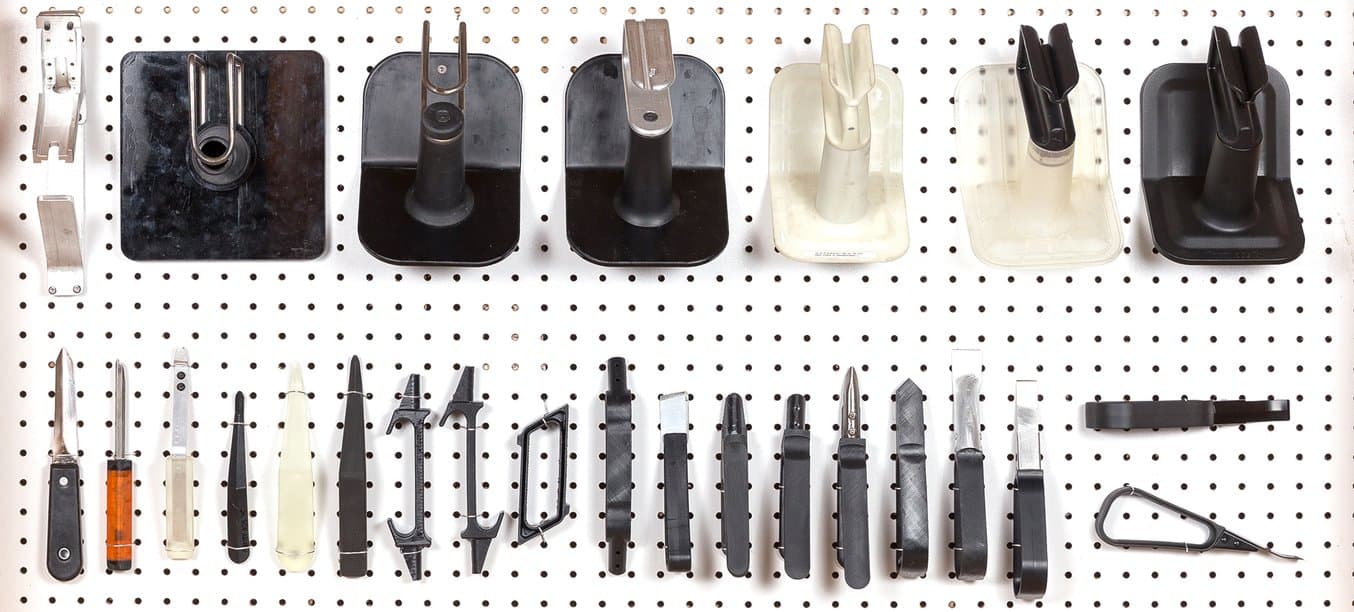
Rapid prototyping is used in a variety of industries, by Fortune 500 companies and small businesses alike, to speed up development, decrease costs, improve communication, and ultimately create better products.
Using rapid prototyping, engineers and designers combine the power of CAD software with additive manufacturing technology to easily iterate between digital designs and physical prototypes. 3D printing is a natural part of this process, replacing time-intensive tooling and subtractive fabrication methods. But while CAD has become ubiquitous, 3D printing traditionally has been less accessible and cost-prohibitive.
In the past several years, however, the market has changed. Desktop and benchop technology have democratized additive manufacturing and inspired a groundswell of adoption that shows no sign of stopping.
Read on to learn more about the rapid prototyping process and explore real-world examples of companies that use in-house 3D printing to fabricate prototypes that look, feel, and function like final products.
Table of Contents
- What is Rapid Prototyping?
- Prototyping for People: Testing Size and Fit at Paralenz
- Wöhler 3D Prints Functional Prototypes in Multiple Materials
- Blending Prototyping with Production at RightHand Robotics
What is Rapid Prototyping?
With 3D printing, CAD designs can be quickly fabricated into physical models without outsourcing to a machinist or technician, and with substantially lower material and equipment costs.
This has impacts across the product development process, from prototyping to production.

Accelerated Design and Reduced Costs
Rapid prototyping eliminates the wait time of outsourcing. Engineers prototype in-house, and design for manufacturability from the start, saving time and costs by reducing the risks of potential errors in production.
A good model is a 24 hour design cycle: design during work, 3D print parts overnight, clean and test the next day, tweak the design, then repeat.
The low cost of 3D printers and materials means that accelerated in-house prototyping, even if at a higher volume, still costs less than outsourcing in most cases.
For example, before bringing a stereolithography (SLA) 3D printer in-house, the team at Paralenz, a designer and manufacturer of diving cameras, outsourced SLA models. The company estimated that for one project alone they have spent $15,000 on SLA parts. Purchasing a 3D printer and materials was less than third of that, paying their investment back several times over.

Prototypes That Match Final Parts
The wide range of 3D printing materials on the market today allows designers to simulate a range of injection-molded plastics, and test prototypes at every stage of development:
- Looks-Like: Test design iterations and communicate ideas to stakeholders affordably and quickly.
- Works-Like: Reliably develop proofs of concept and test functional prototypes with materials closely matching common injection-molded plastics.
- Feels-Like: Simulate a range of materials from rubber to rigid, and create prototypes with the smooth finish and feel of end products.
A range of functional materials lets designers 3D print prototypes that look like, feel like, and work like final products.
The ability to create functional prototypes also helps engineers design for manufacturability, even in early stages.
Designing for manufacturability means fewer do-overs down the road between engineering and manufacturing, and when changes do need to be implemented, it will much more affordable and less disruptive to the line.
Agile Manufacturing
Once a part is in production, prototyping doesn’t have to stop. Many companies design a jig or fixture, put it to production, and then never go back and redesign; using standard prototyping methods the time and engineering cost wouldn’t be worth the potential yield increase.
With affordable 3D printing, however, you can can tweak and reassess jigs and fixtures in real time–and even easily update final products.
Learn how Formlabs uses desktop 3D printing in production, from prototyping for manufacturability to printing functioning final parts used on the line.
Prototyping for People: Testing Size and Fit at Paralenz
When designing products that people need to wear or carry, it’s crucial to strike the perfect balance of size, weight, and shape. This becomes even more complicated when a product has to be able to function while submerged in 150 m of salt water.
But the engineers and designers at Paralenz are up for the challenge. The team prototypes their diving cameras early and often, leveraging 3D printing throughout the entire development process.

After consulting with divers and narrowing down the list to the “must-haves” for a product, Paralenz creates several basic designs in different sizes for user testing so they can evaluate the volume, weight, and feel. For example, designers tested multiple versions of a camera’s button, altogether going through through seven or eight different designs, all of which were 3D printed.
“With such a compact product, your design freedom is limited, so we spent a lot of time figuring out how to optimize the design, while making sure that it accommodates all the required features,” said Paralenz’s Michael Trøst.
“As we developed the internals [for the dive camera], many things changed. The battery is a bit smaller than the one we started out with, because we changed the sensor, the lens, and some other parts. There's a lot of back and forth involved. All of the changes we made in the camera, we made 3D prints of, altogether iterating about 20-25 housings on the Form 2 in a matter of a few months.”
If you’re a product designer or an engineer, chances are you’ll need to make a custom enclosure at some point. Whether a simple container to keep small items organized or a fully functional prototype, learn how you can use CAD software and a 3D printer to create a custom snap fit enclosure in five easy steps.
Wöhler Prints Functional Prototypes in Multiple Materials
Aside from the benefits of iterative design, prototyping helps engineers finalize products before committing to manufacturing, avoiding costly mistakes.
Sebastian Leifels, product designer at Wöhler, a Germany-based manufacturer of metrology and inspection technology, needed to design a prototype with close-to-final aesthetics and function to get a new product ready for casting and final manufacturing.
“It is extremely important to prevent mistakes at this stage of the design process. Changes to the casting device as well as the end product are expensive. The costs range from a three-digit up to a five-digit euro figure,” Leifels said.

The product, the Wöhler HF 550 Wood Moisture Meter, is a device with a hard outer casing and soft, flexible buttons, so the final prototype required several different materials.
Leifels used Black Resin for the case and Flexible Resin for the keypad. The keys had to compress when the user pushed them, so the button walls had to be very thin yet durable. Flexible Resin allowed the team to conduct a variety of tests without any damages or functional constraints of the part.
Flexible Resin, Firsthand
Flexible Resin is excellent for simulating soft-touch materials and adding ergonomic features to multi-material assemblies. Request a free sample part to feel it for yourself.
Get Your Sample

Blending Prototyping with Production at RightHand Robotics
The ability to make changes to a product’s design during the production process—agile manufacturing—makes it possible for engineers and designers to produce parts for testers and developers before committing to tooling for mass production, and to continuously improve final products.
Direct 3D printing and moldmaking make these low-volume production runs, from hundreds to low thousands, efficient and economical.
Small batch production is part of RightHand Robotics’ strategy for their ReFlex products. 3D printing provides the flexibility they need to change designs without sinking a lot of cost into the tooling.
“The kind of niche market and the customers that we have are looking for very specific things, and they’re doing very specific research. We want to stay on the forefront of the kind of research that they’re doing. As their needs change, we can change our product to match them,” said Sarah Mendelowitz, lead of the RightHand Labs team at RightHand Robotics.

The company uses SLA 3D printing to prototype components for their ReFlex Hand and industrial systems, test rigs, and in manufacturing to make molds for ReFlex Hand’s fingers.
“Anything that we find in manufacturing or testing, we like to get into our final version of the product right away. Desktop SLA 3D printing really complements that approach because we need a tool that can move as fast as our design process is moving,” said Mendelowitz.
“Being able to 3D print in-house means that that we don’t have to wait on any external timeline to do our prototyping. We can go from CAD to a functional test within the same day.”
How Can 3D Printing Improve Your Product Development?
Discover more ways that 3D printing can kickstart rapid prototyping at your company. Not sure which type of technology is best for your application? Learn how to effectively compare technology and walk through example applications in our webinar, “How to Choose the Right 3D Printing Technology – FDM vs SLA vs SLS.”