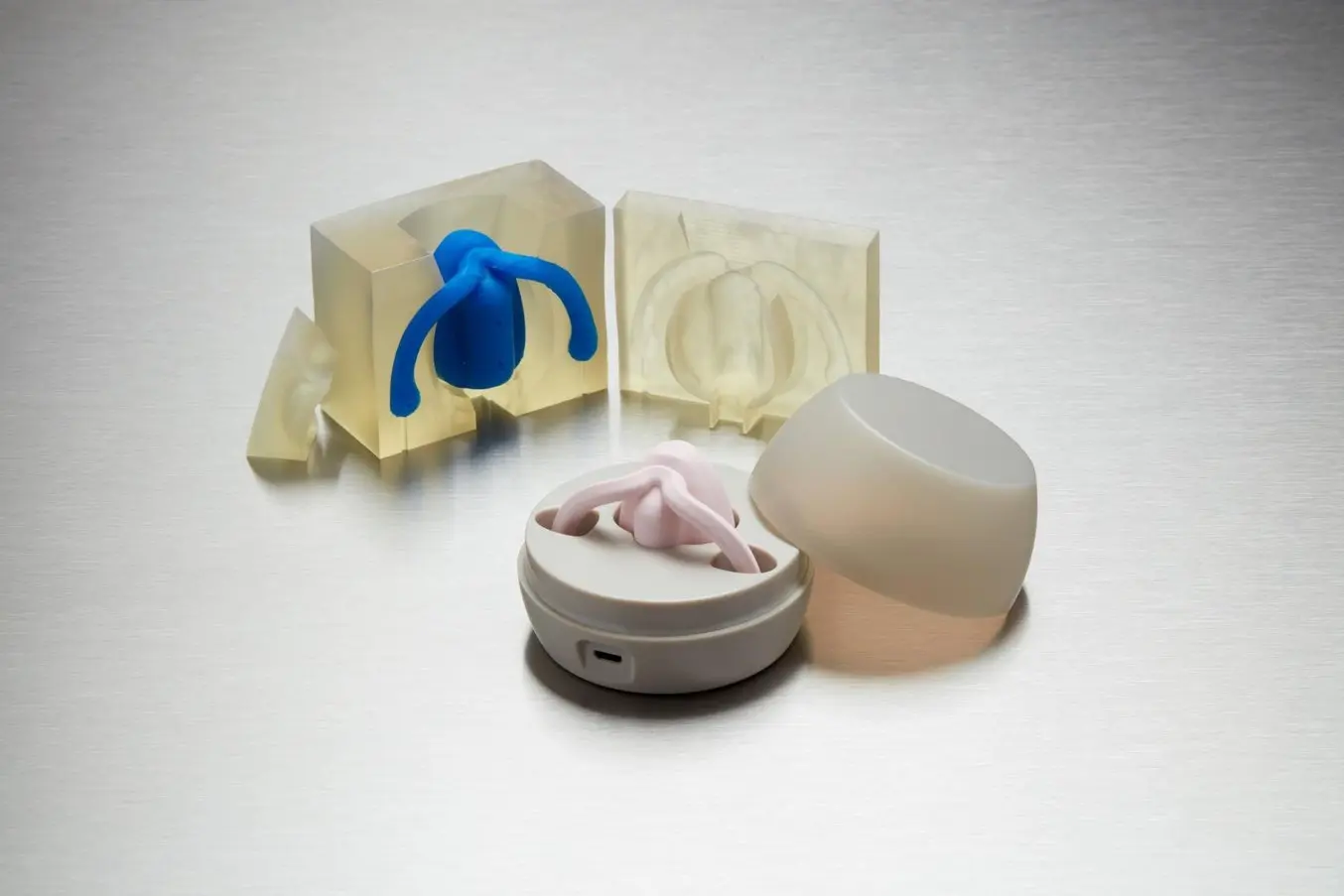
オーバーモールドとインサート成形はしばしば混同されがちです。どちらのプロセスも射出成形の一種で、構造的にも似たパーツを作るため混同されるのも無理はありません。しかしよく知ると、インサート成形とオーバーモールドは実はかなり異なっており、それぞれに独自の利点があることがわかります。
埋め込み型の電子機器から日常的に使う道具のグリップ向上まで、オーバーモールドとインサート成形には多くの利点がありますが、これらの方法の違いを理解してこそ、その利点を最大限に活かすことができます。
この記事の内容:
-
オーバーモールドとインサート成形の基本
-
どの状況でどの製造方法を選ぶべきか
-
オーバーモールドとインサート成形が一般的に使用される用途
-
これらのプロセスを試作品製作に用いる方法
-
3Dプリント製の成形型を使ったインサート成形による試作品の製作方法
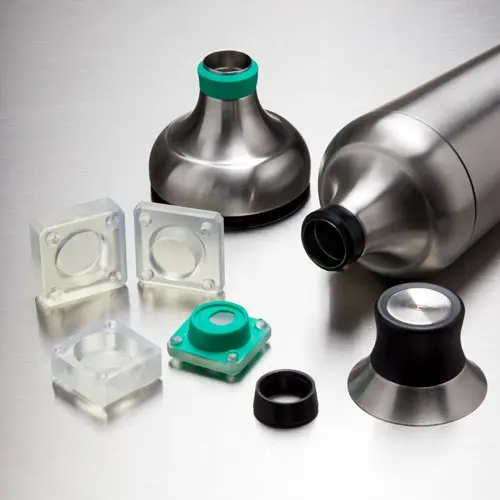
プロダクトデザインのためのシリコン成形
本技術資料では、OXO、Tinta Crayons、Dame Productsのオーバーモールドやインサート成形等、プロダクトデザインや製品製造に使われるシリコン成形の3つの事例をご紹介しています。
オーバーモールドとは?
オーバーモールドは、2つ以上のコンポーネントを互いに重ねるようにして成形する射出成形プロセスの一つです。 2ステップのプロセスを踏むことから、2ショットモールディングと呼ばれることもあります。
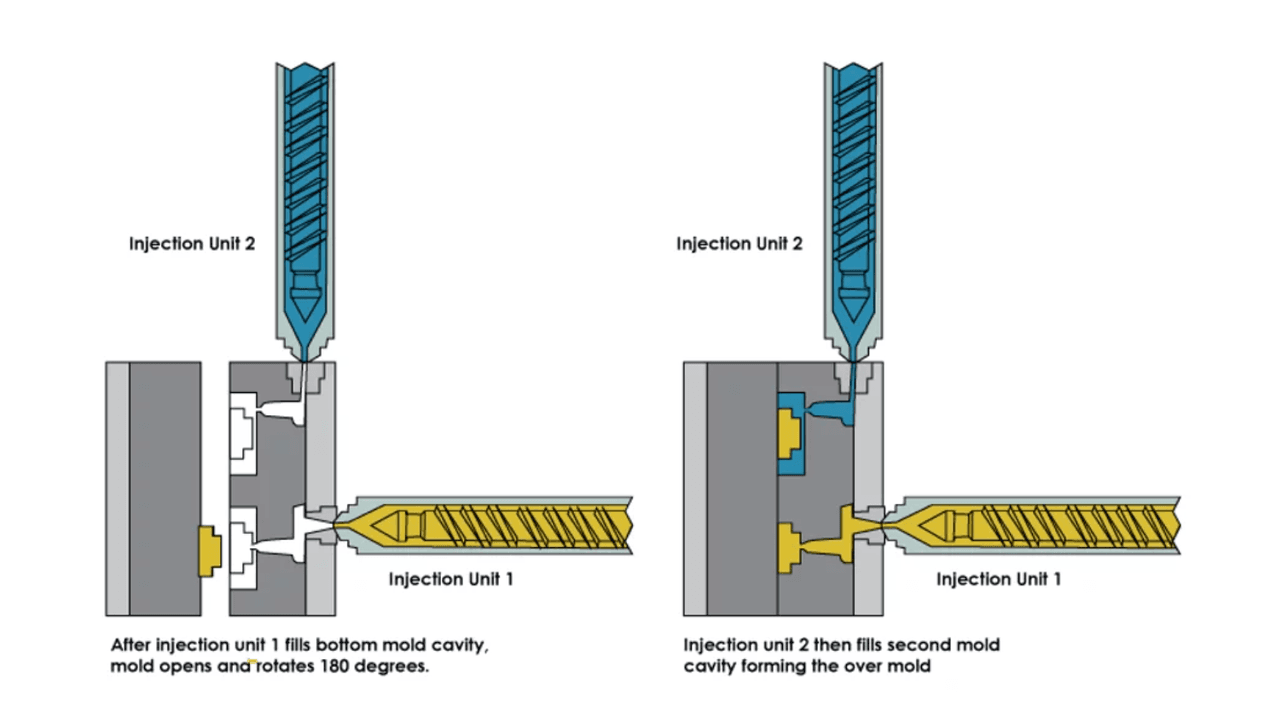
2ステップオーバーモールドのプロセス概略図(出典)
最初のステップでは、ベースとなる材料(基板)を整形して硬化します。オーバーモールドの基板にはプラスチックがよく使われます。そして2つ目の層を1つ目の上に直接成形し、単一の部品を製造します。オーバーモールドは、ゴム製のハンドルがついたプラスチック製品などの製造によく使われます。例えば、歯ブラシを2ショットのオーバーモールドで作る場合、持ち手となるプラスチック製の部分をまず基板として成形し、(歯ブラシを握るときに滑らないように)その上からゴム材を重ねて整形します。
オーバーモールドによく使われる材料
オーバーモールドには以下のように多様な材料が利用できます。
-
アクリロニトリルブタジエンスチレン(ABS)
-
高密度ポリエチレン(HDPE)
-
ポリエーテルエーテルケトン(PEEK)
-
ナイロン(ポリアミド)
-
ポリカーボネート(PC)
-
ポリエチレン(PE)
-
ポリエーテルイミド(PEI)
-
ポリブチレンテレフタレート(PBTR)
-
アクリル(PMMA)
-
ポリオキシメチレン(POM)
-
ポリプロピレン(PP)
-
シリコン(SI)
-
熱可塑性エラストマー(TPE)
-
熱可塑性ポリウレタン(TPU)
-
熱可塑性ゴム(TPR)
オーバーモールドの利点と限界
オーバーモールドには多くの利点があります。複数材料や色を使っての成形が可能で、パーツを全く異なる金型や機械に移さなければならない他の製造方法と比較して作業時間が少なく、それに応じてコストも低くなります。オーバーモールドでは1つのパーツの上に直接もう1つのパーツを成形するので、製品を組み立てる必要がなく、結果として全体的により丈夫で耐久性の高い設計が可能になります。
オーバーモールドは、大量に生産する場合やカラフルな複数層設計の製品の製造に最適ですが、留意すべき制約事項ももいくつかあります。まず、射出成形と同様にオーバーモールドでは高額な先行投資が必要となります。金属から成形型を製造したり調整したりするためには多大な時間とコストがかかり、2ショットの射出成形機は微調整も複雑です。よって、これらのコストを分散させるためには大量に製品を製造しなければなりません。
プロからのヒント:オーバーモールド用の部品や成形型を3Dプリントすることで、試作段階における時間とコストを大幅に節約できます。
インサート成形とは
インサート成形とは射出成形のもう一つの手法で、基盤の上に2つ目のパーツを成形します。インサート成形とオーバーモールドの違いは、インサート成形は既に基板(ベースまたは内側の部品)がある状態で、その上に作業を施す点です。あらかじめ作られたパーツ(ほとんどは全く別の施設または別の会社で製造されたもの)を金型に挿入し、2つ目の層をその周りに成形します。
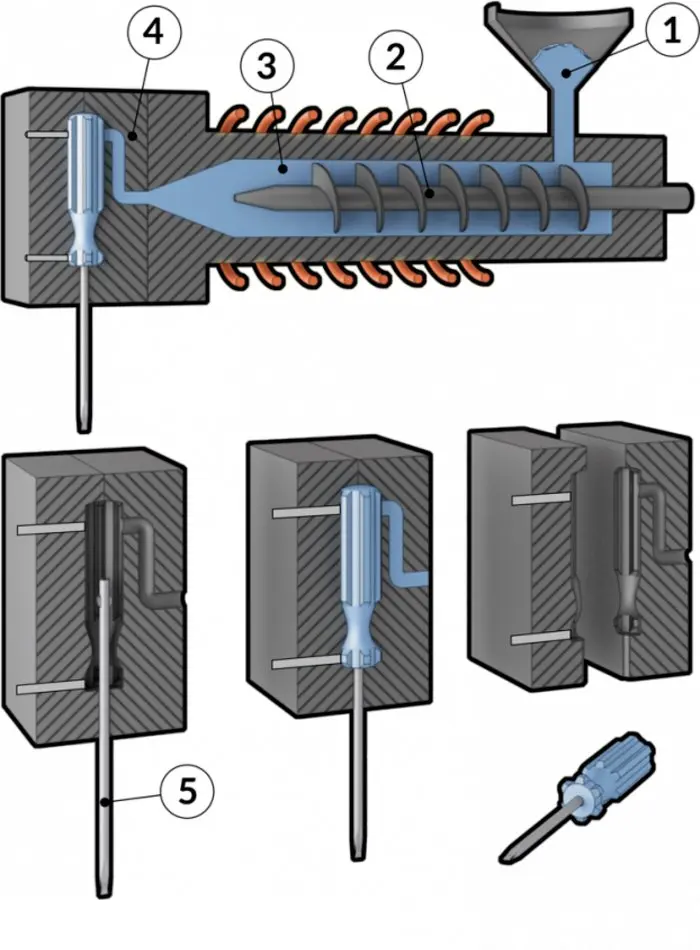
インサート成形でドライバーを作る時の概念図(出典)
インサート成形は金属層の上にプラスチック層を加えるときによく使われ、例としては、ドライバーのねじ回し部分(金属製)にプラスチック製の取っ手を付ける場合などが挙げられます。また、断熱管、配線、その他同様の製品やプラスチック埋め込み型の電子機器の製造にも使われます。
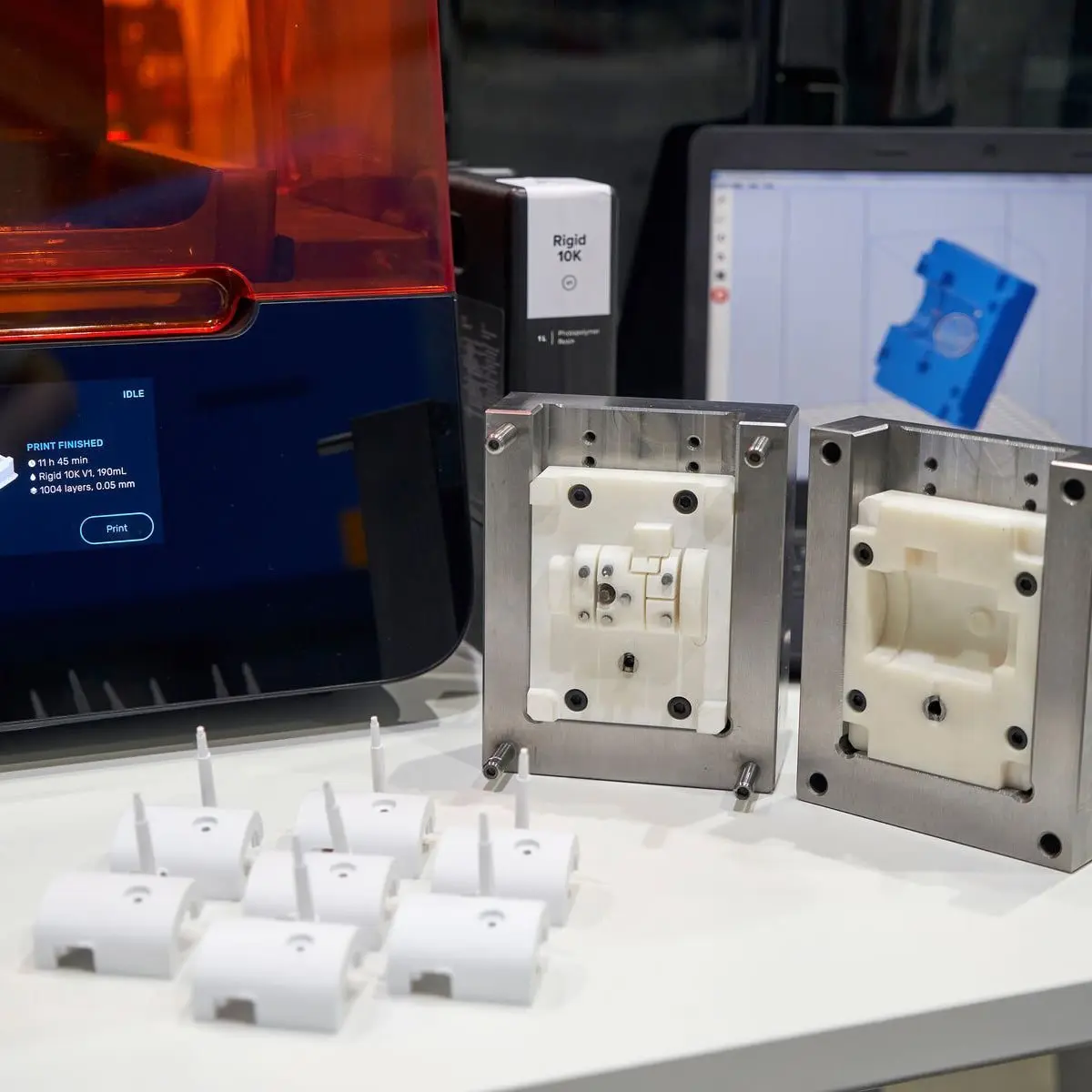
3Dプリントした金型を使った少量高速射出成形
FormlabsのWebサイトでは、3Dプリント製の型を使ってコストと時間を削減しながら射出成形を行う際のガイドライン、また実際にこの手法を導入しているBraskemやHolimaker、Novus Applicationsの事例を掲載した技術資料をダウンロードできます。
インサート成形によく使われる材料
前述のオーバーモールドに使われる(熱可塑性)樹脂と同じ材料を、インサート成形の外側や上層の成形に使うことができます。
インサート成形の利点と限界
インサート成形では、オーバーモールドと同じく組み立て不要で丈夫なパーツを成形することができますが、使用できる材料はオーバーモールドよりも豊富で、例えばコンピューターチップやケーブルなどを樹脂でケーシングできます。インサート成形を最も有効的に使える方法はおそらく、(殺菌可能な)人命救助用医療器具やインプラントに施す樹脂製の覆いを製造することでしょう。
しかしインサート成形には、オーバーモールドと同様の制約もあります。光造形3Dプリンタをテスト工程に使用しない場合、試作品製作が困難になる場合があるほか、実製品の製造のために基板を金型内に入れたままの状態にしなければならないことが多いため、非常に正確に金型を製作する必要があります。
オーバーモールドやインサート成形の有効性を見極める
想定の用途に最適な製造プロセスを選定するためのガイドとして、以下にいくつかのポイントを示します。
オーバーモールドに適した条件:
-
成型品が熱可塑性樹脂および/またはゴム製である。
-
複数の層、材料(上記に記載されたものに限る)、および/または色を用いた設計である。
-
基板と2つ目の層のどちらも自分自身で製造する。
-
完成品を外したり分解したりする必要がない。
インサート成形に適した条件:
-
あらかじめ作られた基板を用いる。
-
基板が金属やワイヤ製、またはコンピュータ化されたパーツである。
-
完成品を単一品として製造する。
先駆者たちは絶えず製造方法を状況に合わせて適応させてきたため、これらのルールにはもちろん例外も存在します。それでも、上のチェックリストをご覧になることで想定の用途に最適なプロセスを選ぶ役に立つでしょう。これらの2つの製造方法を併用することも可能です。
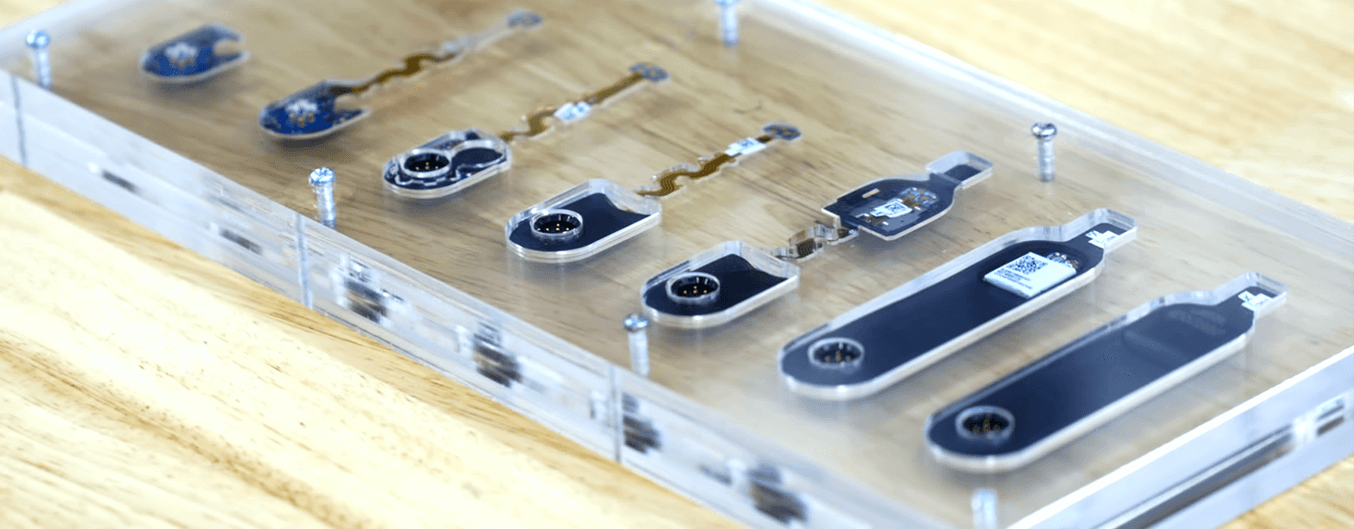
GoogleのATAPチームはウェアラブルデバイスをオーバーモールドとインサート成形を組み合わせて製造。デバイスの製造は、構成部品をプリント基板(PCB)に実装するところから始まる。PCBを低圧のオーバーモールド装置に入れ、プラスチックのブロックを作る。このPCBと柔軟性のあるケーブルが電子部品の構成部品で、熱可塑性ウレタン(TPU)とシリコンゴムの中にオーバーモールドされる。その後PCBAは最終的なオーバーモールドの工程を辿る。
オーバーモールドとインサート成形の基礎
製造業者は、オーバーモールドとインサート成形を使って幅広い業界に提供する商品を製造しています。ここで、通常これらのプロセスの1つまたは組み合わせによって製造される製品例をご紹介します。
消費者製品
家の中を見渡すと、複数カラーの丈夫な単一プラスチック製品を多数見つけることができると思います。それらの多くは、オーバーモールドで製造されたものと考えてほぼ間違いありません。この人気の高い製造プロセスは、ボーリングのピンや子供用ゲームの構成部品から、収納箱やプラスチック容器まで、あらゆる製品の生産に使われています。
歯ブラシ、携帯電話ケース、USBメモリは通常、オーバーモールドおよび/またはインサート成形を使って製造されています。オーバーモールドは、ステップスツール(踏み台)やパティオチェアなど、ツートンカラーの様々なプラスチック家具の製造に使われています。GPSユニットやナビゲーション機器のプラスチック筐体も、オーバーモールドとインサート成形を使って作られていることが多いです。
自動車業界
金属とプラスチックの組み合わせ、またはゴム材料で造られている電気センサー、ギア、留め具、その他の車両部品の製造には、通常インサート成形が使われています。オーバーモールドはドア、ダッシュパネル、ハンドル、ノブ、様々な制御装置など、丈夫でツートンカラーの内側部品を作るのに使われます。特定のモーターやバッテリーもインサート成形のプロセスを通して作られています。
医療業界
樹脂は電子やコンピューター部品に比べて殺菌しやすいことから、医療業界はインサート成形とオーバーモールドされたパーツに大きく依存しています。除細動器、医療用ケーブル、ワイヤはしばしば、インサート成形を使ってプラスチックで覆い、壊れやすい内側の部品を保護することで、最終的な器具の手入れをし易くします。
ペースメーカー等、体内に埋め込むように設計された医療器具は、通常インサート成形を使って製造されます。製造施設では、内視鏡検査や結腸内視鏡検査を行うときに用いる器具など、身体の内側の画像用の様々なカメラ機器の製造にもインサート成形を使っています。
電機業界
電線は、ゴム製の外装をインサート成形することで、より安全に、また耐候性も備わります。製造業者は、消費者の安全のために、携帯電話やコンピュータの充電器等の製品のワイヤ部品をゴムでコーティングします。複数ワイヤを1層のゴムでコーティングしたり、ワイヤを見分けやすくなるように赤や色などの対比色を使って作ることもあります。
美容業界
オーバーモールドとインサート成形は、コスメティックスのパッケージをより魅力的な外観にするために日常的に使われています。デザイナーは独自の表面テクスチャと複数カラーを施したカスタムパッケージを作ることができます。コンパクト、メイク用ブラシ、香水瓶等の製品はすべてオーバーモールドおよび/またはインサート成形を使って製造することができます。
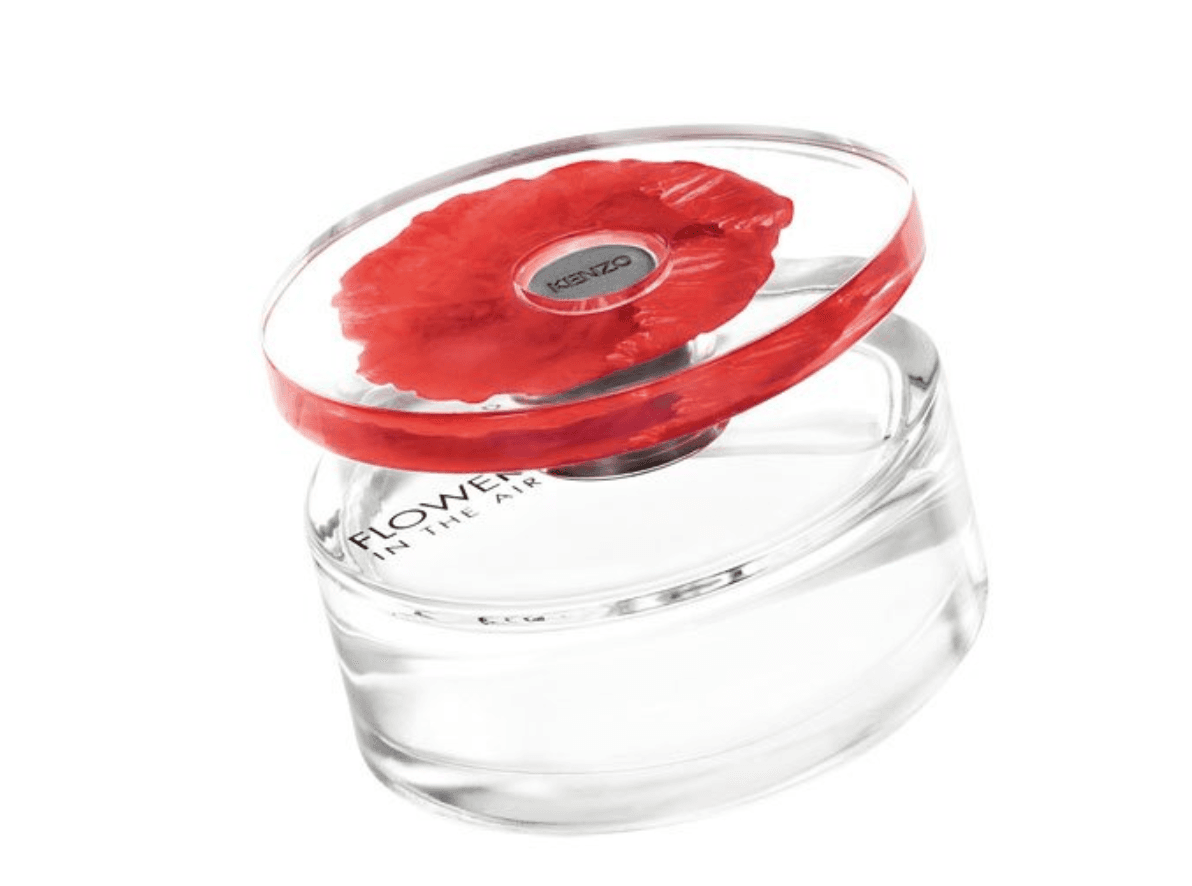
オーバーモールドで作られたKenzoの香水瓶(出典)
オーバーモールド、インサート成形、3Dプリントを使ったプロトタイピング
プロトタイピングは、製品開発には不可欠な工程です。プロダクトデザイナーやエンジニアはコンセプトを試し、 今まで使ったことの無いデザイン要素を解決していかなければなりません。しかしプロトタイピングの欠点はすぐに非常に高額になってしまうことです。また、部品製造を外部委託しているとしたら、さらに多大な時間も費やすことになります。
世界トップのイノベーターたちは、3Dプリントにオーバーモールドやインサート成形等の製造プロセスを組み合わせることによって、これらのプロトタイピングの問題を乗り越えています。
Google Advanced Technology and Projects(ATAP)ラボのデザイナーチームは、3Dプリントとインサート成形を導入することで、テスト期間を3週間から僅か3日間まで短縮し、10万ドル以上のコスト削減を実現しました。Google ATAPチームは高額な電子部品をサプライヤーから買い入れるのではなくテストパーツを3Dプリントした方が、製作時間もコストも大きく削減できることを発見したのです。これはビジネスに3Dプリントと他の製造方法を組み合わせる多様な手段の1つです。
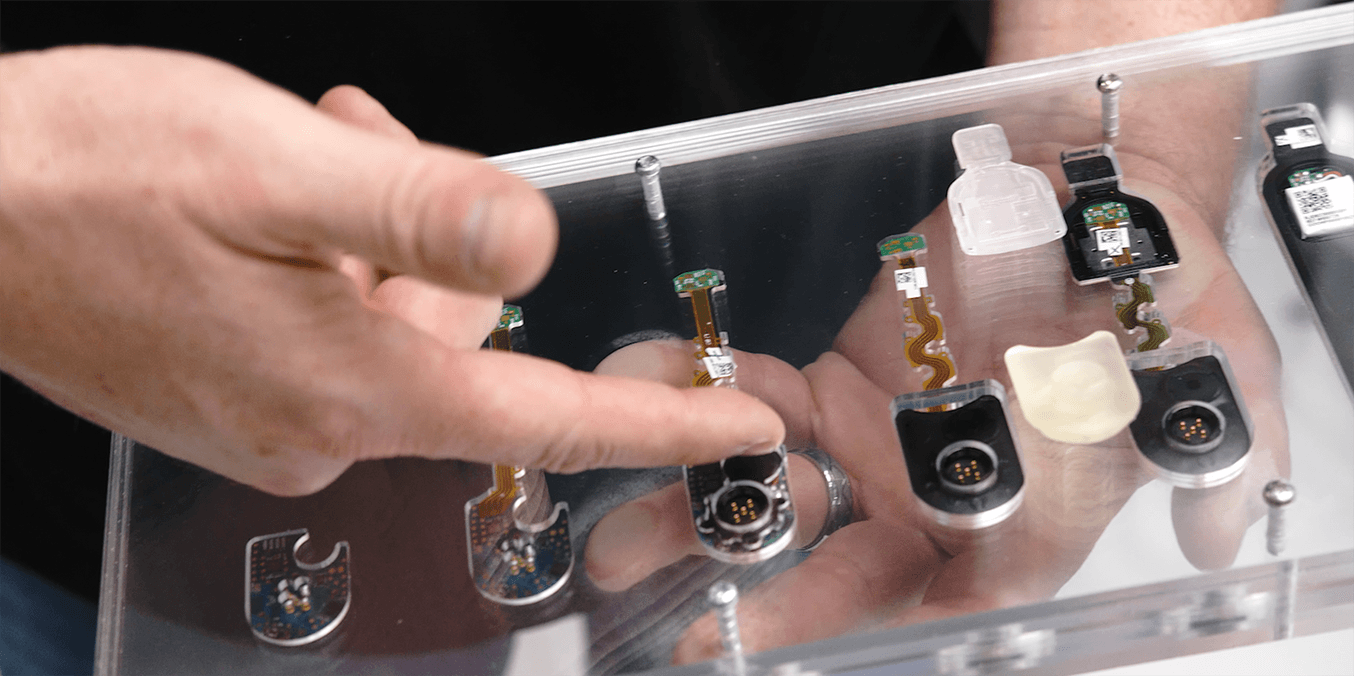
GoogleのATAPチームは工場での初期段階のツール調整にオーバーモールド成形製の電子部品の代替品として 3Dプリント製品を採用した。
また、米ブルックリンに本拠を置くスタートアップ企業、Dame Productsは健康関連グッズのデザインを行っています。同社はシリコンインサート成形を採用し、顧客向けベータ版試作品の内部装置をそのシリコン内に包み込んでいます。Dame Productの製品は、肌に無害で鮮やかな色彩のシリコンで包まれた複雑な人間工学形状をしています。
同社のエンジニアたちは、3~4つのSLA光造形による3Dプリント製金型を駆使して1日に数十点の装置をインサートおよびオーバーモールド成形で試作しています。試作品のシリコンゴムを硬化させている間に次の試作品を脱型して次の充填の準備をすることができ、脱型した試作品の仕上げや洗浄作業も同時進行で行えます。顧客が試作品を試した後に同社に返却されると、その試作品は漂白された後シリコン部が除去され、内部装置は別の新しいベータ版試作品に再利用されていきます。
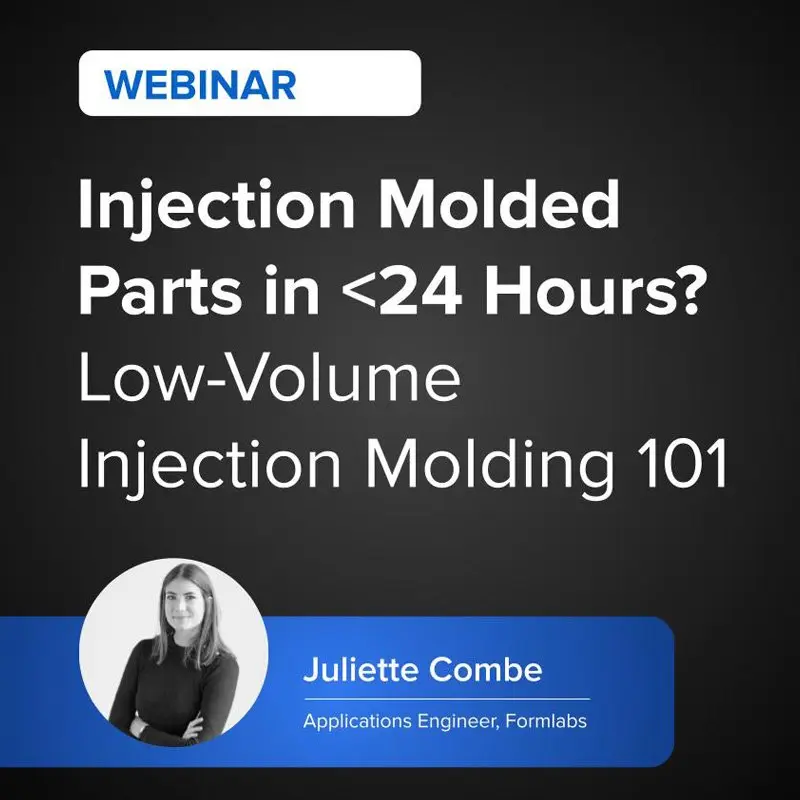
24時間以内に射出成形を完了する方法とは?小ロット量産用の射出成形 101
本ウェビナーでは、射出成形でSLA光造形3Dプリント製型を使用してコストを削減し、製作期間を短縮し、より高品質な製品を市場投入する方法を解説します。
3Dプリント製の金型を用いたインサート成形の手順ガイド
以下の教科書的ガイドを使って、1つのハードウェアをシリコンの中に包み込みます。この事例では、3Dプリントとインサート成形の組み合わせを用いています。
必要な材料と器具:
-
Formlabsのヘラとフラッシュカッター
-
2層ゲル構造医療グレードRTV液状シリコン:ショアA硬度20~40を推奨
-
シリンジ
-
エポキシカートリッジ
-
エポキシ充填ガン
-
ミキシングノズル
-
かくはん棒
-
C型クランプ
-
包むハードウェア (自分で選択したもの)
任意の材料と器具
-
シリコン染料
-
ワセリン
-
振動源
-
ダクトテープ
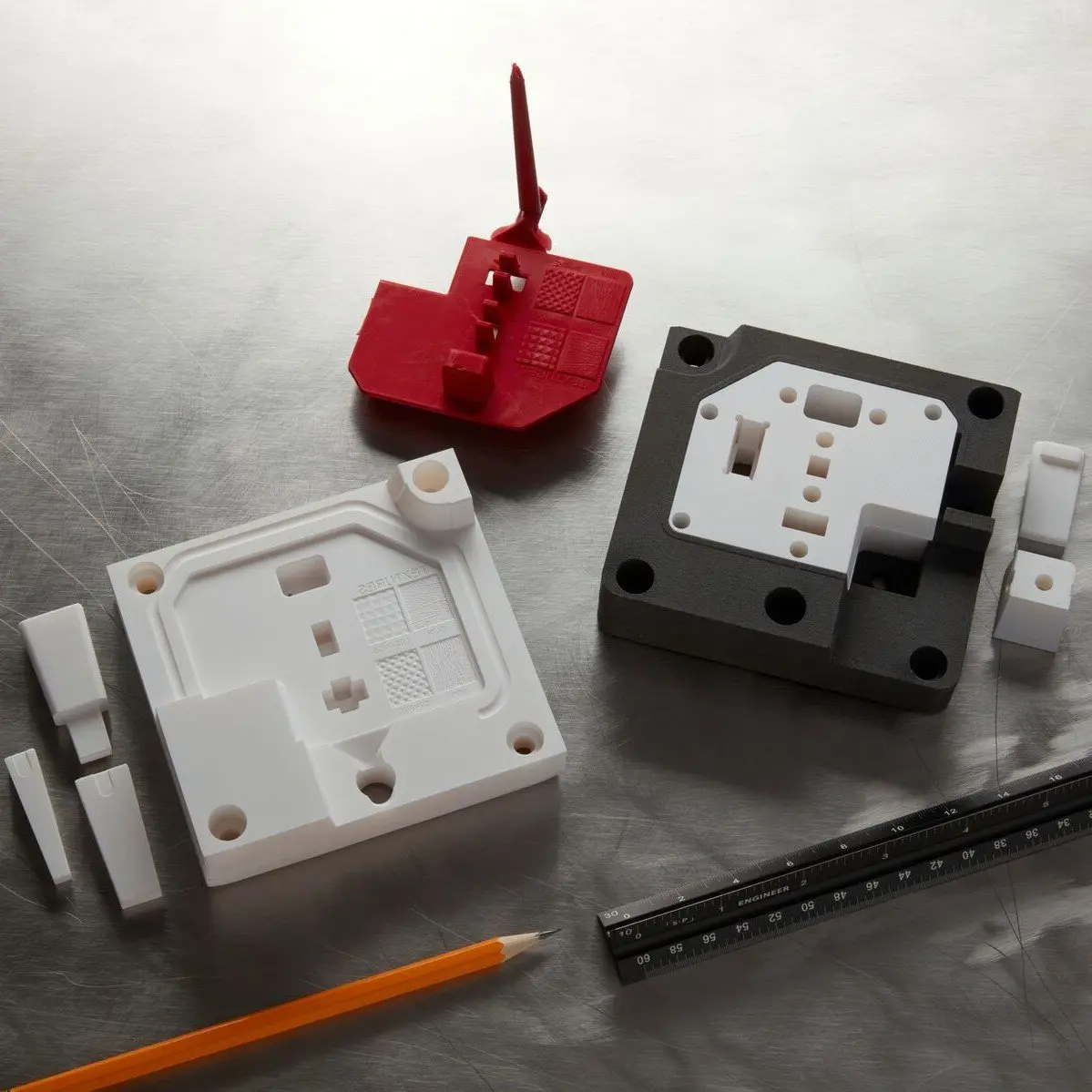
ステップごとの手順:
1. Formlabs Clearレジンで複数パーツの金型をプリント: 層の高さ50μmでのプリントを奨励しています。パーツの方向付けで内側表面にサポート痕が残らないことが非常に重要です。
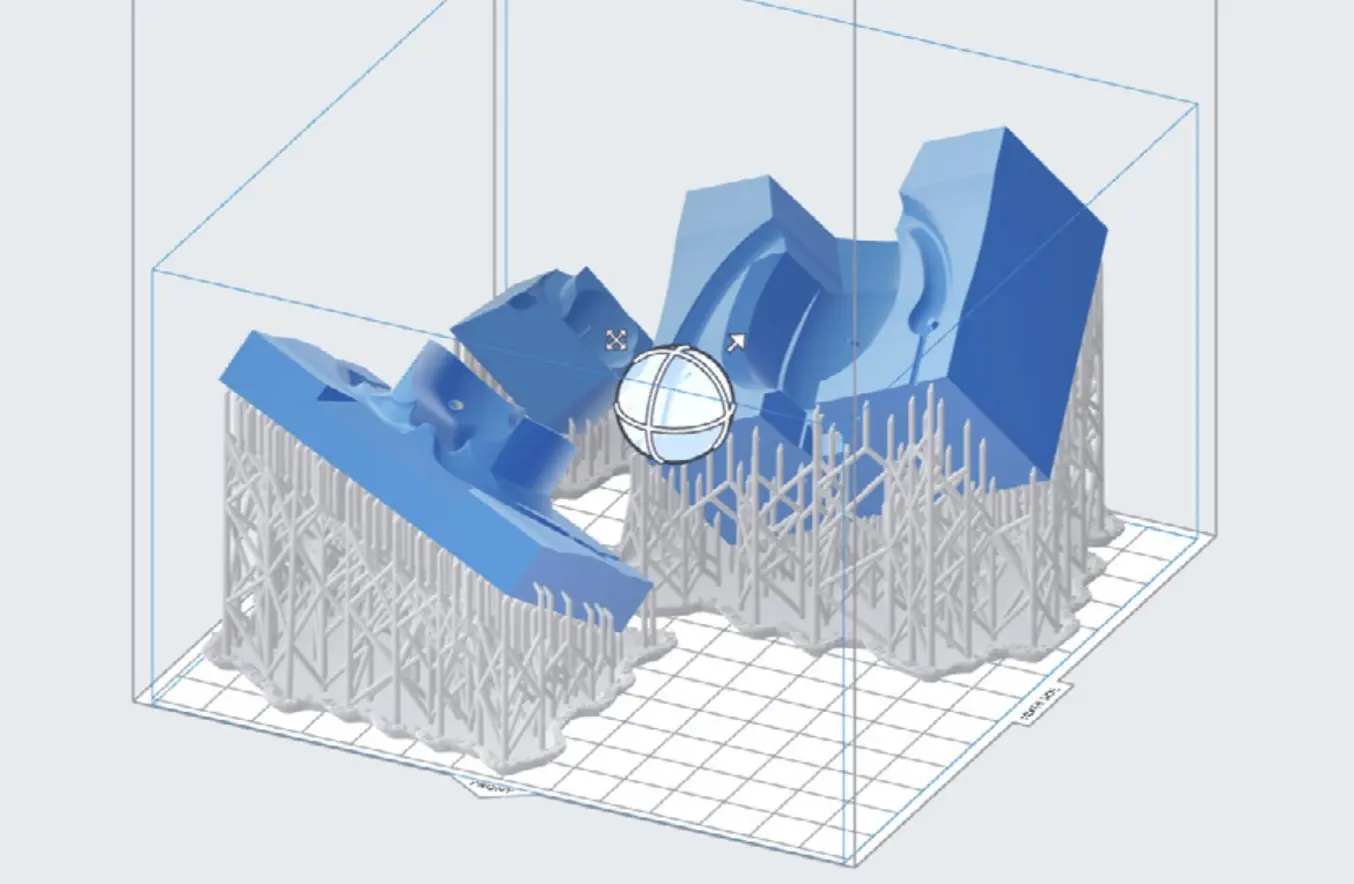
2. 金型を洗浄して二次硬化し、サポート材を除去: パーツが粘つきの無い仕上がりになるまでイソプロピルアルコールで丁寧に洗浄します。Clearレジンは60˚Cで15分間二次硬化することを奨励しています。金型の外側を磨くと非常に透明度の高い仕上がりになります。
3. インサート成形の少なくとも1時間前にシリコンを準備: 液体を別々の注射器を用いて移し、1つのパーツ (AまたはB) でエポキシカートリッジシステムの両側を埋めます。まっすぐに立てて、1時間から1日かけてシリコンからゆっくりとガスを抜きます。任意のステップとして、カートリッジのAまたはBのどちらかの側に染料を加えて丁寧に混ぜ合わせます。
4. 離型剤を適用 (任意): 小さな絵の具ばけで非常に薄い層のワセリンを金型の内側表面に加えます。このシリコンオーバーモールド技術も離型剤を使わずに実践できます。
5. 内側のハードウェアを正しく方向付け: 金型の位置合わせピンはハードウェアの配置に役立ちます。
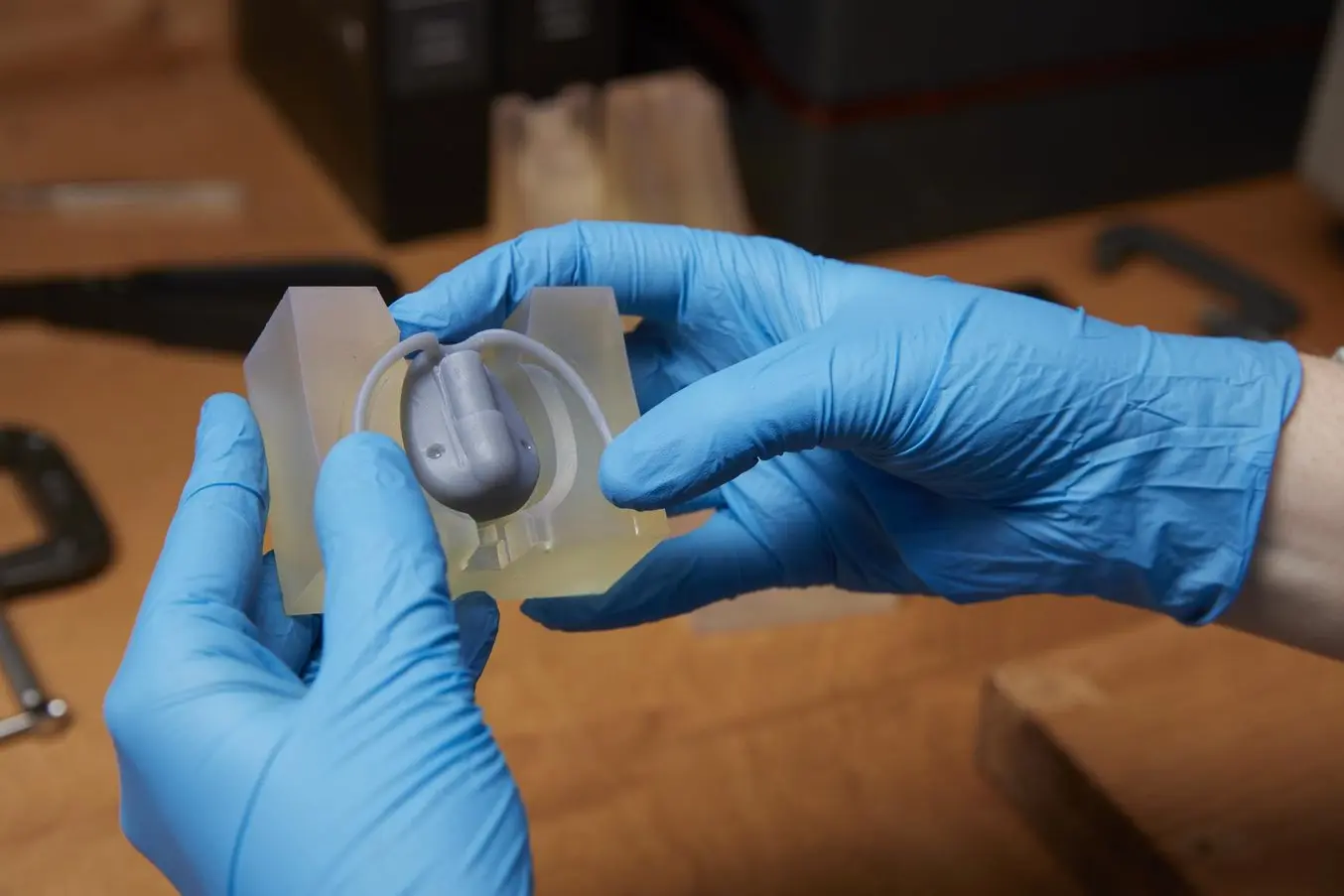
6. 金型を閉じて手動で圧迫: 金型の外側から、ハードウェアが正しく配置・配列されていることを確認します。もしハードウェアの配列が良くなければ、5と6のステップを繰り返します。
7. 金型を固定: 「引きの方向」、または金型の主な分割線に垂直に締めて固定します。固定することでにより内側のハードウェアが動く可能性があるので、再びアライメントを確認します。固定する前にダクトテープで端を密封すると、材料の浸潤やRTV金型成形で生じるのフラッシングを減らすことにつながります。
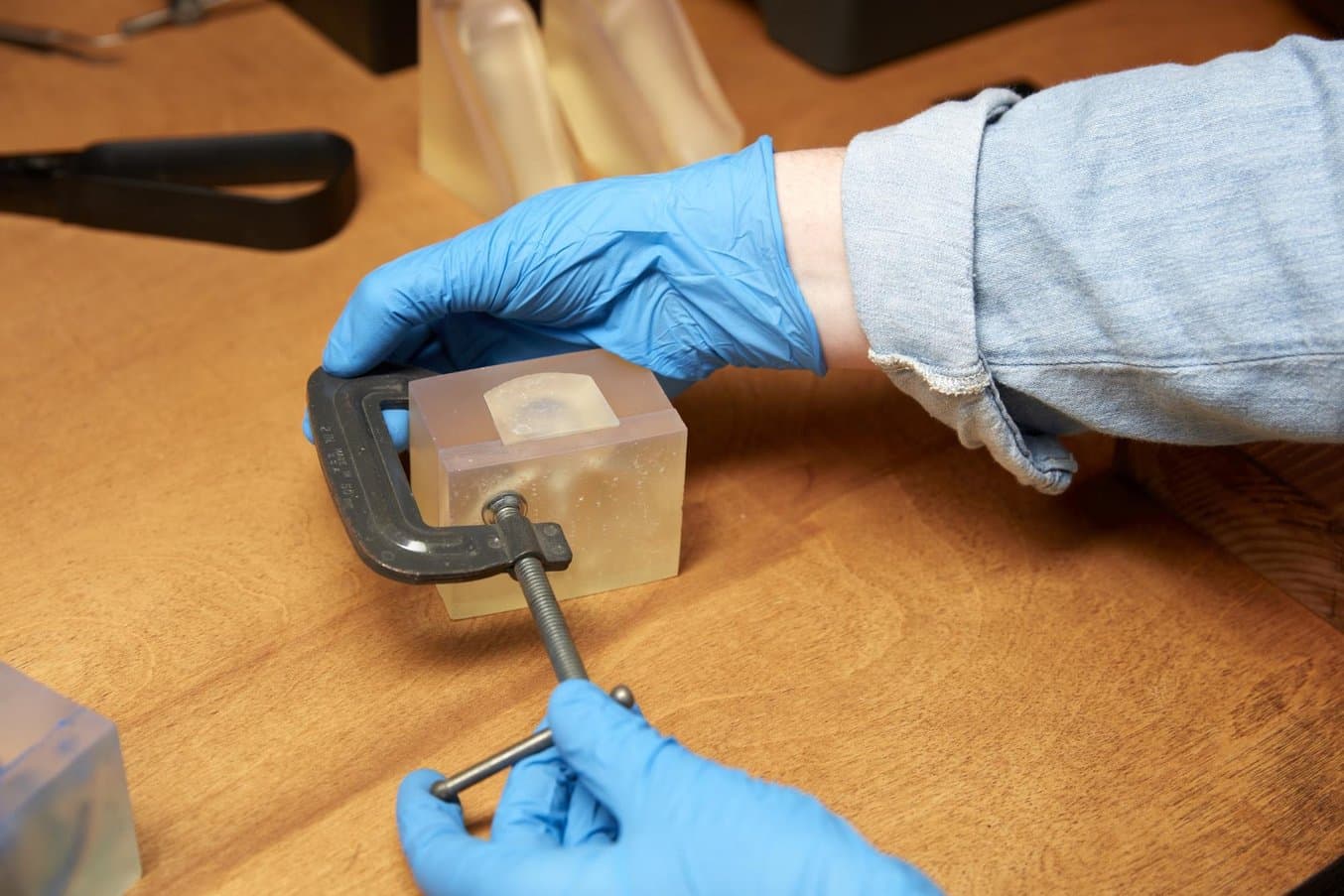
8. エポキシ注入ガンのアッセンブリ: カートリッジをガンに挿入し、ミキシングノズルにねじ留めします。この段階で、よくミキシングされたことの確認のためにノズルの先端部から液体を少し搾り出します。
9. 金型にシリコンを注入: ミキシングノズルの先端部を金型の開口部に差し込み、引き金をゆっくりと引きます。金型へのシリコンの入り具合を見ながら、金型が一杯になりシリコンがすべての通気孔から溢れ出すまで注入します。空気泡が沈下しているときや、材料が分割線に流れ込んでいるときは、注入を止めた後もシリコンが金型の中に沈み込んでいきます。初期注入の後に、必要であればさらに数回少しずつシリコンを加えていきます。充填したら、振動源 (ハンドヘルドサンダー等) を金型の表面に保つと、空気泡を逃がしやすくなります。
10. シリコンの硬化時間: シリコンの説明書から推奨硬化時間を確認します。この時に仕上げを行います。
11. 試作品の離型: まず金型の外側の余分なシリコンをすべてトリミングします。そしてFormlabsのへらまたはマイナスドライバーで金型をこじ開けます。細いひも状のシリコンが金型の通気孔の中にあることも忘れないでください。それらは時間をかけて個別に切り取ることで、金型の中に残ってハードウェアからシリコンを引っ張ることがなくなります。出来上がり品を完全に外す前に、フラッシングをトリミングするのも良いでしょう。
12. 試作品をトリミング、仕上げ、洗浄: フラッシングは必ず排出されるので、Formlabsのフラッシュカッター または鋭い刃でトリミングします。もしも空気泡が表面に真空空間を作ってしまったら、追加の液体シリコンをつぎあてて塗装し硬化させます。試作品は、ベータテスターの手に渡る前に、業界特有のガイドラインを用いてきれいな状態にしなければなりません。
金型は複数回再利用することができますが、通気孔をペーパークリップやドリルビット等の尖ったものを用いて掃除することが必要です。
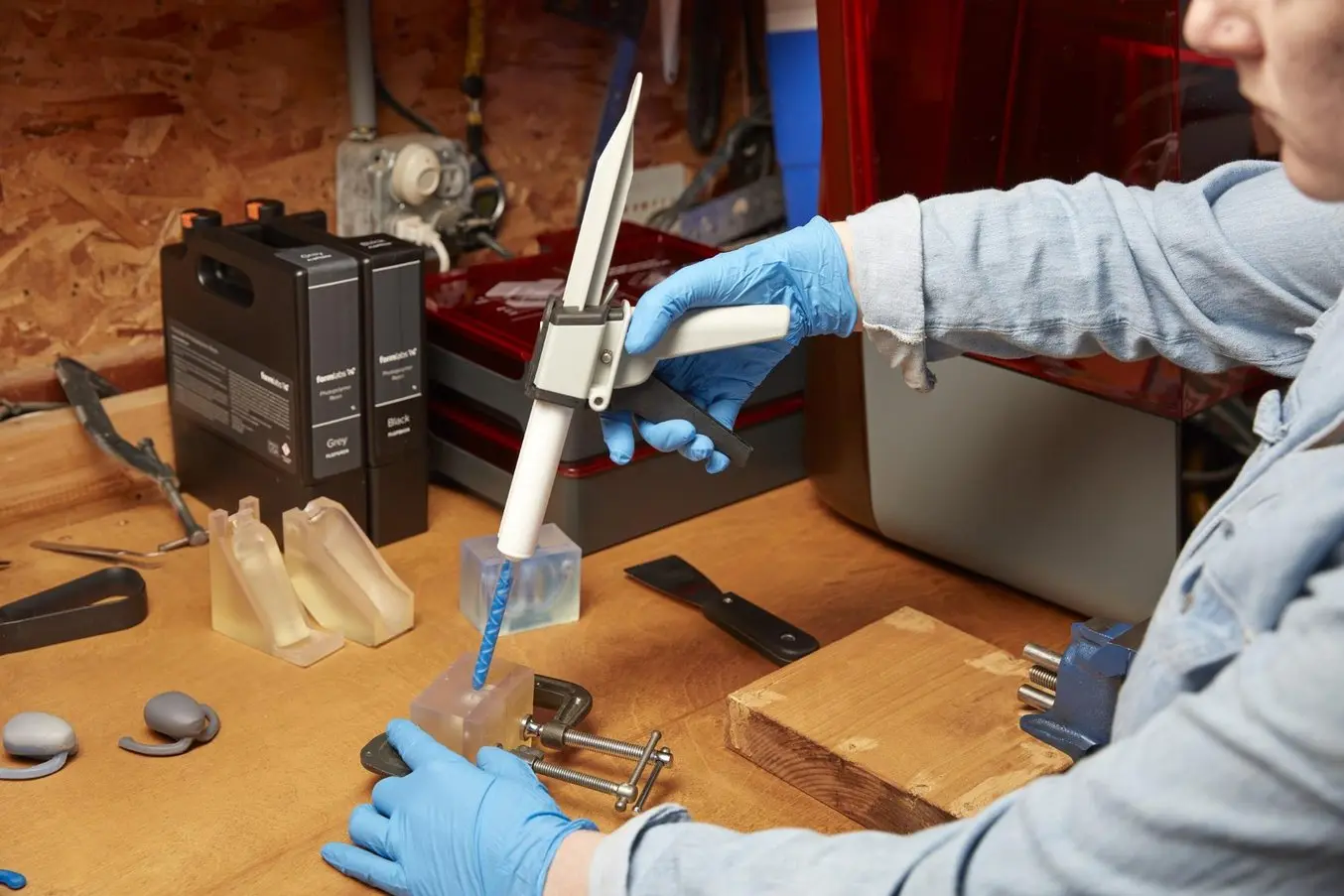
製造とプロトタイピングに関するヒントやアイディアを更に獲得
成形のベストプラクティスについては、技術資料「プロダクトデザインのためのシリコン成形」をご覧ください。シリコン成形、インサート成形、オーバーモールド成形、圧縮成形に関する具体的なアドバイスと実証された方法について解説しています。