SLS 3D Printed Anatomical Models and Surgical Guides for Improved Fracture Treatment and Complex Osteotomies
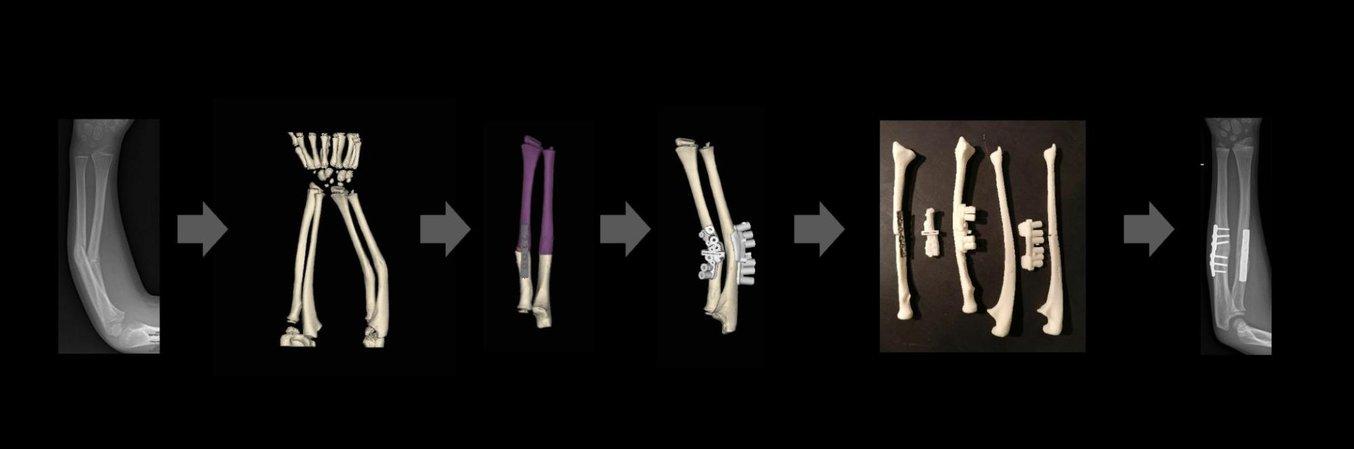
AZ Monica is a rapidly developing general hospital with campuses in the Antwerp area in Belgium, which include a large orthopedic department with 18 orthopedic surgeons, each having their specific area of expertise.
Dr. Frederik Verstreken is specialized in hand, wrist, and forearm surgery, and has been the driving force behind the orthopedic department adapting 3D visualization, digital planning, and 3D printing since he first used digital technologies in 2009.
The orthopedic department first started by outsourcing most of the cases, but now covers the entire workflow from planning to segmentation and the 3D printing of medical instruments using in-house stereolithography (SLA) and selective laser sintering (SLS) 3D printers.
Read on to learn from Dr. Verstreken how the orthopedic department at AZ Monica uses 3D printed anatomical models and surgical guides to treat acute and chronic fractures and conduct complex osteotomies, and his advice on how any institution can start from scratch and build a digital lab.
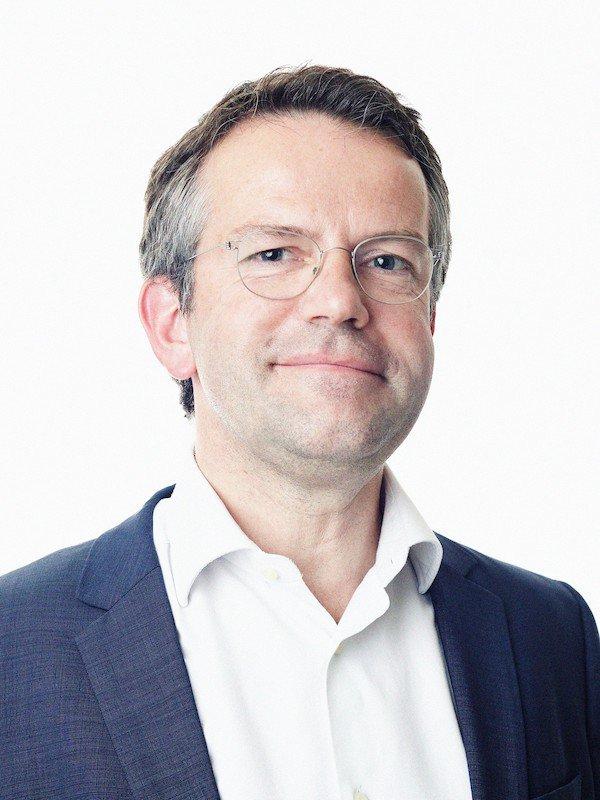
SLS Printing at the Point of Care: How Dr. Verstreken Is Using Materialise and Formlabs To Improve Patient Care at the AZ Monica Hospital
Dr. Verstreken shares how AZ Monica implemented SLS technology at the hospital in Belgium, which enables the team to save time and improve patient outcomes in hand surgery by producing cutting and drilling guides at the point of care.
Conducting Complex Osteotomies With 3D Printed Guides
One of the first core applications of digital technologies at AZ Monica was osteotomies for malunited bones. Broken bones that heal in an incorrect position can look strange, cause pain, and the patient can lose function, such as movement or grip force.
Osteotomies attempt to put the bones back in the right position, but they are complex surgeries because the cases involve three-dimensional deformities that can be angulated, rotated, shortened, or all of these at the same time.
The traditional technique involves looking at 2D X-rays and planning on paper, but this doesn’t provide a complete three-dimensional picture of the deformity, so there is no certainty that what the medical team planned before would be possible to fully achieve in the operating room.
“There are things that we were not able to do, they were just too complex. The chance that we were going to restore normal anatomy was so low that we would not do it. We would just have told the patient that they have to live with it. Life is possible, but you are limited. For example, if you have a forearm fracture and you cannot rotate your arm, it's very difficult to work on a computer. It's very difficult to use a smartphone. It's very difficult to do manual labor and sports.”
Frederik Verstreken, Hand and Wrist Surgeon, AZ Monica Hospital
Digital technologies allow the team to precisely plan each case, 3D print anatomical models to get a tangible extra dimension for the planning process and in the operating room, and also produce precise surgical guides to conduct surgeries with high accuracy. “If we can restore anatomy, then we can restore function as well. There's a strong correlation between making the anatomy as it was before and the patients regaining normal motion and getting rid of the pain,” said Dr. Verstreken.
“It allows us to do things that we were not able to do before. They can regain full forearm rotation if it's a forearm fracture, or wrist motion if it's a wrist fracture. The clinical results are very impressive. It makes a big change in their lives because they can do manual work, drive, and play. Many of our patients are children, so they would have had trouble playing tennis, ball sports, and so on. They can now start doing that all again, thanks to 3D technology.”
Frederik Verstreken, Hand and Wrist Surgeon, AZ Monica Hospital
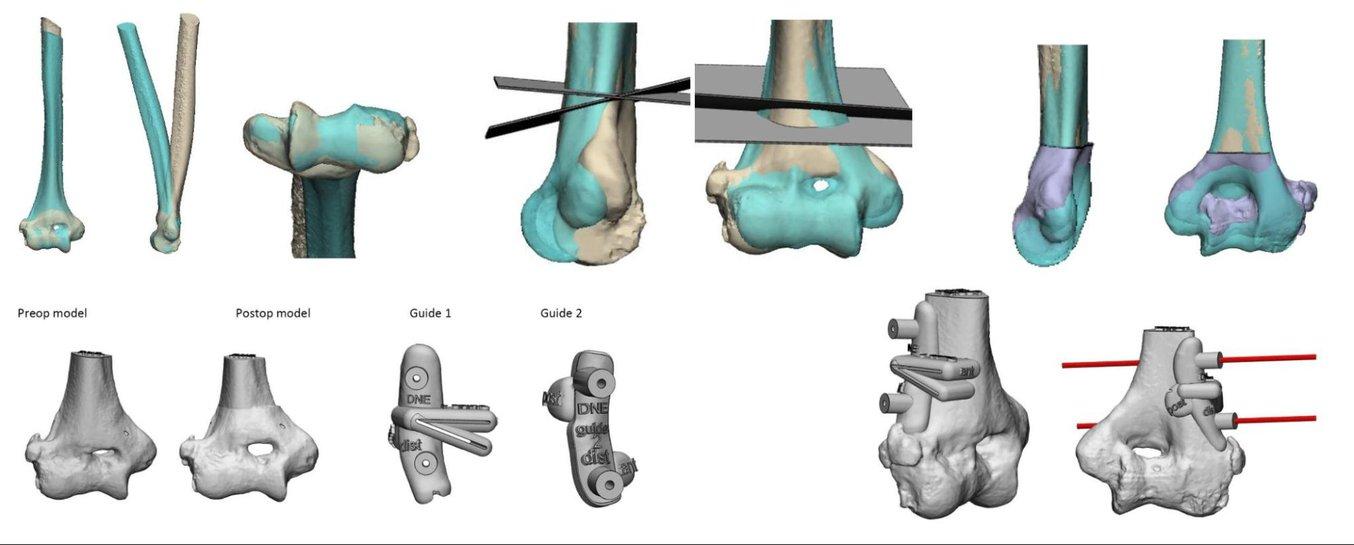
3D planning of a distal humerus malunion, with the normal side superimposed on the abnormal side.
The treatment for these cases using the digital workflow normally starts with a bilateral CT scan. The team segments the abnormal and the normal side, mirrors the image of the normal side, and superimposes it on the abnormal side so they can look at the deformity in 3D.
Then they 3D print anatomical models or look at the case in augmented reality. If they decide to plan corrective surgery, this is done virtually on the computer screen. Based on the deformity, the best location for an osteotomy cut is decided and the fragments will need to be displaced to be in the right position again. They choose which fixation will be needed and what kind of plate is going to fit best for the patient. When the whole operation is done on the computer, the engineer on the team designs surgical instruments that will be 3D printed and used in the operating room to fit on the bone of the patient. This process allows surgeons to exactly copy the virtual surgical plan in the operating room.
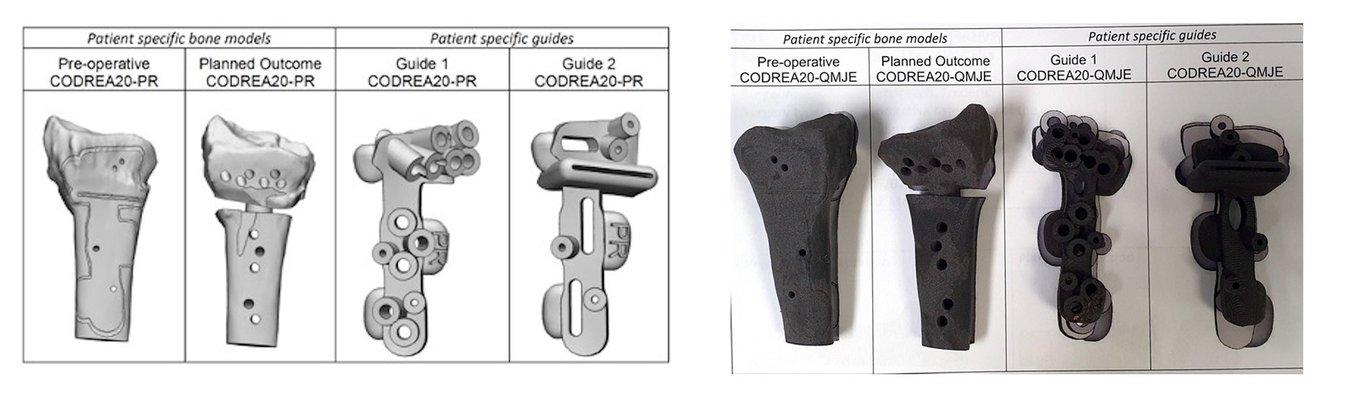
Patient-specific bone models and surgical guides printed in Nylon 12 Powder to treat a distal radius malunion.
“The guides tell us where we need to make holes and where we need to make the cuts, so that when we take a plate, everything will fall in the right position. We are much more accurate than without the guides. We save at least 50% of the time with it compared to doing it freehand. And it's much more accurate.”
Frederik Verstreken, Hand and Wrist Surgeon, AZ Monica Hospital
The instruments that go into the operating room need to pass stringent requirements. They need to be biocompatible and be able to get through steam sterilization at 134 °C. This rules out most 3D printing processes and materials except SLA and SLS 3D printing.
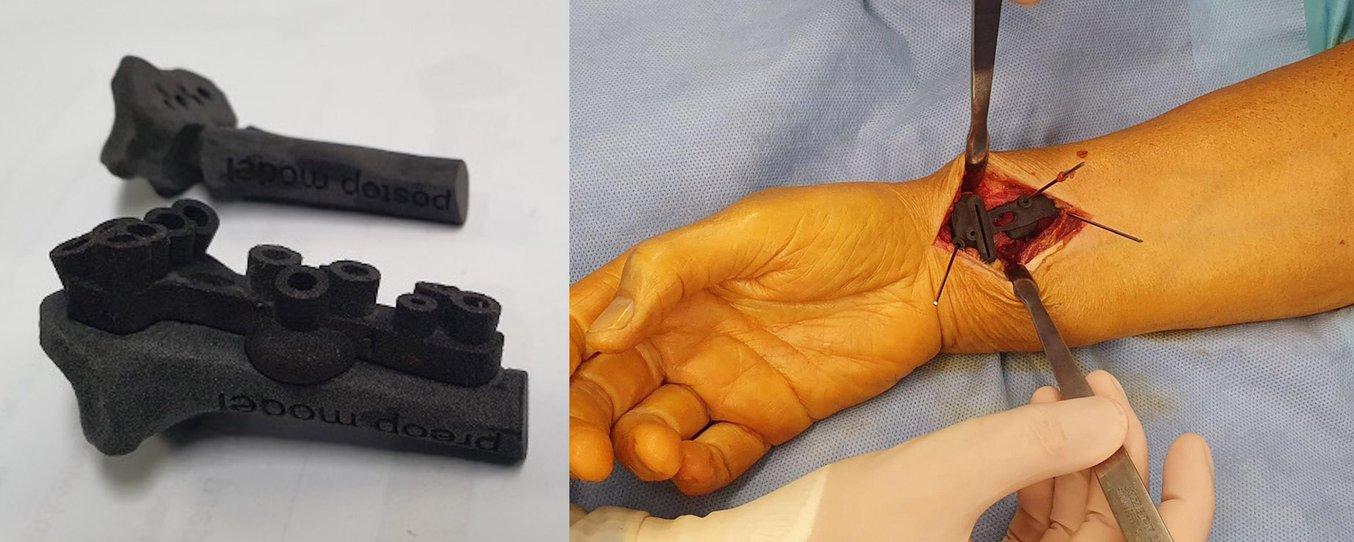
3D printed guide on a preoperative model and in use during surgery.
“I was really happy that the resin printers from Formlabs came. Because for us, that was a printer that was affordable, that was able to print medical-grade materials, and we were able to sterilize them in the hospital. So for us, that was really a game changer. Because we had a small FDM printer that was just a gadget printer, but it was not medical grade. If we tried to sterilize [parts it printed], they would melt. So we could just do a little bit of printing, but nothing serious.
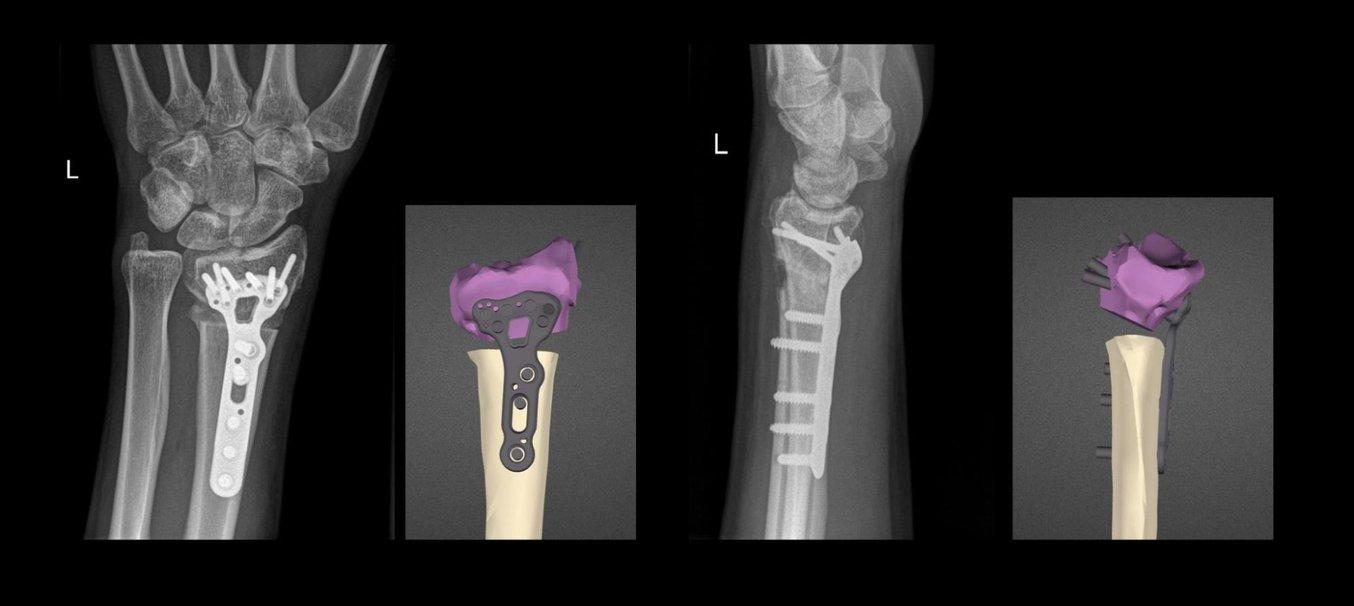
Distal radius malunion case, 3D planned virtual outcome and radiographic outcome 2 weeks after the operation.
Dr. Verstreken first started with resin guides, but found SLS nylon guides even better suited for these types of surgeries, as they were more flexible and less likely to break. So at first, they started ordering nylon parts from external service providers.
“The SLS printers that were on the market were too expensive, too much hassle, and so on. But it was always the idea, that as soon as we can find an affordable SLS printer, we should try to get it. Then the Fuse 1 came along and it was obvious that was the printer we would need for our lab,” said Dr. Verstreken.
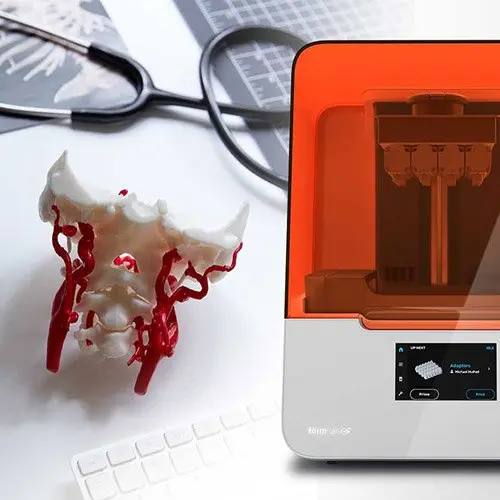
Intro to Medical 3D Printing
Join Formlabs for this introduction to learn best practices for medical 3D printing and see the latest Formlabs Medical ecosystem, including multiple new medical-grade products!
Looking Inside Acute Fractures With Anatomical models
Having in-house 3D printing capabilities also opened the door at the hospital for using digital technologies for acute cases.
“If it's an elective case, like a malunited fracture that's been like that for a year or so, then we have the time and the luxury to plan surgery over a few weeks’ time. But if it's an acute injury, we don't have a week's time. If you come into the hospital at the emergency room with a broken wrist, then usually the wrist gets operated within two, or three days. If we had to outsource 3D printing, we were never sure that the parts would come in time,” said Dr. Verstreken.
“Now, with the printer and our engineer in the hospital, the interaction is much, much better. We can see a fracture today and I can have the printed parts tomorrow morning in the operating room, if we print them overnight. That was impossible when we were outsourcing.”
Frederik Verstreken, Hand and Wrist Surgeon, AZ Monica Hospital
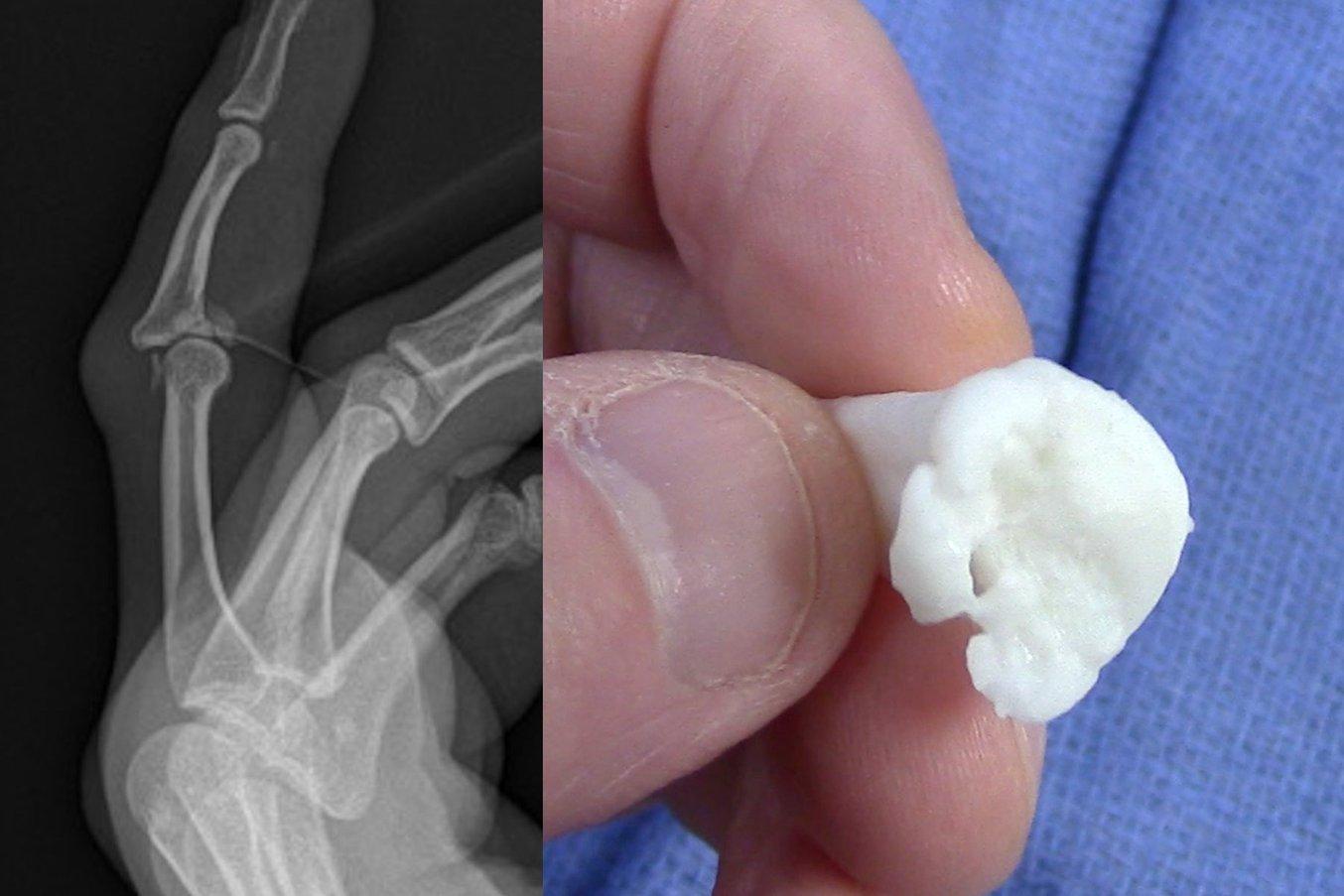
X-ray and the 3D printed anatomical model of a complex finger fracture.
With acute cases, anatomical models are used in planning, for patient education and consent, as well as visual guides in the operating room.
“We use anatomical models primarily for intraarticular factors. So if you have a bone that's broken into different pieces, then we need to put the pieces together in the operating room. If you have a model of the broken bone next to you on the operating table, it really helps you a lot to see where the pieces are and where the bone is exactly broken. Because we cannot look inside the joint. But if we have a printed model of the bone next to us, we can look at the inside and see where the parts are broken and how they are displaced. That helps us a lot in putting the pieces back together in the original position,” said Dr. Verstreken.
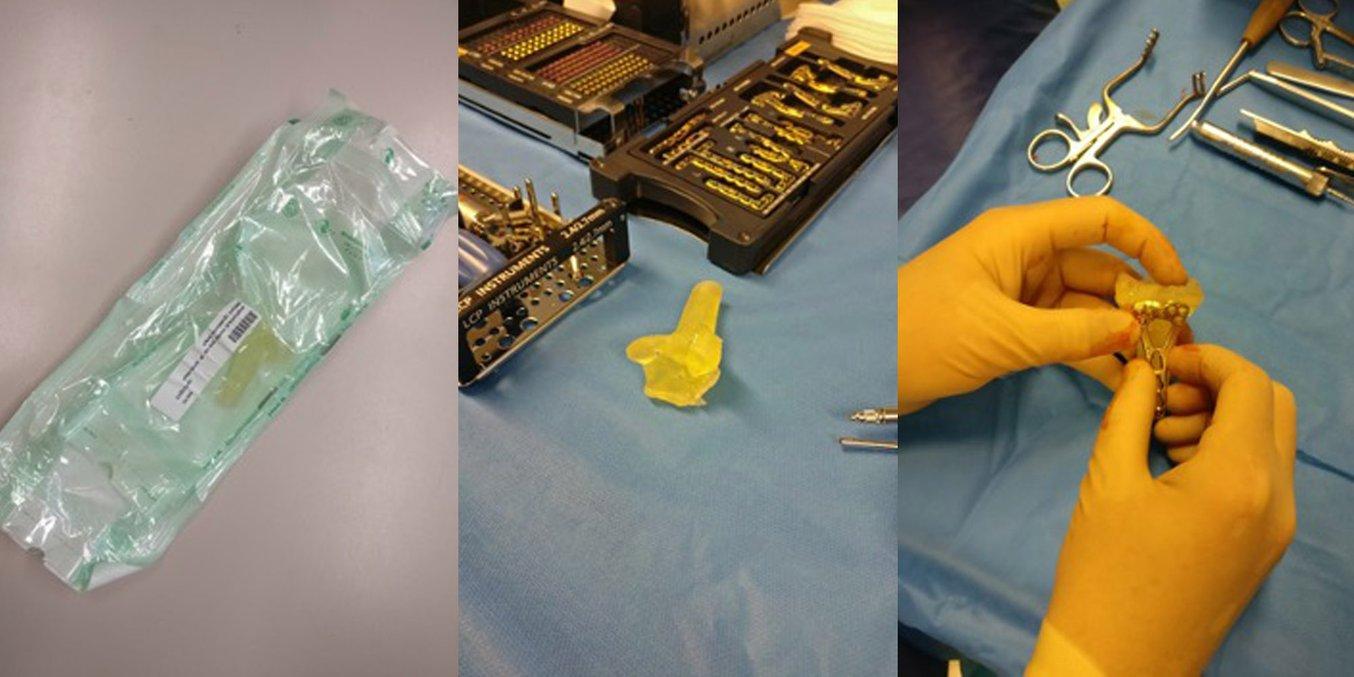
Both SLA and SLS 3D printed anatomical models can be sterilized to be taken into the operating room. This model was used to test the positioning of the metal plate.
“But not just that. It also helps us to prepare the operation on the computer, put all pieces together on the computer like a jigsaw, and then have it next to us printed on the operating table. And the printed model allows us to choose the best fitting plate for that specific case and decide where to position the plates and screws to obtain the best possible outcome,” said Dr. Verstreken.
Dr. Verstreken stated that the combination of visualization, digital planning, and 3D printed anatomical models empowers clinicians to save around 30-40% of the time in the operating room. For these complex cases, they come much better prepared to do the operation than without these digital tools, use less radiation, and still achieve substantially higher accuracy.
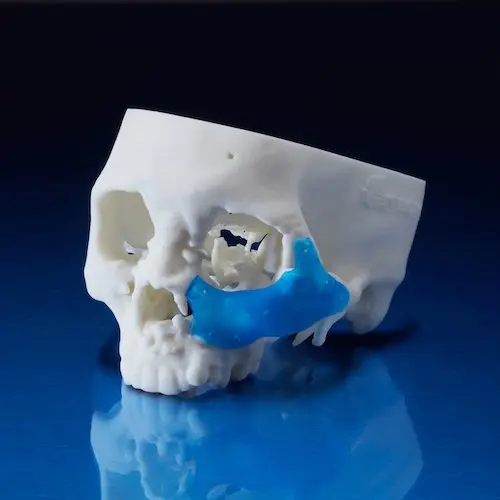
How to 3D Print Anatomical Models for Preoperative Planning and Enhanced Patient Consent
Download our white paper for a practical walkthrough for physicians and technologists to get started creating 3D printed anatomicals models from patient scans, reviewing best practices for setting up a CT/MRI scan, segmenting datasets, and converting files to a 3D-printable format.
Quality Control and Regulatory Affairs With In-House 3D Printing
Beyond the clear clinical benefits, having an in-house 3D printing lab also involves dealing with the regulatory landscape and quality control, for every step of the procedure from data acquisition and storage, the use of computer software for data manipulation, the 3D printing itself, and the follow up of outcome results and complications.
Since 2021, medical devices such as anatomical models and surgical guides need to conform to the Medical Device Regulation (MDR) in Europe as Class IIa devices, which is very similar to regulation in other parts of the world. The regulation is very strict, however, some exemptions exist for “in-house devices” and “custom-made devices” produced in hospitals and used within the same legal entity, which simplifies compliance (Chapter II - Article 5).
Dr. Verstreken and the orthopedic department worked with legal advisors and consultancy companies and received support from Materialise to be able to validate their workflows. The hospital set up a quality control system, which is also easier when everything is done in-house, and the cases and processes are well documented.
When medical instruments are produced by third-party 3D printing providers, they become the manufacturers, and then they have also the responsibility to comply with regulations. This means that the hospital has to answer many questions about the indications and how it is planning to use the devices, which limits the flexibility and freedom of practitioners.
Having everything in-house also makes it easier to have a quality control system. “[With third-party providers], you're never sure how they do it, what their quality control system is, or what powder and printers they use and how. We know now that what we print is exactly what we are going to need. If we use very tiny drill cylinders, for example, 1.2 millimeter drill bits that go through the instrument. We now know, because we tested it on the Fuse 1, that if we plan it 1.2 millimeters, what we're going to get is 1.2 millimeters exactly. If we outsource it, it can be 1.1 or 1.3 millimeters which might not fit as well. So that's a factor of uncertainty. I feel that we have everything under control so that what is designed and is planned in 3D on the computer, is also what's going to come out of the printer, in the exact dimensions that we need,” said Dr. Verstreken.
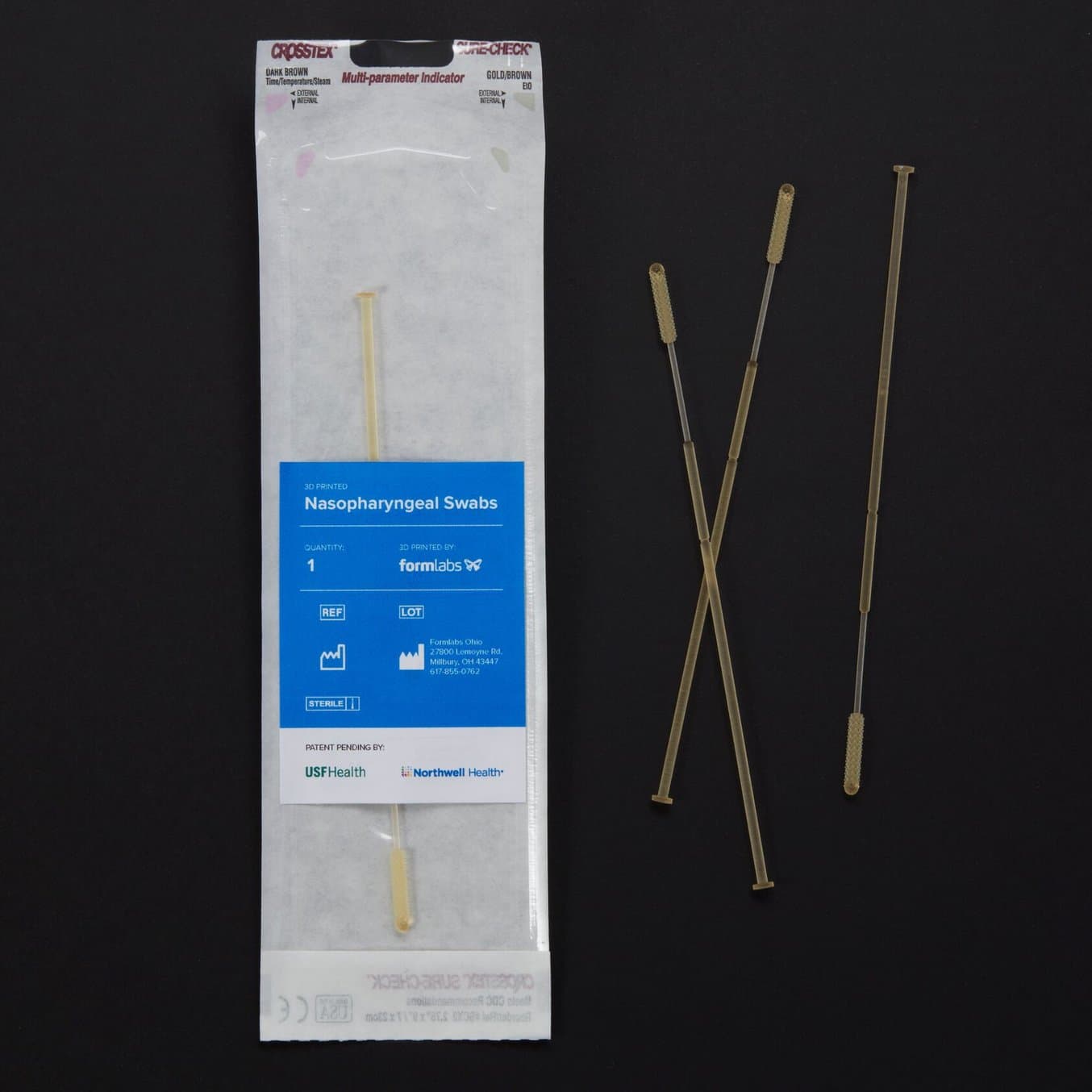
The Ultimate Guide to Quality Assurance and Regulatory Affairs in Medical 3D Printing
This white paper aims to guide users in the medical device industry through every stage of the product development process, from evaluating manufacturing methods and 3D printing technologies to specific regulatory requirements for commercializing and marketing end-use 3D printed medical devices.
How to Start a Digital Lab in a Hospital
While starting a lab for digital technologies in a hospital from the ground up might at first sound like a daunting initiative, it becomes much easier once broken down into smaller stages.
Dr. Verstreken identified a list of key steps that empower practitioners to bring digital technologies in-house:
- Colleagues interested in 3D technologies
- Support from hospital administration and funding
- Imaging
- Clinical engineer and technicians
- Software and hardware (all approved for medical applications)
- External partners: legal advisers, outsourced providers for metal printing, and more
Dr. Verstreken first got exposed to digital technologies in 2009, “I started to become more and more interested in this technology, and the potential on how this could help me in improving the care I was able to give to the patients.“
He first worked with external providers to produce models and guides for a limited number of the most complex cases. As the range of applications and cases gradually increased, other surgeons in the orthopedic department also became interested in using digital technologies, which meant that there were enough economies of scale to start bringing these tools in-house.
AZ Monica then purchased a license for Materialise Mimics software so that the team could start doing segmentation and visualization themselves. As the need for these functions increased, they hired an engineer for planning surgeries and designing guides.
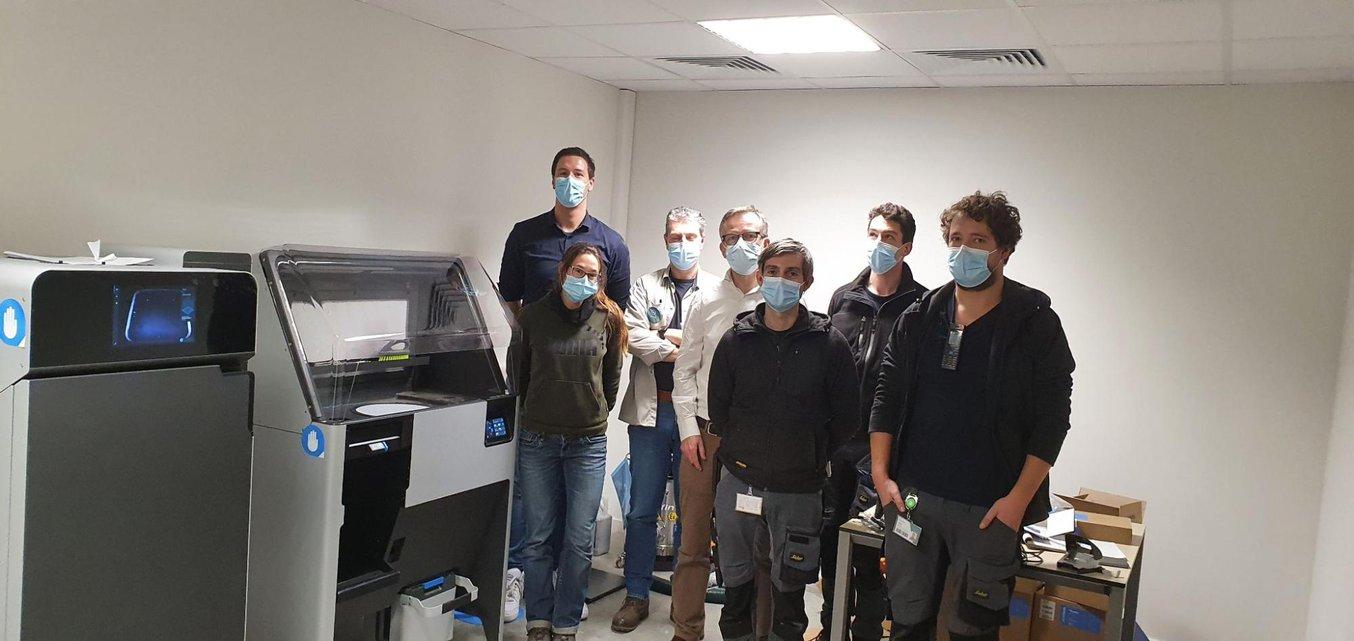
AZ Monica’s team includes an engineer in the imaging lab and a technical department that manages the 3D printers.
To cut lead times and be able to support acute cases, they decided to bring manufacturing in-house with 3D printers. They first purchased a Formlabs SLA 3D printer, which is compact enough that it can be operated within the department. As the demand grew and they wanted to bring SLS 3D printing in-house as well, they decided to involve the technical department, which is now doing the printing and post-processing of the parts.
“The 3D lab we have now is a collaboration between our orthopedic department and the radiology department of the hospital. We had amazing support from the hospital direction, they’re very interested in supporting us here. They feel it's a great way to promote the hospital, as it shows that the hospital is modern, embraces new technology, and it’s focused on the improvement of patient care,” said Dr. Verstreken.
Accelerate Adoption of Digital Technologies
One of the remaining impediments to the adoption of digital technologies is funding. In many countries, these treatments are not yet reimbursed by insurance companies or the government.
In Belgium, patients have to self-pay for this part of the treatment. By doing everything in-house, AZ Monica can keep prices reasonable, but this still limits adoption. Dr. Verstreken thinks that the pressure is mounting and that they are close to reaching a deal for reimbursement not just in Belgium, but in many other countries like Germany or the United States.
He believes that one way to accelerate adoption is through education. He’s part of a hand surgery specialty group focused on digital technologies and their department works with other hospitals in the area that don’t have in-house labs yet.
“It is important to make surgeons more aware of this technology. A lot of people are now talking about it and more and more surgeons are interested. At the moment there are maybe 1-5% of orthopedic surgeons who are really using 3D technology and who know what it is and who know the potential. But at a recent international hand surgery meeting in London, 20% to 30% of everything that was discussed was related to 3D technology. The medical community is a very slow adopter. It takes many, many years. But, I think now we've gone through a point of no return, it's like everybody has seen the light now. More and more hospitals will get in-hospital 3D printing labs. It's a fantastic technology that allows us to give patients better care,” said Dr. Verstreken.
Watch our webinar with Dr. Verstreken where he shares how AZ Monica implemented SLS technology at the hospital in Belgium, which enables the team to save time and improve patient outcomes in hand surgery by producing cutting and drilling guides at the point of care.
Ready to implement 3D printing in your own institution? Have questions about medical 3D printing workflows and solutions?