「私はわずか通り2つ先にある食料品店に買い物に行くことさえ諦めていました。」
WHILLの創業者である杉江理氏がこの言葉を聞いたとき、この状況を何とかして変えなければならないと思いました。現在彼は、「すべての人の移動を楽しくスマートにする」をミッションとする車椅子会社の代表取締役兼CEOを務めています。
次世代型車椅子を開発することは容易なことではありませんでした。WHILのエンジニアチームは、製造工程にFormlabsのプリンタとジェネレーティブデザインを取り入れることで、チームの可能性を押し上げ、全く新しいスタイルの製品を作り出すことに成功しました。
WHILLの車椅子の研究開発を行う平田 泰大氏のお話。
3D造形で開発を加速
スタートアップ企業は数多くの問題に直面しますが、最たるものは時間とコストのプレッシャーです。このことが特に顕著なのはハードウェアのスタートアップ (弊社もその1つ!)で、新しい問題が発生してはゼロから解決策を見つけていくことの繰り返しです。スタートアップ企業の成功の鍵の1つは、予期しないハードルをどう乗り越えるかで、それにはコストと時間がかかってしまうリスクがあります。車椅子製造に必要な部品は複雑であるため、数多くの問題に直面するWHILLにとって、従来の製造方法で少量のパーツを生産することが大きな課題となりました。会社が生き残るためには、各車椅子のコストを下げるための方法が不可欠でした。
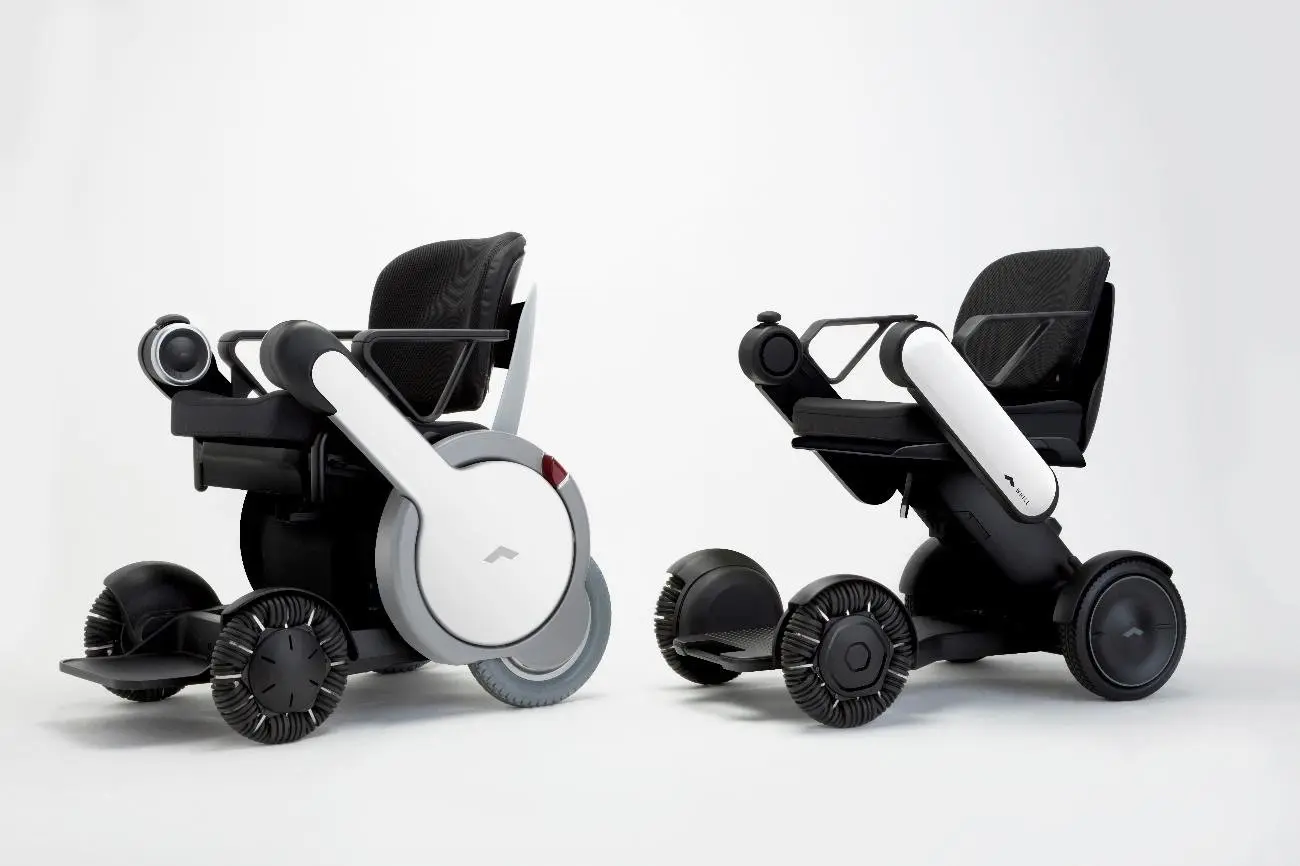
会社は、多くの複雑な車椅子部品のプロトタイプを素早く製造することの重要性を理解し、3D造形の外注先を探すことにしました。しかしWHILLはまもなく、3D造形の外注はコストとスピードに大きな問題があり、チームにとって長期的な実行は不可能であることに気付きました。物理的なプロトタイピングを行わずにプロジェクトを完成させることはできないため、平田氏は内製での3D造形を導入することを決意しました。
「どの形状が適切かを知りたければ、実際に作って確かめることである」
平田氏は、以前使用したことのあるフューズドフィラメントファブリケーション (FFF) に良い印象がありませんでした。しかしFormlabsの成功を目の当たりにし、その製品の1つに投資することを決意しました。2016年に、WHILLは初めてFormlabsのプリンタを導入しました。それ以来、様々なプロジェクトに用いられ、チームのニーズであった「素早く高品質なプロトタイプ」を実現していきました。部品のプロトタイプは、ユーザーが実際に直接触って確かめることが大切です。そういったプロトタイプに必要な造形物は、外観も感触も本物と同じで、安っぽさが無く中が空洞でなければなりません。FormlabsのSLA方式プリンタは、平田氏がエンドユース用プロトタイプにまさに望んでいた、高品質、細かいディテール、手頃な価格のパーツの造形を可能にしました。
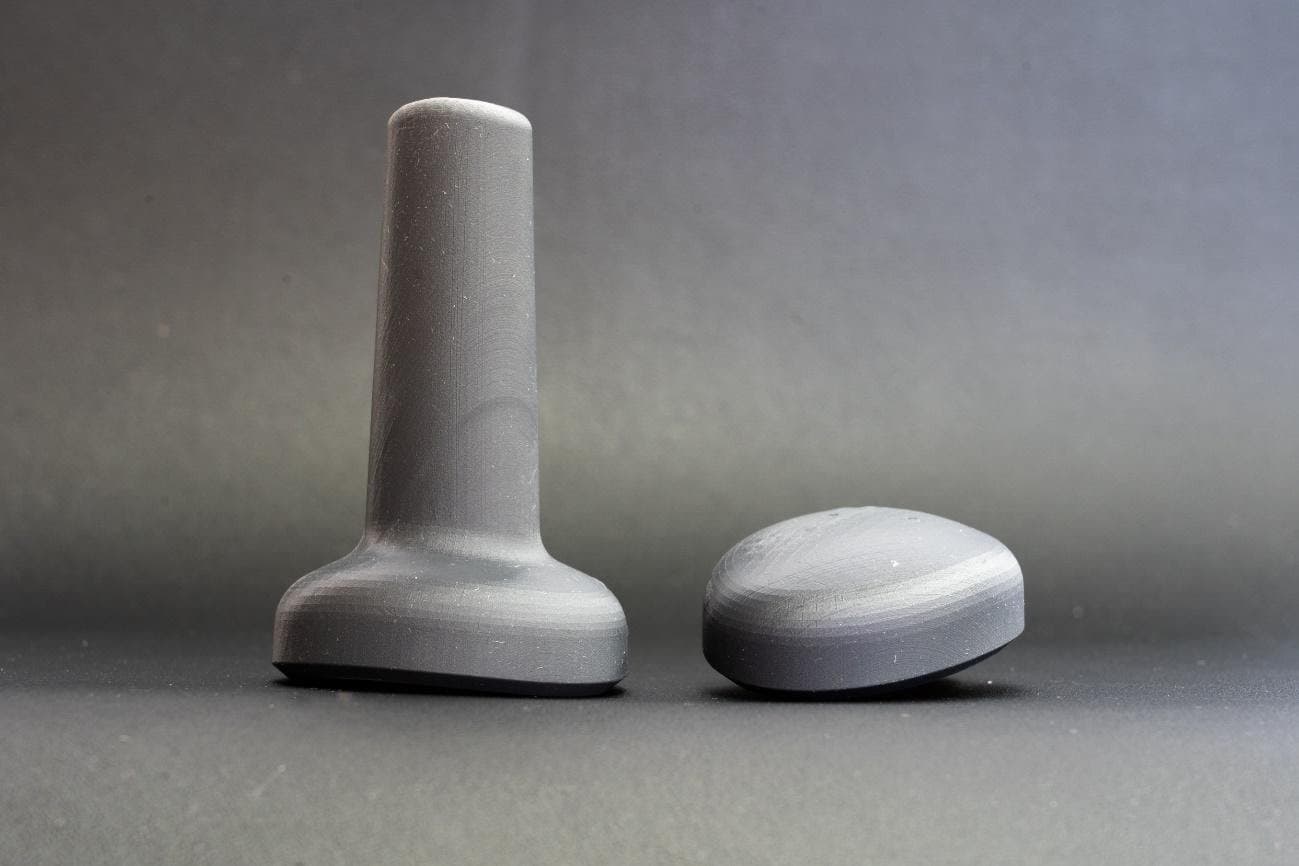
WHILLの開発チームが最終製品を造るために高精細度の3Dプリンタの導入は不可欠でした。触感などの評価を行うとき、少なくともプロトタイプのパーツが量産される最終製品と品質的に同等でなければ、検証する意味がありません。WHILLは、Formlabsのプリンタで作ったパーツはほぼ完璧なサンプルとなり、車椅子のプロトタイプの内部テストとユーザーテストで使われました。
「例えばコントローラーなど、ユーザーが触って確かめるべきパーツのプロトタイプはできる限り多く製作し、検証したいと思っています。かつてのようにプロトタイプを外注していたら、予算とスケジュールの制約によって、製作できるパーツ数や開発研究の機会が限られてしまいます。Form 2を使用し、実際の量産製品に近い触感を有するFlexible レジンを材料に選ぶと、数の制限なく、高精度のプロトタイプを作成し検証することができます。」
平田 泰大
1つのFormlabsプリンタの汎用性を生かし、チームは1つのプロジェクトに様々なレジンを使いました。Flexible Resinは触感が重要なパーツに、Clear レジンは車椅子ディスプレイ周辺の半透明性のパーツに、Tough レジンは高い強度を要するパーツに使われました。ハードウェアのスタートアップにとって、使用事例によって異なる材料が選べ、多数のパーツを正確に造形できるマシンを1台所有することは、時間とコストを大幅に削減することです。
「Form 2は精度が高いだけでなく、停止や故障が滅多にありません。おかげで、我々は毎日多様なプロトタイプを製作し、品質向上のために検証を積み重ねることができました。」(平田)
平田 泰大
プロトタイピングは単に1つのパーツを完成させるためのものではありません。様々な設計を検証することで、多数のパーツの最適化と結合が可能になり、組み立て製品の統合につながります。WHILLは製品に使われるパーツ数を減らし、車椅子の最終製造コストを軽減することができました。内製での3D造形と複雑なジェネレーティブデザインを用いてこうしたパーツが造られたことは、チームにとって大きな躍進でした。
ジェネレーティブデザイン
ジェネレーティブデザインとは何百、ときには何千もの最適化された設計案を生成するために、主要な設計目的、機能、サイズ条件、材料、製造方法、コスト制限などを検討しながら、アルゴリズムを使うプロセスです。
WHILLSのチームは、車椅子の中心部に使う1つの丈夫な部品の製造について考案中でした。彼らはジェネレーティブデザインを用いて、一度に多数の設計案を分析することができました。1回限りの複雑な設計は、コストが高額になたり、従来のワークフローでは実現が不可能になる可能性があります。
「コストを考慮に入れないならば、カーボンなどの軽量材料を用いることができますが、それは現実的ではありません。実現可能な材料で重量を軽減するという目標のために、ジェネレーティブデザインを試してみることにしました。我々は少ない時間の中で、複雑な形状のプロトタイプを製作しなければならず、これを可能にするにはFormlabsの3Dプリンタとレジンしかないと考えました。」
平田 泰大
新たな複雑なパーツがまずCastable Waxを使って内製で造形されました。チームは車椅子の本体部分の生成にAutodeskのFusion 360を使い、ジェネレーティブデザインされた部品を内製でプロトタイプするというプロセスに目を見張りました。結果: WHILLは車椅子のフレームだけで40%軽量化に成功しました。
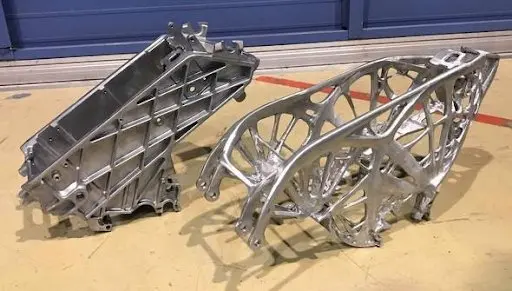
Formlabsのプリンタで内製プロトタイピング
WHILLは内製でのラピッドプロトタイピングのおかげで、素晴らしい製品の製作に成功した数ある企業の1つです。Formlabsのプリンタを導入したことでビジネスが大きく変化したその他の6社を紹介する、ラピッドプロトタイピングe-bookを無料でダウンロードしましょう。