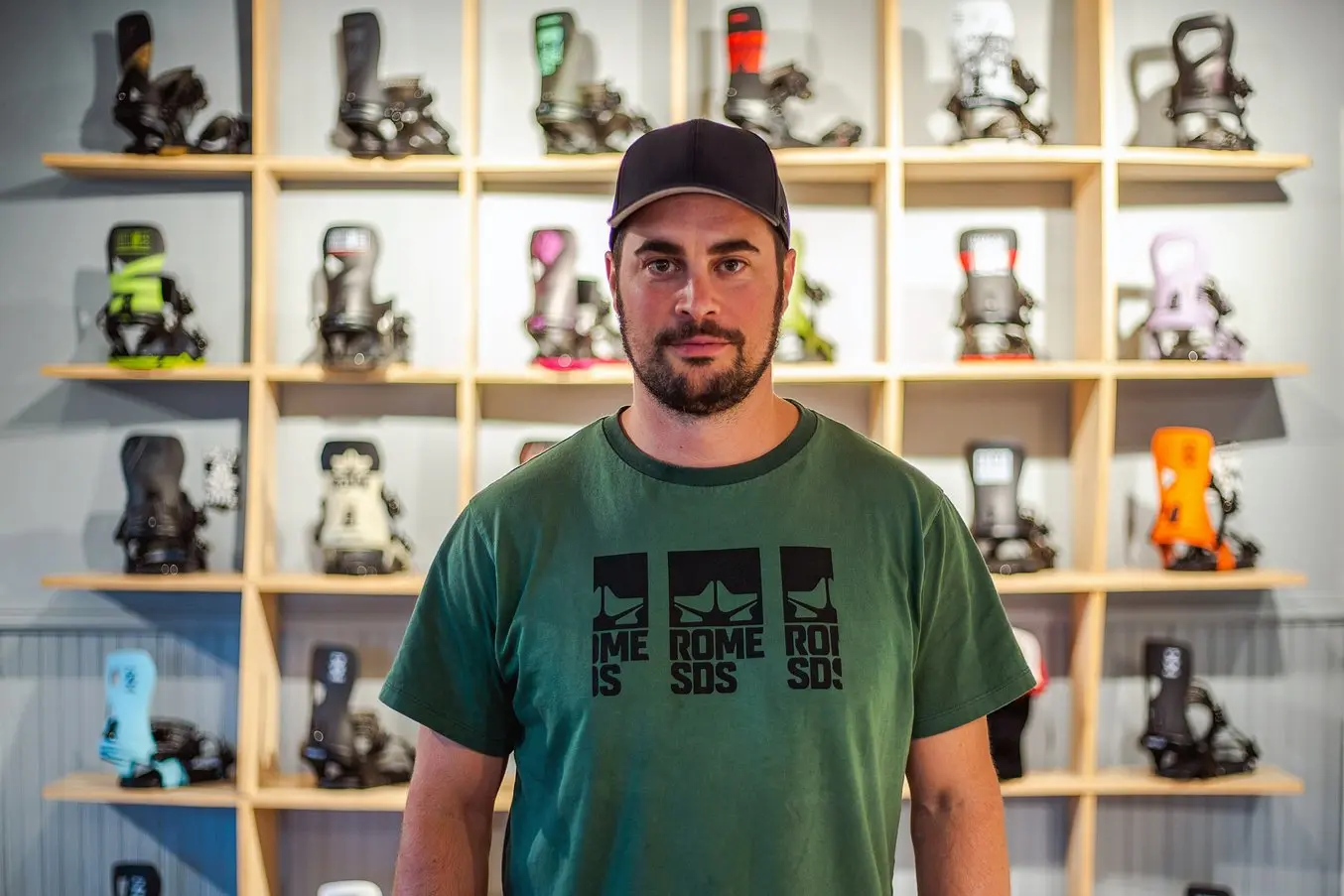
Rome Snowboardsのプロダクトデザイナー、Justin Frappier氏はSLS 3Dプリントを社内導入し、設計、試作品の製作、検証・設計改善のプロセスを毎日実施している。
我々は常に新しいことに挑戦しています。既にROIも見えてきていて、試作品製作の工程を高速化しただけで、最初の5ヶ月で成果が見えました。
Rome Snowboards リードプロダクトデザイナー、Justin Frappier氏
1960年代に発明されてからというもの、スノーボードは常に反骨精神と強い結びつきを築いてきました。若々しく大胆なスター選手、バギーなシルエットが特徴のスノーボードウェア、テレインパークでの派手なフリップなど、高級なウィンタースポーツのパンクな弟分として、サーフィンやスケートボードにも通底するスタイルで同じ嗜好を持つ群衆を引きつけ、カウンターカルチャーのイメージを強めてきました。
スノーボードは、人と違うことをしたいという願望から生まれたスポーツらしく、必要な道具もすべて、その精神を高度な技術で反映しています。スノーボード用品メーカー各社は常に、ゲレンデでフルシーズンに対応でき、スノーボーダーが長時間山で楽しめるような、信頼性が高く頑丈で快適な用品を生み出す新しい方法を模索しています。試作・検証・改善の反復プロセスをスピードアップし、革新的な新しいデザインを安定して生み出せるよう、メーカー各社は3Dプリントを活用した内製に注目しています。
アメリカ バーモント州ウォーターベリーにある従業員10名ほどの小企業、Rome Snowboardsでは、「All Ways Down(すべてを試し抜く)」をモットーにしています。これは従業員の山に対する思いと開発工程に対する会社の信念を表すもので、プロダクトデザイナーのJustin Frappier氏は、バインディング(ビンディング)やブーツを製作する新たな工程や方法を追求し続けています。Romeが最も重視する目標は、フリップ、スピン、スライド時に発生するねじれや衝撃に耐えられ、長時間でも快適に装着していられる用具を製作することです。Fuse 1 SLS方式3Dプリンタによる内製を始めたことで、Romeのイノベーションが高速化し、試作品を山でテストし、これまでより厳密な反復検証ができるようになりました。「我々は常に新しいことに挑戦しています。既にROIも見えてきていて、試作品製作の工程を高速化しただけで、最初の5ヶ月で成果が見えました」とFrappier氏は言います。
Romeは既に業界から高く評価される製品を製作しており、White Linesのような専門誌でレビューを獲得しています。RomeのバインディングVICEを2021〜2022年のスノーボード製品トップ100に選出したWhite Linesは、レビューの中で「確立された技術と高度な機能を組み合わせた、最高に万能性の高いバインディング。ベストセラーのVICEシリーズの最新作として、Romeはまさに誰もが求めていた製品を作り上げた」と称えています。
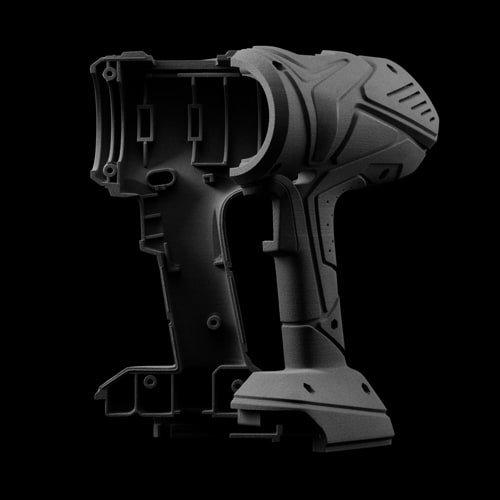
SLS(粉末焼結積層造形)方式3Dプリンタの概要
高強度・高機能な部品を製造できる3Dプリンタをお探しですか?本技術資料では、SLS方式プリンタの仕組み、そして機能確認用試作や実製品用部品の量産に広く用いられている理由を紹介しています。ダウンロードしてご覧ください。
SLSで課題に挑む
Fuse 1を導入する前は、Frappier氏を始めとするRomeの従業員は粘土や接着剤などを使って設計をすべて手作業で行ってから部品を外注で製作して組み立て、外観確認用の試作品として後処理を施していました。以前から3Dプリントには着目していたものの、Frappier氏が実際に3Dプリント製のバインディングを作ろうと研究を始めたのはFuse 1のティーザーを見てからでした。「いつか3Dプリントを取り入れたいと、おそらく8年ほどは考えていたと思います。様々な価格帯の様々な3Dプリンタの長所と短所を比較・検討した結果、Fuse Siftとプリンタがセットになっていて、しかも全体的によく考えられているなと感じたFuse 1が私たちの用途には最適だと思いました」とFrappier氏は振り返ります。
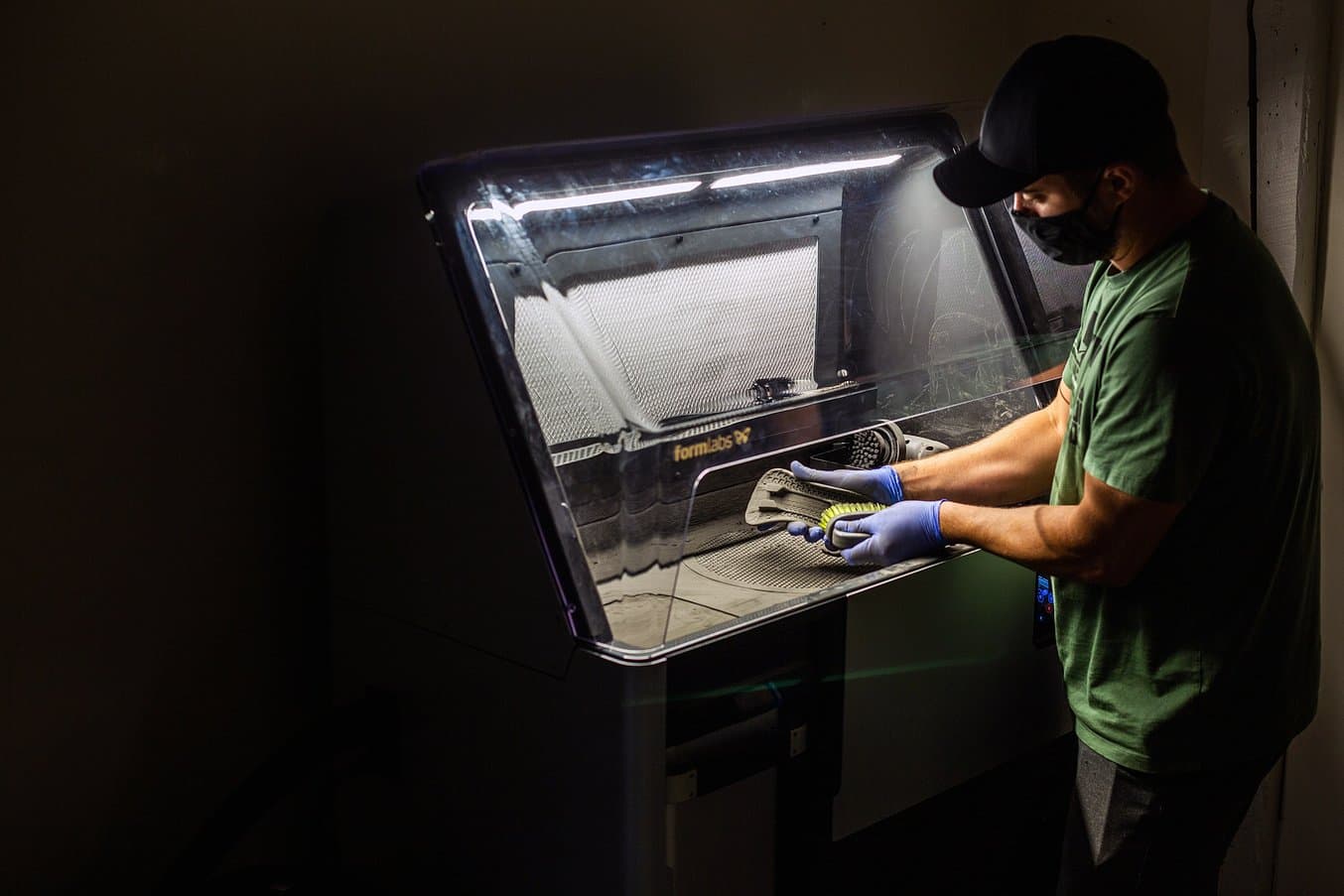
Fuse Siftによって後処理や粉末の回収・再利用プロセスが効率化され、Frappier氏はデザインに重きを置いた作業により多くの時間を割くことができている。
粘土を彫刻することで設計を進める一方、3Dプリント製の部品の製作は国境を超えてすぐのモントリオールにある工場に外注していました。価格的には法外な値段というわけではありませんでしたが、製作期間が長く、より速いスピードに慣れていたRomeでは設計に影響が出ていました。「部品の製作を依頼している会社は他にもありますから、当然順番待ちをしなければならず、開発スピードが部品の製作期間に左右されてしまっていました」とFrappier氏は言います。
カスタマイズ性の高いバインディング部品の開発で知られるRomeのような小企業にとって、開発の遅れは大手メーカーに一歩遅れとる原因になりかねません。Romeの強みは、迅速に試作・検証プロセスを繰り返し、社内承認を素早く取得し、特許取得済みのAuxTech、PivotMount、AsymWrap技術のようにユニークで「業界初」となる製品を生み出せることにあります。
「Fuse 1を導入してまだ半年ほどですが、すぐにそのメリットがわかりました。半年ほど前からバックルの開発に取り組んでいるのですが、バックルを3Dプリントして組み立て、しっかりと嵌まるかどうか、そして他に問題や干渉などがないかを確認します。3Dプリンタを使って部品を製作し、翌朝に確認して組み立て、設計を改善し、その翌日にまた製作できるというのが非常に助かっています」とFrappier氏は言います。
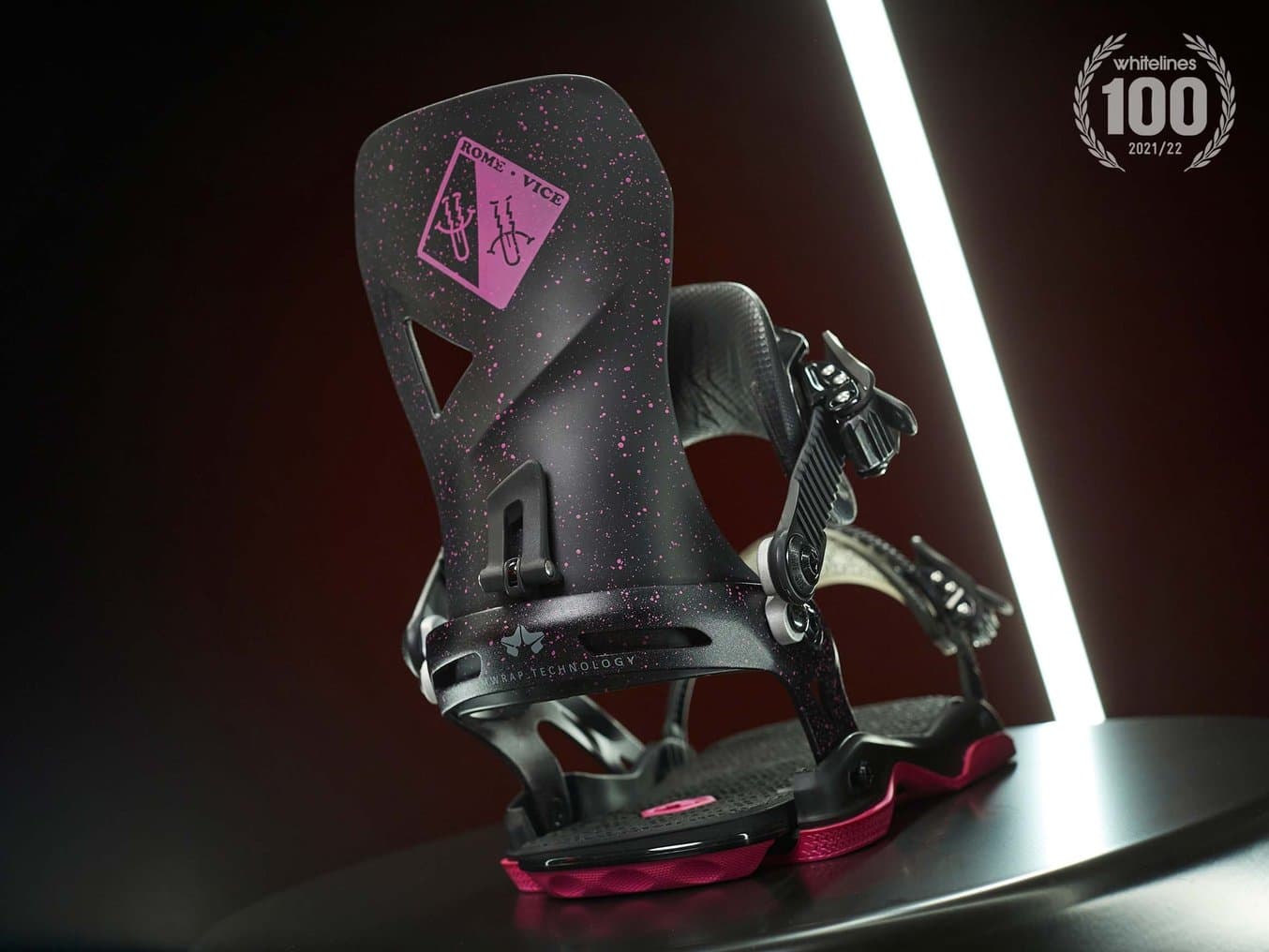
White Linesのレビューでトップ100に選ばれたVICEバインディング。(画像出典:White Lines)
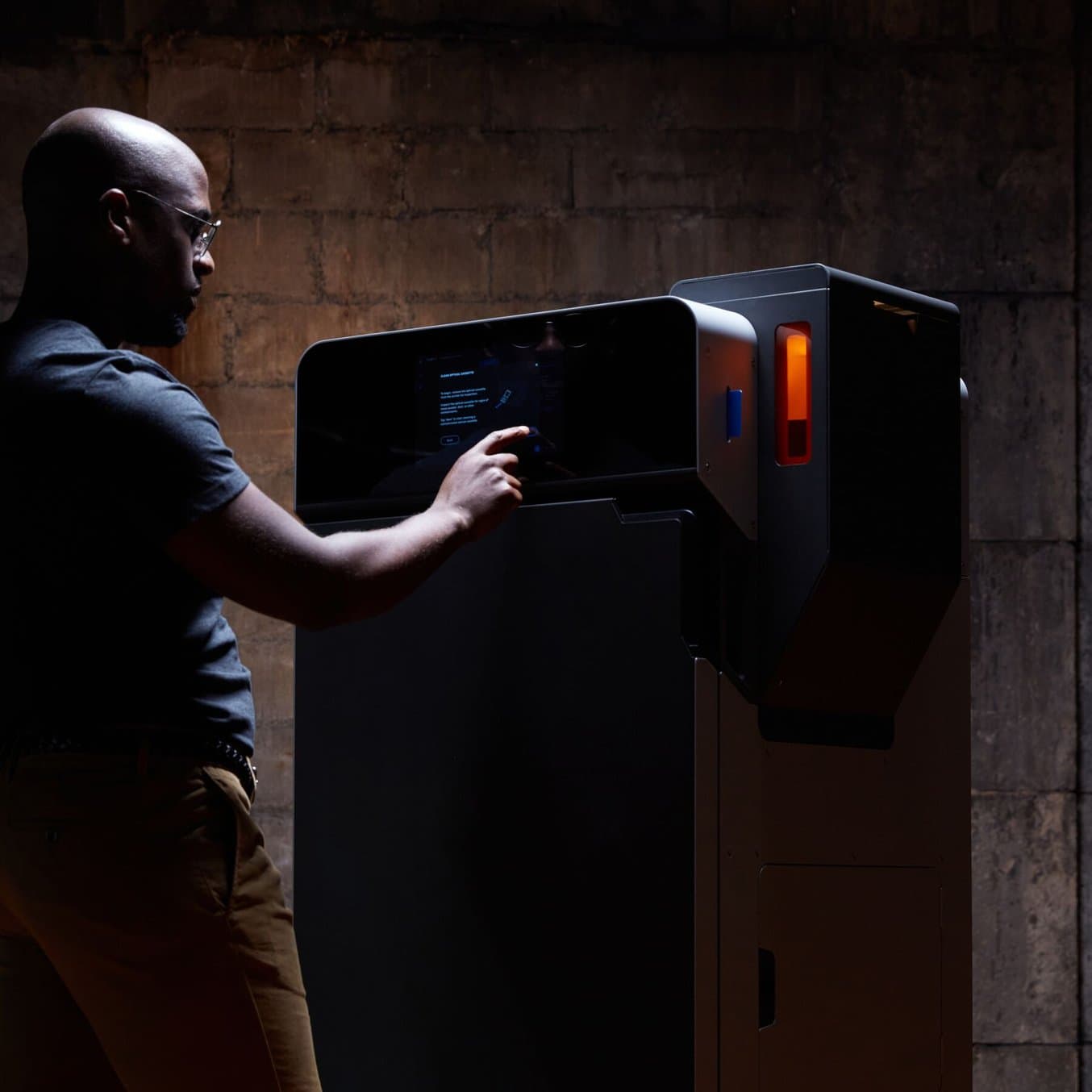
外注か内製か:SLS方式3Dプリントが適するケースとは?
本技術資料では、SLS方式3Dプリンタでの内製と、SLSプリント品を外注で製作した場合を比較し、SLS 3Dプリンタの導入の費用対効果の評価を行います。
使用者のこだわりを具現化
Romeの製品では、スノーボーダーが重量やサイズ、ライディングスタイル、使用環境などに応じてコンポーネントを調整し、一人一人に合わせたフィット感を得ることができます。しかし、そのためには多くの部品が必要なため設計がより複雑になり、シームレスな組み立てを実現するためにも公差を厳密に遵守する必要があります。White Linesのレビューでは、「ハイバックは100%ナイロン製で、ボードは骨に響かないちょうど良い硬さ。どんなライダーでもVICEに乗ればすぐに快適な装着感を楽しむことができる」というコメントが掲載されています。
この使い勝手が実現できるのは、Romeのチームが工程の一つ一つに丁寧に時間をかけて製作しているためです。Frappier氏は次のように述べます。「自分たちの作る部品が完璧で信頼できるものであるよう常に心がけています。部品数が多くてもアセンブリとして完璧なら、お客様は非常に満足度の高い体験が得られます。バインディングが徹底的に設計されているからです。3Dプリントのおかげで、アセンブリとして完璧に機能するようすべての部品を細かく微調整できます」
小さなオフィスから生み出す、大きなインパクト
多くの企業は、知見を共有し合える複数人のデザイナーで構成された大規模なチームを頼って初めて、彼らと同等の詳細な設計を実現しています。Romeにはデザイナーが2人しかいないため、機敏に動ける一方、ノンストップで作業が必要です。Fuse 1は彼らと共に働き、必要に応じて一日中連続プリントを行います。スポンサー候補のアスリートにアピールする際も、この点がセールスポイントになっています。手頃な価格とサイズ感で、設置面積やスタッフの数がそれほど多くない企業でも簡単に導入できます。
他のバインディングメーカーに比べると、私たちは本当に小さな会社です。ウォーターベリーのオフィスには8~10人しかいませんし、3Dプリント環境をフルで装備できているというのは本当にラッキーなことです。多くの人が、私たちはもっと大きな会社だと思ってるんですよ。小さな会社でも導入できるというのが、Fuse 1の素晴らしいところです。
Rome Snowboards リードプロダクトデザイナー、Justin Frappier氏
アスリートや用品販売業者がウォーターベリーのオフィスを訪れると、Fuse 1に対して圧倒的にポジティブな反応がある、とFrappier氏は言います。「このプリンタを見ると、みんな驚きます。設計をその場で3Dプリントし、出来上がった部品をアスリートや販売店の営業担当者にその場で見せ、金型製作に回す前にフィードバックをもらうことができます」とFrappier氏は付け加えます。
機能試作をさらに高速製作
Romeの2022年の製品ラインは3Dプリントで量産とまではいきませんでしたが、それでもチームは、非常にリアルな最終検証用のテスト品を3Dプリントで製作しました。3Dプリンタ導入後、初となる冬シーズン。デザインチームは高度な機能テストを行うことにしました。同社は、バックルやアセンブリが想定した条件に耐えられる品質であることを確認するため、試作品を限界までテストし、完璧だとわかるまではメーカーに部品を送りませんでした。
「時間を無駄にしたくありませんし、徹底的にテストした後に金型を製作できれば、設計が固まっていない段階で作った金型がうまくいかず無駄になることもありません」とFrappier氏はその理由を語ります。
Frappier氏と同社メンバーは3Dプリントだけで作ったバインディング(数本の金具のネジを除く)をバーモントの山に持っていきました。改良を重ねるごとにスピードが上がります。山で実際にバインディングの屈曲や強度、耐久性をテストできることで、Frappier氏は通常の開発スケジュールを数週間も短縮することができました。Rome Snowboardsがブランドとして成功しているのは、そのイノベーション精神のおかげです。クリエイティブなチームが外注部品を何週間も待っていては、せっかくのクリエイティビティが失われてしまいます。
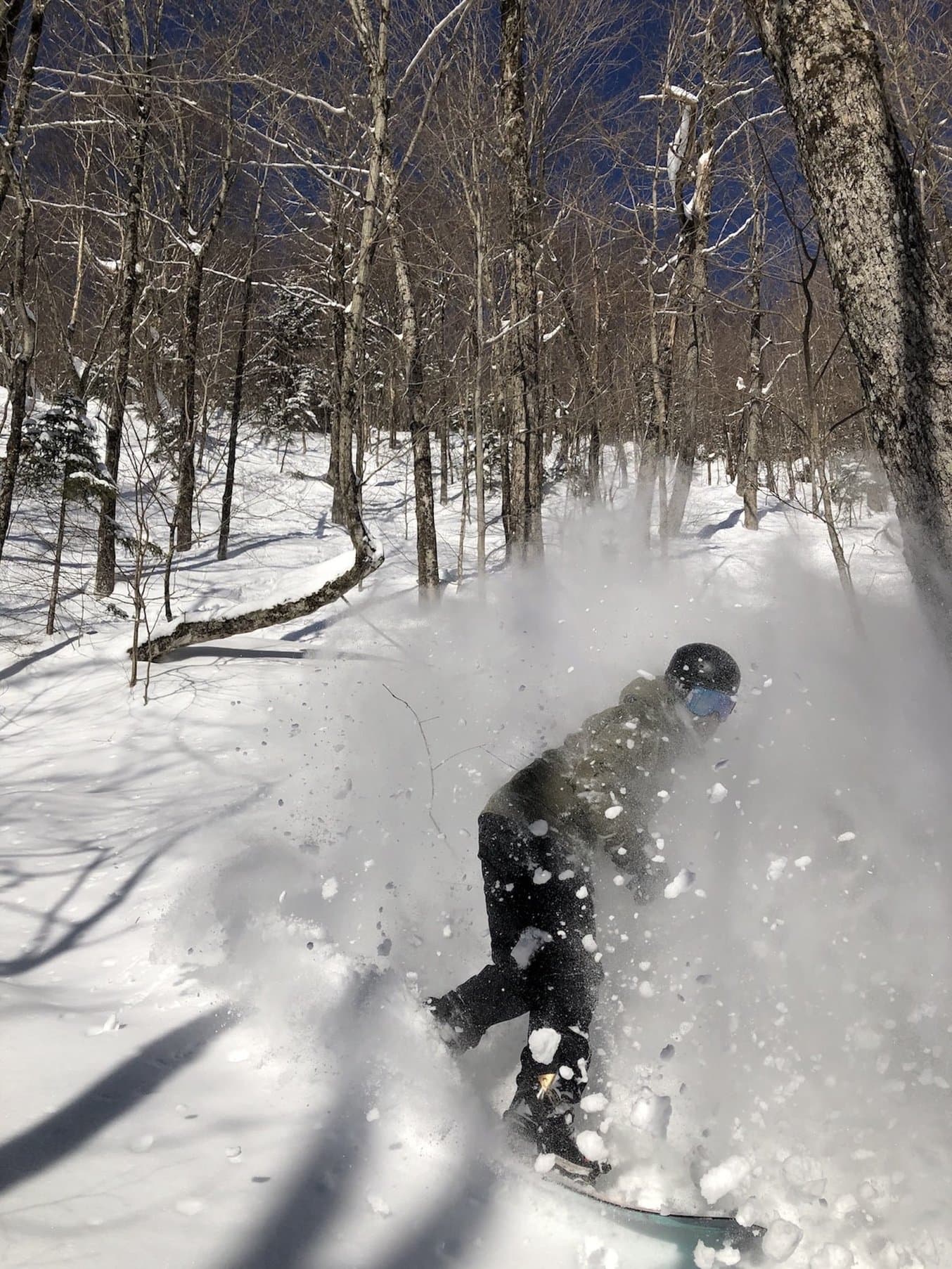
3Dプリント製のボードに乗れる、ということが最大のアピールポイントでした。他の部品では実現できなかったことです。最初はベースプレートとシャーシの部品に乗りました。走るたびにスピードが上がり、しっかりしていて感触も良かったです。今では3Dプリントして山で乗り心地を確かめ、翌日に再プリントする、というサイクルが出来上がっています。
Rome Snowboards リードプロダクトデザイナー、Justin Frappier氏
デザインチームが設計やテスト、試作・検証プロセスの反復というすべてのプロセスを完全にコントロールできるようになったことで、Rome Snowboardsはスノーボード用品の可能性の限界を押し広げ続けることができています。
「私たちは、どのカテゴリーでも業界初のことをやっています。常に、今までにないことをやろうとしているんです。そしてその度に、どんどん腕が磨かれていきます。既にROIも見えてきていて、試作品製作の工程を高速化しただけで、最初の5ヶ月で成果が見えました」とFrappier氏は言います。
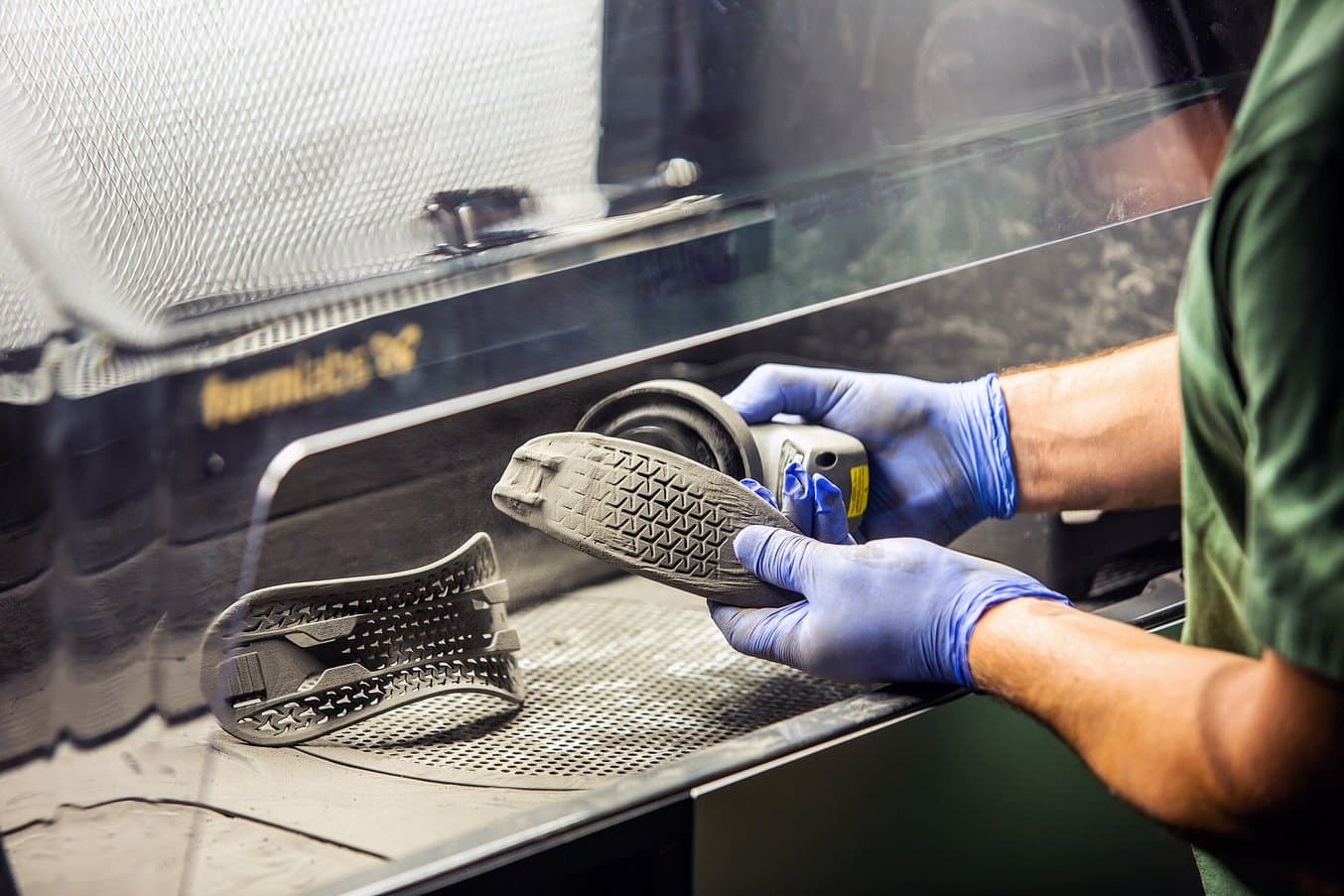
未焼結パウダーの除去・回収・再利用も、すべて1台で完結できる効率的な後処理装置、Fuse Siftで簡単に行える。
Fuseシリーズの3Dプリンタを活用することで、デザイナーは外注による部品製作を待つ間のダウンタイムを発生させずに、製品の機能テストを行い、改善を重ねることができます。Rome Snowboardsでは、Fuse 1の導入によって開発プロセスが大幅にスピードアップしました。お客様の用途でのFuse 1の有用性を確認したい場合は、無償サンプルパーツをリクエストいただくか、製品仕様に掲載の活用事例で詳細をご覧いただけます。