圧縮成形は、汎用的な製造プロセスとして大小問わず多数の製造会社で採用され、大型の航空機部品から小さな哺乳瓶のノズルまで、さまざまな部品を生産するために利用されています。
このガイドでは、圧縮成形の概要、メリット、その用途をご紹介しながら、このプロセスが試作品の製作から部品の大量生産まで、どの段階でも活用できる理由を探っていきます。
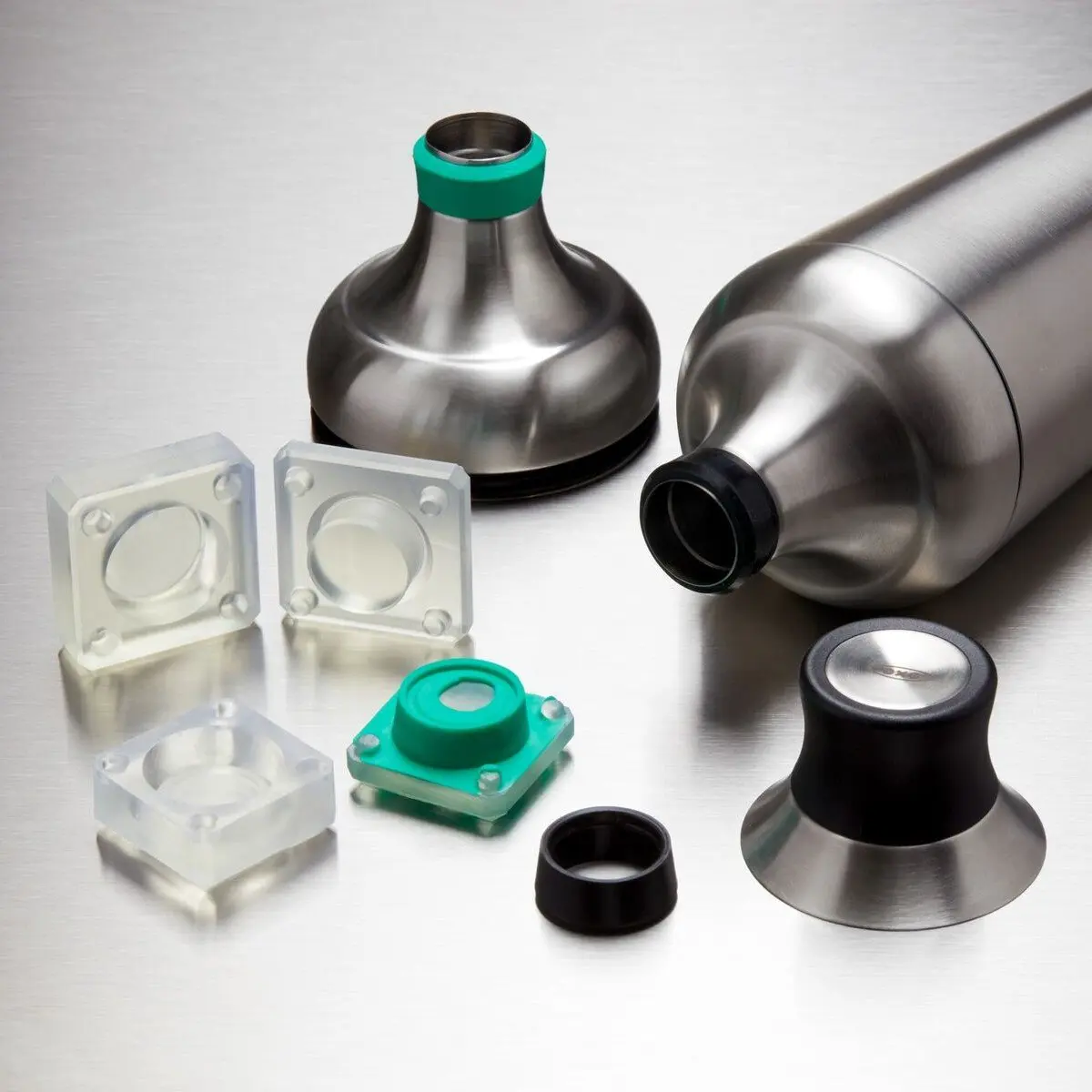
3Dプリント製の成形型でシリコン部品を生産
本技術資料では、成形型を設計する際のベストプラクティスや導入事例などを交えながら、3Dプリント製の成形型でシリコン部品を製造するための手順をご紹介します。
圧縮成形とは
圧縮成形とは、計量した材料を予熱し(この予熱済み材料は一般的に「チャージ」と呼ばれます)、加熱した金型の中に流し込んで加圧することで目的の形状に成形する製造手法です。
圧縮成形の仕組み
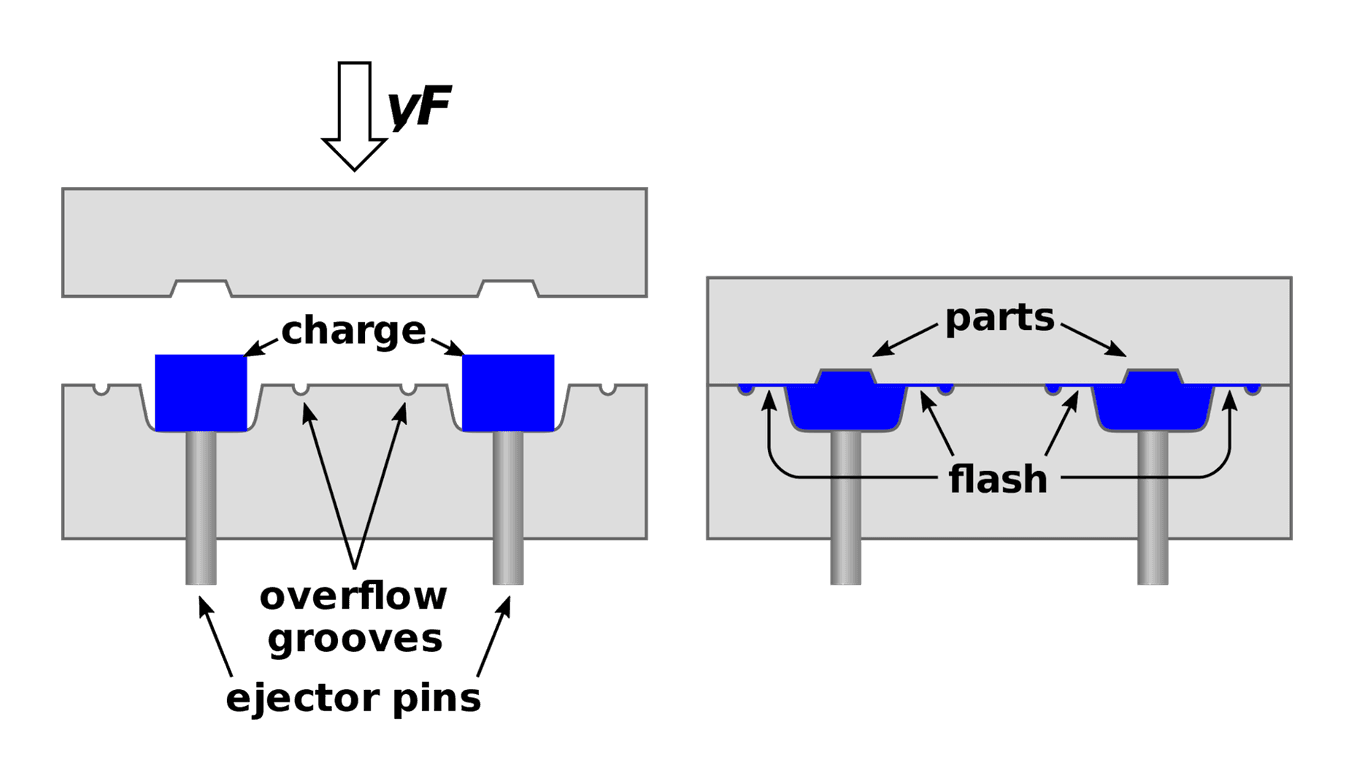
圧縮成形プロセスの概略図。(画像出典)
圧縮成形は次のような手順で進みます。
-
金型の製作:金型は、切削、ダイカスト、3Dプリントなど、さまざまな方法で製作できます。
-
機械のセットアップ:成形に使用する特定の機械や装置によって、金型の洗浄、加熱、その他様々なセットアップ工程が含まれます。
-
チャージの準備:使用する材料の種類を選び、適切な材料の量を決定します。チャージの量が多すぎると余分な材料が金型から溢れ出してバリとなり、後で手作業で切り取る必要が生じます。
-
チャージの配置:チャージを下型の中央に置きます。
-
圧縮:上型を閉じて圧力をかけ、材料を希望の形に成形します。多くのメーカーは、生産スピードを早めるために、圧縮プロセス中に熱を加えることで原材料を柔らかくします。
-
成形品の取り出し:完成品を取り出します。
-
成形品の洗浄:成形品の周りに残ったレジンのバリを手作業で切り落とすなどして取り除きます。また、最終的な組み立ての前に成形品の洗浄が必要な場合もあります。
圧縮成形 vs. 射出成形
圧縮成形と射出成形は非常によく似ていますが、1つ大きな違いがあります。圧縮成形ではチャージを包み込むようにして金型を閉じるのに対し、射出成形ではあらかじめ閉じた状態の金型のキャビティ内にチャージを流します。
現代のメーカーは圧縮成形と射出成形の両方を使用することが多いものの、製造部品の種類に応じて使い分けをしています。射出成形は一般に複雑な部品の製作に適しているのに対し、圧縮成形は比較的単純な形状の成形に適しています。例えば、押出成形技術では製造できない超大型の基本形状などです。
射出成形は圧縮成形よりもサイクルタイムが短いため、部品を大量生産する場合には射出成形のほうが速く、費用対効果も高くなります。しかし、圧縮成形は必要な圧力が比較的低く、金型製作コストが安くなることも多く材料の無駄も少ないため、高価な材料を取り扱う場合にはメリットとなります。
1つの目安としては、大量生産には射出成形が、小〜中規模の量の生産には圧縮成形が適していると考えるとよいでしょう。
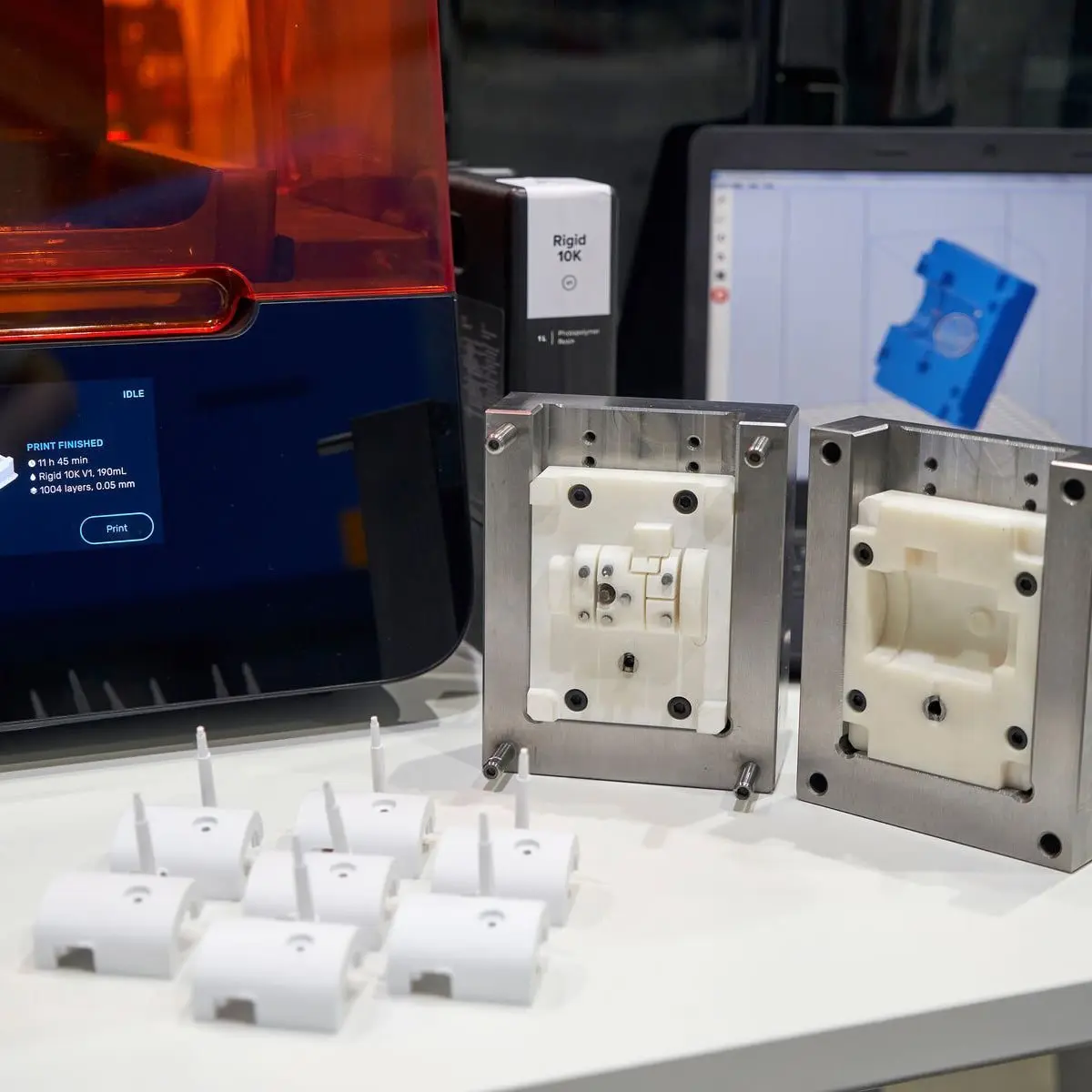
3Dプリントした金型を使った少量高速射出成形
FormlabsのWebサイトでは、3Dプリント製の型を使ってコストと時間を削減しながら射出成形を行う際のガイドライン、また実際にこの手法を導入しているBraskemやHolimaker、Novus Applicationsの事例を掲載した技術資料をダウンロードできます。
圧縮成形のメリットとデメリット
圧縮成形と射出成形の違いについてご紹介したところで、圧縮成形プロセス特有のメリットと制約事項についてさらに詳しく見ていきましょう。
費用対効果
形状が単純で、ほぼ平らな大きな部品を作る場合には、圧縮成形は最も費用対効果の高い製造手法となることが多いです。ただし、多少の曲面やくぼみのある設計は許容範囲内ですが、極端な角度や深絞りを圧縮成形で実現するのは難しい場合があります。圧力が低いため金型製作コストも比較的安く済み、製作した金型はたわみの心配や交換の必要なく長く使用できます。圧縮成形はサイクルタイムが長いため、それに伴うコストを相殺するには、複数のキャビティを持った金型を使って1サイクル内で複数の部品を生産します。
丈夫な部品を生産
圧縮成形では、フローマークやニットラインのない強固な部品を生産できます。圧縮成形品の構造安定性は極めて高く、複合材料を使った部品の製造にも使用されていることから、耐久性や耐食性に優れた部品・製品を簡単に生産できます。
設計の自由度
圧縮成形は、エンジニアや製品開発者にとっても嬉しい製造方法です。例えば、低コストの圧縮成形用金型を利用したプロトタイピングが可能です。コンピュータ支援設計(CAD)ソフトウェアで簡単な圧縮成形用金型を設計し、3Dプリントすることで、シンプルな卓上万力があれば様々な材料を使った成形が可能です。この記事の後半では、OXOによるプロトタイピングの実例をご紹介します。
制約事項
圧縮成形には多数のメリットがある一方、いくつかの制約事項もあります。例えば、急な角度のある部品や、ディテールが重視されるような複雑な部品を製造する場合には、圧縮成形は向いていません。また、1回のサイクルタイムが数分に及ぶこともあり、大量生産向けの成形手法に比べて生産スピードが遅くなります。一方の射出成形では、サイクルタイムがほんの数秒程度であることが一般的です。
さらに、圧縮成形に伴う人件費は比較的高くなることがあります。これは、サイクルタイムが遅い分、作業時間が長くなるためです。また、圧縮成形品からバリを手作業で取り除く必要があるため、時間かかるほか廃棄物が生じます。このような制約事項があるものの、圧縮成形は、私たちが普段何気なく使っている様々な製品の製造に用いられる重要な製造方法です。
圧縮成形の用途
圧縮成形の用途は多岐にわたります。以下は、私たちが普段接することの多い多数の部品や製品のうち、圧縮成形で製造された部品が含まれるものの例です。
-
車両部品:自動車やトラクターなどの車両に搭載する大型部品やパネルは圧縮成形で製造されています。車両の内装のプラスチック部品やエンジン部品の多くも、圧縮成形で作られている場合があります。
-
コンピュータおよびゲーム機器:ビデオゲームのコントローラーやキーパッドなどの部品は、圧縮成形で作られている場合があります。
-
キッチン用品:キッチンツール、調理器具、キッチン器具の多くには圧縮成形で作られた部品が搭載されています。ボール、カップ、プレートなどの食器類(特にメラミン食器)は、圧縮成形で製造されることが多い品物です。
-
電子部品:電気ソケット、スイッチ、保護プレート、計測器などの製造には、圧縮成形が用いられることが多くあります。
-
医療機器および歯科機器の部品:医療業界で使用されるプラスチック部品やシリコン部品の多くは、圧縮成形で製造されています。例えば、注射器のストッパーや人工呼吸器のマスクがその一例です。
圧縮成形を用いて製造されるキッチン用品
圧縮成形機の種類
圧縮成形機には、大型の産業用機械からDIY用の小型のものまで様々なサイズがあり、製造される部品と同じように、圧縮成形機自体も機械を作るエンジニアや設計者の数だけ存在します。次の項目で、いくつかの例をご紹介します。
産業用油圧圧縮成形機
大型の産業用圧縮成形機は、大型の商業部品の製造に最適です。
油圧リフトシステムにより、大型で均一な部品を製造するのに必要な高い圧力が実現できるうえ、作業者は離れた作業版から工程を監視できます。
卓上プレス機
小型の卓上型圧縮機は、小型から中型程度の部品や製品の製造に最適です。Beckwoodの卓上プレス機は、大型の産業用圧縮成形機よりも小型ながら大量生産に適しています。アクセスポイントが複数あるため、成形品の取り出しやバリの除去が簡単に行える柔軟性があるほか、設置面積が小さいため、そこまで大きくない倉庫や生産施設でも導入が容易です。
冷間(ヒートレス)圧縮成形機
圧縮成形では、熱を加えての製造も、熱を加えない製造も可能で、圧縮成形機のサイズに関わらずどちらの製法も選ぶことができます。メーカーによっては、冷間圧縮機を使用しながら、実際に使用するチャージや原材料を予熱したうえで金型に配置することもあります。特定のタイミングで熱を加えることで、完成品の硬化プロセスを制御し、生産サイクルを短縮できます。
湿式圧縮成形機
湿式圧縮成形機は、レジン、エポキシなどの液状物質と固形繊維を結合することで成形します。
耐久性のある自動車部品やコンポーネントの製造には、湿式圧縮成形が用いられることが一般的で、BMWなどの大手企業も、湿式圧縮成形機を生産ラインに取り入れています。
DIY用圧縮成形装置
圧縮設計は、家庭用途の設計やDIYにも適しています。ウレタンなどのやわらかい材料は、比較的低圧で圧縮成形でき、金型の形状が複雑であっても、3DプリンタとCADソフトウェアを使えば簡単に製造できます。小規模なプロジェクトの場合も、シンプルな卓上クランプやレバーシステムを使うことで必要な圧力を加えることができます。
圧縮成形用の材料
圧縮成形には熱可塑性・熱硬化性材料のどちらも利用できます。熱可塑性材料とは、加熱されるとやわらかくなり、冷えると硬くなるプラスチックの一種です。熱可塑性材料は、何度も加熱したり冷やしたり(または形を変えたり)できます。
一方の熱硬化性材料は、加熱されると不可逆的に硬化するプラスチックやポリマーのことで、一度だけしか成形できません。熱硬化性材料は、圧縮成形プロセスにより元に戻したりやり直したりできないような形で化学的に変化します。
圧縮成形で広く使われる材料には、以下などがあります。
-
フタル酸ジアリル(DAP)
-
エポキシ
-
高密度ポリエチレン(HDPE)
-
メラミン
-
ポリアミドイミド(PAI)
-
ポリエーテルエーテルケトン(PEEK)
-
ポリウレタン(PU)
-
ポリフェニレンサルファイド(PPS)
-
フェノール樹脂(PF)
-
ポリテトラフルオロエチレン(PTFE)
-
シリコン
-
尿素樹脂(UF)
-
ウレタン
圧縮成形型を作る方法
圧縮成形する材料やチャージに応じて、金型を作る方法は複数あります。重要なのは、金型が圧縮成形プロセスに耐えられることです。そのため、熱を加える場合は、急激な温度変化や圧縮過程でかけられる高圧力にも耐えられる金型を製作する必要があります。
ダイカスト
ダイカストは、圧縮成形やその他の製造手段向けに金型を作る最も一般的な方法です。他の製造手段よりも低コストで耐久性のある金属部品を製作できることが人気の理由です。なお、ダイカスト用のダイはCNC加工で作られることが多く、この2つの製造手法はよく組み合わせて使用されます。
CNC加工
よりディテールの凝った圧縮成形型には、CNC加工が最適です。CNC加工はコンピュータ化されているためエンジニアは設計をコントロールしやすくなりますが、金型製作が高額になることがあります。メーカーによっては、ダイカストとCNC加工を組み合わせることでより費用対効果の高い金型を製造しています。
3Dプリント
圧縮成形用の金型は3Dプリントで製作することも可能です。小型部品を試作する場合であれば、3Dプリントは最も安価かつ高速な金型製作手段となり得ます。試作品をテストした後CADソフトウェアで設計を微調整し、再度試作を行ってまた検証するという反復検証サイクルも遥かに高速に回すことができます。3Dプリント製の圧縮成形金型は主に、熱を使わない圧縮成形用金型に使用されます。
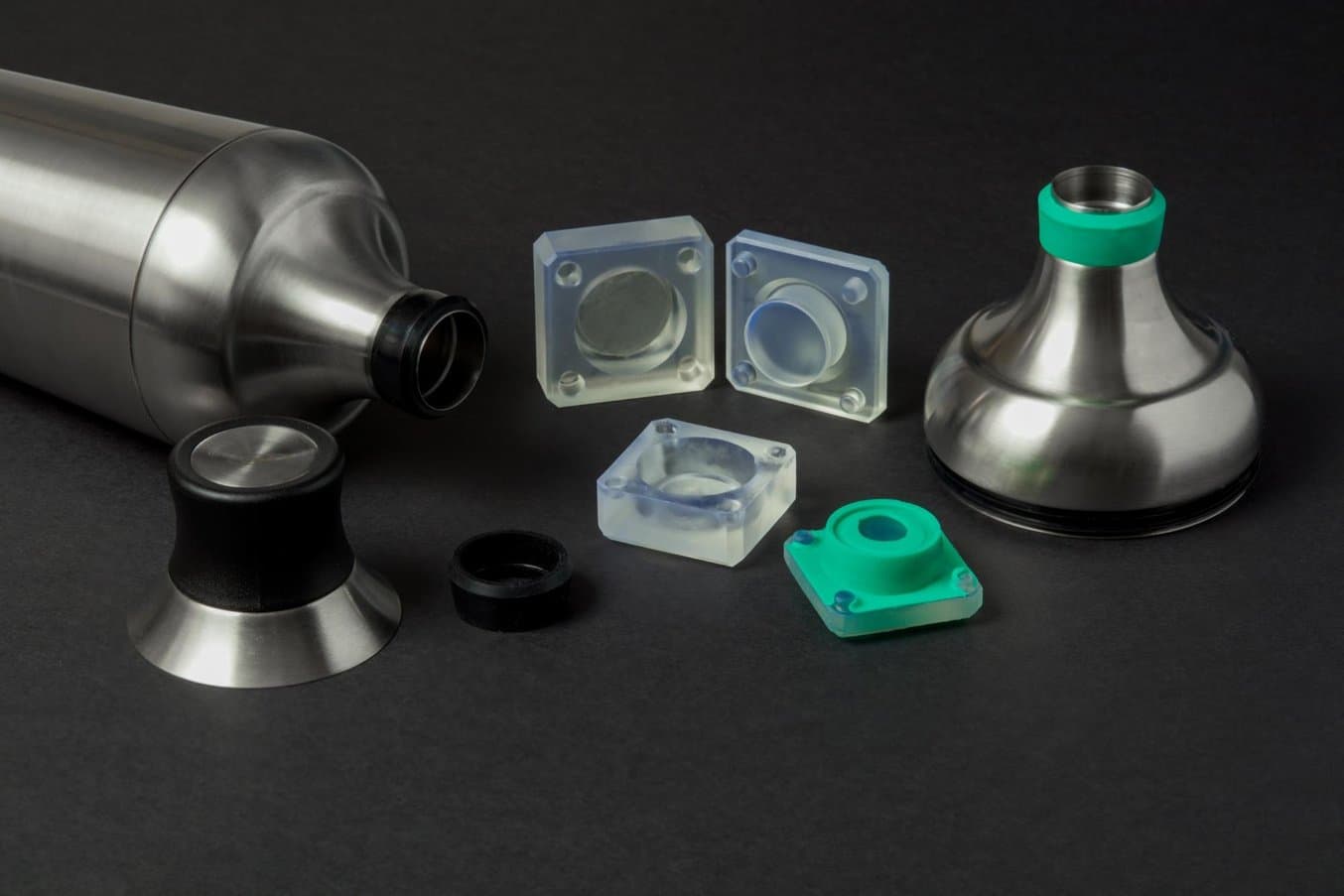
圧縮成形用の金型も3Dプリントなら高速かつ安価に製作できる。
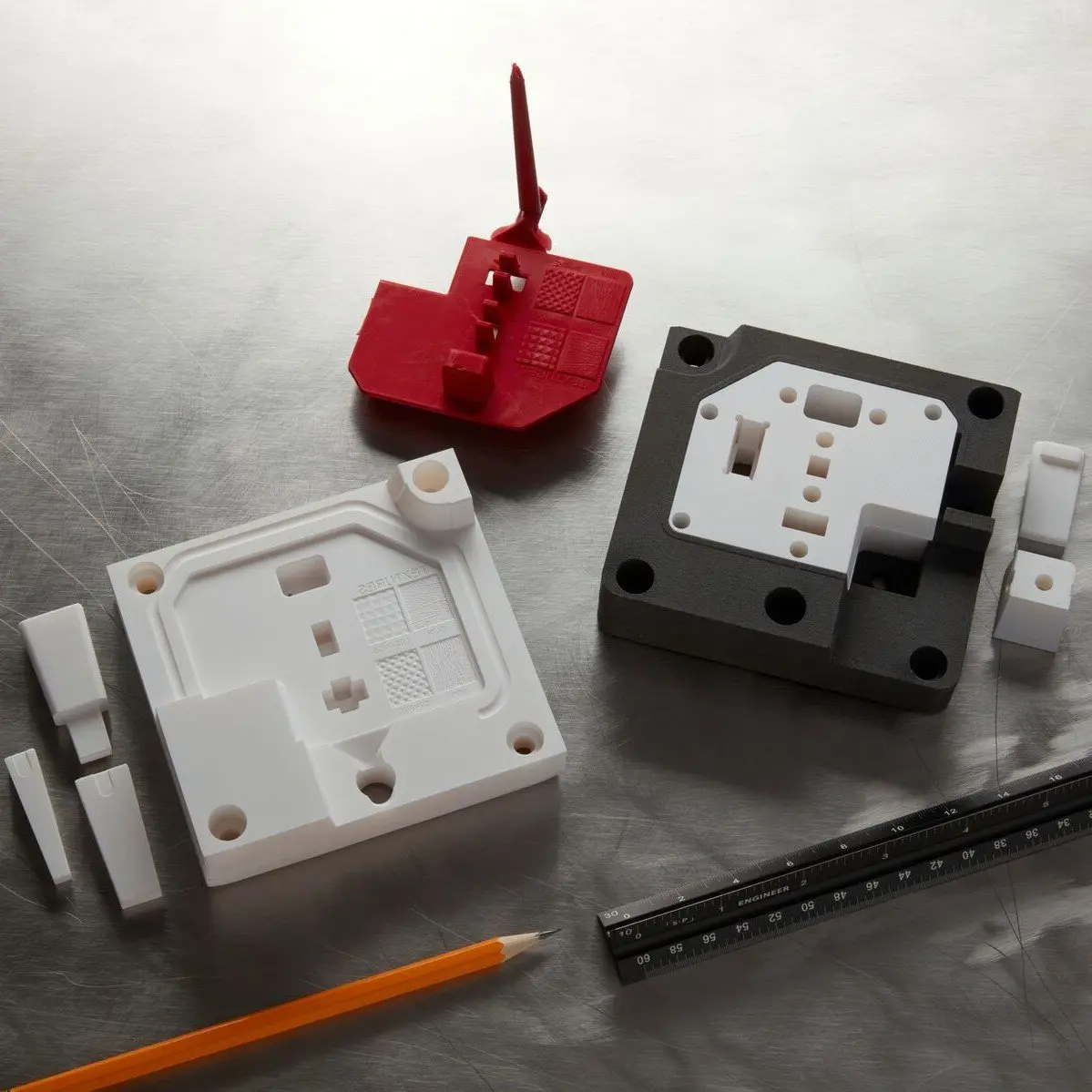
プロトタイピングに圧縮成形を使用するOXOの事例
OXOはアメリカを拠点とするメーカーで、アイコニックなキッチン用品を含め、人間工学に基づく実用的な家庭用品を製造しています。同社の製品開発担当者はSLA光造形3Dプリントを活用して形状や機能のプロトタイピングを行っていますが、ガスケットなどのゴム製部品のプロトタイピングにはハイブリッド方式が欠かせません。
OXOのエンジニアは、カクテルシェーカーの部品の間を密閉するガスケットの機能確認用試作を必要としていました。数々のシリコン材料を検証した後、圧縮成形した2パーツシリコンパテ「Castaldo Quick-Sil」が実製品としてのガスケットに似た密閉式試作品の製造に最適と判断しました。実際、この圧縮成形の試作品は、ガスケット製造に使われる手法と金型設計をよく表しています。
同社エンジニアは、Formlabs SLA光造形3Dプリンタで、Clearレジンを使って金型を作りました。金型の洗浄と硬化が終わると、圧縮成形に向けた準備が行われました。金型の内部表面に離型剤が塗布し、シリコンパテを下型に流し込みます。

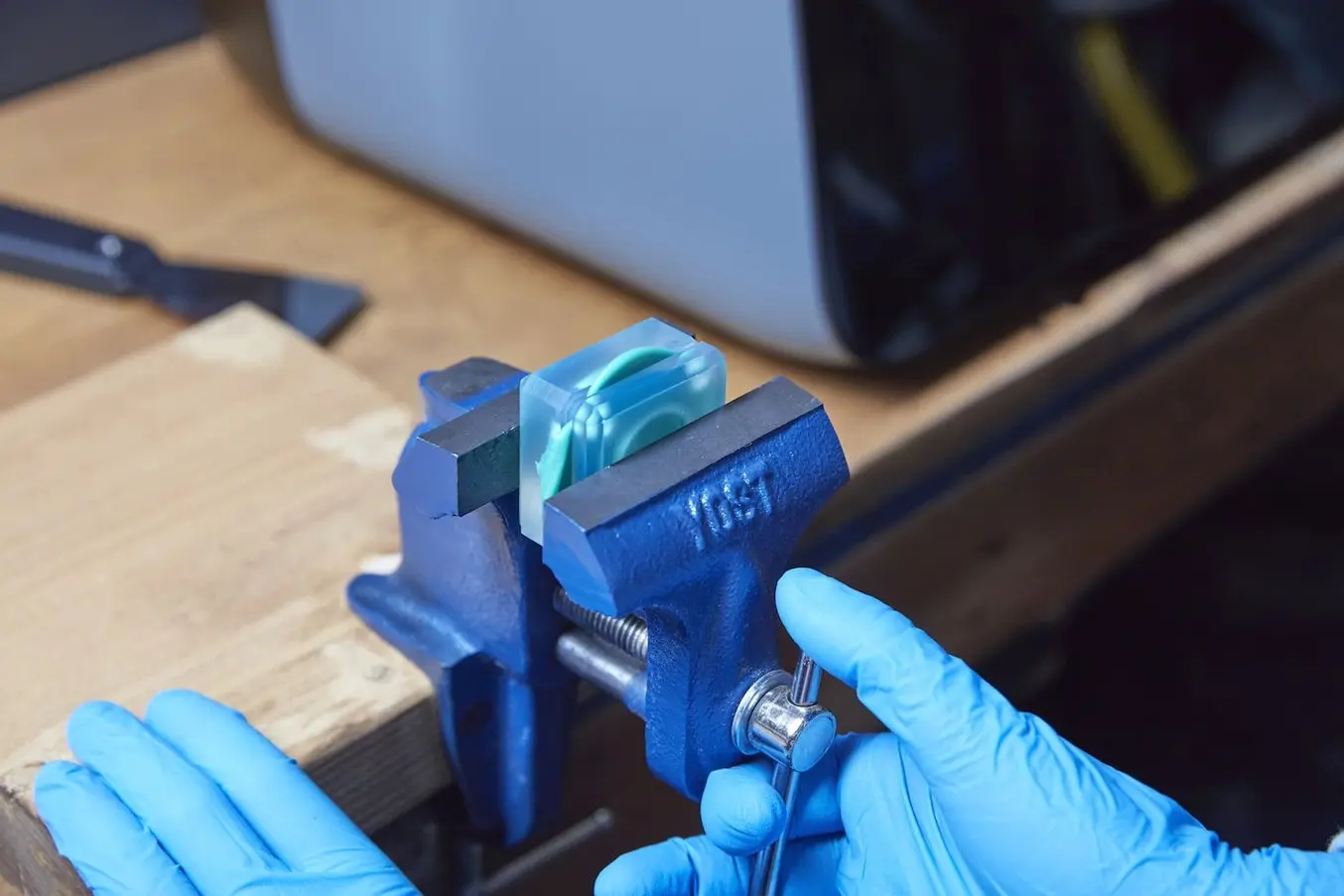
左:3Dプリントした金型にシリコンパテを流し込むところ。右:卓上万力で圧縮される金型。
その後、上型を閉じ、卓上万力で2つの型を閉じることで必要な圧力をかけます。部品が完全に硬化したら金型から取り出し、トリミングを行います。技術資料のステップごとの手順をご参照いただくと、目的に応じて簡単にこのプロセスを応用できます。
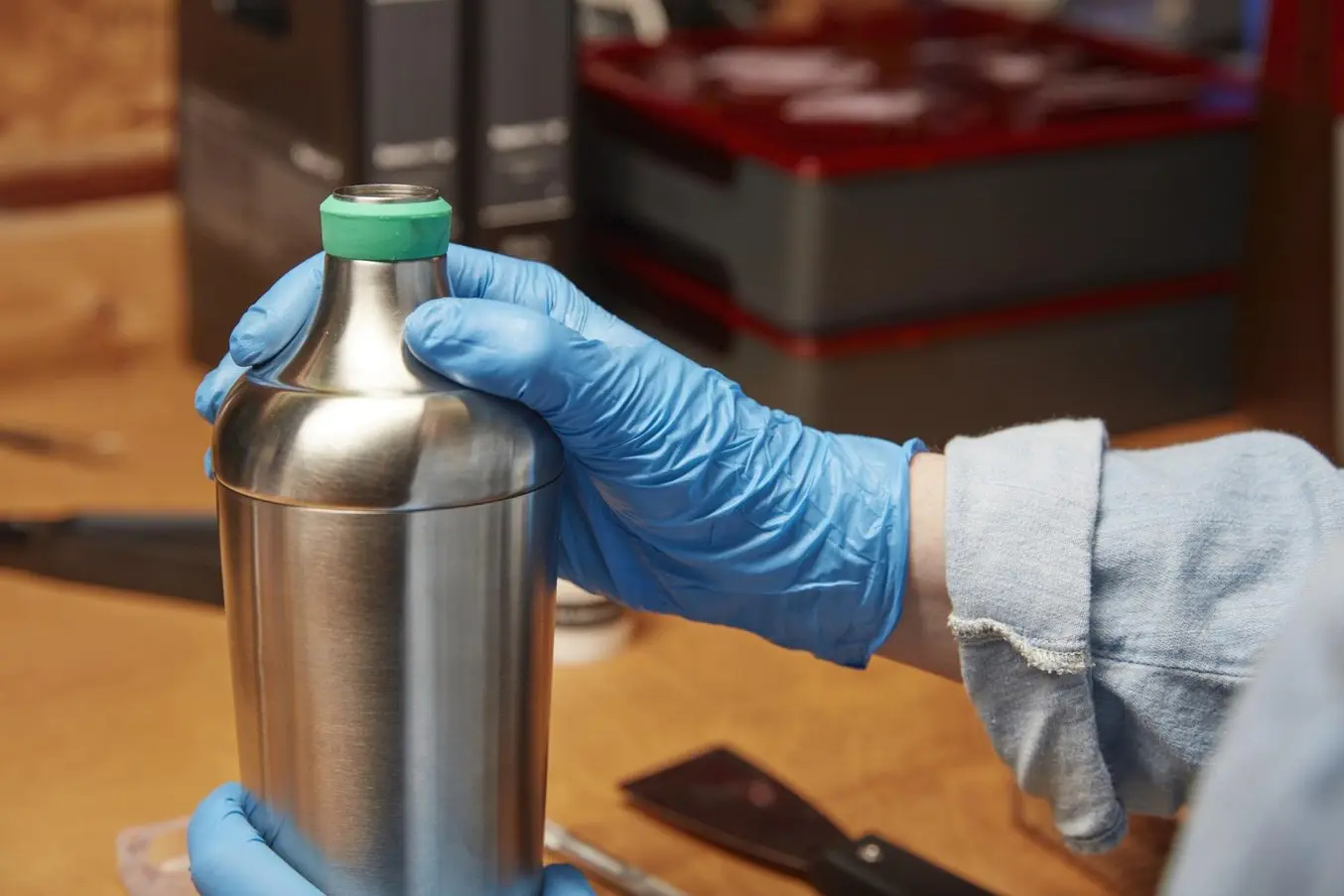
カクテルシェーカーのガスケットの機能確認用試作
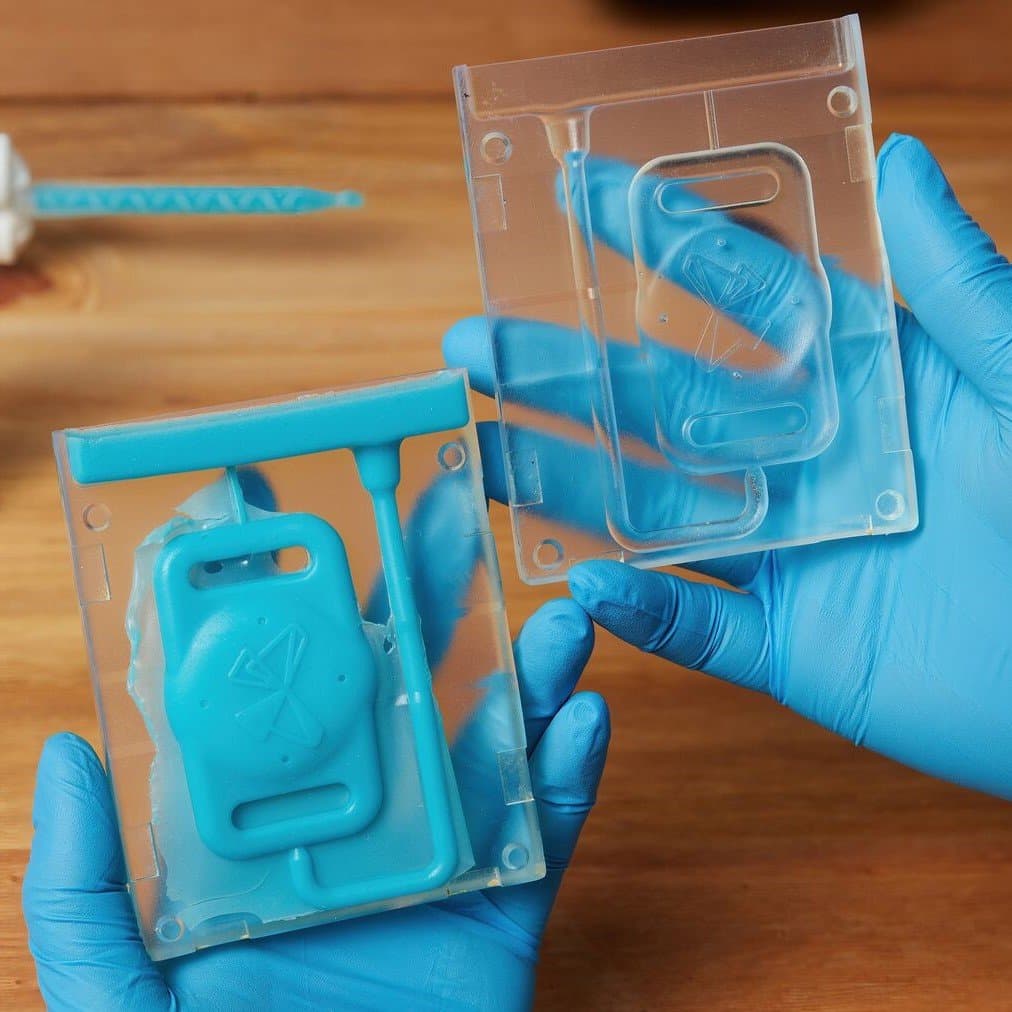
3Dプリント製の成形型を使ったシリコン部品の製造方法
このウェビナーでは、重力金型鋳造法で使用する樹脂型をFormlabsのClearレジンで3Dプリントした例を詳細に解説します。また、用途に応じた成形型の選び方、シリコンレジン対応の3Dプリンタ、そしてシリコン鋳造のベストプラクティスについてもお話しします。
3Dプリントを活用した圧縮成形、射出成形、真空成形、およびシリコン成形
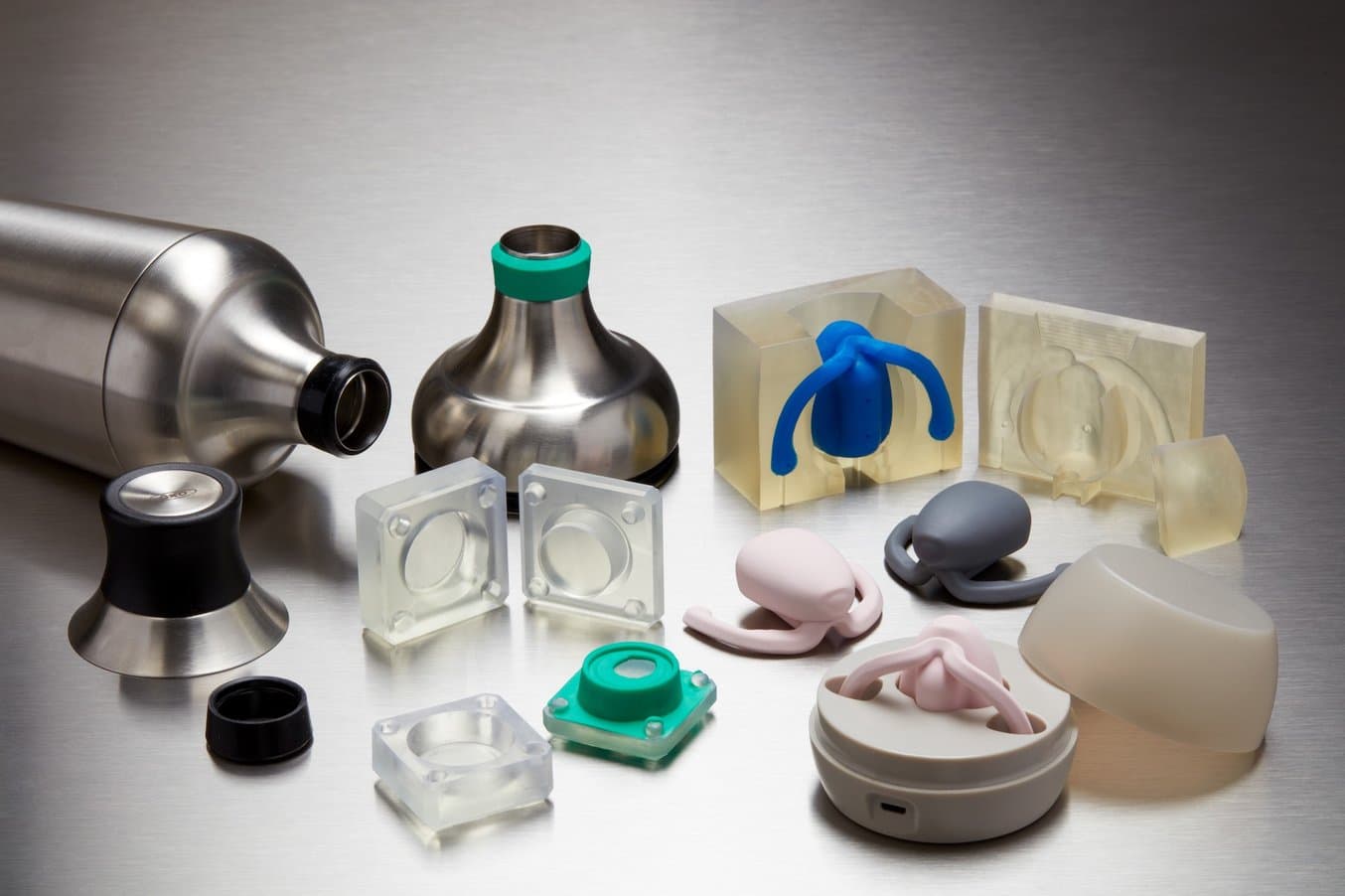
3Dプリントによる成形型製作にご興味がある場合は、無料のトレーニングウェビナーや無料の技術資料をご覧ください。ステップごとの手順をご紹介しています。
-
このウェビナーでは、成形型設計の基本や3Dプリントへの応用法に加え、試作成形型や3Dプリント製成形型の量産での活用事例をご紹介しています。
-
技術資料をダウンロードいただくと、成形型設計のベストプラクティスや実際にFormlabs製品をお使いのユーザー様のケーススタディ、シリコン部品製造用に3Dプリント製の成形型を作る手順などをご確認いただけます。
-
プロトタイピングや量産で使用できる成形型の6つの製作方法(射出成形、熱成形、鋳造エラストマーなど)については、こちらの技術資料をダウンロードしてご確認ください。