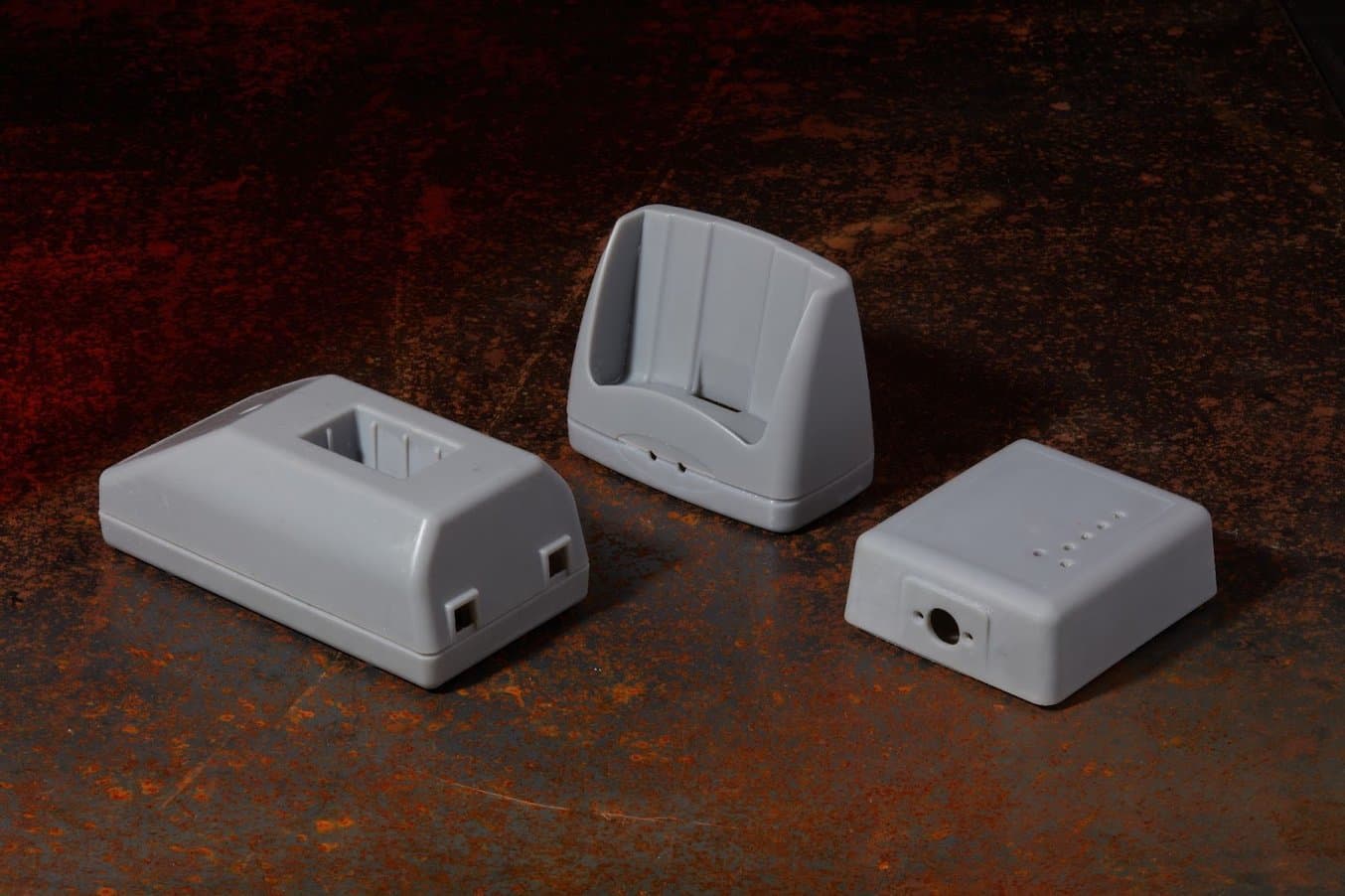
Avance Designは、20年以上にわたって3Dプリントを活用しており、今でも新たな3Dプリント材料が開発されるたびに、新たな用途を見出し続けています。
Avanceは、鋳造、成形、機械加工、FDMによる3Dプリントに加え、3台のForm 3+と2台のForm 3LのSLA光造形3Dプリンタを活用し、医療、ロボット、建築、電子機器向けの製品開発を行っています。Formlabsの新材料、Flame Retardantレジンを使い始めてから、Avanceは開発サイクルの短期化、そしてUL 94認証取得済材料による部品製造コストと労力の削減に成功しています。
Avance Design代表、Tony Parker氏に、Flame Retardantレジンで小ロットでの量産やマスカスタマイゼーションなど、実製品の量産に成功した事例についてお話を伺いました。
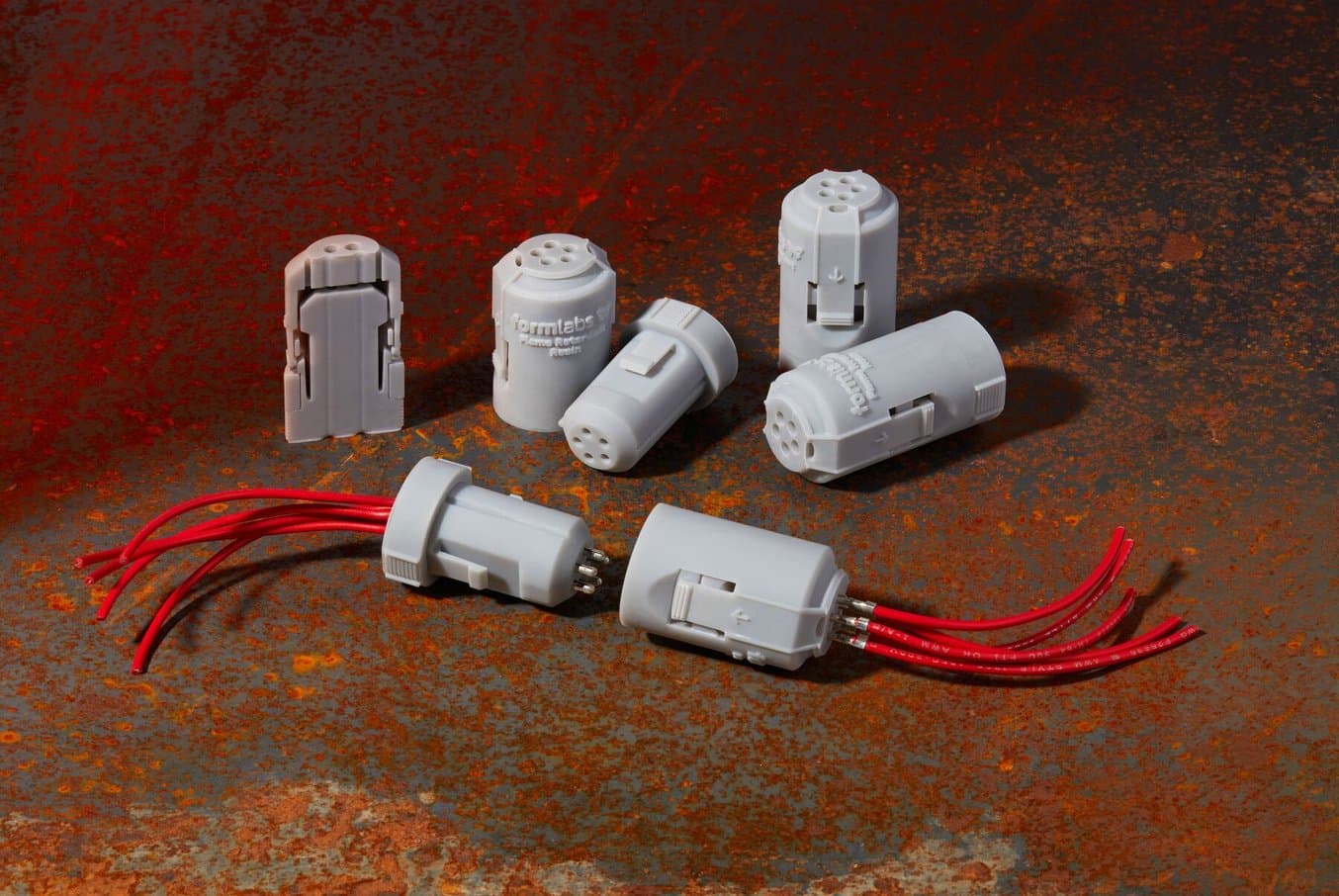
Advance DesignがFlame Retardantレジンで切り拓いた新たな3Dプリントの活用法
Frame Retardantレジンを使って、高温もしくは発火源のある屋内や産業環境で長期的に使用できる、難燃性、耐熱性、耐クリープ性に優れた硬いパーツを簡単に3Dプリントする方法をご紹介します。
3Dプリントによる量産で製造期間を1/3に
Avance Designの顧客の1つであるEnergy Accessは、医療、防衛、重機製造、セキュリティ、ロボット産業で使われている電子機器のバッテリー充電器を特注生産しているメーカーです。特注で設計されたバッテリーは特殊な形状となっており、Energy Accessは専用充電器の設計をAvance Designに依頼しました。「バッテリーが安全に収納・設置できること、そして充電器本体と確実に接続できることが充電器を設計する上で求められた条件でした」とParker氏は語ります。
Avanceにとって、特殊な形状をした機器に合う製品を設計・開発することは難しいことではありません。課題となったのは、3Dプリント製カスタムパーツの材料特性を、実製品で採用される成形での量産品と同等にすることでした。
Energy Accessは、潜在的な環境ハザードを防ぐため、社内標準として採用部品はすべてUL 94認証取得済品と規定しています。そのため、Avanceは既存のEnergy Access製品と併用できる部品を作る必要がありました。「材料特性が同等であれば、こちらで製造した部品をそのまま最終製品に組み付けることができ、最終の組立段階を効率化できます。そのために同等の材料特性を求めているんです。」とParker氏は言います。
ここで求められる強度、表面品質、UL-94の難燃性認証という材料特性を実現するには、従来であればポリウレタン鋳造が必要でした。その場合、3Dプリントや切削で金型を製作し、その周りにシリコン型を作り、市販のUL規格取得済のポリウレタンをシリコン型に流し込み、その後ポリウレタン部品を取り出して後処理を行う必要がありました。「部品1点を作るのに何日もかかり、注文数が20点となると3週間ほどかかります」とParker氏は言います。
FormlabsのFlame Retardantレジンの活用により、Parker氏は工程を簡素化でき、CADでの設計から量産までの高速化を実現することができました。「部品をFlame Retardantレジンで直接3Dプリントすることで、部品20点の製造を1週間程度まで短縮することができました」Parker氏は言います。
難燃性材料での筐体製造方法の比較
手順 | 20点の製造に要する時間 | 造形単価 | |
---|---|---|---|
光造形、Flame Retardantレジン使用 | プリント、洗浄、二次硬化、サポート材除去、塗装 | 4〜5日 | $19.80(材料費:$6.50、人件費:$13.30*) |
FDM、フィラメント使用 | プリント、サポート材の溶解、洗浄、やすりがけ、めっき処理、下塗り、塗装 | 5〜6日 | $42(材料費:$7、人件費:$35*) |
鋳造、ポリウレタン使用 | プリント、洗浄、二次硬化、サポート材除去、シリコン成形、ポリウレタンで鋳造、洗浄、塗装 | 21日 | $85(材料費・成形・ウレタン:$25、人件費:$60*) |
従来の射出成形 | 機械加工や成形を外注 | 20〜30日 | $250(金型製作:$5,000、その後の部品単価:$0.50) |
*Labor costs are calculated at $80/hour.
表面品質と加工性
作業手順の短縮によりParker氏の開発プロセスは大幅に変わりましたが、他にもいくつかの考慮点がありました。結局数年にわたって、FDM方式3Dプリント用のUL認証取得済材料でプリントしています。また、FDMプリンタでの造形品に見られる積層痕のない、優れた表面品質も求められます。「Flame Retardantレジンの表面品質には本当に驚きました。非常に滑らかな外観のパーツは、サンドペーパーをかけると下塗り処理を施したかのように見えます。おかげで表面仕上げや塗装の下準備が楽になり、非常に助かっています」とParker氏は言います。
Avanceチームは、製品全体を組み立てた後も造形品がきちんと機能することを確認する必要がありました。ねじのインサートです。「圧入式のインサートの場合は締結力が強いのですが、特殊なことはせず、穴サイズの推奨事項に従って小さなプレスで圧入してみたところ、造形品は無傷で持ち堪えました。何の問題もなく、インサートを押し込むことができたんです」Parker氏は言います。
この馴染みやすさが、組み立てプロセスを全面的に変えることになります。Parker氏は、Formlabs製プリンタで造形したパーツがUL認証試験をクリアし、充電器の他の部品と同様の滑らかさと強度、そしてねじ部品との一貫した締結が実現すると信じています。Flame Retardantレジンを用いた3Dプリント製パーツは、Parker氏の顧客の組み立て方式にも問題なく使用することができます。「Energy Accessの皆さんも非常に喜んでいました。難燃性材料を使ったFDMや鋳造では満足のいく仕上がりにならなかったからです。設計から生産プロセスに至るまで、同じ材料を使って開発・変更ができることをとてもに気に入ってくださいました」Parker氏は言います。
熱可塑性樹脂を極めて近い物性を持ち、高い表面品質がありながら細部の高精細な表現も可能で、成形品同様の機械的特性をもつ部品が3Dプリントで作れるということは、非常に大きなメリットであり、時間短縮にもつながります。Flame Retardantレジンを使えば、他の方法を採る場合に必要だった多くの作業を省いて、CAD上での設計からそのまま量産品をプリントすることができます。
Tony Parker氏、Avance Design代表
複数の材料を活用した生産
Avance Designでは、UL認証取得済材料以外にも様々なプロジェクトが進行中です。どのプロジェクトも、顧客にとっての最重要機能は何かを協議・分析するところから始まります。Parker氏は、ここでFormlabsのレジンを採用することが多いと言います。「レジンカートリッジを20〜30本程度は常備しています」とは彼の言葉です。最近のプロジェクトでは、医療用の研修シミュレーション端末向けに柔軟性のある材料が必要でした。そこで、Parker氏はFlexible 80Aレジン を使ったパーツを設計しました。これが成功を収め、AvanceはForm 3+を使って1000点以上のパーツをプリントし、少量生産の事例も確立しました。
建築業界も可能性のある分野です。周りの装飾や雰囲気に合ったドア部品など、小ロットの量産が必要になるのです。顧客は、建物の装飾やスタイルに合った電子筐体のカスタムデザインをAvanceに依頼します。成形や機械加工にかかるコストを避けつつ、最終用途で求められる強度と形状を実現するため、Parker氏はForm 3+とForm 3を活用して少量生産を行うようになりました。
新しい可能性を開拓
新たな材料を手にしたParker氏は、Flame Retardantレジンの新たな可能性に胸を躍らせます。「まだ鋳造やFDMプリント技術が当たり前だと思っている人もいますが、このレジンの可能性を知れば、新しい可能性を見出せます。低コストで迅速に部品が作れるのですから」Parker氏は言います。
Avanceの顧客の中には、鋳造工程が複雑なために、医療、エンジニアリング、ロボット産業用途で3Dプリントを使いたがらない人がいるとParker氏は考えます。「お客様の中には、鋳造工程を検討されたものの、労力を考えると費用対効果が見合わないと判断した方もいるでしょう。直接3Dプリントできるようになった今、特定の要件が存在する業界でも活用できる可能性があり、今後の展開に期待しています。」とParker氏は言います。
Flame Retardantレジンの詳細や用途については、製品ページをご覧いただくか、Formlabsまでお問い合わせください。