Kriwat GmbHは、ドイツのキールに本社を置く整形外科専門の医療器具プロバイダーです。創業当初から、スポーツにおけるパフォーマンスと最先端医療研究を融合させるという独自の視点を取り入れてきました。
Michael Kriwat氏は1987年、レクリエーションやプロのアスリートを対象にトレッドミルを使った歩行分析をドイツで初めて実施した専門家の一人として事業を開始しました。それ以来、同社はキール、ハンブルク、プリーツに6つの拠点を構え、75人のチームを擁するまでに成長し、包帯やインソール、人工装具、矯正用シューズの分野で患者ひとりひとりに合わせたケアを提供してきました。
整形外科医療業界は現在、深刻な技師不足に直面しています。手間のかかる装具の製作を志願する若い専門家はほとんどおらず、ましてや家族経営のことが多い中小企業経営の責任を引き受けても良いと思う人はなかなかいません。
本記事では、Michael氏の息子であるLais Kriwat氏がSLS(粉末焼結積層造形)方式3Dプリントを活用してインソール製造工程をデジタル化し、ビジネスを近代化することでこれらの課題に対処しながら、3Dプリントによるインソール製造量1万足を目指す道のりについて詳しくご紹介します。
手作業による製作工程に3Dプリントで変革を起こす
矯正用インソールの従来の製作方法は非常に手間がかかるうえに作業場所が汚れやすく、ユーザーとプロバイダーの両方にとって面倒なものでした。まず、発泡成形でユーザーの足型を採取します。その足型に液体のポリマーを流し込んで足の形を再現し、そこから矯正用インソールを製作します。
これには、埃や化学物質の蒸気が充満した環境で作業を行う専門的なスキルと多くの手作業が必要です。「私自信、修業時代にはとても悩まされました。化学薬品を使って製造しなければならないものがたくさんあるんです。研削盤で研磨が必要なものも多く、常に化学薬品や粉塵に接触した状態で作業をしなければいけません。そういう背景から、化学薬品との接触を減らすべく、新しいやり方を編み出すという目標を自分に定めました」とLais Kriwat氏は言います。
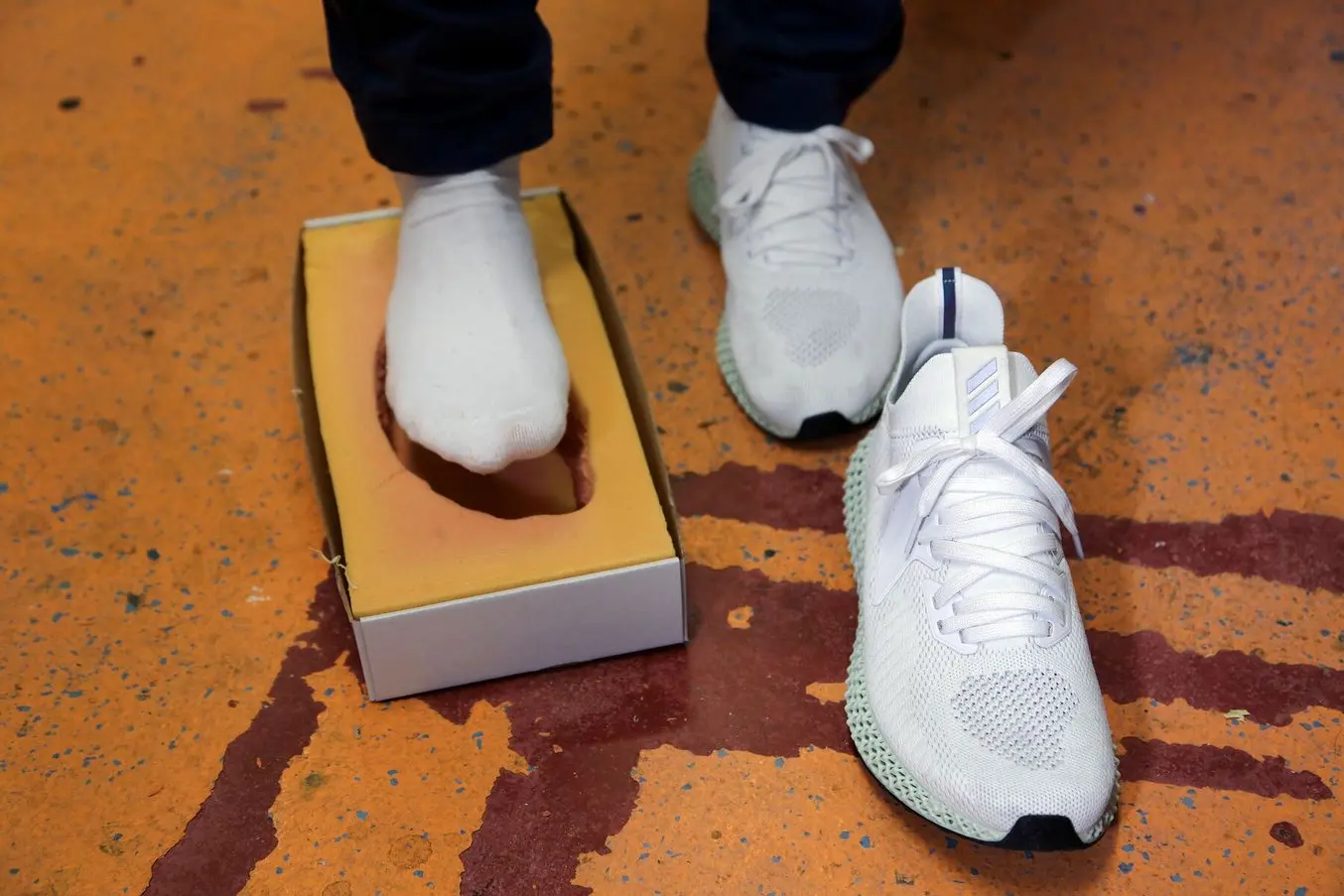
従来のやり方では、発泡成形でユーザーの足型を取得する。
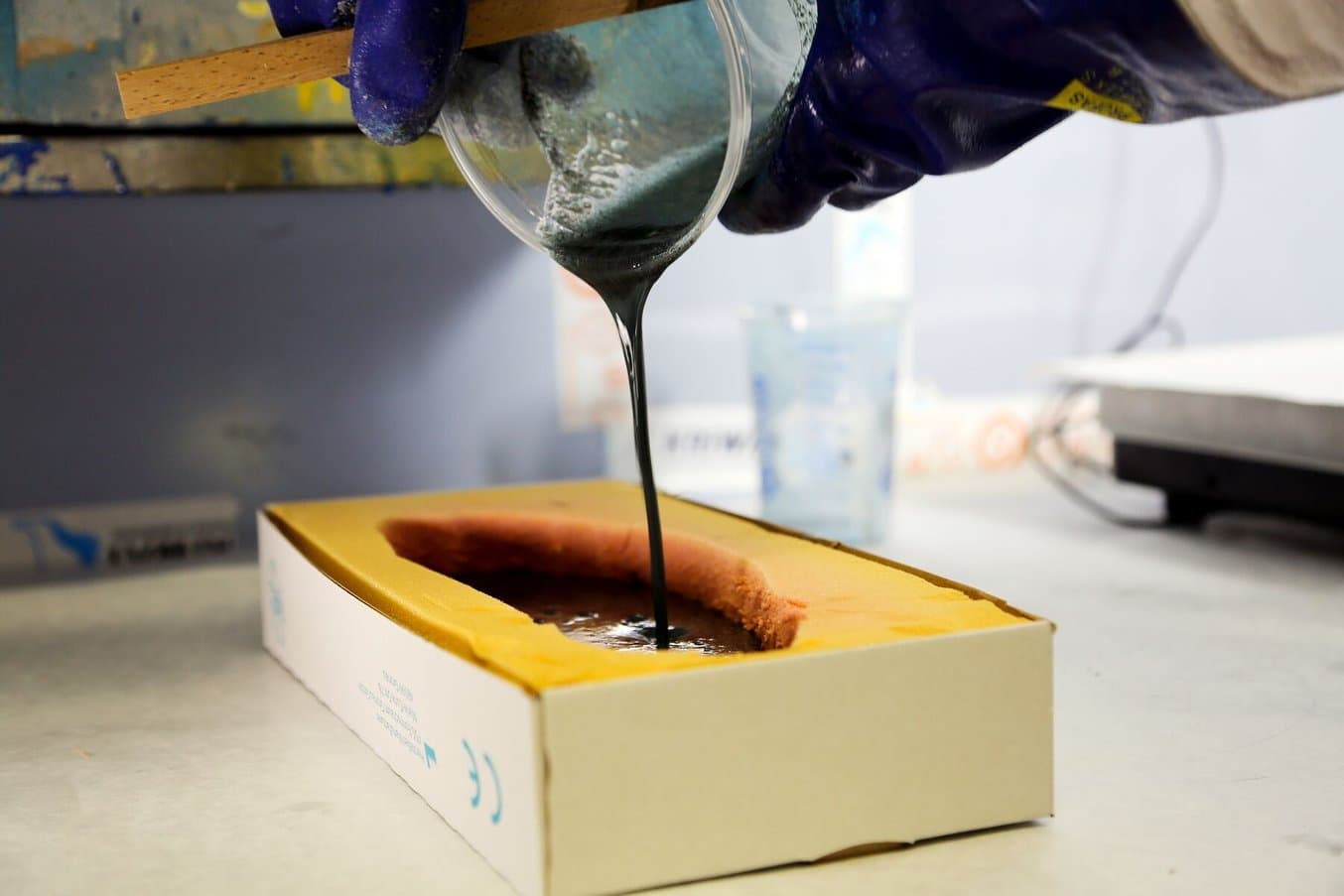
その後、成形型を薬品で満たして足型を再現する。
最近この業界に足を踏み入れたばかりのLais氏は従来の製造方法の課題を身をもって体験し、もっと従業員を惹きつけられるような環境にするためには、何か変化が必要だと感じました。
「この業界が直面している最大の課題は、人材不足です。この職業に興味がある人、仕事として手作業でものづくりをしたい思っている人を見つけるのは難しいので、この仕事自体をもっと興味深いものにしなければいけません。そこで、新しい技術が非常に重要になるんです」とLais Kriwat氏。
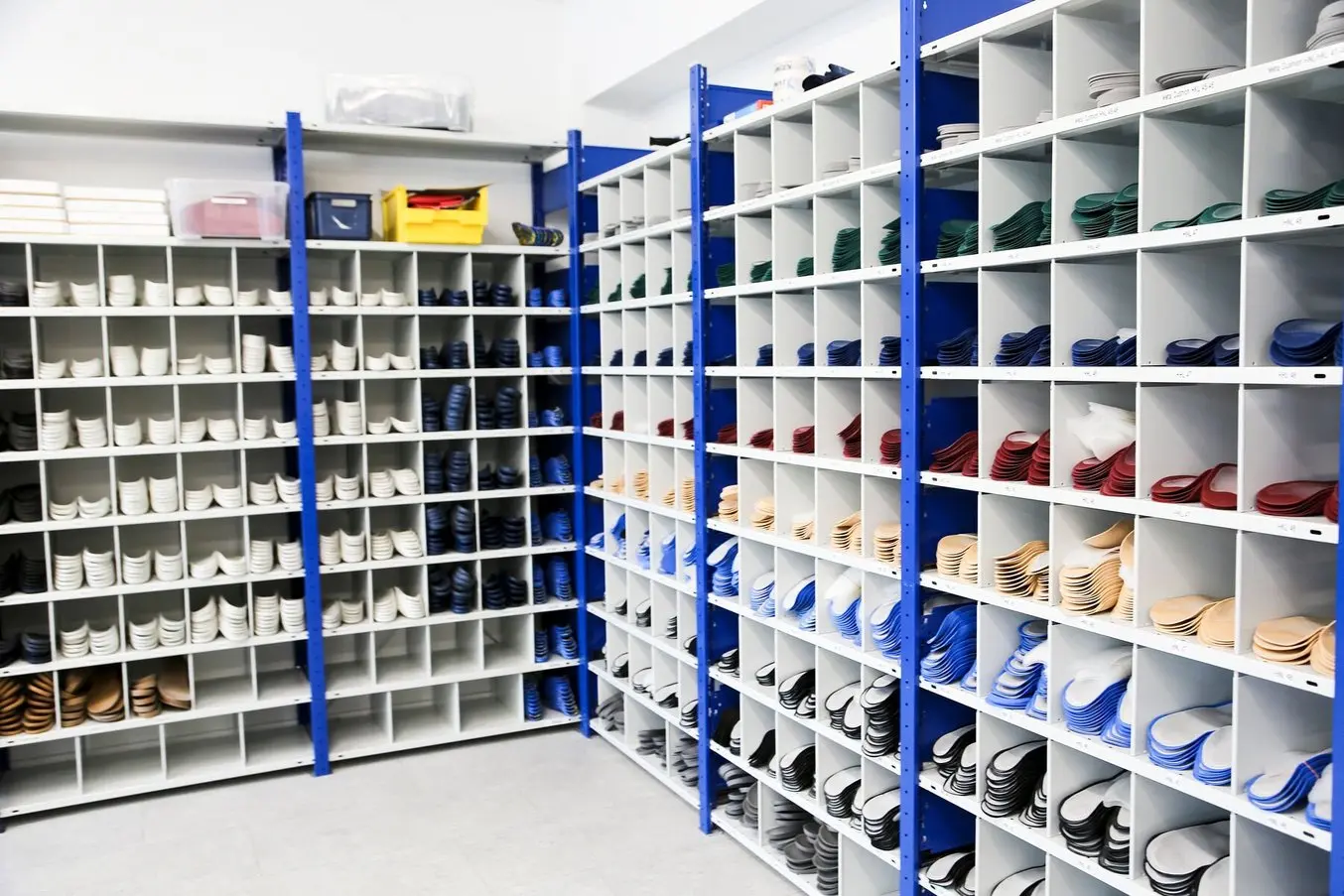
Kriwat GmbHでは、毎年数千点のインソールを生産している。
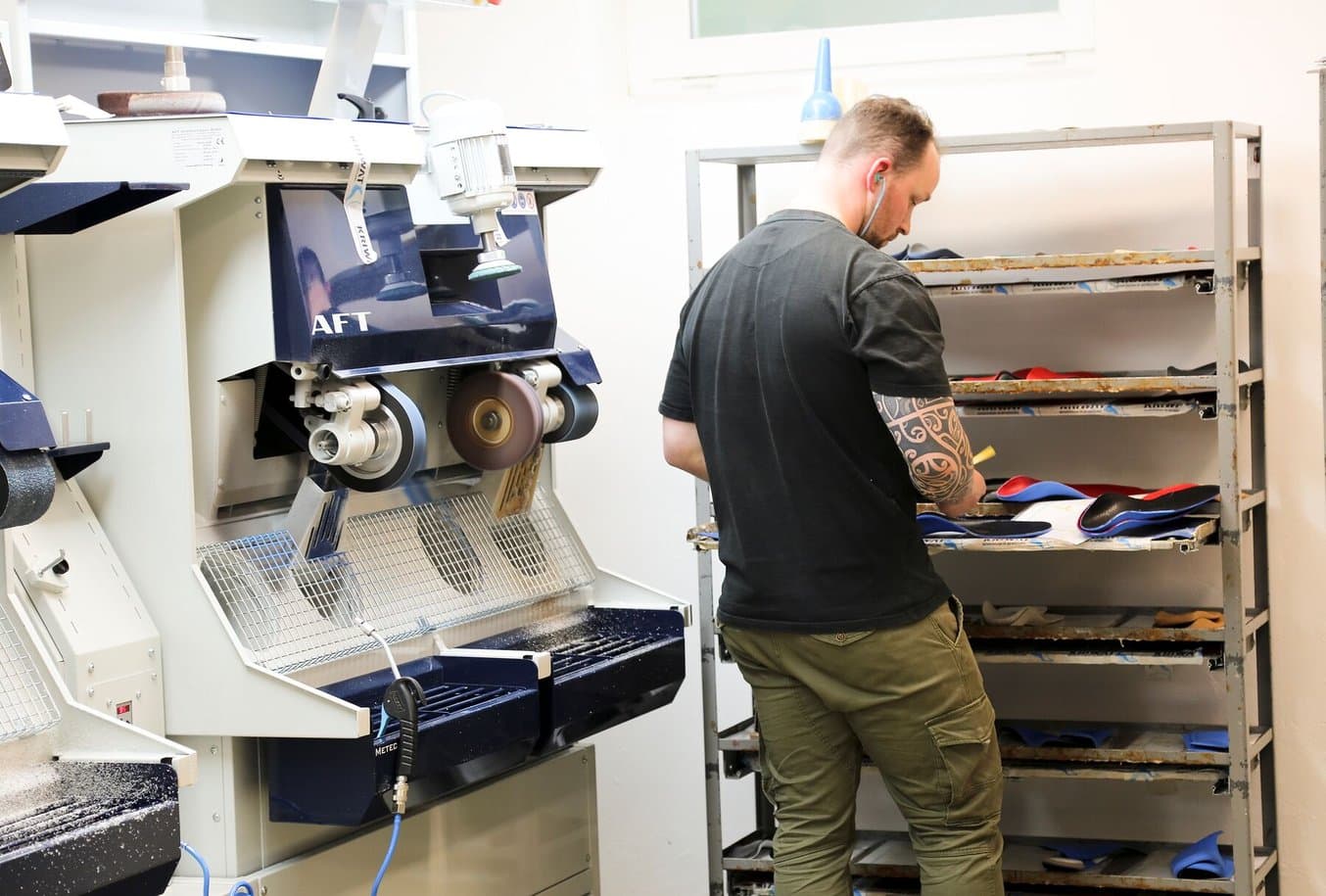
矯正用インソールを製造する従来の作業手順は、非常に手間のかかるものだった。
Lais氏が3Dプリントを試し始めたのは2017年。最初は小型のFDM(熱溶解積層)方式3Dプリンタで趣味の作品や試作品を製作するところから始めました。3Dデザインと3Dプリントの扱いに慣れてきた頃、家業にこの技術を導入する方法を模索し始めました。SLA光造形方式の存在を知った同社は、人間の足サイズでもプリントが可能なForm 3BLを購入し、矯正具の製造に新しい可能性を切り開きました。Lais氏は徐々に新しい用途での3Dプリントの活用方法を習得していき、やがて事業の中核であるインソールの製造に着目し始めました。
「最初は、次に何をしたらよいのかわからないことばかりでした。頼りになるパートナーを探し始めたところ、Formlabsに出会ったんです。本当に幸運だったと思います。この出会いでようやく、頭の中にあったアイデアを具現化することができました。デザインを送ると、実際に3Dプリントしたものを送ってくれるので、その設計がそもそも3Dプリントでうまくいくのかどうかを事前に確認できました。このあたりは私にはまったく経験がありませんでしたから、Formlabsには本当に助けられました」と、Lais Kriwat氏は振り返ります。
Laisはインソール製造工程を徐々にデジタル化し、実製品を社内や顧客と共にテストをして検証しました。デジタル化された新しい工程では、これまで手作業で行っていた足型の取得を3Dスキャンに置き換え、デジタル設計と3Dプリントによって煩雑な手作業が削減されました。従来の工程と3Dプリント製のパーツを組み合わせて、最終的な製品を製作します。
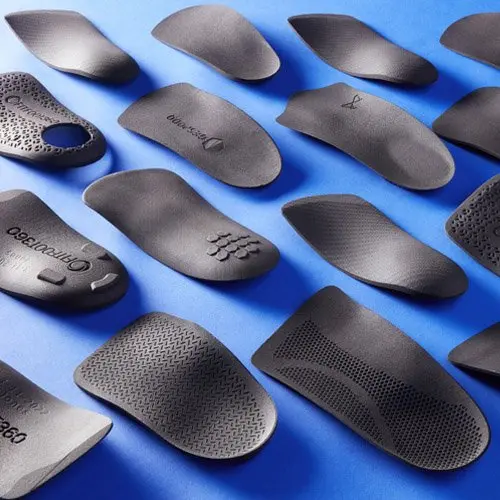
硬質なインソールシェルを3Dプリント
本ガイドでは、Formlabsが提供するコンパクトで手頃な価格のSLSプリンタで、400万回以上の曲げ試験も耐え抜く強度と靱性を備えたインソールを製作する方法をご紹介します。Fuse 1+ 30Wで製作したインソールシェルで、インソール製作へと大きな一歩を踏み出せるようお手伝いします。
インソール製造における3Dプリントの利点
Kriwatでは、SLS 3DプリンタのFuse 1+ 30Wを2台とNylon 11パウダーを使用して、個々のインソールコアやインソール全体を製作しています。当然のことながら、完全にデジタル化に移行する前に、Lais氏は矯正用インソールの製作方法を変えることで会社と顧客の双方にとってどんなメリットがあるのかを証明する必要がありました。Lais氏が強調した主な利点は以下の通りです。
作業時間の削減
新たな製作方法では、3Dスキャンを取得した後、同日中にデジタルモデルを作成し、他のインソールと合わせて1つのバッチにし、Fuse 1+ 30Wで夜のうちに3Dプリントしておくことができます。翌日、完成品に後処理を行い、従来の手順でコア周りのインソールを製作したら、その次の日にはインソールが完成します。
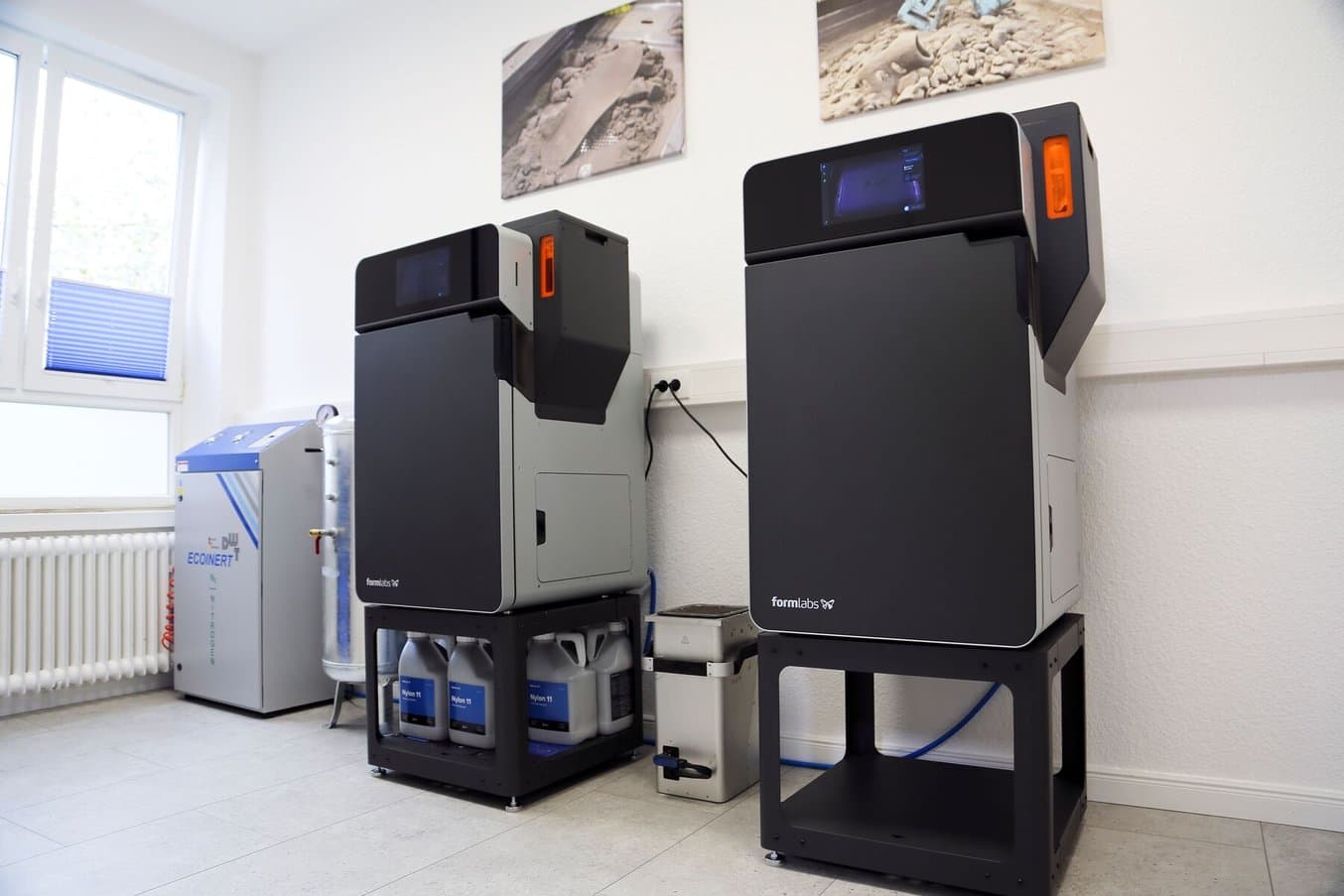
Kriwat GmbHは現在、社内でFuse 1+ 30W SLS 3Dプリンタを2台稼働させている。
「現在では、患者様の足に完璧にフィットする装具を24時間以内に製作できるようになりました。迅速なケアを提供できることが私たち自身にとって大きなメリットとなっていることはもちろんですが、何よりも大切なのは、悩みを抱えた患者様に対して最短で最善のケアを提供できることです」
Kriwat GmbH 経営陣、矯正用シューズ製作技師、Lais Kriwat氏
コスト削減
手作業で行っていた従来の製作方法に比べ、新しいデジタル工程は材料費と人件費の両面で経済的なメリットがあります。多くの作業をデジタル化することで、必要な材料や作業量を削減できるためです。Kriwatほどの製作量がある場合、一度3Dスキャナと設計用のソフトウェアを購入してしまえば、大量の成形用フォームや液体薬品を購入し続けるよりも安価になります。
さらに、製作にかかる時間が短くなることで1人あたりが担当できる患者様の数も増え、労働力の削減にもつながります。Lais氏は、3Dプリントのおかげで製造コストを約15%〜17%抑えられたと見積もっています。
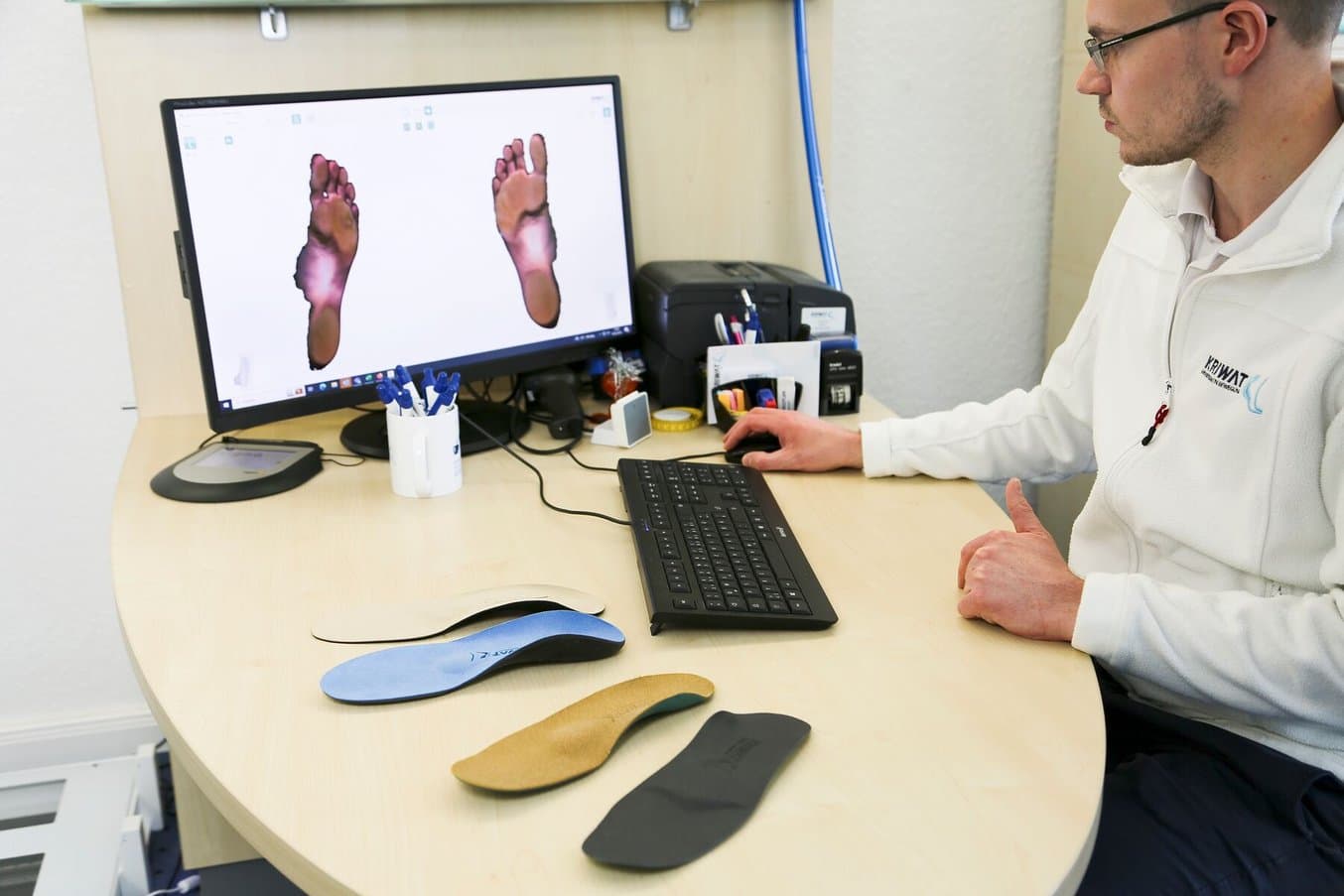
3Dスキャンでは、より正確で完全な足型を取得できるほか、データをデジタルで簡単に送信可能。
同社はすぐに、3Dプリンタの社内導入によってコスト削減と作業工程を大幅に改善できる可能性を見出しましたが、SLS方式3Dプリンタのほとんどは価格が非常に高額なものばかりで、同社の予算からは大幅に外れていました。その中で唯一、Fuse 1+ 30Wだけが中小企業にもアクセスしやすい価格帯で、かつ同社が求めていた工業用パワーを実現できるSLS 3Dプリンタでした。
「Formlabsの大きな利点は、もちろんコスト面でアクセスしやすいことです。うちは中堅企業ですから、このソリューションに投資ができます。他のメーカーや同業他社では実現できなかったでしょう」
Kriwat GmbH 経営陣、矯正用シューズ製作技師、Lais Kriwat氏
簡素化された作業手順
SLS 3Dプリント方式のFuseシリーズには、インソール製造の作業手順を簡素化できる多くの機能が備わっています。造形中は未焼結パウダーが造形品を支えるため1回に多量のインソールをまとめてプリントでき、作業手順の最適化とコストの削減を実現します。SLSプリントの造形品はざらついた表面が特徴で、この表面が様々なタイプの実製品向けに接着剤やカバーを使用する際に最適です。ナイロンで作る造形品は、機械加工や研磨を行うことで実製品用途として完璧な表面に仕上げることも可能です。
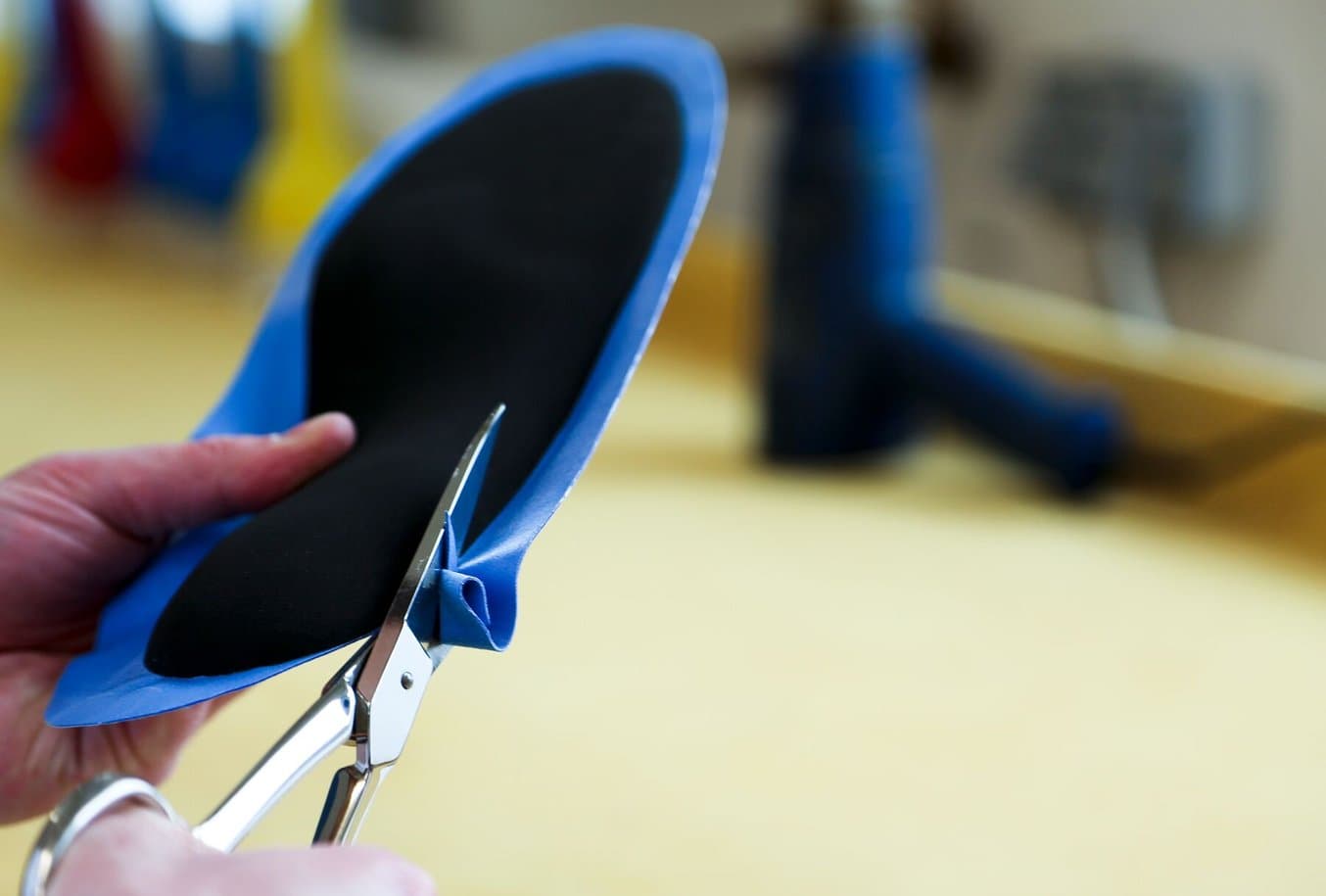
3Dプリント製のインソールとインソールコアにカバーやその他パーツを組み合わせて実製品が完成する。
Formlabsのオンライン管理ツールDashboardでは、オペレーターが複数台の3Dプリンタを管理したり、プリントの進捗状況や材料の在庫状況を確認できるほか、プリントジョブのステータスに関する通知を受け取れます。Lais氏は、この要素が計画には欠かせないと言います。これまで数々の3Dプリンタ用スライサーソフトウェアを使用してきたLais氏はまた、Formlabsの無料造形準備ソフトウェアPreFormのわかりやすさと使いやすさを実感しています。
「PreFormは、素早くプリントを開始するのに最適なソフトウェアです。私たちにとっては、他の従業員にも3Dプリントがいかに簡単なものかを見せられることが重要なんです。PreFormは子供の遊びのように簡単に使えて、説明もしやすく、プリントジョブをプリンタにすぐに送信できるので、理想的ですね」
物流の改善
デジタル化によって、物流管理も簡素化できます。Kriwat GmbHは現在、ハンブルクの店舗に3Dスキャナを設置しています。これにより、デジタルデータをキールにある本社に簡単に送信できるようになりました。以前は、インソールの製造拠点である本社まで手作業で作成した足型を輸送する必要があり、定期的に長距離移動が発生するため、時間とコストがかかっていました。
持続可能性
輸送の必要性が低減される以外にも、3Dプリントによって様々な方法でインソールの製作工程を持続可能なものにできます。デジタル工程では、患者様の足のレプリカ製作が不要なため、その製作に必要だった原材料が大幅に削減されます。Kriwat GmbHは、何千点もの足型モデル、未使用のまま余ったフォーム、化学廃棄物の適切な処理方法を考える必要がなくなりました。Fuseシリーズの効率的なシステムでは、造形時に使用しなかった未焼結パウダーを次の造形で再利用できるため、廃棄物を削減、あるいは完全になくすことができる循環型の工程が実現します。
「持続可能性は私の世代にとって最も重要なテーマですから、材料の廃棄量を減らすことでした。例えばここにプラスチック用のゴミ箱がありますが、ゴミ箱の回収を毎週ではなく4週間に1度のみに変えられるよう、ゴミを最小限に抑えることが私の目標でした。また、化学薬品の使用量と廃棄量を減らしたいとも考えていました。FormlabsのSLS方式では、本当に必要なものだけをプリントできるので、この面でも私の希望に完璧にフィットしていました」とLais Kriwat氏は言います。
インソール製造の未来の革新を牽引
Kriwatは3Dプリントの導入後、最初の1年でインソール製造工程の約50%をデジタル化し、約10,000足のインソールコアとインソールを3Dプリントで製作することを目標にしています。しかし、同社で活躍する2台のFuse 1+ 30W SLS 3Dプリンタは、将来に向けてさらに多くの可能性を秘めています。
「デジタル化の第一歩としては、伝統的な手作業による工程をデジタル化することが目的でした。つまり、インソールの形状や特殊なインソールをコンピューターに取り込み、最終的に3Dプリンタで実際に製造するところまでです。今後は、3Dプリント技術だけを使ってまったく新しい製品も作る予定です」とLais Kriwat氏は述べます。
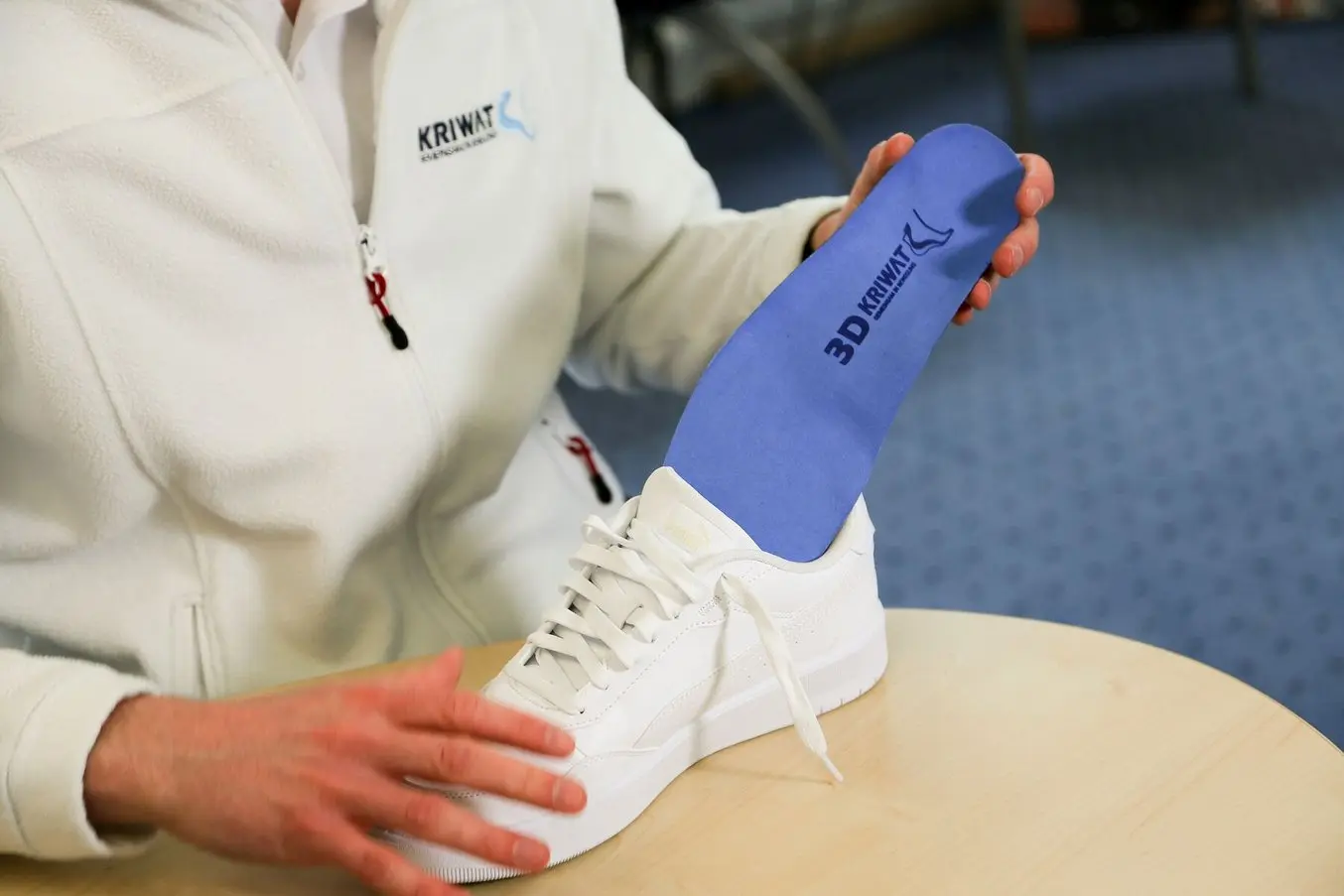
現在の製造工程をデジタル化した今、Kriwatは3Dプリントだからこそ可能な革新的な新製品を開発することを次の目標にしている。
SLS 3Dプリントで可能になる自由な設計により、歩行時の体圧分散、個別のプレミアム製品、従来の方法では製造できなかった特殊なサポート器具、ランニングやサッカーなどのスポーツで足を最適にサポートする薄型製品などが可能になります。
「15年前には不可能だった新しい可能性を市場に提供できることに、とてもワクワクしています。今はまだ想像もできないようなことも、近い将来、すぐに実現できるようになるでしょうね」
Kriwat GmbH 経営陣、矯正用シューズ製作技師、Lais Kriwat氏
インソールの3Dプリントに関する詳細は、3Dプリント活用例の紹介ページでご確認いただけます。また、Formlabsの3Dプリンタに関するご質問は、Formlabsのスペシャリストまでお気軽にお問い合わせください。