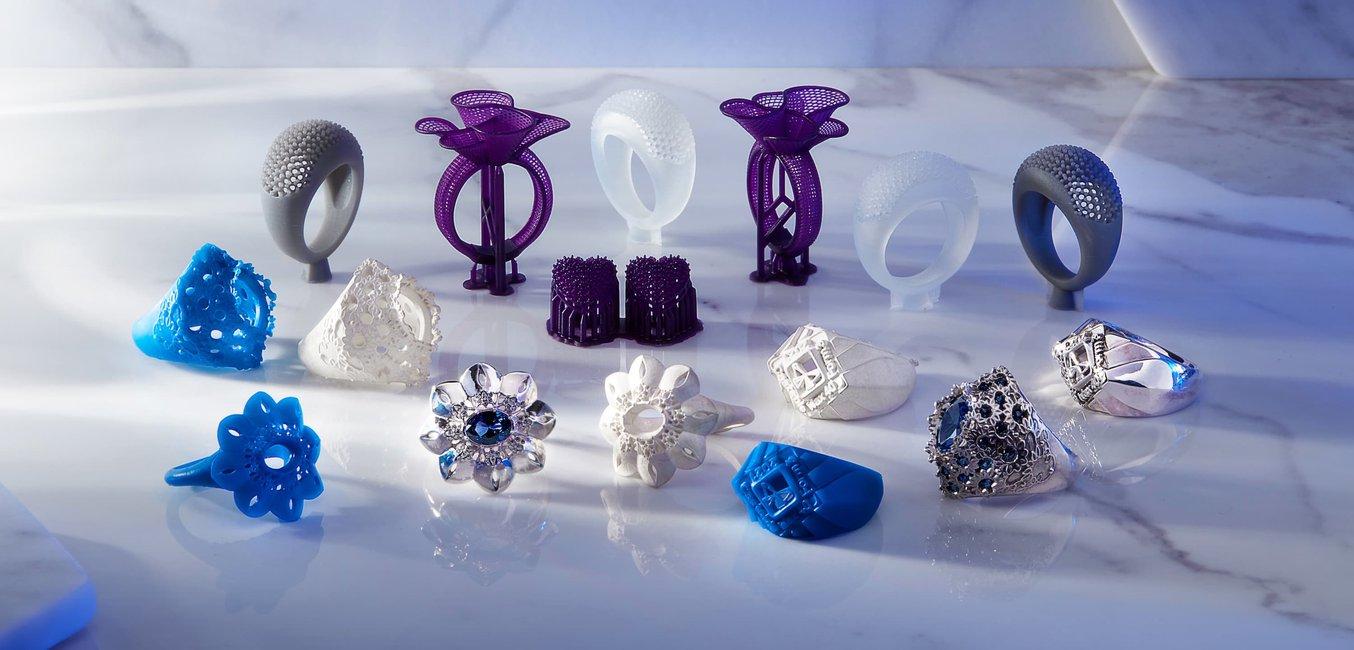
3Dプリント製のリングの原型と実際に貴金属で鋳造したリング。
ロストワックス鋳造とは金属鋳造の手法で、ワックス(ロウ)で製作した原型を台材に仕込み、焼成で原型を溶かし出して台材を鋳型にした後、金属材料を流し込むことで製品を作る製法です。
ロストワックスは最も古い金属製法の 1 つで、その歴史は6千年前にまで遡りますが、この製法は今でもジュエリーや歯科、アートの分野を中心に広く活用されています。工業分野ではインベストメント鋳造と呼ばれ、エンジニアリングや製造業で精密な金属製品を作る際に使われます。
もともと職人技の手工芸と同列に捉えられることが多かった製法ですが、現代の作り手たちはデジタルデザインと3Dプリントで手順を簡素化し、製造時間の短縮、コストの削減、工程の再考を行い、ロストワックス鋳造を21世紀らしいものに変革しています。
本記事では、デジタルテクノロジーによってどのようにロストワックス製法が活用されているのか、そしてそれがジュエラーや歯科、製造業にどのような影響を与えているのかをご紹介します。
ロストワックス鋳造とは
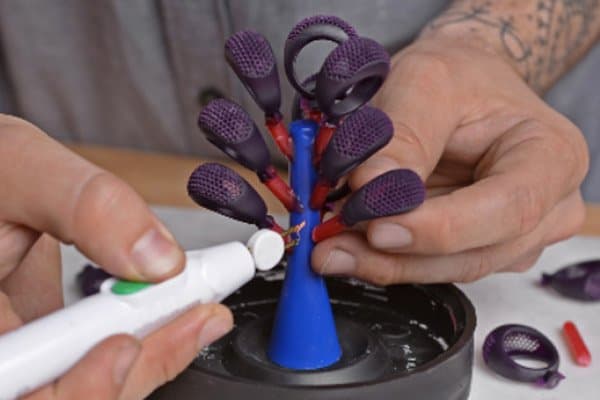
原型を湯道でつなぎ合わせて鋳造ツリーを作る。
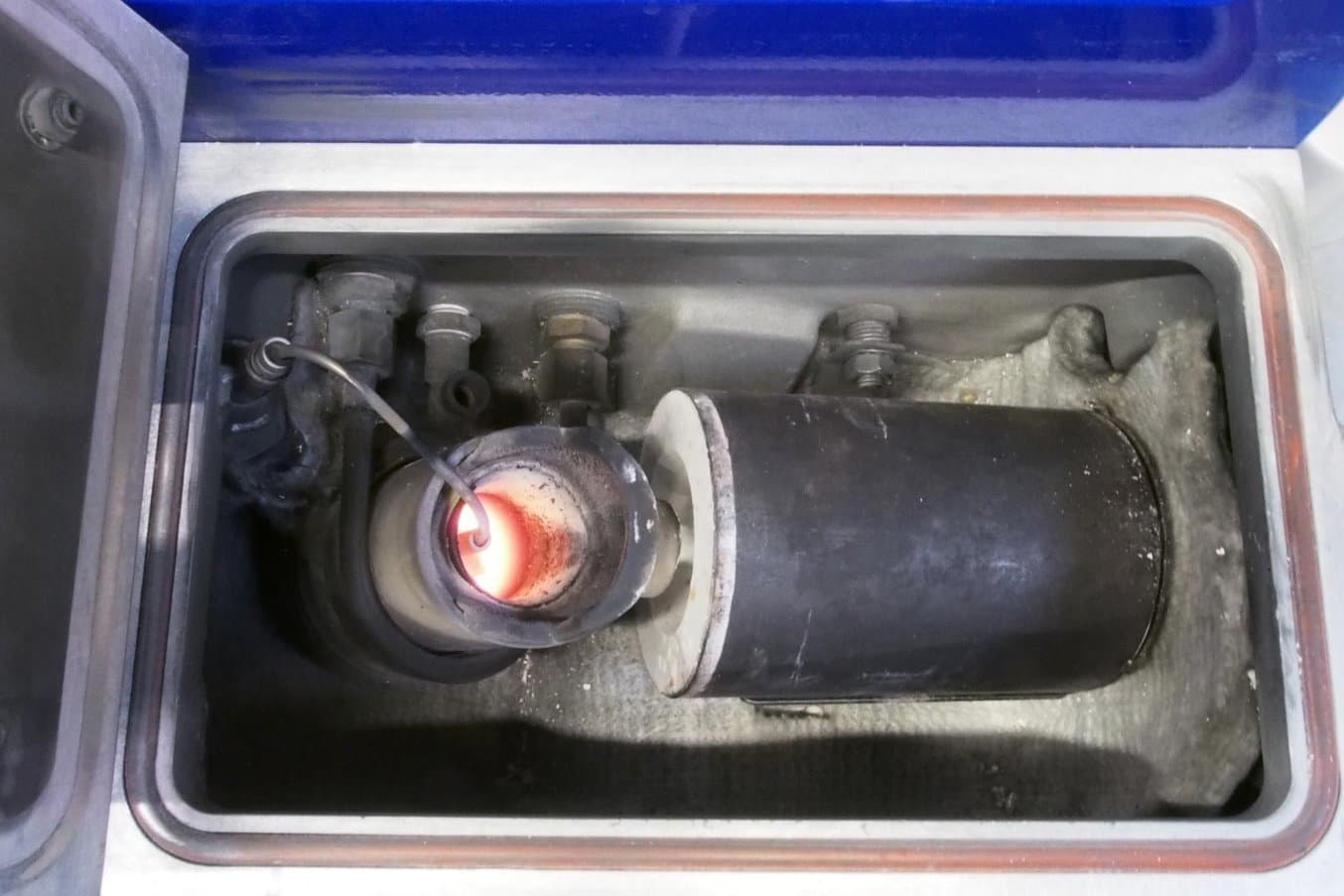
溶かした金属をインベストメント型に流し込む。
ロストワックスの手順は産業や用途により異なりますが、一般的には以下の通りです。鋳造部品には、ワックスモデルそのものから作るダイレクトキャスティングと、ワックス製のレプリカであるマスター(原型)を使用するインダイレクトキャスティングの2つがあります。ダイレクトキャスティングの場合は、ステップ1のあとすぐにステップ4に移ります。
-
モデルの製作:ワックス(ロウ)からデザインを彫り出します。モデルのサイズや複雑さは、ワックスを削る人のスキルや使用する鋳造設備の性能により異なります。
-
鋳型の製作:鋳型師がこの模型を鋳造し、鋳型を研磨して「マスター」パターンを作ります。この原型をもとに、ゴムでワックス用の型を作り、原型の周りを熱しながら加硫することで、柔かいワックス用の型ができあがリマス。
-
ワックス原型の製作:溶かしたワックスをゴム型に注入、あるいは流し込みます。これを何度も繰り返すことで、オリジナルデザインのコピーをいくつも作ることができます。
-
ワックス原型の組立:複数のワックス原型を湯道でつなぎあわせると、ツリー形状が出来上がります。これにより溶かしたワックス(ロウ)が流れる道ができ、その後溶かした金属が空洞部を埋めていきます。
-
インベストメント材料の塗布:ワックスツリーはシリカ液に浸すか鋳型に入れて液状のインベストメント石膏でコーティングを行います。
-
焼成:インベストメント材料が乾いたら、鋳型を上下逆さまの状態で釜に入れます。こうすることでワックスが溶け、内側に原型と同形状の空洞が出来上がります。
-
流し込み:インベストメント型を釜の中でさらに加熱し、溶かした金属との温度差を縮めます。金属を溶かし、重力や真空圧を利用して金属を空洞の中に引き込みます。
-
取り外し:金属の粗熱がとれたら、インベストメント金型を水につけて急速に冷やすことで耐火石膏を溶かし、粗鋳造品を取り外します。湯道(スプルー)は切り取って再利用し、鋳造部品は鋳造痕を消すために洗浄を行います。
-
仕上げ:鋳造品は、やすりがけ、研磨、切削、サンドブラスト処理を施し、最終的な形状や表面の仕上げを行います。必要に応じて鋳造品に熱処理を施すことで材料の機能的特性をさらに高めることもできます。
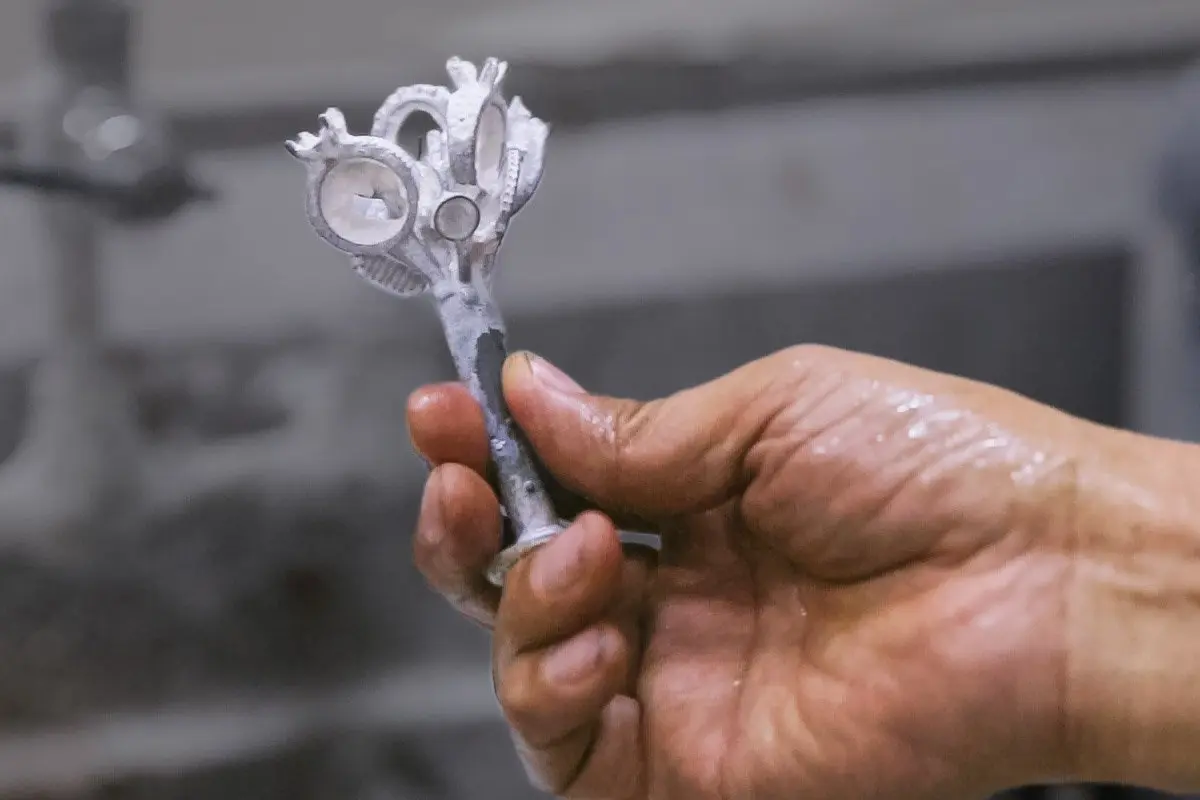
取り外した後の鋳造ツリー。
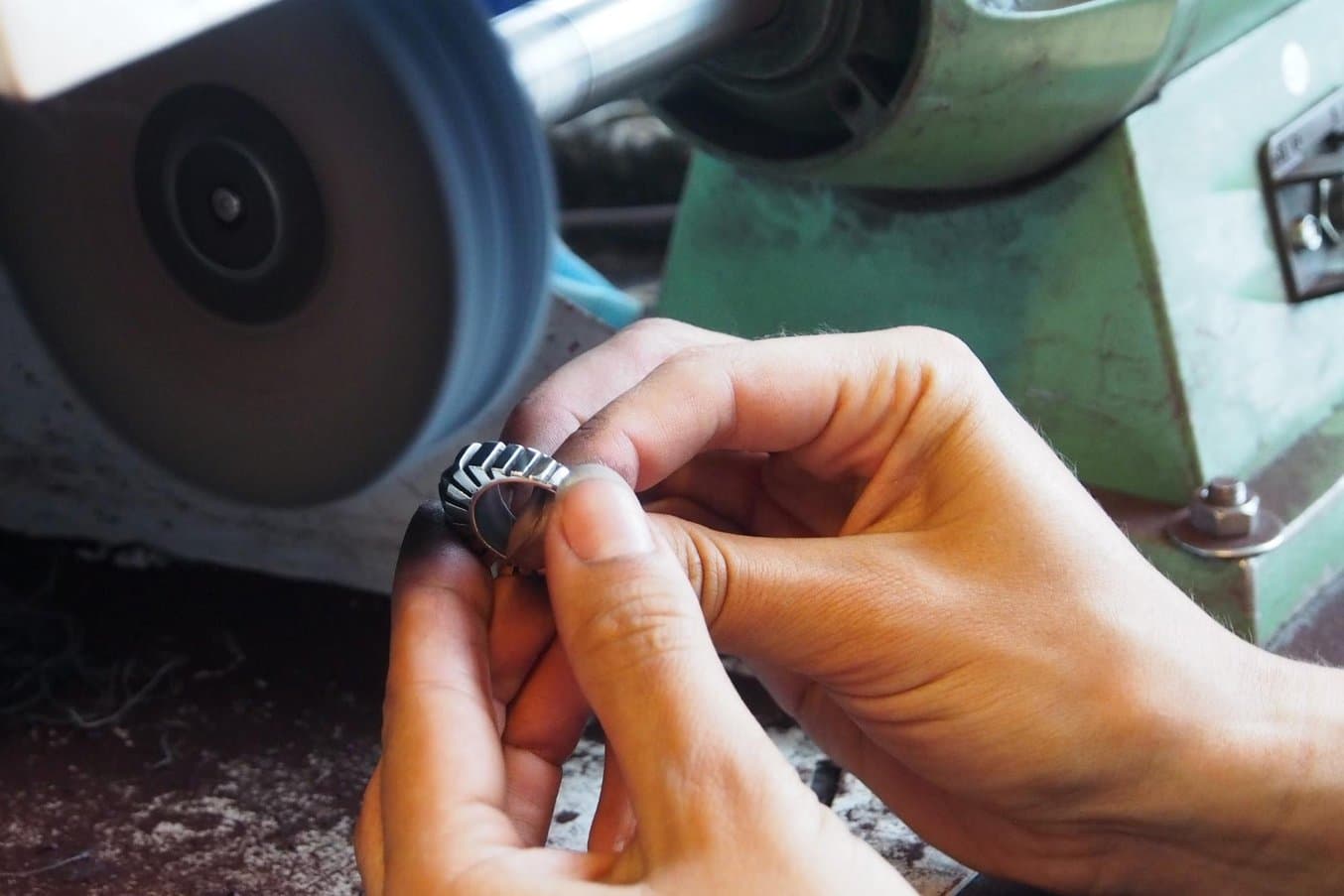
鋳造品にやすりがけや研磨、切削などで仕上げ処理を行う。
ロストワックス鋳造の歴史
ロストワックス鋳造の起源は、文明の起源と同じと言っても過言ではないでしょう。王権の象徴である杖、彫像や家具など、ロストワックス鋳造で作られた工芸品は、イスラエルやベトナム、ナイジェリア、ニカラグア、インダス川沿岸など幅広い地域で見つかっています。ロストワックス鋳造品の最古のものとして知られているのは、6千年以上も前にインダス文明で作られた魔除けです。
彫刻品や織物などの製造で何世紀にもわたって使われてきたロストワックス鋳造ですが、18世紀ごろ、ヨーロッパではピースモールド法が台頭するようになります。19世紀に業界の需要の高まりを受け、その一部はインベストメント鋳造で作られるようになりました。
歯科業界では、金属製のクラウンやインレー、オンレーの製作にロストワックス鋳造が広く使われています。この背景からもわかるように、ロストワックス鋳造の歴史は現代にまで紡がれているのです。
デジタル設計と3Dプリントでロストワックス鋳造を21世紀仕様に
現在、デジタルソフトウェアツールや3Dプリントにより、ロストワックス鋳造の可能性が広がっています。

デジタルワークフローは、原型のデザインから始まる。原型を3Dプリントし、鋳造の準備をした後は、鋳型を作り3Dプリントの型を焼成する。鋳造が完了したがら、完成品に研磨やその他仕上げ処理を行う。
デジタルワークフローでは、デザイナーはCADソフトウェアを用いてデジタルでデザインを制作し、工業品質の3Dプリンタで原型を製作し、ゴム型などで鋳造します。ポジティブパターンの焼成後は、従来のインベストメント鋳造と同じ工程です。
デジタルテクノロジーにより、時間を要する手作業の必要性が大幅に減り、デザイン自体の保存や修正、その後の再現が簡単に行えます。
デジタルテクノロジーを使ったロストワックス鋳造の用途
エンジニアからジュエリーメーカーまで、デジタルテクノロジーによって甦ったロストワックス鋳造の新たな可能性は様々な分野で活用されています。
ジュエリー
ロストワックス鋳造が最初に使用されたのは、ジュエリーや繊細な装飾品の製造でした。しかし精密なデザインと複雑な形状を要するジュエリー用に、手作業でワックス型を製作するには非常に高度な技術が必要です。需要自体やファッショントレンドの遷移が激しいジュエリー業界ではもはや、手作業中心の製作法だけでは市場が変化するスピードに対応するのが難しくなってきています。
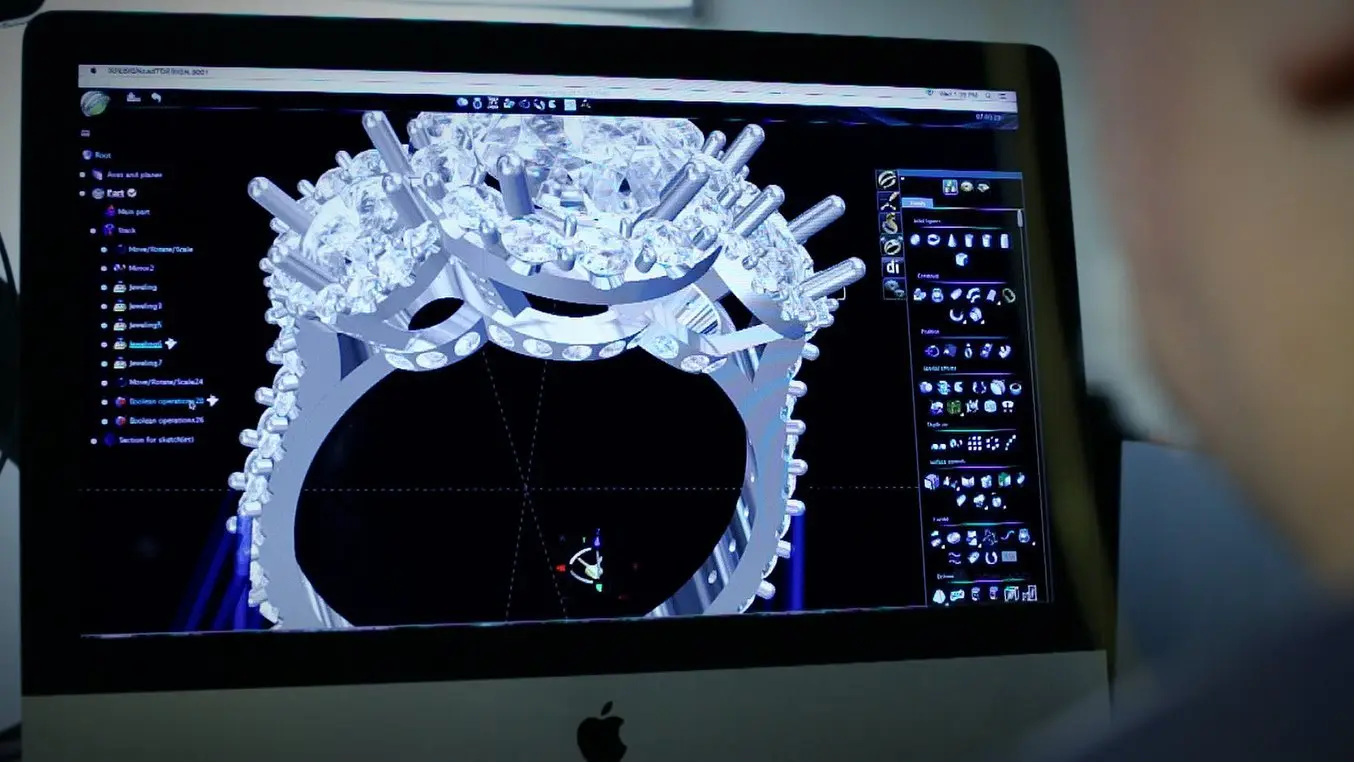
ジュエリーデザイナーは、ジュエリー用のCADソフトウェアを使ってジュエリーをデザインできる。これにより、以前であれば何時間もかけてワックスから慎重に掘り出していた複雑な形状も、より簡単に作れるように。
デジタル設計や高度な材料、手頃な価格で導入できる光造形3Dプリンタにより、ジュエリーメーカーやデザイナーたちが行うコンセプト設計、試作品製作、そして製造方法が変わってきています。

SLA光造形方式3Dプリントで、手作業での掘り出しが難しい複雑な形状を再現。
ジュエリーデザイナーは、ジュエリー用のCADソフトウェアを使ってジュエリーをデザインできます。これにより、以前であれば何時間もかけてワックスから慎重に掘り出していた複雑な形状も、より簡単に作れるようになります。
手頃な工業品質のデスクトップ3Dプリンタを使えば、従来のワックス型と遜色なく鋳造で使用できる原型をあっという間に作ることができます。3Dプリンタにより、形状に制約を設けることなく自由なデザインが可能です。精密に制御されたレーザーにより、繊細なフィリグリー、浮き彫り文字、細かいパヴェ石の設定など、デザインのディテールを驚くほどシャープに捉えることができます。
ジュエリー業界でデジタルワークフローを導入する際に一番の課題となるのが、デジタル設計のスキルとトレーニングです。しかし、ジュエリー業界に新しく入ってくるデザイナーたちは、流れの変化に取り残されないよう、従来の設計手法はもちろんのこと、ジュエリー用のCADソフトウェアや3Dプリンタの使い方を習得しています。
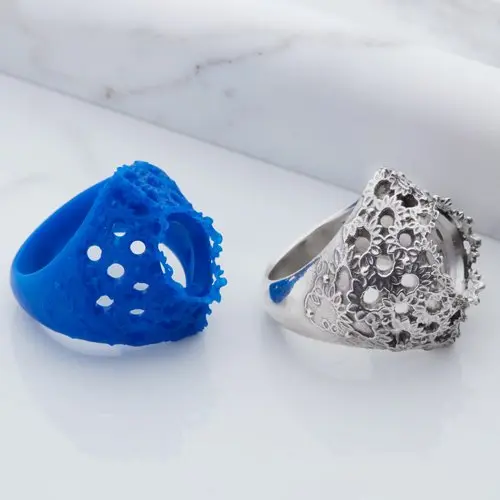
3Dプリント製のジュエリー型の鋳造
本技術資料では、3Dプリント製の型を使って高級ジュエリーを鋳造する方法、ならびにダイレクト・インベストメント鋳造(ロストワックス鋳造)が金型製作技術としてどのように機能するかについて説明します。

歯科医療
ロストワックス鋳造やプレス成形法は、数十年にわたって歯科業界でインレー、オンレー、クラウン、セラミックの製造に使われてきた製法です。合金クラウン、オールセラミッククラウン、部分義歯のフレームワークやその他インプラントの修復に使われてきました。
従来、ワックス原型は、患者の歯に手で押し付けて採得していました。この型は従来通りのロストワックス鋳造の工程と同じく、ツリーに湯道を作って焼成を行います。
デジタル技術を使うと、歯科医たちは口腔内スキャンで患者の歯型をデジタル採得したり、ラボでデスクトップスキャナ用いて物理モデルや印象(インプレッション)を採得したりすることができます。スキャンデータはCADソフトウェアにインポートされ、歯科技工士らが補綴物を設計します。製作した型をワックスに似た材料を使って3Dプリントし、従来のワークフローで鋳造やプレスを行います。
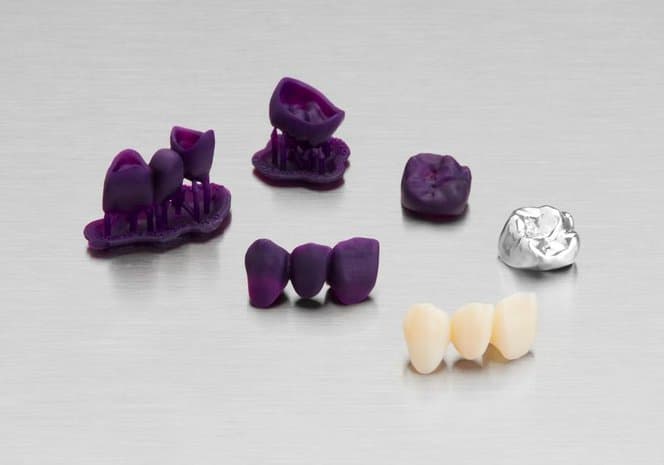
歯科用クラウン、インレー、部分義歯に使う型をワックスに似た材料を使って3Dプリントし、従来のワークフローで鋳造やプレスを行う。
歯科業界では、患者の口腔内構造が印象として採得されるため、デジタル設計による制約はあまりありません。歯科用のCADソフトウェアでは設計プロセスを簡素化でき、従来であれば熟練の技師と複数の手順が必要だった型の製作も3Dプリントで自動化できます。
デジタル技術を使ったロストワックス鋳造なら、アナログとデジタルの長所を最大限活かし、信頼性が高く一貫性のあるデジタルワークフローと、誰もが簡単に扱える機器を用いて高精度な型を作れるようになります。
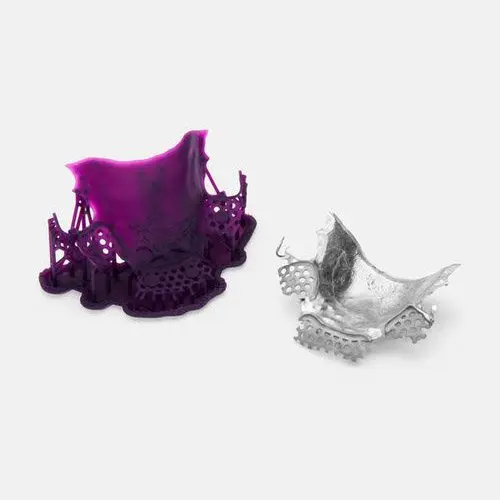
歯科用のCastable Waxレジン:効率的でコストパフォーマンスの良い製造を
本ウェビナーでは、固定製修復物を内製する方法、クラウン、ブリッジ、取り外し可能な部分義歯(RPD)をデジタル製造する際のワークフローのヒントをご紹介しています。
製造業
高い寸法精度を持った金属部品の大量生産が必要な業界では、鋳造はいまだにコスト効率が良く生産性のある製造手法です。航空宇宙、自動車、医療機器業界などで欠かせない部品が製造されています。
これまで、ダイレクトインベストメント鋳造(ロストワックス鋳造の産業用途)で使う型は、大量生産の必要がない場合は手作業で掘り出すか切削で作るのが一般的でした。3Dプリントであれば、エンジニアや鋳物工場が直接型を製作することができ、鋳造による製造時間を短縮したり、従来のDFM(Design For Manufacturability)による制約下では実現できなかった設計の自由度が得られるようになります。
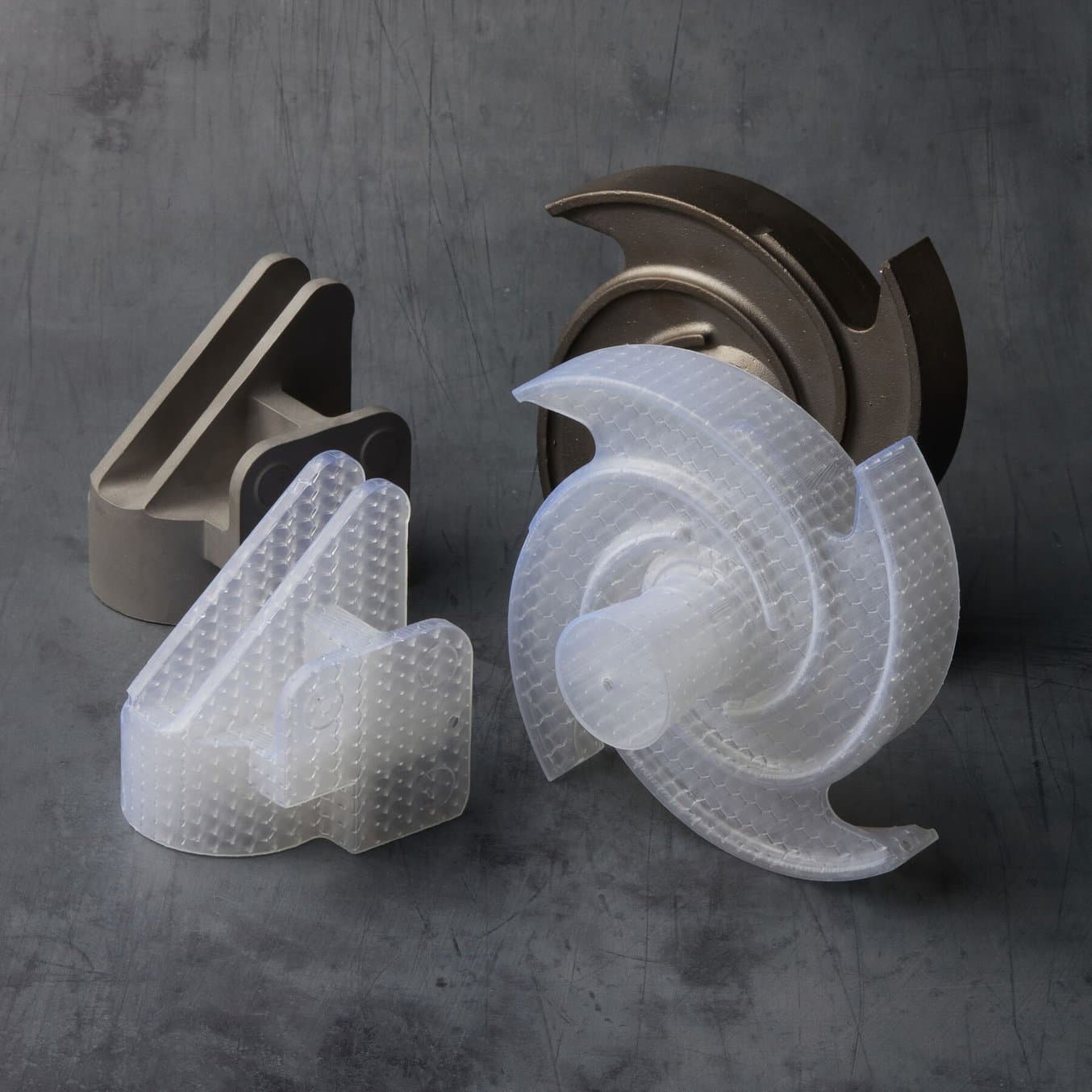
高精度・高効率な鋳造を実現 3Dプリントを活用した金属鋳造
本ウェビナーでは、実績ある複数の鋳物工場が、Formlabsの3Dプリンタで造形した3Dプリント製の原型を使って金属部品の鋳造に成功した方法を解説します。FormlabsのClear CastレジンやMaterialise Magicsのラティス構造生成ソフトウェアを従来の鋳造方法に組み入れることで、金属部品の品質を向上させながら、コストや製作期間を削減した方法をご覧いただけます。
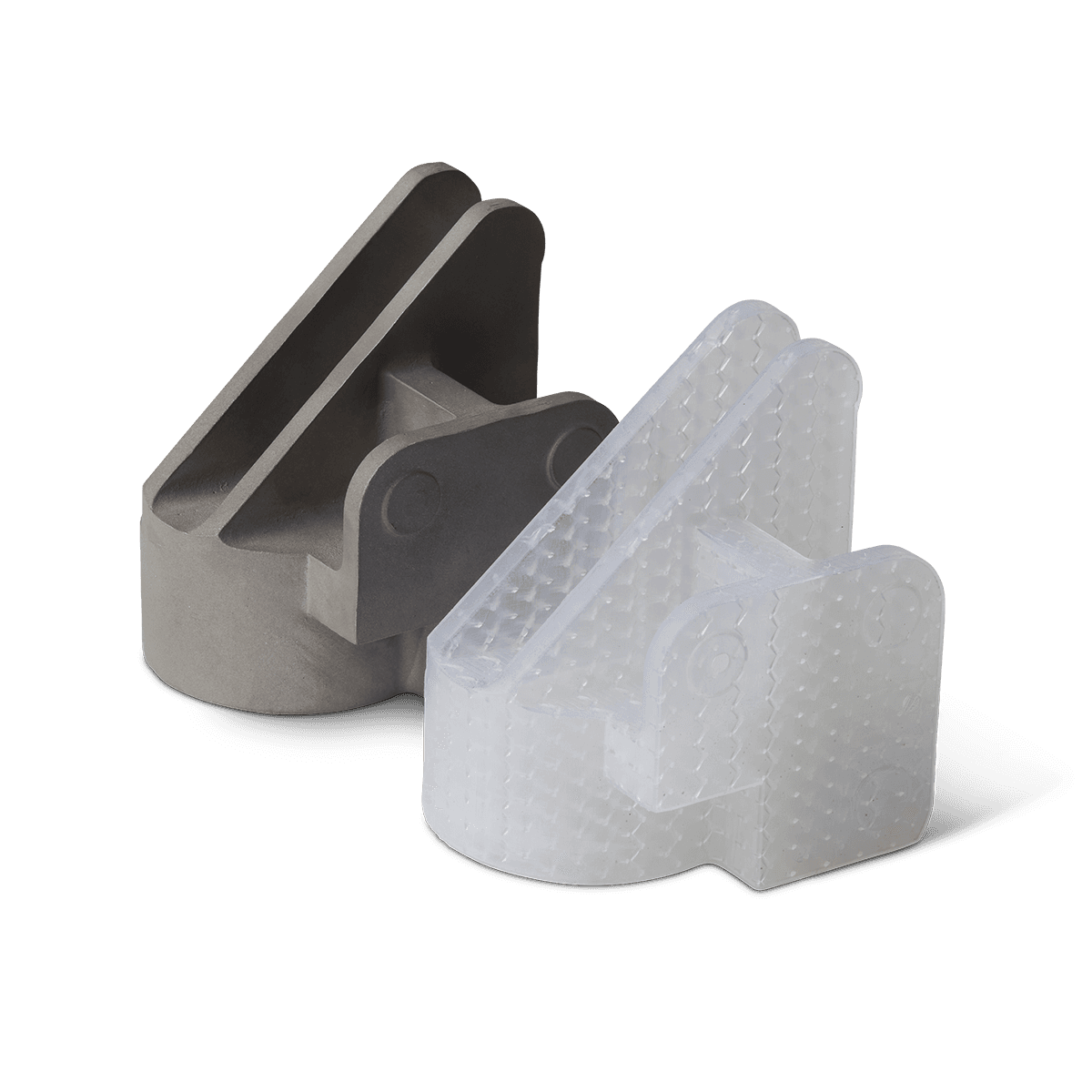
工業品質のインベストメント鋳造を3Dプリント製の原型で Formlabs Clear Castレジンの活用法
本技術資料では、実績ある複数の鋳物工場が、FormlabsのSLA光造形プリンタで造形した3Dプリント製の原型を使って金属部品の鋳造に成功した方法をご紹介します。

True Castレジンを使った3Dプリントは既存の鋳造手順に組み込みが可能で、厚さ5mmまでのジュエリー用部品、エンジニアリング用部品を製作できる。
デジタルツールによって進化したロストワックス鋳造は、テクノロジーと伝統は必ずしも相反するものではないことを私たちに教えてくれます。技術を適切に導入すれば、特注ジュエリーから大量生産が必要な自動車部品に至るまで、様々な用途で高品質なパーツを製造でき、驚くほどの効率性とデザインの自由度が得られます。
Formlabsの光造形3Dプリンタの詳細またはその他のご相談については、Formlabsまでお気軽にお問い合わせください。