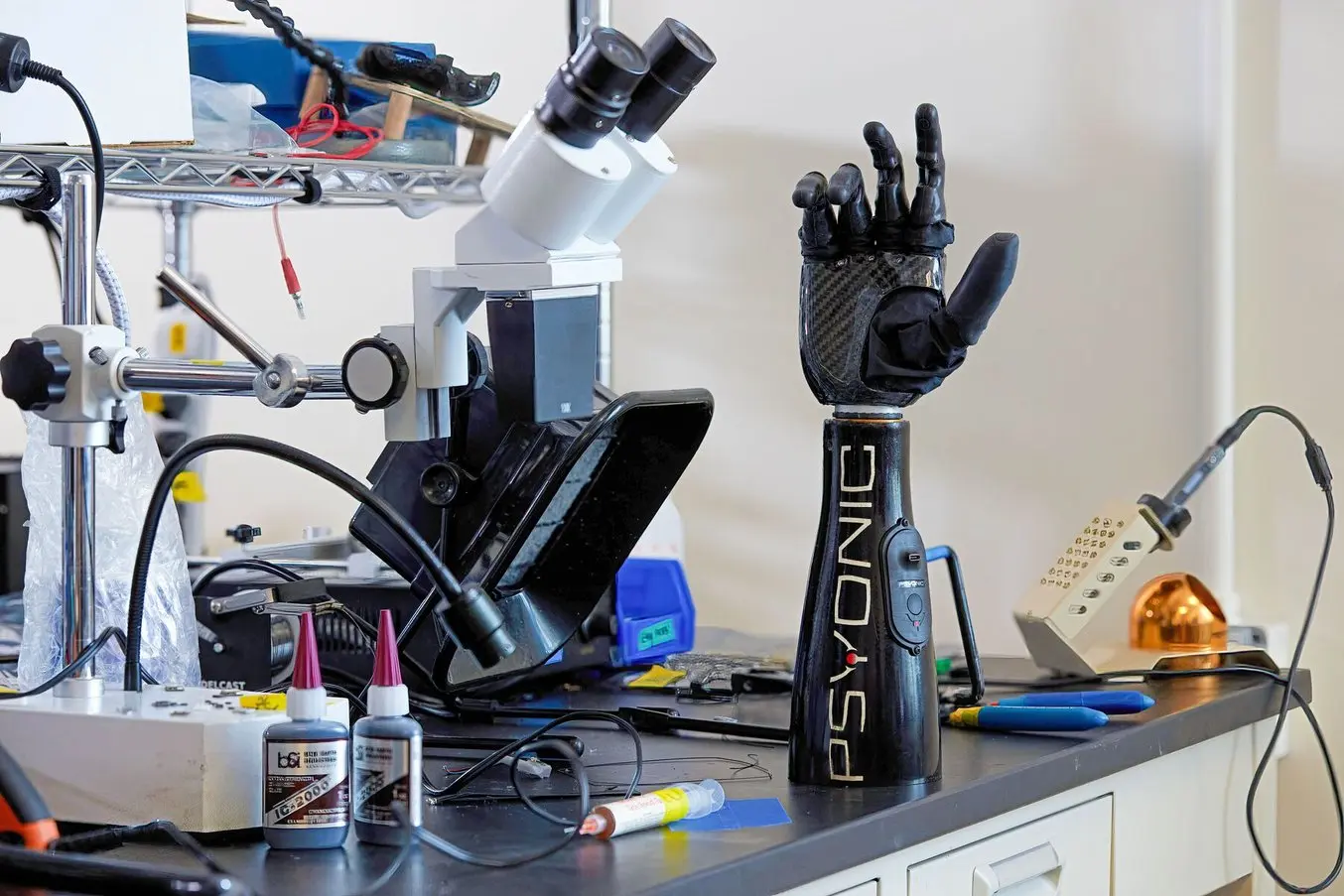
世界では、5,000万人以上の人が外傷性の四肢切断に苦しんでいます*1。生命の危機を乗り越えて回復した患者の方々にとって、義肢装具を着けた生活という新たな世界に足を踏み入れることは、痛みを伴うことでしょう。ほとんどの人は、車の運転、ジムでのトレーニング、家の掃除など、これまで通りの普通の生活に戻りたいと願っているものの、従来の義肢装具の多くは高価で、それを身に着ける患者にとっても満足のいくものではなく、そして壊れやすいものでした。現在、高度な義肢を必要とする患者のうち、実際に購入できるのは10%程度しかいないと言われています。
そしてこの市場に一石を投じたのが、Ability Handを開発したPSYONICです。3Dプリント、射出成形、シリコン成形、CNCマシンなど多彩な製造方法を駆使して自社設計・製造されたAbility Handは、彼らの生活とモビリティを回復することが期待されています。
結論から入ると、PSYONICはFormlabsのSLA光造形3Dプリンタで以下のようなことを行いました。
- FDAに登録されたメディケア対象製品となる、過去に存在しなかった上肢の装具をゼロから作る
- 患者からの意見を積極的に収集し、それを反映した試作品を内製で即座に製作することでAbility Handのデザインと機能を改善する
- 真の意味でのハイブリッド生産方式でAbility Handを可能な限り安価で提供する
- 後に紹介するGarrett Anderson軍曹のような患者の方々が以前の生活に戻れるようサポートする
- 高度な義肢装具を購入できる患者を10%から75%まで向上できる価格と入手性を実現する
- 耐久性、耐衝撃性に優れた3Dプリントの先端材料を活用し、長寿命の部品を製作する
本記事ではPSYONICのCEO、Aadeel Akhtar博士とリード・メカニカルエンジニアのJames Austin氏に、同社Ability Handの開発背景と、これまで未開拓だった先進義肢装具市場の現状、そして同社の市場参入戦略において3Dプリントがいかに重要な役割を果たしたのか、お話を伺います。また、同社のAbility Handの最初期ユーザーの1人である米軍曹、Garrett Anderson氏にもお話を伺います。
義肢装具にはイノベーションが必要だ
2005年、イラクに派遣されていた米軍曹Garrett Anderson氏の車両に路肩に設置して通行車両を狙う爆弾、いわゆるロードサイドボムが直撃しました。Anderson軍曹は、軽度の脳損傷と顎の骨折、そして右腕の肘から先を切断する必要があると診断されました。帰国後は、幸いにも生活の大部分を以前と同じように送ることができ、イリノイ州立大学に入学して学部生として修士号を取得し、2人の子供を授かっています。
現在の義肢装具市場は、ごく基本的な機能を果たすということで今でもフックが使われることがあるほど、旧態依然としたものです。他の医療分野が急速に進歩しているにもかかわらず、義肢装具にはまだそうしたイノベーションの波が到来していないようでした。
そんな中、Anderson氏はAadeel Akhtar(アーディル・アクタル)という名の若い博士号取得者と出会います。彼もまた、義肢装具の現状に満足していませんでした。「これは、私が7歳の時に見つけた将来の、人生の目標でした。私の両親はパキスタン出身です。7歳の時にパキスタンに行った時、初めて手足の不自由な人に出会いました。彼女は私と同年代の子どもで、右足を失い、木の枝を松葉杖代わりにしていたんです。そういうきっかけがあってこの分野に進み、最先端のバイオニックデバイスを作り、誰もが現実的に買えるものにしたいと考えるようになりました。」
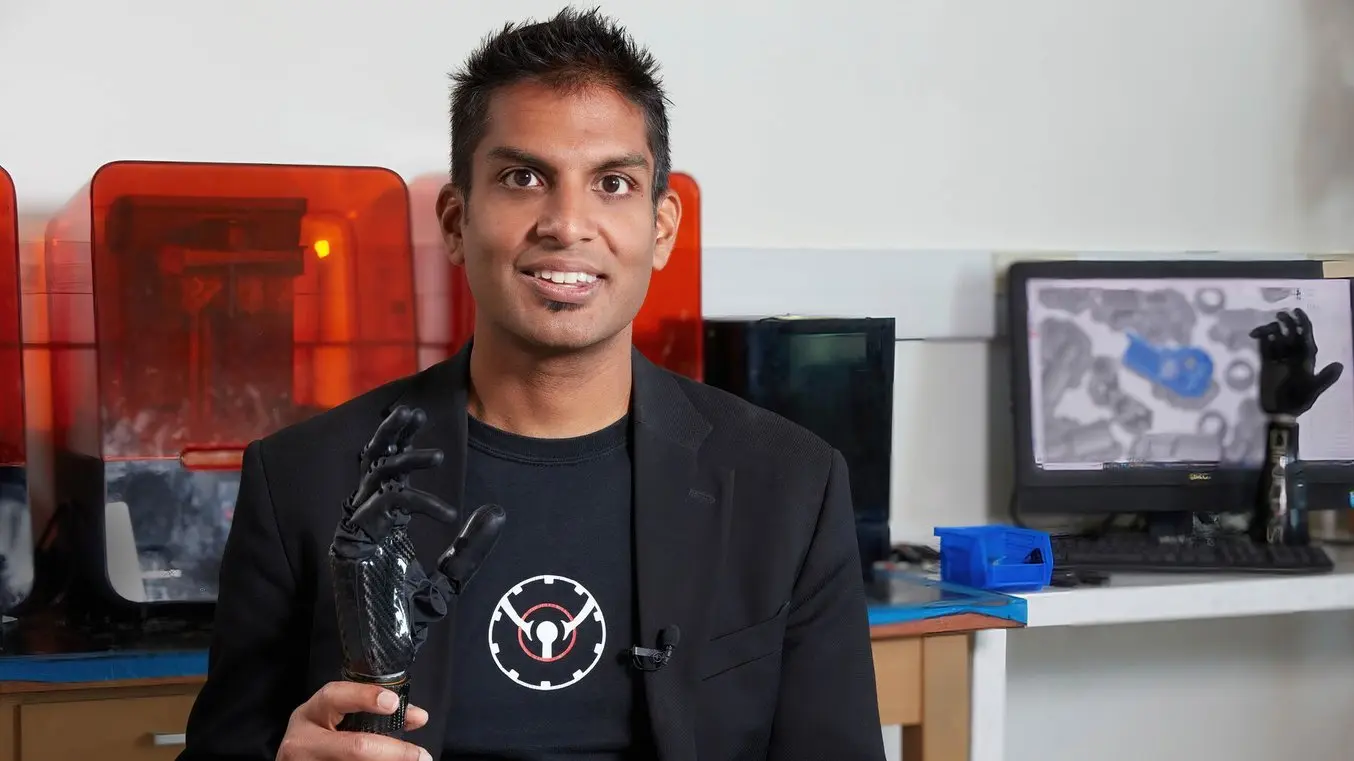
最新版のAbility Handを手にするCEOのAadeel Akhtar氏。
しかし、業界をリードする新たな義肢を市場に送り出すのは簡単なことではありません。「この7年間で9種類のプロトタイプを製作し、やっとのことでFDA登録のメディケア対象製品となるAbility Handが米国内で発売できました」とAkhtar氏は言います。
最新のハイブリッド製造方式とは
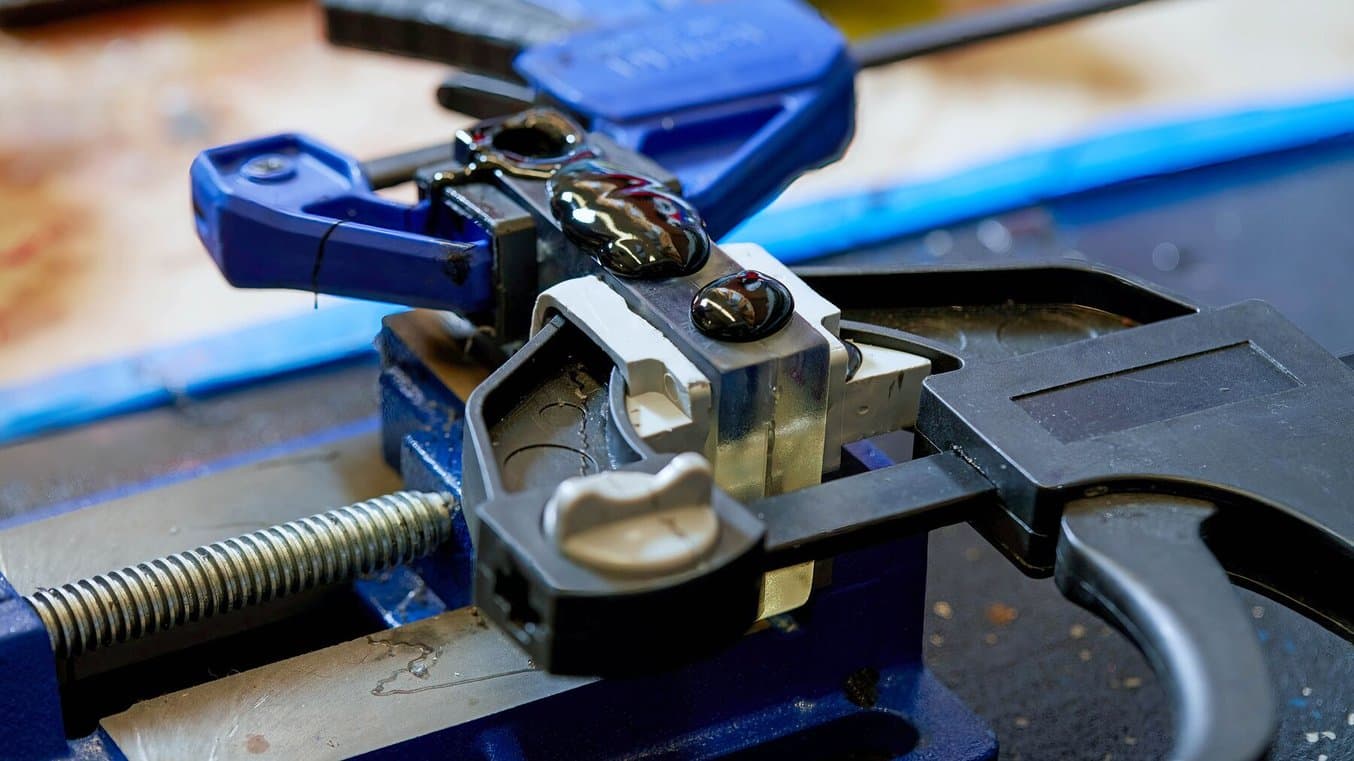
3Dプリントは、大企業でも中小企業においても、新製品の試作品製作、ひいては開発期間の短縮と市場投入の高速化のため、広く浸透しています。医療機器製造のような研究開発の初期コストが高い分野では、3Dプリントはエンジニアリングチームのツールボックスの中でも重要な存在となっています。
次世代型の義肢義肢とは、ユーザーの意思に素早く反応し、日常生活の中で壊れない十分な耐久性があり、ユーザーが疲れたり腕を痛めないよう軽量で、触れたもののリアルな感覚が感じられるものでなければならない― これは素晴らしいことです。
PSYONICのようなスタートアップ企業が従来の義肢装具市場を覆すことができるほど、デバイスの製造には変化があったのでしょうか?
- 3Dプリントは、数十年前から試作や製品開発で広く利用されている。現在では、3Dプリントの技術もより成熟し、特にSLS(粉末焼結積層造形)やレーザー光造形(SLA)の3Dプリントは製造業で広く普及が進んでいる。
- 実製品用の部品が高い生産能力で高品質にプリントできる技術の進歩、そして材料の目覚ましい革新により、3Dプリントは新興医療機器の製造にも導入されている。
- 3Dプリンタは、最終製品を直接プリントする用途だけでなく、金型(樹脂型)や生産/組立用治具などを製造する中間工程として従来型の切削や成形に3Dプリントを取り入れる「ハイブリッド製造」にも大きなメリットが利点がある。これはラピッドツーリングという名称で知られる。
同社のリード・メカニカルエンジニア、Austin氏の考えは次のようなものです。「新旧の製造方法をミックスしたりマッチングしたりする手法は、特に私たちPSYONICのようなスタートアップ企業にとって、非常に重要だと思います。従来の製造方法だけでは、私たちのように小規模な義肢装具メーカーは、市場で競争できなかったでしょう。CNCでのマシニングや射出成形など、特に何度も試作を繰り返して微調整する必要があるような場合では、初期費用の時点でコストが天文学的な金額になります。私たちには到底無理でした。しかし、3Dプリンタの登場とその3Dプリントの中でもいろいろな選択肢が広がったことで、試作品を安価で迅速に製作できるようになり、検証とデザインの修正を繰り返し、小規模かつ低コストで製品が製造できるようになりました。3Dプリント、特にFormlabsの3Dプリンタは、その素晴らしい機能と価格で私たちPSYONICの立ち上げと、その開発プロセスで絶対的に重要な役割を果たしました。」
ここで、PSYONICが社内で3Dプリントを使用してAbility Handを製造するプロセスを少し見せてもらいましょう。
炭素繊維部品の成形作業を内製
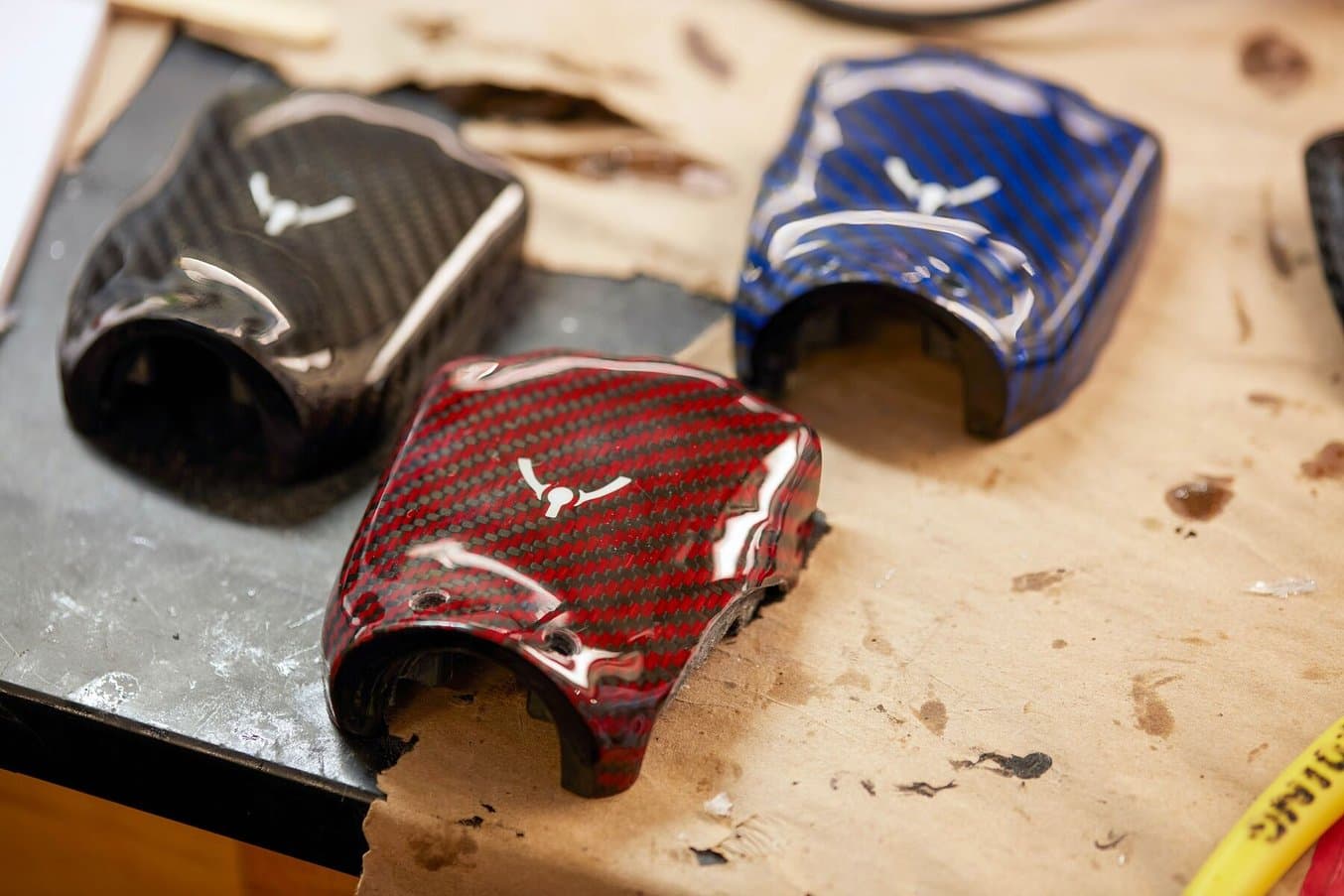
炭素繊維部品が内製できたことは、PSYONICがAbility Handを継続的に改善する上で非常に大きなメリットがあった。
炭素繊維は非常に強力な材料で、Ability Handの軽量化を図りながら耐久性や強度を大きく高めることができます。しかし、CFRPのような複合材でカスタム品を製造するにはハンドレイアップ成形による手作業となりますが、それには金型が必要です。金型製作には非常に高いコストと長い製作期間が求められるため、少量生産やワンオフ品を作るために金型を起こすことは現実的ではありません。しかし現在では、3Dプリントか従来のマシニングかといった選択は必要なく、単に両方をハイブリッドとして併用することができるようになっています。
Austin氏は、「炭素繊維を成形する金型を作る時、特に初期の試作からの反復検証ではSLA光造形の3Dプリントは本当に重要でした」と言います。「私たちには、例えばマシニングで金型を製作できるだけの資金も時間もありませんでした。そこで、FormlabsのHigh Tempレジンで金型を作ってみることにしたんです。High Tempは、少し割れやすいですが耐熱性が非常に高いため、プリプレグを意図した通りの形状にプレスしてオーブンで硬化し、問題なくAbility Handに接着できました。」
PSYONICが採用した3Dプリント製の金型は、従来の金型製作のコストを大きく削減し、製作期間の短縮も可能な非常に注目度が高い手法です。必要な精度が得られる3Dプリントのノウハウさえ習得していれば、エンジニアが手作業で削ったりCNCを扱うことなく低コストで、数時間以内に金型を直接プリントすることができます。PSYONICのような医療機器スタートアップでは、High Tempレジンや強度と剛性がより高いRigid 10Kレジンなどで、従来では製作できなかった細部にまでこだわった複雑な形状を持つ金型が製作できます。
Austin氏は、High Tempレジンで複数の金型を製作し、非常に安価なコストで設計の細部を検証しながら作業を進めました。「形状に調整が必要ならCAD上でデザインを調整し、再度3Dプリンタで造形すれば、新しいHigh Tempの型ができ上がります。コスト的にも時間的にも、何度も調整できる心の余裕も生まれました。長期的な継続性を考慮して、最終的な量産用の金型は切削で製作することにしましたが、初期の試作や検証用の簡易型には、Form 3とHigh Tempがとても役立ちました」と語っています。High Tempレジンは、0.45MPaで238℃の荷重たわみ温度を持ち、オートクレーブの熱と圧力に耐えることができるFormlabsのエンジニアリング用レジンです。
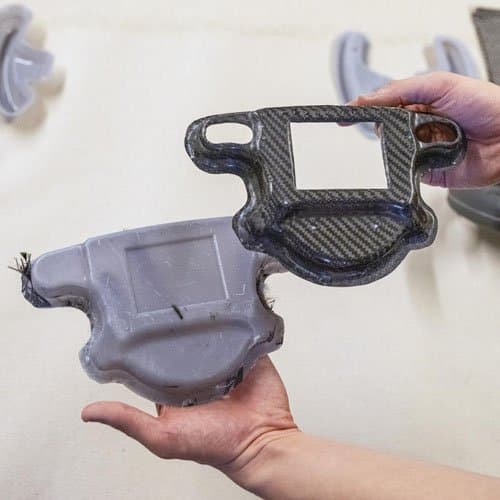
3Dプリント製金型で炭素繊維部品を製作
本ホワイトペーパーでは、CFRPやFRPなど複合材を成形するレイアップ用金型の設計ガイドライン、そして炭素繊維部品を作るプリプレグとハンドレイアップの方法を手順ごとに解説していきます。
※本ホワイトペーパーは現在翻訳中です。近日のアップデートをお待ちください。本資料の内容についてのお問合せは[email protected]までお問合せください。
リバースエンジニアリング
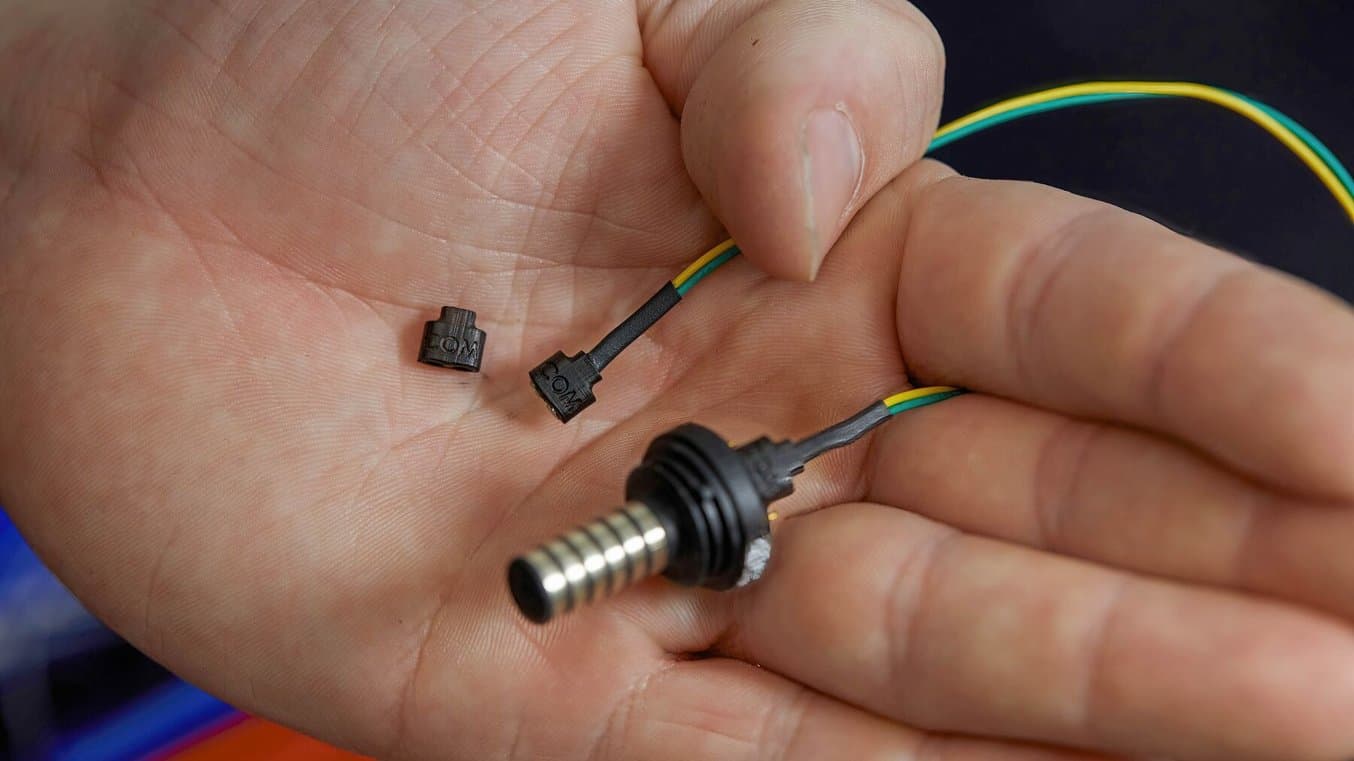
PSYONICは小型コネクタをリバースエンジニアリングで賄うことでコストを低減している。
リバースエンジニアリングは、部品の現物さえあればデジタルデータが得られる素晴らしい方法ですが、試作品を作り上げる際にも貴重なオプションになり得ます。リバースエンジニアリングに習熟したエンジニアがいれば、3Dプリンタでさまざまな部品をリバースエンジニアリングで迅速に製作でき、手早く確実に必要な部品を入手することができます。
医療分野で働く人なら、医療用のカスタム部品がいかに高価かご存知でしょう。ほんの小さなクリップでさえ、交換に何万円もかかるってしまう世界です。中小企業にとって、ましてPSYONICのように世界の誰もが購入できる製品を目指すスタートアップにとって、こうした部品コストは大きな課題でした。
そこで同社は、再び社内の3Dプリンタに目を向けました。開発のスピードアップとコスト削減が行えないかと考えたのです。Austin氏は「他社製品との互換性が必要な部品もあるため、それを購入することもあります。しかし医療機器業界の部品はほとんどが高額で、我々の目標を達成するのが難しくなってしまいます。しかし小さな部品であれば、こうしてリバースエンジニアリングで3Dファイルを起こして、自社で生産することもできます。」
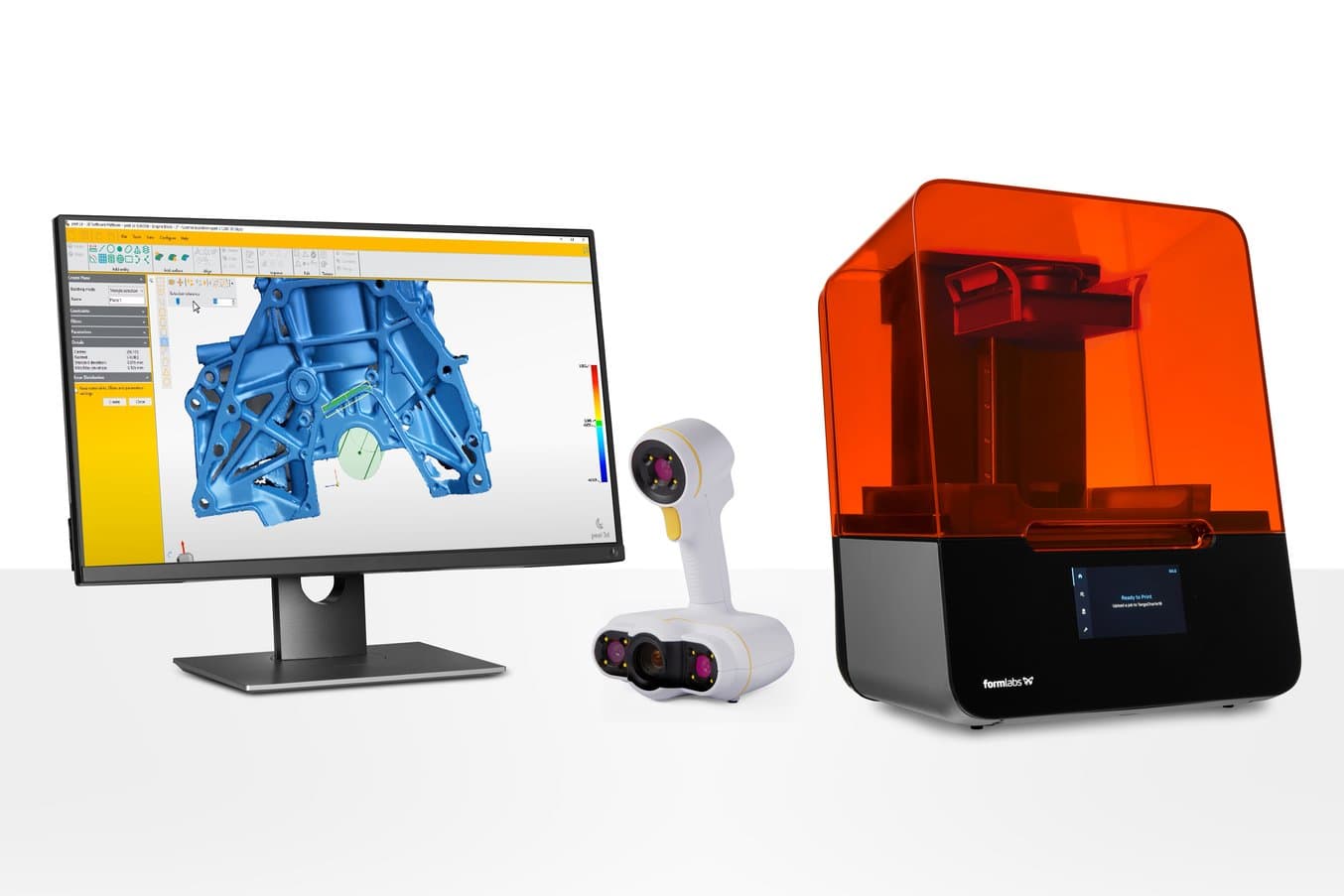
3Dスキャン+3Dプリントでリバースエンジニアリング
本ホワイトペーパーでは、3Dスキャンと3Dプリントで行うリバースエンジニアリングの始め方を解説しています。現在販売されている3Dスキャナのご紹介も行っています。
※本ホワイトペーパーは現在翻訳中です。近日のアップデートをお待ちください。本資料の内容についてのお問合せは[email protected]までお問合せください。
注型と射出成形にラピッドツーリング
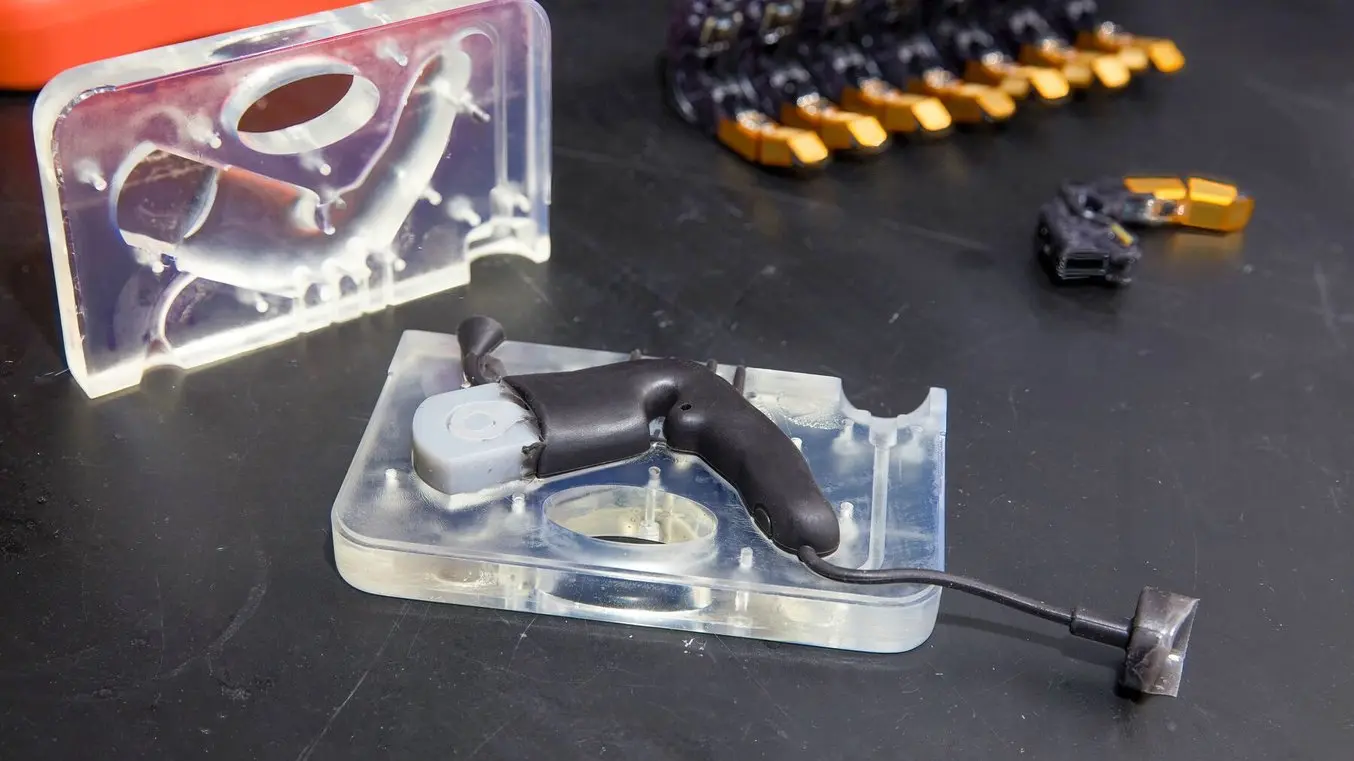
医療機器の開発プロセスに、射出成形による小ロットの量産が導入できれば多くのエンジニアにとって素晴らしいことでしょう。そこで新製品の開発に「ラピッドツーリング」と呼ばれる3Dプリントによる金型や治具の高速製作を導入して金型や治具の製作あるいは試作を行えば、金属の切削で金型製作を行う従来の方法よりも、遥かに効果的で安価です。当初PSYONICはコスト削減のため、Ability Handの指を含むすべてのパーツを3Dプリントで製作していましたが、特に指部分はより頑強なものにする必要があることがわかり、指を直接プリントするのではなく、金型の方を3Dプリントする方法に切り替えたのです。
この発想の転換について、Akhtar氏は「私たちが直面した最大の課題は、このハンドをいかに低コストで製造するかということと同時に、如何にして他の何よりも高い耐久性を持つものにするかということでした」と語っています。低コストで製造するという点については、我々は当初からAbility Hand全体を3Dプリントで製作することで、超が付くほどの高いコストパフォーマンスを実現していました。しかし販売されている従来のバイオニックハンドに対する一番の不満は何かという点でいくと、500万円以上もかけて購入したバイオニックハンドが壊れてしまうことなのだと、多くの患者や医師の話を聞くうちにわかったのです。
「以前から販売されていたようなハンドの指は硬い部品でできており、日常生活の中でテーブルの角に指をぶつけてしまったりすると、その衝撃で関節が折れて壊れてしまうようでした。しかし、私たちのAbility Handの指は柔軟な材料でできています。私たちはそういった材料面での機能性も含めてAbility Handに取り入れて、耐久性を高めたいと考えたのです。」
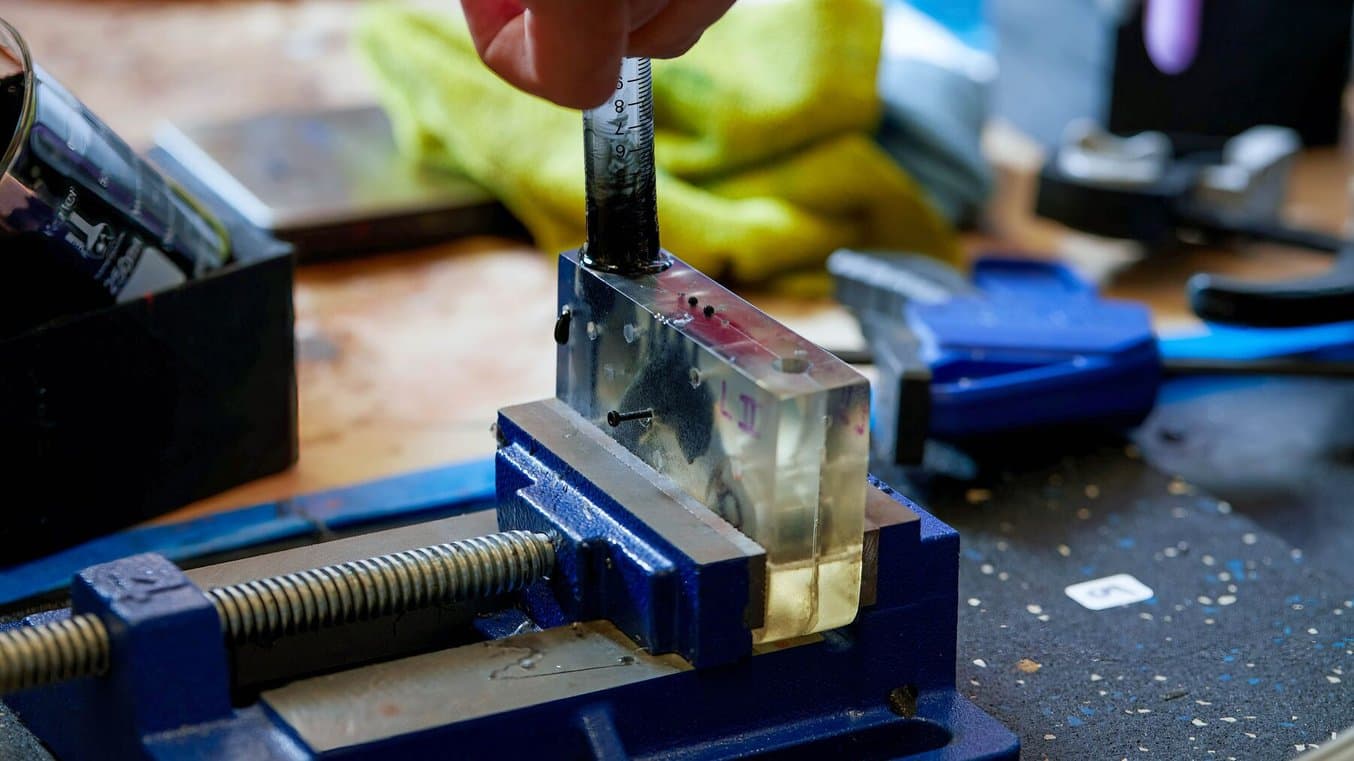
「まず、FDM(熱溶解積層/Fused Deposition Modeling)方式の3Dプリンタで金型を製作しました。FDMプリンタは手早く安価にプリントができる反面、高い圧に耐えられません。金型というものは、非常に高い精度で滑らかな表面をもってプリントしなければならず、SLAの方が適しています。指の成形には当初、FDMでプリントした金型を使っていました。しかしFDMでの金型では射出成形すると、どうしても表面がきれいに仕上がらないという問題がありました。FDMは1層ずつ押し出して重ねていく方式なので、筋が入ってしまうんです。そのため成形品にはすべて、こういう奇妙な縞模様のテクスチャが上についてしまうのです。Form 3のClearレジンでのプリントに変更すると精度が格段に上がり、より滑らかな表面でプリントできるようになりました。そこで私たちが採った方法は、作りたい指や親指の形状を反転させてブロックから削り出し、インジェクションが行えるようにシリコンの型にランナーやインレットを設けます。型の設計が終わり、Clearレジンでプリントしたら、その中に3Dプリント製の骨を入れ、指の骨格を形成します」。
さらに、「そのClearレジン製の型をクランプで固定し、2液のプラチナシリコンを混ぜて注射器を使って手作業でシリコンを注入し、指を包み込むように型の中にシリコンを充填します。そうすると指をきれいに包み込むことができ、とてもきれいに仕上がります。この型は脱型してすぐ、何度も使用できました。Clearレジンの唯一の欠点は、時間の経過と共に摩耗してしまうことです。しかしそうなったとしても、新しい型をプリントすれば翌日には元の通り高精度な型ができ上がり、型を交換してまたすぐ成形を再開できます。」
Austin氏は、最終用途の部品と金型の両方で、Form 3での最高解像度(積層ピッチ25ミクロン)でプリントを行いました。Austin氏は「すべての材料で、可能な限り高い解像度でプリントしています。Tough 1500レジンで製作する部品の場合、非常に精密なフィットが必要だからです。手のひらの内側とそれを包む部品の周囲に、非常にタイトにフィットするよう作る必要があります。そこに精度のばらつきや誤差があると、動作時の摩擦が大きくなったり部品の位置がずれたりするので、最適なフィット感と機能性を実現するため可能な限り精密に作る必要があります。金型の場合は、最高解像度でプリントするのは表面を可能な限り滑らかに仕上げるためです。そしてForm Washで徹底的に洗浄することで、非常に滑らかな表面が得られます。そしてその後、部品を成形するシリコンに反映することができます。」
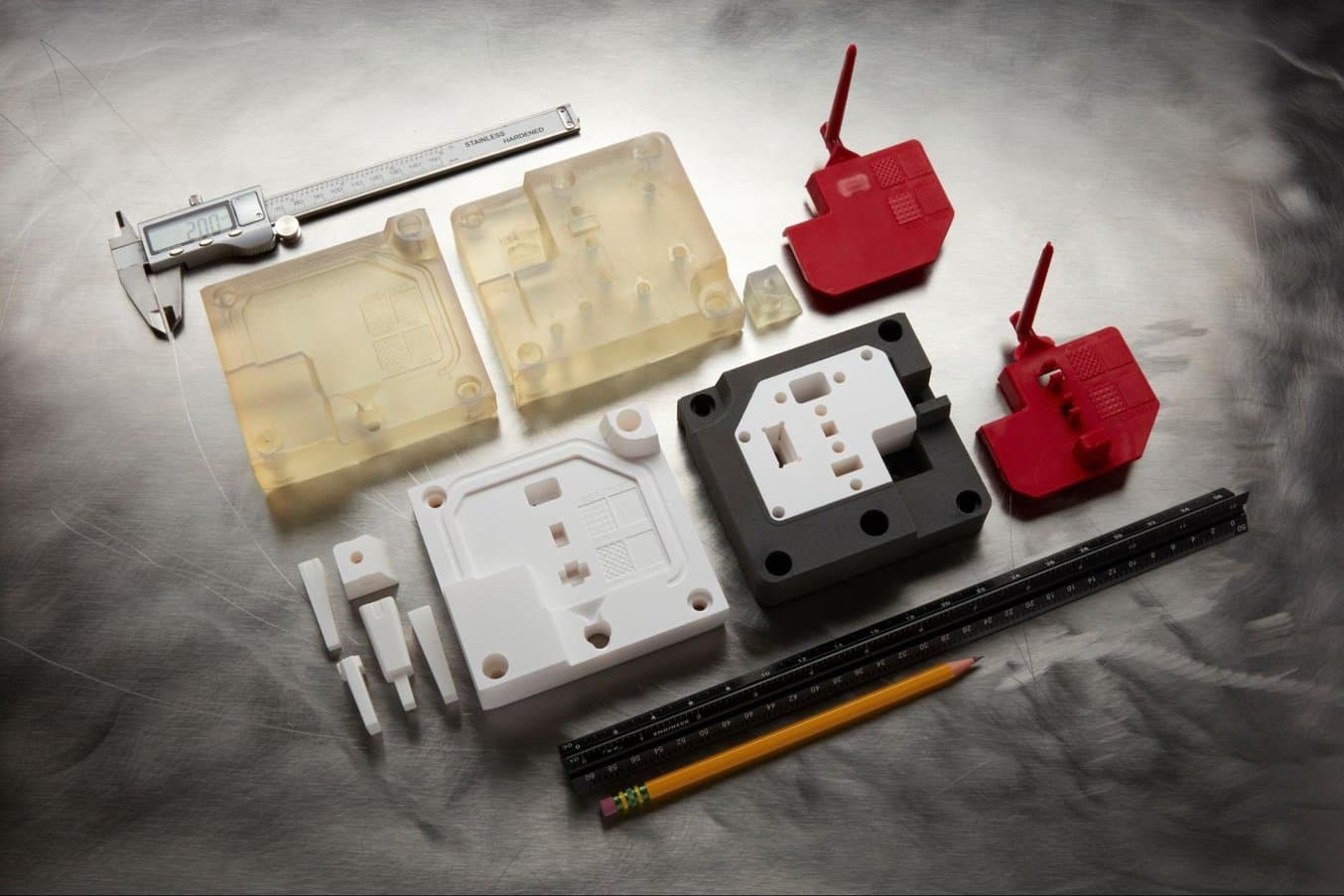
ラピッドツーリング総合ガイド
本ホワイトペーパーでは、各種成形用の金型や治具を3Dプリントで高速製作する「ラピッドツーリング」と呼ばれる方法について、その概要とFormlabs製品を活用したラピッドツーリングの各種事例をご紹介しています。
ユーザーの声を基にラピッドプロトタイピングで迅速に改善
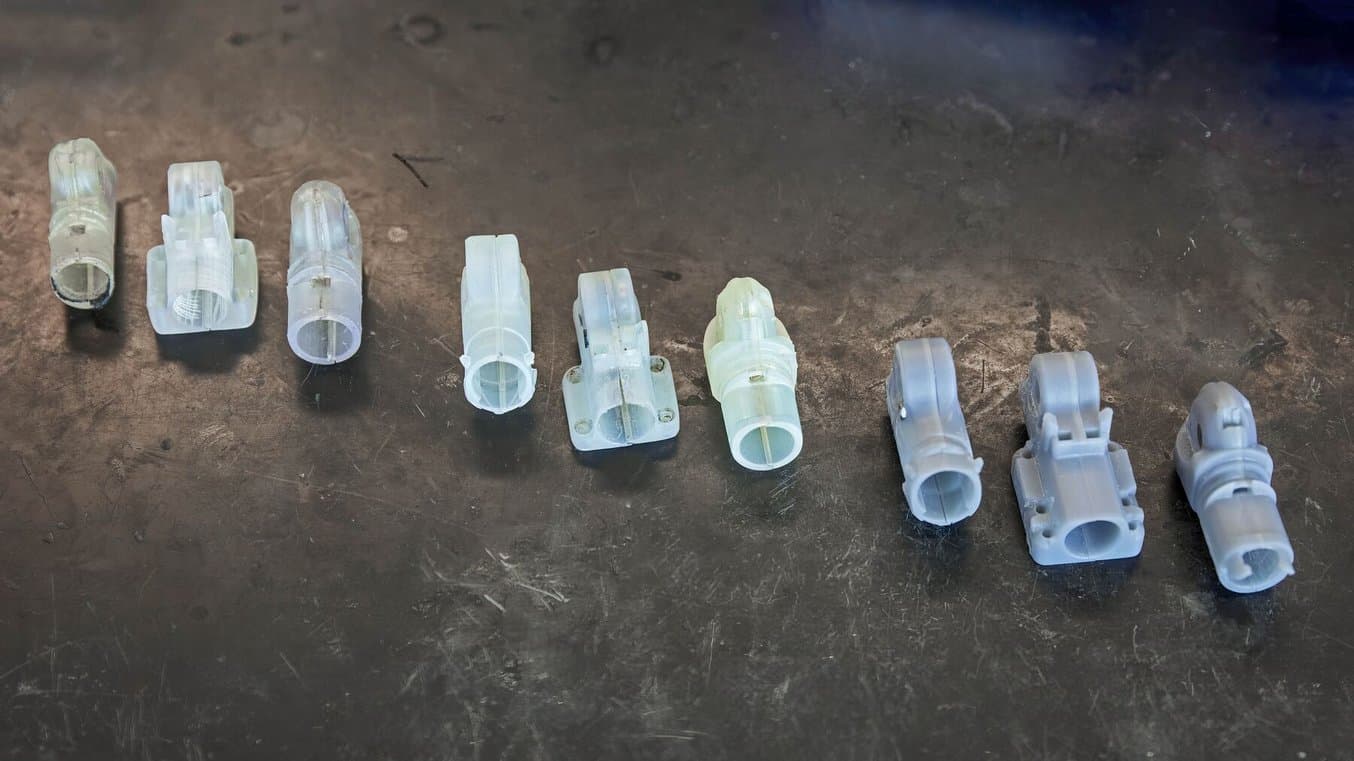
PSYONIC has prototyped countless numbers of parts over the past few years, incorporating customer feedback into the design of the Ability Hand.
新たなデバイスの開発において、ラピッドプロトタイピングは重要な役割を担っています。医療機器の場合、患者や医師から重要なフィードバックを受けることがあるため、その重要性はより際立ったものとなります。医療機器メーカーは、規制や臨床のハードルをパスできるだけの厳密さはもちろん、フィールドテストの準備が整うまでに1つの部品の試作を何百回も行うことがよくあります。Austin氏はAbility Handをテストする際にこれを間近で目の当たりにしてきました。「患者さんが、私が想像もしなかったような方法でハンドを壊してしまうことが何度かあり、それを設計上の対応で簡単に解決できることに気が付きました。そしてその変更して実装し、試作し、検証して、1〜2週間で新しいAbility Handを送り出すことができました。」
「私たちは、その時々に必要なことを最適化するために製造方法のバランスを取るようにしています。試作品の多くは、まずFDMやSLAでプリントされた樹脂で作られます。SLAのレジンによるプリント品でも全く問題ないものもあります。一方で、よりコストがかかりはしますが、金属をCNCで切削して作り、長期間の使用に耐えられる耐久性を重視するケースもあります。このような幅広い選択肢を持つことで、個々の部品に最適な組み合わせが行え、最善の方法を常に採ることができます。製造コストを抑えながら、最高のパフォーマンスを発揮できるのです。」とAustin氏は言います。
最終部品の製造も3Dプリントで
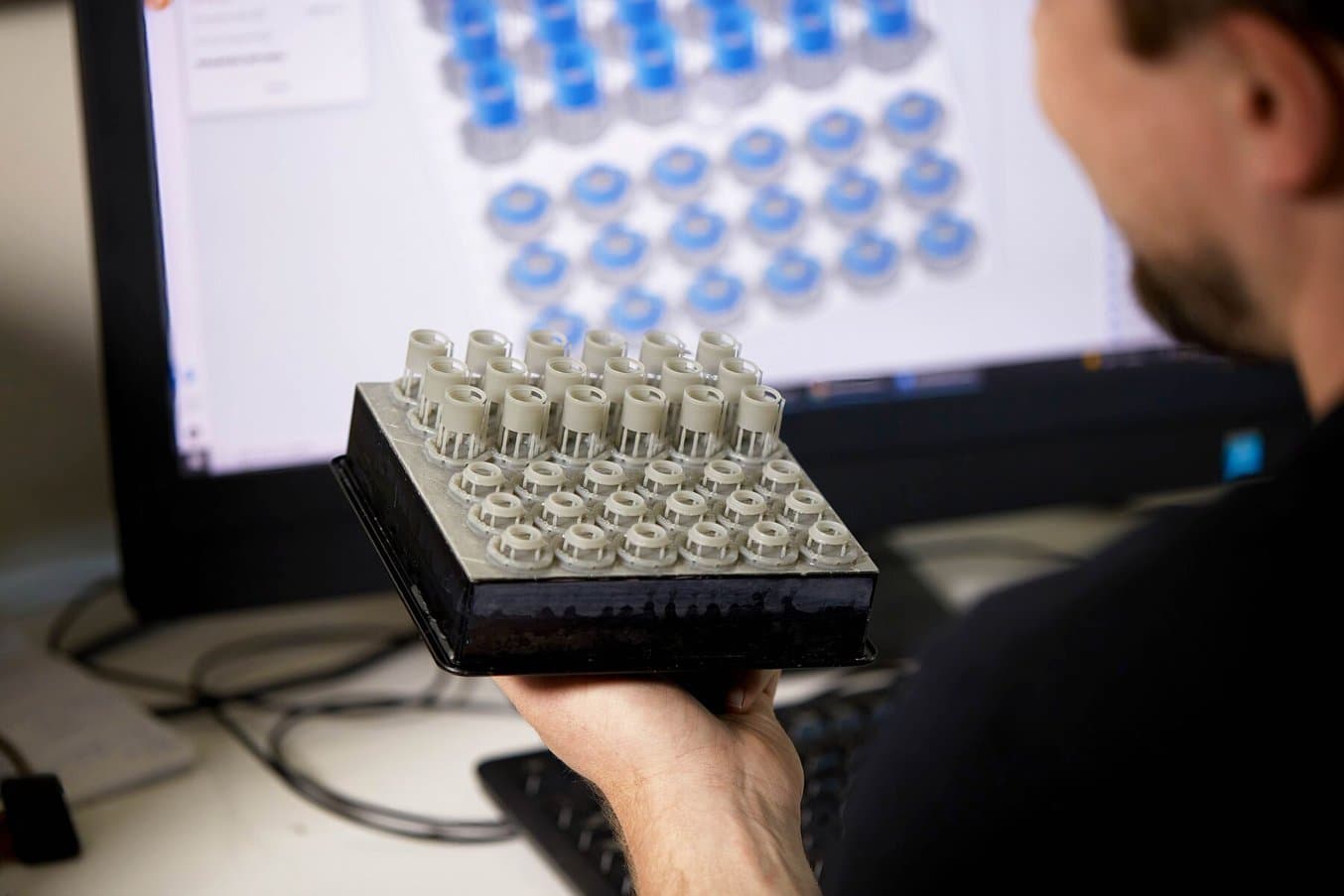
Tough 1500レジンでプリントした最終部品を手にするAustin氏。
近年の3Dプリント材料の進歩により、3Dプリンタ品はそのまま顧客に見せるためのモデルや最終部品にまで対応できるものが増えています。高額なコストを要する金型製作の必要性を低減し、開発期間という面でも大幅な短縮が実現できています。
Austin氏はTough 1500レジンのプリント品を何度も検証し、Ability Handの部品のうち相当な数の最終部品を同レジンで製作できると判断しました。
「SLAでの3Dプリントは、試作品の製作が主な用途でした。しかし事実として、最終部品にもかなり多用しています。特にPPライク材のTough 1500レジンでのプリントは、精度も他のどんな3Dプリント品よりも優れており、経済的にも射出成形より遥かに効率的です。私たちの目的、製造規模、強度、精度、機械的特性、耐熱性、耐衝撃性など、部品に対する物理的な要件においてTough 1500レジンは正直に言って最高の材料です。私たちのすべての製品でずっと使い続けています。」とAustin氏は話してくれました。
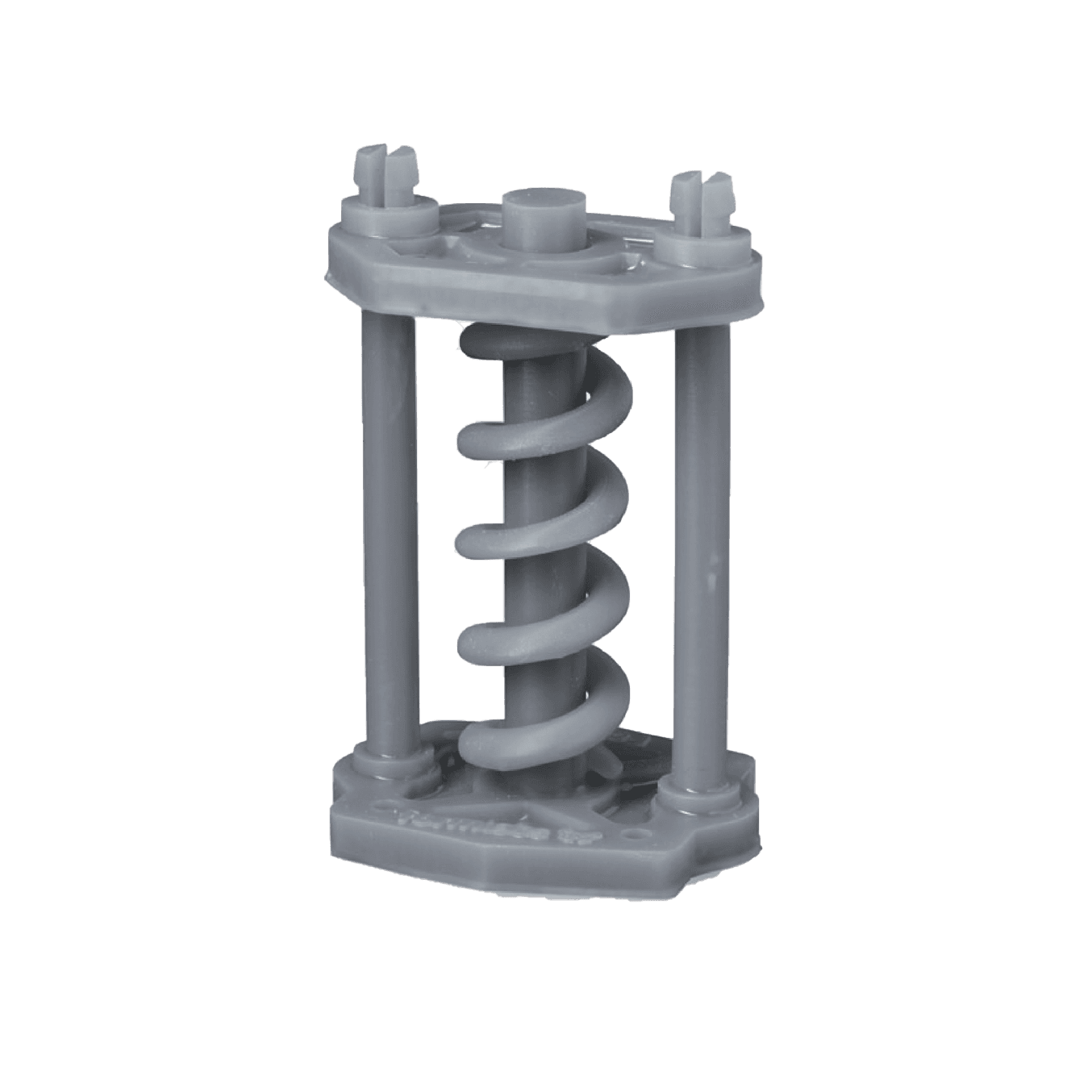
Tough 1500レジンの無償サンプルパーツ
Formlabsのプリンタで実際に造形したTough 1500レジンやその他の材料のサンプルパーツを無償でお届けします。精度や品質を貴社にてご検証ください。
誰からも手の届く製品へ
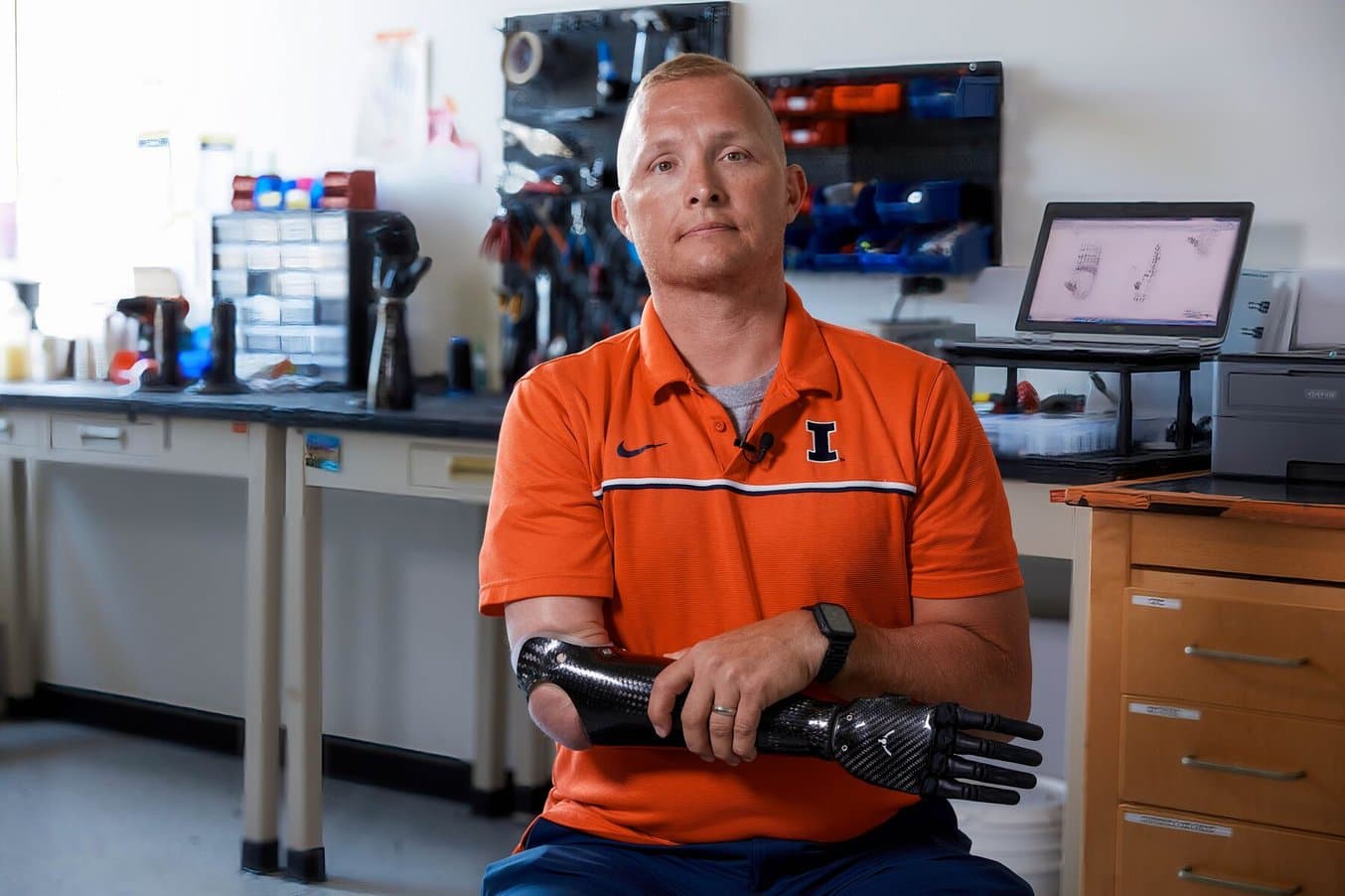
PSYONICのビジネスを成長させるため、Akhtar氏と同社のメンバーは最新のハイブリッド製造技術と革新的なエンジニアリングソリューションを求めました。そしてPSYONICはその事業を拡大し、世界中のユーザーに製品を提供することを視野に入れています。現在のところ同社の事業は北米市場における成長に注力しており、2022年後半にはAbility Handの生産が開始される予定です。
「私たちの患者が求めているのは、日常生活における普通の動作ですが、私たちはそれ以上のことを達成できました。それは、Ability Handの設計に多くの工夫を凝らしたからです。」と、Akhtar氏は語っています。 Anderson軍曹は「今年の初め、この義手で娘の手に触れたとき、初めて感覚として娘の手の感触を感じることができたんです。」と話してくれました。