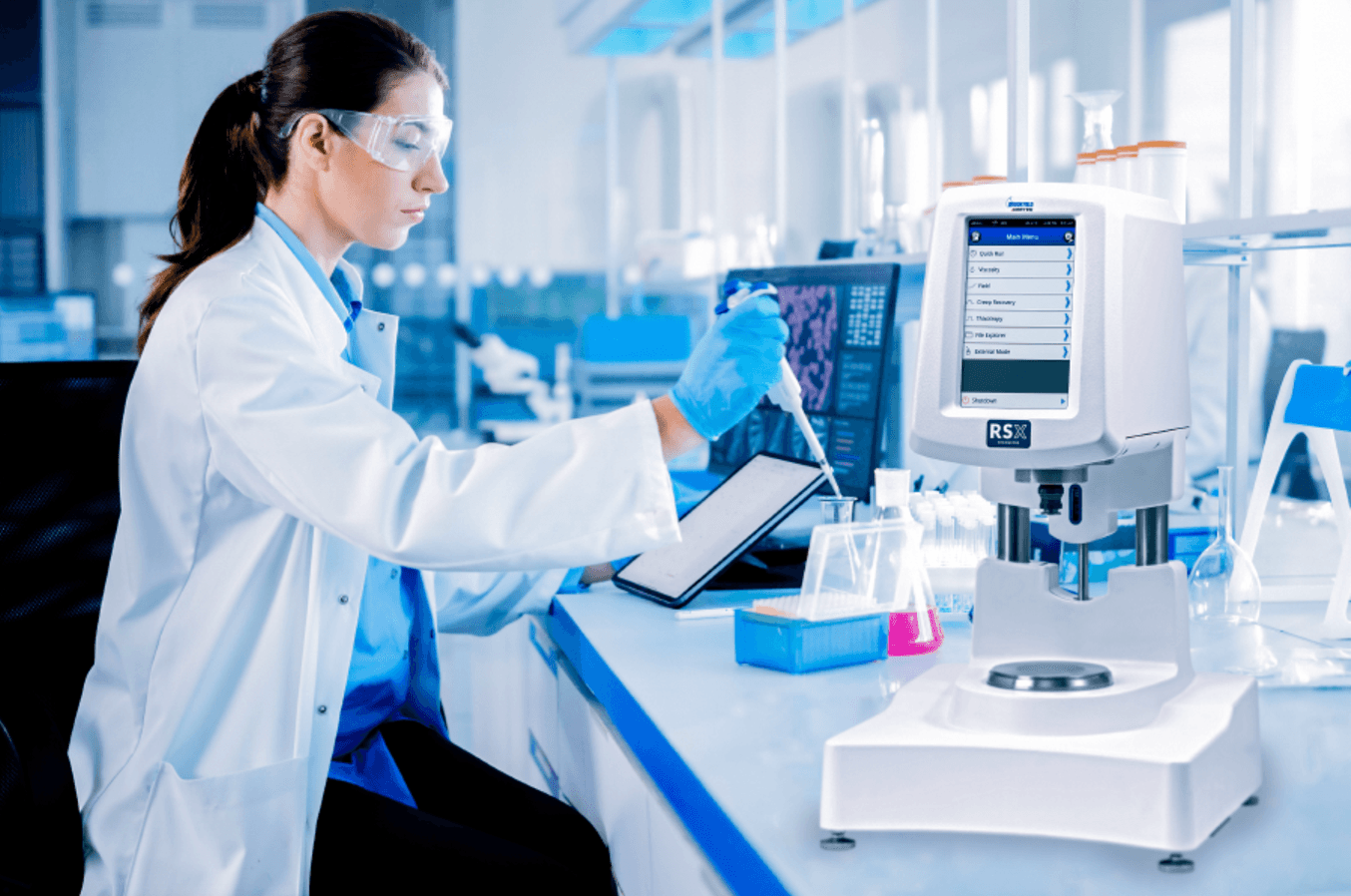
All photos provided courtesy of AMETEK Brookfield.
At this point, many large hardware manufacturers have adopted 3D printing as part of their design strategy for new products — it’s well understood as a powerful tool for prototyping. Fewer of these businesses, however, have successfully deployed comprehensive additive manufacturing strategies for the later stages of their workflow.
AMETEK Brookfield, a leading global designer and manufacturer of material characterization equipment, has successfully integrated 3D printing for not only design and prototyping, but also fixturing, tooling, and even stop-gap production of end-use parts. One component of that integration has been bringing selective laser sintering (SLS) 3D printing in-house.
The Formlabs Fuse Ecosystem enables Brookfield Manufacturing Engineer Ethan Rowe to manage hundreds of requests from the internal validation and manufacturing operations teams. By batch-producing parts, he can quickly deliver industrial quality 3D printed components for multiple applications. "Bringing SLS in-house has allowed us to further adopt AM through the business due to its excellent finish and material properties," says Rowe.
Bringing Additive to the Shop Floor at Brookfield
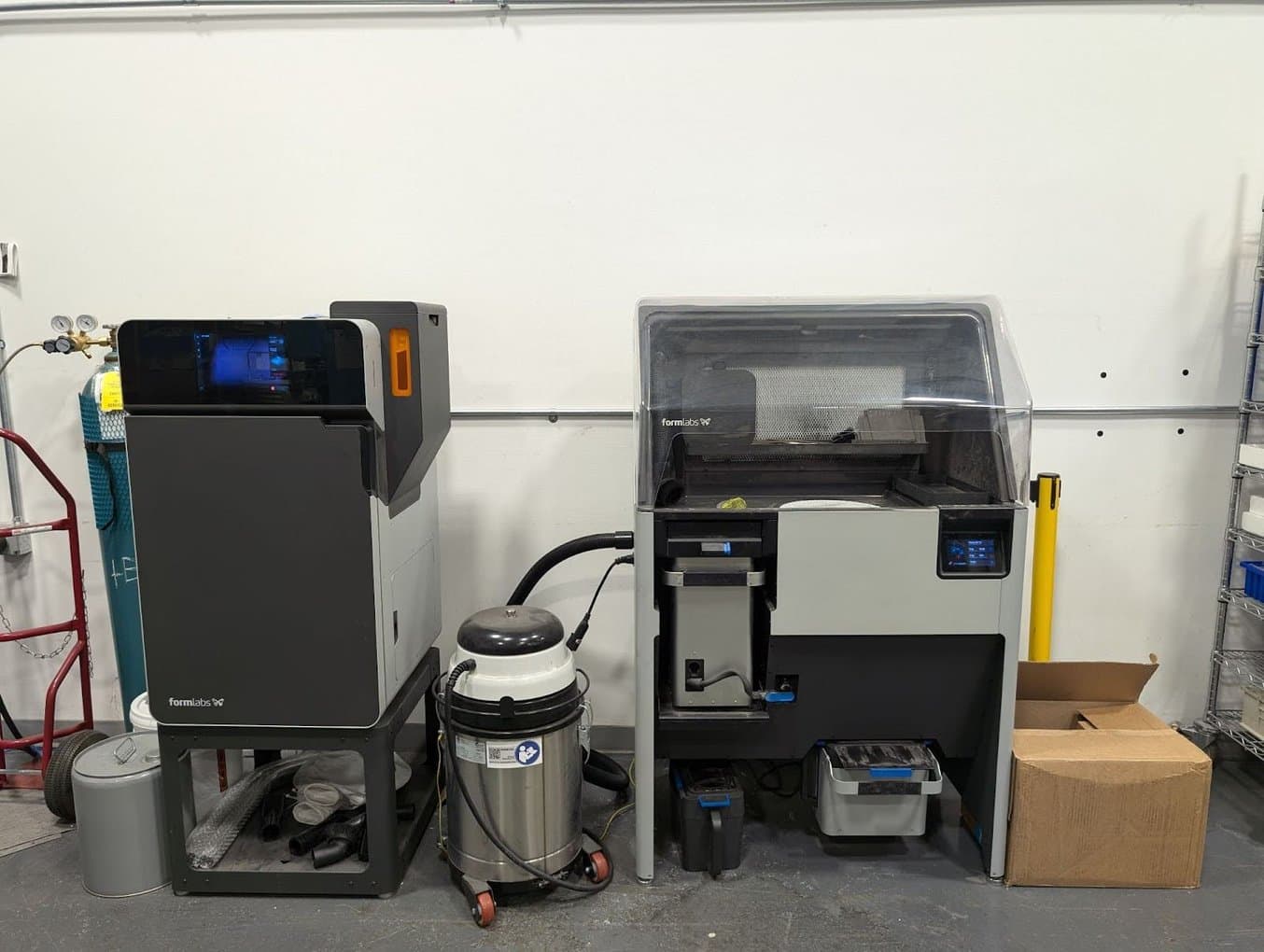
In-house production with the Fuse Series SLS 3D printers doesn’t have to take up a large footprint — the Fuse 1+ 30W printer and Fuse Sift pictured here cover just a few square feet of floor space and don’t require complex infrastructure.
At the AMETEK Brookfield manufacturing location in Middleboro, Massachusetts, the design, engineering, and manufacturing teams utilize a range of fabrication technologies to develop industrial lab equipment. Their powder flow testers, texture analyzers, viscometers, and more of the industrial equipment form the backbone of validation processes for hardware manufacturers in industries like automotive, aerospace, utilities, chemical manufacturing, and more.
The Manufacturing Engineering team supports these products at each stage in its lifecycle, from design, to validation, to production. Leveraging a fleet of 3D printers, Rowe is looking to find opportunities for improvement and optimization. “We work on production that enables manufacturing. It’s a lot of tooling and fixturing for the machine shop and assembly floor, as well as new product development and finding parts that represent cost savings in material, time, or labor. I touch pretty much all the products here in some way,” says Rowe.
The shop has seven fused deposition modeling (FDM) 3D printers, as well as CNC milling, laser etching, stamping, and more. After using FDM for several years, the team began to look for solutions for end-use quality nylon parts. They had been machining aluminum and printing nylon on their FDM printers, but both options were expensive and time-consuming. The FDM nylon filament was costly, and the parts displayed layer lines that made it difficult to use them in customer facing applications. “We had been trying to 3D print nylon for a long time, but the FDM equipment to do it is expensive. We were doing shipping guards, fixturing, and prototyping, but nothing we were super happy with,” says Rowe.
In addition to part quality, the team was looking for a more flexible, scalable workflow. “We were also looking for repeatability, and the ability to batch produce parts, to have the technology grow and shrink to meet demand. I wanted to be able to print 1000 of something, or 200 of something and have it be the same kind of commitment.”
Adding the Fuse 1+ 30W allows Rowe to shift production in response to demand from around the Middleboro campus. Using the Fuse Series, he can do seven iterations of one design overnight, and print hundreds of small fixtures the next day to be used on the assembly floor.
“The Fuse itself is really, really easy to use, and it beats throughput from an FDM printer. And I have more confidence that the parts are going to come out right.”
Ethan Rowe, AMETEK Brookfield Manufacturing Engineer
Cost Savings: Replacing Machining and Reducing Labor Time
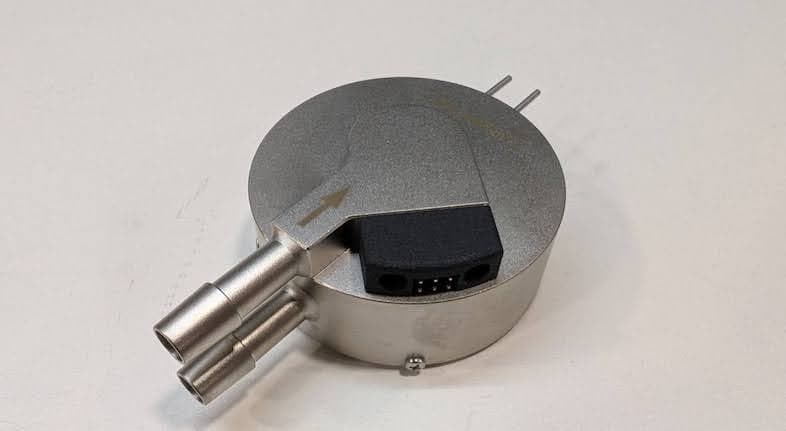
The small electronics clips for an RTD Port connection on this cone plate accessory are traditionally milled, in quantities of a few hundred each year. Though the milling is easy, they have to be hand-loaded, which takes hours. Producing these end-use parts on the Fuse Series drastically reduces labor costs.
Rowe’s team focuses on finding projects where they can deliver maximum value. They look for opportunities where a Fuse Series component can deliver the performance and end-use aesthetic of an injection molded or milled part, without the hands-on labor time of a machinist.
For one product, the Wells-Brookfield cone plate accessory, the machine shop had to mill hundreds of small electronics clips for an RTD Port connection component every year. The cost of the material wasn’t the issue — it was a small component, and easily machined — but the effort of loading these small, finicky parts one by one into the milling machine required hours of hands-on labor. Once Rowe identified the opportunity, he worked with the internal testing validation team to design a 3D printable replacement. Overnight printing in nylon on the Fuse 1+ 30W allowed them to go from concept, to design and validation, to end-use production all with one machine and one workflow.
“It definitely simplifies things — working with the same material from prototyping to end-use production is really beneficial. In the past, I’d want to be prototyping in something less expensive, which might hide the imperfections you would see later on, but now we can do both in one material,” says Rowe.
The design workflow optimization saves the company money and speeds up the time to get the solution to the customer. But the real cost savings comes from labor cost savings. Loading these parts into the milling machine was the bulk of the parts’ total cost to produce. With a 3D printer capable of end-use production parts, the labor became a non-factor, and switching from milling to SLS reduced costs by 88%.
“Though it’s traditionally machined, we can put 1000 into the Fuse at once, and avoid the time to hand-load these parts into the milling machine. The price per part went from $25 to $3.”
Ethan Rowe, AMETEK Brookfield Manufacturing Engineer
Adding Complexity Without Additional Cost or Time
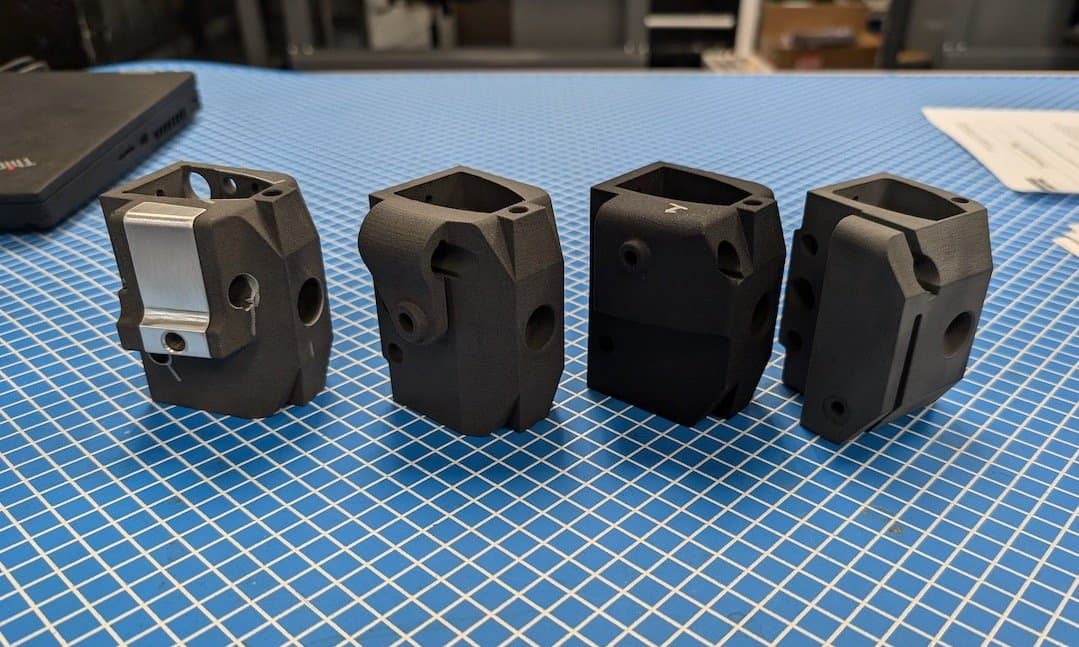
These components for Brookfield’s HPQA™, Helipath Quick Action Lab Stand have several features that are impossible to machine. Rowe’s team steadily produces these in-house, making about 12-15 every week, while keeping their supply chain agile and allowing for any design adaptation down the road.
Having the Fuse 1+ 30W printer just down the hall means the validation and design teams can add features and test them without backing up the machine shop or having to simplify their design. On one new product for the HPQA™, Helipath Quick Action Lab Stand, the team was able to add features throughout the process that were previously impossible to machine. First a metal clip, then a screw thread, a motor housing, and an internal cavity with a custom extrusion — the part kept evolving. The part had originally been sent to the machine shop for their typical workflow, but was turned down.
“Our machine shop no-quoted this, so we then looked at outsourcing, and it would have cost about $50-$70 to outsource to an MJF printer. With in-house Fuse, it costs us $15-$20 of powder and materials, and we’re doing about 1000 of these a year.”
Ethan Rowe, AMETEK Brookfield Manufacturing Engineer
In-house SLS meant Rowe could print a new iteration every day to be tested, and that complexity in the design didn’t translate to more material or labor. “3D printing these parts allowed us to have a bunch of these expensive features on a traditionally machined design relatively easily. The real benefit for SLS for parts like this is that it would require expensive equipment to machine, and it would take a lot of time. With 3D printing, I got 10-15 of these parts in the span of a week,” says Rowe.
Many of these components are used as final validation parts that need to stand up to rigorous testing. When they meet with customers and their management teams, the feedback has been overwhelmingly positive. “Our project manager’s feedback is that the parts looked casted, as opposed to 3D printed. Typically, 3D printing has the connotation of layer lines, but these look really nice,” says Rowe.
Stop-Gap Production for Supply Chain Fixes
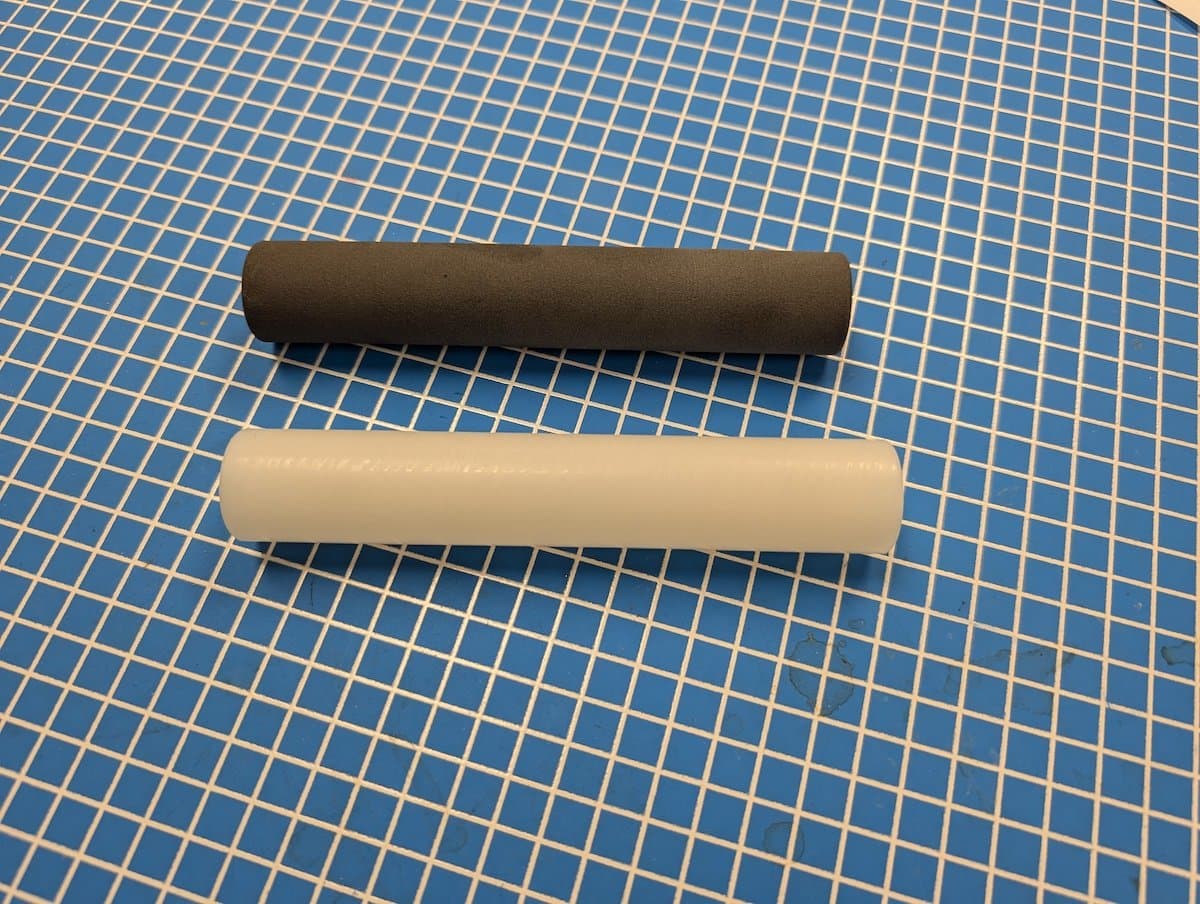
When a supplier couldn’t deliver an order of 30 spring retainers in time for a project, Rowe’s team reverse engineered the parts, validated them through functional testing, and produced the on-site with their Fuse 1+ 30W SLS printer and Nylon 12 Powder.
Recently, a vendor had their own supply chain snarls; they didn’t receive an overseas shipment of components and couldn’t deliver an order of 30 small spring retainers to AMETEK Brookfield. Rowe’s team was able to step in with the Fuse 1+ 30W and Nylon 12 Powder, and put the spring retainer component through a reverse engineering process, validation testing, and production run of 30 components in under two weeks.
“We ran the spring through torture testing and life cycle testing as well as elevated heat tests. We then shipped it back and forth between facilities to give it the full gamut of how mailing services will abuse it. After it survived, we printed it and kept it as an alternative manufacturing option,” Rowe told us.
The original part was a simple nylon extrusion and didn’t cost Brookfield much, so the advantage isn’t in high cost-savings. Instead, producing these parts in-house on the Fuse Series gave the team more flexibility and security — they were able to keep their production running without a hiccup and deliver their customer orders on time. “It was fast. There was no redesign necessary, so we could print it immediately. We had them ready for testing the day after someone asked for them.”
Process Improvement at AMETEK Brookfield
Brookfield looks to increase operational efficiency at their headquarters, in-house additive manufacturing is playing an ever-larger role. Bringing SLS 3D printing in-house with the Fuse Series has added another tool to address inefficiencies and find cost-saving opportunities.
Each kind of 3D printer has its own advantages. For some parts, like quick widgets on the assembly floor, assembly operators have access to their own FDM machines. For more complex designs or end-use, customer-facing production, SLS is the best option. “For many of our use cases, SLS is a better option to FFF manufacturing," says Rowe.
To learn more about the Fuse Series and the Formlabs SLS Ecosystem, visit our page. To see the quality of SLS 3D printed parts, request a free sample of Nylon 12 Powder.