Formlabsから新登場の光造形3Dプリンタ Form 4、そして生体適合性材料対応のForm 4Bは、液体レジンを硬化させて造形する次世代技術Low Force Display™(LFD)プリントエンジンに支えられています。
LFDプリントエンジンにはさらに6つの高度なサブシステムが搭載されており、超高速造形、確かな信頼性、優れた造形品質、豊富な高機能材料対応で業界に新たな基準を打ち立てます。
Low Force Display™テクノロジーとは
Form 4に搭載されている次世代Low Force Display™(LFD)プリントエンジンは、3Dプリンタの性能に関する業界基準を再定義し、ほかにはない確かな信頼性と造形スピード、造形品質、寸法精度、利用可能な材料の多彩性を、1台のプリンタで実現します。
LFDの基盤となっているのは、前世代機に搭載されていたFormlabsの独自技術Low Force Stereolithography™(LFS)プリントエンジンです。2011年以降、50,000社以上の企業が130,000台以上のFormlabs 3Dプリンタを利用して、4億点以上もの高性能部品を製作してきました。
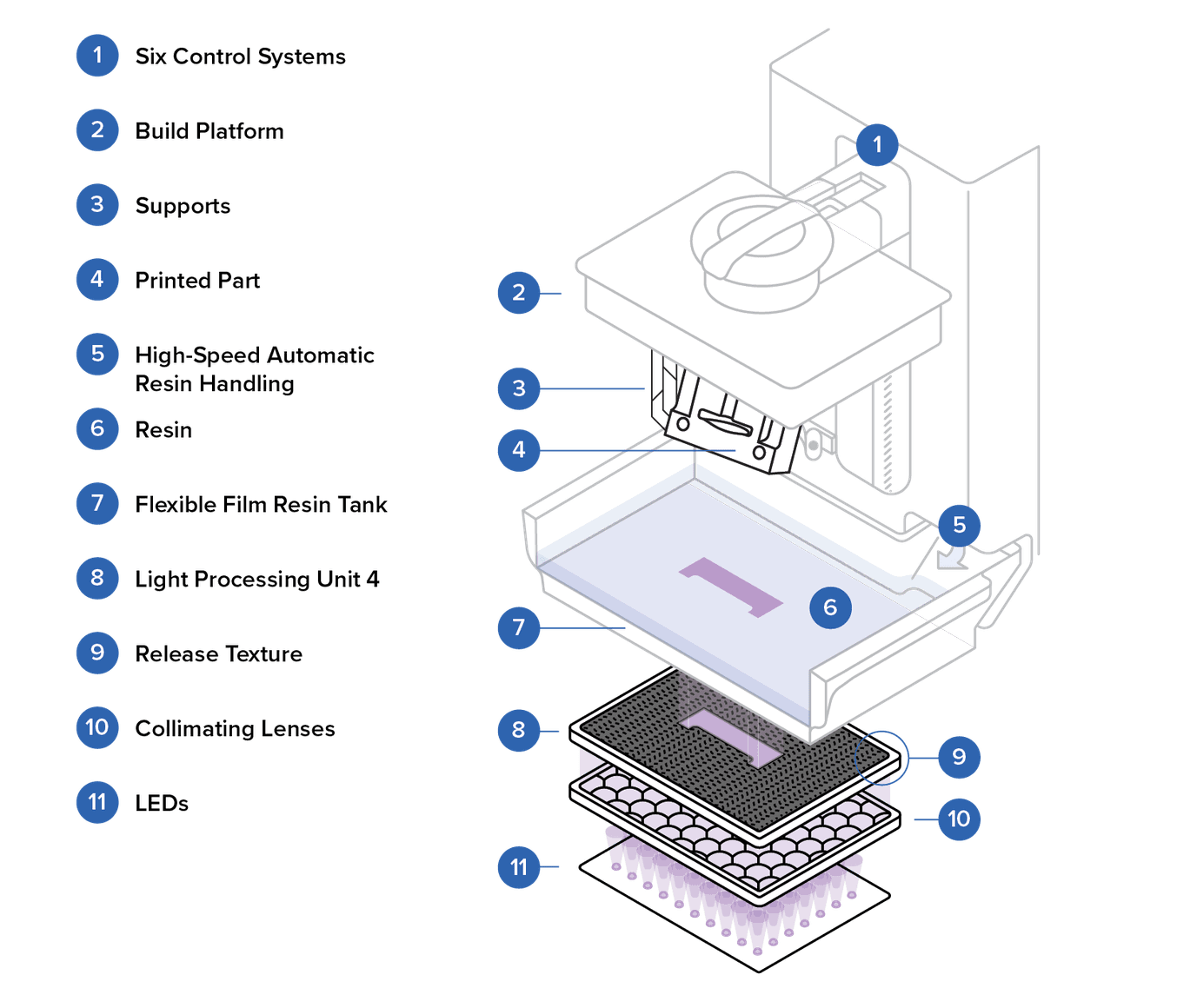
SLA光造形方式は、1984年に科学者のチャック・ハル氏が世界初の商用3Dプリントテクノロジーとして特許を取得した技術です。工業品質のラピッドプロトタイピングという新たな可能性を切り開き、Apple、Boeing、Fordといった大手企業の製品設計工程に革命的な変化を引き起こしました。しかし、当時はプリンタの本体価格やサイズ、仕組みの複雑さ、使用できる材料の制約などから、実際に導入できるのはFortune 500(フォーチュン500)に掲載されるような大企業に限られていました。
Formlabsは、2011年発表のForm 1でSLA光造形方式をデスクトップサイズに小型化することに成功し、エンジニアやデザイナーといった全く新しいユーザー層にも工業品質のツールを用いたプロトタイピングや量産の内製化という可能性を開きました。
2015年に発売されたForm 2では、デスクトップサイズのSLA光造形3Dプリンタをさらに進化させるべく、レジン自動供給機能、手間いらずの材料交換、最大造形サイズの40%拡大、タッチスクリーンによる操作、Wi-Fi接続、信頼性、幅広い高性能材料の提供といった機能拡充が行われました。
2019年には、LFSを搭載したForm 3とForm 3B(生体適合性材料対応)がリリースされました。LFSは光造形方式の一種で、レジンタンクの底を柔らかいフィルム製にし、リニア照明を活用したことで、造形品質と信頼性を画期的に高め、これまでより滑らかな表面品質と、造形品を剥がす際の負荷を軽減したことによるライトタッチサポートを実現しました。
最近では、光学システムによって造形スピードが大幅向上したこともあり、レーザー方式のSLA光造形からDLP方式やLCD方式に切り替えるメーカーが多くなっています。しかし、表面品質や信頼性、高精細さ、ハードウェアの耐用期間などを妥協しなければならないケースが多く見受けられます。Form 4のLFDプリントエンジンはこれらの課題を解決すべく、工業品質で求められるスピード、信頼性、造形品質のすべてを1台のプリンタで実現できるよう開発されました。LFDは、バックライトユニット、レーザーユニット(LPU)、リリーステクスチャ、統合カメラなど、さまざまな高度サブシステムを新たに搭載しているほか、柔らかいフィルム搭載のレジンタンクやレジンカートリッジ、レジン自動供給機能、インテリジェント制御システムにもアップデートを行い、機能を大幅に改善しました。
Form 4 | Form 3/B/+ | |
---|---|---|
造形方式 | マスク式光造形(MSLA)方式 | SLA光造形方式 |
プリントエンジン | Low Force Display™(LFD) | Low Force Stereolithography™(LFS) |
プリントエンジンの主要構成部品 | バックライトユニット レーザーユニット 4(LPU 4) リリーステクスチャ 底面に柔らかいフィルム採用の新設計レジンタンク インテリジェント制御システム レジンの高速自動供給機能 | レーザー レーザーユニット(LPU) 底面に柔らかいフィルム採用のレジンタンク レジンの自動供給機能 |
光源 | バックライトユニット(LED)、コリメートレンズ | レーザー |
レーザーユニット(LPU) | LCD(液晶ディスプレイ)、リリーステクスチャ | ガルバノメーター、ミラー、空間フィルタ |
最大造形サイズ | 200 x 125 x 210* mm 5.25リットル | 145 × 145 × 193* mm 4.05リットル |
* Form 4/Bで高さ190mm以上、Form 3/B/+で高さ185mm以上のモデルをプリントする場合、造形品を取り出す際にレジンタンクも一緒に取り外す必要があります。Form 4/Bで190mm以上、Form 3/B/+で185mm以上のプリントジョブを設定した場合、PreFormがユーザーに注意喚起を行います。
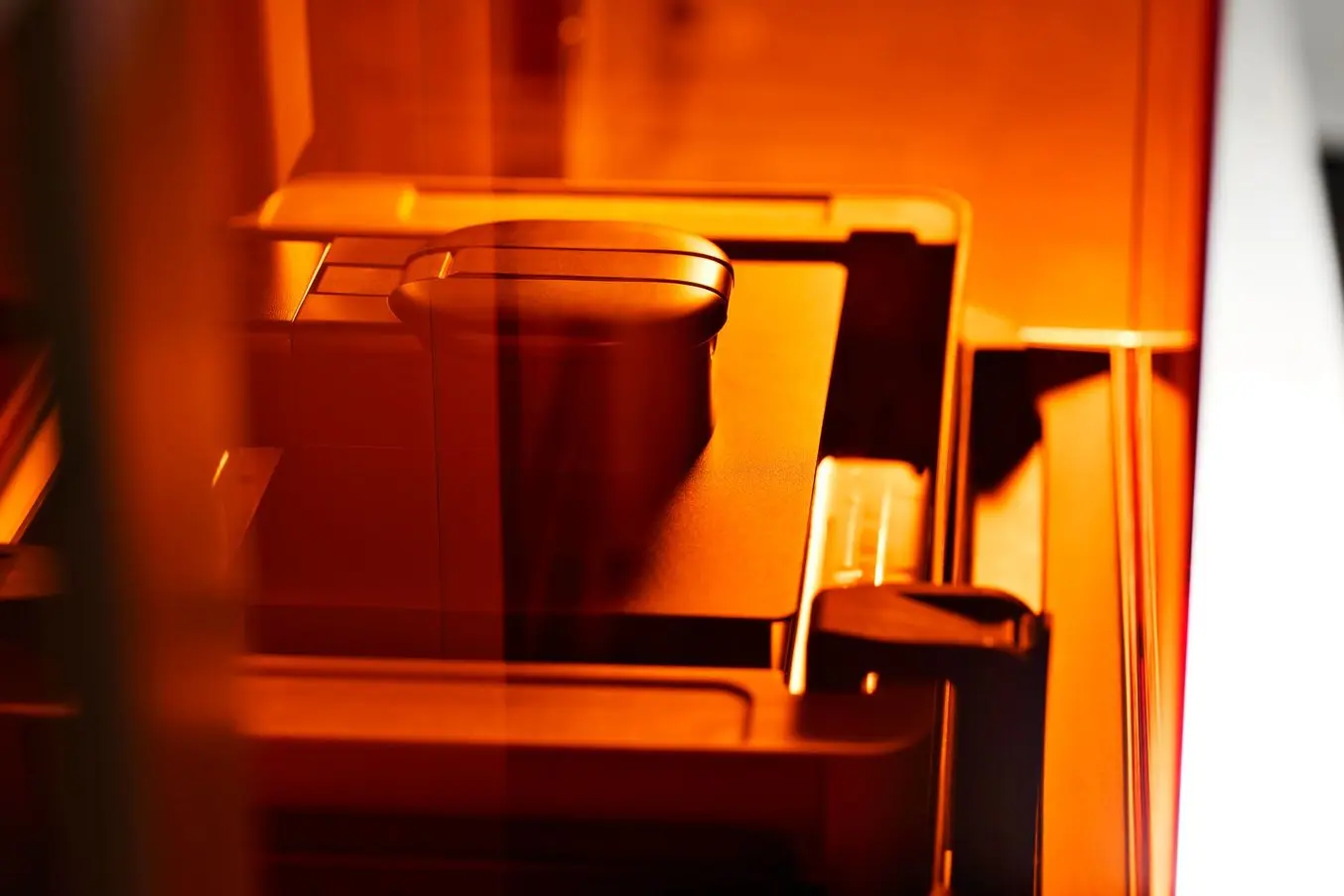
LFDの仕組み
LFDプリントエンジンの要となるのはバックライトユニットです。60個のLED、統合冷却システム、コリメートレンズを使用して光強度16mw/cm2の超高出力光線を照射することで、ビルドプラットフォームのどの箇所でも優れた造形品質と精度を維持しながら超高速造形を実現します。
バックライトユニットがレンズアレイを通してエリア一帯に満遍なく光線を投影することで、より平行かつ均一な照射が可能になり、明暗のムラを排除します。カスタムレンズアレイが平凸レンズで構成されていることで、高出力でも平行かつ均一な光線の照射が可能になります。
その後、光線はレーザーユニット(LPU)4を通過し、偏光板や光学コーティング、カスタム液晶ディスプレイによってモデルの各層の形に変形されます。ピクセルサイズ50μmの高精細LCDと事前設定済みのアンチエイリアスにより、シャープなディテール、滑らかな表面品質、厳しい公差にも対応する精度を実現します。カスタムLCDは光透過率が高く、光パワーを最大限に高めた状態でレジンに照射することで超高速造形が可能になっています。
既存のLCDベースの3Dプリンタとは異なり、LPU 4は耐久性が高く、常に一貫した品質で材料やモデルの高さに応じて600,000〜1,900,000層もの造形ができるよう開発・製造されています。さらに、金属フレームや傷に強い表面コーティング、スマートソフトウェア(残留物検出機能、荷重制限機能)でさまざまなダメージにも強い設計です。LPU 4の交換が必要になった場合でも、誰でも簡単に低コストでの交換が可能です。
光線がレジンタンク内の液体レジンに到達すると、一層分の液体レジンが即座に硬化し固い層を作ります。一層分が出来上がるとビルドプラットフォームが持ち上がり、Z軸が出来上がった層をレジンタンクの底から剥離します。
これまでの光造形方式では剥離時にかかる力が大きな課題となり、ユーザーは3Dプリンタ選定の際に造形品質、信頼性、造形スピードのいずれかを諦めなければなりませんでした。Form 4では、新たな独自技術リリーステクスチャと新しくなったFlexible Film Resin Tankで剥離力を最小限に抑えます。
リリーステクスチャとは、独自のマイクロテクスチャが施された光学フィルムで、空気の通り道を作ることでレジンタンクがLPUに吸着してしまうのを防ぎます。
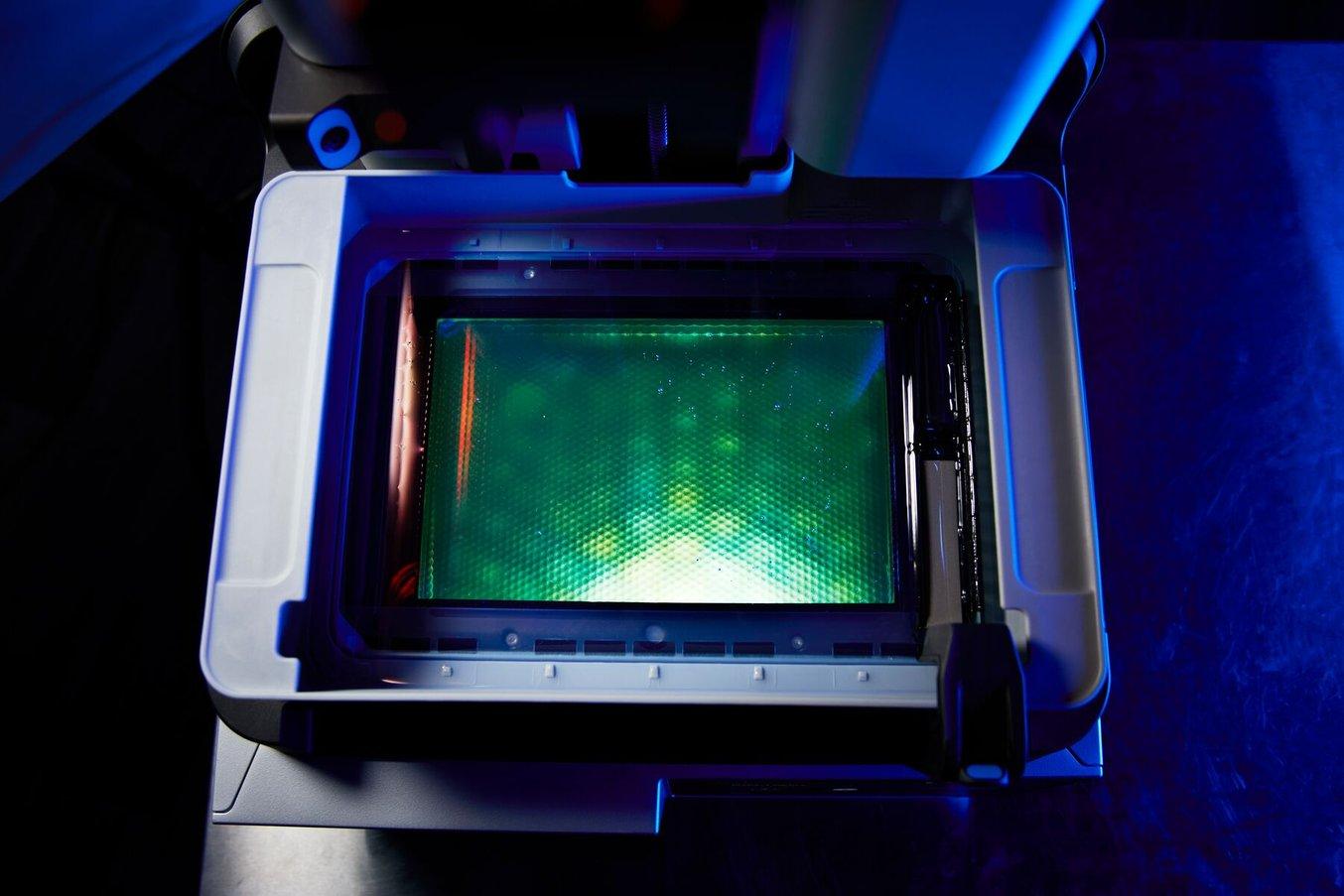
Form 4のカスタムレンズアレイは平凸レンズでできており、高出力でも平行で均一な光を照射可能。
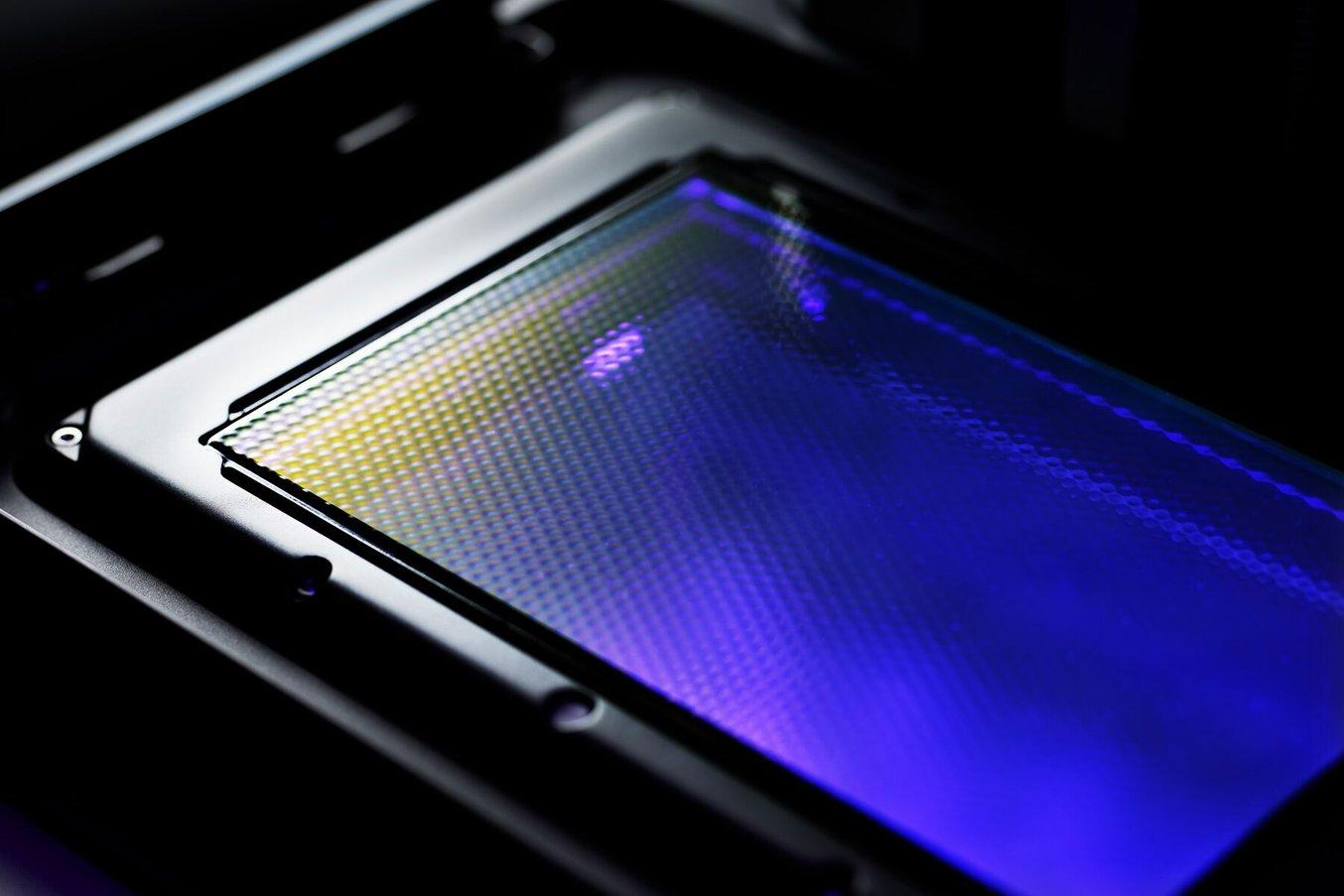
独自のリリーステクスチャで空気の通り道を作り、レジンタンクがLPUに吸着するのを防ぐ。
Form 4でデザインが新しくなったレジンタンクがプリンタ内部で液体レジンを受け止め、液体レジンが硬化する基盤を提供します。レジンタンク底面には2層の柔らかいフィルムが採用されており、硬化済みの層の端から優しく引き離すことで、造形中に各層にかかる剥離力を低減します。
リリーステクスチャと柔らかいフィルム採用のFlexible Film Resin Tankがそれぞれ造形中にかかる負荷を大幅に低減することで、Form 4は超高速ながら滑らかな表面品質と細かなディテール表現を実現しています。さらに、ライトタッチサポートで積層痕を最小限にとどめ、射出成形品に匹敵する製品を高速かつ安定して製作できます。
レジン自動供給機能の向上と新材料
これまではプリント開始前にレジンの予熱を待たなければなりませんでしたが、Form 4ではもう必要ありません。レジンヒーターと赤外線温度センサー搭載のForm 4は、レジンの予熱時間を短縮し、最短で造形を開始できます。ヒーターと赤外線センサーがレジンの温度を正確に制御することで、粘性の高い材料も使用できるようになります。
さらに、2層のフィルムがついたFlexible Film Resin Tankは耐久性に優れ、維持費と廃棄物を最小限に抑えます。フィルムの上層は耐薬品性と柔軟性を備え、硬質で丈夫な下層は傷や穴などのダメージに強い設計です。レジンタンクは、プリンタに装着するためのラッチやレジンを簡単に充填できる注ぎ口が付いているほか、レジンこぼれを防ぐ大容量サイズ(プリントしていない時は2.3L)で使いやすい設計になっています。
レジンタンクには再利用可能な蓋が付いており、在庫として複数のレジンタンクがある場合も縦に積み重ねての保管が可能です。レジンの色や種類ごとに別々のタンクが使用できるため、材料の切り替えもタンクを入れ替えるだけで簡単に行えます。
耐用期間いっぱいまで使え、Formlabsが提供するどのレジンでも安定した品質で75,000層以上を造形できるよう設計されています。Flexible Film Resin Tankの価格も前世代に比べて33%減となり、これまで以上に新しい材料を試しやすくなるほか、運用コスト削減も見込めます。
また、レジンタンクに簡単に装着できる高速レジンミキサーのおかげで、造形時間にほとんど影響を与えることなくレジンを迅速かつ均一にかき混ぜることができます。これにより、どんなサイズのモデルでも優れた造形品質と精度を維持し、ビルドプラットフォームのどの箇所でも造形が可能です。レジンミキサーは取り外し可能で、材料が同じなら異なるレジンタンク間でも簡単に使い回すことができます。つまり、Form 4でプリントする予定の材料1種類ごとに1つのミキサーを準備すればよく、廃棄物の量を削減できます。
レジン自動供給システムにより、手作業での充填作業が不要になります。使用するレジンの粘性にもよりますが、新設計のバルブでこれまでより流量が増え、Form 3と比較して5~10倍も速く材料を充填できるようになりました。Form 4のレジンカートリッジ容量は1Lですが、Form 3のカートリッジよりもプラスチック使用量が63%低減、サイズも30%小型化しており、廃棄物の削減と効率的な在庫保管が可能です。プリンタに装着後はカートリッジのロードセルがカートリッジ内のレジン量を計測し、残量を明確に表示するため、レジンの管理がしやすいのも特徴です。
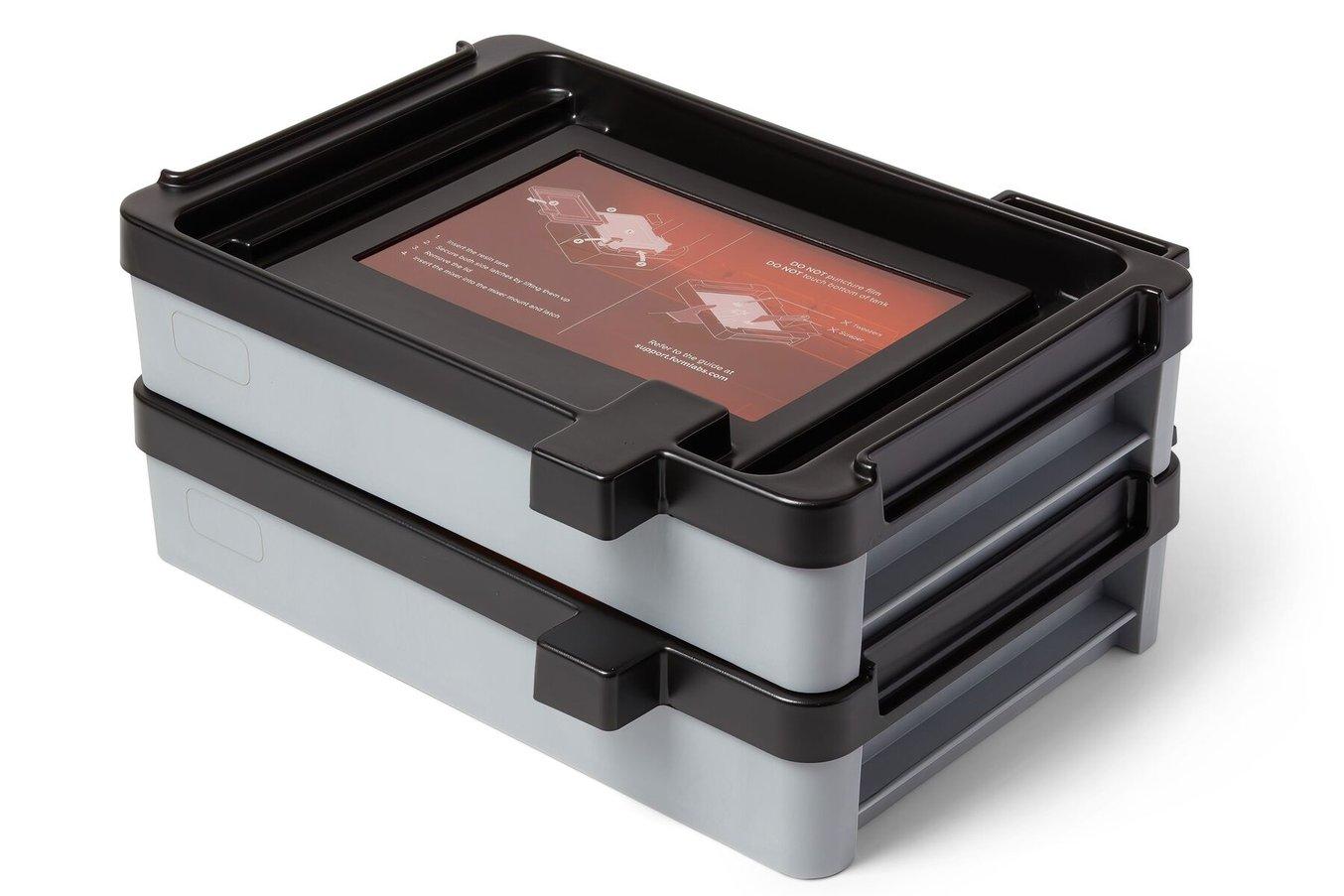
Form 4のFlexible Film Resin Tankには再利用可能な蓋がついており、レジンタンクを積み重ねて保管がしやすい。
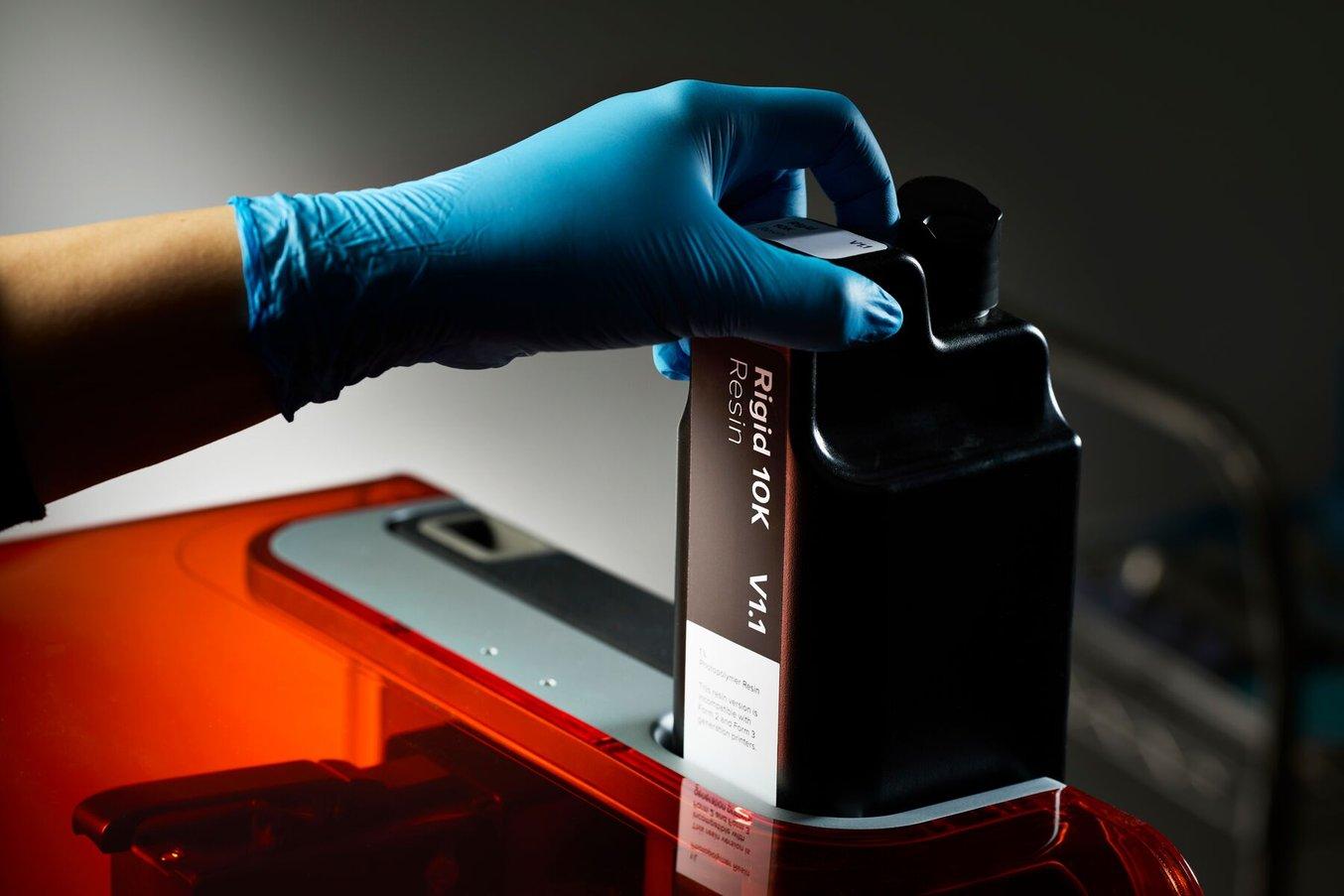
新しくなったレジンカートリッジ容量は1Lだが、プラスチック使用量が63%低減、サイズも30%小型化したことで廃棄物の削減と効率的な在庫保管が可能に。
Form 4はFormlabs材料ライブラリのうち、造形速度、強度、精度、外観が向上した新登場のレジン6種を含む23種類の高機能材料に対応しています。
- スタンダードレジンV5(Clear、Grey、Black、White)は、これまでより強度や色合いが向上したほか、Form 3の2倍〜5倍も速く造形が可能です。
- Fast Modelレジンは、試作品や歯列矯正器具の高速製作を可能にします。
- Precision Modelレジンは、常に高いフィット感を実現する高精度な歯科モデルの製作に最適です。
材料の詳細については、Formlabsの材料ライブラリをご覧ください。
合理化されたユーザーエクスペリエンス
Form 4では、Form 3+の直感的なユーザーエクスペリエンスはそのままに、さらなる機能強化が行われています。Wi-Fi接続(無線)、イーサネット接続(有線)、USBポート、電源スイッチ搭載のこれまでになく使いやすいプリンタで、ビジネスのどんなニーズにも対応します。機能強化により、Form 4は前世代機よりも自立性とインテリジェンスが向上し、ユーザーが他の作業に集中しやすい環境を提供します。

Form 4で強化されたタッチUIにより、診断やキューの管理がさらにしやすく。誰のプリントジョブを実行中か一目でわかる表示で、プリンタに付箋を貼って管理する必要がなくなる。
7インチのタッチスクリーン搭載で、操作はすべて直感的なタッチUIで行います。スクリーンには予防メンテナンスのリマインダ、プリントジョブのステータス、プリンタの準備状況などが表示され、3Dプリントの操作がかつてないほど簡単かつ直感的になっています。
プリンタ名とステータスが常時表示されることで、これまでのようにプリンタに付箋を貼って管理する必要がありません。また、5分間操作が行われない状態が続くとスクリーン上にプリンタ名、レジン、プリンタの準備状態が大きな文字で表示されるため、一目でプリンタの識別と使用状況を確認できます。
事前準備の時間が短縮されたことで、ユーザーはForm 4を起動後1分以内に他の作業に取りかかることができます。プリンタの準備完了後、プリントジョブをコンピュータからプリンタに送信するだけで、あとはForm 4が自動で造形を開始します。
予防メンテナンスのリマインダや診断ツールがスクリーン上に表示されることで、プリンタのスムーズな運用をサポートします。問題が発生した場合はエラーメッセージにサポート記事のQRコードが表示され、問題の解決を可能な限り早めます。
多言語オプションの拡大など、さまざまな新機能も今後のファームウェアアップデートで続々と追加される予定です。
インテリジェント制御システムと統合カメラ
Form 4に搭載されている6つの制御システムが、庫内の温度やレジン量、造形時の荷重、造形状況を正確に測定・維持します。カートリッジロードセルセンサーと伝導ヒーターによる予熱に加え、Form 4にはプリンタのレベリングセンサー、レジンレベルセンサー、統合Z軸荷重センサー、カメラが搭載されています。
プリンタのレベリングセンサー:Form 4の電源を入れると、タッチスクリーン上に自動的にレベリング(水平取り)の操作手順が表示されます。ユーザーは画面に表示される指示に従い、付属のツールでプリンタの脚の高さを調整します。プリンタを水平に設置することで、レジンレベルセンサーがレジンタンク内の液体レジンの量(レベル)を正確に測定でき、常に精度の高い造形が可能になります。
レジンレベルセンサー:レジンタンク内のレジン量を正確に測定し、その情報に応じてレジン自動供給システムを制御することで、レジンレベルや造形性能を常に一定に保ちます。
Z軸荷重センサー:造形中に各層にかかる荷重を測定し、自動的にZ軸の動きを調整することで荷重を最小限に抑えます。これにより、使用材料にかかわらずどんな形状のモデルも、造形速度、造形品質、信頼性の最適なバランスで造形が可能になります。
カメラ:ビルドチャンバー内のカメラが造形完了時の写真を撮影し、Formlabs提供のプリンタ管理ソフトウェアDashboardにアップロードします。Dashboardで造形結果をどこからでも確認できることで、リモート監視やプリント履歴の確認をかつてなく簡単に行えるようになります。この機能を使用したくない場合は、カメラをオフにする、カバーをかける、カメラを取り外すなどの方法で、撮影機能を実質的に無効化できます。
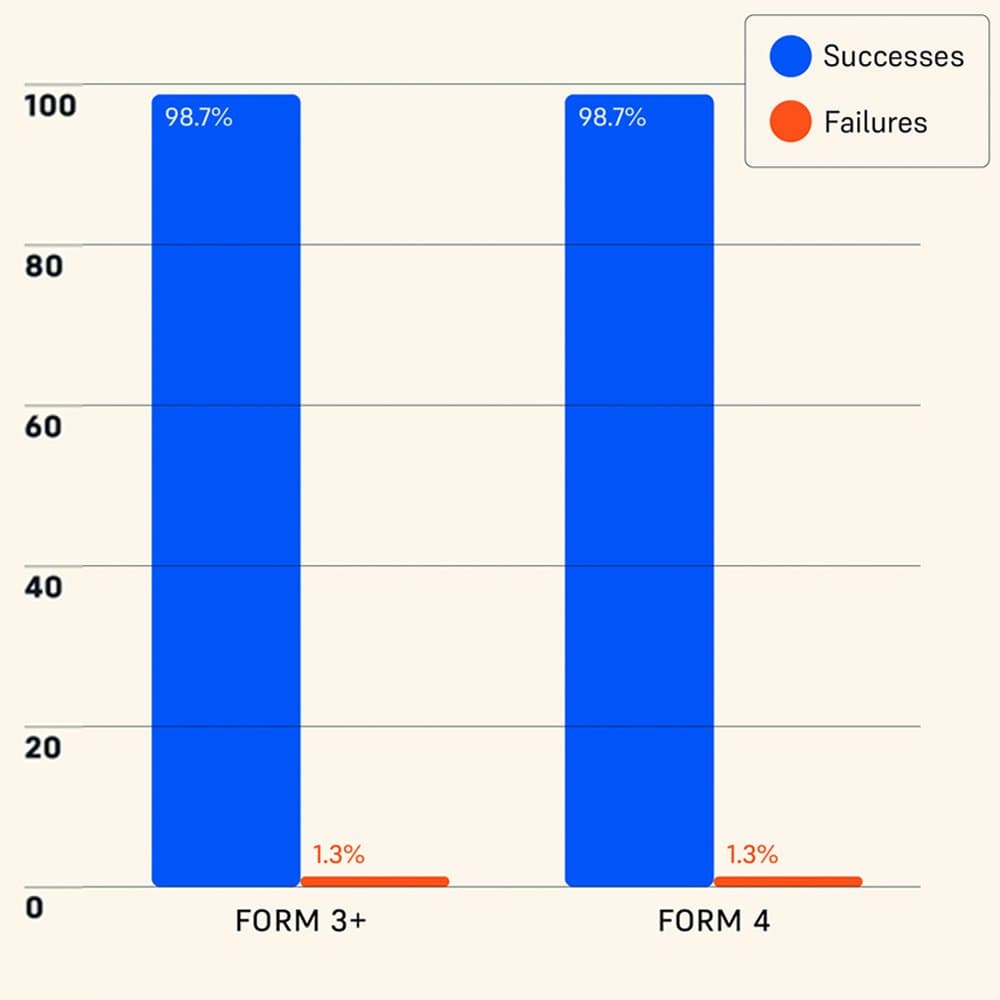
Form 4と他社製光造形3Dプリンタの信頼性に関する第三者試験
独立試験機関により、Form 4 のプリント成功率は 98.7 % と評価されました。テスト方法と結果の詳細についてはこちらの技術資料でご確認いただけます。
ビルドプラットフォーム
造形を最適化し、造形品の取り外しを簡単かつ迅速に行えるよう、2種類のビルドプラットフォームが用意されています。予備のビルドプラットフォームをご購入いただくと、作業をより高速化し、ノンストップでの連続造形も可能になります。
Form 4の新たなBuild Platformの造形面は、耐久性の高いアルミ製です。特許取得済技術、クイックリリーステクノロジー(Quick Release Technology)を搭載したBuild Platform Flexは、専用のツールを使うことなく造形品を僅か数秒で取り外すことができます。また、Build Platform Flexでは造形品取り外しの際に破損してしまうリスクも回避でき、ワークフローをさらに効率化できます。Build Platform Flexの造形面は、長期間の使用にも耐えられ傷の付きにくいステンレス製です。サポート材を使わず造形面に直接プリントできることで、材料コストや後処理にかかる時間を削減できます。
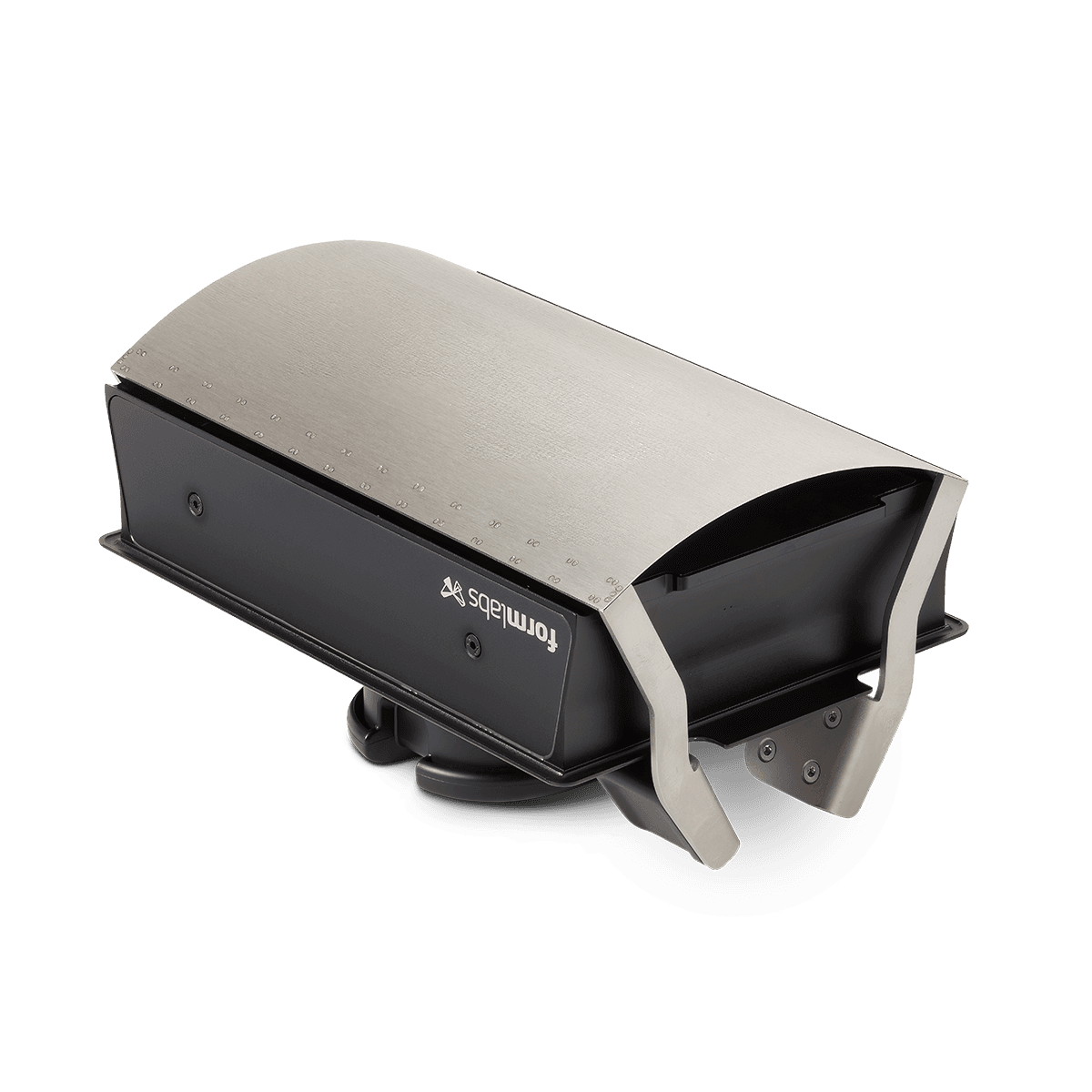
Form 4 Build Platform、Build Platform Flexともに、造形面のサイズは200 x 125mmで、Form 3 Build PlatformやBuild Platform 2の145 x 145mmに比べて造形可能なエリアが拡大しています。
Form 4 Build PlatformとBuild Platform Flexだけでなく、Build Platform(Form 2、Form 3/B/+用)、そしてBuild Platform 2(Form 3/B/+用)のいずれも、第2世代Form Washでご利用いただけます。
Build Platform | Build Platform Flex | |
---|---|---|
クイックリリーステクノロジー(Quick Release Technology) | なし | あり |
使用可能なレジン | すべてのレジン | すべてのレジン(柔軟材料や軟質材料を使った造形品では、クイックリリースによる迅速な取り外しができない可能性がありますが、その場合でも付属のツールを使って手作業で簡単に取り外すことができます) |
Form Wash(第2世代)に対応 | あり | あり |
妥協しない3Dプリントを実現
ものづくりは難しく、一瞬たりとも時間を無駄にできません。Form 4の開発にあたり、Formlabsのエンジニア何よりも重視したのは、スピード、信頼性、精度、材料のパフォーマンスでした。Form 4の機能を支えているのは、お客様の期待を製品をお届けするために、膨大な時間をかけて行った研究開発です。
プリンタが届いたその日から、高精度部品を超高速で造形いただけます。Form 4またはForm 4Bのご購入に関するご相談、またはさらなる詳細情報をご希望の場合は、Formlabsのスペシャリストまでお気軽にお問い合わせください。