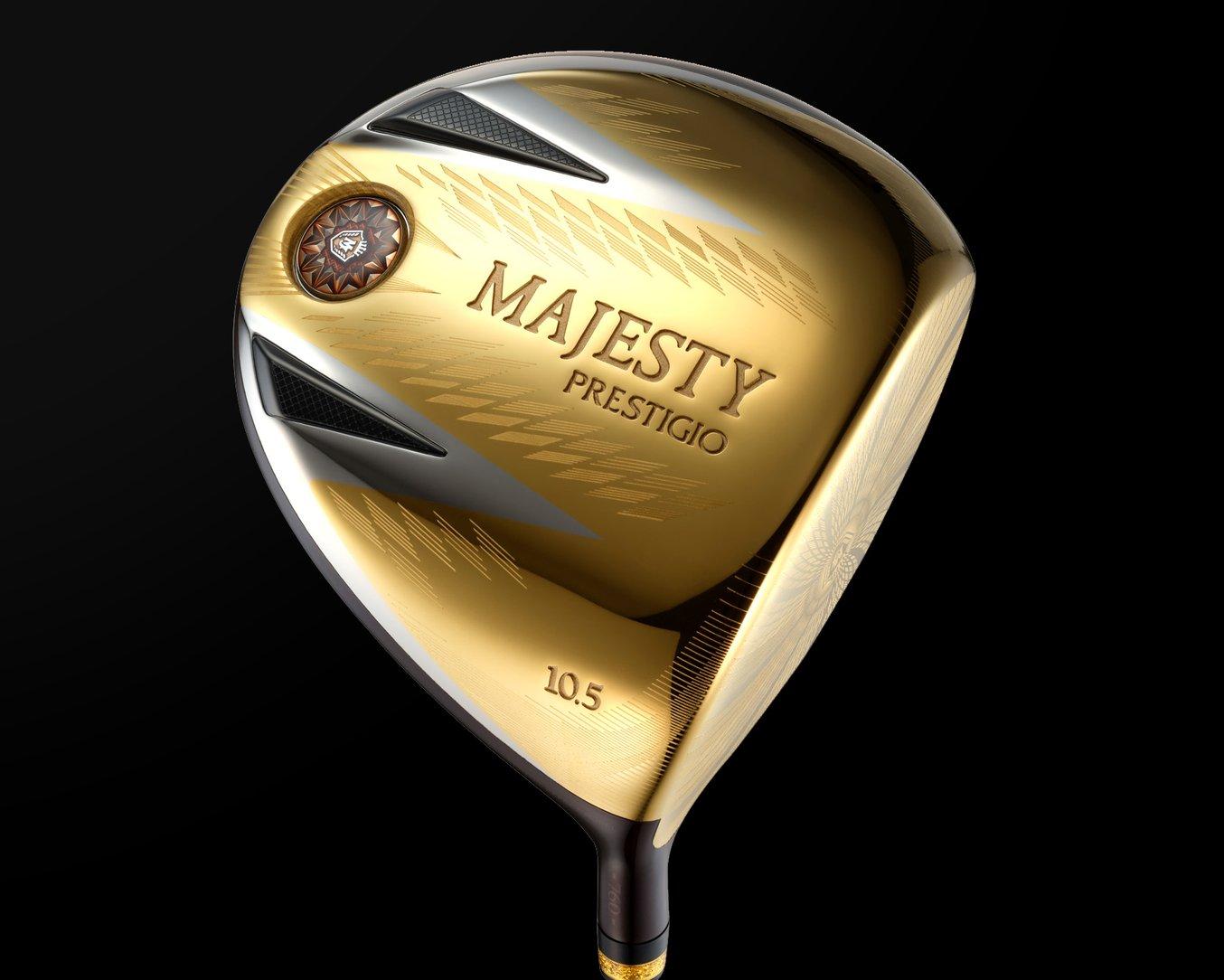
オーナーに最上級の満足と究極の贅沢をもたらすMAJESTY PRESTIGIO 13 DRIVER。
その名の通りのセレブリティ感溢れるデザインはFuse 1+で試作され、確認される。
User Data:
- ユーザー:マジェスティ ゴルフ株式会社(ラグジュアリーゴルフ用品製造販売)
- 使用プリンタ:Fuse 1+ 30W(SLS方式)
- 使用材料:Nylon 12パウダー
- 用途:形状、デザイン、構造確認用試作
- 販売代理店:Brule Inc.
機能だけでなくその付加価値を確認する
一目見た瞬間、違いを歴然と記憶に焼き付ける美しいゴールドやブラックのラグジュアリーなクラブ。マジェスティ ゴルフ株式会社が生み出すのは「最上級の満足と究極の贅沢」をもたらすゴルフ用品だ。世にゴルフ用品メーカーは数あれど、一般的なゴルフ用品はまずスポーツギアとして存在し、それ故に機能性を最優先にプロダクトデザインが生み出される。スタイリッシュなものは存在するが、そのまま調度品やオブジェのように飾るに耐える存在感は、美術品としても高い価値を示す日本刀にも通じるものがあるだろう。
同社のブランド「MAJESTY」のゴルフ用品は、単にプレイするためだけでなく、このプロダクトを所有し、これらMAJESTYのゴルフ用品と共にラウンドを楽しむというライフスタイル、換言すれば明らかな付加価値をオーナーに提供していると言える。そしてその付加価値を創出する上でキーとなるのはデザインだろう。ベースとなる各種クラブの形状だけでなく、個々のシリーズごと、番手ごとの形状やサイズの違いに加えてシリーズや番手を通しての形状やサイズのバランスも非常に重要になるとマジェスティ ゴルフ株式会社 エンジニアリングチームの荻野 裕貴氏は言う。
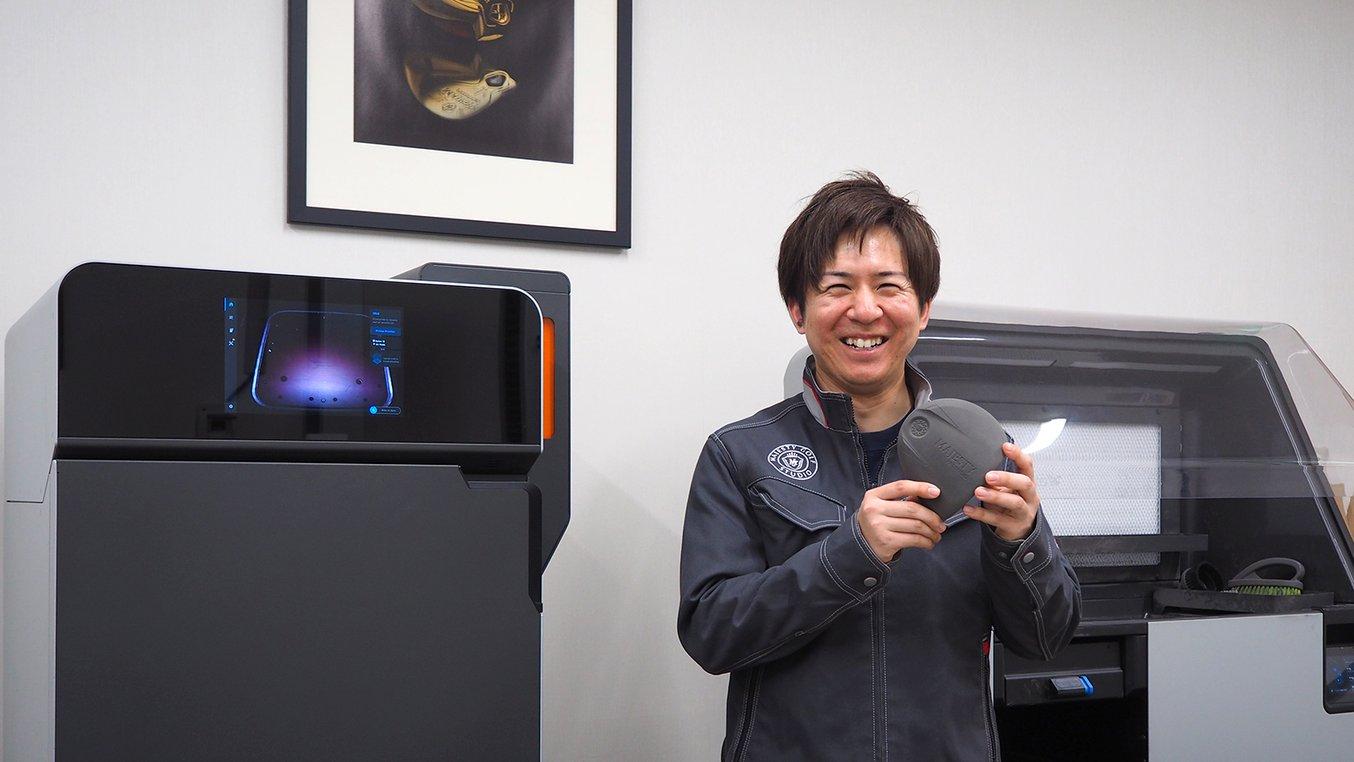
MAJESTY PRESTIGIO 13 DRIVERの試作品を手に笑う
マジェスティ ゴルフ株式会社 エンジニアリングチーム 荻野 裕貴氏。
ラピッドプロトタイピングに20年以上前から3Dプリンタを活用
MAJESTYのプロダクトは、先述のようにただそこにあるだけで異彩を放つ、美しいものだ。しかし「最上級の満足と究極の贅沢」という同社ブランドコンセプトが示すように、ゴルフクラブとしての機能も言うまでもなく重要だ。そこで同社は20年近く前から3Dプリンタを導入し、ヘッドの形状、デザイン、そして構造を試作し、検証を行ってきたという。同社の製品開発サイクルは非常に速く、新製品発売から1ヵ月後には次のモデルの開発に着手し、ウッドだけを取っても1シリーズでドライバー、フェアウェイウッド、ユーティリティとも呼ばれるハイブリッドそれぞれに4種の番手が存在し、しかも男女用でプロダクトが異なる。中韓をはじめ海外でも人気を博す同社製品は、当地限定モデルも提供するため更にラインナップは広がる。
開発の手順はまず、基本形状の設計を固め、そこにそのシリーズのデザインを落とし込んでいく。構造面ではドライバーで3パターン程度準備し、そこから各要件を満たし得るもの1つに絞り、そこから板厚などの詳細を詰めた後、製品としてのデザイン決定後に金型を起こして鋳造で同社が「S1」と呼ぶ最初のサンプルを作成する。それを基に量産に向けて細部の微調整を重ね、4回目のサンプルであるS4辺りで量産用の設計が確定する。こうした開発プロセスをRP(ラピッドプロトタイピング)で短縮するため20年以上前から石膏を材料とする3Dプリンタを活用してきた同社は、装置の老朽化や材料の高騰からプリンタの入れ替えを検討し、その結果2023年11月にFormlabsのSLS 3DプリンタFuse 1+ 30Wを導入した。そもそもの造形方式を含めてインクジェット方式なども比較検討しながら3Dプリンタの選定を行った荻野氏は、Fuse 1+を選んだ理由として、1,000万円程度の手頃な導入価格、そしてプリントの仕方がこれまで使用していた石膏タイプに近い点を挙げた。「Fuse 1+の導入コストは他のSLSと比べて非常にリーズナブルで、消耗品の品目が少なくランニングコストまで含めて低コストで運用できる新しいものという条件に完全に合うものでした」と荻野氏は語る。
「Fuse 1+の導入コストは他のSLSと比べて非常にリーズナブルで、消耗品の品目が少なくランニングコストまで含めて低コストで運用できる新しいものという条件に完全に合うものでした」
荻野 裕貴氏 マジェスティ ゴルフ株式会社 エンジニアリングチーム
微妙な感覚と手にする人のメンタルを左右するヘッドのデザイン
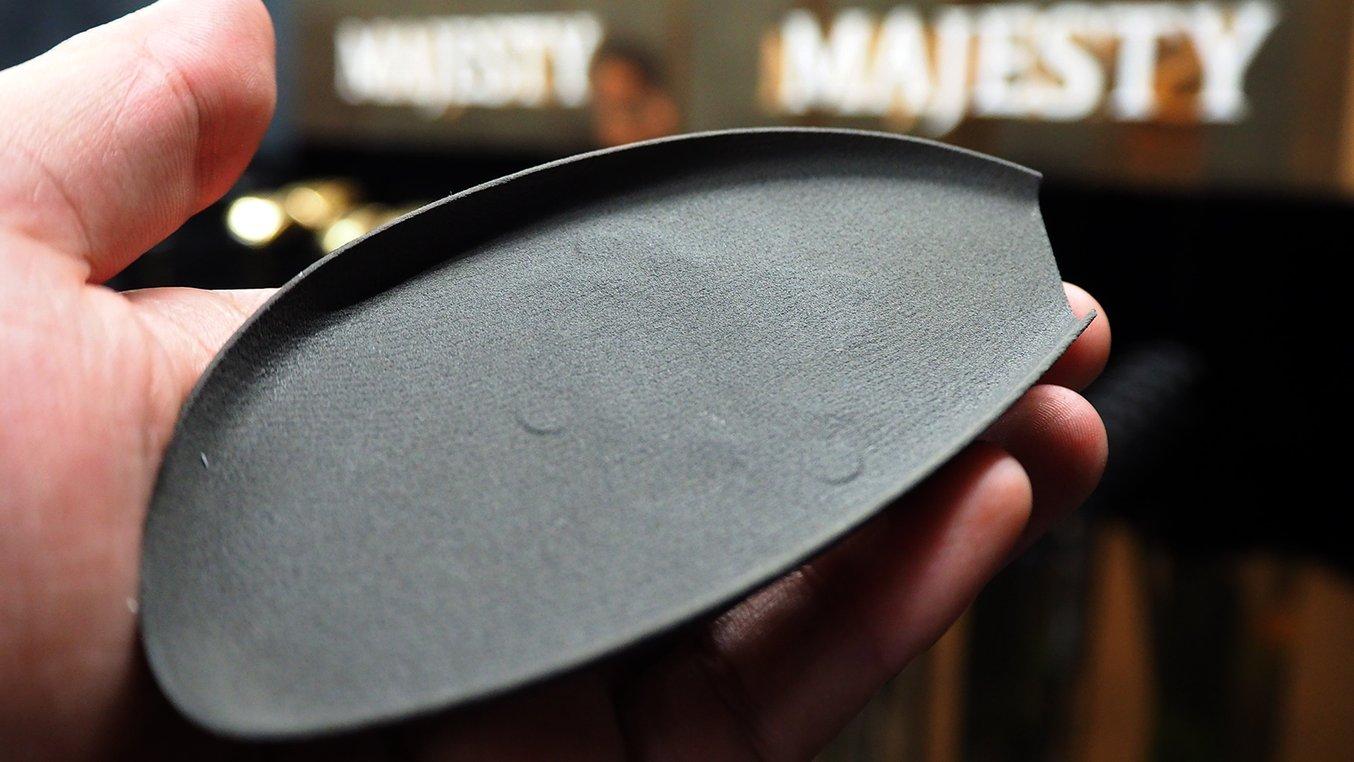
別パーツとして製造するドライバーフェースの裏側。渦を巻くような微妙な凹凸形状は
スウィートスポットにも関係し、飛距離にも関わる。石膏プリンタでは表現できなかったという。
同社ブランドMAJESTYは、その価格帯からもシニア層に多くの顧客を持つ。そのためヘッドの重量は他社製品より軽量に設計されているが、重量は飛距離や手にした時に感じる高級感にも影響を及ぼす重要な要素だ。同ブランドは軽量でありながらも高級感や飛距離を創出すべく、ヘッドが軽量な分シャフトを長めに取ってヘッドスピードを出しやすくする等、随所に独自の創意工夫を加えている。形状面では近年、「投影面積」と呼ばれるアドレス時に見下ろした際のヘッドの大きさが重視される傾向があるが、これはヘッドが大きく見えた方がプレイヤーの安心感を醸成し、結果ミスショット自体が減少するという「メンタルのスポーツ」と呼ばれるゴルフ特有の理由による。同社はこの点にも配慮し、各シリーズや番手ごとに試作を行い、実際のサイズ感を確認する。石膏の白色と比べてNylon 12パウダーのグレー色はヘッドが締まって見え、製品がよりイメージしやすく造形品の社内評価も非常に高いという。
構造面ではヘッドとは別パーツとなっているドライバーフェースの裏面には、非常に微妙な渦巻き状の凹凸形状をデザインし、ヘッド左右の慣性モーメントや飛距離に配慮していると荻野氏は言う。この微妙な凹凸の表現は以前使用していた石膏プリンタでは表現できないものだった。また、ドライバーヘッドの板厚は、軽量化のため最も薄い箇所で0.4mmと他社製品と比較しても類を見ないほどの薄さであるという。しかし3Dプリンタを長年活用する同社では、デザインや構造を確認することが目的の試作時は、量産時同様の板厚で製作する必要がないことから、無理に量産時の設計を試作品設計に適用することなく2mm程度の板厚で制作することで開発スピードを向上している。
また、ドライバーヘッドは開発時に重量が確定しており、その重量を下回るよう開発が行われる。その差分はソールと呼ばれるヘッドの底部に重量体を設置することで調整され、尚且つシリーズごとのコンセプトに沿ってヘッドの重心位置を重量体の設置場所で決定する。この重量体はねじでヘッドに固定され、チップと呼ばれる化粧パーツで覆い隠す事になるが、ねじによる重量体の固定やチップの嵌め込みはFuse 1+導入前は3Dプリンタ製の試作品では表現できず、確認ができなかったという。
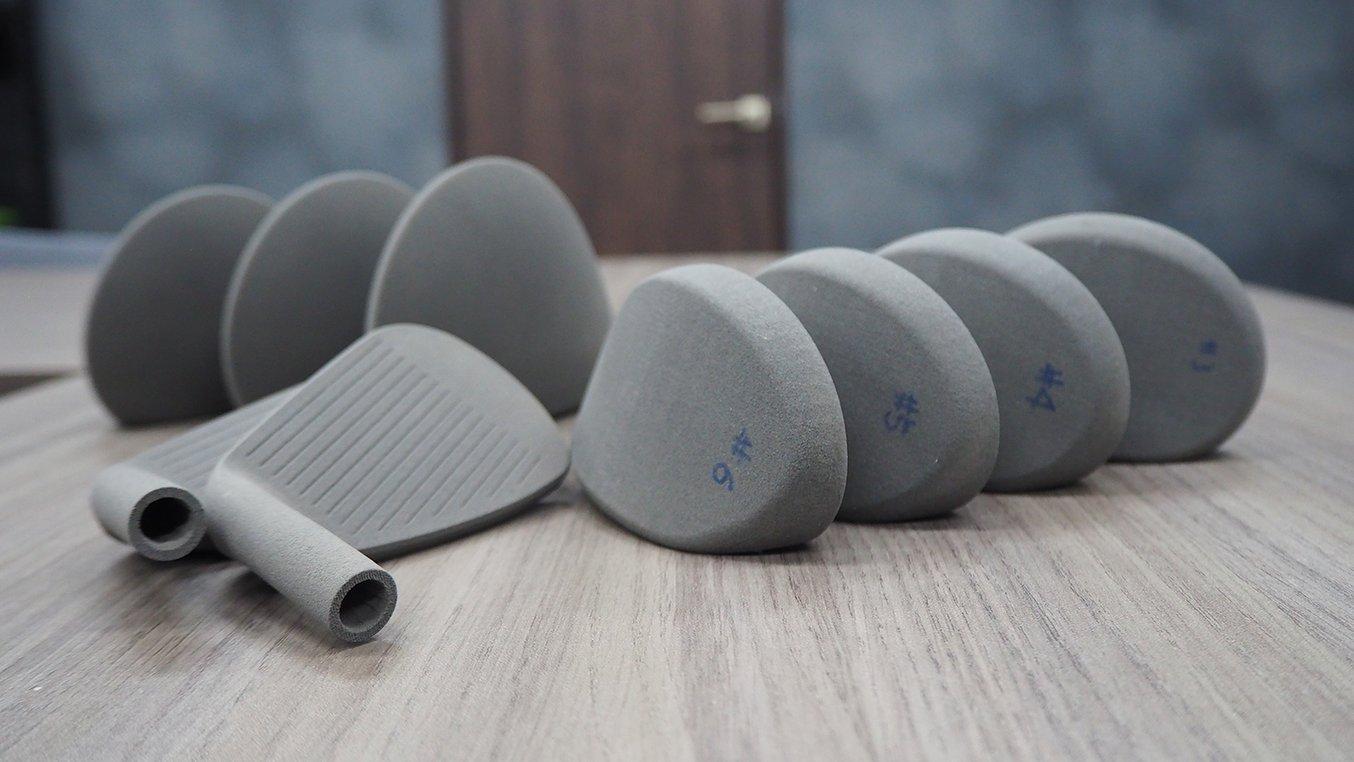
Fuse 1+ 30Wでの形状確認用試作品。
導入直後から問題なく簡単に使えたFuse 1+
このように詳細に及ぶ確認をFuse 1+ 30Wによる試作品で行う荻野氏に、プリントで苦労したことはないかと質問したところ、困ったことは特に無かったという。CADでデザインを進めている段階で2日に1回のペースでプリントを行うという荻野氏は、無料造形準備ソフトウェアのPreForm上でモデルをレイアウトする際にビルドチャンバー壁面からの輻射熱の影響を受けないよう、なるべく端に寄せすぎないことが唯一気を付けている点と荻野氏は言う。
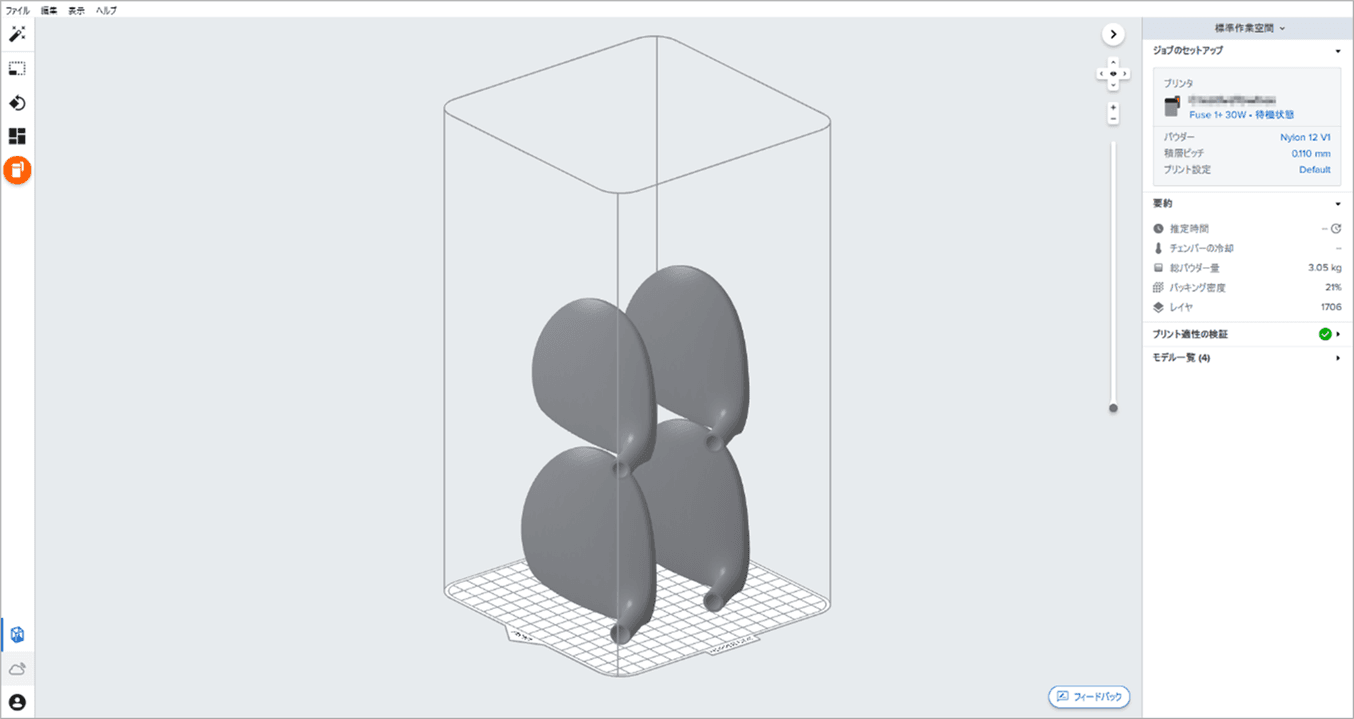
実際のPreForm画面。SLSでは高さ方向に積み重ねてプリントできるため、
複数のモデルを一度にプリントできる。この特徴により小ロット量産にも対応可能だ。
石膏プリンタとの比較という点では、荻野氏は作業場に舞う粉末を挙げる。「石膏の時はすごく粉っぽく、一度プリントしただけで部屋中に粉が舞っている状態でしたが、Fuse 1+に入れ替えてからは部屋の中に粉が舞うこともなくなり、これは凄く良い点だと思っています」と荻野氏。造形品質では、プリント品が壊れないという強度面に大きな違いがあるという。「石膏でのプリント品はネックが折れてしまうので、実際にシャフトを挿し込むことができません。試作品は商談で使うこともあるので、プリント品が壊れてしまうのは色んな意味で良くないのですが、Nylon 12パウダーでは造形品が壊れることもなくなりました。石膏プリンタでは細かいパーツや薄手のものは作れなかったのですが、Fuse 1+では問題なく対応できています。」
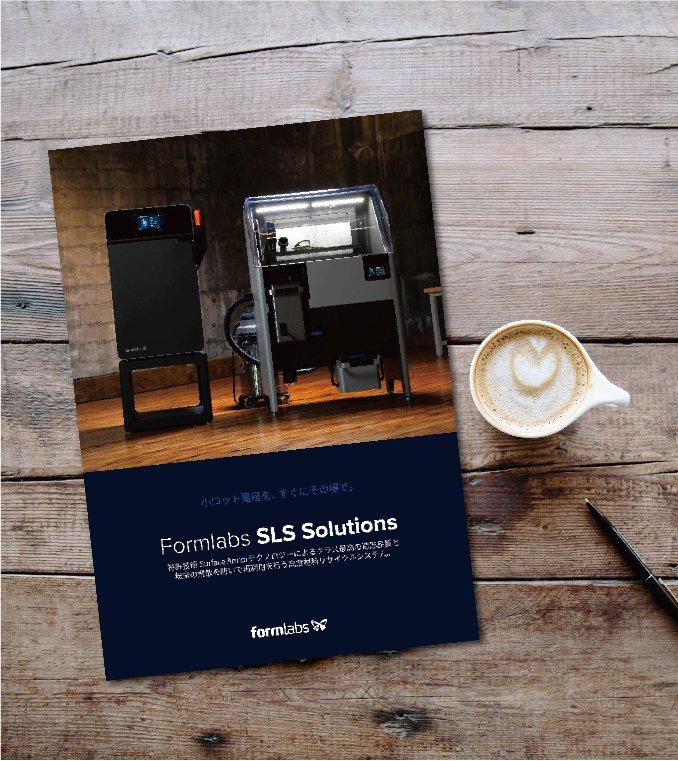
Formlabs SLS Fuseシリーズ総合カタログ
本総合カタログでは、Fuseシリーズの製品や特許技術の解説、各材料の詳細や使い方、そして国内外の活用事例等すべての情報を1冊にまとめてご紹介します。
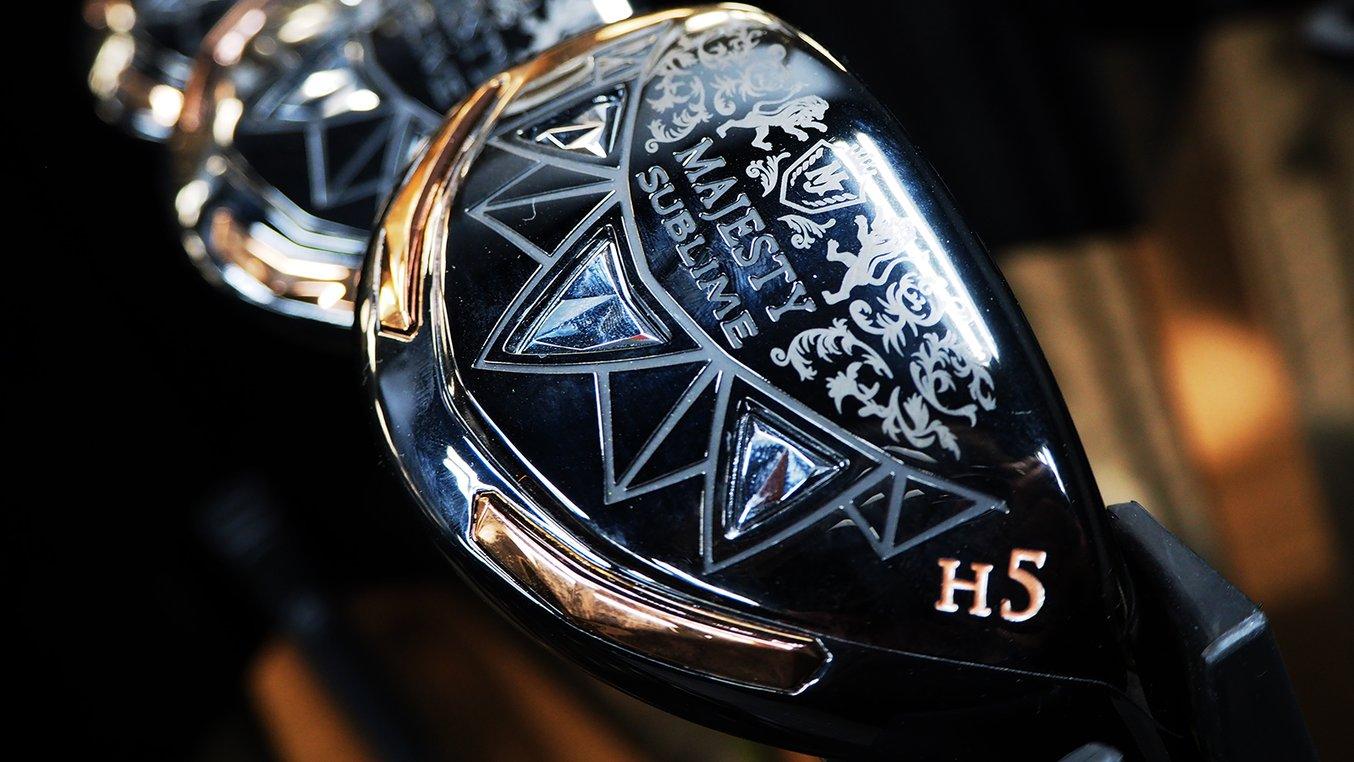
多様なシリーズを誇るMAJESTYの製品。3Dプリンタによる開発期間短縮は重要だ。
設計の制約から自由に−次のチャレンジ
Fuse 1+を活用した今後の展望について、荻野氏はこれまで金型を起こして製作するS1のサンプル段階まで確認ができなかった重量体を隠すチップの嵌め込みなど噛み合わせ部分の設計確認もFuse 1+で行えるようにしたいと語る。上述のようにねじで固定する重量体にフタをする役割を持つチップなど、嵌め込み部品の寸法を検証する作業は金型を起こして製作するサンプルが上がるまで行えなかったが、これをFuseで行えるようになればS1段階でかなり精度の高いサンプルが製作でき、通常S4辺りまで行ってきたサンプル製作をS3やS2レベルで完了できる可能性があるという。
製造業に関わる人なら誰もが知る通り、金型製作には相当な時間とコスト、そして労力と精神力が求められる。一般的には金型製作には1〜2週間を要するため、このサンプル製作工程を短縮できればその分の期間を更なる品質向上やプロモーションに充てることができ、販売戦略の観点からも大きなアドバンテージを得ることになる。反対に、このサンプル製作期間が思うように進まず、トラブル等で遅延が発生した場合は最悪のケースで発売延期に至る可能性もある。Fuse 1+は既に国内外で実製品の小ロット量産で採用されている実績もかなり増加しているだけあって、かなりの精度でプリントが行える。その利点を活かして高精度な試作を行ってよりハイレベルな検証を3Dプリントで完了できれば、もっと柔軟に、もっと迅速に製品開発が進められることを同社の事例は示している。
「Fuse 1+でこういうことができると、新しいことにもどんどん挑戦しやすくなりますよね。S1段階まで進んだ時に、ここまで形にしちゃうともう変更できないよね、ということも無くなります」
荻野 裕貴氏 マジェスティ ゴルフ株式会社 エンジニアリングチーム
単なるゴルフクラブではなく、他に無い付加価値を内包したゴルフクラブを開発するMAJESTYの製品は、オーナーが目にすることのない見えない部分も緻密にデザインと検証を繰り返して生まれている。それは見栄えのするプロダクトとは対照的な地道な作業だ。しかし世の華やかなもの全てが、こうした目に見えない努力の上に成立していることを考えると、同ブランドのコンセプトである「最上級の満足と究極の贅沢」が、決して“軽い”ものではないことがわかるだろう。