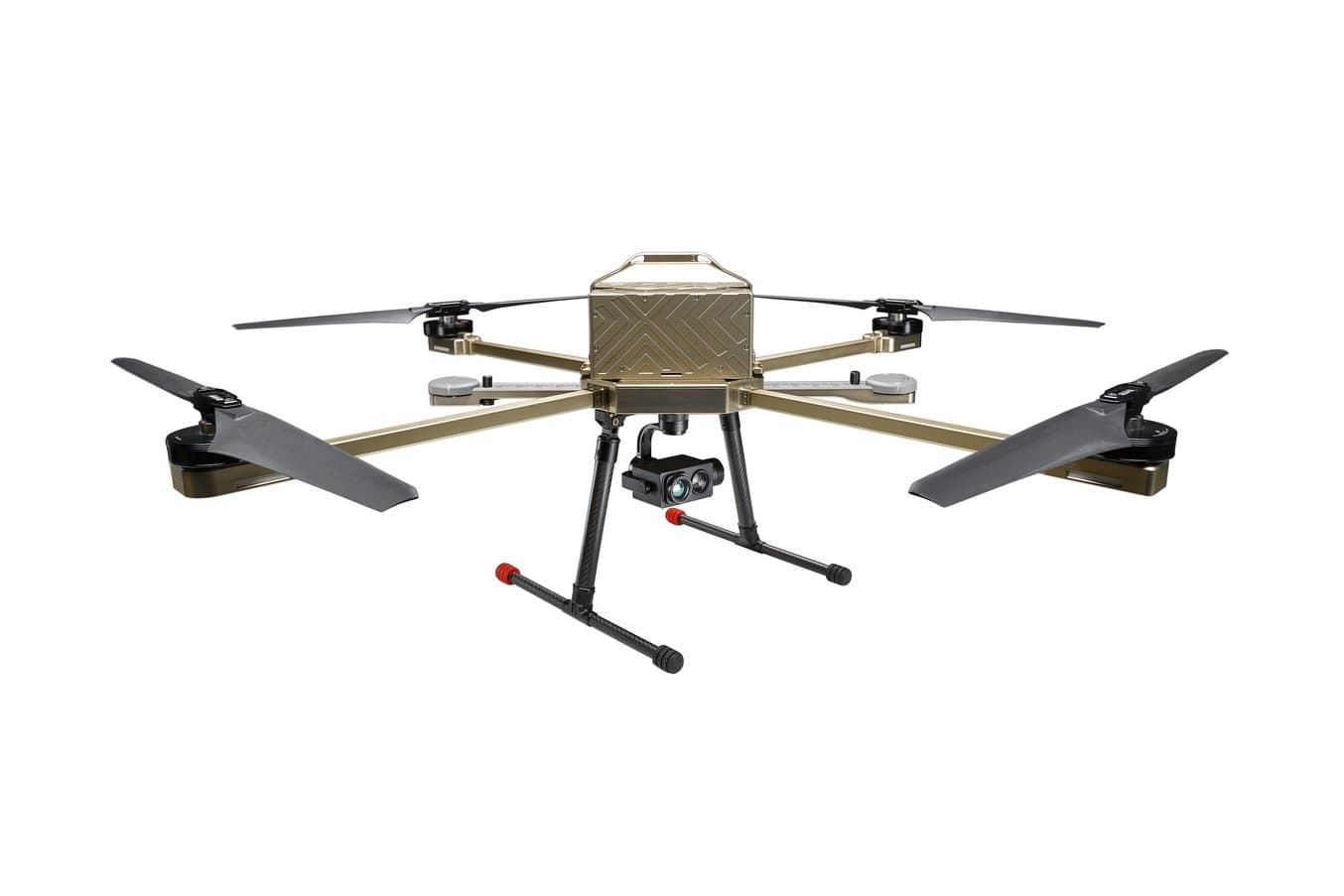
昨今、自然災害、軍事侵攻、沈没船、墜落機などの衝撃的な画像や映像が世界の注目を集めています。この時に目にする映像は、比較的新しい技術であるドローン、つまり無人航空機(UAV)で撮影されたものかもしれません。ドローン技術の進歩に伴い、メーカー各社はドローンの飛行距離、飛行速度、最大積載量の限界に挑み続けています。
南アフリカに拠点を置くドローンメーカーのNextechは、FormlabsのSLS(粉末焼結積層造形)方式3Dプリンタを使用して、さまざまな業界の顧客向けに高性能のカスタムドローンを製造しています。頑丈で実製品用としても使用できる品質を備えたSLS 3Dプリント製部品により、Nextechは合理的なワークフローで設計、試作品製作、製造を行えるようになりました。
今回、同社でメカニカルデザインエンジニアを務めるLiam Kroone氏に、ハイブリッドワークフローの強み、そしてSLS 3Dプリントを導入したことで激戦市場で今の地位を確立することができた背景を教えていただきました。「作業工程に3Dプリントを導入することで、クライアント個別の要求に応えながら、新製品の開発や設計改良がより迅速に行えます」とKroone氏は言います。
本記事では、NextechがSLS 3Dプリントを活用して以下を実現した様子をご紹介します。
-
数百万ドルもするCNC加工機をFuse 1+ 30W 1台に置き換え
-
3Dプリント製の成形型を使ってドローンの翼の先端を炭素繊維材料で製作
-
機械加工、炭素繊維材料、SLS 3Dプリントを組み合わせることでドローンの重量と強度を最適化
ドローンの課題
無人航空機は、主に軍事組織の監視・戦術任務目的で数十年に渡り使用されてきました。その一方で、コストが高いことが足枷となり、農業や野生生物管理、気候科学などの業界では、ドローンの普及が制限されています。予想される気温や気象条件、カメラやその他積載物の種類、燃料源から目標到着地点までの距離など、顧客の用途によって求められる要件も異なります。ドローンの部品には大量生産品が使用されることが多いものの、細部の違いによって必然的にある程度のカスタマイズが必要になります。
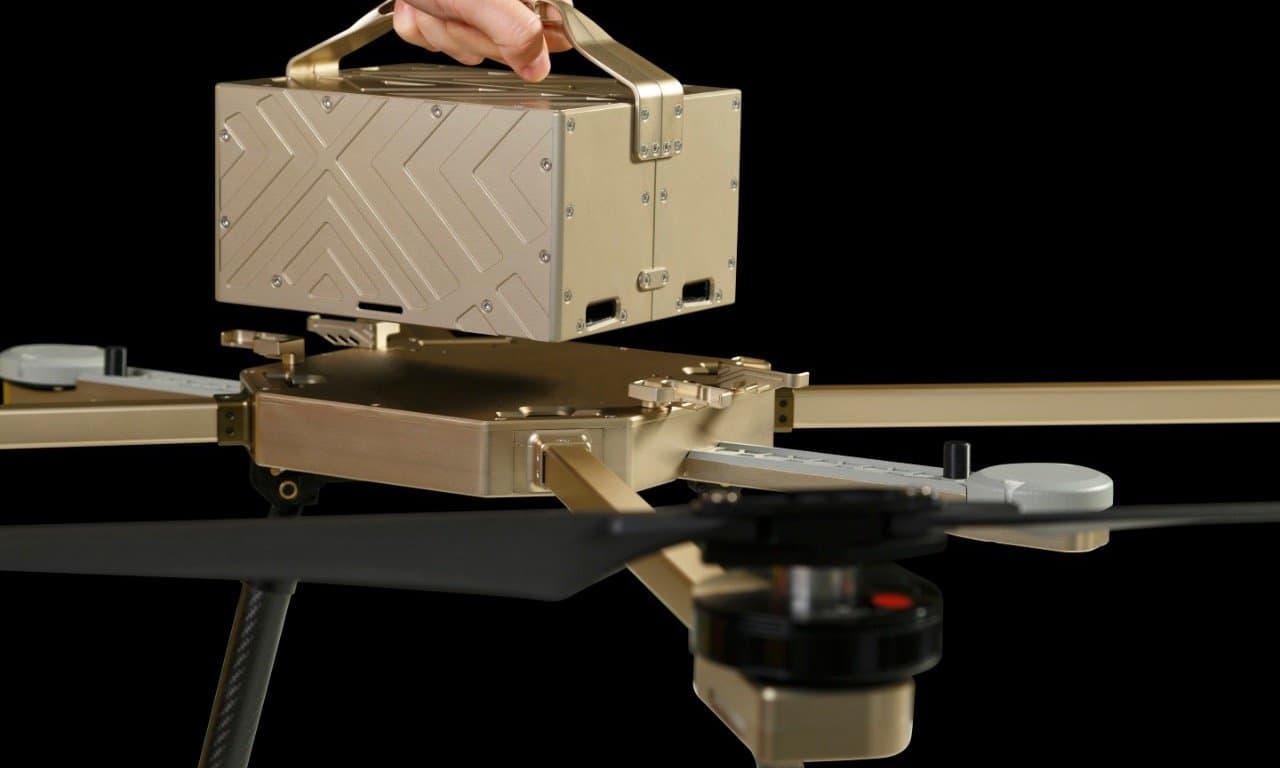
ドローンの部品の中で最も重量が嵩むことの多いバッテリーケース。Nextechは3Dプリントを活用して他の部品を軽量化し、強度や最大積載量を犠牲にすることなくさらに遠距離での飛行を可能にした。
従来の製造技術では、このようなカスタマイズは困難でした。金型の製作や機械加工、ウォータージェットやレーザーで切断するなどの方法は、特に部品形状が複雑な場合はコストがかかります。一方、3Dプリントなら複雑形状の部品やカスタム部品をメーカーが手頃な価格で製造できるようになります。ただし、そのためには適切な3Dプリント方式と材料の選定が必要で、そのことが3Dプリントの普及が限定的である理由の一つにもなっています。Fuse 1+ 30W SLS 3Dプリンタの導入により、Nextechは試作品を迅速に製作し、顧客からのフィードバックを反映した試作・検証プロセスの反復で設計を改良し、手頃な価格でカスタム部品のバッチ生産を実現しています。
SLSの社内導入
Fuse 1+ 30W SLSプリンタを導入する前、Nextechでは試作段階で部品の3Dプリントや加工を外注していました。「地元の大学に依頼し、工業用の大型EOSプリンタで小型部品をバッチで3Dプリントしてもらっていたんですが、製作期間が何週間もかかっていました」とKroon氏は言います。
3Dプリンタを社内導入したことで、開発スケジュールが短縮され、顧客ともより緊密に連携できるようになりました。「顧客向けにカスタム部品を作る場合、高速で試作品製作をする必要があります。同時に、カスタム部品なので形状が繊細かつ複雑で、仕上がりを高品質にすることも重要です。ブラケットを追加して強度、手触り、重量を検証したり、絶縁性を高めるためにガスケットを追加してフィット感や使用感を検証し、高品質な完成品を顧客に送れるようにします」
部品を外注していた時は、このように迅速なペースで試作・設計・検証の反復を行うことは不可能でした。このプロセスに数日・数週間もかけていると、納期までの猶予が短くなり、実施できる機能検証の数も制限されてしまいます。「社内に3Dプリンタがあれば、製造量を大幅に増やしながら、材料の使用量も最適化できます。射出成形用の金型の製作は非常に高価で時間もかかりますが、3Dプリントがあれば金型レスでプラスチック部品を製作できます」とKroon氏は言います。
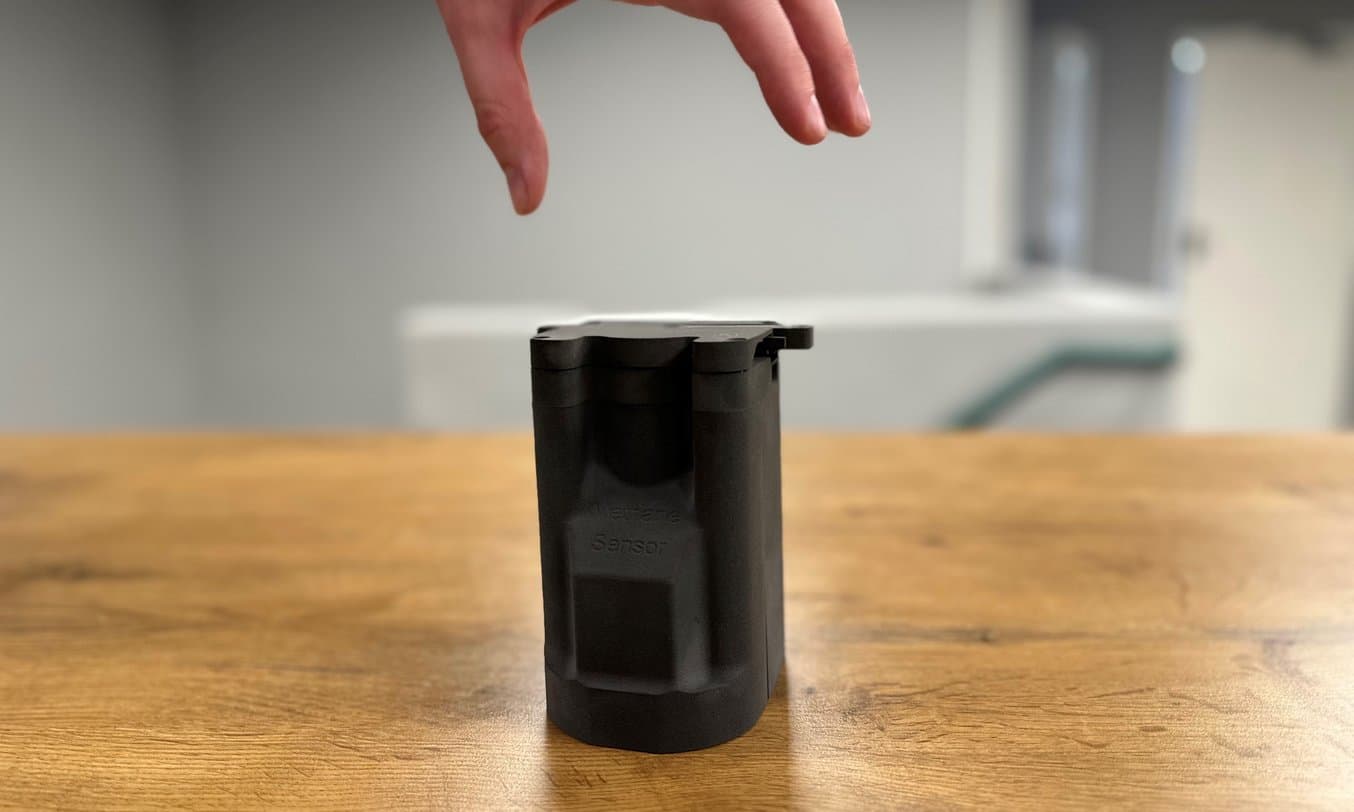
Fuse 1+ 30W SLS 3DプリンタにてNylon 12パウダーを使って3Dプリントしたカスタムデザインのメタンセンター。内製化により設計・製造コストを削減した。
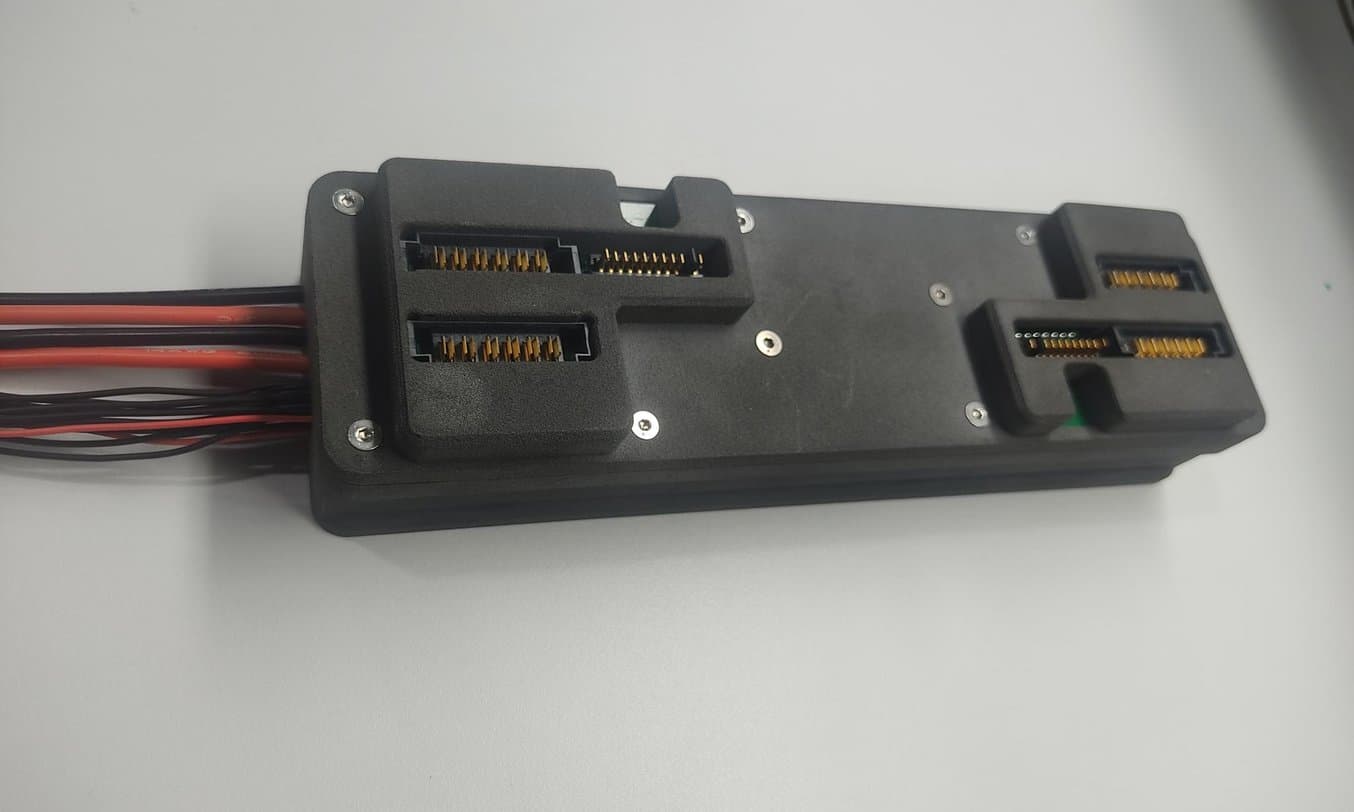
カスタムデザインのバッテリー充電器もFuse 1+ 30WにてNylon 12パウダーで3Dプリントしたもの。内製化により、Nextechはこれまでよりも顧客の設計要件により機敏に対応できるようになった。
補完技術で複雑な部品を製作
農業、環境、野生生物調査用の多様なカメラやセンサーなど、顧客によって搭載機器は異なります。また、ドローンのフレームにそれらを固定するためのカスタムブラケットも必要です。このブラケットはプロジェクトごとに異なり、長距離飛行によって熱を持つ可能性のある燃料源から積載物を遠ざけたり、異なる角度で固定したりします。強度や耐久性が求められるこれらブラケットの設計・製造に、NextechはSLS 3Dプリント、複合材料、加工といった様々な技術を組み合わせて対応しています。同社の強みは、技術を代替としてではなく、補完するものとして最適化できることです。
「従来の加工製法とSLS 3Dプリントを融合させることで、あらゆるものを製造できる時代が来ると感じています」
Nextech メカニカル設計エンジニア、Liam Kroone氏
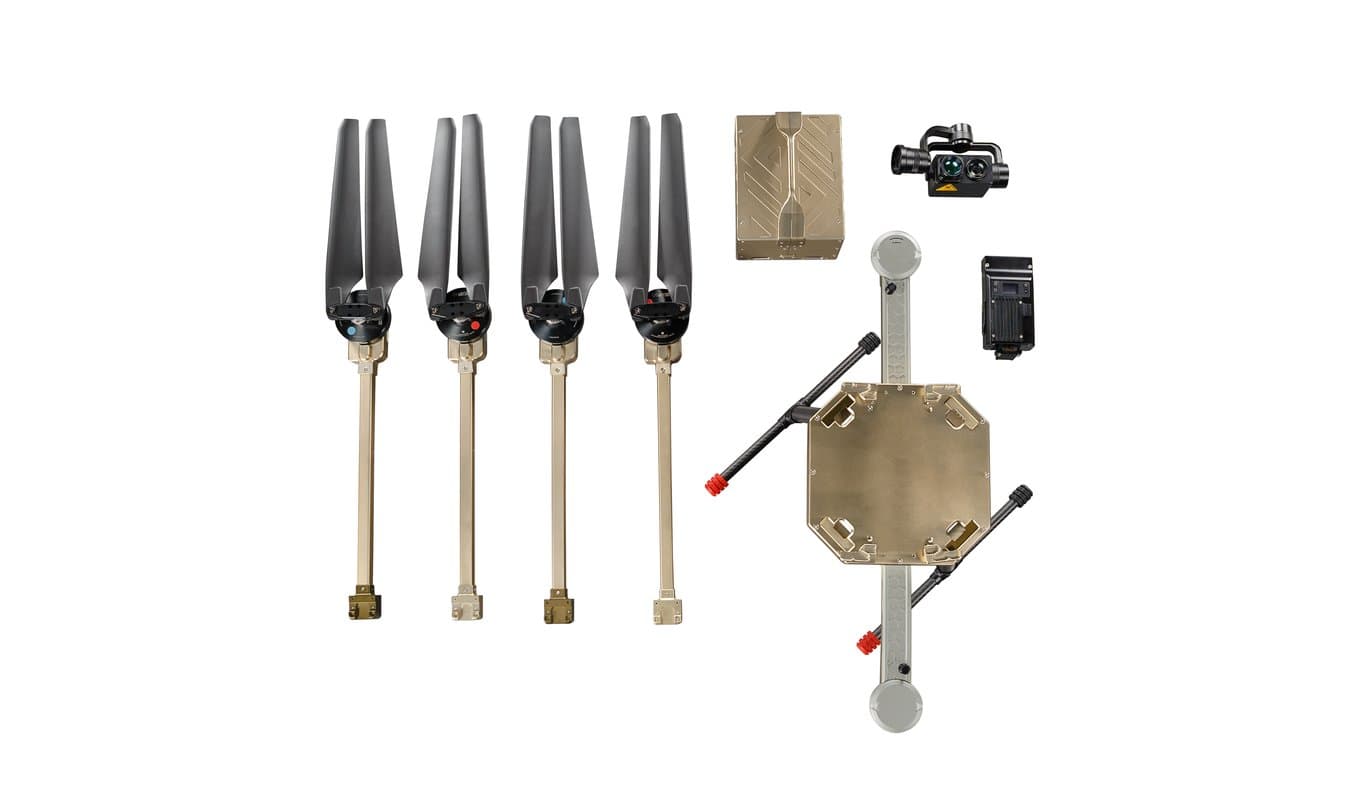
Atlas Tクアッドコプターモデルは、SLS 3Dプリント製の部品(ブレードアンテナ、ジンバルやメタンセンサーのカバー)と、加工で作る金属部品、そして炭素繊維製部品を組み合わせることで、最大積載量を最適化して最高のパフォーマンスを発揮できるユニークな形状を実現。
メルトの測定
Nextech製品の1つに、翼幅3.2m、航続距離100kmにもなる固定翼ドローンがあります。フランス政府と協働したプロジェクトでは、このドローンを北極圏から飛行させ溶けつつある氷床をスキャンし調査を行いました。ドローンには、海洋が氷床の融解速度にどのような影響を与えているかを計測するためのマルチスペクトル画像装置と赤外線画像装置が搭載されました。Nextechは繊細な装置を搭載するために、カスタムのブラケットや機体部品、そして極限状態でもしっかりと機能する翼端も設計する必要がありました。
「ドローンの質量や稼働環境に応じて翼端の形状も変える必要があります。試作品製作中にこういった要素が変化すると、挙動を確認する前にまず加工で製作しなければならず、それだけで高額なコストがかかります」とKroone氏は言います。
翼端は最終的に炭素繊維複合材料で作る予定ですが、そのための金型製作には時間も加工コストもかかります。Fuse 1+ 30WにてNylon 12パウダーを使って3Dプリントすることができれば、最終的な炭素繊維製部品と同様の重量で複雑な形状の部品を製作することができます。
「アルミや炭素繊維材料で作る場合、プロジェクトの初期段階で金型の設計を固めるのは非常に難しいんです。一方、Fuse 1+ 30Wがあればこのように複雑な形状の部品でも製作できますし、複数の設計を試したり、プロジェクトで生じた変更に合わせて新設計をすぐにプリントが可能です」とKroone氏は付け加えます。
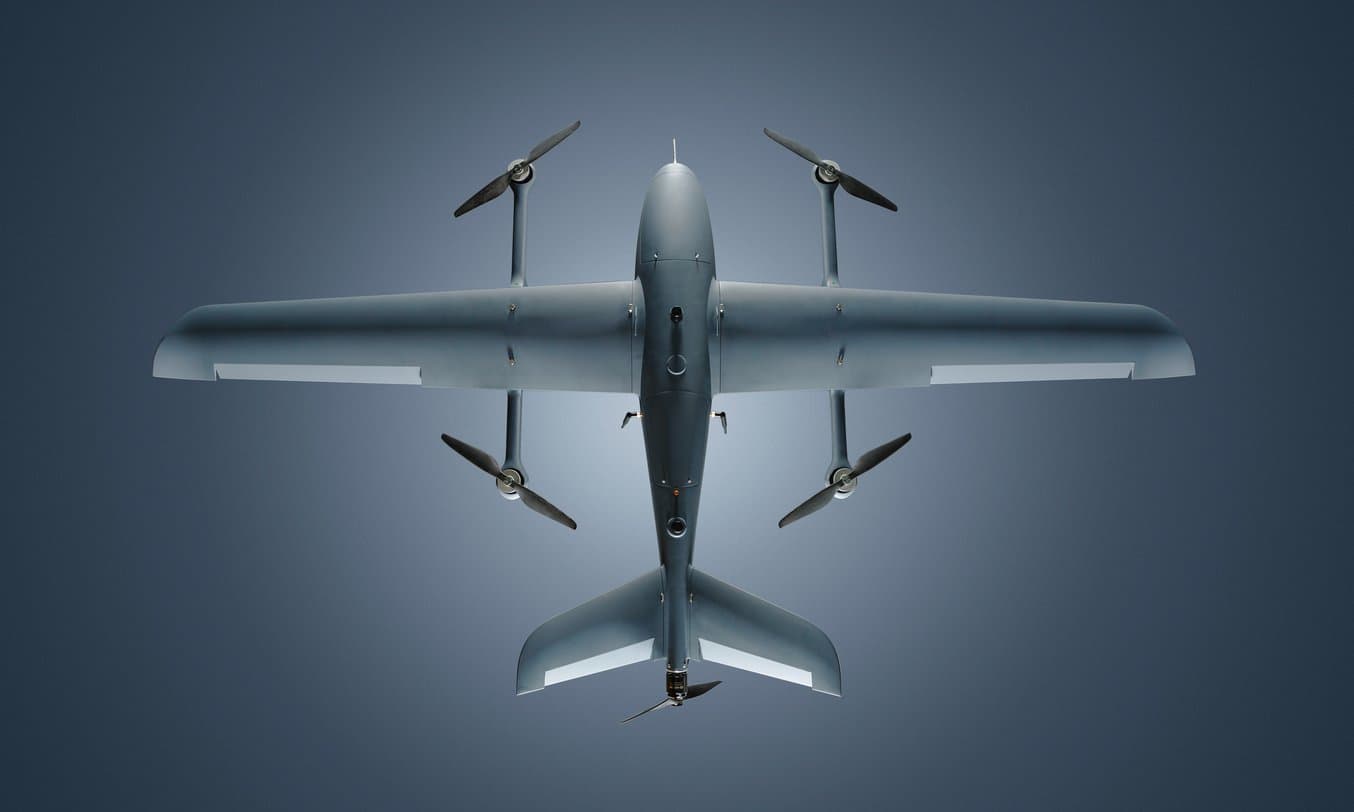
Nextechの固定翼ドローンのレンダリングにより、設計のスケールと複雑さがよくわかる。
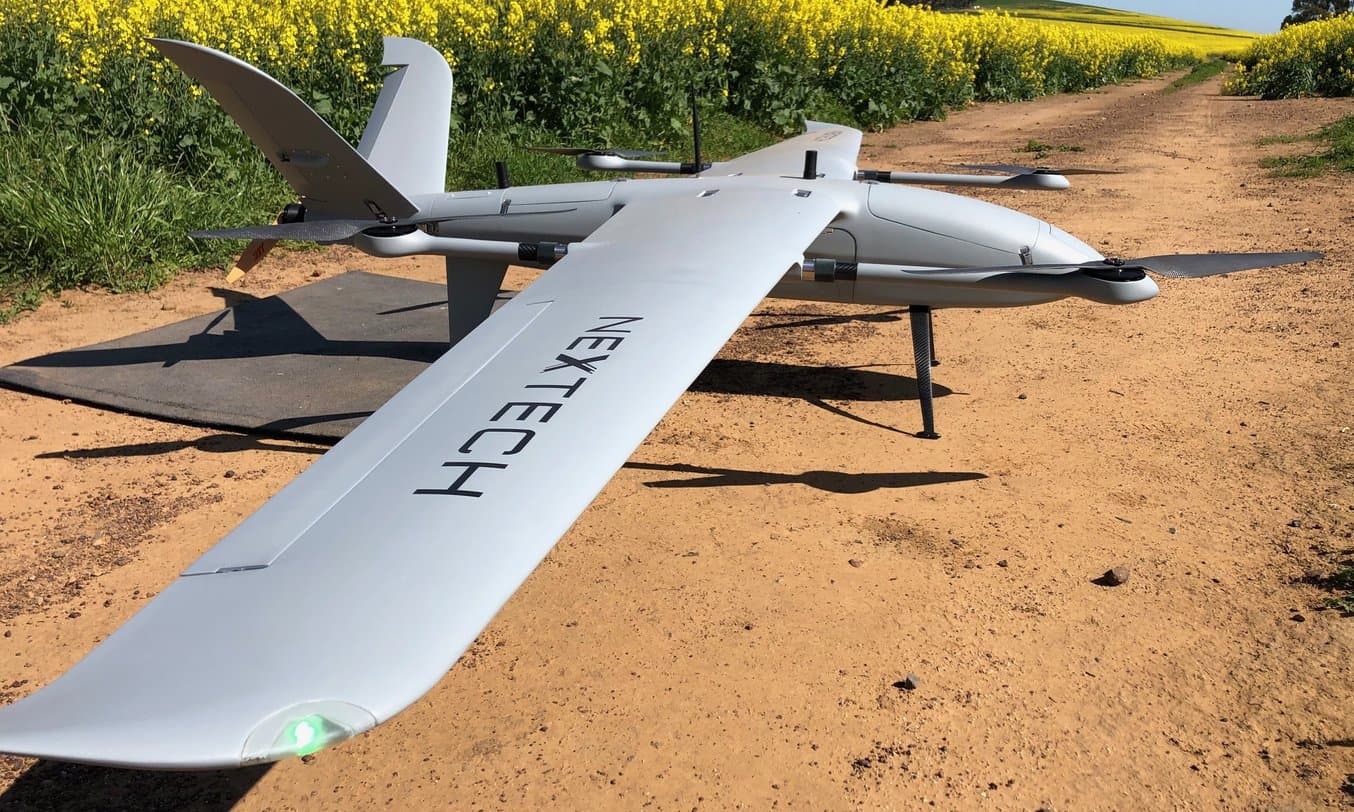
Nextechは、Fuse 1+ 30WにてNylon 12パウダーを使ってプリントした炭素繊維製の成形型を活用して設計を進め、固定翼ドローンの機能的な翼端部の試作・検証を迅速に繰り返して設計を確定させた。
100個の実製品用部品をバッチ量産
同社は、マルチローター式のドローン、Atlas T向けに特定の角度や距離でもデータ送信を続けられるよう複数の設計を考案しました。デバイスの体勢は性能に影響を与え、GPSやアンテナを正しい場所に配置するにはより長い飛行距離とより高い伝送品質が必要になります。長距離アンテナのトラッキング部品が、導電性があり嵩張る材料に邪魔されないよう、搭載機器の固定具とアンテナの両方をカスタマイズする必要がありました。そのためには、非導電性の材料を使って複雑形状を何度も試作・検証して設計を固める必要があります。
Kroone氏は、この時もFuse 1+ 30Wを活用してスナップイン型のスマートバッテリーロケーターを開発しました。実際に使用するドローンに搭載する外装部品と内装部品の両方をNylon 12パウダーで3Dプリントしました。内装部品のサイズと量の多さにより、CNC加工機を効率的にプログラムをすることが難しかったのです。「小型部品なのでCNC加工機で設定するには非常に時間がかかりますが、Fuse 1+ 30Wなら100個の部品を一度にプリントできます」とKroone氏は言います。
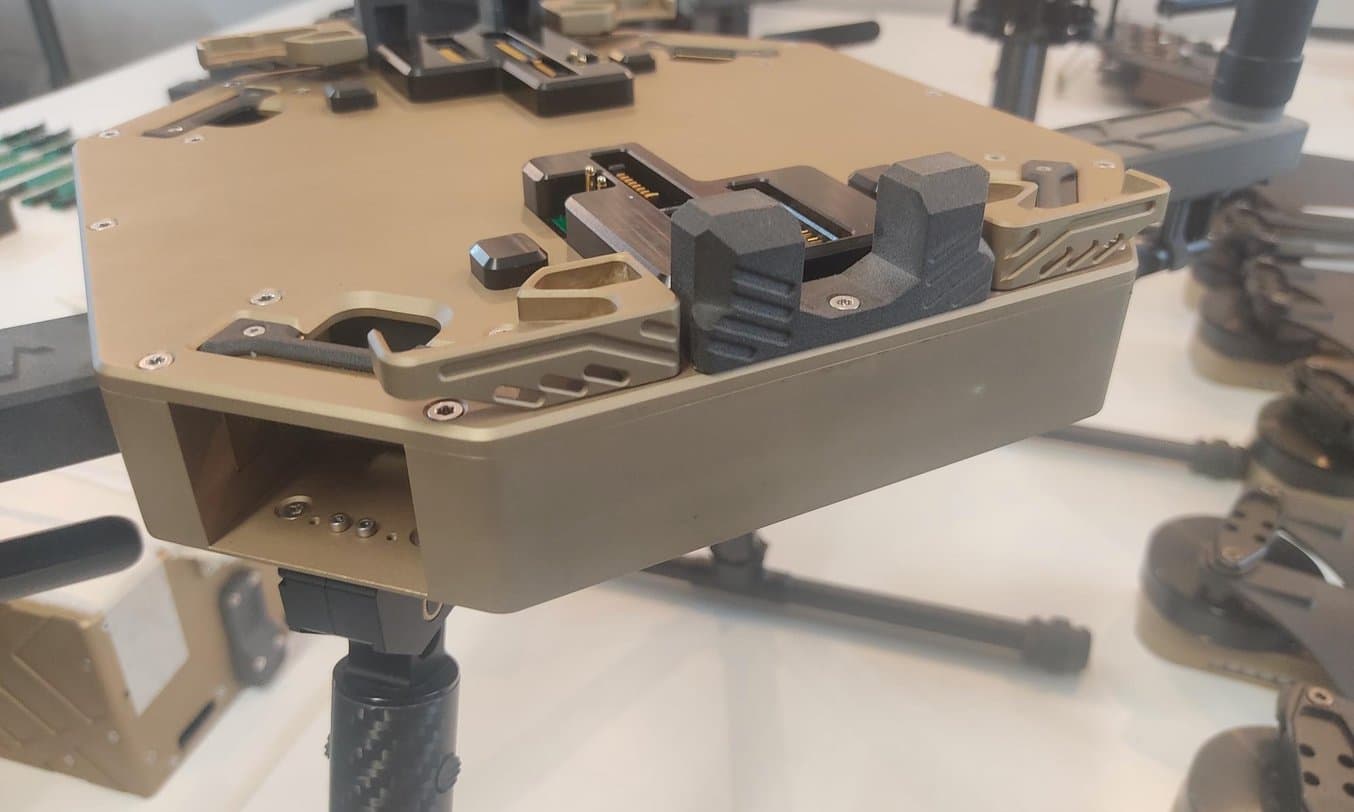
Atlas Tクアッドコプターに搭載されるバッテリーロケーターは、Fuse 1+ 30WにてNylon 12パウダーを使って3Dプリントしたもの。
100万ドルの価値がある装備に相応しい結果
SLS 3DプリントとCNC加工技術を組み合わせることで、Nextechはこれまでより柔軟に設計・製造が行えるようになりました。バッチ量産と複雑な形状の部品製作はFuse 1+ 30Wで行いながら、他の部品は高強度アルミニウム材料を加工して製作しています。SLS 3Dプリンタを比較・検証する際、同社が重視したのはCNC加工機に匹敵する品質を実現できるかどうかでしたが、Fuse 1+ 30Wでその答えが見つかりました。Kroone氏はこう言います。「本当に素晴らしい技術です。CNC加工機には何百万ドルも費やしてきましたが、[Fuse 1+ 30Wの]生産力はそれと同等ながら、価格は$60,000程度で済みます」
Nextechが新たなドローンをローンチするたびに、会社の知名度が上がり、需要も増えます。Nextechは、Fuse 1+ 30Wの安定感がありスムーズな稼働状況を頼りにしています。「高品質のドローンを短時間で製造するためには、常に同じ品質で安定して製作できることが非常に重要なんです。SLS 3Dプリンタの多くはプリント失敗やエラーが多いことで知られていますが、Fuse 1+ 30Wは高品質でサポートも充実しています」とKroone氏は言います。プリンタの安定感とFormlabsが世界各地で提供するトップクラスのサポートにより、常に安定した製造を実現できています。
ドローン業界は激戦市場で、政府機関や研究機関、農業セクターからの大型契約を獲得しようと各社がしのぎを削っています。その中で常にトップであり続けるために、ドローンメーカーは常に新たな技術を取り入れ、顧客の要望に合わせてカスタム可能なオプションを提供する必要性に駆られています。特にSLS 3DプリントやCNC加工による内製能力を有していることが、Nextechが他社と一線を画す理由です。
「バッチ量産を行なっていても、これら技術の一つでも欠けている企業は、将来の見通しをしっかり立てられていないと言う他ありません。必要な時にいつでもすぐに製造できる工程が社内にないことは、大きなハンディキャップになります」
Nextech メカニカル設計エンジニア、Liam Kroone氏
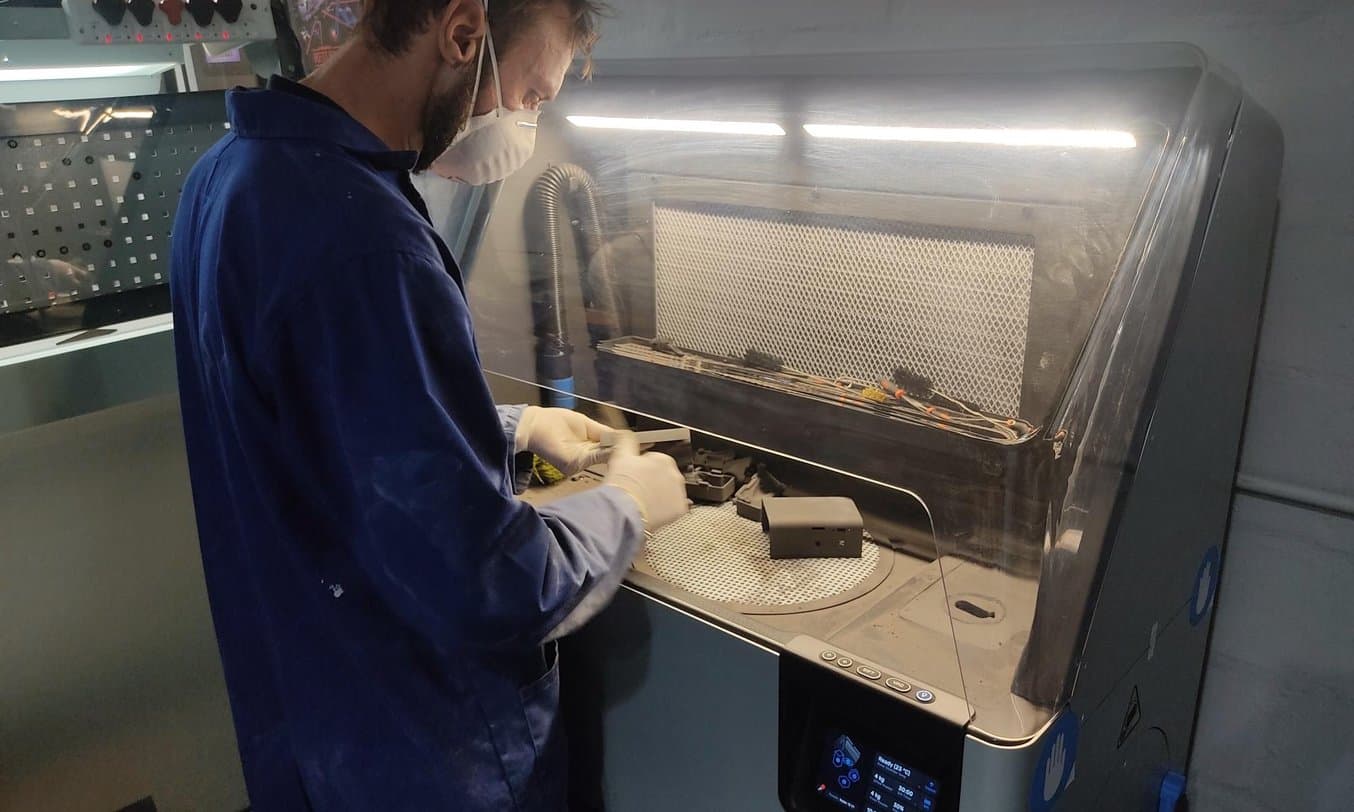
Fuse Siftは、安全で効率的なワークフローで部品から粉末を除去し、回収・再利用ができる後処理装置。
伝統的な製造技術と先進的なAM技術の両方を社内に導入することで、Nextechはドローン業界のトップに躍り出ることができました。安定した稼働を実現するFormlabsのFuseシリーズSLS 3Dプリンタのおかげで、同社はサプライヤーからの変更や顧客の要望に対しても迅速に対応し、製品を改善し続けることができています。
Formlabsの3DプリンタでNextechの事業を支えてくれているのは、弊社の南アフリカ正規販売代理店BuildVolumeです。