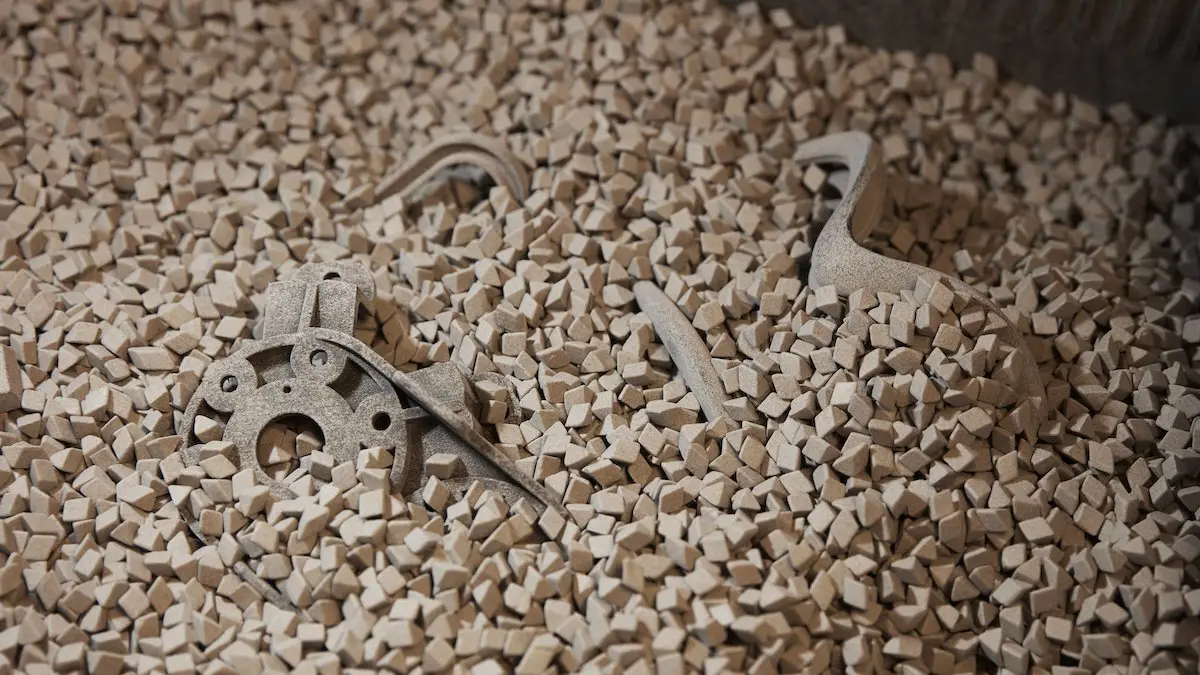
振動仕上げと呼ばれることもある振動バレル研磨は、さまざまな材料で製作した部品の表面の硬度や滑らかさを向上させる確立された方法です。元々は加工品やプレス後の金属ワークからバリを取り除くために使われていましたが、現在では3Dプリント品の表面を滑らかにする方法としてバレル研磨を使うメーカーが増えています。
特に、SLS(粉末焼結積層造形)方式で3Dプリントした部品は表面が僅かにざらついた手触りになることがありますが、バレル研磨を行うことで、実製品用部品として使用可能な表面に仕上げたり、機能アセンブリにもスムーズに組み込むことが可能です。
本記事では、SLS 3Dプリント製部品のバレル研磨(振動仕上げ)についてご紹介します。また、以下のウェビナーでは研磨機の比較や試験結果、作業工程の詳細をご覧いただけます。
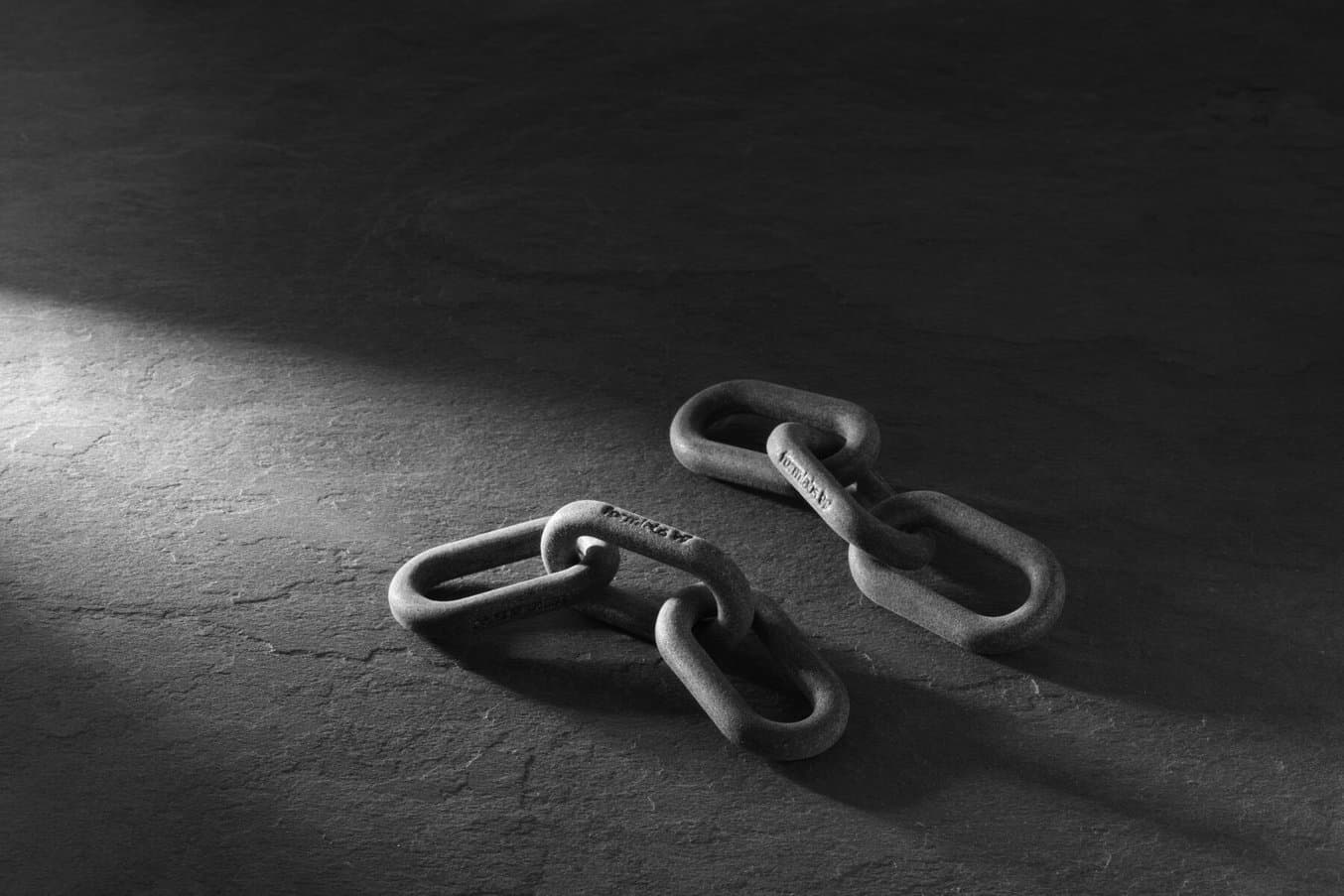
バレル研磨でSLS 3Dプリント品の表面を滑らかに
本ウェビナーでは、お客様の工程に合った機械や材料の選び方を詳細に解説するとともに、優れた表面品質を実現するためのベストプラクティスもご紹介します。
バレル研磨のメリット
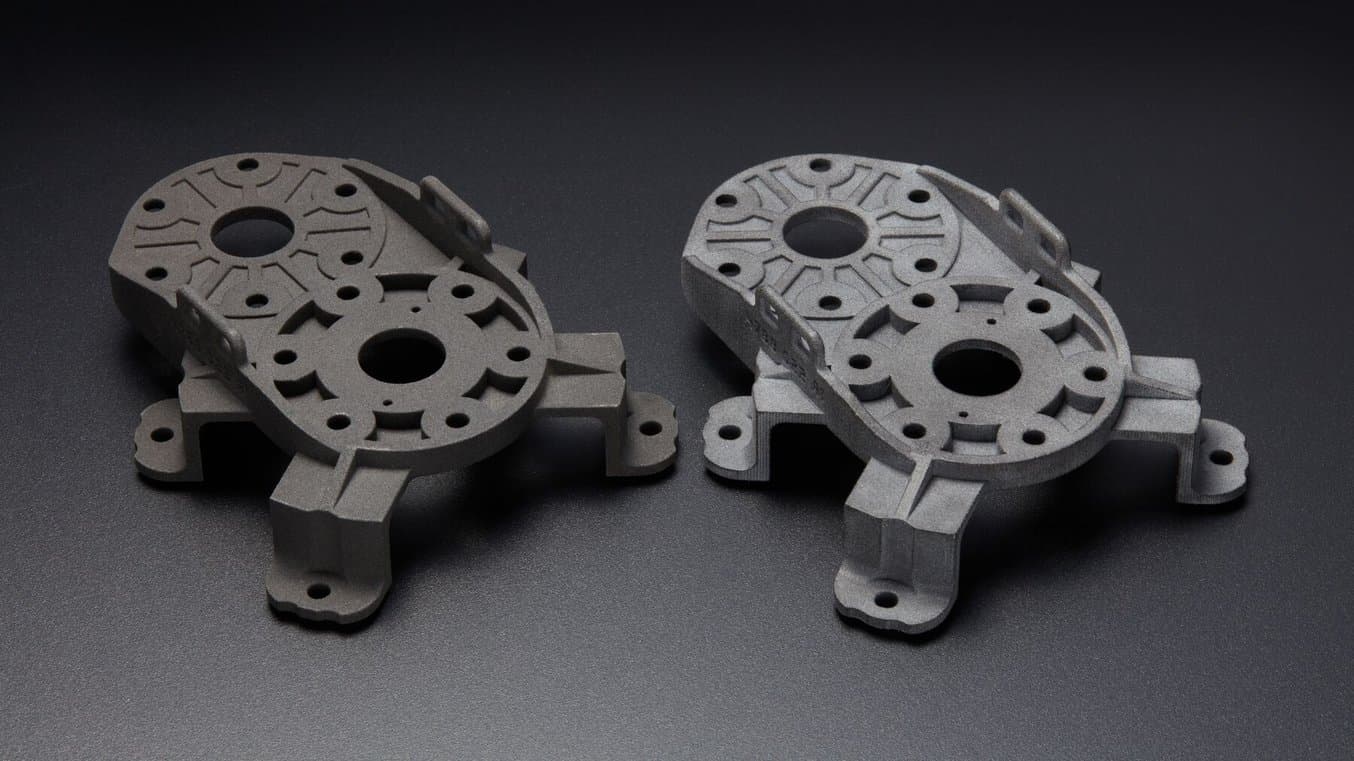
バレル研磨前と後のテスト部品。バレル研磨後の外観は、ライトグレーのマットな質感。
振動バレル研磨とは、複数の小さなメディア(通常は金属、セラミック、樹脂、クルミの殻などの植物等)をワークと共にかき混ぜることで摩擦を発生させ、ワーク表面を磨きながら硬度も向上させる研磨処理です。バレル研磨は大きさや値段の手頃さ、生産工程に多大な労力を要することなく様々なメリットが享受できるため、広く普及しています。
バレル研磨により、3Dプリント品の機能性と外観の向上という、2つの大きなメリットを享受できます。面粗度を向上することで、特に可動部の摩擦係数を引き下げることができるため、ヒンジや機械式の可動ワーク、クリップ、その他可動ワークや移動式の機械に使用されるワークを3Dプリントする場合には、バレル研磨は最適な後処理方法と言えます。研磨後のワークは表面が平滑化されるため、水密性も向上します。
もう1つのメリットである外観の向上ですが、バレル研磨を施すことで見た目の質感や美しさが向上するだけでなく表面の仕上がりが均一化されるため、アクリル塗料等での塗装やセラコートなど各種コーティングを行う際の下準備としても優れています。
実製品用の機能ワークの一部として製作または量産された3Dプリント品やPoC(概念実証)用試作品として製作された造形品は、どれも多くの人目に晒されるため、簡単に表面の硬さや面粗度を向上する手段として振動バレル研磨は良い選択肢と言えるでしょう。
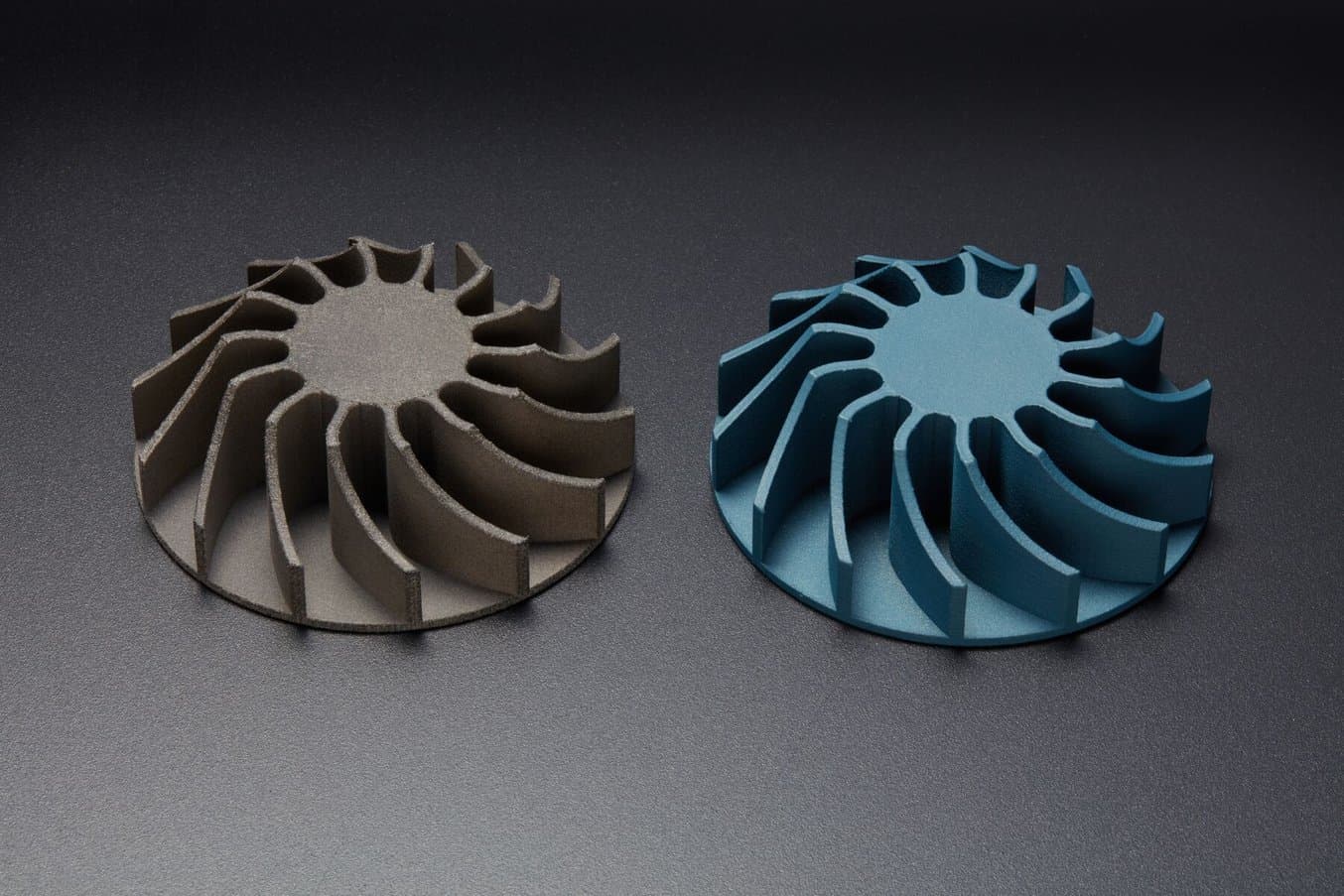
バレル研磨は表面を均一化できるため、塗料やコーティングを行う際の下地処理としても優れている。
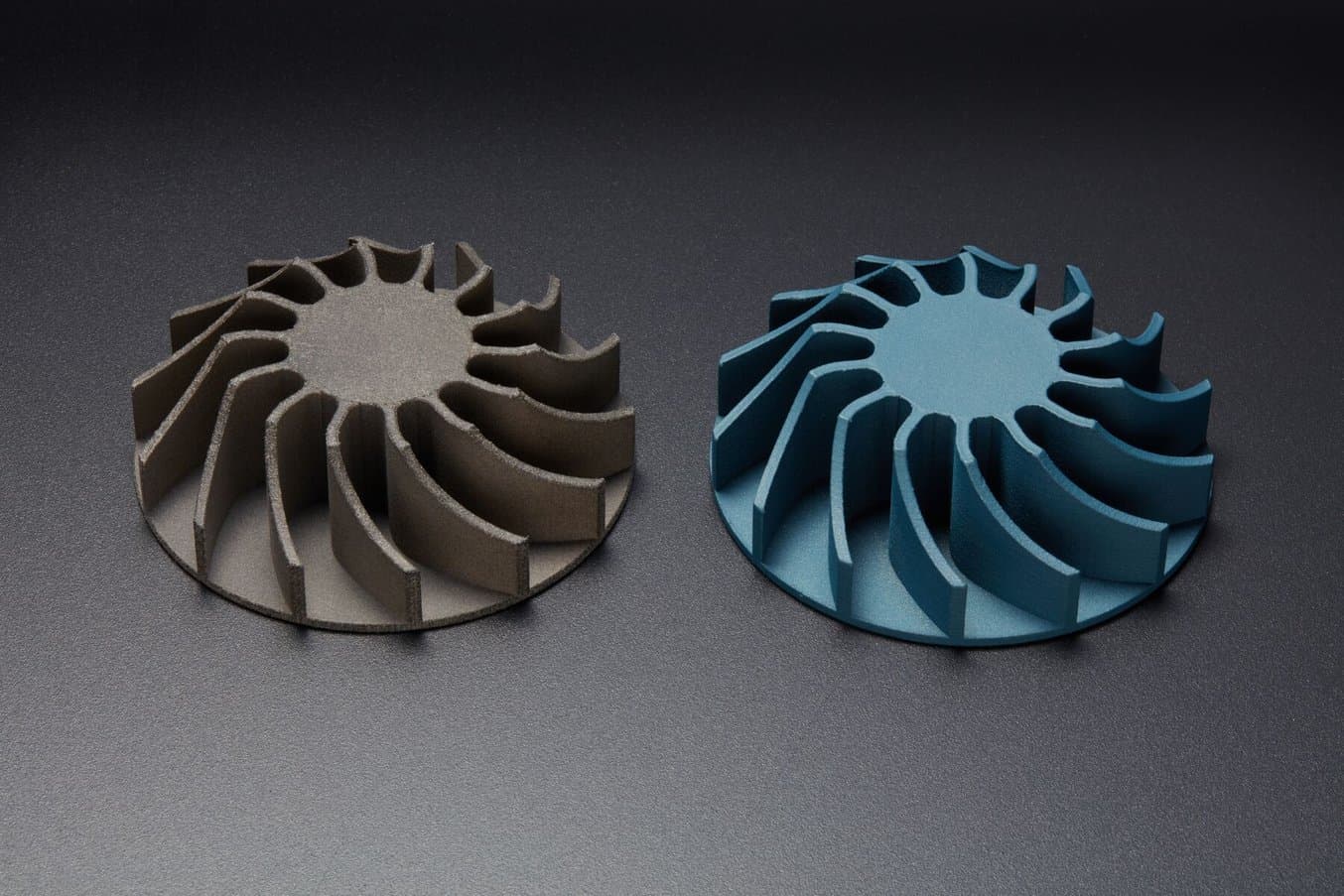
3Dプリント用の高度な後処理方法
このウェビナーでは、Cerakote、電解めっき、ベーパースムージングなど、3Dプリント品に施すことのできる11種類以上の高度な後処理方法をご紹介しています。
3Dプリント品に適したバレル研磨機の選定
3Dプリント製部品に使用できる研磨機には、工業グレードと消費者向けグレードの2つのカテゴリーがあります。工業グレードの研磨機は処理可能な容量や必要な電力要件が大きく、一般的に価格は約 $5,000以上です。工業用の研磨機はマスカスタマイゼーションや量産移行前のテスト生産など、量産レベルの数量を処理したい場合に適しています。
小型のバレル研磨機を複数台使用すれば工業用機と同等の効率で研磨することもできますが、容量が小さいため、同等の仕上げ品質を得るためにはより長い研磨時間が必要となる可能性があります。工業用研磨機で表面を平滑化するのにかかる時間は6時間程度ですが、小型の研磨機の場合には約72時間ほどかかります。工業用研磨機は、中型から大型の部品であっても複数のバッチを簡単に処理できるため、受託メーカーや大規模メーカーなどに最適です。
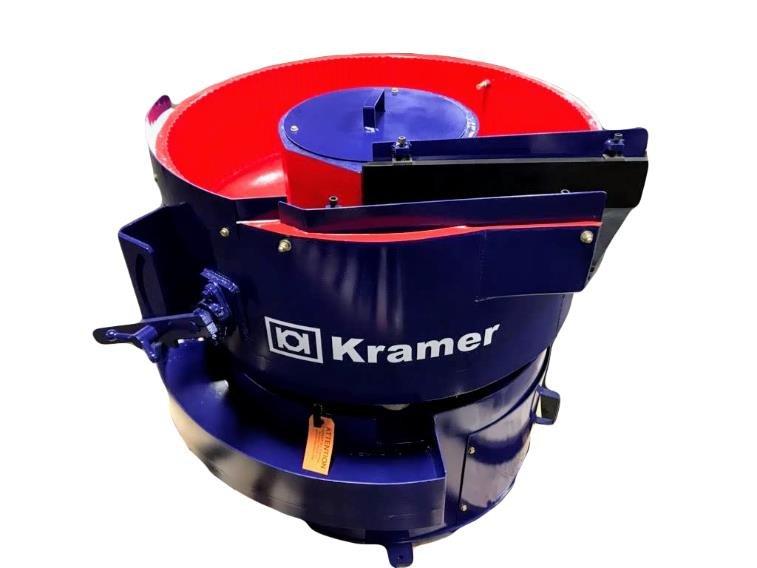
工業向け大ロット量産
例:Rösler
コスト:$5000以上
最適なケース:
-
大容量かつ高速
-
大型ワーク
-
複数の大型ワーク
-
作業手順の自動化
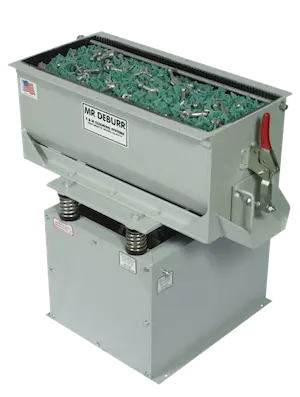
中量生産
例:CM Topline
コスト:$1000〜5000
最適なケース:
-
大型ワーク
-
バッチ単位での小型ワークの一括研磨
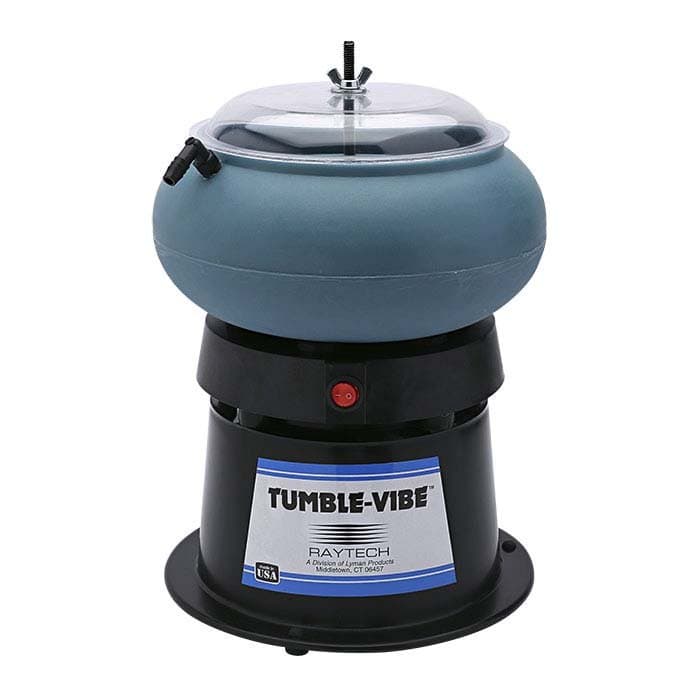
エントリー機小ロット量産
例:Raytech、Tumble Vibe
コスト:$1000以下
最適なケース:
-
特徴的な形状の中型ワーク
-
小型ワークの一括研磨
バレル研磨のメディアとコンパウンドの選定
バレル研磨で使用するメディアペレットには様々な種類がありますが、用途に合わせて適切なメディアを選定できるかどうかで仕上がりが大きく左右されます。代表的なメディアには、ステンレススチール、磁器またはシリカ、ポリエステル複合材、クルミの殻などがあります。メディアの種類により、表面を強力に平滑化して表面粗さを排除するものから外観向上のために軽く研磨するものまで、幅広い効果が得られます。
湿式バレル研磨と呼ばれる工程では、ペレットに水や化学洗剤を加えて湿らせた状態で処理を行います。液体を使用することで、強力な摩擦によって発生する熱を和らげ、ワーク表面の不純物や酸化物を除去できます。しかし、こういった洗剤は高価であると同時に化学廃棄物が発生するため、使用後は適切に廃棄・処理する必要があります。
Media Shapes
When choosing media to be used in a vibratory tumbler, the size and shape of the individual pellets should be considered along with the type of material. Pellets come in large and small sizes and sharp or rounded shapes. Large pellets are used for rougher grinding, such as removing burrs or rust from metal parts. Smaller pellets are used for finer pieces, offer more polishing or burnishing effects, and can be used on a broader range of materials. Sharp pellets (triangles, wedges, and arrowheads) are ideal for finishing complex parts with edges, crevices, and channels, though they have a higher instance of chipping or flaking. Rounded pellets are ideal for lighter-touch polishing and burnishing, and very rarely chip or flake. Though they are slower to fully smooth surfaces, they are much more gentle and can be used for delicate parts.
Detergents
In some vibratory workflows, called ‘wet vibratory finishing,’ water or chemical detergents are added in with the pellets. The liquid helps temper the heat generated by the high friction and can help in removing contaminants or oxides on the surface of the part. Parts will appear cleaner and more polished than with a dry tumbling workflow. However, detergents can be expensive and generate chemical waste, which has to then be disposed of and treated properly. Metal, ceramics, or plastic media can be used in a wet workflow, but organic media such as walnut shells or corn cobs should not be.
Comparison Table: Tumbling Media
Typical Material | コスト | メリット | デメリット | Aggressiveness | |
---|---|---|---|---|---|
金属 | Hardened carbon and stainless steel | $$$ | Short Run Times Prolonged service life and superior wear-resistance Heavy-duty burnishing and polishing | Might damage parts | 高 |
セラミック | Porcelain Aluminum oxide Silicone Carbide Silica | $$ | Heavy-duty burnishing and polishing Most commonly used media | Might damage parts Ceramic bits may flake off and get stuck in channels/negative features | 高 |
Plastic | Polyester, urea, and formaldehyde | $ | Ideal for safely finishing threaded or fragile parts Creates soft, bright surfaces and edges Range of densities available for customization per application | Longer run times | 中 |
有機性 | Walnut shells Corn cobs | $ | Can be used as a secondary vibratory step Can absorb oils and moisture | Longer run times May need to be used in a two-part process | Light to medium deburring |

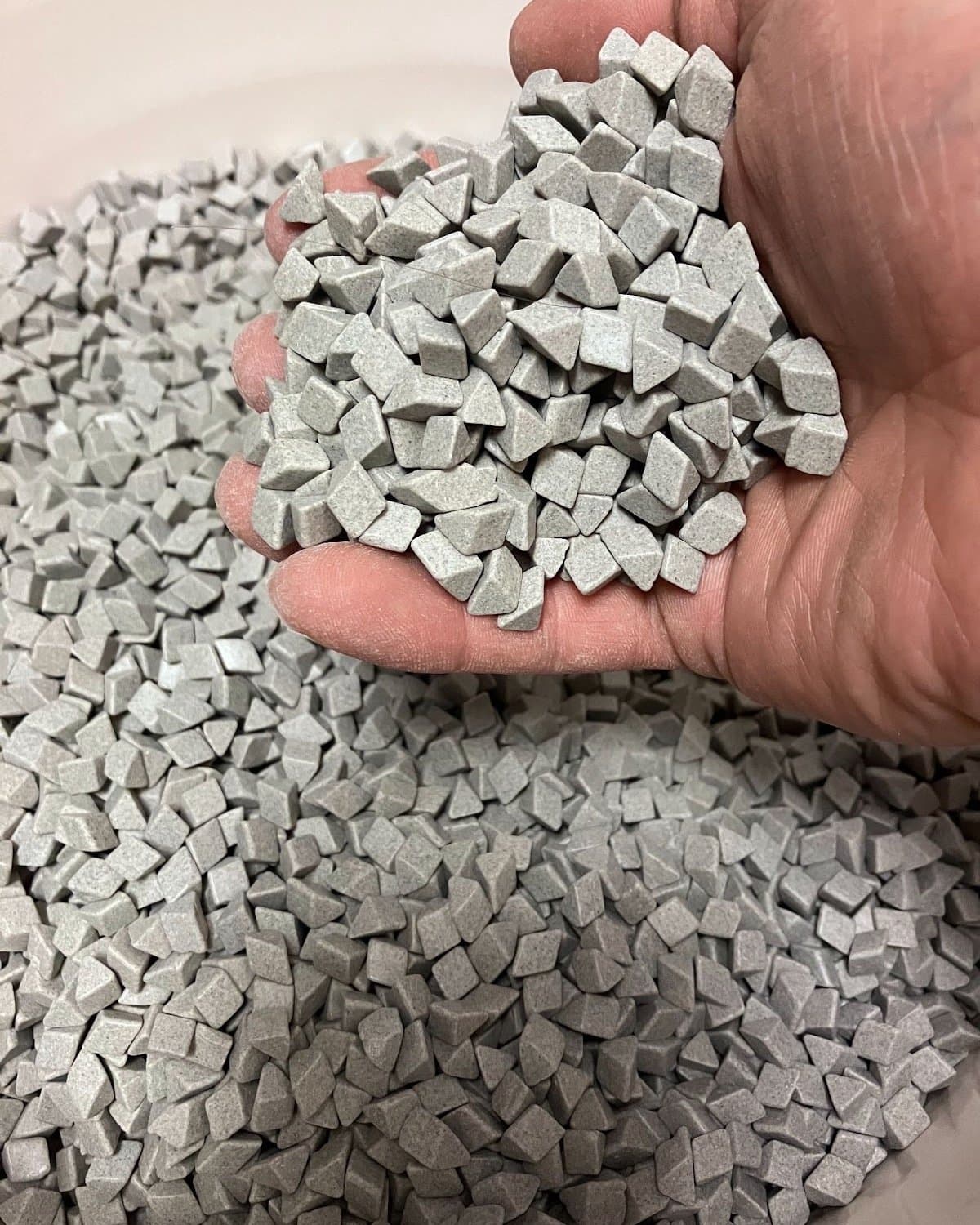
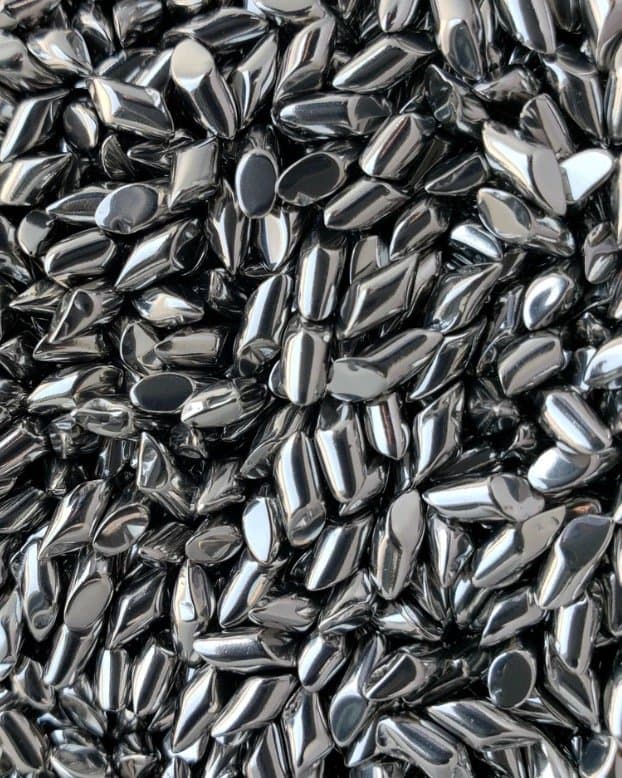
左から右の順に、クルミの殻、セラミック、スチール
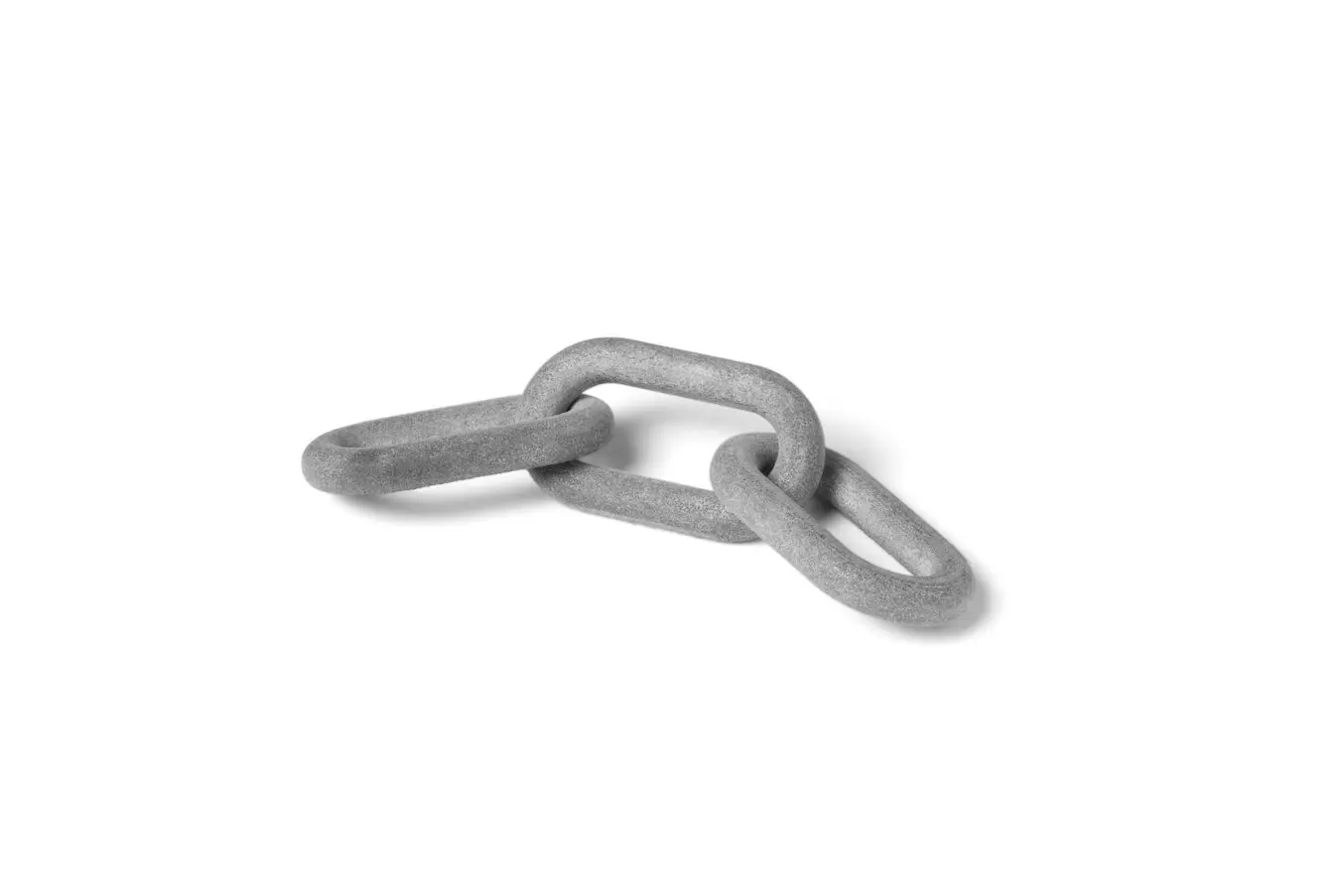
Nylon 11 CFパウダーの研磨済み無償サンプルパーツをリクエスト
手作業による後処理はほぼ不可能な、格子構造を丸ごと3Dプリントした造形品を実際に手にとってご確認ください。DB-300バレル研磨機でアングルカットセラミックメディア(三角)を用い、一晩かけて研磨処理を施しました。滑らかな表面品質は、塗装やコーティング、電解めっきなどの処理にも最適です。
バレル研磨を施したSLS 3Dプリント製部品の用途
3Dプリントの用途では、滑らかな表面品質と摩擦係数の低さが求められることがよくあります。振動バレル研磨で仕上げを行うことで、さまざまな業界や環境で使用されるワークの機能性と外観のどちらも向上させることができます。
バレル研磨で滑らかな表面に仕上げたSLS部品が求められる代表的な用途は、以下の通りです。
-
実製品用部品:SLS方式は少量から中量での製造を得意とし、バレル研磨は多大な作業量を割くことなくバッチ処理で部品表面を滑らかにできる最適な方法です。
-
ヘルスケア: 医療器具やモデル、人工装具や矯正装具の用途では、SLS 3Dプリント品に特徴のざらついた表面品質が課題になることがあります。SLS 3Dプリントと振動バレル研磨を組み合わせることで、ヘルスケア業界の3Dプリント活用に大きな価値を付与することができます。
-
治具:バレル研磨処理を施すことで治具の摩擦係数が減り、表面の硬度が高まり、耐性が高く長期間の使用にも耐えられるようになります。
Vibratory Tumbling End-Use Goods
As 3D printing technology makes mass customization a reality, high-throughput 3D printing applications become more common. The Fuse Series ecosystem enables mid- to high-volume manufacturing of end-use goods that function like injection molded parts while still taking advantage of the design freedom of SLS technology.
Vibratory tumbling is a low-cost method to achieve a surface finish comparable to injection molding, without adding hours of labor or manual post-processing. Batching parts together in a larger tumbler keeps touchpoints low and results optimal. Tumbling also prepares parts for further coating, which can further elevate the functionality, finish, and color of SLS 3D printed parts.
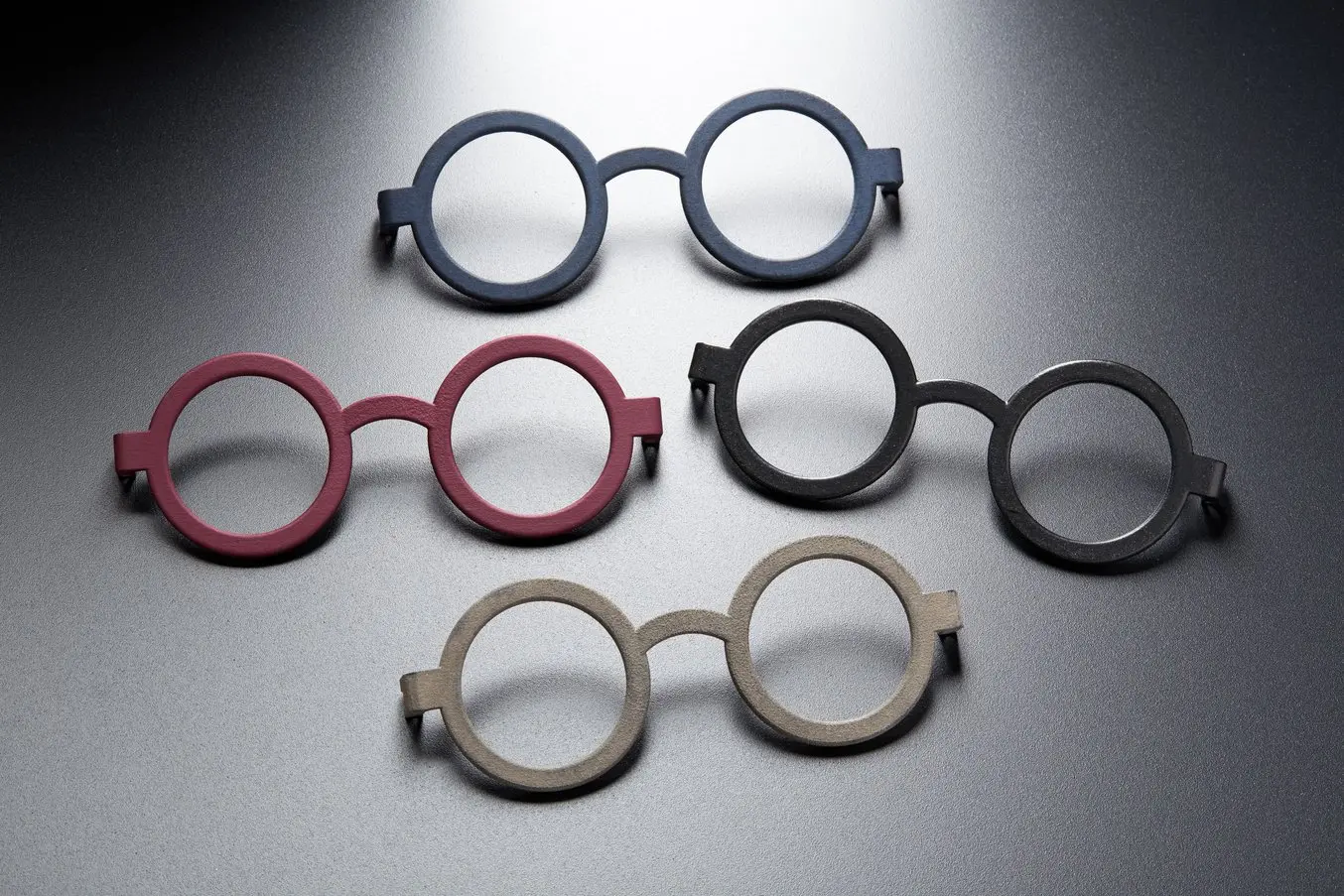
Vibratory tumbling is ideal for improving surface finish and preparing parts for further post-processing, such as dyeing, painting, or coating.
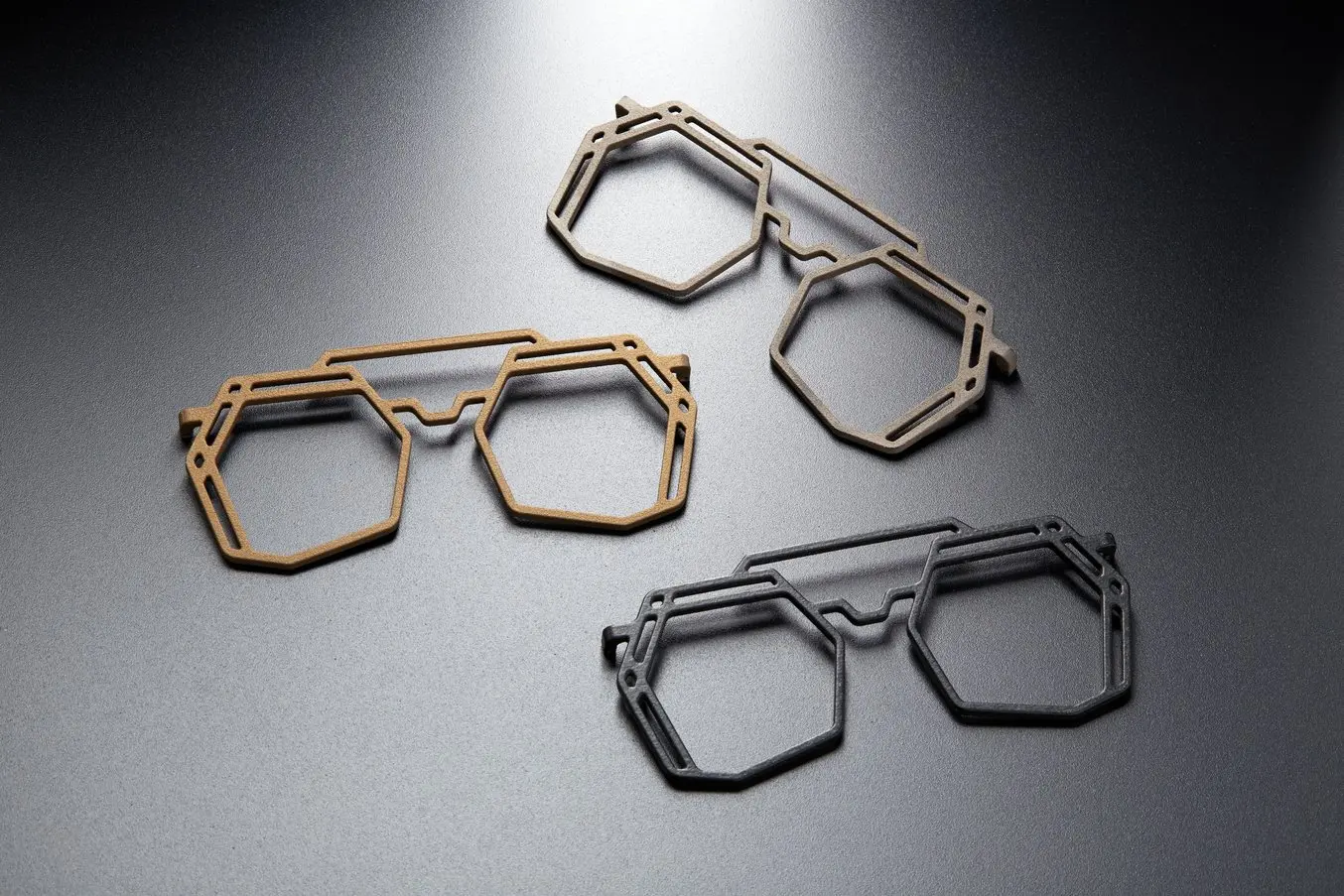
End-use eyewear frames are a perfect application for vibratory tumbling to have a major impact.
Vibratory Tumbling End-Use Goods
As 3D printing technology makes mass customization a reality, high-throughput 3D printing applications become more common. The Fuse Series ecosystem enables mid- to high-volume manufacturing of end-use goods that function like injection molded parts while still taking advantage of the design freedom of SLS technology.
Vibratory tumbling is a low-cost method to achieve a surface finish comparable to injection molding, without adding hours of labor or manual post-processing. Batching parts together in a larger tumbler keeps touchpoints low and results optimal. Tumbling also prepares parts for further coating, which can further elevate the functionality, finish, and color of SLS 3D printed parts.
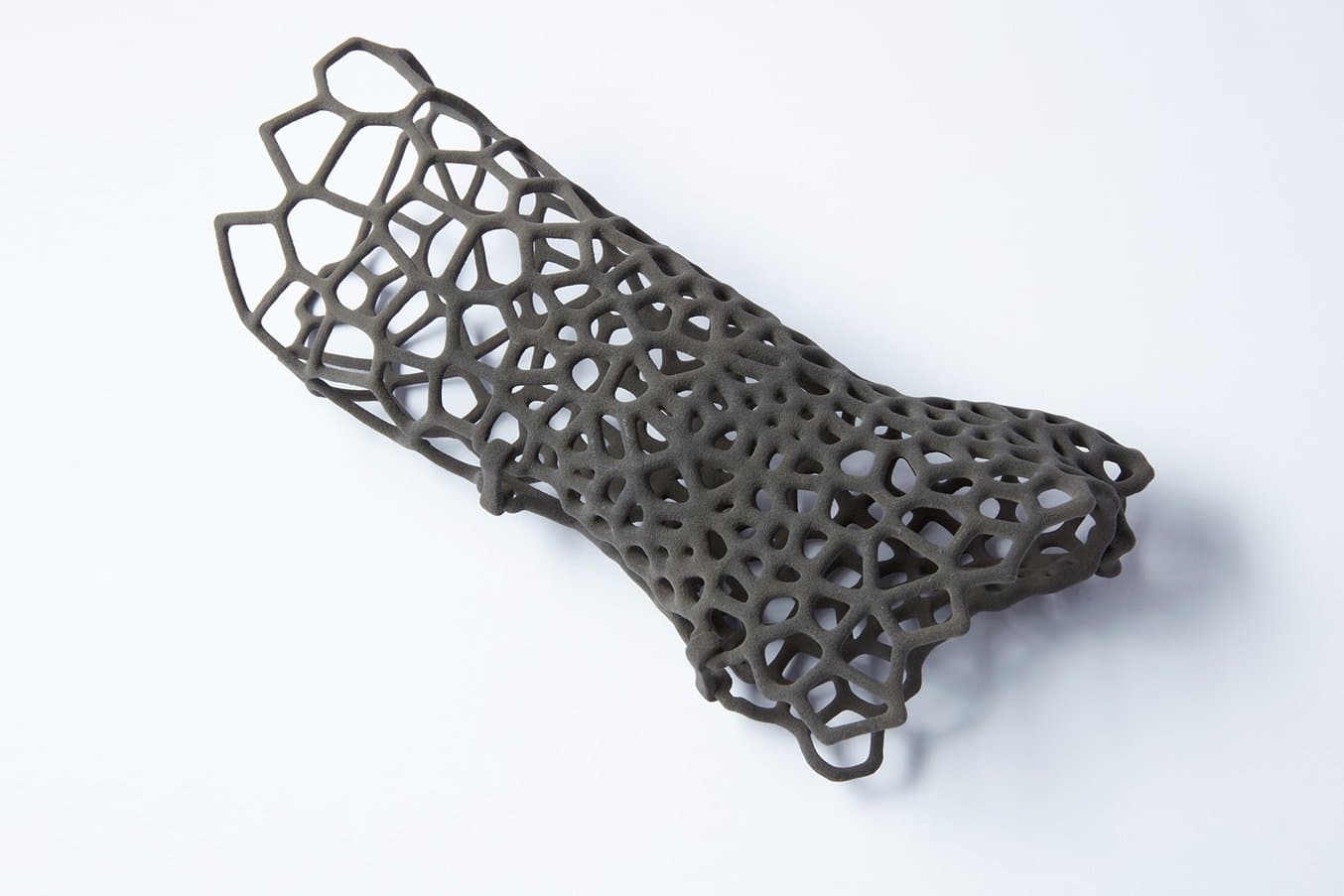
Vibratory tumbling is ideal for improving surface finish and preparing parts for further post-processing, such as dyeing, painting, or coating.
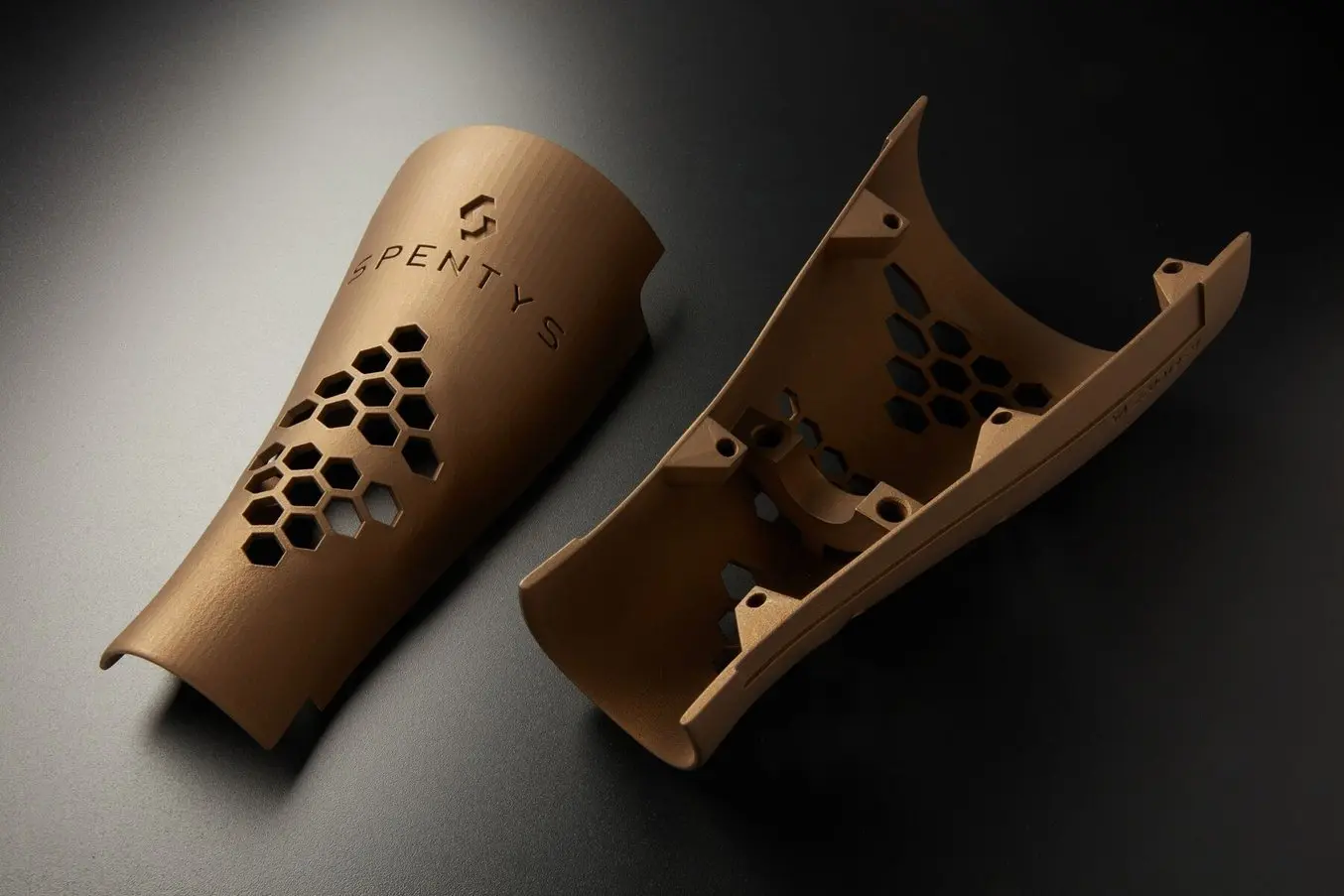
End-use eyewear frames are a perfect application for vibratory tumbling to have a major impact.
Vibratory Tumbling End-Use Goods
As 3D printing technology makes mass customization a reality, high-throughput 3D printing applications become more common. The Fuse Series ecosystem enables mid- to high-volume manufacturing of end-use goods that function like injection molded parts while still taking advantage of the design freedom of SLS technology.
Vibratory tumbling is a low-cost method to achieve a surface finish comparable to injection molding, without adding hours of labor or manual post-processing. Batching parts together in a larger tumbler keeps touchpoints low and results optimal. Tumbling also prepares parts for further coating, which can further elevate the functionality, finish, and color of SLS 3D printed parts.
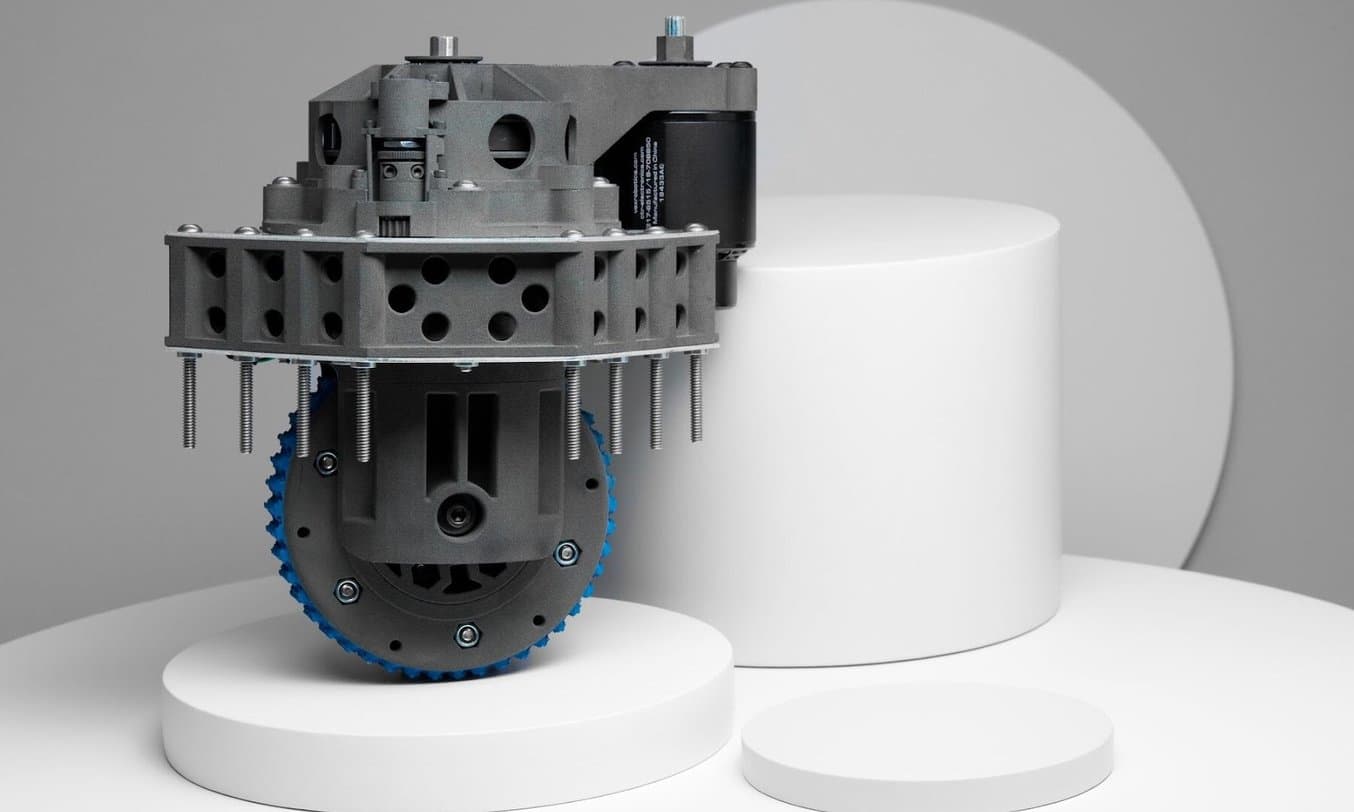
バレル研磨により複雑なアセンブリや治具の耐性が高まる。
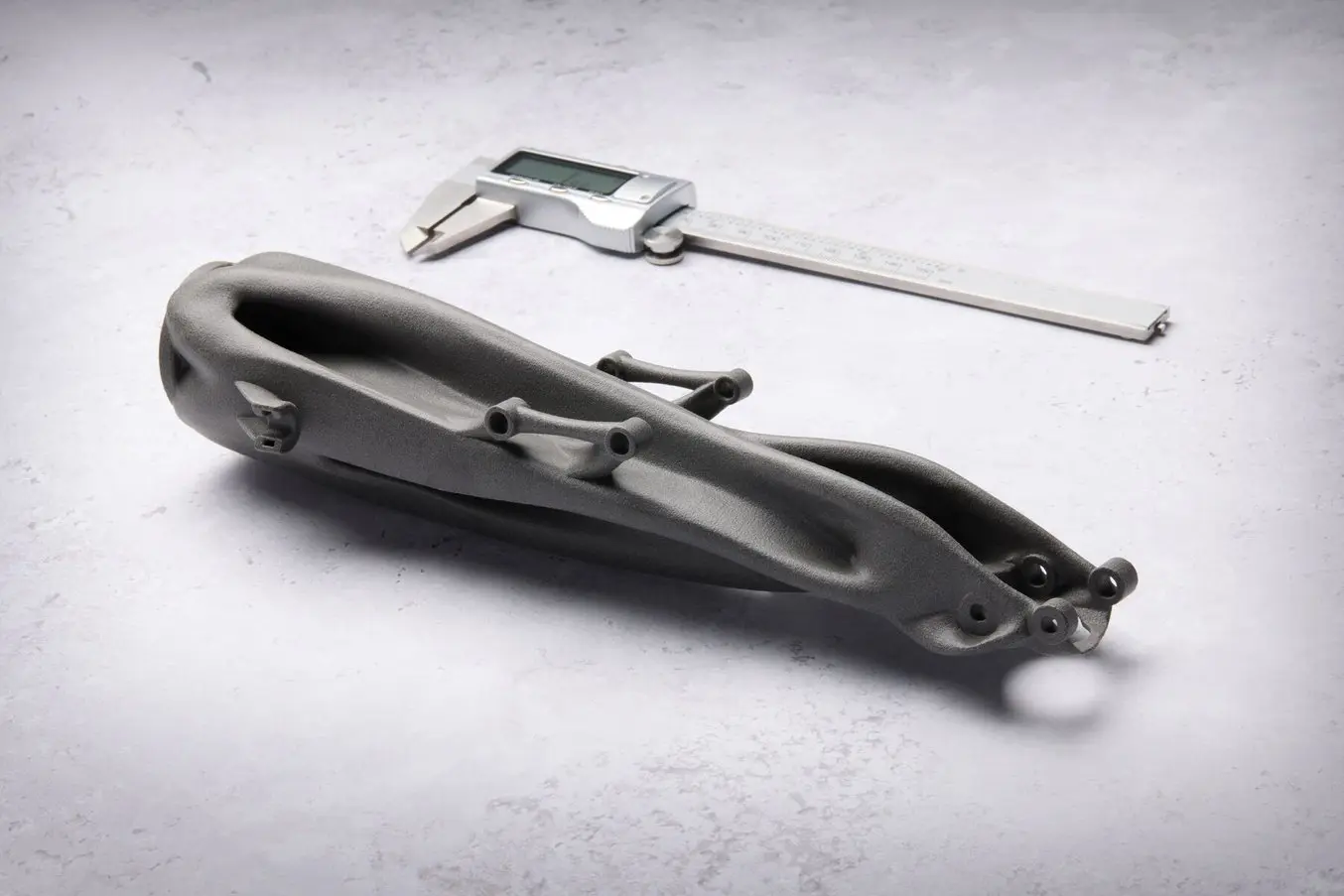
End-use eyewear frames are a perfect application for vibratory tumbling to have a major impact.
試験と試験結果
Formlabsでは、ユーザーの皆さまにとっての利点を最大化できるよう、SLS方式による3Dプリント品で振動バレル研磨機の試験を実施しました。試験では、平面と曲面、内面、外面を全て備えた標準設計の部品を複数3Dプリントしました。
Nylon 12パウダーとNylon 11パウダーを使ってSLS方式3DプリンタFuse 1+ 30Wでプリントした後、標準的な後処理ガイドラインに従ってFuse Siftで粉末除去を行い、CB300振動バレル研磨機(通称Mr.Deburr)でそれぞれ4時間、6時間、8時間かけて研磨を行いました。造形品は全てノギスで寸法精度を測定し、面粗度についてはKeyenceのレーザー顕微鏡を使って測定しました。製品仕様をダウンロードいただくと、試験結果の詳細をご確認いただけます。
The Process
We 3D printed several parts based on one standard design that has flat and curved surfaces as well as interior and exterior surfaces. The parts were printed on the Fuse 1+ 30W SLS 3D printer, depowdered in the Fuse Sift according to standard post-processing guidelines. Parts were printed in both Nylon 12 Powder and Nylon 11 Powder.
Aside from an identification number, each part was identical. These parts were each measured for dimensional accuracy using calipers and for surface roughness using a laser scanning microscope by manufacturer Keyence.
We chose to primarily test in a CB300 vibratory tumbler, commonly referred to as Mr.Deburr. This machine has three cubic feet of tumbling capacity and operates using a 0.75 horsepower motor. Retailing for $3500, Mr. Deburr is a good choice for high-throughput applications. The volume capacity enables multiple batches of SLS 3D printed parts to be tumbled at the same time, or a lower quantity of very large parts. The media used were ceramic pellets in angle-cut triangle shapes, with side dimensions of ¼ inch. A general-purpose finishing compound was used to assist with the process. The liquid compound chosen was “Kramco 1010” provided by Kramer Industries. This liquid works well with ceramic media and is good for deburring and light cutting.
The components tumbled for two, four, six, and eight hours before being removed and re-measured to determine if changes in dimensions and reduction in surface roughness occurred, and to what degree. The surface roughness was again measured using a Keyence VR-5000. The roughness was measured in terms of Sa. Sa is the arithmetic mean of a surface. The Keyence profilometer takes the average height of a surface and then compares the difference in height of each point when compared to the mean. The dimensional accuracy measurements were taken using vernier calipers with an accuracy of ±0.02mm. This allows us to determine the amount of material removed from each surface during the tumbling process. It should be noted that the outcome may be different if using different media, detergent, or machine and that there is a huge range of media in different materials, shapes, and sizes — all of which will impact your results. Based on our discussions with industry leaders, we chose to use ceramic for our tests.
A Note on Smaller Machines
To test out the efficacy of smaller, more entry-level tumbling machines, we also tested parts in a lower-cost model and found that it was unable to achieve the same results as Mr. Deburr, most likely due to the less aggressive churning of the media. However, the smaller tumbler was still able to get the parts mostly polished, to about a 70% reduction in surface roughness over a 48-72 hour period. These results are not included in our tables in order to highlight the efficacy of larger machines and their efficiency for volumes of this size.
Results With Mr. Deburr
Both Nylon 11 Powder parts and Nylon 12 Powder parts were able to have their surface roughness reduced by more than 80% of their original surface roughness after eight hours of vibratory tumbling, and some of the parts managed to reach 80% or less in four to six hours.
A key finding — Nylon 11 Powder and Nylon 12 Powder both started and finished with different surface roughnesses, but their proportional changes are quite similar. In our trials, we determined that Nylon 11 Powder parts have an average initial surface roughness of approximately 35 µm, whereas Nylon 12 Powder parts have an initial surface roughness of approximately 26 µm. Nylon 12 Powder parts were reduced to 4 µm, whereas the Nylon 11 Powder parts saw a reduction down to 5.5 µm. In terms of overall material removed, Nylon 11 Powder (0.12 mm) exhibited slightly less wear than Nylon 12 Powder (.15 mm) over the eight hours of tumbling. This is approximately the same surface roughness as commercial steel piping.
Looking at both graphs that compare the surface roughness reduction to tumbling time, it is apparent that both the smoothing rate and the amount of material removed per hour are decreasing. For both materials, it does not appear that the surface roughness has plateaued, and we hypothesize that if we were to continue tumbling for longer, you would see the Sa values continue to decrease but at increasingly slower speeds.
Visually, we saw several changes over longer tumbling periods; hard corners and edges became slightly rounded, thinner extrusions and highly detailed embossing became slightly worn, and media became embedded in holes and pockets closer to the 72-hour mark.
Nylon 12 Vibratory Tumbling Results
Runtime (hours) | Surface Loss (mm) | Surface Roughness (Sa) | Surface Roughness Reduction (%) |
---|---|---|---|
0 | N/A | 25.687 | 0% |
2 | -0.108 | 10.393 | 59.54% |
4 | -0.126 | 6.314 | 75.42% |
6 | -0.139 | 6.168 | 75.99% |
8 | -0.150 | 4.513 | 82.43% |
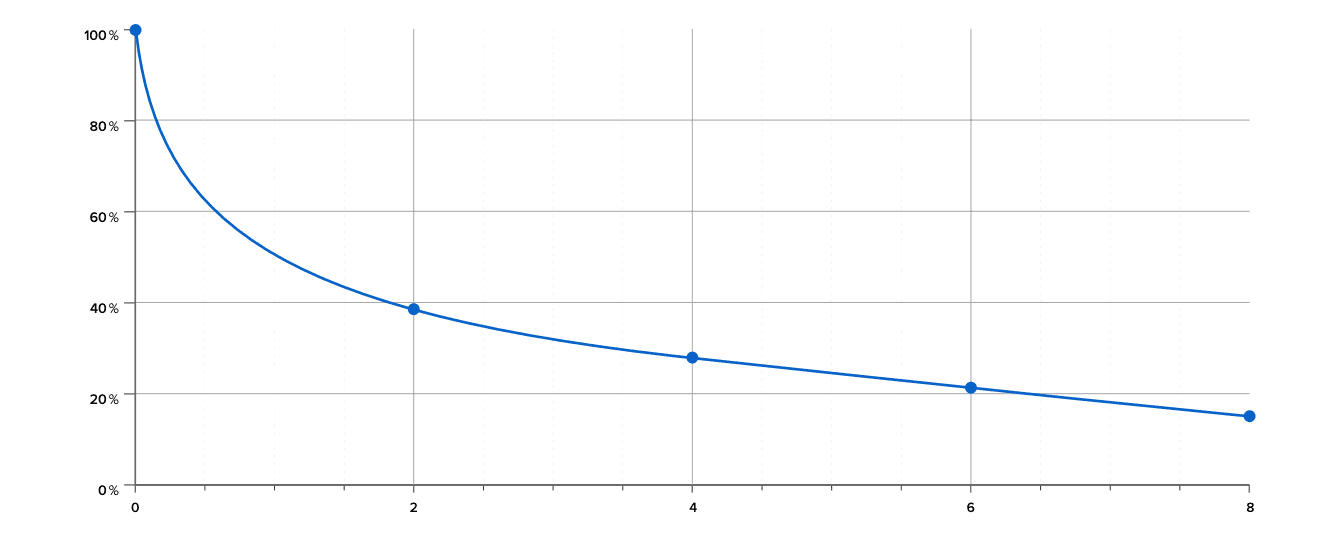
Nylon 12 Vibratory Tumbling Results
Runtime (hours) | Surface Loss (mm) | Surface Roughness (Sa) | Surface Roughness Reduction (%) |
---|---|---|---|
0 | N/A | 35.081 | 0% |
2 | -0.046 | 11.916 | 66.03% |
4 | -0.081 | 10.056 | 71.43% |
6 | -0.106 | 8.367 | 76.15% |
8 | -0.120 | 6.712 | 80.87% |
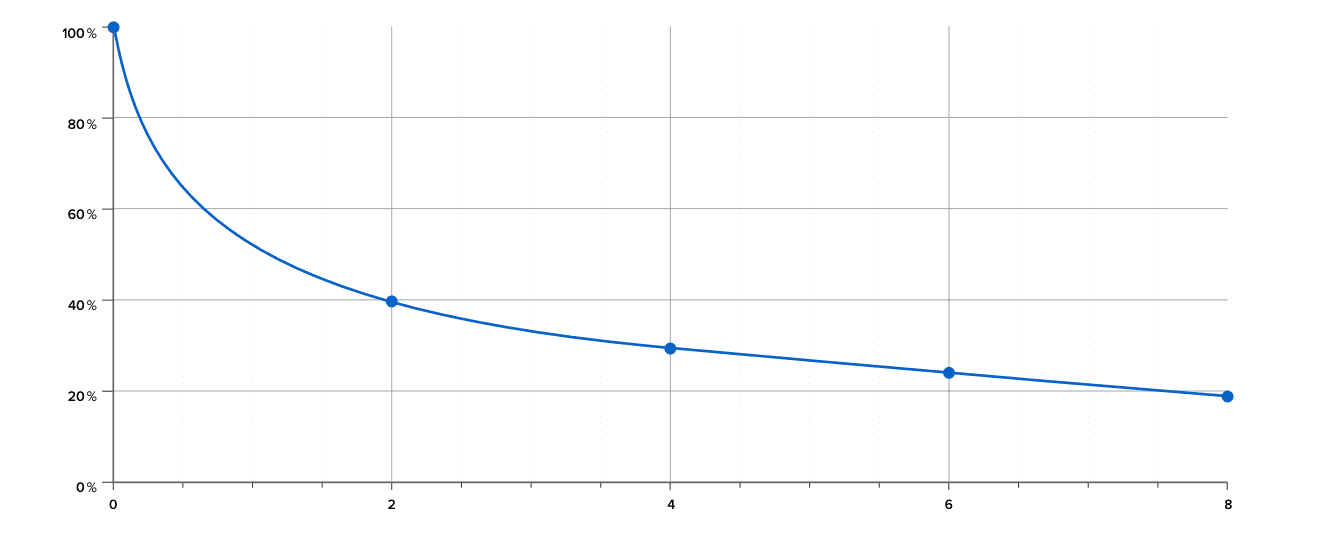
Recommendations
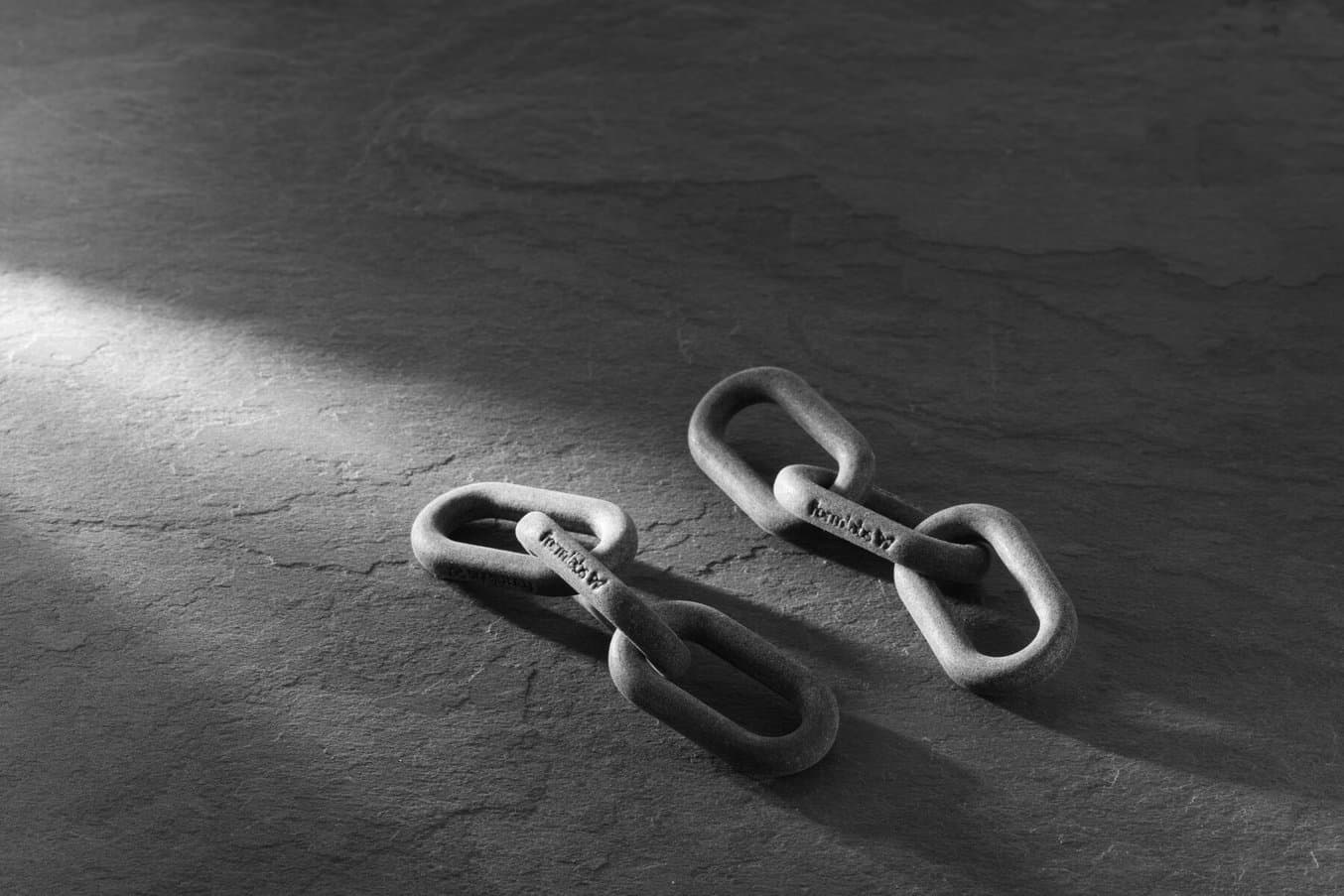
Vibratory tumbling is an excellent way to improve the surface finish of your 3D printed parts. Equipment is affordable, and the workflow is customizable to your exact needs. When adding tumbling to your workflow, keep in mind that different machines and media will produce different results.
When choosing which tumbler to purchase for a 3D printing workflow, first consider your volume of 3D printed parts: mid to high production volumes will require a larger industrial tumbler, while prototyping, manufacturing aids, and rapid tooling applications might only require a smaller, inexpensive tumbler. In these applications, the longer time required by the smaller tumbler shouldn’t negatively affect your workflow.
Choosing your media is the next consideration, and very part dependent. For SLS 3D printed parts, ceramic, plastic, or organic materials will all work, while metal might be too abrasive. For parts with many internal pockets or channels, ceramic media might become flaked and embedded in the parts. Although removal is simple with small hand tools, organic or plastic media might be a better option. For parts that have very fine features, delicate embossing, or thin extrusions, a less abrasive media is optimal. Likewise, choosing rounded media instead of sharp media will help protect delicate parts.
3Dプリントとバレル研磨を試す
振動バレル研磨は、SLS 3Dプリント製部品の外観と機能性を射出成形品に近づけることができる、身近な後処理方法です。3Dプリントの工程に追加する場合、複雑で効果な装置は必要ありません。研磨装置には、設置面積や必要電力の観点でも利用しやすく手頃な価格の選択肢が豊富にあります。