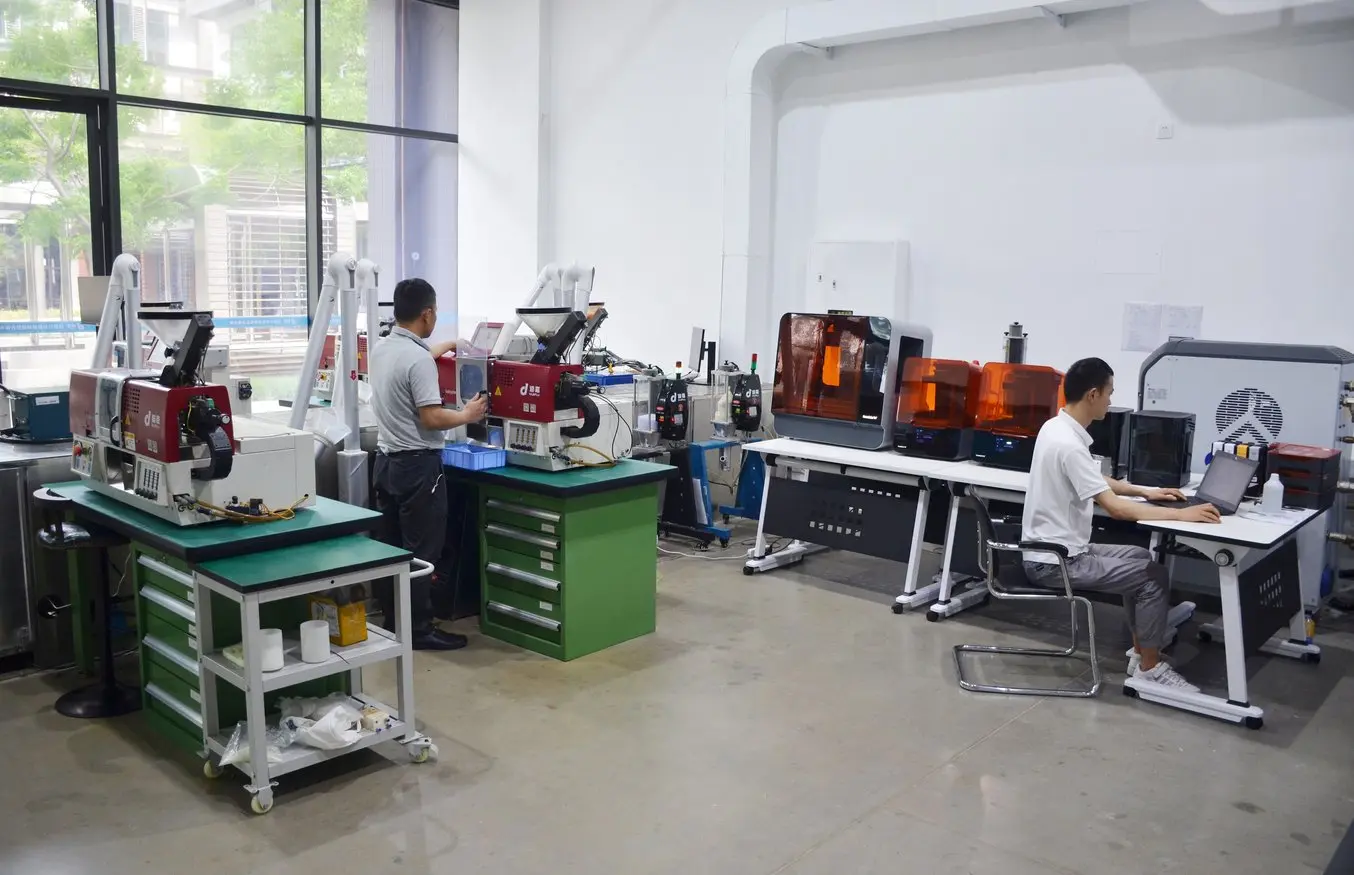
2001 年に世界貿易機関 (WTO) に加盟後数年で、中国は急速に生産量で世界最大の製造大国となりました。この製造能力の多くは、深圳を含む広東省南部の9つの都市グループから成る珠江デルタ地域に集まっています。2020年には、この地域は中国の貿易額の約3分の1を占めていました。
この急速な成長に後押しされて、多くの小さな町工場が国際企業へと成長を遂げています。2005 年に深圳に設立されたMultiplusは、マイクロ射出成形工場としてスタートし、大小プラスチック製品、シングルショットまたはマルチショット(2つ以上の色または材料が、1つの金型で同時に射出成形される)の設計から製造まで、生産過程全体を網羅するソリューションの提供会社に急速に成長しました。現在Multiplus社は、フォーチュン500企業を数社含む年間250社を超える顧客にサービスを提供しています。
その中には、硬質な金型製造の複雑性により、射出成形を行うと従来高コストで多くの時間を要する小ロット生産をリクエストしてくる顧客もあります。
本記事では、3Dプリント製の射出成形用金型を用いて100点ほどの小ロット射出成形の準備期間を4週間からわずか3日間まで短縮したMultiplusの事例を解説します。
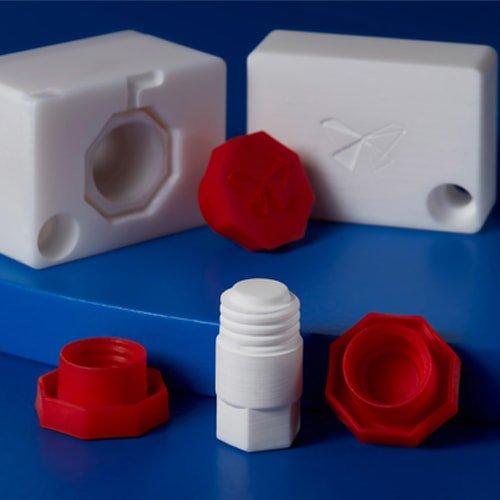
3Dプリント製金型による射出成形で小ロット量産
本技術資料は、光造形3Dプリント製の金型による射出成形でのコストと金型製作コストの削減方法やそのガイドラインを、海外の活用事例を交えながら解説いたします。
高まり続ける小ロット量産のニーズ
動画:小ロット量産に3Dプリント製金型を活用するMultiplusの事例
射出成形に用いる金型は、多くの場合スチールやアルミ等の金属で作られます。しかし小ロット量産では高額で時間もかかる金型を使うと、採算性に関わる非常に大きなコストとなってしまいます。
「現在は業務の大半を占めるほどではありませんが、小ロット品のニーズが確実に高まってきています。デザイン確認や機能確認用の試作品もありますが、実製品用途のものが特に増えています。多くの企業が市場に本格投入する前にベータ品でテストを行いたいと考えるため、これは理に適っていると思います。」と MultiplusのCEO、Kevin Li氏は述べています。
Multiplusは10年以上前に3Dプリントを導入し、以来3Dプリンタの追加導入を重ねてきました。目的は主にプレゼン用のモデル製作やデザイン確認用の部品を様々な材料でプリントし、テストするためです。小ロット量産の需要が高まるにつれ、Multiplusは3Dプリントに注力し、さまざまな材料を調査して安価に樹脂型を製作できる費用対効果の高い方法を模索していました。Formlabsの3Dプリンタで射出成形用の樹脂型を製作した場合、アルミ製の金型を切削で作った場合と比べ、コスト・労力・時間のすべてが削減でき、Babyplast製の工業用射出成形機に設置して問題なく使用できました。
Multiplusがテストした材料の1つがFormlabsのRigid 10Kレジンです。このレジンは非常に高強度高剛性の材料で、射出成形用金型に必要な耐熱性や耐薬品性も備えたガラス分高配合材料です。Rigid 10Kレジンを光造形3DプリンタForm 3でプリントした3Dプリント品は、滑らかでマットな白色で、射出成形品の表面も美しく仕上がります。
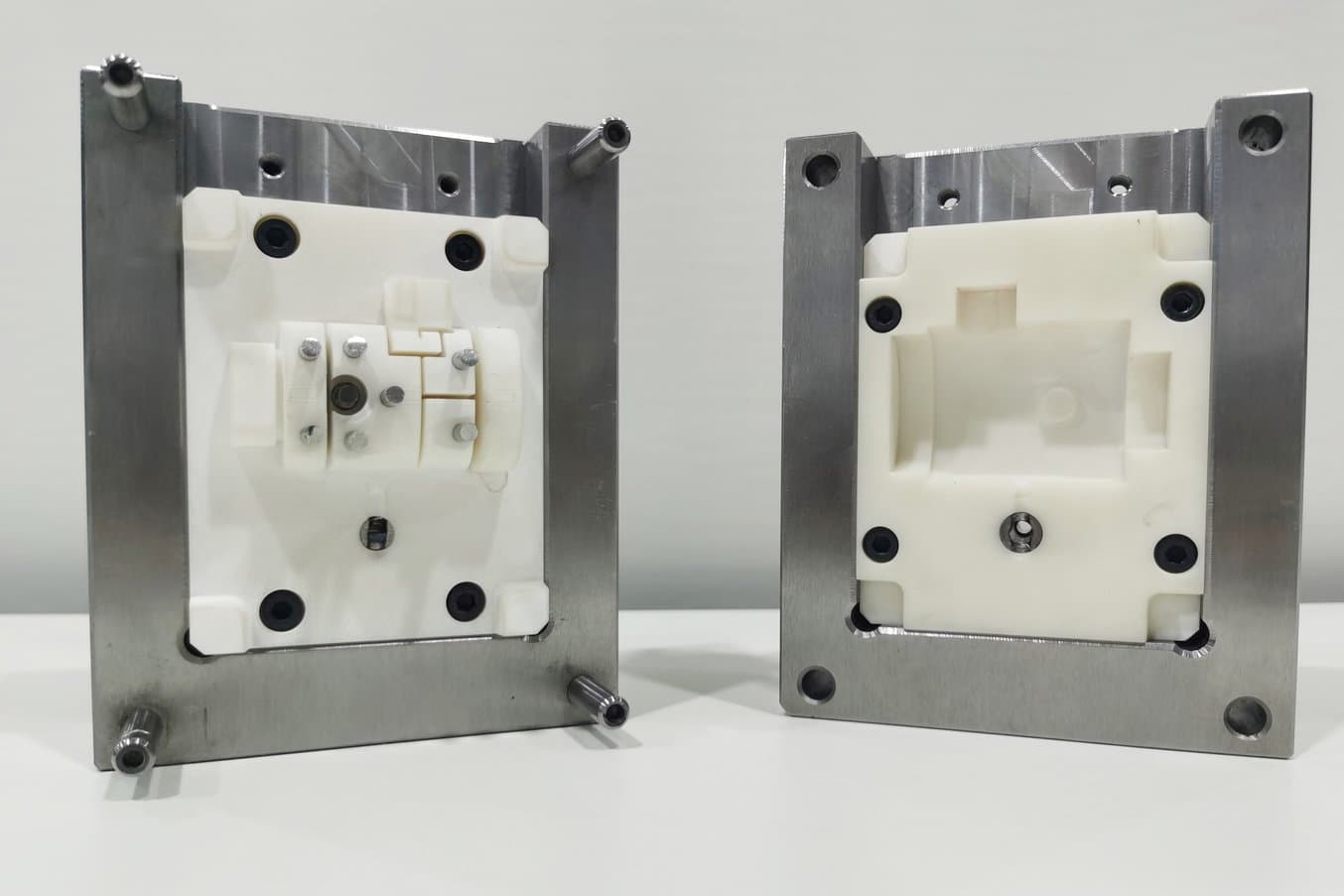
金型枠に組み付けたRigid 10Kレジン製の入れ子。
「成形中に繰り返し加わる圧や熱、その後の冷却にも耐えられる3Dプリント材料は多くありません。我々の経験では、高耐熱材料を使った場合も3Dプリント製の樹脂型は10~20回ほどの射出に耐えられたとしても、その後すぐに割れが発生したり、劣化して成形品の品質が低下してしまっていました。ところがRigid 10Kレジンで製の樹脂型で成形を行った最初のロットでは100点の部品が何の問題なく成形できました」と、Multiplusの射出成形部門マネージャー、Lin Wei氏は述べています。
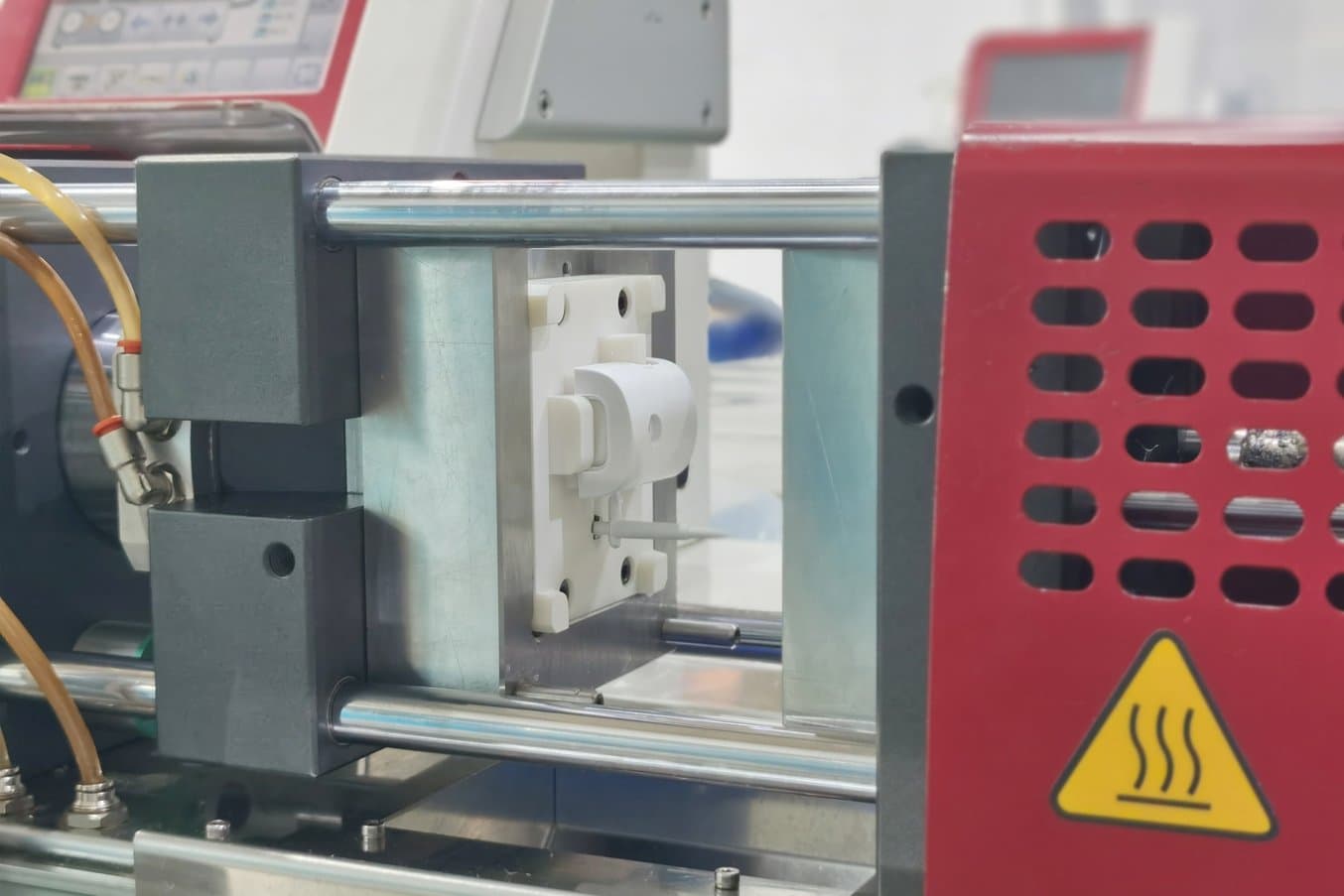
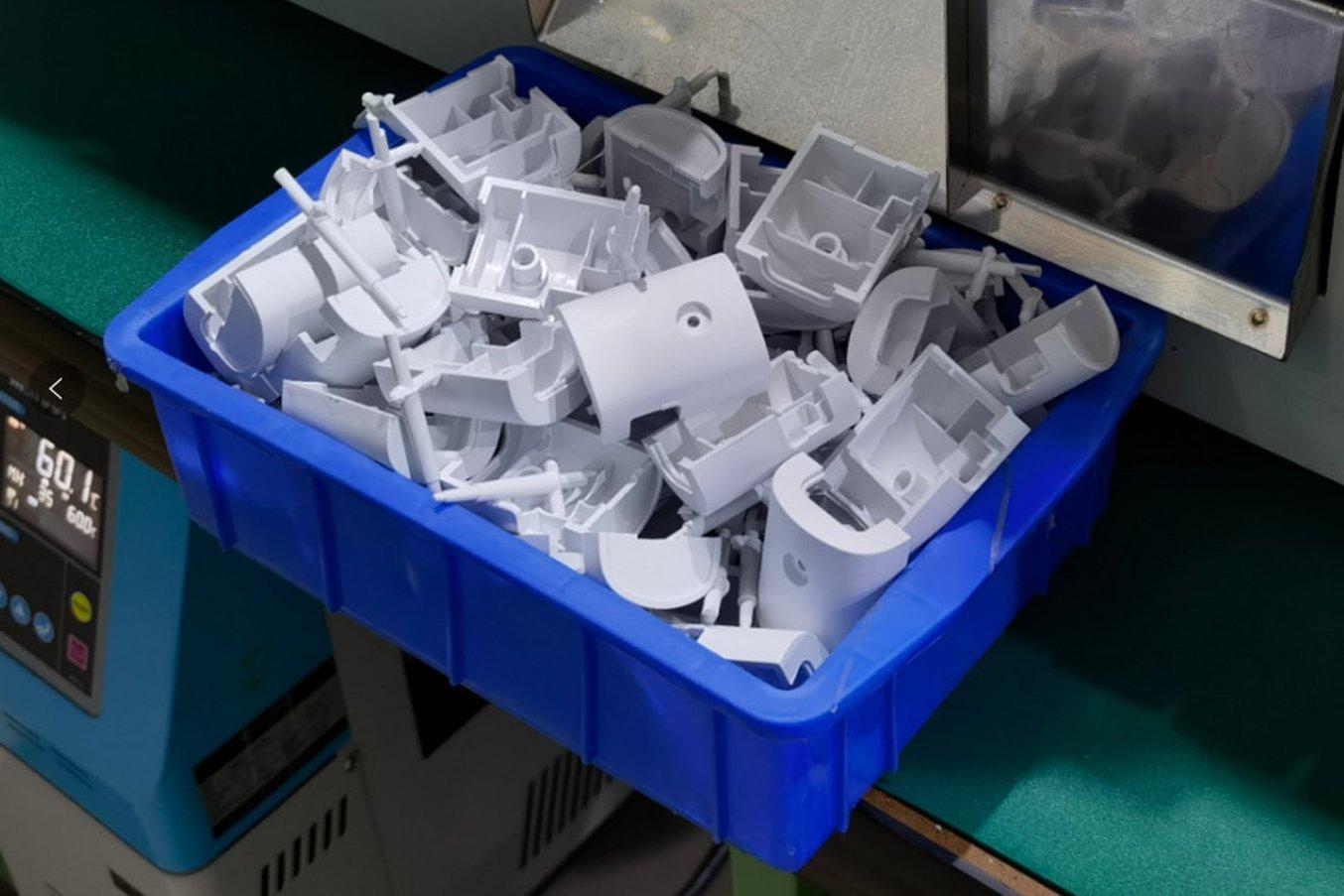
Rigid 10Kレジン製の樹脂型で成形したABS製の電子機器用筺体。
金型製作期間が4週間から1週間に
Multiplusは、ABS、PP、PC+ABS、およびPCで射出成形のテストを行いました。金型を設計した後、1日で金型のプリントと後処理が完了し、30分ほどで3Dプリント製の入れ子を金型枠に組み付け、射出成形機で成形を開始しました。成形開始から成形品の完成までには約3分ほどを要します。Multiplusでは、各3Dプリント製樹脂型の射出回数を100回に留め、それ以上の生産点数がある場合は予め樹脂型を複数点プリントしておき、入れ子を交換して成形を続けます。
複数台の3Dプリンタと射出成形機の活用により、Multiplusは数百点の部品を最短3日で納品できるようになりました。これはCNCで金型を製作して成形する場合に必要となる3~4週間という期間と比べると大幅な短縮となります。
部品100点の射出成形 | 3Dプリント製樹脂型 | 切削での金型製作 |
---|---|---|
製作期間 | 3~5日 | 3~4週間 |
「Form 3の導入で金型製作が大きく高速化されました。特にRigid 10Kレジンは私がこれまで射出成形に使用した中で最高の材料です。今ではクライアントの要望以上に早く製品を納めることもできています」
Kevin Li氏
成形条件別の結果を比較
MultiplusはFormlabsのRigid 10K製の樹脂型を、様々な圧、温度、材料でBabyplast 10/12 Standardという射出成形機を用いて成形しました。成形品は様々な機能を持つ家電製品用のコントロール基盤の筺体です。
このテストで分かったことは、PPを180℃で射出した場合が最も成形しやすいということでした。Multiplusはこの方法で高品質かつ非常に良好な表面を備えた射出成形品の量産に成功しました。この樹脂型は100回の射出を行った後も状態は依然良好で、同様にABSを220°Cで60回射出した場合にも樹脂型に劣化は見られませんでした。Multiplusではスケジュールの都合で樹脂型が破損するまでの試験は行えませんでしたが、PP、ABS、PC-ABS成形用の樹脂型1つあたり100回以上の使用に耐える想定でRigid 10K製の樹脂型を使用できるという結論に至っています。
260°CでPCを成形した試験では、わずか4回の射出で樹脂型が破損しました。これは高粘度かつ融点が250°Cを超えるプラスチックでは、特に試験で使用したような薄肉形状の場合、Rigid 10Kレジンの3Dプリント製樹脂型では対応が難しいことを示しています。一方でHigh Tempレジンは高い荷重たわみ温度を備え、型締め圧力と射出圧力がそれほど高くない場合で樹脂型に使用することができる材料です。
成形材料 | PP | ABS | PC-ABS | PC |
---|---|---|---|---|
射出温度(ノズル地点) | 180℃ | 220℃ | 240℃ | 260℃ |
注入材料量 | 36 cc | 39 cc | 37 cc | 40 cc |
冷却時間 | 80秒 | 60秒 | 50秒 | 90秒 |
射出圧力 | 60 bar | 95 bar | 95 bar | 110 bar |
型締め圧力 | 35 bar | 30 bar | 25 bar | 80 bar |
型締め時間 | 0秒 | 1.5秒 | 1秒 | 2.5秒 |
耐用サイクル数 | 100回以上 | 60回以上 | 60回以上 | 4回 |
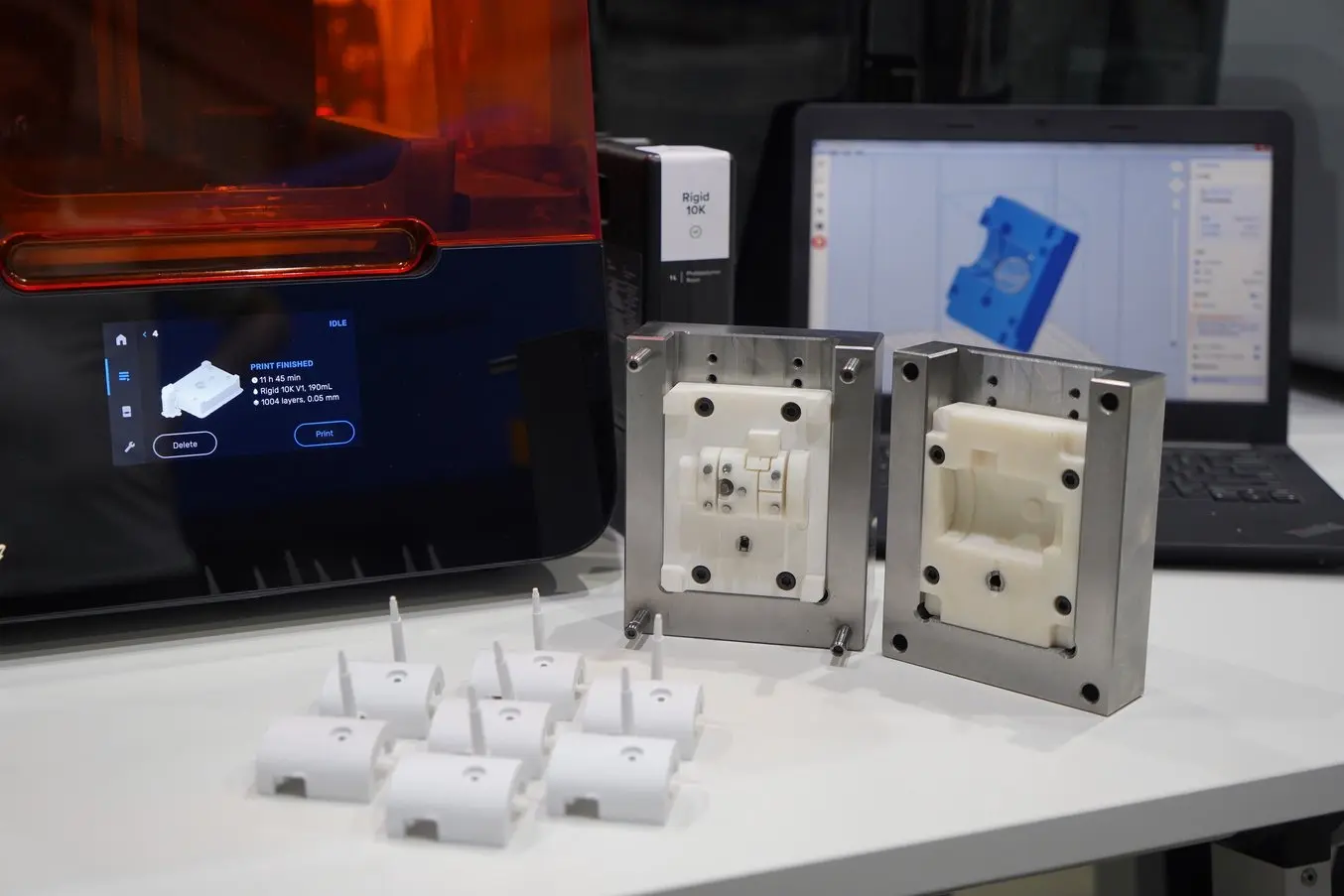
Form 3にてRigid 10Kレジンでプリントした樹脂型で100点以上の量産が可能。
3Dプリント製金型での小ロット量産
3Dプリントを従来工法の射出成形に導入したことで、Multiplusはそのビジネスを拡大し、より多くの受注を得て競争力を高めることができました。同時にコスト削減と納期短縮が実現し、クライアントがより高品質な製品を迅速に市場投入するサポートが行えるようになりました。
射出成形で3Dプリント製の樹脂型を使用する際の作業手順や樹脂型の設計ガイドライン、その他の詳細はこちらの技術資料、またはウェビナーをご覧ください。