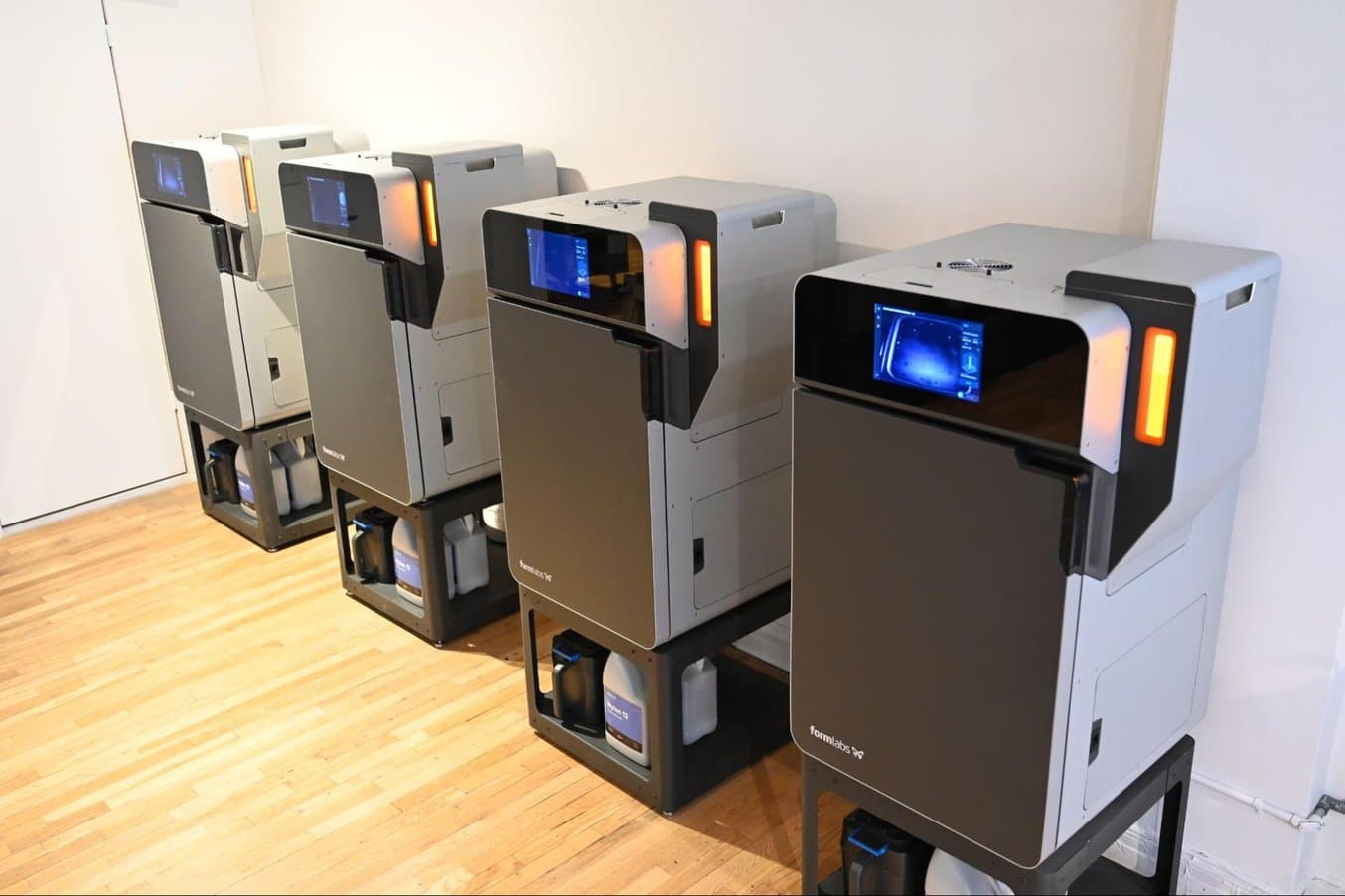
マンハッタンにある3Dプリント受託製造会社PrintPartsは、CEO 兼 創業者Robert Haleluk氏が掲げる「常に顧客の需要に基づき、業務を進化させる」という哲学を貫き、ニューヨーク最大のサービスビューローの1つに成長しています。同社は初期の試作品から実製品用の量産部品までを依頼するエンジニアリング企業数十社を取引先に持ち、常に進歩する顧客のニーズに合わせて事業を拡大することで、信頼できる製造パートナーとなっています。
しかし同社には長年抱えていた課題がありました。耐久性のあるSLS(粉末焼結積層造形)3Dプリントによる試作品や最終製品を求める顧客からの依頼です。最終部品を高強度で製造できる粉末ベースの3Dプリンタは、サイズ的に大き過ぎてマンハッタンにあるPrintPartsの施設内に搬入できず、またその導入コストも非常に高額であったため、顧客のニーズに応えるには粉末3Dプリントを再外注せざるを得ない状況が続いていたのです。
PrintPartsは、省スペースで現実的なコストで導入・運用ができる粉末ベースの3Dプリンタを常に探していました。そこでFormlabsのSLSプリンタ、Fuseシリーズの販売が開始されるやHaleluk氏とCOOのCody Burke氏はこれに飛びつき、4台のプリンタと後処理+パウダー再利用ステーションのFuse Sift2台を導入。そしてPrintPartsは米国内最大のFuse 1ユーザーとなったのです。
FormlabsがFuse 1を発表してすぐに「これこそ我々が求めていたプリンタだ、と私たちは社内で話し合いました。」とHaleluk氏は言います。
スモールスタートからのスケールアップ
Haleluk氏は2016年の5月、何台かのFDM方式3Dプリンタと共にWeWorkのオフィスでPrintPartsを立ち上げました。しかし彼が思い描くビジネスは常に、様々な3Dプリント品を多彩な顧客に供給することでした。Haleluk氏は、射出成形での経験値と強固な結束で結ばれたニューヨークの3Dプリントコミュニティでのコネクションを生かし、部品製造の外注を検討する顧客のネットワークを順調に拡大していきました。
「当時の私にとって、課題は常にボリューム、生産量でした。週産で1万個、最終的には月産10万点の部品を供給できるようになりたかったのです。設備の台数が増えれば生産数も向上します。」とHaleluk氏。
そのためには、24時間安定して稼動できる設備が必要でした。Haleluk氏はFormlabsのForm 2やMarkforgedのFFF(FDM)方式プリンタなど、デスクトップサイズの3Dプリンタに投資を続けました。そして低コストの設備で生産量を向上させ、数百点、数千点の部品を必要とする顧客に小ロット生産のサービスを提供できるようになったのです。
「私は常々、伝統的な製造方法を導入して顧客との長期的な関係性を構築する必要があると考えています。私たちの目標は、試作または生産設計の段階で専門家としてのアドバイスを提供し、アディティブマニュファクチャリングによる最終部品の大量生産の採用をサポートすることで、お客様のビジネスをサポートすることです。」
マンハッタンに3Dプリントの一大拠点を
2018年にマディソン・スクエア・パーク近くにある切手工場跡地に移転してからも、PrintPartsにとってスペースは依然として課題となっていました。ほとんどの受託製造会社は設備を設置するために巨大な倉庫を保有していますが、家賃が高額なマンハッタンにある顧客のすぐそばでビジネスを続けるということは、PrintPartsがレイアウトを工夫して可能な限りスペースを節約する必要があることを意味します。
「私たちが抱えている課題の1つは、明らかにスペースの問題です。大きな設備を置く余裕はなく、他にもいろいろな面で制約があります。Nylon 12が欲しいと思っても、自分たちではできないんです。」とBurke氏は言う。
PrintPartsにSLS 3Dプリントを導入する際の障害は、狭い出入口と小さなエレベータだけではありません。同社の設備導入に対する考え方は保守的で、具体的なビジネスケースが提示され、そこから得られる利益に疑問の余地がなくなるまで待ちの姿勢を貫いてきました。旧来の粉末3Dプリントシステムは、2000万から7000万円以上の投資が必要だったため、これまではSLSを導入する「方程式」が成立しなかったのです。Fuse 1の導入により、PrintPartsはニーズに応え、旧来の粉末3Dプリントシステム1台分以下のコストで、最終的に4台のプリンタを導入することができました。
Sculpteoが1,900社以上のエンジニアリング企業を対象に行った調査では、調査対象の72%が、3Dプリント方式選定時の最大の懸念は強度であると回答しています。一般的に、強度はPrintPartsのような新興企業には手が出せない価格の大型産業機械である粉末ベースの3Dプリンタでしか実現できませんでした。そのため産業用粉末プリンタで製造されたナイロン製部品の製造は外注先に頼らざるを得なかったのです。しかし、FormlabsがFuse 1を発表する以前は、そこにビジネスはあっても、現実的な価格とサイズのプリンタは存在しませんでした。
「Fuseのおかげで、以前から要望の多かったNylon 12による製造を内製化することができ、財務的にも非常に有利になりました。さらに重要なことは、Fuse 1の造形品の品質が別メーカーのもっと高価なプリンタで作った部品と同等以上であり、顧客がそれに満足しているという点です。多くのお客様にとっては以前の半分のコストで製造できるようになっているのです。」
Fuse 1の導入は、顧客とPrintParts双方にとって有益なものとなりました。Fuse 1の販売価格は、部品の製造単価と生産期間を確実に管理しながらプリンタを4台まで増設し、より多くの部品供給を可能にしました。
「Fuse 1でNylon 12製部品の提供を開始したところ、非常にうまくいきました。当社のお客様はより高品質な部品を求めており、SLSでのNylon 12はサポート材なしでプリントできるため、より高品質なプリントが行えます。実際にFuse 1を導入して以降、多くのお客様がよりコスト効率の高いSLSでの量産品質パーツを望んでいることがわかりました。そのためFuse 1でPA(Nylon)12、そして近いうちにPA(Nylon)11製の部品を供給できることを嬉しく思います。
Haleluk氏の推定では、約半数の顧客が詳細な設計と製造計画をもって同社に依頼し、残りの半数は、設計の微調整と材料選定を同社の専門知識を頼りに行う意向を持っています。外注コストの兼ね合いを考慮せずにFuse 1でのプリント品を供給できるようになったことで、PrintPartsはSLS顧客からの依頼のうち約30%を内製で賄えるようになりました。
Haleluk氏は、SLAやFDMのプリンタで複雑な格子構造のサポート材を作るより、パウダーベッドで完全に支持された状態でプリントする方が高品質に仕上がると判断した場合、その顧客にFuse 1でのプリント品を提案することも行っています。
「FDMやSLAでプリントする場合、オーバーハングやサポートが大量に必要になったり、形状が非常に複雑であったりする場合は、SLSを使えば造形作業も楽になります。サポート材が要らない粉末ベースの信頼できるシステムを持つことは、私たちにとってもう一つの切り札になっています。」
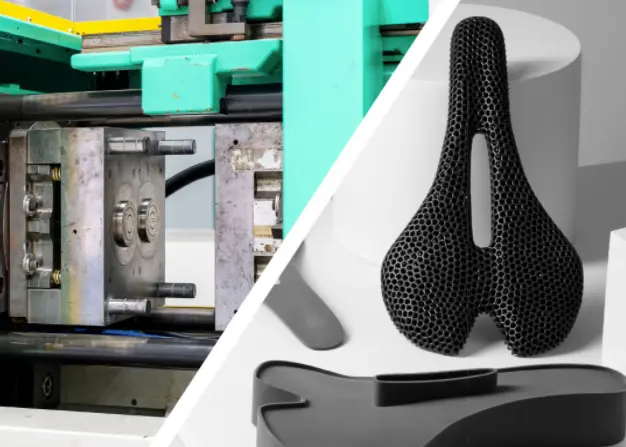
SLS 3Dプリント vs 射出成形:金型レスに切り替えるべき時は?
本ホワイトペーパーでは、射出成形とSLS 3Dプリントのメリットとデメリット、そしてSLSが補完的なソリューションとして活用できるケースについて解説します。
Fuse 1で切り拓く未来
HalelukとBurkeの両氏は、Fuse 1を活用した将来的なサービスについて、材料の幅が拡大するにつれてプリンタを増設し続けることを考えています。彼らの目標は、米国内最大のFuse保有台数を維持することだと言います。マンハッタンの高層ビルでは面積的に不足がありますが、PrintPartsはFuse 1を増やすことはスペースに見合うだけの価値があると確信しています。
「私たちは積極的に将来の可能性を追求しています。私たちは投資を行い、Formlabsの材料や技術にとても満足していますし、素晴らしい顧客と一緒に仕事ができています。」