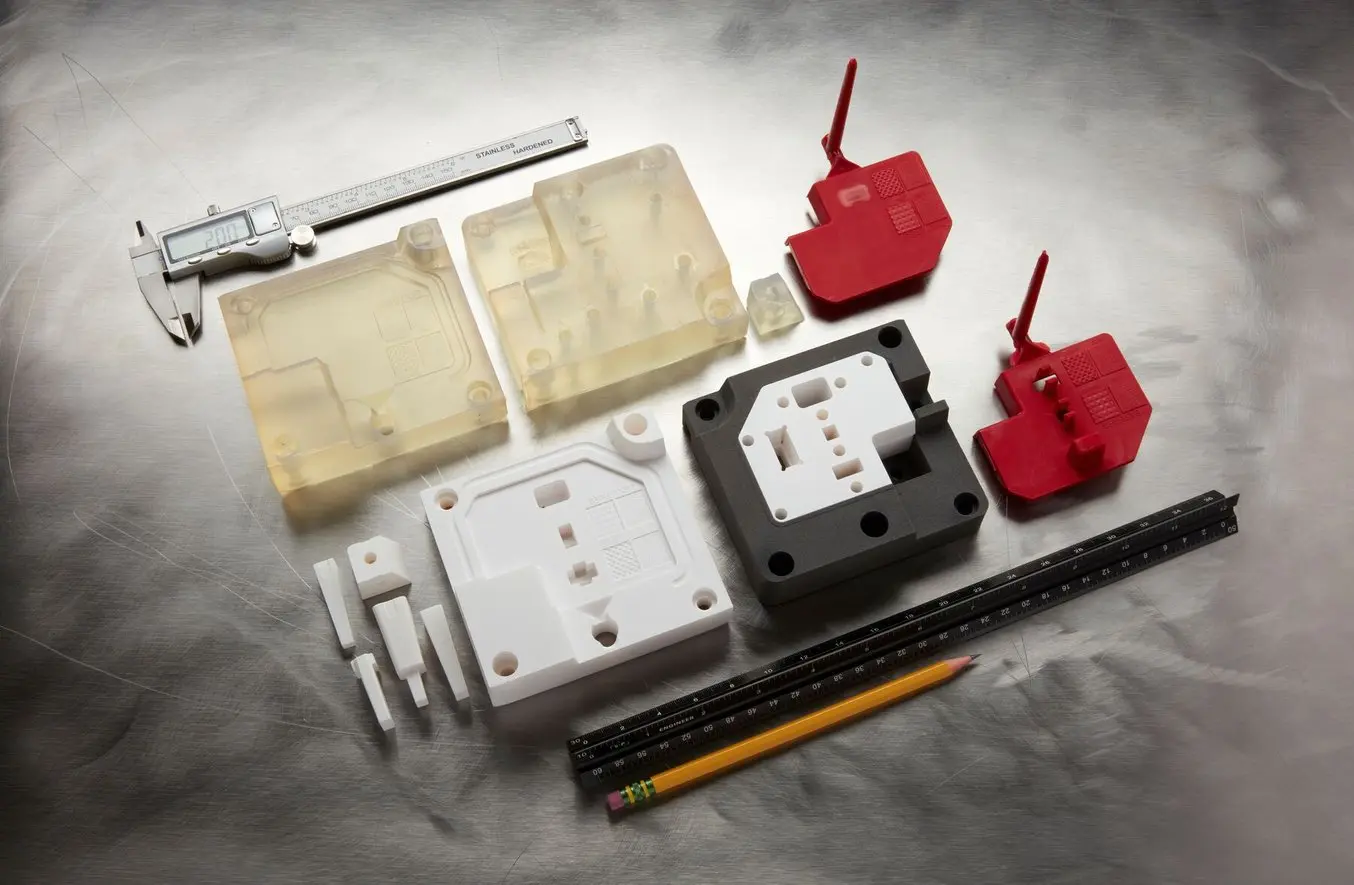
Bei den meisten traditionellen Fertigungsprozessen wie Spritzguss, Thermoformen oder anderen Gießverfahren wird maßgefertigte Werkzeugbestückung für die Herstellung von Endverbrauchsteilen benötigt. Der Werkzeugbau ist jedoch mit hohen Vorabkosten und wochen- oder monatelangen Durchlaufzeiten von Dienstleistern verbunden, was die Produktentwicklung und damit die Markteinführung verlangsamt.
Betriebsinternes Rapid Tooling – z. B. anhand 3D-gedruckter Formen, Modelle oder Werkzeugeinsätze – als Teil der Produktentwicklung gibt Unternehmen die Möglichkeit, das Design und die Materialwahl zu validieren, bevor man zur Serienproduktion übergeht. Außerdem lassen sich damit individualisierte Endverbrauchsteile oder Sondereditionen herstellen.
In diesem umfassenden Leitfaden behandeln wir folgende Themen:
- Was unterscheidet Rapid Tooling von herkömmlicher Werkzeugbestückung?
- Verschiedene Anwendungsbereiche des Rapid Tooling
- Echte Fallstudien bezüglich Rapid Tooling
- Fertigungsverfahren, die vom Rapid Tooling profitieren
- Erste Schritte zur Einführung von betriebsinternem Rapid Tooling
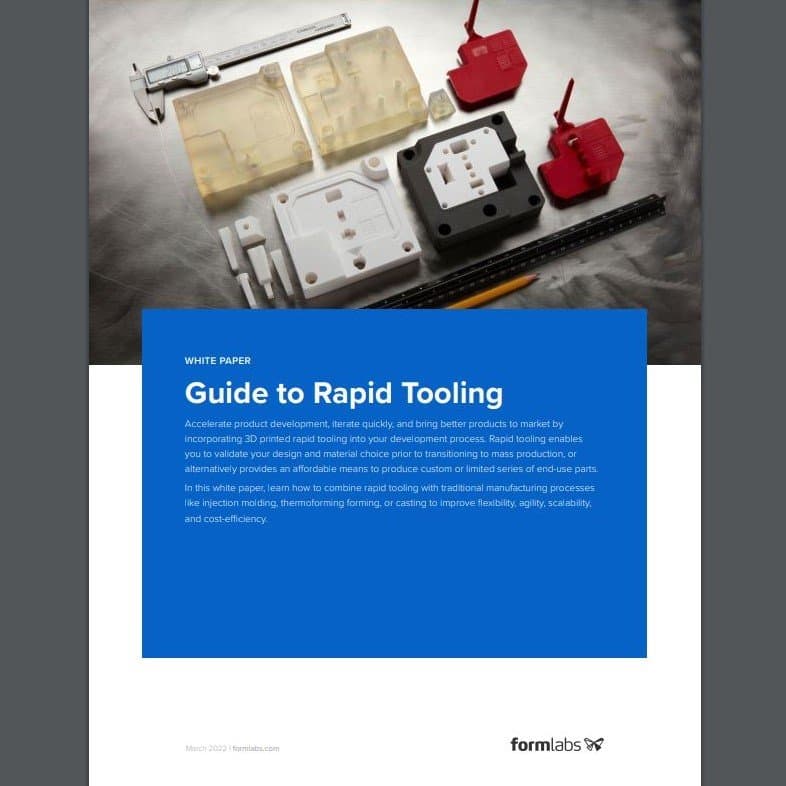
Leitfaden zum Rapid Tooling
Möchten Sie diesen Leitfaden speichern, ausdrucken oder mit Kollegen teilen? Laden Sie ihn als PDF herunter.
Was ist Rapid Tooling?
Rapid Tooling beschreibt eine Reihe an Techniken, mithilfe welcher Sie schnell, kostengünstig und effizient die für traditionelle Fertigungsverfahren benötigte Werkzeugbestückung anfertigen, um Teile schneller oder auch in geringen Mengen herzustellen.
Konventionelle Werkzeugbestückung besteht für gewöhnlich aus langlebigen Metallteilen und wird mittels Zerspanung oder Metallguss hergestellt. Diese Verfahren sind jedoch sehr teuer und eignen sich besser für die großangelegte Produktion. Nutzt man sie zur Iteration der Werkzeugbestückung oder bei der Produktion kleiner Chargen, explodieren die Kosten und auch die Durchlaufzeit erhöht sich drastisch.
Mithilfe von Rapid Tooling als Teil der Produktentwicklung validieren Hersteller ihre Designs und Materialien vor dem Übergang zur Massenproduktion. Das beschleunigt die Produktentwicklung, ermöglicht schnelle Iterationen und bringt letztendlich bessere Produkte auf den Markt. Dank Rapid Tooling können Ingenieure die letztendlichen Produktionsmaterialien verwenden, um die Leistung Ihrer Teile bei realen Anwendungen zu bewerten oder um kleine Auflagen für Beta- oder Validierungstests herzustellen. Außerdem hilft Rapid Tooling bei der Fehlerbehebung im Fertigungsprozess, bevor Sie in teure Produktionswerkzeuge investieren.
Und als ob das noch nicht genug wäre, bietet Ihnen Rapid Tooling die Möglichkeit, Maßanfertigungen oder Kleinserien von Endverbrauchsteilen über Ihre traditionellen Fertigungsverfahren herzustellen, die mit konventioneller Werkzeugbestückung einfach unerschwinglich wären. So testen Hersteller den Markt für neue Produkte, bieten eine größere Produktauswahl an oder individualisieren die Teile entsprechend der Wünsche und Bedürfnisse ihrer Kunden.
Rapid Tooling | Konventionelle Werkzeugbestückung | |||
---|---|---|---|---|
Geschwindigkeit | 24 Stunden Betriebsinterne Produktion mithilfe additiver Fertigungsverfahren | 4–8 Wochen Ausgelagerte Produktion | ||
Kosten der Werkzeugbestückung | Geringe kosten (ähnlich Rapid Prototyping), geringe Gemeinkosten | Sehr teuer, erhebliche Gemeinkosten | ||
Ideales Produktionsvolumen | 1–10 000 Teile, abhängig vom Verfahren und dem Material des Werkzeugs | Ab ca. 5000 Teilen, je nach Produktionsverfahren | ||
Anwendungen | Prototypenentwicklung Produktvalidierung Bridge-Tooling Kleinserien, Sonderanfertigungen oder individualisierte Teile | Massenproduktion |
Der Unterschied zwischen Rapid Tooling und Rapid Prototyping
Falls Ihnen Rapid Prototyping ein Begriff ist, fragen Sie sich vielleicht, was der Unterschied zum Rapid Tooling ist.
Rapid Prototyping ist eine Gruppe von Techniken, die dreidimensionale CAD-Daten (von Englisch „computer-aided design“, zu Deutsch etwa „computerunterstütztes Entwerfen“) verwendet, um schnell ein maßstabsgetreues Modell eines Teils oder einer Baugruppe herzustellen. Da diese Teile oder Baugruppen für gewöhnlich mit additiven Fertigungstechniken und nicht mit den herkömmlichen subtraktiven Methoden gefertigt werden, wurde der Begriff zu einem Synonym für additive Fertigung und 3D-Druck.
Rapid Tooling hingegen verwendet additive Fertigung oder auch CNC-Bearbeitung nicht etwa, um das Teil direkt herzustellen, sondern für Werkzeugausstattung wie Guss- & Tiefziehformen, Urmodelle oder Presswerkzeuge. Diese kommen dann in traditionellen Fertigungsverfahren zur Anwendung, um fertige Teile zu erstellen. Es schließt also die Lücke zwischen Prototypenentwicklung und Produktion und erlaubt die Herstellung von Endverbrauchsteilen.
Soft Tooling und Hard Tooling
Die Begriffe „Soft Tooling“ und „Hard Tooling“ hört man häufig im Bereich des Rapid Tooling.
Soft Tooling bezieht sich im Allgemeinen auf Silikonformen und den Urethanguss. Ähnlich wie auch Rapid Tooling kommt Soft Tooling hauptsächlich zur Anwendung bei der Prototypenfertigung, beim Bridge-Tooling und bei der Kleinserienproduktion. Die Modelle für den Urethanguss werden außerdem auch oft mittels 3D-Druck hergestellt.
Hard Tooling ist quasi ein Synonym für metallische Werkzeugausstattung, dem man am ehesten im Zusammenhang mit Spritzguss begegnet. Auch Hard Tooling lässt sich mittels Rapid-Tooling-Verfahren herstellen, üblicherweise aus Aluminium. Hard Tooling ist langlebig und übersteht große Produktionsmengen, involviert aber wesentlich höhere Kosten als Soft Tooling oder die meisten Rapid-Tooling-Verfahren. Deshalb eignet es sich eher für die Massenproduktion.
Anwendungsbereiche des Rapid Tooling
Rapid Tooling unterstützt eine ganze Reihe herkömmlicher Fertigungsverfahren bei der Produktion von Kunststoff-, Silikon- oder Kautschukteilen, bei Verbundwerkstoffen und selbst bei Metallteilen.
Herstellung von Kunststoffteilen
- Spritzguss
- Thermoformen
- Guss
- Umspritzung und Insert-Molding
- Formpressen
Herstellung von Silikon- oder Kautschukteilen
- Spritzguss
- Guss
- Formpressen
- Umspritzung und Insert-Molding
Herstellung von Verbundwerkstoffteilen
- Thermoformen
- Formpressen
- Umformung
Herstellung von Metallteilen
- Guss
- Blechumformung
Die verschiedenen Rapid-Tooling-Verfahren lassen sich in zwei Kategorien unterteilen: direkte und indirekte Werkzeugbestückung. Die indirekte Werkzeugbestückung fertigt Urmodelle zur Herstellung von Formen oder Werkzeugen, mit denen dann das letztendliche Werkzeug hergestellt wird. Dem gegenüber erstellt bei der direkten Werkzeugbestückung eine Maschine oder ein 3D-Drucker die eigentliche Form, den Werkzeugaufsatz oder das Werkzeug selbst, mit dem das Endteil hergestellt wird.
Spritzguss
Spritzguss ist eines der beliebtesten Fertigungsverfahren für Thermoplaste sowie Silikon- oder Kautschukteile. Und aufgrund der exorbitanten Kosten herkömmlicher Metallwerkzeuge kann insbesondere dieses Verfahren von den Vorteilen des Rapid Tooling profitieren.
Dank günstiger Desktop-3D-Drucker und temperaturbeständiger 3D-Druckmaterialien lassen sich Spritzgussformen betriebsintern drucken, mit denen Sie funktionsfähige Prototypen und kleine Funktionsteile aus Produktionskunststoffen herstellen.
Bei der Kleinserienfertigung (ca. 10 bis 1000 Teile) sparen 3D-gedruckte Spritzgussformen im Vergleich zu teuren Formen aus Metall Zeit und Geld. Außerdem machen sie die Fertigung und die Produktentwicklung agiler. Ingenieure und Designer erstellen so funktionsfähige Prototypen oder Kleinserien von Endverbrauchsteilen zur Validierung der Materialwahl. Sie können ihre Designs dank der niedrigen Durchlaufzeiten und Kosten auch weiter iterieren, bevor in Hard Tooling investiert wird.
Stereolithografie-3D-Druck (SLA) stellt eine kostengünstige Alternative zu gefrästen Aluminiumformen dar. SLA-Teile sind solide und isotrop und es gibt Materialien mit einer Wärmeformbeständigkeitstemperatur von bis zu 238 °C bei 0,45 MPa, die der Hitze und dem Druck beim Spritzguss standhalten.
Der in Shenzhen ansässige Vertragshersteller Multiplus verwendet den SLA-Drucker Form 3 und 3D-gedruckte Spritzgussformen aus dem hitzebeständigen und glasgefüllten Material Rigid 10K Resin, um die Durchlaufzeiten kleiner Spritzgusschargen von etwa 100 Teilen von vier Wochen auf gerade einmal drei Tage zu verkürzen.
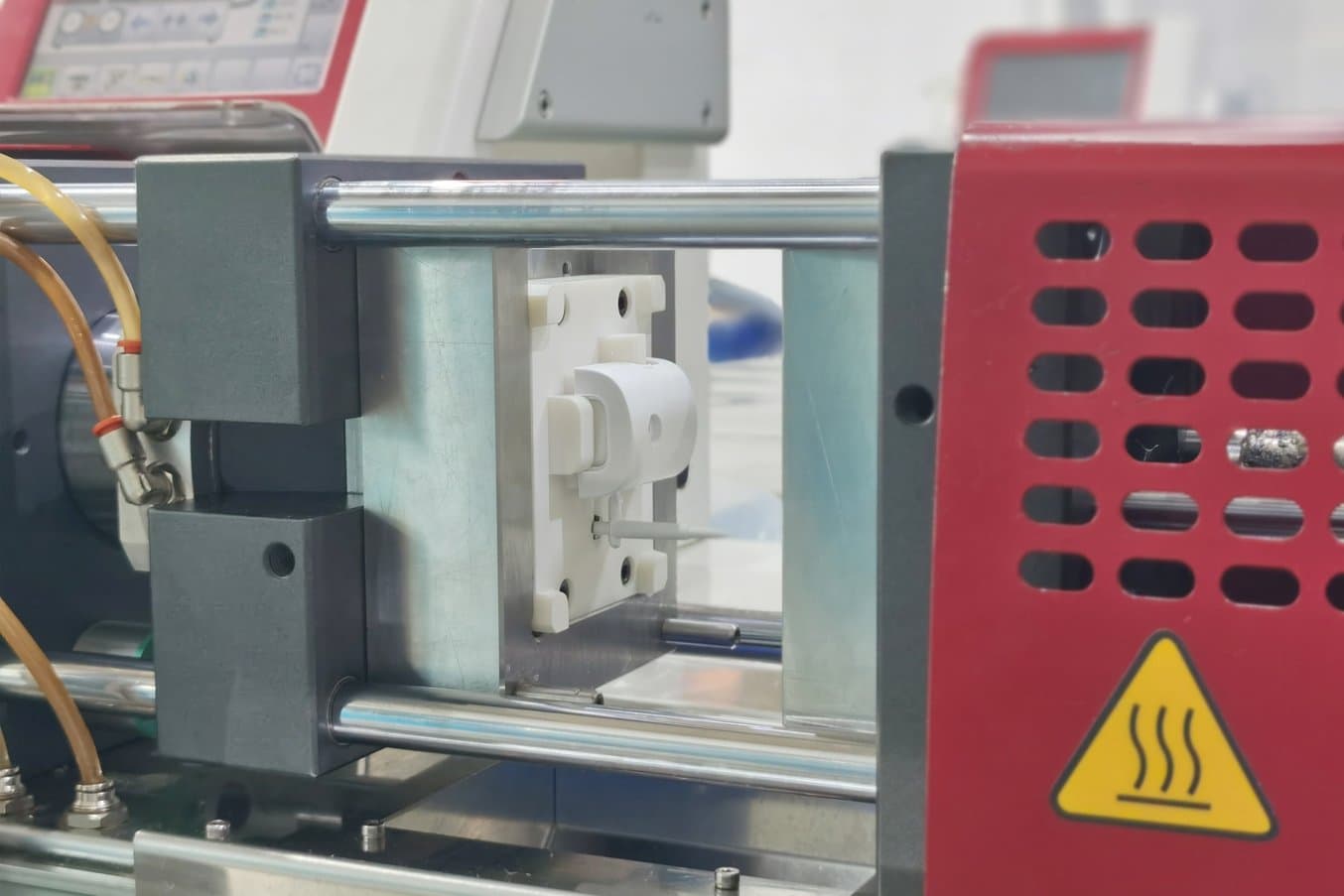
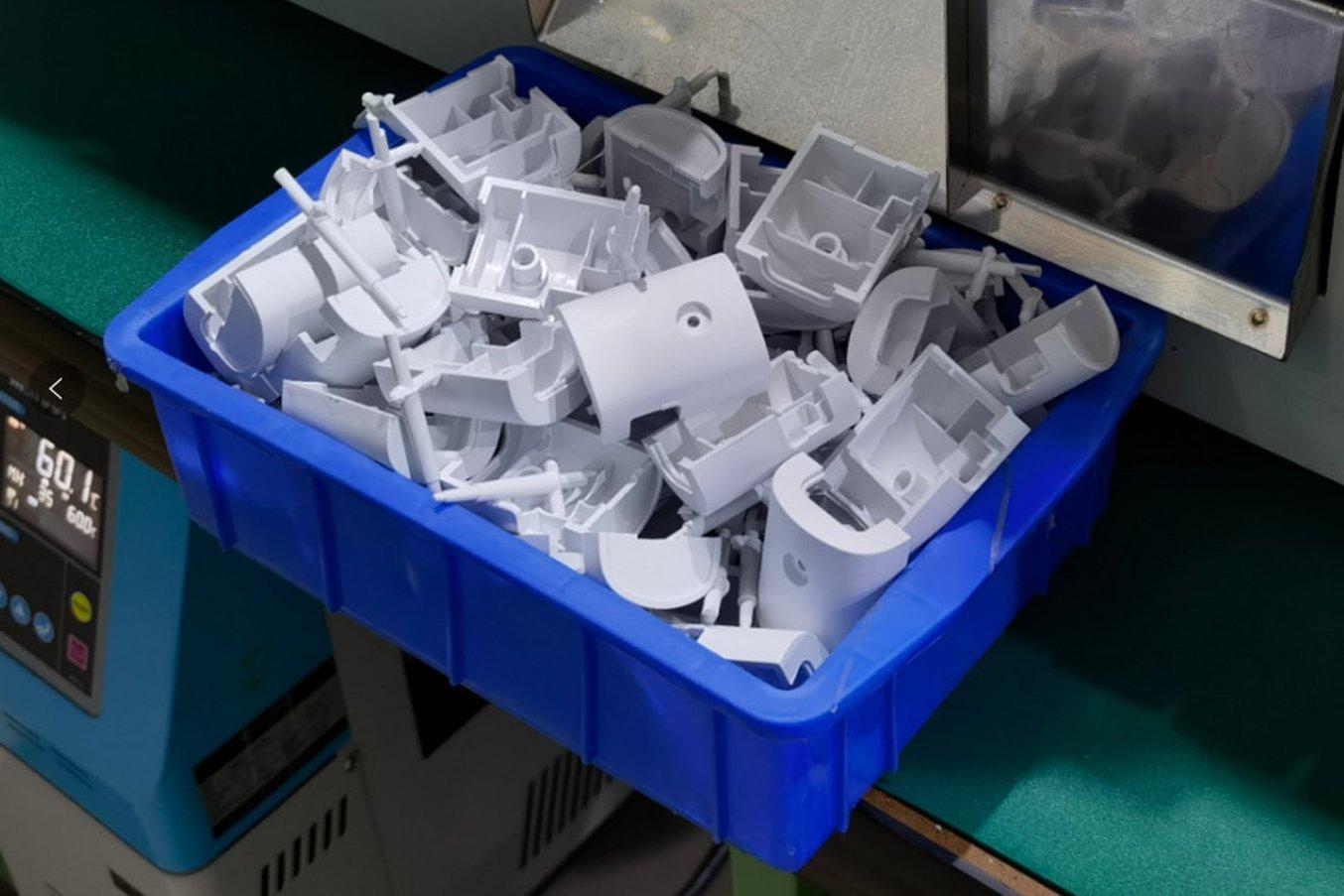
ABS-Gehäuseteile für Bedienelementkästen aus der Spritzgussproduktion mit 3D-gedruckten Formen
Ein weiteres Beispiel sind die Notfallmaskenriemen des Petrochemieunternehmens Braskem sowie die Prototypen und Vorproduktionsteile, die der Spritzgussmaschinenhersteller Holimaker seinen Kunden anbietet.
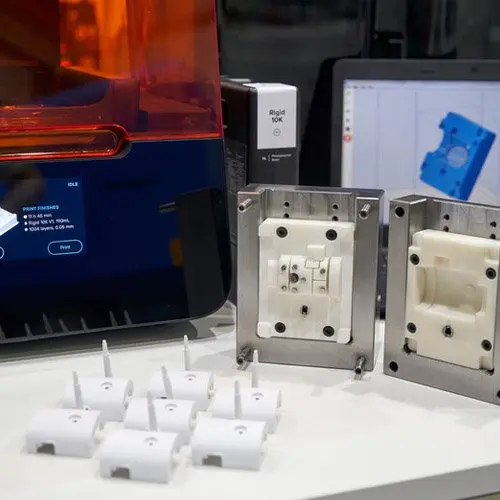
Rasches Spritzgießen von Kleinserien mit Formen aus dem 3D-Drucker
Laden Sie dieses Whitepaper herunter und erfahren Sie mehr über die Methoden und Richtlinien zur Herstellung 3D-gedruckter Spritzgussformen, um die Kosten zu senken und Lieferzeiten zu verkürzen. Es enthält Fallstudien aus der Praxis von Braskem, Holimaker und Novus Applications.
Gespante Formen aus Aluminium können auch für mittelgroße Produktionsvolumen von 500 bis 10 000 Teilen als Alternative verwendet werden und reduzieren die Fixkosten der Formenfertigung. Zerspantes Aluminium ist fünf- bis zehnmal schneller als Stahl und verursacht weniger Verschleiß an den Werkzeugen, was kürzere Durchlaufzeiten und niedrigere Kosten bedeutet. Aluminium leitet außerdem Hitze schneller als Stahl, was weniger Kühlkanäle erfordert und Herstellern ermöglicht, den Formenentwurf zu vereinfachen, wobei kurze Zyklen eingehalten werden.
Thermoformen
Thermoformen (oder Tiefziehen) ist ein umfassender Fertigungsprozess mit all den unterschiedlichen Verfahren, mit denen Hersteller Kunststoffplatten in Form bringen, z. B. Vakuumformen oder Druckformung. Mit Thermoformen fertigen Hersteller Teile aus einer breiten Palette von Thermoplasten und Verbundwerkstoffen.
Viele Unternehmen verlassen sich bei ihren Tiefziehformen auf 3D-Druck. Die Durchlaufzeiten sind schnell und die Kosten gering, insbesondere bei Kleinserien, Sonderanfertigungen und Prototypen. Und obendrein gewährt 3D-Druck unvergleichliche Gestaltungsfreiheit auch für komplexe und detailreiche Formen. Verwenden Sie den Desktop-SLA-Drucker Form 3+ für kleinere Formen und den großformatigen SLA-Drucker Form 3L für Formgrößen von bis zu 33,5 × 20 × 30 cm.
Das Produktentwicklungsunternehmen Glassboard nutzt die hohe Druckgeschwindigkeit von Draft Resin zur schnellen Produktion von Tiefziehformen für Prototypen aus Polycarbonat wie Helmschalen oder Verpackungsteile. So erreicht man dort komplizierte Formgeometrie, die mit traditionellen Verfahren nur schwer herzustellen wären, darunter kleinste Details oder Löcher für eine bessere Vakuumverteilung auf der Oberfläche.
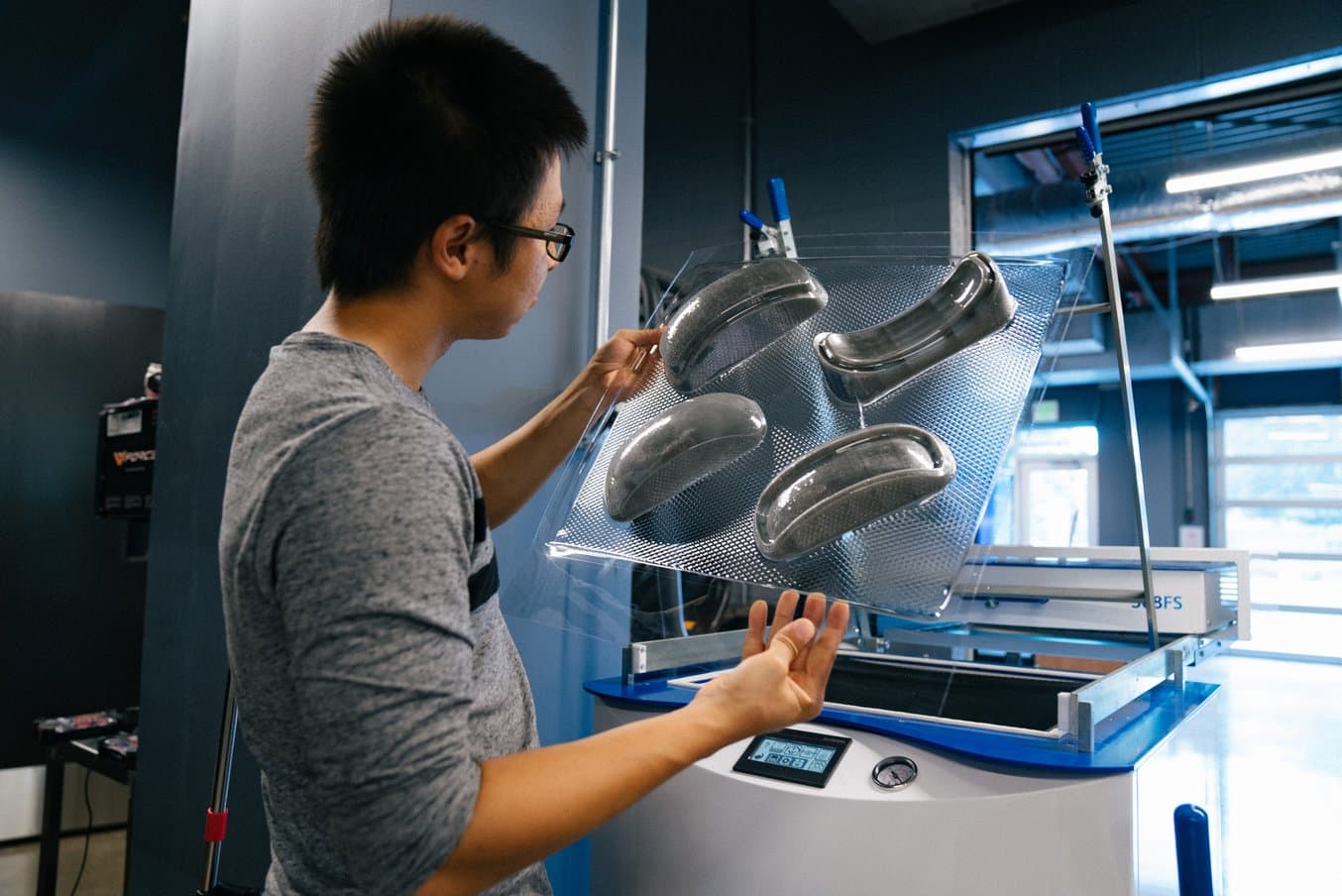
Das Produktentwicklungsunternehmen Glassboard setzt 3D-gedruckte Formen zum Tiefziehen ein, für Prototypen aus Polycarbonat wie Helmschalen oder Verpackungsteile.
Früher fertigte der Kosmetikhersteller Lush die Urformen für die beliebten Produkte von Hand an. Seit kurzem verwendet man dort jedoch 3D-Druck zur Herstellung von Vakuumformen mit detaillierten Designs und Texturen. Dadurch lassen sich Konzepte bereits in weniger als 24 Stunden umsetzen und mehr als eintausend Designs pro Jahr testen.
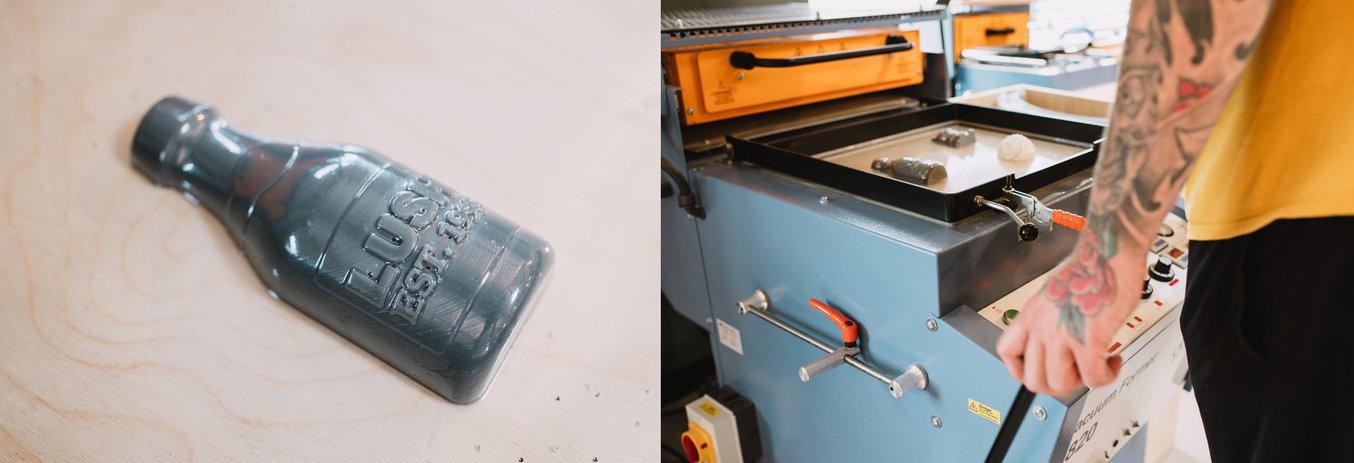
Das Team von Lush Cosmetics fertigt Urformen für den Vakuumformprozess betriebsintern mit 3D-Druck an.
3D-gedrucktes Rapid Tooling eignet sich außerdem ideal für die kostengünstige Herstellung maßgefertigter oder individualisierter Endverbrauchsteile. Beispielsweise ist ein Vakuumformverfahren mit 3D-gedruckten Modellen die gängige Produktionsweise für transparente Aligner in der Kieferorthopädie.
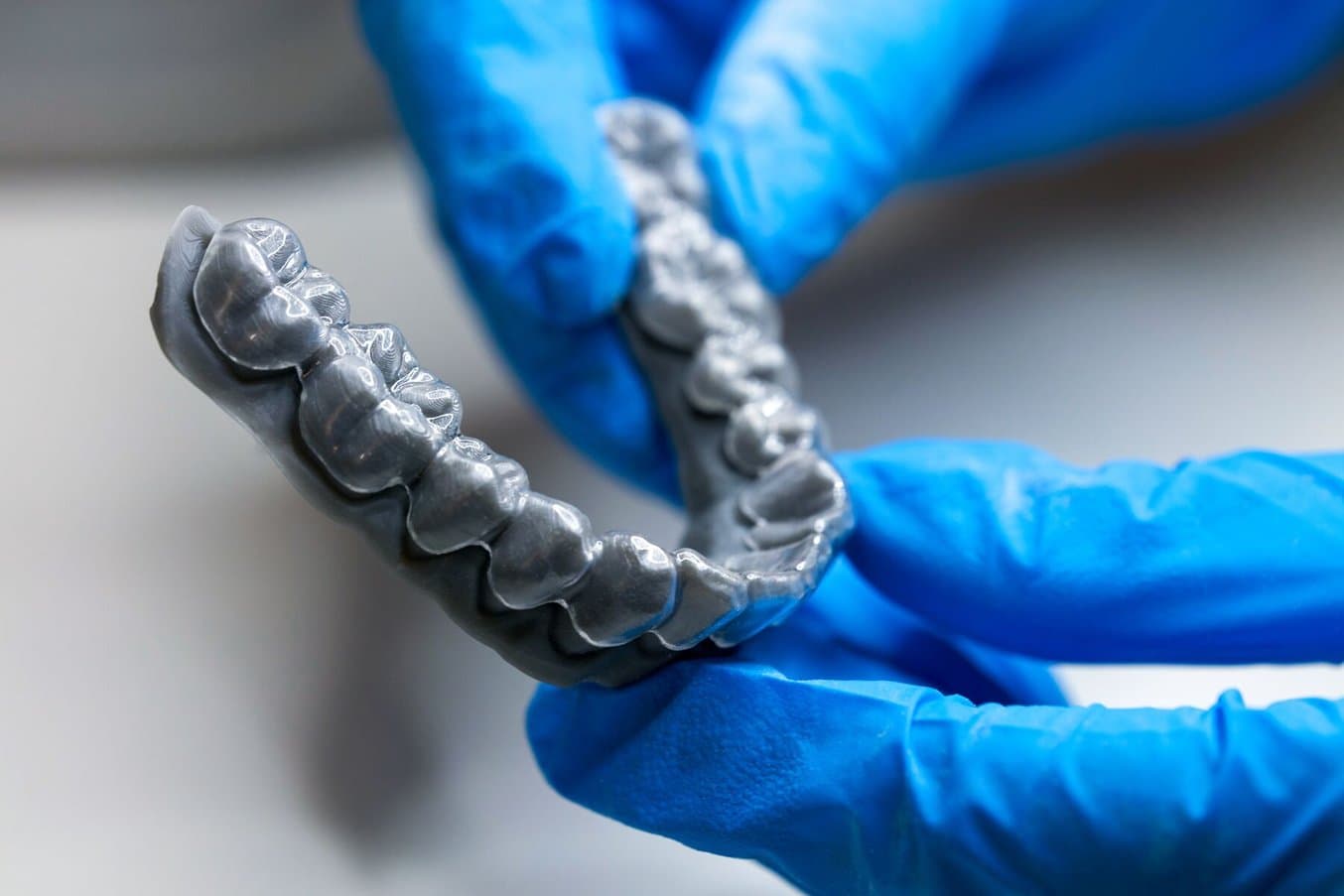
Vakuumformung und Druckformung mit 3D-gedruckten Modellen sind die gängigen Produktionsweisen für transparente Aligner in der Kieferorthopädie.
Hochleistungsverbundwerkstoffe wie Kohlenstofffaser lassen sich gleichermaßen in 3D-gedruckten Formen von Hand laminieren. SLA-3D-Drucker bieten die glatte Oberflächenbeschaffenheit, die für Laminierungsformen so wichtig ist.
Das Formula-Student-Team der TU Berlin laminiert von Hand Kohlenstofffaserteile für Rennwagen in 3D-gedruckten Formen. Diese Formen aus Tough 1500 Resin sind nicht nur stark genug für den Laminierungsprozess, sie sind außerdem flexibel genug, um das Teil nach der Aushärtung leicht von der Form zu trennen. Das eröffnet ganz neue Designmöglichkeiten.
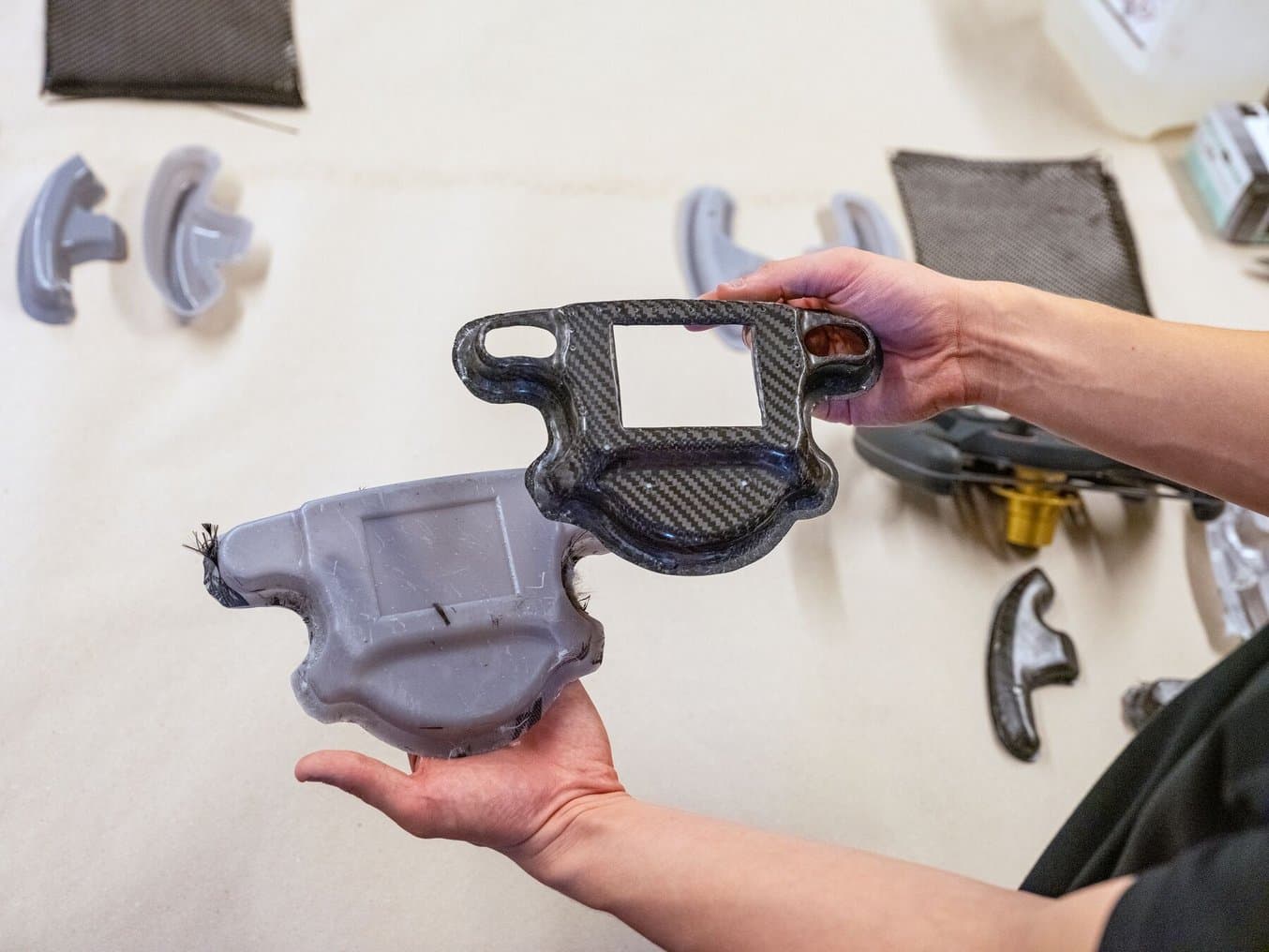
Die 3D-gedruckte Form und das entformte Kohlenstofffaserteil des vorderen Lenkradgehäuses
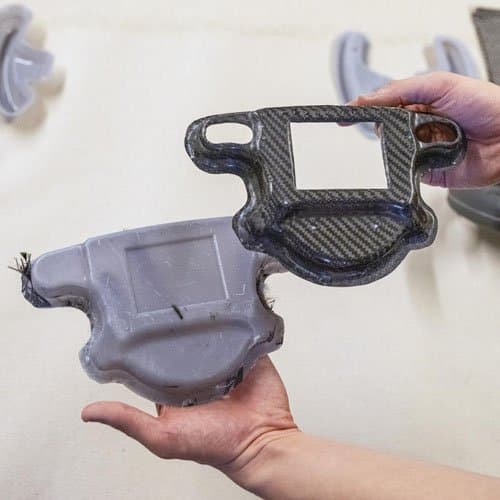
Fertigung von Kohlenstofffaserteilen mit 3D-gedruckten Formen
Laden Sie dieses Whitepaper zur Erstellung von Kohlenstofffaserteilen herunter. Es erläutert Designleitfäden für Verbundwerkstoffformen sowie schrittweise Anleitungen für die Prepreg- und Handlaminierung.
Umspritzung und Insert-Molding
Rapid Tooling mit 3D-gedruckten Formen kommt auch zur Anwendung bei der Formung von Kunststoff-, Silikon- oder Kautschukteilen sowie bei der Umspritzung von Einsätzen oder von interner Hardware.
Das Team von Google ATAP nutzte 3D-gedruckte Nachbildungen als Einsätze anstelle der umspritzten elektronischen Unterbaugruppen bei der Feineinstellung der Werkzeuge in der Fabrik.
Designer im Labor von Google Advanced Technology and Projects (ATAP) konnten ihre Kosten um über 100 000 USD senken und ihre Testzyklen von drei Wochen auf drei Tage verkürzen. Der Schlüssel dazu war die Kombination von 3D-Druck und Insert-Molding. Das Team von Google ATAP stellte fest, dass Sie mit dem 3D-Druck von Testkomponenten Zeit und Geld sparen konnten gegenüber der Verwendung teurer Elektronik von einem externen Zulieferer.
Das Start-up Dame Products mit Sitz in Brooklyn entwirft Produkte für die Gesundheits- und Wellnessbranche. Dort setzt man Insert-Molding ein, um die interne Hardware für Betatests durch die Kunden in Silikon einzufassen. Zur Produktreihe von Dame Products gehören komplexe ergonomische Geometrien, die jeweils komplett von hautverträglichem Silikon in verschiedenen Farben umschlossen sind.
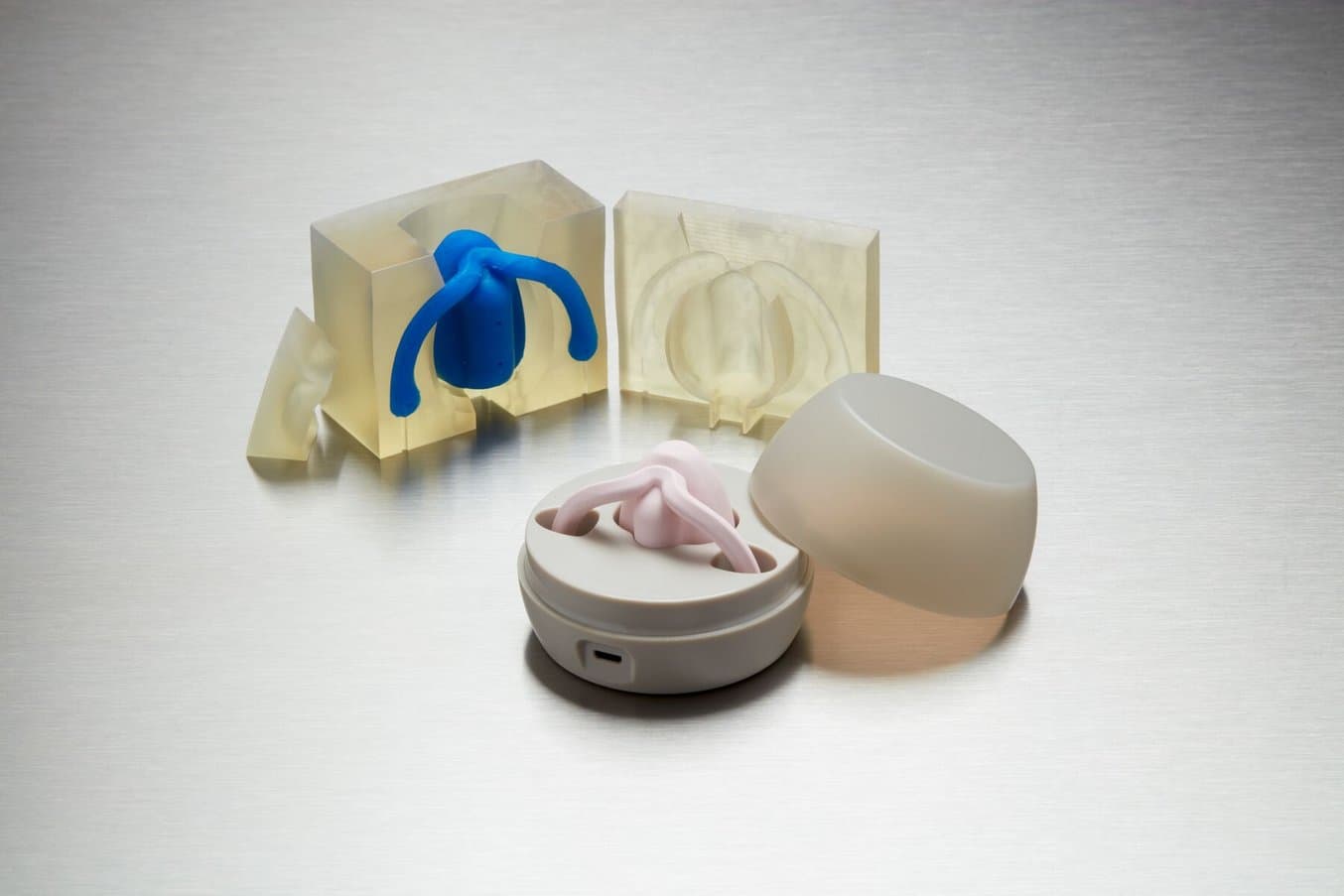
Dame Products setzt Insert-Molding ein, um die interne Hardware für Betatests durch die Kunden in Silikon einzufassen.
Die Ingenieure stellen pro Tag Dutzende Prototypen her, indem sie zwischen drei oder vier Gussformen aus dem SLA-3D-Drucker wechseln. Während das Silikon eines Prototypen aushärtet, kann das nächste schon aus der Form genommen und der darauffolgende Guss vorbereitet werden. Parallel findet die Fertigstellung und Reinigung der entformten Prototypen statt. Wenn die Hardwareprototypen zurück zum Unternehmen gelangen, wird das Betagerät gebleicht, die dünne Silikonschicht entfernt und die interne Hardware dann für einen neuen Betaprototypen verwendet.
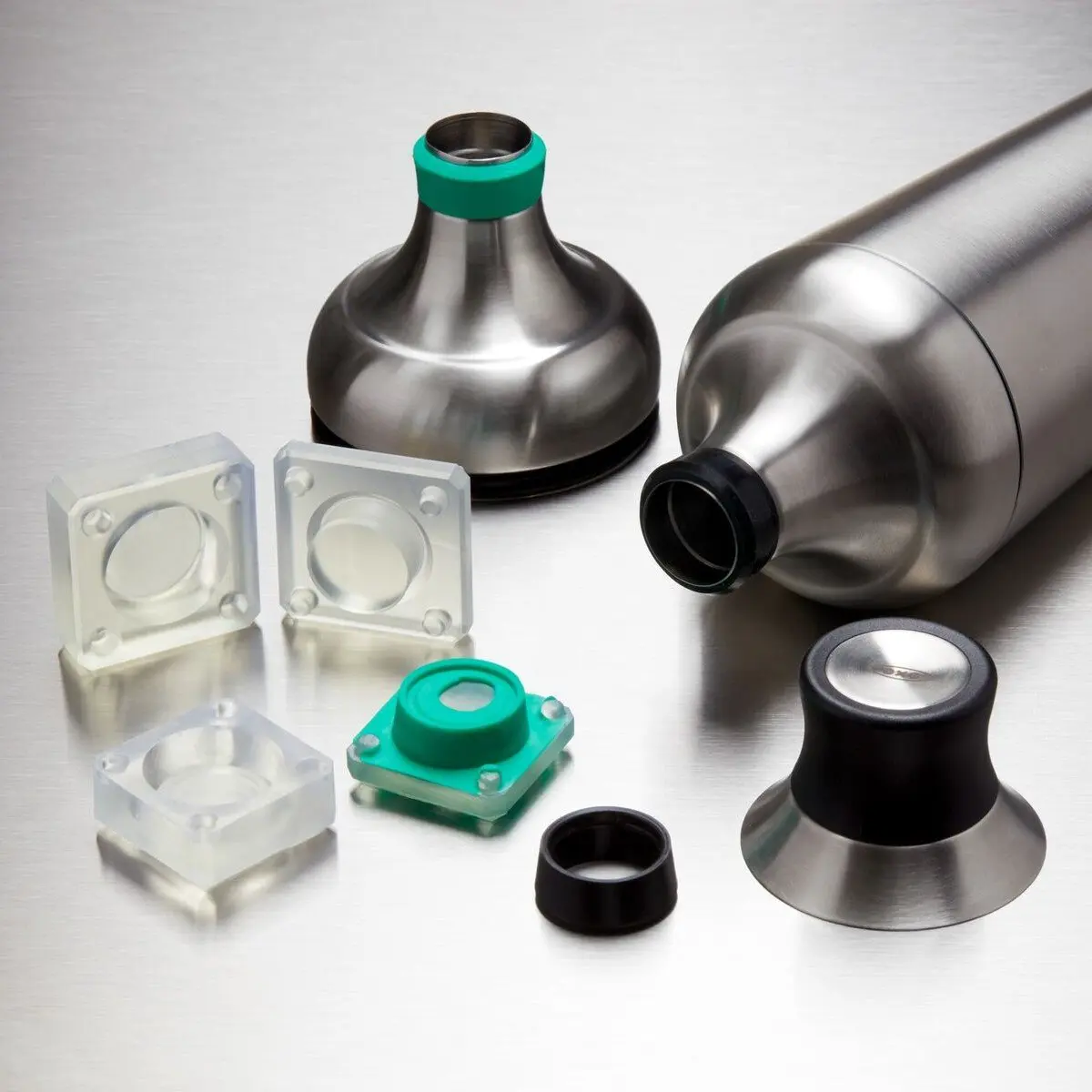
Silikonformenbau für das Produktdesign
Laden Sie diesen Bericht mit Fallstudien von OXO, Tinta Crayons und Dame Products herunter, um von drei verschiedenen Umsetzungen des Silikonformenbaus in Produktdesign und Fertigung zu erfahren, einschließlich Umspritzung und Formpressen.
Formpressen
3D-gedrucktes Rapid Tooling dient auch beim Formpressen zur Produktion von Thermoplast-, Silikon-, Kautschuk- oder Verbundwerkstoffteilen. Bei der Prototypenentwicklung kleiner und mittelgroßer Teile ist 3D-Druck wahrscheinlich die billigste und schnellste Lösung zur Gesenkfabrikation. In der CAD-Software lassen sich schnell mehrere Iterationen erstellen, die dann gedruckt und getestet werden. 3D-Druck kommt dabei am häufigsten für Formpressgesenke zum Einsatz, die ohne Hitzezuführung auskommen.
Die Produktentwickler beim Küchenutensilienhersteller OXO nutzen 3D-Druck zur Prototypenentwicklung gummiartiger Teile wie Dichtungen, wobei sie 3D-gedruckte Gesenke zum Formpressen von Zwei-Komponenten-Silikon einsetzen.
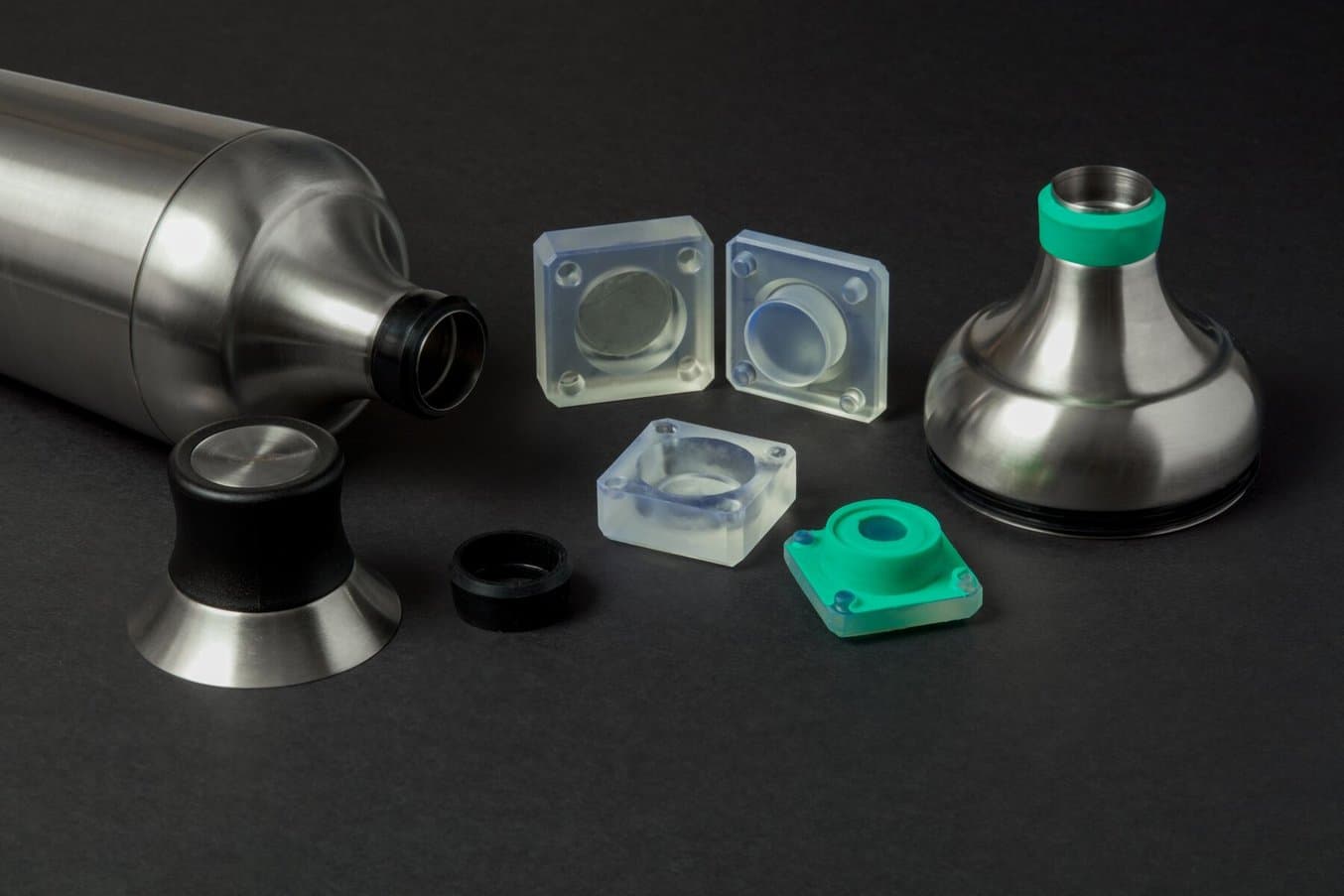
3D-Druck ist eine schnelle und billige Methode zur Anfertigung von Formpressgesenken.
Guss
Ingenieure, Designer, Juweliere und Hobbybastler können sich die Geschwindigkeit und Flexibilität des 3D-Drucks zunutze machen, indem sie Metallgussverfahren wie indirekten Feinguss, Direktfeinguss, Zinngießen und Sandguss mit 3D-gedruckten Modellen kombinieren oder Metall direkt in 3D-gedruckte Formen gießen. Gussteile aus Metall lassen sich mit 3D-gedrucktem Rapid Tooling verglichen mit traditionellem Guss in einem Bruchteil der Zeit herstellen. Gleichzeitig sind die Kosten um ein Vielfaches geringer als beim Metall-3D-Druck.
Stereolithografie-3D-Drucker eignen sich dank ihrer hohen Präzision und der umfassenden Materialbibliotheken für Gussverfahren. So können Metallteile zu geringeren Kosten, mit größerer Gestaltungsfreiheit und schneller als mit traditionellen Methoden gefertigt werden.
Herkömmlicherweise werden Modelle für den Feinguss von Hand geschnitzt oder spanend bearbeitet, wenn das Teil ein Unikat ist oder nur eine Handvoll Teile hergestellt werden soll. Mit 3D-Druck hingegen drucken Juweliere direkt die 3D-Modelle, ganz ohne die Design- und Zeitbeschränkungen der anderen Verfahren.
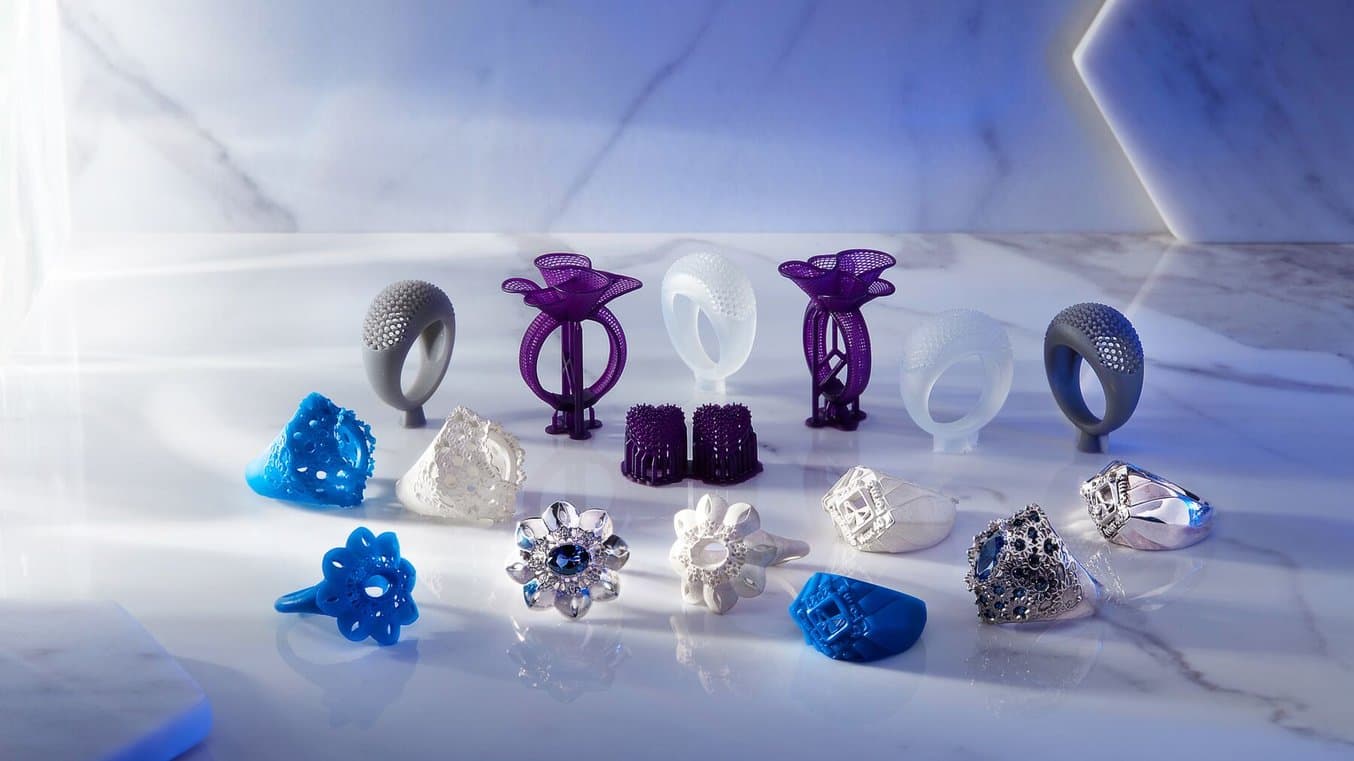
3D-gedruckte Schmuckmodelle und gegossene Edelmetallringe
Ähnlich wie beim Feinguss kann auch 3D-Druck für Sandgussmodelle verwendet werden. Im Gegensatz zu herkömmlichen Materialien wie Holz gewährt 3D-Druck Herstellern die Freiheit komplexer Gestaltung und die Möglichkeit, direkt vom digitalen Design zum Guss überzugehen.
Mit 3D-Druck können Hersteller die Form für Ihr Modell direkt aus Materialien wie High Temp Resin oder Rigid 10K Resin drucken. Diese Kunstharze sind äußerst hitzebeständig. Dasselbe Verfahren lässt sich auch auf Formen für den direkten Zinnguss übertragen.
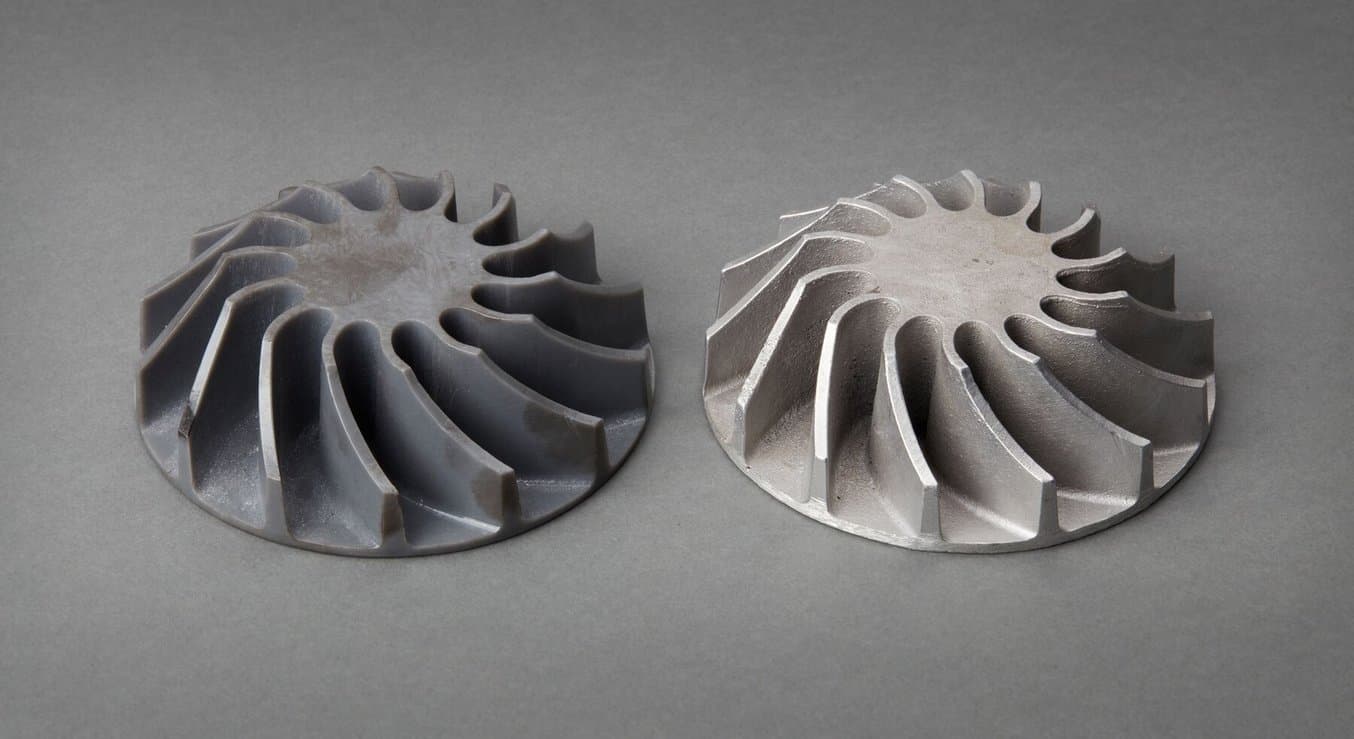
Modell aus Grey Resin und fertiger Aluminiumguss aus einer offenen Sandform
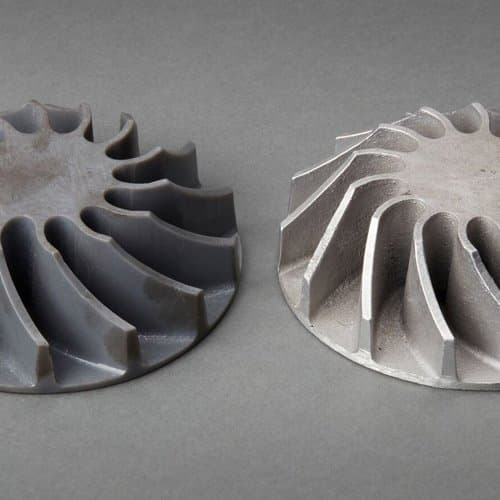
Herstellung von Metallteilen mit 3D-Druck
Erhalten Sie Designleitfäden zur Erstellung 3D-gedruckter Modelle, gehen Sie Schritt für Schritt durch das Direktfeingussverfahren und erfahren Sie die Anforderungen für den indirekten Feinguss und den Sandguss.
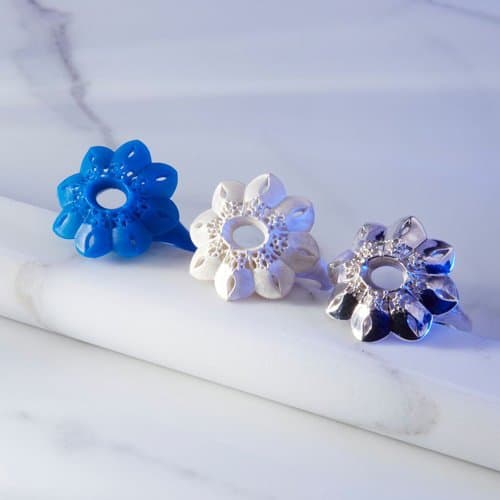
Einführung in das Gießen von 3D-gedruckten Schmuckmustern
Die Art und Weise, wie Juweliere arbeiten, verändert sich – und gussfähige Photopolymer-Kunstharze spielen dabei eine entscheidende Rolle. In diesem Leitfaden lernen Sie, wie Sie filigrane Schmuckstücke mit Mustern aus einem Formlabs-Drucker gießen.
Außer bei Metallen ist Gießen auch noch ein beliebtes Verfahren für Silikon- und Kunststoffteile für Medizinprodukte, in der Audiologie, für lebensmittelechte Anwendungen und darüber hinaus.
Das Medizinproduktunternehmen Cosm fertigt patientenspezifische Pessare für Patientinnen mit Beckenbodenstörungen. Die Formen werden auf einem SLA-3D-Drucker gedruckt. Anschließend wird biokompatibles Silikon in medizinischer Qualität eingespritzt, um das Teil herzustellen. Dank Rapid Tooling aus dem 3D-Drucker erstellt das Unternehmen maßgefertigte Teile ganz ohne die hohen Kosten traditioneller Werkzeugbestückung.
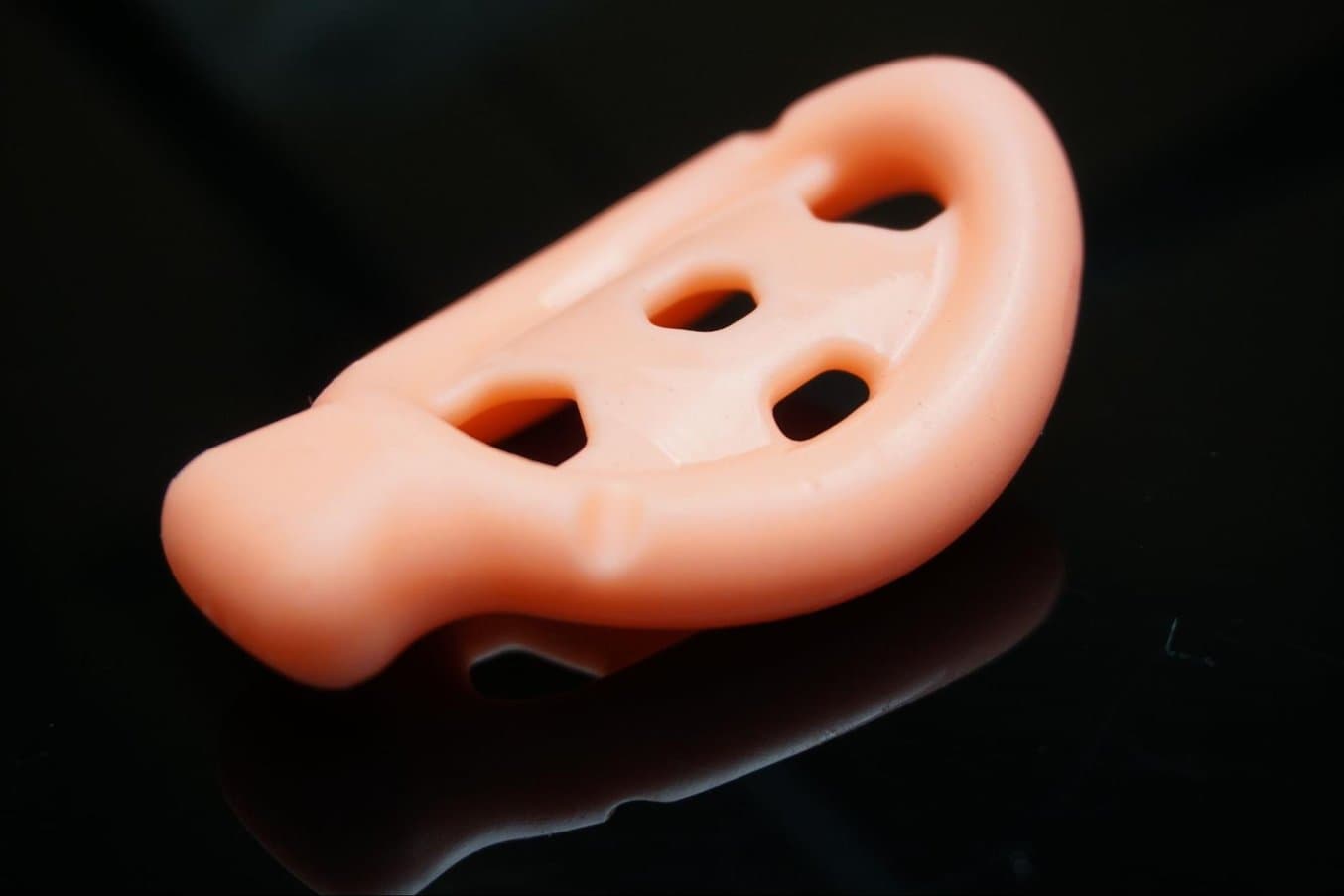
Patientenspezifisches Pessar, hergestellt mit Silikonguss
Die Herstellung maßgefertigter Otoplastiken mithilfe von 3D-Druck hat die Audiologie revolutioniert. Zu den Anwendungen gehören Hörgeräte, Gehörschutz und maßgeschneiderte Ohrhörer. Die digitale Fertigung bietet im Vergleich zur traditionellen Formherstellung bessere Kontrolle und Genauigkeit. Dadurch treten erheblich weniger Fehler auf und es sind weniger Überarbeitungen erforderlich.
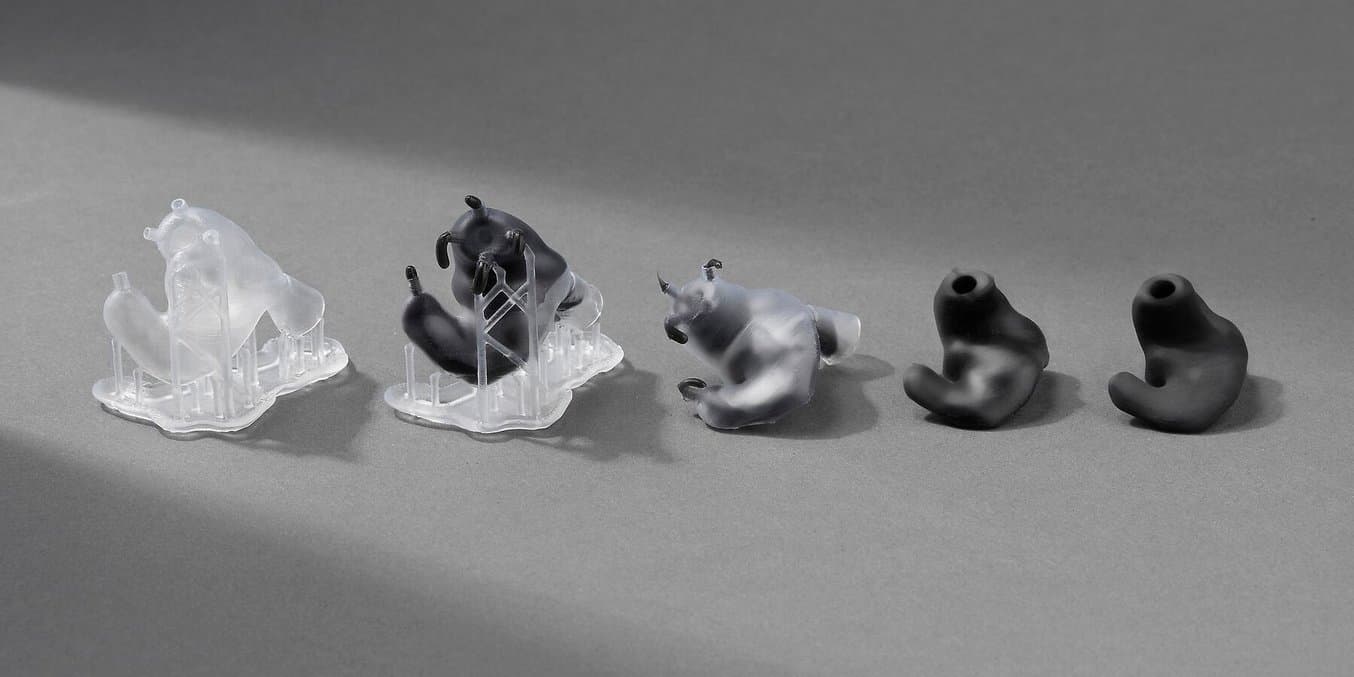
Die verschiedenen Schritte maßgefertigter Ohrstücke mithilfe von Otoplastiken aus Silikon
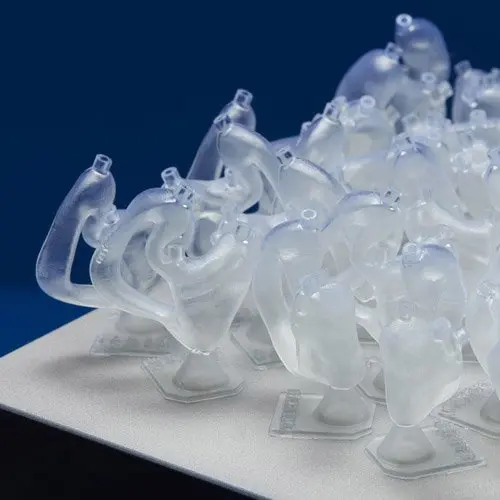
3D-Druck weicher personalisierter Otoplastiken
Gehen Sie Schritt für Schritt durch den Prozess zur kostengünstigen Herstellung maßgefertigter Silikon-Otoplastiken mit einem 3D-Drucker von Formlabs und unserem Standard-Kunstharz Clear Resin.
Blechumformung
3D-gedrucktes Rapid Tooling bietet auch interessante Eigenschaften für die Blechumformung. Dank hoher Präzision und glatter Oberflächenbeschaffenheit produzieren SLA-Drucker Werkzeuge mit ausgezeichneter Merkmalabbildung und wiederholbareren Ergebnissen. Mithilfe einer vielseitigen Materialbibliothek mit verschiedensten mechanischen Eigenschaften optimieren Sie das Ergebnis der Umformung durch die Auswahl eines für den speziellen Anwendungsfall geeigneten Kunstharzes. SLA-Kunstharze sind isotrop und im Vergleich zu anderen 3D-Druckmaterialien relativ stabil unter Belastung. Durch die Werkzeugbestückung aus Kunststoff kann außerdem das Polieren als Arbeitsschritt entfallen, da Formwerkzeuge aus Kunststoff keine Spuren auf dem Blech hinterlassen – im Gegensatz zu solchen aus Metall.
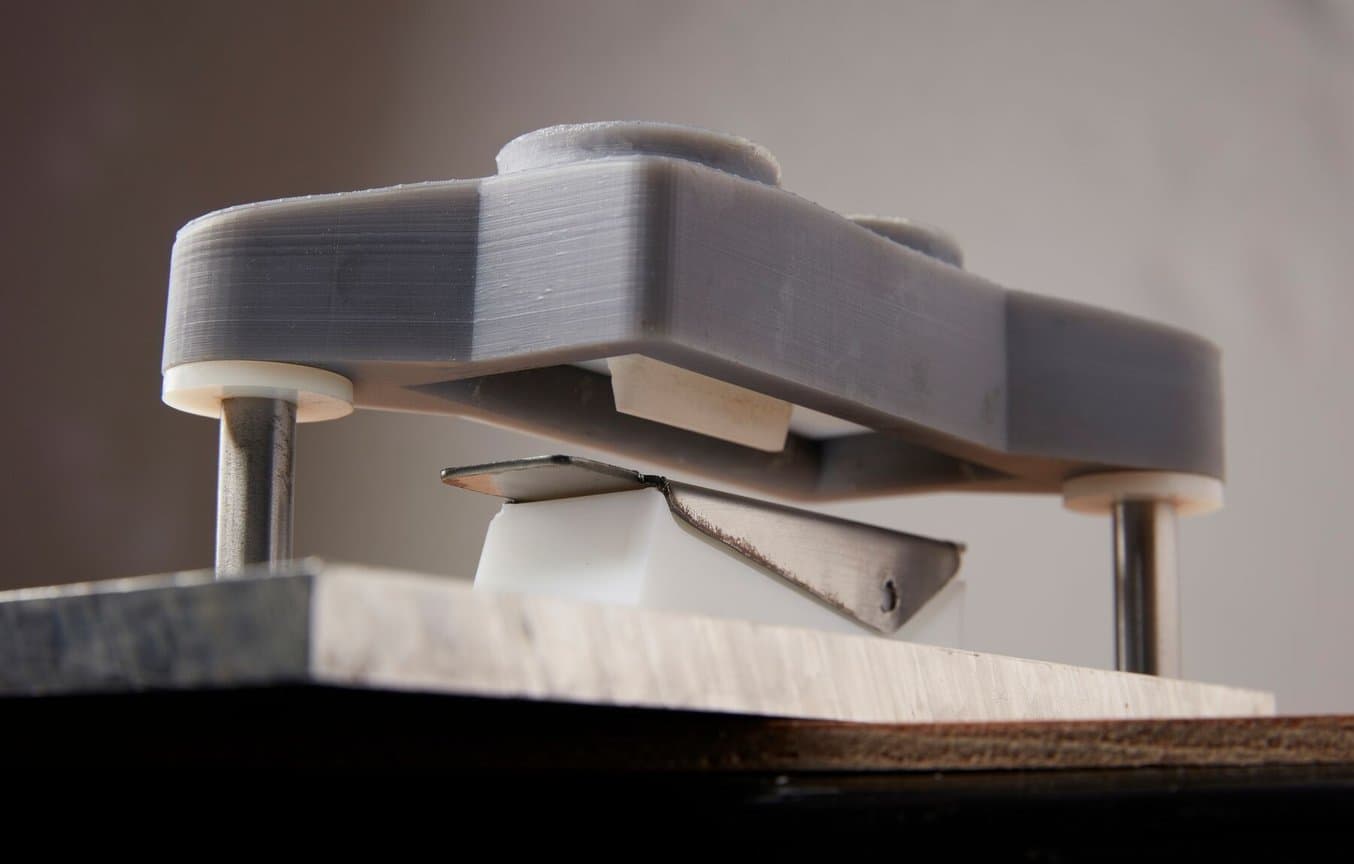
Verschiedene Iterationen 3D-gedruckter Ober- und Unterwerkzeuge zur Formung eines Ersatzklingenschutzes
Der Mechanismus ähnelt dem allgemeinen Arbeitsablauf der Blechumformung. Der Unterschied liegt im Design und Druck des zweiteiligen Werkzeugs aus Ober- und Unterwerkzeug. Der Blechzuschnitt wird zwischen den beiden Formwerkzeugen aus Kunststoff platziert und mit einer Hydraulikpresse oder ähnlichem Gerät gepresst.
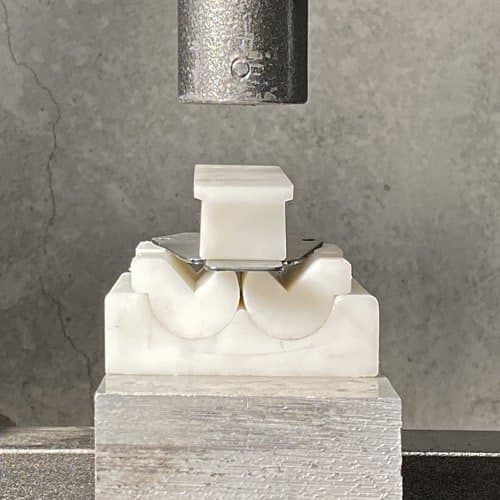
Rapid Tooling für die Blechumformung mit 3D-gedruckten Formwerkzeugen
In dieser Studie wird die Tauglichkeit SLA-gedruckter Formwerkzeuge zum Formen von Blechteilen untersucht und gezeigt.
Herstellung von Rapid Tooling
Die beliebtesten und geläufigsten Verfahren zur Herstellung von Rapid Tooling sind 3D-Druck und Zerspanung. Vergleichen wir einmal beide Optionen, um die richtige Lösung zu finden für die Anwendung, das Fertigungsverfahren, die Produktionsmenge und alle weiteren Faktoren.
3D-Druck
3D-Druck ist die schnellste und erschwinglichste Produktionsmöglichkeit für das Rapid Tooling einer Vielzahl von Anwendungen. Wie wir bei den vorherigen Beispielen gesehen haben, nutzen direktes und indirektes Rapid Tooling den 3D-Druck auf unterschiedliche Weise, um für vielfältige Fertigungsverfahren funktionsfähige Werkzeuge herzustellen, beispielsweise Gussformen, Modelle oder Presswerkzeuge.
Unter den verschiedenen 3D-Druckprozessen bieten SLA-Drucker die vielseitigsten Lösungen zur Werkzeugbestückung. SLA-Druckteile sind präzise, wasserdicht, haben eine glatte Oberfläche ideal für Gussformen und bilden bei Formen und Modellen auch kleinste Details ab.
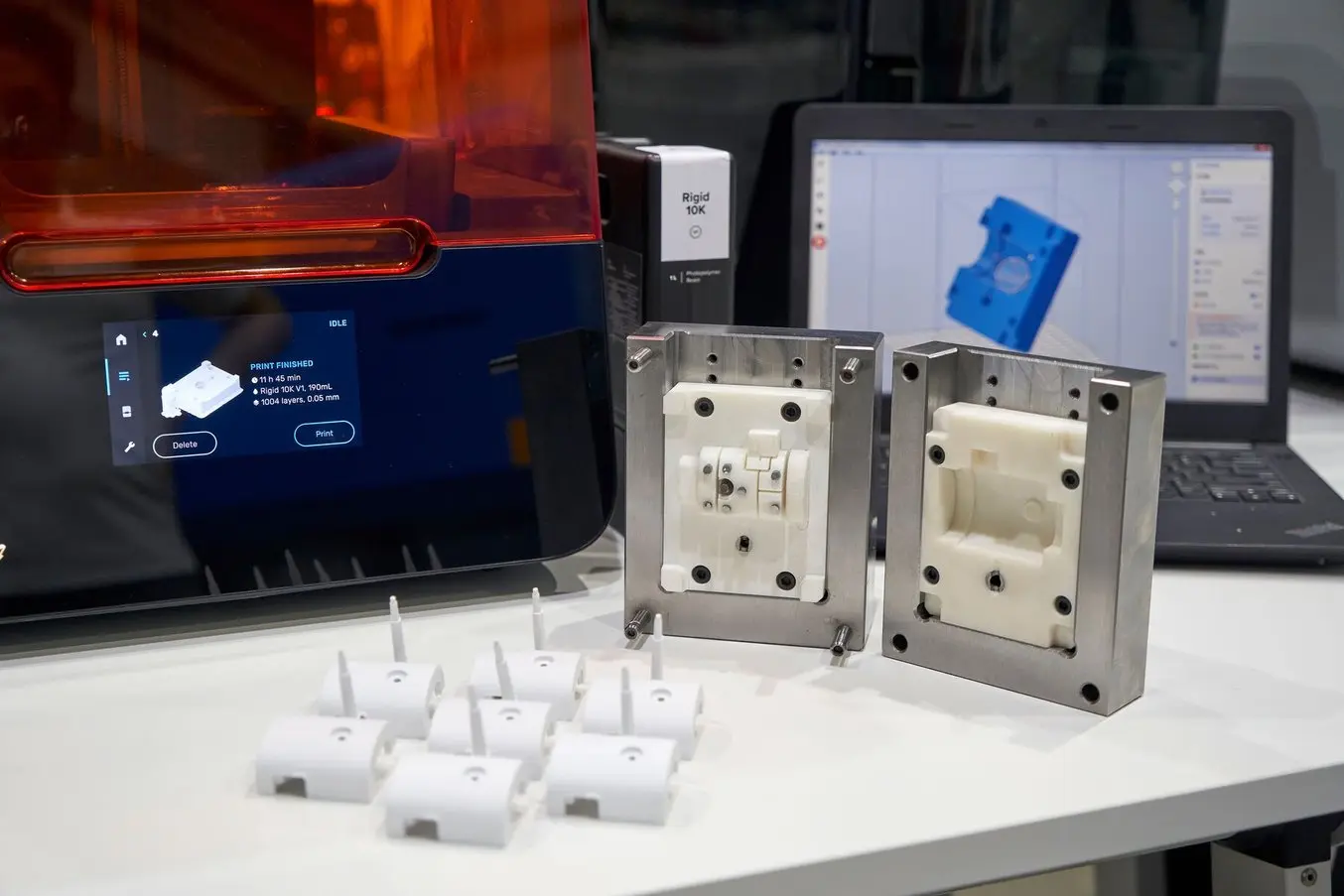
3D-gedrucktes Rapid Tooling eignet sich ideal für den Spritzguss von Kleinserien.
Die Hochleistungsmaterialien fügen sich leicht in industrielle Arbeitsabläufe ein. Mit ihnen fertigen Sie starke, glatte, hochdetaillierte Formen und Modelle, mit denen sich Hunderte bis Tausende von Teilen herstellen lassen.
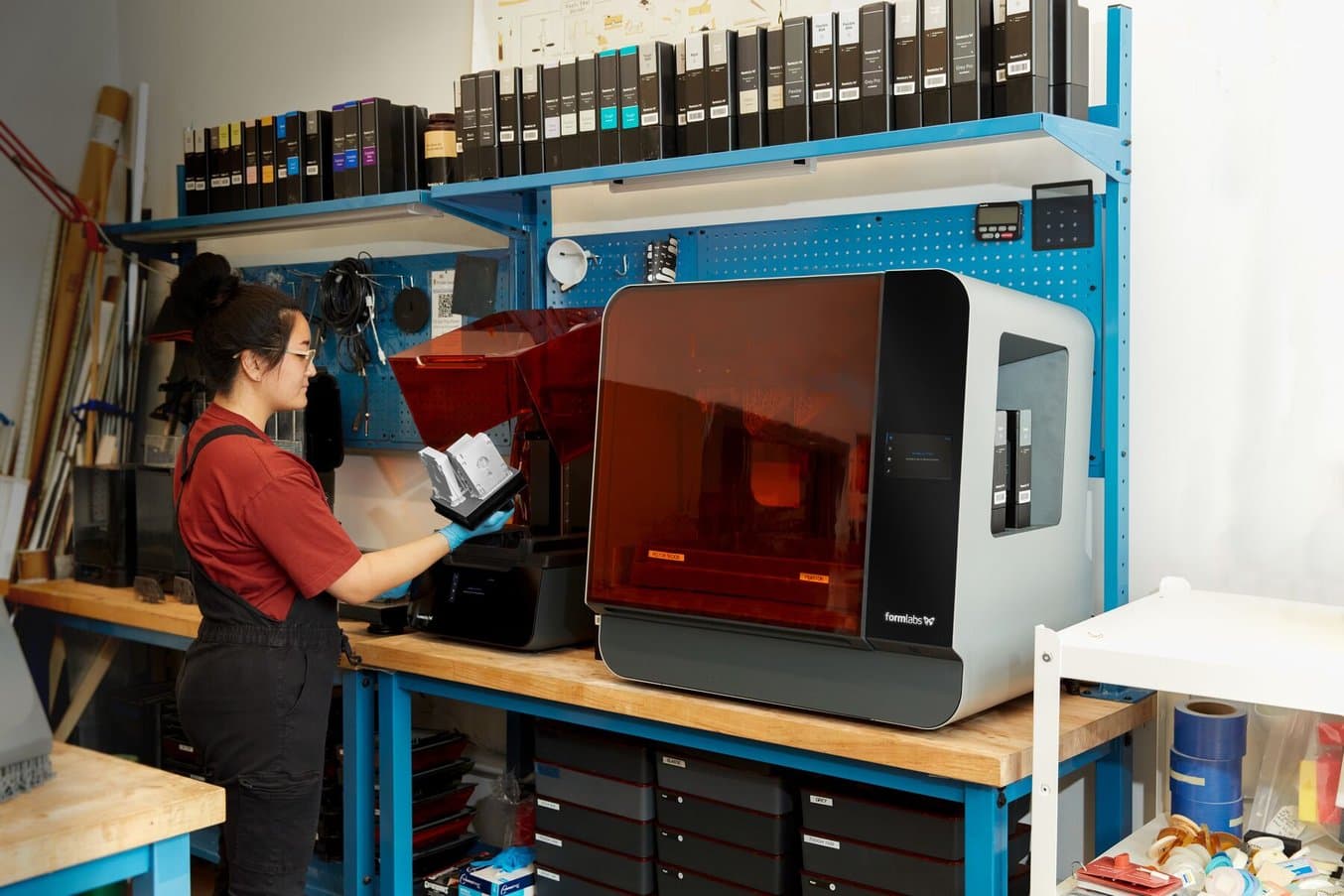
SLA-3D-Drucker lassen sich leicht betriebsintern aufstellen, was das Rapid Tooling noch schneller und zugänglicher macht.
SLA-Drucker machen betriebsinternes Rapid Tooling zugänglicher denn je. Eine 3D-Druckstation kann auch mit einem begrenzten Budget leicht betriebsintern eingerichtet und unterhalten werden. So erstellen Unternehmen ihr Rapid Tooling in unter 24 Stunden und iterieren ihre Designs schneller als mit jedem anderen Prozess.
Zerspanung
Zerspanung ist eines der geläufigsten Verfahren zur Herstellung konventioneller Werkzeugbestückung wie Hard Tooling, lässt sich aber auch für Rapid Tooling einsetzen. Statt aus langlebigen Metallen wie Stahl oder Nickellegierungen wird Rapid Tooling meistens aus Werkzeugplatten, Holz, Kunststoff oder Aluminium zerspant.
Gegenüber 3D-gedruckter Werkzeugbestückung ist die Zerspanung weicher Materialien manchmal effizienter für großformatige Werkzeuge und sehr einfache Geometrien. Doch mit zunehmender Designkomplexität steigt der Arbeitsaufwand schnell. Werkzeugbestückung aus Aluminium ist langlebiger und wird allgemein für kleine oder mittelgroße Produktionsmengen verwendet, insbesondere beim Spritzguss.
Zerspanungsgeräte sind teurer und benötigen sachkundiges Fachpersonal. Die betriebsinternen Arbeitsabläufe sind verglichen mit 3D-Druckern komplex, besonders bei Einzelstücken wie den verschiedenen Prototypiterationen beim Rapid Tooling. Deshalb lagern viele Unternehmen die Zerspanung an Dienstleister aus, was jedoch oft wochenlange Durchlaufzeiten nach sich zieht und somit den „Rapid“-Aspekt eliminiert.
Vergleich der Fertigungsverfahren für Rapid Tooling
3D-gedruckte Werkzeugbestückung | Zerspante Werkzeugbestückung | |
---|---|---|
Methode | Betriebsinterne Werkzeugbestückung und Teileproduktion | Ausgelagerte Werkzeugbestückung und oft auch Teileproduktion |
Erforderliche Geräte | 3D-Drucker, Fertigungsgerät (Desktop-Spritzgussmaschine, Tiefziehgerät usw.) | - |
Material | 3D-gedrucktes Polymer | Zerspante Werkzeugplatte, Holz, Kunststoff oder Aluminium |
Kosten der Werkzeugbestückung | € | €€–€€€ |
Durchlaufzeit bis zum Endprodukt | Ein bis drei Tage | Eine bis vier Wochen |
Ideales Produktionsvolumen | < 500 Teile | 50–10 000 Teile |
Anwendungen | Prototypenentwicklung Produktvalidierung Maßanfertigungen Kleinserien und Sonderanfertigungen Übergangsproduktion | Produktvalidierung Kleinserien und Sonderanfertigungen Übergangsproduktion |
Rapid Tooling aus dem 3D-Drucker
Rapid Tooling lässt sich nahtlos in viele traditionelle Fertigungsprozesse integrieren. Der Arbeitsablauf unterscheidet sich etwas, abhängig vom jeweiligen Fertigungsverfahren, umfasst jedoch im Allgemeinen die folgenden Schritte:
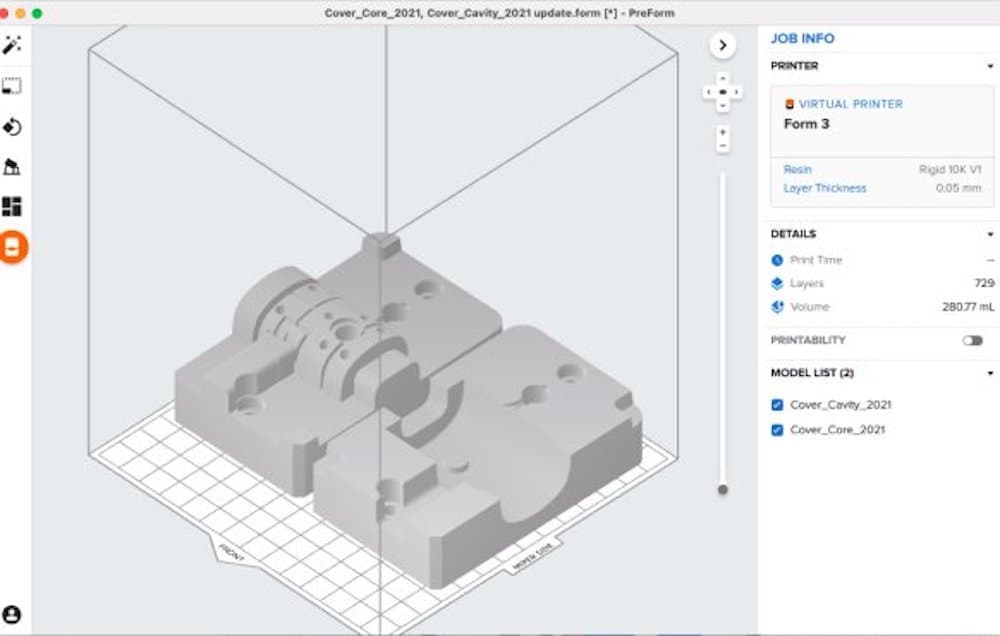
1. Design
Entwerfen Sie die Formen, Modelle, Aufsätze oder Werkzeuge in der CAD-Software.
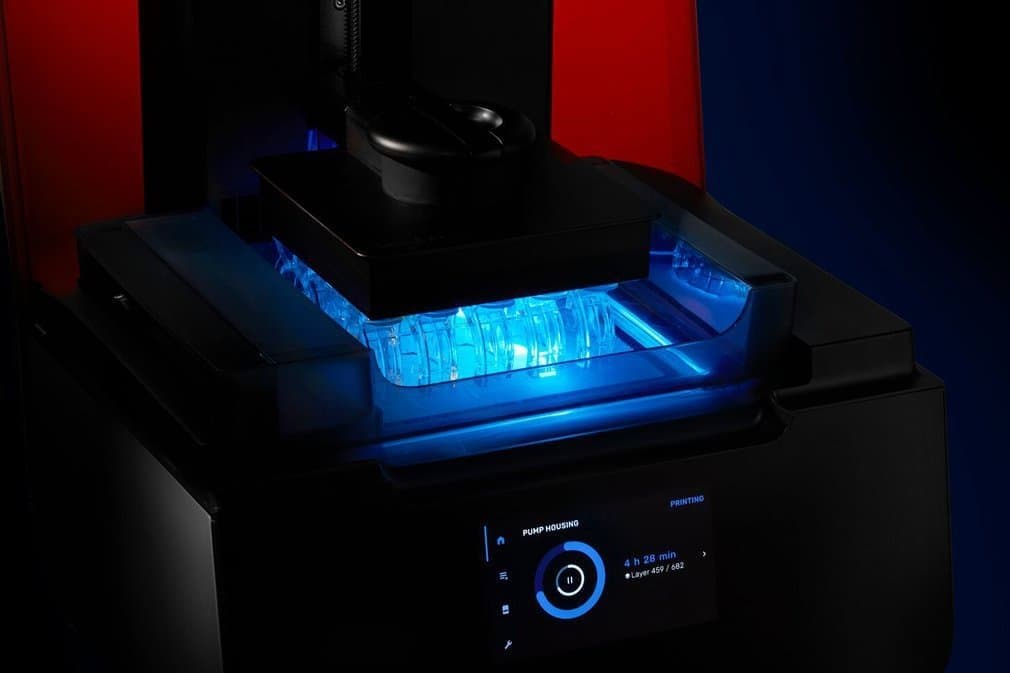
2. 3D-Druck
Wählen Sie das richtige Material für Ihre Anwendung aus. Formlabs bietet eine umfassende SLA-Materialbibliothek zum 3D-Druck zahlreicher Rapid-Tooling-Anwendungen.
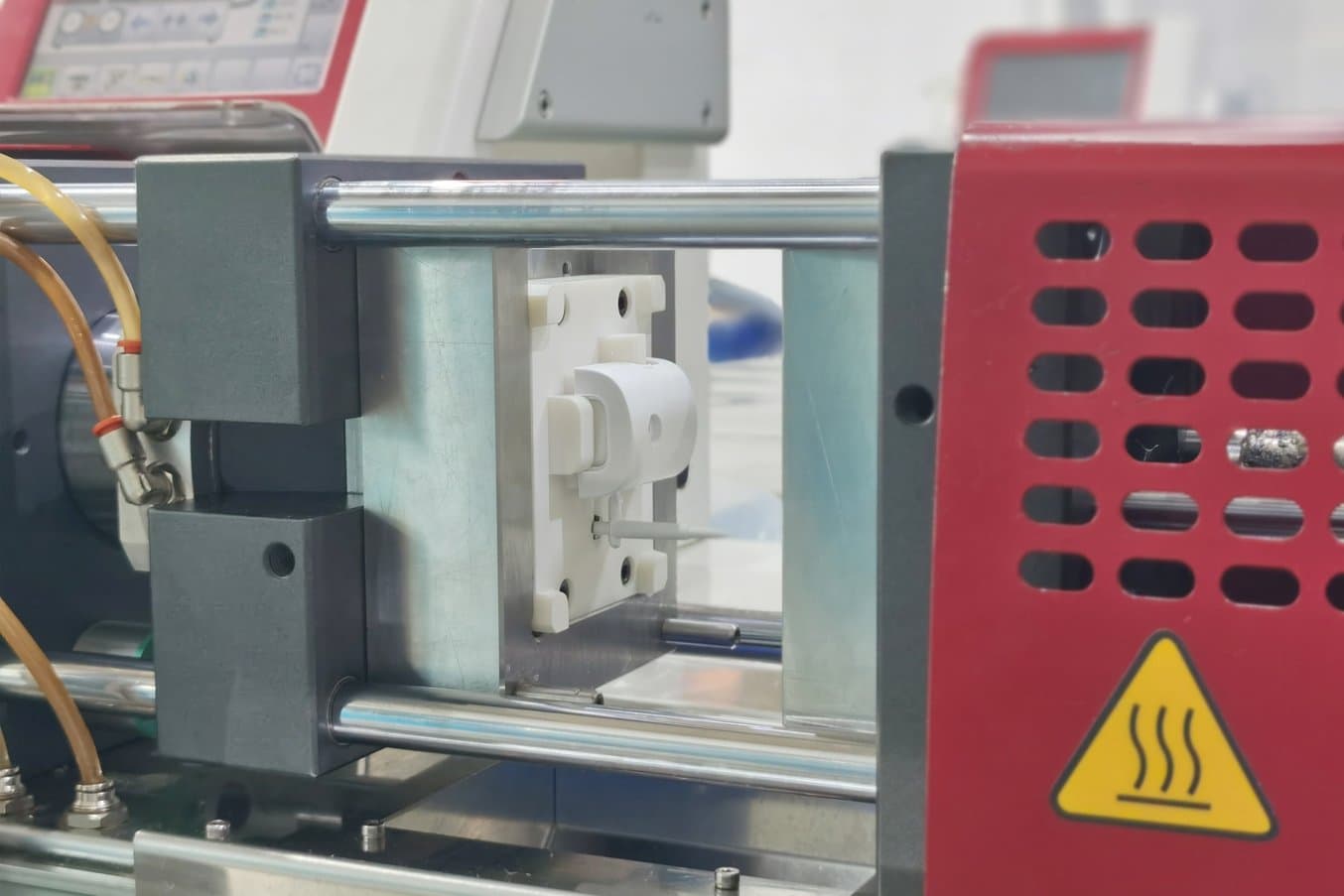
3. Fertigung
Mit direktem Rapid Tooling nutzen Sie das 3D-gedruckte Werkzeug in Ihrem Gerät und führen so den Produktionsprozess durch. Mit indirektem Rapid Tooling erstellen Sie Formen oder Werkzeuge anhand eines Urmodells und nutzen das daraus resultierende Werkzeug in Ihrem Arbeitsablauf.
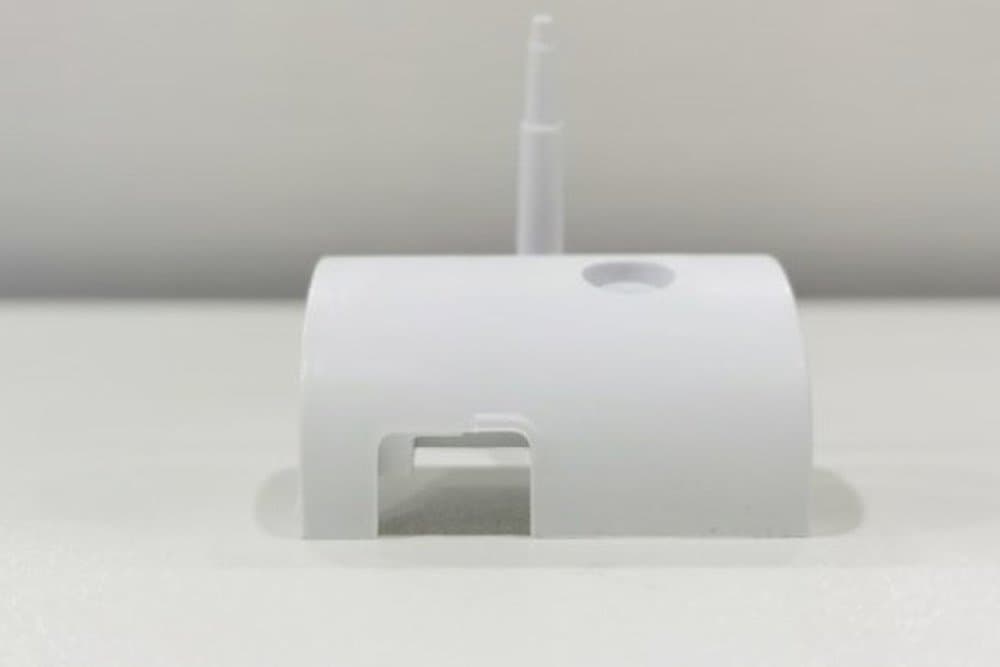
4. Nachbearbeitung
Führen Sie die nötigen Nachbearbeitungsschritte durch, um die gewünschte Qualität des Endprodukts zu erreichen.
Erste Schritte zum Rapid Tooling
Kombinieren Sie Rapid Tooling aus dem 3D-Drucker mit traditionellen Herstellungsverfahren, um bessere Flexibilität, Agilität, Skalierbarkeit und Kosteneffizienz in Ihrem Produktionsprozess zu erreichen. Validieren Sie Ihre Designs und Materialwahl, noch bevor Sie zur Massenproduktion übergehen, und produzieren Sie individualisierte Endverbrauchsteile oder Sondereditionen.
Entdecken Sie die verschiedenen Prozesse und laden Sie die Whitepaper inklusive Arbeitsabläufen, Leitfäden und realen Fallstudien von unserer Website herunter. Sollten Sie Fragen haben, wenden Sie sich an die Lösungsspezialisten von Formlabs.