Help3Dの創設者Andrea Pirazzini氏は、12 Pollici Italian Cupチャンピオンシップで自身が乗ったピットバイク用のインテークマニホールドをFormlabsの3Dプリンタで製作しました。
Pirazzini氏のチームがモーターサイクルの機能向上を目指す際は、できる限り直線的な出力を目指し、局所的な圧力の低下を引き起こす可能性のあるフランジは使用せずに馬力を制限できるよう、流体力学解析を取り入れてマニホールドの絞り型の設計をしてきました。
その中でPirazzini氏は3Dプリントに注目したわけですが、それは同じ部品を低コストで何種類も造形し、翌日にテストをして本番のサーキットで優位に立てるよう改良を重ねられると考えたからです。実際、Pirazzini氏のチームメイトであるElia Marescutti氏は、3Dプリント製のマニホールドを搭載したバイクで2021年のチャンピオンシップ優勝を果たしました。本記事では、Pirazzini氏がどのようにこのプロジェクトを進めてきたのかをご紹介します。
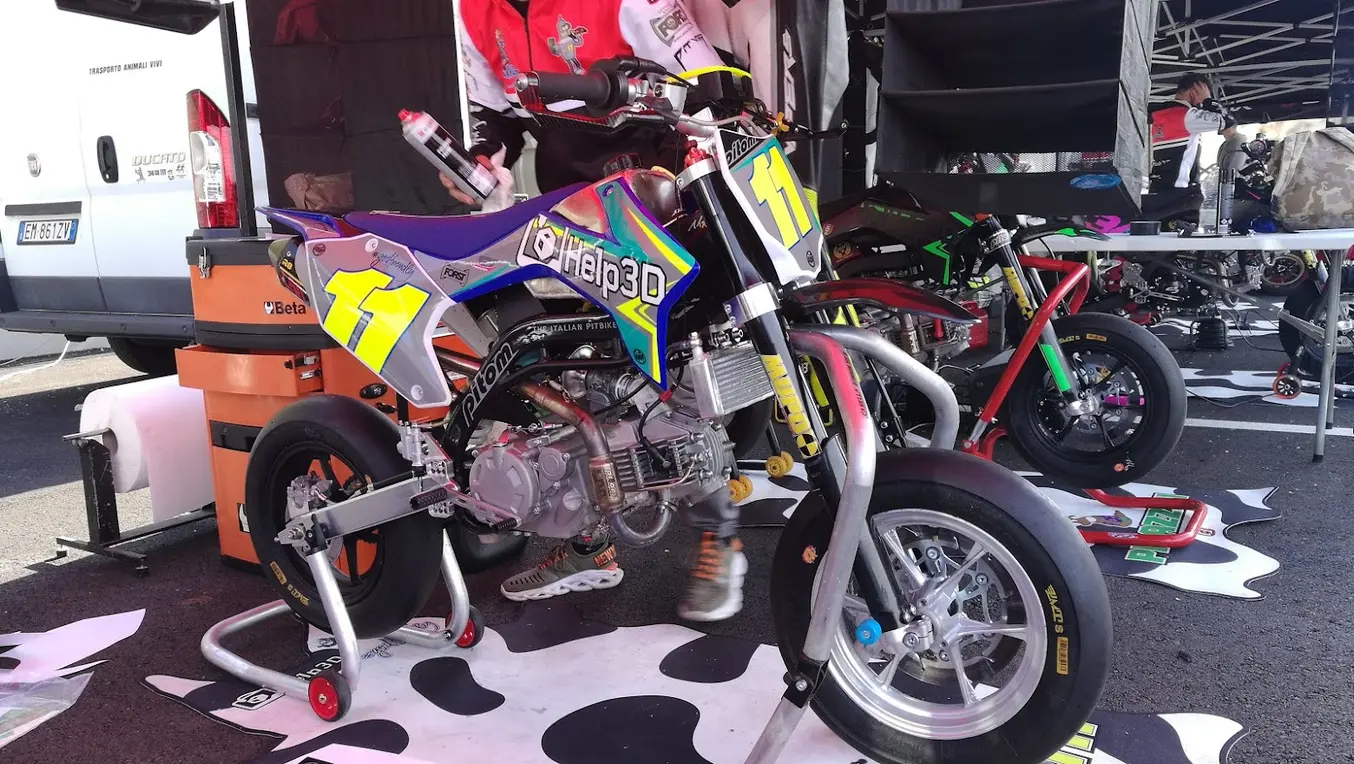
2021年のS1 Overチャンピオンシップで優勝したElia Marescutti氏のバイク。Form 3でプリントした特注のマニホールドを搭載。
マニホールドのリバースエンジニアリングで性能を最適化
Pirazzini氏がモーターサイクルに乗り始めたのは2012年。それ以降、ストップウォッチのサポートブラケットなどを始め、自身のバイクに使用する細々とした部品を3Dプリントで製作してきました。当初、機能性と耐熱性に優れた部品を3Dプリンタで製作することには躊躇していたPirazzini氏ですが、Rigid 10K Resinの発売で状況が一変します。
材料特性を詳しく調べていくうちに、従来はアルミを切削加工して作っていたインテークマニホールドを3Dプリンタで製作したら面白いプロジェクトになるかもしれない、と考えたのです。彼は過去にFDM(熱溶解積層)方式を試したことがありますが、その時は空気の漏れによりキャブレターやエンジン出力が損なわれ、期待した結果が得られませんでした。
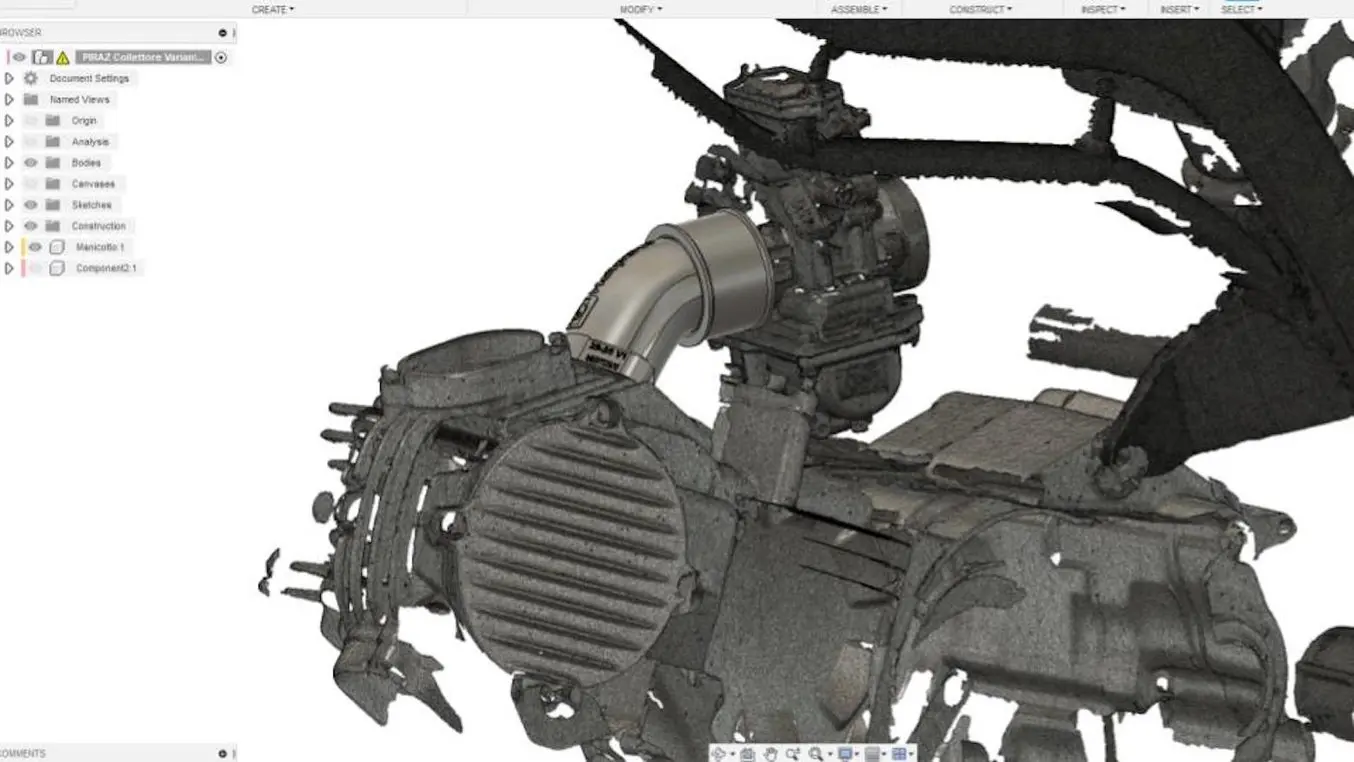
ピットバイクのエンジンの3Dスキャン。
プロジェクトの開始にあたり、Pirazzini氏はまず3DスキャンとAutodeskのFusion 360を使ってマニホールドのリバースエンジニアリングから始めました。2ストロークエンジンのフレームとキャブレターを3Dスキャンすることでマニホールドのサイズを正確に測定でき、フレームやマフラーに接触しない位置にキャブレターを設置することができました。また、インテークトランペットとインテークダクトも設計しました。CADを使用したことでシリンダーヘッドの吸気口の直径をキャブレターと合わせることができ、段差や圧力低下、乱流の発生を避けることができました。
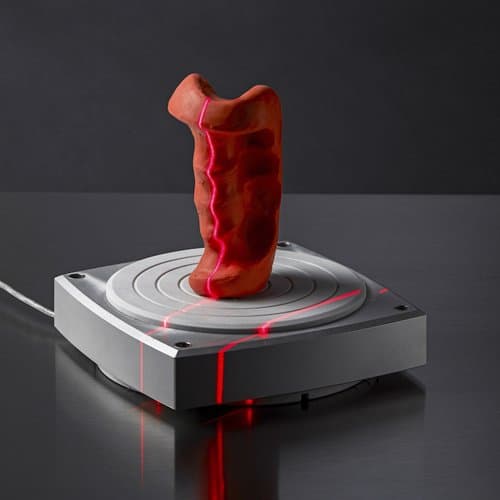
3Dスキャンを活用したリバースエンジニアリング、修復、計測
3Dスキャンや3Dプリントは、複製や修復、リバースエンジニアリング、計測などの分野でも活用できます。本技術資料をダウンロード、もしくはウェビナーをご視聴いただくと、3Dスキャンと3Dプリントがこれらの用途でどう活用され、設計手順の洗練化につながっているかをご確認いただけます。
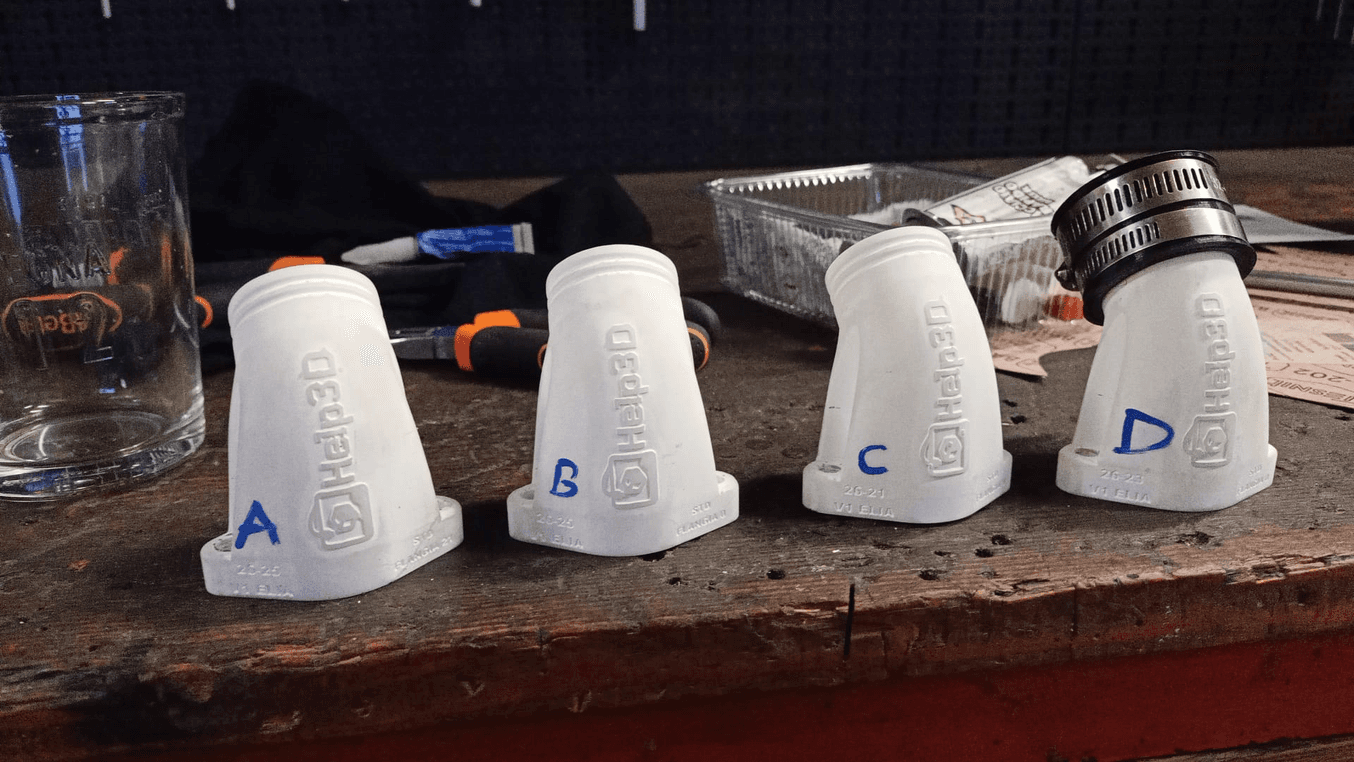
Form 3でプリントした様々な種類のインテークマニホールド。
Pirazzini氏は、最大出力を制限するためにマニホールドを取り外さなければならない場合に備え、直線性を失うことなく出力を制限できるサイズのマニホールドを3Dモデルで作成しました。そのモデルを使ってテストベンチで試運転し、エンジンの種類ごとに適切なマニホールドを見つけることができました。
その結果、従来のように馬力を損なうことなく、エンジンの回転数を上げてデリバリーカーブを延長することができました。つまり、3Dプリント製のマニホールドではチャンピオンシップの規則制限を守りながら、標準的な切削加工のマニホールドと比較してエンジンの馬力を約1馬力、ほぼ10%向上させることができたのです。
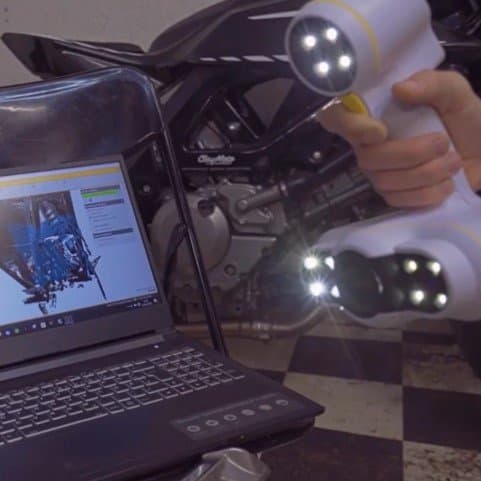
3Dスキャンで現代の製品開発をサポート
本ウェビナーでは、Peel 3Dを用いながら、3Dプリント工程に3Dスキャンを導入することで製品開発プロセスを改善する方法をご紹介します。
Rigid 10Kレジンで耐熱性に優れた部品を製作
Pirazzini氏が新しく設計したマニホールドは、Rigid 10Kレジンを使ってForm 3で積層ピッチ100ミクロンでプリント。積層痕がほとんど目立たない滑らかな表面に仕上がりました。表面処理には従来通り耐水性のサンドペーパーを使いました。FDM方式で製作したマニホールドの場合は外部や内部に防水処理を施す必要がありますが、SLA光造形方式なら最初から剛性と防水性の高い部品を製作できます。
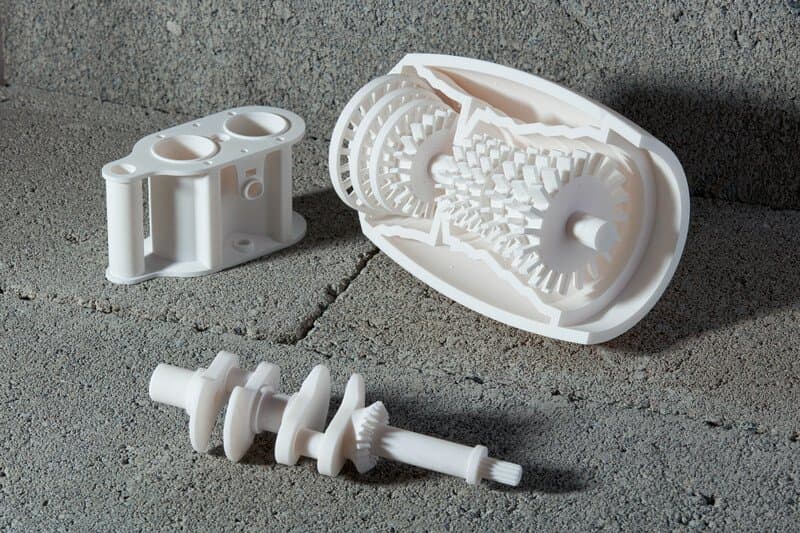
無償サンプルパーツのお申込
Rigid 10Kレジンは、Formlabsのエンジニアリング系レジンで最高の剛性をもつ材料です。Formlabsの品質を直接手に取ってご確認ください。サンプルパーツを無償でお届けいたします。
造形時間はマニホールドの厚みやサイズによって変動しますが、通常は2時間〜2時間45分の間で、各部品の造形単価は€10〜€12程度です。Pirazzini氏は一晩で7種類ものマニホールドを製作し、そのまま翌日にテストすることができました。
Help3D創設者 Andrea Pirazzini氏
「PreFormは、3Dプリント業界で最もシンプルかつ優れた機能を提供してくれる造形準備ソフトウェアです」
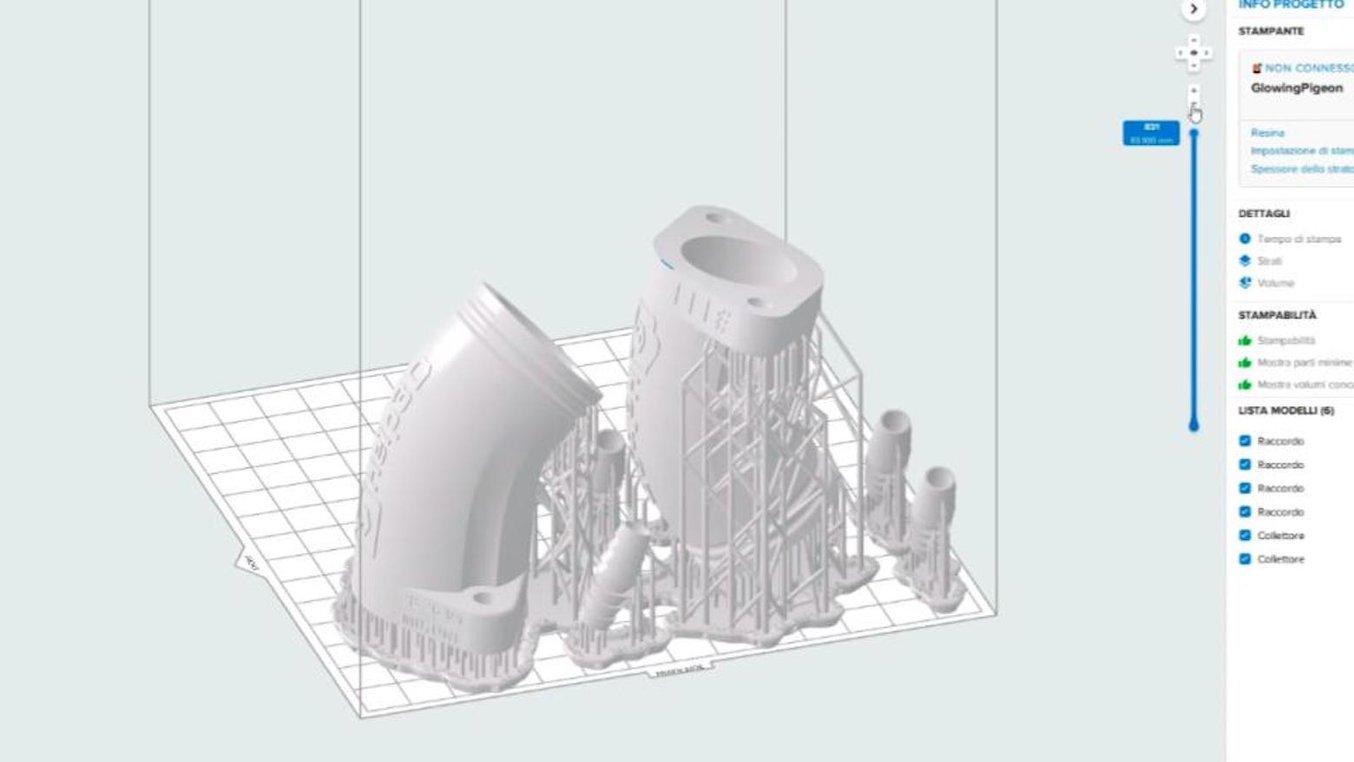
PreFormで造形準備中の2種類のインテークマニホールド。
造形準備ソフトウェアのPreFormでは、造形品を手動で配置することも自動で向きや角度を調整することもできます。Pirazzini氏は、この自動調整機能が特に便利だと教えてくれました。サポート材の数を最小限に抑えつつ、ユーザーが必要だと感じたら手動で追加・削除が行えるからです。また、プリントジョブの中で要となるエリアにサポート材が不足している場合もソフトウェアが通知してくれます。
Help3D創設者 Andrea Pirazzini氏
「Form 3で特に素晴らしいと思うのは、サポート材と造形品の接点が非常に小さく、サポート材を取り除く際に痕がほとんど残らないことです」
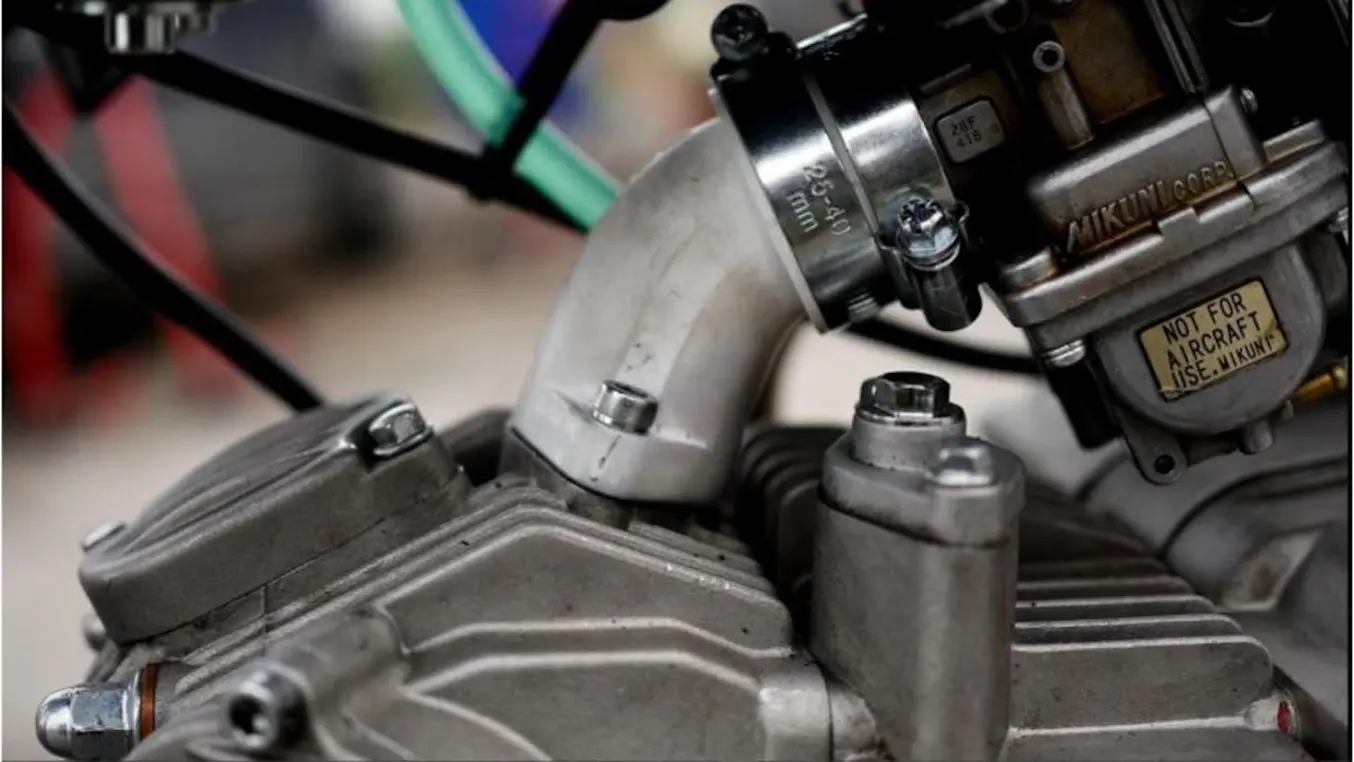
3Dプリント製品の実力
Pirazzini氏がForm 3で3Dプリントしたマニホールドは、高温と低温のどちらにも完璧に耐え、今でも彼のピットバイクに搭載されています。サーモグラフィを使った検証では、Rigid 10Kレジンの熱的特性が格段に優れていることもわかりました。3Dプリント製のマニホールドに冷却フィンを搭載した場合、従来のアルミ製のマニホールドと比べて40~50度も低い温度を保っていることがわかったのです。さらに、外気温度が約33度にものぼる屋外で20~25分間のレースを行った後でさえ、火傷することなくマニホールドに触れるほど低温を保っていました。
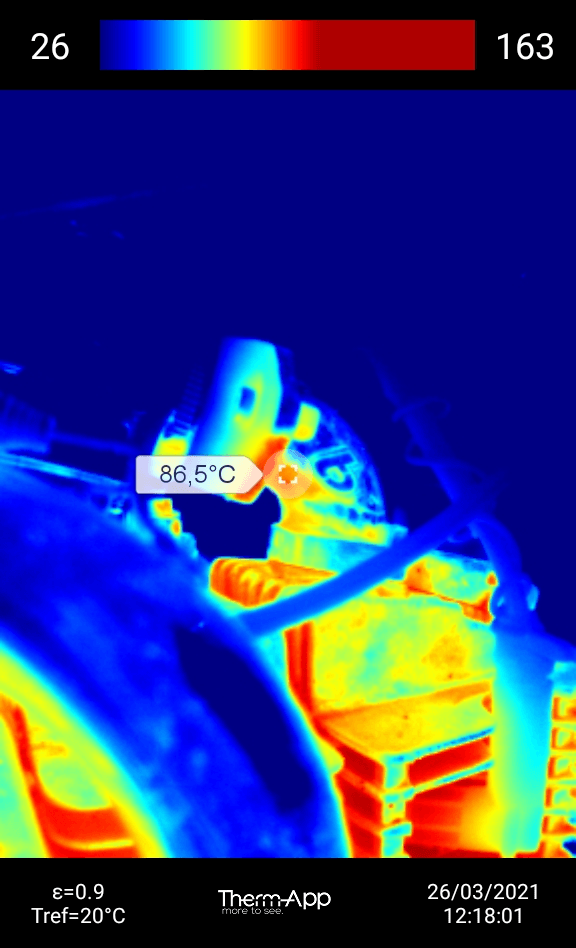
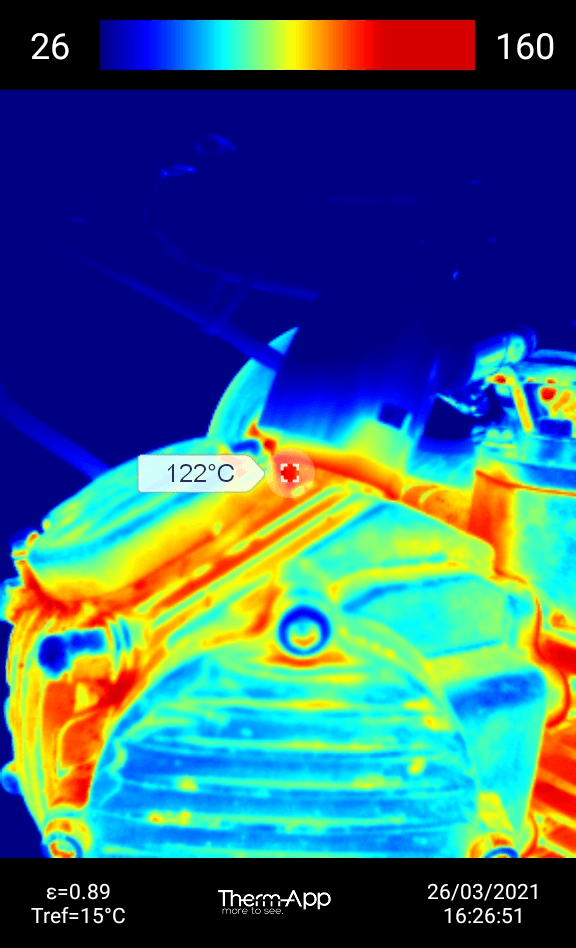
今後のプロジェクト
今回ご紹介したインテークマニホールドは、Rigid 10Kレジンで実現した活用例のごく一部です。インテークマニホールドの製作後、Pirazzini氏は、同材料を2ストロークエンジンのリードバルブ、タペットカバー、シリンダーヘッドのカップリング用のフランジ、その他耐空性が求められる様々な部品の製造にも活用できるのではないかと期待しています。