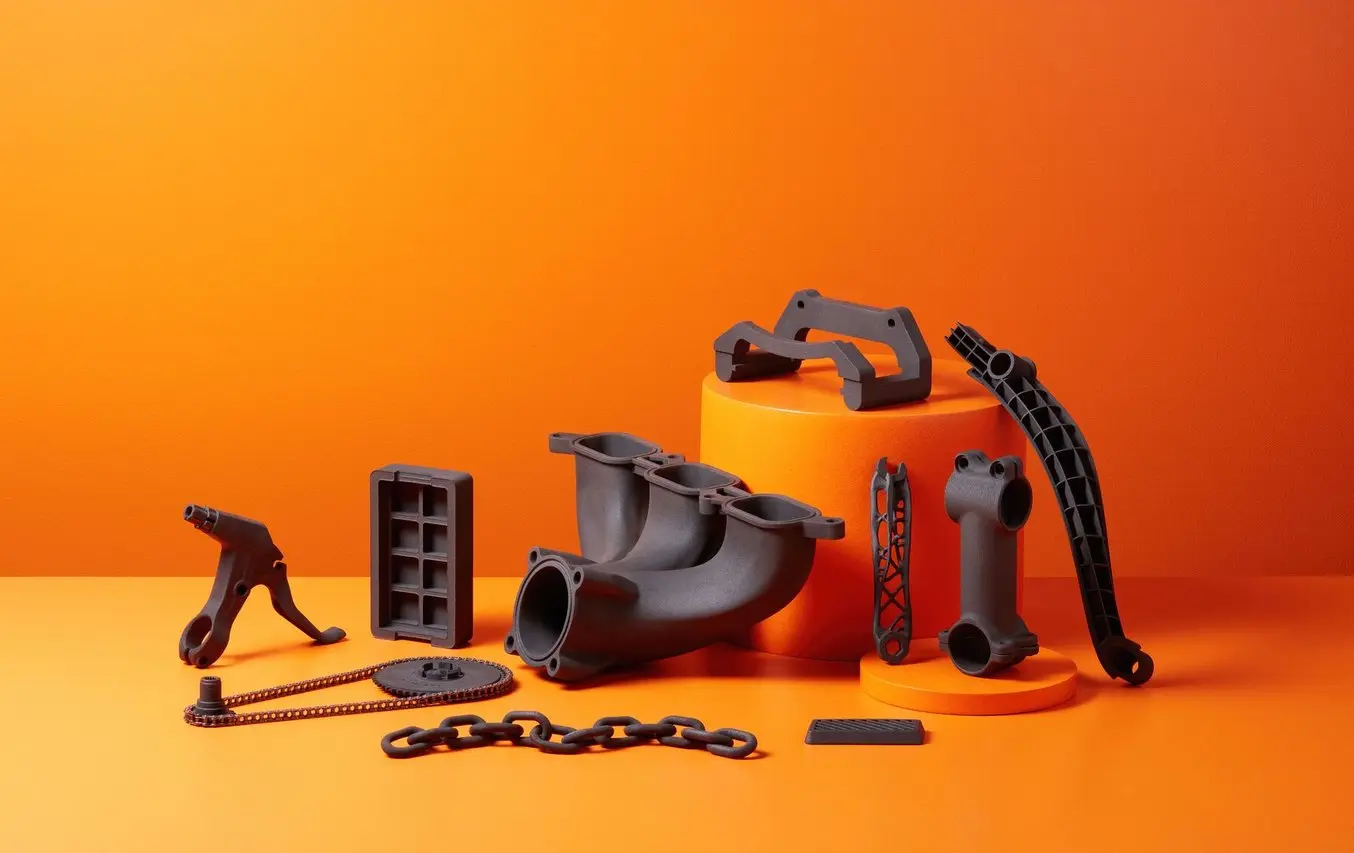
Formlabs の材料ライブラリに新たに加わった初の炭素繊維強化材料、Nylon 11 CFパウダーは、SLS方式3DプリンタFuse 1+ 30Wで使用できます。Nylon 11 CFパウダーの登場により、メーカーの皆さまは、従来のオーバーレイや切削加工を行うことなく高強度で軽量な高耐熱部品を製造することが可能になりました。
高い荷重たわみ温度、引張弾性率、剛性を持ち合わせたNylon 11 CFパウダーの代表的な用途は以下のようなものです。
- 航空宇宙製品のケーシング、治具、 固定具
- 自動車部品の製造あるいは試作、試験用治具
- 電気駆動のモビリティ製品車両のケーシング
- 補修/交換部品または復刻部品の製造
炭素繊維強化部品は、軽量でありながら高い強度と耐熱性、剛性を要する用途で幅広く使用されます。既に広く採用されている炭素繊維強化部品ですが、3Dプリントでの使用事例はまだ少なく、FormlabsのFuseシリーズプリンタのように低コストで導入・運用でき、尚且つ誰もが簡単に扱える3Dプリンタは初めてで、今後更なる普及が期待されています。
炭素繊維とは?
炭素繊維は、通常ポリアクリロニトリルまたは木材の副産物等を原料に、極高温で原料から非炭素成分を「焼き払う」形で製造されています。こうして作られた繊維は、ほぼ完全な炭素結晶の織物構造を有した炭素繊維として製品化されます。これらはレジンを加えてプリプレグとなるシートに加工されたり、布に織り込まれたり、あるいは3Dプリンタで粉末材料に充填されて焼結されることで部品へと加工されます。
炭素繊維強化樹脂などの複合材料は、鉄(スチール)、木材、アルミニウムから作られた加工部品よりも、多くの優れた性能を有しています。炭素繊維はベースとなる材料に強度を付加するものですが、重量はほぼ増加しません。こうした複合材料は、軽量でありながらも鉄や木材よりもはるかに高い強度を持つことが多々あり、自動車のダクトやマニフォールド、エンジンの空気循環システム、航空宇宙のケーシング、スポーツ用品、造船業界などで広く活用されています。電気自動車、風力タービン等のサステナブルな分野でも、炭素繊維部品の高強度で軽量な特性は航続距離や効率向上を目的として導入が進んでいます。
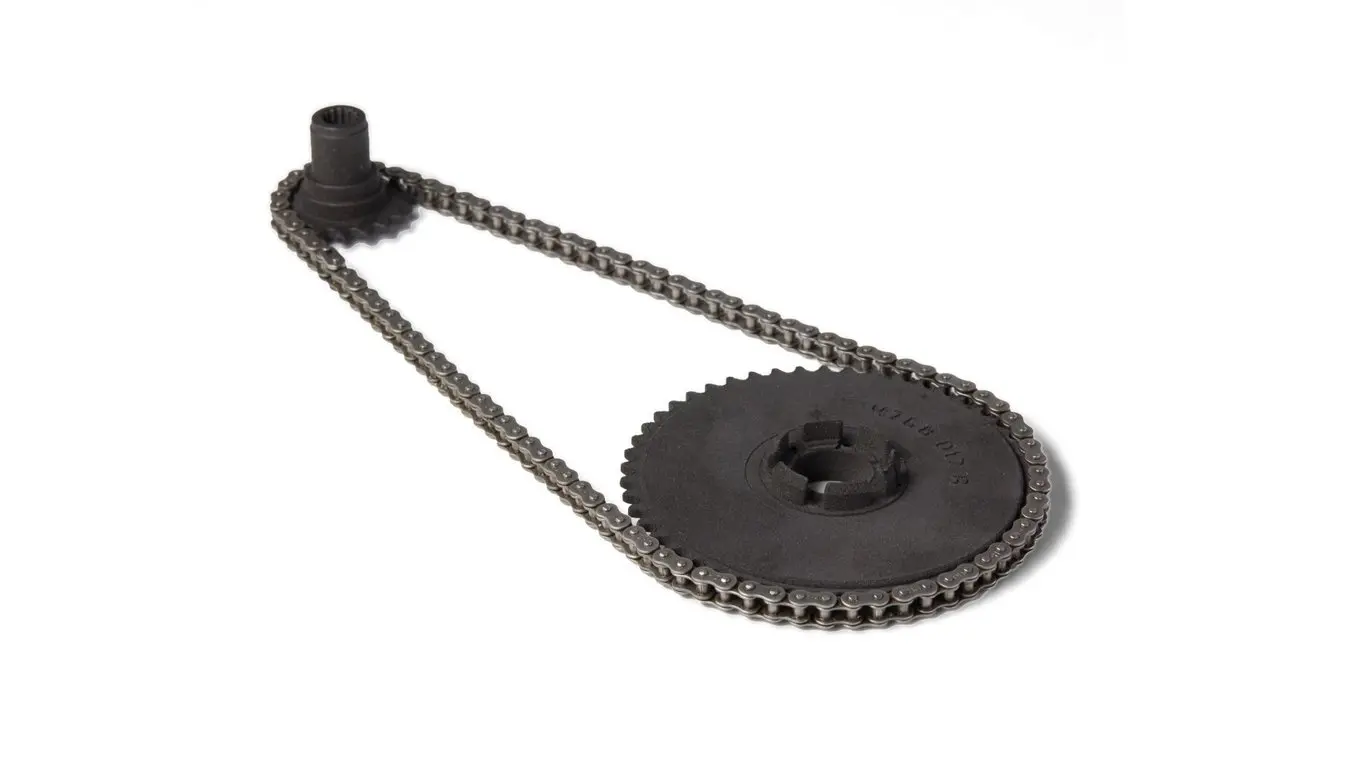
従来の炭素繊維強化部品の製造方法
炭素繊維部品製造の最もよく知られた方法は、ハンドレイアップ、プリプレグでのラミネート、あるいはレジントランスファーモールディング(RTM)等です。これらの方法にはすべて金型が必要で、非常に多くの手作業を要します。
実は金型そのものは低コストで3Dプリントすることができます。そのため中小規模のメーカーは、従来よりも遥かに低コストで炭素繊維製の最終部品を製造できるようになりました。しかし、3Dプリント製金型を用いても、生産できる量、そして形状には限界があります。管の内部や微細な凹凸、そして数十数百単位での成形品を作るのは難しく、多大な時間を要してしまいます。
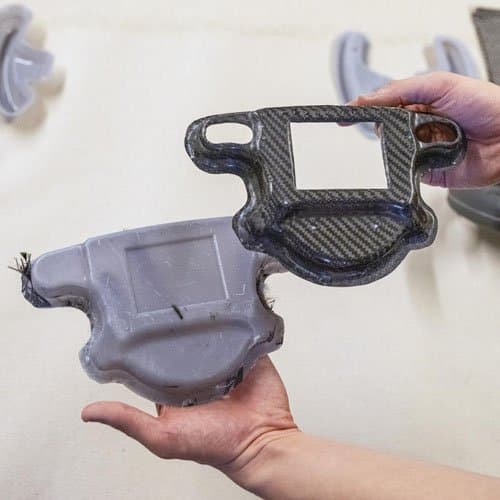
3Dプリント製金型での炭素繊維部品の作り方
本ホワイトペーパーにて炭素繊維などの複合材を成形する金型の設計ガイドラインと、炭素繊維部品を作るためのプリプレグ/ハンドラミネートの作業手順をご覧ください。
Nylon 11CFで炭素繊維強化部品を3Dプリント
近年、粉末状の炭素繊維をナイロン粉末のような一般的なSLS用材料に充填するという複合材料の開発やより高出力なレーザーの実装により、3Dプリントで炭素繊維強化部品が製造できるようになりました。
多くの3Dプリント品同様、3Dプリントでの炭素繊維部品は、従来の炭素繊維部品に完全に取って代わるものではなく、補助的な方法として考えるべきものです。最大引張強さは従来の炭素繊維部品ほど高くはないものの、Nylon 11 CFパウダーでの3Dプリント品はベース材のナイロンよりも強度や剛性が劇的に向上します。3Dプリント製の炭素繊維部品の利点は、Fuse 1+ 30Wプリンタにより、高難度なデザインでも形にできること、そして従来の生産方法よりも大幅に高速かつ多額の人件費を必要としない方法であること、加えて省スペースであることや作業手順が高水準で効率化されていること等が挙げられます。
アディティブマニュファクチャリングは、従来のように金型を使った成形のような形状面の課題とは無縁で、サポート材を必要としないSLS方式のメリットがデザインの自由度をより一層向上します。3Dプリントによる炭素繊維部品製造の導入を検討する際に障害となるのは、炭素繊維強化材料に対応する3Dプリンタの価格が高額であることです。
Formlabsの高速SLSプリンタ、Fuse 1+ 30Wは導入・運用共に低コストで優れた機能と信頼性を備え、炭素繊維強化材料での高精度なプリントを実現したことで、その障害を克服しました。他の多くの工業用3Dプリンタと違い、Fuse 1+ 30Wは1,000万円未満という他社製品の数分の一のコストとプリント時間で炭素繊維部品の生産が可能です。また、Nylon 11 CFパウダーはFuse 1+ 30Wでのみ使用することができ、そのFuseシリーズ最新モデルのプリンタでその信頼性と一貫性が実証されています。
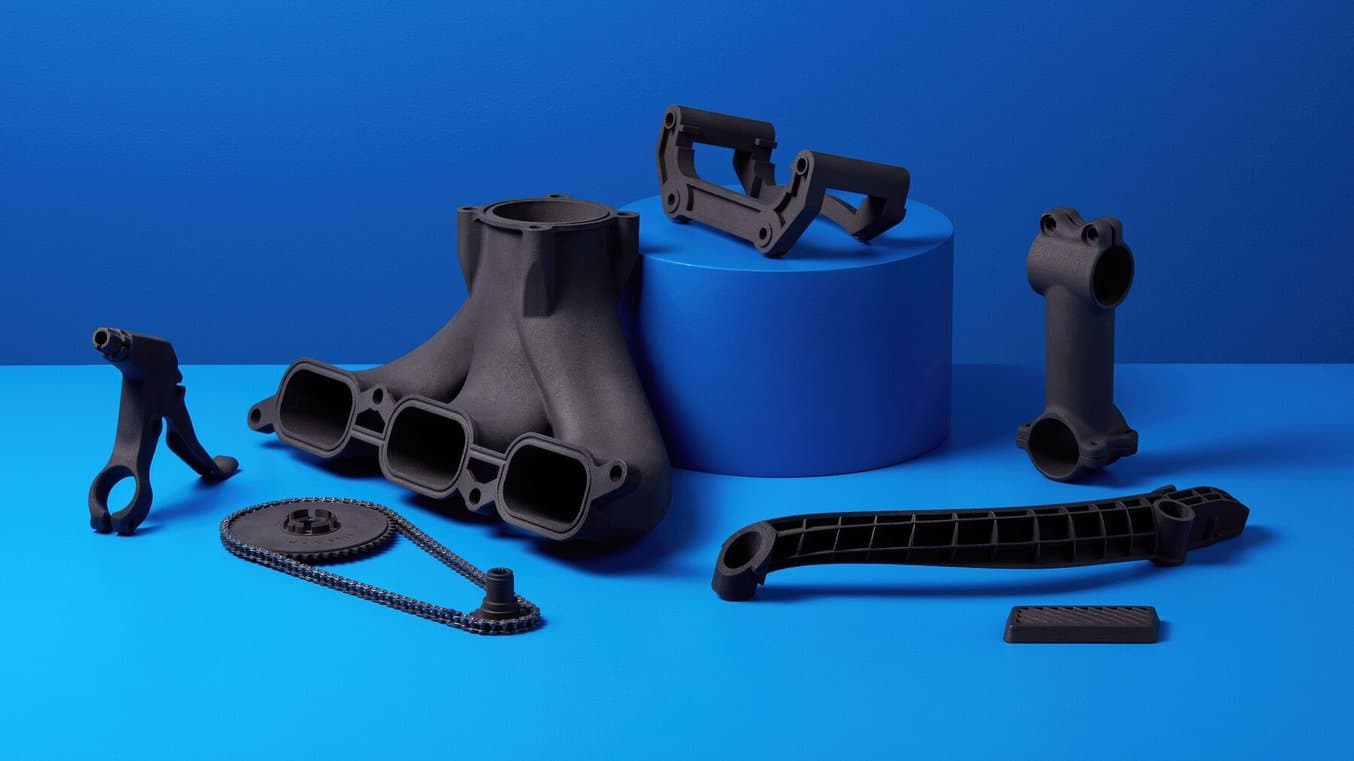
高強度かつ軽量の部品製造に最適な材料
Nylon 11 CFパウダーは金属製の交換部品や補修部品、あるいは復刻部品を内製で製造する際に、ファーストチョイスとなるべき材料と言えます。工場設備に故障が発生した時、設備メーカーや交換部品メーカーから調達するのでは、ダウンタイムによる損失で数千万円単位の損失が発生してしまいます。交換部品を3Dプリント品で賄うというアイデアは、多くの企業が長年望んでいたものの、まずはその交換部品に耐え得る材料が待ち望まれていたのです。Nylon 11 CFパウダーはそれに対応できる材料であり、SLSでそれが実現できるということは、1点単位での製造ではなくバッチ生産が可能となることを意味しています。繰り返しの衝撃や高い耐熱性を要する交換部品や金属部品からの置き換え品として、高剛性高強度かつ軽量という特性を存分に活用いただくことができます。
材料 | Nylon 11 CF | Nylon 12 GF | Nylon 12 | Nylon 11 |
---|---|---|---|---|
最大引張強さ(X軸/MPa) | 69 | 38 | 50 | 49 |
最大引張強さ(Y軸/MPa) | 52 | 38 | 50 | 49 |
最大引張強さ(Z軸/MPa) | 38 | 38 | 50 | 49 |
引張弾性率(X軸/MPa) | 6500 | 2800 | 1850 | 1600 |
破断伸び(X軸/%) | 9 | 4 | 11 | 40 |
破断伸び(Y軸/%) | 15 | 4 | 11 | 40 |
破断伸び(Z軸/%) | 5 | 3 | 6 | N/A |
アイゾット衝撃強さ(J/m) | 74 | 36 | 32 | 71 |
荷重たわみ温度@1.8Mpa(℃) | 178 | 113 | 87 | 46 |
荷重たわみ温度@0.45MPa(℃) | 188 | 170 | 171 | 182 |
また、Nylon 11 CFパウダーは高い剛性と耐衝撃性を持ちながら非常に軽量であることから、生産ライン上で使用される各種の治具や固定具、工具の製造にも非常に適しています。金属部品の製造に際して、Nylon 11 CF製の部品にそのまま置き換えることができない場合でも、Nylon 11 CFは変形や破壊を起こすことなく高温の金属部品を掴むツールとして使用することも可能です。
実製品で使用する部品の場合、ドローン等の航空宇宙やモビリティ製品においてはNylon 11 CFパウダーの高い耐熱性と耐衝撃性も同様に利点となります。ドローンや空を飛ぶ乗り物は、雲の上を飛行する際に、太陽や燃料の補給方法によっては高温に晒されます。例えばバッテリー式のドローンは、熱をもったバッテリーから部品を保護するために耐熱ケーシングが必要で、ジェット燃料で飛行する航空機は当然ながらエンジン内の燃焼によって高熱に晒されます。
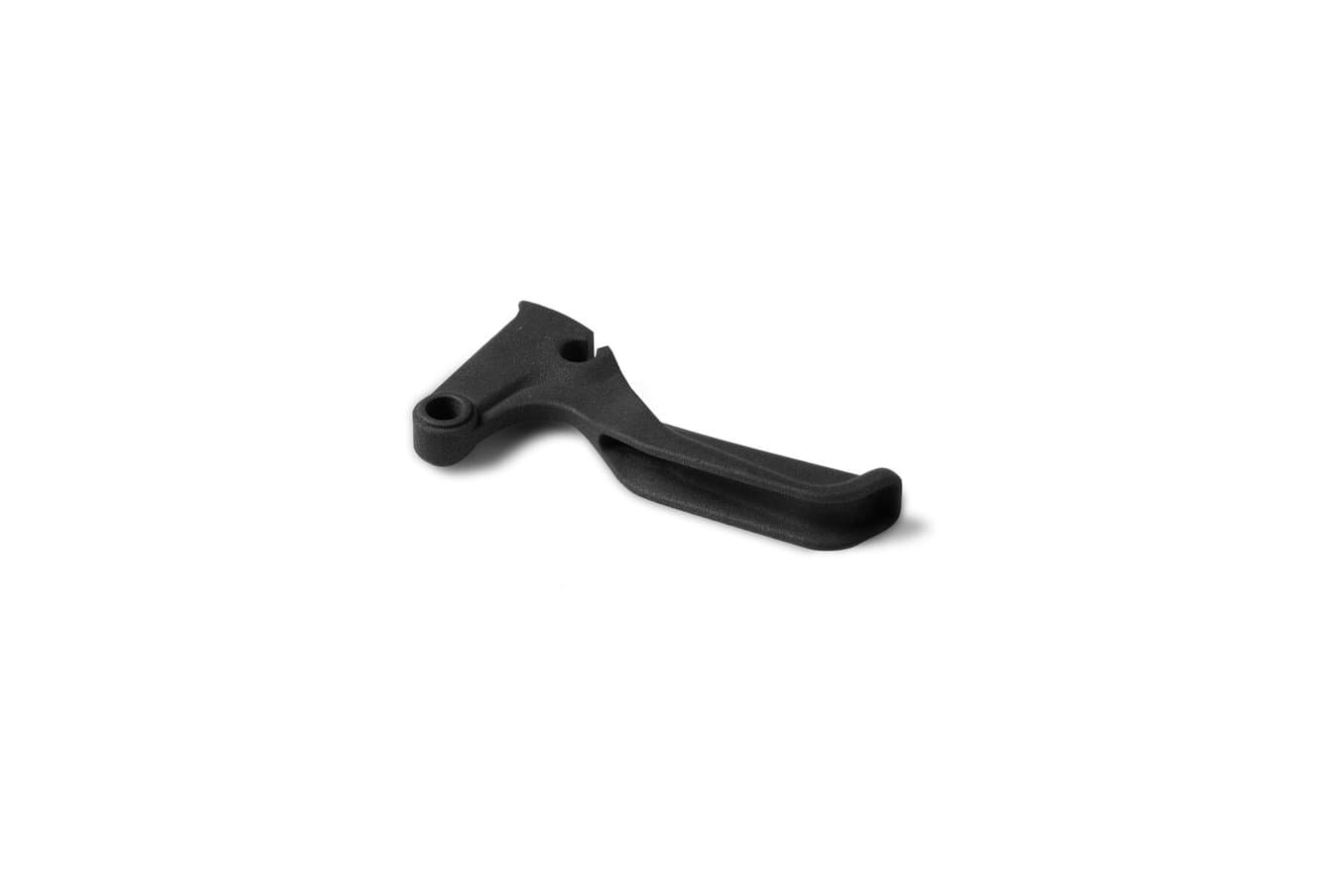
造形品の強度を最大化する造形時の向き
Nylon 11 CFパウダー製品の特徴は炭素繊維に起因する高い引張強さにあるため、プリント時にはモデルの向きを考慮する必要があります。
Fuse 1+ 30Wは、プリント時に内部でリコーターがX軸方向に動いてパウダーを敷き詰めるため、炭素繊維もX軸方向に向けられていきます。その結果、造形品の最大引張強さ(UTS)はX軸方向で最も強化されることになります。(Z軸方向のUTSは38MPa、X軸方向のUTSは69MPa)そのため造形品の強度を最適化するには、造形品が実際の使用箇所で受ける応力の方向をX軸に向けて配置してプリントする必要があります。
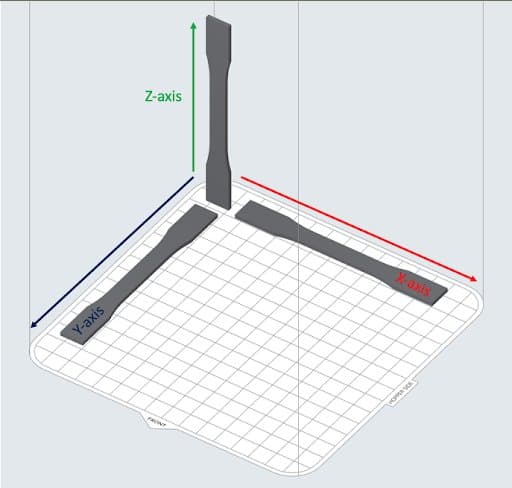
炭素繊維の強度を最大限に引き出すには応力方向をX軸に向ける形で配置する。
プリンタに最適化して開発されるFormlabsの材料
Nylon 11 CFは、同時に発売された高速SLSプリンタFuse 1+ 30Wに最適化して開発され、ユーザーが初めて本材料を使用する際にも簡単に扱えるよう配慮されています。本材料はFormlabs初の炭素繊維強化材料となるものの、既存の複合材料であるRigid 10KレジンやNylon 12 GFパウダーは優れた高機能材料として自動車、航空宇宙、製造など様々な産業で新たな用途を開発してきました。
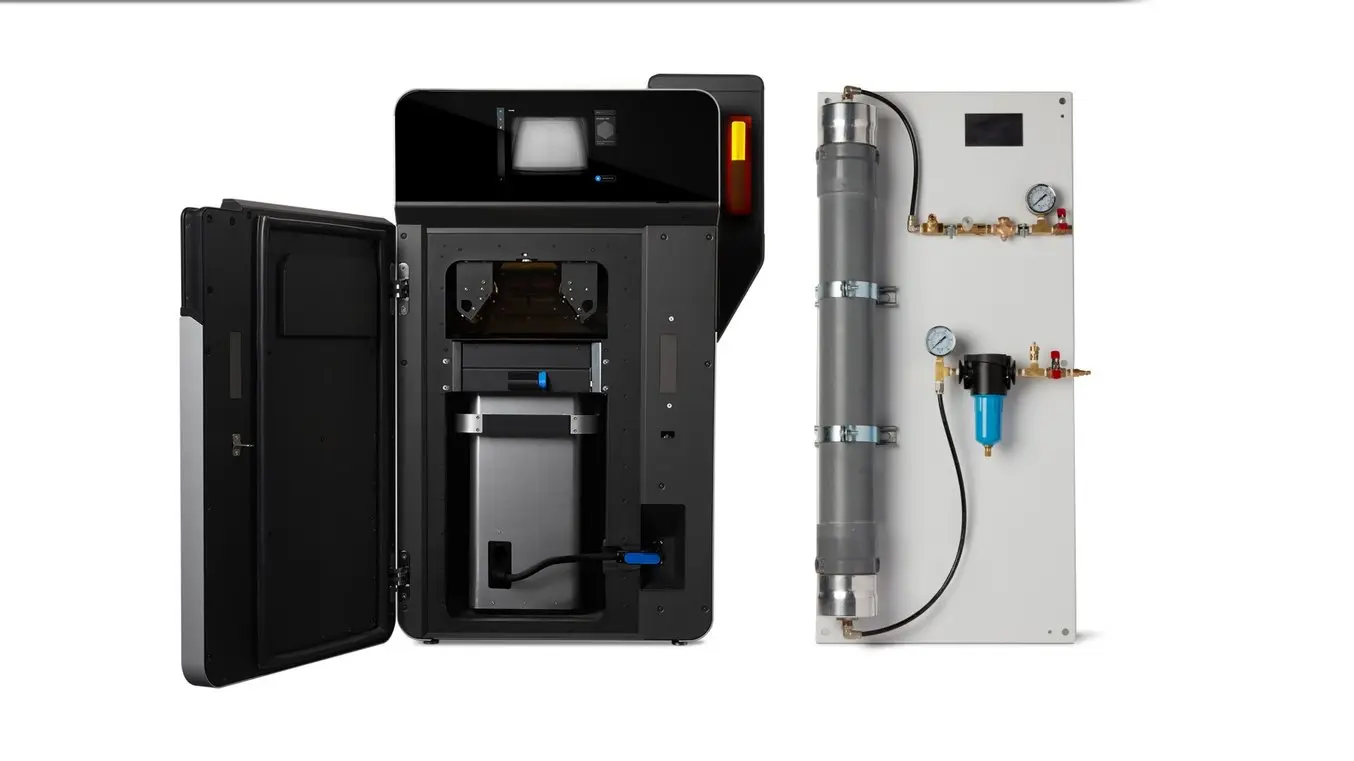
Fuse 1+ 30Wでは窒素ガス発生装置で高効率ワークフローが実現できる。
新製品の高速SLSプリンタ、Fuse 1+ 30Wにはビルドチャンバーを含めたプリンタ庫内に安定した不活性ガス環境を作り出す窒素充填のオプション機能があります。Nylon 11 CFパウダー製の造形品は、不活性ガス環境でプリントすることで材料の酸化による劣化を防止し、造形品周囲に残る未溶融パウダーの品質も維持することで材料リフレッシュ率を低減し、よりコスト効率の高い生産が可能となります。
窒素充填を行うことでNylon 11 CFのリフレッシュ率は30%となりますが、これはパウダー再利用時に混ぜ合わせる未使用の新パウダーの比率を表すもので、再利用時に必要な未使用パウダーが僅か30%に抑えられることを意味します。材料リフレッシュ率を低く抑えつつビルドチャンバー内にモデルを高密度にパッキングすることで、理論上材料ロスを全く出さないゼロウェイスト・プリントにつながります。
また、Nylon 11 CFパウダーは従来品のNylon 11パウダーから2~3時間程度のクリーニング作業で切り替えられるため、導入のハードルも高くありません。他社製の旧来型SLSプリンタでは材料を切り替えたい時は、1日から数日のクリーニング作業を要し、事実上材料の切り替えは非現実的でした。この機能により、Fuse 1+ 30Wは複数の材料に対応できる生産設備を運用しながらも、より収益に直結する業務に集中することができます。
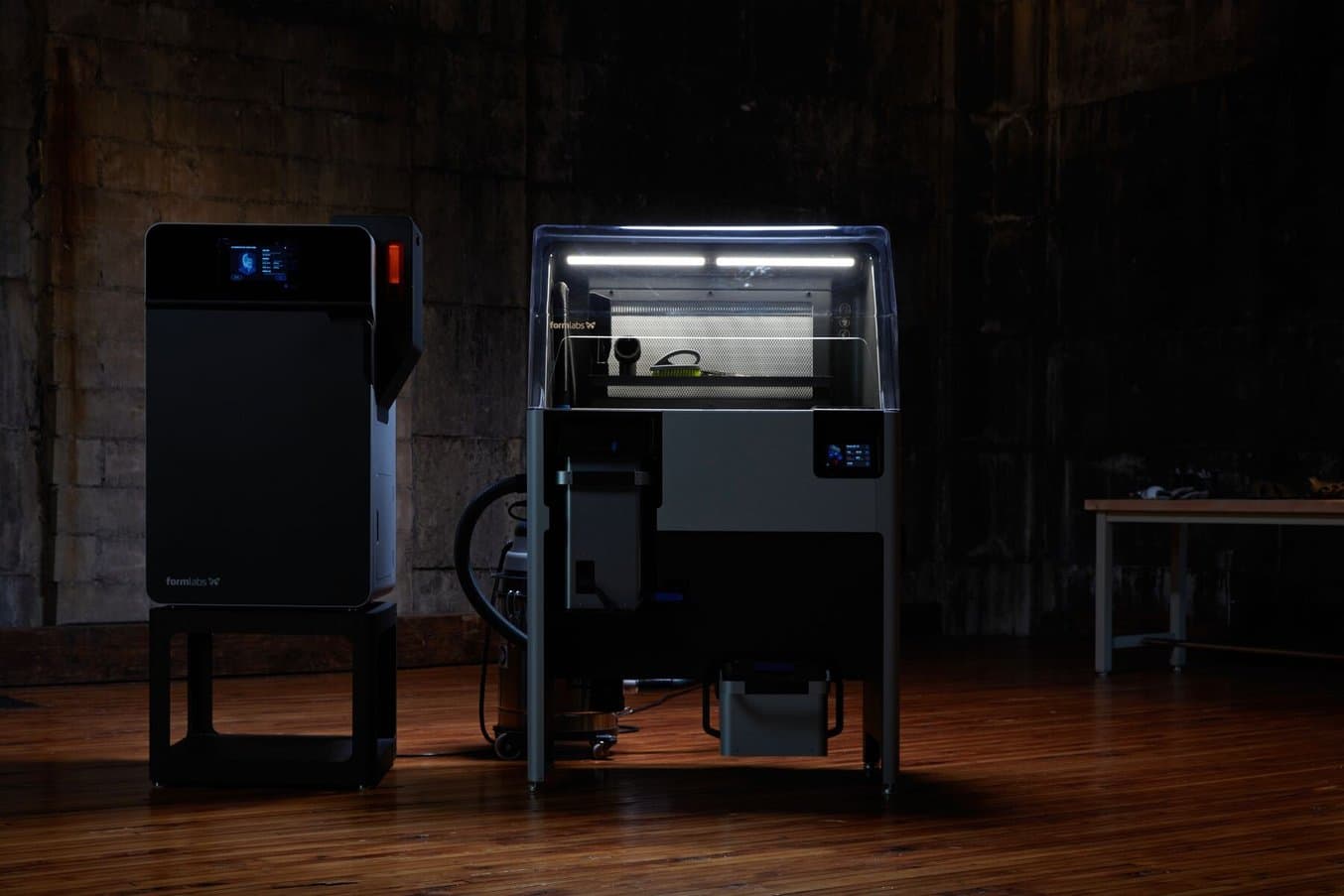
Nylon 11 CF対応の新たなシーブ(ふるい)をFuse Siftに取り付けることで、他のSLS材料を使用する時と同じ後処理ワークフローが行える。
SLSによる内製化を実現する最後のピース
現在多くの製造メーカーは、試作品や実製品用の部品、交換または修理用パーツ、各種の治具等、様々な用途でサプライヤーからSLS製の部品を調達しています。内製化の実現には必要な部品を十分な量で確保し、SLS(多くの場合複数の)プリンタの導入コストを正当化する必要があります。
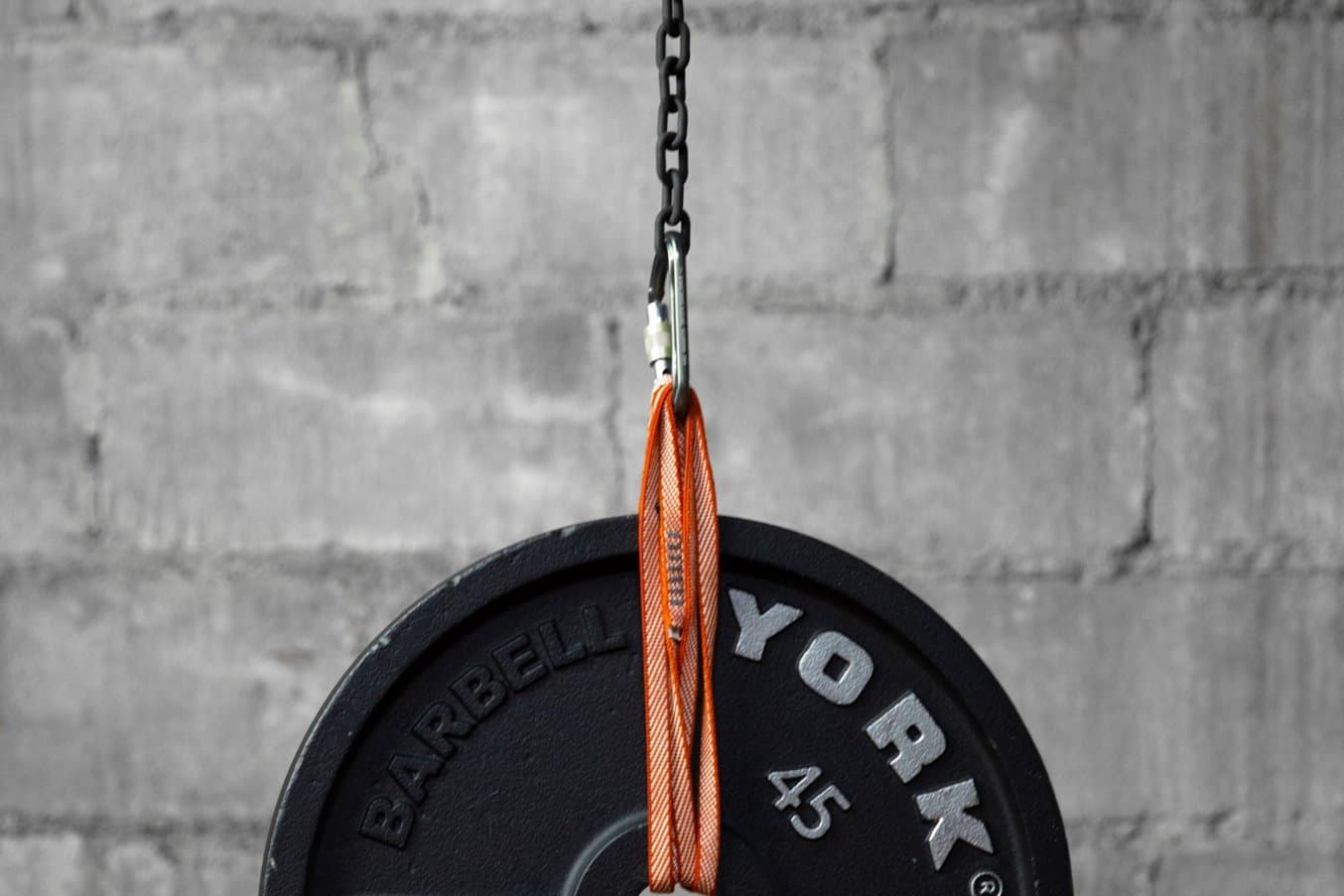
Nylon 11 CFパウダーの発売は、単にFormlabsのSLS用パウダーが拡充されたというだけでなく、新たな用途への可能性を開きました。製造メーカーは、耐熱性、繰り返しの衝撃に対する耐性、高い強度といった特性が求められるSLS造形品が製造する必要があり、この新材料はそれを実現するものです。Fuse 1+ 30Wと新しいNylon 11 CFでのワークフローは、管理やメンテナンス、2台目以降の追加導入も簡単に行え、尚且つ導入・運用も共に低コストを実現しています。