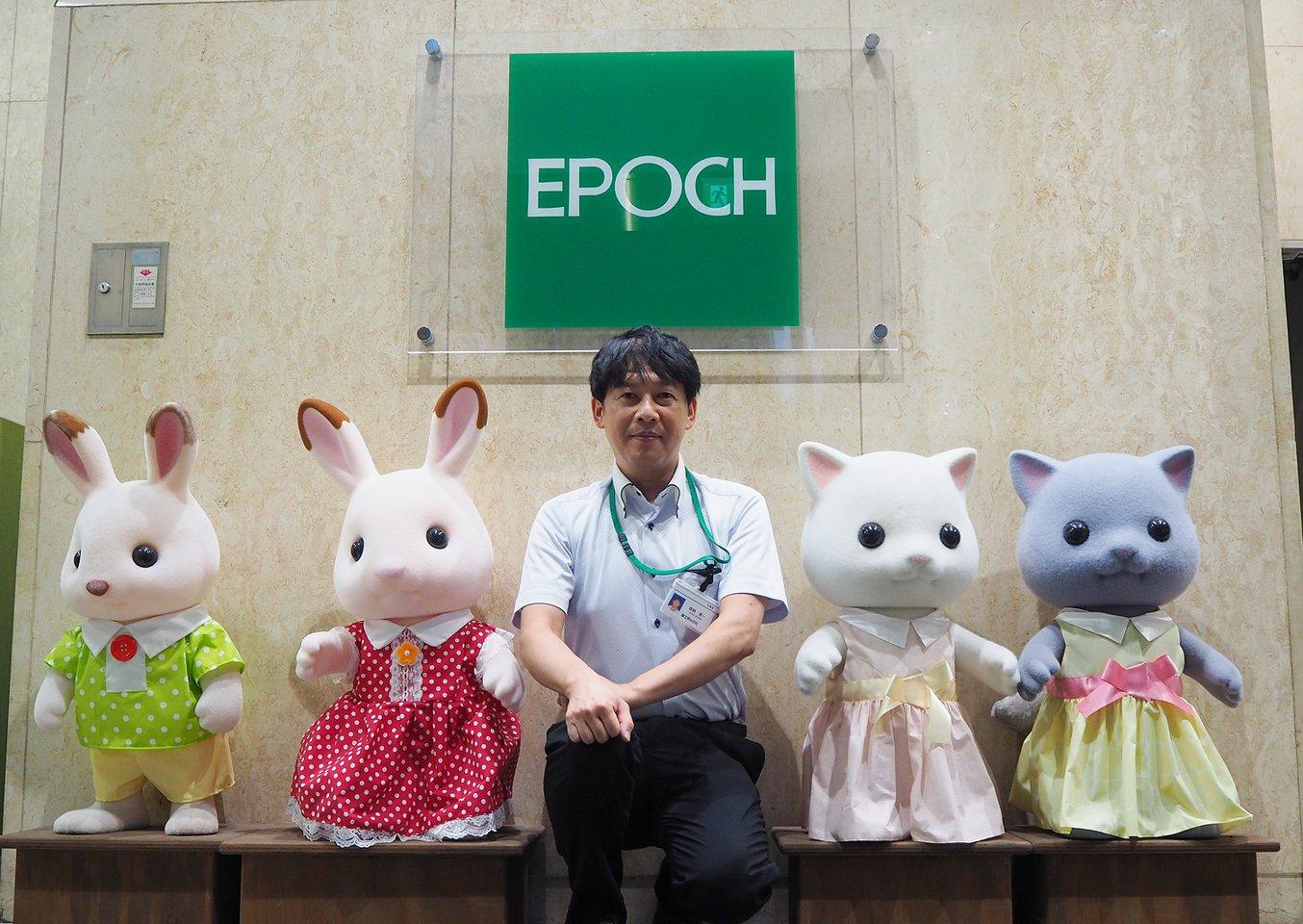
株式会社エポック社 シルバニア本部技術室 マネージャー 西野晃一氏と同社本社ビル入口を彩るシルバニアファミリー。
User Data:
- ユーザー:株式会社エポック社
- 採用製品:Form 3(SLA光造形方式)
- 使用材料:Flexible 80A、Durable、Tough 2000、High Tempレジン
- 用途:シルバニアファミリー関連製品を主としたデザインレビュー、社内確認用試作
画期的な技術は使いこなしてこそのもの
デジタルテクノロジーをはじめとした多くのエポックメイキングな新技術が当たり前のように続々と登場する今日、企業がそうした新技術を導入するのは決して簡単ではない。当然ながら、新たな技術は誰の目にも新しく、それがために理解を得ること自体が課題となることも珍しくない。また、技術はあくまで特定の目的を果たすためのツールであり、金銭的な投資によって導入できたとしても、それを企業として、あるいは部門として使いこなし、有用性が認められる形で運用するまでには導入後に時間的な投資も求められる。
株式会社エポック社 シルバニア本部の西野晃一氏は、同社の3Dプリンタ導入・活用に最大の貢献を果たした人物だ。同氏と3Dプリントの関係の始まりは、2006年まで遡る。当時、東京都大田区の東京都立産業技術研究センター城南支所では国内メーカーの光造形機とMaterialise社のSTL編集ソフトウェアMagicsのSGモジュールが利用でき、西野氏は当初からSGモジュールで自動生成されるサポート材を、プリント後のサポート材除去を考慮して最適化できないか研究していたという。その後も積極的に外部で3Dプリンタメーカーやユーザーと交流を行いながら光造形方式の研究を進め、2008年には手軽で後処理の労力も少ないインクジェット方式に出会い、2013年にはそのインクジェット方式の大型機を社内に導入。「スライサーソフト(造形準備ソフトウェア)のPreFormも使いやすく優秀で、Form 2の時代から注目していた」というFormlabsのSLA光造形方式3DプリンタForm 3も2021年5月に導入し、現在はインクジェット方式の大型機2台とForm 3の計3台を運用している。
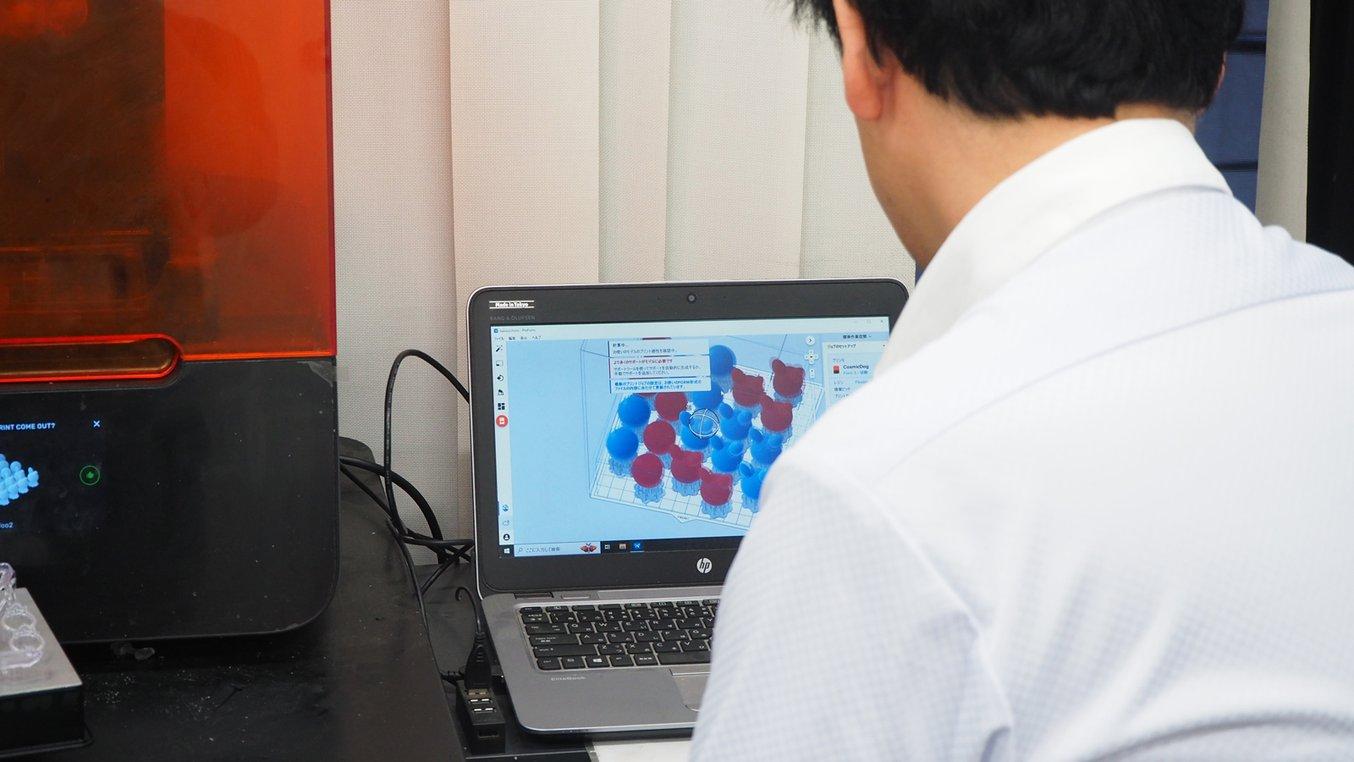
東京都江東区にある株式会社エポック社本社の造形室で作業を行う西野氏。
フルカラーのインクジェットプリンタとForm 3を使い分け
2006年より様々なプリンタに触れながら3Dプリンタによる造形の研究を重ねた西野氏が率いるエポック社本社の造形室では、現在2台のインクジェットプリンタでシルバニアファミリーの家や家具、人形等のフルカラーでプリントしたいもの、大型品、そしてイベントやシルバニアパークでの展示品を製作しているが、このハイエンド機ではカバーできないものをForm 3で賄っている。
「光造形の良いところは、中まで材料がしっかり詰まるところと、材料特性が優秀なところです。〇〇ライクと呼ばれますが、本当にそれに近い性質がしっかりあります。ゴムライクなんかは特に優秀で、インクジェットではこれほどのゴムのような質感は表現できません。」
西野 晃一氏 株式会社エポック社 シルバニア本部技術室 マネージャー
西野氏は、Form 3で遊園地のジオラマでシルバニアの人形が手に持つ風船や靴、リュックサックなどを硬質ゴムライクのFlexible 80Aレジンで製作する等で活用している。用途はインクジェットプリンタ同様に社内でのデザインレビューや試作品の製作だ。使い分けの背景について西野氏に伺ったところ、インクジェットプリンタでは積層する上での層間の剥離が発生することがあり、また靴のような中空部のある構造では中空部分にサポート材が入ってしまうため、微細なサイズの造形品には適さないのだという。
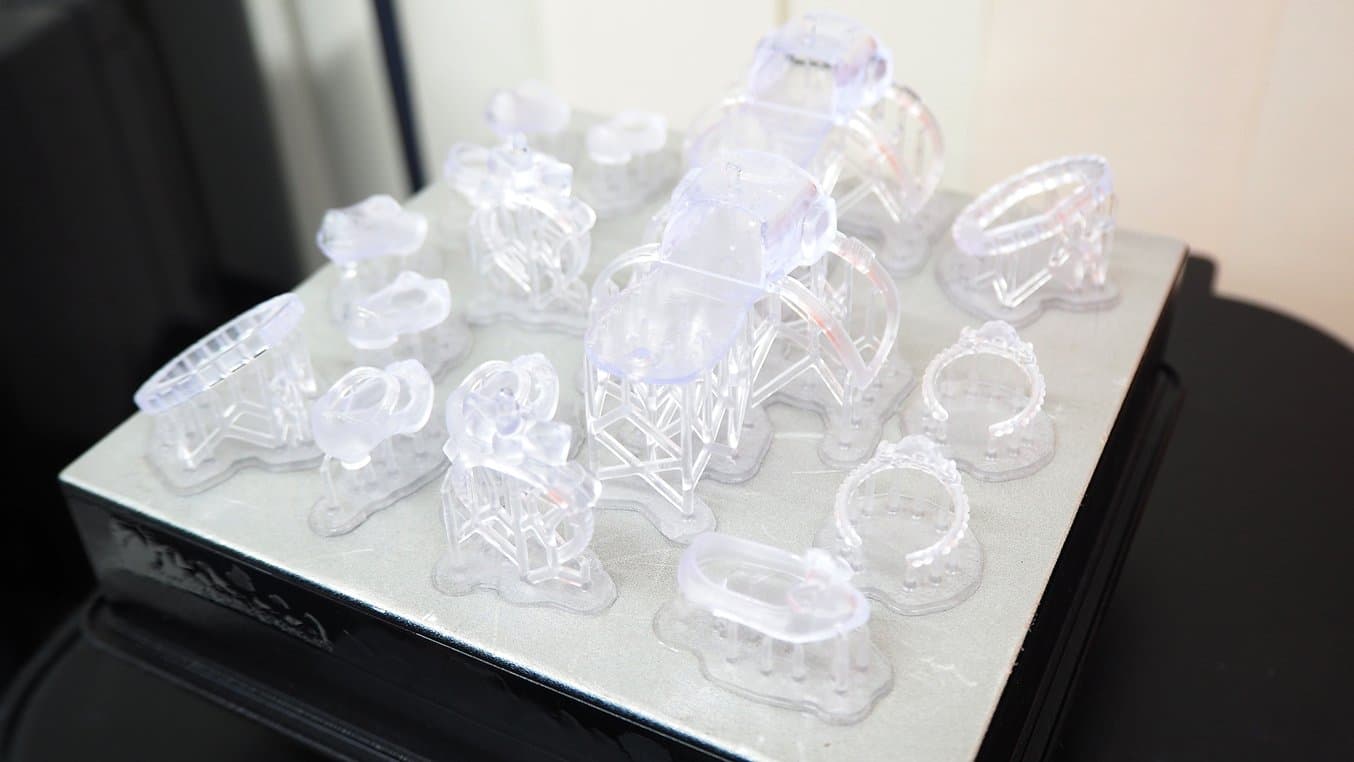
西野氏がFlexible 80Aレジンで製作したシルバニアファミリーのアクセサリー類。靴やリュックサックのほか、頭に付けるティアラなども見える。
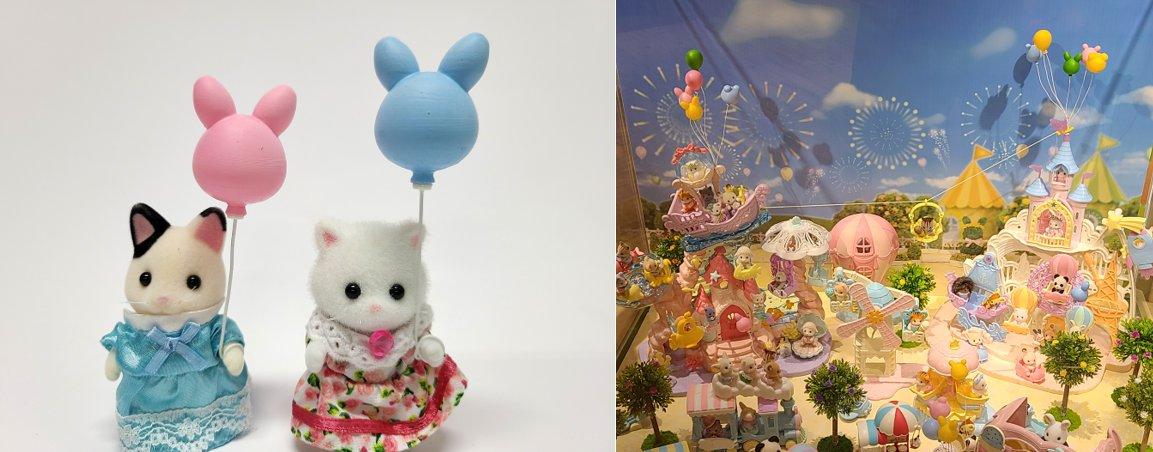
完成した風船を持つシルバニアファミリー(左)と遊園地のジオラマ(右)。一般的な丸い風船のほか、ウサギ、リス、クマの形の風船も。最もプリントが難しそうなウサギからプリントを始めたという。
これらの社内用途でのプリントの他にも、西野氏はシルバニアファミリーのテーマパークであるシルバニアパーク内で実際に使用される「あるもの」を、同氏ならではの工夫を凝らして製作している。それは、来園者の子ども向けの魚釣り用の魚で、同氏曰く「本物の魚を釣ってもらうわけにはいかないので、これも3Dプリンタで作ろうと考えました。吊り上げられて多少乱暴に扱われても壊れないようにと思い、最初はABSライクのTough 2000レジンを試しましたが、お子さまが釣り上げた後、岩にぶつけてしまったりすることもあるので、軟質のFlexible 80Aにしようかと思いましたがそれでは柔らか過ぎ、最終的にポリエチレンライクのDurableレジンにしました。光造形品は紫外線の問題がありますが、塗装しているとは言え何も問題なく泳いでくれています。」
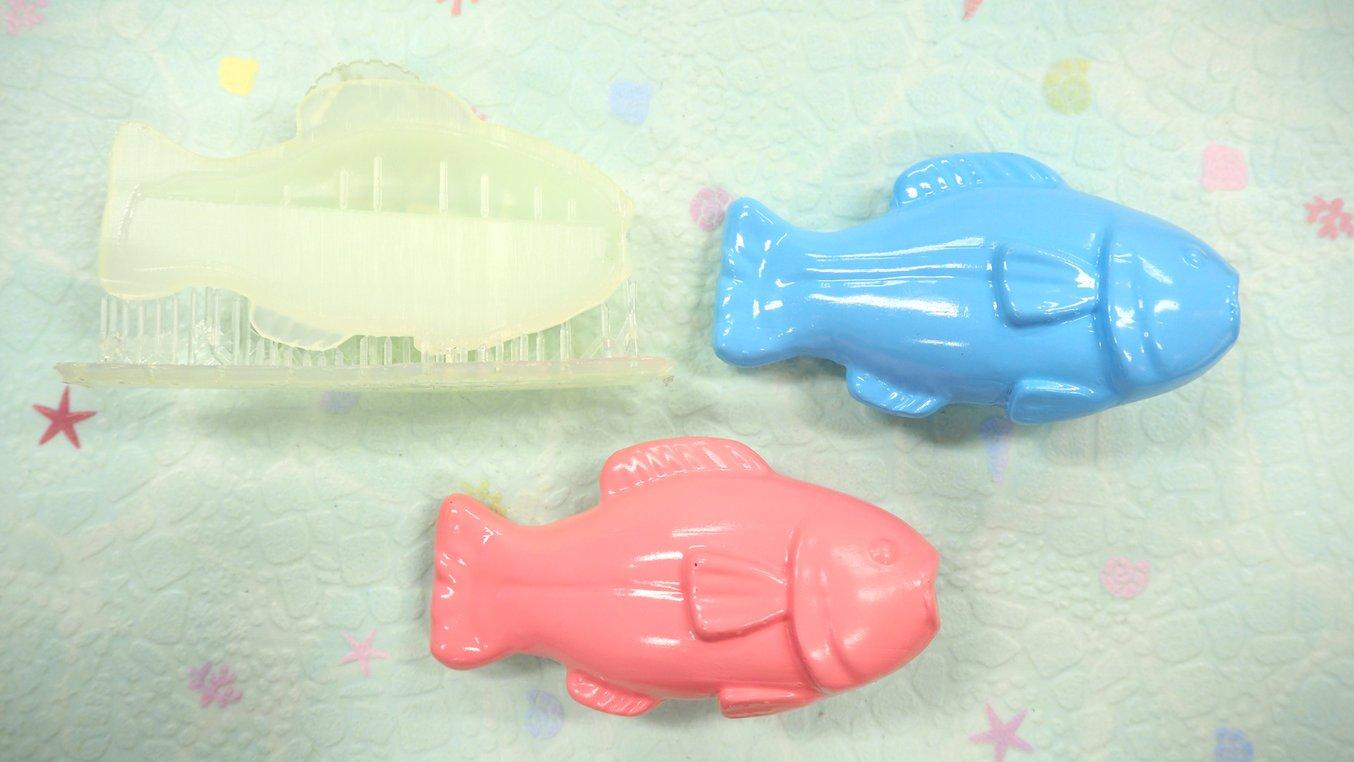
Durableレジンでプリントした魚(左上)と実際に使用されている魚。塗装が施され、魚釣りができるよう口元に磁石が仕込まれる。
事も無げに「泳いでいる」と言う西野氏だが、実際の人工池の水面に3Dプリント品の魚を浮かべるところを想像してみてほしい。水に沈んでしまっては釣ることができず、かと言って水に浮いても横に寝た状態で浮いていては死んだ魚のように映ってしまう。光造形の長所として中まで材料がしっかり詰まる点を挙げた西野氏だが、この利点を活用しながら魚本来のまっすぐに縦方向に立った状態で水面に魚を浮かべることができるよう、魚を二分割にし、内部空洞のサイズに微調整を繰り返すことで最適な比率に辿り着いたという。Tough 2000で試した後にDurableレジンに変更した際にもレジンの比重が異なるため、更なる調整を行ったという。
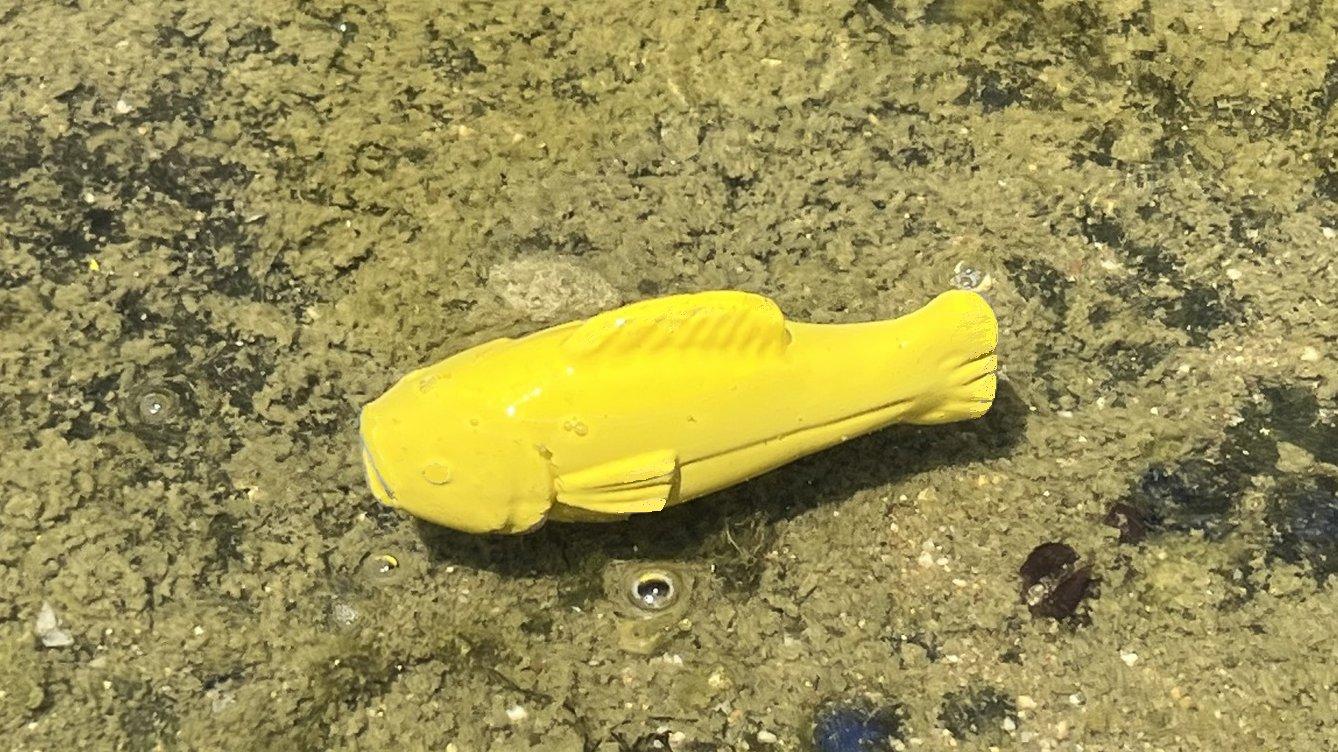
シルバニアファミリーのテーマパーク「シルバニアパーク」の人工池で泳ぐ西野氏製作の魚。材料選定から横に倒れて浮いたり沈むことのないよう設計上の工夫まで試行錯誤を重ねた。
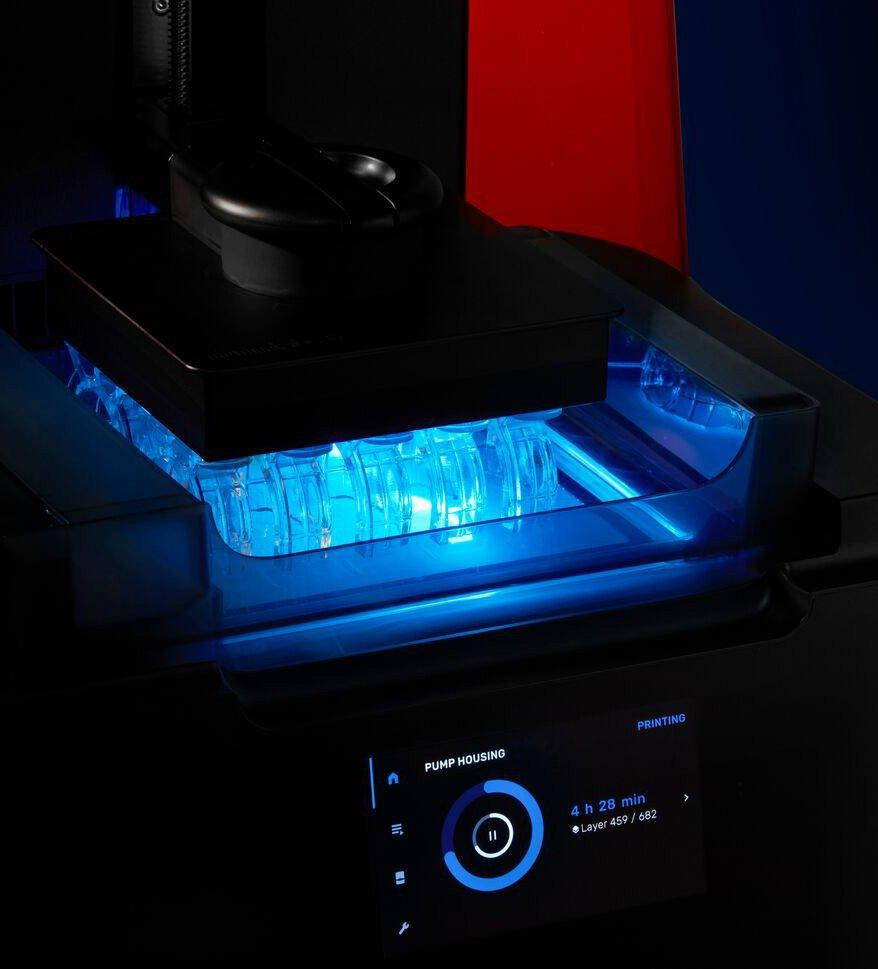
Formlabs光造形製品総合カタログ
本総合カタログでは、FormlabsのSLA光造形方式3Dプリント製品、極高精度を実現する特許技術LFS(Low Force Stereolithography™)技術の解説、各レジンの一括比較と詳細、使い方ガイド等光造形の情報を総合的にご紹介しています。
できそうなものしかやらないなら、外注と同じ
西野氏はシルバニアファミリーを担当するシルバニア本部に籍を置くが、当然エポック社の商品はシルバニアファミリーだけではない。西野氏は社内のあらゆる部署から「こんなものを作れないか」と相談を受け、日々3Dプリンタを駆使してチャレンジを続けている。冒頭にある通り、3Dプリンタのような新技術は導入後に社内で運用スキームに乗せる、そして社内で広く有用性を認められることが非常に重要だ。エポック社における3Dプリンタ活用をリードする西野氏は、どのようにして現在の立ち位置を得るに至ったのか、その経緯を聞いた。
「例えば風船であれば、これまでの経験と材料特性で『いける』とわかりました。Solidworksの回転機能を使ってウサギ等の耳を作りましたが、耳の部分で負荷の伝わり方が変わってしまうので最初は少し心配でしたが、上手くできました。PreFormの画面上ではサポートが不足しているという警告が出て、画面上では真っ赤ですけどね(笑)。」Formlabsの造形準備ソフトウェアPreFormは、ビギナーのユーザーでもプリントが成功するよう造形の成功率を重視したアルゴリズムでサポート材の自動生成やプリンタビリティ(造形が成功する可能性)が判定される。しかし熟練したユーザーであればPreForm上で警告が出ていたとしても、PreFormのアルゴリズム以上の、よりギリギリの線で勝負できる感覚を有している。こういった感覚や想定通りの形状、精度が得られなかった時の対処法こそが、3Dプリンタを使いこなすユーザー側のノウハウだ。3Dプリンタも加工機などと同様に、道具である以上はそれを使うユーザー側の力量によって当然ながら出来栄えは変わってしまう。想定通りの結果を得るには経験が不可欠なのだ。
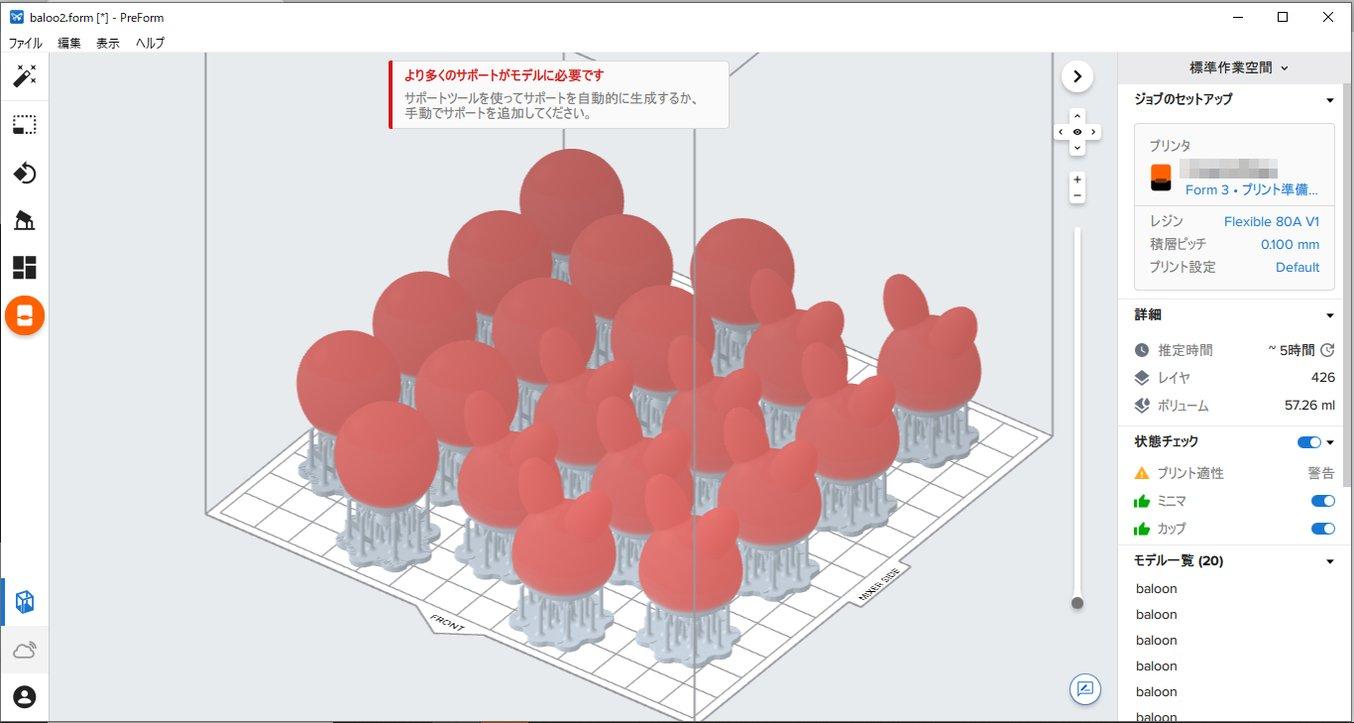
西野氏が触れた風船のPreForm画面のスクリーンショット。すべての風船が真っ赤な状態だが、経験則と材料特性からプリント可能と判断し、見事に成功。西野氏はこれまで数百個の風船を製作している。
しかし経験とは、時に困難を乗り越えてこそ得られるものでもある。3Dプリンタを使いこなす技術と経験を有し、それを武器に社内でその有用性を広く認知させ、多くの部署と人から頼られる同氏は、ひとつひとつの仕事から何を得るか、そしてそれをどのように発信するかという2点を非常に重視しているように見える。
先ほどの風船も、当初は市販品のミニチュア風船を購入することを考えたという。しかし風船から伸びる細い紐がイメージに合わず、自分たちで作ろうということになった。その1つのチャレンジの中でも西野氏は更に小さなチャレンジを重ね、シルバニアファミリーの世界観に完全に合致したものを手に入れている。
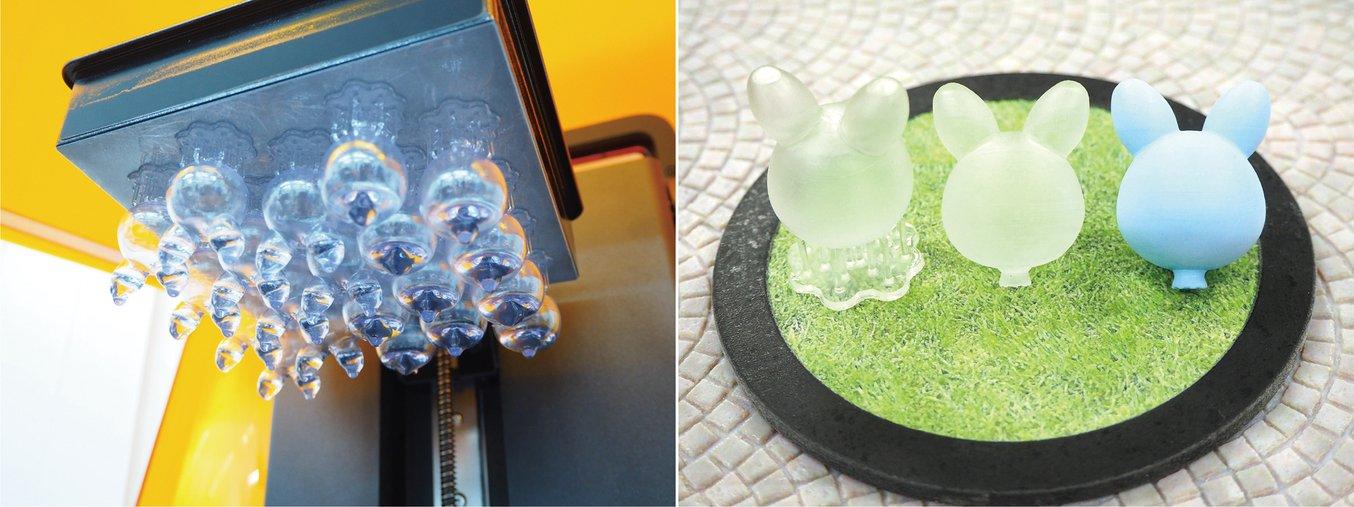
プリント完了時の風船(左)と後処理工程ごとの風船。内部にサポートを付けずにFlexible 80Aでプリントし、サポート材を除去して5分程度磨き、塗装で仕上げる。
私たちは、身の回りにある多くのツールを必ずしも教科書通りに使うだけではない。長く、あるいは頻繁に使うものであればあるほど「応用」を効かせるものだ。そうした「応用」も、ひとつひとつの仕事の細部に考えを巡らせ、丁寧に学びを得ることを繰り返すからこそ試行錯誤が実のあるものとなる。そしてそれを垣根を作ることなく広く共有し、周囲の理解と評価を得ていくことで、これまでの試行錯誤のプロセスも意味のあるものへと変わるのだろう。これは、あらゆる業務分野や役割が細分化され、深掘りされていく現代の社会人全員が身に付けるべきスキルの一つなのかも知れない。
6分40秒でわかるForm 3+
子供に夢と感動 大人に遊び心を
エポックメイキング(Epoch Making)という言葉がある。「新たな時代を作るような」「画期的な」という意味で用いられるその言葉を、理念ではなく「使命」として掲げるエポック社は、1958年に野球盤の発売と共に設立され、1985年3月20日には一世を風靡し空前のロングヒットとなるシルバニアファミリーをリリースした。どれも当時は画期的な商品であり、新たな時代を作ったと言える商品だろう。ではそんな同社の理念は何かと言うと「子供に夢と感動 大人に遊び心を」というものだ。西野氏はこれまで数百個に及ぶ風船を製作していると書いたが、その多くは社内他部署の人たちに始まり、同社に見学で訪れた人たちや社外で出会った人たちにプレゼントしている。「3Dプリントに興味を持ってもらえれば」と話す同氏だが、そこにはおもちゃメーカーで働く人としての、純粋な「人を楽しませたい」という心が透けて見える。
「自分自身で一歩一歩チャレンジを重ね、自身からこの機械ならこんなことができると他部署にも提案を行わなければ、ただのCADオペレーターになってしまう」と話す西野氏は、自身への厳しさとは対照的に、誰よりもその理念通りに子供に夢と感動、大人に遊び心を与え、伝えている人なのではないだろうか。