Bespoke Solutions With Formlabs: Empowering Medical Device Development and Surgical Training
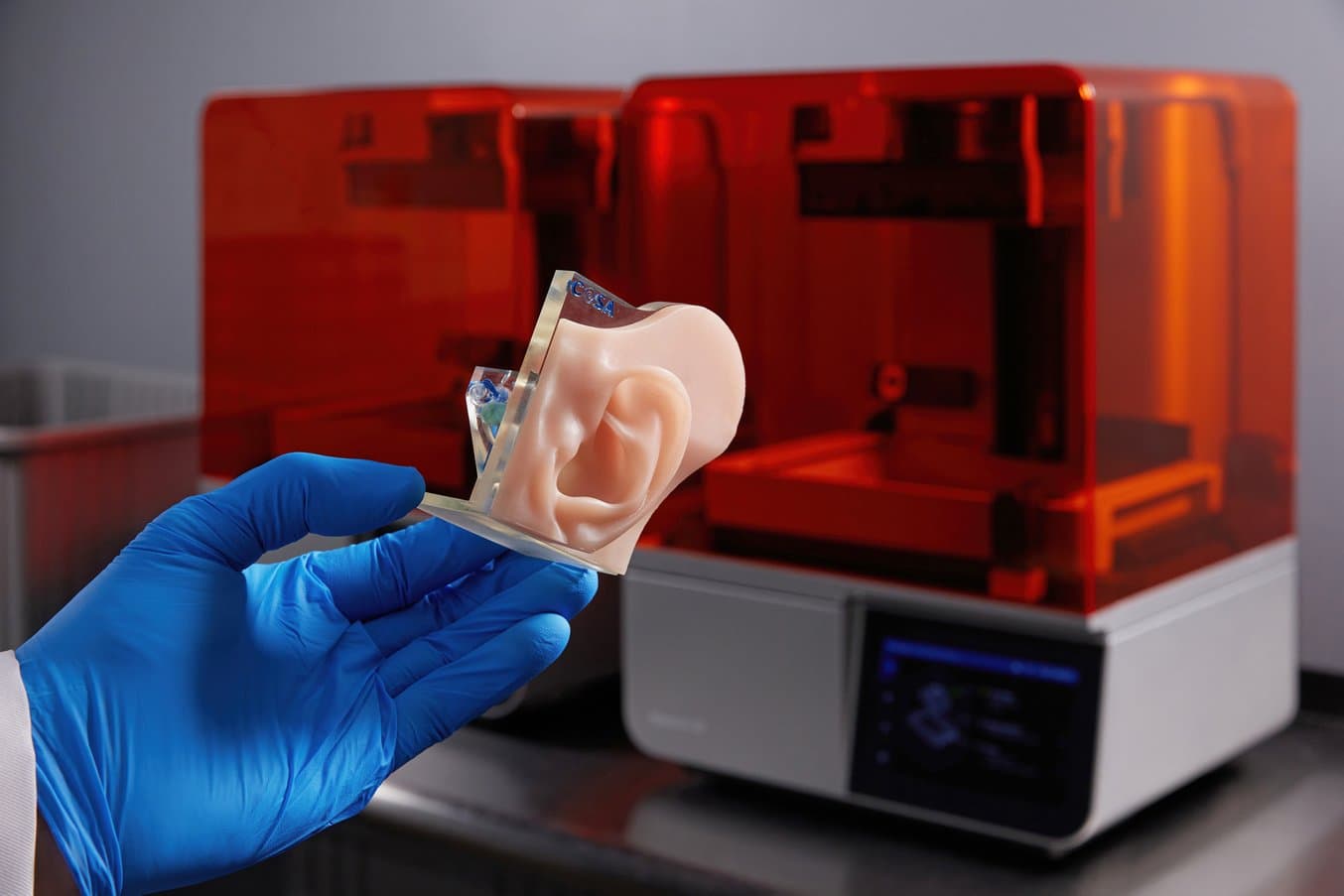
COSA Ltd. co-founders Dr. Filip Hrncirik and Dr. Iwan Vaughan Roberts offer bespoke yet accessible anatomical models relevant for audiology; ear, nose, throat (ENT) surgery; and head and neck and neurological applications. COSA Ltd. looks to disrupt the anatomical model market with high quality models that can both generate visual and functional models. This work would not be possible without 3D printing due to the complex geometries, internal channels, need for versatile materials, and high tolerances required of the products COSA Ltd. produces.
“Especially as a small company that started about two years ago that does so many types of prints, Formlabs really allowed us to start as a business. We’ve been able to extract so much value from the Formlabs printer.”
Dr. Iwan Vaughan Roberts, cofounder, COSA Ltd.
Formlabs resin 3D printers enable COSA Ltd. to offer bespoke solutions at lower costs, increasing the accessibility of surgical training tools and improving the diversity of training courses.
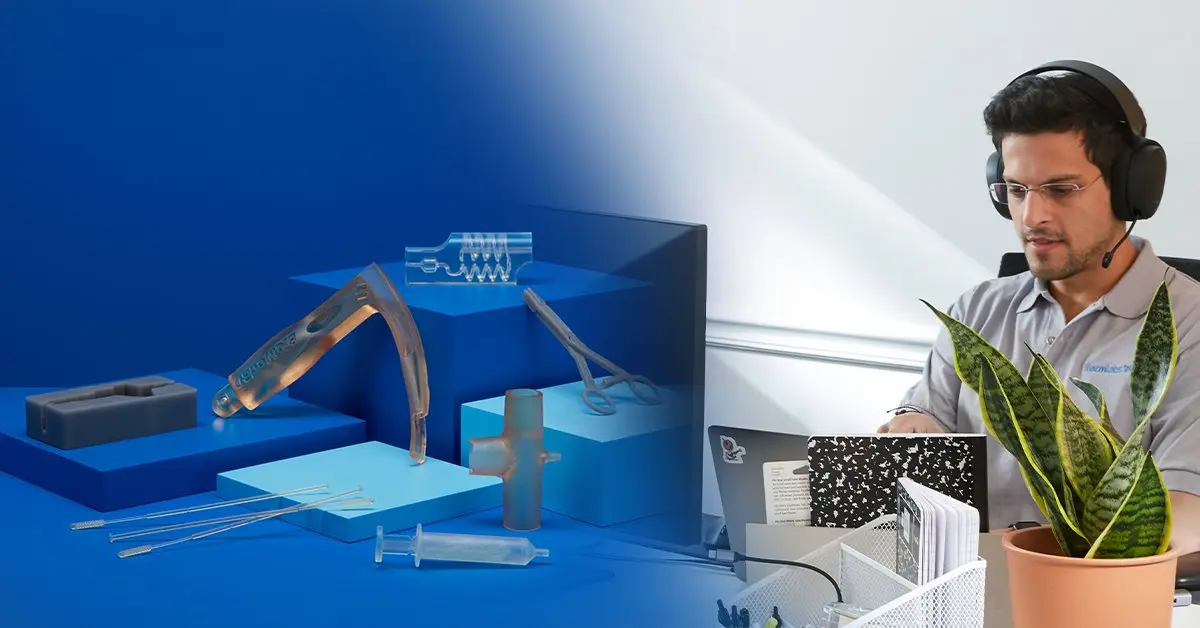
Talk to Our Medical Sales Team
Whether you need to make patient-matched surgical tools or are prototyping for a cardiac medical device, we’re here to help. Formlabs Medical team are dedicated specialists who know exactly how to support you and your company's needs.
Anatomical Models for Surgical Training
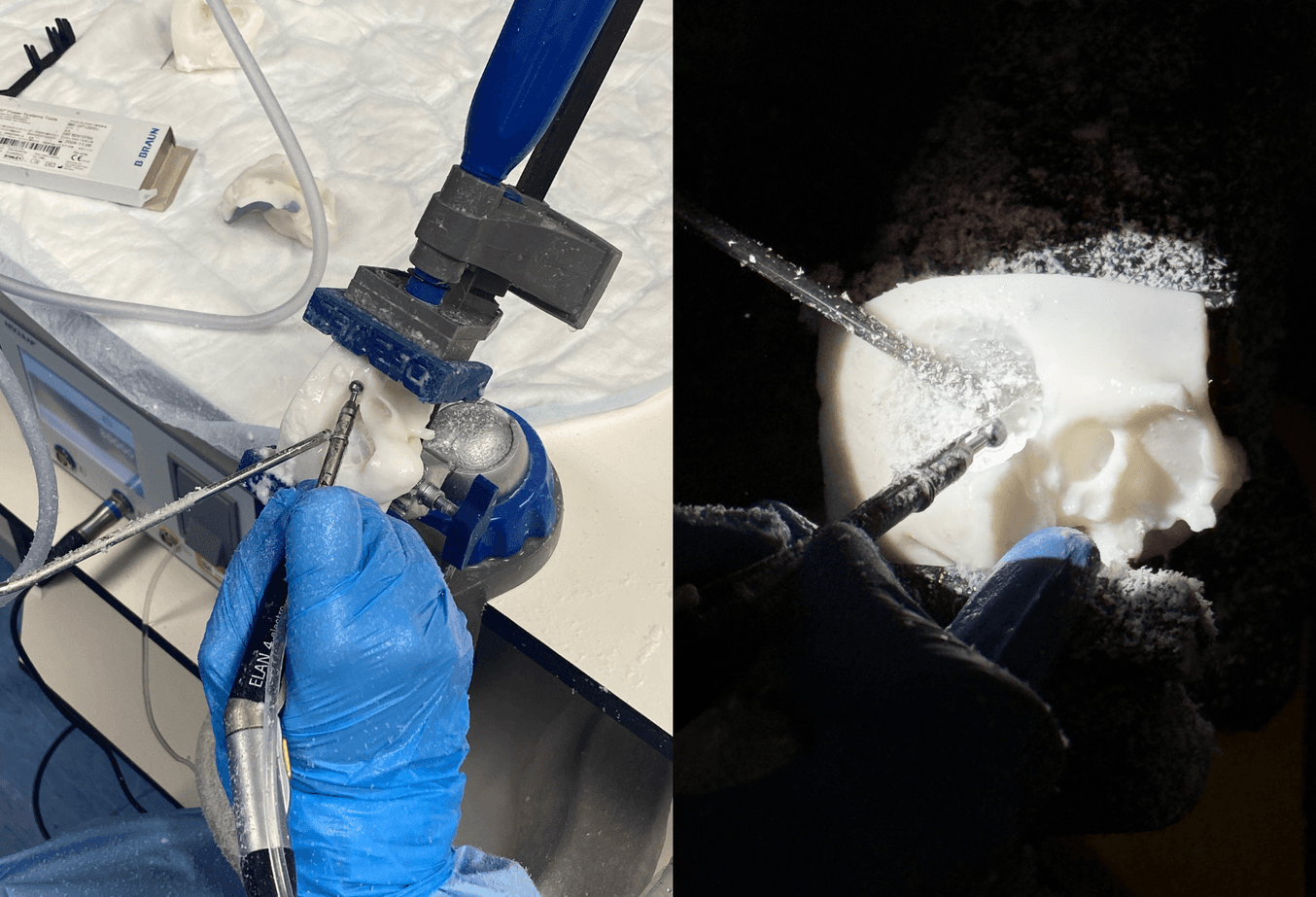
The models are used by ENTs to practice various drilling procedures and techniques.
Training for surgeries is typically done on cadavers and are vital for enabling surgeons to experience real anatomy and practice. Cadavers are very expensive, difficult to access in the UK due to regulations, and limit the possible atypical anatomies that trainees are exposed to. For example, for cochlear implants and ear-based surgeries, one cadaver could provide two ears to train different procedures. This means that the first time a surgeon may be exposed to a particular malformation or a particular disease case is during the actual procedure.
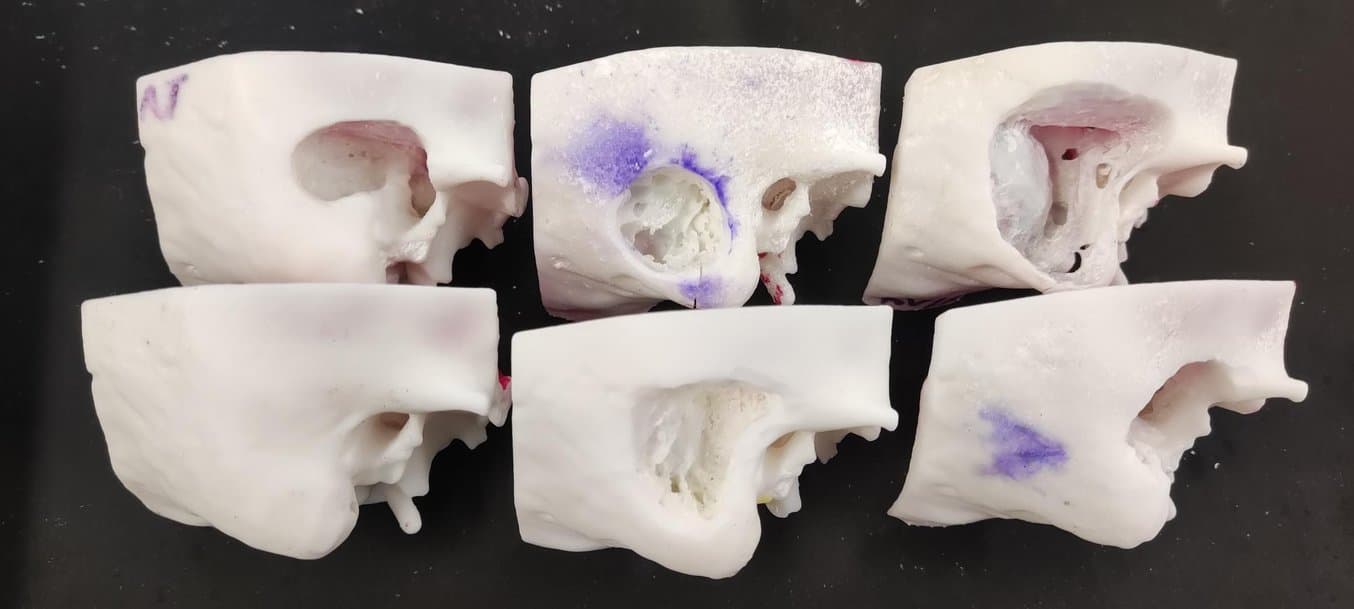
3D printing means trainees are exposed to variations and malformations they might otherwise only see during an actual procedure.
3D printing anatomical models helps to democratize access, so every participant in a course can practice on multiple models for a more thorough and complete training. Additionally, by collaborating with anatomy departments, COSA Ltd. are building a library of various head anatomical structures, including atypical cases. With 3D printed models, participants can gain hands-on experience with these variations, ensuring they are better prepared for complex procedures.
In addition to surgical training, having accurate models is also vitally important in the development and testing of novel medical devices and surgical techniques required for the new procedures. Large animal models often don't replicate human anatomy, and cadavers have their own limitations as the preservation process alters tissue properties.
“With cadavers you have to take what you get, however, with 3D printing you can either systematically manipulate the model to understand how these variables affect your outcome, or replicate numerous different real surgical cases if you have access to the scans and the relevant features can be reconstructed. This is similar to the approach of digital twin models that are increasingly being adopted for derisking and accelerating the development pipelines for new healthcare interventions.”
Dr. Iwan Vaughan Roberts, cofounder, COSA Ltd.
COSA Ltd. starts with a scan and then goes through 20-30 different iterations. Surgeons test the models along the way, and their feedback alters what anatomical features should be included, as well as the adjustments required to structural properties. The goal is to make the model feel like drilling a bone. This is achieved through internal structures in the model.
“Because it’s an enclosed structure with lots of internal structures, the only way to fabricate it is through 3D printing. A lot of our work is in the design to both make the models scalable but also repeatable when batches of models need to be made efficiently and at reasonable cost for real world use.”
Dr. Iwan Vaughan Roberts, cofounder, COSA Ltd.
Feedback serves an additional benefit, too, as validation of these models with clinical schools and academic institutions is vitally important to their usefulness and adoption.
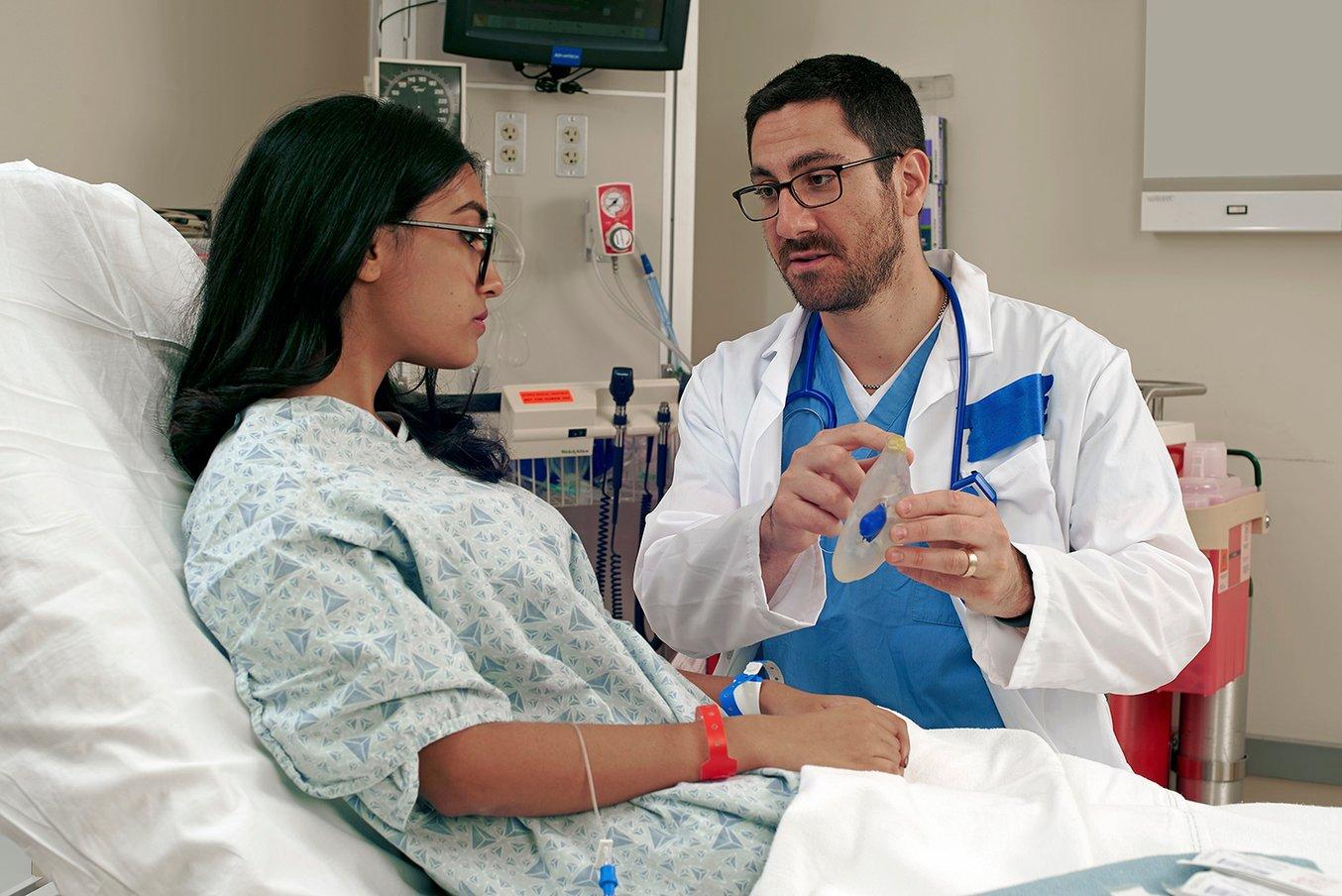
How to 3D Print Anatomical Models for Preoperative Planning and Enhanced Patient Consent
This white paper offers a practical walkthrough for physicians and technologists to get started creating 3D printed anatomical models from patient scans, reviewing best practices for setting up a CT/MRI scan, segmenting datasets, and converting files to a 3D printable format.
Formlabs SLA 3D Printers: Fine Finishes and High Resolution
Temporal bones, which house the inner ear, are very porous. Micro CT scans are used to capture the anatomy of the internal channels that is necessary to reconstruct the model with the detail and porosity required. Beyond model design, material selection is key in ensuring that the model behaves like bone when it’s being drilled.
Stereolithography (SLA) 3D printing offers the materials and precision needed to produce the fine details and precise internal channels required for a bone-like anatomical model. Fused deposition modeling (FDM) and low-cost resin 3D printers either can’t achieve the level of detail required to produce bone-like anatomical models, or can’t do so reliably.
“Formlabs is in a perfect space. FDM or the cheaper resin printers can achieve some of the resolution of these models, but not reliably, and there is some pain in optimizing the printer to work well by itself. On the other hand, the high-end multi-jet printers are hundred thousand pounds machines. The ROI on those is much longer than with Formlabs.”
Dr. Filip Hrncirik, co-founder, COSA Ltd.
“FDM printing just doesn’t come close to the amount of fidelity you need in terms of the material properties and the resolution. On the other side of the spectrum, material jetting printers make it difficult to capture the pores needed, and are very expensive — especially for something that’s drillable. To work with the NHS, we need something that makes sense in terms of cost efficiency.”
Dr. Iwan Vaughan Roberts, co-founder, COSA Ltd.
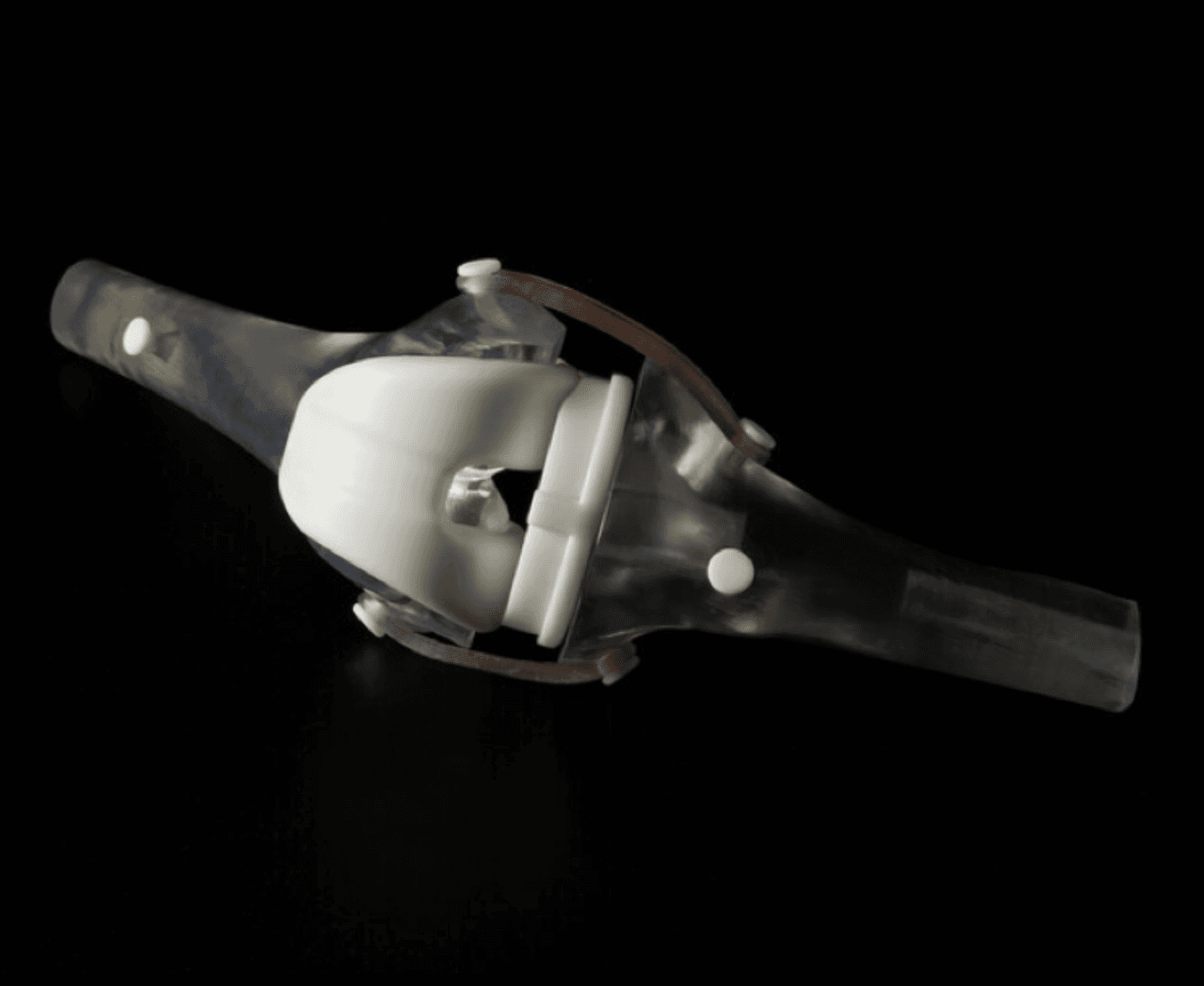
Creating Bone Simulation Models for Cutting and Drilling
3D printed bone-simulation models are revolutionizing medical training, surgical planning, research, and medical device development. This application guide walks through the bone-simulation material options for stereolithography (SLA) 3D printing and the entire in-house manufacturing process for bone-like anatomical models intended for cutting and drilling.
High-Accuracy Models Empower Communication and Medical Device Development and Testing
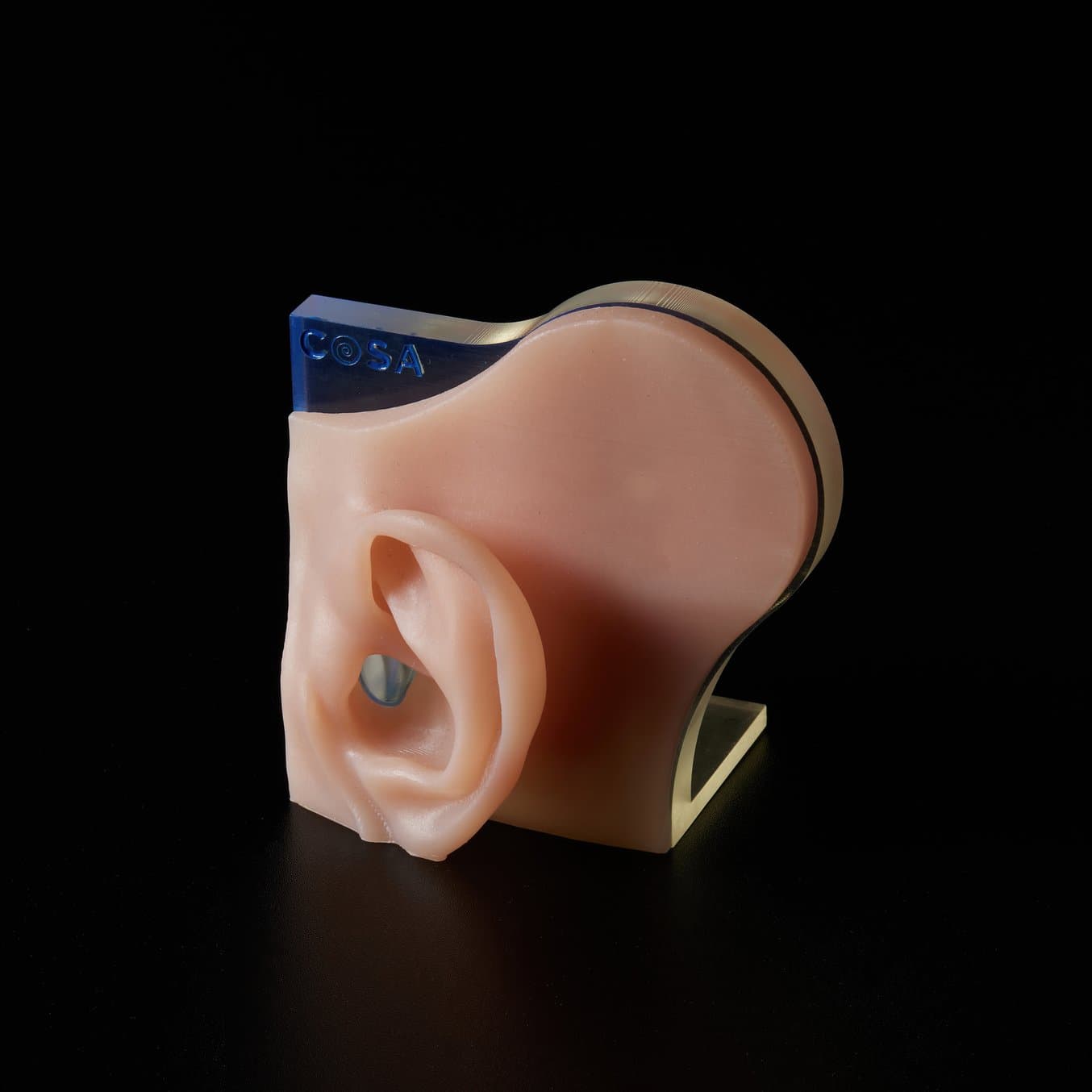
Printed in Clear Resin and Flexible 80A Resin, clinicians can insert a real cochlear implant into this model.
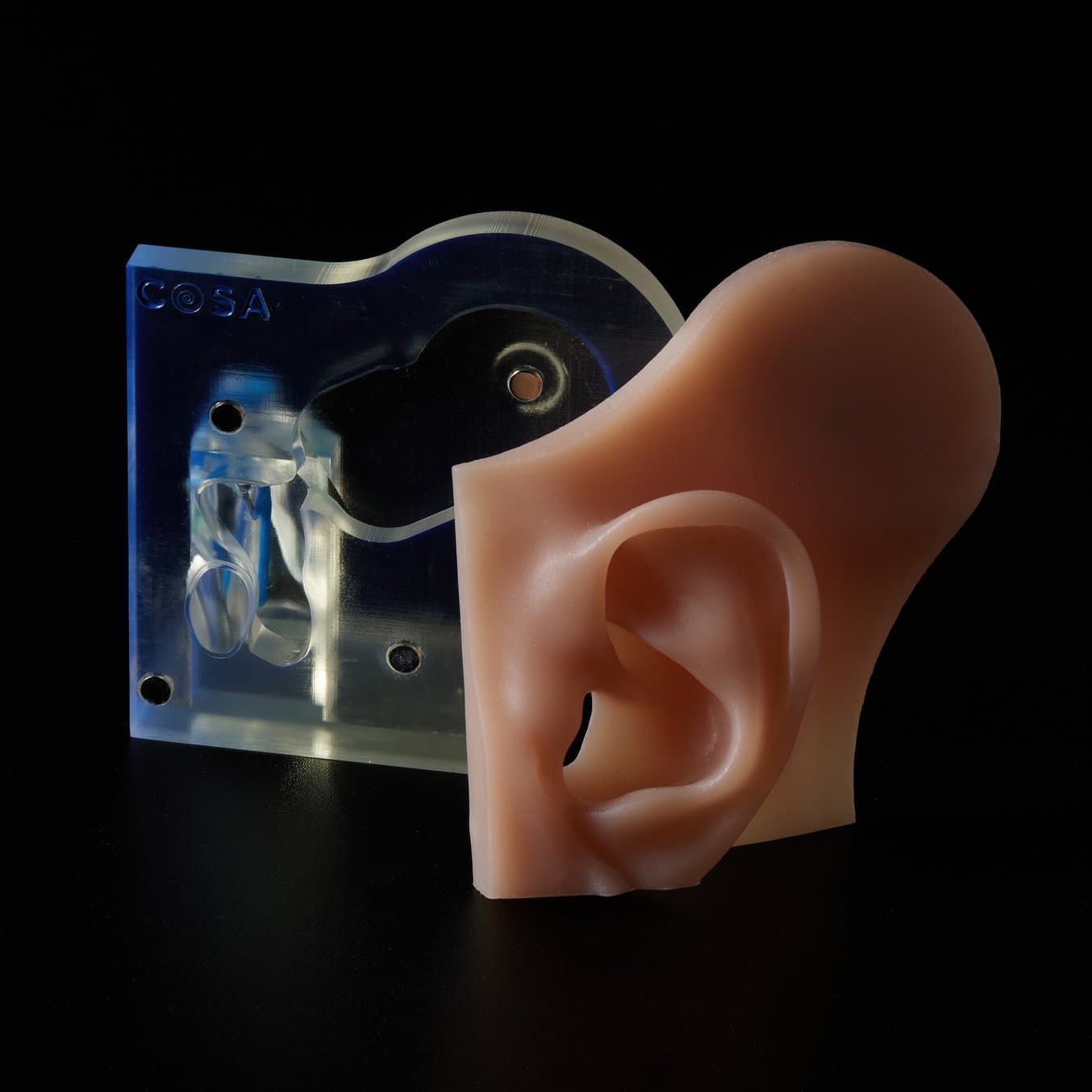
After printing, the small bones in this model are painted, and magnets are added to attach the skin to the clear model.
The Visual Ear Model above was developed with accurate but simplified anatomy highlighting key considerations for cochlear implant surgery. The goal was that it be visually appealing while enabling a clinician to put a real cochlear implant inside and demonstrate how the medical device works.
This model has several requirements. The small bone and eardrum must be printed separately and then slotted in after being colored, and both rigid, clear materials and flexible colored materials are required.
“We could go with a multi-jet system, but it’s way more expensive, and we actually got better results on the Formlabs with post-processing in terms of the surface finish and final details. We never thought we’d be able to print something so fine as those small bones. But with different orientations, it prints really well.”
Dr. Iwan Vaughan Roberts, co-founder, COSA, Ltd.
Clear Resin is used for the bony anatomy, while the skin is Flexible 80A Resin dyed with Color Kit — all printed on Form 3B+ and then assembled with magnets. COSA Ltd. originally sent a cochlea model (spiral object in the inner ear) to five printer manufacturers to validate their technology, but Roberts found that “The Formlabs is just so much more versatile, able to print so many different materials, plus the usability updates and improved support.”
Other models were developed to replicate both the mechanical and electrical properties of the cochlea. Small channels were required for these models and Roberts says that “We managed to add different pores within the structure and conductive saline within the structure. The amount of pores you have determines the conductivity.”
These tailored models enable the testing of implantable devices; in addition to conductivity, COSA Ltd. has developed models for insertion forces testing and integrated sensors into 3D printed setups to measure pressure. These models can also be used for training and development of the device. Hrncirik says, “We are taking from the clinical perspective — we talk directly to the surgeons who are doing the surgery, we directly talk to the end user — we are getting constant feedback on our products.“ This enables COSA Ltd. to provide medical device companies with valuable information that can be used for development, including tailored training.
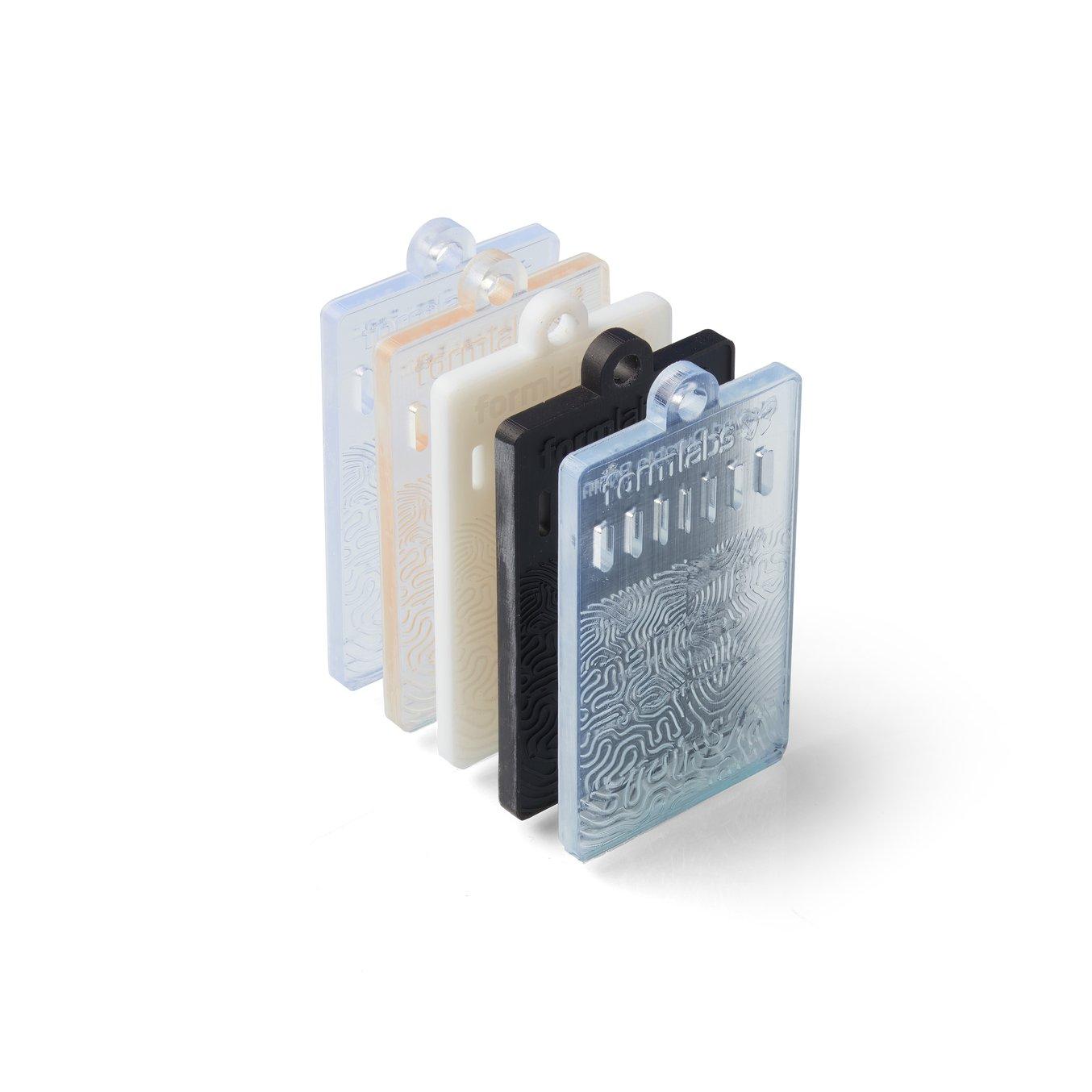
BioMed Resin Swatches
Each BioMed Resin swatch features embossed and debossed designs, 0.5-2.0 mm cutout thicknesses, as well as regulatory information unique to that resin.
Production Reliability
“What we really appreciate with Formlabs is the success rate of printing. We have enough problems with the design itself — micro CT, design segmentation, meshes — so I really appreciate that you put something into the machine and there’s a 90-95% success rate it will come out as it should. Which is great. Even though we have a DLP 3D printer for microchannels, it’s such a pain to work with, that we’d prefer to use Formlabs. Because with Formlabs, if we want something 20 times, it’s super easy, and the deviation is minimal.”
Dr. Filip Hrncirik, co-founder, COSA Ltd.
One project manufactured in-house, referred to as the extendable ear, is a 3D printed part that houses a microphone. Worn by classroom teachers, the extendable ear transmits to bone-conducting headphones worn by students with persistent ear infections. For projects such as this, with production runs under 500, the part is manufactured in-house via 3D printing as the cost of a mold would be prohibitive.
“Our projects are quite bespoke. We’re not printing huge numbers, but having the reliability of Formlabs so we can do runs of 10s is quite good. There are also lots of small usability things like being able to print remotely.”
Dr. Iwan Vaughan Roberts, co-founder, COSA Ltd.
The 98.7% third-party validated reliability of Form 3 and Form 4 ensures consistent production while Dashboard print management software enables remote print management and notifications, giving the small company flexibility.
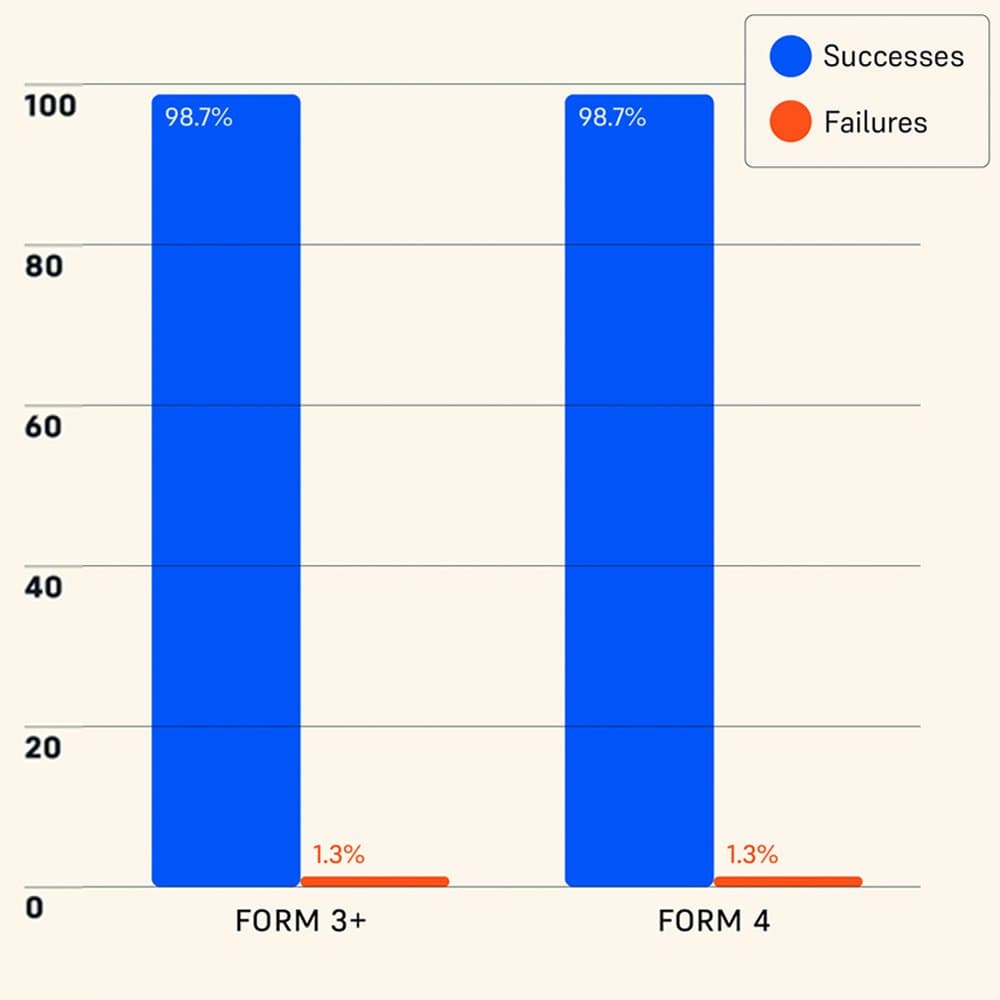
Independently Tested Reliability of Form 4 and Other Resin 3D Printers
Formlabs Form 4 was measured to have a 98.7% print success rate by an independent global leader in product testing. Read a complete description of the test methodology and see the results in our white paper.
Improving Accessibility, Training, and Development With Formlabs 3D Printing
“We are keen to make models that are really functional and replicate real anatomy, showing variation in different people and even going more patient-specific with individual surgical guides and complex procedures. There’s still a gap with specific procedures and cases and we want to open up access to really high-quality simulators.”
Dr. Iwan Vaughan Roberts, co-founder, COSA Ltd.
With Formlabs 3D printers, COSA Ltd. can develop and produce a variety of bespoke products for specific procedures and clinically informed visual models flexibly and at low costs. Hrncirik says, “Most anatomic models nowadays are injection molded and then hand painted, which is really time-consuming. So I would expect in the next few years that most of these manufacturers would transition to 3D printing. Including creating bigger, better, and faster models.”
Explore Formlabs resin 3D printers to start printing or contact sales to discuss the optimal solution for your business.