At Formlabs Audio, we believe that the future of the consumer audio experience is custom fit earphones. Due to the rapid adoption of smartphones and 3D printing, it is possible, for the first time, to combine phone scanning, manufacturing automation, and affordable 3D printing to enable mass customization, bringing custom fit as an accessible earphone category to the mass market.
In this post, we will discuss how easy it is to create a custom-fit earpiece for a Bose in-ear headphone. Watch the video to learn more.
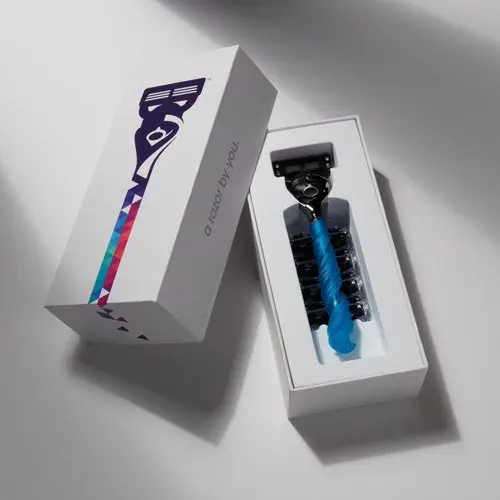
Guide to Mass Customization
This guide will provide manufacturers with insights into the different approaches to customization, how to choose the most applicable approach, and more.
Obtaining and Preparing a File
Custom fit earphones offer a unique individual listening experience, keeping out unwanted noise while feeling comfortable enough for all day use.
This gives a secure fit that removes any possibility of earphones falling out of the ear, in addition to improved comfort and noise isolation.
Customers are now able to use their own smartphone to scan their ear, replacing the more traditional ear impression process. In this case, the Hearables3D smartphone app can be used to deliver a scan in less than a minute by using artificial intelligence to improve scan quality and reconstructing parts of the ear not captured from the phone.
The scan is then sent directly into a cloud-based machine learning system that uses statistical modelling to convert the scanned ear shape within seconds into a specific earphone design, ready for 3D printing on a Formlabs 3D printer.
From CAD to 3D Printer
Files can be imported from your smartphone directly into your favorite CAD software. Here, you’re going to want to make sure the base of the eartip matches the form and shape of the earphone you wish to attach it to.
Historically, hearing aid manufacturers would employ a skilled modeller to help complete this step. But rapid advancements in ear scanning and CAD software have lowered the skill-barrier needed, allowing a wider range of users and small businesses to create eartips. Many CAD programs even offer fully automated steps to complete the process.
From CAD, the eartip is sent directly into Formlabs’ PreForm software which prepares the 3D print file for a Form 3B printer.
The Form 3B is an advanced desktop 3D printer developed for healthcare. Our precise, reliable ecosystem takes the guesswork out of audio fabrication so faster workflows are easily achievable. Leveraging the benefits of the Form 3B Low-Force Stereolithography Technology, the low peel forces produce increased accuracy and amazing smooth surface finish right off the build platform and into the patient's ear. With a build platform more than three times the size of some competing 3D printers (14.5 × 14.5 × 18.5 cm) and less than half the price, Formlabs delivers a truly unique triple value proposition: quality, throughput, and price.
With affordable in-house printing from Formlabs, bringing a custom fit audio experience to your patients and customers has never been more achievable. From clinics looking to offer one hour same day in-clinic services, or labs looking to scale their business to allow production of up to 100 prints on a single machine per day, Formlabs evolves the digital audio workflow to the next generation.
Apply Lacquer To Custom Fit Earpiece
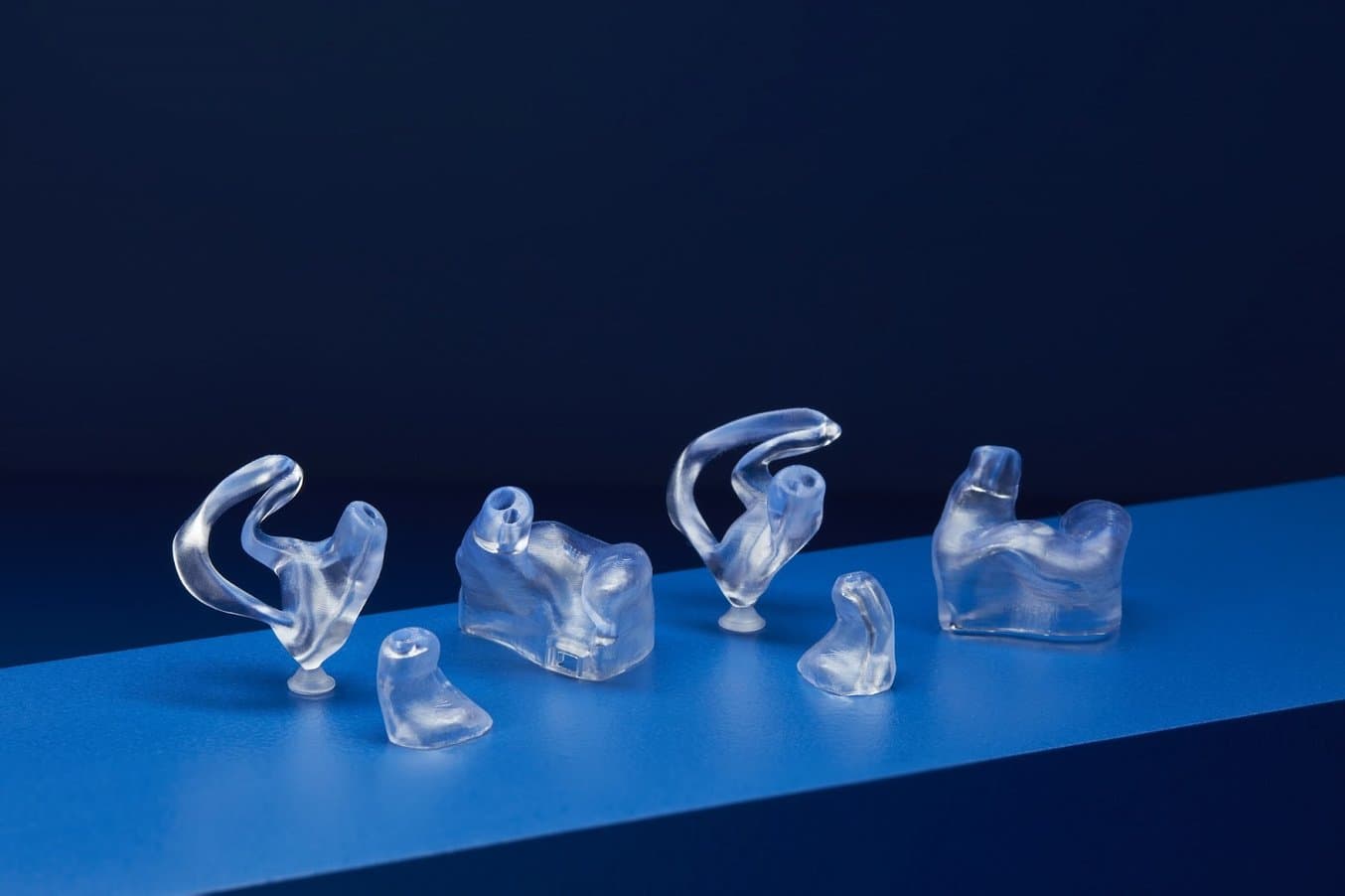
After removing the parts from the build platform, they need to be put through the Form Wash and Form Cure, removing excess resin and bringing the material to it’s full properties. Finally, the parts are lacquered so that the Flexible 80A Resin is safe to be inserted into the customer's ear.
The final step of post-processing is to apply a lacquer. In the video above, we show the use of a LP/W lacquer from Egger, while other common lacquer options are available from Dreve and Detax. For safety and biocompatible, check with the lacquer manufacturer to make sure the material meets your requirements.
At this point, the earpiece is ready to be sent to the customer. A formally long, complex process is finished in just a few hours.
Formlabs 3D Printing Family
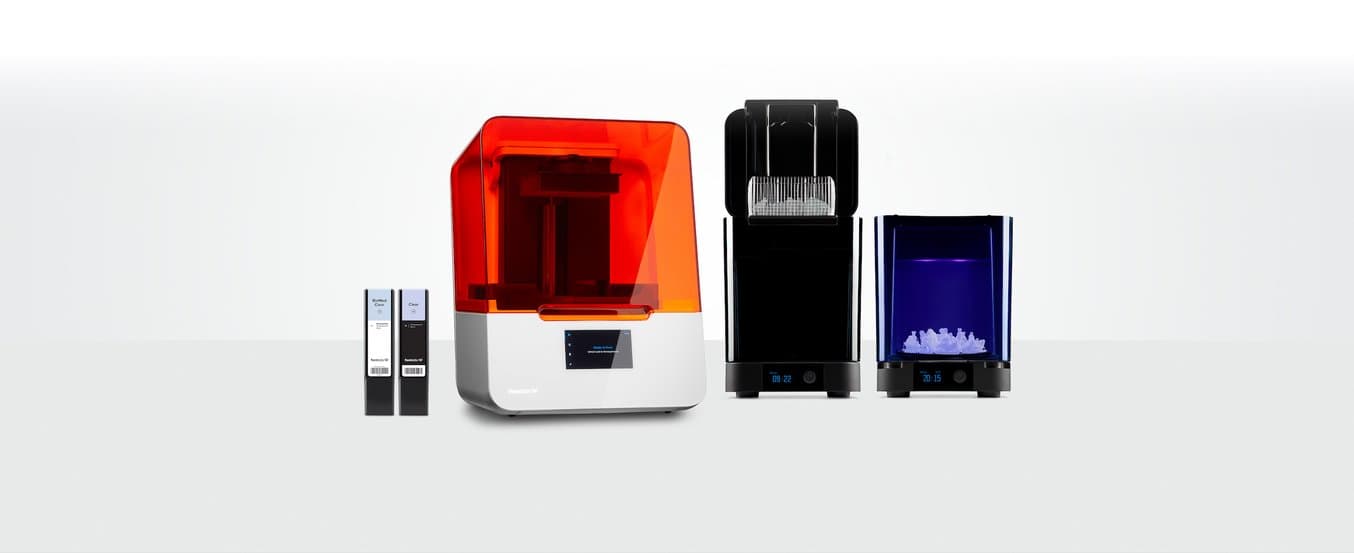
This workflow is enabled by the Formlabs Audio family.
In this workflow video, we use Flex 80A Resin. Flex 80A Resin can withstand bending, flexing, and compression, even through repeated cycles. Flexible 80A Resin is the most stiff soft-touch material in our library of Flexible and Elastic Resins, with an 80A Shore durometer to simulate the flexibility of rubber or TPU.
Formlabs has also created a material specifically for the Audio industry by offering BioMed Clear Resin, a clear high-impact resistant biocompatible resin for hard earmolds, shells, and in-ear monitors.
This important investment is part of Formlabs’ commitment to bring affordability to the digital production of hearing aids, ear protection, and consumer audio.
“Using Formlabs BioMed Clear Resin on our Form 3B printers allows us to produce biocompatible hard acrylic hearing aids that have a high detailed finish directly from the build platform. We have been able to quickly scale our digital production, benefiting from the affordability and performance of the Form 3B and BioMed Clear.”
-Paul Thorpe, Lab Manager, Universal dB
Want to experience BioMed Clear Resin for yourself? Order a free sample part below.