
今年の春に誕生したForm 4は、驚きのスピードと高精細造形で業界基準を揺るがしました。次世代のLow Force Display™(LFD)プリントエンジンに支えられ、3Dプリンタの性能を再定義し、ほかにはない確かな信頼性と造形スピード、造形品質、寸法精度、利用可能な材料の多彩性を、1台のプリンタで実現する製品となりました。
今回発表となるForm 4Lでは、Form 4と同じ革新的な技術を大容量で実現。最大 353 x 196 x 350mmの造形サイズを誇るForm 4Lは、高精細な大型モデルの製作や高い生産量にも高速で対応します。
大容量の光造形3Dプリントを初めて手頃な価格で実現したのは前代機のForm 3Lでしたが、ユーザーは造形時間の長さによって開発や生産工程の遅れを感じることがありました。これらのペインポイントに対処すべく開発されたForm 4Lでは、驚きのスピード、信頼性、コストパフォーマンスを大容量のプリントでも実現します。プロジェクトを理想のペースで進めながら、直感的なワークフローや豊富な材料など、Form 4で得られるメリットはすべてそのままご利用いただけます。
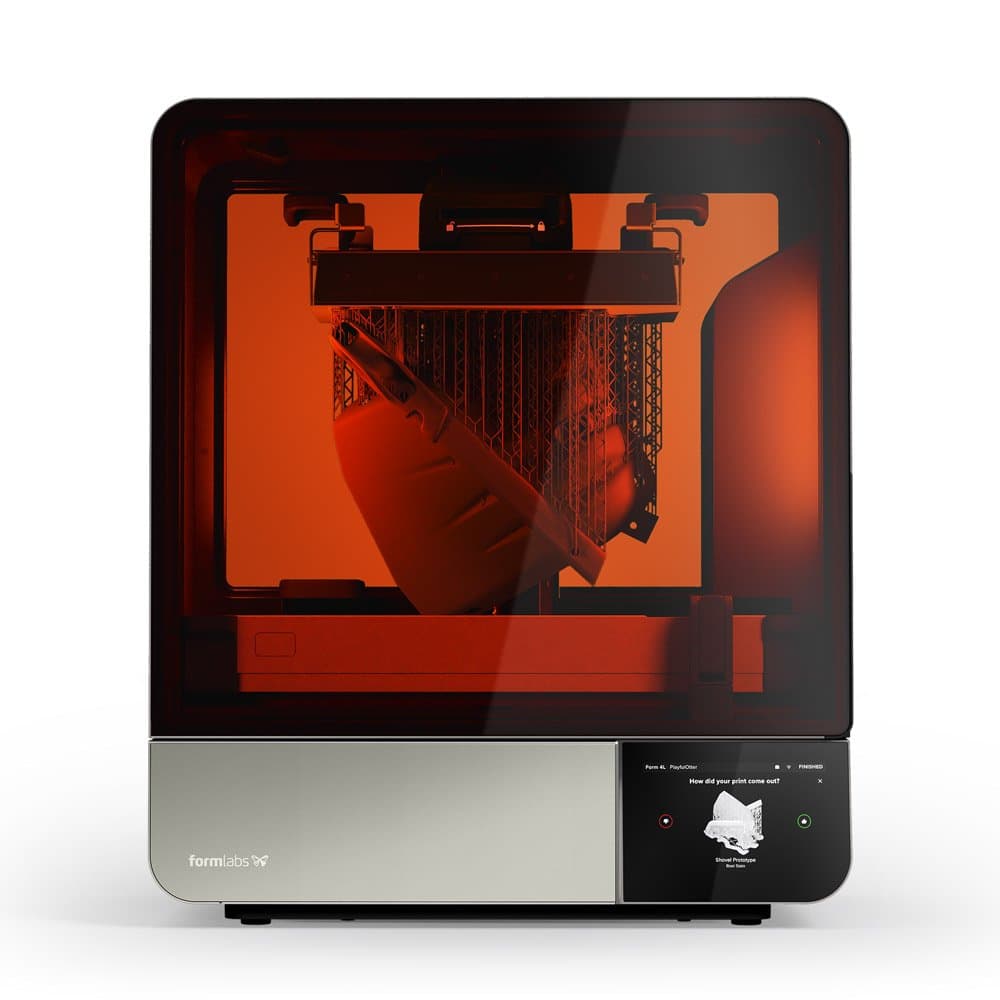
製品デモでForm 4Lを詳しく知る
次世代の大容量光造形3Dプリンタ Form 4Lは、Form 4で実現した驚きのスピードと精度、信頼性を、まったく新しいスケールで叶えます。
Form 4Lを支えるLow Force Display™テクノロジー
Form 4Lは、マスク式光造形(MSLA)方式という、光源をモデルの面一体に照射しながら、液晶画面を使って光源を選択的にマスキングし、光にさらされた部分だけを光重合という化学反応で硬化させる3Dプリント方式を採用しています。これにより造形速度は大幅に向上する一方、表面品質や安定性、高精細度、ハードウェアの耐久性がトレードオフとなることがよくありますが、Form 4Lのテクノロジーはこれらの課題に対処し、高精細・高精度な大型モデルでも高速かつ安定的な造形を叶え、さらには滑らかな表面に仕上げます。
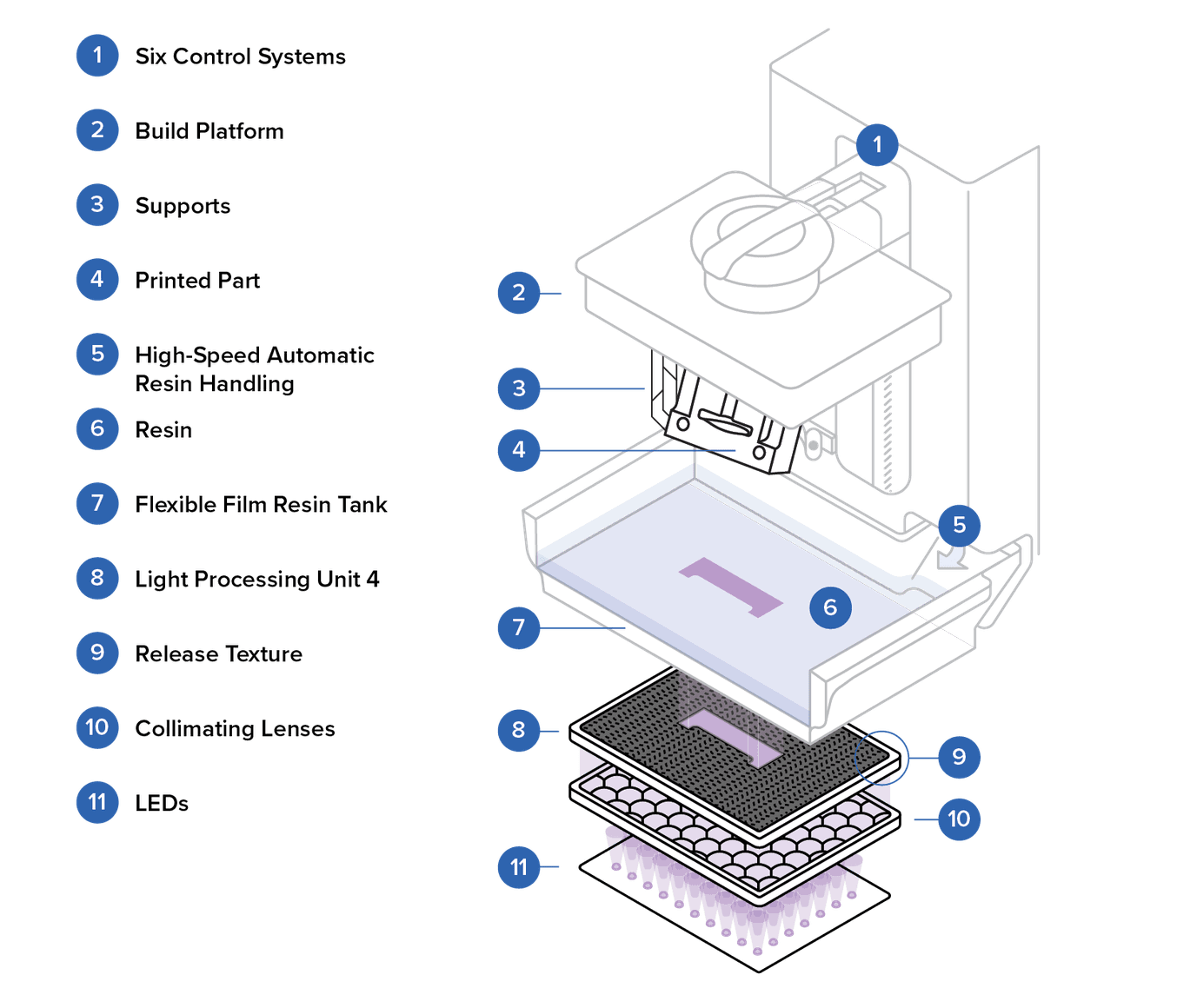
Form 4LにはForm 4と同じ技術開発が行われた。
Form 4Lの基盤となるLFDプリントエンジンには、核となるバックライトユニットが搭載。145個のLEDによる超高出力光源とコリメートレンズで、16mW/cm2という強力な光学パワーで光を照射します。その後、光線はLPU 4L(ライトプロセッシングユニット)を通過し、偏光板や光学コーティング、カスタム液晶画面によってモデルの各層の形に変形されます。こうすることで超高速造形を叶えながら、ビルドプラットフォームのどの箇所でも優れた造形品質や精度を維持します。
LPU 4Lは耐久性と安定性が高く、常に一貫した品質で材料やモデルの高さに応じて600,000〜1,900,000層もの造形ができるよう開発・製造されています。LPU 4Lは長く使える設計ながら、必要に応じて簡単・迅速に交換も可能です。
SLA光造形プリンタのForm 3Lは、レーザーを使ってモデルの形状をなぞります。一方、Form 4Lは、MSLAとLFDを採用することで造形品質を犠牲にすることなく超高速造形を叶えます。
Form 4シリーズプリンタを支えるテクノロジーの詳細については、こちらをご覧ください。
大型モデルも、超高速で
Form 4Lの造形速度はForm 3Lの2〜4倍で、造形サイズは13%向上、そして造形可能な最大高さは6%向上しています。つまり、以前は複数パーツに分けてプリントし、最後に組み立てていたモデルも、一度にプリントできるようになります。小型部品なら、より多くの数量を1回のプリントで造形できるようになり、生産量の向上も狙えます。
Form 4L | |
---|---|
最高造形速度 | Fast Modelレジン使用で80mm/時* |
平均 | 30mm/時** |
変動範囲 | 材料により10〜80mm/時の間で変動 |
Fast ModelレジンV1を積層ピッチ200μmで造形した場合の最高造形速度。一般的なエンジニアリング、プロダクトデザイン、製造、歯科用途でテスト品を造形した際の実際の造形時間に基づく。
積層ピッチ100μmで造形した場合の全材料の平均造形速度。造形時間は材料、積層ピッチ、造形品の形状によって変動する可能性あり。
Form 3Lはすでに大容量のFDM(熱溶解積層)方式3Dプリンタよりも高速な造形を実現していましたが、Form 4Lの技術革新により、その記録は打ち砕かれることになります。Form 4Lは、主要なFDMプリンタには大きすぎるモデルにも対応可能なほか、さらに多くの数量を一度にプリントできることで生産量も向上。それでいて、ほぼすべての造形が6時間以内に完了します。同じようなモデルを他の3Dプリンタで製作しようとすると、最低でも一晩、多くの場合には数日かかることが一般的です。
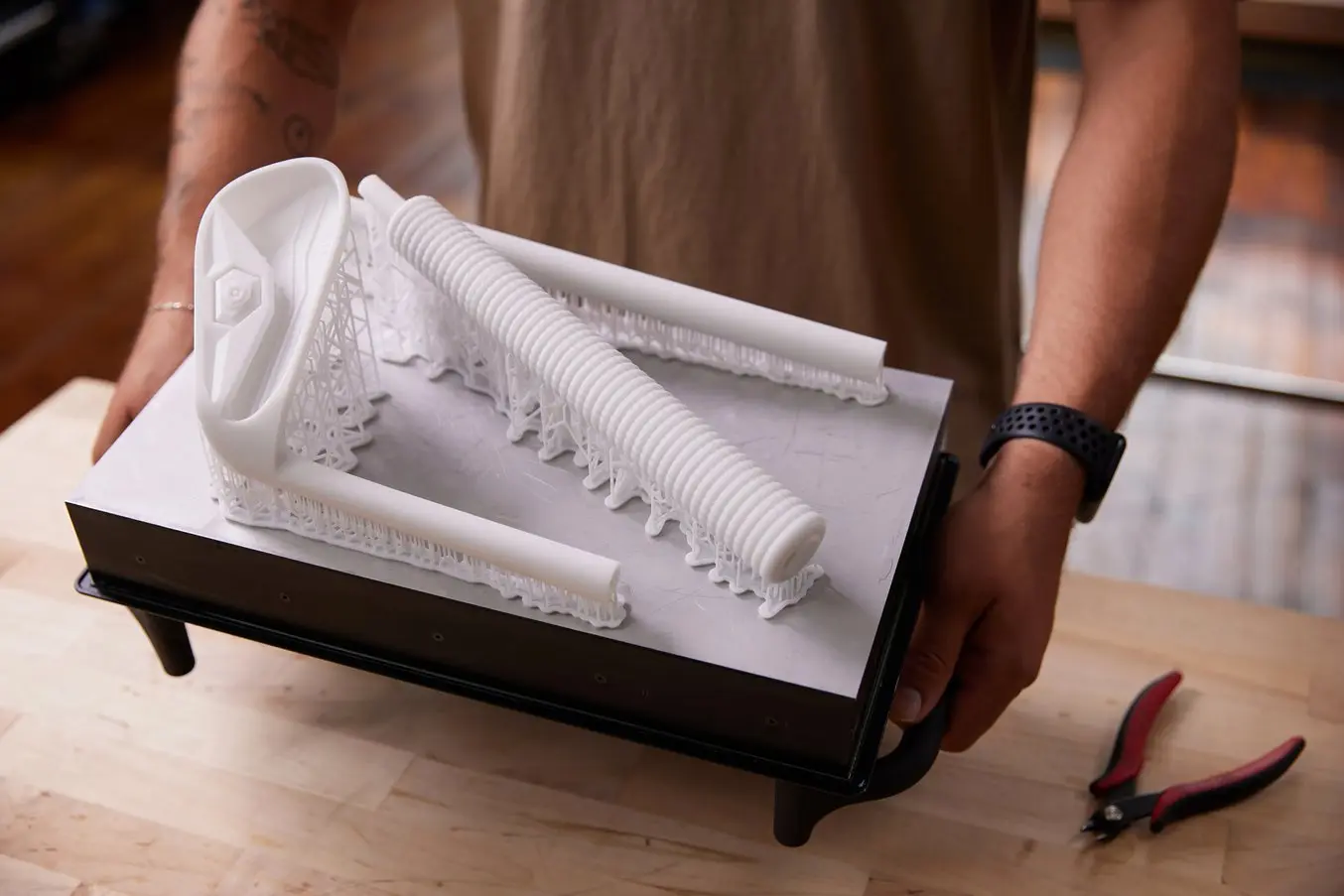
ミニゴルフクラブ
Form 4L:5時間50分
Form 3L:17時間17分
主要なFDM:10時間38分
大容量FDM:68時間34分
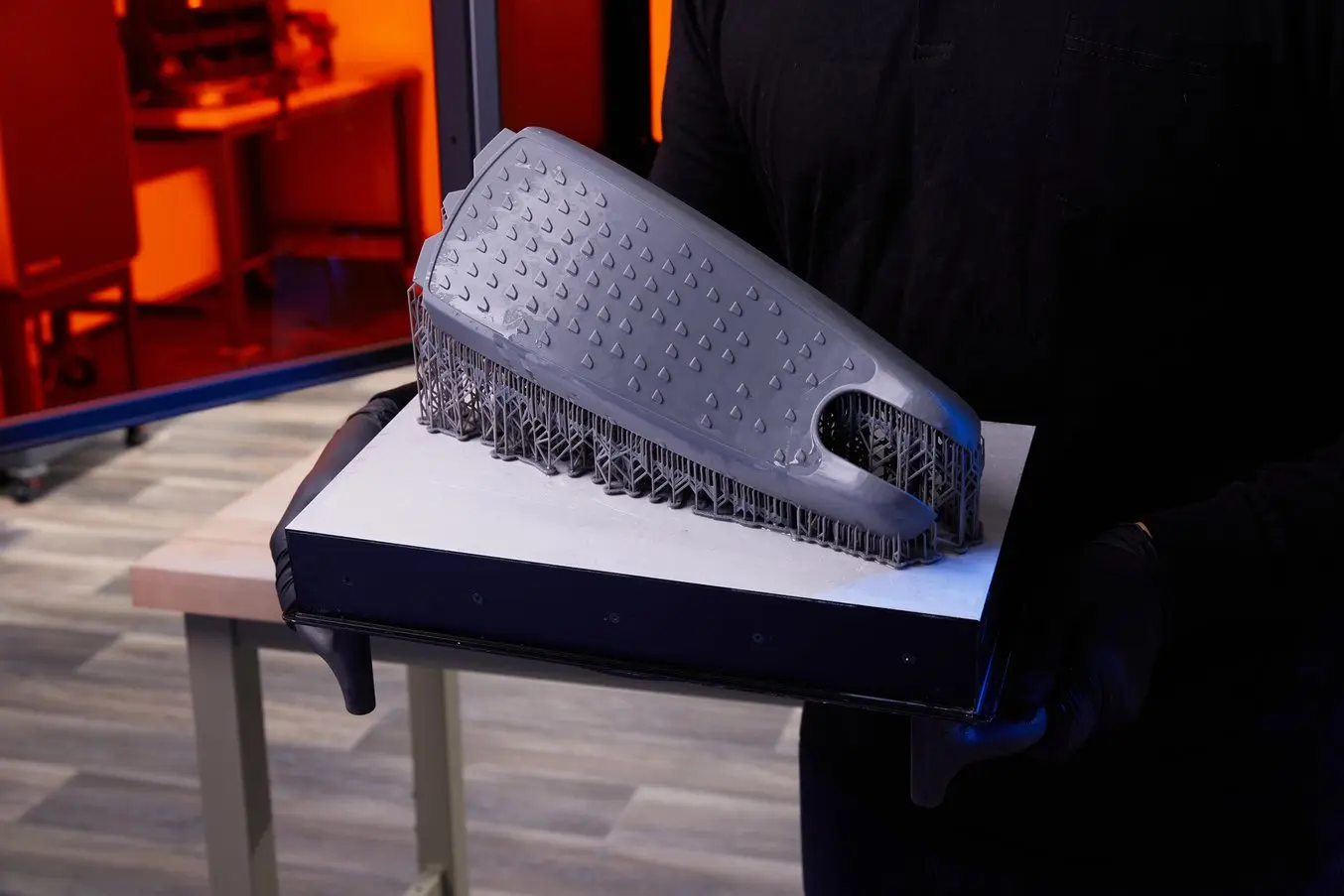
RadioFlyer製スクーターカバー
Form 4L:4時間58分
Form 3L:18時間47分
主要なFDM:12時間43分
大容量FDM:76時間48分
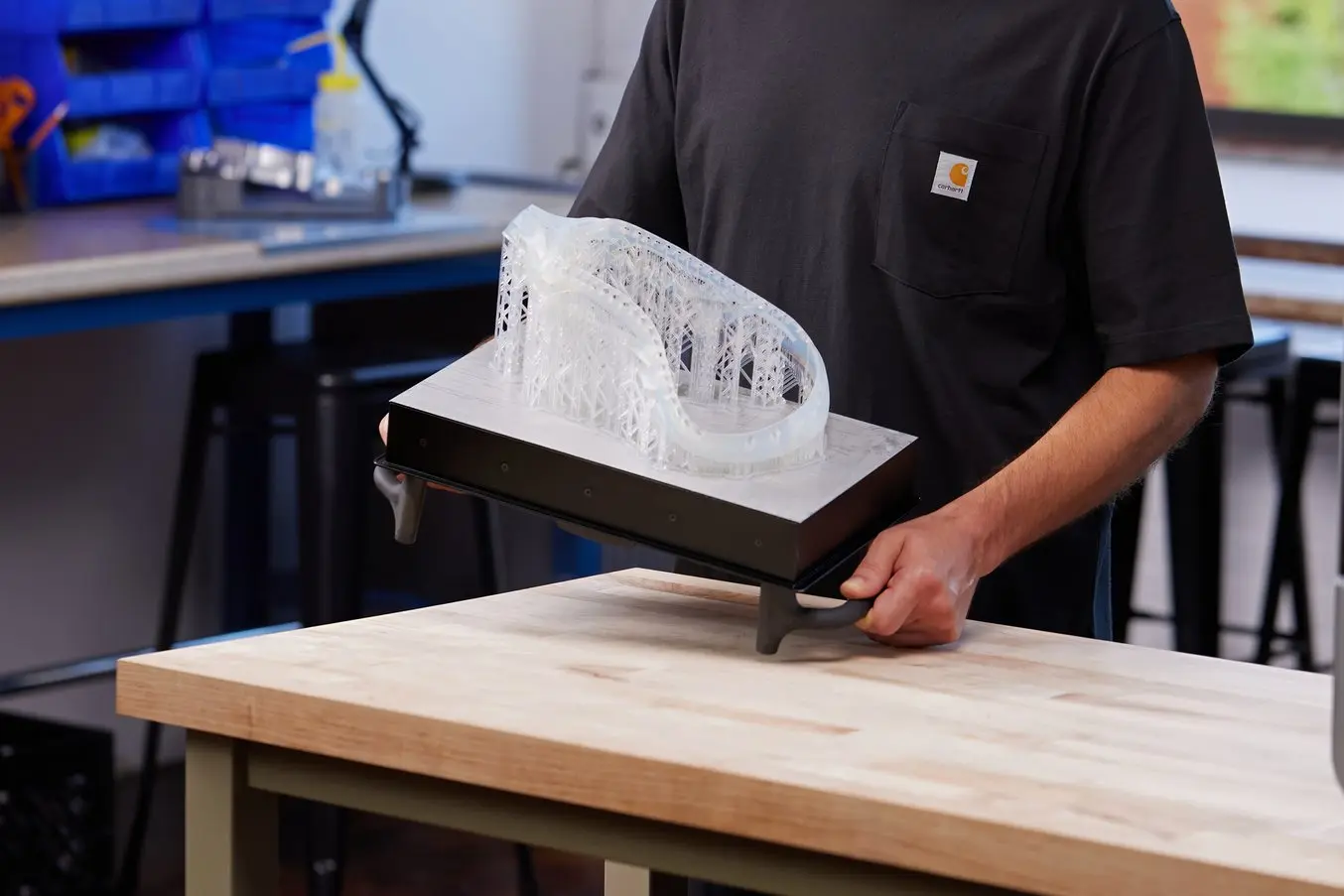
ラクロスヘッド
Form 4L:4時間54分
Form 3L:21時間57分
主要なFDM:14時間24分
大容量FDM:62時間32分

Stingrayシート
Form 4L:2時間37分
Form 3L:21時間6分
主要なFDM:サイズオーバー
大容量FDM:42時間3分
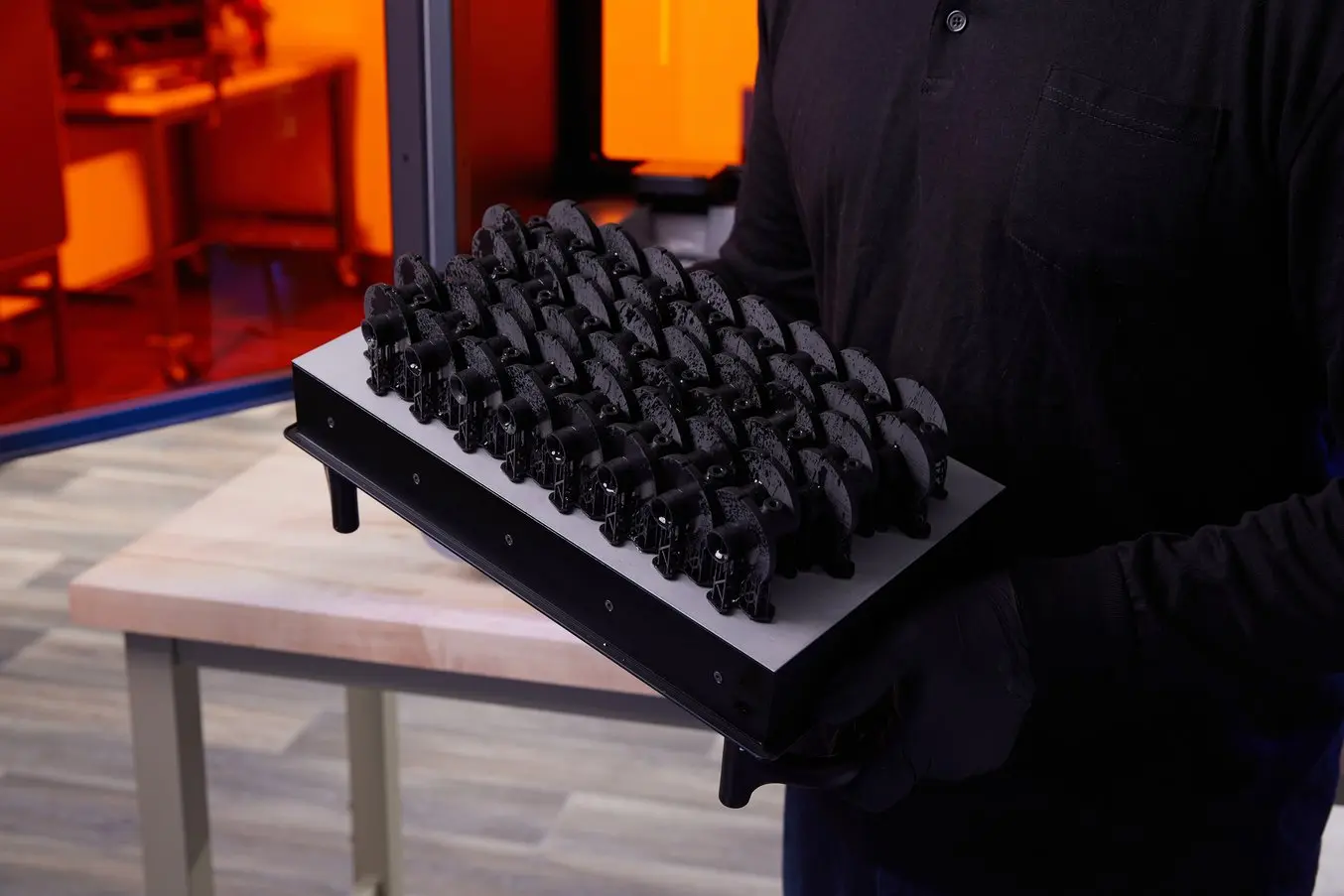
バックホルダー
Form 4L:4時間12分で50点
Form 3L:22時間52分で50点
主要なFDM:12時間48分で20点
大容量FDM:86時間49分で22点
注:主要なFDMプリンタの造形時間はBambu X1Cを、大容量FDMプリンタの造形時間はUltimaker S7をもとに算出。
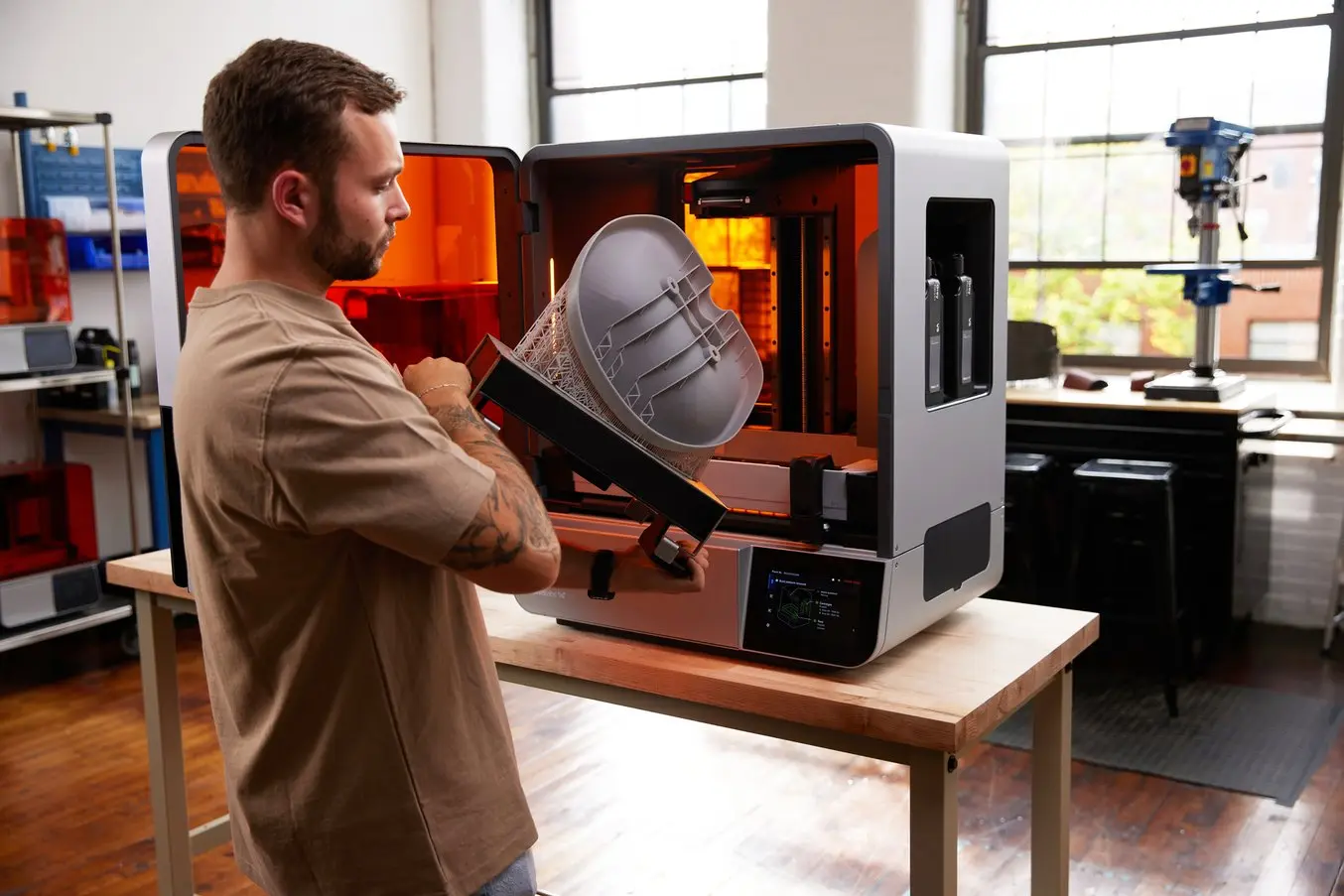
RadioFlyerの作るStingrayシートは、主要なFDMプリンタではサイズオーバーで対応不可に。Form 4LならFast Modelレジンを使ってわずか2時間37分で造形。同じパーツをForm 3Lで製作した場合と比べてスピードは8倍、大容量FDMプリンタと比較した場合には16倍に。
もちろん、造形時間とコストは造形品の形状、材料、レイアウト、造形の向き等により変動します。それでも、Form 4LのLFDプリントエンジンにより、比較可能な範囲だけでも造形時間が大幅に短縮されたことがわかります。また、ビルドプラットフォームの拡大によりさらに大きな造形が可能になったことで、以前なら2回に分けてプリントしなければならなかったり、仕上げ工程で複数部品を組み立てるといった追加のワークフローが必要だったパーツも、Form 4Lなら一度に対応できるようになります。
安定生産を、いつでも
高速造形はイノベーションを加速する可能性を秘めている一方、プリントが成功しなければ意味がありません。プリントが失敗すると、時間もレジンも無駄になり、作業工程が中断してしまいます。造形サイズが大きくなると失敗の確率が上がるうえ、失敗した時のコストもかさみやすくなるため、大容量3Dプリントをさらに難しくする要因にもなっています。
大型モデルの造形は困難がつきまといます。Form 3Lに対するユーザーフィードバックでは、安定性がいちばんの難点であると指摘する声が多く見られました。Radio FlyerのAgostino LoBello氏はこう言います。「Form 3Lには色々と悩みの種がありましたが、Form 4Lでは精度が高まり、さらに高速で安定感も増したので、今後はもっと使う機会を増やしていこうと思っています」
「Form 4BLの限界を試すような使い方をしてきたのですが、これまで造形に失敗したことは一度もありません。高負荷下での安定性は目を見張るものがあります」
セントルイス小児病院 3Dプリントエンジニア、Brian Albers氏
Form 4Lでは、マシンの信頼性に直接アプローチする機能改善が行われました。ベータテスターやFormlabsの社内エンジニアが何百回ものテストプリントを行い、Form 4Lの限界を試してきました。LFDプリントエンジンに加え、Form 4Lに搭載されたシステムが、高速、高精度、高信頼のプリントを実現しています。
マシンの信頼性は工場から始まり、すべてのプリンタが60項目にわたる較正や品質管理検査を通過します。造形が始まると、Form 4Lの内部システムやスマートセンサーが安定したプリント品質を維持します。例えば、6つの統合型センサーがレジン温度、レジンレベル、造形中の荷重、造形ステータスを正確に制御したり、赤外線による温度センサー搭載のレジンの高速予熱機能により、材料に応じてレジンの温度を25〜45°Cまで加温します。
機械的に結合されたミキサーも速度と信頼性が増し、粘度の高いレジンもムラなく混ぜ合わせ、高性能材料を常に均質に利用できる状態を作ります。安定感とスピードが向上したカートリッジ式のレジン供給で、材料の補充によるプリントの一時停止を防ぎ、予想造形時間内でノンストップの造形を実現します。
Z軸荷重センサーは、モデル形状や使用材料に応じて造形品質と造形速度のバランスを自動で最適化します。統合型カメラでどこからでもプリントの状況を確認できるほか、予防メンテナンスのリマインド通知でForm 4を常に健康に保ち、安定的な稼働をサポートします。
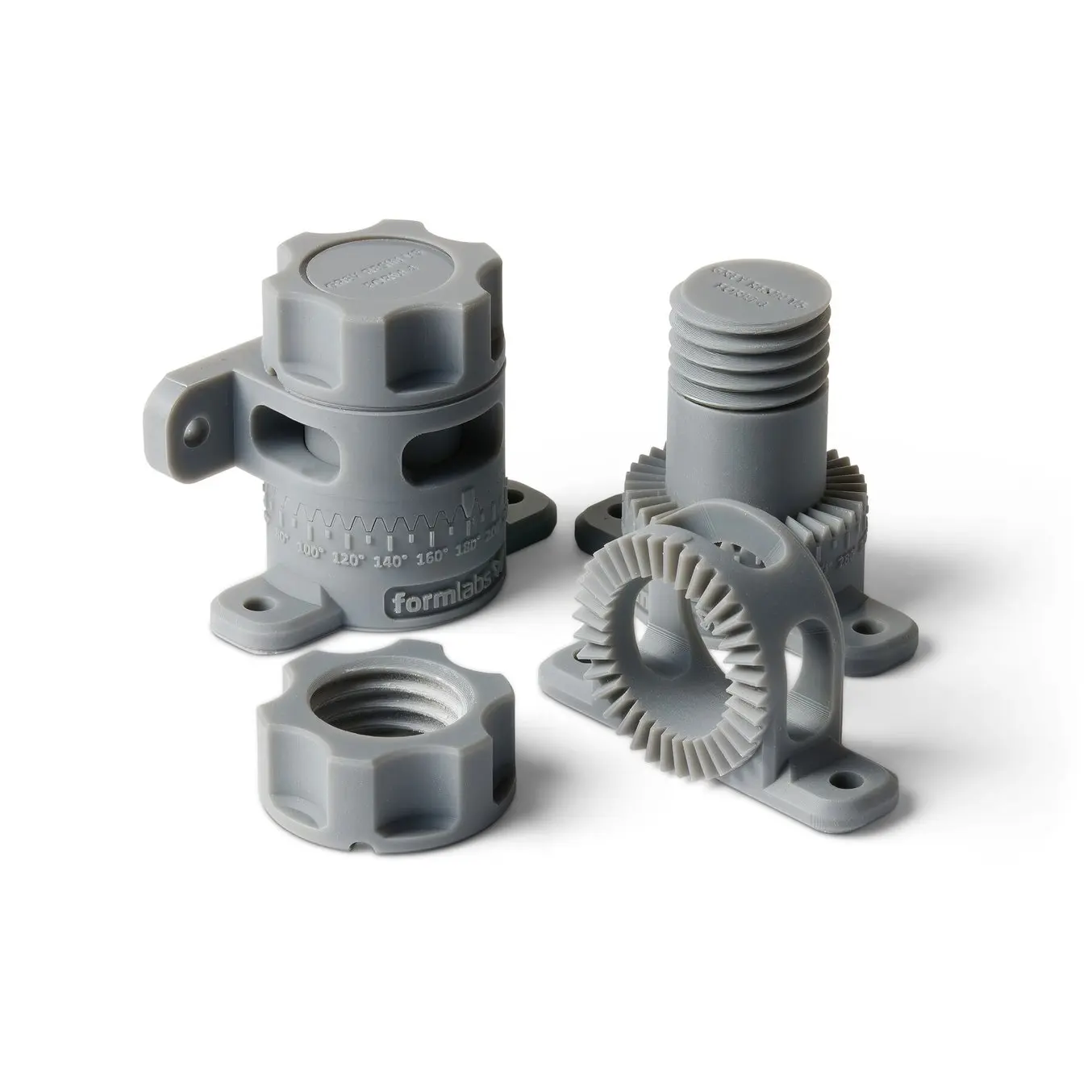
Form 4L vs. Form 3L、一目で比較
Form 3Lは、SLA光造形の魅力である多様な材料と高精細さを生かした大型モデルの造形を可能にしてきました。Form 4Lは、その大容量プリンタを再設計・再エンジニアリングしたことで、大型モデルの造形時間を一営業日以内に短縮しながら、射出成形品に匹敵する表面品質を叶えます。
Form 4L | Form 3L | |
---|---|---|
造形方式 | マスク式光造形(MSLA)方式 | SLA光造形方式 |
プリントエンジン | Low Force Display™(LFD) | Low Force Stereolithography™(LFS) |
プリントエンジンの主要構成部品 | バックライトユニット ライトプロセッシングユニット4L(LPU 4L) リリーステクスチャ 底面に柔らかいフィルム採用の新設計レジンタンク インテリジェント制御システム レジンの高速自動供給機能 | レーザー レーザーユニット(LPU) 底面に柔らかいフィルム採用のレジンタンク レジンの自動供給機能 |
光源 | バックライトユニット(LED)、コリメートレンズ | レーザー |
レーザーユニット(LPU) | LCD(液晶ディスプレイ)、リリーステクスチャ | ガルバノメーター、ミラー、空間フィルタ |
最大造形サイズ | 353 x 196 x 350mm 13.9 x 7.7 x 13.8 in 24.2L | 335 × 200 × 300 mm 13.2 × 7.9 × 11.8 in 21.4L |
「大きな変化としてはやはりスピードの向上ですが、寸法精度も以前より向上しています。今は、最大造形サイズいっぱいのボックスも失敗せず造形できるようになりました。同じサイズをForm 3Lで造形した時は、ボックスと蓋がしっかり合わなかったんです。Form 4Lの前は、CNCルーターを使って加工してしまうか、SLSで複数部品を製作して組み合わせていました」
Radio Flyer 製品開発エンジニア、Agostino Lobello氏
37種類以上の業界屈指の材料と、Open Material Modeにアクセス
Form 4Lの新たなテクノロジーにより、業界屈指の23種類以上のFormlabs材料が利用可能になります。その中には、性能が向上し、深みのある色合いと鮮明なディテールが特徴の、6種類の新レジンも含まれます。Formlabsの生体適合性レジンを使用する場合は、Form 4BLで37種類以上の材料をご利用いただけます。
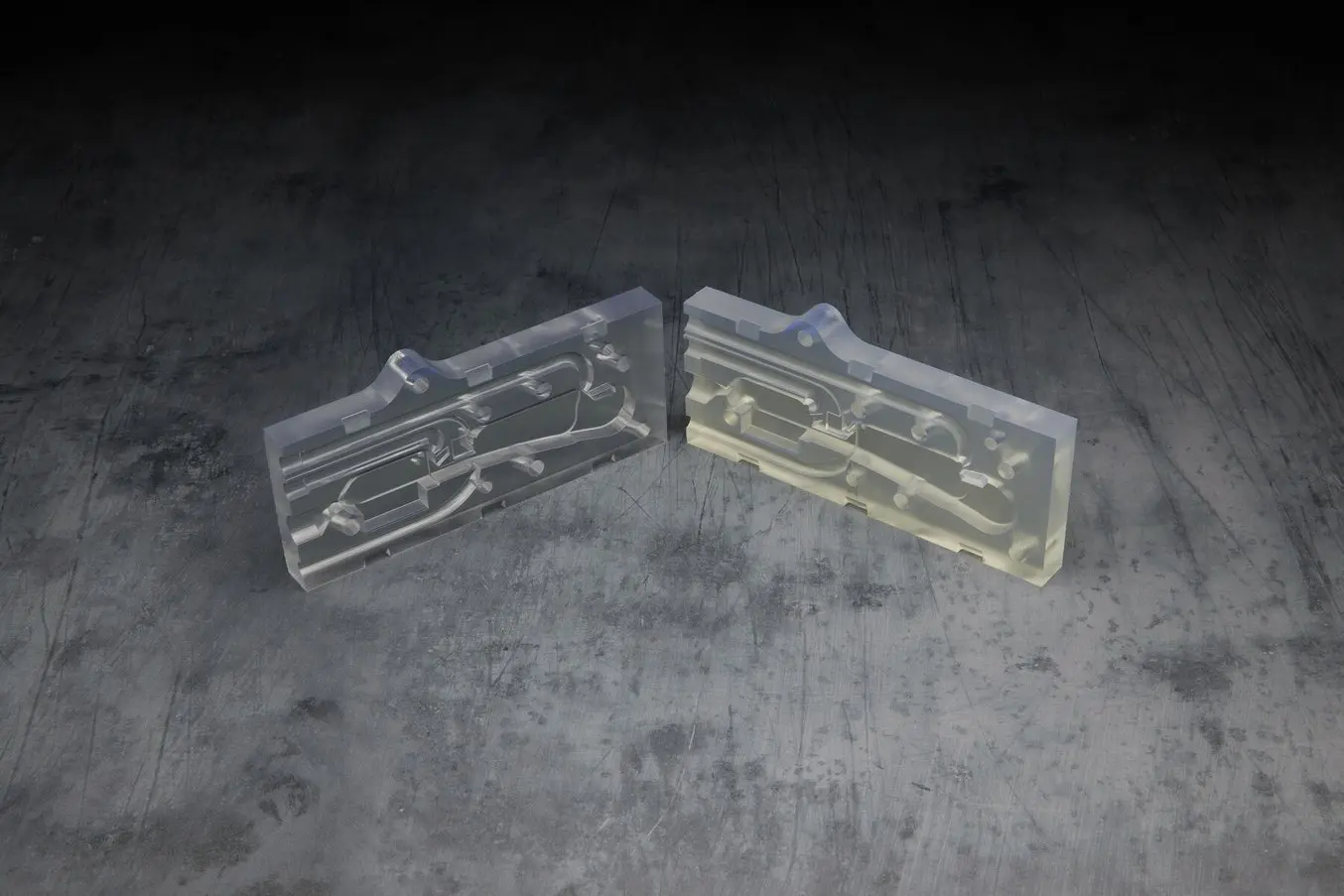
Form 4世代プリンタ用のClearレジンV5(左)は、Form 3世代プリンタ用のClearレジンV4(右)より透明度が増していることがわかる。
次世代のレジンカートリッジでレジン供給のスピードも5〜10倍(材料の粘性による)アップしたことで、造形開始までの時間も短縮できるほか、カートリッジ本体にも再設計が行われ、廃棄物の63%削減と30%の省スペース化を実現しています。さらに、Form 3Lと同様、Form 4LでもResin Pumping System(RPS)がご利用いただけます。5Lのレジンをプリンタに直接供給できることで、頻繁なカートリッジの交換が必要なく、レジンのボリュームディスカウントと合わせて時間もコストも削減できます。
造形品のサイズが大きくなったからといって、必ずしもコストが上がるわけではありません。Form 4L向けのスタンダードレジンは、Form 3シリーズ向けのレジンに比べて価格が30%低く、レジンタンクなどの消耗品も耐久性が増して長寿命化しました。交換が必要な場合も、これまでより低コストでご購入いただけます。
Formlabsのオープンエコシステムは、Form 4Lでご利用いただけます。Open Material Mode(OMM)によるサードパーティ製の材料を使った造形のほか、パワフルなハードウェアと造形設定の微調整が可能なPreFormエディタを駆使したカスタムレジンの開発も可能になります。研究者や熟練ユーザーにとっては、3Dプリントの限界を押し広げ、レジン開発や各用途特有の材料特性の開発をさらに進化させるきっかけとなるかもしれません。
Formlabsレジンの詳細については、Formlabsの材料ライブラリをご覧いただくか、無償のサンプルパーツをリクエストいただくと実際の造形品を手に取ってご確認いただけます。サードパーティ製の材料を使った造形を開始するには、OMMをご購入ください。
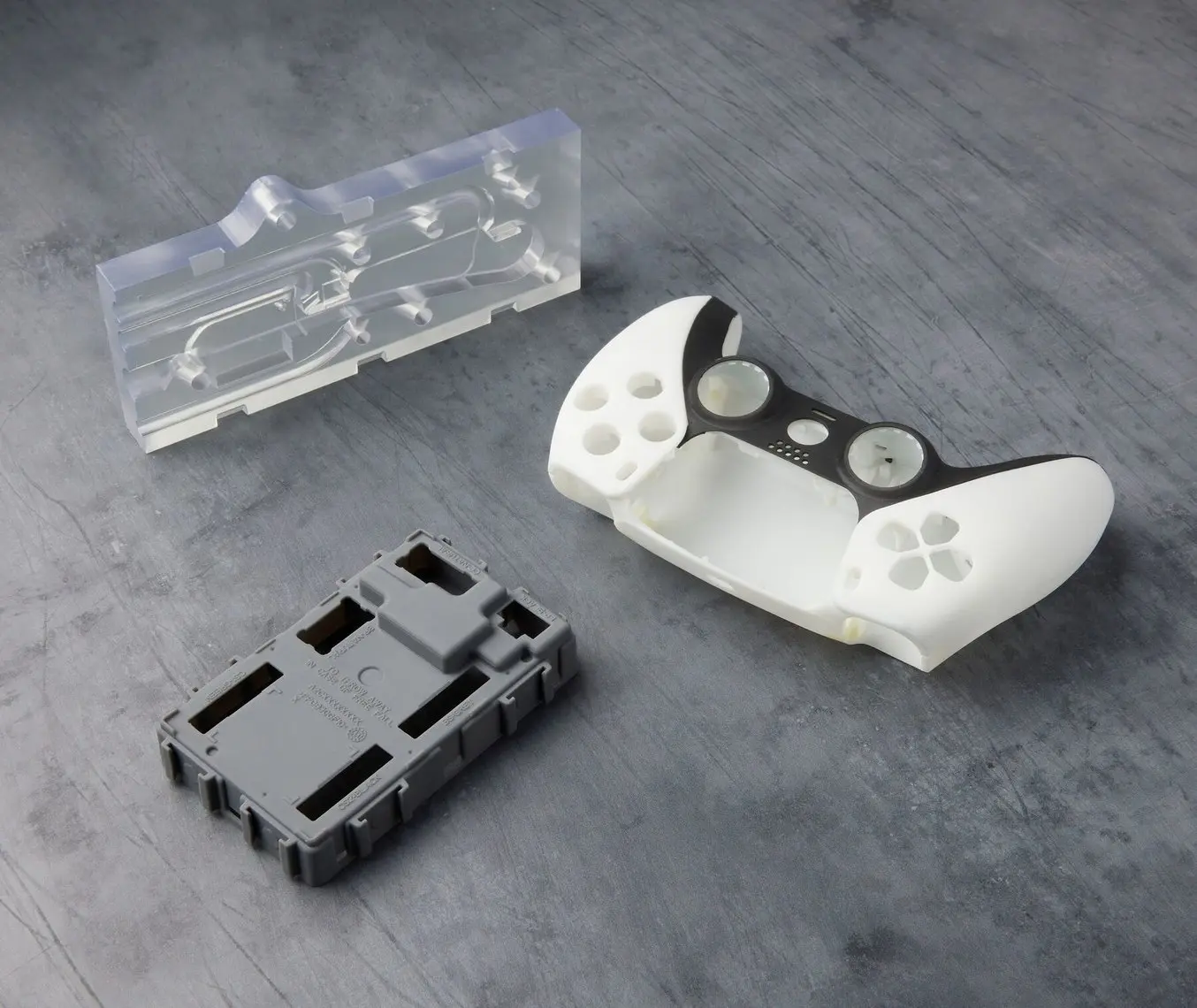
一歩先の生産性へ
Form 4は、高精度なプリントを超高速で叶えるという偉業を成し遂げました。Form 4Lは、これをさらに次のレベルへと押し上げ、MSLAの生産性に込められた可能性を最大限に引き出しながら、造形可能なサイズにおいてさらに高い水準を打ち立てます。大型モデルの造形がたった6時間以内で可能になった今、大型のプロトタイプならお昼休憩が終わる頃に、造形サイズいっぱいの複数モデルの造形なら翌朝までに手に取ってご確認いただけるようになります。
大型モデルの造形も、超高速で。Form 4Lを今すぐお試しください。以下のウェビナーでは、Form 4Lの詳細をさらに深掘りしています。お客様用途に合わせたForm 4L導入のご相談については、Formlabsまでお気軽にお問い合わせください。