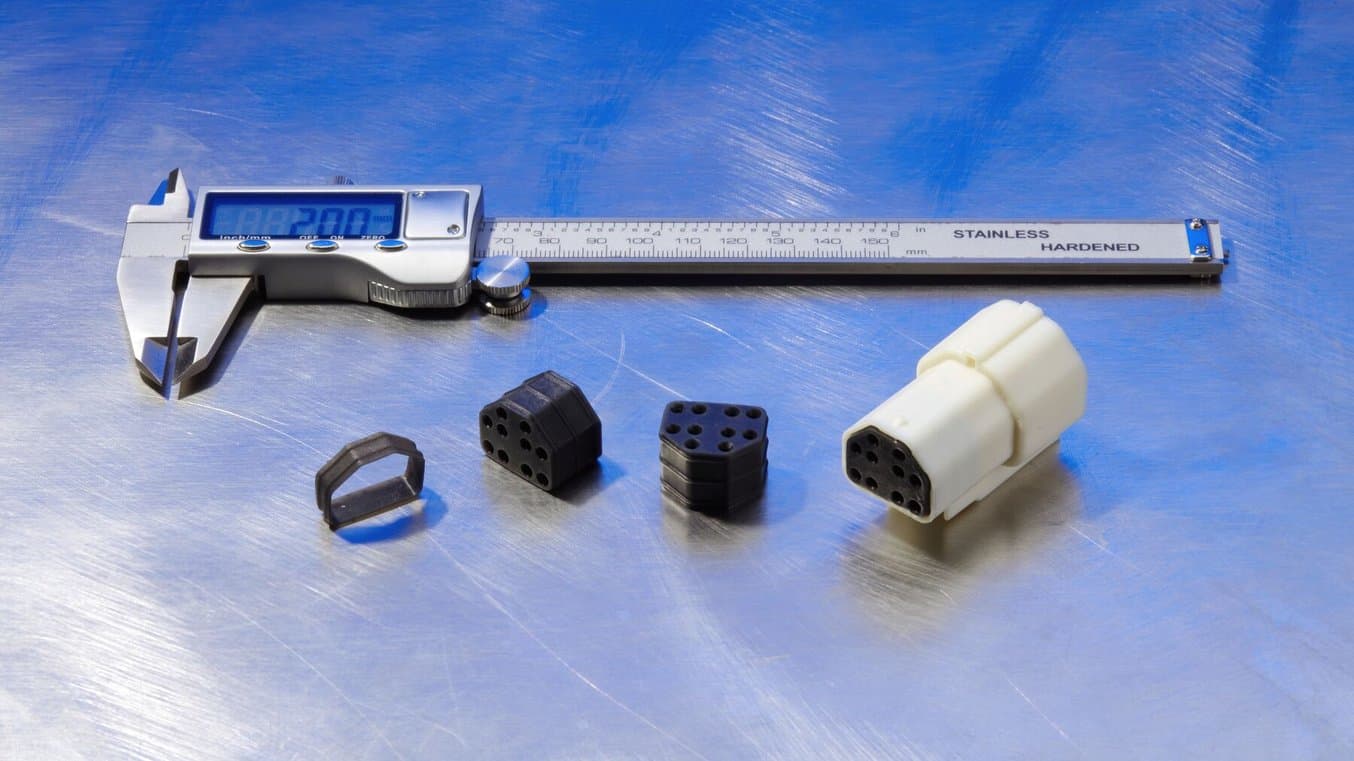
HGM Automotive ElectronicsがSilicone 40Aレジンで製作したコネクタシール
HGM Automotive Electronicsは、自動車アフターマーケット向けに最先端の電子機器を設計・供給する専門メーカーです。
HGM Automotive Electronicsの研究開発ディレクターであるGuy Cardwell氏は、ビンテージカーを多く扱うHGM Automotiveならではの課題として、エンジンの点検や修理に必要な部品を見つけることの難しさを指摘しました。特に部品が生産終了になると、コネクタやその他の電気部品がさらに入手困難になっていきます。
そこで、部品をオンデマンドで内製するのに最適な3Dプリントを、試作品製作や少量生産用に取り入れました。しかし、ここはIP保護等級や耐薬品性など特殊要件への遵守が求められる規制産業のため、使用する材料の選択が非常に重要です。自動車用コネクタシールの材料として最も一般的なのはソフトシリコンですが、軟質シリコン製の部品を作る方法は限られています。射出成形はコスト面で少量生産に向かず、また従来のシリコン鋳造では時間がかかってしまいます。
Formlabsから新たに登場したSilicone 40Aレジンは、初めて手頃な価格にて、柔らかくしなやかで耐久性のある部品の製造を可能にしたシリコン100%の3Dプリント材料で、「まさに求めていたもの」とCardwell氏は言います。厳しい化学的・機械的試験により、この新材料が実製品用自動車部品として優れた機械的特性と耐薬品性を持っていることが証明されました。同社は新材料のベータ・プログラムにも参加し、同材料を使った試作も行いましたが、主とする目標はあくまでも実製品用部品の少量生産です。
「Silicone 40Aレジンは完璧ですね。サプライヤーから仕入れていたシリコン材料の特性とかなり近いです」
Guy Cardwell氏 HGM Automotive Electronics 研究開発ディレクター
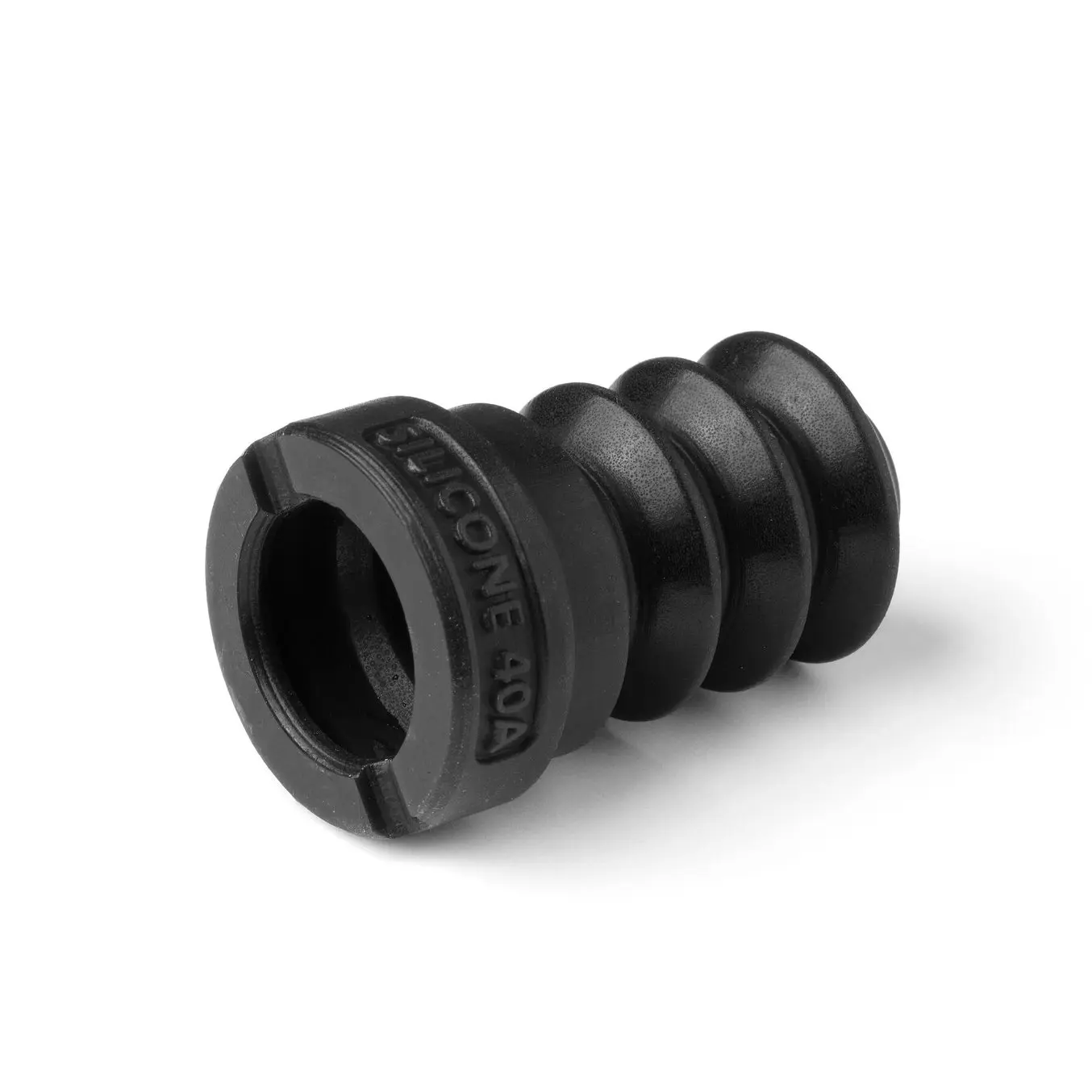
Silicone 40Aレジンでコネクタシールの設計に新たな可能性を
その他の製造手法 | Silicone 40Aレジンを使った3Dプリントの利点 |
---|---|
外注での射出成形 | 製造期間を90%削減 コストを98%削減 |
内製でのシリコン鋳造 | 難易度の高い複雑な形状も細部まできめ細かな表現が可能 作業時間、人為的ミスのリスク、製造期間を削減 10点〜1000点まで製造量を拡大でき、何度でも同じ部品が製造可能 |
コネクタの製造に成功したHGM Automotiveは、続けてカスタムシールの製造にも乗り出しました。シールも一般市場にはほとんど出回っておらず、見つかったとしても品質が十分でないことが多い、調達が困難な部品です。コネクタ用カスタムシールの開発で生じる課題は、適切な柔軟性を持つエラストマー材料がないことが原因でした。射出成形用の型を作り、非常に柔らかいウレタンを使って部品を作ることは可能です。ただしその場合は、金型の製作だけで$6,000ドルから$10,000ドルもコストがかかってしまいます。1万点の部品が必要な場合であればこの値段でも割に合いますが、実際の生産量は年間100点〜1000点程度です。さらに、一度金型を作ってしまうと設計変更はほとんど不可能です。形状が複雑になりがちなコネクタシールの場合、これは大きな障害になります。「あらゆる問題がコストと柔軟性に関わることでした」とCardwell氏は言います。
製作期間 | コスト | |
---|---|---|
外注での射出成形 | 3~4週間 | 金型製作$10,000 部品単価$0.5 |
Silicone 40Aレジンで内製した場合 | 部品25点で6時間 | 部品単価$1~2 |
HGM Automotiveは、コネクタシール100点の生産でコストを98%、生産期間を90%削減することができました。
もともと同社はFormlabsの柔軟性・軟質材料であるElastic 50Aレジンを使用してコネクタシールを生産していましたが、その材料でも柔軟性が足りなかったのです。コネクタは手作業で組み立てるため、シリコンの代わりにウレタンなどの硬い材料を使った場合、「純粋に材料との相性が悪いために」組み立てにはおそらく2~3倍の時間がかかるだろうとCardwell氏は付け加えます。
もう一つの選択肢は、これまでにも他の部品の生産に使用したことのある従来のシリコン鋳造です。しかし、このコネクタは9本のワイヤーがシールに接続されているという特殊な設計のため、形状が複雑です。穴や繊細な形状によって型からの取り外しも困難になることが予想され、全体として3Dプリンタの精細さが求められる設計でした。
「鋳造でもできないことはないのですが、[繊細な形状の場合は]本当に慎重に進めなければならず、非常に時間がかかります。なので、3Dプリンタでバッチ単位の量産ができるというのは、他の方法に比べて贅沢な選択肢でした」
Guy Cardwell氏 HGM Automotive Electronics 研究開発ディレクター
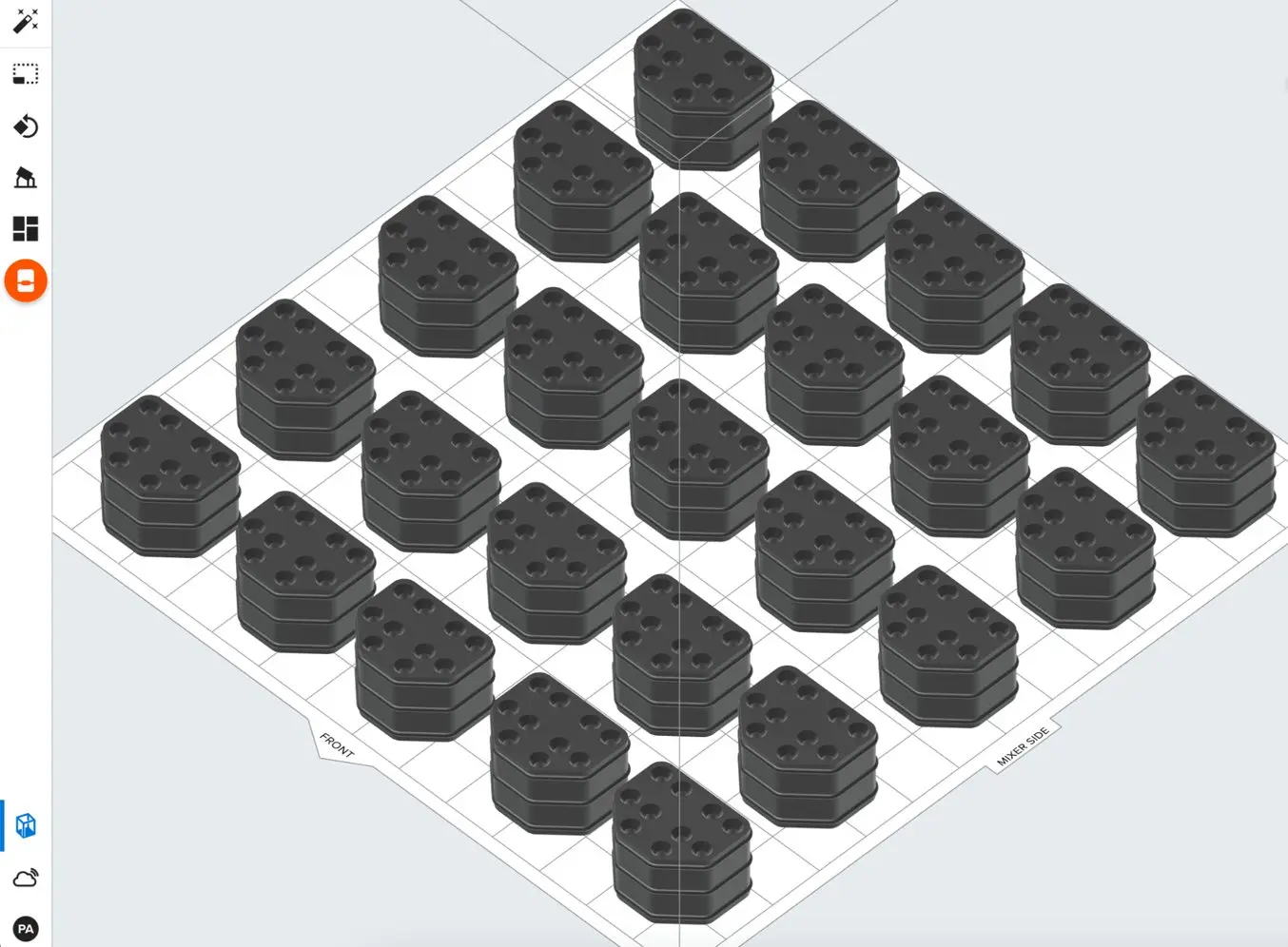
PreFormで造形準備中のHGM Automotive Electronics製コネクタシールのCADファイル。厚さ1センチほどしかないシールに9本のワイヤーが接続されている。細かなディテールが必要な緻密な形状のため、射出成形用の金型製作やシリコン鋳造では実現が難しい。Form 3+でコネクタ25点が4時間30分で造形完了した。
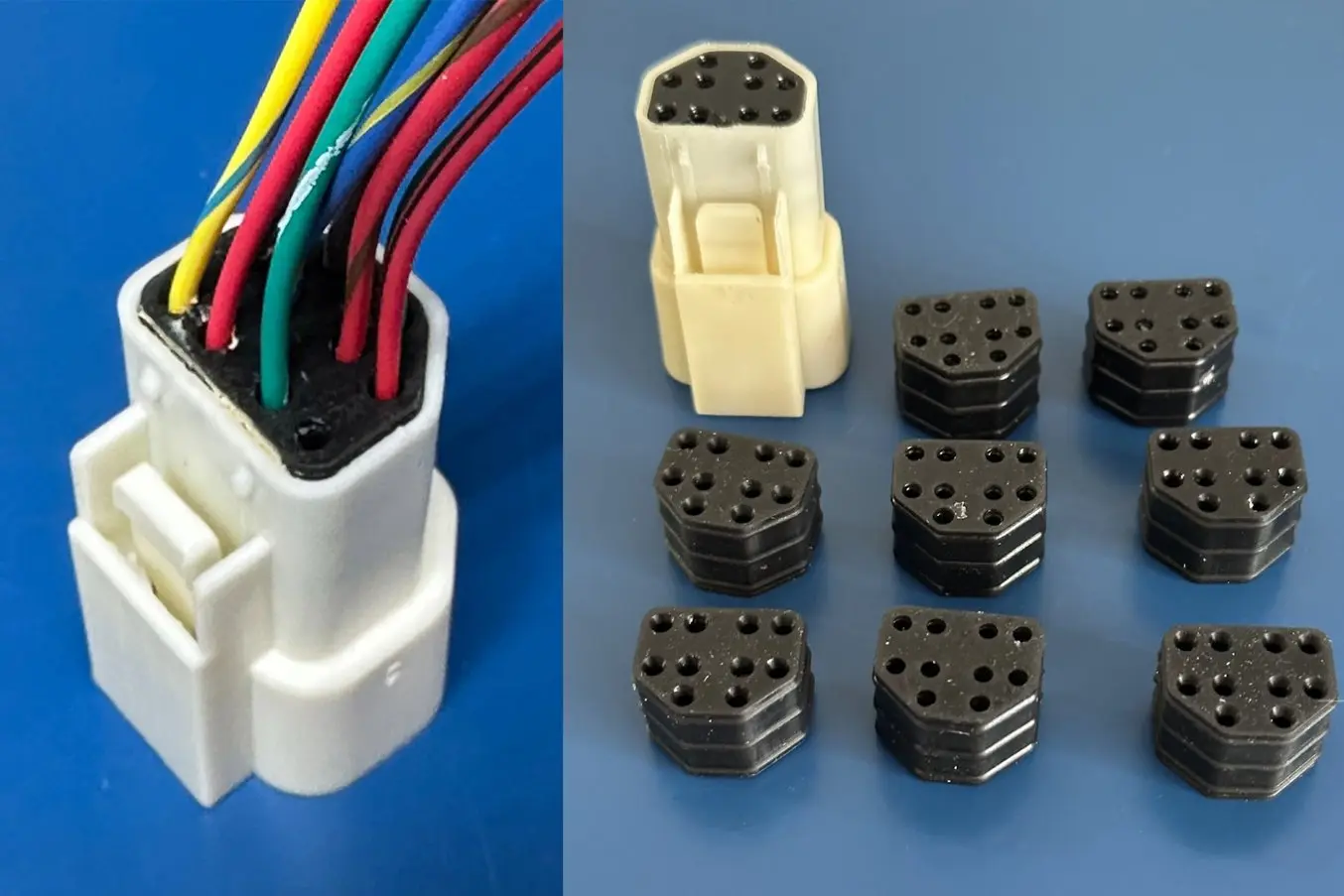
プリントされ、筐体と電子装置と一緒に組み立てられる コネクタシール
「実製品用の材料に非常に近く、ほぼ完璧でした」
Guy Cardwell氏 HGM Automotive Electronics 研究開発ディレクター
Silicone 40AレジンのおかげでHGM社は小ロット量産が必要な部品も内製し続けることができました。また、この材料は他にも様々な使い道があるという点も魅力です。Cardwell氏のチームはすでに、コネクタシール以外への使用も検討しています。新材料の主な利点は実製品の生産で使われる材料と非常に似ていることで、特に弾力性や引裂強さ、柔軟性という点でHGM Automotive Electronicsの用途に最適な特性を発揮することができました。
「Silicon 40Aレジンのおかげで、以前であれば非常に高額で時間のかかる成型法でしか実現できなかった形状も試せるようになり、設計面でも柔軟性が得られました。今後、新しい市場の開拓や、これまではコストや複雑さがネックで手の届かなかった部品の生産にも乗り出せそうです。他社の3Dプリンタでも柔軟な材料はプリントできますが、本物のシリコンやTPU部品と同等の品質や耐久性を実現できるのは、FormlabsのSLA光造形プリンタでSilicone 40Aレジンを使って造形した部品だけです」
Guy Cardwell氏 HGM Automotive Electronics 研究開発ディレクター
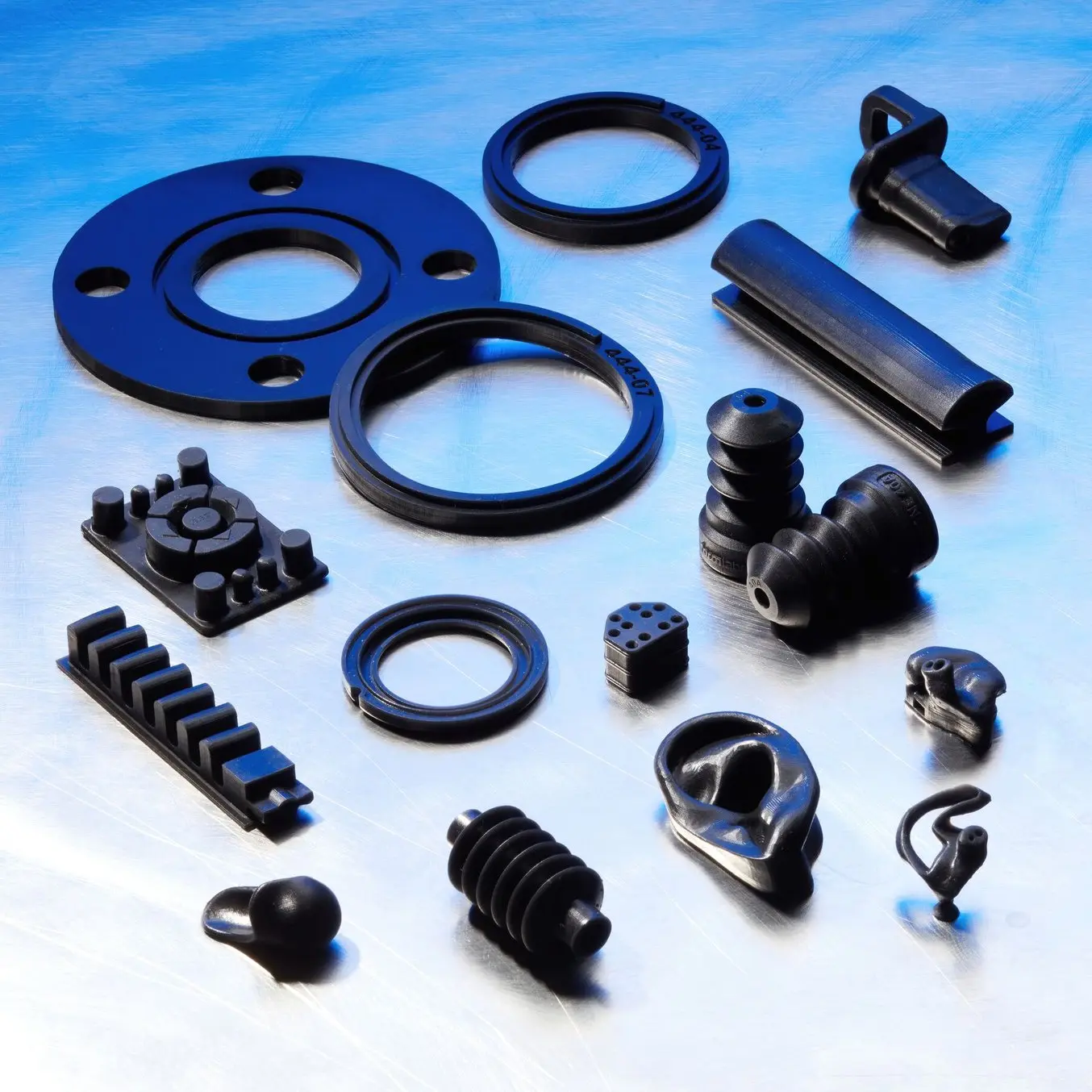
試練を乗り越えて勝利へ:Silicone 40Aレジンで耐熱性や耐薬品性などの業界要件をクリア
「Silicone 40Aレジンは、弾力性や扱いやすさといった、この用途で必要な特性をすべて持っています。これまでの社内試験では、耐薬品性の点では鋳造や射出成形で作ったシリコン部品に匹敵することがわかっています」
Guy Cardwell氏 HGM Automotive Electronics 研究開発ディレクター
自動車用部品の場合、用途によっては水深1メートルから2~3メートル程度でも耐えられる防水性のシールが必要とされることが一般的です。さらに、水、オイル、トランスミッション・フルードなど自動車に使われる標準的な流体に対する耐薬品性も求められます。Cardwell氏は、部品の試験のためにサンプルをいくつかプリントし、車のエンジンルームで機能試験を行いました。プリントしたシリコン部品のサンプルを車のエンジンルームに置いたまま、6週間に渡って通常の運転条件下で耐熱性と耐薬品性の試験を行いました。
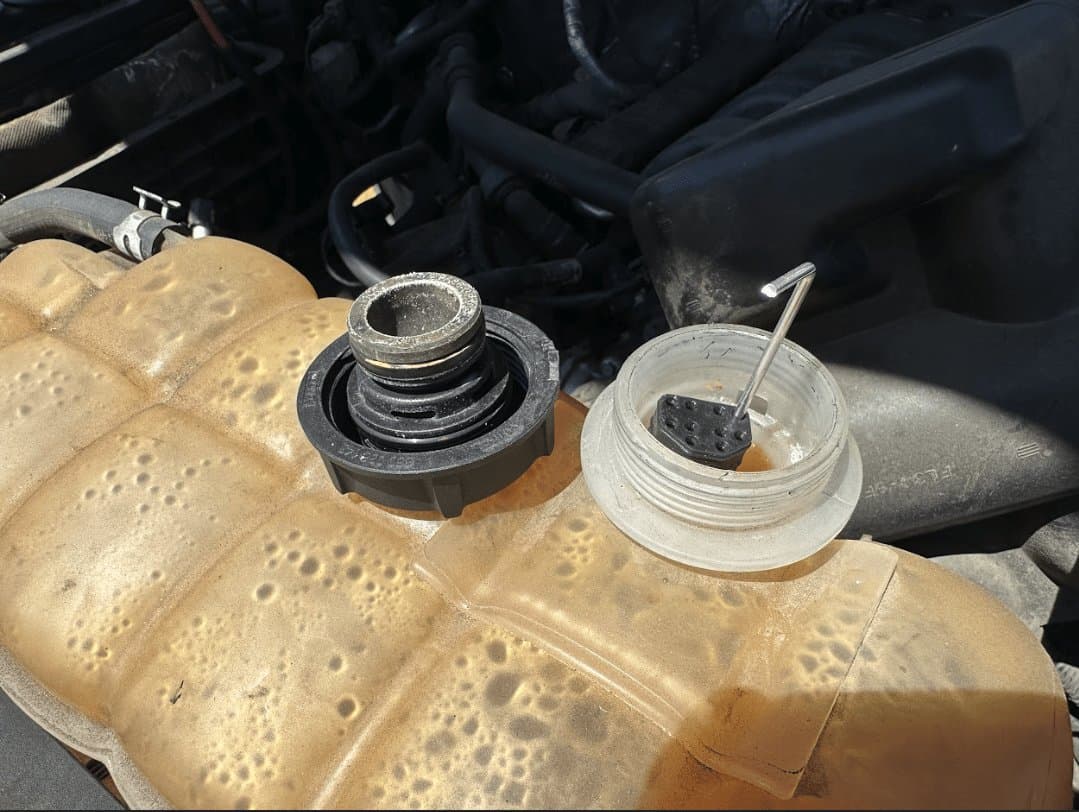
HGM Automotive Electronics社が、自動車エンジンの冷却水タンク内の、Silicone 40Aレジン製コネクタシールの実地試験を行なっている様子。
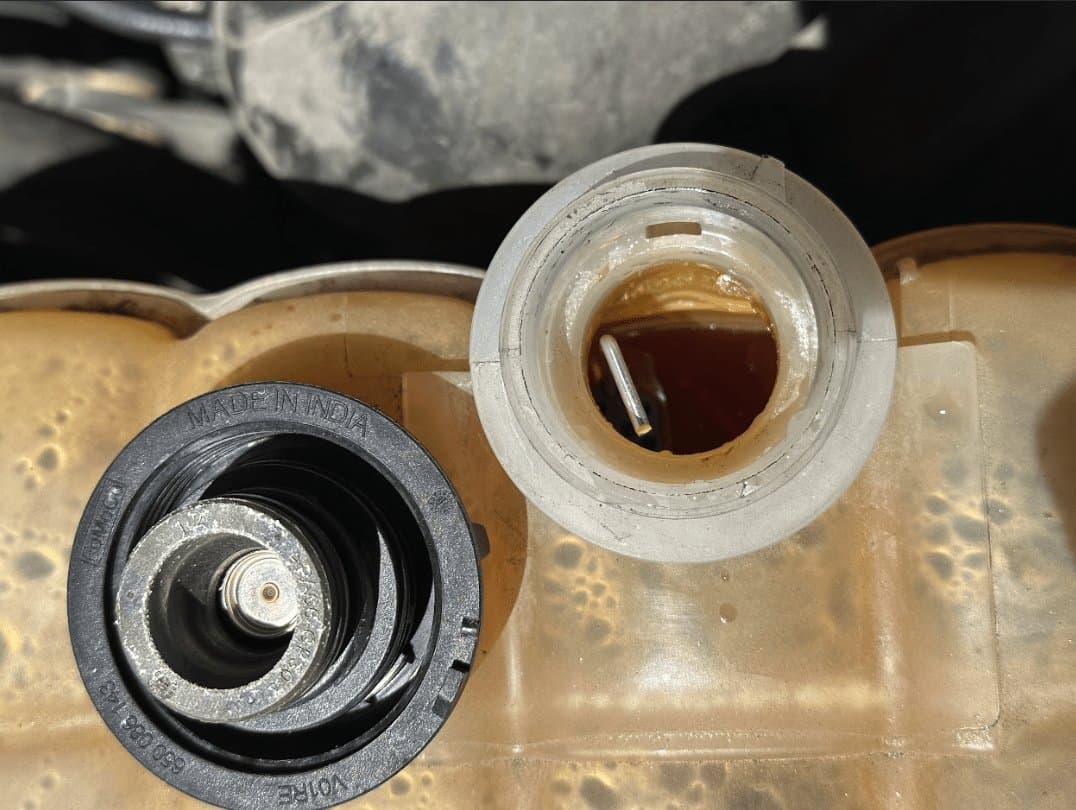
「エンジンルーム内のさまざまな流体に部品を浸して温度サイクル試験を行いました。水でも試験しましたし、トランスミッション・フルードでも静的試験をしました。不凍液も使いましたよ。このシールが通常侵入を防ぐものといえば、水です」とCardwell氏は付け加えます。熱サイクル試験とさまざまな流体で流体暴露の試験を6週間行なった結果、Cardwell氏はSilicone 40Aレジンの水密性と耐熱性を強調しました。自動車用電子部品の温度範囲は-40°C~105°Cです。Silicone 40Aレジンはガラス転移温度(Tg)が-107°Cで耐熱温度が-25°C~125°Cと、耐熱性の要件を完璧に満たしていました。「この材料が射出成形のシリコンと同等の特性を持っているのではないかと仮定して、試験を進めました」と言うCardwell氏の期待通りの結果となりました。Silicone 40Aレジンの材料特性は実製品に使用している材料と同等で、Carwell氏率いるチームの選択肢に加わるに相応しい材料でした。
広範な実地試験を経て、HGMチームは新製品であるシリコン100%のレジンに大変満足し、今後さまざまな用途に活用できるのではないかと期待しています。彼らは今、コネクタシールの実製品用部品の生産にも本材料の使用を検討しており、生産量は年間500~1,000個を見込んでいます。Cardwell氏はさらに、このレジンの用途を広げていくことも検討中で、「コネクタだけでも、候補になる製品が少なくとも4つはあります」と期待に胸を膨らませます。
HGM Electronicsのイノベーションを後押し
Silicone 40Aレジンにより、HGM Automotive社はこれまで高価で時間のかかる工程でのみ可能であった設計の開発が柔軟に行えるようになり、新たな市場の開拓を実現しています。
「[サンプル品を]社内で配ったところ、みんなが唖然として『一体どうやって作ったの?』と言っていました。材料として、すごく魅力的です。今後どのような用途に使えるかは、実際に使ってみないとわかりません。実際に使ってみないと本当の性質はわかりません。でも、コネクタの生産だけには留まらないだろうと思っています。この材料で実現できることがたくさんあるのは、まず間違いないですよ。」
Guy Cardwell氏 HGM Automotive Electronics 研究開発ディレクター
Cardwell氏は今後、「軟質ゴムの特注品にも対応できます」と顧客に伝えられることを楽しみにしています。彼は今、多種多様なカスタムシール、ガスケット、そして下の写真のような新しい高電圧シリコン絶縁体ブーツの開発を検討しています。

Silicone 40Aレジンを使って3Dプリントしたスパークプラグブーツ
「3Dプリント製のシリコン部品をどう活用するかと聞かれたら、今すぐには答えられません。でも、今後それを見出していくのがとても楽しみです」
Guy Cardwell氏 HGM Automotive Electronics 研究開発ディレクター