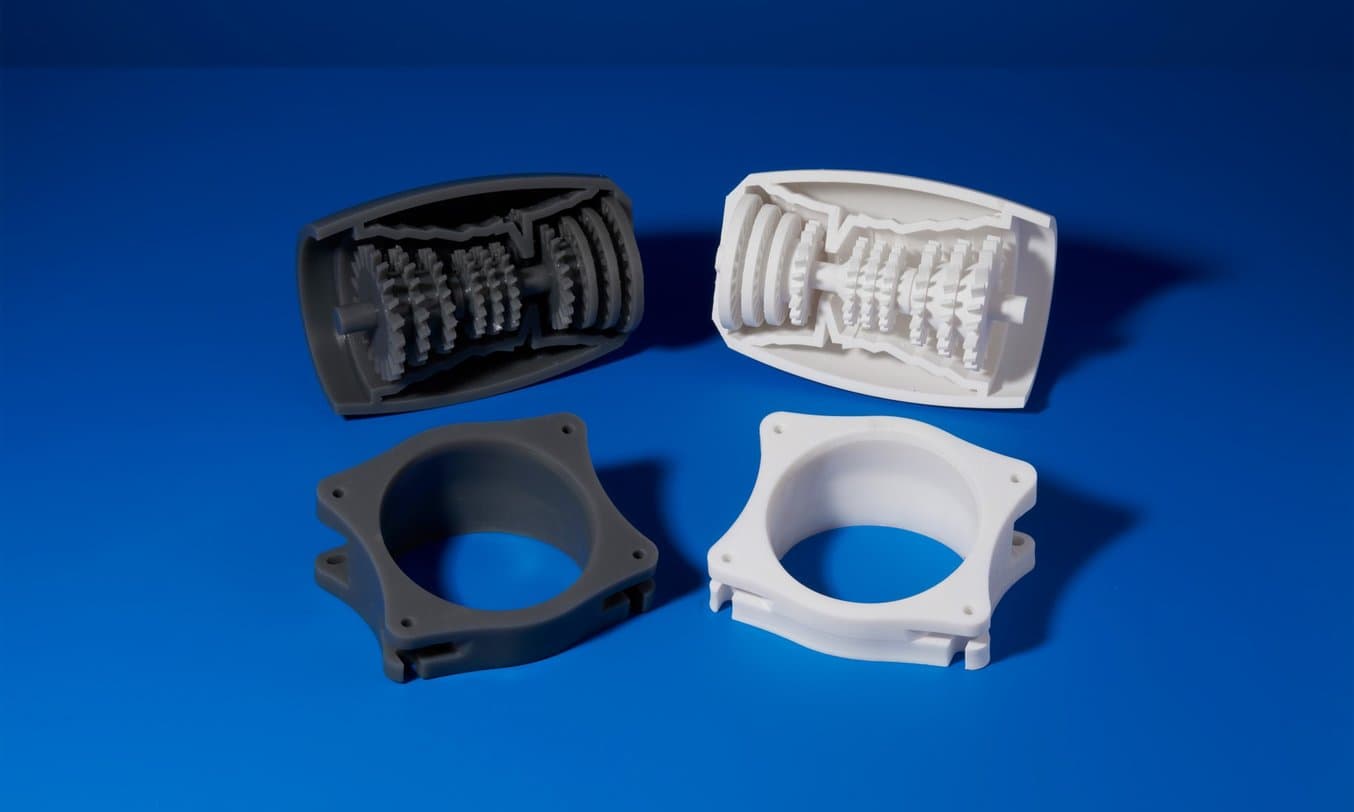
Stereolithography (SLA) 3D printing’s ability to support a wide range of materials is one of its greatest strengths. As Formlabs adds more resins to our library, the number of applications and use cases expands. Our newest resins, Rigid 10K Resin and a reformulated Draft Resin, push the boundaries of what SLA materials can achieve. Together, Draft Resin and Rigid 10K Resin complement the natural progression of product development, supporting customers from quick initial designs through high performance parts. Learn more about:
-
What makes Rigid 10K Resin our stiffest material, perfect for strong, industrial-grade prototypes
-
How its strong, stiff, and thermally stable properties allowed Rigid 10K Resin to be used for wind tunnel testing at Texas A&M University
-
Why Draft Resin prints 4X faster than Formlabs standard resins
Our New Family of Rigid Resins
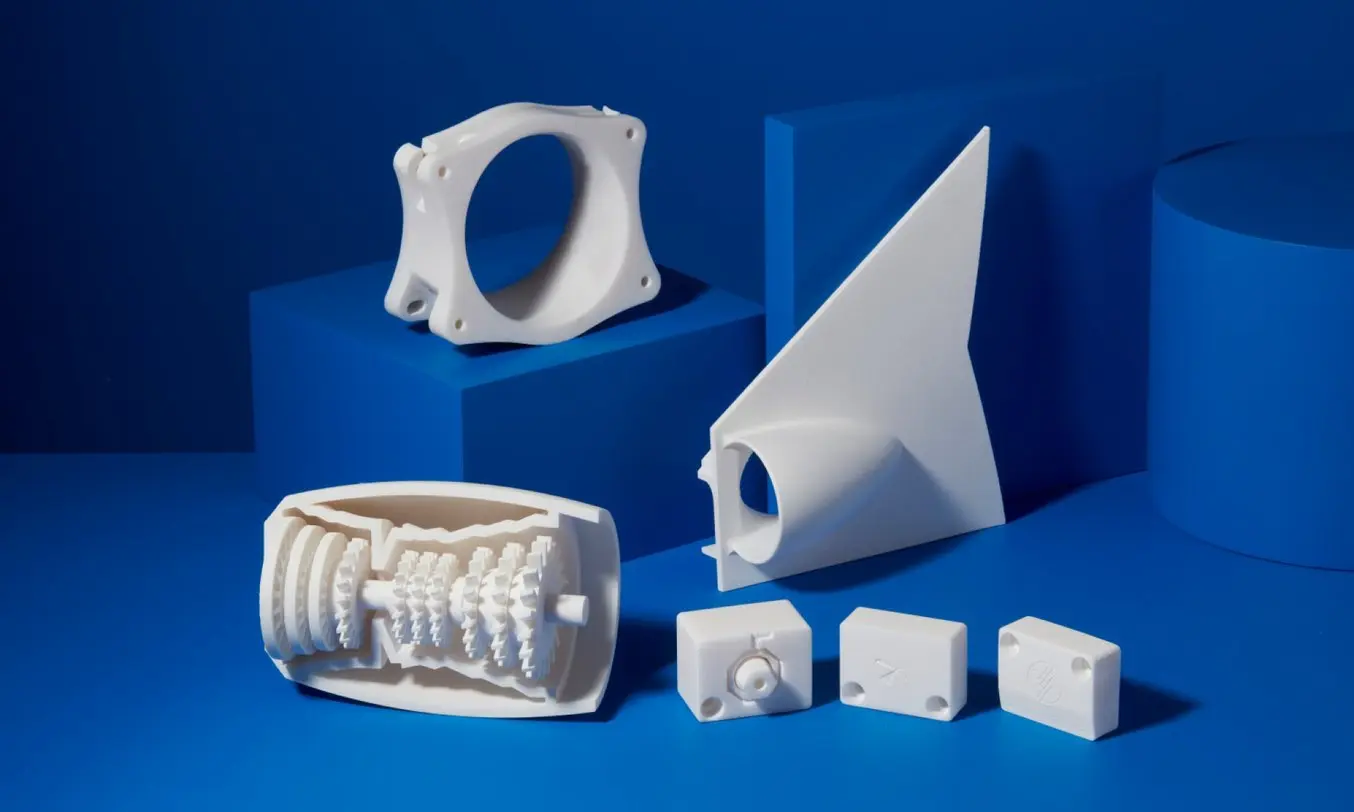
We are excited to announce our new family of Rigid Resins, a bundle of strong, stiff, and stable resins that are optimal for prototyping strong and stiff parts that need to resist bending. This family includes Rigid 4000 Resin (previously named Rigid Resin) and our new Rigid 10K Resin. Parts made from these materials are thermally and chemically resistant and will be dimensionally stable under load, but will experience brittle failure when pushed to their limits.
These resins are ideal for:
-
Turbines and fan blades
-
Jigs, fixtures, and tooling
-
Fluid and airflow components
-
Electrical casings
-
Automotive housings
Our family of Rigid Resins is distinct from our family of Tough and Durable Resins--while they may exhibit similar characteristics at a first glance, these two families have their unique advantages. Choose Rigid Resins for prototyping strong and stiff parts that resist bending, as they can handle more stress and load than Tough and Durable Resins.
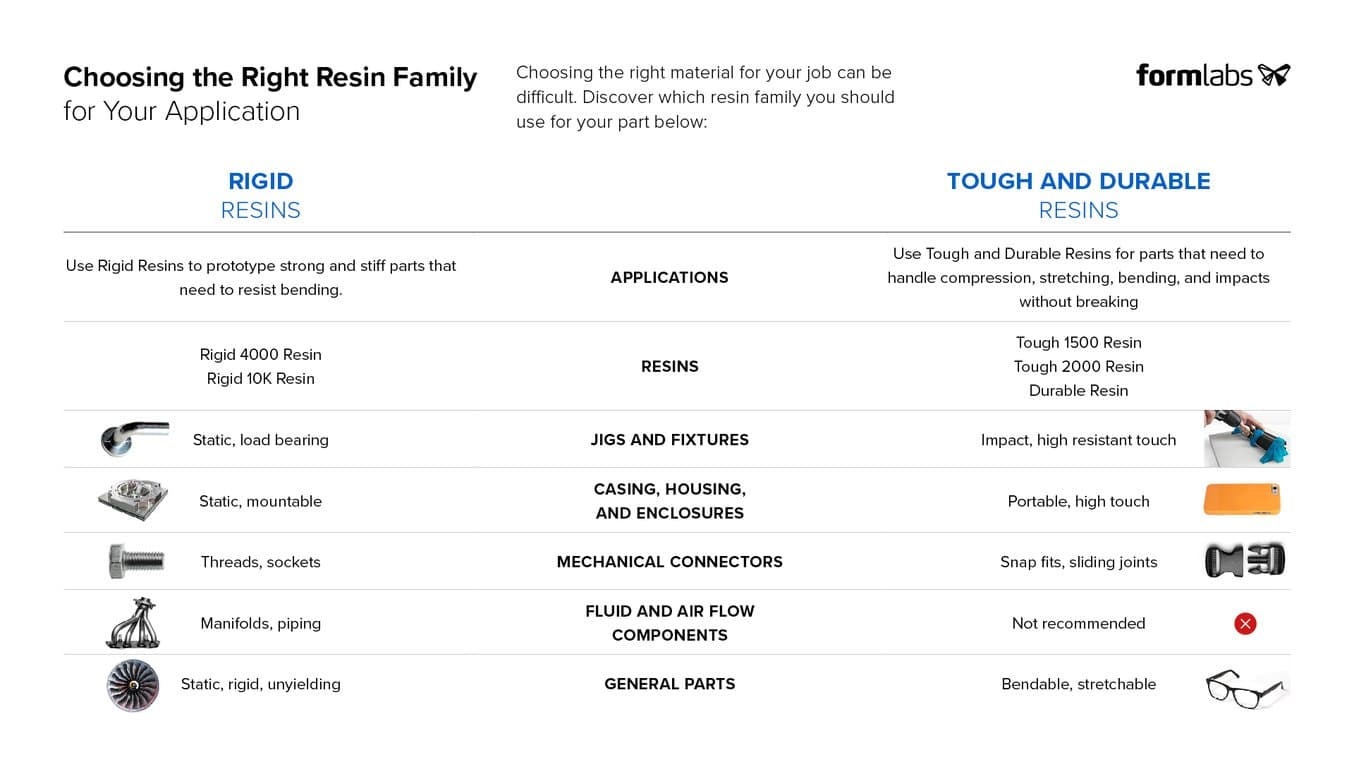
Within our family of Rigid Resins, there are distinctions between Rigid 4000 Resin and Rigid 10K Resin. While Rigid 4000 Resin is best for stiff and strong engineering-grade parts that withstand minimal deflection, the highly glass-filled Rigid 10K Resin elevates our Rigid Resin family and is best for extremely stiff and strong industrial-grade parts requiring complete rigidity and high stability.
How Rigid 10K Resin Suits Strong, Industrial-grade Prototypes
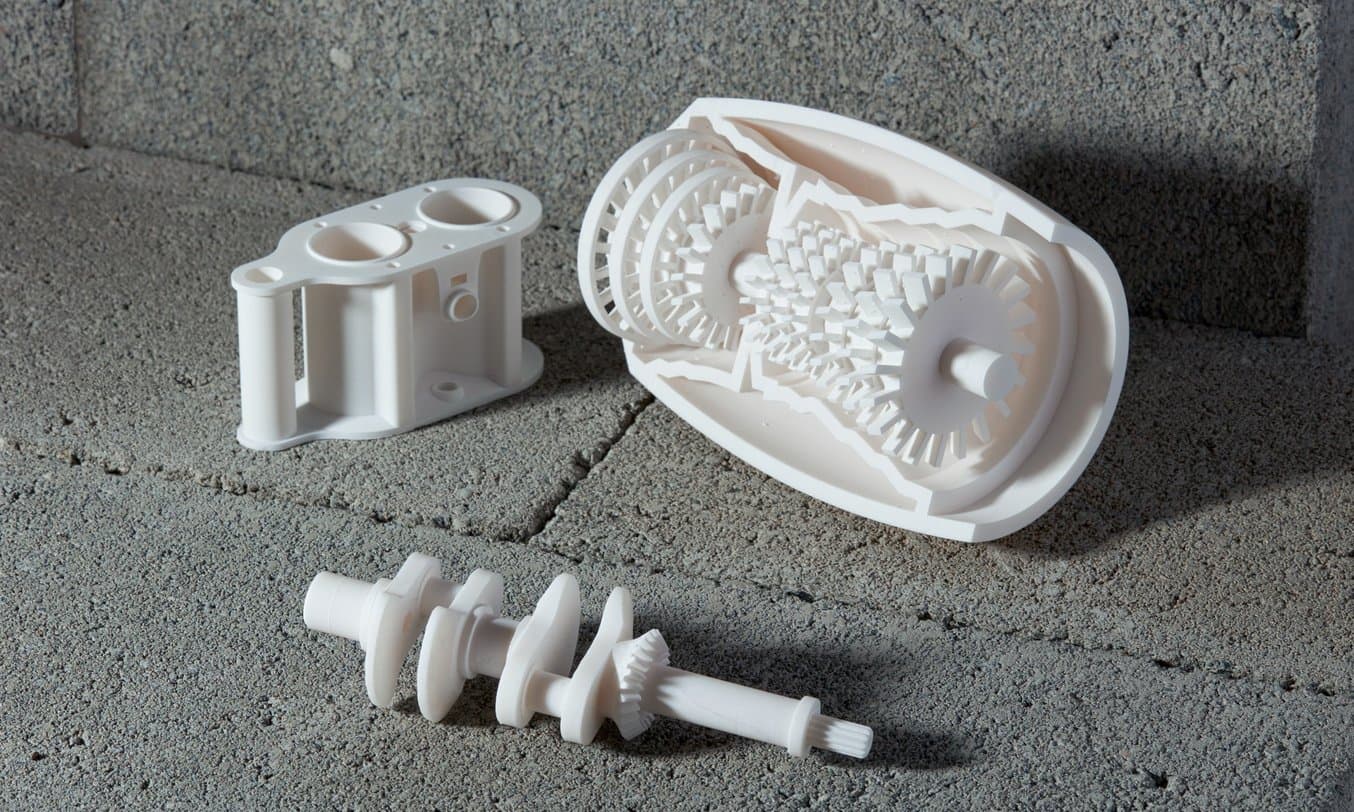
The stiffest material in our engineering portfolio, Rigid 10K Resin should be chosen for precise industrial parts that need to withstand significant load without bending. Rigid 10K Resin exhibits a smooth matte finish and is highly resistant to heat and chemicals.
Rigid 10K Resin is ideal for:
-
Short run injection mold masters and inserts
-
Aerodynamic test models
-
Heat-resistant and fluid-exposed components, jigs, and fixtures
-
Simulating the stiffness of glass and fiber-filled thermoplastics
Because of its incredible stiffness and strength, Rigid 10K Resin can be used across multiple industries for high-performance applications: engineering and manufacturing, aerospace and automotive, and injection molding.
Injection molding is one of the most novel uses for Rigid 10K Resin. By incorporating 3D printing into the injection molding process, manufacturers can eschew expensive and time-consuming metal machining. Rigid 10K Resin’s strength, stiffness, and thermal resistance make it ideal for short-run injection molding. Because of its strength, a mold made from Rigid 10K Resin can withstand injection pressures without breaking. Its stiffness ensures the mold will maintain its shape under pressure, producing accurate and precise parts. Its high thermal resistance means the mold will maintain rigidity even under high injection temperatures.
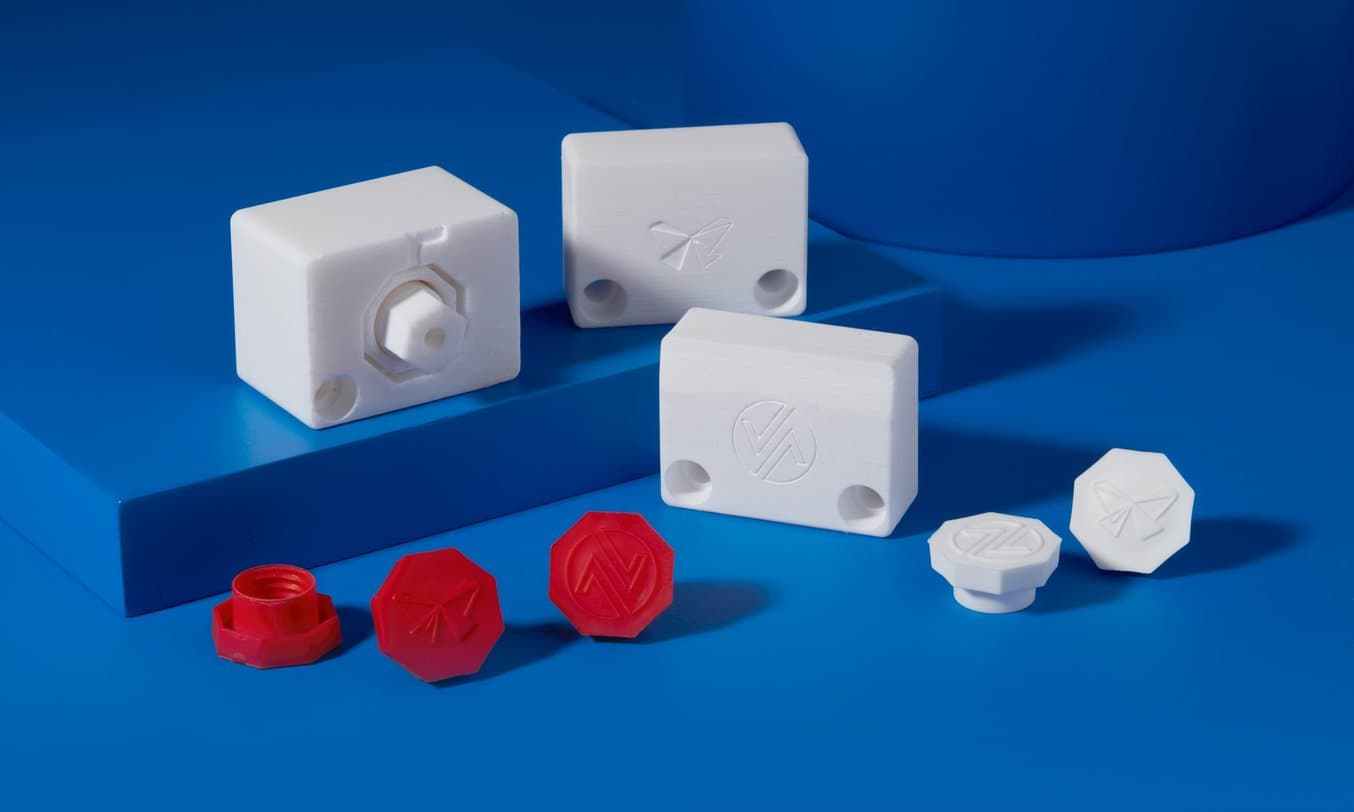
Learn How Novus Applications Used Rigid 10K Resin for Injection Molding
By 3D printing injection molds using Formlabs’ Rigid 10K Resin, Novus was able to achieve their desired outcomes while saving costs and time by a few days.
At Texas A&M University, many different wind tunnel projects are in motion--from helicopter blades to trash cans, to name a few.
According to Lisa Brown, manager and engineer at the Texas A&M Wind Tunnel, the team turned to SLA 3D printing with Formlabs to take advantage of materials like Rigid 10K Resin. Brown said they’ve been looking at replacing some pieces on an aircraft model they tested for NASA a few years ago, starting with parts they originally printed in polycarbonate with an FDM 3D printer.
“We could directly compare the FDM to the Formlabs prints. That was a first big eye opener for us, is that the big difference in surface quality between the two. So we started there and then we started printing some parts that would replace the metal pieces that we had made. And so that was an interesting comparison as well, to see how close a printed version could approximate the metal tail surface that we had made here,” Brown said.
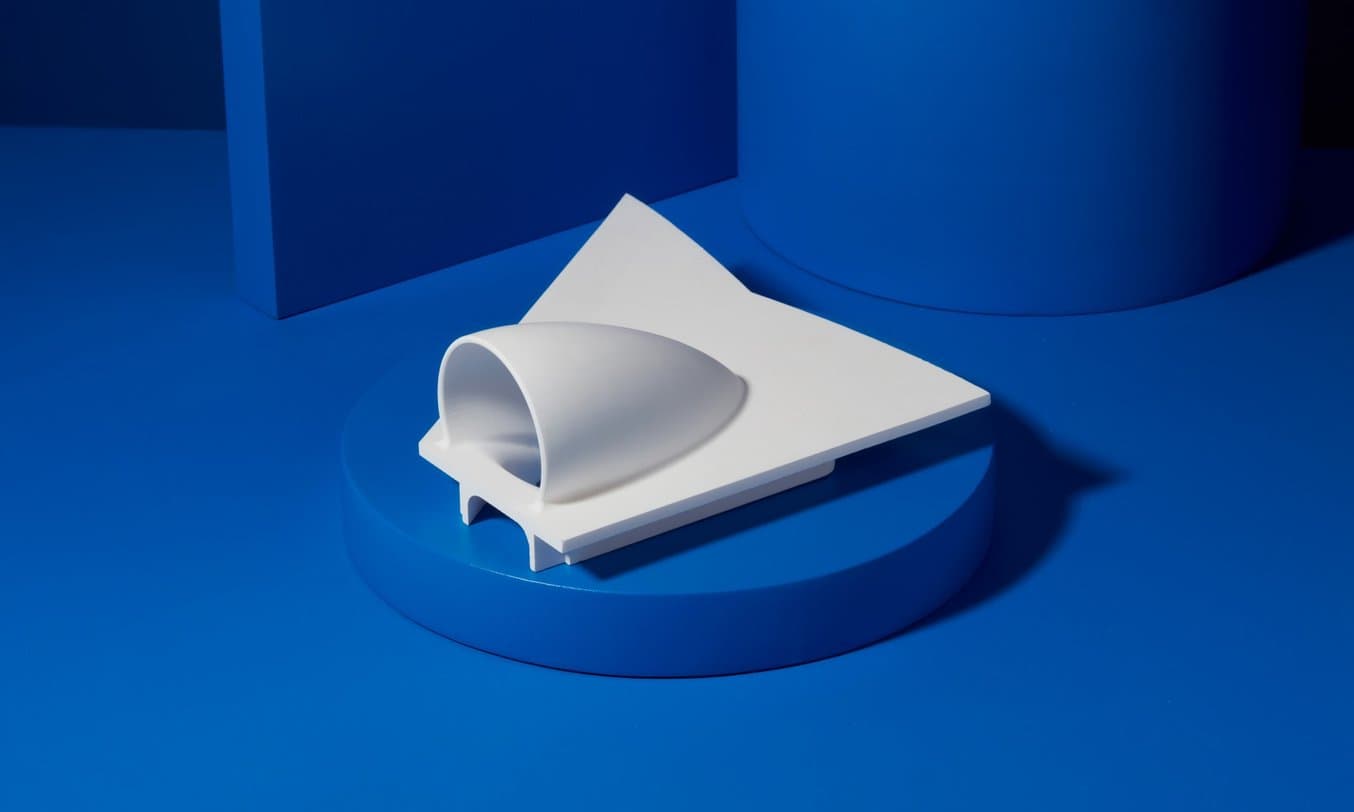
For wind tunnel testing, it was important for Brown and their team to have incredible surface quality with a smooth finish, in addition to being able to withstand deformation. Brown said they were impressed with Rigid 10K Resin.
“We do need the properties to be rigid enough that it's not going to deform. So another part of the outer mold line...is making sure that shape stays what it is. And so if we make a wing, we need to, if at all possible, make it to where that wing isn't going to bend under a load or change shape,” Brown said. “We're trying to keep the same model and the same shape throughout the whole testing...if we have a material that's too flexible, then it's not going to be suitable for a wind tunnel test.” Rigid 10K Resin fit the bill with its stiffness.
It was important for Brown to work with a material that allows air to flow over the smooth surface of the wings. “What we're really concerned with is that outer mold line or that outer shape that's touching the air flowing over it. That's why surface quality is such a big thing for us,” Brown said. “This material allows us with so much less hand finishing to get to a very beautiful, smooth finish. Very similar to what we'd see out of a metal machine part, but with a lot less human interaction with it than we'd have to do with machining it from scratch.”
How Draft Resin Speeds Up Rapid Prototyping
We are excited to unveil a new formulation of Draft Resin. Printing four times faster than Formlabs standard materials, Draft Resin is ideal for initial prototypes and rapid iterations. Because of its incredible print speed that facilitates faster design and prototyping, Draft Resin helps bring products to market faster. From fast print initiation speeds to minimal support removal, wash, and cure times, Draft Resin has an optimized workflow to truly maximize efficiency.
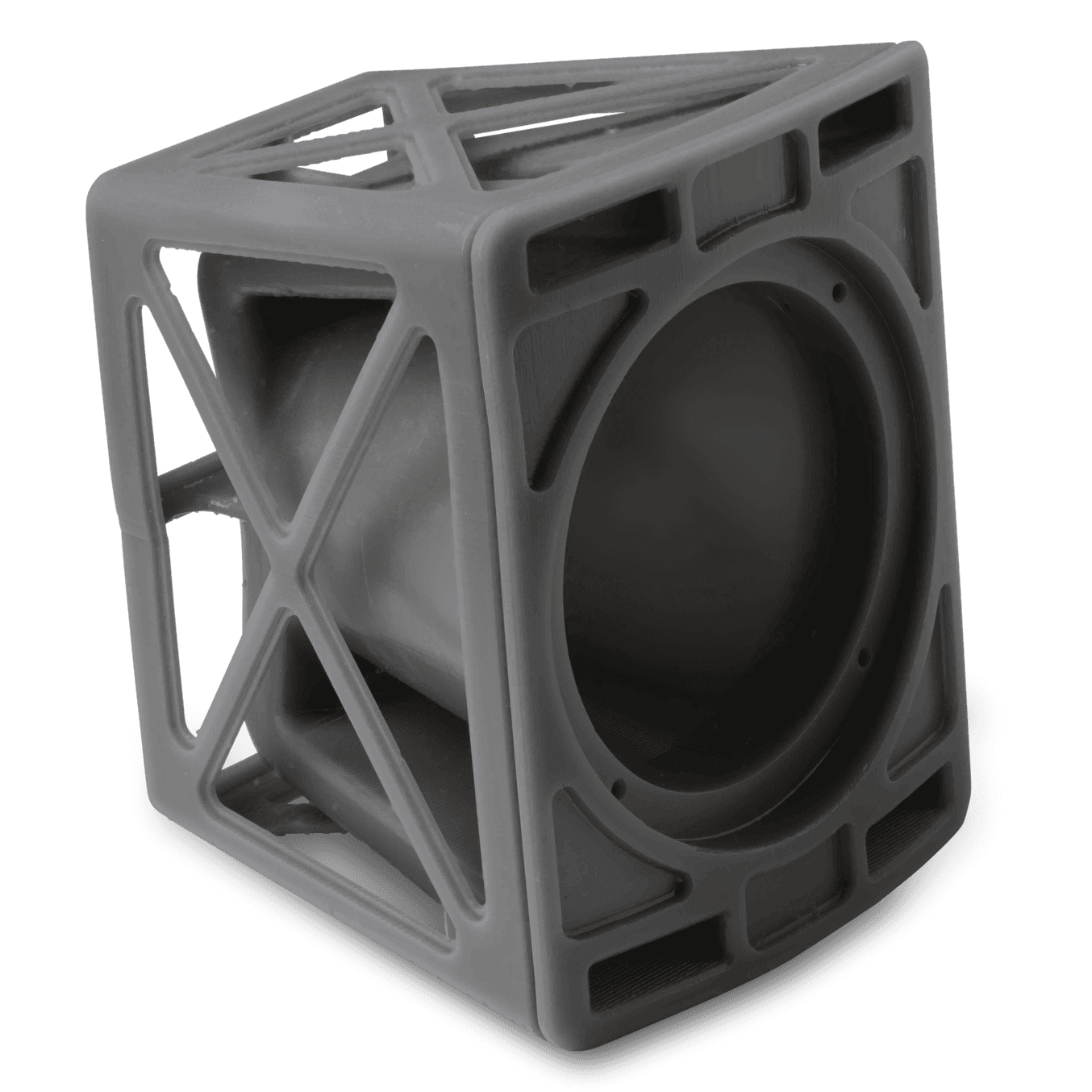
100 microns | 200 microns |
---|---|
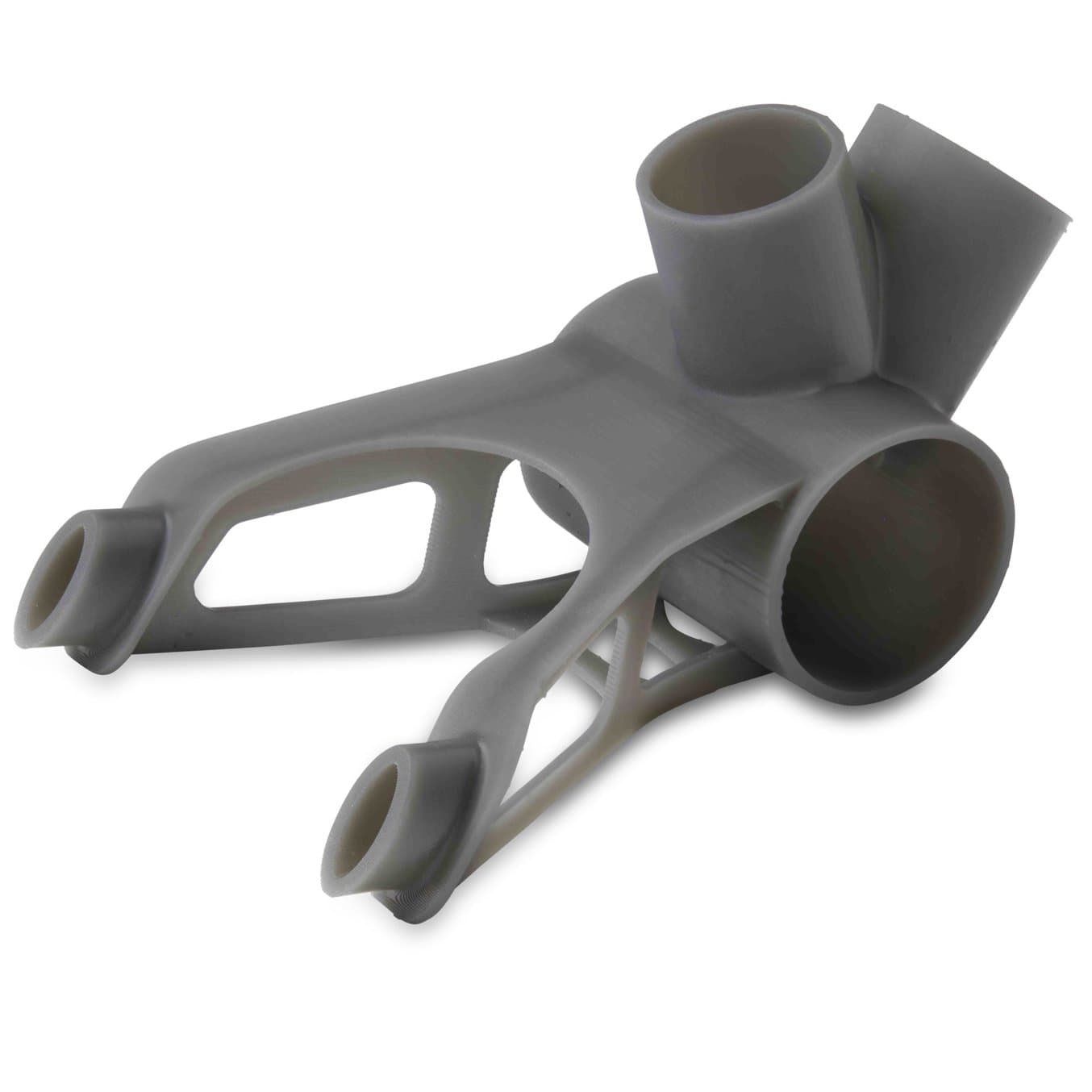
100 microns | 200 microns |
---|---|
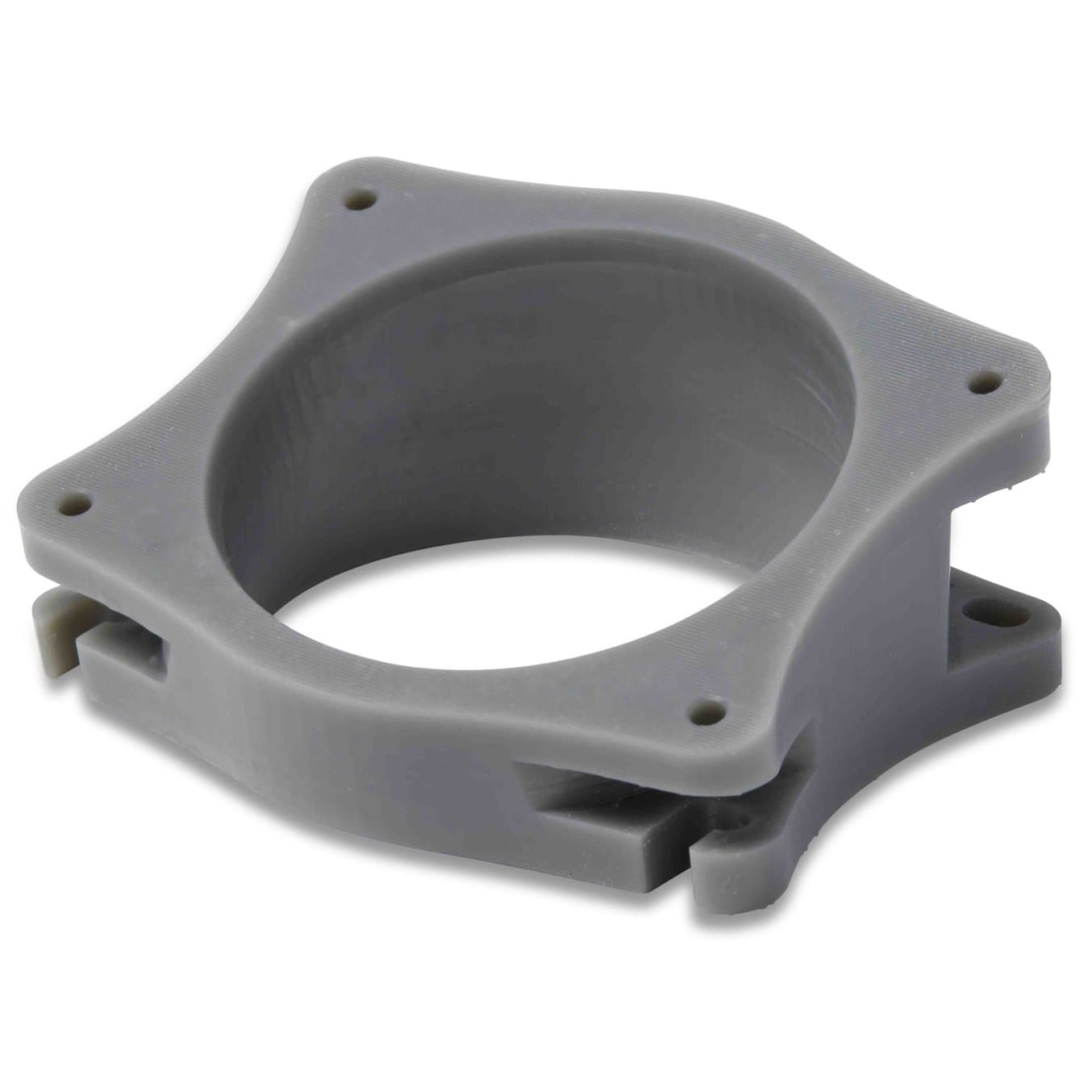
100 microns | 200 microns |
---|---|
Draft Resin is ideal for the following:
-
Initial prototypes
-
Rapid design iterations
-
Live 3D printing demos
-
High throughput applications
Faster print time doesn’t mean compromising quality--our reformulated Draft Resin reduced layer thickness by 33 percent, improving surface finish.
On the Form 3L, Draft Resin is a powerful material for producing full scale prototypes quickly without sacrificing detail. Large parts print in hours, rather than days, improving productivity. This combination can spur more printing possibilities and fuel innovation.
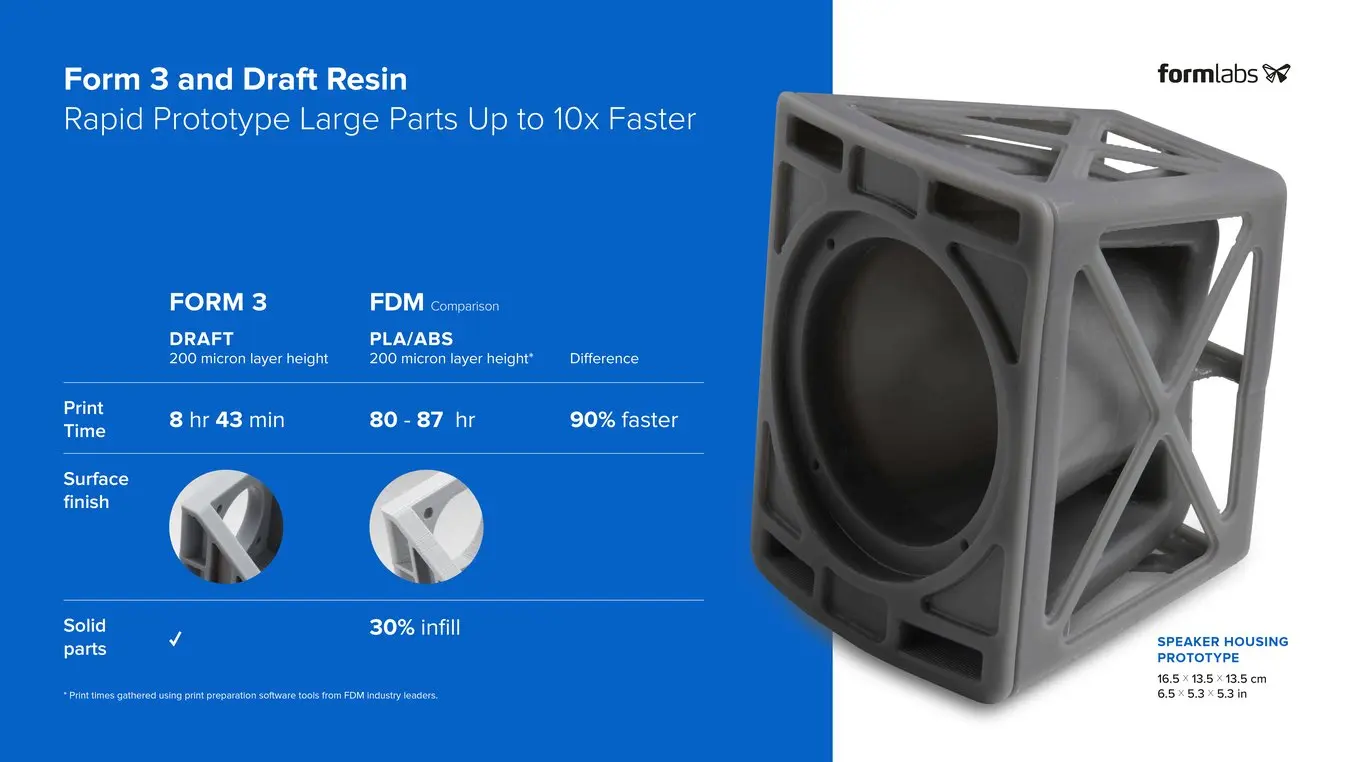
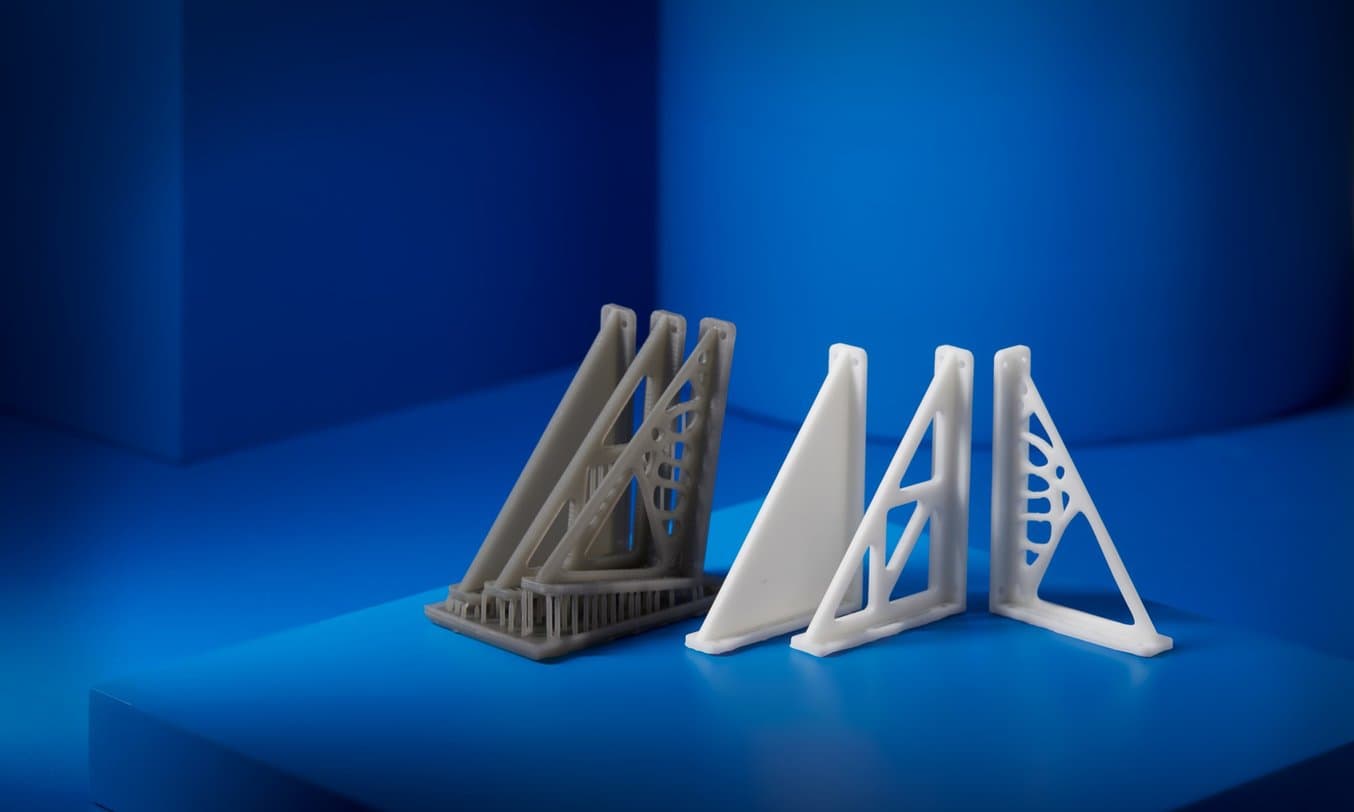
From Quick Designs to High Performance Parts: Explore Our New Draft and Rigid 10K Resins
Looking to learn more? Watch our fireside chat where Formlabs product managers dive deeper into these materials and applications.