
金属鋳造は、依然として米国内だけでも16万人の雇用を生み出す500億ドル規模の産業でありながら、鋳物工場における生産量は10年前の半分以下にまで減少しています。生産量の減少は、安価な海外生産、金属の代替となる材料の性能向上、鋳造工程に求められる熟練技術者の減少など、様々な要因が複雑に絡み合っています。それでは、航空宇宙、自動車、エネルギーといった重工業メーカーはどのようにして金属部品を迅速かつ手頃な価格で調達しているのでしょうか?
今でもこういった業界向けに製品を供給し続けている鋳物工場は、新しい生産方法を取り入れ、新たな技術を試すことで変わらず繁栄を続けてきました。今回私たちは、Diversified Metalsmiths, Inc.のJohn Farr氏に、同社がどのように最新技術を既存の金属鋳造工程に取り入れ、コスト削減や製作期間の短縮を実現し、需要への反応を高めてきたのかについて、お話を伺いました。
Diversifiedでは、Formシリーズ SLA光造形3Dプリンタと新たに登場したClear Castレジンを活用し、これまでの鋳造工程を変更したり外注に依存したりすることなく、迅速かつ手頃な価格で鋳造に使う原型を内製しています。
「Form 3Lを購入した主な理由は、原型製作にかかるコストの違いです。Form 3Lと関連機器を償却した場合でさえ、現在受けている注文分は収支均衡となりますし、今後の注文にいたっては部品1点あたり200ドル以上も節約できる想定です。アクリル製の原型を作る場合も、SLA光造形でClear Castレジンを使って原型を作る場合も、鋳造前後の工程にほとんど違いがありません」
Diversified Metalsmiths 技術部長、John Farr氏
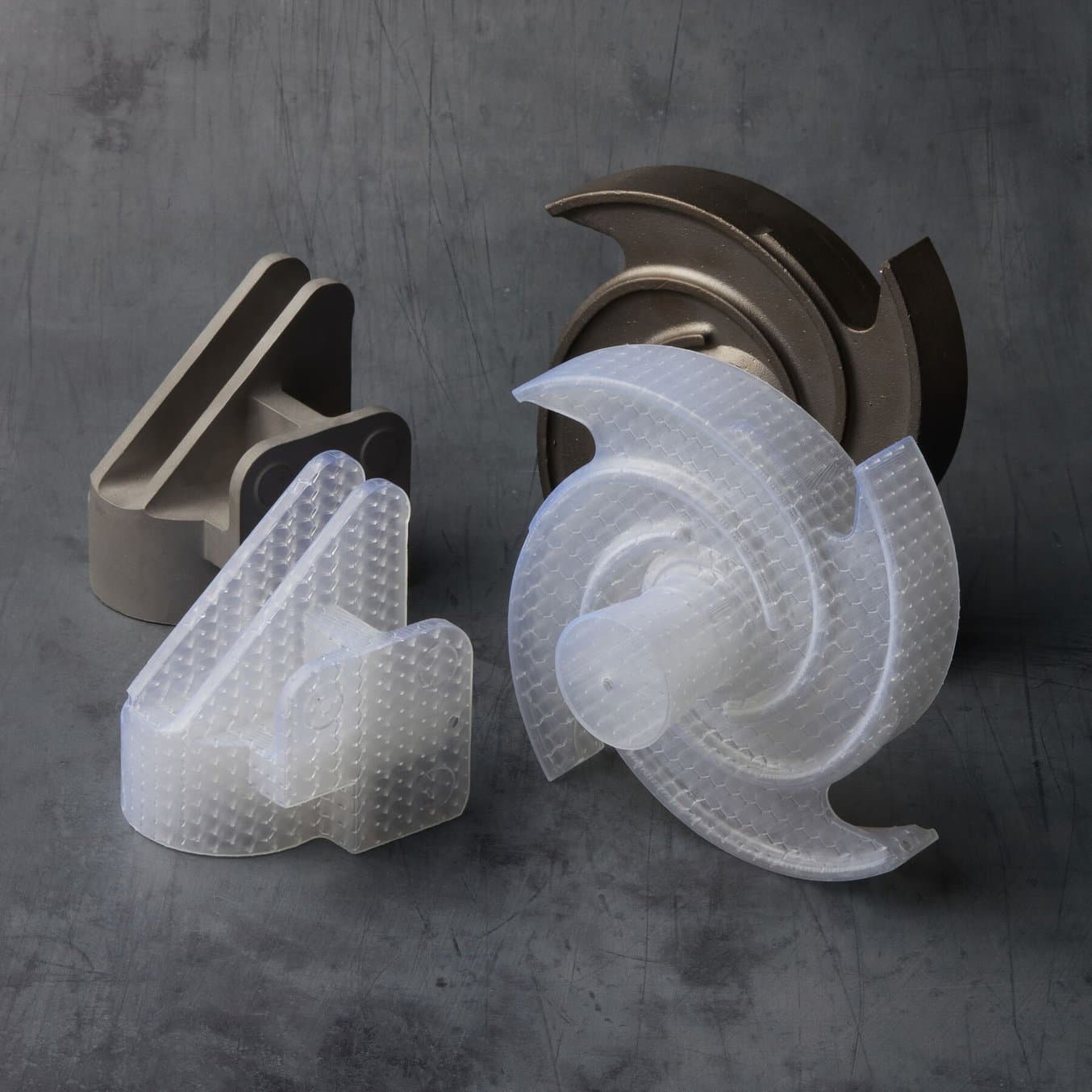
高精度・高効率な鋳造を実現 3Dプリントを活用した金属鋳造
本ウェビナーでは、実績ある複数の鋳物工場が、Formlabsの3Dプリンタで造形した3Dプリント製の原型を使って金属部品の鋳造に成功した方法を解説します。FormlabsのClear CastレジンやMaterialise Magicsのラティス構造生成ソフトウェアを従来の鋳造方法に組み入れることで、金属部品の品質を向上させながら、コストや製作期間を削減した方法をご覧いただけます。
Diversifiedの多様な顧客ベース
Diversifiedは大量生産工場というより「工房」のような存在ですが、こういった工場は実は珍しくありません。全国に点在する多くの小規模鋳物工場は、高精度かつ短納期で手に入る製品を求めてやってくる常連顧客のために、Diversifiedと同程度の規模で生産を行っています。「私たちの顧客は、いろいろな会社に見積を依頼するようなことはしません。私たちなら希望通りの製品を提供できると、すでにわかっているからです」とFarr氏は言います。
公差要件が厳しい金属部品を少量〜中量だけ、できるだけ短期間で製作してほしい。そんな時は、Diversifiedが頼りになります。同社の受注量の約70%は、インペラ、ポンプハウジング、バルブ、ドレン、グレート、工業用流体部品など、流体制御関連の部品です。残りの30%は、ドローンの製造に始まり自動車部品や医療機器、さらにはファインアートに至るまで、幅広い注文を受け付けています。
生産量は多少変動するものの、Diversifiedでは毎月約3トンもの鋳造品を生産しています。同社では生産する部品に応じて複数の鋳造炉を使用しており、大半は容量400ポンドの鋳造炉に収まる小型の製品ですが、大型部品の場合には1100ポンドの鋳造炉を使います。
Diversifiedがコンスタントに注文を受け付けている製品があります。それがチタン製のインペラで、年間受注量は100個です。しかし近年、チタンのコストが上昇したことで、同社は鋳造工程の他の部分でコストを削減する方法を探さなければならなくなりました。その解決策の一つが、SLA光造形3Dプリントを活用した原型の製作です。チタンのコスト上昇を相殺する手段として成功を収めてきました。
伝統工法と近代技術の融合
金属鋳造はある意味では非常に伝統的な産業といえ、その中核となる工程は何千年もの間ほとんど変わっていません。その一方で、鋳物工場は近代的な製造工法のパイオニアともいえます。Diversifiedでは、Farr氏率いるチームが3Dプリントテクノロジーをいち早く採用しました。「私たちはもう90年代半ばあたりから、何らかの形で3Dプリント製の原型を使ったインベストメント鋳造に携わってきたんですよ」とFarr氏は言います。
Diversifiedが最初に3Dプリントを活用したのは、ワックスを使った原型製作でした。これまで使っていたワックス原型(液体ワックスを中空構造の金型に流し込んで作るもの)の製作に、桁違いの時間とコストがかかるようになってしまったためです。あるプロジェクトでは4つの金型が必要でした。水溶性ワックスコア、チル化したワックス、チル化した水溶性ワックスを流し込む金型と、完全に組み立てた状態の金型です。こういった金型は全てオーダーメイドで、出来上がった金型にワックスを注入し、組み立て、そして(頻繁に)完璧にならない部分の再加工も必要でした。「インベストメント用のワックス型を1つ作るのにかかる工数は、膨大でした。ほぼ1日がかりの作業でしたから、長くは続かない作業だったんです」と、Farr氏は当時を振り返ります。
そこで、同社は従来の射出成形工程をそのまま置き換えるものとして、3D Systemsのワックス3Dプリンタとサーモジェット3Dプリンタを導入しました。その数年後、同社の顧客が新製品を紹介します。VoxelJetバインダージェットプリンタでPMMAポリマーを3Dプリントしたもので、それまで使用していたワックスプリンタよりもきれいに燃え尽き、寸法安定性も高いものでした。
業界のいたるところでコストが上昇し始めていたため、ポリマー3Dプリンターを持つ他の業者に外注することすら非常に高額になっていました。原型1つにつ300ドルものコストがかさむようになり、プリンタの導入となれば6桁以上の費用がかかります。
「価格の上昇とともに、他のものを探し始めなければなりませんでした。FDMとSLA光造形を検討し、水溶性のサポート材が使用できるという理由からまずはFDMプリンターを5台導入しました。当時は、それだけで十分だったんです」とFarr氏は言います。
しかし、ある顧客から年間100個のインペラ生産について打診があった時、Farr氏のチームは新たなソリューションを見つけるべく、大容量SLA光造形3DプリンタのForm 3Lについて再びFormlabsに問い合わせることになったのです。
Formlabs製品で金属鋳造を
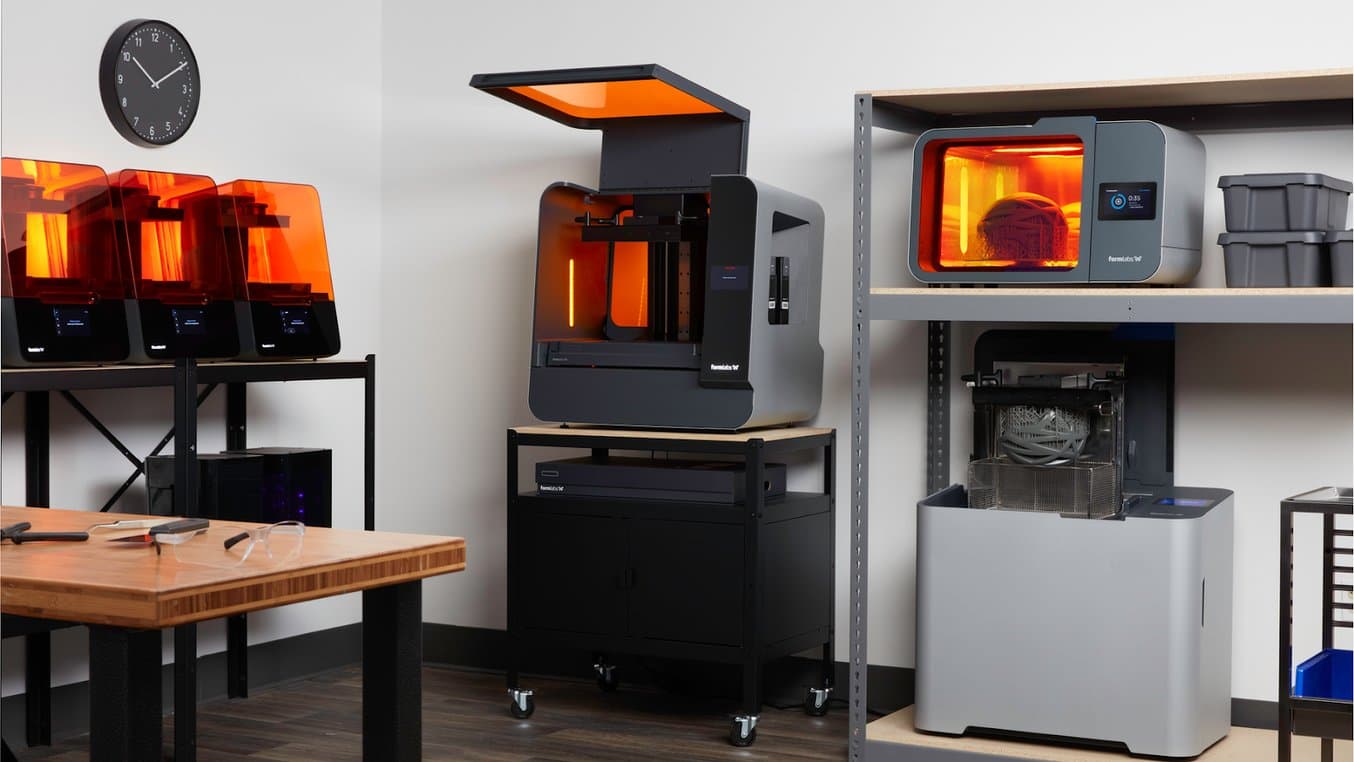
Form 3L、そして後処理装置のForm Wash LとForm Cure Lは、ホビイスト向けのどんなデスクトップサイズ3Dプリンタよりもフォームファクタが大きく、作業手順のわかりやすさと造形品質の高さが特徴。
Diversifiedが新しい3Dプリンタを探していた時、満たすべき要件がいくつかありました。まず、材料はきれいに燃え尽きること、そして信頼性が高く使いやすい製品でありながら、インペラを造形できるのに十分な容量があることでした。「Formlabsの製品とサポートの両方が、私たちにとって最適な選択肢だったんです。プリンタのフィット感と仕上がりの品質、ソフトウェア。どれをとっても同価格帯の他製品よりはるかに優れているように思えました」とFarr氏は言います。テストとしてFormlabsチームにサンプルパーツの造形を依頼した結果、Farr氏はForm 3LとClear Castレジンをすぐに既存工程に組み込めると確信します。これまでの焼成温度やスラリー配合、製品の設計を変える必要はありません。それだけではなく、Formlabsプリンタで造形する原型には直接湯口を追加できため、工程が若干改善したのです。
「Clear Castレジンで作った原型を、作業工程にそのままそのまま組み込むことができました。アクリル製の原型はできなかった湯口の直接プリントも可能になったことが、嬉しいですね」
Diversified Metalsmiths 技術部長、John Farr氏
ここまでで原型製作の工程は簡単に切り替え可能なことがわかりましたが、焼成工程の検証が残っていました。そこでもClear Castレジンは、外注していたアクリル製原型の代わりとして効果的に機能することを実証しました。「焼成工程も、アクリル製の時とほぼ変わりません。ほとんど同じように扱えるため、問題なく組み込めます」とFarr氏は言います。
現在、Diversifiedがインペラ用の3Dプリント製原型1つに支払うコストは、材料費と人件費で80ドル強です。外注に300ドルがかかっていた頃に比べ、同社は3Dプリントの活用事例を拡大し新しい用途を開発しながら、プリンタに投資した分のROIをすぐに達成できました。週に3回プリントするだけで、プリンタ本体の元を9カ月以内に回収することができています。
外注のアクリル製原型 | Clear Castレジンで内製した原型 | |
---|---|---|
コスト | $300 | $80 |
製作期間 | 2週間 | 24時間 |
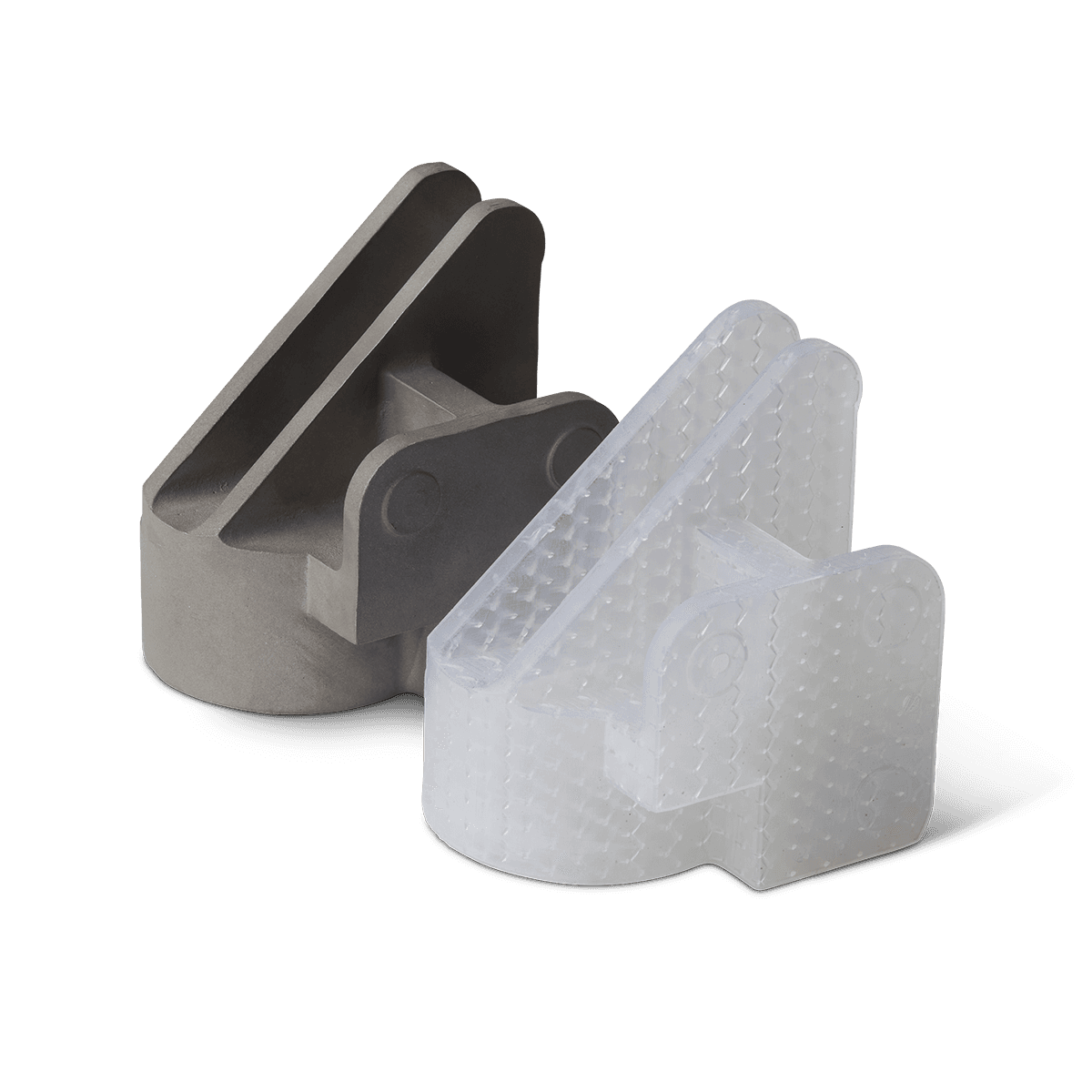
工業品質のインベストメント鋳造を3Dプリント製の原型で Formlabs Clear Castレジンの活用法
本技術資料では、実績ある複数の鋳物工場が、FormlabsのSLA光造形プリンタで造形した3Dプリント製の原型を使って金属部品の鋳造に成功した方法をご紹介します。
必要な時に、必要なだけ
インベストメント鋳造用の原型は壊さなければならないため、生産量が多い場合には全ての原型を3Dプリントすることが必ずしも最適な解決策とは限りません。しかし、Form 3LとClear Castレジンを最も有効活用できる生産量の「スイートスポット」があります。「顧客からこの部品を1000個欲しいと電話があったら、その時点で金型製作をします。ただ、そういう金型は3万ドルくらいする可能性があるので、大量に作らないとそのコストを正当化できません」とFarr氏は言います。
Form 3LやClear Castレジンのようなプリンタとレジンを社内に導入することで、全体的な工数を削減し、複雑な形状や寸法の製品であっても最初から失敗なく作ることができます。
「砂型ではインベストメント鋳造ほど正確なものは作れません。3Dプリント製の原型のようにほぼ完璧な形状が望ましいのは、事前準備や後処理の段階で作業時間を削減できるからです。後処理では他の部品を研磨する必要が出てくるかもしれませんから。3Dプリントを導入してからというもの、プリンタのボタンを押すだけで後は他の作業に集中でき、鋳造後の加工や手作業による処理も必要なくなったので、節約できた時間を考えると3Dプリント製原型のコストはすぐに元が取れます」と、Farr氏は話してくれました。
Clear Castレジンでプリントを始める
3Dプリントは、何十年にもわたってインベストメント鋳造の工程に組み込まれてきました。すべての状況に適しているわけではありませんが、材料科学と造形精度の進歩により、特定の作業ではより効果を発揮しやすいツールとなっています。
Formシリーズ SLA光造形3DプリンタとClear Castレジンの組み合わせなら、業界をリードする精度と灰が残らずきれいに燃え尽きる材料成分で、「セットしたら後はお任せ」な工程を実現できます。造形前の事前準備が少なく、造形後も研磨や手作業での加工の手間がかからない3Dプリント製原型は、既存工程を変更することなく、製造単価を下げながら生産現場に新たな可能性をもたらします。
Clear Castレジンを、ぜひ一度お試しください。3Dプリント製の原型を使用した金属部品のインベストメント鋳造については、以下から技術資料をダウンロードして詳細をご覧いただけます。