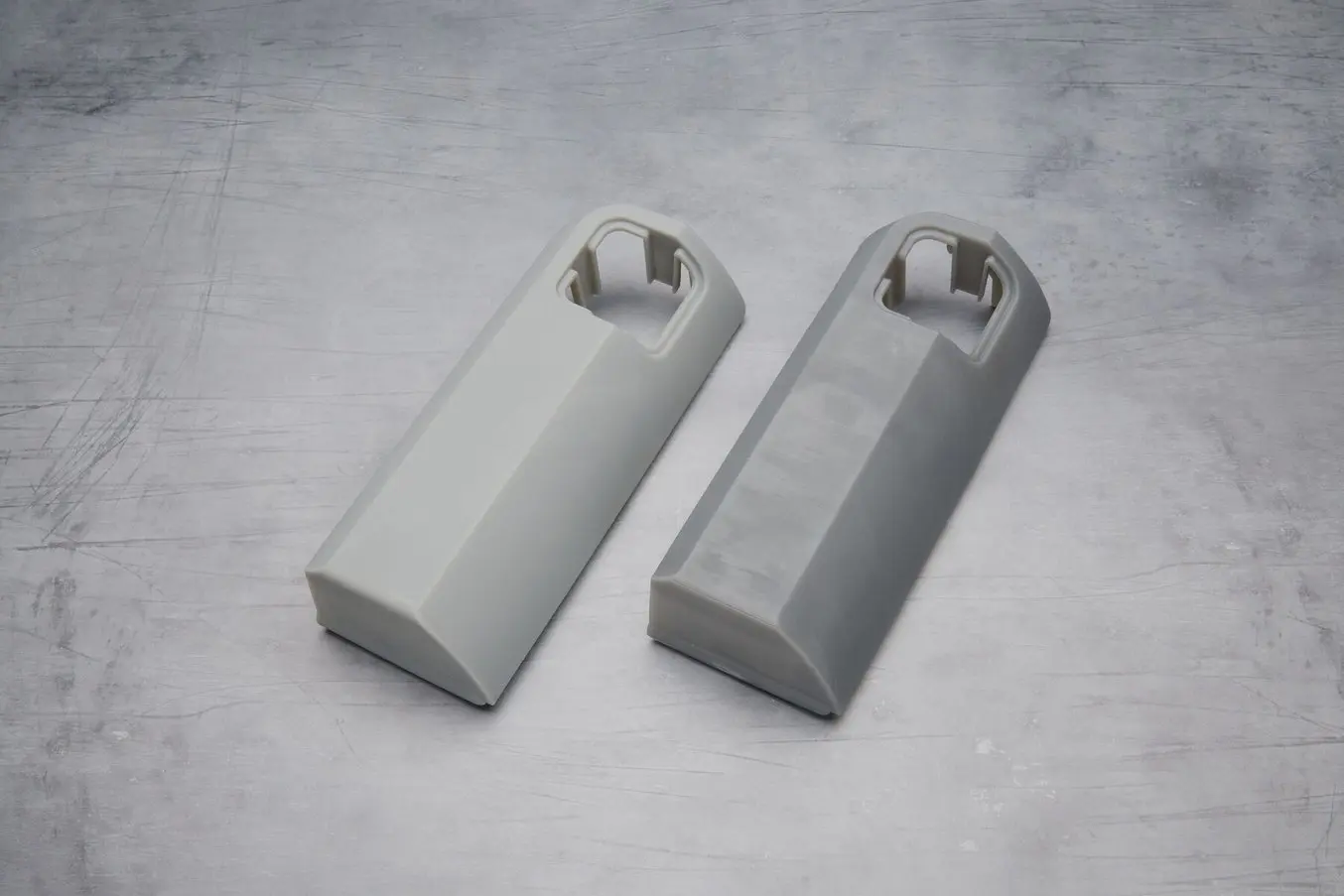
SLA-3D-Drucker ergeben die beste Oberflächenbeschaffenheit, also Teile mit glatten, matten Oberflächen. Mit Fortschritten in der 3D-Druck-Branche im Allgemeinen und der SLA-Technologie im Speziellen haben sich auch diese Ergebnisse weiter verbessert.
Einer der bekanntesten Unterschiede zwischen FDM-, SLA- und SLS-3D-Druckteilen ist die unterschiedliche Oberflächenqualität. Die schichtweise „Klebepistolen“-Methode von FDM verursacht Schichtlinien, die bei genauer Betrachtung sichtbar sind. Daher erfordern die Druckteile einen höheren Nachbearbeitungsaufwand, was die Gesamtproduktionszeit verlängert. Schichtlinien verhindern auch, dass aus halbtransparenten oder lichtdurchlässigen Materialien wirklich durchscheinende Teile entstehen; das Licht bricht sich selbst an winzigen Linien im Material, was die Transparenz des fertigen Teils trübt.
SLA-3D-Drucker erzeugen Teile, die von spritzgegossenen Kunststoffen fast nicht zu unterscheiden sind. Ihre überragende Oberflächengüte ist ideal für finale Beurteilung von Prototypen und Endprodukten, selbst in der Kategorie Konsumgüter, wo Oberflächenqualität und Glätte von größter Bedeutung sind. Außerdem können SLA-3D-Drucker aufgrund des Fehlens von Schichtlinien fast vollständig transparente Teile herstellen. Klare Teile sind hilfreich für Gussanwendungen, bei denen so der Einspritzvorgang beobachtet werden kann, aber auch für das Design von Produkten aus transparenten Endmaterialien, für die Mikrofluidik, medizinische Anwendungen und vieles mehr. Im zahnmedizinischen 3D-Druck können SLA-Kunstharze wie Premium Teeth Resin die glatte Optik von Zahnschmelz simulieren, sodass Zahnprothesen nicht von echten Zähnen zu unterscheiden sind.
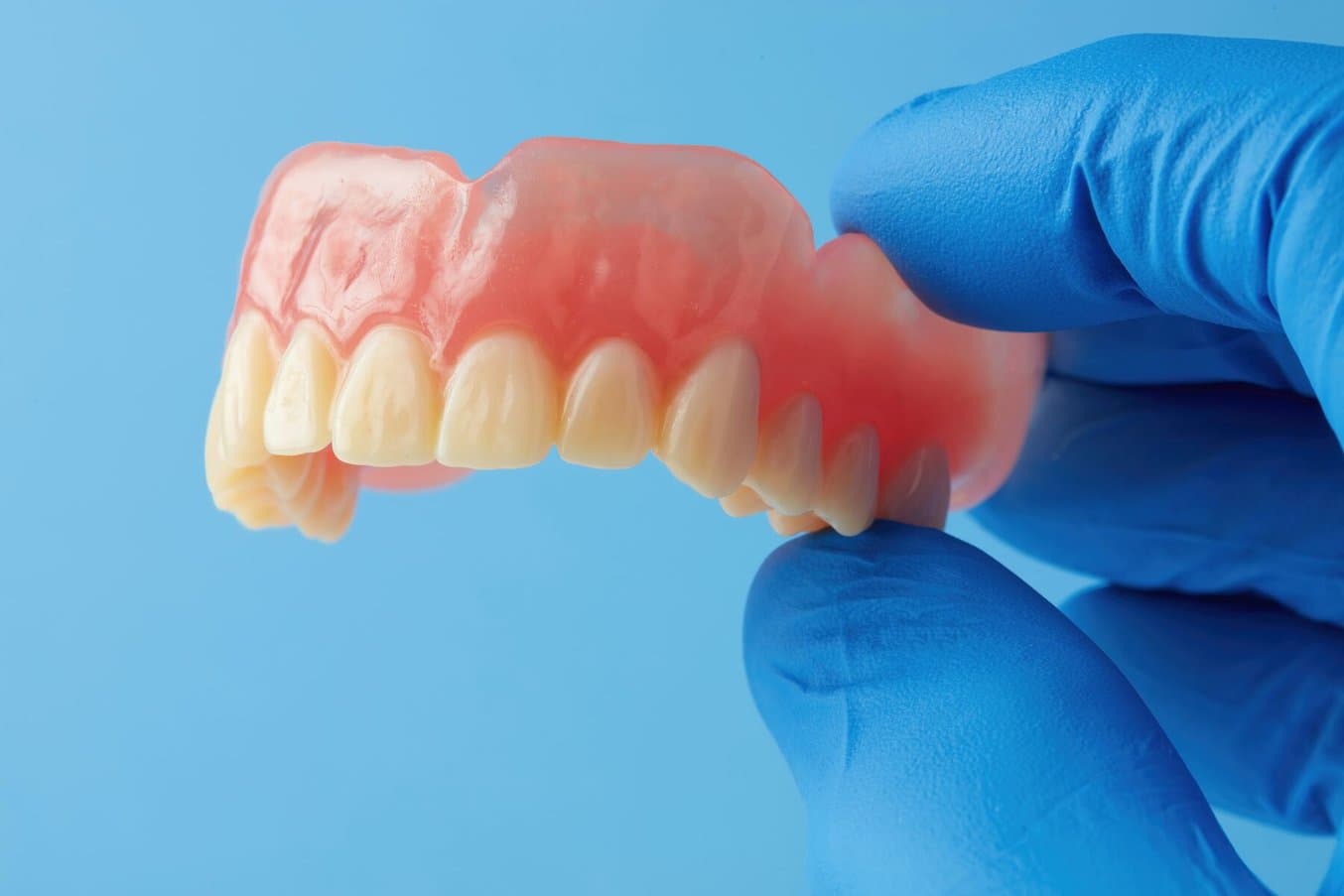
SLA-3D-gedruckte Teile haben eine erstklassige Oberflächenqualität, sodass Teile wie diese 3D-gedruckten Prothesen nicht von echten Zähnen zu unterscheiden sind.
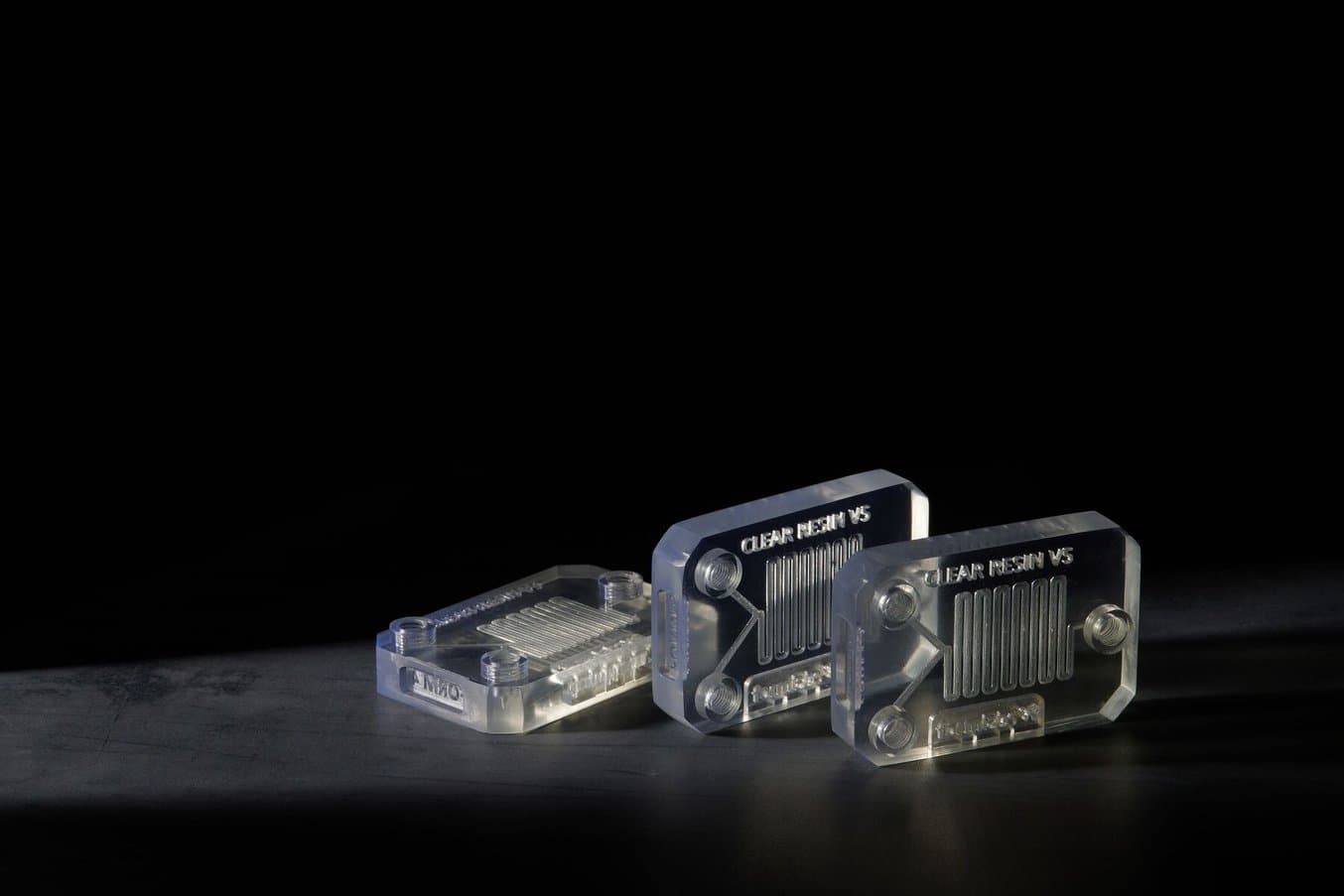
Das Fehlen von Schichtlinien lässt die mittels SLA 3D-gedruckten Teile aus Clear Resin fast völlig transparent erscheinen, denn Schichtlinien haben eine lichtbrechende Wirkung.
Mittels SLS 3D-gedruckte Teile haben eine leicht raue oder körnige Oberfläche. Da SLS-Teile jedoch ohne Stützstrukturen gedruckt werden, ist es einfach, eine einheitliche Oberflächenbeschaffenheit über das gesamte Teil zu erzielen. Im Gegensatz dazu müssen SLA- und FDM-3D-gedruckte Teile oft nachbearbeitet werden, um kleine Spuren zu entfernen, die von den Stützstrukturen hinterlassen wurden. Zudem können SLS-3D-gedruckte Teile, die dampfgeglättet oder sandgestrahlt und poliert wurden, eine glänzende, glatte Oberfläche erreichen, genau wie SLA-Teile.
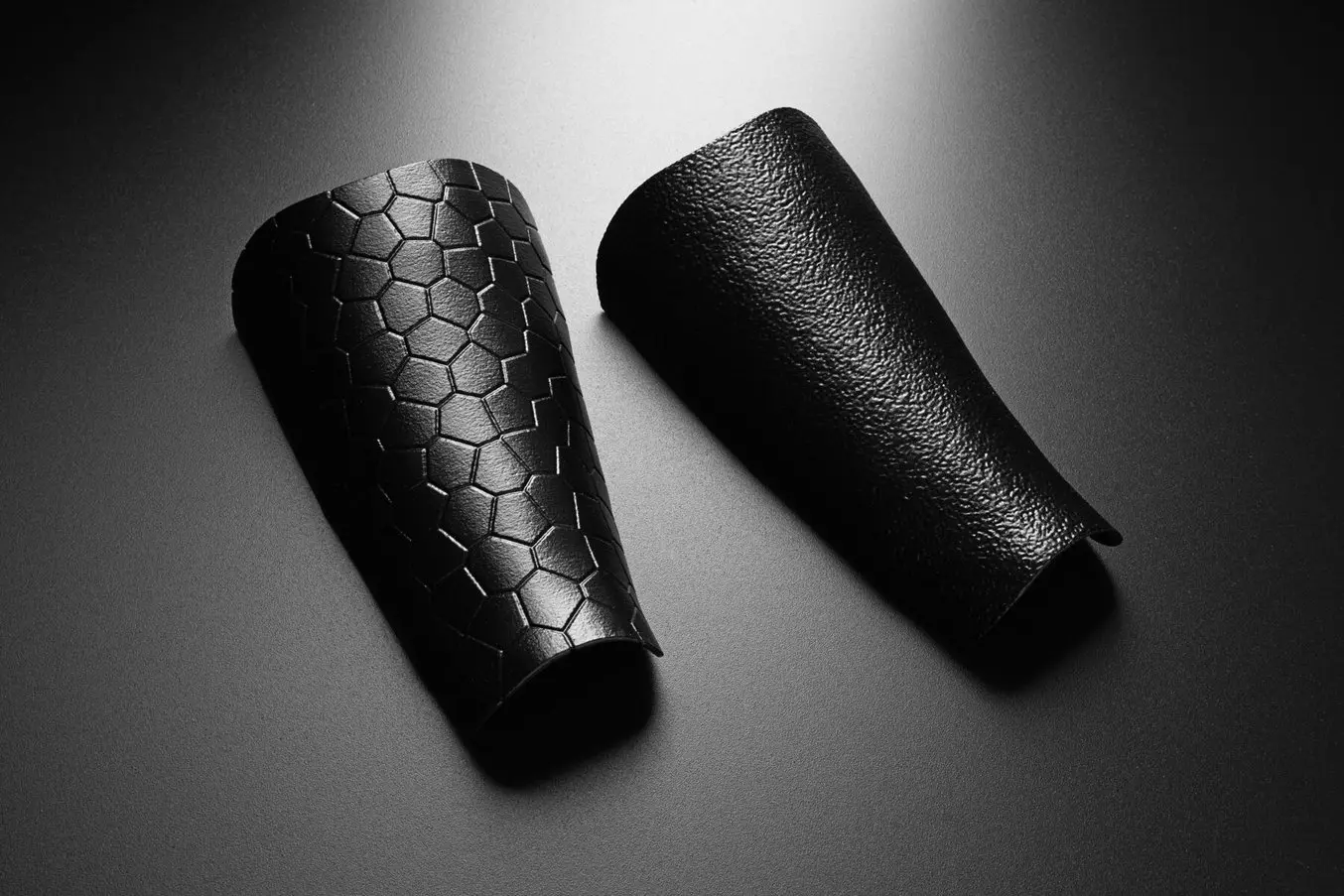
Zwar haben SLS-Teile nach dem Druck eine leicht körnige Oberfläche, doch durch Nachbearbeitungsmethoden wie Vapor Smoothing lässt sich ein Oberflächenfinish in Endproduktqualität erzielen. Die abgebildeten Teile wurden mit unterschiedlichen Oberflächenstrukturen gedruckt und anschließend mittels Vapor Smoothing geglättet, um raue Oberflächenbereiche zu entfernen.
Arbeitsablauf und Benutzerfreundlichkeit
Sehen Sie sich die Schritte vom Design zum fertigen 3D-Druck mit dem SLA-3D-Drucker Form 4 an. Dieses Video behandelt die Grundlagen der Bedienung des Form 4, von der Software und den Materialien bis zum Drucken und Nachbearbeiten.
Der Arbeitsprozess besteht sowohl beim FDM-, SLA- als auch SLS-3D-Druck aus drei Schritten: Design, 3D-Druck und Nachbearbeitung.
Zuerst entwerfen Sie mithilfe einer beliebigen CAD-Software oder 3D-Scandaten ein Modell und exportieren dieses in ein 3D-druckbares Dateiformat (STL oder OBJ). Anschließend brauchen Sie eine Druckvorbereitungs- oder Slicer-Software, um die Druckeinstellungen für den Drucker festzulegen und das digitale Modell für den Druck in Schichten zu zerteilen. Der Schritt der Druckausrichtung kann mit einem simplen Klick auf die Funktion „Ein-Klick-Druck“ in Formlabs' Druckvorbereitungssoftware PreForm erledigt sein, oder sich sogar auf die manuelle Auswahl der Druckeinstellungen und die Feinabstimmung der Materialeinstellungen erstrecken. Unabhängig von der Technologie erfordern kostengünstige Geräte in der Regel einen höheren Arbeitsaufwand, was Fehler bei den Teilen oder einen ineffizienten Druckprozess zur Folge haben kann.
Professionelle 3D-Drucker wie der SLA-3D-Drucker Form 4 oder die SLS-3D-Drucker der Fuse-Serie bieten oft die Option, Modelle automatisch einzurichten, wobei sie auf ausgiebig getestete Einstellungen und Materialabstimmungen zurückgreifen. Die SLS-Packfunktion, die in PreForm für die Fuse-Serie verfügbar ist, kann sogar die Software von Drittanbietern übertreffen: Sie stapelt und verschachtelt Teile effizient in der Konstruktionskammer und erzielt damit eine höhere Packdichte und niedrigere Kosten pro Teil.
Sobald der Druckvorgang beginnt, können die meisten 3D-Drucker bis zu dessen Abschluss unbeaufsichtigt laufen – auch nachts. Moderne SLA-3D-Drucker wie der Form 4 verfügen über ein Kartuschensystem, das das Material automatisch nachfüllt. Sogar Automatisierungslösungen stehen zur Verfügung – etwa der Form Auto für die Serie Form 3, der das Entfernen der Teile und den Start neuer Drucke automatisiert.
See how to go from design to 3D print with the Form 4 SLA 3D printer. This video covers the basics of how to use Form 4, from the software and materials to printing and post-processing.
Sehen Sie sich die Schritte vom Design zum fertigen 3D-Druck mit dem SLA-3D-Drucker Form 4 an. Dieses Video behandelt die Grundlagen der Bedienung des Form 4, von der Software und den Materialien bis zum Drucken und Nachbearbeiten.
Der Arbeitsprozess besteht sowohl beim FDM-, SLA- als auch SLS-3D-Druck aus drei Schritten: Design, 3D-Druck und Nachbearbeitung.
Zuerst entwerfen Sie mithilfe einer beliebigen CAD-Software oder 3D-Scandaten ein Modell und exportieren dieses in ein 3D-druckbares Dateiformat (STL oder OBJ). Anschließend brauchen Sie eine Druckvorbereitungs- oder Slicer-Software, um die Druckeinstellungen für den Drucker festzulegen und das digitale Modell für den Druck in Schichten zu zerteilen. Der Schritt der Druckausrichtung kann mit einem simplen Klick auf die Funktion „Ein-Klick-Druck“ in Formlabs' Druckvorbereitungssoftware PreForm erledigt sein, oder sich sogar auf die manuelle Auswahl der Druckeinstellungen und die Feinabstimmung der Materialeinstellungen erstrecken. Unabhängig von der Technologie erfordern kostengünstige Geräte in der Regel einen höheren Arbeitsaufwand, was Fehler bei den Teilen oder einen ineffizienten Druckprozess zur Folge haben kann.
Professionelle 3D-Drucker wie der SLA-3D-Drucker Form 4 oder die SLS-3D-Drucker der Fuse-Serie bieten oft die Option, Modelle automatisch einzurichten, wobei sie auf ausgiebig getestete Einstellungen und Materialabstimmungen zurückgreifen. Die SLS-Packfunktion, die in PreForm für die Fuse-Serie verfügbar ist, kann sogar die Software von Drittanbietern übertreffen: Sie stapelt und verschachtelt Teile effizient in der Konstruktionskammer und erzielt damit eine höhere Packdichte und niedrigere Kosten pro Teil.
Sobald der Druckvorgang beginnt, können die meisten 3D-Drucker bis zu dessen Abschluss unbeaufsichtigt laufen – auch nachts. Moderne SLA-3D-Drucker wie der Form 4 verfügen über ein Kartuschensystem, das das Material automatisch nachfüllt. Sogar Automatisierungslösungen stehen zur Verfügung – etwa der Form Auto für die Serie Form 3, der das Entfernen der Teile und den Start neuer Drucke automatisiert.
Erfahren Sie mehr über den SLS-Arbeitsablauf mit den SLS-3D-Druckern der Fuse-Serie. Dieses Video führt Sie durch jeden Schritt des SLS-3D-Druckverfahrens, vom Design und Packen der Konstruktionskammer bis hin zur Pulverrückgewinnung und dem Sandstrahlen.
Der letzte Schritt im Arbeitsprozess ist die Nachbearbeitung. Sie umfasst einige grundlegende Aufgaben wie das Entfernen von Stützstrukturen (FDM und SLA), das Waschen und Nachhärten von Teilen (SLA) oder das Entfernen von überschüssigem Pulver und die Reinigung von Teilen (SLS).
FDM-Teile weisen aufgrund des Drucks mittels „Klebepistolen“-Methode oft klar definierte Schichtlinien auf. Diese Schichtlinien müssen aufwendig geschliffen oder geglättet werden, damit die Teile für anspruchsvollere Anwendungen eingesetzt werden können. Zwar gibt es lösliche Filamente für den Druck von Stützstrukturen, doch bei vielen Teilen müssen dennoch harte Stützen weggeschnitten und die Oberflächen geschliffen werden, um Stützspuren zu entfernen. Diese beiden Schritte können viel Zeit in Anspruch nehmen, was die Gesamtarbeitszeit für den FDM-3D-Druck erhöht und den Durchsatz verringert.
Das Fundament jedes Workflows zur SLA-Nachbearbeitung ist das Entfernen von überschüssigem Kunstharz von der Druckteiloberfläche in einem Alkohol- oder Etherbad. Dieser Waschvorgang kann manuell erledigt werden, oder aber durch den Einsatz einer automatisierten Wascheinheit , die die Druckteile für einen voreingestellten Zeitraum mit der Flüssigkeit umspült. Nach der Spülung benötigen einige SLA-Teile eine Nachhärtung, um ihre optimalen Materialeigenschaften zu erreichen. Auch dies kann mit fortschrittlichen Nachhärtegeräten automatisiert werden.
Zu den grundlegenden Schritten der SLS-Nachbearbeitung gehören das Entfernen von überschüssigem, ungesintertem Pulver von den Teilen und das Bestrahlen mit einem abrasiven Strahlmittel, um sie vollständig zu reinigen und die Oberflächen zu glätten. Einige SLS-Hersteller bieten weder eine Strahlanlage noch ein komplettes Pulverrückgewinnungssystem an, andere wiederum nur zu extrem hohen Preisen. Das SLS-Ecosystem von Formlabs umfasst den Fuse Sift und den Fuse Blast, die den Prozess der Pulverrückgewinnung und Teilereinigung schneller, einfacher und sauberer gestalten.
Weiterhin gibt es fortschrittliche Nachbearbeitungsmethoden für 3D-Drucke wie Beschichten, Glätten, Lackieren, Dampfglätten oder Galvanisieren. Mit solchen Verfahren lassen sich die Ästhetik, die mechanischen Eigenschaften und die Gesamtleistung verbessern, um die Teile für eine breite Palette von Anwendungen tauglich zu machen. Wenn Sie mehr über die Nachbearbeitung erfahren möchten, lesen Sie unsere vollständigen Leitfäden zur Nachbearbeitung für den SLA- und SLS-3D-Druck.
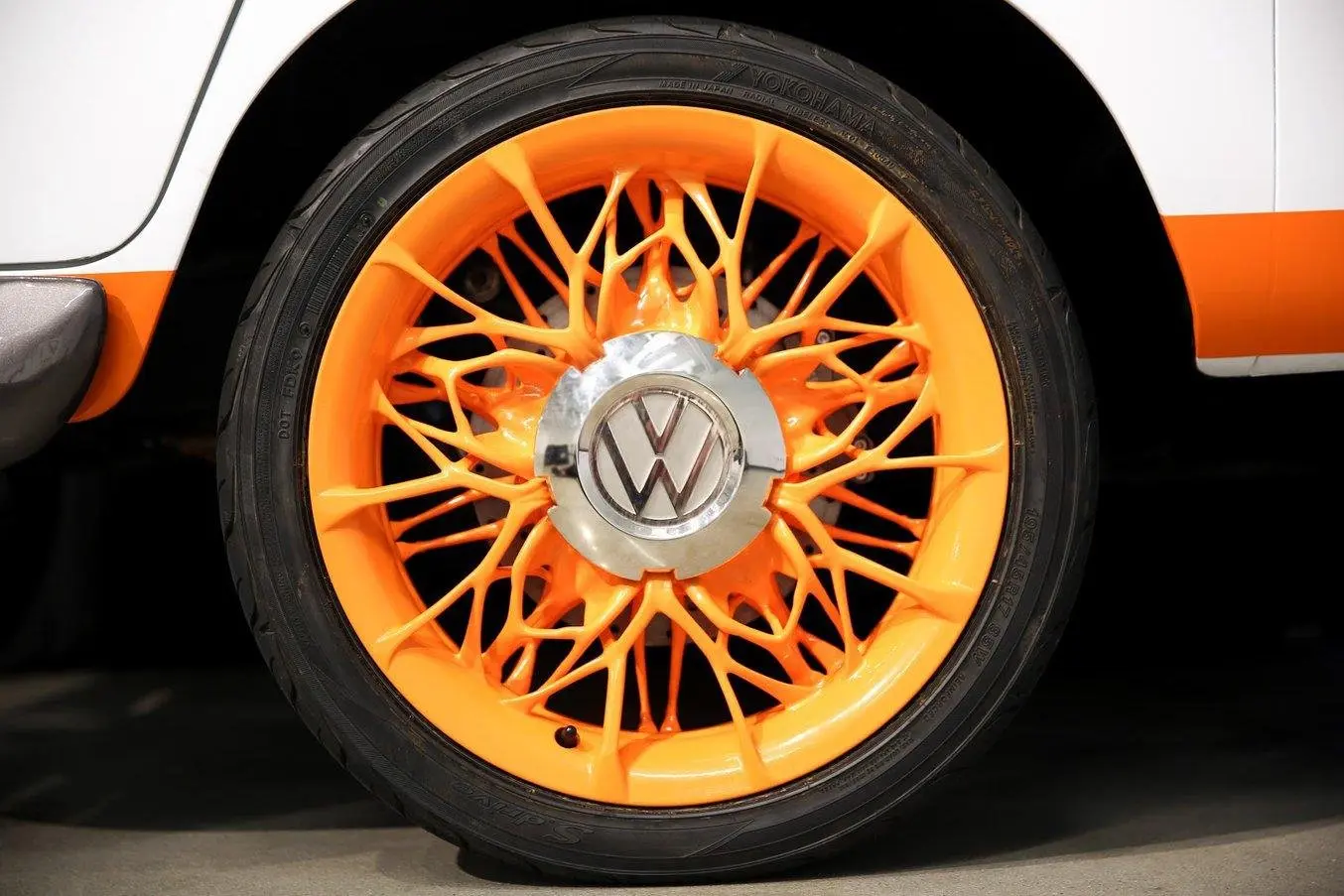
Fortgeschrittene Nachbearbeitungstechniken für den 3D-Druck
In diesem Webinar erfahren Sie alles Wissenswerte zu mehr als 11 fortgeschrittenen Nachbearbeitungstechniken für den 3D-Druck, unter anderem Cerakote-Beschichtung, Galvanisierung und chemische Dampfglättung.
Materialien und Anwendungen
Die Wahl des richtigen 3D-Druckprozesses ist erst die halbe Miete. Letzten Endes sind großteils die 3D-Druckmaterialien ausschlaggebend für die gewünschten funktionalen und mechanischen Eigenschaften, wie auch für die Optik.
Die Leistung von FDM-Teilen aus Filament, SLA-Teilen aus Kunstharz und SLS-Teilen auf Pulverbasis lässt sich oft nur schwer direkt vergleichen, da die drei Technologien nicht die gleichen Materialien verwenden oder Teile auf dieselbe Weise herstellen. Es gibt jedoch in allen Druckverfahren analoge Materialien, sodass sich auch beim Wechsel von einer Technologie zur anderen leicht die gleichen (oder sehr ähnliche) Materialeigenschaften erzielen lassen.
Filamente für Schmelzschichtung (FDM) | Kunstharze für Stereolithografie (SLA) | Pulver für selektives Lasersintern (SLS) | |
---|---|---|---|
Allgemeine Verwendung | PLA | Standard-Kunstharze (matt, transparent, verschiedene Farben) | Nylon 12 |
Robuste technische Materialien | ABS, Nylon, PETG | Kunstharzfamilie Tough und Durable | Nylon 12, Nylon 11, Polypropylen |
Starre technische Materialien | PEEK, ULTEM, Verbundwerkstoffe (glasfaser- oder carbonfaserverstärkt) | Steife, feste, starre Harze (glasfaserverstärkt) | Nylon-Verbundwerkstoffe (glasfaser- oder carbonfaserverstärkt) |
Flexible technische Materialien | TPU | Flexible oder Elastomer-Harze, reines Silikon | TPU, Polypropylen, Nylon 11 |
Spezialisierte Materialien | Verbundwerkstoffe (Kohlenstofffaser, Kevlar, Glasfaser) | Flammhemmende Harze, Feingussmaterialien, technische Keramik, Wachsverbundstoffe, (zahn-)medizinische Materialien | Nylon-Verbundwerkstoffe (glasfaser- oder carbonfaserverstärkt) |
FDM-Drucker verwenden in erster Linie Filamente aus gängigen und bekannten Thermoplasten wie ABS und PLA. Technische Materialien wie Nylon, PETG oder TPU und Hochleistungsthermoplaste wie PEEK oder carbonfaserverstärkte Verbundstoffe sind ebenfalls verfügbar, jedoch häufig nur mit ausgewählten professionellen FDM-Druckern kompatibel.
Bei FDM-Filamenten handelt es sich oft um die gleichen Materialien, die auch für Massenproduktionsverfahren wie Spritzguss oder Thermoformen verwendet werden. Aufgrund dieses gemeinsamen Nenners ist FDM als Prototyping-Option eine naheliegende Wahl, da darauf Verlass ist, dass das Material während des gesamten Design- und Fertigungsprozesses dasselbe bleibt. Allerdings erschwert das FDM-3D-Druckverfahren die Verwendung der Teile für funktionalere Anwendungen, da es Schichtlinien hinterlässt und die funktionale Festigkeit beeinträchtigt.
FDM-Teile eignen sich hervorragend für schnelle Überprüfungen im Produktdesign, um zu validieren, ob ein Teil das richtige Aussehen hat, oder für Ausbildungszwecke bei der Lehre von 3D-Drucktechnologien. Für das Prototyping von Konsumgütern bieten FDM-Teile eine kostengünstige Lösung, um sich einen Eindruck von der Optik und dem Handgefühl eines Teils zu verschaffen.
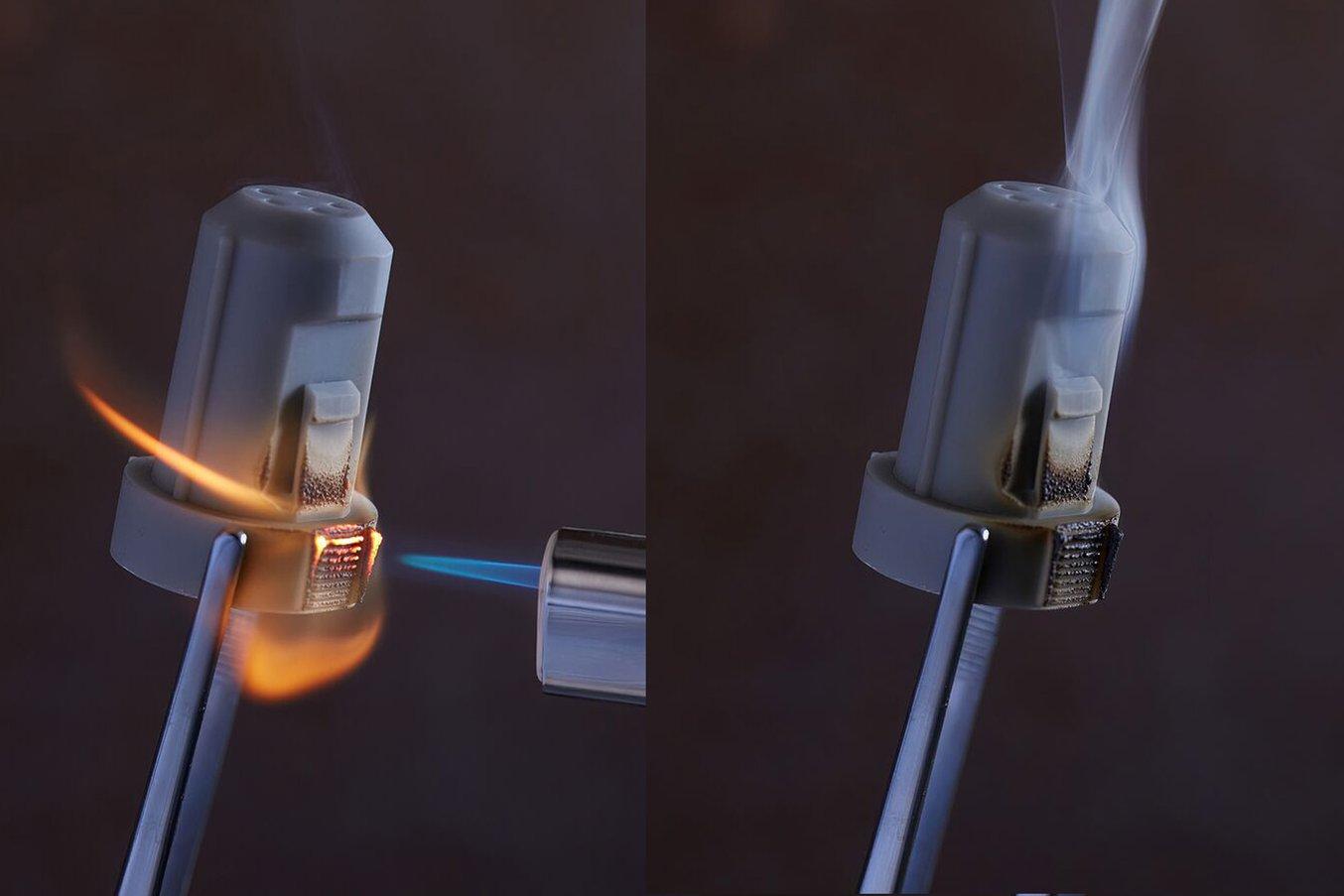
Formlabs' Flame Retardant Resin ist ein mit UL 94 Blue Card zertifiziertes Spezialkunstharz zur Herstellung selbstverlöschender, halogenfreier Teile.
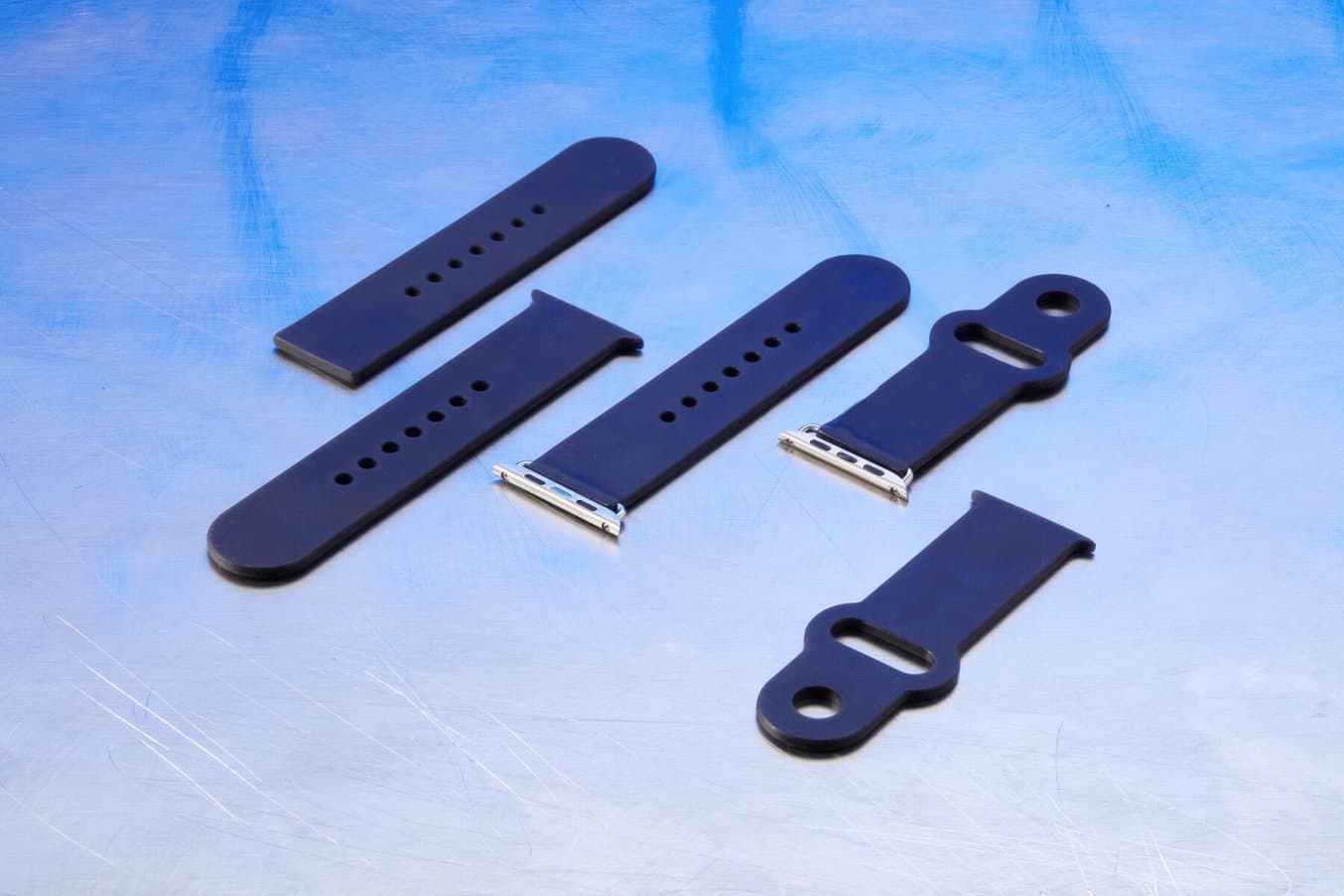
Silicone 40A Resin ist ein reines Silikon mit mechanischen Eigenschaften, die in Maschinenbau und Produktentwicklung altbekannt sind.
Die Materialien für SLA-3D-Drucker werden speziell formuliert und können sich von Hersteller zu Hersteller unterscheiden. Die Vorteile der Formulierung eigener Harze liegen darin, dass die Hersteller ihre Maschinen umfassend für die Verwendung ihrer Kunstharze kalibrieren können, was eine höhere Genauigkeit und wiederholbare Ergebnisse gewährleistet. Der Nachteil ist, dass viele Kunden mit SLA-Kunstharzen nicht im gleichen Maße vertraut sind, was zu Wissenslücken und damit zu mangelnder Akzeptanz führen kann. Eigens formulierte Harze ermöglichen es SLA-Herstellern jedoch, spezielle Materialien für fortgeschrittene Anwendungen anzubieten, wie z. B. Dentalharze für Langzeitprothesen oder technische Keramikmaterialien.
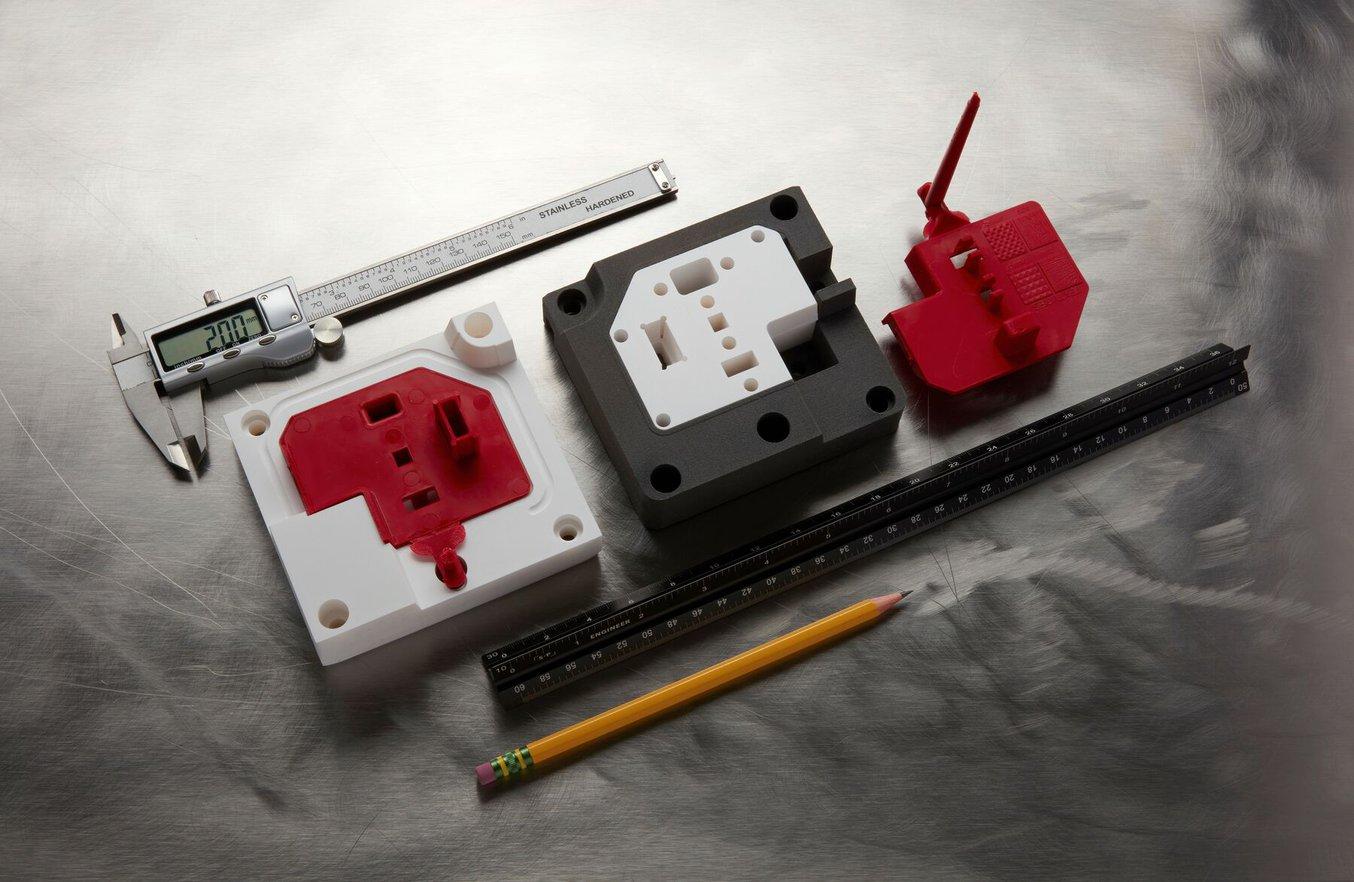
Rigid 10K Resin ist ein hochgradig glasgefülltes Material mit extrem hoher Steifigkeit, das glas- und fasergefüllten Thermoplasten ähnelt. Es eignet sich ideal für Anwendungen im Rapid Tooling, beispielsweise für Spritzguss, Blasformen oder Thermoformen.
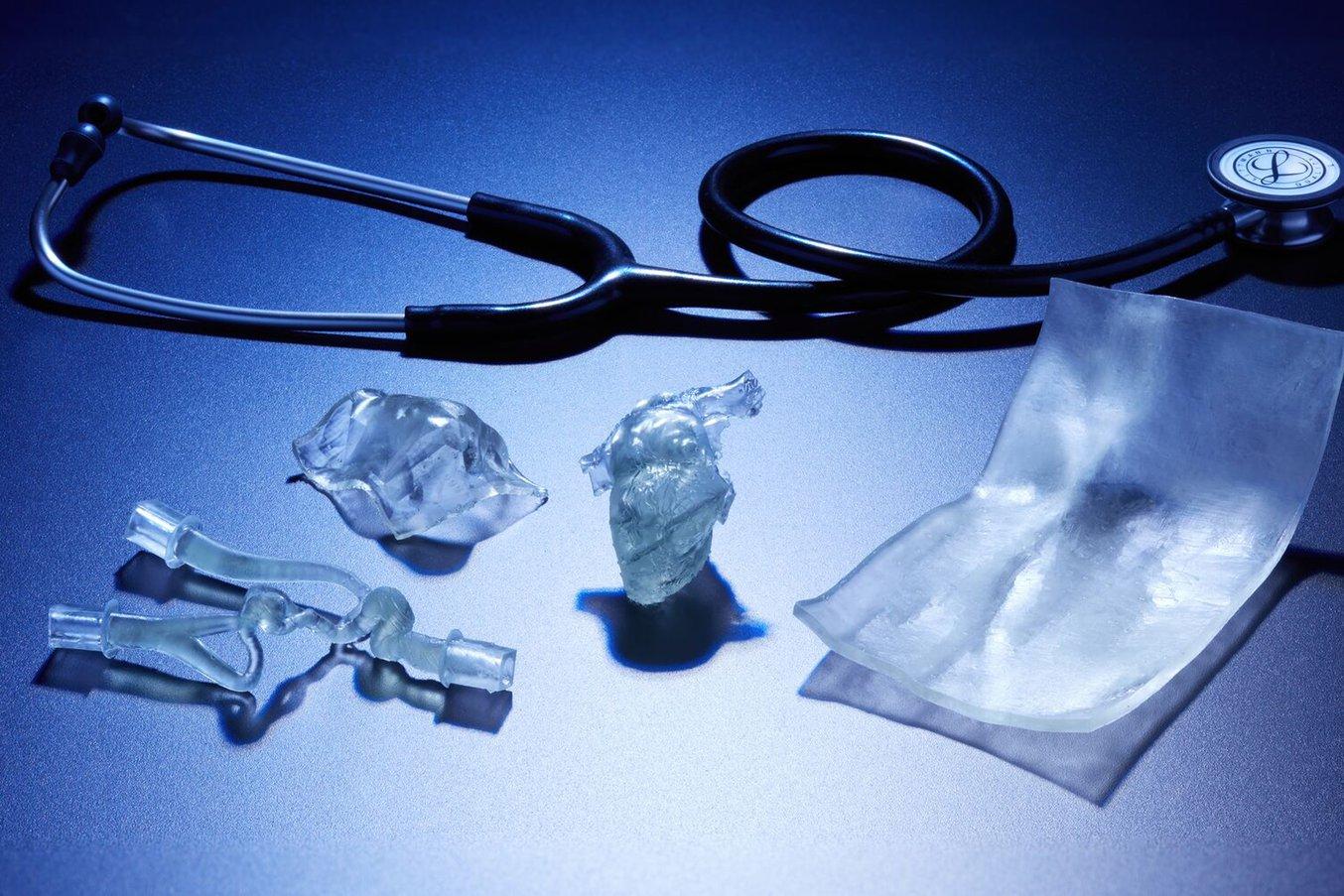
BioMed Elastic 50A Resin ermöglicht der Gesundheitsbranche den Druck weicher, elastischer, biokompatibler Teile mit komplexen Formen, wie etwa patientenspezifischer Medizinprodukte oder Modellen von Weichgewebe.
Im Allgemeinen können SLA-3D-gedruckte Teile vom Design bis zur Fertigung in jeder Phase verwendet werden. Aufgrund ihrer Isotropie und der ausgezeichneten Oberflächenbeschaffenheit eignen sie sich ideal für funktionales Prototyping, Go-/No-Go-Tests, die Produktion von Endverbrauchsteilen und Fertigungshilfsmittel. Dank der Möglichkeit, einzigartige, neue Formulierungen wie technische Keramiken oder ausbrennbare Wachsverbundstoffe zu entwickeln, ist SLA für bestimmte Branchen und Anwendungen eine perfekte Lösung. Für allgemeinere, branchenübergreifende Anwendungen bieten SLA-Kunstharze die nötige Haltbarkeit und Festigkeit, um als End-of-Arm-Werkzeuge, Robotergehäuse, Dichtungen, chirurgische Bohrschablonen und vieles mehr verwendet zu werden. Die Bandbreite der möglichen Formulierungen eröffnet nahezu grenzenlose Möglichkeiten zum Einsatz von Teilen aus Kunstharz.
Formlabs bietet mehr als 40 einzigartige, speziell formulierte Kunstharze für den SLA-3D-Druck, darunter fortschrittliche technische Keramik, flammhemmende Harze mit guten Bewertungen hinsichtlich Rauch und Toxizität, statisch ableitende Materialien und sogar Materialien für Medizinprodukte wie Zahnprothesen oder permanente Kronen.
Bei SLS-3D-Druckmaterialien handelt es sich um bekannte Thermoplaste in Pulverform, wie Nylon, TPU und Polypropylen. Diese Pulver bieten eine hohe Leistung und ihr Materialverhalten ist wohlbekannt. Einige Hersteller von SLS-3D-Druckern bieten eigene Formulierungen dieser Pulver an, andere vertreiben Pulver anderer Hersteller als White-Label-Lösung. Durch die Kombination branchenüblicher Materialien mit geometrischer Flexibilität, hoher Produktionskapazität und Festigkeit eignet sich der SLS-3D-Druck ideal für jedwede Anwendung – vom Prototyping über Funktionstests und Fertigungshilfen bis hin zur Endproduktion.
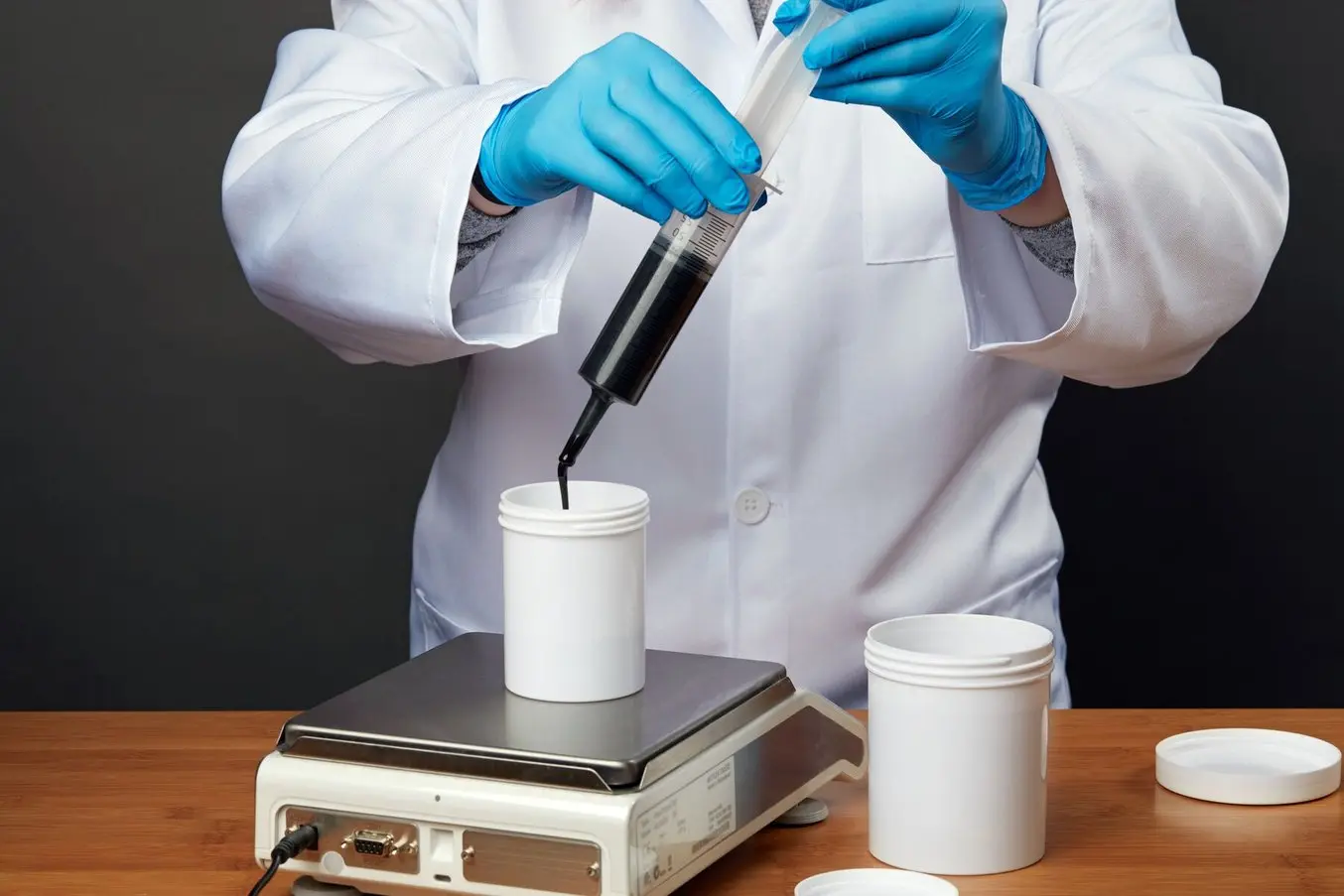
Formlabs als offene Plattform
Maximieren Sie das Potenzial Ihres 3D-Druckers mit Formlabs Developer Platform. Drucken Sie auf Formlabs-3D-Druckern mit jedem bei 405 nm härtenden Photopolymerharz bzw. jedem bei 1064 nm sinterbaren Pulver, legen Sie Ihre Druckeinstellungen individuell fest oder entwickeln Sie Softwareintegrationen.
Fertigungsvolumen
Das Fertigungsvolumen der Technologien FDM, SLA und SLS fällt sehr unterschiedlich aus. Obwohl jede Technologie auch im Großformat verfügbar ist, haben die gängigsten FDM- und SLA-3D-Drucker Desktop- oder Benchtop-Format, während die gängigsten SLS-3D-Drucker im Benchtop- oder noch größeren Format verfügbar sind.
FDM-3D-Drucker gibt es in einer Vielzahl von Größen und Fertigungsvolumen. Das FDM-Verfahren wird durch die Größe nicht begrenzt oder beeinträchtigt; eine hochpräzise Düse kann auch großformatige Teile herstellen, einzig das Motorsystem hierfür ist größer und langsamer, da es einen größeren Bereich abdecken muss. Auf dem Markt sind auch riesige FDM-3D-Drucker mit Druckgehäusen erhältlich, die eher an kleine Räume erinnern als an Benchtop- oder Desktop-Geräte. Diese sind jedoch extrem unüblich. In der Regel sind FDM-3D-Drucker Desktop- oder Benchtop-Geräte und werden meist für schnelles Prototyping oder als Lehrmittel in Klassenzimmern und FabLabs eingesetzt. Das Fertigungsvolumen gängiger FDM-3D-Drucker für den Desktop liegt normalerweise im Bereich von 200 x 200 x 200 mm.
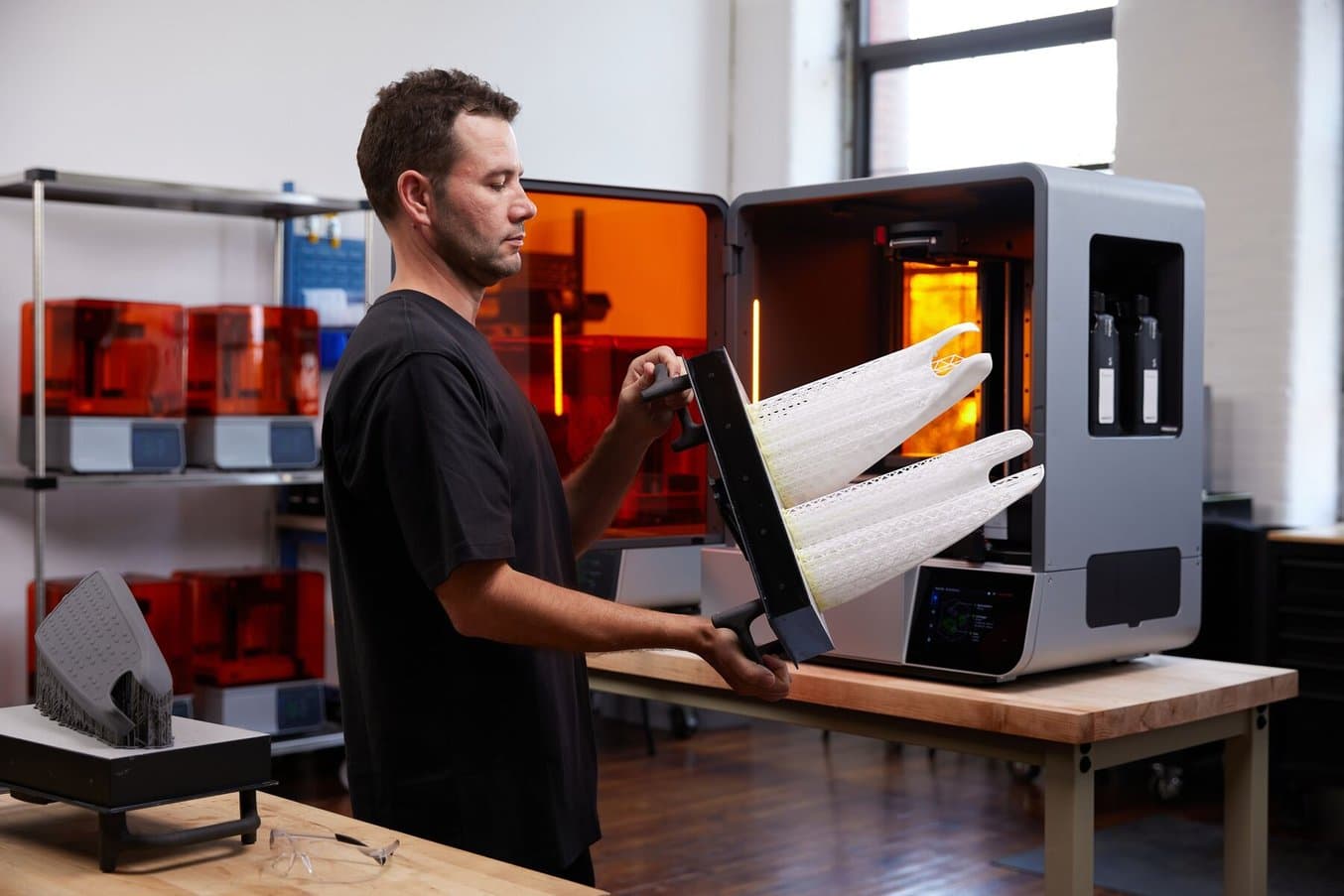
Der Form 4L ist ein großformatiger SLA-3D-Drucker, der sich ideal für Prototypen in voller Größe oder durchsatzstarke Anwendungen in Rekordgeschwindigkeit eignet – die meisten Drucke werden in unter sechs Stunden abgeschlossen, und sogar Druckteile in voller Höhe des Fertigungsvolumens benötigen weniger als einen Tag.
SLA-3D-Drucker sind ebenfalls in verschiedenen Größen erhältlich, vom Desktop- bis zum großen Industriedrucker. In der Vergangenheit waren laserbasierte SLA-3D-Drucker monolithische Großanlagen; sie beanspruchten meterweise Bodenfläche und benötigten zusätzliche Belüftungssysteme und spezielle Schaltkreise. Diese industriellen Systeme kamen in den vergangenen Jahrzehnten häufiger in Unternehmen zum Einsatz, die sowohl die hohen Anschaffungs- und Wartungskosten stemmen als auch den höheren Platz- und Infrastrukturbedarf von konventionellen Stereolithografie-Druckern bedienen konnten.
Kunstharz-3D-Drucker im Desktop-Format wurden durch die Erfindung des invertierten SLA-3D-Drucks ermöglicht. Mit der Implementierung der Technologie durch mehr und mehr Hersteller wurden kleinere Drucker mit einem quaderförmigen Fertigungsvolumen von ca. 10–20 cm in jeder Dimension zur Norm. Der Form 3+ von Formlabs bietet beispielsweise ein Fertigungsvolumen von 14,5 × 14,4 × 19,3 cm, während der Form 4 mit 20 × 12,5 × 21 cm ein 30 % größeres Fertigungsvolumen bietet.
Ebenso wurde auch der Kunstharz-3D-Druck im Benchtop-Format erst durch die Kombination der invertierten SLA-Technologie mit verbesserten Ablösetechniken möglich. Benchtop-3D-Drucker wie der Form 4L, der ein Fertigungsvolumen von 35,3 x 19,6 x 35 cm bietet, sind kompakt und einfach zu bedienen und bieten ein vergleichbares Fertigungsvolumen wie die traditionellen großen Industriesysteme. Derartige Geräte eignen sich perfekt für die Prototypenfertigung von Konsumgütern in voller Größe sowie für die Herstellung von Endprodukten mithilfe von 3D-gedrucktem Rapid Tooling.
SLS-3D-Drucker waren traditionell nur in großen Formaten erhältlich und waren typischerweise größer als FDM- oder SLA-Drucker für den Desktop. In jüngsten Jahren hat es allerdings auch Bestrebungen gegeben, Desktop-SLS-Drucker auf den Markt zu bringen. Die überwiegende Mehrheit der SLS-3D-Drucker hat jedoch Benchtop- oder ein noch größeres Format – wobei herkömmliche Industriemaschinen große Stellflächen benötigen. Die Fuse-Serie von Formlabs mit ihrem Bauvolumen von 16,5 × 16,5 × 30 cm lieferte den ersten Drucker, der die SLS-Technologie sowohl in Bezug auf die Kosten als auch auf die Größe zugänglich machte – dank der Fuse-Serie konnten kleine Unternehmen mit begrenztem Platzangebot endlich betriebsinterne Geräte anschaffen.
Geschwindigkeit und Durchsatz
Da mehr Unternehmen sich heute zur Produktion und zur schnellen Designiteration auf 3D-Druck stützen, gewinnen die Druckgeschwindigkeit und der Durchsatz bei der Auswahl der Technologie an Bedeutung. Der ideale 3D-Drucker produziert in kurzer Zeit hochwertige Teile, ohne Abstriche bei der Genauigkeit, Zuverlässigkeit oder Materialleistung zu machen.
Die Geschwindigkeit des FDM-3D-Drucks wird durch das Extrusionsverfahren und die Motorleistung bestimmt. Um präzise Teile zu erstellen, müssen FDM-3D-Drucker das Filament mit einer bestimmten, konstanten Geschwindigkeit extrudieren und die Düse in der XY-Ebene gleichmäßig bewegen. Eine Beschleunigung dieses Prozesses kann zu Schwankungen bei den mechanischen Eigenschaften des Filaments und zu ungenauen Ergebnissen führen.
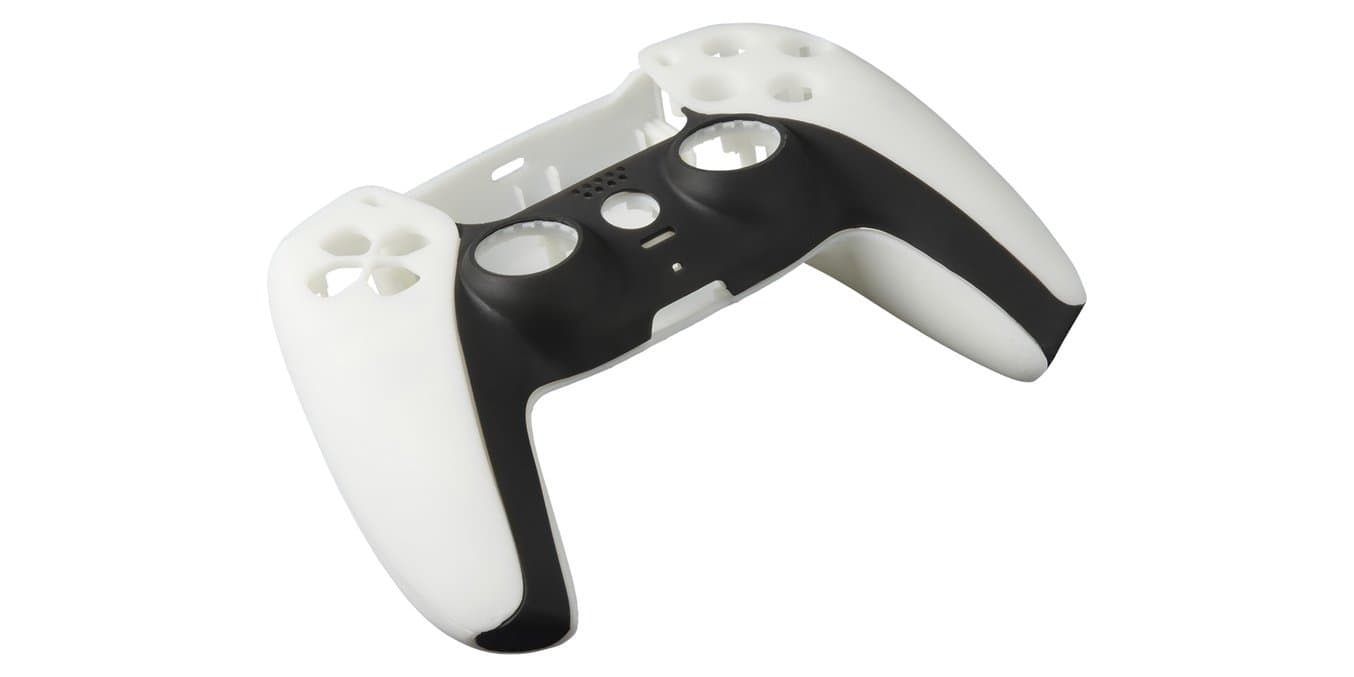
Druckgeschwindigkeit im Vergleich: Gaming-Controller
FDM-3D-Druck wählen | SLA-3D-Druck | SLS-3D-Druck | |
---|---|---|---|
1 Baugruppe (3 Teile) | 10 h 32 min | 2 h 36 min | 3 h 52 min Druck (6 h 52 min Abkühlung) |
5 Baugruppen (15 Teile) | 52 h 40 min | 13 h | 9 h 38 min Druck (13 h 47 min Abkühlung) |
Vergleich von Druckern und Druckparametern:
- FDM-3D-Drucker: Bambu Lab X1, PLA Basic, 120 Mikrometer Schichthöhe, 15 % Fülldichte
- SLA-3D-Drucker: Form 4, Grey Resin, 100 Mikrometer Schichthöhe
- SLS-3D-Drucker: Fuse 1+ 30W, Nylon 12 Powder, 110 Mikrometer Schichthöhe
Beim SLA-3D-Druck fällt die typische Druckgeschwindigkeit je nach Druckverfahren unterschiedlich aus, wobei der MSLA-Druck am schnellsten ist. Neueste MSLA-3D-Drucker wie der Form 4 und Form 4L von Formlabs nutzen eine Kombination aus leistungsstarkem Drucksystem und fortschrittlichem optischen System, um die einzelnen Schichten in wenigen Sekunden auszuhärten.
Der Form 4 und der Form 4L wurden entwickelt, um Teile mit Geschwindigkeiten von bis zu 100 mm pro Stunde herzustellen. Dafür kommen speziell entwickelte Materialien wie Fast Model Resin zum Einsatz. Die meisten Drucke mit dem Form 4 sind in weniger als zwei Stunden fertig, ganz unabhängig vom verwendeten Material. Das erlaubt mehrere Designiterationen am selben Tag. Und auch mit dem Form 4L sind die meisten Drucke in weniger als sechs Stunden abgeschlossen. Selbst Drucke, die die volle Höhe des Druckers erreichen, oder Großserien, die die gesamte Konstruktionsplattform mit Teilen vollpacken, werden in weniger als einem Tag gedruckt. Das eröffnet gleichzeitige Iterationen großer Teile oder die Produktion in hohen Stückzahlen.
Alle 3D-Druckverfahren sind im Laufe der Zeit schneller geworden, aber keines kann mit den Fortschritten beim Kunstharzdruck mithalten. Wenn diese Geschwindigkeit Tag für Tag und Woche für Woche addiert wird, sind die Durchsatzvorteile außergewöhnlich. Der Form 4 und Form 4L halten jetzt mit Hochdurchsatz-Technologien wie dem Spritzguss mit. Der Druck voller Konstruktionsvolumen im Laufe von wenigen Stunden, mehrmals am Tag, kann die Produktion einer Spritzgussmaschine mit mittlerem Volumen erreichen – ohne die hohen Anfangskosten für die Produktionswerkzeuge.
SLS-3D-Drucker sind schneller als FDM-3D-Drucker, weil ihre Hochleistungslaser die einzelnen Pulverschichten schneller abtasten, als sich eine Extruderdüse über ein FDM-Druckbett bewegen kann. Allerdings ist die Laserbewegung dennoch langsamer als das Aufleuchten der Lichtquelle, die bei DLP- oder MSLA-Drucktechnologien verwendet wird. Obwohl sie streng genommen nicht in die Druckzeit einfließt, muss beim SLS-3D-Druck auch die Abkühlzeit der Konstruktionskammer berücksichtigt werden. Da der Laser das Pulver bei extrem hoher Temperatur sintert, muss die Kammer abkühlen, bevor sie nachbearbeitet werden kann, was zu einer längeren Gesamtvorlaufzeit für die Teile führen kann.
Für die Produktion ist diese kombinierte Druck- und Nachbearbeitungszeit für SLS-Teile jedoch oft nicht von Belang. Obwohl die Druckzeit für einzelne Teile etwas länger ausfallen kann als bei anderen Technologien, ist der Gesamtdurchsatz von SLS-3D-Druckern hervorragend, da sich viele Teile in einer Konstruktionskammer unterbringen lassen. Dank des größeren Fertigungsvolumens und der Möglichkeit der Verschachtelung können Teile in der Kammer dicht gepackt und so das gesamte Volumen ausgenutzt werden. So kann zum Beispiel ein vollgepackter Druckauftrag auf dem Fuse 1+ 30W über Nacht abgeschlossen werden, während die Abkühlung tagsüber außerhalb des Druckers erfolgt, was die Bereitstellung von Teilen am selben Tag und einen 24/7-Durchsatz ermöglicht. Darüber hinaus kann die Nachbearbeitung recht schnell gehen, denn Maschinen wie der Fuse Sift und Fuse Blast automatisieren einen Großteil davon und es sind keine Stützstrukturen zu entfernen.
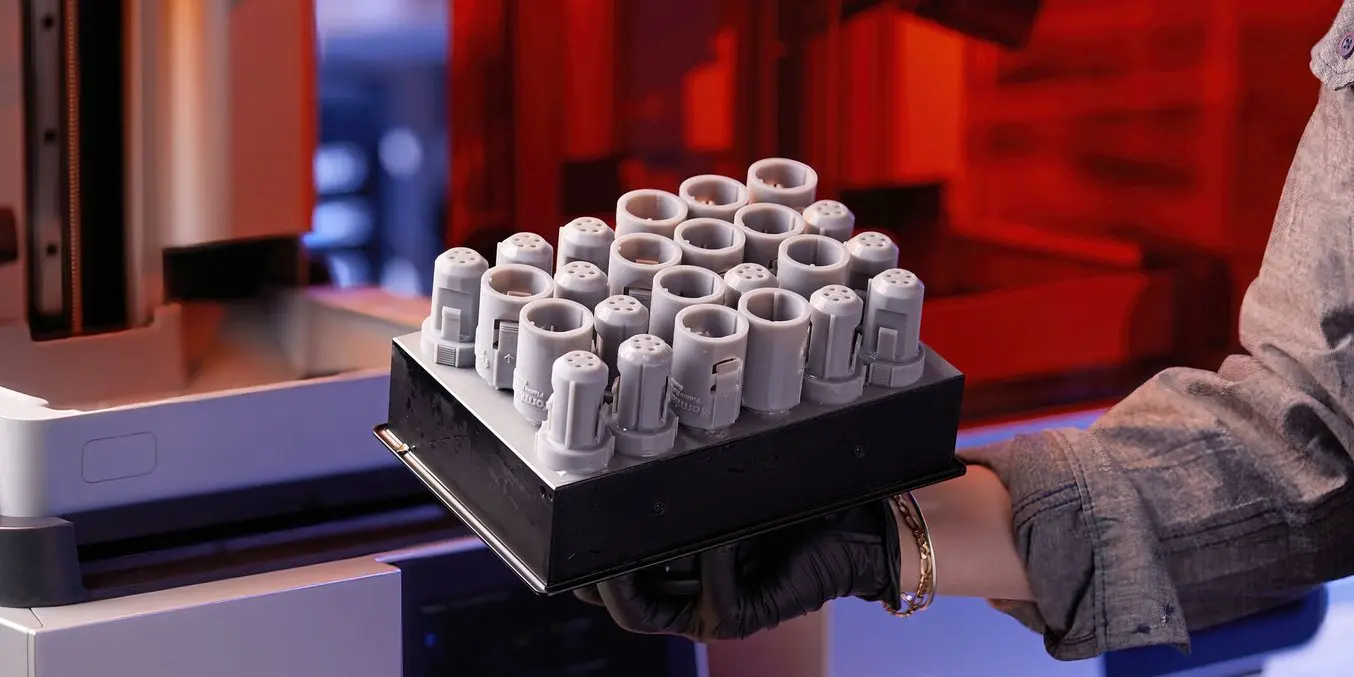
Druckgeschwindigkeit im Vergleich: Elektrischer Verbinder
FDM-3D-Druck wählen | SLA-3D-Druck | SLS-3D-Druck | |
---|---|---|---|
1 Baugruppe (2 Teile) | 2 h 38 min | 1 h 3 min | 3 h 30 min Druck (6 h 27 min Abkühlung) |
50 Baugruppen (100 Teile) | 84 h | 13 h 2 min | 12 h 59 min Druck (13 h 49 min Abkühlung) |
Vergleich von Druckern und Druckparametern:
- FDM-3D-Drucker: Bambu Lab X1, PLA Basic, 120 Mikrometer Schichthöhe, 15 % Fülldichte
- SLA-3D-Drucker: Form 4, Grey Resin, 100 Mikrometer Schichthöhe
- SLS-3D-Drucker: Fuse 1+ 30W, Nylon 12 Powder, 110 Mikrometer Schichthöhe
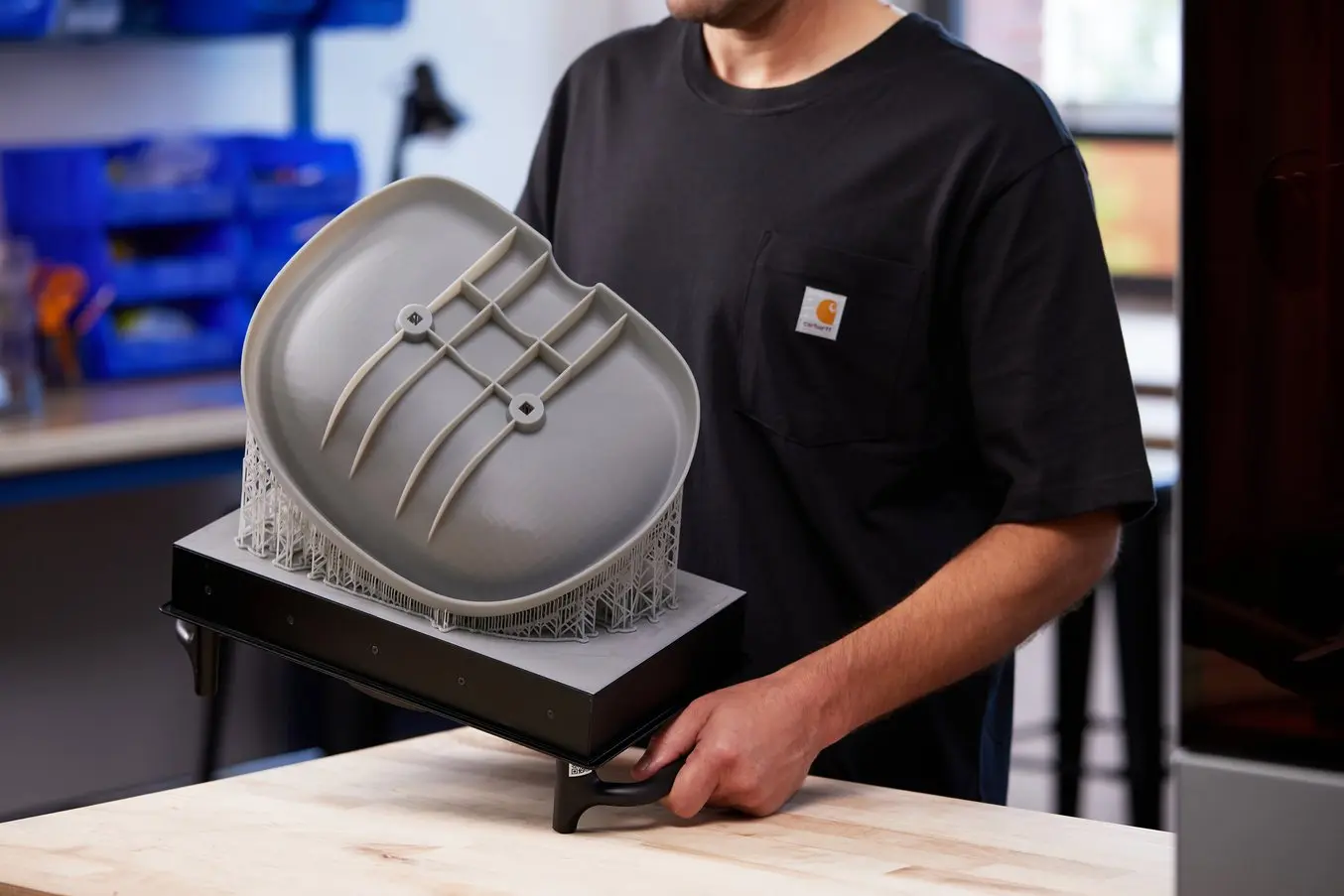
Druckgeschwindigkeit im Vergleich: Sitzprototyp von Radio Flyer
FDM-3D-Druck wählen | SLA-3D-Druck | |
---|---|---|
1 Prototyp | 42 h 3 min | 2 h 37 min |
Vergleich von Druckern und Druckparametern:
- FDM-3D-Drucker: Ultimaker S7, PLA, 100 Mikrometer Schichthöhe, 20 % Fülldichte
- SLA-3D-Drucker: Form 4, Fast Model Resin, 200 Mikrometer Schichthöhe
Kosten und Kapitalrendite
Wie viel kosten FDM-, SLA- und SLS-3D-Drucker und wie schnell rentieren sie sich? Um Ihre Kapitalrendite zu berechnen, müssen Sie den Anschaffungspreis, die laufenden Betriebskosten, die Materialkosten und die Arbeitskosten kennen.
Eines der zentralen Verkaufsargumente für FDM-Drucker sind die geringen Gerätepreise. Da FDM-Drucker für Einsteiger für niedrige dreistellige Beträge zu haben sind, können Hobbyisten und kleine Unternehmen FDM ausprobieren und entscheiden, ob 3D-Druck etwas ist, womit sie arbeiten möchten. Für diejenigen, die nicht wissen, wo sie anfangen sollen, sind die niedrigen Kosten eines FDM-Druckers oft überzeugend genug, um einen Kauf zu rechtfertigen. Jedoch können solche preiswerten FDM-Lösungen unzuverlässig sein und erfordern häufig Fachkenntnis, um sie langfristig am Laufen zu halten.
Professionelle Desktop-FDM-Drucker sind benutzerfreundlicher und besser für Unternehmen geeignet, bei Preisen zwischen 2000 € und 8000 €. Industrielle Systeme sind ab 15 000 € erhältlich. Sie bieten im Allgemeinen bessere Qualität, eine höhere Druckqualität und größere Fertigungsvolumen. Wenngleich sich diese Geräte für die Herstellung von Funktionsteilen eignen, gibt es bei diesem Preispunkt viel Konkurrenz, da SLA-Drucker eine größere Palette an Anwendungen und hochwertigere Drucke bieten.
Am unteren Ende der Skala stehen preiswerte Kunstharz-3D-Drucker, die für 200 € bis 1000 € erhältlich sind. Solche Geräte können sich für Hobbyanwendungen oder für den Einstieg eignen, aber sie erfordern Kalibrierung und Feinjustierung für jeden Harztyp und sind in der Regel weder zuverlässig noch langlebig. Das führt häufig zu höheren Kosten aufgrund von Wartung, vergeudeter Zeit, Fehldrucken und Materialverschwendung.
Professionelle SLA-3D-Drucker liegen typischerweise im Bereich von 2500 € bis 10 000 €, während großformatige Kunstharz-3D-Drucker für 5000 € bis 25 000 € erhältlich sind.
Im Bereich der SLS-Technologie ist die Auswahl kleiner. SLS-3D-Drucker haben in der Regel ein höheres Preisniveau als FDM- oder SLA-Drucker, obwohl auch SLS in den letzten Jahren erschwinglich geworden ist. Das macht es kleineren Unternehmen möglich, Kontrolle über ihre Produktion zu übernehmen, und verschafft größeren Unternehmen flexible Fertigungsoptionen.
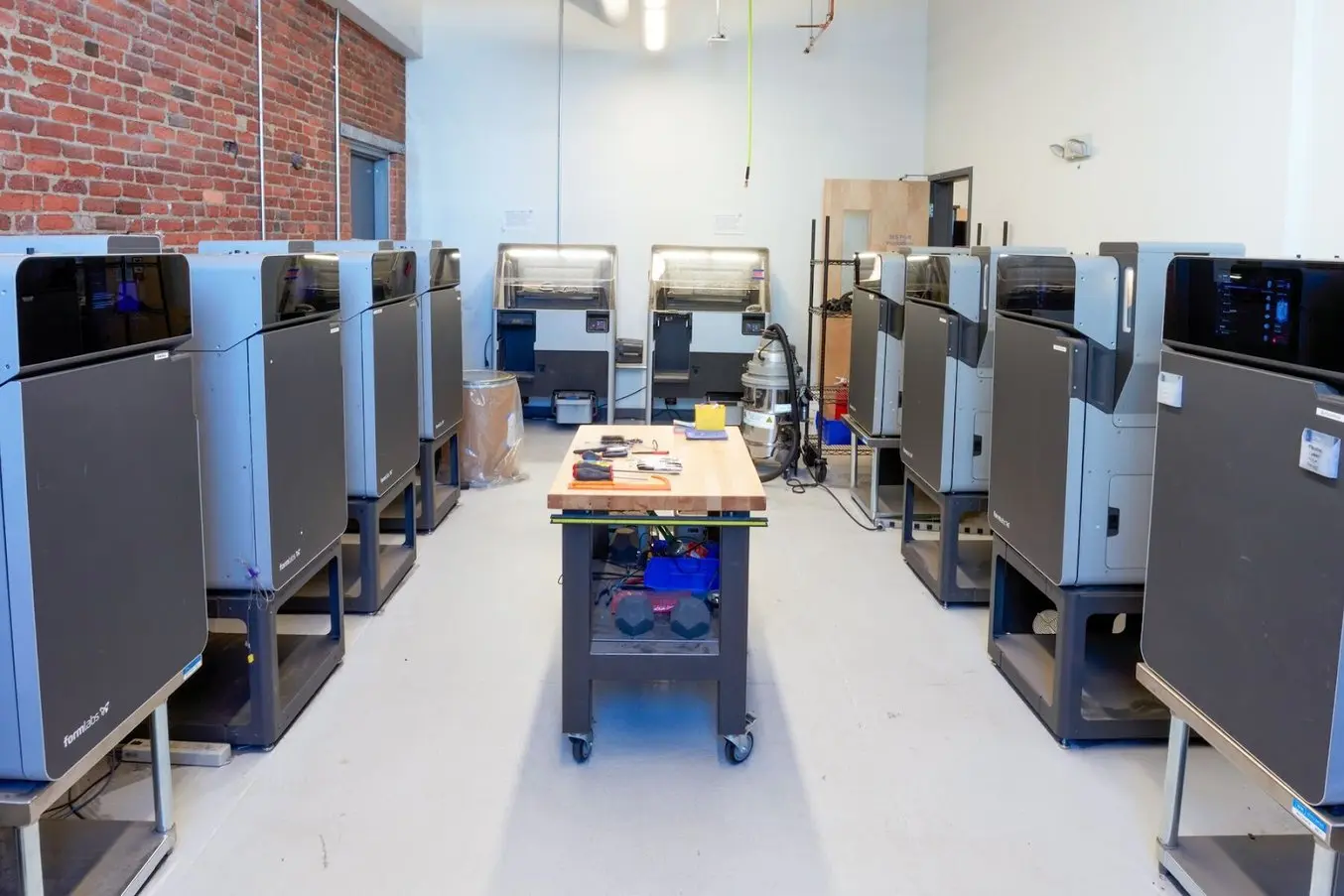
Erschwingliche SLS-Geräte haben es möglich gemacht, auch bei dieser industriellen Technologie hochzuskalieren. Zugängliche, erschwingliche Flotten von SLS-Druckern machen den 3D-Druck zu einer kosteneffizienten Methode zur Herstellung von Teilen.
In der Vergangenheit waren SLS-Drucker fast ausschließlich im Bereich von 200 000 € und mehr angesiedelt. Mit der Einführung der Fuse-Serie wurde SLS zum ersten Mal zugänglich, und die Möglichkeit, einen SLS-Drucker für weniger als 30 000 € (Drucker inkl. Entpulverungskit) zu erwerben, war etwas völlig Einzigartiges. Die Fuse-Serie setzte neue Maßstäbe in Sachen Zugänglichkeit, ohne Kompromisse bei der industriellen Qualität oder der Leistung einzugehen. Dass ein gesamtes Ecosystem, einschließlich der Pulverwiederverwertung und der Reinigung mit Fuse Sift und Fuse Blast, für unter 60 000 € erhältlich ist, ist revolutionär und hat kleinen Unternehmen, Einzelpersonen und Bildungseinrichtungen die Möglichkeit eröffnet, erstmals Kapazitäten für leistungsstarken 3D-Druck durch Pulverbettfusion ins eigene Haus zu holen. Die nächst teurere Option kostet sechsstellige Beträge und kann Servicepläne von bis zu 30 000 € pro Jahr einschließen. Indem Formlabs die Vorgängerversion der Fuse-Serie, den Fuse 1, zu einem noch günstigeren Preis anbietet, macht es den SLS-Druck sogar noch erschwinglicher. Für Prototyping-Labore, bei denen hohe Stückzahlen und Durchsatz nicht im Vordergrund stehen, liefert der Fuse 1 noch immer konstant hochwertige SLS-Teile.
Bei der Betrachtung der Betriebskosten von 3D-Druckern sind die Kosten für Druck- und Verbrauchsmaterial nicht zu vernachlässigen. FDM-Filamente sind im Vergleich zu Kunstharzen für den SLA-3D-Druck relativ kostengünstig, sowohl aufgrund ihrer weiten Verbreitung als auch wegen des weniger komplexen Herstellungsprozesses.
Gängige FDM-Materialien wie ABS, PLA und ihre verschiedenen Mischungen sind ab etwa 30 €/kg verfügbar, während Spezialfilamente für technische Anwendungen 100 bis 150 €/kg kosten können. Lösbare Stützstrukturmaterialien für FDM-3D-Drucker mit doppelter Extrusionsdüse kosten 100 bis 200 €/kg. Diese Filamente sind leicht zu beschaffen, und aufgrund ihrer weit verbreiteten Verwendung in einer Reihe von Herstellungsverfahren hat der Wettbewerb die Preise gedrückt. Filament ist lagerstabil und hat kein Verfallsdatum, sodass die Anbieter ihre Preise ohne Berücksichtigung von Engpässen oder Nachfrageschwankungen festlegen können.
Bei SLA-Kunstharzen ist die Formulierung, Herstellung und Lagerung komplizierter, was insgesamt zu ihrem höheren Preis beiträgt. Zwar gibt es kostengünstigere Harze, die in der Regel von Drittanbietern separat vom Drucker als Lösung für bestehende Geräte verkauft werden, doch diese erfordern mehr Feinabstimmung und gehen mit Problemen wie starken Gerüchen oder potenziell schädlichen Chemikalien einher.
Die Standard-Kunstharze von Formlabs kosten 99 € pro Liter, sodass hochwertige 3D-Druckteile für verschiedene Anwendungen und Branchen leicht zugänglich werden.
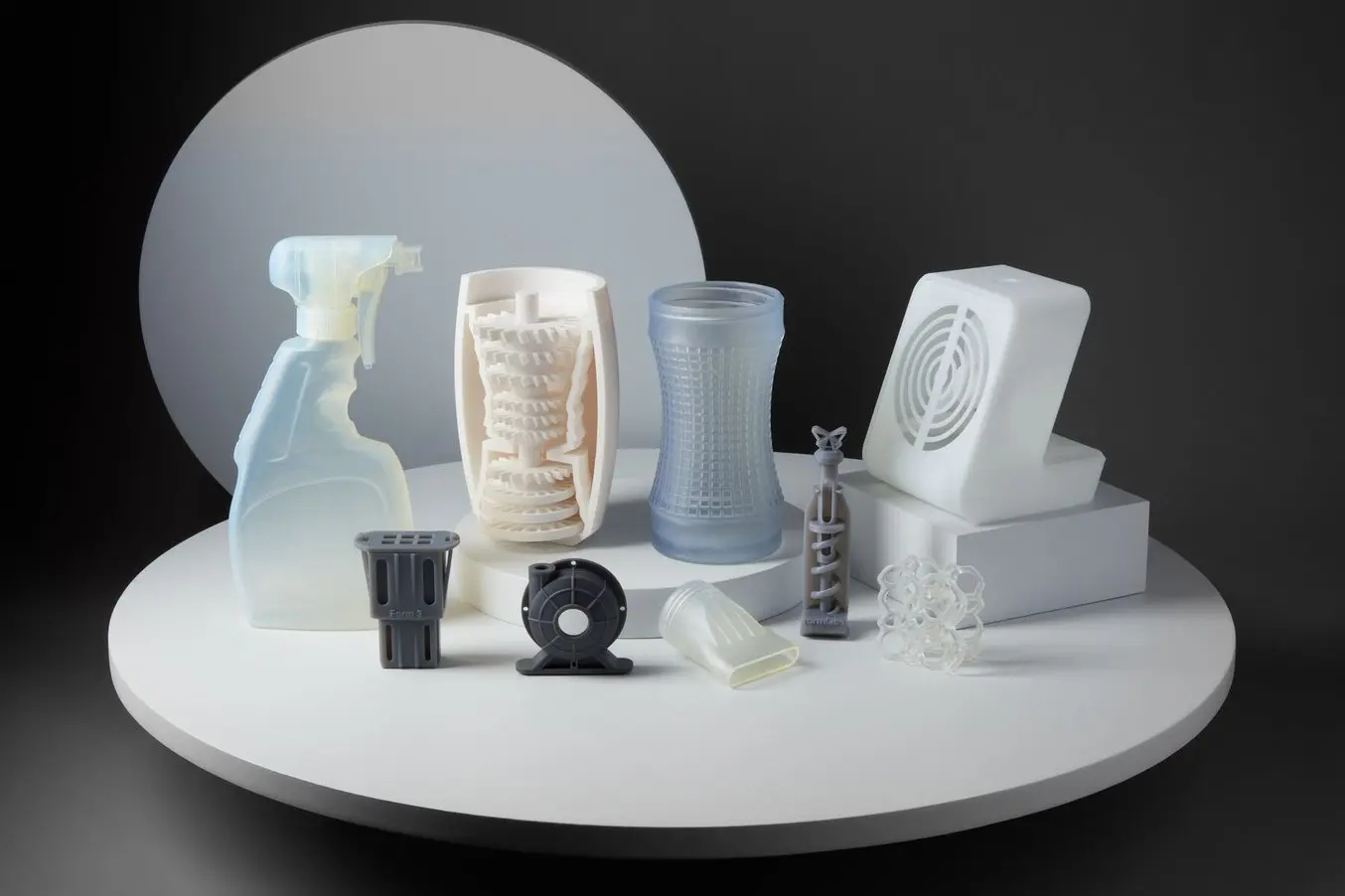
SLA-Kunstharze sind teurer als FDM-Filamente, und zwar aus dem einfachen Grund, dass sie speziell für bestimmte Anwendungen formuliert werden und ihre Herstellung mehr kostet als der Kauf von Standardfilamenten.
Kunstharze werden in der Regel vom Druckerhersteller formuliert (wobei einige Hersteller offene Plattformen oder White-Label-Harze anbieten), und ihr Preis spiegelt die kostspielige Forschung wider, die in ihre Entwicklung einfließt. Hersteller mit einem eigenen Kunstharzangebot wenden zudem für die Prüfung und Validierung der Druckeinstellungen Ressourcen auf, damit die Harze auf dem jeweiligen Drucksystem einsetzbar sind. Diese Investitionen in Forschung und Entwicklung schlagen sich zwar auf die Kosten für den Verbraucher nieder, führen aber zu einer höheren Druckzuverlässigkeit und besseren Ergebnissen. Bei den herstellerspezifischen Harzen handelt es sich oft um völlig neue Materialien, statt um branchenübliche Werkstoffe wie ABS oder PLA, und deren Entwicklung erfordert umfangreiche Ressourcen.
Die meisten SLS-Hersteller bieten Pulver zu einem branchenüblichen Preis von ca. 100 €/kg an, wobei einige, darunter auch Formlabs, Preisnachlässe für größere Mengen gewähren. Niedrigere Kilopreise gehen oft mit einem Nachteil einher: Das Pulver kostet weniger, weil die Drucker einen größeren Abstand zwischen den Teilen erfordern, um das Risiko von Wärmestaus zu verringern. Die empfohlene Packdichte für große Systeme ist oft auf etwa 8–10 % begrenzt, was bedeutet, dass genauso viel Material entsorgt werden muss, wie in die gedruckten Teile einfließt. Somit fällt bei diesen Systemen eine Menge nicht wiederverwertbares Pulver an, was die laufenden Betriebskosten in die Höhe treibt. Bei den SLS-Systemen von Formlabs ist die Packdichte unbegrenzt, und je höher die Dichte, desto effizienter wird der Drucker betrieben.
Der letzte – und oft vernachlässigte – Teil der Gleichung sind die Arbeitskosten. FDM-Teile erfordern oft eine umfangreichere Nachbearbeitung, um eine glatte Oberfläche zu erzielen, insbesondere wenn sich auf dem Teil Stützen befinden. Einige professionelle FDM-Drucker bieten lösliche Stützstrukturmaterialien an, sodass die Teile durch Auflösung der Stützen in einem Lösungsmittel schnell nachbearbeitet werden können. Allerdings müssen FDM-Teile, selbst mit löslichen Stützen, in der Regel häufiger manuell geschliffen werden, um eine mit SLA-Teilen vergleichbare Qualität und Glätte zu erreichen – sofern das überhaupt möglich ist. Für professionelle Anwender*innen ist dieser zusätzliche Arbeitsaufwand oft der wichtigste Faktor, der die Gesamtkosten pro Teil beim Filament-Druck in die Höhe treibt.
SLA-Teile müssen gewaschen und abhängig vom Material auch nachgehärtet werden. Beide Prozesse können jedoch weitgehend mit Zubehör automatisiert werden (z. B. dem Form Wash, Form Cure, Form Wash L und Form Cure L von Formlabs), um die Arbeitszeit zu reduzieren. Professionelle SLA-Systeme beinhalten zudem Software, Firmware und Materialtechnik, um leicht entfernbare Stützstrukturen und eine einfachere Nachbearbeitung zu ermöglichen.
Je nach Design können einige SLA-Teile auch ohne Stützstrukturen gedruckt werden, während gestützte SLA-Druckteile lediglich geringfügiges Schleifen erfordern, um die Stützspuren zu entfernen und eine hochwertige Oberflächengüte zu erzielen.
Beim SLS-3D-Druck ist die Nachbearbeitung erforderlich, um ungesintertes Pulver von den Teilen zu entfernen (jedoch keine Stützen, da diese nicht notwendig sind) und durch Sandstrahlen eine glatte Oberfläche zu erzielen. Diese Prozesse können mit Nachbearbeitungslösungen wie dem Fuse Sift und Fuse Blast einfach rationalisiert und automatisiert werden, um Arbeitskosten zu minimieren und Einheitlichkeit zu gewährleisten. Darüber hinaus können diese automatisierten Arbeitsschritte in Chargen durchgeführt werden, was die Arbeitskosten bei hohen Produktionsvolumen senkt.
Als Faustregel kann gelten, dass FDM-3D-Drucker die billigsten Teile fertigen, sofern nur einfache Prototypen in kleinen Stückzahlen gedruckt werden. Kunstharzbasierte SLA-3D-Drucker bieten eine höhere Auflösung, bessere Qualität und eine breite Palette von 3D-Druckmaterialien zu einem leicht gehobenen Preis. Dieser Preisunterschied schwindet jedoch schnell, sobald komplexe Designs oder mehr Teile gedruckt werden, da er durch eine weniger aufwendige Nachbearbeitung wettgemacht wird. SLS-3D-Drucker haben zwar die höchsten Anschaffungskosten, aber die Pulverkosten sind wettbewerbsfähig und die Arbeitskosten häufig minimal, sodass sie für Anwendungen mit hohem Durchsatz am kosteneffizientesten sind.
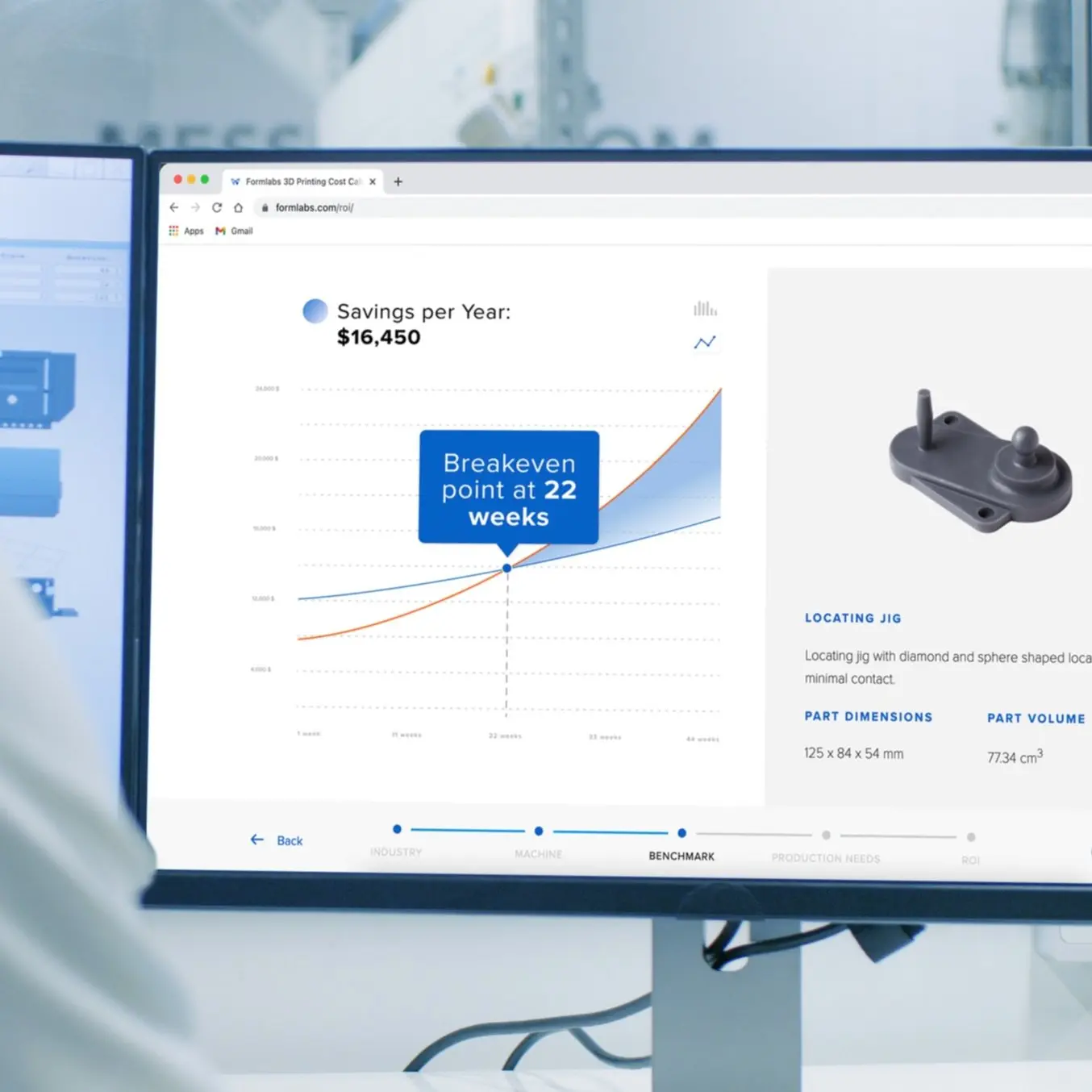
Berechnen Sie Ihre Zeit- und Kostenersparnis
Nutzen Sie unser interaktives ROI-Tool zur Berechnung Ihrer Zeit- und Kostenersparnis beim 3D-Druck mit einem Formlabs-Drucker.
Parallele Nutzung von FDM-, SLA- und SLS-3D-Druckern
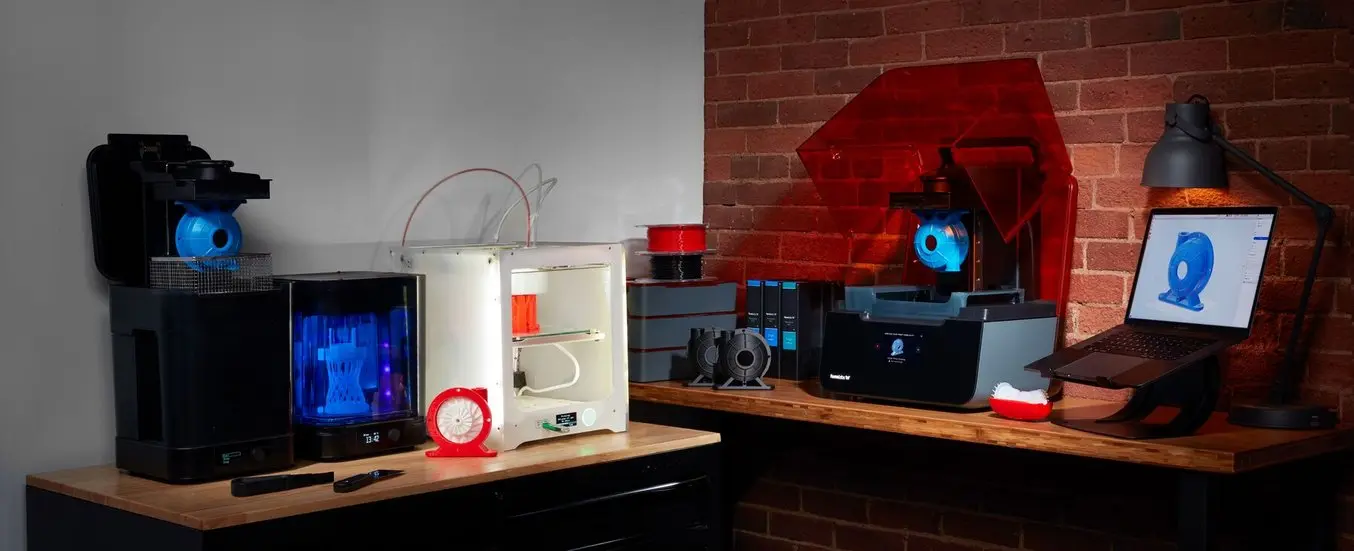
Die meisten Unternehmen, die den 3D-Druck regelmäßig in ihren Prozessen einsetzen, nutzen mehr als eine Technologie. Genau wie CNC- oder Spritzgussmaschinen zählen 3D-Drucker für Ingenieur- und Designteams als eines von vielen Hilfsmitteln in ihrer Werkzeugkiste – je nach den Anforderungen des Teils und der Prozessphase findet sich für jede Aufgabe das richtige Werkzeug. FDM-, SLA- und SLS-3D-Drucker haben unterschiedliche Stärken und werden idealerweise als komplementäre Werkzeuge eingesetzt.
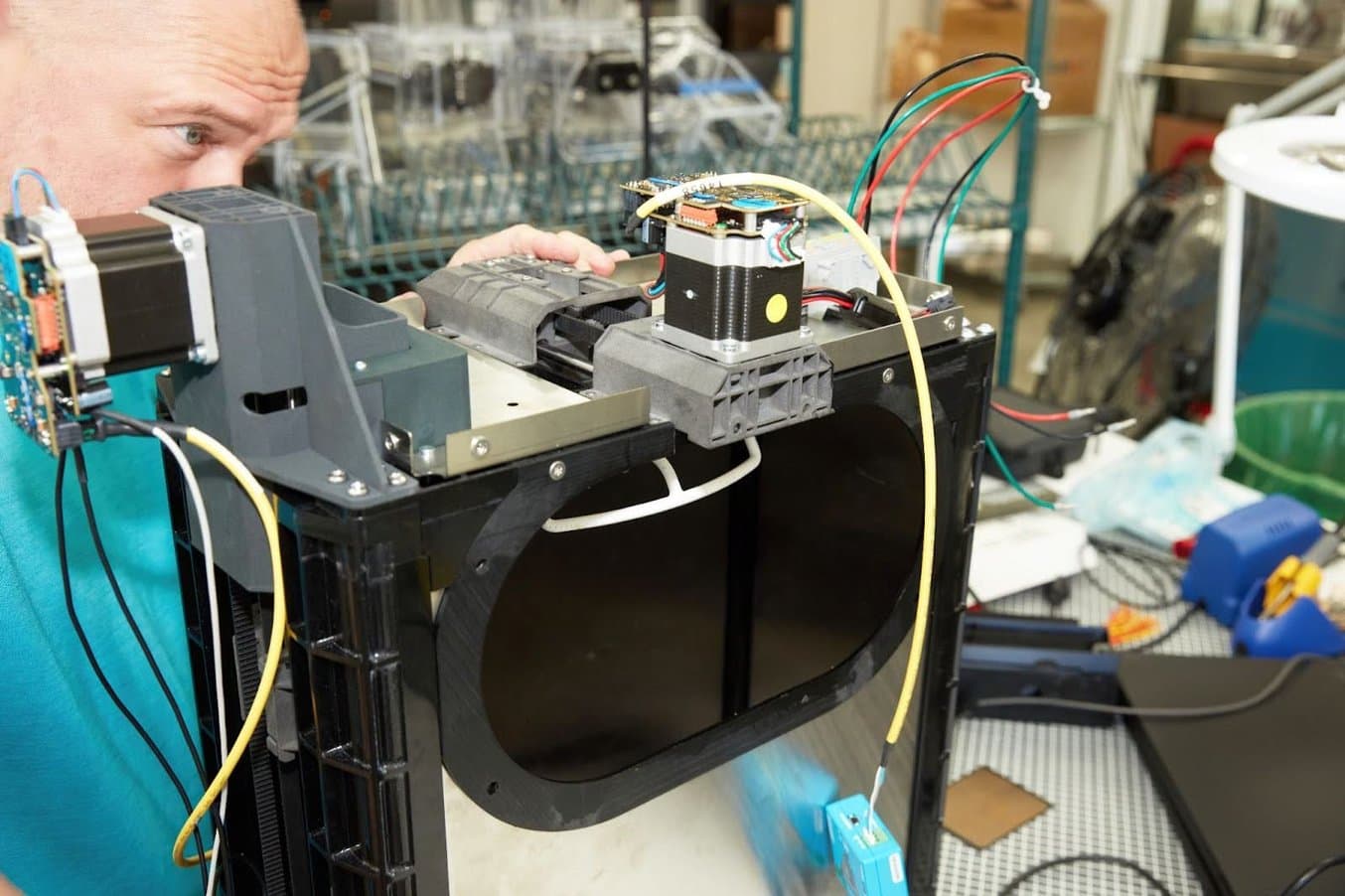
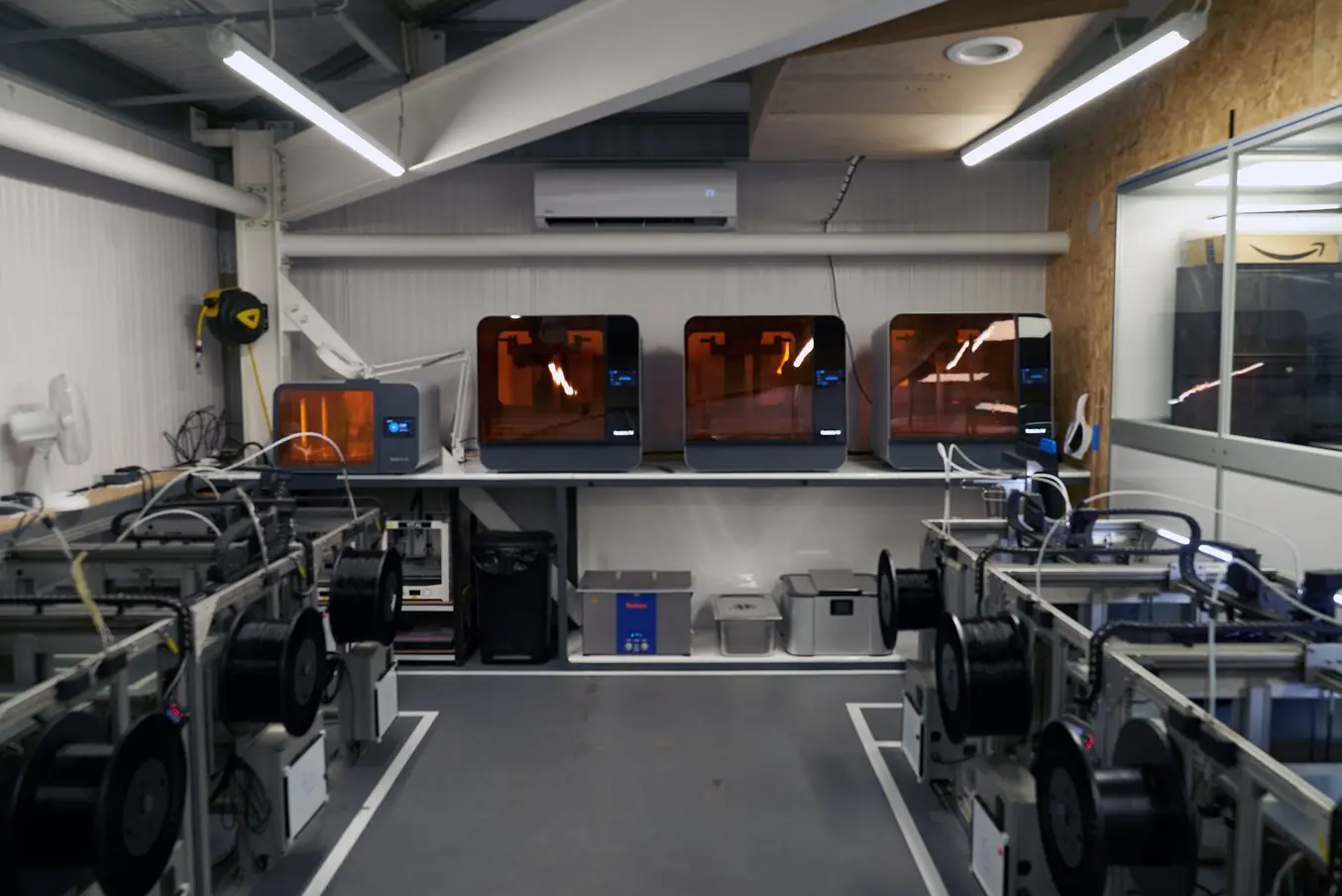
Hier einige praktische Beispiele:
-
Brose verwendet FDM-, SLA- und SLS-Technologien für die Herstellung verschiedenster Teile, von ersten Prototypen von Automobilbauteilen bis hin zur Produktion von Sitzbauteilen in Stückzahlen von 250 000 oder mehr.
-
Labconco nutzt SLA-, FDM- und SLS-Technologien zur Herstellung von Komponenten von Laborgeräten für die Endverwendung, Werkzeugen, Halterungen und Vorrichtungen sowie Prototypen. Produktingenieur Brent Griffith entwickelt Ideen mithilfe von FDM-Druckern, um die Kosten für die Prototypenerstellung niedrig zu halten, bevor er sie mittels SLA oder SLS für den Einsatz in den Geräten oder dem Labor 3D-druckt.
-
Hyphen nutzt FDM-3D-Drucker für schnelle Designvalidierungen. Für Werkzeug und Endverbrauchsteile stützt sich das Team jedoch auf seine SLA-Drucker der Form-Serie, da hier hohe Genauigkeit und geringe Reibung gefordert ist. Mit den drei SLS-Druckern der Fuse-Serie wiederum werden Bauteile für die Endverwendung hergestellt, die wiederholten Belastungen standhalten müssen oder empfindliche elektronische Komponenten schützen. Viele Strukturteile für Maschinen werden vollständig mit SLS 3D-gedruckt.
-
Der Laborleiter von Vital Auto, Anthony Barnicott, betreibt 14 großformatige FDM-Drucker, drei großformatige SLA-Drucker der Form-Serie und fünf SLS-Drucker der Fuse-Serie, um funktionale Prototypen und Teile für die Designvalidierung von Konzeptfahrzeugen im Auftrag von Marken wie McLaren, Volvo, Nissan, Lotus und anderen zu produzieren.
-
Black Diamond nutzt den SLS-3D-Druck mit der Fuse-Serie und Nylon 12 Powder, um Komponenten für Kletterausrüstung für die Endverwendung herzustellen, die das Team in der Wasatch-Gebirgskette in der Praxis testet, bevor es in ein Spritzgusswerkzeug investiert. Das Black-Diamond-Team verwendet außerdem Desktop- und Benchtop-SLA-Drucker der Form-Serie für schnelle Iterationen und Designprüfungen großer Teile wie Helme, die glatte Oberflächen in Endproduktqualität benötigen.
-
Foil Drive, ein australischer Hersteller elektronischer Foiling-Ausrüstung, druckt auf seinem SLS-Drucker der Fuse-Serie Gehäuse für Elektromotoren für die Endverwendung in Stückzahlen von 100–2000 Teilen. Nylon 12 Powder hält der starken Beanspruchung in Unterwasserpropellern stand, und für die benötigten mittleren Produktionsvolumen rechnet sich der SLS-3D-Druck. Foil Drive verwendet SLA-3D-Drucker der Form-Serie mit Tough 2000 Resin und Rigid 10K Resin für Schaufeln von Propellern und Laufrädern, die ein- und ausrastbar sind – hierfür ist SLA ideal, denn dank seiner engen Toleranzen funktionieren diese kleinen Baugruppen reibungslos.
Mehr über den SLA- und SLS-3D-Druck erfahren
Laden Sie unser Whitepaper herunter für eine detaillierte Übersicht über das SLA- und SLS-Ecosystem und den 3D-Druckprozess.
Möchten Sie sich selbst von der Qualität des SLA- und SLS-Drucks überzeugen? Wählen Sie eine Anwendung aus unserer Liste aus und fordern Sie einen kostenlosen Probedruck an, um das Material zu finden, das Ihre Anforderungen erfüllt.