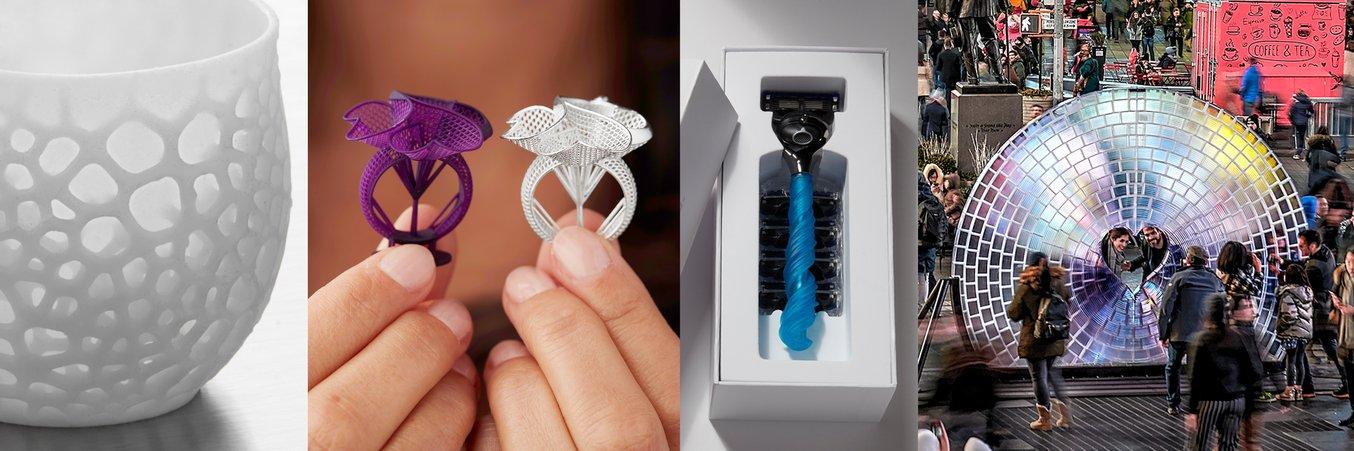
Formlabs had a big year: we became a unicorn, released five materials, made our Vice debut, opened new offices in Budapest, North Carolina, and Somerville, and hired hundreds of people across engineering, design, operations, and more in countries all over the world. But for the rest of our year in review, let’s focus on you. You did some amazing things, and we're proud to help power your successes.
From printing parts that push the boundaries of 3D printed design, to starting businesses that change lives, here’s just a sampling of the amazing work we saw in 2018.
You printed some really incredible parts.
This year, you printed parts that went beyond the build volume, were incredibly small, and featured detailed, intricate geometries that push what’s possible with 3D printing.

We are constantly motivated by the innovative spirit of our users to keep expanding what’s possible with 3D printing, and with each new material we release. In 2018, that meant expanding into numerous filled resins with the launch of Rigid Resin (glass-reinforced), Ceramic Resin (silica-filled), and Castable Wax Resin (wax-filled)—along with the release of Grey Pro Resin and an updated version of High Temp Resin.
You solved hard problems.
Problem solving is at the heart of designing and creating physical objects. In 2018, we heard stories of creative solutions to problems big and small, and users that pushed the Form 2 and our materials to the limit. Here are just a few examples:
Google ATAP Circumvents a Complex Supply Chain
The team at Google Advanced Technology and Projects (ATAP) lab was stuck dialing in the overmolding process in a pre-production manufacturing phase, and they needed to get past it as quickly as possible in order to ship a new wearable device. Using High Temp Resin, the team created a process innovation that allowed them to circumvent a complex supply chain, reducing turnaround time for a crucial component by 85% while saving over $100,000.
Nix Rapidly Prototypes Optically Clear Parts
Choosing the right fabrication method and material can be complicated. When developing their Nix Pro Color Sensor, Nix needed to find a transparent material versatile enough for prototyping internal light pipes, plus fast and cost-effective enough to cycle through many iterations. After much consideration and trial and error with laser cut acrylic, CNC acrylic, 3D printed molds, and outsourcing, they decided to 3D print light pipes in Clear Resin on the Form 2, printing ten different lenses on a single build platform in one afternoon.
A Design Team Fabricates a 3D Printed Structure That Can Withstand Times Square
Alongside design studio Aranda\Lasch and engineering firm LaufsED, the Formlabs design team created Window to the Heart, a sculpture that would remain installed in Manhattan for one month as winner of the Times Square Valentine Heart competition. The journey was fraught with challenges, but in the end, the final 10-by-12-foot structure successfully delighted Times Square visitors for the whole month of February.

You met us, and each other, on the road from Chicago to Cologne.
In addition to meeting you at 70+ events around the globe, this year the Formlabs roadshow traveled across the US and Germany, bringing together local innovators and global disruptors like Amazon, Autodesk, Google, Women in 3D Printing, Hasbro, ZBrush, Siemens, McKinsey, SAP, and more to discuss how accessible 3D printing technology is enabling manufacturing across the business, education, and dental landscapes.

You changed the way things are made.
We kicked off 2018 with a demonstration of a custom earbud production workflow at CES, and throughout the year you proved the power of 3D printing to advance industries, from elevating the standard of care from healthcare to dental, to changing the way movies come to life.
Here’s just a taste of big changes we saw across industries in 2018…
Product Design and Manufacturing: Gillette’s Razor Maker™ Unlocks Consumer Personalization
With the launch of their Razor Maker™ concept, Gillette connected the power of personalized digital experiences to physical products with one of the first examples of direct-to-consumer, end-use 3D printed parts. Using Formlabs Form 2 3D printers as its production engine, Razor Maker™ gives consumers the power to create and order customized 3D printed razor handles, with the choice of 48+ designs, a variety of colors, and the option to add custom text.

Healthcare: Patient-Specific Solutions at Northwell Health
3D printing is bringing doctors closer to patients, delivering treatments and devices customized to better serve each unique individual. Northwell Health, the largest healthcare network in New York State, is at the forefront of this movement, using one of the first installed Form Cell systems to rapidly produce patient-specific models that help surgeons better prepare for operations, reducing time in operating room and the risk of complications.
Dental: Scaling Digital Production at Ashford Orthodontics
Orthodontics is in the midst of undergoing its most significant technological evolution to date, from traditional workflows to digital technologies. The UK’s largest ortho lab, Ashford Orthodontics, is leading the way; the lab created a digital department from scratch that now produces 1,200 clear aligners and retainers a month running a fleet of 12 3D printers.
Entertainment: Creature Designers Go Sketch to Sculpt to Screen
This year, the Form 2 made many on-screen appearances, with cameos in blockbusters like Avengers: Infinity War and television series like MacGyver, but more often 3D printing plays an important role off-screen. Users like Jared Krichevsky, a former creature and character artist at Aaron Sims Creative, now freelancer, are leading the charge in using physical models in the process for making on-screen magic.
Jewelry: Advancing the Industry on All Fronts
Every corner of the jewelry world is embracing the impacts of access to digital workflows. A wave of digital jewelers are bringing even more complex, beautiful pieces to life more efficiently, and creatively, than ever before, casting houses are finding new revenue models, and brands like egf Manufaktur are transforming the retail experience with on-site, consumer-facing jewelry customization.

Art: The Opificio delle Pietre Dure Institute Brings Antiquities Back to Life
At the Opificio, art restorer Mattia Mercante uses 3D printing to emulate the technical virtuosity of the masters, restoring intricate details that would be impossible to reproduce in any other way, so that today we can enjoy art pieces in their splendour and entirety the way their creators intended.
Audiology, and Beyond: Manufacturing Custom Ear Products
In partnership with 3Shape, at CES 2018 we demonstrated an entire production process for custom earbuds that can be deployed in mass markets, but in the audiology space, digital technologies are already transforming businesses. As 3D printing becomes more accessible, more and more hearing specialists and ear mold labs are transitioning to digital workflows. We expect consumer use cases, including earbuds, to follow suit.
You changed lives.
The ability to create diverse, high-quality parts can provide a special power to make change. You’ve seen that throughout this year-in-review post, and some of you have lived it.

One of the most inspirational stories of 2018 came early in the year, when an engineer father in Slovenia refused to accept status-quo orthosis solutions that weren’t working for his young son with cerebral palsy. Frustrated, Matej took matters into his own hands to help his son to walk for the first time.
To help provide precise, patient-specific 3D printed orthotics to help more children in need, Matej and others formed the company aNImaKe, named after Nik.
After Nik's story spread, Matej received media attention and countless heartfelt messages, and hundreds of requests from families around the world looking for help. So far, the aNImaKe team has diagnosed and successfully treated 24 patients, coming from as far as Turkey, the UK, Greece, Spain, and Pakistan. In 2019, Matej plans to continue discussions with experts that would like to adopt aNImaKe's process to bring the solution closer to those who are unable to travel to Slovenia, and work on bringing additional solutions to market.
You continue to drive what’s possible with our products.
We make things that make things: our goal is to empower you to produce parts that help you do your best work, grow your ideas, and advance industries.
Formlabs users have created 25,000,000 successful parts and counting and we can’t wait to see what you do next. Cheers to another year of incredible work!
You’re an email address and a click away from another year of incredible stories!
Now that you’re caught up on 2018, make sure you stay up-to-date in 2019! Sign up for the newsletter for the latest 3D printing stories, all year long.