オーディオ体験の未来を語る時、Formlabsはカスタムフィットのイヤホンが一つの鍵になると信じています。スマートフォンと3Dプリントの急速な普及により、スマートフォンでのスキャン、製造の自動化、そして低コストな3Dプリントによって自分の体に合わせて作られたカスタムフィットのイヤホンを市場に供給することが史上初めて可能になっています。
本記事では、代表的なBoseのインイヤーヘッドホンのカスタムイヤーピースを簡単に製作する方法を解説します。まずは、以下の動画をご覧ください。
3Dファイルのスキャンと準備
カスタムフィットのイヤホンは、丸1日ずっと使用しても快適でありながら、不要なノイズを遮断し、唯一無二の音楽体験を提供するものです。 また、イヤホンが耳から外れる心配がなく、装着感やノイズキャンセル機能も向上します。
現在では従来の耳型採取に代わり、ユーザーが自身のスマートフォンで耳の形をスキャンできるようになっており、Hearables3Dアプリを使えば、AIでスキャン品質を向上させながらスマートフォン端末で完全にスキャンできなかった部分を再構築しながら、1分もしないうちにスキャンが完了します。
スキャンデータはクラウドベースの機械学習システムに送信され、統計モデリングにより、数秒以内にスキャンされた耳の形状を特定のイヤホンデザインに変換し、Formlabsの3Dプリンタでプリントする準備が整います。
CADソフトウェアから3Dプリンタへ
スキャンデータのファイルは、スマートフォンから自身が使用しているCADソフトに直接インポートできます。ここでイヤーチップの根元部分が、使用したいイヤホンの形と一致しているかどうかを確認します。
これまで補聴器メーカーでは、経験を積んだモデラーが職人技によって耳型の採得を行ってきました。しかし3DスキャンとCADソフトウェアの急速な進歩によって必要なスキルのハードルが下がり、より幅広いユーザー、あるいは中小規模のメーカーでもイヤーチップを製作できるようになりました。多くのCADソフトでは、このプロセスを完全に自動化することも可能です。
イヤーチップのファイルは、CADソフトからFormlabsの無料造形準備ソフトウェア「PreForm」に直接送信され、生体適合性材料に対応したSLA光造形3Dプリンタ「Form 3B+」あるいは「Form 3BL」用に3Dプリントファイルの準備を行います。
デスクトップサイズのForm 3B+と、大容量機であるベンチトップサイズのForm 3BLは、共にヘルスケア用に開発された高度なSLA光造形3Dプリンタです。高精度高信頼性の特許技術により、オーディオ製品の製作や試作において推測で進めざるを得ない不確かな要素を排除し、より高速な作業を簡単に実現できます。Form 3B+とForm 3BLに実装された独自の特許技術「LFS(Low-Force Stereolithography)テクノロジー」によって造形中に発生する不要な応力を最小化することで、驚くほど滑らかな表面品質を実現します。Formlabsは、競合する3Dプリンタの3倍以上のサイズ(145×145×185mm)と半分以下の価格で、品質、作業効率、価格という3つの価値を提供するユニークな3Dプリンタを実現しています。家庭用にも販売される非常に安価な3Dプリンタでは、使用する材料ごとの収縮率などが最適化されておらず、どの材料でも同じようにプリントされるため造形の成功率や寸法精度に大きな影響を及ぼしますが、Formlabsでは自社開発材料の利点を生かし各材料ごとのパラメータをアルゴリズムがすべて把握し、その材料に最適なプリントで極高精度を実現しています。
Formlabs製品による低コストな内製3Dプリントで、患者や顧客にカスタムフィットのオーディオ体験を提供することが、かつてないほど手軽に実現可能となっています。1時間の即日サービスを提供したいクリニックや、1台の機械で1日に100点のプリントが行えるようビジネスの規模を拡大したいラボ等に、Formlabsはデジタルオーディオ製作のワークフローを次世代に進化させるサポートを行っています。
イヤーモールドをラッカーで仕上げる
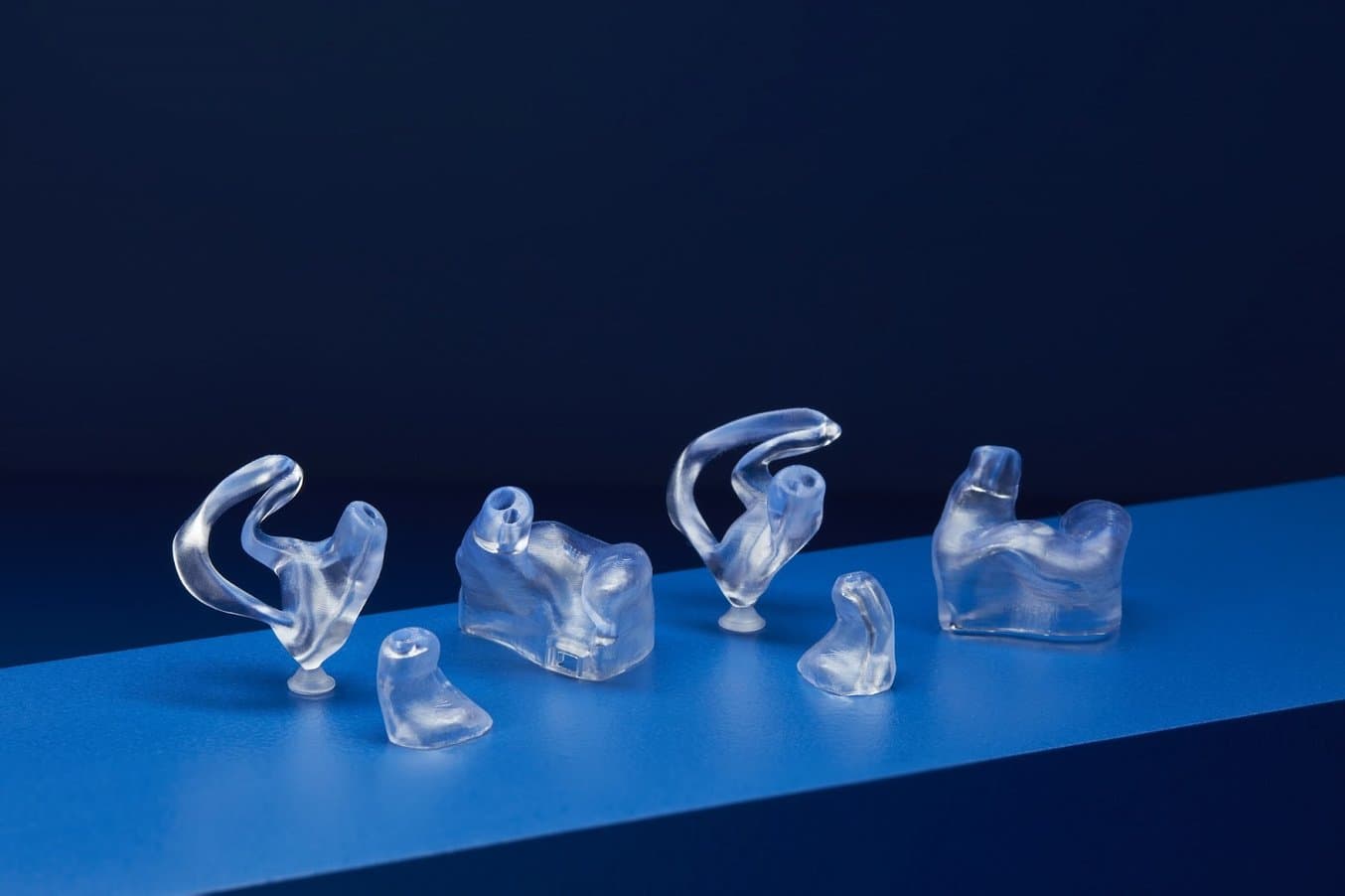
造形品はプリント完了後、Form Washでの洗浄で表面に残る液体レジンを洗い流し、Form Cureでの二次硬化によって材料特性を十分に引き出す必要があります。その後、仕上げ作業として生体適合性材料ではないFlexible 80Aレジンをユーザーの耳に入れても安全なように、パーツにラッカー塗装を行うことでコーティングします。
仕上げの最終段階はこのラッカー塗装です。上の動画では、Egger社のLP/Wラッカーを使用していますが、他にもDreve社やDetax社、そして日本国内でも一般的なラッカーが販売されています。安全性や生体適合性については各ラッカーのメーカーに確認し、条件を満たした塗料であることを確認の上、ご使用ください。
この作業が終わると、カスタムフィットのイヤホンはお客様のもとにお届けする準備が整います。旧来は長く、複雑だった工程が、わずか数時間で完了します。
Formlabsの3Dプリント製品
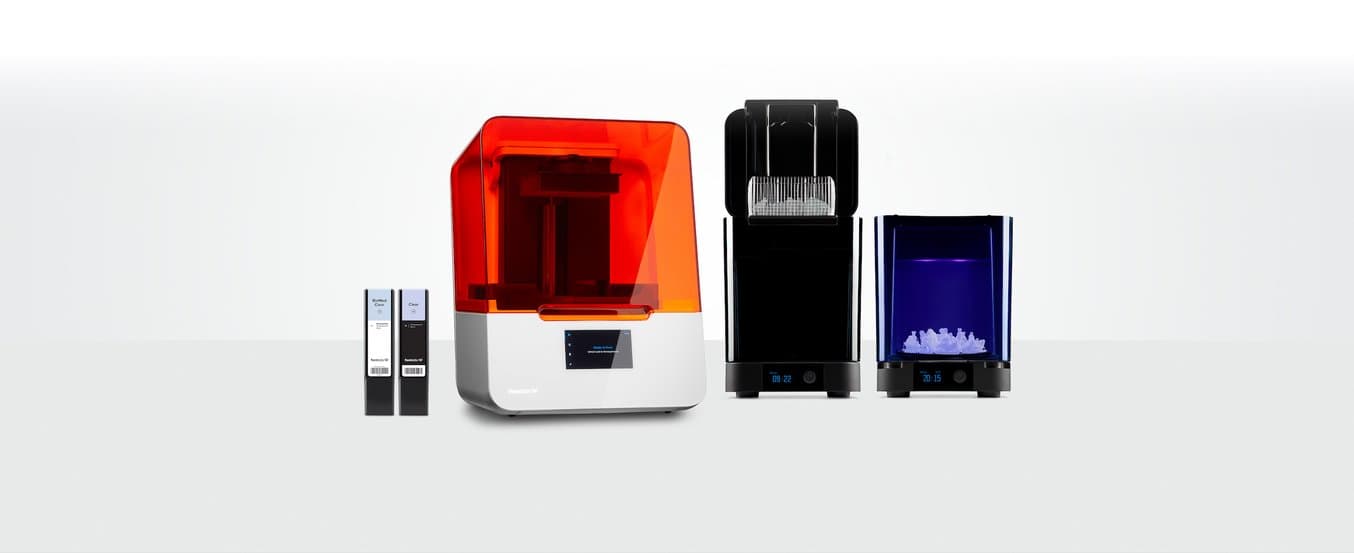
今回のワークフロー動画では、Flexible 80Aレジンを使用しています。Flexible 80Aレジンは、曲げ、折り、圧縮を繰り返し行っても、耐えることができる工業用材料です。Flexible 80A ResinはFormlabsのFlexible & Elasticレジン製品の中で最も硬い軟質材で、柔軟性においてゴムライク、またはTPUライクの材料として80Aショアデュロメータの硬度を備えています。
また、Formlabsはヘルスケア業界に特化した、透明かつ高い耐衝撃性を持つ生体適合性材料であるBioMed Clearレジンを提供しており、ハードイヤモールド、シェル、インイヤーモニター等にもご活用いただけます。
このBioMed Clearレジンは、補聴器、防音用の耳栓やイヤーマフ、その他消費者向けオーディオ製品の試作や製作を低コストに内製化できるというFormlabs製品のメリットを代表する材料でもあります。
「Form 3BでBioMed Clearレジンのプリントを行うことで、生体適合性を持った高強度なアクリル製補聴器が内製できるようになりました。Form 3BとBioMed Cleaeは価格も手頃で品質が高く、おかげでデジタルファブリケーションによる生産規模を迅速に拡大することができました。」
Paul Thorpe氏 Universal dB ラボマネージャー
BioMed Clearレジンを貴社にて検証してみませんか?以下の無償サンプルパーツのお申込よりリクエストいただければ、貴社までサンプルパーツを無償でお届けいたします。