How Deutsche Bahn Uses 3D Printed Manufacturing Aids to Streamline Vehicle Maintenance
As one of the largest railway companies in the world, Deutsche Bahn is responsible for the mobility of more than 10 million passengers per day. Maintaining the massive infrastructure required to transport millions of people is no small feat — the company operates over 50 plants throughout Germany to service its fleet of passenger and freight trains.
The northernmost plant of DB’s vehicle maintenance subsidiary is located in Neumünster, which employs close to 750 people who maintain, repair, or at times, completely overhaul or modernize passenger coaches for intercity and commuter trains. It is also one of the locations with an on-site 3D printing workshop to make operations more efficient.
“We started with 3D printing in 2015, and since then we have already produced over 100,000 parts at Deutsche Bahn that have resulted in millions of Euros in savings.”
Susanne Tost, Marketing Specialist at DB Group Project 3D Printing
Read on to learn from Carsten Wolfgramm, Manufacturing Engineer and Additive Manufacturing Specialist at DB Vehicle Maintenance, and Susanne Tost, Marketing Officer at DB Group Project 3D Printing, how Deutsche Bahn uses Formlabs 3D printing solutions to produce manufacturing aids that simplify workflows, reduce costs, and help get trains back on the rails faster.
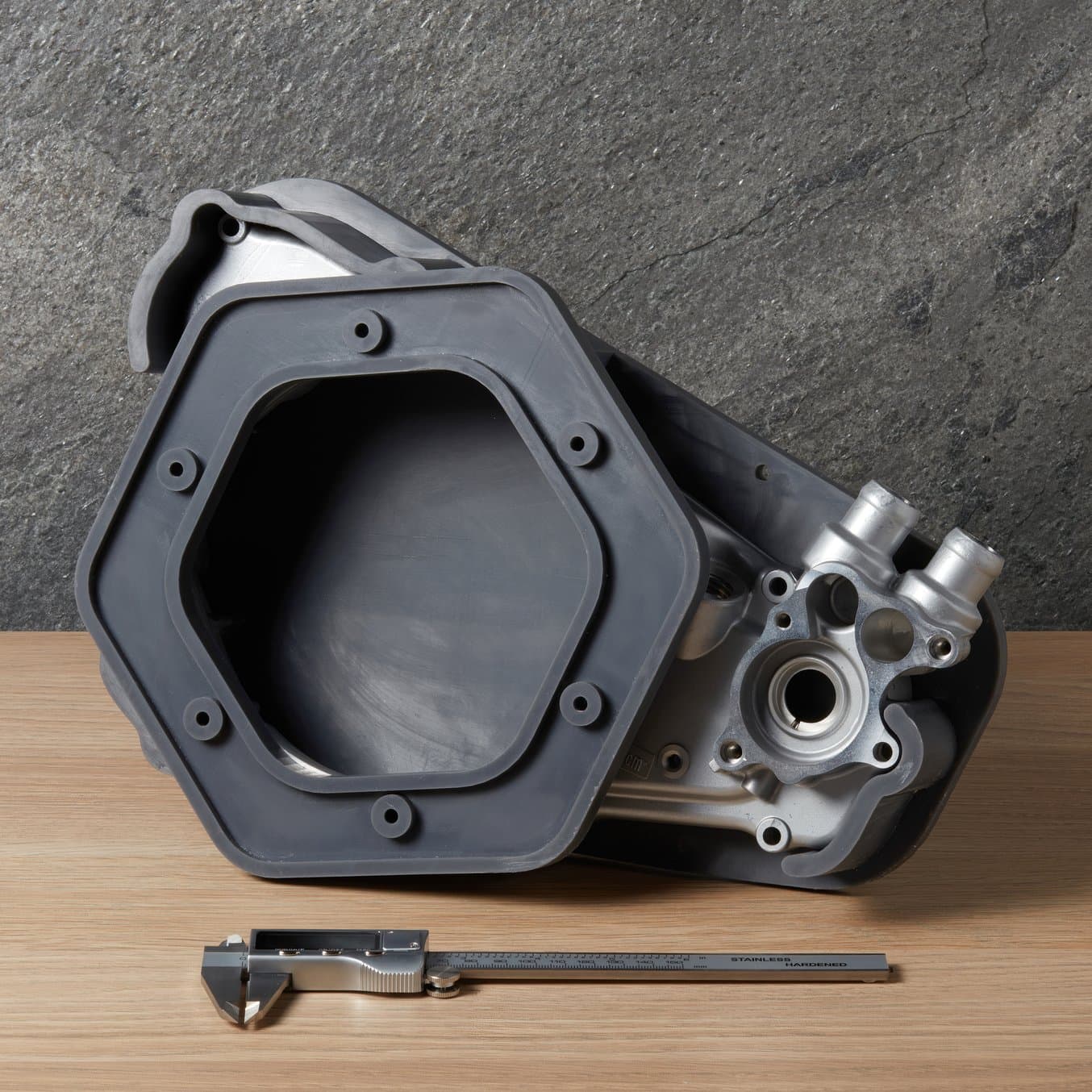
How to 3D Print In-House Jigs, Fixtures, and Other Manufacturing Aids
This white paper outlines the principles behind creating effective jigs, fixtures, and other manufacturing aids in-house.
Producing Manufacturing Aids On-Site, On-Demand
Aimed at business travelers and long-distance commuters and traveling at speeds up to 320 km/h, the Intercity Express or ICE is the flagship passenger service of Deutsche Bahn.
The first-generation ICE 1 coaches have been on the rails for more than 30 years and are now being completely refurbished — practically gutted, rebuilt from the ground up, upgraded with modern amenities, and repainted.
This major modernization project requires close cooperation of multiple plants and departments, as well as various trades, such as painters, locksmiths, electricians, and more. Neumünster is one of the plants acting as a hub for this cross-country operation.
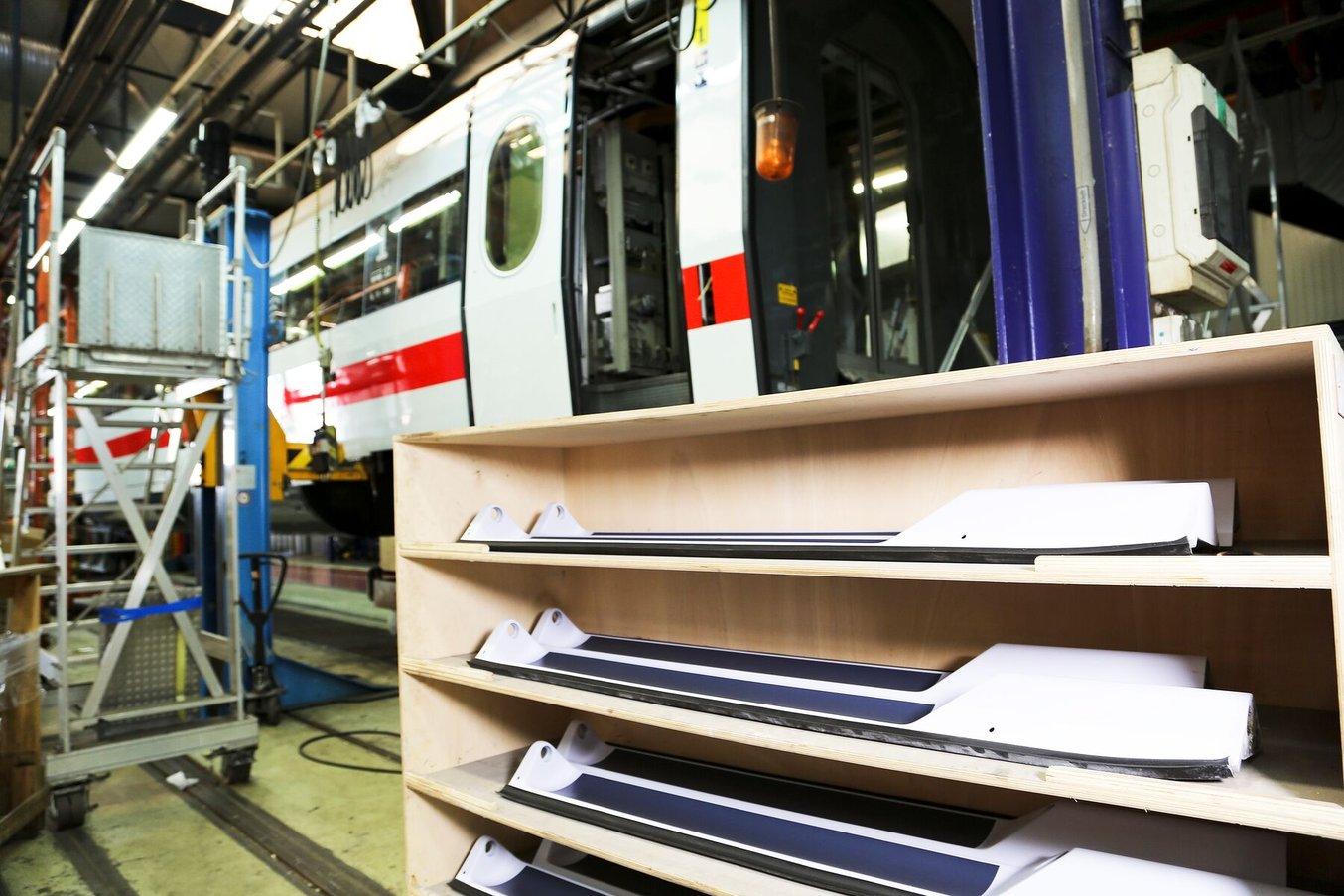
DB Vehicle Maintenance Neumünster is one of the plants involved in the major modernization project of ICE 1 coaches.
“Manufacturing aids are essential because you can't do everything with conventional tools that are available for purchase,” says Wolfgramm.
During the refurbishment of each component and when the coaches are disassembled or reassembled, there are lots of steps that can be done more easily to save time or ensure quality and consistency. When dozens of coaches are modernized, the benefits of these tools quickly add up.
“In close cooperation with the employees here at the plant, but also with the other plants, we are developing a lot of practical tools that help workers glue pictograms, draw lines, or mark spots for drilling holes without having to spend a lot of time measuring things. Today, 3D printing technology can be used to produce great templates that make the work easier,” says Wolfgramm.
Traditionally, these manufacturing aids were produced in the carpenter's shop out of wood by sawing, sanding, and milling, or using conventional metalworking machines such as lathes or milling machines when metal parts were needed. These solutions are, however, much more time-consuming, labor-intensive, and expensive.
“Additive manufacturing offers unmatched capabilities for quickly approaching an initial shape and then refining it. Because we have the digital designs in CAD software, we can quickly adjust them there if they don't fit or need to be changed. Does a design have to be updated, enlarged, reduced, or something? 3D printing — and in particular powder printing — are unbeatable.”
Carsten Wolfgramm, Manufacturing Engineer and Additive Manufacturing Expert, Deutsche Bahn
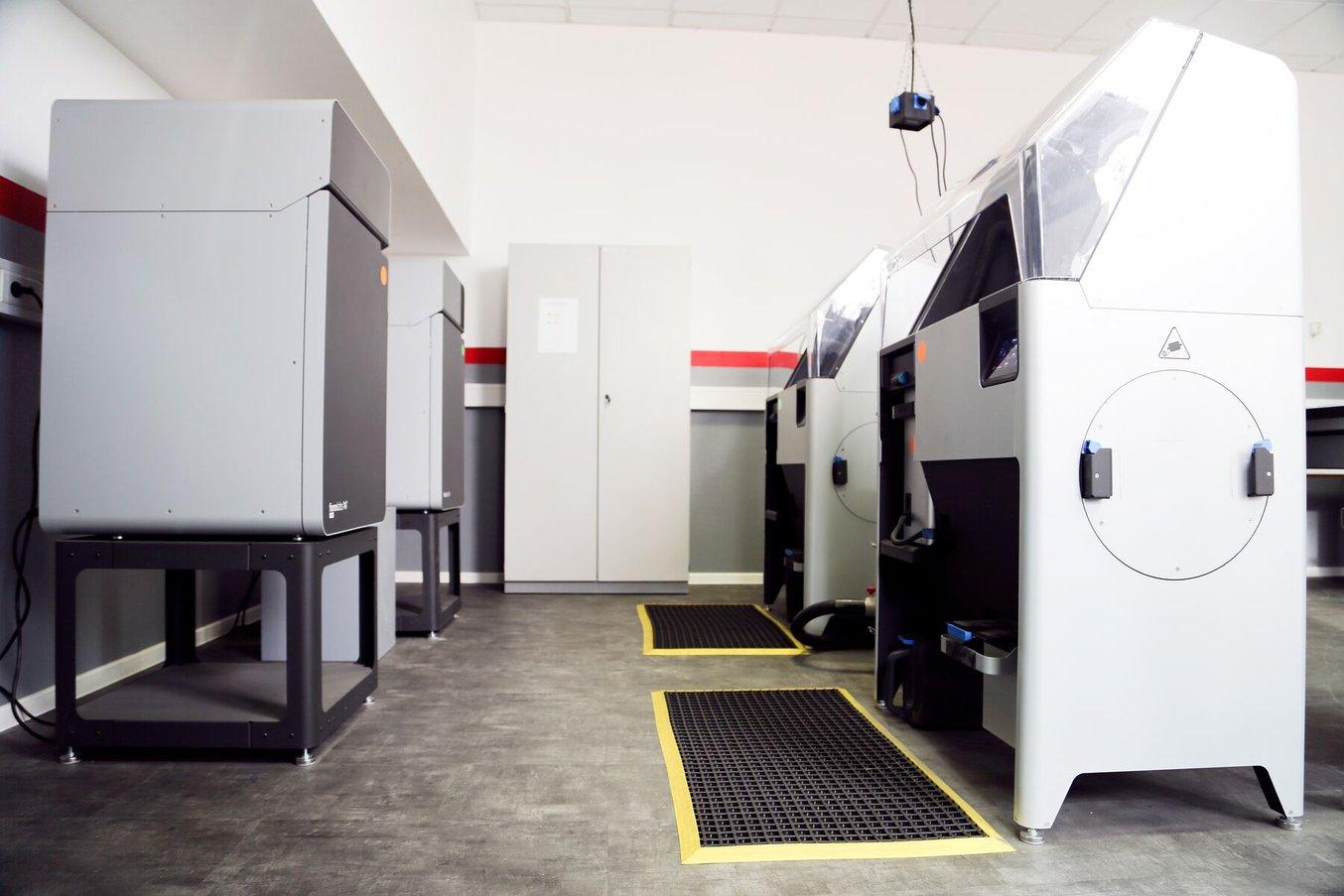
The 3D printing workshop in Neumünster has ten different 3D printers, including two Fuse Series SLS printers.
Deutsche Bahn’s team has worked in a close partnership with Formlabs Platinum Partner IGO3D on the strategic development of additive manufacturing and to identify the right solutions for their business and various applications.
The 3D printing workshop in Neumünster has ten different 3D printers on the site using a wide range of technologies. Two of them are Fuse Series SLS printers, one running versatile and strong Nylon 12 Powder, while the other prints with the flexible TPU 90A Powder. There are also two resin printers in the workshop, the large-format Form 3L and a Form 3.
Depending on the inquiry and the requirements for the component, Wolfgramm and his team can simply choose which printing process and material is the right fit for the job.
“We use Formlabs machines because the price-performance ratio is unbeatable for us. They are reliable and really plug-and-play, especially the SLS printers. This makes the job a lot easier when you’re continuously iterating parts. They run 24 hours a day, seven days a week, all year round."
Carsten Wolfgramm, Manufacturing Engineer and Additive Manufacturing Expert, Deutsche Bahn
Having the 3D printing workshop in Neumünster empowers the team to stay agile and respond to requests quickly on demand. “We are not dependent on supply chains and long delivery times, unlike when we would be sending out the orders,” says Wolfgramm.
“With 3D printing here on the site, we are in the position to be able to respond very, very quickly to the day-to-day needs in the plant. We can create designs for different applications in advance, produce them directly on-site, and then implement them in the plant. No other manufacturing option offers us that”, adds Tost.
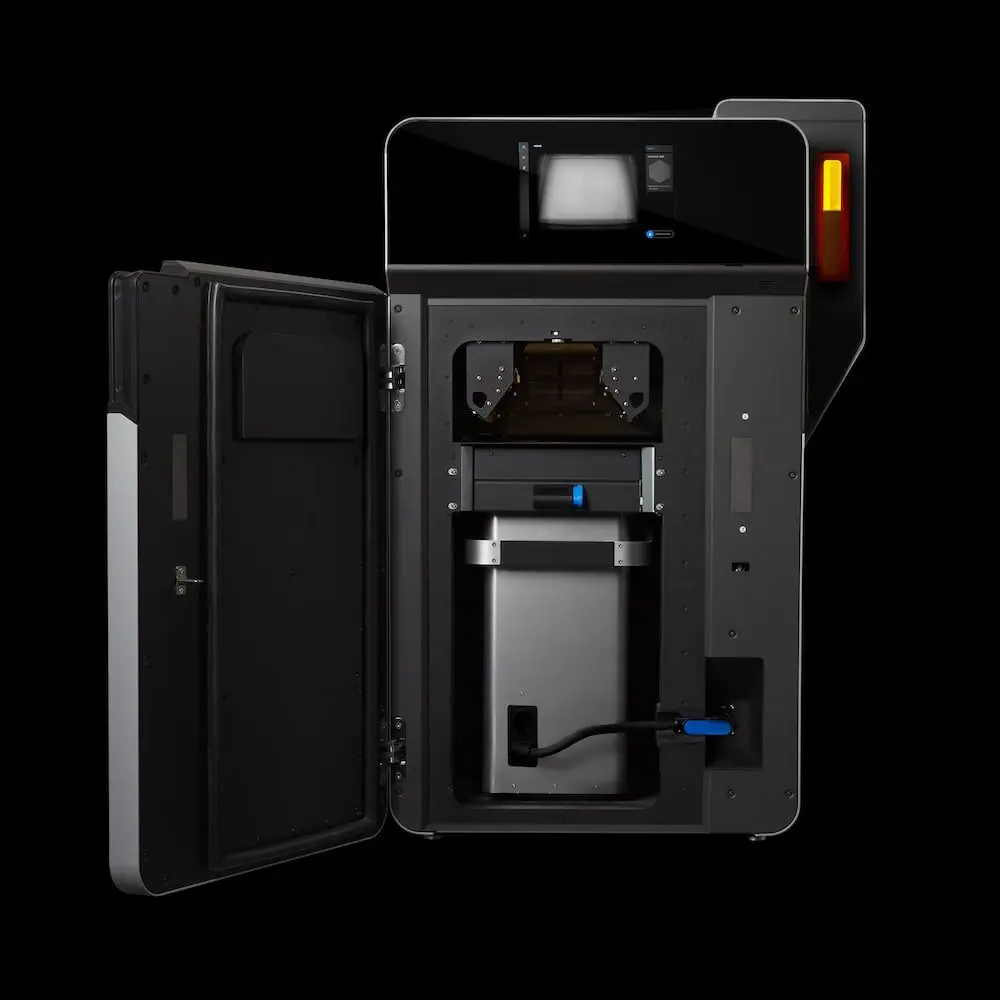
Rapid SLS Production of High Performance Parts with the New Fuse 1+ 30W
Watch our product demo for a walkthrough of the Fuse 1+ 30W and SLS 3D printing with Formlabs experts.
Additive Manufacturing Applications in Neumünster
Masking Tools for Painting
During the restoration of ICE1 coaches, all plastic components are removed, sanded, filled, and repainted. One such part is a large, grooved plastic panel that is mounted behind the door handles of each train coach. Every panel needed a new two-tone paint design, so that the dark sections offer a more long-lasting protection against dirt and traces of use.
Painting curved shapes and more complex paint schemes generally requires painstaking measurements with foldable rulers and calipers, so the painters can mark positions and mask surfaces properly to achieve a consistent finish.
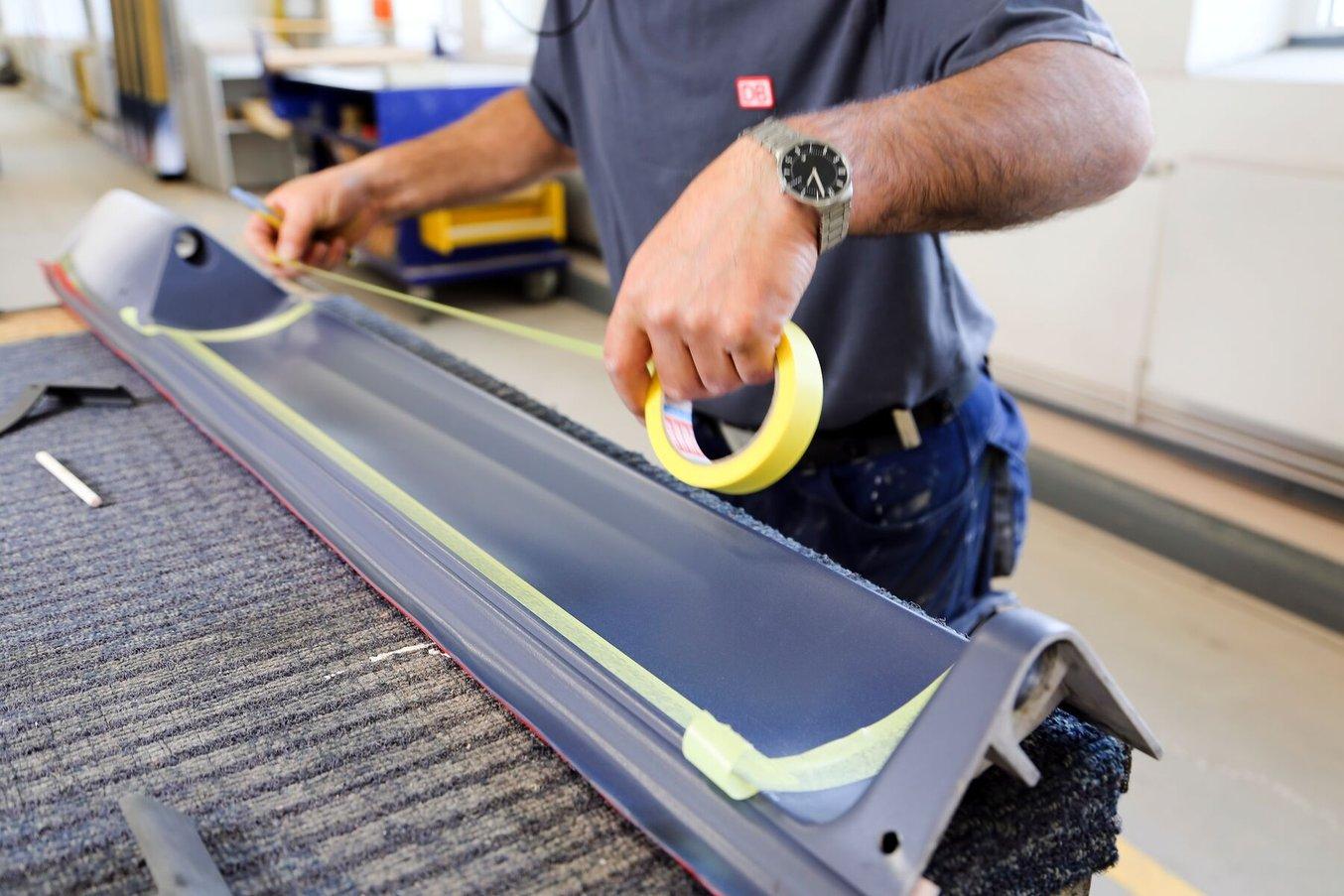
Masking organic shapes is traditionally a time-consuming manual exercise.
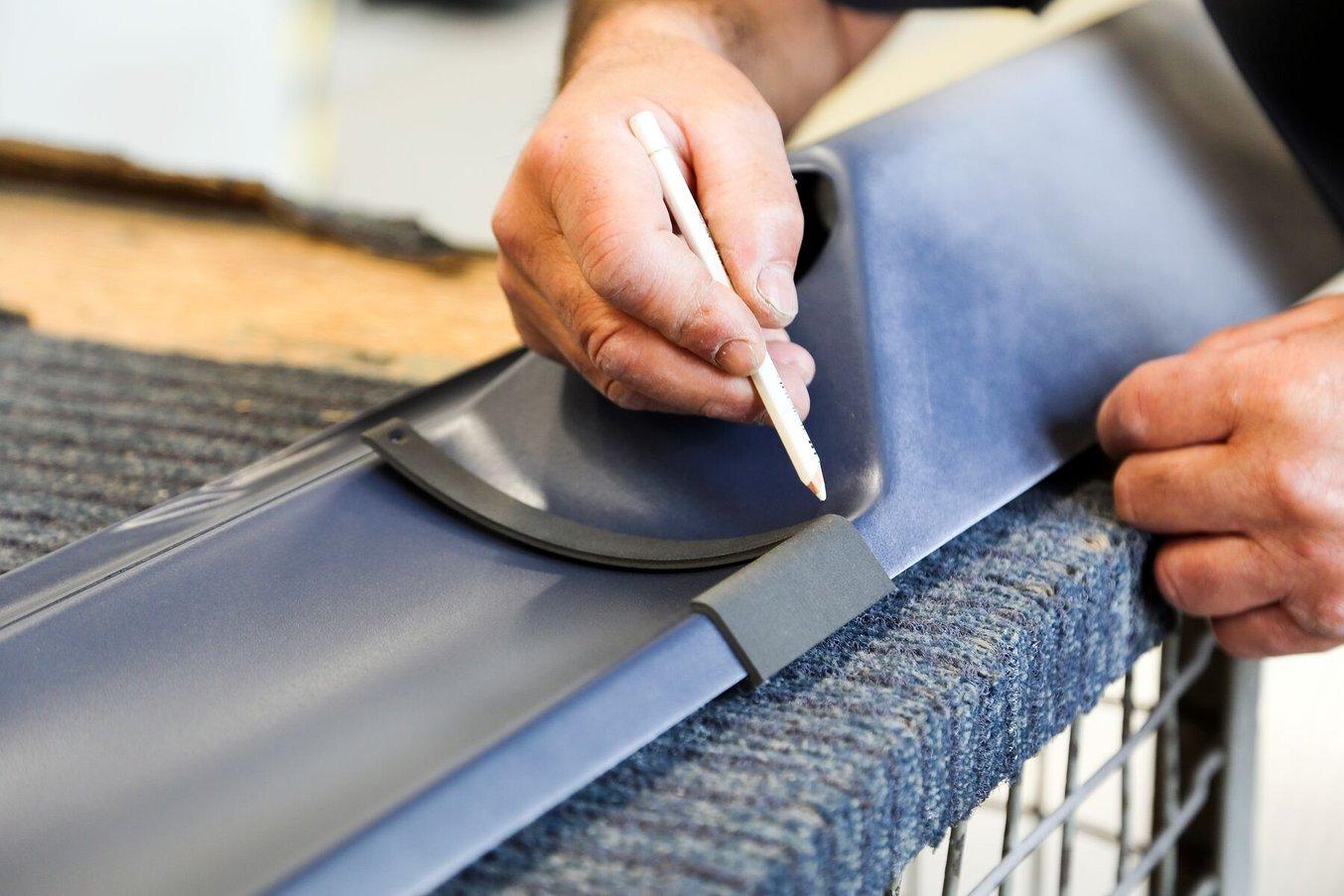
3D printed masking tools can drastically reduce the time spent on measurements.
“With 3D printing, we can easily develop a stencil. We do that once and we can then use it in a variety of ways at other plants and locations. We have examples where we could reduce 30 minutes of painting work to just two minutes.” says Tost.
Compared to traditional tools, 3D printing provides more design freedom to create complex tools that fit certain jobs. “Additive manufacturing, especially the SLS process, allows for complex geometries such as radii and small bulges,” adds Wolfgramm.
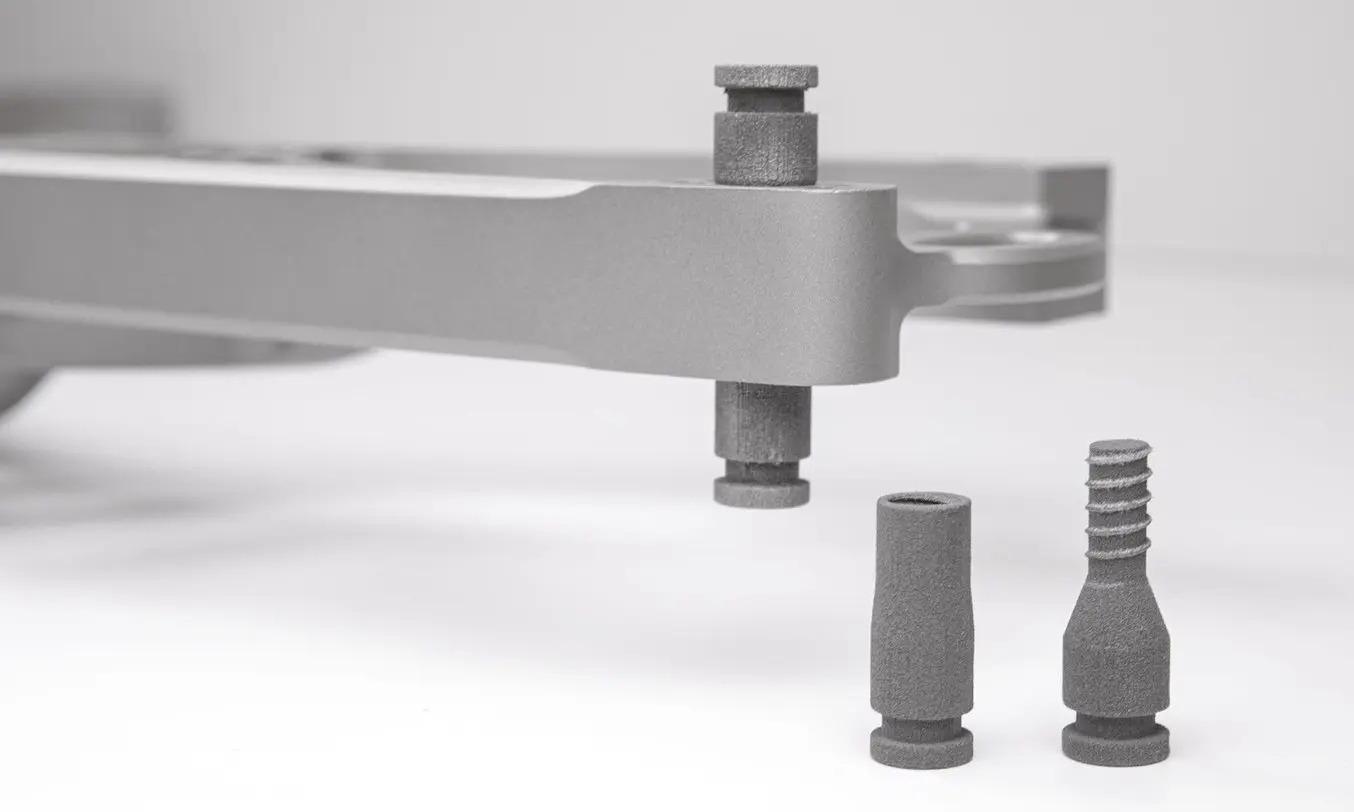
Complete Guide to 3D Printed Masking Tools
In this white paper, we’ll walk through how using 3D printing to create masking tools for painting, coating, plating, or otherwise finishing parts can reduce labor time and costs as well as enable new, complex geometries and finishes.
Scratch Protection for Luggage Racks
When the coaches are disassembled, the luggage racks get removed. After restoration, once the walls are painted and re-foiled, they need to be put back in place. The racks are bulky and heavy, and there’s a very narrow gap between them and the wall, so there was a need for a flexible material to use as scratch and impact protection. If the workers scratched the walls by accident, it resulted in expensive and time-consuming rework. DB’s team designed the custom protective covers and printed them on the Fuse 1+ 30W using flexible TPU 90A Powder.
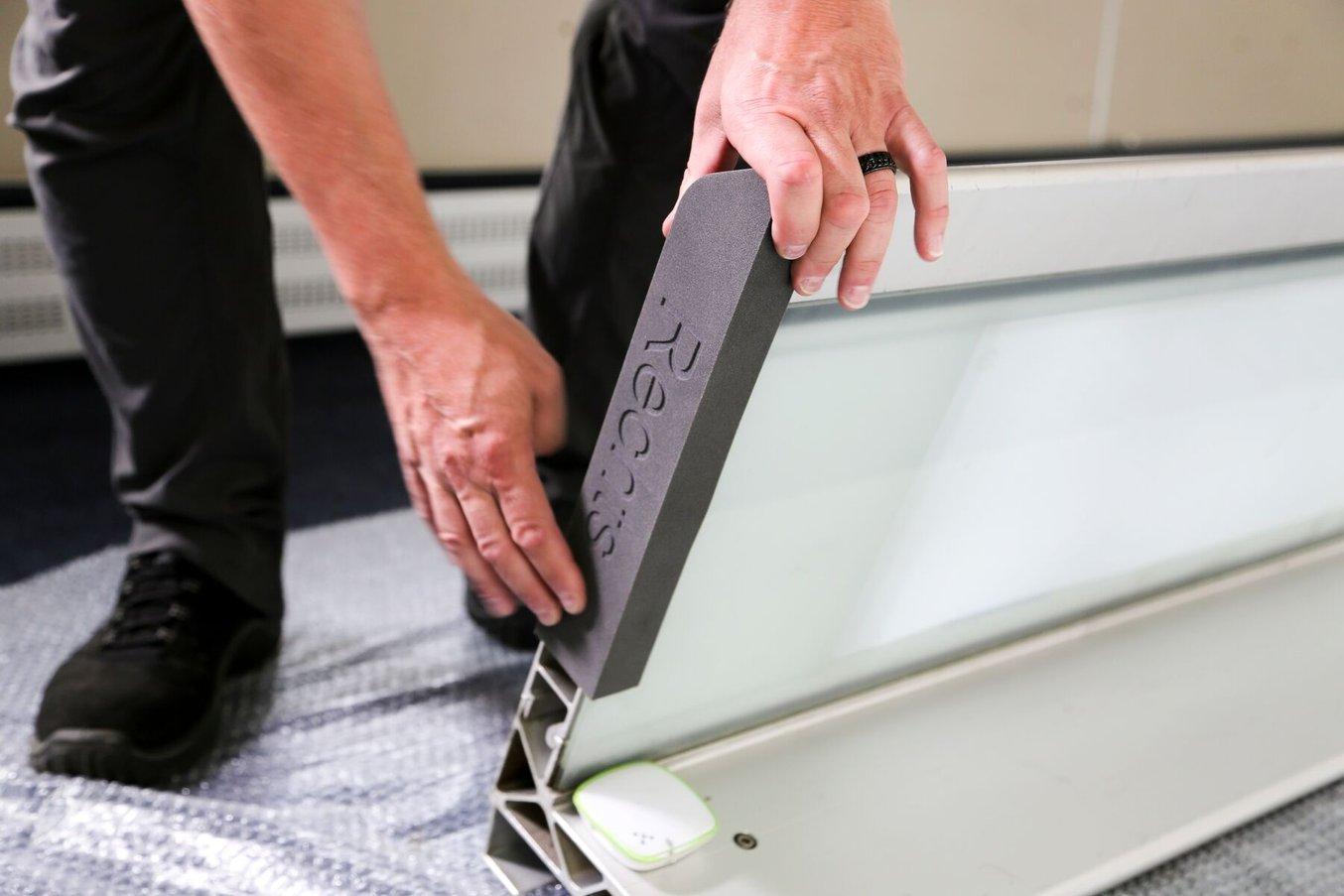
A flexible material, TPU 90A Powder, is used by the team for scratch and impact protection.
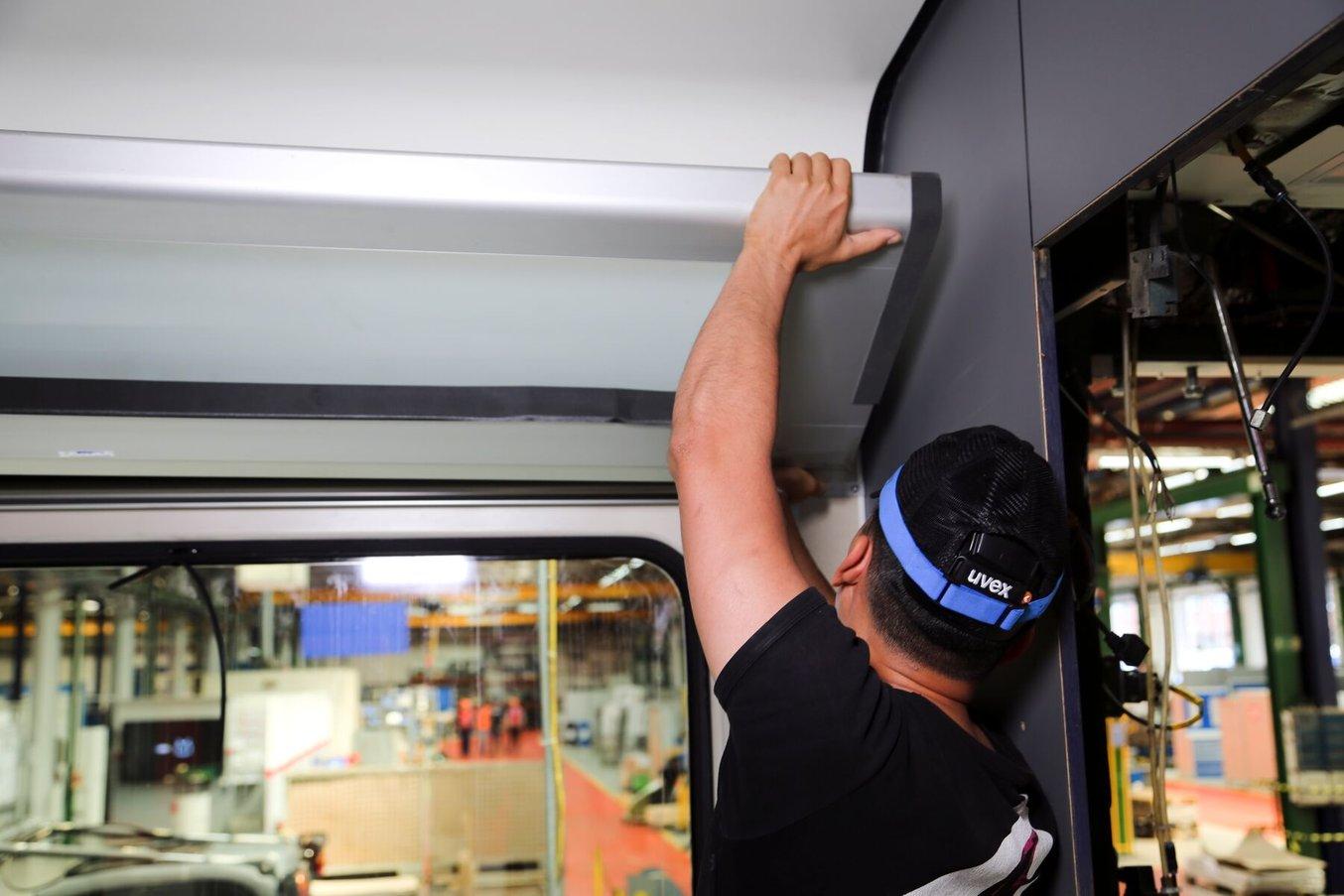
SLS 3D printing enables a slim design that can fit between the luggage rack and the wall.
“Before we developed this scratch protection and 3D printed it, our colleagues always masked it conventionally with bubble wrap or similar tools to try to avoid scratches — but this was not always successful. It’s the first time that we finally managed to completely eliminate scratches thanks to the new TPU parts,” says Wolfgramm.
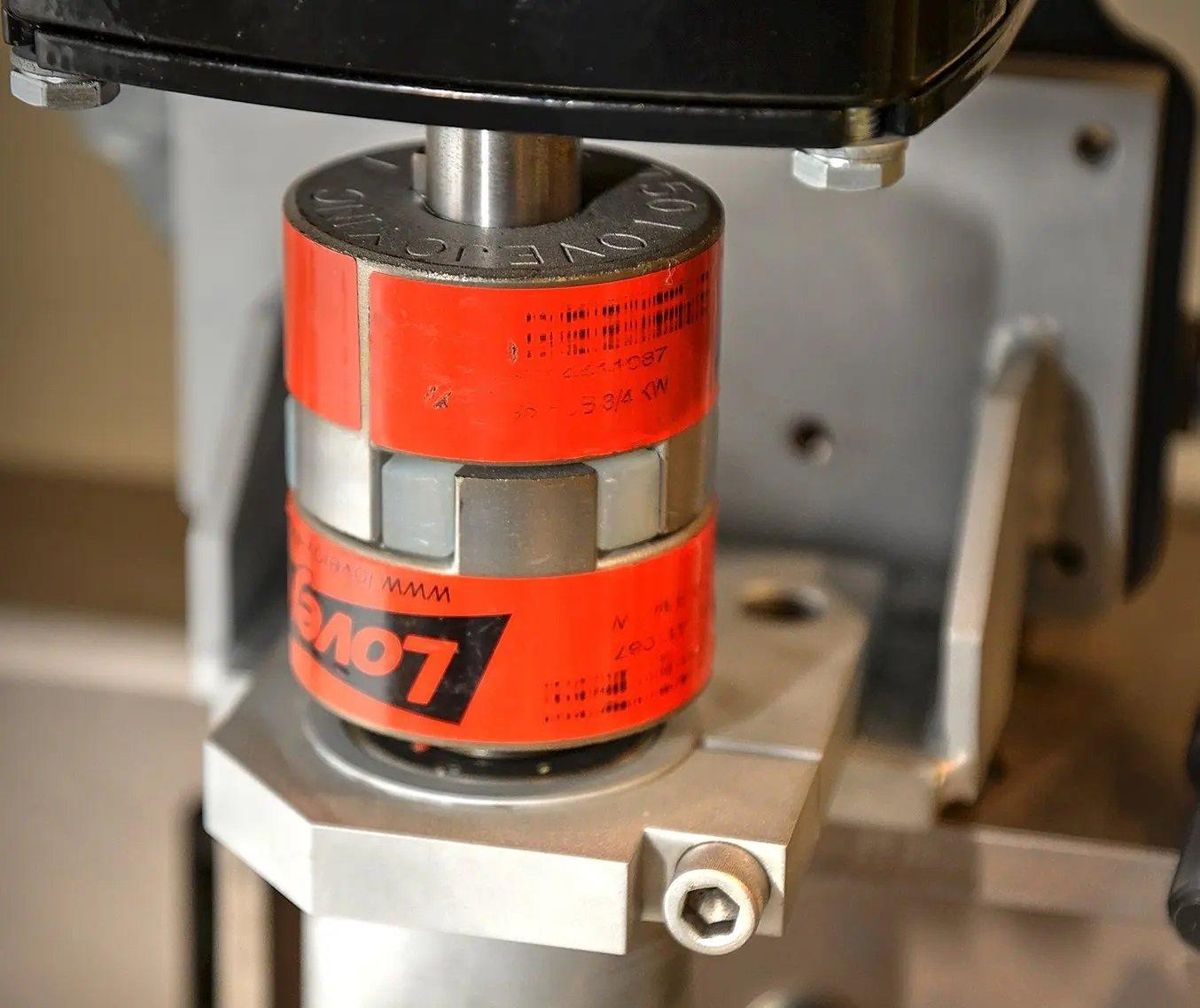
Enhance Manufacturing Efficiency with 3D Printed Jigs and Fixtures
Watch now to discover the power of in-house 3D printing for creating tailored jigs, fixtures, and tools, resulting in streamlined manufacturing operations and lowered production costs.
Cable Guide Cover Cap Prototype
As ICE 1 coaches were manufactured more than 30 years ago, there are parts that simply don’t exist anymore. During the restoration process, the team recognized that many of the cover caps that protect and guide cables for the electrical sockets mounted under the seats were broken during cleaning or went completely missing. As these are custom parts, they could not find replacements for them easily.
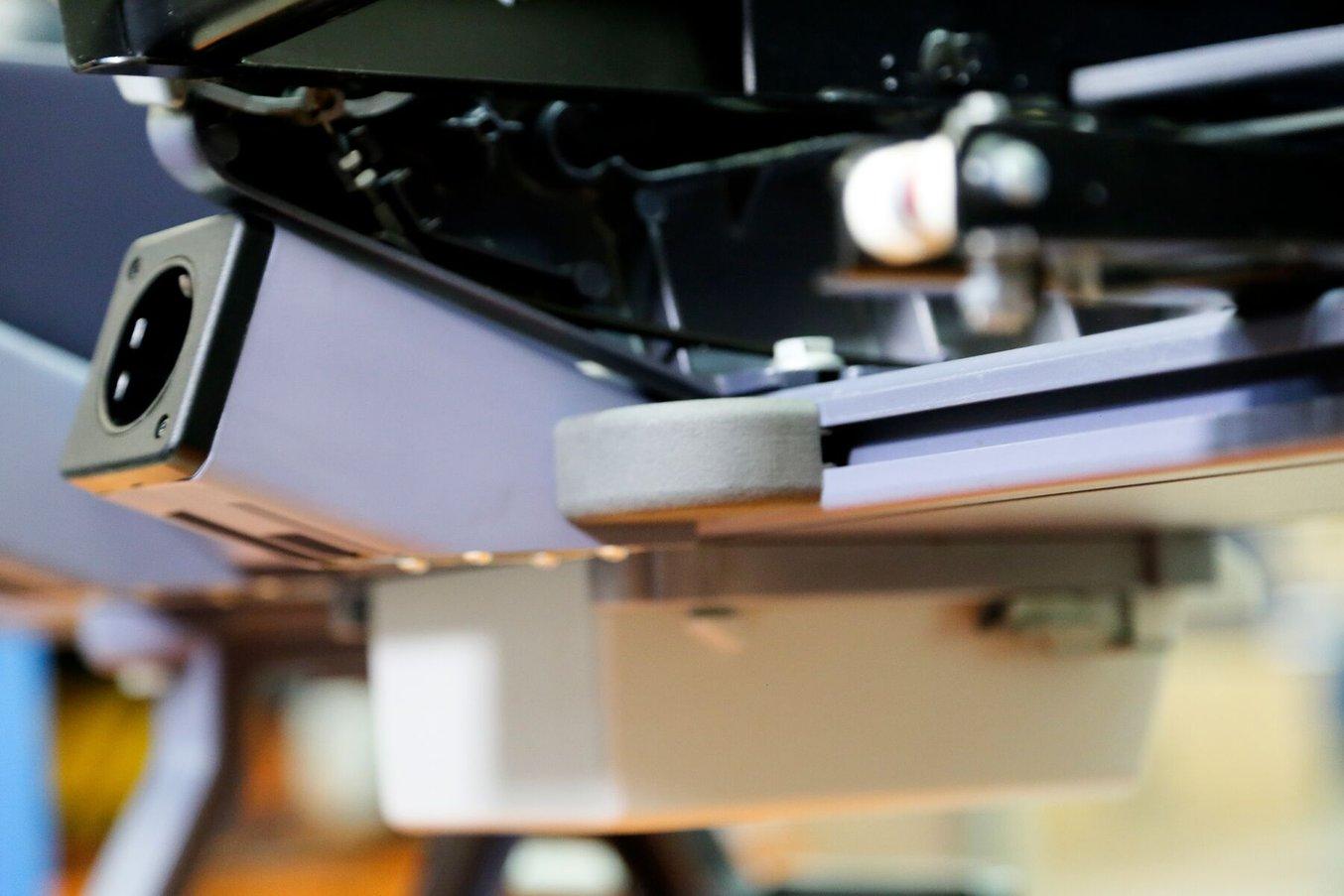
Many of the cover caps that protect and guide cables for the electrical sockets went missing on ICE1 coaches.
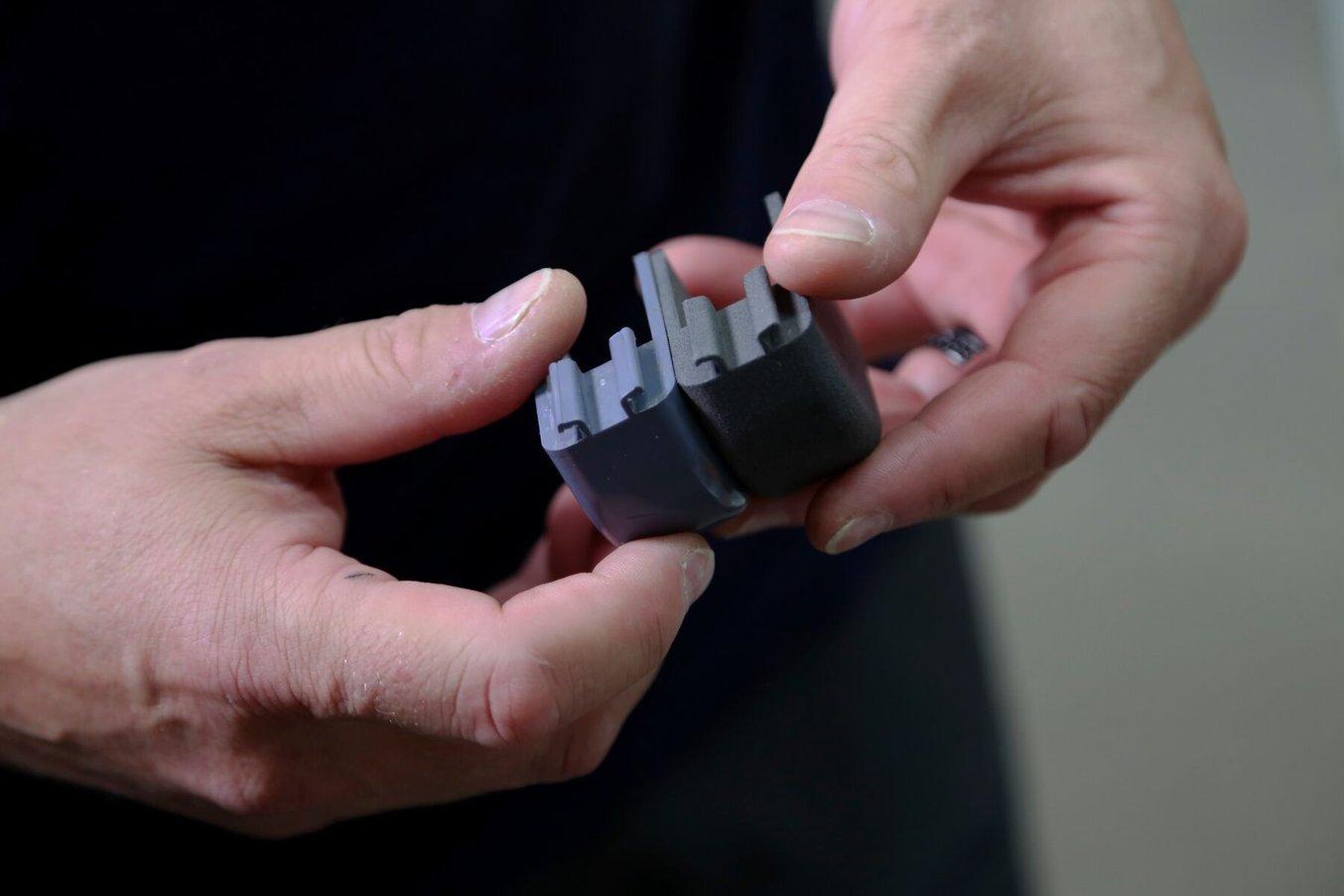
DB’s team reverse engineered the design and used SLS 3D printed prototypes to test the fit and get a feel for the real dimensions.
“They were reconstructed by DB Group and we were asked to print the prototypes with SLS 3D printing and Nylon 12 Powder to test the fit and get a feel for the real dimensions. I think already the second version fit perfectly, it was easy to slide it on. The possibilities SLS printing offers are top-notch. The fit, the speed, the material is strong enough, so we can really try it out,” says Wolfgramm.
Handheld Scanner Holder
Manufacturing aids can also be used to simplify the day-to-day tasks of workers in various plants. Employees of DB Fernverkehr working in materials management use handheld scanners to identify and manage materials. Normally, they had to carry the scanners around in their hands and put the devices down if they wanted to pick something up or use both of their hands.
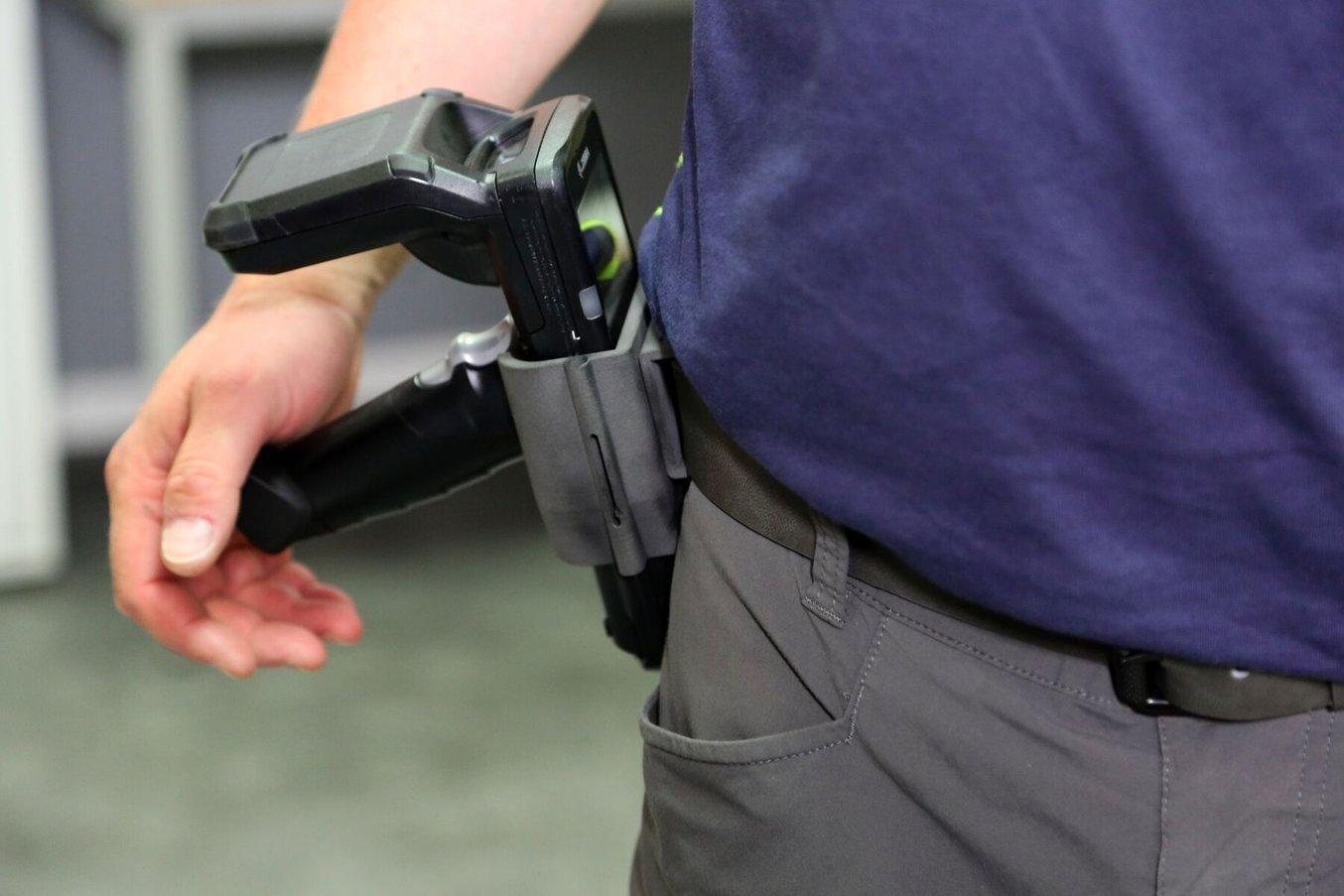
Employees in materials management needed a way to mount handheld scanners, so they could keep them close by without continuously occupying one of their hands.
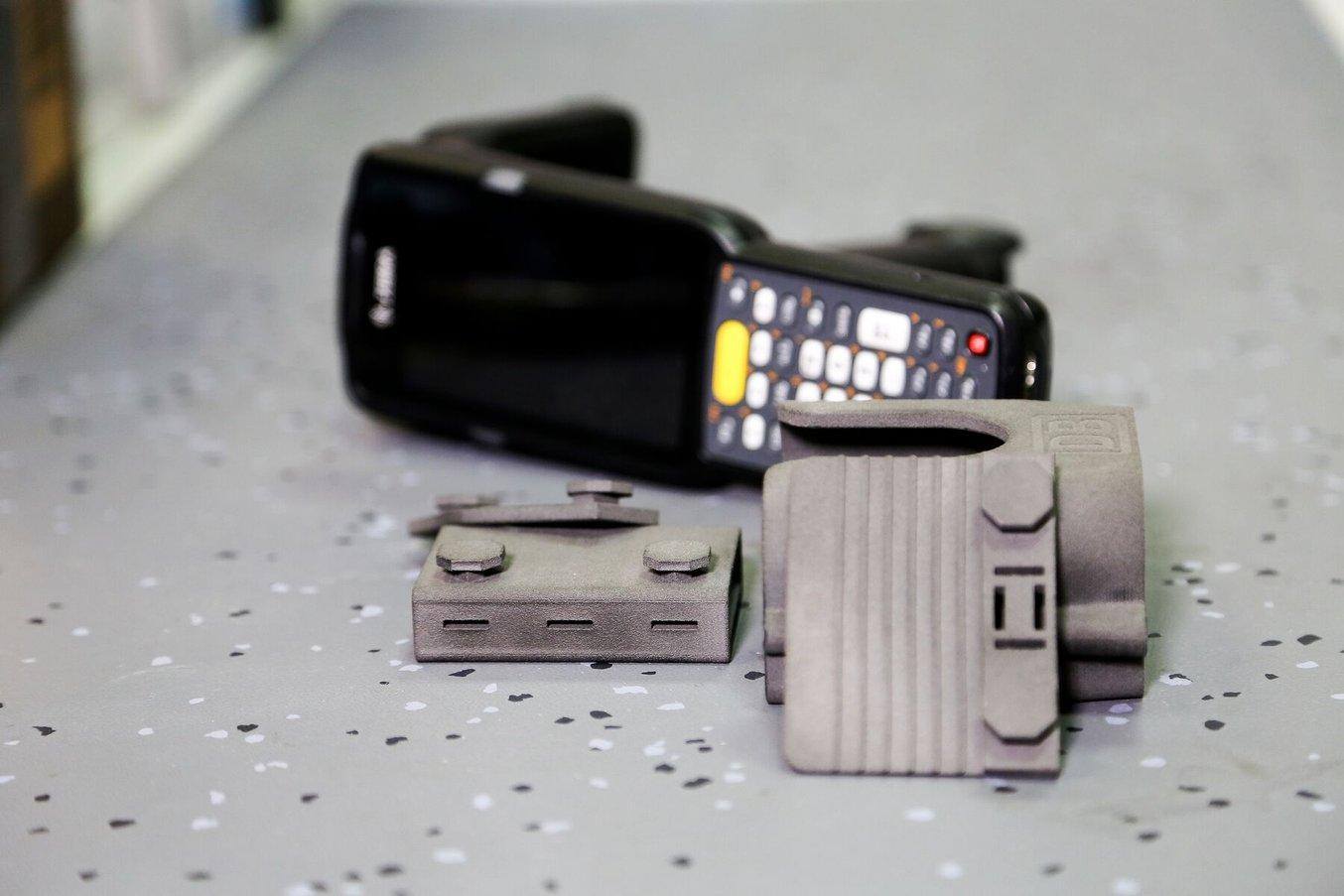
The team created three different mounts that can be attached to a bag, a belt, or a shadow board.
“They asked: ‘Can't you somehow design a mount for this handheld scanner so we can carry it around and have it always accessible?’ Ultimately, we created three different holders that you can attach to a bag, a belt, or a shadow board. SLS 3D printing is easy because it prints true to fit, and I don't have any big support structures to remove, so I don't have to do a lot of post-processing, besides depowdering and blasting,” says Wolfgramm.
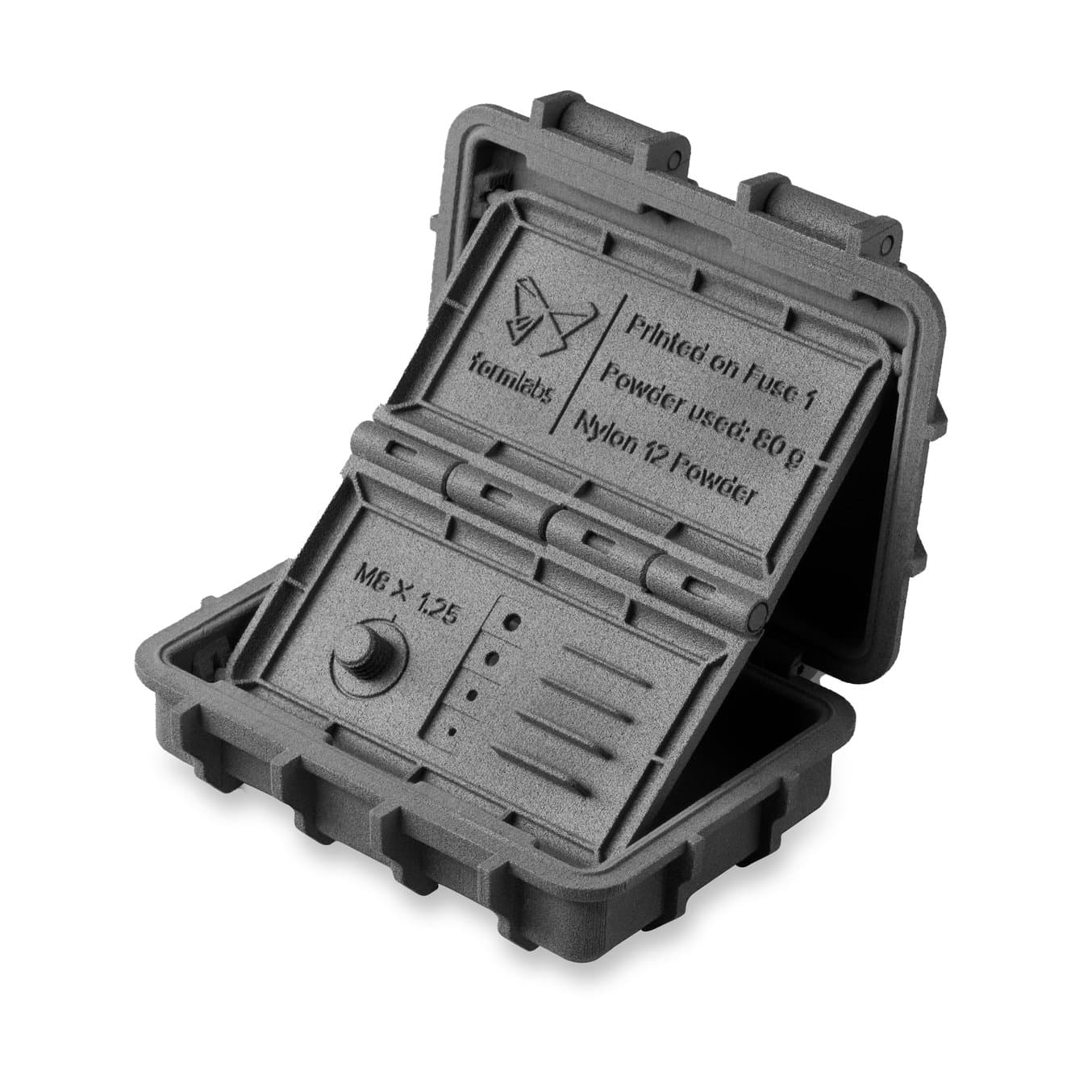
Request a Free Sample Part
See and feel Formlabs quality firsthand. We’ll ship a free SLS sample part printed on the Fuse 1+ 30W to your office.
Digitization in Vehicle Maintenance for the Future
“Additive manufacturing is here to stay. It makes complex geometries possible that could never be achieved with conventional machines and it makes it possible to simply manufacture and reproduce tools without incurring high additional costs. Once a tool or part has been digitized, it can be printed anywhere in the world,” says Wolfgramm.
The ultimate goal is, of course, to be able to manufacture more end-use 3D printed spare parts for their fleet. However, safety regulations for trains are just as stringent — or sometimes even more so — than aircraft. Today, the stringent regulations can only be met with the industrial FDM printers on site. Deutsche Bahn is collaborating with Formlabs and other partners to develop workflows, processes, and materials that can be certified to fulfill these requirements in the future.
“Our goal is to digitize 10 percent of all spare parts in vehicle maintenance by 2030. This will enable us to remanufacture parts on demand within a very short time. It’ll ensure that we can continue to deliver parts quickly, but also that we are green and handle materials and resources ecologically, thus also solving many other challenges.”