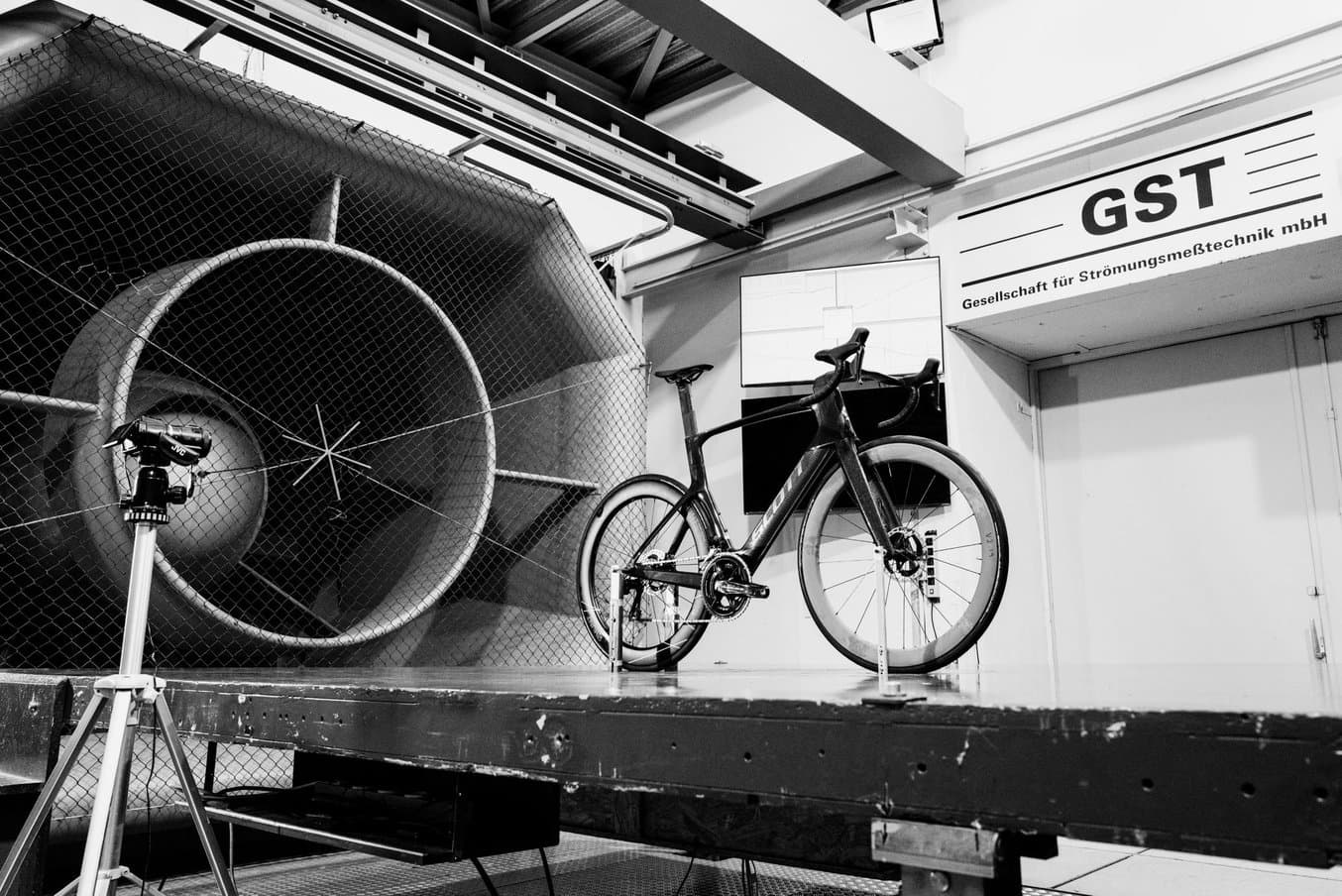
南ドイツのFriedrichshafen Windkanalで行われたHunt Bike Wheelsのリムプロファイル検証の様子
通勤やアウトドア、ワークアウト、レースなど、世界中でサイクリングの人気が高まる中、自転車メーカーにとっては変わり続けるトレンドや技術の発展に遅れを取らないことが何よりも大切です。The Rider Firmは、消費者向けに直販を行う世界有数のホイールメーカーHunt Bike Wheelsを始め、Privateer BikesやCairn Cycles、Dissent 133など、最先端の高性能ギア、コンポーネント、自転車メーカーに製品を提供しています。
資金力に余裕のあるライダー以外にもアクセスしやすい高性能自転車やコンポーネントの生産を目指す同社は、潤沢な予算を確保できる昔ながらの自転車メーカーよりもスマートで効率的な製造工程が必要です。イノベーションを促進し作業工程をより高効率なものにするために同社が最初に行ったのは、大容量SLA光造形3Dプリンタ Form 3Lを導入し、3Dプリントによる内製化を行うことでした。
自転車業界の主要な製造拠点は台湾ですが、The Rider Firmの製品開発はイギリスで行われています。そこで、Form 3Lを存分に活用して試作品製作を行なっています。私たちは今回、Privateer Bikesの開発エンジニアであるDan Hicks氏とHunt Bike WheelsのデザインエンジニアであるPatrick Brown氏にお話を伺い、彼らの製造工程に関するインサイトと、常に新製品を開発し続けるエンジニアリングチームにとってForm 3Lがどんな役割を果たしているかを教えていただきました。
Hunt Bike Wheels:リムの風洞試験用に実物大機能試作品を3Dプリントで製作
Hunt Bike Wheelsという社名は、より良い製品を作るためにあらゆるディテールを粘り強く追い求めるという同社のミッションに由来しています。経験豊富なエンジニアたちがチームとなり、さまざまな地形で卓越した性能を発揮するホイールセットを作るべく、たゆまぬ努力を続けています。広範な研究、開発、検証を通じてホイールのエアロダイナミクスを最適化し、スピード、安定性、効率の向上を目指しています。プロの自転車競技ではマージナルゲインがすべてです。時速45kmで走るホイールセットの空気抵抗の差はで2%〜5%と極小ですが、この僅かな差が1位と10位を分けるのです。
Patrick Brown氏が説明してくれたホイールの開発工程では、まずエンジニアがさまざまなリムプロファイルを設計するところから始まり、数値流体力学(CFD)を使って仮想的な風洞環境を作り出し、それぞれのプロファイルを検証します。CFD解析で最も高いパフォーマンスを発揮できるリムプロファイルを特定し、その後3Dプリント製の試作品を使って実環境で検証を行います。
最新のLIMITLESSホイールセットでは、CFD解析によって約45種類のリムプロファイルを検証し、最も空気抵抗が小さく、横風のハンドリングが特に優れているものを特定しました。最終的にフロントホイールを4種類とリアホイールを3種類3Dプリントし、南ドイツのFriedrichshafen Windkanalで検証を行いました。
大容量な造形が可能なForm 3Lでは、各セクションに使用されるスポーク穴の数に応じて、自転車のホイールを5つまたは6つのセクションに分けてプリントでき、ビルドプラットフォームには一度に4つのリムセクションを納めることができます。二次硬化と後処理を施した3Dプリント製部品をエポキシ樹脂で接着し、ハブ、スポーク、タイヤをすべて組み合わせた機能確認用試作が完成です。
Grey Proレジンの使用についてPatrick Brown氏は、3Dプリント製のホイールは「実製品より若干柔らかいものの、炭素繊維製ホイールセットの張力の約65%を受けることができます。非常にまっすぐかつ正確に作ることができるので、風洞試験で使用するには十分です」と言います。
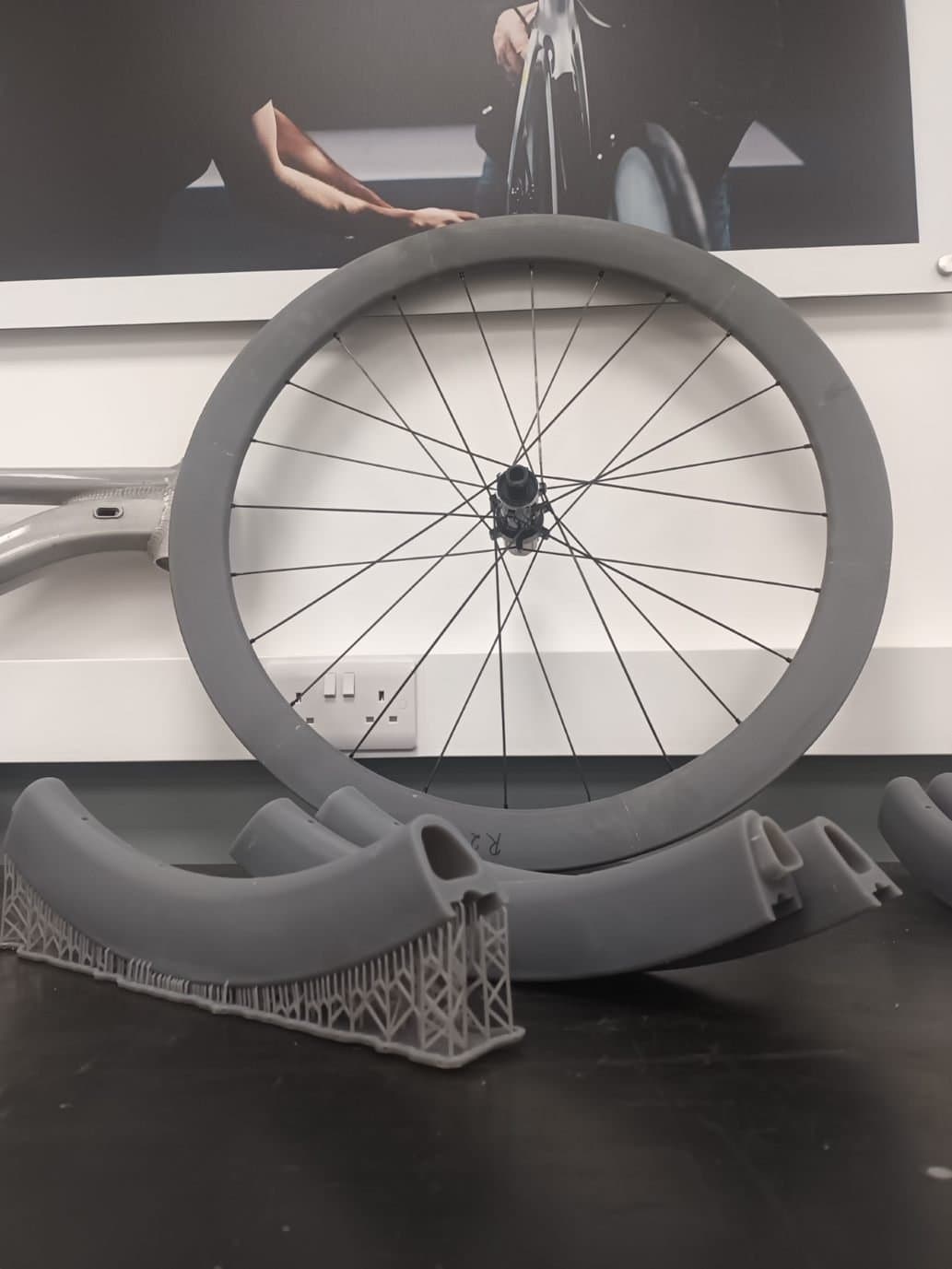
Grey Proレジンは炭素繊維製ホイールセットの張力を約65%受けることができ、試作品用の材料として最適。
Hunt Bike Wheelsは以前、さまざまなホイールセクションの3Dプリントをサードパーティのサービスプロバイダーに依頼していましたが、これには多くの課題がありました。まず、エンジニアは最終的なホイールプロファイルを2~3か月前に送っておかなければならず、そのために工程が遅れたり、変更が発生した場合にも柔軟な対応ができません。実際、Form 3Lを導入した後、直近のプロジェクトでは「[終業時間]直前に最後のプリントを終えることができ」直前まで試作・検証を行えたとBrown氏は言います。また、外注した部品にはタイヤに空気を入れる時に耐えられるほどの強度がなく、中には亀裂が入ってしまう部品もあり、検証には適していませんでした。
「今ではより長時間シミュレーションを行い、新しいプロファイルを開発し続けることができます。社内でこうやって柔軟な対応ができることが、大きなメリットになっています」
Hunt Bike Wheels デザインエンジニア、Patrick Brown氏
「タイヤがホイール上で正しい形状になるまで空気を入れ続ける必要があります。3Dプリント製の部品には、形状の正確性だけでなく、全体のエアロダイナミクスが適切になるよう十分な強度が備わっていることが重要なんです」開発工程で求められるこういった重要な要件も、Grey Proレジンなら満たすことができます。Grey Proレジンは形状的な精度が非常に優れているだけでなく、空気を入れたタイヤから加わる最大3.5バールもの圧力にも耐えられる強度を備えています。Brown氏はまた、エアロダイナミクスの検証時にはGrey Proレジンが持つ優れた表面品質が重要な要素になったことも強調しました。
「[風洞では]ローラーの上を走らせるので、ホイールは時速45kmで回転することになります」
Hunt Bike Wheels デザインエンジニア、Patrick Brown氏
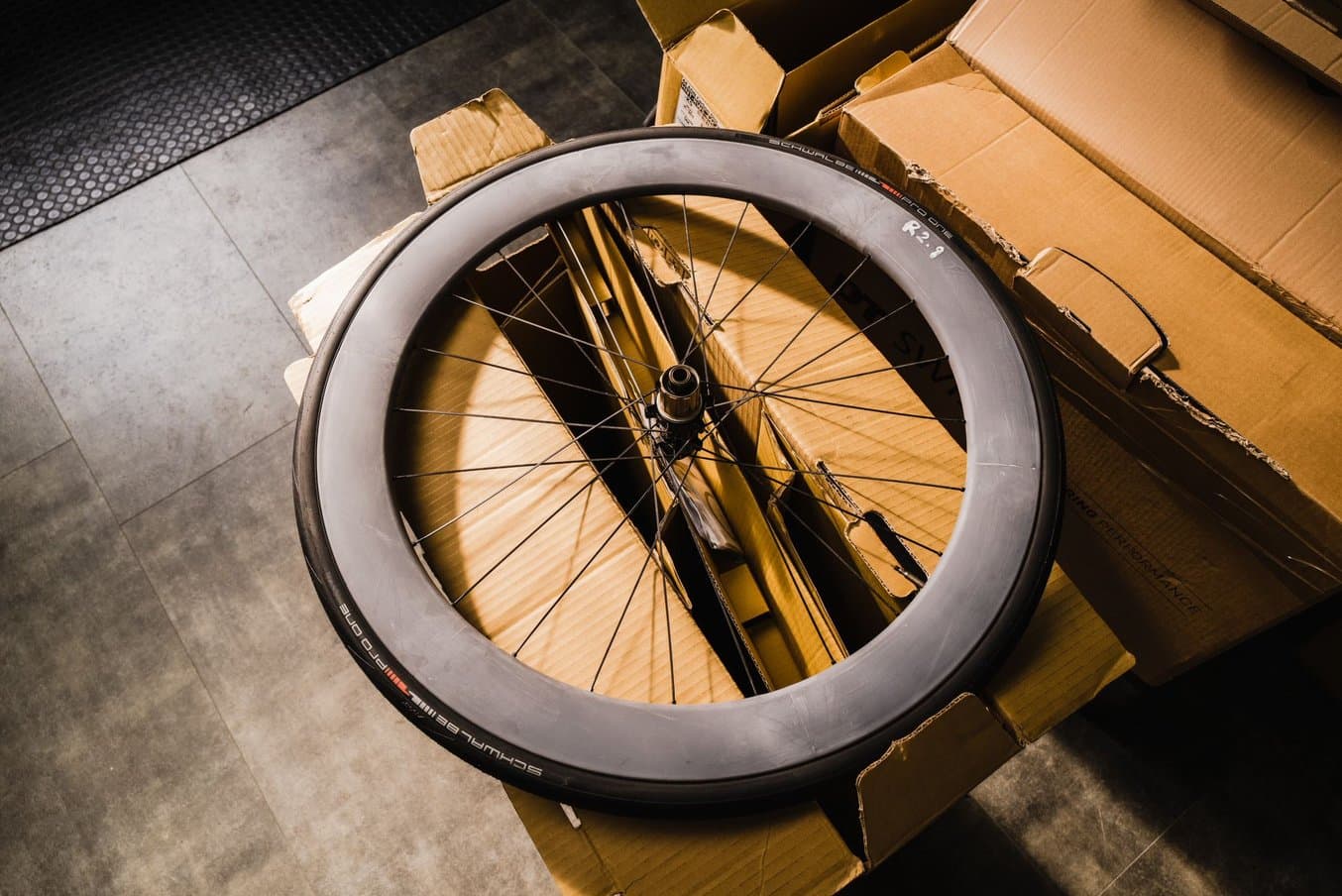
エアロダイナミクス検証ではGrey Proレジンの優れた表面品質が鍵に。
3Dプリントによる内製が可能なことで、エンジニアリングチームはコストを削減しながらも、試作・検証工程をこれまでより多く繰り返すことができます。外注していた時は、Hunt Bikes Wheelsはリムの試作品を1つ製作するのに約2000ポンドを費やしていました。Form 3Lを導入した今は、このコストを90%削減でき約200ポンドにまで下げることができました。
「これまでより多くのホイールを風洞に持ち込めるようになり、より広範なCFD解析が可能になりました。そのおかげで通常なら試作・検証を3〜4サイクル繰り返して得られる最適な設計を、すぐに割り出せます。今では製品開発のたびに、最初のリリースで既に優れた製品ができるという自信があります」とHicks氏は言います。
Form 3Lは現在、The Rider Firmが競合他社をリードし続けるビジネスモデルの重要な役割を担っています。Hicks氏は、「試作品を賢く製作し無駄のない事業運営を行うことで、大企業の製品と同等のエアロダイナミクス性能を備えたホイールを、半分の価格で提供できます」と語ります。
Privateer Bikes:自転車全体のフレーム製作とラピッドプトタイピングで限界に挑戦
Privateer Bikesでは、自転車全体のフレームからフレームのプロテクターに至るまで、さまざまな試作品の製作にForm 3Lを活用しています。
新しい自転車の開発に取り組むPrivateer Bikesのエンジニアリングチームは、自転車フレーム全体やフレームの複雑な箇所をそれぞれ異なるサイズで3Dプリントしました。これにより、ベアリングやサスペンション・フォークをフレームに押し込むなどしてコンポーネントを取り付け、製造可能な状態を維持しさまざまな大きさのフレームでクリアランスのダブルチェックが行えるようになりました。「クリアランスや組立方法、コンポーネントのフィット感、サスペンションが動いたときに何かとぶつかる可能性などをチェックできます」
さらに、フレーム全体を3Dプリントすることで、社内のグラフィックデザイナーがスプレーで塗装をしてアートワークのコンセプトを試したり、新作自転車のデカールを考えたりすることができます。フレームは、Grey Proレジンを使って小型の部品を複数3Dプリントした後、組立・接着します。組立と部品の接着が完了した自転車はかなりの圧力にも耐えられます。「それなりに手荒く扱っても問題ありません。
色々なことを試せるので、3Dプリントは非常に重宝しています。マーケティングチームにとっても、製品を実際に目で確認できるというのがいいですね。デザインについて話す場合、その場で一緒に確認できる試作品があるというだけで、コミュニケーションが格段に捗ります」とHicks氏は言います。
Hicks氏はまた、Form 3Lは特に自転車のカスタムフレームプロテクターの試作品製作に役立っていると言います。マウンテンバイクの場合、チェーンがチェーンステーにぶつかることが多く、うるさいだけでなくフレームを痛める可能性があることが難点でした。そこで同社は、チェーンステーに貼り付けっ可能なゴム製のフレームプロテクターを開発しました。
同社にはこの種のパーツを試作する設備がないため、通常であれば台湾のサプライヤーに設計を送って金型を製作してもらい、実製品のサンプルを送ってもらう必要がありました。これだけのプロセスですが、製作期間は通常3~4カ月ほど、費用は$3,000〜$4,000ほどかかります。このプロセスを辿っていた場合、設計変更のたびに新しい金型製作の費用がかかるため、設計の微調整や試作・検証の反復による設計の最適化は難しかったでしょう。
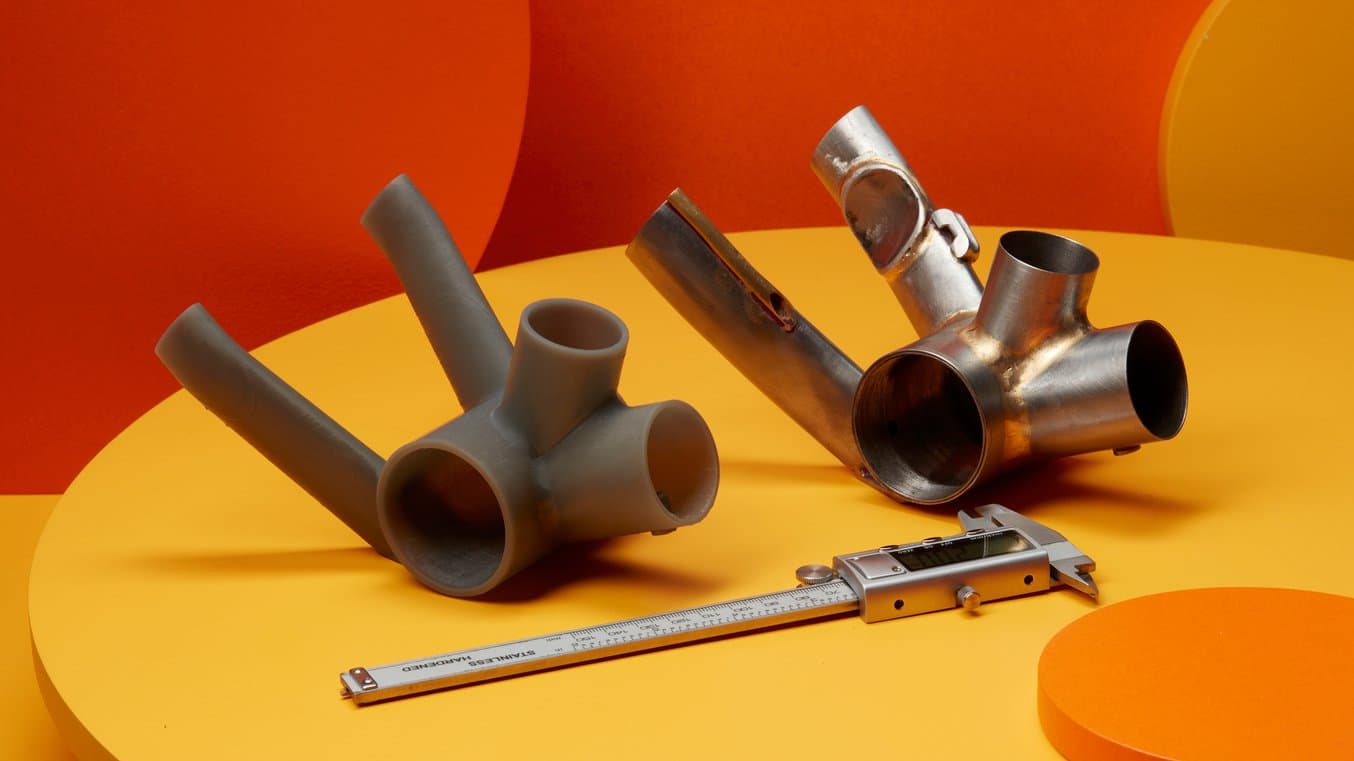
ラピッドプロトタイピング:適切な工程と材料の選定
本ウェビナーでは、コンセプトモデルや機能確認用試作をこれまでにないスピードで製作し、実際の使用環境に合わせた試験を行い、その結果に応じて設計を迅速に修正する方法をご紹介します。
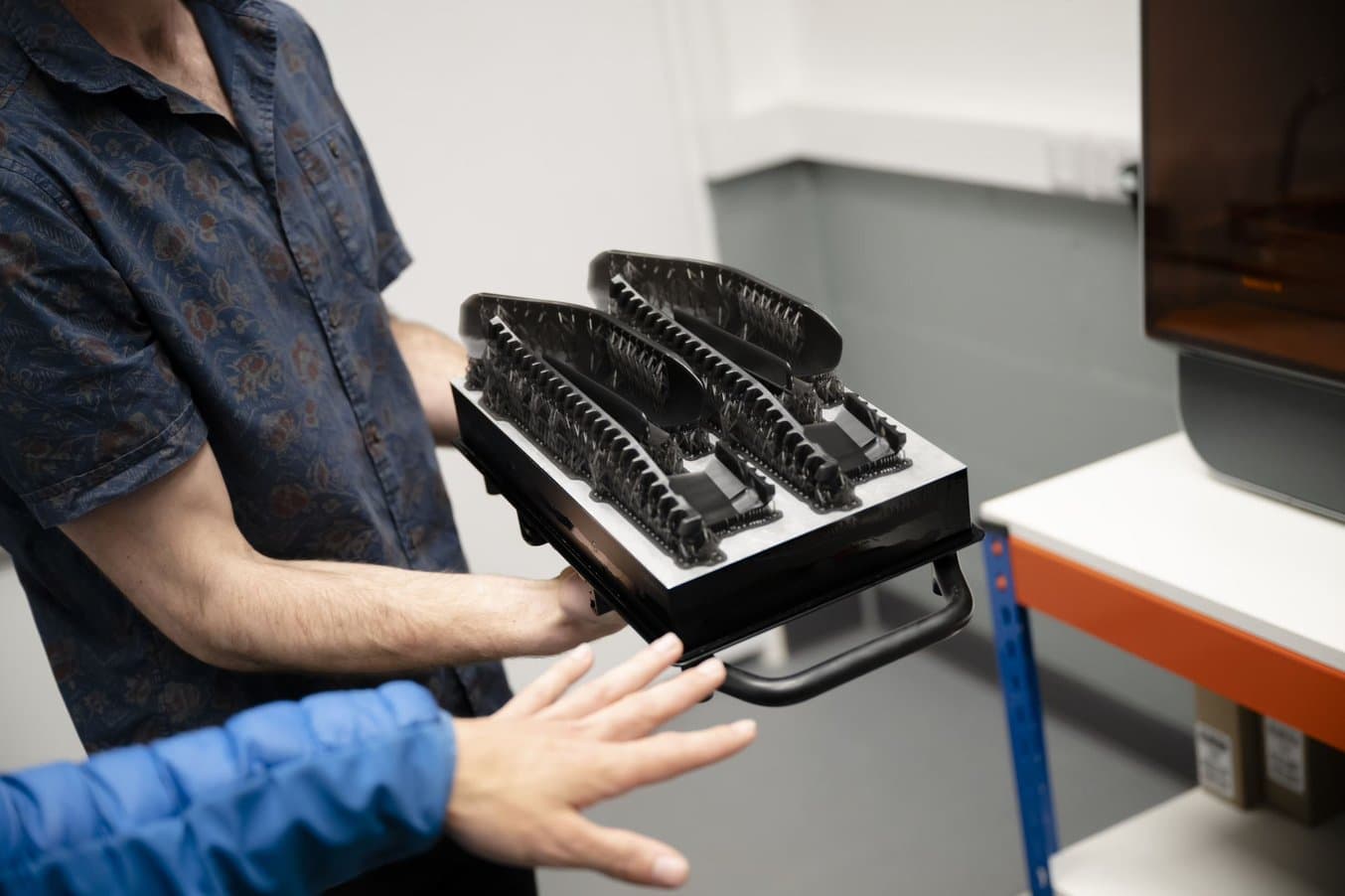
Form 3Lは、Flexible 80Aレジンを使ったフレームプロテクターの試作品製作に最適な3Dプリンタ。
3Dプリントにより、Privateer Bikesのエンジニアは3〜4種類のデザインで試作品を高速製作できます。「3Dプリントなら、設計変更をしてもほとんどコストがかかりません。事前に設計を確定できるので、製造用ファイルをメーカーに送ったらすぐに製造を開始できます」と言うHicks氏は、プロジェクトの期間にして6ヶ月、金型製作費用にして$4,000〜$5,000を削減できたとも付け加えます。
「事前に設計を確定できるので、製造用ファイルをメーカーに送ったらすぐに製造を開始できます」
Privateer Bikes 開発エンジニア、Dan Hicks氏
同社がこの用途に選んだFlexible 80Aレジンは、「デュロメーターがちょうど良く」自転車に直接貼り付けて検証をする機能確認用試作として最適でした。同社は製作したプロテクターを数ヶ月間自転車に装着して検証を行い、チェーンが当たる場所や音が出る場所をチェックし、その結果に基づいて設計に改良を加えました。
「メーカー向けにたくさんの設計を考えました。金型の分割線やそれがどう機能するかを考える際に、実際に目で見て確認できる方がずっと簡単だからです」
Privateer Bikes 開発エンジニア、Dan Hicks氏
3Dプリントでトレンドの変化にも迅速に対応
「自転車の用途は人によって違いますから、2年後にどんな使い方がされているのかは想像できません。でも、今では変わりゆくトレンドに迅速に対応でき、新しいことにも挑戦できるという自信があります」
Privateer Bikes 開発エンジニア、Dan Hicks氏
The Rider Firmは近い将来、E-バイクやそのコンポーネントの開発にも力を入れたいと考えています。こういった自転車の設計はさらに複雑で、Hicks氏は「装着するコンポーネントが増えれば増えるほど製造も難しくなる」としながらも、3Dプリントがあればこういったセットアップの試作品も製作できるだろうと述べています。
「用途は人によって違う」という自転車のトレンドが今後どう変わっていくのか。The Rider FirmのチームはForm 3Lを武器に、イノベーションを推進しながら変化するトレンドにもいち早く対応する準備が整っています。