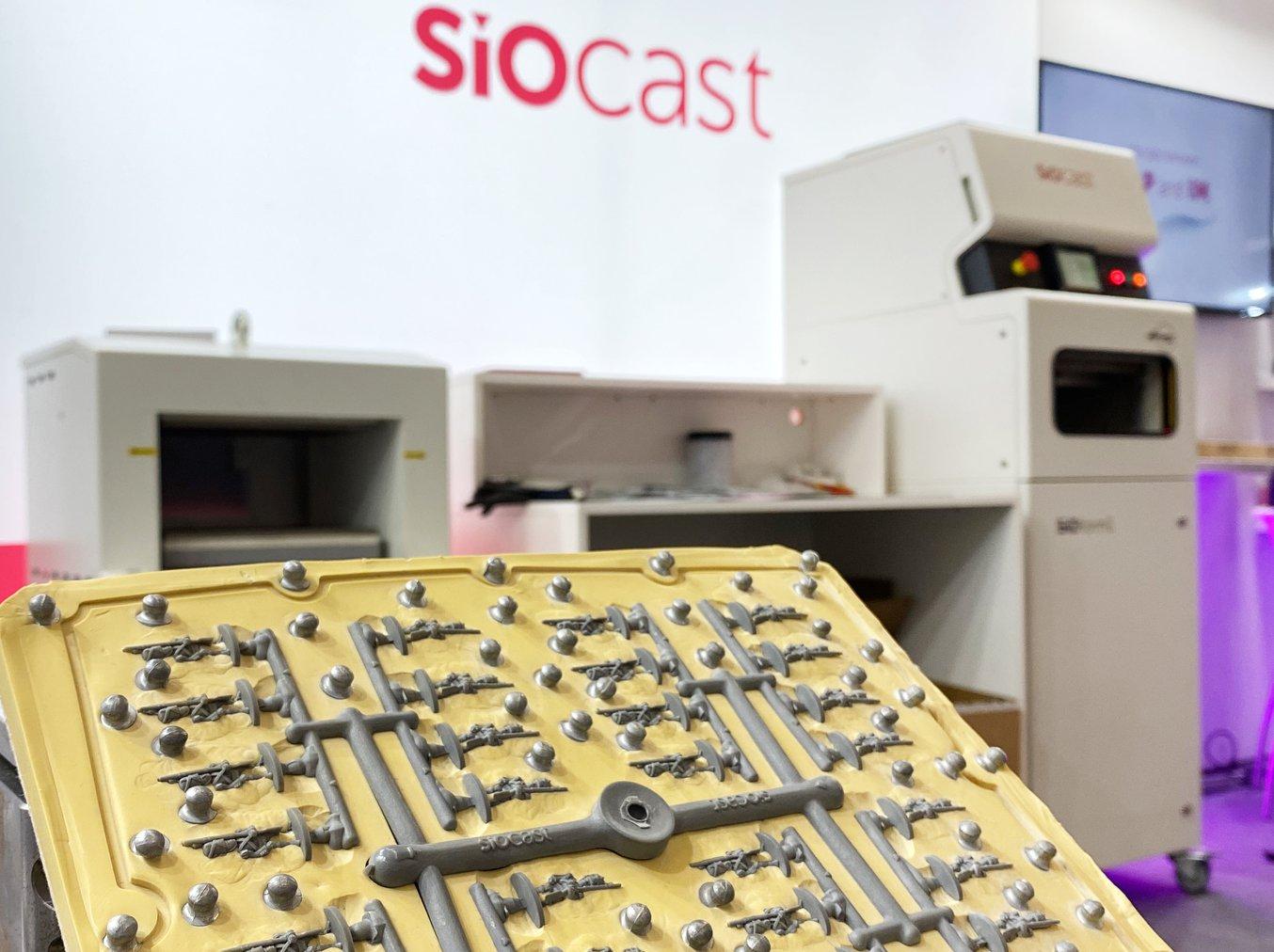
SiOCASTは、高品質で毒性のない部品をリーズナブルな価格で内製できるよう、独自の高速生産システム、成形機、材料を提供してミニチュア製造の未来を切り開こうとしています。
3Dプリントとシリコン成形、射出成形のメリットを融合させた独自システムで使うシリコン型を3Dプリント製の原型から起こすSiOCASTの技術は、小規模なスタジオからMonster Fight Club(The Witcher、Cyberpunk RED)、Reaper Miniatures(Bones)、Warlord Games(Blood Red Skies、Bolt Action)など業界最大手のミニチュアメーカーまで、すでに幅広く採用されています。
本記事では、SiOCASTのCEO兼共同創設者であるFerran Navarro氏が、ミニチュアや小型部品を熱可塑性プラスチックで製造する同社のAlemany Systemと呼ばれる技術とその製造工程でどのようにFormlabsの3Dプリンタを活用しているかを詳しく解説します。
3Dプリントと射出成形のギャップを埋めるSiOCASTの新技術
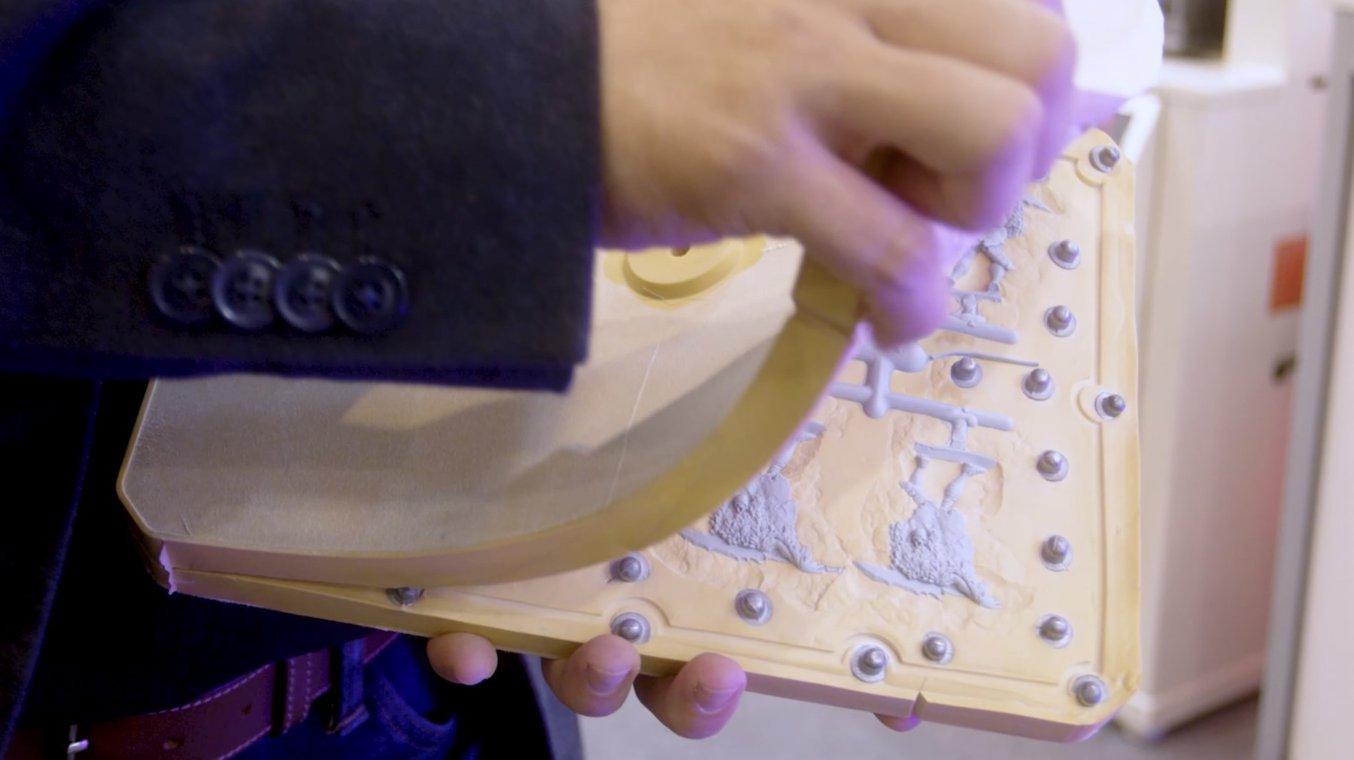
ミニチュアを大量生産するための従来の技術は高額で品質が低く、生産規模の拡大が困難でした。その中で最も一般的な製法の1つである射出成形は最大で数百万点の生産が可能ですが、金型製作のコストが高く製作期間も長くなります。初期投資や大量に生産しなければならないことも、中小企業の市場参入を妨げる大きな障壁となっていました。また、大手ミニチュアメーカーにとってもミニチュアの新デザインをリリースしなければならないことが大きなリスクになります。
一方で、SLA光造形方式3Dプリンタのような技術を使えばミニチュアフィギュアを直接3Dプリントするという方法も可能で、参入障壁を低く抑えながらディテールまで高精細に表現することができます。しかし、大量生産の場合は3Dプリントは射出成形には及びません。通常、ミニチュアメーカーが3Dプリントを使うのは単発品や極端に少量の生産、またはマスカスタマイゼーションが一般的です。
遠心鋳造法やレジン鋳造などすでに確立されているミニチュア製造技術は、非常に労力がかかり作業場も汚れ、生産規模の拡大が難しく多くの場合有毒な材料を使用するため、工業クラスの生産工程として採用するには複雑な技術なのです。
SiOCASTはこれらの課題に取り組むことを目標に設立されました。SiOCASTは、35年以上にわたって遠心鋳造法とシリコン成形業界を専門にソリューションを提供してきたスペインのConiexのスピンオフ企業です。3Dプリントと射出成形の間にある生産性のギャップを埋めるべく8年間にわたって行ってきた内研究開発の集大成とも言える会社で、異なる部品を50〜50,000点、時には400,000点にのぼる膨大な量を生産しています。
SiOCASTが開発し特許を取得した熱可塑性レジン射出成形機は、高精細な3Dプリント製の原型から起こした高温加硫シリコンゴム型を使用し、玩具に使っても安全な耐久性の高い材料で小型部品を生産します。
すべての工程が環境に優しく、海外のサプライヤーに頼ることなく国内生産が可能なSiOCASTの成形機は4年足らずで収益性が実証され、すでにアメリカ、イギリス、アジア、EUなど複数の国や地域でさまざまな企業に導入されています。
弊社のこの技術は、遠心鋳造法とレジン鋳造、射出成形を融合させた新技術です。できる限りシンプルに誰でも導入できるような技術にするため、さまざまな改良を重ねてきました。工程を自動化することで大型の射出成形機と同等の生産性を実現した他、取り扱うシリコンも非常に低コストで安全、そして国内生産が可能というメリットがあります。
Siocast CEO兼共同創業者 Ferran Navarro氏
3Dプリントを活用してシリコン型を高速製作
シリコン型の製作はこれまで物理的な原型やパターンから起こさなければならず、さらにこの原型やパターンも手作業や遠心鋳造法、CNC加工による製作が必要でした。
しかし、Formlabsの3Dプリンタのような高品質で手頃な価格のSLA光造形方式3Dプリンタが登場したことで、SiOCASTは高精細な3Dプリント製の原型を使って成形型を起こすことができるようになりました。
SiOCASTの成形型の製作工程。
SiOCASTの成形型の製作工程をご紹介します。
1. デジタルで型を設計
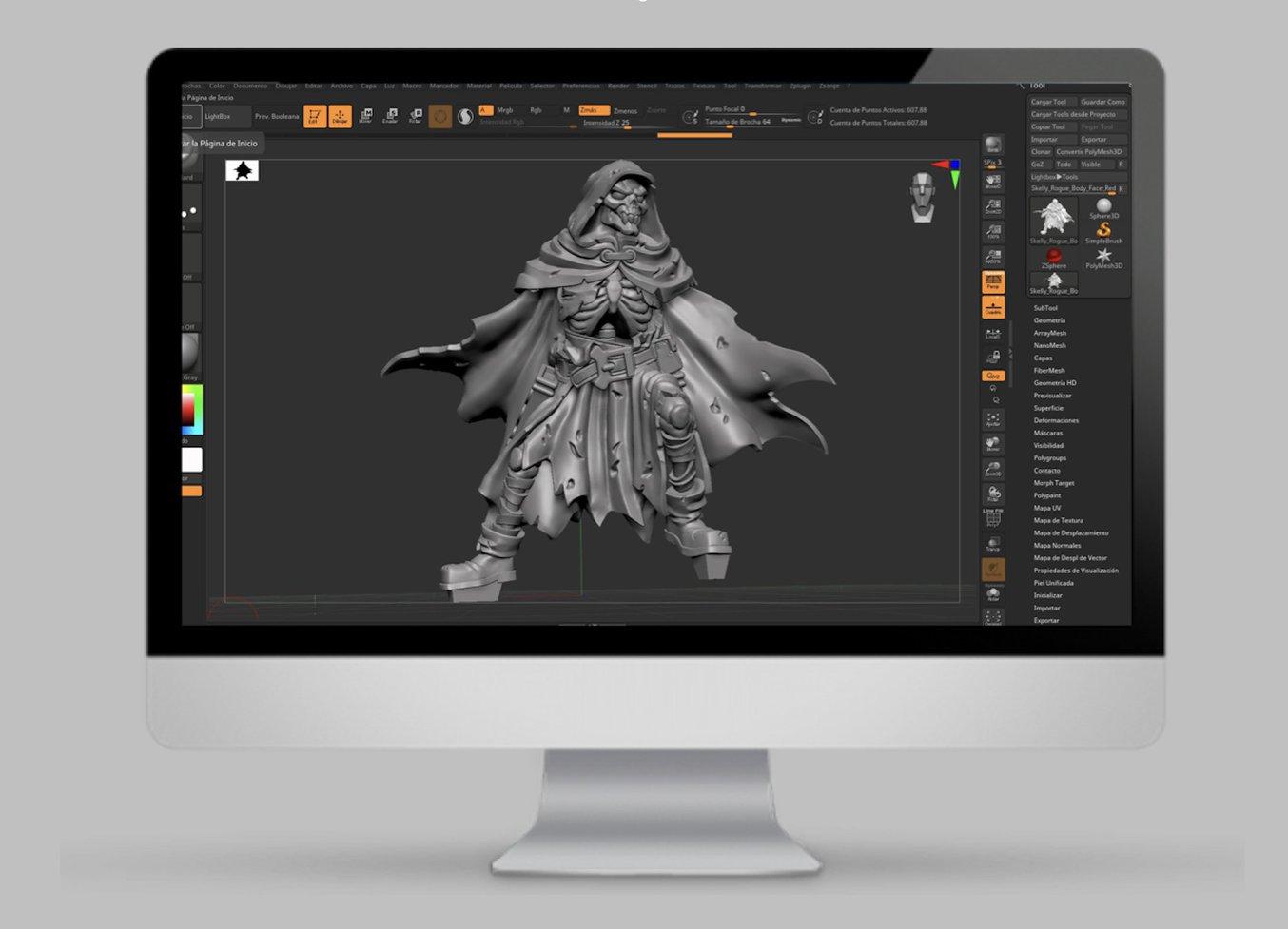
Broken Anvil Miniaturesが設計した3Dモデル。
デザイナーがCADソフトウェアを使ってモデルを可能な限り詳細まで設計します。ここで設計したディテールがすべて3Dプリント製の型で再現され、そこからSiOCASTの成形型にも複製され、実際に生計を行います。SiOCASTの成形機ならアンダーカットの多いデザインも実現可能です。現在、SiOform1で成形できる実部品の最大厚みは40mmです。この設計段階で、標準ファイルライブラリから射出成形で使うゲートも追加します。
2. 原型とランナーを3Dプリントで製作
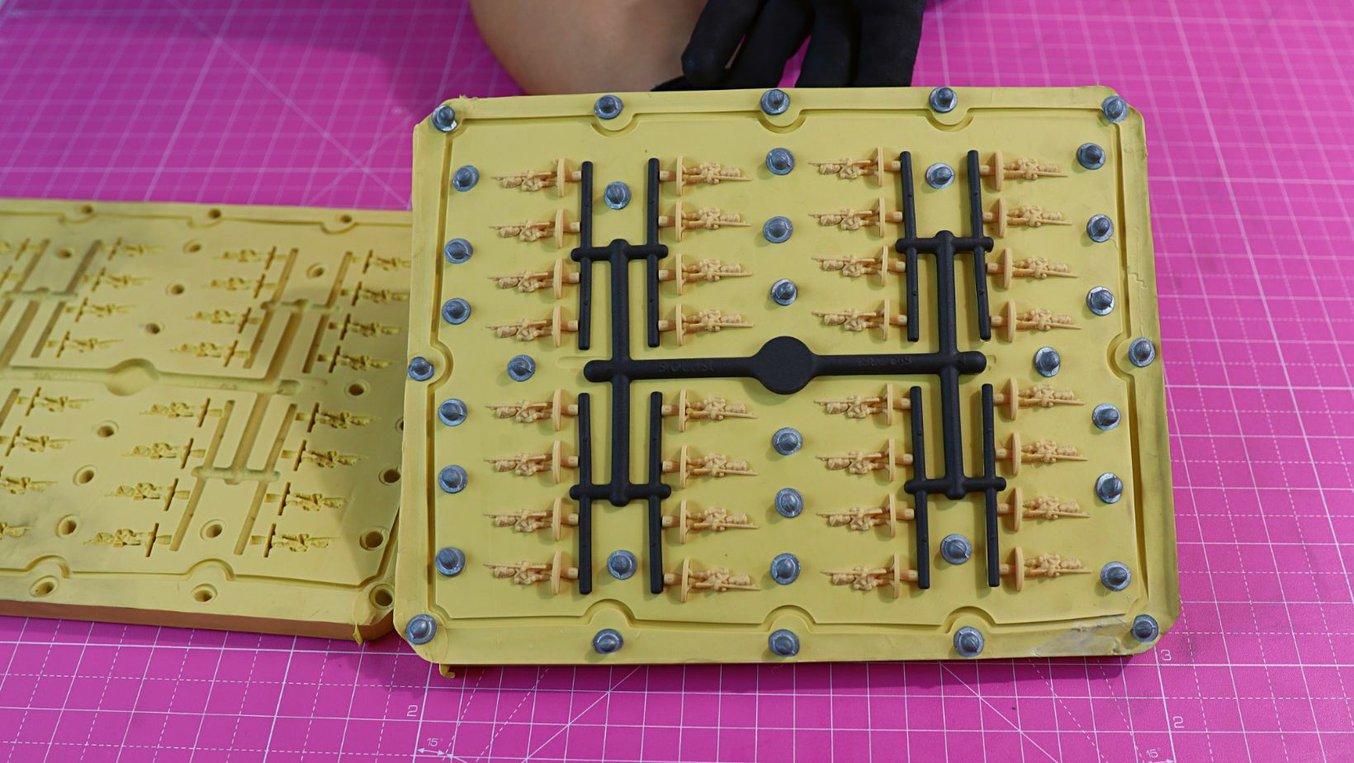
Form 3+で造形した原型とFuse 1で造形したランナー。
型のデジタル設計が完了したら、SiOCASTはFormlabsの造形準備ソフトウェアPreFormとForm 3+ SLA光造形プリンタを使用して、高温にも耐えられ、加硫工程で優れた機械的特性を発揮するModel V2レジンで原型を3Dプリントします。
造形時の角度は約45度に設定します。平面がビルドプラットフォームに接地している場合には、ヘラが造形品を壊してしまわないよう、角の面取りをします。
「所有している4台のFormlabsプリンタは、どれも常にフル稼働しています。Formlabsのプリンタを導入しているのは私たちだけではありません。SiOCASTを導入しているお客様も、原型に求める要件を満たすにはFormlabsのプリンタが1台〜2台必要になります。中にはFormlabsプリンタを4台も所有しているお客様もいて、3Dプリントの需要の高さが伺えます」とFerran氏は言います。
Form 3+ SLA光造形プリンタで、高品質な原型を手頃な価格でわずか数時間で製作することができます。ディテールを最大限に再現するために、同社では積層ピッチを25ミクロンに設定してミニチュアを造形しています。
私たちはこれまで、DLP方式やSLA光造形方式、SLS方式など、さまざまな技術や3Dプリンタを試してきました。さらに高精細なディテールを求めるお客様はDLP方式を選びますが、その場合レジンの耐久性がやや落ちる可能性があります。こういった高度なディテールの再現性と加硫への耐久性が必要な用途には、私たちは主にFormlabsのSLA光造形プリンタを使っています。そして機能部品の生産も始めた今、Form 3+で積層ピッチを25ミクロンに設定できることで、安心して原型が製作できます。
Siocast CEO兼共同創業者 Ferran Navarro氏
造形後は、洗浄および二次硬化工程を自動化したFormlabsのForm WashとForm Cureで後処理を行います。
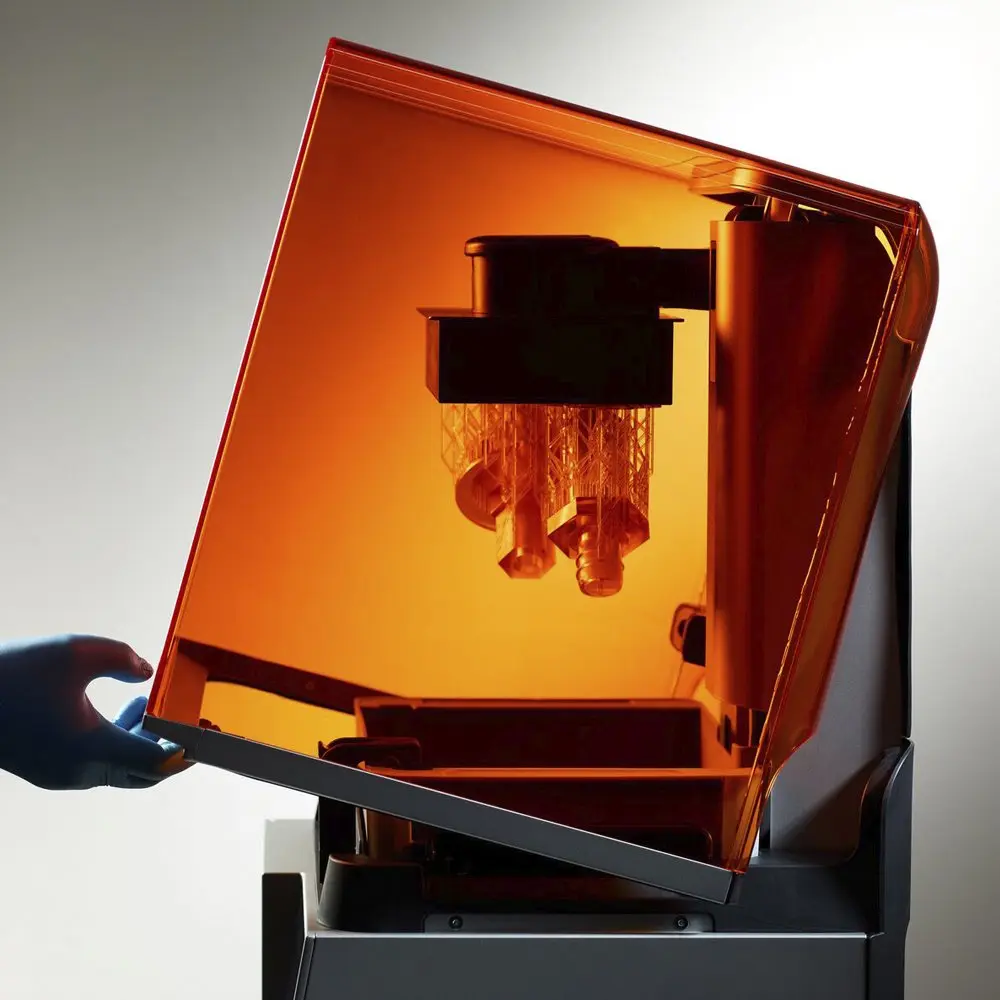
デスクトップサイズSLA光造形方式3Dプリンタの概要
高精細3Dモデルを製作できる3Dプリンタをお探しですか?本技術資料をダウンロードして、SLA光造形方式が高精細なモデルの製作においてどれほど広く活用されているか、その仕組みも含めてご確認ください。
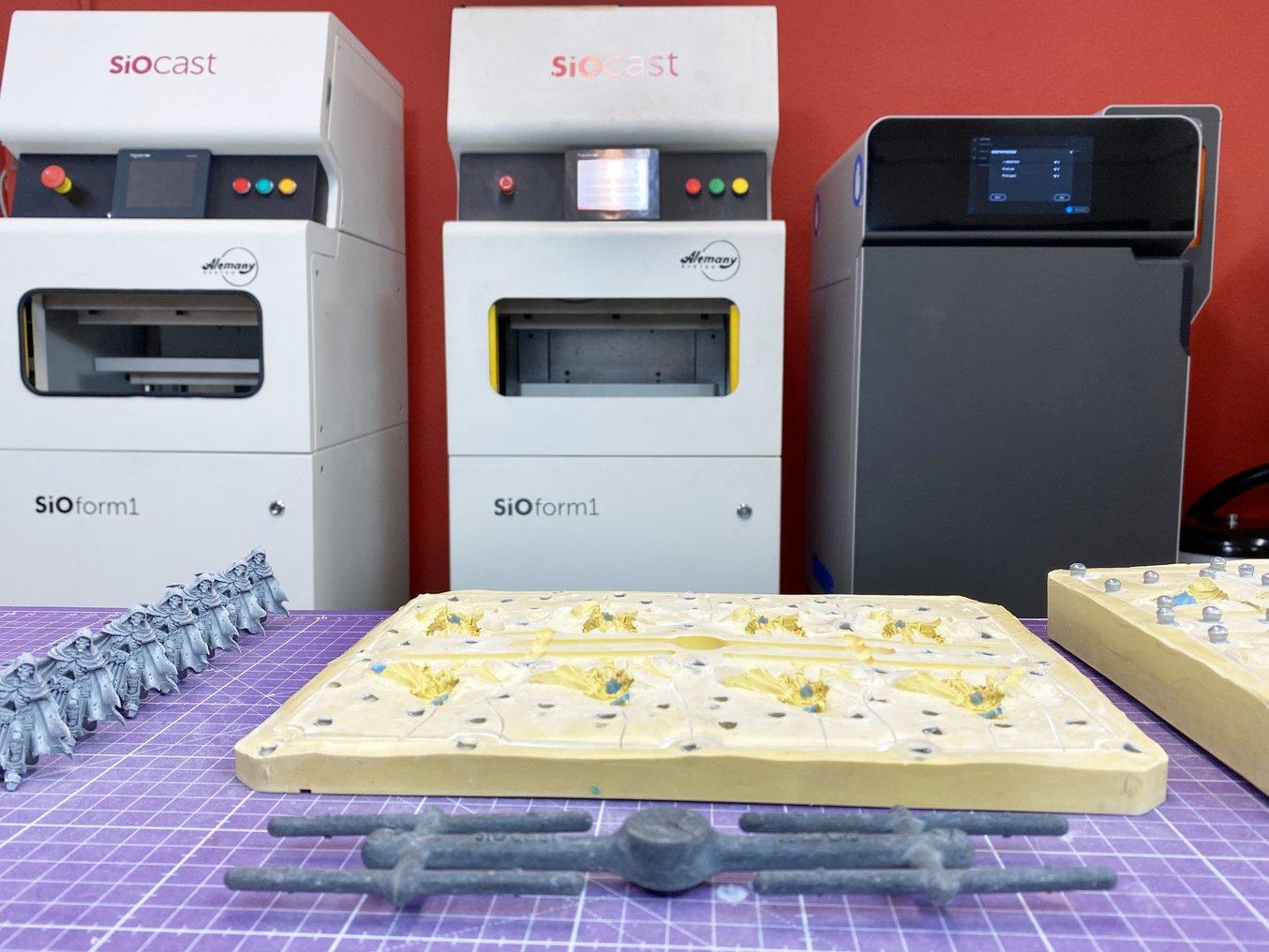
Fuse 1で造形したランナー。
SiOCASTは原型の製作だけでなく、鋳造工程で必要になるランナーの製作も3Dプリンタで行っていて、製作にはSLS(粉末焼結積層造形)方式プリンタのFuse 1を使用しています。SLS方式でプリントしたランナーは耐久性に優れ、造形する際もサポート材が不要で複数の造形品をビルドチャンバーに収めることができるため、世界中にいるSiOCASTの顧客に供給できます。
Fuse 1で工程が高速化されたおかげで、ランナーの試作・検証プロセスを何度も繰り返し行って設計内容を確定することができるようになりました。社内の研究開発プロジェクトとして過去2年間で成し遂げてきたよりも多くのことを、たった2週間の間にこなせている感覚があります。
Siocast CEO兼共同創業者 Ferran Navarro氏
SLS方式の3Dプリント工程はSLA光造形方式の場合とほとんど同じです。造形準備ソフトのPreFormでプリント用のファイルを準備し、Fuse 1 3DプリンタでNylon 12パウダーを使って造形。その後、Fuse Siftで後処理を行います。SiOCASTではFuse Siftの他にConiexのAbrastという装置で、アディティブマニュファクチャリングで製作した部品の表面処理を行っています。
3. 加硫でシリコン型を製作
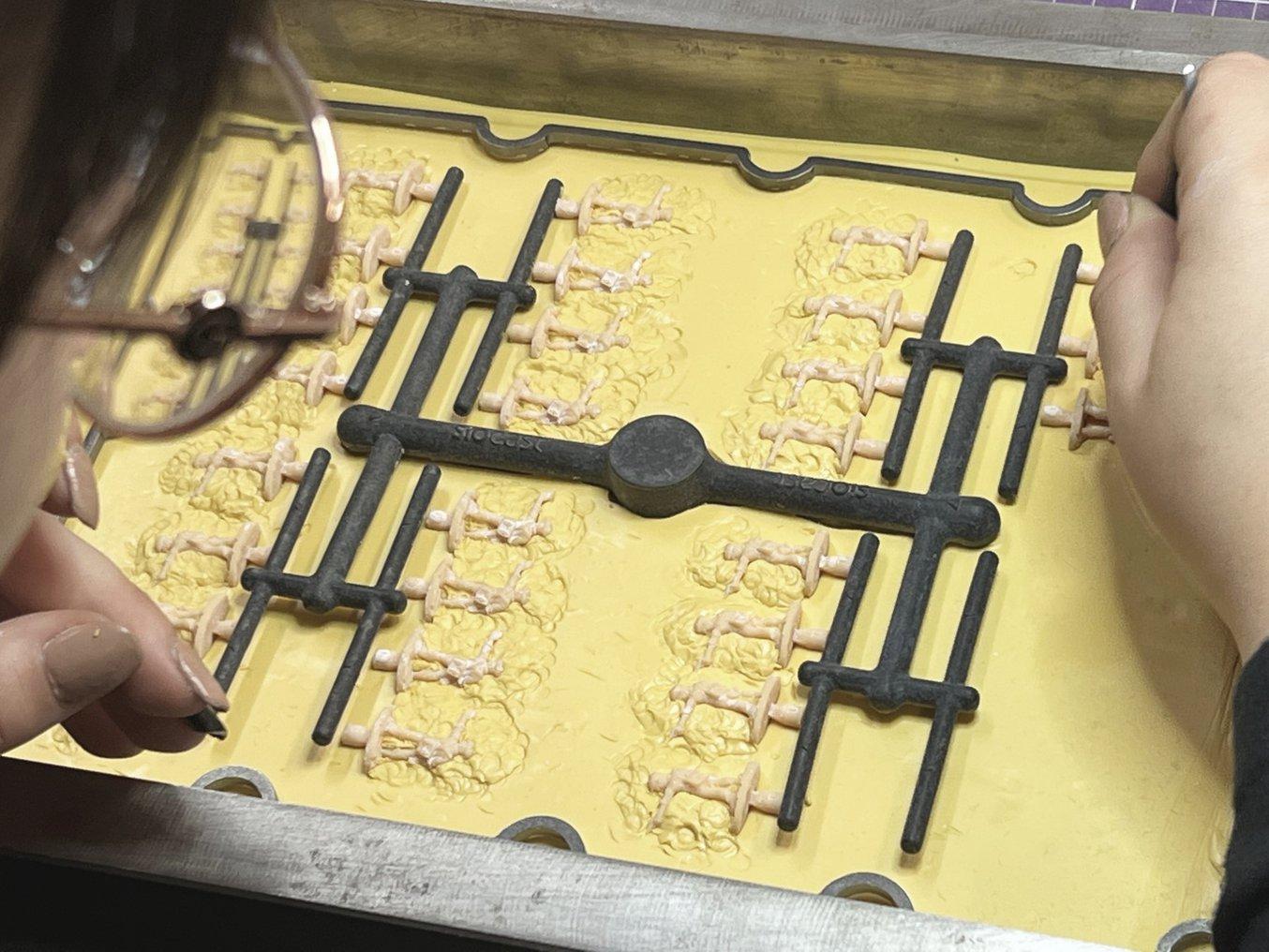
加硫による型の製作準備
原型とランナーを3Dプリントで製作したら、次はSiOmoldシリコンゴムで型を製作します。SiOmoldはSiOCASTが提供しているショアA硬度65または80の高温加硫(HTV)シリコン材料で、CONIEXグループが特注で作った耐熱性と機械耐性に優れたエラストマーを成分としています。CNC加工で製作した硬く精密な金属枠の中にシリコンラミネートシートを被せ、3Dプリント製の原型をシリコンシートの上に均等に配置し、意図するパーティングラインが出せるよう周りに慎重にシリコンを足していきます。SLS方式で3Dプリントしたランナーも配置し、プレスしてスラブを成形します。
センタリングユニットを使用して上型と下型をしっかり固定します。その後、離型剤となるタルクを表面に撒き、シリコンの両側が互いにくっつくのを防ぎます。シリコンの最上層を重ねたら、金属ボックスのフレームを閉じます。製作する型の複雑さにもよりますが、この工程の所要時間は10分〜2、3時間程度です。
その後、金属ボックスを加硫プレス機SiOpressの中に入れます。プレス機の中ではシリコンと3Dプリント製の原型を10バールの圧力でプレスし、シートと型の間の空気を抜き、120℃で加熱します。40~60分程度の加硫工程の間にシリコンシートが液化して3Dプリント製の原型通りに細部まで形状化され、熱によってエラストマーの分子鎖が結合することで加硫処理された型が出来上がります。
冷却後、型を開き3Dプリント製の原型をキャビティから取り出すと、SiOCAST成形機で使用する型の完成です。3Dプリント製の原型は、そのまま別の加硫工程で再利用することができます。
特殊な離型剤を使用しているので、加硫後に3Dプリント製の原型がシリコンに固着することもなく、次の型の製作時に再利用することができます。Formlabsのプリンタで3Dプリントした原型は、大体3~4回、またはそれ以上の加硫工程に耐えることができます。
Siocast CEO兼共同創業者 Ferran Navarro氏
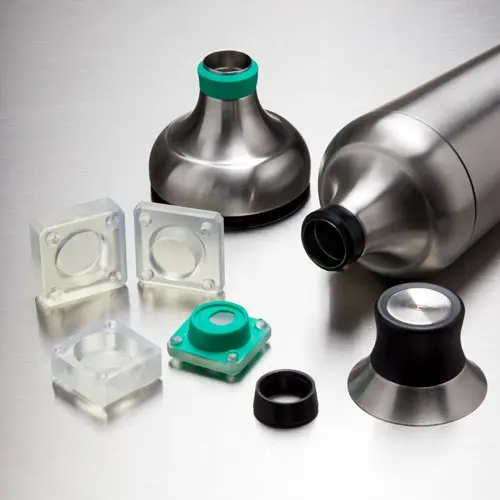
プロダクトデザインのためのシリコン成形
本技術資料では、OXO、Tinta Crayons、Dame Productsのオーバーモールドやインサート成形等、プロダクトデザインや製品製造に使われるシリコン成形の3つの事例をご紹介しています。
4. SiOform1でミニチュア製造
加硫処理したゴム型の上型と下形を重ねた状態でSiOform1の中に入れ、射出条件を設定します。射出開始のボタンを押すと機械が動き出し、ゴム型から空気が抜かれ、240℃で液化した熱可塑性レジンが射出されます。
型が冷めたら、成形機から取り出すことができます。この工程にかかる時間はわずか30秒程度(厚みのある型なら1分程度)で、完了後はすぐに次の型を投入することができます。
成形機から取り出して数秒間冷却したら、ミニチュアを型から取り出してスプルーを切り取ることができます。SiOCASTの熱可塑性レジンと自社開発のシリコンゴムの組み合わせにより、ミニチュアの取り外しも簡単です。
ミニチュアの大きさや量にもよりますが、1回の成形で平均4~64点のミニチュアを作ることができます。最大成形数は1回あたり100点までで、成形工程全体にかかる時間は従来のレジン鋳造より10〜20倍も速くなっています。
1つの型を冷却している間は別の型を使い、冷めたら再度成形機に入れて使用することができます。通常は3~9種類の型をローテーションさせていて、1時間に25~40点の成形が可能です。この工程が自動化されていれば、射出成形を1時間あたり最大60~80回行うことができ、1時間あたりに製作できるミニチュアの数は100~1000点に増えます。
Siocast CEO兼共同創業者 Ferran Navarro氏
シリコン型の大きさは210 x 270mmで、厚さは最大50mmまで変更でき、実製品の厚さ40mmにも対応できます。型は約300~500回の成形に耐えることができるため、短期生産にも連続生産にも適用できます。
SiOCASTの顧客は、readyCASTサービスを使用してシリコン型を同社から直接購入するか、型を内製するかを選ぶことになりますが、一般的に後者の方が人気があります。SiOCASTは、初心者の方でも安心の完全トレーニングパッケージを提供しています。
業界に革新を起こすシステム
3Dプリンタでミニチュアを直接3Dプリントするというのは、どちらからというとホビイスト向けの1回限りの生産や少量だけ生産する場合に向いている方法ですが、SiOCASTはこの方法でプロのミニチュア製作の基準も打ち立てました。
製品を受け取った消費者からは、レジン鋳造、金属製のミニチュア、射出成型品のどれからも得られない、耐久性が高く繊細なディテールまで表現されていながら塗装が簡単なミニチュアが実現できたという声が届いています。
SiOCASTの成形機を導入している企業には、Monster Fight Club(The Witcher, Cyberpunk RED)、Warlord Games(Blood Red Skies, Bolt Action)、Reaper Miniatures(Bones USA)、Titan Forge Miniatures、Corvus Belli(Infinity the Universe)、Yedharo Models、Creature Casterなどがあります。
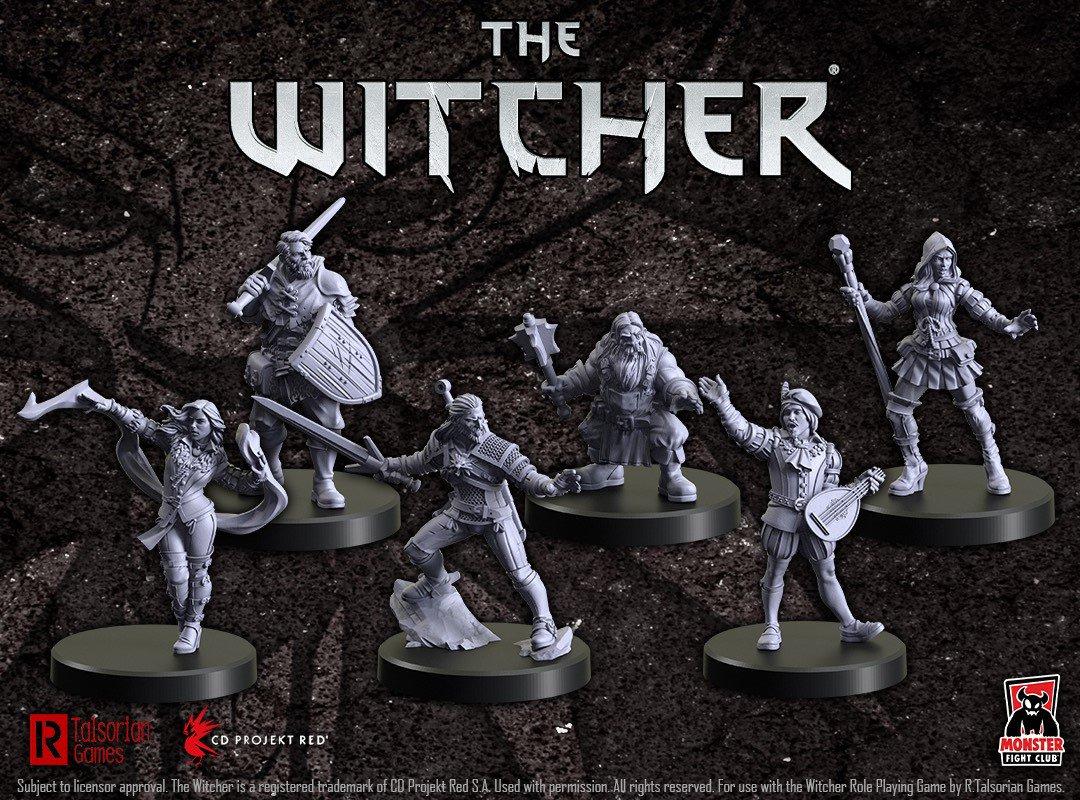
Monter Fight Clubが製作したThe Witcherのミニチュア。
SiOCASTは、ミニチュア市場だけでなく、アニメや漫画業界においても高い評価を得ています。
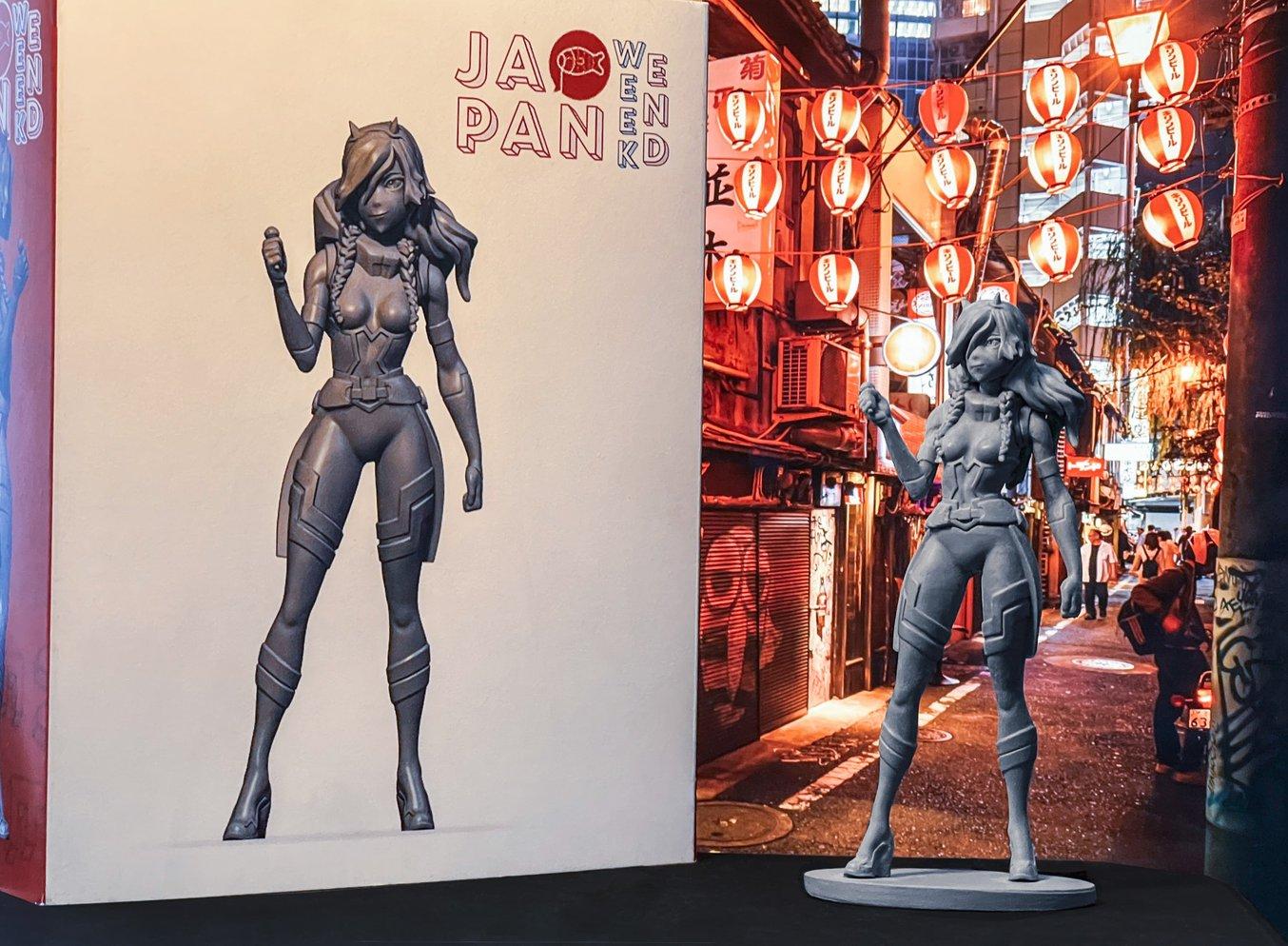
SiOCASTで製作したJapan Weekendのミニチュア。
SiOCASTは現在、ジオラマ市場にも事業を拡大しており、すでに主要なジオラマメーカーとの提携も始まっています。
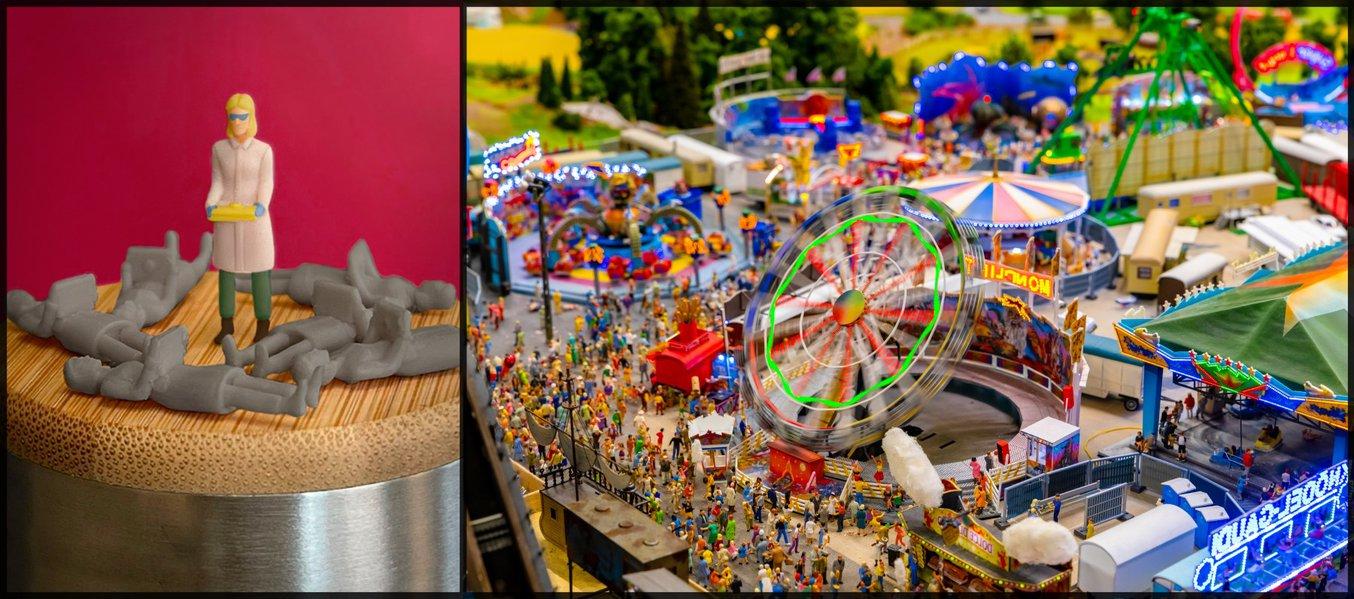
Miniatur Wunderlandが製作したジオラマ。
Galladoria Gamesのようなロールプレイングゲームのメーカーも、SiOCASTで得られるメリットを地形模型やジオラマ市場に広げている一社です。ミニチュア市場以外でSiOCASTに移行する企業の数は日々増え続けています。
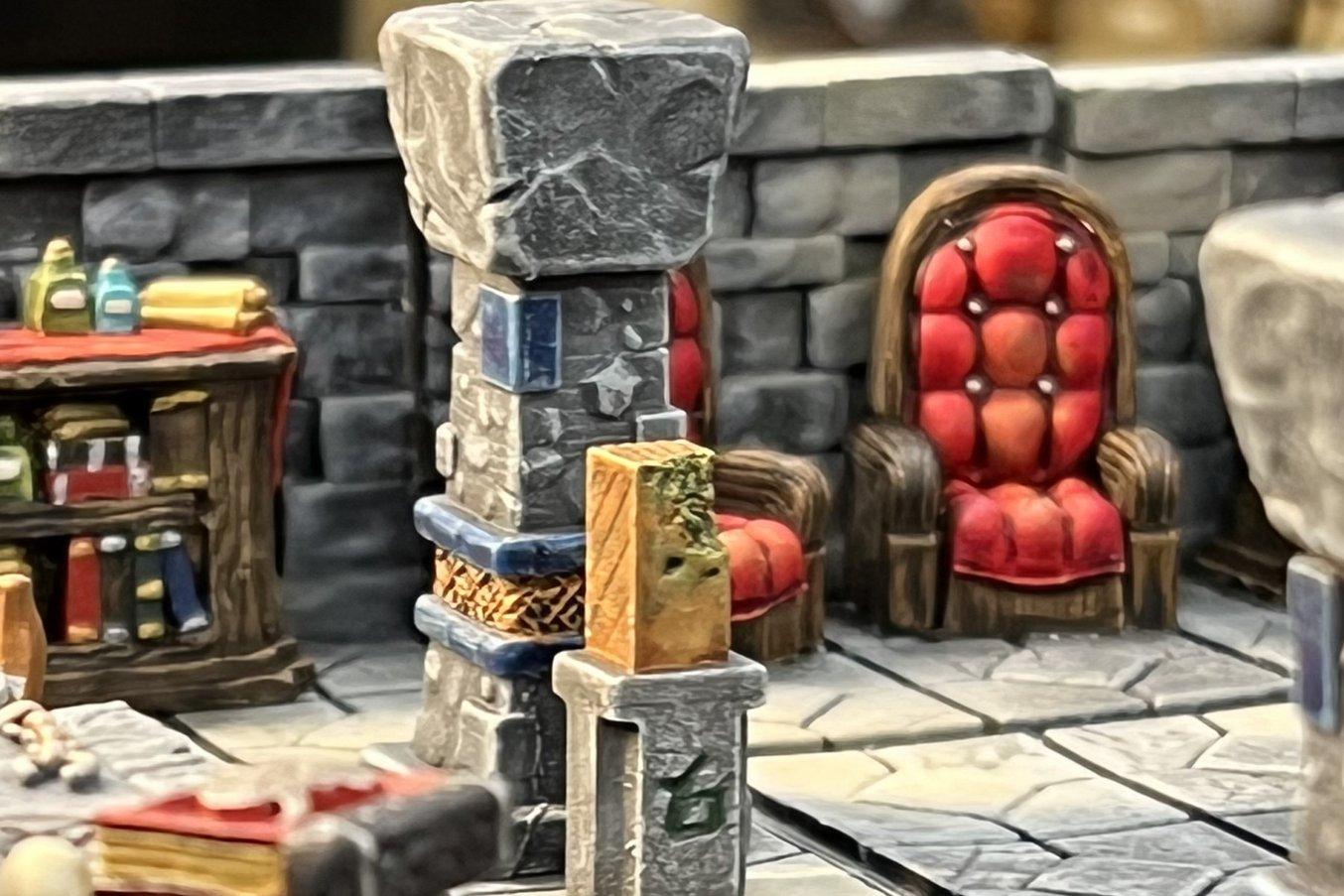
Galladoriaが製作したD&D地形。
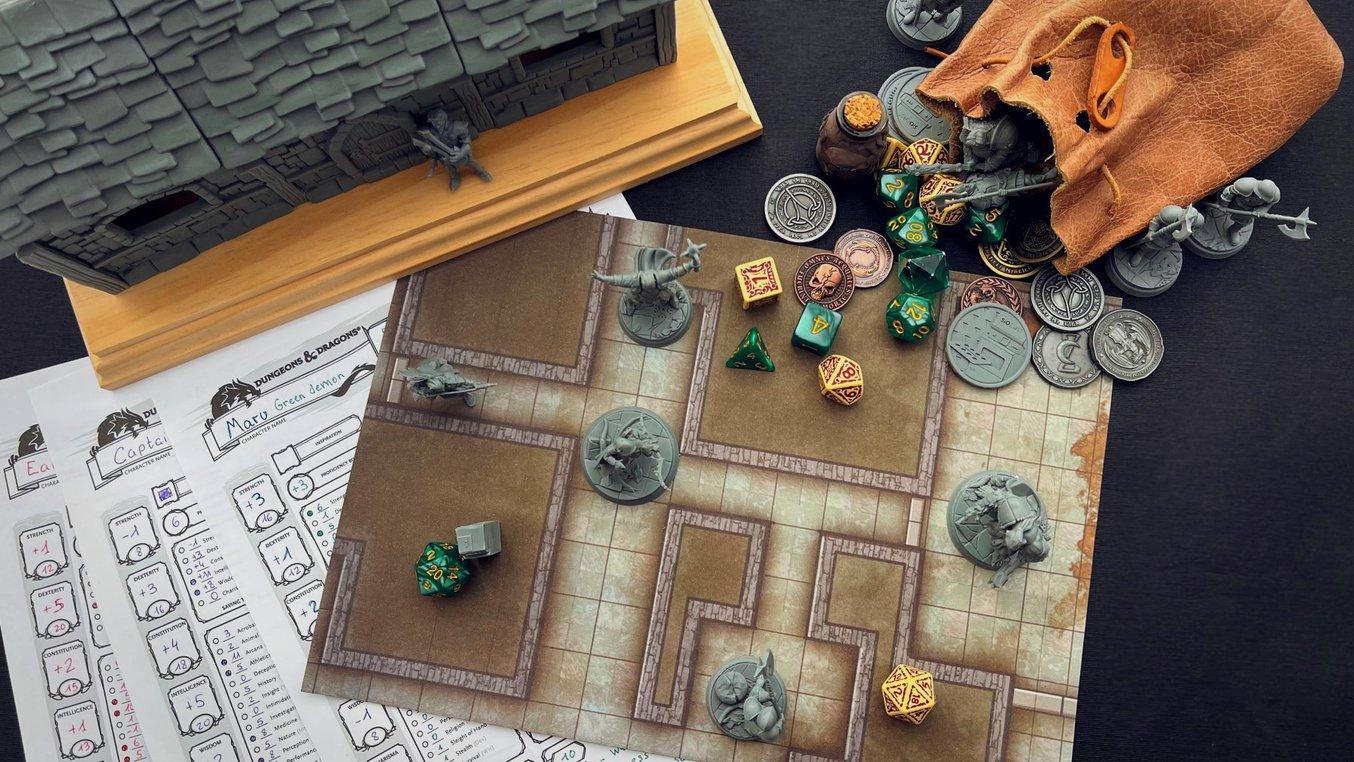
SiOCASTで製作したDungeons & Dungeonsの部品。
ローカル生産
SiOCASTが新しい生産技術を打ち立てたことで、業界の歯車が大きく動き始めました。Ferran氏は、従来の方法でプラスチック品の生産を100%内製化できるミニチュアメーカーは、世界でも数社しかないと言います。ほとんどの企業は製造を中国に依存しており、物流コストが高く製作期間も長くなるうえ、最低発注数量(MOQ)も多くなりがちです。しかしSiOCASTの成形機を導入すれば、企業の規模に関わらず生産を内製化することができます。
例えば、Reaper MiniatureのBones USAコレクションはSiOCASTと提携して金属製ミニチュアから熱可塑性ミニチュアに移行しただけでなく、製造拠点を中国からアメリカに移すことにも成功しました。
環境に優しい、廃棄物ゼロの製造を
SiOCASTは、自社開発のプラスチックSiOresに有毒性がなくEN-71 Toy Safe認証を取得していること、そして環境に優しい製造システムを実現できたことを誇りにしています。ミニチュア用の成形型は再利用可能なため、失敗品やランナーは粉砕して新しい材料と混ぜ合わせることができ、廃棄物ゼロのプラスチック製品生産システムを実現しています。
ローカル生産を実現し需要にも柔軟に対応できるシステムを導入することで、在庫を抱える必要がなく、売れ残りによる無駄も発生しません。また、ミニチュア製造に必要な機械自体がコンパクトなため設置面積も小さく済みます。
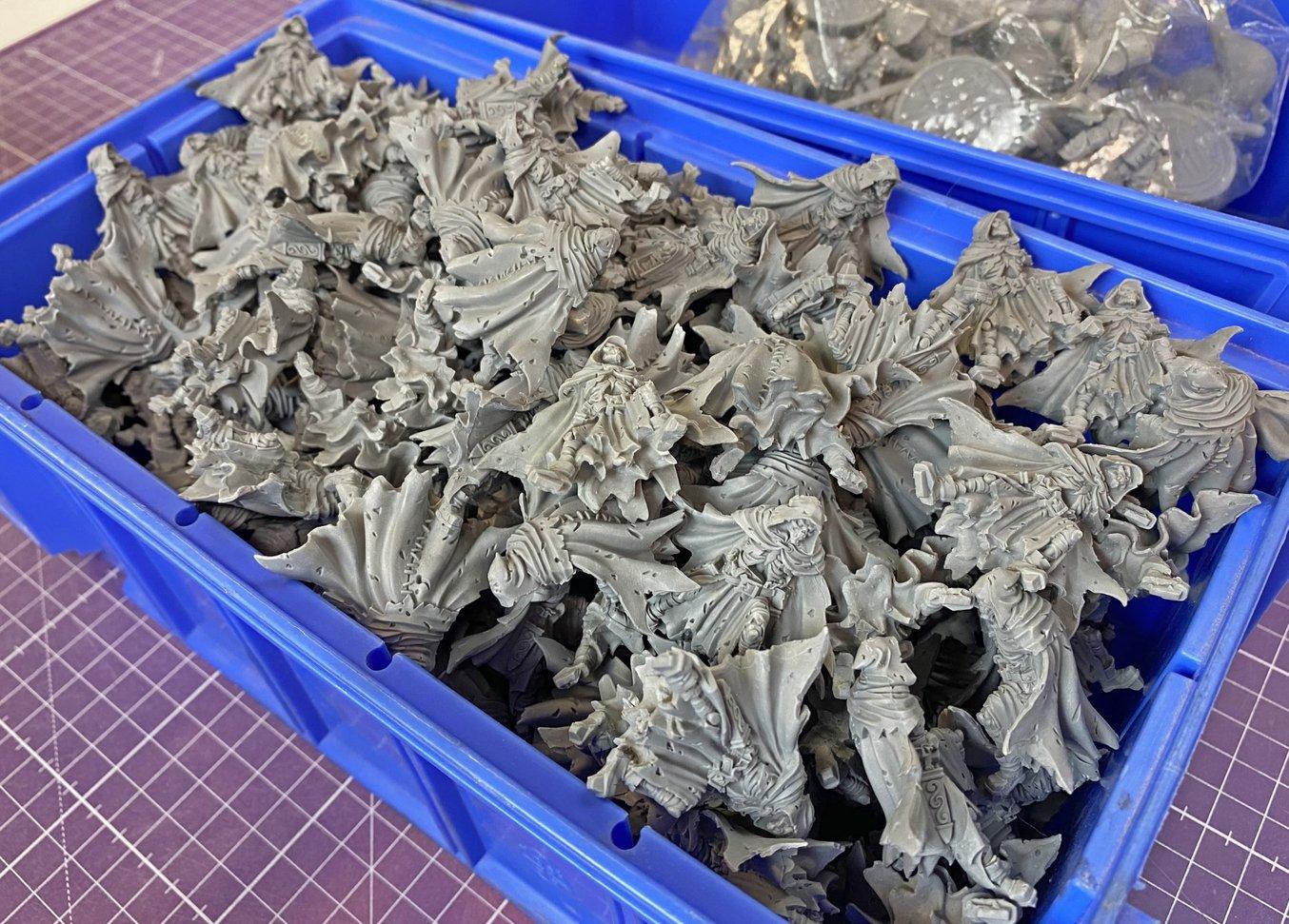
ローカルで生産されているBroken Anvil Miniatureの高品質ミニチュア。
「このシステムがあれば10平方メートルほどの小さな部屋で内製による大量生産が可能です。手動の射出成形機は非常に優れているのですが、サイズや生産量の観点では制約が多く、同じことは実現できません」とFerran氏は言います。
「また、射出成形で作るスプルーが大量の廃棄物になります。プラスチックの約20%はゴミ箱行きなのです。ミニチュアは海外で製造するのが一般的なので、完成品を米国まで輸送しなければなりません。また、最低発注数量の関係で2万個のユニットを製造したとして、半分は売れるかもしれませんが残りの半分は売れ残れば廃棄しなければいけません。射出成形は大量生産の場合には費用対効果も高いのですが、環境に優しくなく、二酸化炭素排出量も多いのです。レジン鋳造では、SiOCASTを使った時の20倍以上のシリコン残渣が発生し、さらに未使用のランナーとして有毒なレジンの30~40%が廃棄されることになります」
精細な高品質ミニチュアを、リーズナブルな価格で
ミニチュアに求めるものは何かと尋ると、消費者の答えの第一位に挙がるのは常に「ディテールの精細さ」です。
しかし、そのような高精細なフィギュアをリーズナブルな価格で製造するというのは、なかなか実現できるものではありません。Ferran氏はその状況を、こう説明してくれます。「どのような用途であっても、金型を低コストで製作できて、シリコンで複製できる精巧なディテールを再現し、それでいて射出成形のような工業クラスの生産性を手に入れたい、というのが製造に関わる人全員の本心でしょう」
SiOCAST成形機の成功事例の1つに、Warlord GamesでBlood Red Skiesの機体を4色展開で40万点以上生産できたことが挙げられます。この規模の大量生産となるとこれまでは射出成形でしか対応できず、再現できるディテールの精巧さはどうしても劣ってしまいます。
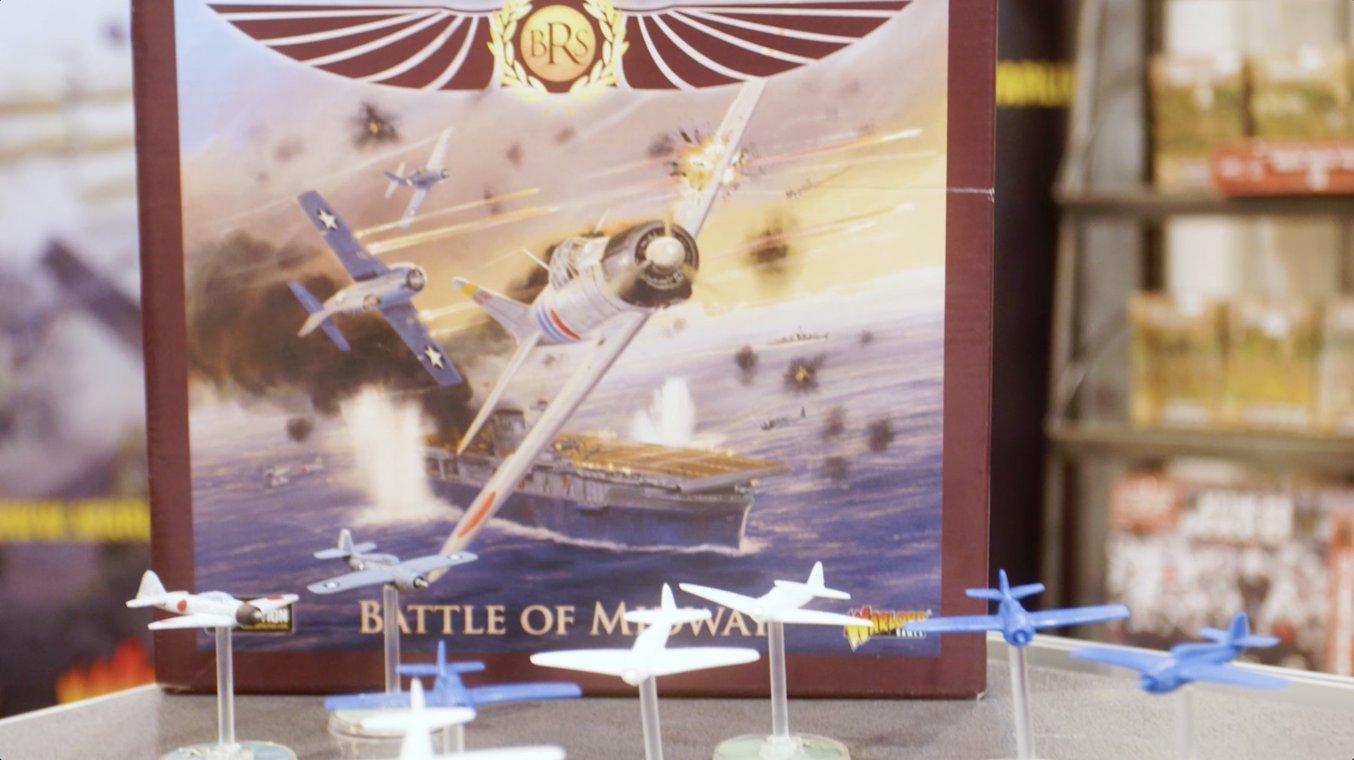
SiOCASTでRed Blook Skiesの飛行機を40万点以上製造。
射出成形では金型製作に5~1万ユーロ程度かかるため、収益をプラスにするには機体ごとに1万~1万5千点程度販売しなければなりません。もちろん、射出成形では非常に低価格でプラスチック製品の生産が可能ですが、製作期間の長さや対応可否、再現できるディテールの精細さを考慮する必要があります。射出成形を使って業界最高品質のミニチュアを提供しているメーカーでも、シリコンで得られるようなディテールは再現できておらず、その差は歴然です。
Siocast CEO兼共同創業者 Ferran Navarro氏
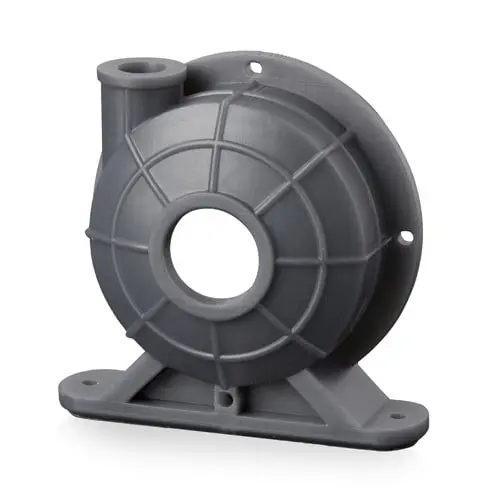
新しい用途への拡大
SiOCASTの成形機は他の業界からも好評で、フットウェアやキーキャップ、医療用コネクタ、オーバーモールド成形品、その他さまざまな種類の軟質部品や耐久性の高い部品の生産に活用されています。例えば、顧客の1社は、Fuse 1とForm 3+で3Dプリントした原型を使ってフライトシミュレーターのトリムスイッチとトリムダイヤルを製作しました。この企業は、SiOCASTの成形機を導入したことで、表面品質が優れた実部品を低コストかつ短期間でローカル生産することができました。このような要件を満たせる技術は、まだ他にありません。
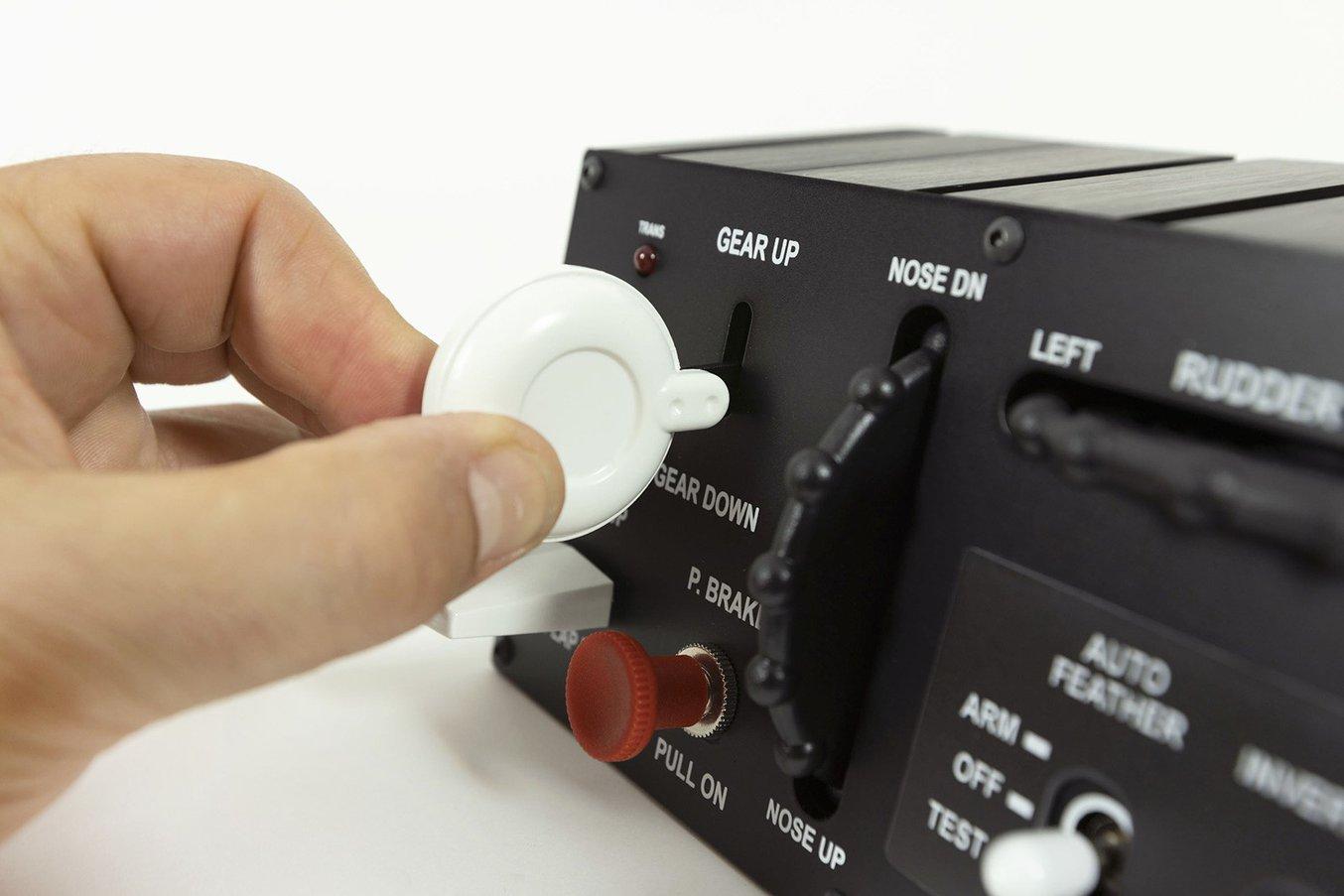
SiOCASTで製作したAplica Designのフライトシミュレーター用部品。
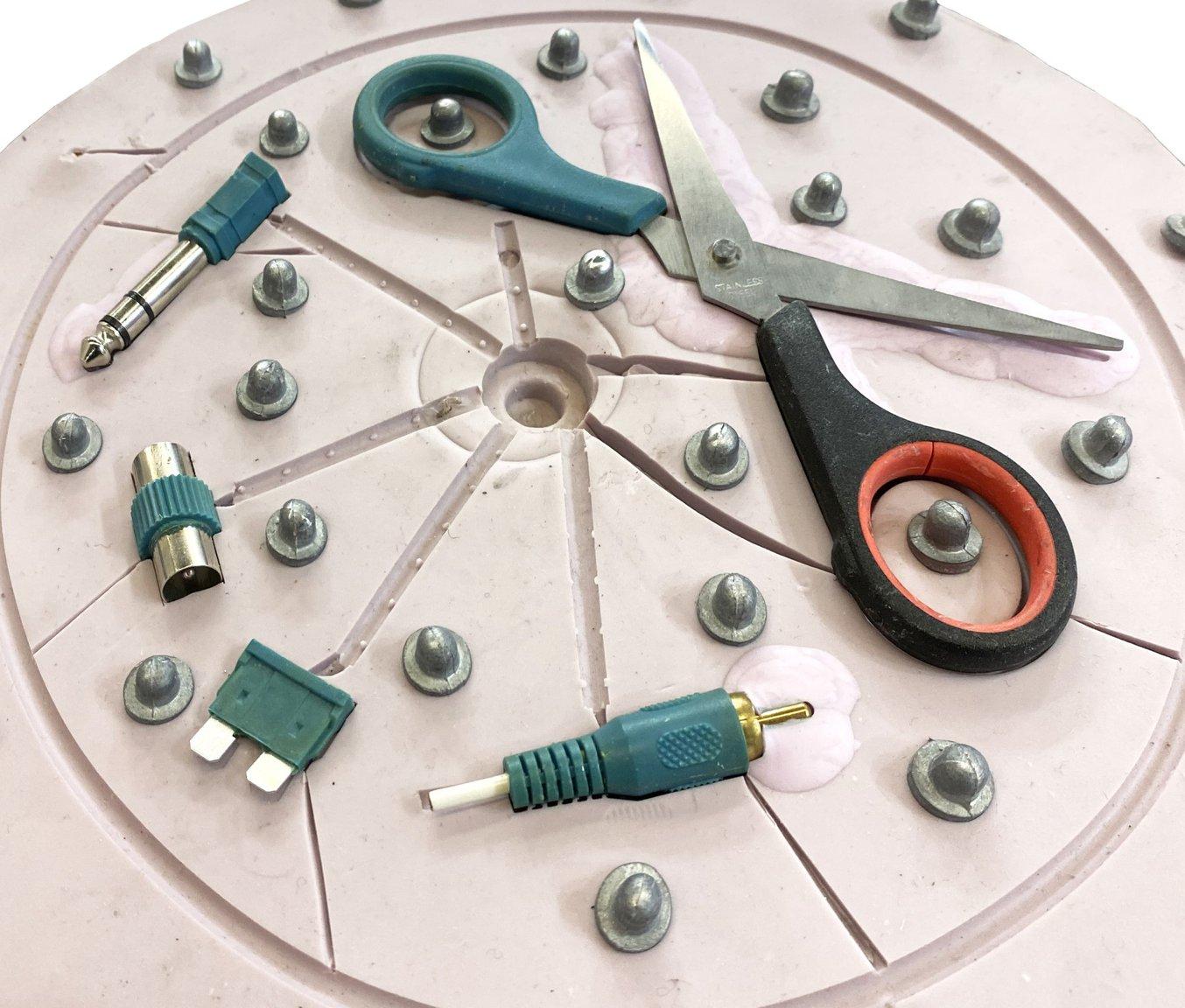
SiOCASTで作った型を使ってオーバーモールド。
「弊社がミニチュア事業から始めたのは、私たちが最も精通している分野だったからです。それが今では、新たな用途が何千と目の前に広がっています」と、Ferran氏は未来を見据えます。