How SLS 3D Printing Enabled the Mass Production of a Food Delivery Robot in Six Months
Savewo, a Hong Kong-based product design, development, and manufacturing company, was established in 2020 to produce medical equipment for COVID-19 relief efforts in the island city. In the three years since its inception, Savewo has become one of the most sought-after and reliable manufacturing and development partners for Hong Kong-based companies in the fields of robotics, medical devices, and more.
Savewo relies on a combination of traditional and modern manufacturing techniques to help their partners move from design to mass production. Recently, Savewo accomplished an extraordinary feat, working with Rice Robotics to ramp up their production from a single prototype to hundreds of robots that include thousands of end use 3D printed components in only six months.
To accomplish this, Savewo relies on a fleet of Fuse 1+ 30W selective laser sintering (SLS) printers and the Fuse Sift post-processing system. SLS 3D printing enables a more efficient design cycle, greater design freedom, superior quality tolerance and precision, and optimal mechanical properties with Nylon 12 Powder. By proving their ability to ramp up mass production for such a technologically advanced product, Savewo has leapt ahead of their competition and are looking to expand their capabilities.
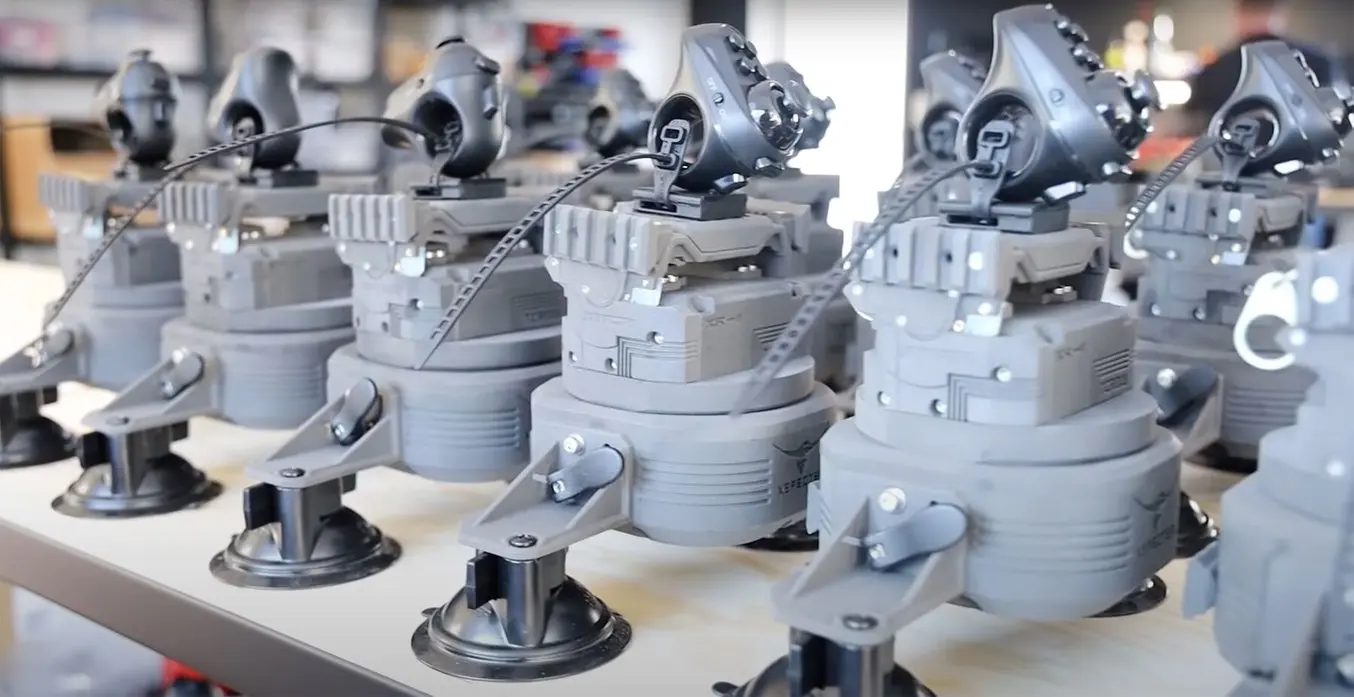
SLS for End-Use Production
3D printing for end-use production is not only possible, it's more affordable, agile, and scalable than ever with the Fuse SLS Ecosystem. Visit our SLS for Production page to compare production methods, learn about bulk powder pricing, and see production in action for 15 different manufacturers currently using the Fuse Series.
Turning Production Issues Into Opportunities
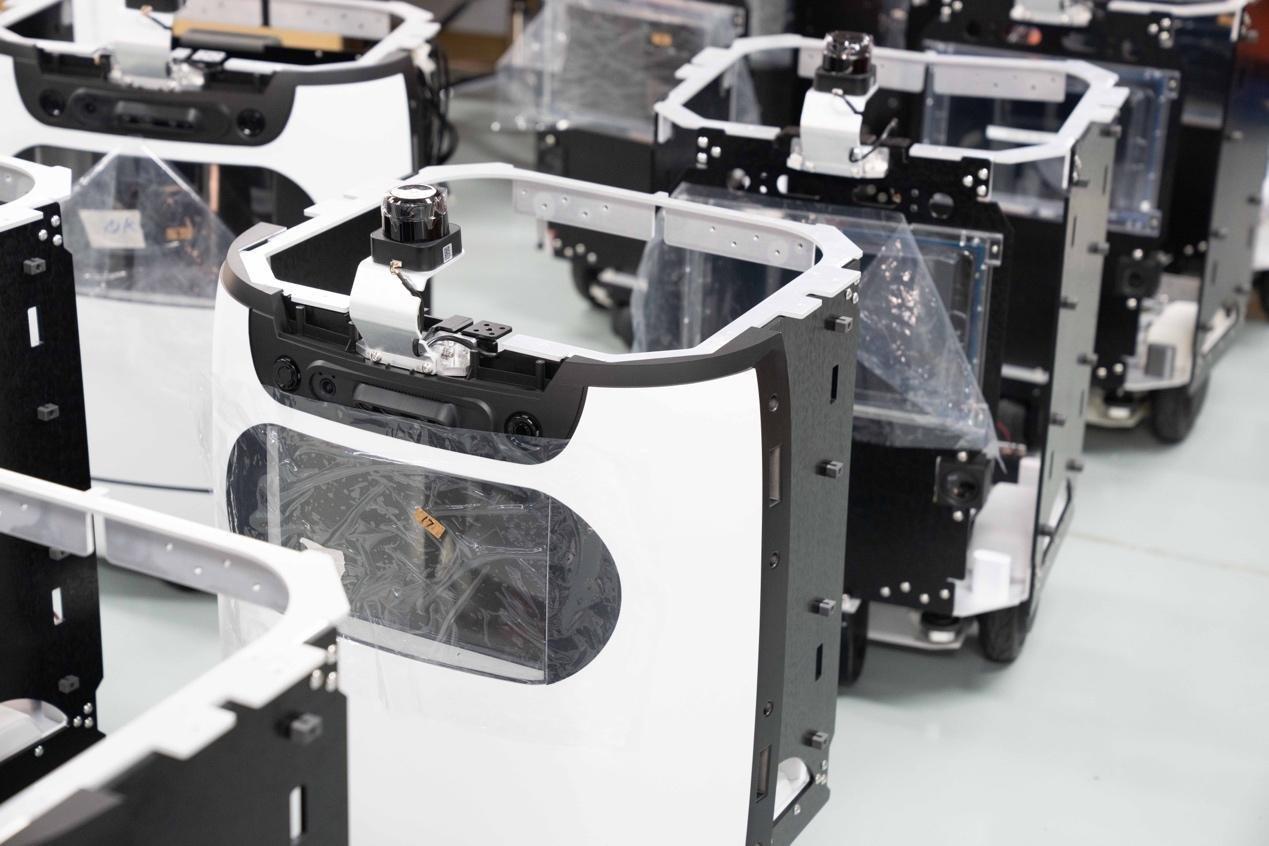
The Rice Robotics team was looking for a collaborative partner that could accomplish the impossible in just six months.
Rice Robotics, also a Hong Kong-based company, designs and manufactures robotic systems for use in food delivery, disinfection, and inspection sectors. Though their innovative designs have been deployed in small volumes, when Rice began to look for mass-production solutions, they ran into issues.
Quality control, communication breakdowns between Rice and their previous large contract manufacturer, and differences between the intended design and the final molded products all influenced Rice’s decision to look for a Hong Kong partner that could work with them. The only catch — the timeline was getting tight, and the new manufacturer would have only six months to go from first design to mass production.
SLS 3D Printing: The Six Month Saviour
With only half a year to get Rice’s product from design to production, Savewo knew that a traditional product development process wasn’t possible. They leveraged their fleet of Fuse Series SLS printers in every stage of development and production, from iterative design to functional testing, to end-use components in final-run robots.
Speed of Development
For many robotics companies, especially in Hong Kong and mainland China where mold manufacturers are in close proximity and very inexpensive, ordering tooling and injection molding for prototypes is a viable method of iterative development. For such a shortened timeline, however, Savewo knew 3D printing was the only way they’d get it all done. Their four Fuse 1+ 30W printers allowed them to print 24/7, around the clock.
“Traditional industrial manufacturing methods take a long time. With Fuse 1+ 30W, we can print directly, and when we need to make changes, we can immediately change the design and print it again. This can greatly speed up the entire development process, and the printed part can be placed on the robot for testing.”
Savewo R&D Engineer Mr. Feng
Design Freedom
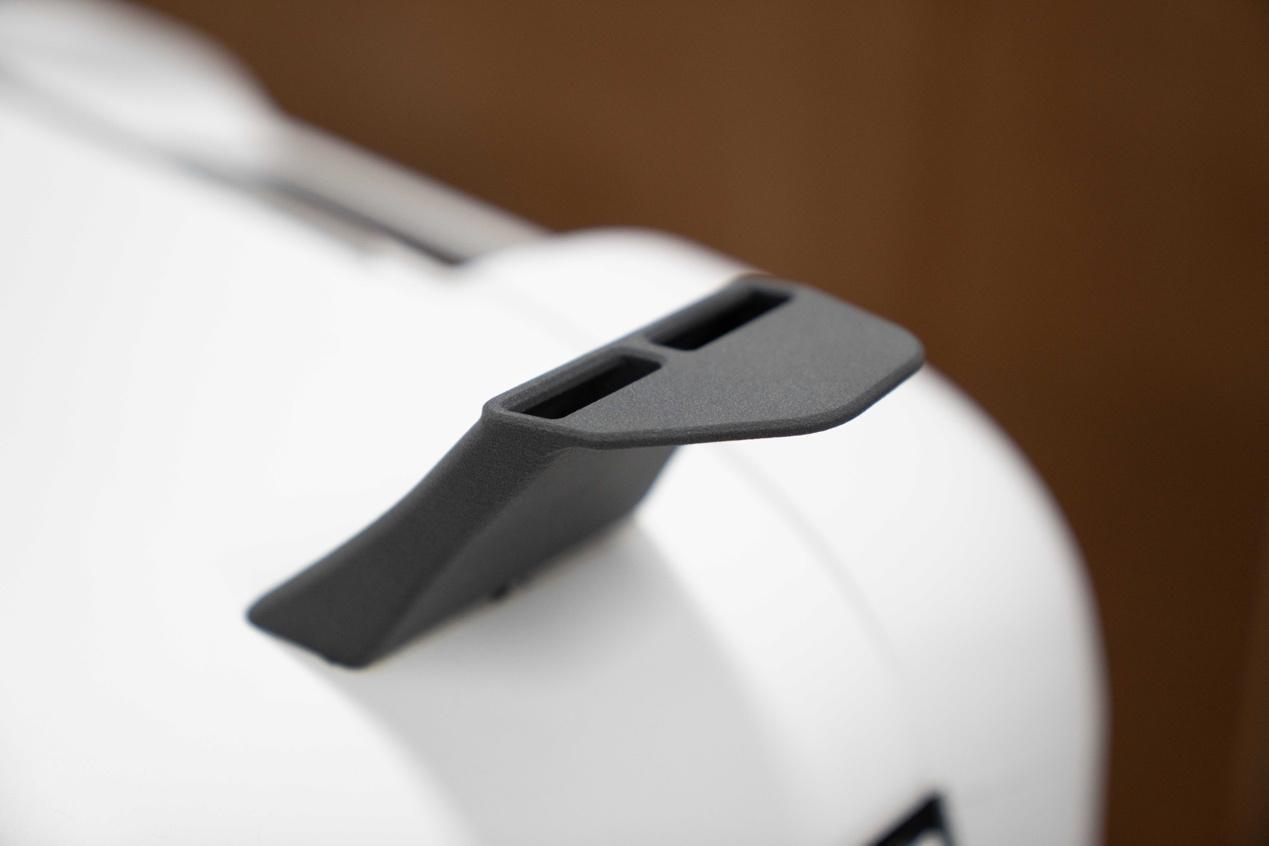
3D printing end use parts allowed the team to design complex components that would not be cost-effective to produce with traditional manufacturing methods.
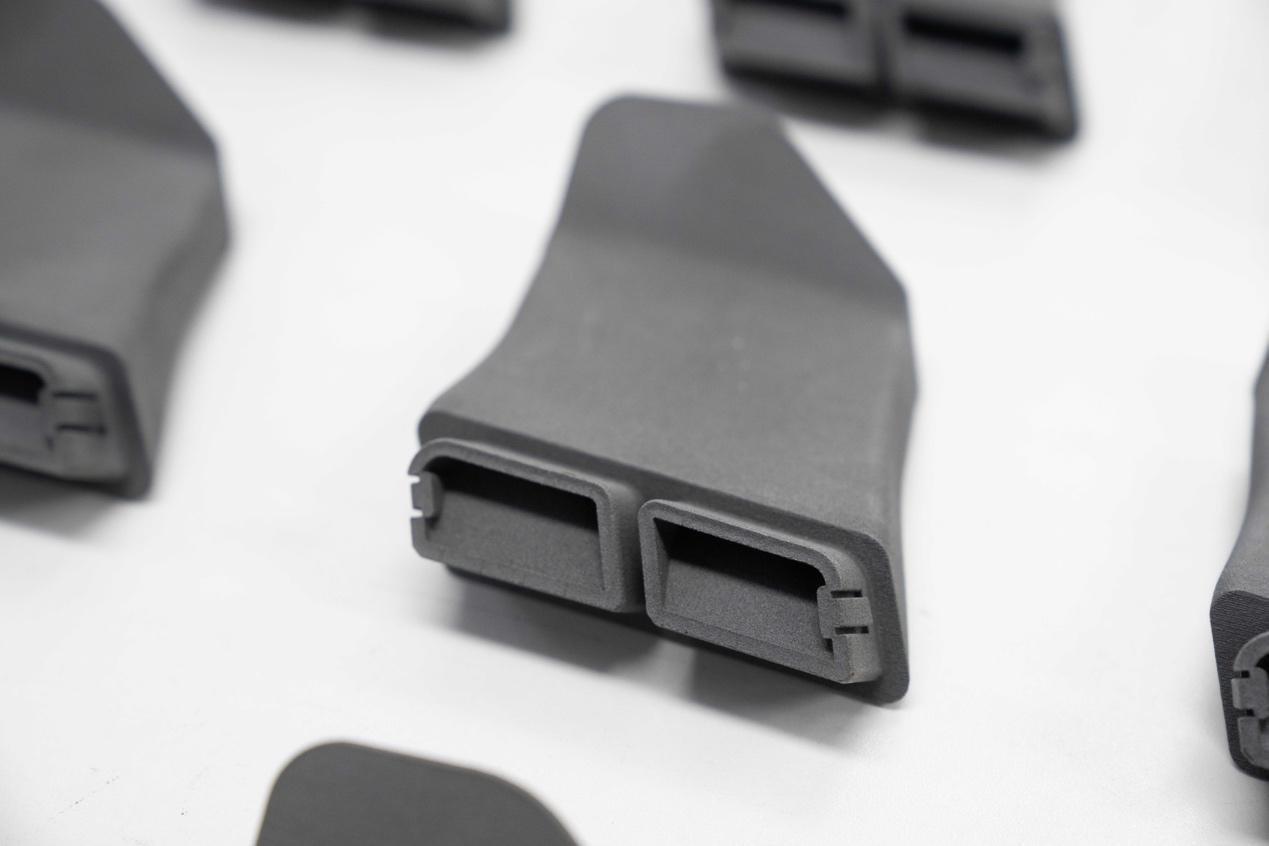
Once Savewo decided to commit to SLS 3D printing, a whole new set of possibilities opened up. The Fuse Series SLS printers have self-supporting powder beds, enabling parts that have overhangs, undercuts, internal channels, or other design features that make traditional manufacturing methods expensive and difficult.
By 3D printing these complex parts, Savewo was not only able to turn out revisions overnight, but they were able to extend the scope and functionality of the robotic components by creating innovative and organic designs. “Some part designs that cannot be produced at a low cost by traditional manufacturing methods can now be realized easily and accurately with the help of SLS 3D printing," said Mr. Zhong, Senior Mechanical Engineer of R&D at Savewo.
Tight Tolerances and Control Throughout the Process
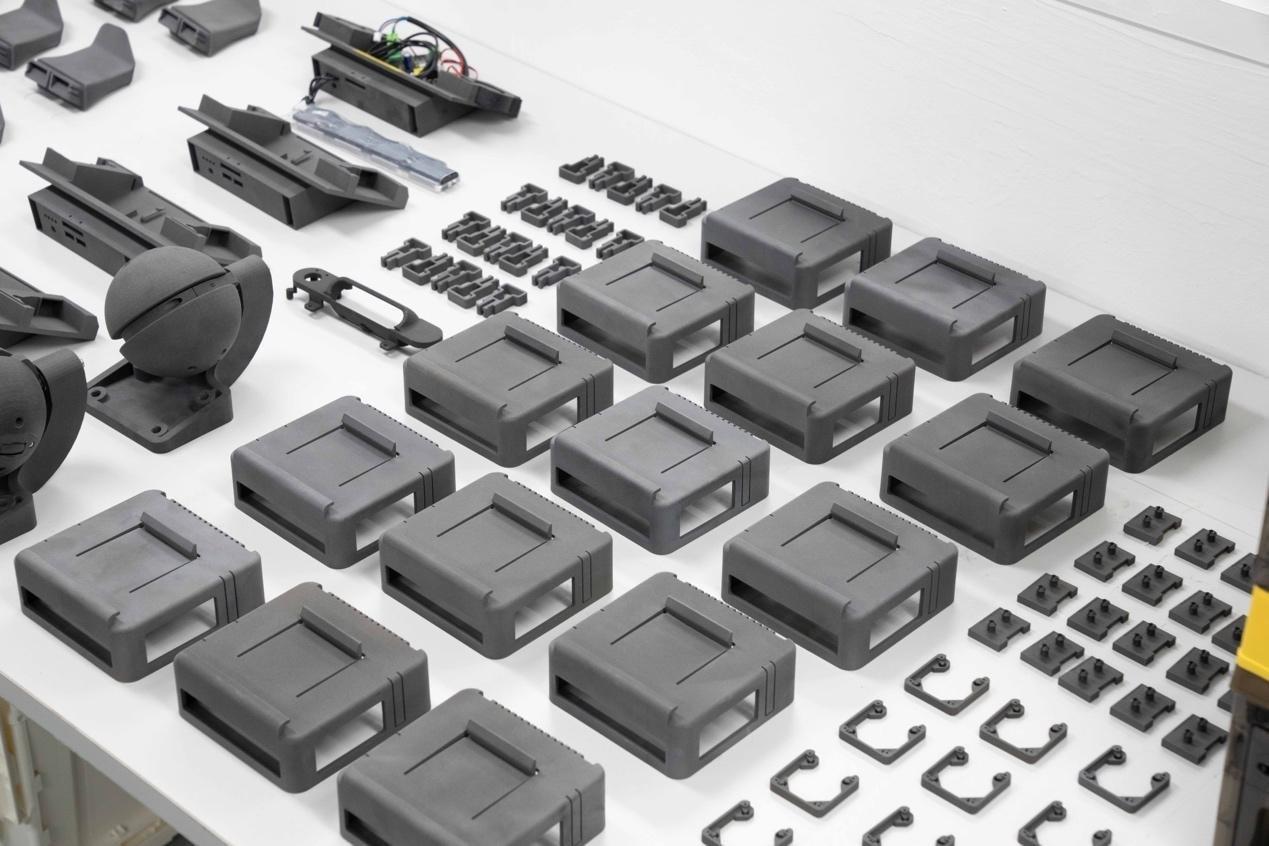
Producing parts with SLS 3D printing makes it easier to align parts and control tolerances.
One major problem Rice encountered when dealing with their previous contractor was a lack of consistency between designs, prototypes, beta tests, and end-use molded parts. There was a lack of dimensional accuracy between these stages due to the multitude of different technologies used and the lack of clear communication from the manufacturer. Additionally, throughout the design process parts had to be changed slightly to make allowances for heat, time, and expansion that occur during the industrial injection molding process, which led to differences between the intended design and final parts.
Savewo’s smaller size and clear, open lines of communication meant that engineers at Rice could communicate their needs and be involved as much as necessary with the printers themselves. Parts could be redesigned for additive manufacturing easily since Rice had such easy access to the means of production — the Fuse printers. Furthermore, Rice didn’t have to include design considerations for molding, so part designs could stay consistent through every step of the process, from 3D printed prototypes to the final parts.
Producing End-Use Parts With Nylon 12 Powder
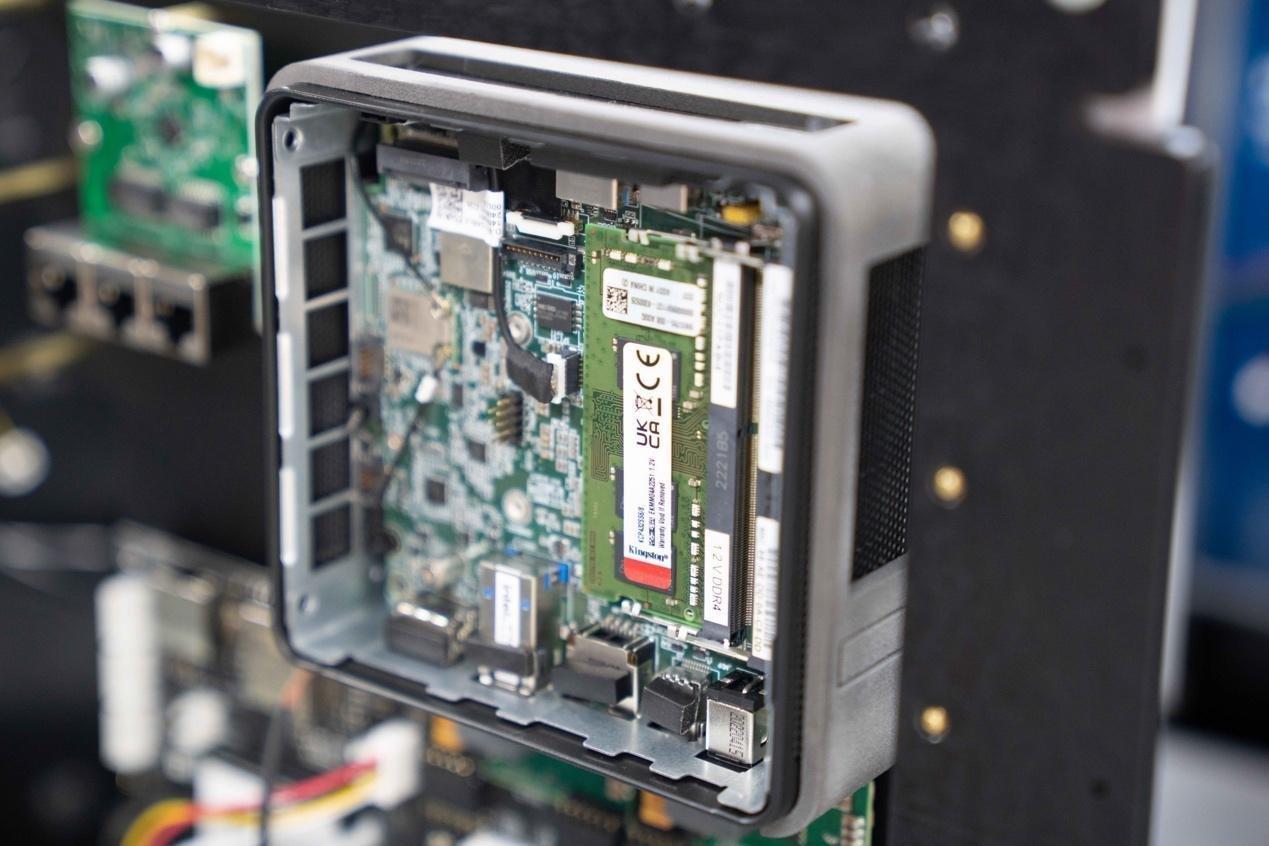
Nylon 12 Powder creates parts that are strong, durable, and slightly flexible — ideal for robotics applications where parts endure a lot of friction and bouncing.
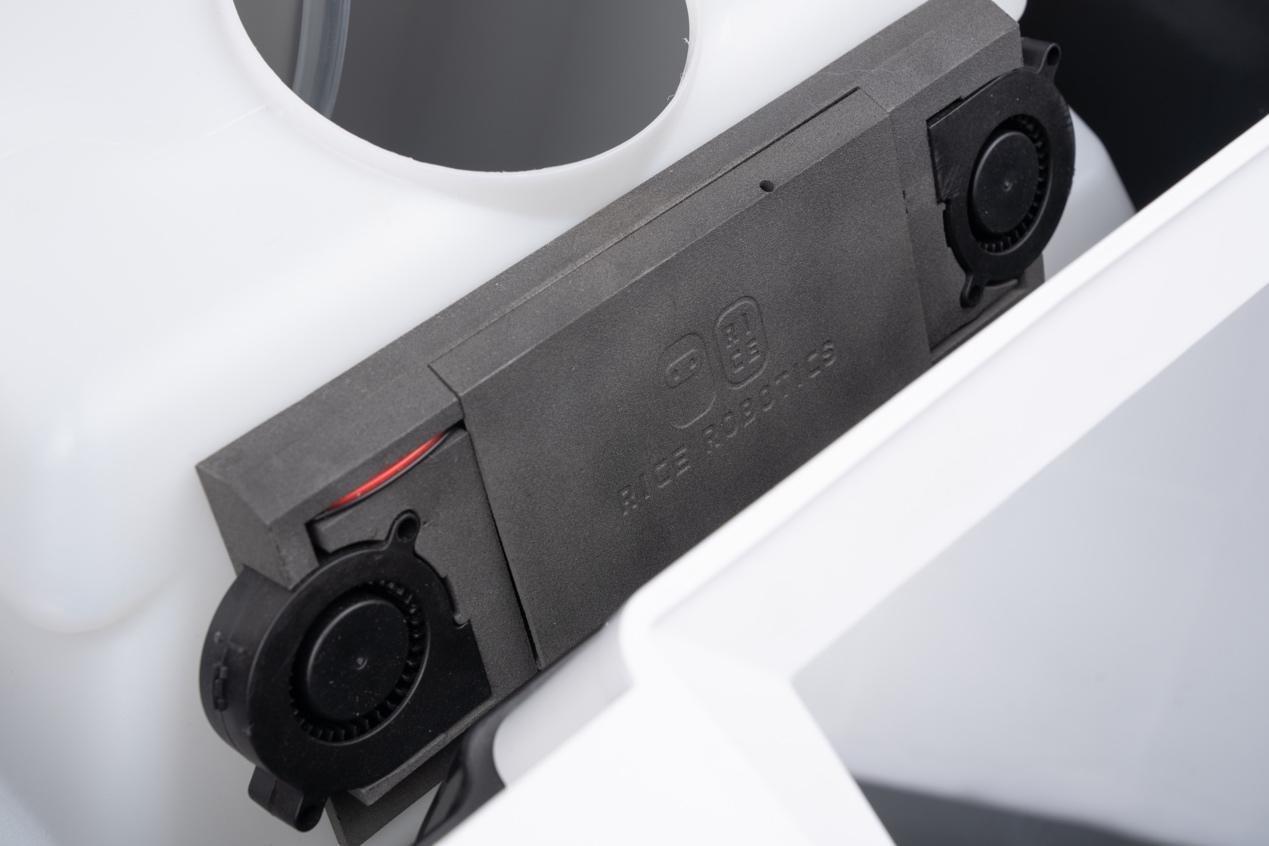
Many of those final parts are printed for end-use production on the Fuse Series printers. The strength and durability of Nylon 12 Powder parts make them ideal for rugged applications like robotics. Nylon is a familiar material for engineers and the material properties are well known. For Rice, they may have taken a leap of faith that Savewo could hit mass production volumes, but they could have confidence that the final nylon parts would behave like injection molded plastics.
Robotics calls for many functional assemblies, with multiple components fit together with working joints or fastened hinges. 3D printing hasn’t always been up to the task of creating parts strong enough to withstand the constant pulls, pressures, torque, and friction of being in an assembly, but SLS-printed parts can. Nylon 12 Powder parts printed on the Fuse 1+ 30W can be printed with threads pre-designed, or they can be tapped with heat-insert screw threads.
Savewo leveraged this ability to join together many parts, proving the versatility of the fabrication method and material. "Nylon 12 Powder has sufficient hardness, toughness, and good mechanical properties. Most of our 3D printing parts have threads. When using Nylon 12 Powder to directly print parts, there will be no need to tighten or loosen the screws many times,” said Mr. Chen, Savewo’s Director of Research and Development.
On the Rice 2 an indoor food delivery robot, connecting parts of its skeleton and shell were printed on the Fuse 1+ 30W. These connectors have to withstand the constant vibration that the robot produces while “walking” as it stabilizes the skeleton and shell. The flexibility of Nylon 12 Powder makes it ideal for this type of stabilizing components. Other SLS end-use parts on the Rice 2 are the atomizer module (the entire PCB, leaf fan, joint buckle), air outlet, and the fixing of the central processing unit system and shock absorber system.
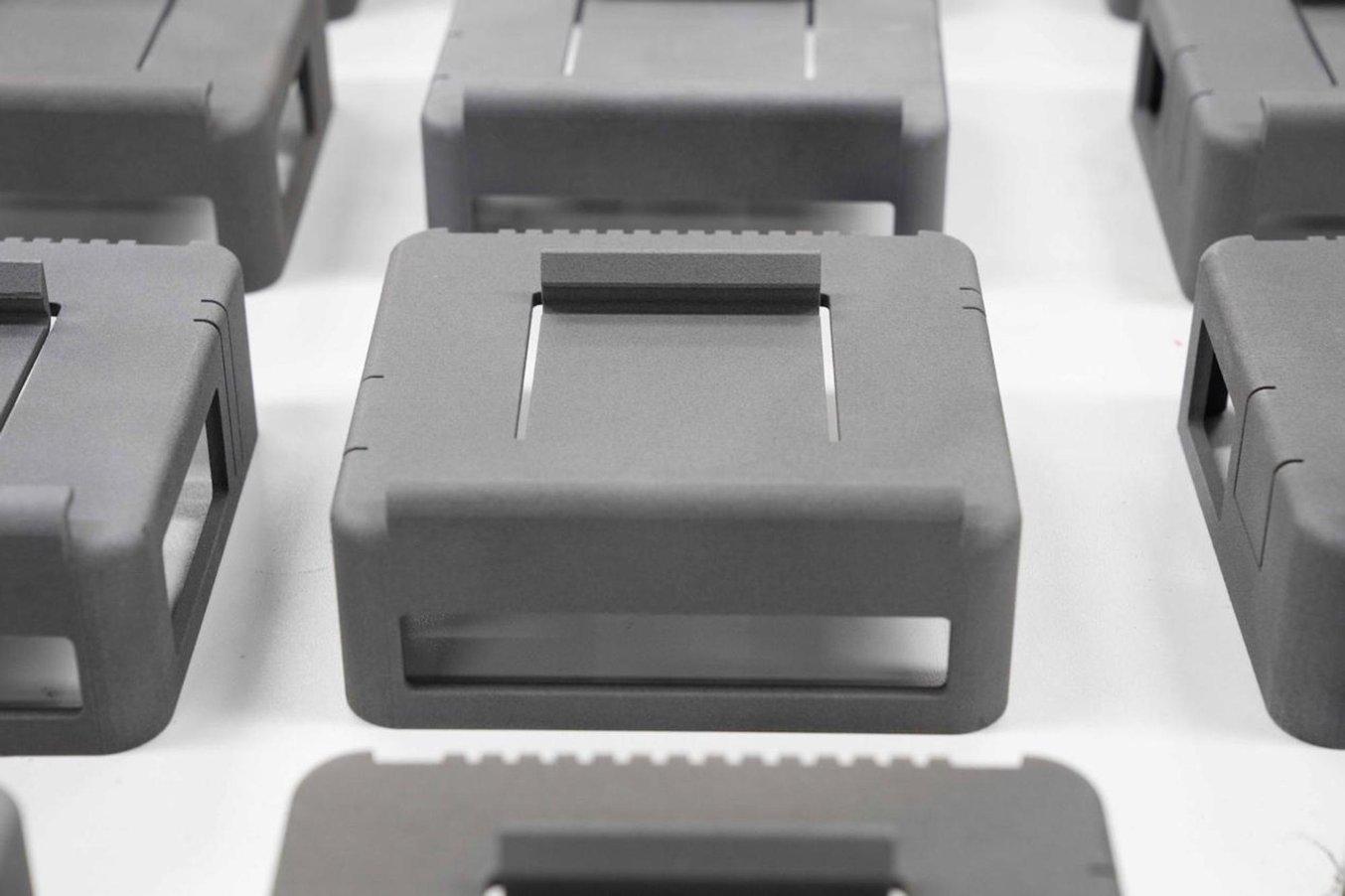
Even large outer-shell components on the robots are printed on the Fuse Series in Nylon 12 Powder and testing has proved that they can withstand pressure, impact, and general wear and tear.
Producing 50 Robots Per Week Amid Continuous Development
Savewo’s in house factory with four Fuse 1+ 30W SLS printers and a Fuse Sift post-processing station is capable of producing enough end us parts to produce 50 Rice 2 robots each week. More importantly, 3D printing parts on the Fuse 1+ 30W provides continuous optimization opportunities, without having to rework the expensive tooling for molding.
If they had to work with the traditional factory model and use injection molds for production, which involves scheduling, proofing, modification, and other steps, the lead times would have been between 45-60 days for each part and each modification. For this project, these long lead times and the high costs meant an unacceptable risk.
Savewo's engineers classified certain and uncertain factors in the product. For the large parts with high certainty in the Rice 2, they designed molds and used traditional manufacturing with injection molding, while 3D printing was used for uncertain parts that would likely require multiple changes throughout the development.
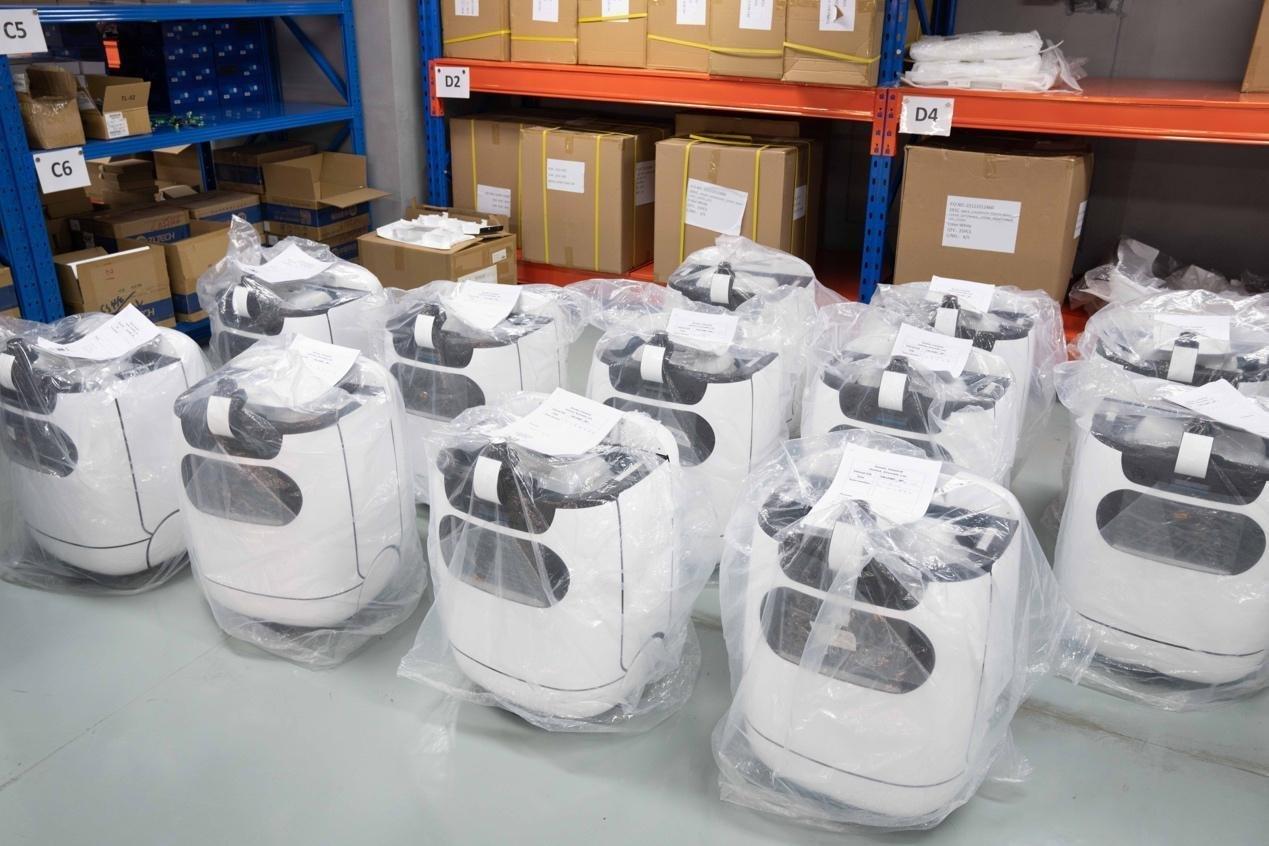
Producing on four Fuse Series SLS printers nonstop empowers Savewo to deliver 50 robots per week, even amid redesigns of some parts.
Small Island, Big Difference
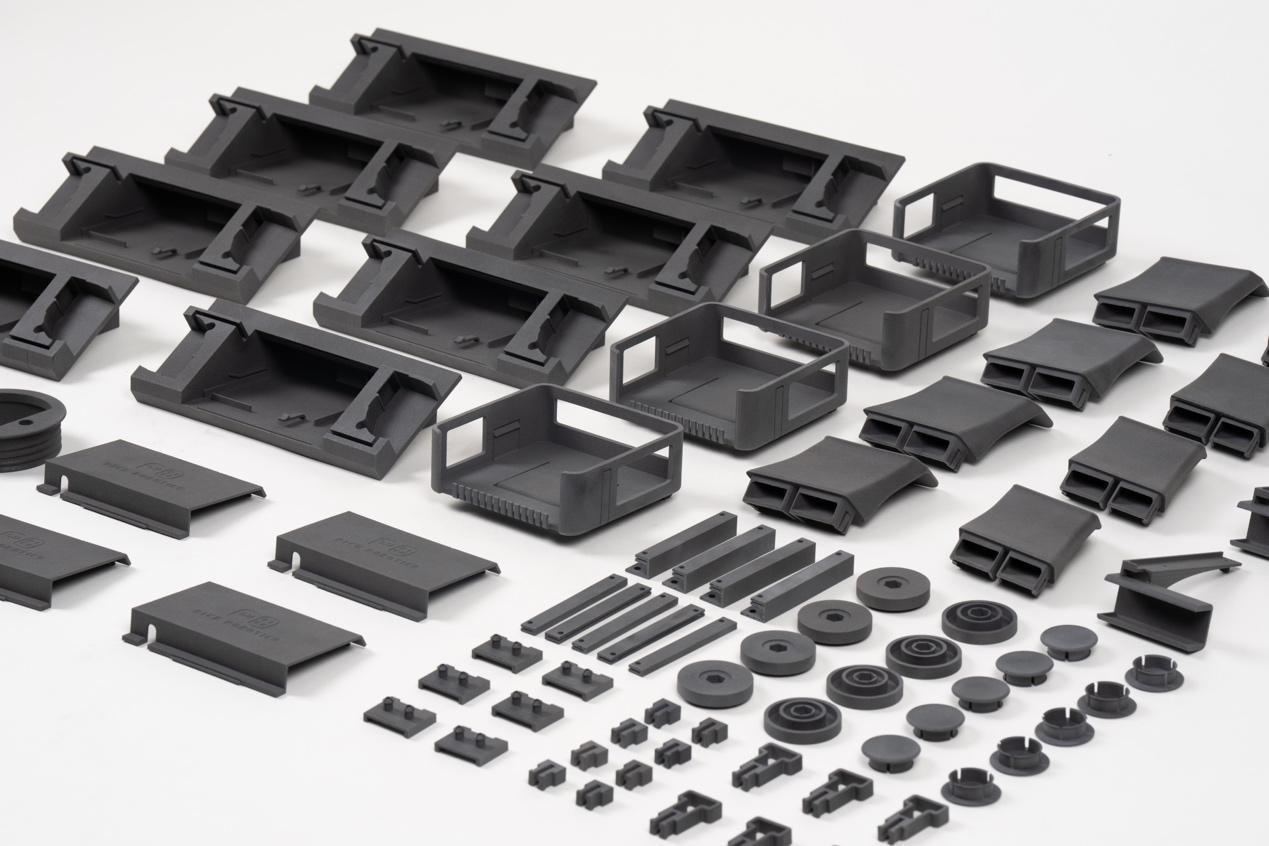
Manufacturing hundreds of small components means that the Fuse Series printers are running nonstop.
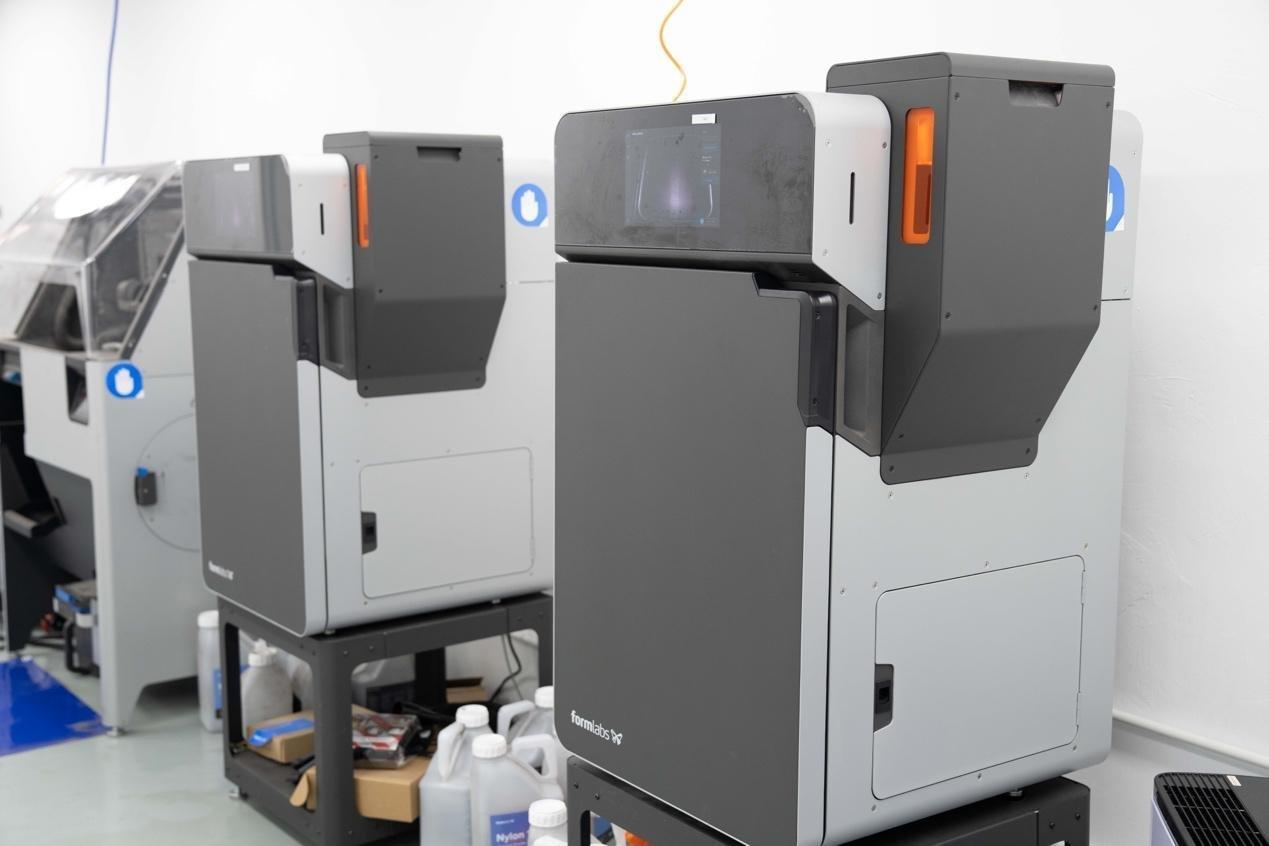
In Hong Kong, real estate isn’t cheap, and buildings and businesses go up, not out. The size and scale of the Fuse Series printers mean that Savewo could scale up production, without having to change facilities or invest heavily in more square footage. After buying their first machine, they quickly added three more to ramp up production. Now operating four Fuse 1+ 30W printers and one Fuse Sift, their R&D and manufacturing teams can quickly and efficiently move through each stage of the design process.
The entire process of taking the Rice 2 robot from reworked design to end-use mass production within such a short time frame helped Savewo not only gain internal confidence their hybrid manufacturing process would work, but also establish themselves as the leading option for Hong Kong’s innovative companies. “We hope that Savewo can become the cradle of innovation and technology in Hong Kong and promote the development of Hong Kong industry 4.0. Ultimately, we hope that SAVEWO can make Hong Kong-made business cards famous overseas again,” says Mr. Ding, CEO of Savewo.
The Fuse 1+ 30W printers can help small companies accomplish big things. The affordable SLS system provides an accessible, easy-to-use workflow, a reliable and familiar materials library, and the tolerances and accuracy of injection molded parts. Savewo has leveraged the scalability of these machines to succeed in a highly competitive and crowded market.
Learn more about the Fuse Series or contact our team to discuss how you can leverage SLS 3D printing in product development and production at your own business.